Granulation of sludge under different loads of a glycerol fraction from biodiesel production
Abstract
The aim of the research was to evaluate the possibility of using the crude glycerol fraction from biodiesel manufacturing processes for granular sludge production. The experiment was carried out simultaneously in four sequencing batch reactors (SBRs) at different carbon loads: 0.2 ± 0.08, 0.6 ± 0.16, 1.1 ± 0.27, and 1.3 ± 0.35 g COD/g TSS per cycle (COD – chemical oxygen demand, TSS – total suspended solids). Granulation did not occur in the reactor with the lowest organic carbon load. In the remaining reactors small granules began to appear after 25 cycles of reactor operation. In all reactors the efficiency of carbon removal remained at ca. 80%. The highest granular sludge production per cycle was 0.31 ± 0.28 g TSS/L; it was obtained at an organic load of 1.1 ± 0.27 g COD/g TSS per cycle. Most of the introduced COD was removed in the reactors during the first 5 h of aeration; the COD removal rate was correlated with the organic load and varied from 123.12 to 472.76 mg COD per litre and hour.
Practical applications: With the increasing production of biodiesel fuel a problem arises with the utilization of glycerol that is a by-product of the process. By-product glycerol fraction from small agricultural installations is usually contaminated. Its composition varies depending on parameters of the transesterification process and it is unprofitable to purify it. In the present research we investigated one possible way of dealing with the by-product. The glycerol fraction was successfully used as a carbon source for the production of aerobic granular sludge. The granules obtained can be used as a seed sludge in granule-based reactors, or can be cofired with coal or directly combusted. Since aerobic granular sludge is one of the most promising technologies investigated during the last few years it appears to possess high utility.
Abbreviations:
COD, chemical oxygen demand; SBR, sequencing batch reactor; TSS, total suspended solids.
Introduction
Present trends in the fuel market are encouraging the production of an alternative fuel called biodiesel 1. During the manufacturing processes, apart from biodiesel, a raw glycerol side fraction is produced which makes up ca. 10 wt% of the total amount of biodiesel fuel produced. The physical and chemical properties of the by-product glycerol depend on the method used to produce the biodiesel fuels. Biodiesel production in large installations involves purification of glycerol fraction for further use. However, chemical purification of raw glycerol fraction from small agricultural biodiesel installations is unprofitable. The quality parameters of glycerol fraction vary significantly depending on technology applied. The glycerol by-product contains up to 60% of glycerol and up to 27% each of water and methanol 2. Farmers can store this waste or dispose of it in a way that sometimes represents a threat to the natural environment. One of the solutions is the use of nonpurified glycerol as a liquid fuel in combustion plants to produce heat energy 2. In this work we investigated the possibility of granular sludge production using glycerol fraction as an organic carbon source.
In the last few years, increased attention has been focused on a form of self-immobilization of microorganisms known as biogranulation. In this process cell-to-cell interactions occur resulting in the formation of dense microbial consortia called granules. Granular biomass cultivation is promoted by proper selection of the operating conditions of the wastewater treatment process, e.g., short sedimentation time and a high volumetric exchange rate. In comparison with activated sludge, granules are characterized by a better settling ability, longer biomass retention time, and a higher biomass concentration. It is also possible to apply organic load rates up to 15 kg COD/m3 per day (COD – chemical oxygen demand) in granule-based reactors 3. Granules are usually cultivated in airlift or bubble column reactors with h/d (ratio of reactor height to diameter) ratios of 10 or more using a wide range of substrates, e.g., glucose, acetate, phenol, dairy effluents, or wastewater 4. From an engineering perspective, installations employing technologies based on granular sludge require smaller surface area and clarifier dimensions and are more economical in comparison with technologies based on activated sludge. The main disadvantage of granular sludge technology is the long time (usually a few months) needed for granule cultivation. This time can be shortened by seeding the reactor with already existing granular sludge cultivated on organic carbon sources such as glycerol fraction.
Since granular sludge technology allows treating wastewater containing a high organic load and is a promising technology for decentralized wastewater treatment 5 in our experiments we investigated the granulation of activated sludge in an sequencing batch reactor (SBR) as a function of different organic loads of a glycerol fraction stemming from biodiesel production.
Materials and methods
In the experiment four SBRs with a working volume of 6 L and a height to diameter ratio of 1.5 were employed. Seed sludge was collected from a conventional municipal wastewater treatment plant in Olsztyn (Poland) and sieved using a 0.5 mm sieve to remove large particles. The temperature in the experimental room was ambient (21 ± 2°C) and the pH of the reactors was kept between 7 and 8. The reactors were supplied with air at a constant velocity of 6 L/min; a wastewater exchange ratio (n) of 67% was employed. The SBRs were operated in a 12 h cycle, with the following operating strategy: aeration (705 min), settling (5 min), decantation (5 min), and filling (5 min). During the filling period, 4 L of a mixture of wastewater and glycerol fraction was added to the reactor to make a final working volume of 6 L. The wastewater was prepared according to Coelho et al. 6, however, no organic carbon was added. The glycerol fraction (423 g COD/L, oil and grease 77 g/L, total nitrogen 0.98 g/L) was obtained from an agricultural biodiesel installation in Lubomino (Poland). The glycerol fraction was added to wastewater in amounts resulting in different mean COD concentrations in the reactors at the beginning of the aeration phase (Table 1). The experiment was carried out for 74 days (148 cycles).
Reactor | ||||
---|---|---|---|---|
A | B | C | D | |
COD (mg O2/L) | 353 ± 63.9 | 704.4 ± 94.1 | 1120 ± 181.6 | 1400 ± 198.4 |
Organic load (g COD g TSS−1 cycle−1) | 0.2 ± 0.09 | 0.6 ± 0.16 | 1.1 ± 0.28 | 1.3 ± 0.35 |
Sampling was carried out on the influent and effluent of the reactor. All samples were filtered using a 0.2 µm micropore filter before being assayed. Oil and grease in the glycerol fraction was measured using a Soxhlet extractor and total nitrogen was measured by distillation. COD, total suspended solids (TSS), volatile suspended solids, and sludge volume index (SVI) were measured according to Standard Methods 7. The net granular sludge production was calculated as the difference between the TSS at the end and at the beginning of the cycle. On the 70th day of the experiment, samples were taken every 1–3 h during the SBR cycle to follow the COD concentration changes in the reactors. Granulation was documented using a digital camera (Canon G5, resolution 5 Mpic). The average diameter of granules was measured on the base of photographs as a circle equivalent diameter of 100 granules randomly obtained from the reactor in the 146th cycle. The correlation analyzes were performed using the STATISTICA 8.0 software (StatSoft, Tulsa, USA). The strength of the correlation was evaluated according to Stanisz 8.
Results and discussion
Glycerol fraction from biodiesel production contains substances, such as methanol or soaps, that are potentially toxic to microorganisms. Aerobic degradation of this waste using activated sludge was difficult, because its activity was inhibited and the biomass bulked (data not shown). Aerobic degradation of the glycerol fraction by granular sludge is more effective because microorganisms present in the granules are entrapped in a matrix of extracellular polymeric substances (EPS) and can better survive unfavorable conditions and the presence of toxic compounds.
In the experiment different amounts of glycerol fraction were introduced to the reactors to adjust organic loads enabling efficient granulation and effective removal of organic carbon. Tay et al. 9 showed that effective cell aggregation and granule formation demands optimization of the organic load rate in the reactor. These authors observed that, in aerobic sludge blanket reactors operating at organic load ratings of 1, 2, 4, and 8 kg COD/m3 per day, aerobic granules were not formed at the two lower organic load rates. In our experiments granulation did not occur in the reactor with the lowest organic carbon load of 0.2 g COD/TSS per cycle. In the remaining reactors with organic loads at the beginning of aeration in the range 0.6–1.3 g COD/TSS per cycle, small granules appeared only after 25 cycles of reactor operation and their amount increased gradually during successive cycles. The average diameter of mature granules was 3.2 ± 1.2, 4.75 ± 1.8, and 5.1 ± 1.4 mm in reactors B, C, and D, respectively; however, some of them had diameters reaching 10 mm (Fig. 1). Similar diameters of granules (6–9 mm) were observed by Wang et al. 10 in a reactor with a sedimentation time of 1 min and an organic load of 4.8 kg COD/m3 per day, however, usually the average diameter of the granules was lower and varied between 0.2 and 5 mm 4.
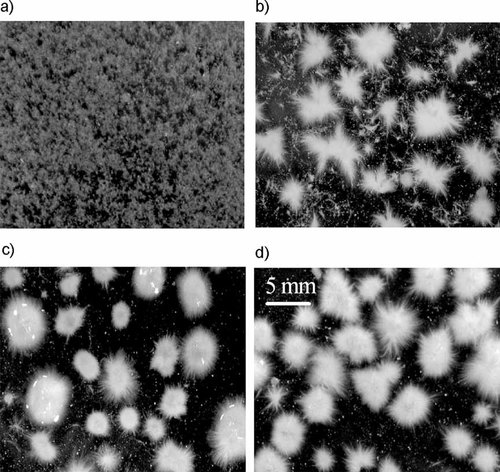
Biomass obtained in the reactors at different glycerol fraction load: activated sludge obtained at organic load of 0.2 g COD/g TSS per cycle (a), granular sludge obtained at organic loads from 0.6 to 1.3 g COD/g TSS per cycle (b–d).
In aerated SBRs, aggregates of microorganisms are in constant motion and the turbulence and shearing forces in the reactor promote regular, spherical shapes of the aggregates. The high h/d ratio of the reactor ensures a longer trajectory of circular flow, favoring aggregates shearing. Beun et al. 11 suggest using SBRs with high h/d (column SBRs) for granular sludge cultivation, since this makes it easier to select granules on the basis of settling velocity. In the present experiment we successfully cultivated granular sludge in SBR with a low h/d (1.53). However, because the hydraulic forces per unit section of the reactor were lower in comparison with column reactors, the biomass was less sheared and the granules dimensions were larger than noted in column reactors.
The morphology of granules depends strongly on the carbon source introduced to the reactor. The glycerol fraction is a complex mixture of substrates with glycerol as the dominant compound. Feeding the reactor with this substrate resulted in cultivation of granules with a fluffy surface stemming from the presence of filamentous bacteria (Fig. 1). Granules with a similar fluffy surface were observed by Tay et al. 12 and Beun et al. 11 in reactors fed with glucose and ethanol as the main sources of organic carbon. The growth of filamentous microorganisms in granules worsens the settling properties of biomass, increases the effluent TSS, and finally results in biomass washout and a decrease of TSS in the reactor 13. In the present research the morphology of the granules increased the SVI that remained at a level of 200 mL/g. The average biomass concentration was, therefore, rather low and equaled 2.1 ± 0.6, 1.4 ± 0.3, 1.3 ± 0.3, and 1.5 ± 0.48 g TSS/L for reactors A, B, C, and D, respectively.
In all reactors the efficiency of carbon removal remained at ca. 80% (Fig. 2). The average COD concentrations in the effluent were 75 ± 26.2, 115.5 ± 66, 295.3 ± 96, and 276 ± 97 mg O2/L in reactors A, B, C, and D, respectively. Only in reactor B, at organic load of 0.6 g COD g TSS−1 cycle−1, both granular sludge and a good quality of the effluent were obtained. A strong correlation (R2 = 0.77) was observed between the net granular sludge production in a cycle and the organic load (Fig. 3). The highest granular sludge production of about 0.31 ± 0.28 g TSS/L per cycle was noted at an organic load of 1.1 ± 0.27 g COD/g TSS per cycle. In reactor D the granular sludge production was lower than in reactor C. This may be evidence of an inhibiting effect or toxicity of methanol and soaps in the glycerol fraction at the highest applied load. The net biomass production is, in general, positively correlated with the load of organic substances in the reactor. Our results suggest that the use of the glycerol fraction as a carbon source enforces the optimization of organic load, because after reaching a particular value, the net production does not further increase but is inhibited by substrates introduced to the reactor.
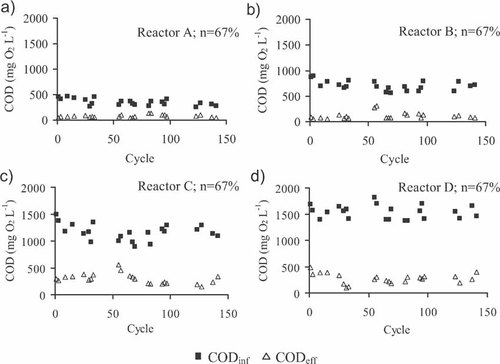
COD concentration in the influent (CODinf) and the effluent (CODeff) wastewater at organic carbon load of 0.2 ± 0.08 g COD g TSS−1 cycle−1 (a), 0.6 ± 0.16 g COD g TSS−1 cycle−1 (b), 1.1 ± 0.27 g COD g TSS−1 cycle−1 (c), and 1.3 ± 0.35 g COD g TSS−1 cycle−1 (d).
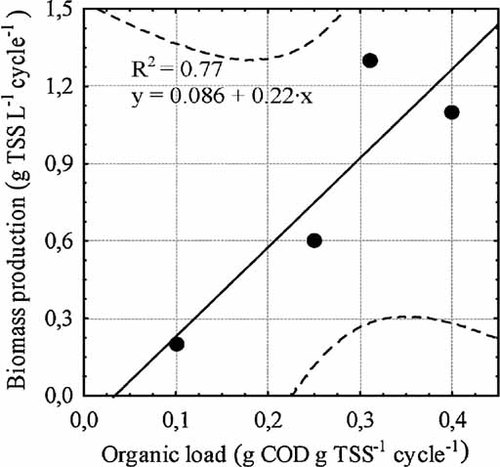
Correlation between the organic load and granular sludge production in an SBR cycle (R2 – determination coefficient).
In cycle 140, samples were taken in order to systematically measure COD concentration changes during the cycle. Most of the introduced COD was removed during the first 5 h of aeration following first order kinetics (Fig. 4). With increasing organic load, the rate constant (k) fell from 0.513 h−1 in reactor A to 0.446 per hour in reactor D. The initial rate of COD removal (r) was correlated with the organic load and varied from 123.12 to 472.76 mg COD/L per hour, in reactors A and D, respectively. These results indicate that in the future applications the aeration phase might be shortened to about 5–6 h while still maintaining the effluent quality.
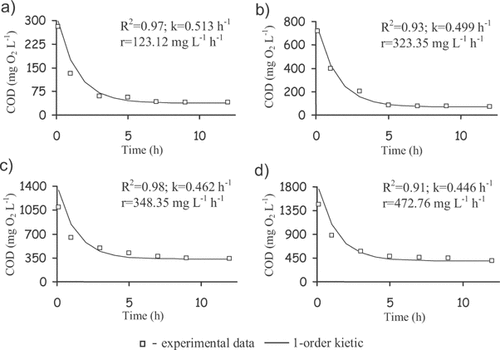
COD removal during an SBR cycle at organic carbon load of 0.2 ± 0.08 g COD g TSS−1 cycle−1 (a), 0.6 ± 0.16 g COD g TSS−1 cycle−1 (b), 1.1 ± 0.27 g COD g TSS−1 cycle−1 (c), and 1.3 ± 0.35 g COD g TSS−1 cycle−1 (d). For each organic carbon load determination coefficient (R2), the rate constant (k) and the initial rate (r) of COD removal are given.
Conclusions
The glycerol fraction generated in the biodiesel industry can be used for granular sludge production. The granular sludge obtained in the experiment can serve as seed sludge for granule-based SBRs, thus shortening the start-up period. The minimum organic load enabling activated sludge transformation into granules was 0.6 g COD/g TSS per cycle. The highest granular sludge production was noted at an organic load of 1.1 ± 0.27 g COD/g TSS per cycle. Granules were successfully cultivated in the reactors with a low h/d ratio, however, their diameter was significantly higher in comparison with those grown in column reactors.
Acknowledgements
This work was funded by the research project 528-0809-0801 of the Polish Ministry of Science and Higher Education.
The authors have declared no conflict of interest.