Methane Pyrolysis for CO2-Free H2 Production: A Green Process to Overcome Renewable Energies Unsteadiness
Abstract
The Carbon2Chem® project aims to convert exhaust gases from the steel industry into chemicals such as methanol to reduce CO2 emissions. Here, H2 is required for the conversion of CO2 into methanol. Although much effort is put to produce H2 from renewables, the use of fossil fuels, especially natural gas, seems to be fundamental in the short term. For this reason, the development of clean technologies for the processing of natural gas with a low environmental impact has become a topic of utmost importance. In this context, methane pyrolysis has received special attention to produce CO2-free H2.
1 Introduction
One of the major challenges of our time is to decrease the level of greenhouse gases (GHG) in the atmosphere to reduce global warming. In this context, Germany is expected to become carbon neutral by 2050 (Fig. 1) 1, thus, much effort has to be put to diminish CO2 emissions. To achieve this goal, the development of new strategies to use CO2 as a raw material has received special attention in the last years 2. Among the CO2 emitters, the iron and steel industry plays a major role in the industrial sector in Germany 3. Here, the Carbon2Chem® project emerges precisely with the objective of converting the gas emissions from the steel industry into valuable chemicals. Specifically, an important route followed within the Carbon2Chem® project is to convert the exhaust gases into methanol 2. The synthesis of methanol from steel mill exhaust gases involves the hydrogenation of CO2. Currently, the production of hydrogen envisaged within the project is based on water electrolysis using electricity from renewable resources such as wind and solar energies. When the electricity is generated exclusively from renewable energy, water electrolysis is the only available technology capable of producing hydrogen with zero carbon footprint, obtaining oxygen as the sole by-product 4. Nevertheless, water electrolysis based on renewables is accompanied by some challenges, such as fluctuations of renewable energy, geographic limitations, and problems related to energy storage 5.
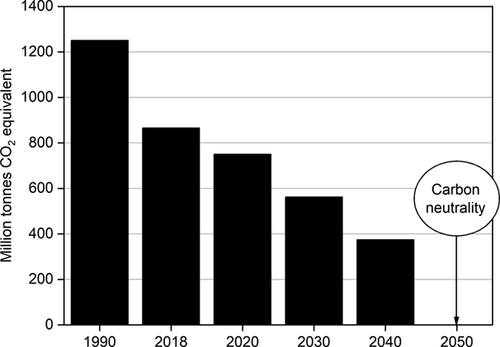
Taking into account that a typical industrial plant operates for 8000 hours per year 6, hydrogen has to be provided during all this time to get a continuous CO2 hydrogenation and, therefore, to avoid the release of industrial CO2 emissions to the atmosphere. In addition, an increasing number of annual operating hours will also increase the economic feasibility of the applied CO2 hydrogenation. Fig. 2 shows the annual full load hours of wind and solar energy in Germany in 2019 7. In the case of offshore wind energy, the problem associated with energy transportation has still to be overcome. Therefore, onshore wind and solar energies are nowadays the renewable sources available for a sustainable hydrogen production, but they could provide hydrogen only for up to 2000 hours a year. An additional problem is related to power fluctuations, which means that there will be periods with energy deficit but also others with excess energy production. The extra hydrogen produced could be stored and used when needed. Nevertheless, large-scale hydrogen storage remains a challenge at present 8. In addition to this, although the use of renewable energy will grow in the next years, it is predicted that in the short term renewable powers will represent only 16 % of the global energy (Fig. 3) 9. This is far too less to face the challenges coming along with the reduction of CO2 emissions. For these reasons, the production of hydrogen cannot depend entirely on renewable energies and additional hydrogen sources are required.
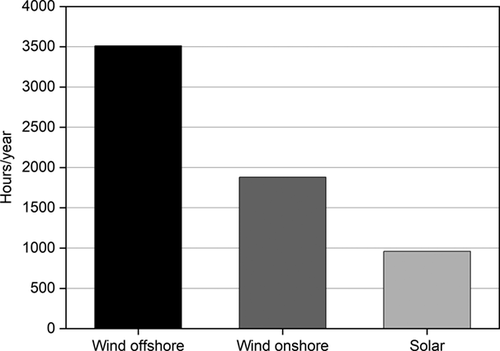
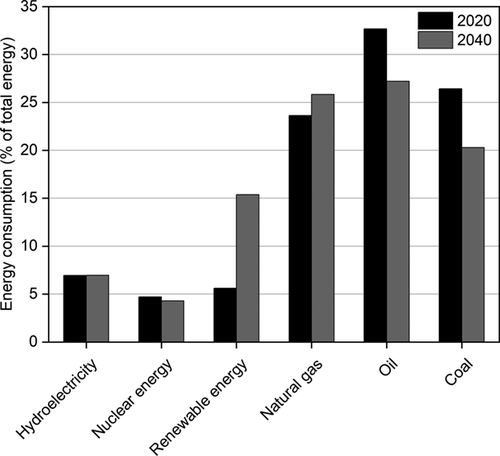
The thermal decomposition of methane, which is the main component of natural gas, is a suitable technology to provide clean hydrogen when renewable power is not sufficient to fulfill the hydrogen demand. This process is usually referred to as methane pyrolysis. Methane pyrolysis splits CH4 directly into its components, i.e., hydrogen and carbon. Unlike other technologies that use fossil resources, such as coal gasification or steam methane reforming, the greatest benefit of methane pyrolysis is the production of CO2-free hydrogen. Solid carbon is the only by-product resulting from the thermal decomposition of methane, so neither a CO2 separation step nor its subsequent storage is needed 10-13. The carbon product could be marketable, which would improve the economics of the process depending on its characteristics and price 10, 13-17. Currently, there is a lack of market for the large amounts of carbon resulting from methane pyrolysis, so new applications have to be found 13, 17. Nevertheless, the development of feasible industrial applications for the carbon produced to achieve economic benefits is still challenging 14. In addition, it is unlikely that there will be a dramatic increase in carbon use in the near future 13. For these reasons, an economic process that does not depend on the selling price of the carbon by-product has to be industrially developed. Despite this limitation, the clean character of methane pyrolysis makes this technology a potential candidate to address the lack of hydrogen via renewables. Methane pyrolysis can supply the necessary hydrogen to achieve a steady conversion of CO2 to methanol, and thus, a continuous removal of CO2 emissions.
2 Hydrogen Production Technologies
Water is the most abundant and convenient raw material for hydrogen production since its processing via electrolysis produces only hydrogen and oxygen 18. The electricity needed for water electrolysis must come from renewable resources to convert this technology into a purely green process. However, renewable energies fluctuate and cannot provide hydrogen during all the operating hours of an industrial methanol plant based on steel mill exhaust gases. Therefore, the additionally required hydrogen has to be supplied by other alternative processes.
Like water, biomass is considered a renewable feedstock. Biomass can be converted into a hydrogen-containing gas mixture via gasification. Although the technology for biomass gasification is already well developed on a large scale, the production of hydrogen accompanied by high amounts of CO2 as well as the exhaustive post-treatments for hydrogen purification are the main drawbacks of this technique 19-21. For this reason, biomass gasification is generally intended for the production of syngas to generate energy or synthesize fuels rather than for hydrogen generation 22.
Nowadays, the production of hydrogen from fossil resources is still preferred over renewable raw materials due to economic and technical reasons for large scale production 23, 24. Coal gasification and steam reforming of natural gas are the most popular technologies for producing hydrogen using fossil fuels as feedstock 14. Coal gasification currently accounts for 18 % of the global hydrogen production 10. In this process, the partial oxidation of coal is carried out in a high-temperature and high-pressure reactor, giving rise to a mixture of hydrogen and carbon oxides (syngas) 25, 26. The energy efficiency of coal gasification is relatively high (63 %), but the large carbon footprint makes this process an undesirable technology 19, 23.
Methane, the main component of natural gas, is a suitable source of hydrogen since it has the highest H/C ratio among all hydrocarbons and, thus, a larger amount of hydrogen can be obtained compared to that of carbon 27. Steam methane reforming (SMR) is the most common hydrocarbon-based technology for hydrogen production and satisfies approximately 48 % of the global hydrogen demand 10. SMR involves the catalytic reaction between methane and steam to produce hydrogen and carbon oxides 10, 21. Additional hydrogen can be produced by the reaction between the formed carbon monoxide and water via the water-gas shift reaction 10. Although SMR is highly energy-efficient (75 %), the production of high CO2 emissions forces the separation and sequestration of CO2 via a carbon capture and storage (CCS) process. The greenhouse gas emissions are decreased by the use of CCS systems, but the net energy efficiency drops to 60 % 28.
Methane pyrolysis is considered a suitable alternative technology for hydrogen production. Methane pyrolysis implies the thermal decomposition of methane to form hydrogen and solid carbon 23, 29. From the thermodynamic point of view, the decomposition of methane is energetically much more economical than water electrolysis, i.e., only 37.5 kJ are necessary to produce 1 mol of H2, whereas 286 kJ per mol H2 are required in water electrolysis (Fig. 4). Although methane pyrolysis is not – unlike water electrolysis – a sustainable process due to the use of a fossil raw material, this technology can be a timely alternative owing to the large amounts of natural gas reserves available.
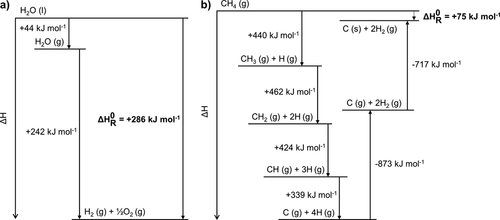
In comparison to SMR, methane pyrolysis is a more environmentally friendly technology since the formation of CO/CO2 is avoided and only solid carbon is obtained as reaction by-product 10-13. The sequestration of carbon as a stable solid is obviously more favorable than the capture of CO2 from the gas product after SMR. Methane pyrolysis has an energy efficiency of 58 %, which is comparable to SMR when the separation of CO2 is taken into account 28. Nevertheless, the application of methane pyrolysis is limited by the requirement of a solid catalyst, which rapidly deactivates 10. Additionally, although the carbon product is marketable, there is still today an absence of established markets for the large carbon by-product quantities 13, 17. The development of new markets and applications for the produced carbon may improve the economics of this process 10, 13-17, although it is unlikely to find markets that can accommodate such large amounts of carbon 14. Despite these limitations, methane pyrolysis appears to be the greenest alternative to address the lack of hydrogen from renewables in an industrial methanol plant based on exhaust gases from the steel industry.
3 Reaction Mechanism of Methane Pyrolysis
-
Methane chemisorption on the catalyst surface
-
Dissociation of chemisorbed CH4 into a methyl radical and a hydrogen atom:
-
(1)
-
Stepwise dissociation reactions resulting in elemental carbon and hydrogen:
-
(2)
-
(3)
-
(4)
-
Aggregation of atomic hydrogen into molecules:
-
(5)
-
Carbon nucleation followed by the formation and growth of carbon deposits

In the early 1960s, several authors 46, 47 calculated the activation energy of the initiation step according to their experimental data and compared this value with the activation energies of Eqs. (1) (101 kcal) and (6) (94 kcal) determined in previous studies. The values obtained in 46, 47 were closer to the activation energy of the second equation, therefore, this reaction was assumed to be the initiation step. Some years later, the initiation step of methane pyrolysis was studied in depth by single pulse shock tube experiments 37. Contrary to the previous authors, here, it was concluded that the splitting of methane into a methyl radical and a hydrogen atom (Eq. 1) was the initiation step. The experimental results obtained in this work demonstrated that Eq. 6 could not correspond to the initial reaction step. In another study, although both equations were proposed as possible initiating reactions, it was stated that methane decomposition would most likely start from Eq. 1 36. These controversial results can be explained by the different temperature regimes used in the investigations 48. Researchers who investigated methane pyrolysis in a temperature range of about 900–1400 °C suggested a decomposition of methane following Eq. 1. On the other hand, those who studied methane pyrolysis between ca. 1400 and 1900 °C attributed Eq. 6 to the initiation step.
-
The carbon-containing gas precursor, e.g., a hydrocarbon, adsorbs and dissociates in elemental carbon on the catalyst surface.
-
The carbon atoms dissolve into the bulk of the catalyst particles giving rise to a liquid metastable carbide and diffuse within the particles.
-
The solid carbon precipitates at the backside of the catalyst particles and forms carbon nanostructures.
The VLS mechanism is well accepted because it is in good agreement with the apparent activation energy obtained for the growth of carbon nanofibers over metal catalysts (Fe, Ni, Co) 51. This mechanism considers carbon diffusion through the catalyst bulk as the rate-limiting step for the growth of carbon nanofilaments 49, 52. A more recent study by Helveg et al. 53 using in-situ analytical techniques suggests a modification of the VLS model. Contrary to the VLS mechanism, these authors propose that carbon atoms do not necessarily diffuse into the bulk of the metal particles. In this case, it is established that surface transport of carbon atoms is the rate-determining step for the nanoparticle growth. This mechanism was later corroborated for the growth of carbon nanotubes and graphene by other authors 54, 55.
Although it is widely believed that methane pyrolysis follows a radical mechanism, only few works are validated with experimental data. Many recent studies are based on old research and no progress has been made in the last years. In fact, the kinetic parameters (pre-exponential factor, activation energy, and reaction order) of each intermediate elementary reaction step are still unknown 20. On the other hand, the VLS model proposed by Baker et al. 49 or the mechanism suggested by Helveg et al. 53 establish a rate-limiting step for the growth of carbon nanoparticles that is not taken into account in the radical mechanism. Therefore, it is still unclear whether the overall rate-determining step corresponds to the dissociation of CH4 into a methyl radical and a hydrogen atom, to the carbon diffusion through the catalyst bulk or at the surface of the catalyst particle, or to a combination of these steps. Additionally, there is no evidence of how different catalysts or operating conditions affect the limiting step and the reaction mechanism in general. The reaction mechanism has to be fully elucidated to develop catalysts that accelerate the kinetics under optimized experimental conditions. Only in this way further improvements in catalytic activity will be achieved.
4 Catalytic Methane Pyrolysis
Methane is a very stable molecule due to the strong C–H bonds and the symmetry of its molecular structure 20. For these reasons, methane pyrolysis occurs only at temperatures above 1100–1200 °C in the non-catalytic process. However, the incorporation of a catalyst can significantly reduce the reaction temperature depending on its nature 20, 23, 29, 56. Several metal and non-metal catalysts (generally carbon materials) have been developed for this process over the years 29. Additionally, some molten metals and molten salts have been successfully applied for methane pyrolysis in recent years 26.
4.1 Metal Catalysts
Transition metals like Ni, Fe, and Co have been widely studied as active species for methane pyrolysis 20, 29, 57-61 due to their high activity, moderate operating temperature, and the possibility of producing valuable carbon nanotubes as by-product 62. Their 3d orbitals are partially filled and can accept electrons from the C–H bonds of methane, which facilitates its decomposition 20, 29, 57-61, 63. These metals also offer high solubility and carbon diffusion through their crystalline structure 64. The following trend with respect to their activity has been reported: Ni > Co > Fe 57, 60, 61, 65-67. Nickel-containing catalysts have been extensively investigated since Ni is considered the most active metal for this process 68, 69. However, nickel-based catalysts deactivate rapidly at temperatures above 600 °C because the active metal sites are encapsulated within the carbon formed during the reaction 20, 27, 57, 60, 66, 70-74. In the case of cobalt catalysts, their activity is lower compared to nickel catalysts 75, 76. In addition to this, cobalt has toxicity issues and a higher cost than nickel 56, 60, 77. These are probably the reasons why cobalt-based catalysts have not received much attention lately 20.
When metal catalysts are used, a regeneration process is required to remove the carbon deposits from the spent catalyst after the reaction. Many authors have proposed to regenerate metal catalysts by burning the carbon with air or steam. However, the production of COx during the regeneration process is a major disadvantage against the green character of methane pyrolysis 78-87. Therefore, to mitigate any COx emission, other regeneration techniques for metal catalysts have to be investigated. Until a robust market for the carbon by-product is established and other regeneration methods are available, storing the produced carbon seems to be the most reasonable solution. Nevertheless, since the carbon by-product is contaminated with the active metal, the use of nickel or cobalt catalysts should be avoided due to their high toxicity. Consequently, cheaper and safer catalysts, such as iron materials, are needed for the industrial application of methane pyrolysis 87.
Iron is less active than nickel 76 but more resistant to carbon deactivation and, hence, more stable at higher temperatures 71, 73, 88 due to the higher diffusion rate of carbon in iron 65, 66, 71, 89. Iron catalysts have been reported to be stable up to 700–1000 °C 20, 73, 86, 90. They are considered the best candidate to industrialize the pyrolysis of methane 86, 91 because they are cheaper and more environmentally-friendly than Co- and Ni-based catalysts 91-94. Supported iron catalysts 86, 91, 95-98, but also some bulk, non-supported catalysts (Fe2O3, Fe3O4) 73, 90, 99, 100 and organometallic precursors 43, have been tested. The use of organometallic compounds as iron precursors allows the in situ generation of catalysts for methane pyrolysis. For instance, the decomposition of iron pentacarbonyl (Fe(CO)5) and ferrocene (iron dicyclopentadienyl, Fe(C5H5)2) produces active iron clusters for the pyrolysis of methane, but also gives rise to different gases 43. In the decomposition of iron pentacarbonyl, CO is obtained as by-product. Ferrocene decomposes into a gas mixture composed of hydrogen, methane, and cyclopentadiene, among other compounds. Although the concentration of these gases is low, in both cases, a purification process must be accomplished to remove the undesirable impurities from the outlet gas. The contamination of the gaseous product with unwanted compounds may explain the scarce application of organometallic iron precursors in the decomposition of methane.
Some improvements in iron catalysts still need to be made for industrial implementation. The main challenge is to unravel the reaction mechanism over iron catalysts to develop materials with enhanced activity at lower temperatures. Likewise, cheaper iron catalysts with a better stability and alternative regeneration methods without COx emissions must be explored.
4.1.1 Role of Metal Promoters and Catalyst Support
Many efforts have been made to extend the lifetime of metal catalysts, especially that of nickel-based materials. Here, the incorporation of a second metal as a catalyst promoter has been shown to have a positive effect on the catalyst activity and stability. Palladium and copper are the most common metal dopants of nickel catalysts. The resulting metal alloys (Ni-Pd, Ni-Cu) with high lattice constants provide a higher capacity for carbon accumulation, so that the catalyst deactivation is inhibited for longer reaction times 64, 101. Metal promoters create a balance between the dissociation rate of methane and the diffusion rate of carbon 102. In other words, carbon diffusion through the metal particles is favored by catalyst promotion. As a result, the formation of encapsulating carbon on the active sites is prevented and the catalyst lifetime is prolonged 61, 64, 101, 103. Additionally, suitable dopants enhance the dispersion of the metal particles on the catalyst support 66, 104-107 and improve the reducibility of the metal species. The higher reducibility is related to a hydrogen spillover effect induced by some dopants, such as Pd and Cu. These metals are active sites for the dissociation of hydrogen during the catalyst reduction step prior to the reaction, which facilitates the formation of metallic nickel 63, 64, 106-108. Furthermore, the weaker interaction between the metal particles and the support after catalyst doping also contributes to an improved reducibility of the metal species 101, 103, 106, 107.
Different catalyst supports have been investigated to avoid thermal sintering and encapsulation of the active metal sites 63, 67, 95, 109, 110. The metal-support interaction is a critical parameter that affects the dispersion and reducibility of the metal species and, thus, the catalytic performance. A strong metal-support interaction prevents sintering and agglomeration of the metal particles and improves their fine dispersion on the support. Consequently, the stability of the catalyst is enhanced. Nevertheless, a very strong interaction between the metal and the support may hinder the reducibility of the metal precursor oxides or result in the formation of hardly reducible metal-support species (solid solutions, spinel structures) that are inactive for the decomposition of methane 63, 89. As a consequence, the formation of active metal sites is prevented and the catalytic activity is negatively affected 86, 89, 91, 111-115. Despite the inactivity of the metal-support species, some authors have reported a positive role of these species since they could avoid agglomeration of the metal particles 86, 91. In general, supported catalysts with well-dispersed and easily reducible metal species result in better catalytic performance. Therefore, a suitable metal-support interaction must be found to achieve a compromise between the dispersion and reducibility of the metal species.
4.2 Carbon Catalysts
-
lower cost
-
higher resistance to temperature and better stability
-
safe storage of the carbon product due to non-toxicity
-
tolerance to impurities, e.g., sulfur resistance
-
no contamination of the carbon by-product with metal particles
-
mitigation of CO2 emissions (unlike metal catalysts: the regeneration of metal catalysts by burning the carbon accumulated on the catalyst surface produces significant amounts of COx)
-
the produced carbon may also have some catalytic effects
-
no need for catalyst regeneration
Different carbon materials have been investigated for the thermal decomposition of methane: activated carbon (AC), carbon black (CB), glassy carbon, acetylene black, graphite (graph), diamond powder, coal char, fullerene soot, fullerenes C60/70, carbon nanotubes, and ordered mesoporous carbons (CMK materials). According to their crystallinity, carbon materials are classified into highly ordered (graphite and diamond), less ordered (turbostratic and pyrolytic carbon, such as glassy carbon, fullerene soot, fullerenes C60/70, carbon nanotubes, and CMK materials), and disordered (amorphous, microcrystalline, such as activated carbon, carbon black, coal char, and acetylene black) carbons 23, 79. Amorphous carbons are formed by hexagon plates or layers parallel to each other but without following an order. On their surface, the regular arrangement of carbon bonds is disrupted, leading to dislocations, low-coordination sites, vacancies, atoms with free valences, discontinuities, edges, defects, and other energetic abnormalities that are known as high-energy sites (HES). A high number of HES usually means a low carbon crystallite size, and it is generally accepted that they determine the initial activity of carbons in methane decomposition. HES are considered the main fraction of active sites in carbon catalysts since methane can interact with the chemically reactive edges of carbon crystallites, giving rise to its dissociation into carbon and hydrogen 20, 62, 79. Disordered forms of carbon with a high defect concentration (activated carbon, carbon black) have been reported to be catalytically more active than ordered structures (graphite, diamond powder) 20, 79, 81, 118. The following order can be established in the catalytic activity of carbons: amorphous > turbostratic > ordered 79.
4.2.1 Initial Activity of Carbon Catalysts
Among carbon catalysts, activated carbons and carbon blacks are the most studied due to their high catalytic activity compared to well-ordered structures 17, 20, 23, 119, 120. Activated carbons are initially more active than carbon blacks, but carbon blacks result in more sustainable processes due to their higher stability 73, 78-81, 118, 121-127. The catalytic performance of activated carbons and carbon blacks has been compared to other carbon materials in several works. For instance, the activity of different carbons (CB, AC, multi-walled carbon nanotubes (MWNT), and graphite) has been investigated at 1100 °C 73. The following trend was established with respect to the initial catalytic activity: AC (mesoporous) > CB (black pearls 2000) ≈ AC (microporous) > CB (vulcan XC72) > MWNT > graph.
The high initial activity of mesoporous activated carbons can be linked to the high density of C-graphene defects 62, 128. In fact, a linear correlation between the initial activity and the amount of defects on the graphene layers has been reported in several works 81, 82.
The initial decomposition rate of methane over carbon catalysts has been related not only to the defect concentration but also to other factors, such as the concentration of oxygenated groups or the specific surface area. In several works, it was found that the initial activity of carbons depends on the concentration of oxygenated groups on the catalyst surface, i.e., methane can react directly with these oxygen groups or more likely these groups are released as COx creating active sites that promote methane dissociation. Nevertheless, it was concluded that the catalytic activity of carbons cannot be attributed only to the presence of these oxygenated groups. Surface defects, dislocations, vacancies, and low-coordination sites play a major role as well 79, 122, 125, 129. Concerning the specific surface area, this is another parameter associated with the initial activity of carbon catalysts, although its effect is a controversial topic. This can be due to the comparison of carbons from different precursors, so that the activity depends not only on the surface area but also on their structure, which varies with the carbon nature 128. In general, when carbons of the same nature are compared, those with higher surface areas usually exhibit a better catalytic activity 80. This trend is not always observed when considering carbons of different nature. In this case, not only the specific surface area affects the activity but also the structure of the catalyst is a determining factor 11, 130.
4.2.2 Stability of Carbon Catalysts
Regarding the stability of carbon catalysts, different parameters have been reported to influence their lifetime. The following tendency was observed with respect to the stability of different carbon catalysts 73: CB (vulcan XC72) > CB (black pearls 2000) > MWNT > graph > AC (mesoporous) > AC (microporous). Carbon blacks are thus the most resistant catalysts to deactivation, attributed to their well-defined concentric graphene layers that generate large inter-particle spaces.
In several works, a relation between the stability and textural properties, such as the total pore volume and external surface area, has been discussed. For example, the amount of carbon accumulated prior to deactivation (related to the long-term behavior) has been linked to the total pore volume of the fresh catalysts. These parameters depict a linear dependence, i.e., a larger pore volume can accumulate a bigger amount of carbon before deactivation 82, 119, 125. Additionally, carbon catalysts with a high external surface area show a good stability because they offer higher accessibility to methane molecules even after the accumulation of numerable amounts of carbon 11, 62, 81.
Despite the large number of recent works on the performance of carbon catalysts in methane pyrolysis, there are still challenges to be overcome in the near future. For instance, the reaction mechanism over carbon catalysts is uncertain and must be clarified to improve their activity on the decomposition of methane. A correlation must also be established between the carbon structure and its role in the catalytic activity since it is still not well understood or at least is a matter of debate nowadays. It is generally accepted that the defects of the carbon structure are the active sites for the pyrolysis of methane. However, their effect on the reaction mechanism and the synergy between these sites and other surface properties (oxygenated groups, surface area, pore volume) are still unclear 17.
4.3 Molten Metals and Molten Salts
The use of molten metals (Ti, Pb, Sn), molten metal alloys (Ni-Bi, Cu-Bi), and molten salts (KBr, NaBr, NaCl, NaF, MnCl2, KCl) in liquid bubble column reactors has been investigated for methane pyrolysis during the last years 26, 131-138. In a liquid bubble column reactor, the decomposition of methane takes place inside the bubbles, so that they can be considered as individual microreactors. The bubbles open at the upper interface of the liquid media and the carbon by-product and hydrogen are released. Since the density of carbon is lower than that of the molten media, the carbon produced floats atop of the liquid metal/salt surface, rises with the bubbles, and is deposited at the surface of the liquid column. Therefore, the carbon produced does not affect the reaction zone inside the bubbles, and the liquid at the surface of the bubble is a continuously renewed catalyst 137. The main advantage of liquid bubble column reactors is the possibility of a continuous carbon removal from the liquid media due to density differences. This prevents blockage of the reactor as a result of carbon accumulation 26, 132, 136. Moreover, the contamination of the molten metal or molten salt by the carbon product is prevented 135, 137. Nevertheless, the applicability of this technology on an industrial scale is still a challenge today. The main drawbacks are the high required temperature (> 1000 °C) as well as finding a stable molten media at such high operating temperatures 26.
5 Carbon Product
Besides hydrogen, carbon is a major product of methane pyrolysis, so an economic benefit could be created depending on its quality. Different carbon structures have been reported over metal and carbon catalysts. The kind and quality of the obtained carbon strongly depends on the reaction conditions and the catalyst applied. The formation of carbon nanotubes and carbon nanofibers generally occurs over metal catalysts 73. In this case, the reaction temperature has been shown to have an effect on the properties of the carbon product. For instance, the diameter and length of carbon nanofilaments decrease at high operating temperatures 61, 65, 66. Furthermore, the formation of nanocarbons with a higher crystallinity and graphitization degree was observed at elevated reaction temperatures 139. In carbon-catalyzed reactions, carbon deposits with different morphologies have been obtained 73. The structure of the produced carbon depends on the nature of the carbon catalyst. For example, the formation of carbon black was reported over activated carbons, whereas reactions catalyzed by carbon blacks resulted in amorphous turbostratic carbons. Carbon nanotubes have also been used as a catalyst in the pyrolysis of methane. Here, the growth of the nanotube walls is favored and the formation of multi-walled carbon nanotubes takes place 73. The characteristics and grade of the carbon by-product determines its selling price and subsequent commercialization. Therefore, obtaining a valuable carbon product may generate profits and improve the economics of the process on an industrial scale 10, 13-17. Nevertheless, if methane pyrolysis is implemented industrially, the current market will not be able to absorb the large amounts of carbon produced 13, 17. In addition, since the carbon market is unlikely to increase in the coming years 13, the economic viability of the process cannot depend on carbon commercialization.
6 Influence of Operating Conditions
Different operating conditions, such as temperature, pressure, or gas hourly space velocity (GHSV), have been explored in the thermal decomposition of methane. Methane pyrolysis is an endothermic equilibrium reaction, so high temperatures shift the equilibrium towards the production of hydrogen. Therefore, higher temperatures lead to higher methane conversions and hydrogen yields 17, 23, 65. However, the formation of carbon deposits is also enhanced by the increasing conversion. In the case of metal catalysts, the carbon produced covers the active sites, causing the rapid deactivation of catalysts and, thus, shortening their lifetime. In addition to this, the sintering of particles occurs at high temperatures and contributes to the activity loss of metal catalysts 60, 63, 83, 91, 108, 139-146. Carbon materials also deactivate faster at higher temperatures. In this case, the deactivation mechanism is attributed to: 1) decrease in the specific surface area; 2) decrease in the pore mouth, which prevents the diffusion of methane into the pores; and 3) decrease in the pore volume 119, 130. As shown in Fig. 5 116, the thermal decomposition of methane is usually carried out in the 800–1000 °C range when carbon materials are used as catalysts, unlike the non-catalytic process, which requires temperatures above 1100–1200 °C. The reaction temperature also differs for metal catalysts depending on the active species. For instance, nickel catalysts can work effectively in a lower temperature range (500–700 °C) compared to iron catalysts (700–900 °C).
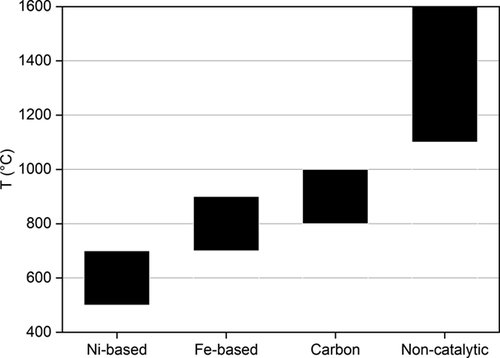
According to Le Chatêlier's principle, a higher total reaction pressure corresponds to a less hydrogen production due to the equilibrium shift towards the reactant formation. Therefore, a low pressure is desirable to maximize the hydrogen yield. However, maintaining pressures lower than atmospheric is costly and complex 24. For these reasons, methane pyrolysis is usually conducted at a total pressure no more than 1 atm, and the partial pressure of the methane feed gas is often balanced with some inert gases (nitrogen or argon). Under the same total pressure, higher hydrogen yields are achieved at a lower partial pressure of methane 17, 24. The major drawback is the separation of the inert gas from the gas product after the reaction, which significantly increases the overall costs of the process.
Different GHSVs have been investigated in many works. It is generally accepted that high GHSVs lead to lower methane conversions 61, 65, 66, 97, 108, 110, 121, 147. This is attributed to the shorter residence time, lower contact efficiency between the gas and the catalyst, and lower amount of methane adsorbed on the active sites when the GHSV is increased 61, 65, 66, 105, 108, 110, 147-149. In addition to this, high GHSVs cause a faster catalyst deactivation 97, 108, 147. This is due to the higher carbon formation rate compared to the carbon diffusion rate through the particles, which leads to carbon accumulation and consequently catalyst deactivation 150. In the same way, low GHSV values enhance the contact efficiency between methane and the catalyst and, thus, the methane decomposition rate is accelerated 17, 20. In some works, it was claimed that there is a GHSV limit value above which the conversion of methane starts to decrease. On the one hand, an increase in the GHSV improves the mixing between the gas and the catalyst particles. On the other hand, excessive GHSV values accelerate the catalyst deactivation rate as a consequence of the higher amount of carbon produced. Therefore, an optimum GHSV value must be found to obtain a compromise between the activity and stability of the catalysts 141, 151.
7 Natural Gas as Feed Gas
The study of hydrogen production from methane is a crucial step to understand the conversion of natural gas to hydrogen. Natural gas is composed mainly of methane but also of different impurities, such as ethane, propane, ethylene, H2S, and nitrogen 152. For this reason, it is necessary to understand the role of these minor compounds as they may affect the activity and stability of the catalysts.
The effect of ethane, propane, and a mixture of both has been studied in the decomposition of methane over carbon catalysts 152. The hydrogen production exhibits the following tendency depending on the initial gas composition: methane < methane-propane < methane-ethane < methane-ethane-propane. The hydrogen concentration in the outlet gas increases with the addition of ethane and/or propane due to the higher H2 content in these hydrocarbons. Nevertheless, the main advantage of these hydrocarbons is that the carbon derived from their decomposition does not deactivate the carbon catalyst. Therefore, minor amounts of ethane and propane present in natural gas are expected to have no negative effect on the decomposition of methane over carbon catalysts. In a more recent work, the pyrolysis of mixtures composed of methane and ethane was studied 153. Here, it was reported that methane was activated with the aid of ethane, i.e., methane was assumed to be attacked by radical species derived from the pyrolysis of ethane and converted into methyl radicals. Contrary to this work, the addition of propane did not result in the desirable increase in the decomposition rate of methane in other studies 127. These results were related to the morphology of the carbon formed from propane. That is, since methane and propane belong to the same family of saturated hydrocarbons (alkanes), carbons with similar crystallite size and structures are expected from the decomposition of both hydrocarbons. This would result in a similar activity in the methane pyrolysis reaction. However, the role of saturated hydrocarbons in the decomposition of methane, such as ethane and propane, is not clear. For this reason, more research is needed to determine if the effect of these hydrocarbons can be associated with the formation of radical species or with the morphology of the carbon derived from their decomposition.
Besides the effect of the hydrocarbon impurities already present in natural gas, some works have shown that co-feeding of methane with a second hydrocarbon in carbon-catalyzed processes improves the catalytic performance and partially overcomes deactivation problems. Different co-fed gases, such as benzene, acetylene, and ethylene, have been investigated 79. The carbon originated from aromatic (benzene) and unsaturated (acetylene, ethylene) hydrocarbons has been found to be catalytically more active than the carbon produced from methane, so the decomposition rate of methane improves after their addition. Carbons with smaller crystallite size and higher HES concentration were originated from aromatic and unsaturated hydrocarbons in comparison to that resulting from methane. This would explain the positive effect of the carbons produced from acetylene, ethylene, and benzene on the methane decomposition rate. The influence of several co-fed gases over carbon catalysts was also analyzed in other works: propylene 154, ethylene 84, 155, ethanol 156, and carbon dioxide 157. According to these authors, the decomposition of propylene, ethylene, and ethanol gives rise to a carbon product that is catalytically active for the pyrolysis of methane. Furthermore, the incorporation of these hydrocarbons reduces the deactivation of the carbon catalyst. The addition of CO2 enables the in situ regeneration of the catalyst by gasification of the carbon deposits. However, co-feeding with CO2 is not energy-efficient and entails environmental problems 157.
Minor amounts of non-hydrocarbon compounds, such as H2S, are also present in natural gas. H2S has a positive catalytic effect on the methane decomposition rate over carbon catalysts. This was explained by the formation of HS radicals that attack methane molecules to initially produce methyl radicals, resulting in the final formation of hydrogen and carbon 152. This is a great advantage of carbon catalysts over metal-based materials since the latter deactivate in the presence of sulfur compounds. The rapid deactivation of metal-based catalysts by sulfur compounds was also pointed out in other works 158. On the contrary, it was shown that the addition of 1 vol % of H2S does not deactivate carbon catalysts but increases the conversion of methane.
Despite these studies, the effect of all minor compounds in natural gas and the role of co-fed hydrocarbons on the catalytic activity and stability are still unclear. In general, co-feeding with a second compound is favorable from the point of view of process stability but the implementation on an industrial scale is questionable. The feasibility of the co-feeding process depends on the price and the required amount of the co-fed compounds 20. Moreover, depending on the final hydrogen application, some additional purification steps may be necessary to remove the unconverted co-fed hydrocarbons, which may also determine the industrial viability of the co-feeding process 17. Therefore, for the successful industrial implementation of methane pyrolysis, these issues must be fully understood, and thus, further investigations have to be conducted.
8 Implementation of Methane Pyrolysis on an Industrial Scale
Different types of reactors (packed-bed reactors, fluidized-bed reactors, fluid wall reactors, spouted-bed reactors, honeycomb monoliths, molten salt reactors) have been considered for the catalytic decomposition of methane 78, 131-136, 159-161. Among them, fluidized-bed reactors and packed-bed reactors are the most commonly used. The drawback of using packed-bed reactors is the filling of the reactor with solid carbon, which eventually blocks the reactant gas flow in long-term experiments. To avoid such a problem, carbon must be periodically removed 23.
Muradov et al. 161 developed several reactor configurations with continuous carbon removal and reported that fluidized-bed reactors are the most promising for large-scale operation. From the operational point of view, methane pyrolysis could be industrially implemented using a continuous fluidized-bed catalytic reactor, similar to other industrial processes such as fluid coking or fluid catalytic cracking. Fluidized-bed reactors allow continuous addition of fresh catalyst and removal of spent catalyst and carbon deposits. Although the resulting carbon by-product increases the average particle size of the catalyst, the pressure drop in the reactor does not rise significantly and plugging is prevented due to the constant removal of the catalyst. Fluidized-bed reactors also enable a good temperature control and an efficient heat and mass transfer between the catalyst and the gas. Furthermore, hot spots are avoided 17, 23.
An experimental setup using a fluidized-bed reactor with a carbon catalyst coupled with a gas separation unit is represented in Fig. 6 161, 162. Methane (or natural gas) is fed into the fluidized reactor at the bottom and the mixture of hydrogen and unconverted gas after reaction leaves the reactor at the top. The outlet gas passes through a membrane to obtain pure hydrogen, whereas methane is recirculated to the reactor. A part of the carbon particles is removed, so that most of them can be stored after cooling. A small part of the removed carbon passes through a grinder to maintain a suitable particle size for fluidization. The ground carbon is continuously mixed with fresh carbon catalyst and introduced into the reactor. As already mentioned, iron catalysts would also be a potential option for application in methane pyrolysis. In this case, all the catalyst after deactivation should be stored as its regeneration would result in undesirable CO/CO2 emissions.
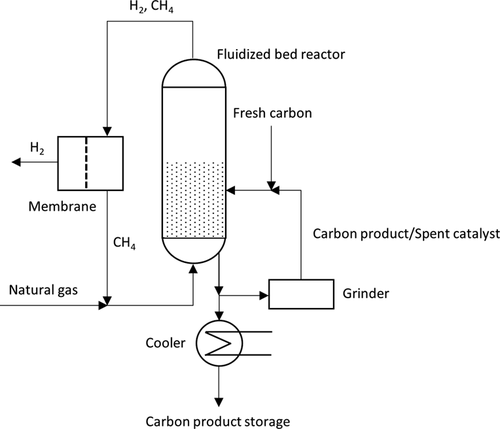
9 Perspectives and Conclusions
To mitigate greenhouse emissions, new strategies have emerged in recent years to convert industrial CO2 into bulk chemicals. In this context, the Carbon2Chem® project aims to produce chemicals like methanol from steel mill exhaust gases. From the environmental point of view, the production of the required hydrogen via water electrolysis based on renewable energies is the most appropriate technology. Nevertheless, the fluctuation and unsteady availability of renewable power force the consideration of other hydrogen sources. Despite the technologies already implemented on a large scale for hydrogen production, such as coal gasification and steam methane reforming, these processes are undesirable due to the large CO2 footprint.
A clean alternative process without CO2 emissions is the pyrolysis of methane, in which methane decomposes into hydrogen and solid carbon. Methane pyrolysis has been widely investigated for many years. Until now, different metal (Ni, Co, Fe) and carbon catalysts have been studied for this reaction. Among them, iron and carbon materials are the most suitable for industrial implementation considering their non-toxicity and the possibility of safe storage of the carbon by-product. However, the hydrogen yields over these catalysts are rather low and the reaction temperatures relatively high. Additionally, the initiation and rate-limiting step as well as the overall reaction mechanism are still unclear. Especially, further studies are required to determine whether the rate-determining step is the dissociation of methane or the formation of solid carbon. Only when the reaction mechanism is fully elucidated, enhanced catalysts can be developed and further improvements in catalytic activity will be achieved. The sale of the carbon by-product for further application would benefit the economics of the global process. However, the establishment of new markets capable of absorbing the large amounts of carbon generated is improbable in the near future. Therefore, carbon storage becomes the most plausible solution and further investigations are required to develop an industrial methane pyrolysis process that is economical regardless of carbon commercialization. Although there are still many challenges, methane pyrolysis is a promising technology to overcome the lack of hydrogen supply from renewables in an industrial plant for the overall reduction of CO2 emissions. Since it is much more energetically economical than water electrolysis and natural gas is highly available, this CO2-free hydrogen source bears good prospects of being a temporary solution until the use of renewable sources is sufficiently expanded.
Acknowledgements
The authors would like to thank the Max Planck Society for financial support as well as the Federal Ministry of Education and Research (Bundesministerium für Bildung und Forschung (BMBF), Verbundvorhaben Carbon2Chem®, support code: 03EK3037C) for funding. Open access funding enabled and organized by Projekt DEAL.
Symbol used
-
- ΔH0R [kJ mol−1]
-
standard enthalpy of reaction
Abbreviations
-
- AC
-
activated carbon
-
- CB
-
carbon black
-
- CCS
-
carbon capture and storage
-
- GHG
-
greenhouse gases
-
- GHSV
-
gas hourly space velocity
-
- Graph
-
graphite
-
- HES
-
high-energy sites
-
- MWNT
-
multi-walled carbon nanotubes
-
- SMR
-
steam methane reforming
-
- VLS
-
vapor-liquid-solid