Estimating COVID-19 Impacts on the Broiler Industry
Joshua G. Maples is an Assistant Professor and Extension Economist in the Department of Agricultural Economics at Mississippi State University. Jada M. Thompson is an Assistant Professor in the Department of Agricultural and Resource Economics at the University of Tennessee. John D. Anderson is a Department Chair and Professor in the Department of Agricultural Economics and Agribusiness at the University of Arkansas. David P. Anderson is a Professor and Extension Economist at in the Department of Agricultural Economics at Texas A&M University.
Editor in charge: Craig Gundersen
Abstract
The COVID-19 pandemic created massive disruptions in meat supply chains including the US poultry industry. Detrimental impacts to chicken demand due to restaurant closures led to supply adjustments affecting broiler producers. The integrated structure of the broiler industry creates significant challenges in estimating grower losses. Farmers who raise broiler chickens do not own the birds and price drops are not directly felt in the same manner as in other commodities. This article examines the broiler industry and presents methodology to better understand the farm-level impacts of COVID-19. Further, this work is useful for policy response considerations for broiler growers.
Introduction
Millions of words have likely been written about the impacts of the COVID-19 pandemic on the economy and agriculture, in particular. Across agriculture, impacts have ranged from euthanized livestock to rotted crops; disruptions in meat processing, restaurants, and grocery stores; and volatile prices (Lusk et al. 2020). The COVID-19 impacts continue to ripple back and forth through our economy, especially in livestock agriculture.
This article focuses on the chicken/broiler industry. Similar to other livestock sectors, the broiler sector faced detrimental disruptions due to COVID-19. In February 2020, USDA forecasted 45.8 billion pounds of broiler meat production in 2020 and an annual average price of $0.87 per pound (U.S. Department of Agriculture, Office of the Chief Economist (USDA, OCE) 2020). The same report in August 2020 showed significant declines from February with a 2020 production forecast of 44.7 billion pounds and an annual average price of $0.704 per pound. The most dramatic decrease occurred in the second quarter due to COVID-19 demand shocks and processing disruptions. USDA estimated second quarter of 2020 production was 4.5% (or 519 million pounds) lower and the price was 29% (or $0.28 per pound) lower than the second quarter forecasts in the February 2020 report.
While it is clear that COVID-19 caused detrimental impacts on the broiler industry as a whole, the industry exhibits features that led to unique impacts within the industry and especially on growers. Perhaps most importantly, almost all production is contracted to growers who do not own the birds. This differs from many other producers of agricultural commodities. Additionally, industry output consists of highly specialized products depending on retail outlet and production is fast compared to other animals, a matter of weeks, which allows for relatively quick adjustment.
These industry attributes create difficulty in understanding the impacts of the pandemic on broiler producers and crafting policy responses using traditional methods. For example, the Coronavirus Food Assistance Program (CFAP) did not provide assistance to broiler growers because it did not provide funding for producers who did not own the livestock (Coronavirus Food Assistance Program (CFAP) 2020). Yet the losses to many broiler growers were significant due to the impact of reduced flock numbers or where flock destruction occurred.
This paper examines the broiler industry and analyzes the impact of COVID-19 on broiler growers. The paper is organized with an overview of the market going into the COVID-19 pandemic, a review of broiler market structure, an analysis of grower impact, and implications for policy response.
The Market Early in 2020
Broiler production was very strong to start 2020. First-quarter slaughter for 2020 was about 5.4% greater than during the first quarter 2019 (U.S. Department of Agriculture, National Agricultural Statistics Service (USDA, NASS) 2020). Eggs set for broilers and chicks placed for broiler growout were well above the year before during the first quarter, setting the stage for continued year-over-year growth into the second quarter (U.S. Department of Agriculture, Economic Research Service (USDA, ERS) 2020). Weekly chicks placed were 2%–4% above 2019 throughout March. First quarter broiler production was 8.2% above the year before, outpacing slaughter due to heavier bird weights.
These strong production numbers reversed when the COVID-19 impacts began. The closure of restaurant dining rooms affected consumer demand for chicken while workforce disruptions affected the chicken supply chain. By the week ending April 25, egg sets were 8.3% below the same week the year before (USDA, ERS 2020). Chicks placed for broiler growout declined 12.9% from the year before by the week of May 2. Young chicken (broiler) ready-to-cook production in May declined 7.1% from the previous May (U.S. Department of Agriculture, National Agricultural Statistics Service (USDA, NASS) 2020). Heavier average weights moderated the effects of reduced slaughter. It was not until late June when chick placement for growout returned to levels from a year ago.
These industry-level impacts were felt differently across participants. It is common for different integrators and specific plants within integrated companies to concentrate on different retail chicken outlets. The whole bird, deboned, and cut-up chicken markets have different bird size specifications. Processing plants and the growers who supply them focus on different retail markets, allowing them to specialize on specific bird sizes, for example anything from a four- to nine-pound bird. That means that the impact of COVID-19 has had differential impacts not only on companies who may be more heavily dependent on one market, but also on specific production complexes who supply these companies. Growers producing different bird weights may face different impacts from restaurant sector closures, for instance.
In 2019, the largest broiler producer, Tyson Foods, representing nearly 21% of the US broiler market and 38.3 million head, produced six-pound birds on average. By contrast, Sanderson Farms, the third largest producer representing 9% of the broiler market and 12.0 million head, produced 8.17-pound birds on average (WATT 2020). In terms of sales outlets, Pilgrim's Pride, the second largest U.S. broiler producer, with 17% market share and 30.3 million head, shipped an estimated 47% of production to grocery stores and 53% of production volume to food service (WATT 2020). Perdue, the fourth largest US broiler producer (7% market share and 12.8 million head), was dependent on grocery store outlets for about 74% of production volume and on food service for an additional 19% of volume. Ninety-five percent of Wayne Farms, the seventh largest producer (5% and 7.6 million head), volume was food service. In addition, the destination market is also important with close to 18% of US broiler production targeted for international markets and individual firms varying in how much of their production is destined abroad (e.g., 4% for Pilgrim's Pride and 15% of volume for Koch) (USDA, ERS 2020; WATT 2020). Given the very different types of markets and bird size produced, the range of impacts on growers could range from very little to the loss of significant numbers of birds or flocks for the year through longer out times.
Structure of the US Broiler Industry
Modern broiler production developed in the 1950s, from the growth of dual-purpose birds (i.e., for both meat and eggs) into concentrated genetic selection for meat type and egg type birds. Broiler production in the United States accounts for 70% of all poultry production value. US broiler production operates as a fully integrated system where integrators are responsible for birds, feed, and technical assistance and producers are contracted to grow and mange birds suppling the land, facilities, labor, and management. The broiler industry is broadly characterized by two primary sectors: breeding and growout. Breeding birds are those that are raised for hatching eggs through the primary breeding and parent stages to produce broiler chicks for growout. Growout is the final stage and where broilers are raised for harvest. The broiler industry functions under a contract growing system with 99% of broilers and broiler breeders grown under contract (U.S. Department of Agriculture, National Animal Health Monitoring System 2010). While these sectors are linked in the broiler production chain, they differ in meaningful ways such as management, length of production, housing types, manure management, geographical concentrations, value of birds, and product produced (i.e., eggs compared to carcasses). In order to understand these general sectors of the broiler industry, broiler breeding and growout are discussed separately below.
Broiler Breeders
Broiler breeders are roosters and hens (sexually mature adult chickens) that produce fertile hatching eggs. The length of production varies from 60 to 80 weeks. Broiler breeding has several stages of production, starting with genetic stock through primary breeders (pedigree/elite stock, great-grandparent stock, and grandparent stock) and ending with parent stock, which supply the hatching eggs to be grown as broilers. The number of birds increase (while the value per bird decreases) with each level of the broiler breeder progression with pedigree birds accounting for 5.4%, great-grandparents 14.4%, and grandparents 77.1% of the primary breeding level (US Department of Agriculture, National Animal Health Monitoring System 2010).
Growers are paid based on breeder management and the number of settable eggs supplied to the hatcheries. At the end of their production, these birds may be harvested and used in further processed foods. Breeders are typically produced in open-floor buildings that use a series of raised nesting boxes and belt-driven egg collection systems. Feed is provided by the integrator and is sex and age specific to account for egg production by hens and weight maintenance by roosters. Hatching eggs are transported to predominantly integrator-owned hatcheries who are responsible for hatching fertile eggs in appropriate, climate-controlled incubators.
Broiler Growout
Growout is the final production stage for broilers where chicks (of both sexes) are placed on farms and grown to the desired age/weight before harvest from four to eight weeks of age. Broiler production is primarily concentrated in the southeast region of the United States. In 2019 the top six broiler producing states in terms of head, pounds, and value accounted for 66% of US production and in descending order by size are: Georgia, Arkansas, North Carolina, Alabama, Mississippi, and Texas (U.S. Department of Agriculture, National Agricultural Statistics Service (USDA, NASS) 2020). These states represented $21 billion of the $31.7 billion 2019 broiler production value. From 2012 to 2017, the U.S. Census of Agriculture indicated a growing number of broiler farms from 42,226 to 42,858 (USDA, NASS 2019). The demand for broiler products continues to grow domestically and internationally. Since 1992, chicken meat has been the most consumed meat in the United States. The 2019 annual per capita consumption was 95.1 pounds of chicken compared to 58.1 pounds of beef consumed (U.S. Department of Agriculture, Office of the Chief Economist (USDA, OCE) 2020). In 2019, 16% of total U.S. broiler production flowed to international markets (USDA, OCE 2020) with the top five chicken export destinations by volume being Mexico, Cuba, Taiwan, Angola, and Vietnam (U.S. Department of Agriculture, Foreign Agriculture Service (USDA, FAS) 2020).
Broilers are produced in houses that are climate controlled for the age of the bird, where younger birds need additional heat lamps. Broiler houses are either tunnel ventilated or curtain-sided, where both are appropriately ventilated to maintain the air quality for birds. Tunnel ventilated broiler houses have solid side walls and use large fans and vents to move and exchange air throughout the house. Curtain-sided houses raise and lower the curtains that run along the length of the house to manage airflow and air exchange. Broilers are free to move throughout the broiler house and have free access to feed and water at all times. Strict biosecurity protocols are used to protect the health and safety of the broilers, which may include limiting nonessential traffic on farm, truck washes in or out of the farm, foot baths, and predator control.
Feed is produced by the integrator using age-specific feed rations which include starter feed for newly hatched chicks, developer feed for birds in the development phase, and grower feed for mature birds. These specified foods are optimized for growth and complete nutrient requirements for broilers. Feed is delivered to farms throughout the lifecycle of the broiler.
Broilers are moved to slaughter facilities when they reach their target age or weight. Broilers are then processed into ready-to-cook whole birds, cut into ready-to-cook parts, or continue onto further processing. These birds are consumed in the United States and around the world. Producers are paid based on their contract, with payments based on total weight of birds produced and, frequently, including special monetary incentives for flock uniformity.
Estimating Farm-Level Impacts
Due to the integrated nature of contract broiler production, farmers growing birds under contract do not generally face price risk. Contracts specify the terms for grower compensation. While these terms may include some variable component (e.g., a “tournament”-based premium structure or a seasonal energy cost component), base compensation is generally fixed relatively firmly. This is not to say, however, that contract broiler growers have no revenue risk. Adverse changes in key production parameters can result in significant financial risk for contract growers despite the relative stability of the compensation rate.
Static Budget Analysis of Flock Losses
Solving this derivative at expected levels of the other variables provides a simple estimate of the impact of the marginal value of a broiler flock. For example, let us assume the following values for the production parameters in equation 6): PMTR = $0.07 per pound; SQFT = 100,000 square feet; DENSITY = 0.85 square feet/bird; DL = 5.5%; WGT = 6.5 pounds; and α = 0.25 (i.e., TVC equals 25% of total revenue).
In this example, the loss of a full flock would be expected to reduce net revenue by just under $38,000, or about $0.38 per square foot of production capacity. This calculation represents a lower bound on the marginal value of a broiler flock. In reality, TVC will not likely vary with production in a constant proportion. For example, differences in economies of scale across individual components of TVC would preclude that simplified outcome. Conceptually, TVC varies with production—not necessarily with any single element that contributes to production. Thus, while some variable costs may vary directly with number of flocks, others may not. With respect to broiler production, for example, costs associated with cleaning out a house will vary with production but will not necessarily be directly proportional to the number of flocks raised. While the cost of between-flock cleaning practices will be incurred with each flock, a grower will likely have to do a more comprehensive full cleanout for the year whether five flocks or six have been grown. The point is, to the extent that some variable costs do not vary directly with number of flocks, the result in equation 7 likely underestimates the net impact of losing a flock. To derive a more realistic assessment of the marginal value of a broiler flock, a more empirical approach is necessary.
Stochastic Budget Analysis of Flock Losses
The preceding exercise is a useful way to isolate the effects of a change in key production parameters (in this case, average number of flocks per year) on expected values for key financial metrics (in this case, net cash flow). However, to fully appreciate how changes in production parameters impact the financial viability of an operation, a more comprehensive and realistic evaluation of financial outcomes is in order. Such evaluation is a challenge because the data needed to define distributions of and correlations between production parameters (and, incidentally, compensation rates) is proprietary. Still, anecdotal sources of data, such as growers themselves and agricultural lenders, coupled with judicious assumptions about distributional parameters provide a starting point for more robust risk evaluation.
Table 1 presents a detailed enterprise budget for a hypothetical four-house broiler operation.3 This budget is used to develop a stochastic simulation of net cash flow in order to evaluate grower financial risk associated with relevant production parameters. Production variables will be assumed to follow a triangular distribution as described in table 2, with correlations between the variables as described in table 3.4 Production variables are simulated using the procedure described in Clements, Mapp, and Eidman (1971), with the exception that the information in the rank correlation matrix rather than the covariance matrix is used to derive correlations, consistent with the approach described in Anderson, Harri, and Coble (2009).
Width | Length | ||
---|---|---|---|
House dimensions (feet) | 60 | 600 | |
Number of houses | 4 | Bird density (sq. ft./bird) | 0.85 |
AVG. bird size (live weight, lbs.) | 6.5 | Flocks/year | 5.30 |
Death & condem. loss (%) | 5.5% | Payment rate ($/lb, live) | $ 0.070 |
Other payment ($/SQ. FT.) | $ - | Litter value ($/ton) | $ - |
Square feet each house | 36,000 | Total square feet | 144,000 |
Number of birds/house | 42,353 | Number of birds/flock | 169,412 |
Birds placed/year | 897,882 |
Year 1 | |||||
---|---|---|---|---|---|
Item | Unit | Quantity | Price | Total | |
Cash receipts | |||||
Payments for birds delivered | PER POUND (LIVE) | 5,515,242 | $ 0.0700 | $ 386,067 | |
Variable costs | |||||
Labor | HOURS/HOUSE | 668 | $ 15.00 | $ 40,068 | |
Paid labor | % | 0% | $ - | ||
Electricity | /SQ. FT./FLOCK | 763,200 | $ 0.0375 | $ 28,620 | |
Fuel | House/flock | 21 | $ 350 | $ 7,420 | |
Supplies and miscellaneous | HOUSE/flock | 21 | $ 675 | $ 14,310 | |
Building & equipment repairs | House | 4 | $ 6,806 | $ 27,225 | |
Other equip. repairs & maint. | Farm | 1 | $ 2,500 | $ 2,500 | |
Crust out/windrow/ cleanout | /House/flock | 21 | $ 500 | $ 10,600 | |
Interest on operating capital | % | 90,675 | 2.0% | $ 1,814 | |
Total variable costs | $ 92,489 | ||||
Fixed costs | Total investment | ||||
Building cost | $/House | $ 371,250 | $ 1,485,000 | houses | |
Equipment cost | $/House | $ 123,750 | $ 495,000 | equipment | |
Percent financed | % | 100% | |||
Depreciation on buildings | 0.5 | Salvage | $ 49,500 | ||
Depreciation on equipment | 0.25 | Salvage | $ 53,036 | ||
Depreciation on other equipment | 0.25 | Salvage | $ 5,357 | ||
Interest on buildings | 15 Years | Annually | 4.5% | $ 66,825 | |
Interest on equipment | 7 Years | Annually | 5.5% | $ 27,225 | |
Interest on other equipment | 7 Years | Annually | 5.5% | $ 2,750 | |
Property taxes (houses) | Farm | 1 | $ 11,664 | $ 11,664 | |
Insurance | SQ. FT. | 144,000 | $ 0.0420 | $ 6,048 | |
Telephone/alarm | Farm | 1 | $ 1,500 | $ 1,500 | |
Total fixed costs | $ 223,905 | ||||
Principal on buildings | $ 71,449 | ||||
Principal on equipment | $ 59,877 | ||||
Principal on other equipment | $ 6,048 | ||||
Total loan payments (P&I) | Annual | $ 234,175 | |||
Return to unpaid labor, land, overhead, risk & MGT. | Annual | $ 69,674 | |||
Operator/family labor | $ 40,068 | ||||
Return to land, overhead, risk & MGT. | Annual | $ 29,606 | |||
Net cash flow | $ 40,192 |
- Note: The bold values represent totals within the table.
Most Likely | Minimum | Maximum | |
---|---|---|---|
Days in birds | 48 | 45 | 52 |
Days out (5.3 flocks) | 20 | 18 | 23 |
Days out (4.3 flocks) | 36 | 32 | 41 |
Stocking Density | 0.85 | 0.80 | 0.90 |
Avg. Bird Weight | 6.50 | 6.20 | 6.85 |
Death Loss | 5.50% | 3.75% | 6.25% |
Days In | Density | Avg. Bird Weight | Death Loss | |
---|---|---|---|---|
Days In | 1.00 | 0.91 | 0.92 | 0.60 |
Density | 1.00 | 0.96 | 0.63 | |
Avg. Bird Weight | 1.00 | 0.62 | ||
Death Loss | 1.00 |
- Notes: Spearman correlation coefficients.
Net cash flow is used as the primary metric to assess financial risk in these simulations because grower operations are typically financed with minimal equity and for relatively long terms (seven to eight years on equipment; ten to fifteen years on barns). One of the major risks to a contract broiler grower's financial viability is that a disruption in production will reduce cash flow to the point that debt cannot be serviced (MacDonald 2014). It is assumed in these simulations that the contract grower is financed at 100% on buildings and equipment and is still in the repayment period on both.5 It is further assumed that all labor in the operation is operator/family labor.
The cumulative distribution function for net cash flow for an average of 5.3 and 4.3 flocks per year are presented in figure 1. This figure shows the risk environment facing contract broiler growers. The first key point to note is that in what should be considered the normal scenario of 5.3 flocks average per year, the median value for net cash flow is $43,503 per year.6 On this four-house operation, with 5.3 flocks per year, a grower could reasonably expect to be able to meet all financing obligations, pay out-of-pocket expenses, and have about $43,500 left for other obligations and family living. Further, in this scenario, the likelihood of experiencing negative cash flow (i.e., of leaving some payment and/or cash expense obligations unpaid) is low: actually, zero given the relatively narrow distributions of production parameters used here. This result should not be surprising. A major part of the appeal of contract broiler production is that it provides a reasonably reliable source of income to the farm operation (MacDonald 2014). These simulation results are consistent with that expectation.
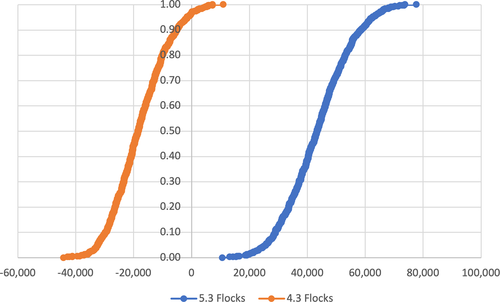
By contrast, if the grower experiences extended out times such that number of flocks fall to 4.3 on average, median cash flow falls to ($18,272). Moreover, the probability of experiencing negative cash flow increases dramatically: to around 95%. In other words, falling one full flock below normal in terms of average production makes it extremely difficult for a grower who is still in the repayment period on his or her loans to meet cash flow obligations, much less contribute to family living expenses.
Note that this assessment of the marginal value of a flock assumes that as the number of flocks received per year goes down, other production parameters remain stable. To the extent that a reduction in flocks might be accompanied by other changes that would further reduce production (e.g., lower stocking density) the results reported here would understate actual losses. In reality, an integrator wanting to reduce production substantially and on short notice (as has been the case with COVID-19) may be forced to adjust several production parameters at once. Thus, it may well be the case that as out-times increase, integrators also reduce stocking density and/or bird weight as a means of managing the shift to lower production. This would imply that the results here may be on the low side of reasonable expectations for grower losses associated with flock reductions. To illustrate, suppose that a shift from an average of 5.3 flocks per year to 4.3 flocks per year is associated with a 5% reduction in average stocking density. In that case, the median net cash flow associated with the one-flock loss would be ($32,544)—a decline of $76,047 from the average-5.3-flock median net cash flow.
Conclusions and Implications for Policy Responses
The structure of the broiler industry leads to complexities in designing farm-level policy responses to market downturns such as the one created by the COVID-19 pandemic. COVID-19 clearly led to losses for the broiler sector but it is much less clear on how to provide relief for broiler producers who were impacted. Producers of other livestock such as cattle and hogs are eligible for varying levels of direct payments per animal through CFAP. However, that policy design does not work well for targeting farm-level losses for poultry producers since the growers do not own the birds or control the timing and number of birds they grow.
Our model allows for a better understanding COVID-19 impacts on broiler growers. The farm-level estimates presented in this paper show the potential impacts of the most common sources of loss for broiler producers. If demand for chicken declines, the effect on contract growers will most likely be production slowdowns that lead to increased time between flocks or a reduction in stocking density. Both of these adjustments significantly impact broiler growers and can lead to negative annual returns. Our model provides the framework for policymakers to estimate losses for impacted producers.
Policies aimed at providing relief to the broiler sector face these challenges of estimating loss and utilizing a measurable variable to determine eligibility. Public data do not exist to determine how many producers were actually affected by production adjustments or the level by which they were impacted. One measurable variable is square feet of broiler house space. While relief payments based on square feet would be relatively straightforward to administer, legitimate concerns could be raised about equitable treatment of growers. In addition to the differing COVID-19 impacts across growers, there also exists considerable variation across growers in farm-level revenue per square foot of house space. This variation can arise from differing compensation structures and production structure such as bird weights and stocking density. Other policy instruments such as poultry loan forgiveness likewise face similar issues of potentially inequitable administrations when compared to losses.
A more targeted relief program would require information to identify producers impacted and the severity of those impacts. While contract broiler growers were not included in CFAP at the national level, state governments have considered relief for broiler producers. The governor of Alabama announced funding to establish the Alabama Agricultural Stabilization Program on August 11, 2020 which includes $4 million to poultry farmers (State of Alabama 2020). The Alabama Department of Agriculture and Industries proposes the poultry funds will be used to “provide direct payments to Alabama resident broiler farmers that have experienced above normal downtimes between flocks and have not been fully compensated for that downtime by their integrator” at a rate of $0.005 per square foot for each day of downtime above twenty-one days. Details on how producers must certify eligibility were not included in the announcement; but it could likely only be accomplished through revealing information from private agreements with integrators. Similar information would likely be needed for any potential national-level program that targets losses due to increased downtime and reduced stocking density. This information could be used in conjunction with our model to calculate relief payments. Requiring private documents for certification would allow for targeted relief but would be more cumbersome to administer than would a self-certification process.
The COVID-19 pandemic created significant disruptions in the broiler industry. The consumer-level disruptions affecting demand for chicken combined with processing disruptions uniquely impacted growers at the farm level in a manner that is difficult to identify and measure. The methodology presented above can be used to better understand the farm-level impacts of COVID-19 and in designing potential policy responses for this pandemic as well as for future disruptions.
References
- 1 Some contracts may have additional incentive payments or seasonal payments to account for higher energy costs. Similarly, in some regions, growers may receive income from the sale of litter as fertilizer. For simplicity, these more complicated revenue sources will not be examined here. Major points of this analysis are not changed by this simplifying assumption.
- 2 The assumption of variable costs as a fixed proportion of revenue is not a particularly strong assumption in this context. Since the payment rate is essentially fixed, both revenue and variable costs fluctuate directly with changes in production.
- 3 This budget was compiled with reference to previous enterprise budgets and cash flow statements developed at Oklahoma State University and the University of Maryland (Doye et al. 2017; University of Maryland 2016).
- 4 Most likely values for the triangular distributions closely match data from roughly a dozen mid-south broiler complexes as compiled by agricultural lenders in the region. Unfortunately, this raw data is proprietary and could not be shared directly with the authors. Minimum and maximum values were set to reflect a range of outcomes that growers could reasonably expect to encounter in the normal course of operations (i.e., in the absence of major market shocks). Correlations were derived from the aforementioned summary of mid-south complex data and were calculated across multiple complexes rather than across time for growers in a single complex. Still, the correlations reflect what should generally be reasonably consistent physical relationships (e.g., between stocking density and death loss) and thus provide a fairer representation of the process being modeled here than would the alternative of ignoring the correlations altogether.
- 5 Shockley et al. (2020) similarly assume that 100% of the cost of contract broiler production equipment and facilities is financed. Goodwin et al. (2005) discuss the relevance of net cash flow as a metric for assessing the financial position of contract broiler growers.
- 6 This rate of facility turnover would be normal for a farm growing industry-average-sized birds. A farm growing smaller birds would turn over faster than this, and a farm growing larger birds would, naturally, turn over more slowly. In those cases, compensation rate and other production parameters (notably stocking density) would differ from those presented here such that income distributions would not differ greatly from this illustration. As noted earlier, the size of bird that a farm grows is related to the supply chain for which the processing complex that the farm delivers to is optimized.