Simulation of Fluid Flow During Direct Synthesis of H2O2 in a Microstructured Membrane Reactor
Abstract
A microstructured membrane reactor has been developed to overcome the safety and productivity challenge of the direct synthesis of hydrogen peroxide. A single membrane is employed for separate, continuous dosage of the gaseous reactants hydrogen and oxygen to the solid catalyst present in the aqueous solvent. Using a custom OpenFOAM® model, the impact of catalyst-coated static mixers with different mixer geometries is studied. It is demonstrated that the custom fluid guiding elements outperform the investigated commercial static mixer under the flow conditions relevant to this application.
1 Introduction
Hydrogen peroxide (H2O2) is a promising “green” oxidant with application in paper, pulp and also wastewater treatment 1. The most common production route for H2O2 today uses the anthraquinone auto-oxidation process 2, responsible for more than 95 % of the total H2O2 production 3. With its high capital expenditures and required wastewater treatment 4, the process is currently only implemented at large scale, since it relies on the economy of scale to achieve viability 5. An alternative reaction route is the direct synthesis of H2O2 by selective conversion of H2 and O2 over a solid catalyst 6, 7. Different combinations of active material, support and reaction medium for the direct synthesis of H2O2 exist, with an extended overview given in 5. Nevertheless, all reaction systems studied for the direct synthesis route are facing the same safety concerns resulting from the direct contact of hydrogen and oxygen given the wide flammability range of the mixture 8, 9.
One of the approaches to cope with this issue are membrane reactors 9, 10. They prevent direct hydrogen/oxygen contact by dosing one or both reactants through a membrane into an organic or inorganic solvent, which contains the solid catalyst 6, 10-12. The major challenge in this kind of reactor is the development of a robust membrane 13. Another concept to tackle the safety concerns are microreactors. Their narrow channels hinder the propagation of an explosion and therefore massively increase the range of safe operation 14. The reactor concept presented in this paper combines both reactant separation with a membrane as well as microfluidic flow synergistically, targeting a new technology for on-site synthesis of ready-to-use hydrogen peroxide solutions 6, 15.
In order to decrease the diffusion length at any fluid velocity contrary to suspension flow catalysis 6, we investigated catalytically coated inserts in the flow channels. Specifically, we used the design of so-called fluid guiding elements (FGEs), recently developed in our institute 16. The impact of the inserts was investigated numerically in a CFD simulation using OpenFOAM® (OF) 17. Special attention is given to the impact of the residence time and channel insert geometry on the reaction.
2 Materials and Methods
2.1 Design of the Membrane Reactor
Fig. 1a illustrates the reactor concept, which was adapted from an earlier reaction module designed in our institute 6. The FGEs are produced using an additive manufacturing technology (laser-beam powder bed fusion, LB-PBF) which places some restrictions on the geometry, in particular avoiding overhangs 18. For this reason, the curvilinear liquid channel design introduced by Selinsek et al. 6 was altered to a straight geometry while the gaseous reactants hydrogen and oxygen were introduced in an alternating manner over the dosing membrane, as illustrated in Fig. 1b. The FGEs do not generate turbulence but aim for a laminar guiding of the fluid flow to keep the pressure drop low by smart division and recombination of the flow and generated partial flows, respectively 16. After partial flow A had contact with the mass transferring region for resaturation, the O2- or H2-dosage area in Fig. 1b, it is directly guided away from the place of exchange to the channel bottom to equilibrate. Then, the next equilibrated partial flow B is led to the region of transfer. The contact time of the fluid with the gas was kept short to keep the diffusion depth of the resaturating gas considerably small in order to guarantee a large concentration gradient and thereby enhance the mass transfer. The same principle has previously been described for heat transfer .
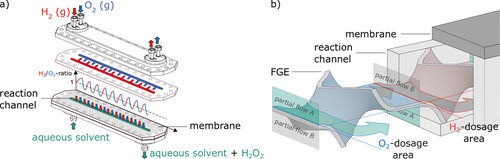
2.2 Material Properties
The transport and material properties are summarized in Tab. 1, with all properties corresponding to a temperature of 298 K (simulations were run at this temperature, and future experiments will be conducted at this temperature). The influence of the additives H2SO4 and NaBr on the fluid properties of the aqueous reaction medium were neglected. Similarly, due to the low solute concentrations expected, it was assumed that the dissolved species H2, O2 and H2O2 did not alter the fluid properties. Only binary diffusion of the individual solutes in the liquid reaction medium as described by the Fickian diffusion model was considered. The simple solution diffusion model, as described in 19, was used to model the mass transport through the dense polymer membrane.

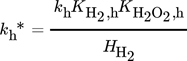
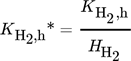

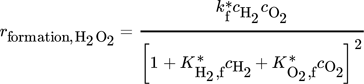
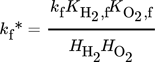
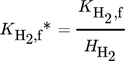
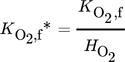
Moreover, a layer thickness of 4 µm with a porosity ε of 0.4 and tortuosity τ of 6, reported for silica coatings employed in the direct synthesis was assumed for all simulated structures 29. Although Gemo et al. 30 provided the experimental proof of negligible internal mass transfer limitations within a comparable operation range for a spherical catalyst of 15 µm diameter, the impact of mass transfer limitations within the catalyst coating layer on the macroscopic reaction rates of the direct synthesis of H2O2 was considered by effectiveness factors. This allowed further studies of a wider catalyst layer range. The effectiveness factors were calculated using Matlab®. All kinetic parameters used are listed in Tab. 2 and 3.
Property |
Value |
---|---|
k0,h [molH2O2kgcat−1s−1] |
25.57 · 106 |
K0,H2,h [Pa−1] |
3.36 · 10−10 |
K0,H2O2,h [m3mol−1] |
2.95 · 10−4 |
k0,f [molH2O2kgcat−1s−1] |
1.60 · 103 |
K0,H2,f [Pa−1] |
2.76 · 10−4 |
K0,O2,f [Pa−1] |
3.38 · 10−8 |
Property |
Value |
---|---|
Ea,h [kJ mol−1] |
43.7 |
ΔHH2,h [kJ mol−1] |
−23.1 |
ΔHH2O2,h [kJ mol−1] |
−4.7 |
Ea,f [kJ mol−1] |
22.3 |
ΔHH2,f [kJ mol−1] |
10.1 |
ΔHH2O2,f [kJ mol−1] |
−12.2 |
2.3 Numerical Model of the Reactor
OF provides a finite-volume-based framework for the creation of custom computational solvers for continuum mechanics problems 17. The CAD model of the FGEs generated in Autodesk® Inventor® was used via STL format import to create the numerical grid using OF meshing tools. The simulation domain consisted of a rectangular channel, which contained the microstructured FGE inserts. The channel used for the investigations had a width of 6 mm, a height of 1.97 mm and a length of 44.5 mm. Additional inlet and outlet zones of 11 mm length each were implemented in order to guarantee a fully developed flow. These zones equal the maximum expected hydrodynamic entrance length calculated analytically.
In the simulation, the flow regime present in the liquid channel was assumed to be laminar, due to the low liquid flow rates in the range of milliliters per minute as used in the concept presented in 6 and 15 as well as channel geometries in the millimeter range. The maximum expected Reynolds number Re calculated in a void rectangular channel with a width of 6 mm and a height of 1.97 mm for an estimated, elevated flow rate of 16 mL min−1 was 75, which confirmed the validity of this assumption. Moreover, the system was considered isothermal and the flow field incompressible due to the nature of the aqueous reaction medium under the conditions given.
Three phases are present in the actual reactor, namely the gaseous H2 and O2 flowing through separate reactor channels, the solid membrane and the solid catalyst applied onto microstructured FGEs as well as the liquid reaction medium. To simplify the problem, a single-phase model was adopted for the simulation by merely considering the liquid phase with the dissolved reactants and the product. Thus, the membrane and the catalyst coating were defined as system boundaries. Moreover, it was assumed that the feeding gas phases remain constant in their composition, even in case of possible cross-contamination of the H2-gas channel with O2 by desaturating gas and vice versa. This is justified in case of the gas channels being flushed sufficiently and permanently with the corresponding pure gas. Fig. 2 shows a schematic representation of the simulated geometry. The implemented patches of the simulation and the applied boundary conditions can be taken from Fig. 3.
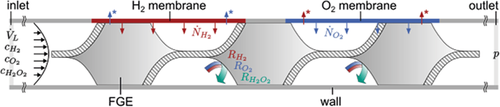
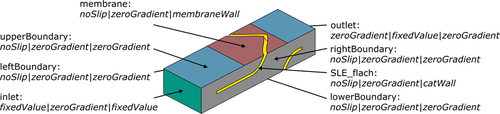
OF's blockMesh utility was used for the background mesh, while snappyHexMesh was used to generate the computational grid so that the FGE features were captured correctly and high gradient regions were resolved particularly well. Mass diffusion processes impose much stricter constraints on mesh resolution than fluid dynamics 31. Thus, at least three cell layers were used within the concentration boundary layer to ensure the proper capture of concentration gradients and mass transport phenomena as recommended by Bothe and Reusken 31. Correspondingly, three additional grid layers were added within a distance of 0.03 mm, which is lower than the expected minimum concentration boundary layer thickness estimated from mass transfer correlations. To ensure sufficient grid refinement, different grid resolutions were investigated and their maximum residuals as well as the resulting maximum species imbalances were evaluated as control quantities. The acceptable residual for a stable result was set to 1 · 10−4 for the concentration. The errors obtained from mass and individual species balances applied to the overall system had to be below the threshold of 1 %. A grid of 7 million cells of an average size of 10−13 m−3 was finally used in the simulation.
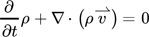



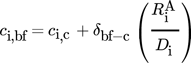

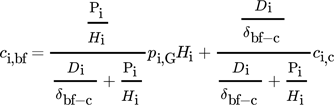
The derived solver was verified by the comparison with the (semi-)analytical solutions of three different configurations of a simplified, cylindrical channel geometry evaluated using Matlab®.
2.4 Considered Case: Influence of the Geometry of the Microstructured Channel Insert on Reactor Performance
As the catalyst is applied as a coating onto the microstructured channel inserts, the inserted structure's geometry is expected to have a considerable influence on the reactor performance. This was investigated by carrying out CFD simulations with two different geometries of mixing inserts. A commercial static mixer (SMX®, from Sulzer AG, Winterthur, Switzerland) with a geometry adapted from 32 was compared with a customized FGE developed in our institute. While the inserts' overall widths, heights and lengths are identical, the surface area of SMX® available for the application of catalyst exceeds the FGE's surface area with an area ratio SSMX/SFGE of 2.27. Similarly, the volume reduction of the liquid flow channel due to the inserted structure was higher in case of the SMX® resulting from its slightly bigger volume. This leads to a volume ratio of the resulting liquid volumes of VL,SMX/VL,FGE = 0.94. The influence of the volumetric flow rate was evaluated by carrying out simulations with both geometries over range between 0.7 and 15.9 mL min−1. The system pressure and temperature were set to 2 bar and 298 K. In all simulations, a membrane arrangement of alternating H2 and O2 dosing zones of 2 mm length each and a distance of 1.27 mm in between was chosen.
3 Results and Discussion
A comparison of the pressure drop over the length of the liquid flow channel for the case of no insert, the SMX® insert and FGE insert is shown in Fig. 4. At low residence times (corresponding to higher flow velocities) the pressure drop for SMX® inserts is significantly higher than for FGE inserts. At higher residence times, the difference between the pressure drop for SMX® versus FGE is smaller. The calculated H2O2 outlet concentrations cH2O2,out achieved with the two different types of microstructured channel inserts are compared in Fig. 5a. Fig. 5b shows the comparison of the H2O2 outlet concentrations cH2O2,out per surface area of the respective insert Sinsert. As a reference, the corresponding values for a void channel without inserts but with catalyst coated lower and side walls are given additionally in all graphs.
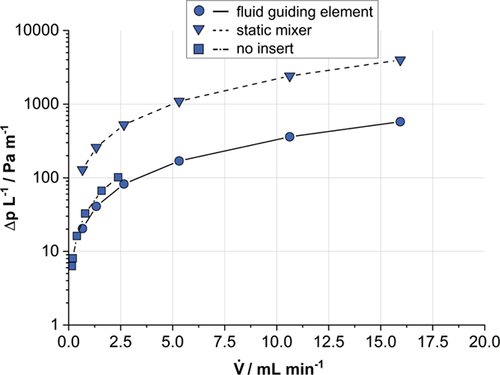

At all investigated modified residence times (), the performance of the reactor with SMX® inserts in terms of cH2O2,out appears to be superior to the one with FGE inserts (Fig. 5a). This is to be attributed to the SMX's higher surface area and the corresponding increased amount of catalyst present in the system, the H2O2 outlet concentration ratio cH2O2,SMX/cH2O2,FGE exceeds the surface area ratio SSMX/SFGE at all residence times. This may be explained by an enhancement of the SMX's mixing properties at increased liquid velocities in the laminar flow regime, which is consistent with findings of Rahmani et al. 33. On the other hand, the FGE is beneficial in terms of the overall pressure drop (Fig. 4) over the length of the liquid flow channel as the structure does not contain any abrupt changes in its geometry and thus imposes less resistance to the liquid flow 16. It can also be seen from Fig. 5b that the achieved H2O2 outlet concentration relative to the insert's surface area of the FGE (i.e., the productivity per catalyst mass) is even significantly higher than the one of the SMX® at all residence times. With H2O2 hydrogenation as consecutive reaction path in the reaction network, comparably low residence times (high tmod) proved to be beneficial 15, which is why it may be concluded that the implementation of catalyst-coated FGEs has a beneficial effect on the reaction system.
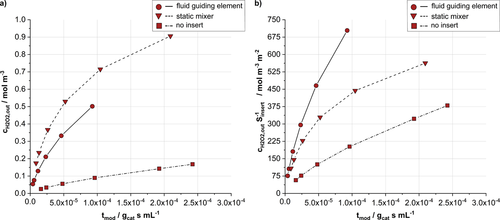
4 Conclusion
In the simulations presented, the influence of the microstructured insert's geometry on the reactor performance quantified by the H2O2-outlet concentration cH2O2,out was investigated at different volumetric flow rates by comparing a FGE insert with a standard SMX® at different flow rates. Higher product concentrations in general were found to be achieved with the latter. This is attributed to the static mixer's higher surface area and therefore high amount of catalyst present in the system. The use of FGEs, however, is beneficial in terms of pressure drop at lower residence times and higher productivity relative to a defined catalyst mass is achieved.
To conclude, the basis has been laid for the optimization of a microstructured membrane microreactor for the direct synthesis of H2O2 facilitated by spatially resolved CFD simulations. Further research will validate the implemented solver against experimental results, paving the way to a precise reaction control of this demanding multiphase reaction.
Acknowledgements
Financial support by the German Research Foundation (DFG) through the Research Unit 2383 ProMiSe under Grant No. DI 696/13-2 is gratefully acknowledged. The authors acknowledge support by the state of Baden-Württemberg through bwHPC. Open access funding enabled and organized by Projekt DEAL.
Symbols used
-
- Di,H2O [m2s−1]
-
Fickian diffusion coefficient of gas i in H2O
-
- c [mol m−3]
-
molar concentration
-
- ci,bf [mol m−3]
-
concentration of the gas i at the boundary face
-
- ci,inlet [mol m−3]
-
concentration of the gas i at the inlet of the simulated field
-
- ci,sat [mol m−3]
-
saturation concentration of the gas i, according to Henry's law
-
- Hi [mol m−3Pa−1]
-
Henry constant of gas i
-
- ΔHi [J mol−1]
-
reaction enthalpy
-
- K [Pa−1]
-
sorption equilibrium constant
-
- k [–]
-
kinetic rate constant
-
- k0 [–]
-
pre-exponential factor (reaction rate)
-
- L [m]
-
length
-
- mcat [g]
-
catalyst mass
-
- pi [Pa]
-
partial pressure of gas i
-
- Ri [–]
-
rate of generation or destruction of species i due to chemical reactions
-
- r [mol s−1kg−1]
-
reaction rate per catalyst mass
-
- T [K]
-
temperature
-
- tmod [gcoats mL−1]
-
modified residence time
-
- SSMX/FGE [m2]
-
surface area of the inserts (SMX®/FGE)
-
- Sinsert [m2]
-
surface area of the respective insert
-
- v [m s−1]
-
velocity
-
- VL,SMX/FGE [m−3]
-
volume in the liquid channel after implementing the insert (SMX®/FGE)
-
[mL min−1]
-
volumetric flow rate
Greek letters
-
- δ [m]
-
distance, thickness
-
- ε [–]
-
porosity
-
- η [–]
-
catalyst effectiveness factor
-
- μ [Pa s]
-
dynamic viscosity
-
- νH2O [m2s−1]
-
kinematic viscosity of H2O
-
- τ [–]
-
tortuosity
-
- ρ [kg m−3]
-
material density
-
- Ρi [mol m−2s−1Pa−1]
-
membrane permeance of gas i
Sub- and Superscripts
-
- A
-
per unit area
-
- bf
-
boundary face
-
- c
-
center
-
- G
-
gas
-
- H2
-
hydrogen
-
- H2O2
-
hydrogen peroxide
-
- L
-
liquid
-
- O2
-
oxygen
-
- wc
-
wallcoat
-
- *
-
adapted property
-
-
vector quantity x
Abbreviations
-
- FGE
-
fluid guiding element
-
- PDMS
-
polydimethylsiloxane
-
- PET
-
polyethylene terephthalate
-
- PI
-
polyimide
-
- OF
-
OpenFoam®