Printable Elastic Porous Conductor for Stretchable Keypads
Abstract
Electrodes, which are essential components of electronic devices, must possess high electric conductivity; thus, most electronic devices currently use rigid metal electrodes. However, electrode stretchability is important for wearable applications, which have recently attracted significant attention. This study describes a strategy for fabricating printable and highly stretchable porous conductors by combining silver flakes with poly(3,4-ethylenedioxythiophene) polystyrene sulfonate. It is found that the fabricated electrode can be stretched by over 400% while retaining high conductivity, which decreases from 532.9 S∙cm−1 at 0% strain to 133.2 S∙cm−1. Furthermore, the novel electrodes exhibits high durability even after 1000 cycles of 100% stretching, which can be an ideal characteristic for skin electronics. The obtained conducting material is used as an electrode for a wearable keyboard, which can be rolled up/out repeatedly, and its reliability exceeds 1000 cycles of operation.
1 Introduction
Advances in wearable technology have been driven by strategies in stretchable materials and design, which play a critical role in achieving desirable properties, particularly combining electrical performance with stretchability. Variations in geometry, including 2D/3D wavy patterns,[1-4] porous structures,[5-8] and elastic medium-rigid filler matrices[6-12] facilitate the utilization of rigid materials in the development of stretchable devices. These devices encompass a wide array of applications, spanning from wearable healthcare systems[13-15] and stretchable displays[16, 17] to artificial skin[18-20] and stretchable printed circuit boards.[21, 22] Despite numerous advancements, the insufficient durability of stretchable conductors limits their use in wearable applications where endurance against repeated stretches of up to 30% on the skin and 100% on joints is imperative. Consequently, there persists a high demand for robust and stretchable electric conductors.
Various conductive fillers with high aspect ratios, such as carbon nanotubes and metal nanowires, are promising materials for composite conductors due to their low percolation thresholds.[23-25] Although the low filler concentration results in high material stretchability, it does not always accompany the desired level of conductivity. In fact, composite conductors with high filler loadings often exhibit the opposite behavior: high conductivity but poor stretchability. This trend persisted until a material employing a self-organized strategy was introduced, demonstrating a conductivity of 35 S∙cm−1 at a strain of 480%.[10] Due to the high filler concentration and softness of the polymer matrix (which led to its high mobility of conductive fillers), the applied strain caused easy migration of filler particles and their subsequent agglomeration, thus rebuilding the conductive path. Furthermore, leveraging the dynamic nature of polymer structures presented a promising strategy to improve the reconstruction of conductive pathways within polymer matrices.[26, 27]
In this work, we developed a novel material structure designed to facilitate self-organization and optimize mechanical/electrical properties by incorporating poly(3,4-ethylenedioxythiophene) polystyrene sulfonate (PEDOT:PSS) with a conductive composite consisting of silver flake and silicone rubber. The combination of conductivity and stretchability is achieved through conductive networks of Ag flakes, which are cost-effective and highly conductive, embedded in a biocompatible silicone rubber matrix, as previously reported.[28, 29] Incorporating PEDOT:PSS into this conductive composite enables structural control, ensuring maintained conductivity under mechanical deformation. The proposed solution-based approach for fabricating an elastic conductor is well-suited for large-area manufacturing processes, such as circuit printing, as demonstrated by the successful fabrication of a stretchable keypad array.
2 Results and Discussion
PEDOT:PSS consists of two ionomers: hydrophobic PEDOT (electrically conducting material) and hydrophilic PSS (electrically non-conducting material); therefore, it behaves like an emulsifier[30] which can develop pores inside the elastic medium through a reverse-micelle induced process.[8] Figure 1 describes the overall procedure for fabricating a stretchable porous conductor (SPC). The process begins with the formulation of SPC paste, achieved by mixing Ag flakes stabilized by an aliphatic capping agent (DSF−84, ≈3 um), serving as a conductive filler; silicone rubber (Ecoflex 00–30) utilized as an elastic medium; organic solvent (4-methyl-2-pentanone); deionized water; and PEDOT:PSS (EL−P5015). The optimal mass ratio of the aforementioned constituents stands at 9:2:3:0.45:0.15, respectively (Figure 1a). Subsequently, the mixed solution is stirred until a homogeneous phase is attained (Figure 1b; detailed sizes and specifications of the employed Ag flakes are listed in Figure S1 and Table S1, Supporting Information).
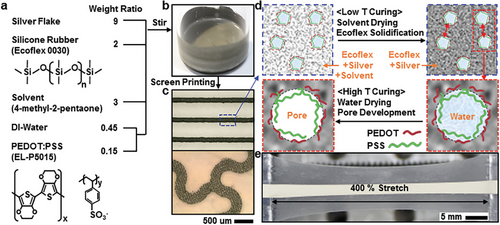
The obtained SPC paste is screen-printed onto the elastic substrate in various patterns (Figure 1c), and the resulting system undergoes mild curing inside a convection oven at 60 °C for 60 min. The stepwise heat treatment process was essential for creating uniform porous structures. The initial stage (60 °C) allows water to remain in liquid form while removing organic solvent and initiating Ecoflex crosslinking. The subsequent stage (110 °C) enables controlled water evaporation from the solidified matrix, creating well-defined pores. The final stage (130 °C) ensures complete removal of any residual liquids. During this stage, the solvent evaporates, and the silicone rubber gradually cross-links, while the water remains in a liquid and dispersed state within the printed paste. Following mild curing, the oven temperature is incrementally raised to 110 °C for 90 min and then to 130 °C for 120 min in order to facilitate the evaporation of residual water and solvent, resulting in the formation of a porous structure.[8] The formation of reverse micelles in our system is driven by the unique amphiphilic nature of PEDOT:PSS. In the initial mixture, the hydrophilic PSS segments preferentially aggregate around water droplets, while the hydrophobic PEDOT segments extend outward into the surrounding organic solvent and silicone rubber matrix. This self-assembly process creates stable reverse micelles where water droplets are encapsulated by PSS (inner layer) and PEDOT (outer layer). During the subsequent heating steps, the gradual evaporation of water leaves behind well-defined pores, while the PEDOT network maintains crucial electrical pathways between silver flakes. This mechanism explains both the uniform pore formation and the maintenance of electrical conductivity in our system. Due to the emulsifying properties of PEDOT:PSS, PSS effectively interacts with water molecules in the SPC paste, attracting PEDOT, which in turn repels water. As a result, PEDOT molecules migrate away from the water, positioning themselves among the Ag flakes (Figure 1d). This series of process enables the stretching of SPC by over 400% while maintaining its conductive properties intact (Figure 1e).
The morphology of the printed paste was assessed using optical microscopy (Figure 2a–c) and scanning electron microscopy (SEM, backscattered electron detection mode, Figure 2d–i). The printed paste prepared without PEDOT:PSS and water exhibited a smooth and clean surface (Figure 2a,d). However, the introduction PEDOT:PSS and water led to pore formation in the SPC paste (Figure 2b,e), as revealed by SEM, energy-dispersive X-ray spectroscopy (EDS; see upper inset of Figure 2e and Figure S2 (Supporting Information) for elemental mapping data on Ag), and atomic force microscopy (AFM; see Figure S3, Supporting Information). A wrinkle-like structure was developed on the surface of SPC after 100% stretching/releasing cycles (Figure 2c,f; Figure S4, Supporting Information), which can be attributed to the pores providing extra length to SPC and a higher Young's modulus of SPC as compared to that of the substrate (Ecoflex). The morphology of the SPC was further examined through cross-sectional analysis (Figure 2g–i), where the bright spots corresponded to the Ag-rich regions, while the dark spots represented the pore regions. The obtained results confirmed the development of pores throughout the SPC following the addition of PEDOT:PSS and water.
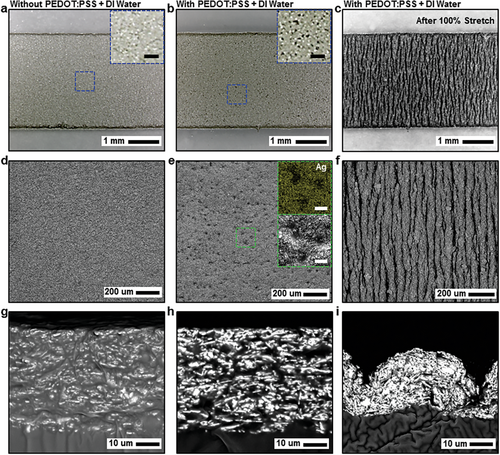
Printed SPC for stretching tests, which was composed of Ag flakes, Ecoflex, and PEDOT:PSS (31.1, 67.8, and 1.1 vol.%, respectively), was prepared as specified in Figure S5 (Supporting Information). As shown in Figure 3a, the initial resistance of the SPC was 0.04 Ω, which gradually increased with the applied tensile strain (ε), reaching 1.30, 3.83, 10.85, and 27.27 Ω at ε = 100%, 200%, 300%, and 400%, respectively. Similarly, a light-emitting diode (LED) was powered using the SPC as the connecting electrode (Figure 3b). Even when the electrode was stretched to greater than 100% of its original length, the LED remained consistently lit without any dimming or flickering (see Movie S1, Supporting Information for a detailed LED test under mechanical deformation). Dynamic durability is another important parameter for stretchable conductors. During durability testing, the prepared SPC was repetitively stretched and released at strains of 30% and 100% (see Movie S2, Supporting Information). As shown in Figure 3c,d, the fabricated SPC demonstrated excellent durability even without pre-strain treatment. After 1000 stretching cycles, the SPC resistance was 13.32 Ω at a strain of 30% and 108.16 Ω at a strain of 100%. These values were relatively small; therefore, the change in resistance due to stretching had virtually no effect on the performance of a circuit containing a resistor (Movie S2, Supporting Information).
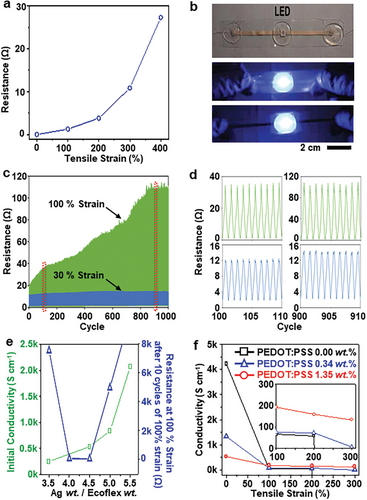
The performance of the SPC was affected by the following three main factors: 1) the ratio between the conductive filler and the soft matrix; 2) the addition of PEDOT:PSS; and 3) the porous structure. To verify the individual effect of these factors, the conductive filler/soft matrix ratio was varied first by adjusting the weight ratio between the Ag flakes and Ecoflex components from 3.5 to 5.5 (Figure 3e). The initial conductivity of the resulting material increased with a higher Ag flake/Ecoflex ratio, while its stretchability decreased because of the insufficient amount of the soft matrix. Optimal conductivity and stretchability were observed at an Ag flake/Ecoflex ratio of 4.5. Therefore, this ratio was fixed at 4.5 for all subsequent experiments.
The addition of PEDOT:PSS significantly impacted SPC performance, despite its small weight fraction compared to other constituents. As shown in Figure 3f, adding PEDOT:PSS dramatically decreased the initial conductivity of the SPC while increasing its stretchability. Due to the heterogeneity of the resulting system, the Ag flakes are easily reorganized into conductive pathways. However, SPCs containing more than 1.35 wt.% of PEDOT:PSS exhibited unstable performance. Therefore, in subsequent experiments, the weight fraction of PEDOT:PSS was fixed at 1.35 wt.%. The porous structure of the SPC also strongly influenced its stretchability. As indicated by the results of Figure S6 (Supporting Information), the material's porosity depended on the amount of added water. The conductor synthesized without water addition had no pores and broke easily under strain. Adding water to the paste mixture increased the SPC's porosity. However, the excessive number of pores increased the material's resistance and decreased the durability of the conductive path (Figure S7, Supporting Information). In addition, the printed SPC was subjected to stepwise heat treatment. Initially, it was heated to a temperature below the boiling point of water in order to evaporate solvent species while retaining water within the matrix. Subsequently, the temperature was raised above the boiling point of water to evaporate both the water and any residual solvent traces. Without the described stepwise treatment, the resulting SPC failed to develop pores, thereby losing its strain resistance, which is a characteristic feature of the reverse micelle-induced process for creating porous structures.[8]
To fabricate a matrix of stretchable switches using the SPC, a novel buried via-hole development process was applied. This involved placing blocking materials at desired locations to prevent them from being covered by the spacing material. The blocking materials were then removed to create space for via holes.
For the bottom and top electrode layers of a 4 × 4 matrix, the prepared SPC paste was printed on silicone rubber substrates using screen printing and then cured (Figure 4a). Each electrode layer consisted of four independent lines, with each line comprising three parts: round, straight, and pentagonal. The round parts of the top and the bottom electrode lines were subsequently aligned and separated through the via holes. The straight parts connected the round parts of the same layer to the pentagonal part, which was wired to a parameter analyzer. Subsequently, melted paraffin (which solidifies easily at room temperature) was positioned on the round part of the bottom layer as a blocking material to occupy the space for a buried via (Figure 4b). The paraffin can be substituted with any removable material, including water (see Figure S8, Supporting Information). To fabricate a spacer, liquid silicone rubber was poured onto the bottom layer and then cured (Figure 4c). The amount and dilution of the liquid silicone rubber controlled the thickness of each layer (Figure S9, Supporting Information). To produce the via holes, the paraffin pillars were removed after solidification of the applied silicone rubber. Finally, the top layer was combined with the spacer/bottom layer by spreading a silicone bond (SilPoxy, Smooth-on) on the spacer layer, followed by aligning and attaching the top layer (Figure 4d).
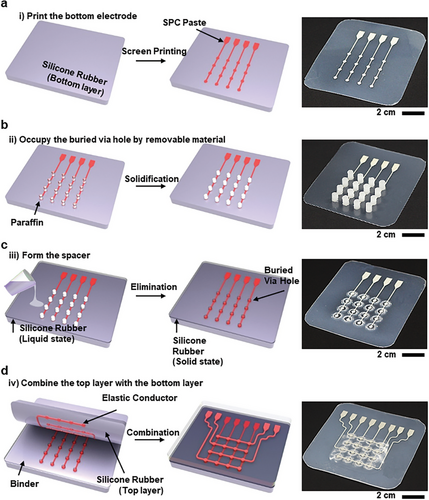
The finalized stretchable keypad (Figure 5a) consists of a 16-switch matrix (Figure 5b). To test its functionality, sequential typing was performed as follows: double-pressing SW 5, triple-pressing SW 9 and SW 3, and single-pressing SW 10. The electrical signals from each switch were monitored, and the resulting currents precisely matched the expected sequence (Figure 5c). Because the switch's resistance increments were much lower than a 10 kΩ resistor, the switch exhibited consistent current responses to pressing and releasing at various contact times (0.1, 1, 5, 15, and 25 s; see Figure 5d). The spacer of the switch decoupled the typing action (pressing the button of the switch) from the stretching process. Although the switch was stretched by up to 40%, the circuit remained open until contact was made between the top and bottom electrodes during typing (Figure 5e). Additionally, the switch maintained its functionality under various uniaxial strain magnitudes (0%, 10%, 20%, 30%, and 40%; Figure 5f).
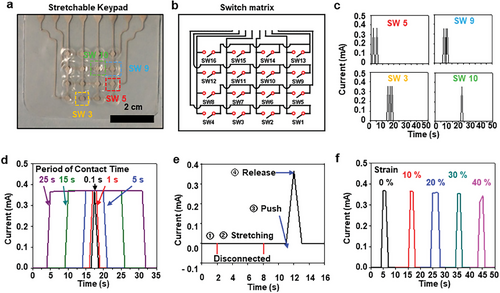
The time-resolved measurements of the switch response (Figure 6a,b) revealed an immediate response of ≈0.2 ms for both pressing and releasing. Due to the recovery delay of the elastic materials, slight increments and decrements in the signal were observed after pressing and releasing the keypad, respectively. However, even with this delay, both the response and relaxation times remained under 0.8 ms. To assess the durability of the stretchable keypads, cycle tests were conducted to evaluate the mechanical reliability of the fabricated switch (Figure 6c). The results demonstrated consistent performance over 1000 typing cycles at a pressing load of 40 g and a typing speed of 1 click s−1. By continuously monitoring the current output signals, each signal corresponded clearly to its respective pressing load without overlap or disconnect (Figure 6d–f).
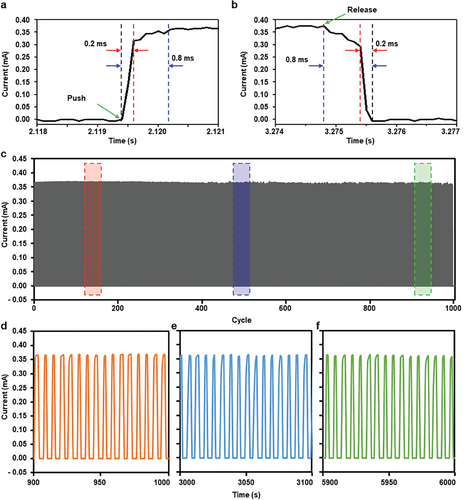
3 Conclusion
In summary, the developed elastic conductor demonstrated exceptional performance, combining ultrahigh stretchability (up to 400%) with outstanding durability (sustaining 100% stretching for 1000 cycles over ≈2 days). This material was successfully employed to fabricate a stretchable keypad array using a novel buried via-hole development process. These remarkable properties were attributed to the synergistic effects of dynamic self-organization, a porous structure, and a stretchable design. PEDOT:PSS played a significant role in the junctions between silver flakes and the formation of porous structures, which alleviated the strain on the conductor during stretching, while the heterogeneous structure enhanced its durability. Notably, this innovative SPC represents a significant breakthrough, as its fabrication process does not require any pre-strain treatment. While the stretchable keypad developed in this study highlights the material's potential, further optimization is possible by modifying the soft medium, controlling pore size, and refining the morphology of the conductive filler to enhance electrode performance.
4 Experimental Section
Preparation of SPC Pastes
The SPC paste was prepared through a systematic mixing process. First, 90 mg of Ag flakes (DSF84, Daejoo Electronic Materials, Republic of Korea) were dispersed in 30 mg of 4-methyl-2-pentanone solvent through mechanical stirring at 500 rpm for 10 min. Then, 1.5 mg of PEDOT:PSS (ELP5015, AFGA, EU) was added and stirred for 5 min, followed by the addition of 20 mg of silicone rubber (Ecoflex 00–30, Smooth-on, USA) with 15 min of further mixing. Finally, 4.5 mg of deionized water was added dropwise under constant stirring. The complete mixture was stirred at room temperature for 30 min until a homogeneous paste was obtained. The viscosity of the final paste was maintained between 15 000 and 20 000 cP at 25 °C for optimal screen-printing properties. Additional solvent was added if needed to adjust the viscosity. The prepared paste was used within 4 h to ensure consistent printing quality.
Morphological and Electrical Characterizations
The morphologies of the samples were characterized by a digital single-lens reflex camera (EOS 700D, Cannon, Japan), optical microscope (BX51, Olympus, Japan), FE-SEM (Inspect F50, FEI, USA), and AFM (Dimension Icon, Bruker). The electrochemical measurements were done using a Keithley 2400 digital sourcemeter (Keithley Instruments Inc., USA) with the custom-made 4-point probe, and a NI PXI-4065 digital multimeter (National Instruments, USA) for 2-wire resistance measurement. The electrical current output was monitored by the parameter analyzer (B1500A, Agilent, USA). To measure the material electrical properties during stretching, a strain machine with a motor controlled by a microcontrolled unit (Arduino UNO, USA) was integrated with the SPC, as shown in Figure S5 (Supporting Information). A section of the tested SPC (1 cm gap between the rigid sections) was stretched by the motor at a stretching speed of 1% sec−1.
Measurement and Evaluation of the Stretchable Keypad
The switch operation was tested using a custom-made pressing machine (Figure S10, Supporting Information) with a constant force of 0.44 N, which ensured reliable contact between electrodes for consistent switch actuation throughout all testing conditions. The durability testing was conducted using an automated testing system applying a consistent pressing force of 0.44 N at a rate of 0.5 Hz, while simultaneously maintaining various strain conditions. The electrical response was continuously monitored throughout the testing period to ensure reliability of the measurements.
Acknowledgements
This research was supported by a grant of the Korea Health Technology R&D Project through the Korea Health Industry Development Institute (KHIDI), funded by the Ministry of Health and Welfare, Republic of Korea (grant number: HI19C075300). Korea Research Institute of Chemical Technology (KS2521-10), Korea Planning & Evaluation Institute of Industrial Technology (KEIT) grant funded by the Ministry of Trade, Industry and Energy (20025622).
[Correction added on 6 March 2025, after first online publication: Acknowledgements section has been updated in this version.]
Conflict of Interest
The authors declare no conflict of interest.
Author Contributions
J.L. and S.H.K. contributed equally to this work. J.L. developed the idea. S.H.K. designed the experiments. J.L. and S.H.K. conducted the experiments and analysis. D.C and C.C investigated. S.J. wrote the manuscript text.
Open Research
Data Availability Statement
The data that support the findings of this study are available from the corresponding author upon reasonable request.