Separation Units 4.0 – Trenntechnik in der chemischen Industrie auf dem Weg in die digitale Zukunft. Eindrücke und erste Ergebnisse vom Tutzing-Symposion 2019
Separation Units 4.0 – Separation Technique in Chemical Industry on its Way in a Digital Future. Impressions and First Results from the Tutzing-Symposion 2019
Abstract
deIm Oktober 2019 trafen sich Vertreter aus Akademia und Industrie auf Einladung der ProcessNet-Fachgemeinschaft „Fluiddynamik und Trenntechnik” zur Statusbestimmung und Weiterentwicklung des Fachgebiets. Dabei lag der Fokus dezidiert auf dem einzelnen Trennapparat und der fluidverfahrenstechnischen Trennoperation selbst. In fünf Themenclustern mit jeweils mehreren Workshops wurden künftige Entwicklungen und sich stellende Trennaufgaben, Chancen, Herausforderungen und Potenziale der fluiden Trenntechnik identifiziert sowie intensiv diskutiert. Darüber hinaus wurden mögliche und notwendige Vernetzungen und Kooperationen mit anderen Branchen und Wissensdisziplinen erörtert, welche die Basis für weiterführende Konzeptentwicklungen und für die Ableitung notwendiger Aktivitäten sind.
Abstract
enIn October 2019 the ProcessNet Section „Fluid Dynamics and Separation” invited experts from academia and industry to discuss the status and future developments in the field. In contrast to earlier events considering a whole plant the focus was complementary on apparatus level. In five clusters within several workshops decision makers evaluated opportunities, challenges, and further cross-linking with other branches as a basis for further activities such as white paper, roadmap, etc.
1 Einleitung
Die ProcessNet-Fachgemeinschaft „Fluiddynamik und Trenntechnik” ist die Heimat vieler seit Langem etablierter und erfolgreicher Arbeitsgebiete bzw. Fachgruppen. Insbesondere mit Blick auf die derzeit und in Zukunft ablaufende digitale Transformation und vor dem Hintergrund einer sich verändernden Rohstoffbasis und gesellschaftlichen Randbedingungen, wurde deren Bedeutung für die strategische Ausrichtung und zukünftige Aufstellung der Fachgemeinschaft diskutiert. Rund 90 Entscheidungsträger aus Industrie, Forschungseinrichtungen und Hochschulen nahmen an interdisziplinären Vorträgen, Workshops und Diskussionsrunden teil (Abb. 1). Ziel des 58. Tutzing-Symposions war die Entwicklung eines Zukunftsbildes der Fluid-Trenntechnik insbesondere unter den Aspekten der Digitalisierung, des Wandels der Rohstoffbasis und der klimatischen Herausforderung. Daraus werden strategische und konzeptionelle Maßnahmen für Forschungsinitiativen, Aus- und Weiterbildung und die zukünftige Ausrichtung der Fachgemeinschaft abgeleitet.
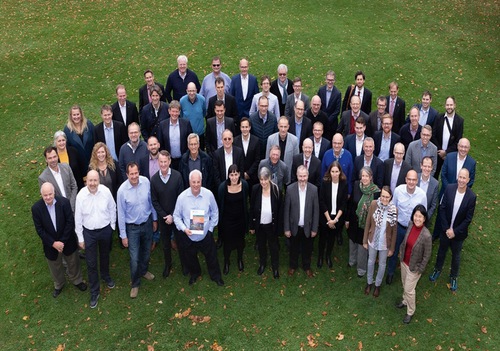
Das Programmkomitee bildeten Prof. DI Dr. Hans-Jörg Bart, TU Kaiserslautern, PD Dr. Michael Bortz, Fraunhofer ITWM, Kaiserslautern, Dr.-Ing. Achim Gritsch, BASF SE, Ludwigshafen, Prof. Dr.-Ing. Marcus Grünewald, Ruhr-Universität Bochum, Prof. Dr.-Ing. Dr. h.c. Uwe Hampel, Helmholtz-Zentrum Dresden-Rossendorf, Dr.-Ing. Michael Häberl, Merck KGaA, Darmstadt, Dr.-Ing. Andreas Hoff, Evonik Technology & Infrastructure GmbH, Hanau, Dr.-Ing. Carsten Knösche, BASF SE, Ludwigshafen, Prof. Dr.-Ing. Jens-Uwe Repke, TU Berlin, Dr. Thomas Runowski, Bayer AG, Leverkusen, Prof. Dr.-Ing. Stephan Scholl, TU Braunschweig, und Dr.-Ing. Sebastian Zeck, ProcessNet „Wanted Technologies” (ehemals BASF), DECHEMA, Frankfurt am Main.
2 Digitale Transformation
Die digitale Transformation durchdringt weite Teile der Industrie mit einer zunehmenden Vernetzung und Digitalisierung entlang der Wertschöpfungsketten. Basierend auf dem Whitepaper der DECHEMA „Digitalisierung in der Chemieindustrie” entsteht die Vision eines gläsernen Trennapparates mit einem zeitlich, örtlich und methodisch dichten Monitoring der Betriebszustände, das eine daten- und modellbasierte Optimierung transienter oder instationärer Prozesse wie In-/Außerbetriebnahme, Laständerungen etc. erlaubt. Auch der nicht bestimmungsmäßige Betrieb (Phasenmitriss, Schäumen, Verbacken etc.) wird am Einzelapparat erkannt und in übergeordnete Strukturen kommuniziert. Basis ist hier die Implementierung von innovativer Messtechnik und neuartigen Sensoren in Kombination mit datengetriebenen, wissensbasierten oder rigorosen Modellen zur Prozesssimulation und -führung. Ein Betrieb an Stabilitäts- bzw. Kapazitätsgrenzen ermöglicht einen höheren Durchsatz mit steigender Effizienz, unverminderter Prozesssicherheit und gleichbleibender Qualität der Produkte. So wird künftig der Betrieb in einem Betriebsfenster und nicht wie bisher an einem Arbeitspunkt zum Regelfall werden, was auch bereits im Prozessdesign zu berücksichtigen ist.
Darüber hinaus bringen eine zunehmend volatile Energie- und Rohstoffbasis neue Herausforderungen für die Trenntechnik mit sich. Die zur Verfügung stehenden und für den Prozessbetrieb nutzbare Energieträger verändern sich und erfordern in Folge eine Anpassung der Apparate- und Anlagentechnik. Eine stärker biobasierte Rohstoffversorgung stellt neue Trennaufgaben und damit Herausforderungen an die einzusetzenden Trenntechniken. Die Komplexität der Herausforderungen wird weiter verstärkt durch die gesellschaftliche Forderung nach der Etablierung von klimaneutralen Produktions- und damit einhergehenden Trennprozessen.
Das Symposion sollte die mit dieser Digitalisierung der Trenntechnik und den weiteren Zukunftsthemen verbundenen Chancen und Herausforderungen identifizieren und konkretisieren sowie eine Vernetzung der Trenntechnik mit weiteren Branchen (Softwareingenieure, MSR-Technik, Betreiber, Hersteller) fördern. Damit reiht sich das Symposium mit seinen Schwerpunkten logisch in eine ganze Reihe von Veranstaltungen der ProcessNet ein, so auch das letztjährige 57. Tutzing-Symposion mit dem Titel „100% digital! Überlebensstrategien für die Prozessindustrie”, das sich auf modulare Anlagenplanung und -bau und verteilte Intelligenz fokussierte. Der Fokus beim 58. Tutzing-Symposion lag auf bereits vorhandenen Anlagen, sogenannten Brown-Field-Anlagen (z. B. Abb. 2, grüner Bereich am Themencluster B, Sensorik) bzw. zukünftiger Produktionsapparate der chemischen Industrie (Bulk-, Spezial- und Feinchemikalien). Von Molekularer Modellierung und Künstlicher Intelligenz bis zu deren Umsetzung in möglicher zukünftiger Apparate- und Anlagentechnik wurde ein Bogen gespannt, der die Trenntechnik aus Sicht von Industrie und Akademia für die zukünftigen Herausforderungen ertüchtigt sowie die Chancen und neuen Möglichkeiten zu ihrem Nutzen erschließt.
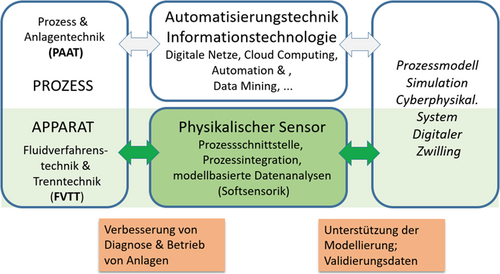
Weitere wichtige Zukunftsaspekte, wie eine zunehmend volatile Energie- und Rohstoffbasis, wässrige Einsatzströme mit geringer Wertproduktkonzentration und die Forderung nach klimaneutralen Prozessen, wurden speziell unter dem Gesichtspunkt der fluiden Trenntechnik umfassend diskutiert. Als übergreifender und unverzichtbarer Aspekt wurde dabei auch die (berufs-)lebenslange Aus- und Weiterbildung thematisiert.
In seinem Eröffnungsvortrag zum Thema „Automatisierte, vernetzte Anlagen: Wer ist für Algorithmen verantwortlich?” benannte der Rechtsanwalt Dr. M. Neupert mit einem paragraphenfreien juristischen Blick künftige Grundprobleme und ordnete diese ein. Ein autonomer Anlagenbetrieb fordert das Gewissen heraus: Was verstehen wir unter Autonomie und Verantwortlichkeit? Wer trägt die Aufsichtspflicht über lernende Systeme? Wie gehen wir mit dem Verlust klarer Grenzen als Kehrseite der Vernetzung um? Der zweite Abendvortrag von Prof. Dr. Markus Kraft, University of Cambridge, widmete sich dem Thema: ”How to make use of cyber-physical systems in industry 4.0 in process industry, energy sector and environment”. An Beispielen demonstrierte er dabei insbesondere die Notwendigkeit der semantischen Interoperabilität als Voraussetzung für die vertikale und horizontale Integration autonomer, dezentralisierter Systeme und Cloudservices.
3 Fünf Themencluster zur Apparatesituation
Auf dem Symposion wurden in den drei Tagen die folgenden fünf Themencluster behandelt, wobei der letzte Themencluster eine grobe erste Zusammenführung des Diskutierten unter dem Aspekt der fluiden Trenntechnik darstellt. Nachfolgend soll ein kurzer Einblick in die fünf Cluster gegeben werden, wobei eine Vertiefung der Themen in weiteren Artikeln erfolgen wird.
A) Apparate heute & morgen
Das Design von Apparaten und deren Auslegung stellen den Kern der Expertise im Bereich der Trenntechnik dar. In den letzten Jahren neu entwickelte Simulations- und Auswertemethoden sowie innovative Fertigungsverfahren eröffnen neue Lösungsansätze und haben das Potenzial, die typische Aufgabenverteilung zwischen Hochschulen, Apparateherstellern, Dienstleistern und Betreibern nachhaltig zu verändern. Da diese Veränderungen teilweise heute schon in Ansätzen bei den Prozessen in den Life Sciences einsetzen, wurden sie gemeinsame mit dem Cluster D diskutiert und werden dort vorgestellt.
B) Neue Entwicklungen in der Sensor- und Messtechnik
Neue und verbesserte Sensorik ist ein entscheidendes Element der digitalen Transformation in der Trenntechnik. Zukünftige Sensorentwicklung in der und für die Trenntechnik bedarf des verfahrenstechnischen Blicks, um geeignete Prozessschnittstellen zu schaffen, eine robuste und kostengünstige Prozessintegration der Sensorik zu gewährleisten und modellbasierte Softsensorik für den Anlagenbetreiber bereitzustellen. In intensiver Gruppenarbeit und Diskussion in den Expertenkreisen wurden die folgenden drei Thesen für zukünftige Sensorik in der Trenntechnik formuliert.
These 1
-
Kabellose Sensoren mit autarker Energieversorgung und drahtloser Kommunikation und Datenübertragung,
-
Sensoren für hohe Temperaturen und raue Prozessbedingungen,
-
Softsensoren für die Überwachung des Anlagenistzustands und für die Prozessoptimierung.
These 2
-
Entwicklung multipler kostengünstiger Sensoren,
-
Implementierung von Messeverfahren für verteilte Parameter (verteilte Sensoren, Sensorarrays, Bildgebung, Prozesstomographie).
These 3
-
schlafender Sensor mit Aufwachfunktion,
-
nachrüstbarer Sensor,
-
Clamp-on-Sensor,
-
Single-use-Sensor (Einmalsensor).
C) Kombination von Daten und Modellen: Möglichkeiten und Grenzen
Der schnelle und unbegrenzte Zugang zu „sauberen” Daten und die Verknüpfung dieser über intelligente Algorithmen und Modelle sind essenziell, um einerseits verborgenes Wissen nutzbar zu machen und andererseits ganz neue Innovationsmöglichkeiten zu eröffnen. Die wesentliche Frage ist, was die wesentlichen Handlungsfelder bei der modellbasierten Beschreibung von Trennapparaten sind. Dabei ergaben sich vier Thesen (s. a. Abb. 3).
I. Kopplung von Skalen
-
(Quantenmechanische Elektronenstruktur),
-
Molekulare Eigenschaften,
-
Laboruntersuchungen und -kalibrierung: Strömung, Mehrphasigkeit und Transportprozesse,
-
Maßstabsvergrößerung auf industrielle Skalen,
-
(Apparate und Anlagenverbünde).
II. Dynamische und modulare Simulation und Optimierung
-
Look-up-Tabellen/modellbasierte Kennfelder: Beherrschbarkeit großer vorsimulierter Szenarien und Datenmengen durch künstliche Intelligenz (KI),
-
offene, modulare, erweiterbare Plattformen (Modelle und Daten sind nicht fixiert, sondern „leben”, müssen angepasst/erweitert werden),
-
Lösungsalgorithmen mit definierten Schnittstellen zur Austauschbarkeit,
-
Permanente Adaption von Steuerung/Regelung durch Berücksichtigung von Modellinformationen.
III. Modellentwicklung
-
Kombination von Computational Fluid Dynamics (CFD) mit Thermodynamik (Phasengleichgewichte) und Chemie (Reaktionen),
-
Messtechnik zur Erhebung von Daten an Grenzflächen,
-
insbesondere auch die notwendige modellmäßige Beschreibung von Fehlzuständen. Eine reine Beschreibung des Auslegungspunktes, des Betriebs am einzelnen Arbeitspunkt, wird künftig nicht mehr ausreichend sein.
IV. Workflow zur Integration von Daten und Modellen
-
unüberwachtes Lernen zum Erkennen von Features und Korrelationen
-
auf Rohdaten,
-
auf Daten, die bereits so vorverarbeitet wurden, dass sie nur noch Informationen über physikalisch nicht abbildbare Phänomene beinhalten (z. B. nach Ausgleichsrechnung),
-
überwachtes Lernen/Modellidentifikation einschließlich Quantifizierung der Unsicherheiten,
-
Vorschläge für neue Experimente aufgrund des aktuellen Modells, die einen möglichst hohen Informationsgehalt haben, also die Unsicherheiten bestmöglich reduzieren.

D) Trenntechnik in der Life Science – Prozess sucht Anlage
Zur Herstellung neuer Produkte in den Life Sciences, hier speziell der Produktion kleiner, auf chemischem oder biotechnologischem Weg synthetisierter Moleküle pharmazeutischer Wirkstoffe, wird nur in seltenen Fällen eine eigene, dedizierte Produktionsanlage errichtet. Vielmehr werden neue Produktionsprozesse für neue oder weiterentwickelte Produkte, wie z. B. eine neue Formulierung eines bekannten Wirkstoffs, meist unter Nutzung eines bestehenden Apparate- und Anlagenparks inklusive Umfeld und Infrastruktur in einer Mehrprodukt-Batchproduktion gefertigt. Häufig wird für jeden Verfahrensschritt separat entschieden, wo er realisiert wird, um ein wirtschaftliches Optimum zu erreichen. Diese logistische Herausforderung ist nur mit einer sehr guten Kenntnis und Dokumentation der Prozessschritte und einer Standardisierung der Produktionstechnik für sicherheits- und entsorgungstechnisch herausfordernde Stoffe in einem internationalen Umfeld zu bewerkstelligen. Für regulierte Prozesse muss zusätzlich jeder Schritt dokumentiert werden.
Diese Thematik und die sich daraus ergebenden Fragestellungen und Lösungsansätze wurden in Tutzing in einer eigenen Diskussionsrunde unter der Überschrift „Trenntechnik in den Life Sciences – Prozess sucht Anlage” behandelt. Dazu wurden zwei typische Szenarien diskutiert: eine Inhouse-Produktion mit den Einheiten Entwicklung, Engineering und Produktion als den Key Playern, sowie eine externe Produktion, mit dem Prozesseigner, dem Lohnfertiger und den Apparatelieferanten als zentralen Beteiligten. Jeder Hersteller eines Produktes muss – für den eigenen Anspruch, im Fall von regulierten Prozessen auch für die Behörden – für jeden Prozessschritt, ob eigen oder fremd produziert, das Know-how im Sinne eines Betreibers besitzen. Die Beschaffung, Dokumentation und Verfügbarmachung dieses Wissens beginnt in der Entwicklung, wächst bei der Herstellung von Testchargen und dem Transfer in die Produktion und begleitet die fehlerfreie Produktion.
-
Der Workflow und alle Workflowelemente werden voll digital über den gesamten Lebenszyklus.
-
Standardisierung und Flexibilisierung prozesstechnischer Funktionseinheiten unterstützen die schnelle Prozessimplementierung in eine vorhandene Infrastruktur.
-
Die Bedeutung und Intensität vertikaler Netzwerke nimmt zu.
1. Der Workflow und alle Workflowelemente sind voll digital über den gesamten Lebenszyklus
Dies beginnt mit der optimalen Dokumentation, Validierung und Auswertung aller verfügbaren und relevanten Informationen (Einflussgrößen, Messgrößen, Prozessparameter, Entsorgung, Servicemedien, stofflicher und wo nötig energetischer Bilanzierung von absatzweisen und kontinuierlichen Prozessschritten, Abgleich mit Online-Daten und -Modellen etc.) über alle Stationen des Lebenszyklus. Robuste und versionierte Prozesssimulationen stellen ein zentrales Element der Dokumentation und Rückverfolgbarkeit, Know-how-Sicherung, Kommunikation mit Dritten sowie Referenzpunkt weiterer Bearbeitungsschritte, wie Apparateauslegung, Entwurf eines Sicherheitskonzeptes oder der Mess- und Regelstrategie, dar.
Eine zentrale Bedeutung kommt in diesem Kontext einem weiterentwickelten Verständnis von Apparate- und Anlagentechnik und deren Funktion in einem Produktionsprozess zu. Die letztlich auf den verfahrenstechnischen Grundoperationen beruhende Prozesstopologie muss in korrespondierenden apparate- und anlagentechnischen Funktionseinheiten gespiegelt werden. Die Funktionseinheit als Ganze wie auch alles zentrale Equipment darin ist selbstüberwachend und fernabfragefähig. Dies erfordert die Ausstattung mit lokaler Intelligenz zur First-Level-Verarbeitung von originären Prozess- und gegebenenfalls Produktdaten. Damit ist jederzeit eine Analyse der Equipmentperformance möglich. Dies beinhaltet auch die Bereitstellung aller Equipment-bezogenen Informationen zur Einbindung in eine übergeordnete Strategie und Optimierung einer Predictive Maintenance durch die simulationstechnische Spiegelung aller Hardware-bezogenen Funktionalitäten. Die daraus gewonnenen Produkt- und Prozessdaten sowie deren intelligente Verarbeitung und kommunizierbare Bereitstellung in einem Digitalen Zwilling ist ein zentraler Bestandteil einer solchen Funktionseinheit.
Basis für das erlangte Prozess- und Produktwissen sind intelligente Sensoren, die aufgrund eines geeigneten Apparatedesigns repräsentative Messdaten liefern, die von einem Modell validiert und verwendet werden, so dass ein möglichst feinmaschiges Netz von Soll/Ist-Abgleichen gespannt wird und die Schnittstellen zwischen Apparaten, Units oder Anlagenteilen klar spezifiziert sind.
Die Betrachtung des gesamten Lebenszyklus beginnt mit der maximalen Ausbeute an Informationen aus und während der Rezept- bzw. Verfahrensentwicklung (mit wenig Materialeinsatz) für die späteren Prozessrealisierung. Die Kombination und synergistische Nutzung hochintegrierter Messtechnik und Sensorik, Modellierung und Optimierung sichert auch in dem Spannungsfeld „hohes Risiko des Scheiterns” versus „entspannte Terminsituation” einen stetig wachsenden Wissensgewinn.
2. Standardisierung und Flexibilisierung prozesstechnischer Funktionseinheiten unterstützen die schnelle Prozessimplementierung in eine vorhandene Infrastruktur
Die oben eingeführten Funktionseinheiten für ausgewählte Anwendungen müssen für eine schnelle, nahtlose und flexible Nutzung in einem Produktionsprozess standardisiert ausgeführt werden. Welche Elemente und Aspekte dieser Standard in einem ersten Schritt im Detail umfasst, wie eine Standardisierung konkret auszuführen ist, z. B. bezüglich Werkstoffauswahl, Anschlussmaßen für Rohrleitungen, Nutzung von Servicemedien etc., und wie dazu bereits vorhandene Standardisierungen in Form von Normen, z. B. die DIN-Normen von Apparateausführungen oder die NAMUR Open Architecture für die Automatisierungsarchitektur, einzubinden sind, ist in interdisziplinären Fachgesprächen zu vereinbaren. Eine standardisierte, erweiterbare Instrumentierung stellt sicher, dass diese produkt- und prozessspezifisch eingesetzt werden kann sowie neue verfügbare Technologien nahtlos integriert werden können. Die standardisierte Einbindung in bzw. Bereitstellung von Kommunikationsplattformen in Prozessdatensysteme muss auch die Funktionsaufteilung von lokaler bzw. dezentraler und zentraler Intelligenz in Prozessleitstationen beinhalten. Erste Schritte in diese Richtung könnten die Definition und exemplarische Ausgestaltung verschiedener, zentraler trenntechnischer Funktionseinheiten sein.
3. Die Bedeutung und Intensität vertikaler Netzwerke nimmt zu
Vertikale Netzwerke verbinden Apparatehersteller, Ingenieurdienstleister, Genehmigungsbehörden und Anlagenbetreiber. Insbesondere wird eine verstärkte Kooperation von produzierenden Unternehmen mit Apparateherstellern erwartet. Dabei kann es zu einer Verlagerung, Verschiebung von Aufgaben kommen und daraus neue Geschäftsmodelle erwachsen. Das Leasing von Apparaten oder ganzen Funktionseinheiten, das Vorhalten einer entsprechenden standardisierten, normierten und in die Infrastruktur eines produzierenden Unternehmens „drop-in-fähigen” Hardware kann das gebundene Kapital eines Herstellers reduzieren und dem Anbieter gleichzeitig ein weiteres Geschäftsfeld eröffnen. Prozessentwicklungsaufgaben und Apparateauslegung werden immer häufiger aus der Hand der Zulieferer kommen. Dies allerdings erfordert eine frühzeitige Einbeziehung von Know-how-Trägern, Stakeholdern und Genehmigungsbehörden bereits in der Phase der Ausarbeitung eines Transfers eines neuen Produktes in eine geeignete Produktionsumgebung. Vertrauen, Kommunikation und interdisziplinäres Verständnis zwischen allen Beteiligten sind essentielle Voraussetzungen.
E) Herausforderungen für die Fluid-Trenntechniken in der Zukunft
-
Welche Trennproblem sind in 10 Jahren zu lösen? Hier wurde einhellig herausgearbeitet, dass die Komplexität der Trennaufgaben zunehmen wird und die In-situ-Trennung zu Aufbereitung stark wässriger und biologischer Systeme einer Schlüsselrolle zugesprochen wird.
-
Die Frage nach künftigen Trennmethoden und ob Trennmaschinen an Bedeutung gewinnen wird, war eine weitere Thematik, mit der sich eingehend beschäftigt wurde. Dass die etablierten Trennverfahren nicht verschwinden werden, sondern ihre Bedeutung grundsätzlich bestehen bleibt, war schnell Konsens. Allerdings werden hybride Trennverfahren weitere Verbreitung finden und das Flexibilisierungspotenzial von Trennmaschinen muss verstärkt nutzbar gemacht werden, will man u. a. auf die volatilen Energiemärkte angemessen reagieren.
-
Die Frage nach den Herausforderungen der Bildung von Fachleuten stellte den dritten Themenschwerpunkt in diesem Cluster dar. Neben einer weiteren soliden Wissensbasis an Grundlagen wird die Vernetzung von Lern- und Wissensgebiet immer wichtiger werden, will man die komplexen Trennaufgaben der Zukunft meistern.
In diesem Symposion wurden auch abschließende Thesen erarbeitet, die in den weiteren Publikationen (Positionspapier, etc.) vorgestellt werden. Die Folgeaktivitäten dazu sollen in einem Temporären Arbeitskreis „Separation Units 4.0” koordiniert und fokussiert werden (1. Sitzung dazu war am 21.11.2019 bei der DECHEMA in Frankfurt).
Acknowledgements
An dieser Stelle sei ganz herzlich dem Organisationskomitee, insbesondere Dr.-Ing. Michael Häberl, Merck KGaA, und Dr. Thomas Runowski, Bayer AG, für den inhaltliche Input des Essays und Dr.-Ing. Sebastian Zeck, ehemals BASF, nun ProcessNet „Wanted Technologies” (http://wanted-technologies.de/), DECHEMA, gedankt, der das Komitee organisatorisch immer wieder in die korrekte zeitliche Spur gebracht hat. Natalie Fey und Nina Weingärtner von der DECHEMA haben sich um die lokale Organisation verdient gemacht und den Aufenthalt in Tutzing bei fast sommerlichem Spätherbstwetter zu einem Ereignis in bleibender Erinnerung gemacht.