Eucommia Ulmoides Gum Soft-Hard Gradient Composite Materials with Shape Memory Property
Abstract
Eucommia Ulmoides gum (EUG) is a natural polymer material with unique “rubber-plastic duality” and good shape memory properties. In this paper, the hardness of EUG is greatly reduced by adjusting the cross-linking density and adding physical microspheres for foaming. The results show that the more sulfur and foamed microspheres are used, the lower the hardness of EUG, the greater the deformation of the material, and the smaller the penetration force. By adjusting the amount of foaming agent, a series of lightweight and high-toughness foamed EUG can be obtained. The EUG, natural rubber (NR) and foamed EUG are prepared into a hardness gradient composite material with a shape memory characteristic through a co-vulcanization process, according to scanning electron microscope (SEM) observation and 180° peel test results, the three rubber materials has good binding force without the help of adhesive. Each unit of thickness of the composite material can reduce the external impact force by up to 11.6%. In addition, under heating conditions, it only takes 30 s for the crystalline EUG to return to its original shape. The prepared soft-hard gradient sports composite material has a high reduction of external impact force per unit thickness, showing an excellent impact protection effect.
1 Introduction
Every year, ≈75 million people in the world suffer from sports injuries during sport games, and most of them have one thing in common, that is, they do not wear sports protective gear.[1] The purpose of general sports protective gear is to prevent possible sports injuries or to provide targeted protection to injured parts.[2] There are two main points for the protection of materials used in sports. One is to resist external impact through high strength and high hardness; the other is to absorb external impact through relatively soft elasticity. For example, PC, PP, ABS,[3] used for helmet shells, EVA,[4, 5] PBT,[6] etc. used for mouthguards. Although these rigid plastics have high hardness, they are petroleum-based materials and cannot be re-molded after molding. In addition, a variety of new protective materials, such as non-Newtonian fluids,[7] polyurethane foams[8] and fiber-reinforced composite materials,[9] are also used to prepare sports protective gear, but these materials have the disadvantages of high production cost and narrow application range.
Sports protective gear should correct posture and avoid injury, but not limit movement flexibility. Traditional sports protective gear on the market, such as football shin guards, are mainly made of petroleum-based plastic bonded foam materials.[10] They are either simple in structure and poor in protective performance, or due to large-scale commercial development, the shape is fixed and uncomfortable to wear, which will hinder the flexibility of athletes and increase the probability of sports injuries.[11]
Eucommia Ulmoides gum (EUG) is a natural polymer material and widely exists in the rubber-containing cells of various tissues of the Eucommia ulmoides Oliv.[12] Among them, the rubber content of seeds is the most, which is approximate to 10–12%, the rubber content of bark is approximate to 8–10%, and the rubber content of leaves is approximate to 2–4%.The molecular structure of EUG is trans-1,4-polyisoprene, which has a unique “rubber-plastic duality”.[13] EUG composites with excellent shape memory properties can be obtained by methods such as blending and chemical cross-linking.[14-16] At the same time, the materials have good processability and mechanical properties, so they have broad directions in the design of personalized sports protective gear prospects (Scheme 1).[17, 18]
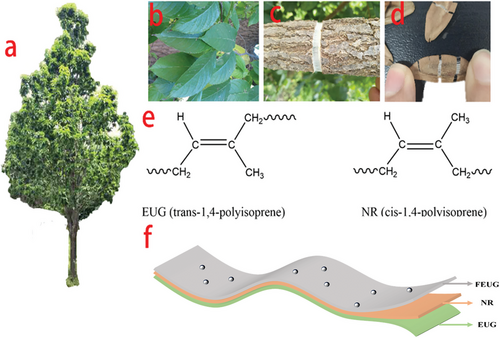
EUG has high hardness, high toughness and excellent impact resistance at room temperature.[19] It can be used as the outer impact-resistant material of sports protective gear, but when designing protective gear, it needs to be combined with soft materials to achieve better protective effect. The author[20] conducted a lot of research on the relationship between the crystallization properties of EUG and vulcanization cross-linking, and found that by increasing the cross-linking density of EUG, the hardness of the material can be greatly reduced. In addition, the soft EUG materials can also be obtained by grafting,[21] epoxidation,[22] hydrogenation modification[23] and blending.[24] Xia[25] studied the addition of a physical foaming microsphere to EUG to make it into a foamed material. The material has low hardness, high toughness, low quality and good shape memory properties.
In this paper, soft EUG was prepared by adjusting different degrees of cross-linking and physical foaming methods, and the hardness gradient composite material was prepared by co-vulcanization process with hard EUG, soft NR and forming EUG, eliminating the use of adhesives. As result, EUG hardness gradient composite material has outstanding modulus and stiffness performance, and also has the characteristics of impact resistance, energy absorption and shape memory characteristics. The material can consider excellent protective performance and wearing comfort, and will be widely used in the field of sports protective gear in the future.
2 Experimental Section
2.1 Materials
EUG was purchased from Shandong Beilong Eucommia Biological Co., Ltd., China. NR (SCR 5) was purchased from Yunnan Yunjiao Group, China. The foaming agent Expancel 920DU40 was purchased from Shanghai Bihe Industry and Trade Co., Ltd., China. Other reagents are commercially available products.
2.2 Sample Preparation
EUG was first masticated at 70 °C, and then vulcanized by a flat vulcanizer. The processing formula was shown in Table 1.
Experimental Materials | Softening EUG Vulcanization /phr | Softening EUG Physical Foaming /phr | NR Vulcanization /phr |
---|---|---|---|
EUG | 100 | 100 | 0 |
NR | 0 | 0 | 100 |
Vulcanization activator | 1 | 1 | 1 |
Cross-linking agent | 3 | 3 | 3 |
Sulfur | 0/0.5/0.8/1/2/4 | 0.8/1/1.5/2/4 | 0.8 |
CZ | 0.8 | 0.8 | 0.8 |
920DU40 | 0 | 2/4/8/10/15/20/25/30/40 | 0 |
2.3 Performance Characterization
2.3.1 Vulcanization Performance of Foamed EUG
The vulcanization performance of EUG was measured using an M-3000FA rotorless vulcanizer (Gotech Testing Machines Inc., China). The test temperature is 180 °C and the test frequency is 100cpm. The effects of sulfur and blowing agent on the torque, scorch time and positive vulcanization time of foaming EUG were investigated.
2.3.2 Foaming Properties of Foamed EUG
2.3.3 Tensile Test
The tensile mechanical properties of foamed EUG were characterized using a CMT4503 universal tensile machine (MTS Company, USA). The tensile mode was selected for the test, and the test was carried out according to the conditions specified in ISO 37:2017. The dumbbell-shaped spline working area was 6 mm wide, and the tensile speed was 500 mm min−1.
2.3.4 Impact Test
In order to evaluate the impact protection performance of the prepared materials, the impact mechanics detection system (IMDS) designed by the research group was used for testing, which could apply a fixed impact force to the material by the pendulum, and the sensor received and read the impact force value and penetration force value before and after the pendulum hit the test sample.
2.3.5 Cross-link Density Test
The cross-link density of the foamed rubber was measured using a VTMR20-010 V NMR cross-link density tester (Suzhou Niumag Analytical Instrument Corporation, China). The test was conducted under the conditions of a magnetic induction strength of 3.5 A m−1, a frequency of 15 MHz, 8000 scan repetitions, and a temperature of 25 °C. Samples were directly cut from 2 mm-thick molded sheets into pieces ≈8 mm long and 5 mm wide. These were placed at the top of a glass tube, stabilized in the magnetic field for 2–3 min, and then tested.
2.4 Scanning Electron Microscopy
The microscopic morphology of the foamed EUG was observed using an S-4800 scanning electron microscope (Hitachi, Japan). The foamed EUG were made into rectangular splines, brittle in liquid nitrogen and then sprayed with gold to observe the cross-sectional morphology.
2.5 Differential Scanning Calorimetry
The crystallization properties of the materials were analyzed using a DSC (STARe SW 13, METTLER-TOLEDO, Switzerland), and the effects of different factors on the enthalpy of the materials and the crystallization melting temperature were explored. During the test, the temperature was raised from 25 to 100 °C to eliminate the thermal history, the temperature was kept constant for 5 min, then cooled to minus 100 °C, and then kept at a constant temperature for 5 min and then raised to 100 °C to stop. The heating and cooling rates were both 10 °C min−1.
3 Results and Discussion
3.1 Research on Softening EUG Vulcanization
3.1.1 Analysis of Vulcanization and Crystallization Properties of EUG
Due to the trans-structure of EUG, it was easy to crystallize at room temperature, so it can be partially cross-linked to make it have a 3D network structure while maintaining a certain crystalline region. At this time, EUG was a shape memory material controlled by the crystallization phase transition.[26]
Figure 1 shows the vulcanization curve of EUG when the vulcanization temperature was 150 °C. The amount of sulfur gradually increased from 0.8 to 4 phr, the MH increased from 3.97 to 9.79 dNm, and the positive vulcanization time decreased from 11.25 to 2.28 min. In addition, when the amount of sulfur added was 4 phr, the rubber compound had the vulcanization reversion phenomenon, which reduced the processing safety, and the maximum torque and minimum torque difference (MH-ML) of the rubber compound increased from 2.23 to 8.21 dNm, indicating that the density of cross-linking of the EUG increased.
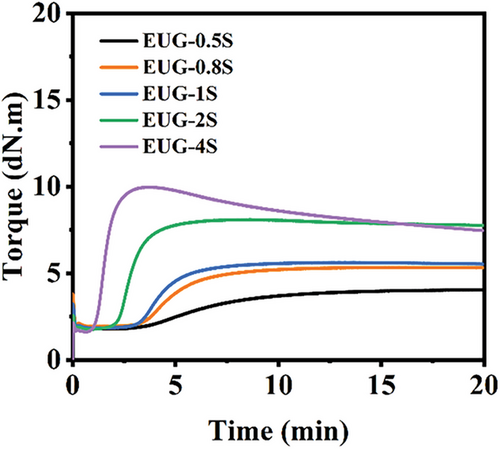
Figure 2 shows the DSC curves of vulcanized EUG and the wide-angle X-ray diffraction (XRD) patterns. As the sulfur content increased, both the crystallization temperature (Tc) and the melting temperature (Tm) shifted to lower values, while the area of the crystal melting peak gradually decreased. Correspondingly, the enthalpy changes (ΔHc and ΔHm) also decreased, indicating a reduction in the crystallization performance of the EUG. These changes suggested that the crystallization temperature of EUG could be controlled by adjusting the sulfur content, thereby influencing the shape memory properties of EUG. The XRD patterns revealed two distinct crystalline peaks at 19.4° and 23.5°. As the sulfur content increased, the intensity of these crystal diffraction peaks significantly decreased, indicating that the crystalline phase of EUG was disrupted due to cross-linking between molecular chains, which resulted in a reduction in crystallinity.
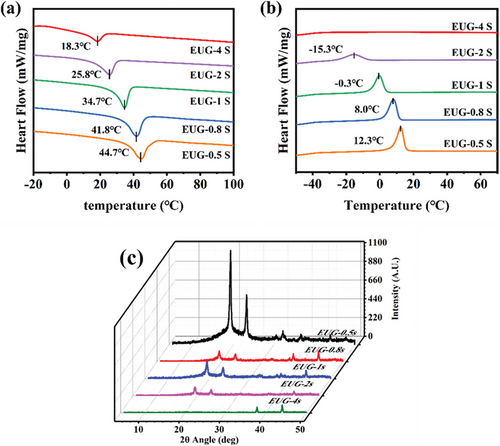
The crystallinity of EUG can be calculated by comparing the melting enthalpy of the material with the melting enthalpy of the standard crystal form and integrating the peaks of the XRD pattern, as shown in Table 2. The crystallinity calculated by the two methods was slightly different, but both showed a decreasing trend with the increase of sulfur dosage.
Sulfur /phr | 0.5 | 0.8 | 1 | 2 | 4 |
---|---|---|---|---|---|
Crystallinity (DSC) /% | 18.6 | 18.1 | 15.6 | 14.1 | 8.2 |
Crystallinity (WAXD) /% | 19.8 | 19.5 | 16.7 | 10.6 | 0 |
3.1.2 Mechanical Properties of EUG
Figure 3 shows the mechanical properties of sulfur-cross-linked EUG. As the sulfur content increased from 0.55 to 4 phr, the hardness and modulus of the material decreased gradually. At 0.8 phr sulfur, the Shore D hardness of EUG was 42°, and the Young's modulus was 94.7 MPa. At this time, the material had high hardness and shape memory characteristics; At 4 phr sulfur, the Shore D hardness of Eucommia gum was 29°, which was reduced by 33%, and the modulus was reduced to 32% of that of unvulcanized EUG, the shape memory property of the material was destroyed, but it was relatively soft, which met the requirements of softening EUG. After cross-linking and softening with sulfur, EUG was transformed from a hard-plastic state into a highly elastic rubber state, resulting in a decrease in tensile strength and an increase in elongation at break, and it was more likely to deform when subjected to external forces.
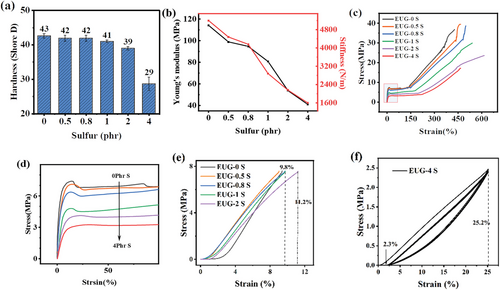
Figure 3e,f) shows the compression curve of cross-linked softened EUG, under constant stress. The compression strain of EUG with 1 phr sulfur was 9.8%. As the sulfur content increased to 2 phr, the compression strain increased by 1.4% to 11.2%; When the amount of sulfur was 4 phr, the irreversible deformation after compression was only 2%; It showed that EUG had high compressive strength and toughness.
To sum up, the test showed that EUG had excellent high hardness performance, but the reduction of its hardness by vulcanization and cross-linking could not meet the requirements of the soft lining of sports protective gear.
3.2 Physical Foaming and Softening of EUG
Vulcanization can effectively reduce the hardness of EUG, but the 3D cross-linked network structure also increases the hardness of rubber materials. The hardness of EUG cannot be infinitely reduced,[20, 27] which cannot meet the application requirements of the soft lining of sports protective gear, so the method of foaming continues to reduce the hardness of EUG.
3.2.1 Characterization and Foaming Mechanism of Physical Foaming Microspheres
Physical foaming microsphere 920DU40 was a microsphere particle with a polymer shell and a liquid alkane sandwich. Through the comparison of SEM (Figure 4a,b), it was seen that the diameter of the microspheres was approximate to 10 µm without thermal expansion, and the surface was rough; After thermal expansion, the diameter of the microspheres increased by four times up to 40 µm, with regular shapes and smooth surfaces.
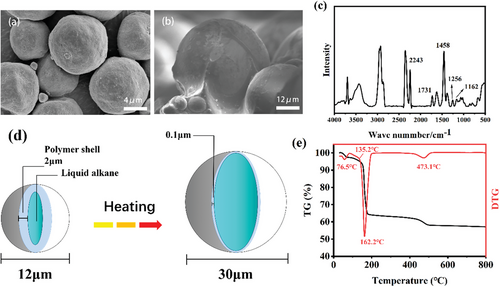
Figure 4c shows the FITR of physically foamed microspheres without thermal expansion, in the spectrum, the stretching vibration peak of R-CN at 2243 cm−1 and the bending vibration peak of C─H at 1458 cm−1 were consistent with the characteristic peaks of acrylonitrile; 1731 cm−1 represented the stretching vibration of -C═O, and 1162–1256 cm−1 was attributed to the stretching vibration of -C─C(═O), which indicated the existence of ester groups; 400–1300 cm−1 was disordered methyl absorption peak. Therefore, it was determined that the physical foamed microspheres had a shell structure composed of polyacrylonitrile and its ester polymer, and the interior of the microspheres was filled with liquid alkane.
The foaming mechanism of the foamed microspheres was attributed to their thermal expansion properties. As shown in Figure 4d, when the temperature increased, the outer shell of the microspheres became soft, and the internal liquid alkane was heated and gasified, causing the microspheres to expand; When the temperature was lowered, the polymer shell hardened and held its shape.
Figure 4e shows a Thermogravimetry Analysis (TGA) curve of the physically foamed microspheres. TGA curve showed that when the temperature was 76.5 °C, the liquid alkane in the microspheres began to vaporize and the weight began to decrease; 135.2–162.2 °C was the optimum foaming temperature range of the microspheres, when the temperature exceeded 500 °C, the polyolefin shell of the microspheres decomposed, while the silica in the foaming agent remained intact and was left as a residue. Moreover, as long as the processing temperature was suitable, the physical foaming microspheres would expand rapidly.
3.2.2 Properties of Physical Microsphere Foamed EUG
It is shown in Figure 5 that with the increase of the number of foamed microspheres, the foaming degree of EUG increased, and the density and hardness decreased significantly. When 40 phr foamed microspheres were added, the material density was reduced from 0.986 to 0.196 g cm−3 (Figure 5b), and the Shore A hardness was 67°, which was 29% lower than that of unfoamed EUG (Figure 5a). In addition, there was a cell structure inside the EUG, which led to a decrease in the tensile strength and yield strength of the material (Figure 5c,d). It was especially seen from Figure 5d, when the foamed microspheres were over 25 phr, the foamed EUG had not the elongation behavior any more, and broke at very short strain, such as 5%. It was closely related to their foamed structure.
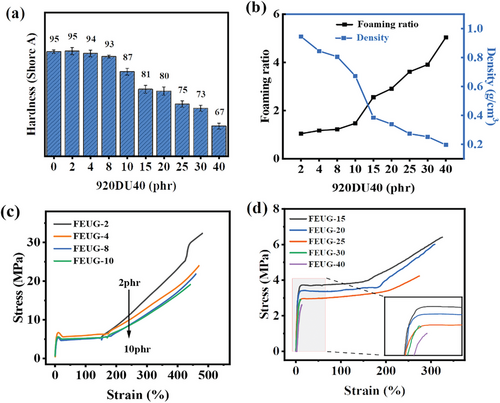
In general, the hardness and density of EUG would be effectively reduced by adding foamed microspheres, and the material would maintain a certain degree of toughness and strength, which could be used to make lightweight sports protective materials. However, the attention was paid that excess foamed microspheres would deteriorate their strength.
3.2.3 Microscopic Structure Characterization of Physical Microsphere Foamed EUG
Figure 6 shows the SEM photos of foamed EUG. It was seen that the microspheres expanded by heat were evenly distributed in the matrix of EUG. The foaming behavior of microspheres significantly affects the material's structure and properties. At low microsphere contents (2–8 phr), a “sea-island structure” is formed, with uniform microsphere dispersion maintaining the matrix's integrity and providing moderate softness. At 10–25 phr, microsphere clustering creates interconnected networks, increasing porosity and improving impact absorption. Beyond 30 phr, overcrowding leads to microsphere rupture, forming voids that weaken the material's tensile strength and elongation.
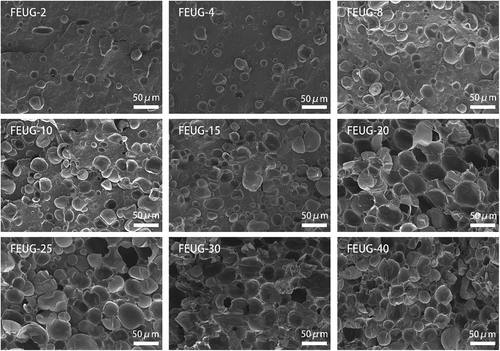
This progression, from dispersion to clustering and rupture, highlights the relationship between microsphere behavior and material performance. By fine-tuning the microsphere content, the material can be tailored to achieve an optimal balance between softness, toughness, and energy dissipation, meeting specific application requirements.
It can be known from the analysis above, under the condition of keeping the higher mechanical strength, adding 25 phr physical foamed microspheres can effectively reduce the hardness of the material, greatly improve the impact resistance of the material and extend the impact time. So, the foamed EUG material with 25 phr physical foamed microspheres (FEUG25) was very suitable to apply the sports protection field. In order verify its protection effect, the impact test was conducted to FEUG25.
Figure 7 shows the SEM photographs of the section of the FEUG25 after impacting by IMDS. It was seen from Figure 7a, after once impact, the foamed microspheres in the EUG matrix became flat and long, indicating that the microspheres played a role in absorbing and dispersing the impact energy. After being subjected to five times impacts, most of the microspheres was impacted to very flat state and some microspheres ruptured leaving holes. The impacted test showed that the foamed EUG was not suitable for using as a protective material alone, and the foamed material would deform and the internal structure would be damaged under the action of external force.
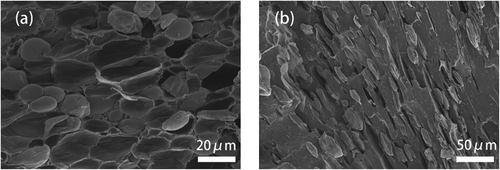
3.2.4 Effect of Sulfur Dosage on Physical Microsphere Foamed EUG
Micromorphology
Cross-linking density is a key factor to adjust the foam morphology of physical microsphere foamed EUG. Figure 8 shows a SEM photograph of FEUG25 after adding different parts of sulfur. It was seen when 0.8 phr sulfur was added, the size of the microspheres was uneven, and the average diameter was ≈65 µm. With the sulfur dosage increasing to 1.5 phr, the micromorphology microspheres were controlled by cross-linking density and their average diameters shrank to 40 µm. When the sulfur dosage increased to 2 phr, the cross-linking network limited the expansion of foamed microspheres and broke some of the microspheres. When 4 phr sulfur was added, the microspheres were broken more frequently, and the diameter shrank to 35 µm. So, 1–1.5 phr sulfur was chosen to control the foam morphology of FEUG25.
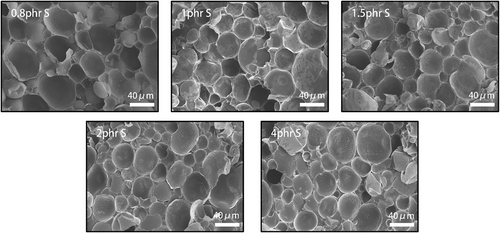
Crystallinity Analysis of Foamed EUG
The shape memory characteristics of foamed EUG were closely related to its crystallinity. Figure 9 was the DSC curve of the foamed FEUG25. It was observed that with the increase of the amount of sulfur used, both Tc and Tm of the material move to low temperature, and the crystalline melting peak area gradually decreased, and ΔHc and ΔHm decreased as well. It was seen from Table 3 that with the increase of the amount of sulfur, the crystallinity of the FEUG25 decreased slightly, indicating that the degree of crystallinity can be controlled by adjusting the amount of sulfur. Compared with unfoamed EUG, the sulfur had a little effect on the degree of crystallinity of the foamed EUG, indicating that the increased surface area of EUG through foaming was more conducive to the formation of crystals. This was very beneficial for the foamed EUG to keep the shape memory properties.
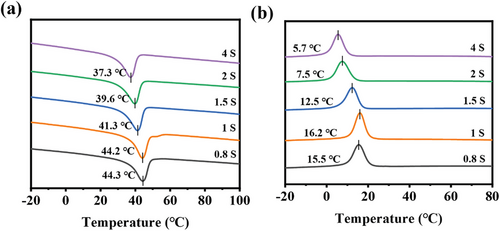
Sulfur /phr | 0.8 | 1 | 1.5 | 2 | 4 |
---|---|---|---|---|---|
Crystallinity /% | 16.2 | 15.7 | 15.5 | 15.1 | 14.7 |
Melting temperature /°C | 44.3 | 44.2 | 41.3 | 39.6 | 37.3 |
Crystallization temperature /°C | 15.5 | 16.2 | 12.5 | 7.5 | 5.7 |
Crystal Melting Enthalpy /J*g−1 | 22.9 | 22.2 | 21.9 | 21.3 | 20.7 |
Physical Properties
The mechanical properties of FEUG25 with different sulfur dosages were studied, the results were listed in Table 4. It was seen that the more sulfur was added, the lower the hardness and foaming ratio of the sample, the higher the density and the cross-linking density. The reason was that when the amount of sulfur was small, the EUG was just in the low cross-linking density stage, the viscosity of the FEUG25 was low, and the microspheres were easy to expand; The increase of the sulfur amount would increase the viscosity of FEUG25, which would limit the expansion of the microspheres, resulting in a decrease of the foaming extent of FEUG25. The hardness of the material was controlled by the competitive relationship between the degree of crystallization and the degree of foaming. Therefore, under the two factors, as the amount of sulfur increased, although the foaming ratio did not increase, the hardness decreased. It indicated that the degree of crystallization had more influence on the hardness. For example, when 4 phr sulfur was used, the degree of crystallization decreased 9.3%, however, the foaming ratio decreased 19.4%, as a result the Shore A hardness of the FEUG25 decreased to 68, and did not increase because of the decrease of the foaming ratio.
Sulfur /phr | 0.8 | 1 | 1.5 | 2 | 4 |
---|---|---|---|---|---|
Density /g*cm−3 | 0.273 | 0.28 | 0.29 | 0.318 | 0.336 |
Foaming ratio | 3.6 | 3.5 | 3.3 | 3.1 | 2.9 |
Cross-link density /*E-4mol*mL−1 | 1.72 | 1.80 | 1.89 | 1.94 | 2.00 |
Hardness/ Shore A | 75 | 74 | 72 | 71 | 68 |
Figure 10 shows the mechanical properties of FEUG25, from Figure 10a, it was seen that, with the increase in the amount of sulfur used, the stress–strain curve of FEUG25 became higher and longer. Therefore, the Young's modulus and stiffness of FEUG25 increased greatly, as shown in Figure 10b. When the amount of sulfur was 0.8 phr, the sample only bore the tensile stress of 1.6 MPa, and the modulus was 25.6 MPa; while when the amount of sulfur was 4 phr, the tensile strength of the sample was increased to 3.52 MPa, and the modulus was increased to 43 .78MPa. In addition, the stiffness increased greatly as well, which would increase the resistance to deformation capacity.
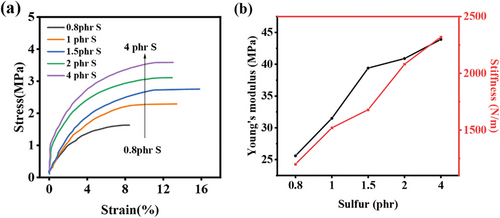
3.3 Soft-Hard Gradient Composited Material of EUG
3.3.1 Vulcanization Properties
Through the integrated co-vulcanization process, the foamed EUG and EUG were used as inner and outer layers, and a layer of soft natural rubber or softened EUG with high cross-linking degree was sandwiched in the middle to prepare a soft-hard gradient composite material. The prepared material had a multi-level hardness gradient, and the preparation process is simplified and the cost is reduced without the use of adhesives.
Figure 11 shows the vulcanization curves of the three selected materials. From the curves, it was seen that the amount of sulfur in the EUG needed to be controlled to maintain good shape memory properties, resulting in a slightly longer positive vulcanization time. The positive vulcanization time of natural rubber and foamed EUG was basically the same, and the three materials had no vulcanization reversion after long-term vulcanization, which indicated that they had the basis of co-vulcanization.
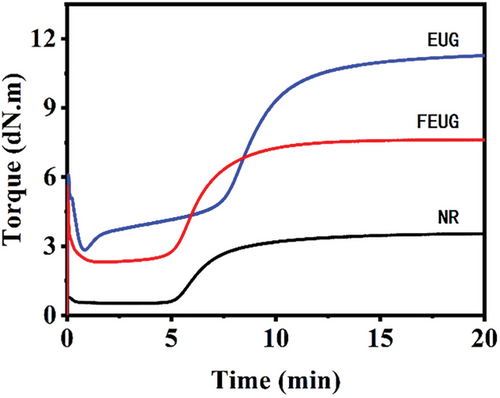
EUG and natural rubber were prepared into a double-layer hardness gradient material by co-vulcanization process, and then further co-vulcanized EUG, natural rubber and physical foaming EUG to prepare a three-hardness gradient material, as shown in Figure 12.
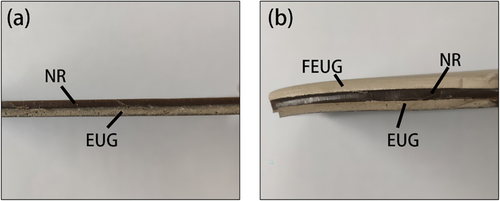
3.3.2 Microscopic Characterization
Figure 13 shows a scanning electron microscope photo of the prepared three-hardness gradient composite material, and the cross-sections of the three materials with different hardness showed different morphologies. Among them, the left side was EUG, the cross-section was relatively rough and there were large bumps, which indicated that the liquid nitrogen brittle cross-section of EUG was uneven surface because of the toughness caused by low glass transition temperature; the right was the FEUG25, and the expanded foamed microspheres distributed closely in EUG matrix; The middle was natural rubber, the cross-section near the EUG was relatively flat, only a transition region was visible and no obvious interface was visible. On the contrary, interface between the FEUG25 and NR was visible clearly. The rough surface of FEUG25 contributed the interface, even the two materials were co-vulcanized into an integral whole. These two interfaces would be observed clearly by Figure 14.
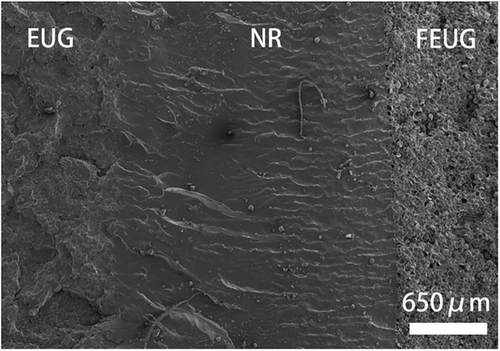
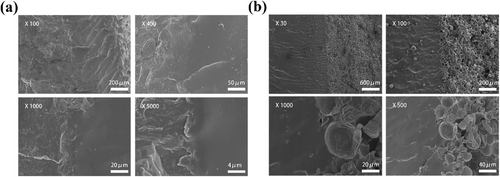
Figure 14a shows a SEM photo of the interface between EUG and NR. The boundary between the two rubbers was relatively blurred, and there was a thin shadow at the interface. This indicated that during the vulcanization process, the molecular chains of EUG and NR formed a cross-linked network under the action of the cross-linking agent.
Figure 14b shows the interface between NR and FEUG25. There were a large number of microspheres that are thermally expanded at the interface between the two materials, and the interface was relatively clear.
3.3.3 Mechanical Properties
Peeling is one of the common failure forms of rubber joint.[28] The 180° peel strength test was carried out on the hardness gradient composite material, and the maximum peel strength of EUG and natural rubber was measured to be 2.71±0.12N mm−1. And under the action of external force, the natural rubber broke after reaching the stress limit, but there was no peeling phenomenon between the EUG and the natural rubber (Figure 15a). The maximum peel strength of the interface between the NR and the FEUG25 was 1.82±0.04N mm−1, and the interface peeling phenomenon occurred. This test indicated that the interaction force between FEUG25 and NR was far weaker than that of EUG and NR (Figure 15b), although both formed by vulcanization bond. The main reason was that contacted area between FEUG25 and NR was smaller than that of EUG and NR.
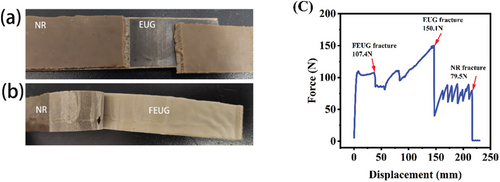
Tensile tests were carried out on the prepared three-hardness gradient EUG composites, and the tensile properties and performance of the samples were characterized by force–displacement curves, as shown in Figure 15c. Since the resistance to external force was mainly dominated by the EUG with a larger modulus, the composite material would also have a certain yield phenomenon. Subsequently, the physical foaming EUG with relatively weak mechanical properties broke at the displacement of 36.7 mm, the EUG broke at the displacement of 146.4 mm, and at the displacement of 216.2 mm, the NR finally broke, and the entire composite material was completely broken.
Although the total strain of the material was only 46.8% when the foamed EUG broke, toke the impact-resistant protective gear for example, the entire protective gear would not reach such a high strain. At the same time, due to the integrated co-vulcanization process, the connection between different materials was tight, the overall structure of the composite material can be kept intact, and the protective performance would not be greatly affected.
3.4 Study on Impact Resistance
Through impact mechanics testing, the relationship between the mechanical response of the sample and the time change would be tested when the material was subjected to an external instantaneous impact force, and its impact protection performance could be evaluated. Figure 16a shows the impact mechanical testing data of EUG and foamed EUG with different degrees of vulcanization. The maximum impact force transmitted the unvulcanized EUG was 276.5N, and the duration of impact force transmission was 2 .7ms. When 4phr sulfur was added, the maximum impact force transmitted the material was 166.8N, and the impact force transmission duration was 3 .7ms. At this time, the material can reduce the external impact force by 74.3%.
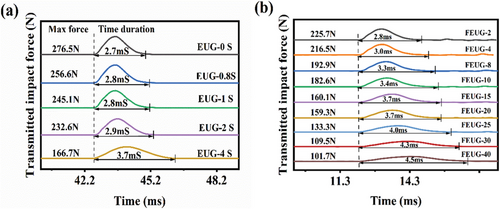
Figure 16b were the impact mechanics test curves of microsphere foamed EUG with the increase of foamed microspheres, it was seen that the maximum impact force transmitted by the material decreased and the impact time prolonged, which meant that the impact protection performance was improved. When the foamed microspheres were 25 phr, the foamed EUG reduced the external impact force by 79.5%, and the impact force transmission duration was 4 .0ms. When the foamed microspheres were 30 phr, the material reduced the external impact force by 83.2%, the force transfer duration was 4 .3ms.
The impact mechanical testing test was carried out on the prepared soft-hard gradient composite material. It should be noted that the thickness of the test sample was 7 mm, which was 56% of the thickness of the cross-linked softened EUG sample. Among them, the thickness of EUG was 2 mm, the thickness of NR was 2 mm, and the thickness of physical microsphere foamed EUG was 3 mm.
According to Figure 17, after the first impact, the soft-hard gradient composite reduced the external impact force by 81.3%, The material in unit thickness reduced the impact force by 11.6%, while the foamed EUG in unit thickness reduced the impact force by 6.4%. It was seen that the impact protection performance of the composite material was significantly improved. The same point was subjected to multiple impact tests. With the increase of the number of impacts, the maximum impact force transmitted the material increased and the response time shortened, which indicated that the protective performance would decrease to a certain extent when subjected to multiple impacts. The reason was that the pendulum would decrease the thickness by hitting the same spot continuously, such as five times. As a result, the impact force transmitted the material would increase and the force transfer duration decrease.
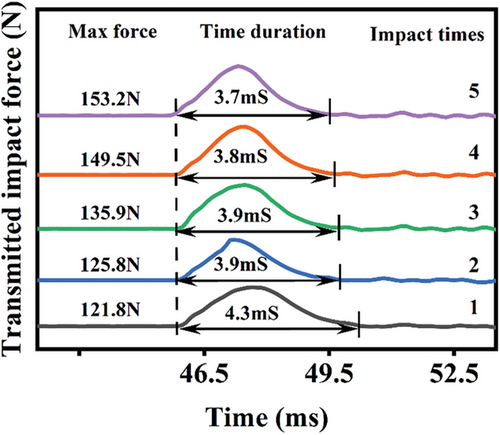
3.5 Characterization of Shape Memory Performance
The shape memory properties of the EUG composites were investigated. First, the samples were folded into U shape at a temperature of 65 °C and cooled to room temperature to fix the shape, as shown in Figure 18. It was seen that the shape changes of different EUG composites heated to 65 °C once again. Due to the good elasticity of natural rubber, it tokes 18s for the EUG-NR composite to return to the unfolded state, as shown in Figure 18a. The foamed EUG would soften immediately after being heated, and it toke 14s for the EUG-foamed-NR composite to recover from the temporary shape to the unfolded state, as shown in Figure 18b. The soft-hard gradient composite material of EUG was thick, and it toke ≈30s to restore the shape to the original unfolded state at 65 °C. This composite material still had good shape memory properties after co-vulcanization, which was beneficial to the preparation and application of sports protective gear in the future.
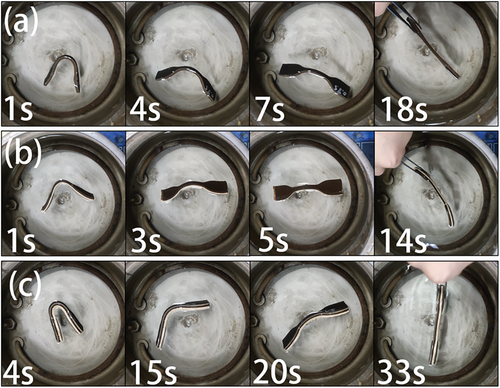
4 Conclusion
This study developed soft EUG materials by regulating cross-linking density and introducing microsphere foaming. The results highlighted that increasing sulfur reduced crystallinity, hardness, and modulus, enhancing elasticity. At 4 phr sulfur, EUG reached a Shore D hardness of 38 and a modulus of 41 MPa.
Foaming with microspheres further softened EUG, lowering its density and hardness while improving energy absorption. At 25 phr microspheres and 1.5 phr sulfur, the material achieved a density of 0.28 g cm−3 and reduced impact forces by up to 83.2%.
Finally, combining EUG, foamed EUG, and NR through co-vulcanization produced a soft-hard gradient composite with strong interfacial adhesion and shape memory functionality, ideal for sports protection applications.
Acknowledgements
The authors are deeply grateful to the financial support granted by the National Key Research and Development Program of China and the National Natural Science Foundation of China (Grant no. 2022YFB3704800, 2022YFB3704804, 52273051, and 52221006).
Conflict of Interest
The authors declare no conflict of interest.
Open Research
Data Availability Statement
The data that support the findings of this study are available from the corresponding author upon reasonable request.