One Century of Bioenergy in Germany: Wildcard and Advanced Technology
Abstract
Bioenergy is the oldest renewable energy resource and has a long tradition in heat provision. However, with the establishment of the chemical industry and engineering the application field as extended to the power and the transport sector. This article outlines the development of power and fuel production from biomass over a period of hundred years until today, as well as future prospects. The crucial technical innovations of bioenergy with regard to political and historical events are reflected. Despite of improvements in the last decades, mainly associated with issues like resource availability, technical efficiency or emission mitigation, the future energy supply by biomass has to be even more efficient, demand-oriented and integrated step-by-step in a more renewable energy system.
1 Introduction
Bioenergy is almost as old as humankind. However, from the discovery of fire, sometime between 500 000 and 1 500 000 years ago 1 there was a long way to technology development of bioenergy. This development was accompanied by social expectations of bioenergy's capabilities. The classical sequence of energy transition in the major economized states had followed gradual shifts from total reliance on fuelwood and charcoal to increasing uses of coal, in both domestic and industrial settings 2 (Fig. 1). Especially with the beginning of the industrialization and the economic and social upswing, plants as energy source became less important, as fossil energy resources with a much higher energy density were increasingly used. Nevertheless, in times of energy crises or in phases of agricultural overproduction, technology development of bioenergy has received a push. Hence, on the one hand a continuous use of wood in small heating and cooking devices can be stated, but on the other hand, new bioenergy carriers had been developed for a wider application within the fossil supply system. Therefore, the provision and application of bioenergy from gaseous and liquid biofuels has dramatically changed since the first volume of Chemie Ingenieur Technik has been published in 1928. Beside the use for heating purposes, in the beginning of the 20th century biomass was also used to produce electricity and liquid biofuels.
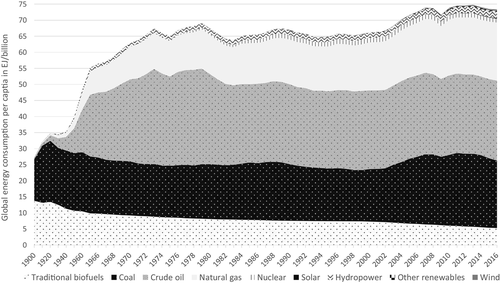
In this paper, an overview of the development of bioenergy with a special focus on liquid and gaseous bioenergy carriers in Germany for the timeline between 1928 and 2028 is given. Important frame conditions and key technology developments are figured out, which have driven the bioenergy use over different periods. Furthermore, the actual use is pictured and, finally, the important strategic steps for bioenergy expected for the next decade is discussed. With this chronicle, we take the chance to congratulate the journal and hope that we can discuss in the 100th volume of CIT in 2028 about the real-world experiences of today's estimation.
In the following the main technical developments and use of liquid and gaseous bioenergy carriers in Germany are described during: (1) the first half of the last century – from the 1920s to the end of the Second World War, (2) the cold war between 1946 and 1989, (3) the German bioenergy boom from 1990 till the 2010s, (4) the actual status, and (5) future expectations. An overview on the most relevant milestones in the last century is provided. Nevertheless, the largest share of biomass for energy use in all the decades is dedicated to the provision of heat from wood ovens, stoves and boilers. With more than 10 million installations in Germany also today 3 the combustion of solid biofuels is the silent giant of the renewable energy supply. Overall woody biomass provides about 90 % of the global primary energy annually 4.
2 From 1928 to 1945, Era of the Weimar Republic to the Nazi Regime: Answers to Energy Hunger and Wastewater Problems
Urbanization and industrialization have been in full progress in Germany at the beginning of the 20th century. In 1930s around two thirds of the Germans lived in cities with more than 20 000 inhabitants and around a quarter in large cities with more than 100 000 inhabitants 8. This came along with increasing amount of waste and wastewater and the need for safe street lighting and more energy. Eventually, the mid-twenties of the last century were quite a successful time for the development of new technical processes in industrial chemistry, which also influenced the application of bioenergy significantly in the present (cf. Tab. 1). Nevertheless, biomass was used mainly traditional, in the sense of oven wood and charcoal and as biofuel for the muscle power of the vehicle horse (see Box 1).
Box 1. Biofuels 100 years ago A short history of a bio-based journey from Leipzig to Berlin |
100 years ago, around a quarter of the agricultural area in Germany was still used for the cultivation of oat (Rainer Tietböhl, Deutscher Bauernverband, DBV 9) to feed the 3.7 million horses 10. The agricultural land for oat was with around 3.5 M ha 11 the second largest after rye and before wheat 12. The close linkage between the number of kept horses (1927, 8.1 km−2, 13 and the size of the harvest oat can be retraced until the 1960s 14. Today, oat accounts only around 1.8 % (115 500 ha) of the cultivation land for cereals 15, 16. |
A rough calculation comparing the necessary cultivated land for oat in 1928 and biodiesel (rape) nowadays for a distance between Leipzig and Berlin (190 km) reveals the following results. The agricultural land for the cultivation of oat is almost 2- to 5-times as large (194 m2) as it is needed for the cultivation of rape for biodiesel (76 m2). The calculation is based on the assumption, that a moderate horse (600 kg) with an average speed of 21 km h−1 needs around 443 MJ digestible energy (DE) per day, being equitable to ca. 38.6 kg of oat 17. For the needed energy content per ha cultivated land this means for 190 km around 2.3 MJ m−2 for oat in 1928 and 5.8 MJ m−2 for biodiesel nowadays. The distance of 190 km can be compared with the fastest pony-express of 1850, which needed 8 h and 10 min for a distance of 193 km running with an average speed of ca. 24 km h−1 18. Consequently, the progress in biofuel production is less area, faster velocity, greater distance and better availability. Moreover, it has to be considered, that actually at least two horses are need, if one should always be at the start. |
Since the early 1990s, rapeseed press cakes have been used successfully in animal feed, especially for cattle and pigs. Other possible applications include fermentation (biogas plants), composting or fertilization 19. Last but not last, during biodiesel production rapeseed cake is a by-product. Therefore, it is nowadays possible to run a car and feed animals in parallel. |
2.1 Biogas Production along with Wastewater Treatment
Anaerobic digestion (AD) of biomass for producing biogas is known since centuries. Primarily biogas was used to generate heat and later also electricity 20, 21. The roots of the modern biogas technology (anaerobic technology) in Germany were marked mainly at the end of the 19th and beginning of the 20th century by the developments of urban water management due to accumulating wastewater and accompanying (drinking) water pollution 22. At the beginning, the utilization of energy was not focused in AD processes. It was rather regarded as a by-product of wastewater treatment. In the first half of the 20th century the microbial and biochemical process of AD from organic matter was intensively investigated 23, 24. First special digesters for large-scale anaerobic wastewater treatment were built in Germany by Prof. Karl Imhoff 20, 25 in the 1910s and 20s (cf. Fig. 2 and Tab. 1). This was the start for distributing sewage gas (later known as biogas) via gas systems in urban areas for production of heat and electricity. Based on a patent of Imhoff, the first heated digestion tanks, which were separated from the actual wastewater treatment process, were used for anaerobic sewage sludge treatment in Essen. From 1927 on, the wastewater treatment plant in Essen was the first feeding-in surplus sewage gas in the public gas network and selling the product. Further cities followed 20. Due to the fuel shortage in 1937, the cities of Halle, Pforzheim, Essen, Erfurt, Pössneck, Munich and Heilbronn even replaced liquid fossil fuels in their municipal vehicle fleets with Otto engines by biogas. However, the gas had to be compressed and was delivered in heavy steel cylinders 25. The German chemical company IG Farben produced light rubber tanks, which could be easily mounted on the roof of the buses and cars 26. To increase the yield of sewage gas, further organic matter and waste was added to the slurry (also called as co-fermentation) of the German wastewater treatment plants. For example, in Stuttgart material from grease separators was co-fermented from 1940 on 27. Nevertheless, at this time the potential of biogas production from sewage sludge and organic municipal waste was regarded as limited 28.
Main scientific events and technical applications in the bioenergy sector |
|
---|---|
Beginning of the 20th century until 1945 bioenergy as answer to energy hunger and wastewater problems |
|
Around 1900 |
City and synthesis gas is mainly produced by coal gasification. |
1910s – 20s |
First special digesters for anaerobic wastewater treatment (Imhoff). |
1920s |
Invention of first technically mature wood gas generators for mobile use (Imbert). |
1925 |
Fischer and Tropsch invented a synthesis process of diesel-like fuel from coal. |
1927 |
First feeding-in surplus sewage gas in a public gas network by the wastewater treatment plant in Essen. |
1927 |
World's first hydrogenation plant at the Leuna plant (based on the Bergius Pier process). |
1928 |
First edition of the CIT. |
1930s |
Development of a process to hydrolyze cellulose from wood chips (Scholler). |
1931 |
Start of mass production of the Imbert generator by the German company of Johannes Linneborn. |
1931 |
Nobel Prize in Chemistry for Bergius Pier process/coal liquefaction (as basis for direct liquefaction of biomass). |
1937 |
First operation of municipal vehicle fleets with biogas in the cities of Halle, Pforzheim, Essen, Erfurt, Pössneck, Munich and Heilbronn. |
1940 |
Optimization of fuel from grass, leaves, seaweed, sawdust, scrap lumber, corn, etc. (Berl, Technical University Darmstadt). |
1944 |
Imhoff builts an agricultural plant producing biogas from manure and agricultural waste and residues. |
1946 – 1989: Cold war and bioenergy reanimation only after the energy crisis |
|
1947/48 |
First operation of agricultural biogas plants in Germany (e.g., in the Odenwald). |
1950s |
Construction of 13 biogas plants according the system Schmidt-Eggersglüss. |
1953 |
First industrial-scale thermophile pilot biogas plant was operated in Thuringia (GDR). |
1958 – 86 |
Operation of the longest-operating biogas plant (farmer Resch from Bernloch, Swabian Alb). |
1967 |
Central role of acid-producing bacteria in the fermentation was recognized. |
1970s |
First resumption of activities on biomass gasification and liquefaction. |
1973 |
State funding research on the combustion of straw and wood is established in Bavaria (Bavarian State Institute for Agricultural Engineering). |
1980s |
Establishment of eight demonstration and pilot biogas plants in industrial-scale in the GDR. |
1988 |
Increasing efficient and controlled biomass combustion systems due to the introduction of emission limit values for small combustion plants according to the BImSchV. |
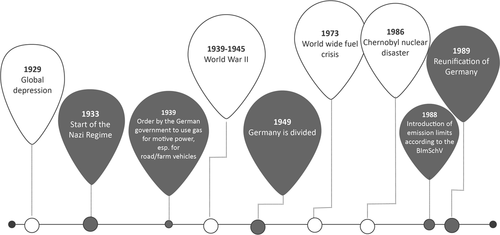
In addition, municipal waste management became necessary. In 1906 the Charlottenburger Abfuhrgesellschaft in Berlin introduced a three-part system, separating the house waste in ash/slag, kitchen/food waste and rubbish (e.g., rags, old clothes and shoes, glass, old furniture) based on an American model. Even it was ceased in 1917 because of financial reasons and the unwillingness of the population to participate, it was the starting point for the provision of residues for biogas treatment 29.
Finally, also the first biogas plant for manure was established. In general, the first biogas plants in the agriculture were very small-scale and homemade plants, constructed by farmers or agricultural engineers in Bavaria and Baden-Württemberg. This development was motivated, as large amount of semi-liquid manure along with logistical and odor problems occurred 25. At that time processes were used, which are similar to co-fermentation. Hence, the rise of agricultural (biogas) plants had started. In 1944 an agricultural plant that produced biogas from manure and agricultural waste and residues was built by Imhoff 30.
2.2 New Processes for a Wider Application of Solid Fuels
In the 20s leading chemists in Germany realized that due to progressive developments in science and technology new cross-border disciplines of chemistry opened up, which linked the work of chemists with the one of engineers and apparatus constructors 31. This initiated a lot of innovations, such as the Fischer-Tropsch process, Bergius process, wood gasification, but also an increasing fuel demand. Mainly coal, wood and peat were used for energy generation and chemical processes. To increase the availability of liquid and gaseous fuels, gasification processes were developed and became the dominant energy conversion technology, which enabled the industrialization process 32. Three pathways were mainly developed: provision of town gas, dedicated gas generators and vehicles, and generation of liquid fuels by thermochemical processes.
Provision of Town Gas
In particular, the gasification technology represented an integral feature in the public supply of gas and electricity. To assure working also in times with daylight, from the middle of the 19th century on so-called illumination gas was provided by municipal companies in the cities. Therefore, it was also referred to as town or city gas. Later the gas was also used for the operation of gas cookers and boilers. Town gas was produced mainly from coal (coal gas) in gas plants by gasification. It contains mainly hydrogen (ca. 50 %), followed by methane, nitrogen, carbon monoxide, and volatile hydrocarbons in small quantities. In times of coal scarcity also wood, peat or other organic compounds were utilized 33. Almost all middle and larger cities run a gas plant and provided the gas via municipal gas networks. Only in the 1960s the gas supply was transferred from town to the cleaner natural gas 34.
Dedicated Gas Generators and Vehicles
Due to the huge shortage of liquid fuels in Germany and other European countries, experiments were made to run vehicles on wood, coal, or even both. Generators were constructed or improved to convert timber, charcoal and coal at a high temperatures (between 1600 und 1800 °C 35) into a sufficiently tar-free syngas (consisting of atmospheric nitrogen, carbon monoxide, hydrogen, traces of methane, and other gases), also called wood gas or producer gas. After cooling and purification, the gas was injected into the cylinders of a regular internal combustion car 36, 37. The gas was also effectively used in (stationary) industrial applications, such as saw mills and pumping stations, fire boilers for industry and home or as basic chemical feedstock, such as ammonia for fertilizers 35. First technically mature wood gas generators for mobile use were developed by the Lorraine chemist and engineer Georges Imbert in the 1920s. In 1931, he sold the licenses, among others, to the Germany company of Johannes Linneborn and the mass production of the Imbert generator started 36, 187, 188. Under the Nazi regime, and especially during Second World War, wood gas generators in vehicles were pushed mainly due to reasons of energy autarky (see Sect. 2.3).
Generation of Liquid Fuels by Thermochemical Processes
In general, at that time biofuels from renewable resources were usually used in niche markets as they tended to be too expensive. However, the main aim was to achieve independence from foreign raw materials and to save foreign exchange as part of the autarky efforts of the Nazi regime. 38 Ethanol from paper processes, gases and liquids from wood pyrolysis units, as well as vegetable oils for diesel engines were common. Yet, biofuels have been increasingly chosen in case of emergency fuel shortages or agricultural surpluses 39. Next to the wood gas technology, Fischer and Tropsch invented a synthesis process of diesel-like fuel, which was patented in 1925. Conventional vehicle fuel could be substituted, which ultimately covered 90 % of German consumption at that time 40.
Another way to produce fuel from brown coal (lignite) is the Bergius Pier process. In 1913, Dr. Friedrich Bergius discovered a process for coal liquefaction, for which he was awarded with the Nobel Prize in Chemistry in 1931. Due to further developments of the BASF chemical engineer Dr. Matthias Pier in 1927, the world's first industrial-scale hydrogenation plant for producing gasoline and coal was put into operation at the Leuna plant 41-43. BASF bought the patent and built several plants to supply Germany with synthetic fuel and lubricants 41. In the years 1943/44 about 4 million t a−1 of gasoline were produced in 12 hydrogenation plants. In addition, 600 000 t a−1 petrol was produced in nine Fischer-Tropsch plants 44 and used for the aircraft fleet and other military purposes 45. Compared to petroleum-based fuels, however, both processes were not competitive, so that they did not play a role after the war. Although these processes were based on (brown) coal (coal-to-liquid, CtL), they initiated the interest in solid-to-liquid fuel technologies, also applicable for biomass (especially wood, straw, energy crops) 40. Most of the synthetic fuels, about 1.7 billion liters, were produced in 1942 from coal. After all, about 267 million liters of ethanol fueling German road vehicles were mainly produced from potatoes. It is estimated that 54 % of the pre-war German fuel production was derived from non-petroleum sources, of which only 8 % was ethanol from renewable sources 46. In the 1930s, Heinrich Scholler developed a process to hydrolyze cellulose from wood chips by an acid-based process 47. Ernst Berl, a chemical professor at the Technical University Darmstadt optimized the process and made fuel from grass, leaves, seaweed, sawdust, scrap lumber, corn, cornstalks and cotton 48. In Europe over 20 plants converting wood wastes to ethanol via the Scholler process were constructed by 1941, mostly in Germany, Italy and Switzerland 49.
2.3 Wood as Precious Fuel for Energy Autarky
In general, two major developments characterize the wood consumption under the Nazi regime. On the one hand, the total wood consumption increased because of the economic recovery. On the other hand, initiated by the German policy of autarky, big efforts were made to decrease the relative wood consumption (use of wood per produced unit) in order to reduce the dependency on imported timber 50. The numbers for harvesting fuel wood is statistically proven only for few years. It was almost halved from 1927 with 24.7 M solid cubic meter 189 to 1939 with 12.1 M 50, 51, by public campaigns and administrative measures 50. It is assumed that the use of fuel wood in rural areas is not included in these statistics. Nevertheless, wood savings were realized mainly by decreasing the demand of fuel wood and residues and waste, which should be used more effectively.
Measures were taken to support coal-, gas-, electro- and more effective wood-fired ovens in the households, as well as to improve the supply of alternative fuels as coal and gas 52, 53. Furthermore, in 1937 a regulation was issued prohibiting the burning of raw wood that can be still used as timber (Regulation on promoting the harvesting of timber). Further strategies based on the autarky policy foresaw that no wood residues should possibly be generated or largely be utilized further, respectively 54. Therefore, wood chips were boosted for the relatively new wood hydrolysis industry or, after particular preparation, used in wood gas generators (see Sect. 2.2). By the end of the war five wood hydrolysis factories were operated, which produced mainly alcohol as additive for petrol and diesel 55.
The decade from 1930 to 1940 is characterized above all by the further development of small automotive and portable gas products 56. At the end of the 1930s, about 9000 wood gas vehicles were in use in Europe 190. To increase the numbers of these vehicles, from 1935 on the adaption from petrol/diesel-powered vehicles was granted by the National Socialist government and the taxes were reduced 54, 57. Further, the establishment of a nationwide net of wood petrol station was started 58, 59. In 1935, a test drive of an average of 12 000 km with 46 lorries with generators of different design and different fuels (wood, charcoal, peat coke, etc.) was carried out with the aim of further development of the generators 54. The four-year plan of 1936 scheduled a network of about 2300 wood petrol stations 60, 61. In 1941, special prepared wood and charcoal for gas producer vehicles were sold at over 1000 petrol stations 56. Between 1934 and 1940, the amount of reported wood gas vehicles in Germany accounted between 1200 and 1500 62-64. In 1935 a rail motor coach (railcar) was powered by a wood gas generator and began to run near Cologne 35.
In 1938 only 0.3 %, corresponding to 1070 trucks, were equipped with wood gas generators 65. Practical experiences showed that wood gas vehicles could not be operated economically. Further unfavorable properties were mainly the reduced performance, relatively poor efficiency, smaller loading capacity, insufficient gas cleaning, high maintenance effort and cumbersome handling 66-68. Nevertheless, due to the energy autarky efforts, in 1939 the German government ordered the use of gas for motive power, especially for road and farm vehicles 35, 69. However, not only private cars but also buses, trucks, artillery tractors and tanks, motorcycles, ships, rail vehicles, etc. were equipped with wood gasification units 54, 70. Commercial wood gas generators were produced in different design types by many prominent manufactures as Imbert, Mercedes Benz, GM, Ford, Porsche, etc. For example, conversion kits (Gazogene units) were produced to mount them on the roof of the vehicles or fastened to the sides 35, 70. In the Volkswagen (type 60, post war Beetle) and in the German Army Kübelwagen a whole wood gasification unit (type 230) was installed directly in the modified bonnet (hood), which was refilled by a hole in the bonnet 71.
Due to the strong military ambition of the Nazi regime, in 1942 the gas producer program was transferred to the Ministry of Armaments and War Productions (Zentralstelle für Generatoren). By the end of the war in Germany around 500 000 generators and producer gas vehicles, respectively were produced by the Imbert Company in Cologne, which was the largest manufacturer these days 35, 72. In Munich, for example, the city administration was restarting waste collection after the war with wood gasifier cars 73.
The renewed access to relatively cheap imported gasoline after the war immediately led to a decrease of wood-run vehicles due to their economic and technical disadvantages 37, 67, 68. The consumption of a 5-ton car for a distance of 100 km accounted to around 100 kg beech wood. Further examples for wood consumption in wood gas vehicles are given in Box 2. The power loss of the engine was indicated with ca. 20 % 60. In general, the application and research of the wood gasification correlates closely with the cost and availability of liquid and gaseous fossil fuels 37.
Box 2. Examples for wood consumption in wood gas vehicles |
Assuming that 1.5 m3 round wood can be converted into 540 kg wood gas, 4 kg L−1 gasoline (135 L gasoline) could be substituted. In the case of charcoal, out of the same amount of round wood 120 to 140 kg charcoal can be produced, substituting 2 kg L−1 gasoline (65 L) 37. Under normal conditions, wood (chips) is added to the gas generator every 80 to 100 km 35. Alternatively, another example shows that with a 5-kg Christmas tree in the tank, a car à la Imbert could drive around 25 km. The lifetime of wood gas vehicle was estimated to be around 70 000 km. 74 |
3 From 1946 to1989, Bioenergy Reanimation After the Energy Crisis
After World War II, Germany was destroyed and divided among the victorious powers. In 1949, the Federal Republic of Germany (FRG, West Germany) and the German Democratic Republic (GDR, East Germany) were founded. In both countries, liquid and gaseous bioenergy carriers only played a minor role. The revival of bioenergy technology had only started from 1973 along with the worldwide fuel crisis and high energy prices. Renewable energies were increasingly funded by the state to increase the use of domestic resources for energy supply and reduce energy dependency. In East Germany the energy demand was continuously increasing. The energy consumption per capita was twice as high as in West Europe or even Japan in the early eighties 75.
The increasing awareness of the limits of fossil fuels, increasing environmental problems and the Chernobyl disaster, however, led both states to a reorientation of their energy policy. In West Germany in 1986, the Ministry of the Environment was established, which was the main driver of the German energy transition. In the GDR, for instance, the energy experts planed for the renewable energies only a share of 0.75 % for the year 2000 76.
3.1 Never Ending Biogas Pioneering
In West Germany, already 1947/48 the first agricultural biogas plant was established on the farm of Philipp Berthaloth in Rohrbach (Odenwald) according to the system „Darmstadt“ of the Technical University Darmstadt – a fermentation canal method with horizontal long axis stirrer after 28. This plant was operated with manure from two horses and eight cows. The biogas, around 8 to 10 m3 daily, was used in the kitchen for cooking and baking. 20, 25. A major agricultural biogas plant with an annual biogas capacity of 40 000 m3 was built in 1948 in Allerhop (Lower Saxony in North Germany) by Ferdinand Schmidt from Verden 77-79. The system was based on interchangeable containers according to Schmidt-Eggersglüss 28. The recipe of the first so-called biological humus and gas plant (Bihuanlage/Bihu plant) included: manure of ten cows, two centner (200 kg) haulm of potatoes and vegetable waste, respectively or the same amount of other waste from plants. The ingredients are mixed and rotten together with digested sludge from the sewage plant in two digester tanks (each 60 m3). With the gas the tractors rototiller was operated. Further, the digestate was used as fertilizer for the fields, as it contained more nutrients than the dung and could be better absorbed by the plants 79, 80.
In East Germany the Academy of Agricultural Sciences (Akademie der Landwirtschaftswissenschaften in Jena-Zwätzen) and agricultural research facilities and faculties (among others University of Dresden, Potsdam-Bornim, agricultural faculty in Jena etc.) mainly did research on biogas technologies. Private operators were usually not involved 25. The research aiming for large industrial-scale biogas plants was in particular based on the knowledge of already existing sewage gas and landfill gas technologies 25. In 1953, the first industrial-scale thermophile pilot plant was operated in Thuringia, but closed in 1957 due to technical problems and high heat losses 81, 82.
Until the 1950s between 50 and 70 biogas plants were established in West and East Germany 28. In West Germany, some of these plants were shut down because of operational defects and the decreasing oil price between the 1950s and 60s. At this time the price of heating oil was about 0.10 € L−1 and dropped until 1972 to 0.04 € L−1 21.
Even a lot of biogas plants closed down, two plants stand out. Out of thirteen biogas plants constructed in the 1950s according the mentioned system of Schmidt-Eggersglüss, only the Bihu plant of the monastery Benediktbeuren in Bavaria survived from 1955 until 1979. In two digester towers, each with a capacity of 240 m3, the manure of 180 livestock units could be processed and 300 m3 of biogas was produced. Around 200 m3 gas could be stored in the gas cover. The biogas was used for cogeneration of heat and electricity (CHP): one third for the heating of the digester towers, another third replacing wood for cooking in the kitchen for 200 persons and heating of the monastery; the remaining third supplied a 70-PS gas/diesel engine, which drove the central pump and a 60-kVA generator for power generation. During the operating time of 23 years, only the central pump and lately the agitators had to be maintained 80, 83. The farmer Resch from Bernloch, Swabian Alb, used one of the longest operating biogas plants, running from 1958 to 1986. In that time, around 400 000 m3 biogas and 500 000 kWh electricity were generated from the manure of 12 cows. An important feature of the plant was a special axial mixer, which produced a kind of a pulp from the liquid and solid manure. The plant generated an average of 42 m3 biogas per day. Resch calculated that per year 300 L heating oil per cow could be saved 84.
The relatively far reaching status-quo of biogas research in wastewater treatment and agriculture after the Second World War was published by the working group “Biogas” of the German Ministry of Agriculture in 85. For instance, it was only in 1967 that the microbial basis for the engineering process for the biogas plants was created and the central role of acid-producing bacteria in the fermentation process recognized. In 1979, the topic biotechnology was included in the CIT journal 31. Nevertheless, until the early 1990s, very few operators knew how the fermentation process actually works and operated their plants according to the trial and error principle 25.
3.2 Reactivation of Biogas with the Fuel Crises
Under the impact of the oil crisis (1973), the awareness of expanding alternative energies in due time raised. Especially, the West German government gave impulses through research programs to wind and solar energy, as well as to the use of heat pumps. Despite the fact that the focus of energy policy was less on bioenergy, researchers intensified their investigations and several interdisciplinary working groups were established 82.
Nevertheless, first companies began to erect professional biogas plants 20. In the 1980s the amount of biogas plants in West Germany was estimated at around 70 bigger plants and 30 smaller (testing) plants 21, 82. A share of 40 % of the plants was established by new manufactures. At the same time it is supposed that in Switzerland existed around 100 and in Austria two biogas plants 82. In contrast to the application of biogas technology in the 1950s, not solid manure, but slurry without litter was mainly used as substrate 21. Increasingly co-substrates were added, such as plant biomass (silage), dung or other organic waste and residues to increase the gas yields. In the mid-1980s, CHP plants have not been introduced to the market, yet. The main challenge was a lack of efficient feeding and stirring systems and the high sulfur content of the gas 25.
After the fuel crisis abated, development of biogas use declined again from 1985 to 1990 20, 21. Furthermore, fertilization aspects played an important role for farmers to decide for the utilization of biogas. Not least because of that biogas was particularly connected with organic farming. In 1981, the oldest, still operating, biogas plant was constructed at an organic farm in Hessen 86. In the eighties, further eco-pioneers followed to construct self-made biogas plants 87. In 1990/91, the number of biogas plants in West Germany was estimated at approx. 100, of which around 70 were assumed to be operated on organic farms 88. This trend did not continue during the biogas boom. In the early 2010s only one to maximum two percent of the produced energy from biogas came from organic farms, although it accounts for around 7 % of the total agricultural area. 89
Also in East Germany nutrition aspects were the promotor of the biogas sector: The animal production was centralized in big agricultural production co-operatives 25 and around 77 million tons of manure were generated by the industrial livestock production in 1980 76. Thus, the aim of the state program based of the X. party congress was the generation and storage of biogas for energy 90. This included above all the development of concepts for processing semi-liquid manure into fertilizer with lower costs than the synthetic production of nitrogen fertilizers. The produced heat was regarded as by-product or even waste, and biogas was not seen as contributing to the big energy issues 91.
As a result, eight demonstration and pilot biogas plants in industrial scale 20 with a fermenter volume from 500 to 80 000 m3 were constructed 82. The first big agricultural biogas plant of that type was established in 1982 in Vippachedelhausen, close to Erfurt. The plant is based on a process of the VEB “Complete Chemical Plants” (VEB, people-owned enterprise) of the Technical University in Leuna Merseburg 92. The biggest biogas plant was established in 1985 in Nordhausen, Thuringia with 37 m high steel containers and a volume of 8000 m3 each. Partly the gas was converted to electricity via the first CHP plant with a gas engine (reportedly, 82) and a modified tractor (ZT 300) was fueled by liquid biogas. The plant is still in use today and has an installed electrical power of 2.2 MW. At least 80 % of the total biogas was produced in Thuringia 82. At this time the first biogas plant with a horizontal plug flow system, erected in 1985 in Rippertshausen, was unique in the world. This plant was still operated until 2004 with organic waste as co-substrate. The last biogas plant of the former GDR was built in Zoben, close to Plauen in Saxony in 1987. It was the only plant that operated via a two-stage process with an upstream hydrolysis. Another technical feature of this plant and the one in Nordhausen was that it was equipped with a system for recirculation of the solid material for further digestion. Dry chicken manure from 0.25 million laying hens was mainly used as substrate. Today the plant runs with organic waste 82. At the time of the reunification 1990 around 80 biogas plants were operated in Germany, some are still in use 20.
3.3 Slight Developments of Liquid Biofuels and Gasification
The research on conversion technologies such as gas motors and generators for power production as well as liquid biofuels was not focused in West Germany and the former GDR 25. However, CHP plants and heat pumps based on biogas offered a wide field of application, especially in agriculture 75. Wood played an important role as cost-effective raw material for private households in West Germany; in the East, the wood industry was nationalized. In case of biofuels, the West German Government launched a program for introducing cars, which run on a mixture of 15 % methanol and 85 % petrol. At this time, the technology for producing methanol from wood was more advanced and economic than for ethanol production. As part of the overall test program, thirty petrol stations offered this fuel in 1980. 49
In East Germany biogas was regarded as the most relevant renewable energy for substituting liquid fossil fuels, especially diesel in the agricultural sector 191, with an estimated potential of 0.5 to 1 % 93 up to round 8 % 94 of the diesel consumption in agriculture in the year 1986. Major technical difficulties were found in the storage of biogas in the vehicles. Therefore, biogas or biomethane, respectively was compressed (CNG) or liquefied and stored as LNG (liquified natural gas) in vacuum isolated cryotanks in the vehicles. In research projects different prototypes of LNG vehicles were constructed and tested and LNG was produced 94. A small-scale plant for the liquefaction of methane was developed (−161 °C) and different types of automobiles were modified for the operation with LNG, such as a Wartburg, Polski FIAT (gas Otto engine), the truck W50 with a gas diesel engine or the LNG tractor ZT300 94. For instance, the tractor ZT300 was equipped with a special 200-L cryotank and a gas diesel engine 94. At the same range or operating time, the cryotanks had only 1/7 of the mass of the pressure cylinders for compressed biogas or methane CNG, respectively 94.
Box 3. Excursus: The oil crisis put forth new fuels for stoves and boilers to the market |
In the area of solid biomass, interest of research and industry has risen especially in the combustion of straw as one of the most important renewable energy sources in the agriculture 95. For instance, in the 1970s, the Bavarian State Institute for Agricultural Engineering of the Technical University Munich (nowadays TFZ) intensified their research on energy use of biomass from agriculture and forestry focusing on processes of energy use from wood and straw (later adding ethanol and plant oil) 19, 96, 97. First furnaces fired with straw have been developed and explicitly funded by the German government. Main goals were especially the improvement of the energy efficiency and mitigation of the emissions as NOx, CO, particulate matter, etc. 98. It was estimated that the required heating oil for the agriculture could be completely substituted by 20 % of the total produced straw amount 96, 99. These developments not only laid the foundations for today's widespread production of heat from wood, but also the basis for electricity generation from solid fuels. |
Furthermore, with the development of wood pellets, the range of applications for wood fuels has been significantly expanded. Pelletizing of biogenic raw materials was already a well-known technology from the animal feed industry and was adapted for the production of wood pellets 100. In the early 1980s, the aircraft engineer Jerry Whitfield from Seattle developed the first automatic stove to be fired with wood pellets from pressed chips for domestic use. In most countries, pellets were first used in large-scale plants in the early 1990s and only gradually discovered for private use 23, 101. The first pellet stoker in Europe was launched in Austria in 1989 102, but it took until 1998 that wood pellets were also established on the German market 101. |
4 From 1990 to the 2010s, the German Bioenergy Boom
Between the great debates of reunification, the topic of environmental protection and renewable energies had briefly disappeared from the agenda 25. To increase the share of renewable energy a law on legally granted feed-in tariffs for electricity from renewables was launched (Stromeinspeisegesetz 1991). This was the starting point for the German energy transition. The law was renamed in the Renewable Energy Sources Act (EEG) in 2000 and amended many times in the coming years. It has become the key element of the bioenergy boom in the German power sector 103. The motivation for the expansion of bioenergy was manifold. The reduction of the demand for fossil fuels, the saving of greenhouse gases and the securing of energy supplies and overproduction in agriculture at European level were relevant drivers 104.
4.1 Power from Wood – Technologies for Efficient CHP Systems
From 1990 to the 2010s, a wide range of CHP plants was developed, including pellet stirling, micro-CHP plants and CHP plants with fuel cells 105-107. In 1993, Germany's first municipal straw heating plant with a capacity of 3.15 MW, based on the cigar burning principle, went into operation in eastern Thuringia. The straw, 3000 t a−1, is generated as waste from the surrounding cereal production 108.
The majority of the biomass power plants range between 150 and 500 kW and supply the agricultural enterprises. Larger plants with an output of up to 20 MW are operated in municipal sewage treatment plants and in the wood industry. Microplants under 150 kW for the heat supply of single-family houses are mainly based on solid biogenic fuels. 109
Since the EEG came into force in 2000, the number of biomass (heating and) power stations has increased more than 20-fold (taking into account estimates for the addition of wood gasifiers) and the installed electrical power has increased sevenfold 110. A large number of processes and variations were developed, but these did not always meet the requirements of the market 111, 192. Wood gasification CHP plants have been increasing noticeably since 2011, especially in the output range up to 200 kWel. Almost 700 biomass (heating and) power stations including thermo-chemical wood gasifiers with a cumulative electrical capacity of around 1511 MWel were in operation at the end of 2014. Due to the Renewable Energy Sources Act 2014 (EEG 2014), the activities of plant manufacturers in the wood gasification sector were increasingly shifting abroad, where the current political conditions are more favorable and enable economic operation 112.
Nowadays, however, the technology of some plant manufacturers has reached a state of the art that permits largely trouble-free plant operation and is acceptable from the point of view of emission control with regard to emissions of odors and benzene 113. Only a few manufacturers, mainly for systems in the low output range, offer now standardized systems manufactured in series production (Spanner, Burkhardt, etc.).
The production of wood pellets in Germany started in 1996 with pellet boilers from Austria and very small operation systems. The following year, the installed annual production capacity amounted to 6500 t 114, 115. In 1996, pellets were approved as solid fuel, but only established in the German market two years later 101, 115. Since then, wood as a raw material has literally become socially acceptable and is experiencing a renaissance as a modern energy source 101. In 2000, the pellet boom started, seven pellet production plants were registered 116. By 2017, around 437 000 pellet furnaces were in operation in Germany 101.
4.2 The Hype of Energy Plant Expectation
In parallel in the 1990s, the European agriculture production was more and more under pressure due to overproduction. Hence, the European Commission introduced the tool of set aside of the arable land. In 1988/89, set-aside was fixed at 15 %. This set-aside rate was adjusted annually in line with overproduction (see Fig. 3). From 1993/94 on it became compulsory and was reduced to 10 % in 1996 117. Since then, renewable raw resources were allowed to be cultivated on these set-aside areas and eligible for set-aside payment. Agriculture entered the politically intended production of first-generation biofuels, i.e., ethanol and biodiesel 118.
Bioenergy was seen as a valve for agricultural overproduction. In 1995, 10.83 % of arable land was set aside, added by around 3 % set-aside area for the cultivation of renewable resources. In 2006, set-aside dropped to 6.24 %, whereas side-aside area for the cultivation of renewable resources increased slightly to 3.34 % (see Fig. 3). In Germany, arable land on which renewable resources were cultivated has increased more than fivefold since the beginning of the 1990s, not only including set-aside land. In 2005, more than 1.4 million ha of arable land were cultivated with renewable raw materials in 2005, which corresponds to 12 % of the total arable land 119. In autumn 2007, the set-aside percentage was set at 0 % and abolished in 2009 due to the increased demand for agricultural products 120.
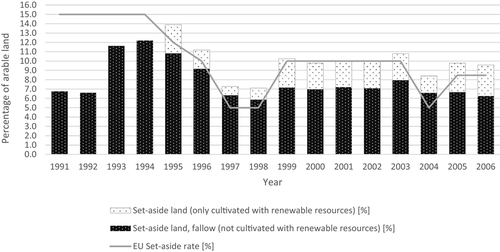
Under the debate of the national and international energy transition, global biomass potential assessment studies were elaborated to figure out the future role of bioenergy in a renewable energy supply. Most studies indicate the technical bioenergy potential, which describes the part of biomass that can be used considering the given technical restrictions. These include technical feasibility (e.g., salvage rate, conversion losses), structural and legal limitations (e.g., protected areas, cross-compliance regulations, waste legislation) and ecological restrictions (e.g., humus balance) and social priorities (e.g., food and fiber first) 124.
Fig. 4 shows the range of the estimated global potential of 32 studies for the overall biomass potential including raw materials from forests and cultivated biomass from agricultural land as well agricultural residues such as straw, manure and waste. Further, the potential estimation for energy crops in the different studies is shown. The bioenergy potentials given in the studies are presented with their minimum and maximum values of their energy content in exajoules, where available. It should be considered that not all of these studies presented original data.
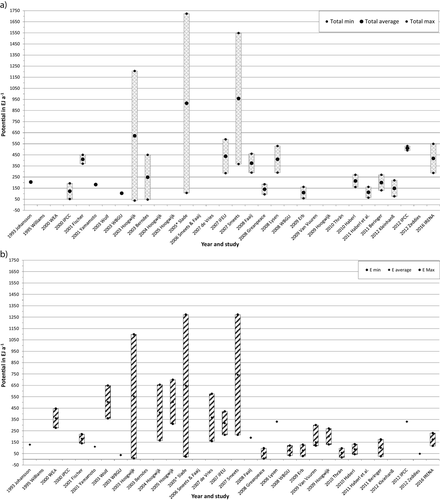
The range of global potentials is between 38 and 1723 EJ a−1. The average global primary energy consumption, including fossil and renewable energies was about 13511.2 Mtoe (542 EJ) in 2017 125. Especially the studies published between 2002 and 2007 came to very ambitious expectations regarding the contribution of biomass to the energy supply. The range of potential estimates for 2050 for energy crops were also very high according to the studies 2002 to 2007. Residual materials are less affected than energy crops. The potential for residual and waste materials is much more sable and estimated in the studies at approx. 135 EJ a−1 plus the use of firewood of 36 EJ a−1, which means 14 GJ a−1 per capita.
Considering those studies, political measures were taken to introduce agricultural-based bioenergy sources into the market in many countries. In Germany the focus was on power provision via biogas and biofuels, respectively 25. However, the disillusion came after only one decade. Questions about the extent to which food crops can or should be used for fuel were increasingly raised. Climate emissions from agriculture were reassessed and the demand for agricultural products increased (2007 crisis: increase in prices, harvest failures, etc.) as well as the awareness of the finite nature of resources. Hence, energy research and policy focused especially on the impacts of biofuels and biogas on climate change, food rights, biodiversity and sustainability 39, 126.
4.3 Feed-in Act Jumpstarts Biogas Development
A third upswing in biogas utilization began at the beginning of the 1990s with the legal regulation of the legally granted feed-in tariff for electricity from biogas 127 and the general conditions of the Closed Substance Cycle and Waste Management Act (Kreislaufwirtschafts- und Abfallgesetz) 21. From 1992 to 2000 the amount of biogas plants increased from 139 to 1050 15, 128. The co-fermentation of organic residues mainly from slaughterhouses, breweries, and food processing companies and biowaste from households further increased economic efficiency 20. Innovation pressure led to optimizations primarily in the area of filling, stirring technology, desulfurization, and engine environment and consequently had a positive economic effect. For the first time, ready-made systems from manufacturers were offered.
In the first decade of the 21st century, biogas technology has undergone rapid development in the agricultural sector. Nevertheless, it was not until the “Renewable Energies Act” (EEG) in 2000 and the guaranteed remuneration for electricity and heat from combined heat and power generation that a real boom of the biogas sector began 20. Energy crops were incentivized since 2003, and thus, increasingly cultivated. Since then, the biogas boom was closely linked to the agricultural sector. However, alternative fermentation processes such as dry fermentation were tested in order to further mobilize the potential of cultivated biomass, especially dry substance-rich fermentation substrates, such as maize whole plant silage 25.
From 2000 to 2010 the number of biogas plants increased from 1050 to 6311 128 with an installed power of 65 MW to 2291 MW 87. The cultivation area for biogas substrates, including mainly maize silage, corn and grass silage, increased from around 20 000 ha in 2000 129 to 650 000 ha in 2010 130. More efficient processes for energy were developed, the feasibility of flexible biogas production was demonstrated 131 and the substrate spectrum broadened. In addition to biogas plants, a large number of sewage gas plants and landfill gas plants contribute an additional 30 % to the supply of electricity from biogas 132.
The fourth EEG entered into force in 2012 and the legal framework was deteriorating. The boom phase for biogas plants was over. However, the new EEG offered for the first time the entry into the so-called direct marketing of electricity via the market premium model and the flexibility premium 82. With the amended of the EEG 2014, drastic new regulations for electricity generation from biomass came into force. This led to a sharp decline in new construction activities, with the exception of special plant concepts for the treatment of residual and waste materials 133. From 2015, the construction of new plants was mainly concentrated on manure and waste plants (small manure plants up to 75 kWel (§27b EEG), biowaste plants (§27a EEG)). Thus, plant system repowering and expansions mainly determined the better use of the coupled heat and the performance of biogas plants. Furthermore, flexible plant operation was subject to intensified research and practical tests. Biogas and biomethane plants, which were entitled to a flexible premium, contributed around 4 TWhel in 2016, or 12 % of electricity generation from biogas 134.
Furthermore, biogas plants provide another way of suppling carbon dioxide for methanation to power-to-gas (PtG) processes. In 2013, the first industrial PtG plant with 6.3 MW was operated in Werlte, in the Emsland region of Northern Germany 135. Here, it was shown how catalytic methanization can be implemented using CO2 from the biogas plant located at the site. In 2015, the general feasibility of biological methanization was demonstrated 82. By the end of 2016, 30 PtG plants with a power consumption capacity of approx. 21 MW were commissioned. First combinations of biogas plants with PtG shows, how sector coupling of electricity and gas can function with the integration of biogas plants. Moreover, the produced renewable methane as a long-term storage option makes the conversion of existing CHP plants to electricity more flexible 136.
With the EEG amendment 2017 (EEG 2017, 2016), the amount of remuneration from biomass is determined primarily via tenders in future. This update is also linked to certain minimum requirements for flexibility and has the clear objective to make the plant portfolio more flexible in the coming years. 133 Because of the low level of new constructions 137, the activities of plant manufacturers in the biogas sector, especially for integrated biowaste fermentation and composting plants, were increasingly shifting abroad 138.
4.4 Ramp Up of Biofuels for Transport from Alternative Resources
Biofuels were often regarded as an important element of the energy transition 139-142. Thus, fuels from agricultural products (biofuels of the first generation) were established in the market, including biodiesel and ethanol as well as pure vegetable oil, hydrogenated vegetable oils (HVO) and biomethane. These are based on resources from agriculture, e.g., rape, cereals, sugar beet, maize, soy or oil palms. To produce larger volumes of sustainable biofuels, in addition to energy plants, residual materials, such as used cooking oil, are already used today for the production of biodiesel, HVO and biomethane 139.
The biofuels market is highly dependent on political and legal conditions. These have changed considerably over the past few years. The generation of those biofuels increased sharply from 2000 (12 PJ) to 2007 (about 170 PJ) and were dominated by biodiesel with ca. 72.8 % and bioethanol with ca. 7.7 % 143. In addition to tax exemptions until 2009, in 2006, the law to introduce a biofuel quota was passed 143. Many new process facilities opened (see Fig. 5, Tab. 2). The first biogas filling station has been opened in Jameln (Wendland) 144. In 2006, the first biomethane plant near Munich fed biomethane into the natural gas grid 82. With biomethane a wide range of using natural gas is provided, including heat, electricity, fuel and process energy. While the existing production capacities for biodiesel in Germany in 2007 of around 3.5 million tons were well above the established biodiesel proportions of around 1.5 million tones (biofuel quota 4.4 % for biodiesel), the expansion targets in the EU were not achieved 145. For 2020, assuming the availability of sustainably produced raw materials, the target has been set to 10 % of the total consumption of petrol and diesel in the transport sector (KOM (2006) 848) 143).
1990 – 2010s: Bioenergy boom (Part I) |
|
---|---|
1993 |
First straw heating plant in Germany in Thuringia (3.15 MWth, 20 t of straw per day) |
1993/94 |
Renewable raw materials can also be cultivated on set-aside areas. |
1996 |
Pellets officially approved as fuel in Germany. |
1997 |
The installed annual pellet production capacity amounted to 6500 t. |
1998 |
First pilot plant for production of methanol from wood in Freiberg by Choren. |
2000 |
First-generation biofuels such as pure vegetable oil, biodiesel and bioethanol introduced to the market (agriculture sector). |
2000 |
The 1000th biogas plant goes into operation. The pellet boom started. |
2004 |
Strong upswing of biogas plants due to renewable energy bonus; 2000th biogas plant in operation. |
2004 |
TOTAL starts commercial production of biodiesel at the Leuna refinery. |
2005 |
First biogas filling station in Jameln (Wendland). |
2005 |
First public bioethanol filling station for E85 opened in Bad Homburg. |
2005 |
CropEnergies GmbH operates one of the biggest production facilities for bioethanol in Zeitz with a capacity of around 400 000 m3 bioethanol, more than 300 000 t of protein feed and 100 000 t of liquefied CO2 per year from 750 000 t of grain and sugar syrups. |
2006 |
First biomethane plant near Munich feeds biomethane into the natural gas grid. |
Since 2006 |
Increased research and development on hydrothermal processes. |
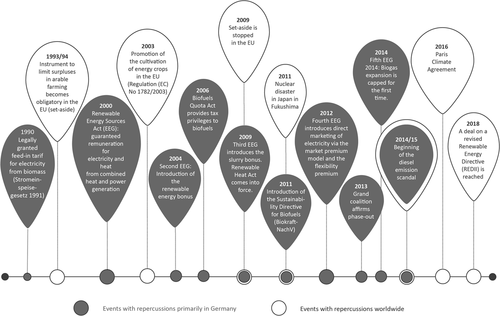
Further research activities have been intensified to produce biofuels from non-food feedstocks like lignocellulosic material in agricultural and forestry wastes, purpose-grown trees and grasses, as well as algae (2nd generation biofuels) via microbial and thermal processes and adapting and improving biofuels for engine compatibility and emission mitigation 47, 146. In 1998, Choren started the first pilot plant to produce methanol from wood in Freiberg, but went bankrupt in 2011 147. Commercial scale plants and notable demonstration scale plants for bioethanol from lignocellulose are in either operation or commissioning (see Fig. 5, Tab. 2). For instance, Clariant operates since 2012 a demonstration plant based on renewable lignocellulosic raw materials, such as wheat straw, corn stover and bagasse with an annual capacity of up to 1000 t ethanol 148, 149. In 2014, VERBIO followed by producing biogas, bioethanol and biomethane from 100 % straw (rye) at the production facility in Schwedt 151. However, technical barriers remain for 2nd generation biofuel production. Synthetic biofuels (BtL) still require some time to reach industrial scale. Biofuels from algae or other alcohols are at a comparatively early experimental stage and will hardly be available on the market in considerable, low-cost quantities in the medium term. In this respect, the classic biofuels biodiesel, ethanol and vegetable oil as well as biomethane are likely to remain the most important renewable alternatives in the mobility sector in the medium term 139 (cf. Fig. 5, Tabs. 2, 3 and 5).
1990 – 2013: Bioenergy boom (Part II) |
|
---|---|
2009 |
Owners of new buildings are obliged to cover the cooling or heating energy demand with renewable energies by the Renewable Heat Act. |
2010 |
First commercial BtL demonstration facility commissioned by Choren. |
2010 |
Germany's largest plant for the production of liquid, biogenic carbon dioxide (from bioethanol production) with capacity of 100 000 p.a. put into operation at Zeitz site of CropEnergies GmbH. |
2010 |
Amendment of the 1st BImSchV tightened emission limits for wood combustion plants. |
2010 |
Feasibility of flexible biogas production is demonstrated. |
2011 |
E10 fuel containing 5 – 10 % bioethanol introduced (Renewable Energy Directive (2009/28/EC)). |
2011 |
Small wood gasification plants are sold on the market on a commercial level more widely. More than 100 wood gasification plants are in operation. |
2012 |
Clariant commissioned so far largest demonstration plant in Germany to produce ethanol from lignocellulosic raw materials. |
2012 |
ZSW commissioned a 250 kWel P2G pilot plant with a capacity up to 300 m3 of methane per day. |
2012 |
Increasing repowering, efficiency increase and demand-oriented operation of biogas plants in the market due to the fourth EEG. Three AD plants (6 MWel) use the flexibility premium instrument. |
2012 |
First commercial-scale virtual power plants (VPP) with biogas plants began operating (e.g., NextKraftwerke, RWE/Siemens). |
2012 – 2017 |
Leading Edge BioEconomy in Leuna demonstrates combined material-energy use of wood in the chemical industry. |
2013 |
2nd generation biofuels from non-food feedstocks more widely marketed on a commercial level. |
2013 |
Worldwide first power-to-gas plant (PtG) with a capacity of 6 MWel (Audi gas plant in Werlte), combining electricity and gas grid by way of electrolysis and methanation. |
5 Current Bioenergy Use
Bioenergy is still the largest German renewable energy source (54 %, 2017) 150. A large proportion of this is provided by wood for space heating 150, 152. Between 2000 and 2015 the use of bioenergy in Germany constantly increased by almost four times 153. In 2017, bioenergy accounted for 7.1 % of the total primary energy consumption of 13 550 PJ in Germany 150, including more than 10 million installations in the heat and power sector and for biofuels as well (Tab. 4).
|
Type of plant |
Number of plants |
Installed power/ production capacity |
---|---|---|---|
Biogenic solid fuels |
|||
CHPa |
biomass (heating) power plants eligible under the feed-in tariff system EEG |
300 |
1369 MWel |
small gasification systems eligible with under the feed-in tariff system EEG (≤ 180 kW) |
400 |
45 MWel |
|
biomass heating plants |
1000 |
2000 – 5000 MWth (range) |
|
small combustion plants – central combustion plants (wood chips, logs, pellets) (2014) |
1 153 300 |
36 372 MWth |
|
small combustion plants – single fire places (2014) |
5 370 000 |
38 982 MWth |
|
small combustion plants – other single room combustion plants (2014) |
4 600 000 |
34 635 MWth |
|
Gaseous biofuels |
|||
CHPd (incl. share of biomethane used as biofuels) |
agricultural biogas production plants |
7640 |
4379 MWel |
small liquid manure plants (≤ 75 kW) |
560 |
40 MWel |
|
fermentation plants for biowaste, food waste and other organic waste |
335 |
no information |
|
biogas upgrading plants for biomethane |
196 |
553 MWel |
|
Liquid biofuels |
|||
CHPe |
vegetable oil CHP (palm oil, rapeseed oil) |
690 |
79 MWel |
biodiesel plants (rapeseed oil, palm oil, used cooking fats and oils) |
30 |
4 million t a−1 |
|
bioethanol plants (sugar, starch) |
5 |
0.7 million t a−1 |
The intensive research, development and market introduction activities for gaseous and liquid fuels resulted in significant higher primary energy supply for gaseous and liquid biofuels compared to the worldwide average: For liquid biofuels, the values for Germany are around 3.5 times as high and even almost 22 times as high for gaseous biofuels (Fig. 6). These figures and the cultivation of renewable resources on 2.65 million ha or 22 % of the arable land, respectively 156 underline that Germany stands for an extraordinary bioenergy policy. In worldwide comparison, energy crops play a rather subordinate role 154. Whereas, the use of solid biofuels per capita is slightly lower than in the world. The majority of this biomass comes from wood, which is globally mainly used in developing countries as firewood and charcoal in traditional fireplaces.
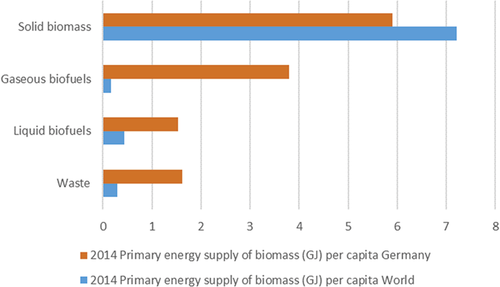
Compared to current use, expectations for future development are gloomy. The EEG provides tender quantities that will significantly reduce electricity generation from biomass by 2035. The use in CHP plants outside the EEG is uncertain with regard to economic efficiency. The goals and instruments for renewable transport fuels for 2030 are currently discussed at European level and might reduce the conventional biofuels use significantly 157.
Consequently, in Germany, instead of further expansion an adaptation of the energy use of biomass is being discussed. This adaptation must be based on the requirements of an energy system based on renewable energies (cf. Fig. 5, Tab. 5).
Since 2014 towards an integrated bioenergy provision |
|
---|---|
2013/14 |
Climate researcher identify BECCS as a relevant option to achieve the climate (IPCC). |
2014 |
VERBIO is producing biogas, bioethanol and biomethane from straw (rye) at the production facility in Schwedt. Up to 20 000 tons straw per year converted to biomethane. |
2014 |
Bioliq® pilot plant supplies synthetic fuel from straw and other biogenic residues. |
2014 |
First Lufthansa sugar-based biofuel (biocerosene) flight from Frankfurt to Berlin/Tegel. |
2014/15 |
End of bioenergy boom: Biogas expansion capped for the first time by the fifth EEG. Only small liquid manure plants built. The annual increase of the biofuel quota abolished and set to 6.25 %. |
2015 |
8000th biogas plant goes into operation. |
2015 |
Feasibility of biological methanization is demonstrated. |
2016 |
First flexible operating laboratory charcoal gasifier with motor engine and less than 1 kWel is running; basis for change from heating boilers to integrated solid biomass CHP in every house is set. |
2016 |
400 000 pellet furnaces in operation |
2017 |
Sixth EEG introducing the tender system mandatory flexibility |
2018 |
Intensive promotion of advanced biofuels is expected (in REDII). |
2018 |
Patent for ultra-small-scale combustion plant for biogenic solid fuels (DBFZ). |
Prospects of bioenergy developments |
|
– CHP infrastructure/transition from boilers for solid biomass in all performance capacities to flexible operating and gap-filling combined heat and power plants, – market introduction of wood-based liquid fuels, – processes for the use of biomass in commercial and industrial processes that require high temperatures, – social acceptance of CCS/BECCS. |
6 Prospects for Bioenergy Use
Considering that Germany has joint the Paris agreement, an overall greenhouse gas emission reduction of 80 to 95 % is envisaged till 2050 compared with 1990 levels 162. These climate protection scenarios require the integration of bioenergy from sustainable biomass into renewable energy systems 163. Although, a very targeted use of the limited biomass is needed. Hence, in the next ten years it will be more likely that the use of biomass is a consistent trade-off process. Key elements of the future bioenergy development to consider are presented Box 4.
Box 4. Key elements of future bioenergy developments |
1) Targeted use of the limited biomass: – systematic optimization of the supply of residues and waste materials from biomass, – integrated bioenergy supply to close the gaps in the electricity and heat sector, – sector coupling with renewable electricity, – provision of heat in industrial processes, – support of CO2 removal from the atmosphere via BECCS or biochar, – provision of liquid biofuels for specific applications (e.g., air, sea and heavy-duty transport), – combination of material and energy use, – combination of bioenergy and biodiversity. |
2) Complex framework conditions, e.g., – further development of EEG and CHP in district heating, – carbon capture storage (CCS), – lignocellulose fuels, – developments in digitalization and bioeconomy/biologizing (i.e., increasing integration of nature's principles into modern economic sectors) 164. |
3) Research needs – comprehensive technology development, – comprehensive technology integration, – improved understanding of the energy system. |
Bioenergy is expected to grow much slower than wind and solar 165 and is more and more used in energy applications, which can be covered by other renewables only with high efforts 133. These include flexible power for phases with low wind and solar power availability, fuels for heavy-duty vehicles, ships and the aviation sector as well as heat for dedicated industry processes and in ancient buildings, which have limitations for insulation. But, the most suitable energy sectors and the related set of technologies to promote are still under discussion 166. While energy crops for energy provision seem to be limited, there is still a relevant unexploited potential of biogenic residues and wastes of 26.9 – 46.9 million Mg (DM) (approx. 390 – 680 PJ) 167. Most of those resources are dry lignocellulosic materials (around 70 %) and only a minor share (13 %) of wet materials for digestion. The remaining 17 % are solid manure 167. Options for flexible and integrated energy provision are currently subject of research and development not only in the power sector, but also for heat and biofuels 168-170.
-
The climate crisis cannot be solved by the transformation of the energy system. The results from climate modeling show that it is extremely ambiguous to fulfil the targets by reducing climate gas emissions. Furthermore, additional CO2 removal from the atmosphere can support the success in combating climate change significantly 171-173. To remove CO2 from the atmosphere carbon capture and storage of the produced CO2 (CCS) is promoted in many climate scenarios. The combination of CCS with bioenergy provision (BECCS) is an interesting option, because renewable energy and CO2 removal are provided in the same process 174-177. With regard to efficiency and costs large-scale systems are required for CCS. In case of BECCS systems, centralized biorefineries or CHP systems are expected. However, the wider social acceptance for CCS is still missing in Germany, thus, the role and future of BECCS is not clear yet 154, 178, 179. If CCS is not accepted and does not achieve a breakthrough in the future, further ambitious measures to reduce greenhouse gases, such as the use of bio-based carbon in biochar systems, must be pursued 154, 172, 178, 179.
-
Liquid fuels from lignocellulosic biomass are not established on the market yet. Continuous and engaged research and development is necessary for the development of cost efficient technologies and concepts. If those liquid fuels are available, they will play a key role in the energy transition of heavy-duty transport, shipping and aviation. Experiences from the past show that the success of such a market implementation cannot be forecasted easily. The combination with BECCS can make biorefineries producing hydrogen attractive 180-182. If the market implementation of liquid fuels from lignocellulosic biomass is not successful, gaseous fuels, such as biomethane might become more important 183.
-
The development of the overall energy infrastructure of the German energy system is still subject of intense discussions. While the power sector is moving very rapidly towards renewable energies (RE), with a share of 36.2 % and an increase of 19.3 % since 2010, the increase of RE in the heating sector is much slower (1.4 % since 2010) 150. The total share of renewables increased during the last five years only slowly from around 11 to 13 % 150. The debate on how to manage the decarbonization is still ongoing, e.g, especially the role of district heating systems will influence the options for biomass in the heat sector, as there are various options for bioenergy provision in CHP systems. If BECCS will be accepted in the public and investments in district heating infrastructure are realized, bioenergy could play an important role in decarbonization. If there will be no CCS acceptance and no additional heat infrastructure, smaller CHP systems with flexible heat and power provision, eventually in combination with biochar, might be more relevant in the future renewable energy system.
Given the different uncertainties in social acceptance, technology development and energy infrastructure, the role of bioenergy in long-term energy strategies is not yet defined in detail. Nevertheless, the availability of bioenergy technologies for integrated systems must be prepared in the next decade. This includes the following aspects.
Safeguarding a Sustainable Resource Base
Exploitation of residues and waste utilization: Residual and waste materials represent a large part of the previously untapped potential for expansion. The further development of efficient recycling paths is therefore crucial. There are considerable differences between residual/waste materials and cultivated biomass, particularly regarding the techniques used for processing, conversion and use. Nevertheless, the energetic utilization of agricultural substrates (especially in biogas plants) continues to be viewed as a relevant contribution to reducing greenhouse gas emissions. Regarding the cultivation of energy crops, the objective of gentle land use and consideration of environmental and water protection is to be particularly emphasized 184. Increasing experience in certification systems of biofuels should be used for the whole bioenergy or even for the bioeconomy sector 185.
Diversified Technology Research and Development
The brief overview of the history showed that technology development takes time and needs continuous attention. Different technologies have been developed during the last two decades, from efficient, clean small-scale wood boilers via gasification systems, flexible biogas plants up to biorefinery elements and biochar processes. To integrate them into 100 % renewable energy supply systems, further optimization of those systems is essential, including efficiency increases, improved automatic control technology, hybrid and multibrid systems, emission-free/low-emission and high biomass flexible bioenergy plants 186.
Improvement in System Understanding
The future role of bioenergy is not only technology-driven. Many additional aspects from the energy system have to be considered such as the development of other renewable technologies, energy prices, international relations, etc. Consequently, the role of bioenergy in different scenarios has to be examined more in detail. Furthermore, integration into the energy system and international climate policy is associated with various additional challenges in terms of environmental and social impacts, such as local environmental impacts and local acceptance. Any transformation from today's bioenergy use into future systems must consider these aspects. Additionally, there are many direct and indirect effects to the environment and society in other regions of the world, which need to be understood and evaluated. Modeling and monitoring are necessary to close those knowledge gaps. The use of the new possibilities of information communication technology (ICT) along with systematic data acquisition and analysis has already begun in order to further develop bioenergy processes, e.g., in biogas plants and small gasifiers.
7 Conclusion
During the last 90 years, bioenergy developments were pushed by different motivations such as local environmental problems and energy hunger, energy security, transformation of the energy system and support of climate gas reduction. For example, at the beginning of the 20th century, municipal waste was collected and separated for the first time due to waste disposal problems in Charlottenburg and sewage gas was used in biogas systems for production of heat and electricity. During the energy crises and Nazi regime gasification was promoted and the scientists began to understand the fundamentals of the gasification process. In the 1990s, energy plants were increasingly cultivated in agriculture due to European overproduction. In the future global climate policy bioenergy may play a key role as carbon sink to achieve global climate protection targets. Nowadays, bioenergy use in Germany is characterized by a high-specific contribution of bioenergy in the power, heat and transport sector. Continuous development of technologies was necessary to contribute to the different sectors at different scales. For the future integration into the energy system, rigorous climate gas reduction strategies are necessary. Consequently, this requires special concepts and technologies for the provision of residual materials and waste and for the integration of bioenergy into more complex and international systems. Clean and in some cases, flexible energy supply from biomass as well as standardized interfaces and controls for the combination of bioenergy with other renewable energies of different scales must be further developed. Nevertheless, there are some fundamental decisions outside the bioenergy sector that will influence the use of bioenergy in the longer term. In particular, the role of CCS perception, the district heating infrastructure and the successful market introduction of liquid fuels from lignocellulosic materials have not yet been decided and will drive bioenergy strategies forward. A wide range of efficient technologies, modular concepts that allow learning systems and adoption as well as a better understanding and monitoring of the different sustainability aspects are necessary elements for a successful further development of bioenergy in the next ten years.
Acknowledgements
We thank our colleagues from the DBFZ for their valuable contributions: Angela Gröber, Anne Mesecke, Christiane Hennig, Jan Khalsa, Volker Lenz, Jan Liebetrau, Ingo Hartmann, Marco Klemm and Roman Glowacki. We would also like to thank Hanns-Rudolf Paur from the KIT regarding historical information on wood gasification and Jacob Thrän.
Biographies
Diana Pfeiffer has been working as project coordinator at the DBFZ in Leipzig since 2009. She is mainly responsible for the coordination of the program support of the German Research Network Bioenergy of the Federal Ministry of Economic Affairs and Energy. Her main tasks are supporting knowledge transfer, strategic networking and the harmonization of methodologies within in the research network. Before, Ms. Pfeiffer worked as a consultant in the Management & Audit Services within ERM based in Frankfurt/Main, Germany and in the Forestry section of the UN Food & Agriculture Organization/Sub-regional Office in Budapest (Hungary). She holds a university degree in Geo-Ecology (environmental sciences). Furthermore, she conducted several environmental projects in the chemical, microbiological and agricultural sector in Ukraine, Norway, Finland and Russia.
Daniela Thrän is professor at the University of Leipzig and head of a multidisciplinary team of scientists at the DBFZ/UFZ investigating research questions on the analysis and assessment of renewable resource systems, in particular on bioeconomy and bioenergy. She is strongly shaping the scientific and political framework conditions for sustainable and efficient biomass utilization, bioenergy provision and bioeconomy processing on national and international level. In 2015, she developed the vision of “Smart Bioenergy”, considering technologies and concepts needed for a more flexible bioenergy provision in future energy systems. As member of leading advisory committees (IEA-Bioenergy, Bioeconomy Council of Germany, European Bioeconomy Stakeholders Panel), she actively designs the German and European bioenergy and bioeconomy strategies.