Exsolution of Ru Nanoparticles on BaCe0.9Y0.1O3-δ Modifying Geometry and Electronic Structure of Ru for Ammonia Synthesis Reaction Under Mild Conditions
Abstract
Green ammonia is an efficient, carbon-free energy carrier and storage medium. The ammonia synthesis using green hydrogen requires an active catalyst that operates under mild conditions. The catalytic activity can be promoted by controlling the geometry and electronic structure of the active species. An exsolution process is implemented to improve catalytic activity by modulating the geometry and electronic structure of Ru. Ru nanoparticles exsolved on a BaCe0.9Y0.1O3-δ support exhibit uniform size distribution, 5.03 ± 0.91 nm, and exhibited one of the highest activities, 387.31 mmolNH3 gRu−1 h−1 (0.1 MPa and 450 °C). The role of the exsolution and BaCe0.9Y0.1O3-δ support is studied by comparing the catalyst with control samples and in-depth characterizations. The optimal nanoparticle size is maintained during the reaction, as the Ru nanoparticles prepared by exsolution are well-anchored to the support with in-plane epitaxy. The electronic structure of Ru is modified by unexpected in situ Ba promoter accumulation around the base of the Ru nanoparticles.
1 Introduction
Ammonia has been a crucial chemical for feeding the massive population growth in the twentieth century since its industrial production via the Haber-Bosch process. Ammonia, particularly “green” ammonia, has attracted significant interest as a carbon-free energy carrier.[1, 2] Ammonia has one of the highest gravimetric (17.8 wt%) weight and volumetric (108 kg-H2 m−3 NH3 at 20 °C and 8.6 bar) energy density among carbon-free energy carriers.[3] The traditional Haber-Bosch process requires high temperatures to overcome the large reaction energy barrier for dissociating the stable nitrogen triple bond (NN).[4] However, exceedingly high pressure is also necessary to compensate for the low thermodynamic conversion ratio of the exothermic ammonia synthesis reaction at high temperatures. High temperature (450–600 °C) and high pressure (100–250 bar) requirements make the Haber-Bosch process economically viable only for extremely-large-scale systems. The production of “green” ammonia using hydrogen from water electrolysis requires a small-scale low-pressure reactor.[5] Water electrolysis typically operates below 30 bar and is coupled with intermittent renewable electricity at remote sites.[6] The need for a highly active ammonia synthesis catalyst is becoming increasingly important for reducing the operating temperature and pressure of the ammonia synthesis reaction.
The ammonia synthesis rate follows a volcano plot, and optimizing the nitrogen adsorption energy is key to achieving high activity.[7, 8] Ru shows superior activity among the studied transition metal catalysts. Therefore, supported Ru catalysts have been widely investigated for ammonia synthesis.[9-14] Two approaches are available to further the catalytic activity of Ru: i) structural modification and ii) electronic structure modification. Experiments and density functional theory calculations showed that the Ru B5-type surface structure facilitates the N2 dissociation reaction, which is the rate-determining step for Ru. The density of the Ru B5 sites is nanoparticle size-dependent, Ru nanoparticles of 3–5 nm show the highest activity,[15, 16] and the activity decreases with increasing size.[17] Electron-rich Ru increases activity by lowering the activation barrier during N2 triple bond dissociation. Electronic structure promotion can be achieved by doping a support material with electron-donating components,[18] using a basic support such as alkali or alkaline earth metal support,[9, 11] and using an inorganic electride support.[10] Recently, Ba-doped[12] and rare-earth oxide-supported[13] Ru catalysts have been reported to improve ammonia synthesis via electronic structure modification.
The exsolution method has been gaining attention as a novel synthetic method for preparing nanoparticle catalysts with controlled size and distribution and enhanced interaction between the nanoparticle and the support.[19-24] The exsolution process involves two high-temperature steps. Transition metal cations, which form nanoparticles, are homogeneously doped in a supporting oxide framework under oxidizing heat-treatment conditions. These cations are exsolved and form metallic nanoparticles at the surface of the supporting oxide framework under reducing conditions and high temperatures.[25, 26] The exsolution procedure provides improved nanoparticle dispersion and size homogeneity compared to conventional nanoparticle preparation methods. Nanoparticles grow from the support material during the exsolution process, and nanoparticles need not be synthesized separately and attached to the support. Nanoparticles prepared from exsolution exhibit outstanding resistance to particle agglomeration because of their strong anchoring to the support.[25, 27] Furthermore, the metal lattice that grows from the oxide lattice facilitates interdiffusion between the two, increasing the adhesion and interaction between the exsolved metal and host oxide.[28, 29]
In this study, we designed highly active Ru catalysts for ammonia synthesis by exsolving Ru nanoparticles from the host material, the BaCe0.9Y0.1O3-δ (BCY) support. The exsolution method is ideal for preparing small Ru nanoparticles with high stability and strong metal-support interactions. The host material BCY was deliberately chosen to maximize the catalytic activity of Ru. Ba[30-32] and Ce[28, 33, 34] are well-known promoters that donate electrons to Ru to increase ammonia synthesis rate. Adding Y to the B site of BaCeO3-δ generated oxygen vacancies and increased the proton conductivity of the oxide.[35-38] The formation of oxygen vacancies is known to promote the exsolution process.[25, 39] The proton-conducting oxide prevents the surface hydrogen poisoning of Ru nanoparticles, resulting in increased catalytic activity for ammonia synthesis and decomposition reactions.[40, 41] The promotional effects of exsolution and the BCY support were verified by comparing exsolved Ru nanoparticles (ex-Ru/BCY), impregnated Ru nanoparticles (imp-Ru/BCY), and commercial Ru/C catalysts. Further analyses using HR-TEM and HAADF-STEM elucidated the role of exsolution in enhancing the ammonia synthesis rate.
2 Results and Discussion
2.1 Exsolution Process of Ru/BaCeYOX Catalysts
Ru nanoparticles on the BCY support were prepared using the exsolution method from Ru-doped-BCY, BaCe0.87Y0.1Ru0.03O3-δ. Ru-doped-BCY was prepared using a glycine nitrate process and subsequent annealing. A 5 h reduction treatment at 1000 °C on Ru-doped-BCY resulted in Ru nanoparticles on BCY (ex-Ru/BCY), as shown in Figure 1a–c. To compare and emphasize the effect of the exsolution, Ru nanoparticles were also prepared by conventional incipient wetness impregnation on BCY, where the BCY support was prepared in the same way as the Ru-doped-BCY but without Ru (imp-Ru/BCY). Commercial Ru/C was used to elucidate the effects of BCY. Extended X-ray absorption fine structure (EXAFS) analysis was performed to investigate the local coordination environment around Ru and the effect of reduction temperature on the exsolution process. First, the local coordination environment of Ru in the Ru-doped-BCY sample before exsolution was investigated by EXAFS fitting, assuming that Ru occupies the Ce site of the BaCeO3 perovskite structure (black line in Figure 1d; Figure S1, Supporting Information). RuO (1.55 Å), RuBa (3.32 Å), and RuCe (4.08 Å) bonds were observed without the RuRu bond (2.36 Å), indicating that Ru was predominantly doped at the B site of BCY without any aggregated metallic Ru nanoparticles. Fitting of the EXAFS spectra provided detailed information about each bond length. The bond length of RuO, 1.99 Å, was ≈0.2 Å shorter than the bond length of CeO (2.19 Å) in BaCeO3, Ru replaced Ce at the B site, and the RuO bond length was similar to RuO2. The bond length to the second nearest neighbor, RuBa, was 0.1 Å shorter than CeBa in BaCeO3. Finally, the bond length between Ru and the third nearest neighbor, RuCe did not show bond-length shortening. The fitted bond lengths indicated that Ru attracted the first nearest neighbor O, and, subsequently, the second nearest neighbor Ba compared to Ce at the same site, causing local strain to the surrounding crystal structure. This local strain can be the reason for the smaller lattice parameter of Ru-doped-BCY compared to that of BCY (Figure 2).
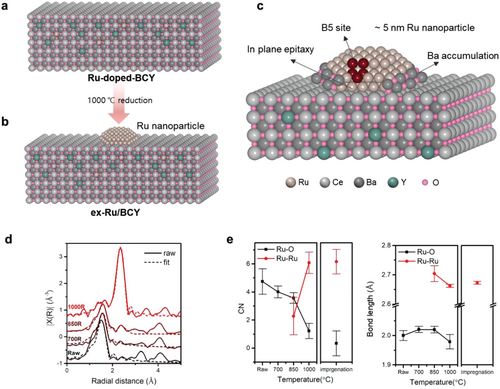
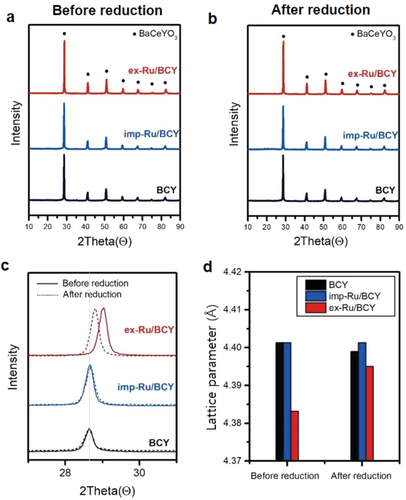
Second, the exsolution process was investigated by performing EXAFS fitting of the Ru-doped-BCY samples reduced at 700, 850, and 1000 °C for 3 h. For this fit, RuRu and RuO single scattering paths were considered, and coordination numbers were obtained using the S02 value of the RuO2 reference powder (Figure 1d–e). No discernible change was observed after the 700 °C reduction treatment, and the EXAFS spectra and fitted parameters were similar to those of Ru-doped-BCY before the reduction treatment. The RuRu bond (2.36 Å) started appearing at 850 °C and had the highest intensity at 1000 °C. As the coordination of RuRu occurs at 850 °C, we confirmed that the significant structural change began at temperatures as low as 850 °C. After the 1000 °C reduction treatment, the RuO peak (1.55 Å) almost disappeared and the RuRu peak was dominant, indicating completion of the exsolution at 1000 °C. Therefore, 1000 °C was set as an exsolution temperature.
XRD was conducted to confirm the crystal structure of the synthesized Ru/BCY catalysts and their exsolution phenomenon (Figure 2). Three different samples, ex-Ru/BCY, imp-Ru/BCY, and BCY, were examined before and after the 5 h reduction (exsolution) process at 1000 °C. All samples before and after reduction showed clear XRD peaks corresponding to the BaCeO3 perovskite structure, but with a small positive peak shift for Ru-doped-BCY (ex-Ru/BCY before reduction), as shown in Figure 2c. Ru-doped-BCY had a compressed crystal structure, indicating that Ce was replaced by Ru, which has a smaller ionic radius, resulting in a smaller lattice parameter (Figure 2d). After the exsolution process (1000 °C, 5 h in 5% H2/Ar), the lattice parameter of ex-Ru/BCY increased to a value comparable to those of BCY and imp-Ru/BCY. The doped Ru, which initially caused internal compressive strain, exsoluted out on the surface of BCY, releasing the internal compressive strain.
The mean particle size and particle size distribution of the Ru nanoparticles were evaluated by high-resolution TEM (HR-TEM). Figure 3 and Figure S2 (Supporting Information) show HR-TEM images and histograms of the Ru particle size distribution for ex-Ru/BCY, imp-Ru/BCY, and Ru/C. Notably, no Ru nanoparticles were present for the Ru-doped-BCY before the exsolution process (Figure S3, Supporting Information). The average Ru particle size of ex-Ru/BCY was 5.03 ± 0.91 nm, and Ru particles showed uniform distribution on the BCY surface. The Ru particle size of imp-Ru/BCY was smaller than ex-Ru/BCY but with a wider size distribution, 3.55 ± 1.62 nm. In contrast to ex-Ru/BCY, imp-Ru/BCY contained several large nanoparticles with sizes close to 10 nm, resulting in a larger standard deviation. The exsolution process is more beneficial than the conventional preparation method for synthesizing nanoparticles with a narrow size distribution. As catalytic properties are often determined by the size of the active component, a uniform size distribution could be beneficial for other catalytic reactions that require a specific particle size.
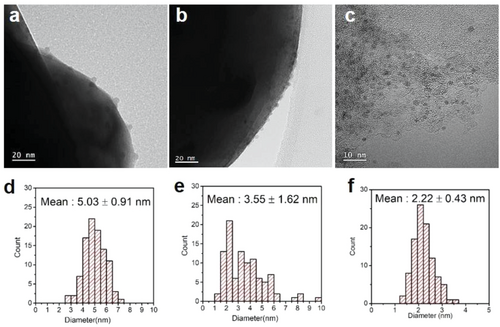
High-angle annular dark-field scanning transmission electron microscopy (HAADF-STEM) and energy-dispersive X-ray spectrometry (EDS) were used to observe the structure and exsolution phenomena of Ru. HAADF-STEM images of the Ru-doped-BCY (ex-Ru/BCY before reduction) showed no sign of Ru nanoparticles, and the EDS mapping image showed a uniform distribution of Ru in the BCY matrix (Figure 4a–c). After the exsolution process, the formation of Ru nanoparticles was clearly observed in both the HAADF-STEM and EDS mapping images (Figure 4d–f). The atomic concentration in the BCY matrix was measured before and after the exsolution. The Ru concentration in the BCY particle of the Ru-doped-BCY was measured as 1.3 ± 0.2 at.% (Figure 4c dotted square 1), which is close to 1.5 at.%, the atomic concentration of Ru added for the synthesis of the Ru-doped-BCY, confirming that Ru is well-doped with the desired concentration at the BCY matrix. After the exsolution process, the Ru concentration at BCY decreased to 0.38 ± 0.01 at.% (Figure 4f dotted square 2), further confirming that Ru exsolved from the BCY lattice, albeit some Ru may still be present inside the BCY matrix. Ru nanoparticles were found on both ex-Ru/BCY and imp-Ru/BCY, with distinct sizes and size distributions. Ru nanoparticles on ex-Ru/BCY show a more uniform size distribution and increased particle-to-particle distance, which can prevent particle agglomeration during high-temperature operations. This result is consistent with a previous report that the exsolution process results in more uniform and well-distributed nanoparticles on the catalyst surface.[19]
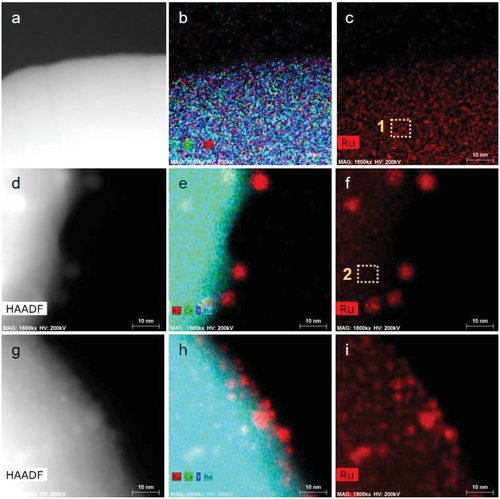
2.2 Catalytic Activity
The catalytic activities of ex-Ru/BCY, imp-Ru/BCY, and Ru/C were tested for low-temperature ammonia synthesis reaction at atmospheric pressure (Figure 5). Before the test, the Ru/BCY samples were pre-reduced to 750 °C for 1 h to remove carbonate compounds on the catalyst surface, which could block the active sites.[32] It can also remove residual chlorine ions present in imp-Ru/BCY, which are poisonous to the ammonia synthesis reaction.[42] Among the three samples, ex-Ru/BCY showed the best activity of 387.31 mmol gRu−1 h−1 at 450 °C, 0.1 MPa, which was approximately eight times higher than imp-Ru/BCY, 47.56 mmol gRu−1 h−1, and twenty times higher than commercial Ru/C, 19.72 mmol gRu−1 h−1. BCY support without Ru was also tested but showed negligible activity, 2.62 × 10−3 mmol gcat−1 h−1, which is two to three orders of magnitude lower than that of Ru-containing BCY samples, confirming that the active site contains Ru nanoparticles. The BCY support had a promoting effect, where imp-Ru/BCY outperformed the Ru/C catalyst. The effect of exsolution was further pronounced when ex-Ru/BCY performed eight times better than imp-Ru/BCY did. Compared to other studies, the ex-Ru/BCY catalyst showed highly promising ammonia synthesis activity (Figure S4, Supporting Information) when the activity was normalized to the amount of Ru used, at 0.1 MPa.[9, 10, 43-53] The catalysts were also compared with Ba-promoted Ru/C catalysts (Ba-Ru/C), which are commonly used catalysts for the ammonia synthesis reaction[54] (Figure S5, Supporting Information). The Ba promoter was introduced into the Ru/C catalyst using the incipient wetness impregnation method. Ba-Ru/C showed the activity of 144.37 mmol gRu−1 h−1 at 450 °C, which is five times higher than Ru/C but more than twice lower than the ex-Ru/BCY catalyst. This result revealed that Ba acts as a promoter for the Ru catalyst, and the promotional effect of exsolution was better than that of the conventional promoter introduction via the impregnation method. The apparent activation energies of the catalysts were 160 and 187 kJ mol−1 for ex-Ru/BCY and Ru/C, respectively. The activation energy of ex-Ru/BCY was lower than that of the conventional Ru catalyst with inert support (Ru/C), but higher than that of some highly active catalysts (51 kJ mol−1 for Ru/C12A7:e- [4] and 41 kJ mol−1 for Ru/BaO-CaH2 [5]). In the case of imp-Ru/BCY, the apparent activation energy changed depending on the temperature range. The apparent activation energy was 83.04 kJ mol−1 under 390 °C and 5.28 kJ mol−1 over 390 °C. We presume that imp-Ru/BCY has different active sites such as Ba-H2.[55] It seems inappropriate to directly compare the activation energy of imp-Ru/BCY to ex-Ru/BCY since the reaction mechanisms are very different for the two catalysts.
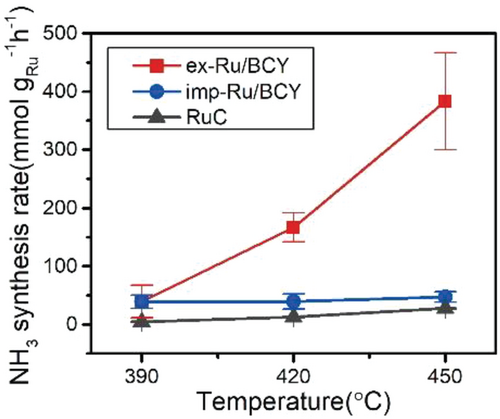
The turnover frequency (TOF) of the tested catalysts were obtained to compare their intrinsic activities. The amount of surface-exposed Ru atoms was quantified by CO chemisorption, and the catalytic activities were normalized per surface-exposed Ru atom.[10, 56] Table 1 shows the CO chemisorption results of each sample. The particle diameter was calculated assuming the particle was spherical and every Ru atom participated in the formation of Ru nanoparticles (the equation is described in the experimental section). The calculated particle diameter for ex-Ru/BCY from CO chemisorption, 12.12 nm, was larger than the measured particle size from TEM, 5.03 ± 0.91 nm. There could be several reasons for the larger calculated particle diameter. A portion of Ru may still be present in the BCY lattice after exsolution, as shown in the EDS result (Figure 4). The Ru nanoparticle prepared from the exsolution has a facet interacting with the support, which is unavailable for CO chemisorption. Finally, as will be discussed later, some portion of the Ru nanoparticle was buried by the surrounding Ba species. The calculated particle diameters for imp-Ru/BCY and Ru/C were 3.51 and 3.47 nm, respectively, similar to the particle size distribution from the TEM (3.55 ± 1.62 and 2.22 ± 0.43 nm, respectively). Based on these results, the TOF was calculated for the 450 °C test. The catalytic activity of ex-Ru/BCY (0.20 s−1) was higher than that of imp-Ru/BCY (0.0035 s−1) and Ru/C (0.0020 s−1). However, Ru particle aggregation was observed for imp-Ru/BCY and Ru/C after the reaction, as described in the following section. Therefore, the TOF values for imp-Ru/BCY and Ru/C may be higher than the values reported in Table 1. As shown in Figure S4 (Supporting Information), ex-Ru/BCY is one of the most active Ru catalysts for ammonia synthesis reactions on a TOF basis. This result indicates that the promotional effect of exsolution on BCY is critical for ammonia synthesis reaction. Further research to increase the dispersion of exsolution catalysts will be beneficial for the practical application of exsolution catalysts.
Ru loading [wt.%] | BET surface area [m2 g−1] | Metal dispersiona) [%] | Active particle diametera) [nm] |
TOFb) [s−1] | |
---|---|---|---|---|---|
Ru-doped-BCYc) | 0.95 | 2.28 | – | – | – |
ex-Ru/BCY | 0.95 | 3.08 | 5.44 | 12.12 | 0.19962 |
imp-Ru/BCY | 0.95 | 3.33 | 37.55 | 3.51 | 0.0035 |
Ru/C | 5 | 686.19 | 37.94 | 3.47 | 0.0020 |
- a) Metal dispersion and active particle diameter were calculated using the CO-chemisorption method
- b) TOF values were calculated from the metal dispersion and ammonia synthesis rate at 450 °C. (The equations are described in the experimental section)
- c) The CO-chemisorption result of Ru-doped-BCY was below the detection limit.
The stability of the prepared catalysts was tested over a 50 h period, and ex-Ru/BCY showed only a slight decline in activity over the course of the reaction (Figure S6, Supporting Information). Further characterizations were conducted to elucidate the promotional effect of exsolution.
2.3 Detailed Characterization of the Exsolved Ru/BCY
The Ru nanoparticle prepared by the exsolution method showed enhanced activity for the ammonia synthesis reaction. We conducted several detailed characterizations to elucidate the effect of exsolution. First, the sinter-resistant character of the exsolved nanoparticles was shown in the electron microscopy images of the tested catalysts. Figure 6 and Figure S7 (Supporting Information) show HR-TEM and TEM-EDS images of ex-Ru/BCY, imp-Ru/BCY, and Ru/C after the ammonia synthesis reaction test. The average particle sizes of Ru for ex-Ru/BCY, imp-Ru/BCY, and Ru/C were measured as 4.56 ± 0.75, 7.82 ± 3.05, and 10.01 ± 2.25 nm, respectively. Compared with the Ru nanoparticle size before the ammonia synthesis test (Figure 3), only the ex-Ru/BCY sample maintained the initial nanoparticle size and distribution. The Ru nanoparticles of imp-Ru/BCY and Ru/C showed severe agglomeration, resulting in an increased particle size and a larger particle size distribution.
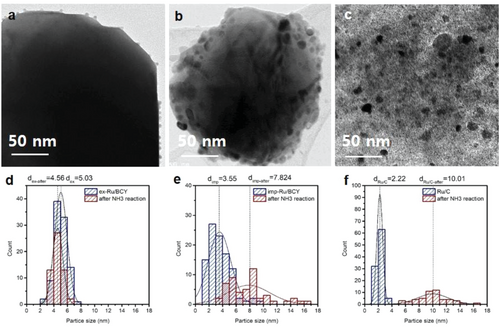
Exsolved nanoparticles are well-known for their exceptional thermal stability. Often, the stability is attributed to their partially buried, socketed structure.[27, 28, 57-59] Neagu et al.[28] reported a partially buried structure of exsolved Ni nanoparticles from La0.4Sr0.4NiXTi1-XO3-d. These Ni nanoparticles did not sinter after 70 h aging at 900 °C and were pinned to their original locations, showing exceptional thermal stability. The socketed structure of the exsolved nanoparticles was later confirmed in situ using environmental TEM observations.[27] Although ex-Ru/BCY showed excellent stability under the reaction conditions, it was difficult to confirm the socketed structure because TEM is inherently a 2D analysis. As discussed in later sections, in-plane epitaxial growth and the surrounding new phase around the Ru nanoparticles may have improved the stability of the nanoparticles. It is easily conceivable that Ru nanoparticles exsolved at an exceedingly high temperature (1000 °C) retained their structure at much lower temperatures (below 450 °C).
Both experiments and density functional theory calculations proved that the ammonia synthesis reaction is a structure-sensitive reaction and that having the optimal Ru nanoparticle size is crucial.[16, 60] The Ru B5-type surface site facilitates the N2 dissociation reaction, which is the rate-determining step for Ru. The B5 site was located at a step site on the Ru (0001) surface and consisted of three Ru atoms in the first layer and two Ru atoms in the above layer.[15, 61, 62] The concentration of B5 sites is critical to the catalytic activity for ammonia synthesis. According to the atomistic Wulff construction, Ru particles with a size of 1.8–2.5 nm have the highest concentration of Ru B5 sites, and the concentration of B5 sites decreases as the particle size further increases.[62] Experiments also showed that the activity is size-dependent, and Ru nanoparticles 3–5 nm in size have the highest activity.[15, 60] Ru nanoparticles prepared by exsolution, ex-Ru/BCY, with a stable particle size of ≈5 nm, are structurally suitable for ammonia synthesis. In addition, maintaining a small particle size is important because the specific surface area available for the reaction is inversely proportional to the size of the nanoparticle.
Further microstructural analysis was conducted by TEM to investigate the epitaxial growth of the Ru nanoparticle prepared by the exsolution method. Numerous HR-TEM images were acquired from each ex-Ru/BCY and imp-Ru/BCY sample. Interestingly, the in-plane epitaxy relationship between the Ru nanoparticle and the BCY matrix was highly developed in the exsolved sample, unlike the impregnated nanoparticle. Figure 7 shows exemplified HR-TEM images of the ex-Ru/BCY and imp-Ru/BCY. Fast Fourier transforms (FFTs) from HR-TEM images exhibit diffraction peaks from the corresponding area, including the Ru nanoparticle and BCY matrix. Figure 7b shows a (0002) diffraction peak from the exsolved Ru nanoparticle coinciding with the (002) peak of the BCY matrix. Both diffraction peaks are parallel to the in-plane of the facet where the BCY matrix is exposed, which means that these diffraction planes are normal to the facet and aligned along the in-plane direction. Figure 7c shows an inverse FFT constructed using the selected diffraction peaks (0002) of Ru and (002) of the BCY matrix, demonstrating that the diffraction planes of (0002) Ru and (002) BCY are well-aligned across the interface. Edge dislocations were observed along the interface, which attributed to the difference between the d-spacings of Ru (0002) (2.138 Å) and BCY (002) (2.198 Å). The slight d-spacing difference between the two could have caused the observed edge dislocations.
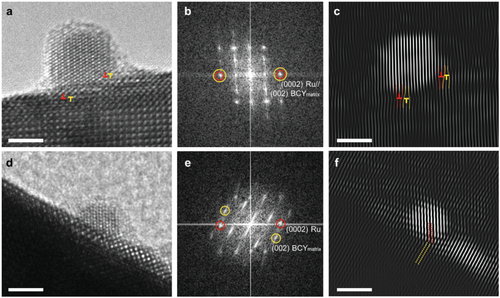
However, imp-Ru/BCY showed no such correlation. Figure 7d shows an HR-TEM image of imp-Ru/BCY, and its FFT is displayed in Figure 7e. Unlike ex-Ru/BCY, imp-Ru/BCY exhibited no diffraction peaks along the in-plane directions. Instead, the (0002) Ru peak was tilted from the surface. Figure 7f shows the inverse FFT image constructed using the (0002) Ru and (002) BCY diffraction peaks, where the Ru and BCY planes are not aligned but tilted. Given that both HR-TEM images were taken at the same zone axis, [100] BCY, the missing diffraction peaks along the in-plane directions reveal that the impregnated Ru nanoparticles grew on BCY with a lower orientation relationship compared to ex-Ru/BCY.
These results demonstrate that the planes of the exsolved Ru nanoparticles are highly epitaxial at a normal angle to the in-plane direction of the surface facet, whereas imp-Ru/BCY was not. Most exsolved Ru nanoparticles frequently exhibit in-plane epitaxy. Owing to the highly developed epitaxial relationship between the exsolved Ru nanoparticle and the matrix, edge dislocations were formed along the interface. A few edge dislocations were found, and they are marked by red (Ru plane) and yellow (BCY plane) “⊥” symbols. As a few edge dislocations were inserted in the Ru nanoparticle (Figure 7c), compressive stress would have developed; however, the combination of dislocation dipoles (red and yellow dislocations) could mitigate it to a certain extent. Epitaxial growth enables faster charge transport and a cleaner interface between the metal and support,[63] and the enhanced metal-support interaction may have resulted in increased catalytic activity.
Notably, exsolved Ru nanoparticles were frequently (≈¼) found that (0001) plane was exposed to the in-plane direction, as shown in Figure 7a–c. This means that the edge steps of the (0001) plane were exposed along the surface of the Ru nanoparticles. These steps provided a highly active B5 site and would have boosted the ammonia synthesis reaction.
Collating these observations indicates that the exsolved Ru nanoparticles are strongly bound to the matrix in an epitaxial relationship and have the (0001) plane exposed to the surface. The edge dislocations are evidence of strong binding between the Ru nanoparticles and matrix. This suggests that the Ru nanoparticles were tightly bound during the ammonia synthesis reaction, resulting in marginal changes in the distribution of the nanoparticle size (Figure 6).
The electronic structural modification of the exsolved Ru nanoparticles was explored by XPS and STEM/EDS characterizations. The electronic structure of Ru/BCY was investigated by X-ray photoelectron spectroscopy (XPS) of the Ru 3d orbital (Figure 8a). The peak position of Ru 3d5/2 in imp-Ru/BCY (280.1 eV) was in good agreement with that of Ru metal. In contrast, the binding energy of ex-Ru/BCY shifted to a lower binding energy (279.1 eV), indicating an increase in the electron density of Ru. Exsolved Ru nanoparticles were frequently observed to be bordered by a structurally modified BCY support, as some species surround the lower part of the nanoparticle. STEM/EDS line profiles were obtained along the Ru nanoparticles and BCY support in the horizontal and vertical directions (green lines in Figure 8b,c) to study these species. These line profiles reveal an unexpected Ba-rich phase, a well-known electronic promoter present around Ru nanoparticles and between Ru and BCY. Ru comprised the B site of the perovskite structure before exsolution, whereas Ba comprised the A site of the perovskite structure. During the exsolution process, Ru at the B site was exsoluted to form a nanoparticle on the surface, creating a B-site deficiency of the perovskite structure, which may have caused the A site occupying Ba to form a secondary material around the Ru nanoparticle.
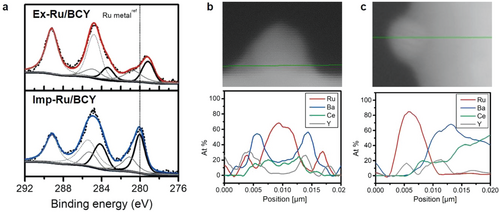
Ba is a well-known catalytic promoter for ammonia synthesis because of its electron-donating ability.[56, 61, 64] The dissociation of the stable NN triple bond is the rate-determining step in the ammonia synthesis reaction.[65] The dissociation of NN is promoted by electron transfer from the electron-rich Ru nanoparticle to the antibonding π orbitals of the NN triple bond. Consequently, electronic promoters such as Ba increase the catalytic activity of Ru by donating electrons to Ru. Hosono et al. reported increased ammonia synthesis activity owing to electronic structural changes,[10] and they also reported highly active Ru catalysts with a Ba promoter.[12] Aika et al. and Nagaoka et al. reported that Ba acts as an electronic promoter for ammonia synthesis.[32, 66] Therefore, electronic structure modification also accounts for the superior performance of ex-Ru/BCY compared to imp-Ru/BCY.[32] The exsolution process is well-suited for the preparation of a Ba-promoted Ru nanoparticle, where the Ba species are formed in situ during the exsolution process and are well-bordered by the Ru nanoparticle surrounding its lower part.
3 Conclusion
Size-controlled Ru nanoparticles with a homogeneous distribution were formed by exsolution from a deliberately chosen support material, BaCe0.87Y0.1Ru0.03O3-δ. Exsolved Ru nanoparticles on BCY (ex-Ru/BCY) showed improved activity for the ammonia synthesis reaction compared to catalysts prepared using the conventional preparation method. The exsolved Ru nanoparticles were sinter-resistant and retained the highly active small nanoparticle size during the reaction. A strong metal support interaction was demonstrated by the in-plane epitaxial growth of Ru nanoparticles on the BCY surface. Finally, the exsolution process produced an unexpected Ba promoter surrounding the base of the Ru nanoparticles, which modulated the electronic structure of Ru, favoring the ammonia synthesis reaction.
Exsolution is a unique and novel process for preparing nanocatalysts with a controlled nanoparticle size, improved stability, and increased metal-support interaction. Various oxide compositions are possible due to the flexibility of the perovskite structure, ABO3, and exsolution of various transition metals, widely used for various catalytic reactions, have been reported to date.[57, 67-69] We have shown that the appropriate choice for the active metal and supporting oxide enables the preparation of a highly active catalyst for the ammonia synthesis reaction. We anticipate that a wide range of catalytic reactions will benefit from the exsolution process through deliberate design of the exsolution catalyst.
4 Experimental Section
Preparation of Ru Catalysts
The Ru-doped-BCY support was synthesized using the glycine nitrate process (GNP). Barium nitrate (Ba(NO3)2, 99%, Sigma-Aldrich), cerium nitrate (Ce(NO3)36H2O, 99%, Sigma-Aldrich), yttrium nitrate (Y(NO3)34H2O, 99.8%, Sigma-Aldrich), and ruthenium(III) chloride trihydrate (RuCl33H2O, Sigma-Aldrich) were used as reagents. Stoichiometric amounts of BaCe0.87Y0.1Ru0.03O3-δ (Ru-doped-BCY) were dissolved in distilled water and stirred overnight. After complete dissolution, glycine (CH5NO2, 99%, Daejung) was added with a glycine-to-nitrate molar ratio of 0.55, and the resulting solution was boiled at 100 °C for 2 h to evaporate excess water. The solution was slowly poured into a heated quartz pot at 300 °C, and auto-ignition occurred.[70] The obtained powder was calcined at 1300 °C for 2 h. The exsolution process was conducted by reducing the resultant powder at high temperature (1000 °C) under a reducing atmosphere (5% H2, in Ar-balanced) for 5 h (ex-Ru/BCY). As a control sample, BaCe0.9Y0.1O3-δ (BCY) without Ru was prepared using the same GNP process and oxidative heat treatment without the final reduction treatment. A conventional nanoparticle catalyst for BCY was prepared using the incipient wetness impregnation method. Aqueous ruthenium(III) chloride trihydrate solution was mixed well with the BCY powder and reduced at 600 °C for 3 h (imp-Ru/BCY). Commercial Ru nanoparticles on carbon (Ru/C, Sigma-Aldrich) catalyst was also used as a control sample to elucidate the effect of the support.
Catalyst Characterization
Powder X-ray diffraction (XRD, D/max2500/PC, Rigaku, Japan) was used to analyze the crystalline structures of the catalysts. Cu-Kα radiation (λ = 1.5405 Å) was used at a scan rate of 1° min−1 and 2θ scan range of 10°–90°. The morphologies of the samples were observed by scanning electron microscopy (SEM, Regulus8230, Hitachi, Japan). High-resolution transmission electron microscopy (HR-TEM, TITANTM 80–300, FEI, U.S. at 300 kV and TEM, Tecnai F20, FEI, U.S. at 200 kV) was used to analyze the microstructural characteristics of the samples and the size distributions of the Ru nanoparticles. Scanning transmission electron microscopy (STEM, Talos F200X, FEI, U.S. at 200 kV) and high-angle annular dark-field scanning transmission electron microscopy (HAADF-STEM) images with an energy-dispersive X-ray spectroscopy (EDS, Talos F200X, FEI, US) detector were used to determine the elemental composition of the catalyst samples. XPS (Nexsa, Thermo Fisher Scientific) was performed to determine the electronic structure of the elements on the surface of each sample. The Ru 3d binding energy was measured using a microfocus monochromatic X-ray Al-Kα (1486.6 eV) source. Because the binding energy of adventitious carbon (284.8 eV) overlapped with the Ru 3d peaks, the carbonate peak (289 eV)is used to calibrate the energy of the XPS spectra.
X-ray absorption spectroscopy (XAS) was conducted at the 10C and 7D beamlines of the Pohang Light Source (PLS). Ru K edge spectra were obtained in fluorescence mode. A reference Ru mesh was measured concurrently to calibrate each sample. RuO2 powder (Ruthenium(IV) oxide, 99.9%, Sigma-Aldrich) was also used as a reference for Ru oxide and to obtain the S02 value to calculate the coordination number. The X-ray absorption spectra were processed and fitted using ATHENA and ARTEMIS software.[71]
Ammonia Synthesis Activity Test
The ammonia synthesis reaction was conducted in a quartz fixed-bed reactor with H2 and N2 gas with high purities at a flow rate of 120 sccm (H2:N2 = 3:1). 20 mg of ex-Ru/BCY and 50 mg of imp-Ru/BCY and Ru/C were used for the activity test. A H2O and O2 gas filter (High-capacity gas purifier, Chromres) was used to increase gas purity. Before the main reaction test, ex-Ru/BCY and imp-Ru/BCY were reduced at 750 °C for 1 h with 99.999% H2 to remove surface carbonates.[32] The reaction was conducted at 390, 420, and 450 °C at a pressure of 0.1 MPa. The amount of catalyst, reaction temperature, and gas flow rate were set to obtain the kinetic parameter of catalysis, and the conversion of N2 was controlled below 15% compared to the equilibrium conversion. The product gas was bubbled into a 5 mm HCl aqueous solution to trap produced ammonia. Ammonia was quantified by the indophenol method based on the Berthelot reaction.[74] The indophenol method is one of the most accurate methods for detecting low ammonia concentrations.[75, 76] In this method, ammonia reacts with phenol and hypochlorite in an alkaline medium to form indophenol blue.[76, 77] An alkaline hypochlorite solution (500 µl) (A1727, Sigma-Aldrich) and 500 µl of phenol nitroprusside solution (P6994, Sigma-Aldrich) were added into a diluted sample, and the mixture was incubated for 30 min in the dark at room temperature. The absorbance of the solution was analyzed using UV-vis spectroscopy (UV-1900i, Shimadzu, Japan).
Statistical Analysis
The ammonia synthesis activity of each sample was measured three times, and the means and standard deviations were calculated from the values. The Ru nanoparticles size was measured based on TEM images. Ru nanoparticles present at the edge of the BCY surface were randomly selected to distinguish Ru nanoparticles from the support. Particle size of at least 100 particles was measured using the Gatan software. And the means and standard deviations were calculated from the values.
Acknowledgements
This research was financially supported by the Korea Institute of Energy Technology Evaluation and Planning (KETEP) (No. 20223030030090), National R&D Program through the National Research Foundation of Korea (NRF) funded by the Ministry of Science and ICT (NRF-2021M3I3A1084278), Institutional Research Project (2E31852), and KU-KIST Graduate School Project (2V09371) of KIST. Experiments using PLS-II were supported in part by MSIT and POSTECH.
Conflict of Interest
The authors declare no conflict of interest.
Open Research
Data Availability Statement
The data that support the findings of this study are available from the corresponding author upon reasonable request.