Isoprene-Styrene Copolymers: Synthesis and Possible Use for Hydrogen Applications
Abstract
The application of isoprene-styrene-based copolymers synthesized via surfactant-free controlled radical polymerization in the area of hydrogen research is presented. The polymers were synthesized in the laboratory and on a pilot scale and tested for their gas transport properties in correlation with the already known commercial poly(4-methyl-1-pentene). The results indicated that the new materials could have applications in terms of hydrogen applications due to the comparable permeability of hydrogen and, in some cases, increased selectivity of hydrogen over oxygen. Further future work will indicate how the new polymers will be utilized.
1 Introduction
Hydrogen is increasingly recognized as a valuable energy carrier due to its potential as a clean, low-carbon alternative. With its high energy density and ability to be stored and transported efficiently, hydrogen can offer a promising solution for decarbonizing sectors such as transportation, industry, and power generation [1-4]. As nations work toward their climate goals, hydrogen can help reduce environmental pollution and reliance on fossil fuels. However, a key challenge remains the safe and efficient storage of hydrogen, given its low volumetric energy density in the gaseous state and the associated risks of flammability [5, 6]. Developing secure storage methods is crucial for the large-scale deployment of hydrogen as a sustainable energy source.
Sustainable hydrogen storage is important for our society as an alternative to the continuous use of fossil fuels that increase the CO2 emissions polluting our environment. Combining lithium-based reactive hydride composite materials (Li-RHC) with poly(4-methyl-1-pentene) (TPX™) enhances hydrogen storage stability by preventing long-range phase segregation and also degradation from contact with the atmosphere [7-9]. Although TPXTM is a highly interesting low-cost material, it is always motivating to work on the properties of this material and especially on the synthesis of alternative polymers capable of being used for hydrogen storage composites.
Given the structural similarity between hydrogenated polyisoprene and poly(methylpentene), this study focuses on synthesizing isoprene homopolymers and isoprene-styrene copolymers at various ratios using eco-friendly, surfactant-free reversible addition-fragmentation chain-transfer (RAFT) emulsion polymerization. Our first goal was to optimize the polymerization conditions to achieve high molecular weight and monomer conversion, which proved challenging. Surfactant-free RAFT emulsion polymerization, also known as polymerization-induced self-assembly (PISA), is an environmentally friendly and scalable technique. It reduces reliance on organic solvents, improves heat transfer, and enhances process safety while allowing the synthesis of polymers with various block units [10-14]. Apart from that, in this work, a first step towards the characterization of the newly prepared polymers for their gas transport properties in relation to their use as hosting materials for metal hydrides was done. More in detail, the gas transport properties of H2, CO2, and O2 were investigated, indicating the application of the materials before the hydrogenation step for the polyisoprene block.
2 Experimental
The synthesis of the copolymer is presented in Fig. 1.
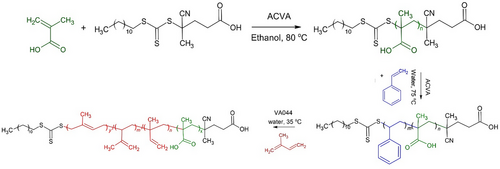
Using a poly(methacrylic acid) macroRAFT agent, random and block PS-PI copolymers were successfully synthesized, targeting a molecular weight of 50 000 g mol−1 and achieving high monomer conversion. The synthesis is described in detail in previous work [15]. In detail, for the polymers used in this work, two copolymers with a PI/PS ratio of 60 and a homopolymer of polyisoprene, designated as PMAA-b-PS40-b-PI60 (B60), PMAA-b-P(S40-b-I60) (R60), and PMAA-b-PI (PI) were prepared.
The PMAA-b-PS-b-PI was synthesized in three steps. First, the macroRAFT agent based on PMAA was synthesized following the literature [16]. A typical synthesis of PMAA via RAFT solution polymerization was conducted according to [15] using 4-cyano-4-[(dodecylsulfanylthiocarbonyl)sulfanyl]pentanoic acid (CDTPA) and (4,4′-azobis(4-cyanovaleric acid) (ACVA) as the initiator, dissolved in ethanol. Methacrylic acid (MAA) was added to the mixture ([typical ratio MAA]/[CDTPA]/[ACVA] = 909/9.5/1) with 0.3 mL DMF that was used as the internal standard for conversion calculation. The solution was degassed by purging with nitrogen for 15 min at 0 °C. The polymerization reaction was conducted in a thermoshaker (CellMedia, Germany) at 80 °C and 850 rpm for 9 h and then quenched by ice-cooling and exposure to air. Subsequently, the reaction solution was precipitated in ice-cold diethyl ether. After that, the polymer was dried, dissolved in THF, and precipitated in diethyl ether. The polymer was dried in vacuum at 30 °C for 24 h and obtained as a light-yellow powder.
A final PMAA conversion of above 77 % could be achieved as it was calculated using proton nuclear magnetic resonance (1H NMR) spectroscopy, while the molecular weight was identified by gel permeation chromatography (GPC) using tetrahydrofuran as eluent and polystyrene as molecular weight standards. Following that step, PMAA-b-PS was prepared through emulsion polymerization following the literature [16], which was subsequently chain extended with a PI block.
For the synthesis of PMAA-b-PS, ACVA together with an additional amount of NaHCO3 (for the dissolving of ACVA in water) were dissolved in water in a polymerization vial. Then, PMAA macroRAFT agent/macro was dissolved in the prepared solution, and styrene was added to the solution (solid content: 20 wt %). The solution was degassed by purging with nitrogen for 15 min at 0 °C. The polymerization reaction was conducted in a thermoshaker at 75 °C and 800 rpm for 2 h and 30 min, achieving a complete conversion as indicated by 1H NMR spectroscopy. Then, the reaction was quenched by ice-cooling and exposure to air.
The synthesized PMAA-b-PS emulsion was directly used for the chain extension with PI block. To this end, PMAA-b-PS emulsion was transferred to the polymerization ampul. Then, VA044 (2,2′-azobis[2-(2-imidazolin-2-yl)propane] dihydrochloride) initiator was dissolved in water to reach a total solid content of 20 wt % for the polymerization. Then, isoprene was added to the solution in the ampule, followed by the same procedure as in the PMAA-b-PI synthesis. The polymerization continued for 24 h at 35 °C. ¹H NMR spectroscopy confirmed the successful synthesis of the block copolymer.
3 Results and Discussion
The molecular characteristics of the synthesized polymers are given in Tab. 1.
Samples | I/Sfeed [% mol] | I/SNMR [% mol] | Conversion [%] | [g mol−1] | * [g mol−1] | Ð |
---|---|---|---|---|---|---|
PI | 100 | 100 | 84 | 43 300 | 28 000 | 2.3 |
R60 | 60 | 50 | 83 | 47 700 | 15 000 | 2.3 |
B60 | 60 | 55 | 73 | 44 500 | 49 000 | 2.1 |
In addition to the successful synthesis of the polymers, their functionality as membrane materials capable of incorporating metal hydrides for sustainable hydrogen storage was a critical aspect of this study [17]. Membrane films of the synthesized polymers (PI, R60, and B60) were prepared using a solution casting method with 5 wt % polymer solutions in THF. A certain amount of the solutions containing 260–300 mg of the polymer was directly cast into a metallic ring placed on a glass plate. Solvent evaporation was performed under constant nitrogen flow at ambient temperature. The films adhered strongly to the glass plate and were peeled off by introducing water into the metallic ring. Subsequently, the films were carefully removed and dried under vacuum at 24 °C for 24 h to ensure the complete removal of solvent residues.
The membrane film of TPXTM was prepared using the same procedure as the other polymers, with hot solution casting at 80 °C. A 5 wt % solution of TPXTM in n-hexane (containing roughly 270 mg TPXTM) was cast directly into a metallic ring placed on a glass plate. The film was carefully removed without the need for water introduction and dried under vacuum at 24 °C for 24 h to ensure the complete removal of solvent residues.
Consequently, comprehensive membrane characterization was performed to evaluate their suitability for this application. Notably, gas transport properties tests for H2, N2, O2, and CO2 gases of membrane films of the synthesized polymers showed a reduced H2 permeability. In particular, the R60 membrane exhibited an H₂ permeability of 10.0 Barrer, which is 12 times lower than that of TPX™, while showing improved H₂ selectivity by factors of 1.5, 2.1, and 1.7 over N₂, O₂, and CO₂, respectively (Fig. 2).
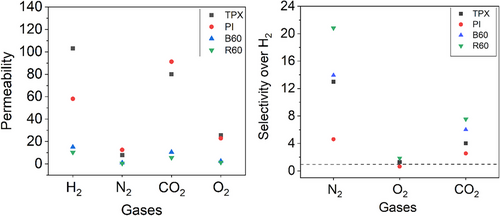
H2 exhibited higher diffusion coefficients across all tested membranes compared to O2, N2, and CO2, with values of 8.7·10−6 cm2s−1, 3.6·10−6 cm2s−1, and 4.0·10−6 cm2s−1, respectively, for PI, R60, and B60. This trend aligns with H2’s smaller molecular size (kinetic diameter: 2.89 Å), which facilitates easier diffusion through the polymer matrix compared to larger gases like O2 (3.46 Å), N2 (3.64 Å), and CO2 (3.3 Å) [18-20]. For instance, the diffusion coefficient of H2 in R60 was 22-fold higher than that of N2, underscoring the influence of molecular size on diffusivity.
The solubility of CO2 was significantly higher than that of the other gases, obtained as 1.3·10−2 cm3(STP)/(cm3cmHg) in R60, compared to 2.9·10−4 cm3(STP)/(cm3cmHg), 3.0·10−4cm3(STP)/(cm3cmHg), and 1.9·10−4 cm3(STP)/(cm3cmHg) for H2, O2, and N2, respectively. This enhanced solubility is attributed to CO2’s condensable nature and its strong interactions with polar functional groups in the polymer [21, 22]. Specifically, the synthesized polymers display significantly higher CO2 solubility compared to TPXTM with the value of 8.8·10−3 cm3(STP)/(cm3cmHg), primarily due to the interactions between CO2 and the polar PMAA segments (13 %) incorporated during the surfactant-free RAFT emulsion polymerization process.
Based on the solution-diffusion mechanism, gas permeability is controlled by both gas diffusivity and solubility [23-25]. The higher permeability of H2 compared to O2 and N2 is, therefore, largely attributed to its superior diffusivity. However, since solubility also plays a critical role in permeability, CO2 exhibits higher permeability than N2 in some membranes despite its larger size and exceptionally high solubility.
The selectivity plot illustrates the H2/gas selectivity of four polymer membranes (R60, TPXTM, B60, and PI) for N2, O2, and CO2. H2/N2 selectivity is highest for all membranes, with R60 achieving the maximum value of approximately 22, followed by TPXTM at around 16, B60 at 12, and PI at 10. The results demonstrate the superior H2 selectivity performance of the R60 membrane compared to the TPXTM membrane.
4 Conclusion
The synthesized R60 polymer demonstrates superior selectivity, particularly for H2/N2 separation, compared to TPXTM, highlighting its potential for gas separation applications. However, its permeability remains inferior to that of TPXTM, which limits its overall performance. To address this, strategies such as optimizing molecular weight, increasing branching, or enhancing crosslinking in low PS-content membranes, alongside hydrogenation of PI, could improve permeability and mechanical stability, positioning R60 as a competitive candidate for industrial-scale gas separation technologies. To sum up, as mentioned, these membranes are in the first steps of their developement and have the necessity to be further optimized in order to become comparable with other standard membranes (i.e., polyimide membranes) used in hydrogen application.
Acknowledgment
The authors thank Silvio Neumann and Maren Brinkmann for performing the 1H NMR and GPC measurements, Dr. Sergey Shishatskiy, Emil Pashayev and Fan Yang for their assistance with the time-lag measurements. Scientific discussions with Prof. Dr. Volker Abetz are greatly acknowledged. This work was supported by the BMBF Project HyPoKo (03SF0657A-D).
Open access funding enabled and organized by Projekt DEAL.
Abbreviations
-
- B60
-
- PMAA-b-PI60-b-PS40
-
- PI
-
- poly(isoprene)
-
- PMAA
-
- poly(methacrylic acid)
-
- PMAA-b-PI-b-PS
-
- poly(methacrylic acid)-b-poly(isoprene)-b-poly(styrene)
-
- RAFT
-
- reversible addition-fragmentation chain-transfer
-
- R60
-
- PMAA-b-P(I60-r-S40)
-
- TPX™
-
- poly(4-methyl-1-pentene)