CO2-Responsive Polymers for Membrane Applications: Synthesis and Adsorption Performance
[Correction added on 15 May 2025 after first online publication: The Article title was corrected.]
Abstract
The pressing need to address climate change has driven research into novel CO2 capture materials. Here, the synthesis of CO2-responsive diblock copolymers, i.e., poly(N-[3-(dimethylamino)propyl]-acrylamide)-b-poly(methyl methacrylate) (PDMAPAm-b-PMMA) through a two-step RAFT polymerization process, as well as the use of the synthesized diblock copolymer as a membrane for CO2 capture were investigated. The resulting diblock copolymer features distinct segments with different properties. The PDMAPAm segment offers CO2-responsive characteristics, while the PMMA segment provides mechanical stability. The gas transport properties of the fabricated thin-film composite membrane composed of PDMAPAm-b-PMMA or PDMAPAm and polydimethylsiloxane with a gutter layer were measured and the CO2 adsorption behavior of both PDMAPAm and PDMAPAm-b-PMMA was evaluated. The copolymer exhibits responsiveness to CO2 and can be customized for use in the fabrication of membranes and membrane adsorbers for direct air capture technologies.
1 Introduction
Carbon capture is a specific area of research that is currently sought after for implementation as a technology [1] in various sectors, including power generation [2], chemical manufacturing [3], and metal production facilities [4], to mitigate CO2 emissions. Apart from that, the small amount of CO2 present in the atmosphere can be captured using the newly developed method known as direct air capture (DAC) [5]. In DAC technologies, a stronger bond between CO2 molecules and the solid adsorbent is necessary, indicating that the process is more associated with chemisorption rather than physisorption [5].
A block copolymer is a type of polymer that derives from combining different polymers as blocks to merge properties like soft and rigid (i.e., in polystyrene-b-polyisoprene), creating a new material with mixed characteristics. Diblock copolymers can have a significant potential as adsorbents for DAC because of their capacity to develop films with a high active area for gas sorption [6-10] and scalability [11-13]. Specifically, diblock copolymers with amine functional groups can exhibit outstanding performance in capturing CO2, given the strong affinity of amine groups for CO2 [14, 15]. Some acrylate polymers such as poly(2-(dimethylamino)ethyl methacrylate) (PDMAEMA) [16-19], poly(N,N-dimethylallylamine) (PDMAAm) [20-22], poly(2-aminoethyl methacrylate) (PAEM) [23, 24] with amine groups that behave CO2-responsive, can be utilized as the first block for further chain extension to diblock or triblock copolymers.
In this research, the focus lies on developing a novel diblock copolymer, specifically poly(N-[3-(dimethylamino)propyl]-acrylamide)-b-poly(methyl methacrylate) (PDMAPAm-b-PMMA), using RAFT polymerization, and its initial application is explored as a thin-film composite membrane and polymer powder for CO2 capture. It should be noted that the type of thin-film composite membranes presented in this work differentiate from the typical gas separation membranes. The thickness of the selective top layer is significantly larger, since the target is to create a type of membrane adsorber.
2 Results and Discussion
The synthesis of PDMAPAm-b-PMMA involves a two-step polymerization of the two monomers. Initially, PDMAPAm was synthesized at 70 °C via RAFT solution polymerization in 1,4-dioxane of the DMAPAm. Subsequently, PDMAPAm serves as a macroRAFT agent to synthesize a PDMAPAm-b-PMMA diblock copolymer by extending the chain through RAFT solution polymerization. Fig. 1 illustrates the pathway for the synthesis of PDMAPAm-b-PMMA.
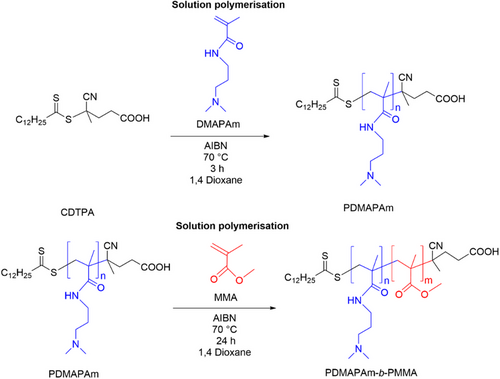
The detailed synthesis procedure of the polymers PDMAPAm and PDMAPAm-b-PMMA is described in previous work [30]. In this study, gas transport properties of the membrane made of the homopolymer PDMAPAm222 and mainly its corresponding diblock copolymer PDMAPAm222-b-PMMA80 were investigated. The diblock copolymer consists of PDMAPAm:PMMA block ratio = 80:20. The apparent number average molecular weights of the polymers were 24.900 g/mol for the PDMAPAm222 and 28600 g/mol for the PDMAPAm222-b-PMMA80, respectively.
The preparation of the PDMAPAm-b-PMMA or PDMAPAm polymer thin-film composite involved three distinct steps. Initially, the polymer PDMAPAm-b-PMMA was dissolved in tetrahydrofuran (THF) to form a solution with a 40 % polymer concentration. Subsequently, this solution was applied to a thin-film composite membrane. This membrane comprises a cross-linked polydimethylsiloxane (PDMS) gutter layer, which is cast onto a porous polyacrylonitrile (PAN) film that is supported by a non-woven substrate. The casting process utilized a doctor blade with a gap set to 50 µm. In the final stage, the cast film was dried under nitrogen (N2) for 24 h. Upon completion of drying, a thin-film composite membrane coated with the PDMAPAm-b-PMMA or PDMAPAm polymer was obtained. The gas transport properties and thickness layers of the PDMAPAm-b-PMMA polymer thin-film composite membrane were then measured using a time-lag device and scanning electron microscopy (SEM), respectively.
2.1 Membrane Morphological Characteristics
The thickness of each layer of the prepared thin-film membrane, coated with PDMAPAm222-b-PMMA80 polymer, was measured using SEM cross-sectional imaging. Fig. 2 represents a cross-sectional SEM image of the PDMAPAm222-b-PMMA80 polymer thin-film composite membrane. The cross-sectional image proves that the membrane has, as expected, three layers: at the bottom, non-woven with a porous PAN layer, which has a thickness of 0.1 µm, then the PMDS gutter layer with a thickness of 40 µm, and on top of it the PDMAPAm-b-PMMA diblock copolymer. From this image, the thickness of the PDMAPAm-b-PMMA was determined to be approximately 2 µm. Since the membrane of the homopolymer PDMAPAm222 was also made with the same method, the thickness of each layer of the PDMAPAm-made thin film composite membrane was assumed to be the same as the diblock copolymer-made membranes.

Another consideration is that the top layer of the membrane, consisting of the PDMAPAm-b-PMMA diblock copolymer, is a non-porous and dense continuous phase. This means that the gas is transported through the membrane at the molecular level via the solution-diffusion mechanism, in which separation is achieved by differences in the solubility of the gases and the difference in the gas concentrations between the feed and the permeate [30].
2.2 Gas Transport Properties
Time-lag and permeabilities of different gases through thin-film composite membranes with and without the PDMAPAm and PDMAPAm-b-PMMA polymer-coated were measured using the time-lag machine to characterize the gas transport properties of the membranes. As mentioned in our previous publication [30], the membrane without coating exhibits extremely high permeability values for all measured gases (vapor H2O, CO2, O2, N2), which means it shows no resistance to these gases. However, after coating it with PDMAPAm or PDMAPAm-b-PMMA polymers, the permeability values turned to be reasonable.
In Fig. 3, the permeabilities of H2O (saturation vapor at a pressure of 10−6 mBar), CO2, O2, and N2 gases are presented, while Fig. 4 compares selectivities of the PDMAPAm222 and PDMAPAm222-b-PMMA80 thin-film composite membranes for the corresponding gases.

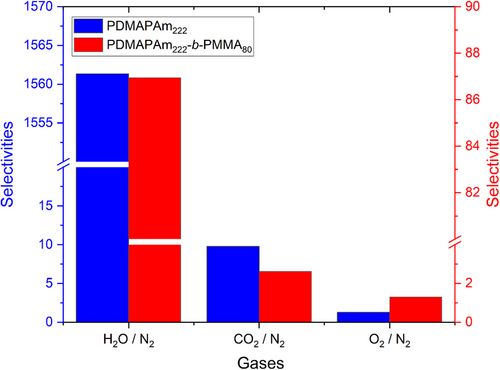
In detail, for the thin-film composite membranes of PDMAPAm and PDMAPAm-b-PMMA, CO2 and H2O gases show larger permeability through the membrane than O2 and N2, making the membrane more selective for H2O and CO2 than N2 and O2. This means that the membranes can separate H2O and CO2 from the rest two gases. As for comparison of gas transport properties of the PDMAPAm222-coated membrane with the PDMAPAm222-b-PMM80-coated membrane, CO2/N2 H2O/N2 selectivities of the homopolymer-coated membrane appear higher than in the corresponding diblock copolymer-coated copolymer. This means that the PDMAPAm-coated membrane can separate CO2 and water vapor from other gases, unlike PDMAPAm-b-PMMA.
The membrane performance can be compared to other types of amine-containing polymers, such as poly(amidoamine) (PAMAM)-based membranes that indicated CO2 permeabilities in the range of 102 to 103 Barrer with CO2/N2 selectivities between 10 and 50 [26]. In addition to that, polyamide-based membranes typically exhibit CO2 permeabilities around 100 Barrer with CO2/N2 selectivities in the range of 10–20 [27], which also meets the selectivities and permeabilities range of PDMAPAm and PDMAPAm-b-PMMA-coated membranes that were obtained from time-lag measurement
Furthermore, by altering the PMMA block amount, different diblock copolymers (such as PDMAPAm222-b-PMMA186, PDMAPAm222-b-PMMA80, and PDMAPAm222-b-PMMA39) of the homopolymer PDMAPAm222 were synthesized. The same kind of thin-film composite membranes were prepared from the polymers and the gas transport properties of the membrane were determined. As illustrated in Fig. 5, by altering the ratio of the first block to the second block of the copolymer (PDMAPAm-b-PMMA), the selectivity of the PDMAPAm-b-PMMA thin-film composite membrane was customized (see Tab. S1 in the Supporting Information). It is clear from the figure below that the membrane's selectivity rises up to five times as the PDMAPAm proportion of the diblock copolymer is increased. This can be explained by the fact that more amine groups that have affinity to CO2 and H2O [14, 28], interact and make the polymer more selective for CO2 in comparison to other gases.
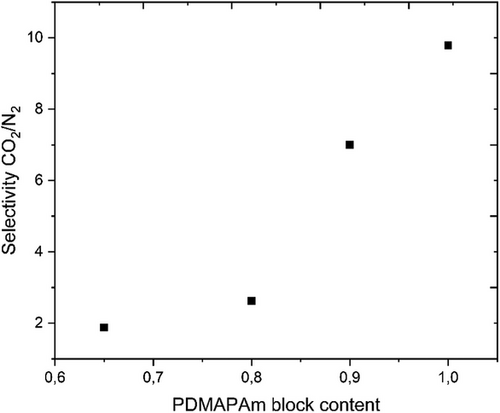
Moreover, considering the thickness of the PDMAPAm222-b-PMMA80 and PDMAPAm222 polymer layer was 2 µm(as mentioned before) and knowing the time lag and permeability of each gas through the membrane, diffusion coefficients and solubility of the gases can be calculated using the equation described in the literature [25].
In Table 1, the calculated values of the diffusion coefficients and solubilities of all four gases for the PDMAPAm and PDMAPAm-b-PMMA polymer film composite membranes are presented.
Polymers | Gases | D [cm2s−1] | S [cm3(STP)/(cm3 cmHg)] | S (CO2)/S (N2) |
---|---|---|---|---|
PDMAPAm222 | H2O | 5.6·10−9 | 2.9·103 | 5.3 |
CO2 | 3.9·10−9 | 2.6·101 | ||
O2 | 1.5·10−9 | 8.7·100 | ||
N2 | 2.1·10−9 | 4.8·100 | ||
PDMAPAm222-b-PMMA80 | H2O | 3.1·10−9 | 8.5·102 | 1.0 |
CO2 | 6.0·10−9 | 1.3·101 | ||
O2 | 2.0·10−9 | 1.9·101 | ||
N2 | 2.2·10−9 | 1.3·101 |
Generally, diffusion coefficients of CO2 and H2O of both PDMAPAm and PDMAPAm-b-PMMA-coated polymer membranes are higher than the diffusion coefficient values of O2 and N2. As for comparison of homopolymer-contained membrane with the diblock copolymer-contained, the CO2 and H2O diffusion coefficients through the PDMAPAm polymer membrane appears almost double times lower than through the PDMAPAm-b-PMMA-coated membrane.
Apart from that, it can be clearly seen from Tab. 1 that CO2 and H2O gases are more soluble in both PDMAPAm and PDMAPAm-b-PMMA-coated polymers than the rest two gases are. Going in more detail, the solubility of CO2 than N2 especially in the PDMAPAm polymer membrane turns to be almost five times higher than in the PDMAPAm-b-PMMA polymer membrane. This can be related to the fact that there is a higher amount of tertiary amine groups per mol in the homopolymer case leading to more physical interaction of amine groups with CO2 than in the diblock copolymer that makes the PDMAPAm polymer membrane more CO2-responsive than PDMAPAm-b-PMMA polymer membrane [30, 31]. This part will be discussed in more detail in our publications.
Furthermore, the PDMAPAm and PDMAPAm-b-PMMA thin-film composite membrane show diffusion coefficients and solubility values for gases that align with the literature for similar polymers. Membranes from hyperbranched polymers such as from poly(amidoamine) (PAMAM) [26] and also polyamide membranes containing PDMS groups [29] exhibit CO2 diffusion coefficients in the range of 10−8 cm2s−1 and solubility values around 10−1 cm3(STP)/(cm3 cmHg)), which agree well with the results in this study.
2.3 CO2 Adsorption Behavior of Synthesized Polymers
Furthermore, to investigate the CO2 capture capacity of the newly developed polymer, CO2 adsorption was measured using the powdered PDMAPAm and PDMAPAm-b-PMMA polymers in the device Rubotherm at 30 °C and up to 2 bar. Fig. 6 illustrates the CO2 adsorption isotherms produced from PDMAPAm222 and PDMAPAm222-b-PMMA80. As it is observed, PDMAPAm and PDMAPAm-b-PMMA polymers illustrate CO2 sorption behavior, and both PDMAPm and PDMAPAm-b-PMMA show similar trends of CO2 adsorption uptake with respect to pressure increase. However, the existence of PMMA in the polymer as a block increases, the CO2 the uptake capacity of the polymer. This may be related to the possible physical interaction that can occur between PMMA and CO2 under mild pressures and temperatures as described in [31].
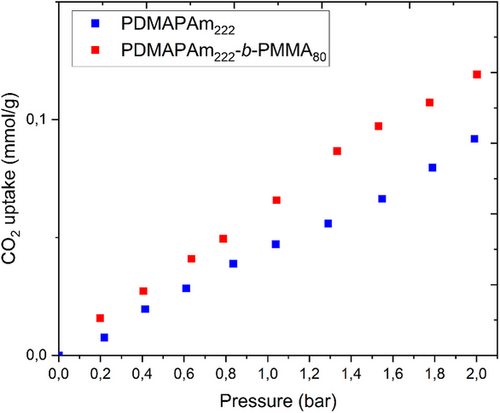
The CO2 uptake capacity of PDMAPAm and PDMAPAm-b-PMMA of 6 mg g−1 at 2 bar and 30 °C is quite comparable with the performance of the other polymers existing in the literature. For comparison, some hyper-cross-linked polymers (HCPs) have shown CO2 uptake capacities ranging from 1.7 mmol g−1 (approximately 75 mg g−1) at atmospheric pressure to 13.4 mmol g−1 (approximately 590 mg g−1) at 30 bar [32, 33]. Another study reported a CO2 uptake of 0.82 g g−1 (820 mg g−1) for certain carbon-sulfur or carbon-nitrogen solid sorbents [34]. While the newly developed polymer uptake is lower than these high-pressure values, it is important to consider the specific conditions and applications.
To sum it all up, both time-lag and sorption measurement demonstrated that the newly developed polymers, PDMAPAm and PDMAPAm-b-PMMA, show CO2-responsiveness because CO2 and H2O diffusion coefficients and solubilities appear to be higher than the rest two gases and the polymers in powdered form exhibit CO2 sorption behavior, which can be comparable with literature. The CO2 sorption and solubility performance of PDMAPAm and PDMAPAm-b-PMMA is promising and could be optimized further for application in DAC technologies.
3 Conclusion
A new CO2-reactive material, namely, PDMAPAm-b-PMMA diblock copolymers, was developed by a two-step RAFT solution polymerization. After that, the gas transport properties of the thin composite film membrane made of the PDMAPAm-b-PMMA polymer and PDMS with a gutter layer were examined. According to the time-lag measurement of the gases, the membrane is more selective for CO2 and H2O than for O2 and N2, which means the membrane can separate CO2 and H2O from the rest of the gases. Additionally, diffusion coefficients of CO2 were calculated to be 2–3 times higher than those for the other three gases, approximately 6.4·10−8 cm2s−1. Ultimately, the CO2 capture performance of PDMAPAm-b-PMMA was evaluated up to 2 bar, revealing that the polymer exhibits significant potential for effective CO2 capture. For the future, this indicates that PDMAPAm-b-PMMA copolymer could be a promising material for application in DAC technologies, which, however, needs to be further advanced via the improvement of polymer synthesis and membrane fabrication.
Supporting Information
Supporting information for this article can be found under DOI: https://doi.org/10.1002/cite.202500056.
Acknowledgment
The authors thank Silvio Neumann and Maren Brinkmann for performing the NMR, TGA, DSC, and GPC measurements, Dr. Evgeni Sperling for SEM measurement, and Dr. Sergey Shishatskiy for his assistance on the Time-Lag measurements. Scientific discussions with Prof. Dr. Volker Abetz are greatly acknowledged. This work was supported by the Initiative and Networking Fund of the Helmholtz Association, project DACStorE (KA2-HSC-12).
Open access funding enabled and organized by Projekt DEAL.
Abbreviations
-
- DAC
-
- direct air capture
-
- PAN
-
- polyacrylonitrile
-
- PDMAPAm-b-PMMA
-
- poly(N-[3-(dimethylamino)propyl]-acrylamide)-b-poly(methyl methacrylate)
-
- PDMS
-
- polydimethylsiloxane
-
- SEM
-
- scanning electron microscopy