Development of a Separation Sequence for the Integration of a Styrene Recyclate into Polystyrene Production
Abstract
This work addresses the processing of a polystyrene recyclate stream into polystyrene synthesis on an industrial scale. Evaluating the energetic demand of the separation process with the following reintegration of the recyclate stream shows a significantly reduced specific energy input compared to conventional polystyrene synthesis. Therefore, recycling polystyrene by pyrolysis and thermal separation shows a considerable potential as a tool for industrial circular production in the plastics sector.
1 Introduction
The already significant contribution of the plastics industry to global greenhouse gas emissions as well as the expected increase in global plastics production require the conversion of industrial production processes to a circular operation mode 1, 2. This requires the implementation of material recycling processes since energy recovery does not allow for the integration of recycled material streams into production processes. Due to a change in the properties in the use phase of the plastics and contamination of the waste streams by collection that is not sorted by type, mechanical recycling leads to downcycling, in which the secondary plastic loses quality compared to the primary plastic 3. It follows, for example, that mechanical recycled plastics often do not meet legal requirements for food packaging and consequently cannot be used for certain applications 4. Industrial production processes therefore need an extension to include a cycle with feedstock recycling as an essential component 5. Most plastics are produced for single-use applications and accumulate as waste after a short service life. In this context, the packaging industry is the most important consumer of plastics and the main producer of waste 1, 6, 7. In 2015, the packaging industry accounted for 39.9 % of plastics consumption in Europe 8. In Germany, a total of 6.15 million tons of plastic waste was detected in 2017 1. In addition, the extraction of petroleum for the production of plastics is becoming increasingly energy-intensive, which means that plastic production processes have a high potential for conversion to closed-loop processes 2.
The bulk plastic polystyrene (PS) is particularly attractive here, as it has a high recycling potential. The plastic is easy to sort and has advantageous properties with regard to raw material recycling. For example, it is known that PS waste can be converted to more than 90 % pyrolysis oil 9, which consists of high proportions > 70 wt % of styrene monomer 10, 11. Thermochemical recycling of PS waste by pyrolysis and a subsequent upgrading of the pyrolysis oil to the polymerizable styrene stream has already been investigated 12. The separation of the recyclate stream was carried out by means of a vacuum distillation column. However, an ecological or economic balancing of such a process is still missing in order to evaluate the positive or negative influence on the respective cycle. Another investigation of the feedstock recycling of PS was considered in the ResolVE project. Here, the waste was depolymerized within an extruder and a pure styrene stream was subsequently obtained by fractional distillation 13, although again, information on the exact implementation and balancing of the process is not provided. Another paper addresses the thermocatalytic depolymerization of PS using acids and bases such as BaO, which can convert 90 wt % of the PS used into styrene 14. Subsequent reintegration into the production of secondary PS and an evaluation of the recycling process are also not provided here.
Besides academic investigation, several large-scale facilities for the recycling of polystyrene have already been announced, i.e., by Toyo Styrene 15, 16 using Agilyx' depolymerization technology, which is based on a pyrolysis of PS waste. The process allows for the reintegration of oligomers in the pyrolysis reactor, leading to increased yields. Following the pyrolysis step and condensation of the pyrolysis gases, light hydrocarbons and a liquid styrene phase are separated and further processed; no further information is provided regarding this separation step 17. Agilyx has recently announced that they will offer their technology jointly with Technip Energies under the trade name TruStyrenyx™ 18. Another investment in a chemical recycling facility has been announced by INEOS Styrolution 19. The process, that aims at the recovery of high-quality styrene just like Agilyx' process does, contains a fluidized bed reactor for the pyrolysis of PS waste 20. For separation and pyrolysis oil upgrading, a distillation unit is employed 21; no information is available regarding specific design and process parameters of the separation sequence.
The present work therefore addresses the development of a separation sequence for a PS recyclate stream, its reintegration into conventional PS production and a subsequent energetic evaluation of the process. Based on the depolymerization of PS by means of pyrolysis, processing and separation steps are investigated using Aspen Plus® simulation software. For the subsequent reintegration of the styrene stream into the conventional production of PS, the polymerization process is also simulated. This results in a complete secondary pathway that can be evaluated in terms of energy.
2 Methods and Modelling Approach
The recyclate stream obtained from pyrolysis consists mainly of the pyrolysis oil, which was experimentally obtained and analysed in previous work 10, in addition to small amounts of coke and gases. The pyrolysis oil itself, which was obtained from the pyrolysis of commercial polystyrene granules – pure GPPS without contaminants and impurities – consists of a total of 27 components present as mono-, di-, and triphenyls. The monoaromatics, which primarily include styrene, toluene, α-methylstyrene and ethylbenzene, make up the majority. Together, these components account for 88.5 % by mass of the pyrolysis oil.
The components are grouped in a knowledge-based manner in a first step to reduce the size of the component list and thus the number of variants of possible separation sequences. The grouping criteria are determined on the basis of a suitable substance data model. The Peng-Robinson equation of state is chosen as the material data model because it is a good approximation for nonpolar material systems with real components. The cubic equation of state depends on the substance-specific acentric factor ω, which is used as the first grouping criterion. This is calculated via the critical quantities Tc and pc and describes the deviation of a molecule from the ideal spherical shape. Substances with similar ω values have similar properties and can be grouped 22. For the determination of the acentric factor, literature sources as well as own calculations according to VDI-Wärmeatlas/D1:3.1-3.3 are considered 23-25. The calculation of the ω values shows the formation of two plateaus, so that the components can be divided into the two groups mono- and diphenyls (a list of the 27 components can be found in the Supporting Information (SI, S1)). For a further grouping of the monoaromatics, it is checked whether the interaction parameter kij is a suitable criterion. The parameter is used for the calculation of the gas-liquid/ liquid-liquid equilibria (VLE and LLE, respectively) 26. The kij values are taken from the NIST database 20. However, a further grouping of the monoaromatics considering the interaction parameters is not reasonable due to the strongly different positive and negative values (SI, S2). Since a thermal processing of the pyrolysis oil is carried out within the scope of the work, a possible further grouping of the diphenyls is checked on the basis of the vapor pressure curves of the components. In principle, significantly lower vapor pressures were found for the diphenyls than for the monophenyls (SI, S3), which is why it makes sense to group the diphenyls as a high-boiling fraction. The grouping steps shown above result in a final component list including 19 components (SI, S4), serving as the basis for the actual simulation of the separation sequence.
Following the determination of the final component list, the model-based preparation of the pyrolysis oil – which is necessary due to the use of a fluidized bed reactor – takes place. After the processing steps within the pyrolysis – separation of the fine dust in a cyclone, quenching of the gas and fine cleaning in the electrostatic filter – the recyclate stream is present in liquid form at a slight overpressure of p = 1.1 bar and ambient temperature (T = 20 °C). Furthermore, the pyrolysis oil contains residues of the sand from the fluidized bed of the fluidized bed reactor used, which are assumed with a mass fraction of approx. 0.2 % at a median value of d50 = 10 μm. The separation of sand and pyrolysis oil is modelled with a sedimentation basin based on the calculation method according to Stieß 27. The basin is mapped in the Aspen Plus® environment as a “Component Separator”. As a further post-treatment step, a suitable inhibitor is added to the stream to inhibit the instability of the pyrolysis oil due to the tendency of the styrene to self-initiate. A commonly used mixture is the solid 4-tert-butylcatechol (TBC) in combination with oxygen. Typically, 15 ppm TBC and 20 ppm oxygen are added to the stream with respect to the amount of styrene 28-31. The absolute amount is determined at each point in the process based on the absolute amount of styrene and the specified proportions (15/20 ppm). The addition is realized in Aspen Plus® by a "mixer". This is followed by a reduction of the operating pressure to minimize the operating temperature of the separation, which reduces the risk of thermal polymerization of styrene as a further measure in addition to the inhibitor dosage. The pressure is assumed to be p = 0.107 bar according to Liu et al. 12. This pressure is consistent with the pressures used for the purification of styrene 32, 33. The recycle stream prepared in this way is separated in a subsequent sequence such that the value product styrene is obtained with a typical purity of at least 99.6 vol % 12, 34. Thermal separation in a distillation column is chosen as the separation operation, since this is a widely used and highly known technology which, moreover, has proven to be a suitable process for the purification of styrene in vacuum mode 12, 13, 31, 32, 35.
3 Results
3.1 Simulation of Separation Sequence

which is considered a guide value for distillation columns with regard to minimum total costs 30, and distillate/feed ratios of 0.1–0.9. The feed of the column is fed at liquid boiling point. The separation cuts result from the consideration of the mass flows and the boiling temperatures of the components contained in the pyrolysis oil. For a pure styrene stream, the immediate neighbouring components must be separated in terms of boiling temperature. Considering relevant mass flows with a mass fraction > 1 %, separation cuts between ethylbenzene/styrene and α-methylstyrene/styrene are obtained. The separation is mapped in a first step in an indirect sequence (Fig. 1) by means of two consecutive distillation columns (11, 12), because the use of two consecutive distillation columns for the implementation of two separation steps means the initially simplest technical implementation. In addition, a relatively low light boiling stream (TBP < TBP,styrene) is fed to the first column compared to the medium/heavy boiling stream, which includes all components with TBP > TBP,styrene. As a result, the energy efficiency of the indirect sequence chosen here may be more advantageous than in a direct sequence which is also commonly chosen. The heat exchangers (W1, W2) provide the liquid-boiling feed and liquid ring vacuum pumps (V1, V2) generate the negative pressure in the system. In the first column, α-methylstyrene and the other medium/heavy components are separated. By means of the second column, a pure styrene stream (> 99.6 mol %) can then be obtained.
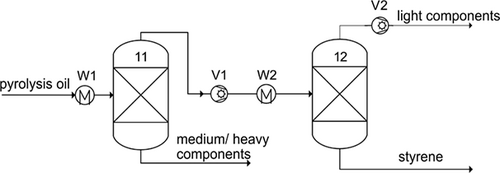
The process parameters of the two distillation columns are listed in Tab. 1. The extreme distillate/ feed ratios of u = 0.89 and 0.09, which result from the high proportion of styrene in the feed, are striking. The reflux ratios set here, 5 and 35, are higher than the typical reflux ratios calculated via Eq. 1. High reflux ratios are largely avoided in technical implementation due to high operating costs. In this case, however, high operating costs due to high reflux ratios are not to be expected, since the stream to be condensed at the head is low. Nevertheless, a possible reduction of the reflux ratio should be examined, and an adjustment of the distillate/ feed ratio is indicated. Therefore, process alternatives that have a different split of the streams or include a third distillation column are discussed below.
Variant |
Separation step |
T [°C] |
p [bar] |
nSt [–] |
Feed stage [–] |
v [–] |
u [–] |
---|---|---|---|---|---|---|---|
a) |
1 |
75.3 |
0.107 |
32 |
22 |
5 |
0.89 |
2 |
72.9 |
0.107 |
88 |
43 |
35 |
0.09 |
|
b) |
1 |
75.3 |
0.107 |
80 |
5 |
20.0 |
0.50 |
2 |
70.7 |
0.107 |
90 |
8 |
35.0 |
0.16 |
|
3 |
76.2 |
0.107 |
50 |
48 |
4.8 |
0.78 |
|
c) |
1 |
75.3 |
0.107 |
80 |
5 |
195 |
0.20 |
2 |
63.9 |
0.107 |
110 |
8 |
17 |
0.40 |
|
3 |
89.2 |
0.107 |
80 |
77 |
6 |
0.49 |
|
d) |
1 |
75.3 |
0.107 |
24 |
23 |
1.44 |
0.50 |
2 |
75.7 |
0.107 |
85 |
60 |
95.00 |
0.09 |
For the separation of a multi-component system, as is the case in this work, columns with side-draw, pre-fractionation columns or the so-called sloppy distillation are used (Fig. 2). Besides known advantages of sloppy and pre-fractionator sequences in terms of energy efficiency, compared to conventional sequences 36, The sloppy distillation (b) is considered because this sequence allows for a flexible operation: although employing three distillation columns and, thus, subsequent increases in CAPEX compared to the indirect sequence, all columns can in principle be operated at different pressures (although this parameter is not varied in our study). Further, variation of the middle product may be varied by means of heat loads in reboiler/condenser, both together adding different degrees of freedom allowing for a flexible operation, which can be of high importance in case of variations, i.e., in feed composition. Operating the second and third distillation common at the same pressure level – as it is assumed in our study – allows for the combination of both the second and third column in one column and obtaining the styrene product as a side stream, what leads to the pre-fractionator sequence (d). The extended sequence (c) can generally be of interest in case of low light component flow and high middle component flow – as it is given in our case – in terms of energy efficiency and is thus investigated additionally. Each process alternative yields a pure styrene stream (> 99.6 mol %) with the required amount of = 2452 kg h−1.
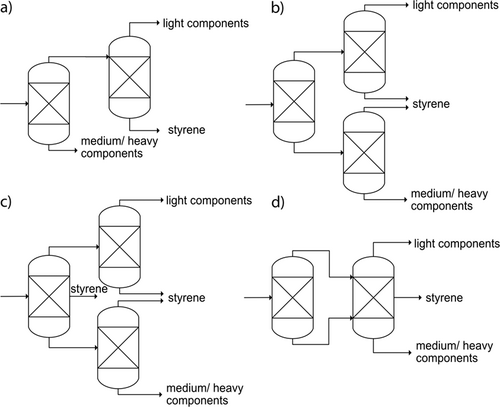
All process alternatives shown in Fig. 2 are optimized with regard to the reflux ratio and the number of stages, meaning that both parameters are varied to achieve the above-mentioned value ranges if possible. The results of this optimization process are shown as "optimized" in Fig. 3. In Fig. 3, the energy requirements of the process variants are plotted with the optimization scenarios for the individual process areas of distillation, heat transfer and vacuum generation. The energy requirements for the distillation columns and the heat exchangers are taken directly from the simulation, whereas the energy consumptions of the vacuum generators were derived from technical data sheets of suitable liquid ring vacuum pumps. The share of distillation in the total energy consumption of the separation sequence is at least 87 % (variant (b) optimized) and thus, as expected, clearly dominates the energy consumption for heat transfer and vacuum generation in all variants investigated. The relatively high energy consumption of variant (c) – in both the initial and optimized variants – is due to the high reflux ratio of the first column: the overhead flow of this column is comparatively high, so that a high proportion is condensed and returned to the column.
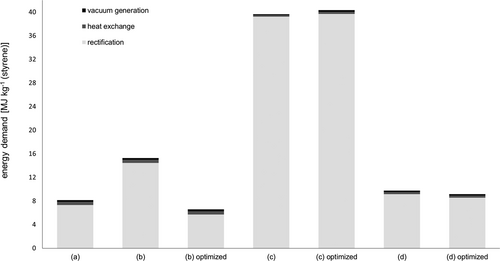
Due to the unsuitable distillate/feed ratio of variant (a) and the relatively high energy consumption of variant (c), process variants (b) and (d) are suitable from an energy efficient operation point of view. In addition to an overall low energy demand, an approximately constant energy demand is also aimed for when identifying a suitable process variant in order to be able to guarantee the utility supply of the process even in the event of varying process parameters and thus to make the process as robust as possible. This sensitivity consideration is carried out by comparing the original variant with the optimized variant. In process alternative (b), there is a comparatively high relative deviation of the optimized variant from the original variant of approx. 57 %, whereas the specific energy input for process variant (d) is approximately the same. In addition, equimolar separations are achieved in process variant (d) – the distillate/feed ratio of the second column is less than 0.5, since there is a side stream (Tab. 1) – and the reflux ratio of the first column is in the range of typical values (cf. Eq. 1). Based on the two process parameters v and u, process variant (d) is therefore a reasonable alternative to variant (a), which also results in a relatively low and constant energy requirement. Therefore, process variant (d) is considered for further investigations.
3.2 Simulation of Polymerization
In order to evaluate the integration of the recovered styrene stream into the industrial PS production, the simulation of the styrene polymerization is necessary. For this purpose, bulk polymerization according to BASF's tower process is selected as the polymerization method. This involves a combination of two stirred tanks (CSTR) and a reactor tower (RPlug). The stirred tanks are operated discontinuously in order to achieve a pre-polymerization of styrene. Then, the reaction mass is fed into the continuous reactor tower 32, 35, 38-40. Finally, the polymer mass is fed out of the reactor tower by screw pumps onto a cooling conveyor and crushed. A PS pellet is produced, which is melted and further processed elsewhere. Tab. 2 summarizes the operating conditions taken from the literature.
|
p [bar] |
T [°C] |
τ [h] |
X [%] |
---|---|---|---|---|
CSTR1 |
1.013 |
80 |
55 |
30–40 |
CSTR2 |
1.013 |
80 |
55 |
30–40 |
Rplug |
1.013 |
110–220 |
28 |
98 |
In the simulation, the purely thermally initiated polymerization of styrene is considered, the mechanism of which is described by the reaction equations (2)–(8). First, two styrene monomers react to form a so-called Diels-Alder dimer AH, which then reacts with a third monomer to form the radicals A* and M*. These two radicals then initiate the polymerization 41, 42.


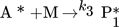
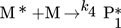



The data for the kinetics are taken from 42 and the POLYNRTL model typically used for polymerization is applied as the material property model. To achieve the conversions as listed in Tab. 2, reactor volumes and temperatures are adjusted. The resulting operating conditions and key reaction parameters of the polymerization are summarized in Tab. 3. The post-treatment of the highly viscous melt is represented in Aspen Plus® in a simplified way by cooling below the glass transition temperature by means of a heat exchanger, whose energy demand is also balanced.
|
p [bar] |
T [°C] |
τ [h] |
V [m3] |
X [%] |
---|---|---|---|---|---|
CSTR1 |
1.013 |
90 |
55 |
100 |
32.31 |
CSTR2 |
1.013 |
90 |
55 |
100 |
32.31 |
RPlug |
1.013 |
120–230 |
28 |
157 |
98.44 |
3.3 Energetic Evaluation of the Circular Production Route of Polystyrene
-
Production of the pyrolysis oil by pyrolysis of the PS waste
-
Post-treatment of the pyrolysis oil to produce a single-phase stable phase
-
Thermal separation of the pyrolysis oil and concentration of the styrene fraction
-
Polymerization of the recycled styrene
With this interconnection, the purity requirement with respect to the styrene fraction in the product stream (cf. Tab. 4: Styrene) ≥ 99.6 vol % is met. The minor components obtained are ethylbenzene at 0.3 vol %, 2,6-dimethyl-1-heptane (0.032 %) and toluene, allylbenzene and alpha-methyl styrene (0.013 % each). The shares of the other minor components are in the low per thousand range. Furthermore, no solid (sand) is present in the post-treated pyrolysis oil and more than 98 % of the styrene is converted to PS (PS granules).
Material stream |
Pyrolysis oil |
Post- treatment pyrolysis oil |
Styrene |
PS granules |
---|---|---|---|---|
Light components |
0.0793 |
0.0795 |
0.0037 |
0.0037 |
Styrene |
0.8102 |
0.8124 |
0.9960 |
0.0156 |
Medium and heavy components |
0.1077 |
0.1080 |
0.0003 |
0.0003 |
Sand |
0.0027 |
0.0000 |
0.0000 |
0.0000 |
TBC [ppm] |
0.0000 |
0.0000 |
9.4 · 10−6 |
1.1 · 10−9 |
PS |
0.0000 |
0.0000 |
0.0000 |
0.9804 |
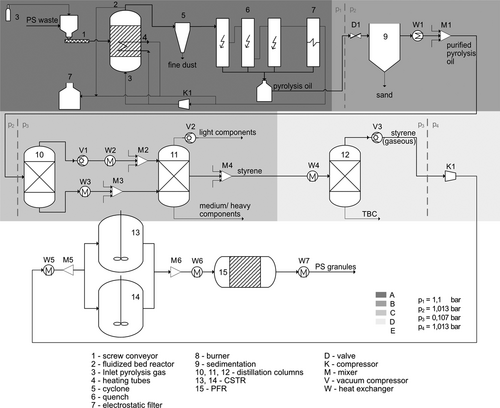
For the energetic evaluation of the resulting circular PS route, the specific energy demand of the subprocess steps are first determined and compared. The energy demand of the pyrolysis sequence is about 13 MJ kg−1 (styrene). This calculation was carried out for a continuously operated fluidized bed reactor, with no heat integration measures considered (for details, see SI, S5). The energy demand of the post-treatment of the pyrolysis oil is neglected in the present work since no relevant energy expenditures are available for this purpose.
The results for the separation sequence and the subsequent styrene polymerization are taken from the simulations performed. In addition, an energy demand of 0.36 MJ kg−1 PS waste is assumed for the comminution of the recycled PS to obtain PS granules 43. The comparison of the energy demand of the sub-process steps shows that more than half (53 %) of the total energy requirement of the circular PS route has to be provided for the pyrolysis step (Fig. 5). While the energy input for distillation also accounts for a high share of the total energy demand at around 40 %, polymerization only accounts for around 8 % of the energy demand. At about 2 MJ kg−1 (styrene), the energy input for polymerization deviates by 15 % from the literature value 44. The total energy demand of the circular PS route, including the production of a PS granulate, is about 24.5 MJ kg−1 (styrene), excluding the energy demand for the pretreatment of the plastic waste and the further processing of the plastic granulates, since the energy demand for the collection and sorting as well as the preparation of PS waste and the processing of the PS granulate is similar for all recovery methods 43. The calculated energy demand of the circular PS route is less than 30 % of the energy demand of conventional polystyrene production which is about 83 MJ kg−1 (styrene) 44. The high energy demand for the production of primary styrene is required for the synthesis of ethylbenzene, since only about 6 % of the cumulative energy demand of the primary route is used for the production process of styrene from ethylbenzene 41. The synthesis of ethylbenzene is not necessary in the production of secondary styrene, resulting in the significantly lower energy demand.
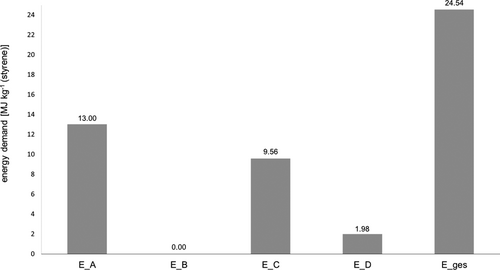
4 Summary
This paper presents a possible separation sequence for a PS recyclate stream from a pyrolysis process, which allows the integration of a styrene recyclate into industrial PS production. Processing and separation of the pyrolysis oil is implemented by a separation of the solids, the addition of an inhibitor and a subsequent thermal separation. The latter consists of vacuum distillation columns connected in series, in which the share of styrene in the recyclate stream is increased to a purity of 99.6 wt %. Various process variants are investigated, which differ in terms of the number of columns, their interconnection and the number of stages, as well as the reflux and distillate/feed ratios. By comparing the respective specific energy demand, a separation sequence with two vacuum distillation columns in a pre-fractionator interconnection is identified as energetically advantageous. The mapping of the complete process from the PS waste stream to the recycling-based secondary styrene is done by implementing a tower process styrene polymerization into the existing model. By producing secondary styrene using pyrolysis, and processing and integrating the processed recyclate stream into the styrene polymerization, about 60 MJ kg−1 of styrene are saved, compared to the conventional production of styrene. Thus, pyrolysis with subsequent treatment of the pyrolysis oil presents itself as a promising option for the industrial implementation of circular production processes.
Supporting Information
Supporting Information for this article can be found under DOI: https://doi.org/10.1002/cite.202100210. This section includes additional references to primary literature relevant for this research 45-49.
Acknowledgements
Open access funding enabled and organized by Projekt DEAL.
Symbols used
-
- d50 [μm]
-
median
-
- k [m3kmol−1h−1]
-
velocity constant
-
- kij [–]
-
interaction parameters
-
[kg h−1]
-
mass flow
-
- n [–]
-
number of
-
- p [bar]
-
pressure
-
- ps [bar]
-
vapor pressure
-
- T [°C]
-
temperature
-
- u [–]
-
distillate/ feed ratio
-
- v [–]
-
reflux ratio
-
- X [%]
-
conversion
Greek letters
-
- τ [h]
-
residence time
-
- ω [–]
-
acentric factor
Sub- and Superscripts
-
- BP
-
boiling point
-
- c
-
critical
-
- min
-
minimum
-
- PS
-
polystyrene
-
- Sek
-
secondary
-
- St
-
stages
-
- Sty
-
styrene
-
- tc
-
chain termination
-
- th
-
theoretically
-
- tr
-
transfer
Abbreviations
-
- A*
-
radical, dimer
-
- AH
-
Diels-Alder dimer
-
- CSTR
-
continuously stirred tank reactor
-
- D
-
deactivated chain
-
- M
-
monomer
-
- M*
-
radical, monomer
-
- P*
-
activated chain
-
- PFR
-
plug flow reactor
-
- PS
-
polystyrene
-
- TBC
-
4-tert-butylcatechol