Poly(Butylene Adipate-Co-Terephthalate)/Silane-Treated Wollastonite-Based Blown Film for Sustainable Packaging Application: Studying the Impact of Uniaxial Stretching on the Final Properties
Abstract
The demand for biodegradable packaging is rising due to plastic pollution corncerns. This study develops biodegradable composites based on poly (butylene adipate-co-terephthalate) (PBAT) and silane-treated wollastonite (S-W) at two concentrations (15 and 25 wt%) through a combination of melt extrusion and blow-film extrusion techniques. Next, the PBAT/S-W composite films underwent uniaxial stretching in the machine direction (MD) to study the effects on their morphology, mechanical and thermal properties, barrier performance, contact angle, and X-ray diffraction (XRD) at different stretch ratios (SR). The incorporation of S-W at 15 wt% increased the mechanical properties, achieving ≈500% for tensile strength and 1000% for Young's modulus for SR6. Thermal and XRD analyses demonstrated that uniaxial stretching significantly enhanced film crystallinity because of strain-induced crystallization. Morphological analysis indicated two opposing effects at high SR: a pronounced alignment of molecular chains in the MD and weak adhesion between the filler and polymer matrix, which can impact the material's structural integrity. The water vapor barrier properties of the PBAT/S-W25% blown film at SR6 exhibited a remarkable 42% improvement compared to the unstretched version. This advancement, resulting from the elevated crystallinity, establishes PBAT/S-W as a viable eco-friendly substitute for single-use plastics in the field of biodegradable packaging.
1 Introduction
Petrochemical-based plastics dominate the packaging industry due to their superior mechanical and physicochemical properties. However, their non-biodegradable nature leads to the accumulation of millions of tons of plastic waste, exacerbating the global environmental crisis. Studies estimate that global plastic waste emissions are ≈52.1 million metric tons annually, with 57% being openly burned and 43% remaining as unburned debris.[1] When factoring in projected population growth, per capita waste generation, plastic content in waste, and inadequate waste management, it is predicted that plastic emissions entering aquatic ecosystems could reach 53 million metric tons annually by 2030, even with current government efforts.[2, 3] In 2019, plastic packaging was the largest contributor to global plastic waste, making up ≈46% of the total.[4] The food packaging sector, in particular, is by far the largest consumer of plastic packaging materials.[5, 6] Although recycling initiatives are prevalent, issues like contamination and the deterioration of polymer characteristics result in only 9% of plastic waste being recycled, 12% being incinerated, and a staggering 79% being deposited in oceans, landfills, and other ecosystems.[7]
To tackle this pressing issue, utilizing biodegradable and bio-based polymers presents a promising solution that can improve recycling efforts and contribute to a sustainable future.[8] One such polymer, poly(butylene adipate-co-terephthalate) (PBAT), has garnered significant attention as a potential substitute for traditional plastics.[9] It is particularly suited for packaging applications, including lawn waste bags, food containers, and film wraps, among others. The demand for PBAT is anticipated to rise steadily, fueled by consumer preferences for environmentally friendly packaging and strict government regulations targeting non-biodegradable plastics.[10] PBAT is synthesized from adipic acid and terephthalic acid as the acid comonomers, along with 1,4-butanediol as the diol comonomer.[11] The production process begins with the formation of oligomeric esters in a pre-condensation reactor utilizing a titanium-based catalyst. This is followed by polymerization through polycondensation under high vacuum conditions.[12] According to various standard tests, PBAT is home and industrial compostable, achieving complete disintegration within 7 weeks.[13] Despite its biodegradability, PBAT is significantly limited by its inferior thermal, mechanical, and barrier properties compared to low-density polyethylene (LDPE), as evidenced by its Young's modulus, which is only 33% that of LDPE.[14] Consequently, this limitation has hindered its widespread use in packaging.[15]
Extensive research has been dedicated to optimizing the utilization of PBAT to achieve properties comparable to those of traditional plastics. These strategies involve blending PBAT with other polymers,[16, 17] grafting it onto various materials,[18] and integrating reinforcements into the PBAT matrix.[19-21] Traditional fillers like glass fiber, calcium carbonate, and talc are effective in producing materials that are both strong and lightweight.[22, 23] However, wollastonite, a calcium metasilicate (CaSiO3) mineral, is gaining attention as a potential substitute, as it provides advantages such as reduced mold shrinkage and enhanced dimensional stability, owing to its inherently low coefficients of thermal expansion and low-cost.[24, 25] Research has shown that wollastonite significantly enhances not only Young's modulus and tensile strength,[26] but also positively influences hardness and impact strength in semi-crystalline polymers.[27] Additionally, it plays a crucial role in promoting crystallinity.[28] Like other silicate minerals, wollastonite particles tend to readily attract hydroxyl groups from water, which can influence their coupling efficiency with non-polar polymers. To address this issue, surface treatments of wollastonite particles are commonly employed. These treatments are generally categorized into two types: non-coupling treatments and coupling treatments.[29] This chemical procedure entails incorporating a coupling agent into the mineral filler, thereby altering its surface characteristics. The coupling agent acts as a connector between the matrix and the filler, enhancing their interaction and overall compatibility.[30]
Blown film extrusion is the leading industrial process for manufacturing plastic films for packaging, as it effectively aligns molecular chains, resulting in films with superior puncture resistance.[31] The stretching process adds significant value to blown or cast films by improving their mechanical, optical, and barrier properties through the precise alignment of polymer chains via heating, drawing, and cooling.[32] Stretching achieves superior chain orientation and alignment compared to traditional methods, and adjusting the stretching ratio (SR) allows for further optimization, resulting in enhanced strength and tensile modulus in the oriented direction of the film.[33] This shows a direct correlation between stretching, crystallinity levels, and the enhancement of water and gas barrier properties.[34, 35] For example, a study has shown that stretching PBAT and poly(lactic acid) (PLA) blends significantly increased the crystallinity of PLA from 6% to 58.6%. Additionally, the oxygen permeability of the PLA/PBAT binary blend at a 75/25 ratio decreased by 22% compared to unstretched (UNST) films.[36] A comparable effect was observed in PBAT/MXene nanosheet composites, where biaxial stretching reduced the water vapor permeability rate (WVPR) to 732 cc/m2·day and the oxygen transmission rate to 6.5 g m−2·day.[37] Other studies have reported comparable findings.[38, 39]
This study advances the field by combining silane-treated wollastonite (S-W), which enhances filler-polymer compatibility, with uniaxial stretching to improve the mechanical properties, barrier performance, and crystallinity of PBAT films. While previous research has examined these factors individually, their combined effects on PBAT films have yet to be explored, making this a novel contribution to the development of biodegradable packaging materials. To address this knowledge gap, this study aims to develop PBAT composites by incorporating S-W alongside film orientation techniques. The addition of S-W (15 and 25wt%) is intended to assess its influence on the films' thermal, mechanical, barrier, and structural properties of PBAT blow films, as well as its potential to serve as a substitute for traditional plastics.
2 Experimental Section
2.1 Materials
PBAT pellets, identified as film grade TH801T, were sourced from Xinjiang Blueridge Tunhe Polyester Co., Ltd. The technical data sheet indicates that the melt flow index ranges from 2.5 to 4.5 g/10 min. S-W was obtained from Dalian Hexin New Material Technology Co., Ltd., Liaoning, China, while the silica gel was supplied by Sigma–Aldrich, Canada.
2.2 PBAT/S-W Composites via Extrusion
Using a Micro-27 co-rotating twin-screw extruder from Leistritz Advanced Technologies Corporation (USA), two unique pellet formulations were created from PBAT/S-W-based composites. Two composites of PBAT and S-W, containing 15 wt% and 25 wt% of S-W, were accurately weighed and thoroughly mixed in zip-lock bags to ensure uniformity. The resulting mixtures were then introduced into the extruder feeder at 8 kg h−1. The temperature profile of the extruder was maintained at 150, 155, 160, 160, 160, 160, 160, 160, 160, 160, and 160 °C, while the screw speed was set to 100 rpm. After cooling the polymer melted in a water bath, and the pellets were dried and processed into pellet form. The moisture content was subsequently measured, and after drying overnight in an oven at 65 °C, the pellets were sealed and stored in aluminum bags.
2.3 PBAT/S-W Composite Blow Films
The production of PBAT/S-W composite films via blown film extrusion was performed using a Collins Blown Extrusion Machine from Collin Lab & Pilot Solutions, Inc. (USA). The extruder operated at various temperatures—30, 155, 160, 165, and 170 °C—across five distinct zones, while maintaining a screw speed of 50 rpm. The die temperature remained stable at 160 °C. After the polymer exited the die, the bubble was expanded to 33% and drawn by take-up rollers moving at a rate of 1.5 m min−1, producing a thin film that was then rolled onto a winder. Nip rollers were used to flatten the bubble before it was collected by the take-up rollers. Throughout the extrusion process, the film was elongated in the machine direction (MD) by the rollers, while the inflation phase stretched it in the transverse direction (TD). Figure 1 illustrates the complete film production process, showcasing both orientations. Table 1 lists the formulations developed in this study along with their respective SR.
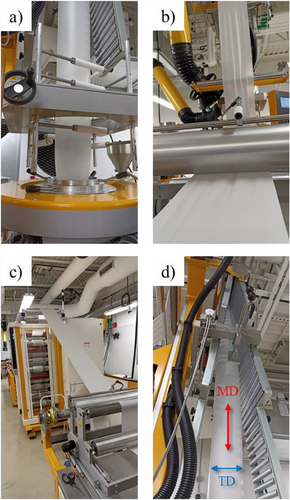
Nomenclature sample | Stretch ratio (SR) | Identification | PBAT [wt.%] | S-W[wt.%] | BUR | DDR |
---|---|---|---|---|---|---|
PBAT/S-W15% | Unstretched (UNST) | PBAT/S-W15% UNST | 85 | 15 | 2.31 | 4.11 |
2 | PBAT/S-W15% SR 2 | |||||
4 | PBAT/S-W15% SR 4 | |||||
6 | PBAT/S-W15% SR 6 | |||||
PBAT/S-W25% | Unstretched (UNST) | PBAT/S-W25% UNST | 75 | 25 | 2.35 | 3.96 |
2 | PBAT/S-W25% SR 2 | |||||
4 | PBAT/S-W25% SR 4 | |||||
6 | PBAT/S-W25% SR 6 |
2.4 PBAT/S-W-Based Composite Characterization
2.4.1 Mechanical Properties
The tensile properties of the films were evaluated using a universal testing machine (Instron 3382, USA) in compliance with ASTM D882 standards. Film thickness was measured with a dial thickness gauge (7301, Japan) with an accuracy of 0.01 mm, and an average of five measurements per sample was recorded. For films exhibiting an elongation at break (ε) above 100%, the grip separation was set to 50 mm, and the crosshead speed to 500 mm min−1. For films with ε between 20% and 100%, these values were adjusted to 100 mm and 50 mm min−1, respectively, following ASTM D882 specifications. Each formulation was tested with ten samples, and the results were reported as the mean ± standard deviation (SD).
2.4.2 Differential Scanning Calorimetry (DSC)
2.4.3 Scanning Electron Microscopy (SEM)
The morphology of the blown film specimens was examined with a scanning electron microscope (SEM) (Phenom Pro X, Netherlands) at a voltage of 10 kV, employing magnifications of 1200×, 2000x, and 3000×. To prepare for the SEM imaging, the samples underwent cryo-fracturing by being submerged in liquid nitrogen, which allowed for the visualization of the cross-section. Film samples that were aligned in the MD were secured onto an aluminum stub using double-sided carbon tape and subsequently coated with gold via a sputter coater to reduce the effects of electrical charging during the imaging process.
2.4.4 X-Ray Diffraction Spectroscopy
2.4.5 Barrier Properties
Within this framework, WVTR represents the speed at which water vapor moves through the film (g m−2·d), T refers to the average film thickness (mm), and ΔP signifies the difference in partial vapor pressure (KPa) between the two surfaces of the film.
2.4.6 Contact Angle and Surface Tension
The water and diiodomethane contact angle of the PBAT/S-W composite films was assessed using a Rame-hart standard goniometer with a super speed digital camera (260-U1, USA). Specimens were cut into 2 × 2 cm2 pieces and placed on the instrument's sample holder. A glass syringe, part of the goniometer setup, dispensed 5 µL water or diiodomethane droplets onto the specimen surface, allowing it to sit for ≈10 s. DROP image advanced software measured the contact angles on both sides of the droplet. The analysis was conducted with a resolution of ±0.01°, accuracy of ±0.1°, and a stage angle set at 0°. Measurements were taken from three different areas of each composite film. This test was performed by triplicate and the results were reported as average ±SD.
Liquid | Γ | γp | γd |
---|---|---|---|
Water | 72.8 | 51.0 | 21.8 |
Diiodimethane | 50.8 | 0.0 | 50.8 |
Using the measured contact angles for the two liquids and their known surface tension values (𝛾𝑙, , and ) as shown in Table 2, Equations (7) and (8) transform into a system of two equations with two unknowns ( and ). DROP image advanced software calculated the surface tension of these PBAT/S-W blown films.
3 Results and Discussion
3.1 Mechanical Properties
In packaging applications, the strength of the film is crucial for its mechanical durability during paving or handling, which affects its overall integrity and functionality.[49] This work aimed to develop cost-effective biodegradable films with strong mechanical performance. To evaluate how different PBAT/S-W formulations affect the mechanical properties, tensile tests were conducted on all film samples. These tests measured the tensile strength (TS), Young's Modulus (YM), and ε in both directions: MD and TD, across all SR ranges. The results are summarized in Figure 2. The mechanical data for the PBAT/S-W formulations are provided in Tables S1 and S2 (Supporting Information).
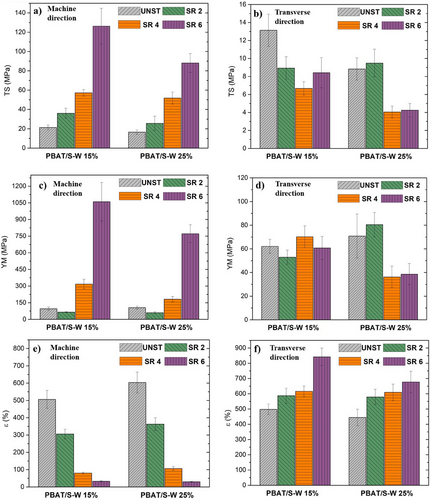
In a previous study,[31] we analyzed the mechanical properties of neat PBAT films processed under conditions similar to those used in this work. TS, YM, and ε were reported as 35 MPa, 37 MPa, and 520% in the MD, and 27 MPa, 18 MPa, and 716% in the TD, respectively. After the addition of 15 and 25wt% of S-W particles, the TS was decreased to 21 and 17 MPa along MD for UNST samples, respectively (Figure 2a). This phenomenon may result from inadequate interfacial bonding between the S-W particles and the PBAT matrix, hindering the effective transfer of stress from the matrix to the S-W particles. Similar results were found by Botta and collaborators,[50] who developed bio-composite blown films based on PBAT and biochar as filler. The authors reported a continuous decrease in TS as the filler content increased, with an approximate reduction of 70% when 20% of the filler was added.
When PBAT/S-W-based composite films were stretched along the MD, the TS increased significantly. Specifically, TS improved from 21 MPa to 126 MPa when 15 wt% of filler was added to the PBAT matrix, as the blown films reached SR 6, representing an increase of 500% (Figure 2a). The same trend was observed for PBAT/S-W25% samples, where TS increased with SR, rising from 17 MPa to 26 MPa, 52 MPa, and 88 MPa as the SR increased from UNST to SR 2, SR 4, and SR 6, respectively. Unlike TS in the MD, this parameter showed a decrease in SR with an increase in TD, reaching its lowest value at SR 4, 7 MPa, and 4 MPa for 15 and 25wt% samples, respectively (Figure 2b). Uniaxial orientation along the MD is believed to reduce molecular chain alignment in the TD, causing a deterioration in mechanical properties. Fereyddon et al.[51] describe this phenomenon as “restricted uniaxial stretching,” in which the molecular chains remain fixed in the TD while uniaxial stretching takes place along MD.
On the other hand, the YM parameter showed a significant increase in their value, in comparison with neat PBAT, after the incorporation of 15 and 25wt% of S-W particles in MD; increasing from 37 MPa to 96 and 106 MPa for UNST samples, respectively (Figure 2c). The maximum values obtained for machine stretch orientation were both at SR 6, with 1060 MPa and 771 MPa for 15 and 25 wt%, respectively. As previously noted, adding a filler to the continuous phase can reduce the mobility of polymer chains, leading to an increase in YM. The same parameter also showed an increase in the TD compared with neat PBAT (Figure 2d). For TD, YM did not exhibit the expected correlation with SR, as no significant differences were observed in the samples with 15 wt% loading.
According to Luoma et al.,[52] the process of orientation significantly improved the stiffness and strength of polymeric matrix films compared to unoriented control samples. Orientation in the MD is more effective in enhancing mechanical strength and stiffness than TD orientation, as crystallites and chain polymers align in the direction of the applied stretch. This alignment results in MD-oriented films exhibiting considerable differences in mechanical properties between the TD and the MD. In this sense, the ε parameter showed completely different results for machine and transverse orientations (Figure 2e,f). Compared to UNST samples, the ε parameter decreased as SR increased in the MD. For example, when 15 wt% of S-W was added to the PBAT matrix, ε reduced from 510% for the UNST sample to 33% for the SR 6 sample (Figure 2e). A similar behavior was observed for the PBAT/S-W25wt% samples, resulting in a reduction of the ε parameter by almost 95%, indicating a transition from a ductile to a brittle nature (Figure 2e). Unlike the trends observed in the MD, this parameter reached higher values for transverse orientation as SR increased. Specifically, it increased from 498% for the UNST sample to 842% for the SR 6 sample in PBAT/S-W15wt% samples, and from 445% for the UNST sample to 677% for the SR 6 sample in PBAT/S-W25wt% samples (Figure 2f). This behavior was previously explained by the phenomenon known as “restricted uniaxial stretching”.
Itabana and coworkers[31] investigated biodegradable composites based on PBAT and talc with 15 and 25 wt% filler contents and reported similar mechanical results. In this study, utilizing S-W particles as inorganic fillers, we observed significant improvements in parameters such as YM for UNST samples and ε across all SR samples. For instance, PBAT with 25 wt% talc particles exhibited ≈475% elongation for the UNST sample, compared to almost 605% for the PBAT/S-W25% UNST sample. The primary distinction between these two types of inorganic fillers lies in their shapes (Scanning Electron Microscopy (SEM), Section 3.3), which markedly influences their performance. In this context, the distinct shapes of inorganic fillers lead to varied distributions within the polymeric matrix, resulting in different mechanical properties.
3.2 Differential Scanning Calorimetry (DSC)
DSC was primarily employed to quantify the crystalline phase content in the samples and to conduct a qualitative analysis of their thermal properties. Table 3 presents the DSC heating data for PBAT/S-W composite films, emphasizing the rise in XCDSC (%), which was derived from the heat of melting noted during the initial heating cycle (as shown in Equation 3).
Formulation | Tg [°C] | Tc [°C] | ΔHcrys [J g−1] | Tm [°C] | ΔHmelt [J g−1] | XCDSC [%] |
---|---|---|---|---|---|---|
PBAT/S-W15% UNST | −29.8 ± 0.5 | 76.0 ± 0.0 | 14.6 ± 0.0 | 118.2 ± 1.8 | 11.0 ± 0.4 | 11.4 ± 0.5 |
PBAT/S-W15% SR 2 | −25.3 ± 2.8 | 75.8 ± 0.0 | 16.1 ± 1.0 | 113.6 ± 2.7 | 12.1 ± 0.8 | 12.4 ± 0.9 |
PBAT/S-W15% SR 4 | −28.3 ± 3.2 | 75.4 ± 0.2 | 16.0 ± 0.2 | 118.1 ± 3.7 | 12.3 ± 1.9 | 12.7 ± 2.0 |
PBAT/S-W15% SR 6 | −34.1 ± 0.5 | 78.3 ± 3.1 | 14.8 ± 1.2 | 110.0 ± 0.9 | 16.9 ± 1.0 | 17.4 ± 1.0 |
PBAT/S-W25% UNST | −29.4 ± 0.0 | 76.2 ± 0.0 | 12.1 ± 0.9 | 118.1 ± 0.1 | 9.7 ± 1.3 | 11.3 ± 1.6 |
PBAT/S-W25% SR 2 | −28.6 ± 0.8 | 76.2 ± 0.2 | 14.9 ± 1.5 | 115.1 ± 0.8 | 12.4 ± 2.4 | 14.5 ± 2.8 |
PBAT/S-W25% SR 4 | −23.6 ± 2.2 | 76.2 ± 0.0 | 15.1 ± 0.2 | 110.9 ± 2.3 | 19.1 ± 1.7 | 22.3 ± 2.0 |
PBAT/S-W25% SR 6 | −19.7 ± 0.6 | 76.6 ± 0.0 | 15.5 ± 0.0 | 115.2 ± 1.4 | 22.0 ± 0.6 | 25.8 ± 0.7 |
During the first heating cycle, the glass transition temperature (Tg) of the PBAT/S-W composite UNST films (15 and 25wt%) was found to range from ≈−30 °C (Table 3; Figure S1, Supporting Information). In this direction, the presence of S-W particles did not affect the Tg, Tm, and Tc values in comparison with the neat PBAT sample.[31] Moustafa and colleagues[53] studied bio-composites based on PBAT and coffee grounds with different filler contents, ranging from 0 to 50 wt%. The authors found that the Tg of the PBAT matrix remained unchanged with the addition of reinforcements up to 20 wt%, and this same trend was observed for Tm and Tc. For PBAT/S-W 25 wt% samples, the Tg decreased from ≈−30 to −20 °C when the sample reached SR 6 (Table 2; Figure S1, Supporting Information). The other thermal properties, such as Tm and Tc, did not show significant changes with uniaxial stretching along different SR samples (Figure S1, Supporting Information). Particularly, the Tg parameter is influenced by various factors such as intermolecular interactions, chain flexibility, branching, and molecular weight, making it a complex and dynamic property.[54]
According to our previous work, the Xc of neat PBAT was ≈11%.[31] With the addition of 25 wt% talc, this value increased to about 17%, demonstrating the good nucleating property of the filler. In this study, however, the incorporation of S-W particles at two different weight contents did not exhibit the same nucleation efficiency. Ding and co-authors[55] demonstrated that incorporating inorganic particles can significantly influence the crystallization and mechanical properties of the polymer matrix. This impact is primarily attributed to two key factors: the morphology and composition of S-W particles. In a study conducted by Liang et al.,[56] the effect of incorporating wollastonite particles into polypropylene (PP) at concentrations ranging from 0 to 40 wt% was investigated. The authors observed that the Xc increased slightly at weight fractions below 30 wt%, followed by a significant rise at higher concentrations, highlighting the pronounced impact of wollastonite particles on the crystallization behavior of PP.
Through uniaxial stretching, Xc of PBAT with 15 and 25% S-W increased steadily, attaining ≈17 and 26% in the SR 6 sample, respectively (Table 3). The DSC thermograms (Figure S1, Supporting Information) clearly show that as the SR increased, the breadth of the ΔHmelt broadened, leading to a corresponding increase in Xc. Onyishi and Oluah[57] examined how the crystallinity and mechanical properties of biaxially stretched polyethylene terephthalate (PET) varied with different SR. The authors found that Xc increased from roughly 6% for PET to ≈35% following biaxial stretching to an SR of 4.0 and 100 °C. This demonstrates a clear relationship between the SR and the level of induced crystallinity. This effect might be explained by strain-induced crystallization, which generates additional crystallization sites.[58] This pattern can be further correlated with the XRD findings discussed in Section 3.4.
3.3 Scanning Electron Microscopy (SEM)
SEM was used to observe the microstructures of PBAT/S-W composites to understand their morphological transformations during the uniaxial stretching process. These observations are presented in Figure 3. In the PBAT/S-W UNST unoriented control films, the S-W particles are successfully dispersed and distributed within the polymer matrix across various weight percentages, exhibiting different sizes, no acicular (needle-like) shapes, and no agglomerations (Figure 3a,c). However, the visible voids observed in both UNST and SR 6 samples, particularly around the polymer matrix and S-W particles, underscores inadequate adhesion between these components. This indicates an area for improvement in composite material performance. The formation of these voids, especially in samples with high SR, is likely due to the detachment of S-W from the fracture surface. This detachment is driven by the transmission of fracture stress along the equatorial axis, leading to gaps between the particles and the polymer matrix.[59]
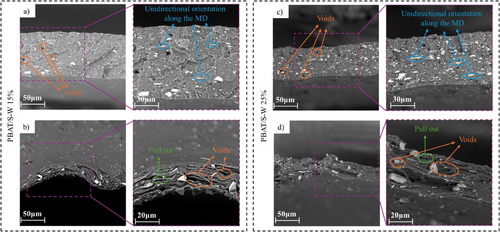
Upon stretching, three distinct effects become evident: 1) film thinning, 2) alignment of S-W particles and polymer chains in the MD (Figure S2, Supporting information), and 3) an increase in voids and particle pullouts as the SR increases. In particular, the first effect is more pronounced for the PBAT/S-W composite with 15 wt% of S-W particles. When the SR increased to 4 (Figure S2a, Supporting information), the film's thickness decreased by almost threefold compared to the UNST counterpart (Figure 3a). The same behavior can be observed for PBAT/S-W25% when comparing the UNST sample (Figure 3c) with PBAT/S-W25% at the highest SR value, i.e., SR 6 (Figure S2c, Supporting information). A higher filler loading in the polymer matrix imposes greater restrictions on the stretching of polymer chains, thereby effectively maintaining the size of the sample.[31] The second effect is also easier to visualize when PBAT/S-W samples reach the highest SR values (Figure 3b,d). The S-W particles and polymer chains align along the MD at high SR, resulting in increased crystallinity. This alignment enhances both mechanical properties (section 3.1) and water barrier performance (section 3.5) compared to the UNST counterparts. The uniaxial stretching process promotes high molecular chain alignment in the MD, contributing to uniformity throughout the material and, consequently, a rise in crystallinity (DSC, Section 3.2, and XRD, Section 3.4).[31, 60] Finally, at higher SR values, an increase in pores, and holes is observed due to the poor interfacial adhesion between the polymer and S-W particles. This weak adhesion causes the S-W particles to be pulled out from the PBAT matrix (Figure 3b,d), which may potentially lead to sample failure. When the S-W particles are subjected to stretching, the fragile adhesion between the S-W particles and the PBAT matrix further deteriorates, leading to the S-W particles being pulled out of the matrix.
In summary, SEM images reveal two distinct trends at high SR that can affect the material's structural integrity: 1) the high molecular chain alignment in the MD, which enhances surface uniformity; and 2) the weak adhesion between the filler and the polymer matrix, which may lead to microscopic deterioration and the formation of defects.
3.4 X-Ray Diffraction (XRD) Spectroscopy
Figure 4 illustrates the XRD diffractograms for both the S-W powder and the PBAT/S-W composite films. The S-W powder exhibited distinct sharp peaks at 2𝜃 values of 11.7, 23.2, 25.5, 27.0, 29.5, 35.2, 39.3, and 47.7, corresponding to the crystallographic orientation of (200), (200), (002), (102), (120), (300), and (400).[61, 62] Additionally, distinctive diffraction peaks at 2𝜃 ≈ 23.0°, 29.5°, and 35.1° were detected in the S-W-filled films, confirming the incorporation of S-W within the PBAT matrix. Furthermore, to compare Figure S3 in Supporting material was added XRD diffractogram of neat PBAT sample with main peaks located at: 17.4, 20.3, 23.1, 24.8, and 28.6° corresponding to the crystallographic orientation of (011), (010), (101), (100), (111), and (104), respectively.[63] These minor diffraction peaks could result from the formation of small quantities of imperfect PBAT crystals during the melt crystallization process of the PBAT specimen.[64] Incorporating 15% and 25% S-W into the film matrix leads to a shift in the peak to either a higher or lower 2𝜃, accompanied by a reduction in peak intensity. This suggests a transition in the crystalline phase, altering the crystal structure of the films. For example, the S-W powder peak located at 23.3° showed a higher peak at PBAT/S-W25% UNST sample than the PBAT/S-W15% UNST, related to a higher concentration of this filler. Furthermore, after uniaxial stretching, the composite films at SR 6 exhibited peak broadening, particularly peaks located near 23° and 29°. In the study conducted by Khan and collaborators,[65] who investigated the stretching of composite films based on poly(vinylidene fluoride) and barium titanate nanoparticles, it was also reported that the decrease and shift of X-ray peaks are associated with changes in the crystal structure. This effect may be due to a reduction in crystallite size resulting from the fragmentation of crystallites at the higher SR of 6 and the formation of new crystalline structures. Similar results were found in the study developed by Nath and co-authors.[54]
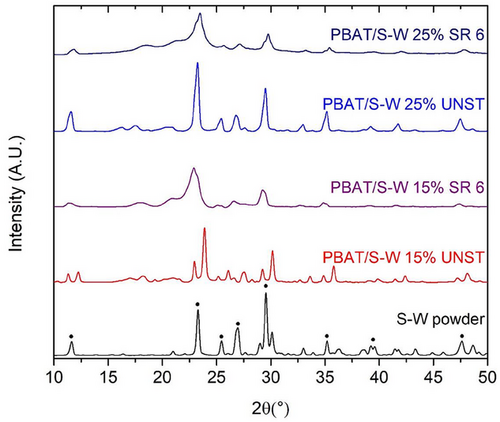
As anticipated, the incorporation of S-W and subsequent uniaxial stretching led to a significant increase in the % crystallinity of the films (Table 4). When the films were uniaxially stretched at SR 6, the XCXRD values for PBAT/S-W15 and PBAT/S-W25% showed an increase of 10.3% and 4.3%, respectively, relative to the non-stretched samples. DSC analysis of the stretched films corroborated this finding by showing a comparable increase in XCDSC (Section 3.2). However, the XC value obtained from XRD was higher than that from DSC, which can be attributed to the imprecision in the DSC thermogram, which overestimates or underestimates crystallization or melt baseline.[66, 67]
Formulation | XCXRD (%) |
---|---|
PBAT/S-W15% UNST | 72.0 |
PBAT/S-W15% SR 6 | 79.4 |
PBAT/S-W25% UNST | 77.2 |
PBAT/S-W25% SR 6 | 80.5 |
3.5 Barrier Properties
Effectively controlling the permeability of packaging materials to volatile substances is essential for preserving product quality and prolonging shelf life.[68] Maintaining product moisture is crucial for preventing texture changes and minimizing weight loss, as it extends shelf life, inhibits microbial growth, and reduces economic losses.[69] WVP governs the passage of water vapor through packaging materials, and when effectively managed, it helps keep food items from taking on moisture and losing freshness. Several factors influence this water permeability, including the polymer's hydrophilicity or hydrophobicity and its level of crystallinity.[70]
WVP of PBAT/S-W composite films was assessed to understand the impacts of S-W concentration and stretching. In Figure 5, a bar graph illustrates a downward trend in moisture permeability with increasing stretch ratios. The water barrier permeability data for the PBAT/S-W formulations are provided in Table S3 (Supporting Information). PBAT/S-W UNST counterpart films with 15 and 25 wt% were 186.9 ± 10.0 and 150.3 ± 8.7 g.mil/m2.day.KPa, respectively. In previous research conducted under similar testing conditions as this study, the WVP of neat PBAT was found to be ≈130 g.mil m−2.day.KPa.[31] Several factors can contribute to the decrease in the performance of barrier properties, including filler content, crystalline domains, SR, and stretching temperature. Shahverdi-Shahraki and collaborators[71] developed composites using polyethylene terephthalate and calcined kaolin, investigating the impact of filler loading, temperature, and SR. They identified that the permeability of composites is affected by three key factors: the barrier effect of particles serving as impermeable barriers, the number of crystalline domains within the sample, and the agglomeration of particles. Specifically, the diminished barrier performance may be due to a high filler content, particularly when the fillers are not compatible with the matrix or present voids or inadequate adhesion, as observed in the SEM images (Section 3.3). A critical factor to consider is the shape, morphology, orientation, and size of the filler, as these attributes can profoundly influence the barrier performance of the composite material.
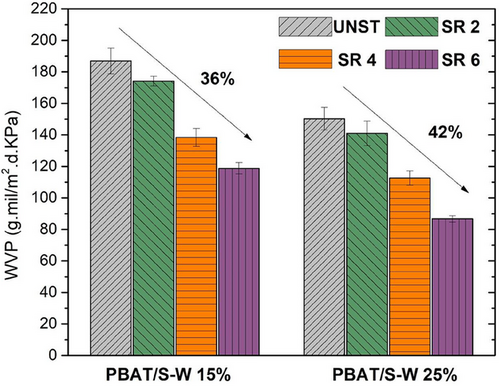
Figure 5 illustrates the decrease in this parameter as the SR increases. The lowest WVP value was achieved at the highest SR (SR 6) for both filler contents. For PBAT/S-W15% samples, the water barrier property decreased by ≈117 g.mil m−2.day.KPa when the composite film reached SR 6, representing a 37% reduction of this parameter. In comparison, PBAT/S-W25% samples recorded a value of 87 g·mil m−2·day·KPa, reflecting an ≈42% reduction. The enhancement of this property could be related to a higher number of crystalline domains within the sample,[72] as reported in Sections 3.2 and 3.4 for XC values for DSC and XRD. Additionally, the phenomena described in Section 3.1 (mechanical properties), which highlight the high alignment of polymer chains due to restricted uniaxial stretching along the MD, contributed to enhanced uniformity. This increased alignment and uniformity promoted greater crystallinity in the material, thereby reducing the WVP values.[31] This effect has a greater influence on the tortuosity of water vapor molecules than the pull-out features observed in the SEM analysis (Section 3.3) for PBAT/S-W SR 6 samples. Li and colleagues[73] investigated composite films incorporating organically modified montmorillonite, with dispersion levels varying from 0 to 13 wt% within the PBAT matrix. These films were created using both film-blowing and biaxial orientation techniques. The authors demonstrated that both methods lead to films with improved in-plane alignment of polymer chains, which effectively aligns the organically modified montmorillonite particles. Nonetheless, biaxial orientation achieved superior alignment of the filler layers parallel to the film surfaces. However, Chatterjee et al.[58] reported a decline in water barrier performance following the stretching of high-density polyethylene films. The authors concluded that uniaxial stretching at a particular SR decreased the tortuosity of the diffusion path due to alterations in crystal lamellae orientation, leading to increased moisture permeability.
The WVP values obtained for PBAT/S-W composites at SR 6 in this work are comparable to those of conventional non-biodegradable petroleum-based plastics, such as polystyrene or Nylon 6, recognizing them as low barrier grade.[74] These materials are widely used in various applications, including packaging, medical devices, and automotive. However, further efforts are necessary to enhance these materials to achieve high or very high barrier grades, defined by WVP values lower than 16 g·mil m−2·d·kPa, to meet market performance requirements.
3.6 Contact Angle and Surface Tension
The wettability test assesses the interactions between a solid and a liquid. Stronger interactions lead to a smaller contact angle, which lowers interfacial tension and facilitates liquid absorption into the polymeric material.[75] The wettability of a material's surface is crucial in determining how fluids interact with it. Hydrophobic materials, characterized by their non-polar nature and low attraction to water, tend to repel it. A contact angle less than 90° signifies a hydrophilic surface, while an angle greater than 90° indicates a hydrophobic surface.[76]
The wettability of the composite films was evaluated by measuring the water and diiodomethane contact angle on their surfaces, with the findings presented in Table 5. The images for the water contact angle on the PBAT/S-W formulations are provided in the Supporting Information. PBAT/S-W composite films containing 15 and 25 wt% of filler showed water contact angle values of 52.3° and 70.9° (Table 5), respectively. The rise in water contact angle with higher S-W content suggests a decrease in hydrophilicity as the filler concentration increases, due to the inherent hydrophobic properties of S-W. According to Ma and collaborators,[77] the hydrophilic group of a silane coupling agent is anticipated to chemically react with the hydroxyl group on the unmodified-wollastonite surface, thereby modifying it to become more hydrophobic. Gu et al.[78] developed composite films based on PBAT/lignin by incorporating varying amounts of silane-modified silica. The authors reported an increase of over 30% in the water contact angle of the matrix when 2 wt% of this filler was added.
Formulation | Contact angle (°) | Surface tension [mN·m−1] | ||||||
---|---|---|---|---|---|---|---|---|
Harmonic-mean | Geometric-mean | |||||||
Water | Diiodomethane | γ p | γ d | γ total | γ p | γ d | γ total | |
PBAT/S-W15% UNST | 52.3 ± 1.3 | 33.3 ± 1.8 | 20.1 | 43.1 | 64.1 | 15.5 | 42.8 | 58.3 |
PBAT/S-W15% SR 2 | 53.7 ± 1.5 | 35.1 ± 2.4 | 20.5 | 42.3 | 62.8 | 15.1 | 42.0 | 57.1 |
PBAT/S-W15% SR 4 | 59.0 ± 1.5 | 30.2 ± 0.7 | 17.4 | 44.4 | 61.7 | 11.4 | 44.2 | 55.6 |
PBAT/S-W15% SR 6 | 61.5 ± 1.4 | 30.7 ± 1.2 | 16.2 | 44.2 | 60.4 | 10.2 | 44.0 | 54.2 |
PBAT/S-W25% UNST | 70.9 ± 2.1 | 47.5 ± 4.5 | 13.2 | 36.6 | 49.9 | 8.2 | 35.7 | 43.8 |
PBAT/S-W25% SR 2 | 73.8 ± 1.0 | 41.1 ± 0.6 | 11.2 | 39.7 | 50.9 | 5.9 | 39.1 | 45.0 |
PBAT/S-W25% SR 4 | 76.9 ± 2.2 | 38.0 ± 4.0 | 9.6 | 41.1 | 50.7 | 4.4 | 40.6 | 45.0 |
PBAT/S-W25% SR 6 | 81.6 ± 3.1 | 51.0 ± 2.1 | 8.7 | 34.9 | 43.7 | 4.2 | 33.7 | 37.9 |
Following uniaxial stretching, the water contact angle increased slightly, peaking at ≈62° at SR 6 for the PBAT/S-W15% composite and ≈82° at SR 6 for the PBAT/S-W25% composite. This behavior could be attributed to the increased contact between the surface and the water droplet, resulting from uniaxial orientation, which enhances the water contact angle of the PBAT/S-W stretched films. These results are in concordance with a barrier, SEM, thermal, and XRD analysis.
Regarding diiodomethane, PBAT/S-W composite films containing 15 and 25 wt% of S-W showed contact angle values of 33.3° and 51.0°, respectively. As a non-polar liquid, the diiodomethane contact angle primarily reflects changes in the dispersive component of the surface energy. For PBAT/S-W15% composites, the diiodomethane contact angle did not exhibit significant changes after uniaxial stretching. The highest contact angle was observed at SR 2 (35.1°), while the lowest was recorded at SR 4 (30.2°), as shown in Table 5. This indicates that the dispersive component of the surface remained largely unaffected by the stretching process. In contrast, PBAT/S-W25% blown films showed changes in the diiodomethane contact angle after uniaxial stretching, decreasing from 47.5° for the UNST sample to 38.0° for the SR 4 sample, obtaining the greatest wettability due to the smallest contact angle.[79] This may suggest that the uniaxial stretching procedure induced modifications at the microscopic level, affecting the surface characteristics for PBAT/S-W25% samples. Wang and co-authors[80] explained that the polymer surface contains both oriented and disoriented cavities, which influence the interaction with molecules when a droplet encounters the surface. The cavity can absorb depending on several factors, among them: polymer chemistry and geometry, and the attractive potential of liquid molecules. The highest contact angle with diiodomethane was obtained with SR 6, reaching a value of 51.0° (Table 5). Following the surface tension measurements, the total surface tension of PBAT/S-W15% samples is ≈10 mN·m−1 higher than that of PBAT/S-W25% for both geometric and harmonic means, as shown in Table 5. This difference could be attributed to the higher S-W particle content in the formulations, which exhibits inherent hydrophobic properties. As SR increases, the surface values for both the harmonic and geometric means decrease, suggesting reduced wettability and a weaker attraction between the surface and the liquid. This effect may be attributed to the alignment of polymer chains at higher SR levels, which leads to increased crystallinity in the samples (SEM, Section 3.3, DSC, Section 3.2, and XRD, Section 3.4).
4 Conclusion
The effects of uniaxial stretching on the morphology, mechanical and thermal properties, barrier performance, contact angle, and X-ray diffraction of PBAT and S-W-based blown films were thoroughly investigated. Two bio-composite films, incorporating 15% and 25% S-W, were successfully produced through blown film extrusion and subsequently subjected to uniaxial stretching at ratios of 2, 4, and 6, aiming for sustainable packaging applications. The incorporation of this reinforcement into the PBAT matrix led to different trends in tensile properties, depending on the MD or TD. In the MD, TS, and YM increased with higher SR, reaching values of 126 MPa and 1060 MPa, respectively, for the PBAT/S-W 15% bio-composite at an SR of 6. The opposite effect was observed for ε in the MD, which showed a reduction of ≈95% when the SR reached 6 for the PBAT/S-W 25% composite. In the TD, the ε exhibited significant changes, increasing by ≈70% from the unstretched state to an SR of 6. The primary difference in tensile properties between the two directions is attributed to uniaxial orientation. Stretching in the MD is believed to interfere with the alignment of molecular chains in TD, resulting in reduced mechanical properties Morphological analysis revealed that S-W particles were well-dispersed in the polymer matrix without needle-like shapes or agglomerations. In addition, SEM indicated two opposing effects at high SR that influence interactions with liquid molecules: a pronounced alignment of molecular chains in the machine direction and weak adhesion between the filler and polymer matrix, which could impact the material's structural integrity. Both DSC and XRD analyses demonstrated that the degree of crystallinity increased with uniaxial stretching, as evidenced by increased percentage crystallinity values calculated from these techniques. This effect is likely due to strain-induced crystallization, which creates additional crystallization sites. The increase in this property could directly enhance barrier performance, which improved by ≈36% and 42% with the addition of 15% and 25% S-W, respectively, achieving values comparable to those of some conventional petroleum-based plastics. Overall, the contact angle increased with higher S-W content, indicating reduced hydrophilicity as filler concentration increased, due to the hydrophobic nature of S-W. In addition, as SR increases, the surface energy decreases, indicating a reduction in wettability. The results revealed that blown films made from PBAT/S-W composites and unidirectionally stretched exhibited better properties, making them well-suited for use in eco-friendly packaging solutions.
Acknowledgements
The authors would like to acknowledge financial support from the Ontario Research Fund, Research Excellence Program; Round 11 (ORF-RE 11–025) from the Ontario Ministry of Colleges and Universities (Project Nos. 056106 and 056184); the Ontario Agri-Food Innovation Alliance−Bioeconomy for Industrial Uses Research Program (Project Nos. 030648, 030699 and 030706); the Natural Sciences and Engineering Research Council (NSERC), Canada Discovery Grants Program (Project No. 401716), and the NSERC Alliance Grants Program (Project No. 401769) along with the partner industry Competitive Green Technologies, Lamington, Ontario, Canada (Project No. 055427) in carrying out this study. This research also benefited from facility funding to the Bioproducts Discovery and Development Centre (BDDC) lab by Fed Dev Ontario, the Ontario Ministry of Agriculture, Food, and Rural Affairs (OMAFRA), the Canada Foundation for Innovation (CFI), and the Federal Post-Secondary Institutions Strategic Investment Fund (SIF) and matching funds from the province of Ontario and numerous University of Guelph alumni.
Conflict of Interest
The authors declare no conflict of interest.
Author Contributions
Matias Menossi performed methodologies, investigation, data curation, formal analysis, visualization, wilt, and writing of the original draft. Manjusri Misra performed conceptualization, investigation, methodologies, validation, supervision, resources and funding acquisition, administration, and review and editing of the manuscript. Amar Kumar Mohanty performed conceptualization, investigation, methodologies, validation, supervision, resources acquisition, and review and editing of the manuscript. All authors contributed to the discussion, reviews, editing, and approval of the manuscript for publication.
Open Research
Data Availability Statement
The data that support the findings of this study are available in the supplementary material of this article.