Separation Units 4.0 – Trennapparate heute und morgen
Separation Units 4.0 – Perspectives on Fluid Separation Technologies
Abstract
deDie chemische Industrie sieht sich mit gravierenden Herausforderungen konfrontiert: Die Einhaltung der Klimaschutzziele, die Auswirkungen der Energiewende und die zunehmende Bedeutung der Kreislaufwirtschaft treffen die gesamte Wertschöpfungskette. Lösungsansätze von der Prozess- über die Apparateebene bis hin zum Einzelphänomen sind notwendig, um die Wettbewerbsfähigkeit dieses zentralen Industriezweigs zu erhalten. In diesem Beitrag werden aktuelle Entwicklungen und zukünftige Handlungsfelder in der Trenntechnik, die für diese Herausforderungen wertvolle Beiträge leisten können, dargestellt.
Abstract
enThe chemical industry will face serious challenges in the coming decade: compliance with climate protection targets, impacts from the “Energiewende”, and the increasing importance of circular economy affect the entire value chain. To maintain the competitiveness of this central industrial sector, innovative approaches are required, from the process level to the apparatus level and down to the scale of individual phenomena. This article presents current developments and future fields of action for separation units that can make valuable contributions to the named challenges.
1 Einleitung
Die chemische Industrie in Europa ist in der gerade begonnenen Dekade mit einer Vielzahl von Herausforderungen konfrontiert, die zwar nicht neu sind, in ihrer Wirkung jedoch immer drängender werden. Die im Jahr 2019 diskutierten und bereits 2020 politisch beschlossenen Maßnahmen zur Einhaltung der Ziele des Pariser Klimaschutzabkommens aus 2015 haben erhebliche Auswirkungen auf die chemische Industrie. Als zentrale Aspekte können die zur Erreichung der Ziele notwendige steigende Bedeutung erneuerbarer Energien, der festgelegte Korridor zur Steuerung der CO2-Zertifikatskosten und die notwendige Reduzierung des Primärenergieeinsatzes genannt werden. 1, 2 Dies bedeutet konkret, dass die chemische Industrie vor einer steigenden Elektrifizierung ihrer Prozesse steht, CO2 als Rohstoff eine größere Rolle einnimmt und die Energieeffizienz der Prozesse weiter verbessert werden muss. Werden die genannten Herausforderungen auf die Trenntechnik als wichtiger Bestandteil chemischer Prozesse projiziert, lassen sich weitere damit verknüpfte Herausforderungen ableiten. Mit steigenden Anteilen erneuerbarer Energien am Energiemix steigt die Fluktuation der zur Verfügung stehenden Energieströme. Wird der Betrieb chemischer Anlagen an diese fluktuierenden Energieströme angepasst, ist damit zu rechnen, dass auch die Stoffströme zunehmend volatil sind. Folglich sind Anlagen und Apparate mit erhöhter Flexibilität, also bspw. großen Betriebsbereichen, notwendig. Gleichzeitig ist eine Verringerung des Energieeinsatzes eine wichtige Voraussetzung für die Entwicklung neuer und die Verbesserung bestehender Verfahren. Dies kann bspw. durch den Einsatz alternativer Trennverfahren erreicht werden, die jedoch zum Teil noch ein enormes Entwicklungspotenzial aufweisen.
In Bezug auf das Bestreben, die Nachhaltigkeit chemischer Prozesse und Produkte zu erhöhen, spielt neben der Energie auch die Rohstoffbasis eine wichtige Rolle. Dabei steigt der Anteil biobasierter Produkte, die basierend auf nachwachsenden Rohstoffen hergestellt werden, stetig an 3a-5. Zudem haben geschlossene Wertstoffkreisläufe (Circular Economy) und das stoffliche Recycling bspw. von Polymeren eine zunehmende Bedeutung 6. Zur Umsetzung dieser Rohstoffe sind in der chemischen Industrie neue Prozesse und Technologien notwendig, denn trotz sinkender Vorhersagbarkeit der Spezifikationen dieser Eduktströme müssen gleichbleibend hohe Qualitäten des Endprodukts bei hoher Energieeffizienz der Umwandlungsschritte erreicht werden. Für die Trenntechnik, die in diesem Zusammenhang vor allem zur Aufarbeitung von Fermentations- bzw. Reaktionsprodukten eingesetzt wird, ergeben sich hier vor allem Herausforderungen bei der thermodynamischen Beschreibung der Stoffströme und der Auslegung von Apparaten auf Basis unsicherer Daten. Zudem ist es notwendig, trotz dieser Unsicherheiten den experimentellen Aufwand in der Prozessentwicklung gering zu halten.
Bei der Bewältigung der genannten Herausforderungen muss die chemische Industrie dennoch ihre Wettbewerbsfähigkeit erhalten bzw. einem steigenden Wettbewerbsdruck standhalten. Zudem erhöht sich die Nachfrage nach immer individuelleren und speziellen Produkten im Bereich der Fein- und Spezialchemie mit entsprechend kleinen Produktlebenszyklen, deren Absatzmengen immer schwieriger zu prognostizieren sind 7, 8. Folglich ist es notwendig, dass die Herstellung dieser neuen Produkte mit deutlich geringeren Planungs- und Entwicklungszeiten (Time-to-Market) für die benötigten Verfahrensschritte möglich ist. Dies ist u. a. durch die Implementierung der Ansätze aus der modularen Anlagentechnik in industriellen Produktionsumgebungen möglich. Aus Sicht der Trenntechnik bestehen in diesem Zusammenhang u. a. die Aufgaben, standardisiertes und skalierbares Equipment zur Verfügung zu stellen und die Entwicklung neuer Verfahren aus dem Labor- in den Produktionsmaßstab zu beschleunigen.
Abschließend ist die Digitalisierung zu nennen, die für alle genannten Herausforderungen als Querschnittsaufgabe relevant ist. Die Möglichkeiten der Digitalisierung können auf allen Skalen zu neuen Innovationen und Entwicklungen führen. Genannt seien an dieser Stelle exemplarisch die Digitalisierung des gesamten Anlagenlebenszyklus mit sog. Digitalen Zwillingen zu Planungs- und Maintenancezwecken auf Prozessebene, die Verwendung der additiven Fertigung zur Herstellung von Equipment auf Apparateebene oder die Auswertung von Messdaten durch Methoden der Künstlichen Intelligenz (artificial intelligence, AI) oder des Machine Learnings (ML) zum besseren Verständnis der ablaufenden Phänomene.
Folglich war es Ziel des Tutzing-Symposiums 2019 Separation Units 4.0, die Möglichkeiten der Digitalisierung für die Trenntechnik zu identifizieren sowie Chancen und Risiken zu benennen. Dazu wird im Rahmen dieses Artikels eine Übersicht einerseits über die derzeit diskutierten Innovationen und Methoden zum Umgang mit den geschilderten Herausforderungen und andererseits ein Ausblick auf zukünftige Handlungsfelder gegeben.
2 Forschung und Entwicklung im Bereich der Trenntechnik heute
Fragt man nach den aktuellen Handlungsfeldern für Forschungs- und Entwicklungsarbeiten in der Trenntechnik, dann wird wohl die Mehrzahl der Antwortenden den Bereich der Biotechnologie nennen. Nicht zuletzt der letzte Zukunftsworkshop der ProcessNet in Wieslich im Herbst 2019 hatte die Biologisierung der Prozesse zu einem der Hauptthemen ausgemacht. Darüber hinaus rückt die Wiedergewinnung bzw. Kreislaufführung von Wertstoffen, insb. aber die Aufarbeitung von kritischen bzw. strategischen Metallen in den Fokus der Trenntechnik. Inflationär auftretende Stichworte wie Circular Economy oder Urban Mining sind nur zwei Indizien hierfür. Diese sich wandelnden Rohstoffquellen, insb. die Bedeutung nachwachsender Rohstoffe, werden zukünftig neue Prozesse und auch neue Prozessführungskonzepte notwendig machen. Durch die Notwendigkeit der Aufarbeitung der Reaktionsprodukte wird sich dies auch in neuen Anforderungen an die Trenntechnik niederschlagen.
-
verbesserte Selektivität von Trennverfahren
-
Aufreinigung verdünnter Lösungen
-
gezielte Beeinflussung bzw. Steuerung der Phasengrenzfläche
-
intensivierte Stoffaustauschprozesse
-
Kombination von Trennverfahren und nicht zuletzt
-
Erhöhung der Energieeffizienz
Dennoch stellt diese Aufstellung eine direkte Übersetzung der Sessiontitel der internationalen Tagung Distillation & Absorption aus dem Jahre 1987 dar. Demnach lässt sich aus Sicht der Autoren klar ableiten, dass sich für die Trenntechnik zwar die Handlungsfelder geändert haben, die Fragestellungen der Forschung und Entwicklung aber letztlich immer noch dieselben sind.
Im Rahmen des Tutzing-Symposions 2019 ist dieser scheinbare Stillstand in den Forschungsthemen intensiv diskutiert worden. Dabei stimmten die Teilnehmer überein, dass sich auf den genannten Forschungsfeldern die Aufgabenverteilung zwischen Industrie und Hochschule, aber auch zwischen Betreiberunternehmen und Apparate- bzw. Equipmentherstellern in den letzten Jahren verändert hat bzw. sich zukünftig signifikant verändern wird. Demnach wird es insofern zu einer Verschiebung der Kompetenzen kommen, dass die Zulieferer der Großindustrie zunehmend Aufgaben der Betreiberfirmen übernehmen werden. Dies wird zwangsläufig zu neuen Arbeitsteilungen, aber auch einer neu zu organisierenden Wissensteilung zum jeweiligen Prozess führen müssen. Ein solcher Veränderungsprozess wird sich nur auf einer stabilen Basis einer vertrauensvollen Zusammenarbeit realisieren lassen.
Ein Ansatzpunkt hierzu sind z. B. die von der ProcessNet-Fachgruppe Fluidverfahrenstechnik jenseits der jährlichen Fachtagungen angestoßene Initiative „Wanted Technologies” und das zugehörige Arbeitstreffen „Effiziente Phasenführung in Kolonnen (EPHA)”. In ungefähr halbjährlichem Rhythmus treffen sich die Fachexperten der Industrieunternehmen, Zulieferindustrie und der Hochschulen zu vorab definierten Fachthemen, um gemeinsame Forschungsprojekte zu definieren und auf den Weg zu bringen. Erfolgreich eingeworbene Projekte, wie die Standardisierung von Experimenten zur Packungscharakterisierung, Standardisierung von Messverfahren zur Charakterisierung von Membranen, die Analyse von Tropfenmitriss in Kolonnen und die Aufklärung von Schäumungsprozessen in Kolonnen, sind nur einige Beispiele für eine zukunftsweisende Zusammenarbeit aller Beteiligten.
3 Innovationen im Bereich Trenntechnik
Einige der zuvor genannten Themenfelder werden in aktuellen Forschungsarbeiten bereits adressiert. Daher werden in diesem Kapitel zunächst die bereits in der Literatur beschriebenen Lösungsansätze für die zukünftigen Herausforderungen dargestellt. Dazu werden die Ebenen Prozess, Apparat und Phänomen betrachtet und exemplarische Themenfelder herausgegriffen. Es gibt sicherlich noch eine Reihe weiterer Themenfelder, die im Zusammenhang mit den dargestellten Handlungsfeldern wichtige Beiträge leisten können, hier jedoch nicht weiter aufgegriffen werden können.
3.1 Anlagen- und Prozessebene
Für die Anlagen- und Prozessebene spielte in der letzten Dekade vor allem die modulare Anlagentechnik zur Erhöhung der Wandlungsfähigkeit und Flexibilität sowie zur Verkürzung von Planungs- und Entwicklungszeiten eine wichtige Rolle. Gleichzeitig folgt aus dem Ansatz modularer Anlagen die Anforderung, dass Informationen, die u. a. für Planung und Entwicklung relevant sind, über den gesamten Lebenszyklus verfügbar sein müssen. Dies ist vor allem dann entscheidend, wenn vorhandenes Equipment durch Rekonfiguration in neuen Prozessen eingesetzt wird. Im Weiteren werden Lösungsansätze für diese beiden Aspekte diskutiert.
3.1.1 Modulare Anlagen
Die Idee der modularen Anlage hat spätestens seit dem Tutzing-Symposium 2009 Einzug in die chemische Industrie gehalten. Das Prozessdesign mittels einfach skalierbarer, wiederverwendbarer und universell einsetzbarer Module kann maßgeblich zur Reduzierung der Time-to-Market bei der Entwicklung neuer Produkte beitragen 9, 10. Mit dem Themenheft „Die 50%-Idee: vom Produkt zur Produktionsanlage in der halben Zeit” der Chemie Ingenieur Technik aus dem Jahr 2012 wurde die Vision für die verschiedenen Aspekte aus Prozessentwicklung und Anlagenbetrieb erstmals breit beschrieben. Im Jahr 2015 wurden die verschiedenen Aspekte im Themenheft „Neue Produktionskonzepte” erneut aufgegriffen und deren Weiterentwicklung dargestellt. Auch der wirtschaftliche Vorteil modularer Anlagen wurde in verschiedenen Arbeiten hervorgehoben 11-13.
Erkennbar ist, dass der Begriff „modular” zunehmend divers verwendet wird und sich zwischen den Definitionen, die in Forschung und Entwicklung verwendet werden 14 und den Definitionen und Sichtweisen der Industrie 15 Diskrepanzen ergeben. Die Definitionen reichen dabei von kleinskaligen Containeranlagen bis hin zu sog. skid-mounted Anlagen, die vor allem für einen einfachen Transport und eine schnelle Montage modular aufgebaut sind. Es ist davon auszugehen, dass kleinskalige modulare Anlagen vor allem in Labor- und Technikumsumgebungen und für die Herstellung kleiner Chargen hochreiner Produkte bspw. für die pharmazeutische Industrie erfolgreich eingesetzt werden. Unter diesen Randbedingungen ermöglichen die hohe Flexibilität bzw. die schnelle Rekonfigurierbarkeit in Kombination mit einer kontinuierlichen Produktion wirtschaftliche Vorteile in Bezug auf Neuentwicklungen und Betrieb.
Für kontinuierliche Weiterentwicklungen auf dem Gebiet der modularen Anlagen ist es notwendig, modulare und skalierbare Apparate zu entwickeln 16, 17 und die Logistikprozesse bzw. die Supply Chain den neuen Produktionsbedingungen anzupassen 10, 18. Zudem fokussieren sich aktuelle Forschungsarbeiten auf den Planungsprozess für die Konzipierung modularer Anlagen 19, 20 sowie auf die Netzwerk- und Logistikplanung für modulare Anlagen 21, 22.
3.1.2 Intelligente Anlagen
In verschiedenen Publikationen wird verdeutlicht, dass eine weitere Reduzierung der Entwicklungszeiten durch eine Vernetzung von Daten und Tools über den gesamten Anlagenlebenszyklus hinweg zu erwarten ist 23-25. Wenn Engineering und Betrieb der Produktionsanlagen durch einen höheren Austausch von Daten über alle Phasen gekennzeichnet sind, kann von einer vernetzten Anlage gesprochen werden. Dies bedeutet allerdings für die Zukunft enorme Anstrengungen hinsichtlich des Zusammenspiels der Tools und Datentypen über den gesamten Lebenszyklus hinweg.
Fillinger et al. 23 nennen als Voraussetzungen für eine Datenintegration über den Anlagenlebenszyklus drei wesentliche Punkte: Die Daten müssen einheitlich benannt und definiert werden, Daten müssen rückverfolgbar für alle beteiligten Disziplinen sein und Veränderungen in den Daten müssen in Form eines ganzheitlichen Änderungsmanagements möglich und nachvollziehbar sein. Kim et al. 26 nennen zusätzlich die Voraussetzung, dass Datendarstellung und -integration unabhängig von Software und Hersteller sein müssen. Zusätzlich spielen die folgenden Aspekte eine Rolle: Konsistenz, kontinuierliche Synchronisation, Fehlervermeidung und die Vermeidung vom Speichern redundanter Daten 27. Für diese Herausforderungen gibt es schon einige Lösungen 23, 26-28, die sich drei verschiedenen Ansätzen zuteilen lassen: Entwicklung eines Datenformats, das alle Daten der verschiedenen Tools verarbeiten kann, Nutzung eines übergeordneten Programms, das alle notwendigen Informationen speichert und weitergeben kann, sowie, mit dem geringsten Integrationsgrad, unabhängige Programme, deren Datenformate kompatibel gemacht werden.
Zusätzlich sind im Zusammenhang mit modularen Anlagen die Bestrebungen zur Standardisierung von Schnittstellen im Bereich der Automatisierungstechnik zu nennen, um die Vision des Plug-and-Produce realisierbar zu machen. Einen aktuellen Überblick zu den dahingehenden Aktivitäten und Herausforderungen geben Bernshausen und Hoernicke 29.
Ein entscheidender Schritt von der vernetzten zur intelligenten Anlage besteht in der zusätzlichen Integration eines Frameworks zur Datenauswertung. Dies ist notwendig, um mittels geeigneter Algorithmen eine Mustererkennung im Betrieb zu ermöglichen. Die intelligente Anlage ist dann in der Lage, basierend auf den erkannten Mustern, autonom Betriebsparameter anzupassen, um permanent am optimalen Punkt zu arbeiten.
3.2 Apparateebene
Für die Apparateebene werden die Themenfelder Flexibilität verfahrenstechnischer Reaktions- und Trennapparate, rotierende Apparate als alternative Trennverfahren und die Möglichkeiten zum Einsatz additiver Fertigungsverfahren in Apparaten der thermischen Verfahrenstechnik herausgegriffen und aktuelle Arbeiten aus den Themenfeldern diskutiert.
3.2.1 Flexible Apparate
In der Literatur sind bereits einige Ansätze beschrieben, um die Flexibilität verfahrenstechnischer Apparate zu erhöhen. Dies kann vor allem durch die steigende Fluktuation von Angebot, z. B. an Energie oder Rohstoffen, sowie Nachfrage seitens der Kunden eine entscheidende Rolle spielen. Dabei ist der Begriff Flexibilität in der Verfahrenstechnik nicht einheitlich definiert. Vielfach geht es in den Arbeiten allerdings darum, einen möglichst breiten Betriebsbereich abzudecken. Dies kann sich bspw. auf den Durchsatz 30 oder die Variation der Feedzusammensetzung 31, 32 beziehen. Erreicht wird die Erhöhung der Flexibilität durch verschiedene Maßnahmen, die im Folgenden exemplarisch dargestellt werden.
Neben der Modularisierung von Trennapparaten, die anschließend mittels Numbering-up auf den gewünschten Durchsatz skaliert werden können 33, werden in der Literatur auch andere konstruktive Maßnahmen beschrieben, um die Flexibilität auch großskaliger Trennapparate zu erhöhen. Dazu nennen Riese und Grünewald 30 die Segmentierung von Trennkolonnen zur Erhöhung der Durchsatzvariation. Ein ähnlicher Ansatz wird für die Erhöhung der Flexibilität von Festbettreaktoren für Power-to-Gas-Anwendungen beschrieben 34. Für beide Apparate führt die Segmentierung zu einem breiteren Betriebsbereich, wobei vor allem die Grenzen hin zu geringeren Durchsätzen aufgebrochen werden. Im Gegensatz dazu wird von Staak et al. 32 eine Trennwandkolonne beschrieben, die durch veränderliche Höhen von Feedzulauf und Seitenabzug die Trennung verschiedener Gemische ermöglicht. Diese Kolonne ist für den Einsatz in Mehrproduktanlagen vorgesehen, die sich durch häufigen Produktwechsel auszeichnen. Somit führen die genannten konstruktiven Freiheitsgrade zu einer schnelleren Anpassung an eine neue Trennaufgabe.
Alternativ zu konstruktiven Maßnahmen an konventionellen Apparaten schlagen Maußner et al. 31 ein optimierungsbasiertes Verfahren zum Design von toleranten Reaktoren vor. Für diesen Fall kann tolerant als flexibel in Bezug auf variierende Feedzusammensetzungen interpretiert werden. Das Verfahren basiert auf dem Konzept der EPFs (elementary process functions) 35 zur Synthese optimaler Reaktorkonfigurationen. Zum Design optimaler Reaktoren für tolerante Prozesse wird das Verfahren dahingehend erweitert, dass die EPFs nicht nur für einen fixen Feed optimiert werden, sondern parallel für eine definierte Variation der Feedzusammensetzung. So wird das optimale Reaktordesign zur Erreichung definierter Produktspezifikationen nicht nur für einen vordefinierten Feed, sondern für variierende Feedzusammensetzungen gefunden. Am Beispiel der Herstellung von Maleinsäureanhydrid aus einem Butan/Buten-Gemisch wird gezeigt, dass der optimale Reaktor für einen toleranten Prozess anders aussieht als der optimale Reaktor zur Erreichung der absolut besten Selektivität in der Reaktion.
Zur Vergrößerung des Betriebsbereichs eines Festbettreaktors schlagen Bremer und Sundmacher 36 eine verbesserte Temperaturregelung vor. Am Beispiel der CO2-Methanisierung für Power-to-Gas-Anwendungen wird gezeigt, dass angepasste Regelstrategien zu einer verbesserten Stabilität des Reaktorverhaltens im dynamischen Betrieb führen.
Eine weitere Möglichkeit zur Erhöhung der Flexibilität besteht in der Integration mehrerer Funktionalitäten in einen Prozess oder Apparat. Am Beispiel der membrangestützten Chlor-Alkali-Elektrolyse beschreiben Brée et al. 37 bzw. Roh et al. 38 diesen Ansatz. Es wird ein Konzept vorgeschlagen, bei dem zwischen zwei verschiedenen Betriebsmodi gewechselt werden kann. Ziel ist es, den Betrieb angepasst an variierende Strompreise möglichst gesamtkostenoptimiert zu gestalten. Dazu wird bei geringen Strompreisen eine Standardkathode verwendet, wodurch bei vergleichsweise hohen spezifischen Energieverbräuchen gleichzeitig Wasserstoff erzeugt wird. Im Vergleich dazu wird bei hohen Strompreisen die Elektrolyse mithilfe einer Sauerstoffverzehrkathode und einem ca. 30 % geringeren Energiebedarf durchgeführt. Es wird angenommen, dass bei der Verwendung einer bifunktionalen Elektrode nach einem Reinigungszyklus zwischen diesen beiden Modi gewechselt werden kann. Ein ähnliches Vorgehen schlagen Caspari et al. 39, 40 für Luftzerlegungsanlagen vor, die ebenfalls in Abhängigkeit des Strompreises in verschiedenen Modi betrieben werden können.
3.2.2 Rotierende Apparate für die thermische Verfahrenstechnik
Im Bereich der thermischen Trennverfahren spielen als rotierende Apparate vor allem die sog. RPBs (rotating packed beds) eine Rolle. Durch den Betrieb im Zentrifugalfeld bei dem 100- bis 1000-Fachen der Erdbeschleunigung zeichnen sich RPBs im Vergleich zu konventionellen Packungskolonnen durch höhere volumetrische Stofftransportkoeffizienten sowie einen intensivierten Impuls- und Wärmeaustausch aus. Dies ist auf die geringeren Filmdicken und kleineren Flüssigkeitstropfen zurückzuführen, die in größeren spezifischen Phasengrenzflächen resultieren. Dadurch kann es zu einer Verringerung des benötigten Apparatevolumens bis zu einem Faktor 10 kommen. Nachteilig sind die höheren Druckverluste im Vergleich zu konventionellen Packungen sowie die Notwendigkeit rotierender Teile zur Erzeugung der benötigten Zentrifugalkräfte. 41 Die konstruktive Ausgestaltung sowie die Möglichkeiten der Phasenkontaktierung sind dabei vielfältig. Cortes Garcia et al. 41 geben einen Überblick über die verschiedenen Bauweisen und Anwendungsmöglichkeiten in der thermischen Verfahrenstechnik, die in der Literatur beschrieben werden. Die Übersicht zeigt auch, dass die Anwendung der RPBs in der Industrie bisher noch nicht so verbreitet ist wie konventionelle Kolonnen und sowohl die Anwendungen als auch die Hersteller auf China und die USA beschränkt sind. Für einen breiten Einsatz in der chemischen Industrie fehlt es neben konkreten Betriebserfahrungen zudem noch an validierten Auslegungsgrundlagen und Regeln für das Scale-up 42. Verschiedene Arbeiten beschäftigen sich daher mit der systematischen Charakterisierung von RPBs.
Neumann et al. 42 führen Untersuchungen zur oberen Betriebsgrenze von RPBs durch. Die Kenntnisse der Betriebsgrenze ist eine zentrale Voraussetzung zur ganzheitlichen Untersuchung der Stofftransportperformance. Kriterium zur Identifikation der oberen Betriebsgrenze ist das Entrainment von Flüssigkeit am Gasaustrittsstutzen. Die Ergebnisse zeigen, dass insb. die initiale Flüssigkeitsgeschwindigkeit und die initiale Flüssigkeitsverteilung einen Einfluss auf die Betriebsgrenze haben. Die initiale Flüssigkeitsverteilung wird dabei mittels verschiedener Eintrittsdüsen manipuliert.
Auch in der Arbeit von Wenzel et al. 43 spielt die Eintrittsverteilung der Flüssigkeit eine entscheidende Rolle. In dieser Arbeit werden die Flüssigkeitsverteilung und die Mikrovermischung von zwei im Gleichstrom geführten Flüssigkeiten in RPBs detaillierter untersucht. Neben dem Düsentyp werden auch der Verteilungswinkel und die Düsenanordnung untersucht. Ziel ist ein Vergleich der Mischgüte mit anderen statischen Mischern. Die Ergebnisse zeigen, dass RPBs eine gute Mischcharakteristik bei geringen Druckverlusten und gleichzeitig hohen Flüssigkeitsbelastungen haben. Für den Fall der gleichgerichteten Flüssigkeitsströmung hat die initiale Flüssigkeitsverteilung einen geringeren Einfluss auf die Hydrodynamik als in der zuvor beschriebenen Arbeit, in der die Hydrodynamik eines Gas/Flüssig-Gegenstroms untersucht wurde. Das zeigt, dass je nach Anwendung unterschiedliche Aspekte eine Rolle spielen.
Neumann et al. 44 schlagen einen entscheidungsbaumbasierten Leitfaden zur Auswahl von RPBs für Gas/Flüssig-, Dampf/Flüssig- sowie Flüssig/Flüssig-Strömungen vor, um diese unterschiedlichen Aspekte im Sinne einer Technologieauswahl einordnen zu können. Ziel dieser Systematisierung ist es, die Auswahl des RPB im Prozessdesign zu unterstützen.
3.2.3 Smart Design für thermische Trennverfahren
Die additive Fertigung und das Rapid Prototyping spielen auf verschiedene Arten zunehmend eine wichtige Rolle bei der Entwicklung neuer Lösungsansätze in der Verfahrenstechnik. Dies ist vielfach durch die zusätzlichen Freiheitsgrade im Design von Werkstücken, die im Vergleich zu konventionellen Fertigungsverfahren in der additiven Fertigung zur Verfügung stehen, begründet. Gleichzeitig spielen auch zeitliche Faktoren eine Rolle, vor allem wenn es darum geht, eine erste schnelle Charakterisierung neuer Ansätze durchzuführen.
In Bezug auf die thermische Verfahrenstechnik gibt es verschiedene Ansätze zum Design von trennwirksamen Einbauten mittels additiver Fertigung. Dabei geht es vornehmlich darum, die bereits beschriebenen zusätzlichen Freiheitsgrade im Design auszunutzen. Die in diesem Zusammenhang relevanten Arbeiten lassen sich hinsichtlich der Apparate, in denen sie eingesetzt werden, klassifizieren. Einerseits werden trennwirksame Einbauten für konventionelle Kolonnen entwickelt und untersucht 45, 46, andererseits werden maßgeschneiderte Lösungen für die zuvor bereits diskutierten rotierenden Stoffaustauschapparate entwickelt 47, 48.
Für die konventionellen Kolonnen werden bspw. Einbauten basierend auf unterschiedlichen Elementarzellen entworfen 45. Bevor diese Einbauten gefertigt werden, werden Druckverlust, Flüssigkeitsholdup und Verteileigenschaften mittels CFD-Simulationen charakterisiert und die Elementarzellen je nach Ergebnis hinsichtlich ihrer geometrischen Eigenschaften optimiert. So wird sichergestellt, dass ausschließlich die vielversprechendsten Geometrien tatsächlich gefertigt und experimentell untersucht werden.
In RPBs gibt es einerseits Untersuchungen zum Einsatz additiv gefertigter Einbauten klassischer Geometrie, z. B. einer mittels Polymerwerkstoff nachgebildeten Metallpackung 47, und andererseits Arbeiten zur Charakterisierung neuartiger, additiv gefertigter Geometrien, wie bspw. sogenannte Zickzack-Packungen 48. Letztere sollen die Vorteile der eher bodenähnlichen RZBs (rotating zigzag beds) mit den Vorteilen konventioneller Packungen für die Anwendung in der Rektifikation kombinieren. So ergibt sich eine Vielzahl von Designgrößen, die mittels additiver Fertigung vergleichsweise einfach in einem Werkstück hergestellt werden können. Ergebnisse experimenteller Destillationsversuche zeigen, dass die Stofftransportperformance der neuentwickelten Packung vergleichbar mit anderen RZBs ist, dabei jedoch ein signifikant geringerer Druckverlust vorliegt.
Neben der Entwicklung von trennwirksamen Einbauten mittels additiver Fertigung wird diese Technologie auch verwendet, um maßgeschneiderte Strukturierungsinstrumente für Mehrphasenströmungen bspw. für Blasensäulen 49 oder Rieselbettreaktoren 50 zu entwickeln. In diesem Zusammenhang spielen insb. sog. periodisch-offenzellige Strukturen (peridic open cell structures, POCS) eine Rolle. Ziel dieser Strukturierung des Reaktionsraums ist es, die in der Mehrphasenströmung auf verschiedenen Skalen und in den Phasen vorkommenden Phänomene zu entkoppeln, um die Effizienz der Reaktionen zu erhöhen. Zentral sind dabei die Sicherstellung einer einheitlichen Blasengrößenverteilung sowie die Verringerung der Rückvermischung mit dem Ziel, eine einheitliche Verweilzeitverteilung der Flüssigphase sicherzustellen. Erste systematische Untersuchungen zum Einsatz in einer Blasensäule zeigen dabei, dass es zu einer Homogenisierung beider genannten Größen kommen kann, wodurch insgesamt positive Effekte zu erwarten sind 49. Weiterführende Untersuchungen zum Potenzial additiv gefertigter Strukturen in Mehrphasenströmungen müssen diese Beobachtungen zusätzlich untermauern.
Noch weitergehend ist der Einsatz additiver Fertigungsmethoden zur direkten Herstellung ganzer Apparate. Dies wird von Mardani et al. 51 für den direkten Druck einer modularen Destillationskolonne vorgeschlagen. Neben dem Apparat, einer gewundenen Kolonne mit einer Gesamthöhe von 15 cm, und den benötigten Anschlüssen für die ein- und austretenden Ströme werden auch die trennwirksamen Einbauten für einige Untersuchungen direkt mitgedruckt. Ziel der Arbeit ist es, die Machbarkeit von CAD-Design über die additive Fertigung bis hin zur experimentellen Charakterisierung für neue Designansätze zu untersuchen. Einen ähnlichen Ansatz verfolgen Fee et al. 52 für die Herstellung kleinskaliger Chromatographiesäulen mittels additiver Fertigung. Die Autoren haben dazu verschiedene Bettkonfigurationen sowie Verteilkonzepte mithilfe von CAD-Methoden entworfen und durch Stereolithograhie hergestellt. Anschließend wird die Güte der verschiedenen Strukturen und Verteilkonzepte mithilfe von Verweilzeituntersuchungen quantifiziert, wobei ein enormes Potenzial der durch die additive Fertigung zur Verfügung stehenden Freiheitsgrade im Bereich Chromatographie festgestellt wird. Ähnliches stellen Han et al. 53 für den Bereich Wärmeübertragung fest. In ihrer Arbeit untersuchen sie die Anwendung polymerbasierter Wärmeübertrager. Dabei wird der Verlust der Wärmeübertragungsleistung bedingt durch den Werkstoffwechsel von Aluminium zu Polymer mittels Geometrieoptimierung ausgeglichen.
3.3 Phänomenologische Ebene
Zusätzlich zu den bereits diskutierten, designgebundenen Ebenen Anlage und Apparat ist es für eine weitere Verbesserung der Verfahren auch notwendig, auf der phänomenologischen Ebene neue Informationen und ein tiefergehendes Verständnis zu entwickeln. Vor diesem Hintergrund werden im Folgenden zwei zentrale Aspekte, der Umgang mit unsicheren Stoffdaten sowie die Anwendung neuer Messmethoden in der Fluidverfahrenstechnik, diskutiert.
3.3.1 Methoden zum Umgang mit unsicheren Stoffdaten
Neben abgesicherten Modellen spielt für die Auslegung von verfahrenstechnischen Apparaten und Prozessen auch eine breite Basis an genauen Stoffdaten eine wichtige Rolle. Für bestimmte Substanzklassen fehlen jedoch teilweise genaue Stoffdatenmodelle. Dies gilt unter anderem für Biomoleküle, die im Zuge der eingangs diskutierten Herausforderungen für die chemische Industrie jedoch in Zukunft eine immer wichtigere Rolle spielen werden. Folglich ist es notwendig, Stoffdatenmodelle für diese Substanzklassen zu entwickeln und zu validieren.
Bioprozesse zeichnen sich zudem dadurch aus, dass viele nicht spezifizierte oder spezifizierbare Stoffe verarbeitet werden müssen. Die Zusammensetzung der Stoffströme ist also nicht immer vollständig bekannt, was eine zusätzliche Herausforderung darstellt. Folglich sind Methoden notwendig, die eine sichere Auslegung von Equipment auch in schlecht spezifizierten Gemischen möglich machen.
Für diese Problemstellung schlagen bspw. Jirasek et al. 54, 55 eine neue Methode zur Bestimmung der Aktivitätskoeffizienten von Zielkomponenten in schlecht spezifizierten Gemischen vor. Im Gegensatz zu bisherigen Arbeiten auf diesem Gebiet, bei denen mit der Beschreibung des Gemischverhaltens ausschließlich über Pseudo-Komponenten gearbeitet wurde 56, wird dieser Ansatz von Jirasek et al. 54, 55 basierend auf Gruppenbeitragsmethoden (z. B. UNIFAC oder COSMO-RS) erweitert. Das Vorgehen basiert auf der Annahme, dass sich in dem Gemisch einerseits Komponenten befinden, die als Stoff und Konzentration bekannt sind und andererseits besteht das Gemisch aus einer Reihe unbekannter Komponenten. Die Informationen für erstere Komponenten können dazu bspw. mittels NMR-Spektroskopie gewonnen werden.
Ein alternatives Vorgehen wird von Baumeister und Burger 57 vorgeschlagen. Hier werden schlecht spezifizierte Mischungen ausgehend von gE-Modellen oder Zustandsgleichungen berechnet. Diese werden für die bekannten Komponenten verwendet und um einen zusätzlichen Term erweitert, der die Auswirkungen der unbekannten Komponenten beschreibt. Dieses Vorgehen wird in anderen Arbeiten ebenfalls genutzt, um mit Unsicherheiten von Stoffdatenmodellen in Prozesssimulationstools umzugehen 58, 59.
3.3.2 Neue Messmethoden
Ziel des Einsatzes innovativer Messtechniken ist ein tiefergehendes Verständnis der komplexen Vorgänge innerhalb der verfahrenstechnischen Apparate und darauf aufbauend die Entwicklung neuer oder verbesserter Modelle, um Unsicherheiten in der Auslegung und im Scale-up der Apparate zu minimieren. Beispielhaft werden im Weiteren die Möglichkeiten zur Untersuchung von verfahrenstechnischen Apparaten mittels tomographischer Verfahren, Gittersensoren und faseroptischer Temperaturprofilmessung diskutiert.
Der Vorteil tomographischer Verfahren besteht darin, dass ein großer Messbereich räumlich und zeitlich aufgelöst ohne Eingriff in den Prozess erfasst werden kann. Gleichzeitig handelt es sich um ein aufwendiges Messverfahren und die gewonnenen Informationen müssen zum Teil aufwendig zu entsprechenden Bildern rekonstruiert werden. In der Forschung werden tomographische Messverfahren jedoch schon seit einiger Zeit eingesetzt, u. a. zur Untersuchung der Strömungsmuster in Mehrphasenapparaten. Dahingehend wurde bereits eine Vielzahl unterschiedlicher verfahrenstechnischer Anwendungen untersucht, u. a. die Gas/Flüssig-Strömung in Packungen 60-62, in RPBs 63 und in Schaumstrukturen 64 oder die Eigenschaften der Flüssig/Flüssig-Durchmischung in Extraktionsapparaten 65.
Eine Alternative zu tomographischen Verfahren stellt der Gittersensor dar. Mithilfe eines Gittersensors können ebenfalls örtlich und zeitlich aufgelöst Mehrphasenströmungen untersucht werden. Allerdings wird bei dieser Messtechnik geringinvasiv in die Strömung eingegriffen. Die Auswertung der gewonnenen Daten stellt sich jedoch zum Teil etwas einfacher dar als bei den tomographischen Verfahren. Folglich wurde auch mithilfe von Gittersensoren bereits eine Vielzahl verfahrenstechnischer Anwendungen untersucht. Dazu gehören u. a. Packungskolonnen 66 und Bodenkolonnen 67 sowie Blasenströmungen z. B. in Blasensäulen 68, 69, gepackte Blasensäulen 70, 71 oder Rieselbettreaktoren 72.
Während in Mehrphasenapparaten die Eigenschaften der Strömung wie bspw. Phasenanteile, Blasengrößenverteilungen oder Strömungsgeschwindigkeiten von besonderem Interesse sind, spielen in heterogen katalysierten Gasphasenreaktionen die Temperaturprofile eine besondere Rolle. Die örtlich und zeitlich aufgelöste Messung von Temperaturprofilen ist durch faseroptische Messtechnik möglich. Stegehake und Grünewald 73 bzw. Stegehake et al. 74 setzen diese Messtechnik bspw. dafür ein, die Wärmetransportphänomene in Festbettreaktoren detaillierter aufzuklären.
Wenn auch nur ausschnittsweise diskutiert, zeigen die Beispiele dennoch, dass durch den Einsatz neuer Messmethoden neue und zusätzliche Informationen zur Aufklärung verfahrenstechnischer Apparate erlangt werden können. Diese Informationen können anschließend dazu verwendet werden, Modelle zu validieren oder zu parametrieren 74-76.
4 Zukünftige Handlungsfelder
Wie im vorangegangenen Kapitel dargestellt, gibt es bereits eine Reihe von Innovationen und Entwicklungen, um den eingangs dargestellten Herausforderungen begegnen zu können. Nichtsdestotrotz gibt es, vor allem getrieben durch die Möglichkeiten der Digitalisierung, verschiedene Handlungsfelder, in denen wichtige zukünftige Entwicklungen für die chemische Industrie angestoßen und vorangetrieben werden können. Im Rahmen des Tutzing-Symposiums 2019 wurden verschiedene dieser Handlungsfelder diskutiert und mit Leben gefüllt. Die wesentlichen Ergebnisse werden im weiteren Verlauf dargestellt und diskutiert.
4.1 Neue Planungsmethoden
Neue Planungsmethoden beziehen sich vornehmlich auf die Entwicklung und Umsetzung neuartiger Prozesse. Im Weiteren werden die Methoden auf die zuvor genannten Herausforderungen für die chemische Industrie projiziert und die entsprechenden zukünftigen Forschungsfragen abgeleitet. Eine Übersicht der verschiedenen, in diesem Bereich laufenden oder bewilligten öffentlich geförderten Projekte in Deutschland, kann 77 entnommen werden.
In Bezug auf die Energiewende ist es einerseits notwendig, durch neue Verfahren und Materialien eine Elektrifizierung der Prozesse zu ermöglichen, andererseits müssen bestehende Verfahren an die neuen Randbedingungen des Energiesystems angepasst werden. Vor allem Letzteres bedarf neuer Betriebskonzepte mit einer zeitlich optimierten und optimal synchronisierten Stromabnahme. Derartige Methoden werden u. a. in den Kopernikus-Projekten „Power-to-X” und „SynErgie” und im BMWi-Projekt „EnEImi2.0” entwickelt. 78, 79 Die Erhöhung der Energieeffizienz kann erreicht werden, indem die Prozesse durch neue Regelmethoden kontinuierlich hinsichtlich ihrer Energieeffizienz optimiert werden. Dazu ist allerdings auch eine permanente Überwachung der entsprechenden Parameter in den Anlagen notwendig. Ein hierfür geeignetes Framework wird im BMWi-Projekt „EnEffReg” erstmals entwickelt und getestet 80.
-
Wie können die Automatisierung, Genehmigung und Inbetriebnahme modularer Anlagen aussehen? Ein möglicher Ansatz zur Lösung dieser Frage wird von Klose et al. Vorgestellt 81.
-
Wie können die Auswahl und optimale Interaktion der Module aus einem definierten Modulbaukasten aussehen?
-
Wie können neuartige Apparatetechnologien in frühen Phasen der Prozessentwicklung berücksichtigt werden? Dazu schlagen Bramsiepe et al. 82 ein neuartiges Framework für die Prozessentwicklung in der Fein- und Spezialchemie vor.
-
Wie können Informationen über den gesamten Lebenszyklus von Modul und modularer Anlage für den Plug-and-Produce-Ansatz verfügbar gemacht werden?
-
Wie können passende modulare Lösungen für die Produktionslogistik aussehen und welche Schnittstellen sind im Sinne eines ganzheitlichen Logistikkonzepts relevant?
Diese Handlungsfelder, die vor allem verschiedene Formen der Schnittstellen betreffen, werden auch zukünftig eine zentrale Rolle für die Implementierung modularer Anlagen in der chemischen Industrie spielen.
4.2 Additive Fertigungsmethoden
Die kontinuierliche Weiterentwicklung der additiven Fertigungsmethoden eröffnet, neben den in Sect. 3.2.3 dargestellten, bereits existierenden Ansätzen, neue Handlungsfelder für das Design von thermischen Trennapparaten. Die Freiheitsgrade der additiven Fertigung ermöglichen die Entwicklung vollkommen neuer Strukturen für eine definierte Phasenführung in Trennapparaten und deren direkte Designoptimierung mittels CFD-Simulationen. Ziel kann es bspw. sein, gezielt Rückvermischungseffekte zu verringern und den Stofftransport zu verbessern. Auch für das Design trennwirksamer Einbauten ist die Entwicklung vollkommen neuer Geometrien möglich, z. B. zur Reduzierung der Fehlverteilung in Kolonnen. Zudem erlaubt die additive Fertigung die direkte Integration von Sensoren in die Struktur bzw. den Apparat. So eröffnet sich das Potenzial, die Sensoren sehr viel gezielter und an Orten zu platzieren, die in konventionell gefertigten Bauteilen nicht erreichbar sind. Auch eine gezielte Heizung oder Kühlung in Kolonnen wird durch die neuen Freiheitsgrade im Design ermöglicht.
Die Handlungsspielräume sind allerdings nicht auf das Design der Trennapparate beschränkt. Allgemein werden bei der Planung, beim Bau und beim Betrieb von chemischen Anlagen durch additive Fertigungsverfahren neue Spielräume geschaffen. Durch den Einsatz bereits weit entwickelter Verfahren ist ein Print-on-Demand von Komponenten möglich. Dies betrifft einerseits die Herstellung von Ersatzteilen, die ggf. schneller zur Verfügung stehen können, als auch andererseits die Herstellung von Laborpackungen für die in der Prozessentwicklung notwendigen Experimente. Zudem ist es möglich, Messstellen und elektrische Verschaltungen in das Design des Equipments direkt zu integrieren. Auch die Entwicklung von standardisierten Apparaten mit austauschbaren Strukturen für den Einsatz in Multi-Purpose-Umgebungen ist denkbar.
Nicht zuletzt wird die Palette der einsetzbaren Materialien und Werkstoffe durch additive Fertigungsverfahren erweitert. Dadurch ergeben sich ebenfalls neue Handlungsfelder. Der Einsatz neuer Materialien eröffnet die Möglichkeit, den Korrosionsschutz durch das gezielte Mitdrucken entsprechender Beschichtungen kostengünstiger zu gestalten. Zudem sind gezielte Oberflächenmodifikationen vorstellbar, durch die bspw. die Benetzbarkeit von Oberflächen eingestellt werden kann. Die Herstellung heterogener Oberflächen eröffnet Einsatzgebiete auch im Bereich katalytischer Beschichtungen oder hochgenauer Membranen mit gezielten Oberflächenparametern. Ganz praktisch können neue Materialien auch dünnere Wandstärken ermöglichen, was zu einer Reduktion der Herstellkosten führen kann.
Abb. 1 fasst die beschriebenen Handlungsfelder noch einmal zusammen und strukturiert diese in Bezug auf die Möglichkeiten, die sich durch additive Fertigungsmethoden ergeben.
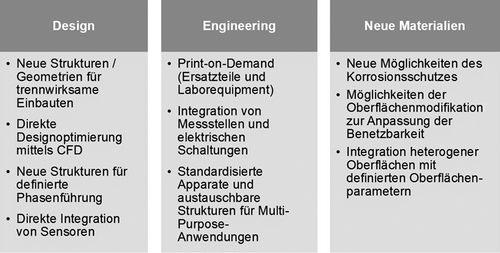
4.3 Neue Messmethoden und Signalauswertung
Wie bereits in Sect. 3.3.2 diskutiert, können neue Messmethoden zum verbesserten Verständnis von Phänomenen innerhalb der Apparate führen. Dieses Verständnis spielt eine zentrale Rolle zur Weiterentwicklung von geeigneten Modellen zur Apparateauslegung und zum Scale-up. Neben der messtechnischen Erfassung spielen auch neue Methoden zur Auswertung der Messsignale eine wichtige Rolle. Demzufolge ergeben sich in den genannten Bereichen verschiedene neue Handlungsfelder.
In Bezug auf die Messmethoden und Messtechniken selbst ist es notwendig, die etablierten Messtechniken noch robuster gegenüber z. B. extremen Prozessbedingungen oder korrosiven Medien zu machen. Zudem kann es interessant sein, bestimmte Sensoren mit verschiedenen Funktionalitäten auszustatten, also mehrere Messgrößen mit einem Sensor aufzunehmen, wie es bei einigen Sensoren bereits durchgeführt wird. Neben der reinen Aufnahme von Messwerten können die Sensoren selbst auch verwendet werden, um die gewonnenen Daten direkt auszuwerten und weiterzuverarbeiten. Derartige Softsensoren sind in der Lage, nicht nur das reine Messsignal weiterzugeben, sondern liefern direkte Aussagen über die verfahrenstechnische Zielgröße. Dadurch lässt sich die Datenverarbeitung deutlich effizienter gestalten. Als zusätzliches Handlungsfeld zeigen die aktuellen Arbeiten, wie sie auszugsweise in Sect. 3.3.2 dargestellt wurden, dass auch die Entwicklung neuer Messmethoden ein wichtiges Feld ist, um neue Informationen über die Vorgänge im Inneren der Apparate zu erlangen. Zudem können neue Kombinationen verschiedener vorhandener Messverfahren ebenfalls zu einem Informationsgewinn führen. Neben einem zusätzlichen Informationsgewinn können bei der zukünftigen Entwicklung neuer Sensoren auch andere Aspekte eine Rolle spielen. Es kann bspw. hilfreich sein, wenn die Sensoren über die Möglichkeit der Selbstdiagnose verfügen und so die Wartung erleichtert wird. Gleiches gilt für den Fall, dass in den Sensor direkt Warnfunktionen integriert sind, bspw. wenn kritische Parameter erreicht oder überschritten werden.
Neben der reinen Aufnahme und gegebenenfalls ersten Verarbeitung der Signale spielt bei höherer Quantität der Signale auch deren Auswertung eine entscheidende Rolle. Dazu zählt die Entwicklung effizienter Auswertealgorithmen. Großes Potenzial kann hier vor allem Methoden aus dem Bereich Künstliche Intelligenz und Machine Learning zugeschrieben werden. Darüber hinaus ist aber auch eine zunehmende Vernetzung der Informationen und die Erkennung von Mustern entscheidend, um die Signale korrekt zu interpretieren. Flankiert werden diese Maßnahmen vom Bedarf geeigneter Konsistenzprüfungen, wenn es darum geht, aus den gewonnenen Informationen bspw. neue Betriebsführungskonzepte abzuleiten. Zudem erfordern derartige Auswerte- und Analysemethoden die parallele effiziente Datenverwaltung.
Wenn die Arbeiten im Bereich der Entwicklung neuer Mess- und Signalauswertemethoden voranschreiten, werden auch neue Handlungsfelder im Bereich Modellierung und Design des entsprechend untersuchten Equipments der thermischen Verfahrenstechnik aufgespannt. Dazu gehören die Entwicklung neuer, datengetriebener Modellansätze und neue Möglichkeiten zur Modellsynthese, angepasst an den spezifischen Anwendungsfall. Zudem besteht die Möglichkeit, bereits vorhandene orts- und zeitaufgelöste Modelle umfassender zu validieren, als dies bisher der Fall ist. Auch können für den Betrieb neue Regelstrategien, wie bspw. die messdatengetriebene Optimalsteuerung, also die algorithmusbasierte Anpassung der Stellgrößen durch permanente Echtzeit-Datenauswertung, entwickelt werden.
Eine übersichtliche Strukturierung der Handlungsfelder, die sich im Bereich neuer Messmethoden und deren Signalauswertung aufspannen und letztlich zu intelligenten Apparaten führen können, ist in Abb. 2 gegeben.
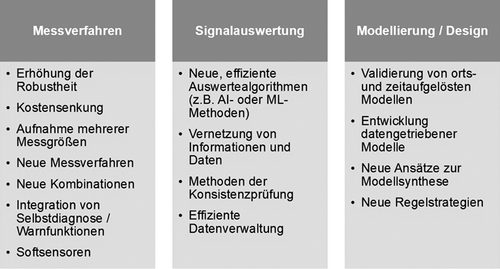
4.4 Neue Simulationstechniken
Die Digitalisierung in Kombination mit der vierten industriellen Revolution erlaubt die Verarbeitung bisher noch nicht dagewesener Datenmengen. Die Verknüpfung von Daten aus den realen Anlagen mit beschreibenden Modellen kann über sog. Digitale Zwillinge stattfinden; also ein mathematisches Abbild der physischen Anlage. Neben der Zustandsdiagnostik, die bspw. mittels neuer Messmethoden oder verbesserter Signalauswertung stattfinden kann, spielen Modellierung und Simulation eine entscheidende Rolle. Das Werkzeug des Digitalen Zwillings erlaubt die Abbildung der Anlage über den gesamten Lebenszyklus, wobei die Modelle über die Lebenszeit hinweg zunehmend detaillierter werden. Die für die Abbildung der realen Anlage notwendigen Modelle können von einfachen Blackbox-Modellen bis hin zu hochaufgelösten Strömungssimulationen reichen. Letztere wurden in Form von Mehrphasen-CFD-Simulationen im Rahmen des Symposiums ausführlich diskutiert.
Mehrphasen-CFD-Simulationen können zu einem besseren Verständnis von physikalischen und hydrodynamischen Phänomenen auf verschiedenen Skalen führen. Limitierend sind aktuell u. a. die Möglichkeiten zur gleichzeitigen Lösung von Impuls-, Stoff- und Wärmetransport ggf. gekoppelt mit Reaktionen auf technisch relevanten Skalen. Unter der Voraussetzung, dass diese Limitierungen durch kontinuierliche Weiterentwicklung aufgebrochen werden, ergeben sich auch für den Bereich der Zweiphasen-CFD neue Handlungsfelder zur Weiterentwicklung thermischer Trennverfahren.
In Kombination mit den additiven Fertigungsverfahren ist es möglich, eine CFD-basierte Strukturoptimierung für Apparate der thermischen Verfahrenstechnik und deren trennwirksame Einbauten durchzuführen sowie Aspekte hinsichtlich eines Scale-up direkt mitzuberücksichtigen. Auch für bestehende Geometrien können durch verbesserte CFD-Verfahren die Auslegung und das Scale-up effizienter durchgeführt werden. Vor allem validierte Mehrphasen-CFD, in denen neben Stofftransport auch Reaktionen berücksichtigt werden können, erlauben frühzeitige Potenzialabschätzungen für neue integrierte und intensivierte Verfahren und können so zu einer Verkürzung der Entwicklungszeiten führen.
Durch effizientere Lösungs- und Meshingverfahren kann es außerdem möglich sein, großskalige und großvolumige Apparate mittels Strömungssimulationen abzubilden und Hinweise bspw. hinsichtlich einer verbesserten Phasenführung zu erhalten. Durch eine genauere Auflösung und Beschreibung von festen Oberflächen ist es möglich, die Auswirkungen unterschiedlicher Oberflächeneigenschaften auf die Fluiddynamik besser zu verstehen. Gleichzeitig kann umgekehrt die Auswirkung einer gezielten Manipulation der Oberflächeneigenschaften abgeschätzt werden.
Durch die Weiterentwicklung der CFD-Methoden ist zukünftig zu klären, welche Schlüsselexperimente in der Entwicklung neuer Verfahren und beim Scale-up bestehender Verfahren notwendig sind. Zur Auswahl dieser Experimente und der benötigten Parametersets sind geeignete Methoden zu entwickeln.
5 Fazit
Die chemische Industrie muss auf eine Vielzahl an Herausforderungen reagieren, um ihre Wettbewerbsfähigkeit zu erhalten. Mit den politisch beschlossenen Maßnahmen zur Einhaltung der Klimaschutzziele aus dem Pariser Klimaschutzabkommen und zur Energiewende ändern sich die Randbedingungen in der Produktion hinsichtlich der möglichen Energiequellen und der Energieeffizienz signifikant. Dies gilt auch für die Rohstoffbasis und die Kundennachfrage. Biobasierte Produkte bzw. das Recycling von Grundstoffen werden zukünftig eine zentrale Aufgabe sein. Gleichzeitig muss eine konstante Qualität gewährleistet werden. Zudem steigt die Nachfrage nach speziellen Produkten mit entsprechend kurzen Produktlebenszyklen.
Neue Lösungen und Methoden auf allen Ebenen sind notwendig, um passende Antworten auf diese Herausforderungen zu finden. Exemplarisch wurden in Sect. 3 bereits verfügbare Lösungsansätze für die Prozess- und Apparateebene sowie zum besseren Verständnis der ablaufenden Phänomene dargestellt. In Sect. 4 wurden zukünftige Handlungsfelder, die zum Teil durch die Möglichkeiten aus dem Bereich der Digitalisierung aufgespannt werden, abgeleitet. Es zeigt sich, dass vor allem (digitale) Planungsmethoden, die Möglichkeiten durch die additive Fertigung, neue Verfahren zur Aufnahme von Messdaten und deren Signalauswertung sowie die Weiterentwicklung von CFD-Simulationen neue Optionen ermöglichen. Diese Handlungsfelder sollten in zukünftigen Forschungsprojekten aufgegriffen und bearbeitet werden.
Biographies
Julia Riese studierte Umwelttechnik und Ressourcenmanagement an der Ruhr-Universität Bochum. Anschließend promovierte sie an der Fakultät für Maschinenbau an der Schnittstelle zwischen Energie- und Verfahrenstechnik. Als Leiterin einer Arbeitsgruppe am Lehrstuhl für Fluidverfahrenstechnik liegt ihr Forschungsschwerpunkt in der Untersuchung der Flexibilität chemischer und thermischer Prozesseinheiten mittels Modellierung, Simulation und Experimenten.
Andreas Hoff studierte Chemietechnik an der Universität Dortmund mit anschließender Promotion im Jahr 2002. Nach seinem Einstieg in die heutige Evonik Industries AG als Prozessingenieur und nachfolgender Technikumsleitung übernahm er kommerzielle und technische Leitungsfunktionen an verschiedenen Standorten für Evonik wie bspw. die Abteilungsleitung für Fluidverfahrenstechnik von 2010 bis 2013. Anschließend übernahm er die globale Geschäftsverantwortung für den Bereich Performance Foams und leitet seit 2017 die Verfahrenstechnik bei Evonik.
Jürgen Stock studierte Maschinenbau an der Ruhr-Universität Bochum und wechselte anschließend zur Promotion an das Max-Planck-Institut für Strahlenchemie in Mühlheim an der Ruhr (heute Max-Planck-Institut für Chemische Energiekonversion). Seit 1988 arbeitet er für Evonik bzw. deren Vorgängergesellschaft Degussa. Hier war er zu einem Großteil seiner Berufslaufbahn in der Verfahrenstechnik in Hanau tätig. Aktuell beschäftigt er sich mit den Auswirkungen der Energiewende und der Steigerung der Nachhaltigkeit in der chemischen Industrie.
Andrzej Górak studierte Chemie an der Technischen Universität Lodz in Polen. Nach einem Forschungsaufenthalt an der Heimatuniversität und bei der Firma Henkel KgaA in Düsseldorf wurde er Professor in Dortmund und Essen. Bis zu seiner Pensionierung im letzten Jahr leitete er den Lehrstuhl Fluidverfahrenstechnik an der TU Dortmund. Seine wissenschaftlichen Interessen liegen in der Trennung von Vielkomponentengemischen und der Auslegung von neuen Trennapparaten.
Marcus Grünewald studierte Chemieingenieurwesen an der Technischen Universität Dortmund, wo er 2000 promovierte. Anschließend war er als Habilitand am Lehrstuhl von Prof. Agar beschäftigt. Von 2004 bis 2009 war er Mitarbeiter in den Arbeitsgruppen Reaktionstechnik und Conceptual Design der Bayer Technology Services GmbH in Leverkusen. Seit 2009 leitet er den Lehrstuhl für Fluidverfahrenstechnik an der Ruhr-Universität Bochum. Er widmet sich dort den Forschungsthemen Modulare Verfahrenstechnik, Mikrotechnik und Mehrphasenapparate.