Kevlar/Basalt and Kevlar/Glass Intra-Ply Reinforced Hybrid Composites: Influence of Basket Weave Fabric Structure on Thermal Properties, Flammability, and Impact Performance
Abstract
This study investigates the influence of basket weave fabric structure and fibre combination on the thermal properties, flammability, and impact performance of intra-ply reinforced hybrid composites. The objective is to evaluate the effect of varying the number of threads in the basket weave pattern (ten threads 5 × 5, six threads 3 × 3, and two threads 1 × 1) and different fibre combinations (Kevlar-Glass (KG) and Kevlar-Basalt (KB)) on composite performance. The composites were fabricated using a handloom weaving process followed by compression moulding. Thermal stability was assessed using Thermo Gravimetric Analysis (TGA), flammability was examined via the UL-94 horizontal burn test, and impact performance was evaluated using the Charpy impact test. The results indicated that KG composites exhibited superior thermal stability, with higher final residue percentages and lower mass loss during degradation. The impact performance was significantly influenced by both fibre combination and weave structure, with KG5 × 5 and KB5 × 5 laminates achieving the highest impact strengths of 2160 kJ/m2 and 2040 kJ/m2, respectively. Flammability tests showed that all composites had a burn rate below 10 mm/min, meeting standard safety criteria. The findings highlight the potential of these hybrid composites for high-performance applications requiring impact resistance and thermal stability, such as aerospace and protective equipment industries.
1 Introduction
Fibers are the primary load-bearing members in composite materials.[1-3] In high-performance applications across civil, aerospace, marine, and automotive sectors, woven fabric reinforcements are widely combined with polymer matrices to enhance mechanical and functional properties.[4-8] Hybrid composites, consisting of two or more types of fibers within a single matrix system, offer an opportunity to synergistically enhance mechanical strength, impact resistance, and thermal stability by leveraging the distinct properties of each fiber type.[9, 10] Among these, intra-ply hybrid composites, where different fibers are interwoven within the same ply, provide advantages such as improved load distribution, enhanced energy absorption, and superior damage tolerance. Kevlar, a high-strength para-aramid fiber, is widely recognized for its exceptional impact resistance, thermal stability, and inherent flame retardance.[11] Basalt and glass fibers, on the other hand, are known for their excellent thermal properties, cost-effectiveness, and high mechanical strength.[12] Combining Kevlar with basalt or glass in intra-ply hybrid structures presents a unique opportunity to exploit the advantages of both fiber types while mitigating their limitations.
The basket weave fabric structure, characterized by an interlaced fiber arrangement, is widely used in textile-reinforced composites due to its superior mechanical stability, uniform load distribution, and enhanced resistance to delamination under impact.[13] However, the primary drawback of the basket weave pattern is its susceptibility to snagging and lower resistance to tearing.[14, 15] This limitation can be mitigated by increasing the number of threads in the weave pattern, which enhances the composite's stiffness and durability. Additionally, intra-ply hybridization—incorporating dissimilar fibers in the warp and weft directions optimizes mechanical properties. Studies have reported that Kevlar-PALF intra-ply hybrid composites with a 6-thread (3×3) basket weave pattern exhibit superior tensile strength and stiffness compared to plain and twill weaves.[16] Similarly, intra-ply hybridization of basalt/epoxy composites with carbon fibers has enhanced tensile strength and thermal stability.[17]
While the mechanical and thermal properties of Kevlar, basalt, and glass fiber composites have been extensively studied, the durability of basalt fiber composites remains a critical aspect requiring further discussion. Recent advances in basalt fiber-reinforced composites have demonstrated remarkable resistance to environmental degradation, including moisture absorption, chemical attack, and UV radiation exposure.[18, 19] Compared to glass fibers, basalt fibers exhibit superior resistance to alkaline environments, making them particularly suitable for civil infrastructure and marine applications.[20] However, long-term aging studies have highlighted that the performance of basalt composites under sustained mechanical loading, thermal cycling, and exposure to harsh environmental conditions requires further investigation.[21-23] In particular, the interaction between basalt fibers and the epoxy matrix over extended periods can influence delamination resistance and fatigue performance, crucial for high-performance structural applications.[24, 25]
Despite the potential advantages of Kevlar-glass and Kevlar-basalt intra-ply hybrid composites, studies on their thermal stability, flammability, and impact resistance remain limited.[26, 27] Furthermore, while the mechanical performance of Kevlar-glass composites has been explored, the effect of varying the number of threads in the basket weave pattern has not been widely investigated.[28-31] Despite the extensive research on hybrid composites, most studies have focused on inter-ply configurations or the mechanical properties of individual fiber reinforcements. The combination of Kevlar-glass and Kevlar-basalt in intra-ply hybrid composites has been explored primarily in terms of mechanical performance and quasi-static indentation, with limited research on their thermal stability, flammability, and impact behavior. Additionally, the effect of varying the number of threads in the basket weave pattern remains largely unexplored. This study addresses these gaps by systematically investigating the synergistic influence of intra-ply hybridization and basketweave architecture on key performance parameters. The novelty of this work lies in its comprehensive evaluation of impact resistance, thermal degradation, and flame retardance, providing critical insights into the structural and functional advantages of these composites. The findings offer a new perspective on tailoring fiber architecture and hybridization strategies to enhance composite performance, making them promising solutions for aerospace, automotive, and protective applications where impact resistance and thermal stability are crucial.
2 Materials and Methods
2.1 Materials
In this work, Kevlar-49 fiber (K),[32-36] C-Glass fiber (G), and Basalt fiber (B) were used as the reinforcement. Epoxy LY556 and hardener HY951 are employed as matrix materials.[37-39]
2.2 Weaving
Initially, the fabric was prepared by weaving using the traditional handloom technique, in which the Kevlar-49, basalt, and glass fiber yarns were woven together to form the composite lamina, as shown in Figure 1. Three different weave architectures, namely plain, twill, and satin weave, were created, and the composites were fabricated and designated, as shown in Table 1.
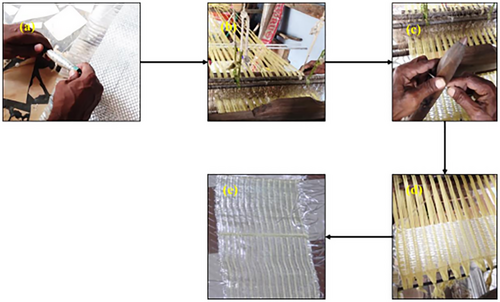
Materials | Density [g/cc] | Tensile strength [MPa] | Elastic modulus [GPa] | Elongation at break (%) |
---|---|---|---|---|
Kevlar-49 | 1.44 | 3620 | 76 | 2.8 |
Basalt | 2.61 | 4150 | 89 | 2.7 |
C-Glass | 2.52 | 3310 | 72 | 4.8 |
LY556 | 1.14 | 73.3 | 3.47 | 4.5 |
HY951 | 1.19 | 52 | 2.8 | 11 |
The selection of basket weave patterns (1 × 1, 3 × 3, 5 × 5) in this study was based on their influence on mechanical performance, impact resistance, and structural integrity of hybrid composites. Basketweave fabrics are widely used in aerospace, automotive, defense, and protective applications due to their high dimensional stability, uniform load distribution, and resistance to delamination. However, the mechanical behavior of composites is significantly influenced by weave architecture, necessitating an in-depth investigation into the effect of different thread configurations on key performance parameters.
2.2.1 1 × 1 (Basic Basket Weave)
This configuration represents the simplest form of basket weave, where each warp yarn passes over and under a single weft yarn. It is commonly used in lightweight, protective clothing, aerospace interior panels, and flexible ballistic applications, where high drapeability and flexibility are required. However, due to its loose structure, impact resistance and stiffness may be lower compared to higher thread configurations.
2.2.2 3 × 3 (Intermediate Basket Weave)
A moderate interlacing structure with improved stiffness and strength compared to 1 × 1. Balances flexibility and mechanical strength, making it suitable for automotive crash-resistant panels, reinforced protective gear, and aircraft structural reinforcements. This pattern provides better load transfer and impact absorption, addressing the limitations of 1 × 1 while maintaining sufficient adaptability for complex structures.
2.2.3 5 × 5 (Dense Basket Weave)
This weave has a higher thread count, increasing stiffness, strength, and impact resistance due to improved load distribution and reduced fiber mobility. Suitable for high-impact aerospace structures, body armor, and ballistic shields, where energy absorption and durability under extreme conditions are critical. The higher stiffness enhances resistance to tearing and delamination, making it ideal for high-performance composite applications.
2.3 Fabrication
The laminates were fabricated through compression molding. The fabrics were placed into a mold size 300*300*3 mm3, poured with resin and hardener, mixed in a 10:1 ratio, and cured for 3 h under 5 bar pressure. The laminates with their corresponding designation are shown in Figure 2.
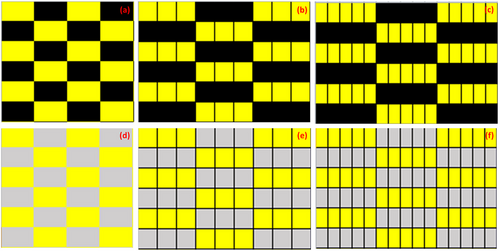
2.4 Characterization
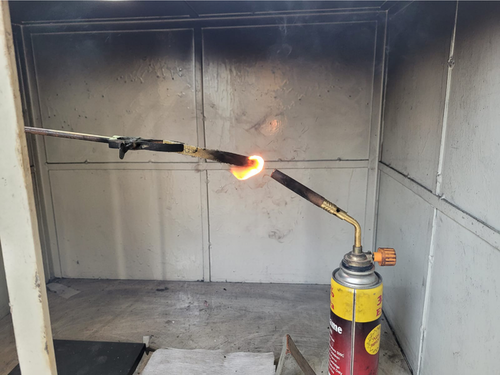
The Charpy impact test was performed to evaluate the impact resistance of the Kevlar-glass (KG) and Kevlar-basalt (KB) intra-ply hybrid composites. The setup and procedure were conducted according to ASTM D6110 standards. The impact test setup is represented in Figure 4. The test is conducted in Hindustan Institute of Technology & Science, Chennai, India. The specimens were cut to the required dimensions as per ASTM D6110 standards. Each specimen featured a V-notch, which helps in concentrating stress and ensuring a consistent fracture pattern during testing. A Charpy impact testing machine was used to determine the energy absorbed by the composite specimens when subjected to an impact load. The machine consists of a pendulum hammer, which swings down from a fixed height to strike the specimen. The specimen was securely placed on two supports in a horizontal position. The pendulum was released from a known height, impacting the specimen at the notched area. The energy absorbed by the specimen during fracture was recorded.
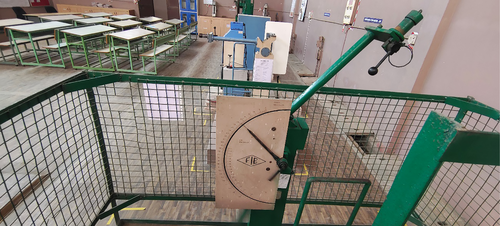
3 Results and Discussion
3.1 Influence of the Number of Threads in the Basket Weave and Fiber Combination
Figure 5a–d illustrates TGA's thermogram and DTG. It can be inferred from the thermogram that major weight loss occurred in two stages regardless of the weave configuration of the composites. 05 samples were utilized for each configuration to determine the influence of the number of threads and a deviation of <2% was observed for each configuration. The average value for peak degradation temperature corresponding to significant weight losses in the first and second stages obtained from the derivative thermogram (DTG) is shown in Table 2. The first major loss occurred between 370 and 380 °C while the second significant weight loss occurred between 550 and 575 °C. All the composites displayed nearly identical thermal degradation temperatures in the first stage, while in the second stage, the thermal degradation temperature of the KG composites was marginally lower than the KB composites. The weave pattern significantly influenced thermal stability, with denser weaves (5 × 5) exhibiting lower mass loss and higher thermal resistance compared to 1 × 1 and 3 × 3 weaves. This suggests that increasing the thread count enhances heat dissipation and reduces polymer degradation, improving overall thermal performance. A key finding from the TGA results is that KG composites exhibited superior thermal stability compared to KB composites. This was evident from their higher final residue percentage, lower mass loss in both degradation stages, and a slower decomposition rate in the second stage. The enhanced stability of KG composites is attributed to the better thermal resistance of glass fibers compared to basalt fibers, which contributes to reduced degradation at elevated temperatures.
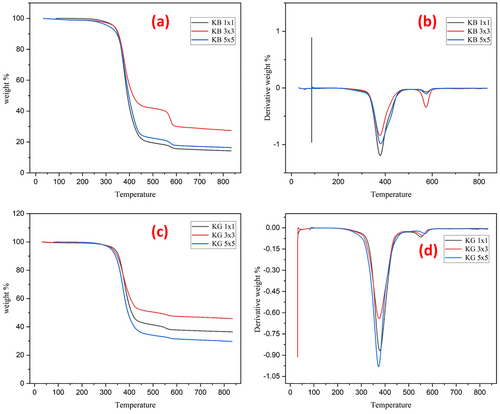
Sample | First stage | Second stage | Final residue [%] | ||
---|---|---|---|---|---|
Mass loss [%] | Peak degradation temperature [°C] | Mass loss [%] | Peak degradation temperature [°C] | ||
KB1 × 1 | 79.24 | 378.03 | 5.79 | 574.90 | 14.28 |
KB3 × 3 | 54.33 | 376.96 | 15.45 | 573.77 | 27.49 |
KB5 × 5 | 74.82 | 380.77 | 6.97 | 574.34 | 16.41 |
KG1 × 1 | 55.46 | 377.72 | 6.59 | 550.52 | 36.49 |
KG3 × 3 | 48.59 | 375.51 | 5.27 | 557.24 | 45.87 |
KG5 × 5 | 62.43 | 372.95 | 6.59 | 569 | 29.75 |
In contrast, KB composites decomposed more rapidly in the second stage, indicating a lower resistance to high temperatures. The final residue percentage further reinforces these observations, with KG composites retaining more structural integrity post-degradation than KB composites. This higher residue percentage suggests that KG composites can withstand higher temperatures without significant material loss, making them better suited for applications requiring thermal stability, such as aerospace insulation, fire-resistant panels, and high-temperature structural components. The findings confirm that intra-ply hybridization and weave structure significantly impact the thermal behavior of composites, providing valuable insights for optimizing material selection in industries where heat resistance and durability are critical.
The influence of weave configuration was evident from the final residue %, which was significantly different from each other. Among the composites, the twill weave configuration displayed the highest residue %. Moreover, in the case of the fiber combination, KG composites outperformed KB composites with higher residue %, as shown in Figure 6.
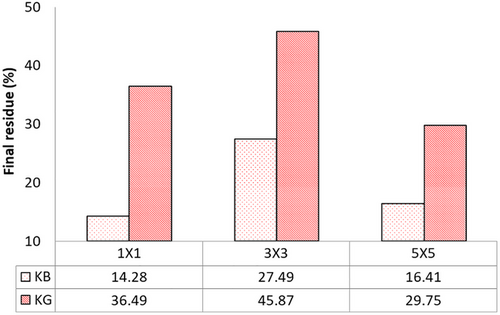
Figure 7 depicts the visual images of the specimens after the UL-94 HB test. A char layer was formed on the specimens as a result of burning. The char formation is a typical characteristic of the composite containing epoxy matrix. It serves as a barrier between the fire and reinforcement, thus protecting and preserving the internal structure. However, the char layer on the surface is brittle, which can break easily and expose the reinforcement, as shown in Figure 7.
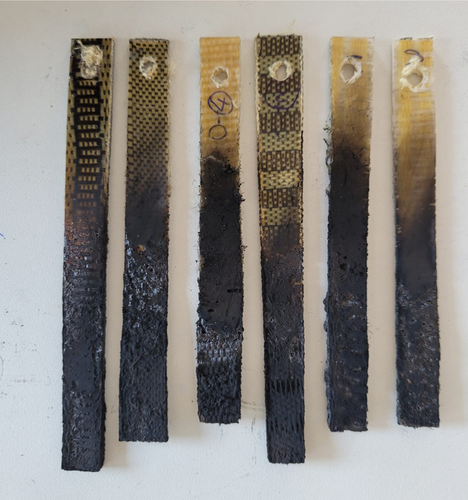
Table 3 summarizes the results of the UL-94 HB test. The general observation was that all the composites exhibited an HB rating and possessed a burn rate much lower than 76 mm min−1. This is an indication of good flame-retardant ability, where the specimen continues to burn for more than 30 s, and the flame extinguishes before the designated length of 100 mm. Interestingly, the weave configuration or fiber combination did not affect the flammability characteristic of the material, as reflected by the nearly identical burn rate values close to each other (Figure 8). These observations were similar to the trend reported in the literature on the bamboo/epoxy laminate with plain weave and twill weave configurations, where the flame propagation rate was not affected by the weave configuration but rather by the thickness of the laminate.[40]
Sample | Burn rate [mm min−1] | Dripping | Cotton ignites | UL-94 rating |
---|---|---|---|---|
KB1 × 1 | 7.34 | yes | yes | HB |
KB3 × 3 | 7.09 | yes | yes | |
KB5 × 5 | 7.29 | yes | yes | |
KG1 × 1 | 7.01 | yes | yes | |
KG3 × 3 | 7.21 | yes | yes | |
KG5 × 5 | 8.11 | yes | yes |
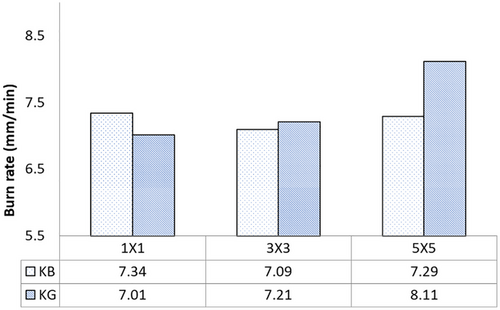
The Charpy impact results are tabulated in Table 4. The number of threads influenced the energy absorbed into the specimen and impact strength in the basket weave pattern, and the trend observed was as follows: 5 × 5 > 3 × 3 > 1 × 1. The superior impact strength for the basket weave pattern was also reported in a recent study, and it was highlighted that impact strength can be enhanced through the jute-banana intra-ply hybrid composite.[41] In addition to the number of threads, the fiber combination also influenced the impact strength, as presented in Figure 9. The KG laminates were found to have significantly higher impact strength than the KB laminates. The impact strength seems to be influenced by the fiber properties such as tensile strength, stiffness, and % elongation at break or strain. The basalt fiber has moderately higher tensile strength and stiffness than the glass fiber (Table 1). However, the % elongation at break was significantly lower for the basalt fiber than the glass fiber. According to Almeida et al., in addition to the weave pattern, the energy absorption characteristic, resistance to the impact load, and its deformability were dictated by the differences in fiber properties.[42]
Composite | Energy absorbed [J] | Impact strength [kJ m−2] |
---|---|---|
KB1 × 1 | 28 | 1120 |
KB3 × 3 | 46 | 1840 |
KB5 × 5 | 51 | 2040 |
KG1 × 1 | 30 | 1200 |
KG3 × 3 | 48 | 1920 |
KG5 × 5 | 54 | 2160 |
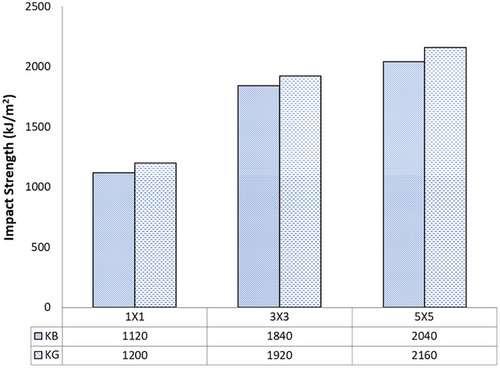
SEM analysis examined the fracture mechanisms in the KG and KB intra-ply hybrid composites after Charpy impact testing. The SEM images revealed critical failure modes that contribute to the overall impact performance of the composites. Several regions in the fractured specimens exhibited fiber pull-out, indicating the weakening of interfacial bonding between the fiber and the epoxy matrix. This failure mode suggests that the load was not efficiently transferred from the matrix to the reinforcement, leading to reduced energy absorption. The extent of fiber pull-out was found to be greater in KB composites, which suggests the low impact strength of KB composite laminate compared to KG composite laminate. Fiber Breakage was prominently observed in KG composites, which indicates that the Kevlar-glass interface was stronger, allowing for better stress transfer. Clean fiber breakage suggests that the composite could withstand higher impact forces before failure. This correlates with the higher impact strength observed in KG5 × 5 (2160 kJ m−2). The matrix showed evidence of micro-cracks, which were initiated due to the high-stress concentration near the impact zone. In some cases, debonding between the fiber and matrix was observed, indicating interfacial failure as a dominant failure mechanism. The extent of matrix cracking varied based on the weave pattern, with denser weaves (5×5) showing less micro-cracking due to better load distribution.
The SEM analysis provided valuable insights into the fracture mechanisms governing the impact performance of hybrid composites. The stronger Kevlar-glass interface and reduced delamination in KG composites explain why they exhibited better impact resistance than Kevlar-basalt composites. These findings emphasize the importance of weave architecture and fiber selection in designing high-performance composite materials for aerospace, automotive, and protective applications. The fractured specimens observed under the scanning electron microscope shown in Figures 10 and 11 revealed the typical failures such as fiber pull-out, fiber breakage, and matrix micro-cracking that occur as a result of the impact load.
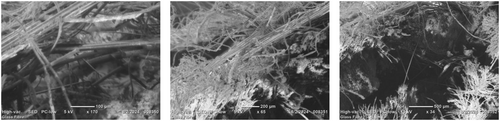

4 Practical Implications Based on Industry Perspective and Applications
4.1 Practical Implications and Research Limitations from an Industry Perspective
The findings of this study have significant practical implications for industries requiring high-performance composite materials, particularly in aerospace, automotive, and protective applications. The demonstrated superior impact resistance of KG intra-ply composites, enhanced thermal stability and flame retardance make them highly suitable for aircraft structural components, ballistic protection gear, and automotive crash-resistant panels. Meanwhile, despite their lower impact strength, KB composites offer a cost-effective alternative with moderate mechanical performance and good thermal resistance, making them viable for fire-resistant panels and lightweight, protective enclosures. The study highlights the importance of optimizing basket weave configurations to tailor composite performance for specific applications, providing valuable insights for material engineers and manufacturers in selecting the right fiber combination and weave pattern.
However, this research has certain limitations that warrant further investigation. The impact testing was limited to Charpy tests, which assess notched specimens under a single impact condition. A more comprehensive study involving drop-weight impact tests and real-world crash simulations could provide a deeper understanding of dynamic impact behavior. Additionally, the study focused on thermal stability through TGA analysis, but further evaluation using dynamic mechanical analysis (DMA) and fire resistance tests would offer better insights into high-temperature performance. The research topic can also explore long-term durability, environmental aging, and moisture absorption effects, which are crucial for real-world applications. Future studies should address these aspects further to validate the industrial feasibility of these hybrid composites and expand their potential applications.
4.2 Application Suitability
- KG composites, with their superior impact resistance (2160 kJ m−2) and thermal stability, can be used in aircraft structural components, interior panels, and protective enclosures.
- KB composites, offering moderate impact strength but good thermal resistance, can be utilized in fire-resistant panels and insulation components.
- The high-impact energy absorption of KG composites makes them ideal for crash-resistant structures, bumpers, and reinforced door panels in automobiles.
- KB composites, being cost-effective, can be used for heat shields, underbody protection, and lightweight protective structures.
- The HB rating and self-extinguishing characteristics of both composites suggest their suitability for fire-resistant protective clothing and shields.
- The good thermal resistance and mechanical strength of these composites can be leveraged in fireproof panels, impact-resistant doors, and ship hull reinforcements.
- Their flame retardance (burn rate <10 mm min−1) makes them suitable for fire-resistant structures in buildings and marine vessels.
4.3 Future Directions
- 1. Advanced Impact and Fatigue Studies
- ○ Conduct drop-weight impact testing and real-world crash simulations to evaluate dynamic impact behavior.
- ○ Investigate fatigue performance under cyclic loading to assess long-term durability in structural applications.
- 2. Environmental and Aging Effects
- ○ Study moisture absorption, UV degradation, and thermal cycling to understand the environmental aging of these composites.
- ○ Assess corrosion resistance and chemical stability, particularly for marine and aerospace applications.
- 3. Fire and Thermal Performance Enhancement
- ○ Explore the addition of fire-retardant additives or nanoparticle reinforcements to improve flame resistance.
- ○ Investigate the effect of alternative resin systems (e.g., phenolic, thermoplastic, or bio-based resins) on thermal and mechanical performance.
- 4. Process Optimization and Scale-Up
- ○ Develop automated weaving and composite fabrication techniques for mass production to improve consistency and cost-efficiency.
- ○ Study the effect of different curing conditions, resin formulations, and hybrid stacking sequences on overall performance.
- 5. Multi-Functional Composites
- ○ Investigate the integration of conductive fillers for electromagnetic shielding applications in defense and aerospace.
- ○ Explore the potential for self-healing or smart composites that can repair damage and extend service life.
By addressing these future research directions, the applicability of Kevlar-glass and Kevlar-basalt intra-ply hybrid composites can be further optimized for advanced engineering applications, making them even more competitive in aerospace, automotive, defense, and structural industries.
5 Conclusion
This study systematically investigated the influence of basket weave intra-ply hybrid composites with varying thread configurations on impact resistance, thermal stability, and flammability performance. The results demonstrated that fiber combination and weave architecture significantly affect composite properties. KG laminates consistently outperformed Kevlar-basalt KB laminates, particularly in impact strength and thermal stability. Among the tested configurations, KG 5 × 5 exhibited the highest impact strength (2160 kJ m−2), followed by KB 5 × 5 (2040 kJ m−2), confirming that increasing the number of threads enhances energy absorption capacity. TGA revealed that KG and KB laminates underwent thermal degradation in two stages, with KG composites exhibiting higher final residue percentage and lower mass loss, indicating better thermal stability. The UL-94 horizontal burn test confirmed that all composites achieved HB flame rating with burn rates below 10 mm/min, meeting industry safety standards. Notably, fiber combination and weave configuration had minimal impact on flammability performance, as all samples displayed self-extinguishing characteristics.
The selection of basket weave patterns in 1 × 1, 3 × 3, and 5 × 5 was driven by the need to investigate the progressive influence of weave density on impact, thermal stability, and flammability. These configurations mimic real-world structural requirements, allowing for optimized material selection based on specific industry needs. The study provides a foundation for future research into advanced hybrid weave architectures, enabling further customization of composite materials for high-performance applications.
Acknowledgements
This work was supported by the Scientific Research Fund of Nanjing Forestry University (Nos. 163050206 and 163050234), Czech Science Foundation GA CR Project (No. 23–06352 S), Ministry of Science and Technology of China under Foreign Young Talents Project (No.QN2021014006L), National Natural Science Foundation of China (No. 51878354) and 333 talent high-level projects of Jiangsu Province. Any research results expressed in this article are those of the author(s) and do not necessarily reflect the views of the foundations.
Conflict of Interest
The authors declare no conflict of interest.
Author Contributions
All authors have accepted responsibility for the entire content of this manuscript and approved its submission.
Open Research
Data Availability Statement
The data that support the findings of this study are available from the corresponding author upon reasonable request.