High Thermal Conductivity Polymer Composites Fabrication through Conventional and 3D Printing Processes: State-of-the-Art and Future Trends
Abstract
The lifespan and the performance of flexible electronic devices and components are affected by the large accumulation of heat, and this problem must be addressed by thermally conductive polymer composite films. Therefore, the need for the development of high thermal conductivity nanocomposites has a strong role in various applications. In this article, the effect of different particle reinforcements such as single and hybrid form, coated and uncoated particles, and chemically treated particles on the thermal conductivity of various polymers are reviewed and the mechanism behind the improvement of the required properties are discussed. Furthermore, the role of manufacturing processes such as injection molding, compression molding, and 3D printing techniques in the production of high thermal conductivity polymer composites is detailed. Finally, the potential for future research is discussed, which can help researchers to work on the thermal properties enhancement for polymeric materials.
1 Introduction
Polymers and their composites play a vital role in various applications such as aerospace, automotive, microelectronics, biomedical, and so on. This is due to their inherent properties discovered through continuous research and development on their properties. Most polymers have the least thermal conductivity which makes them a secondary choice in many engineering applications involving high heat generation applications where device cooling is highly mandatory, mainly in microelectronics. Therefore, enhancing the thermal conductivity of the polymer composite is imperative to widen their application in various sectors. Recent advancements in research in polymer composites introduced many ways to enhance thermal conductivity. Nanoparticle reinforcement is one of the dominant techniques which is helping to achieve high thermal conductivity.[1]
The existence of a well-interlinked thermal conductive path/network constructed (Figure 1) using high thermal conductivity reinforcement within a matrix could increase the thermal conductivity of composite materials.[2] Those reinforced nanoparticles may be in the form of single, hybrid, surface-treated nanoparticles, magnetically aligned particles, etc.
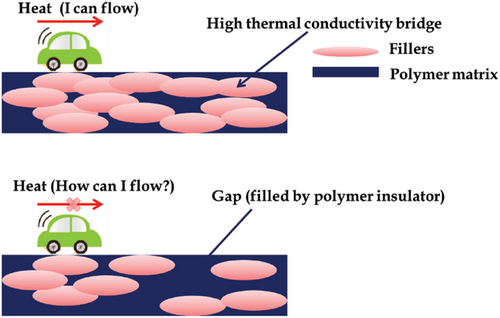
Polymers are typically good thermal and electrical insulators and their thermal conductivity could be improved with the addition of high thermal conductivity nanoparticles such as ceramics (Al2O3, h-BN, AlN, SiC, and so on), CNTs, 2D materials (graphene, CNNS, BNNS). The thermal conductivity of the resultant nanocomposite depends on many factors as indicated in Figure 2. The presence of impurities on the surface of 2D materials, such as BNNS and carbon materials is deleterious due to their intrinsic thermal and electrical properties as they originate from electron and phonon scattering, which causes a decline in electrical and thermal conduction.[3]

1.1 Enhancement of Thermal Conductivity of Polymers Using Nanoparticles
The thermal conductivity of various polymers can be enhanced by introducing high thermal conductivity nanoparticles into the polymer matrices.[4] The most commonly used nanoparticles in polymer nanocomposites are Al2O3, h-BN, SiC, SWCNT, and MWCNT.[5, 6]
Ruan et al. have used urea melt to aminate GO to produce NH2-GO. Furthermore, the prepared NH2-GO was converted into NH2-rGO through a thermal reduction method. The prepared NH2-rGO (with various wt.%) was reinforced in PI with the motive of obtaining high thermal conductivity. It was found that the reduction of interfacial adhesion between the filler and matrix material can be possible by the optimum amination process. As a consequence, it was found that low interfacial resistance and phonon scattering was achieved and these phenomena improved the thermal conductivity in both in-plane and through-plane directions than the pure PI. The 15 wt.% NH2-rGO reinforced PI showed an in-plane thermal conductivity of 7.1 Wm−1K−1 which is 8 times higher than that of the pure PI.[7]
However, reinforcement of the aforementioned nanoparticles in a single or hybrid form improves the thermal conductivity of polymer nanocomposites only to a certain level.[8] Besides, instances such as augmented power density with shrinkage in size (i.e., modern electronic devices) demand higher thermal conductivity, which is difficult to attain through this technique.
1.2 Enhancement of Thermal Conductivity of Polymers Using Physical/Chemical Changes
It is noticed that the reinforcement of high thermal conductivity nanoparticles is not only sufficient to reach higher thermal conductivity but it needs some additional techniques like reduction of interfacial resistance, surface treatment of fillers, etc.[9]
Equation (1) has three variables: l is the phonon mean free pathway, u is the sound velocity, Cv is the volumetric molar heat capacity that determines polymer properties, and k is the thermal conductivity of the polymer. The Cv is evaluated by the properties of a resin whereas, l is determined by the crystallinity and orientation of the cured epoxy.[11-15] To achieve high thermal conductivity, the variable l needs to be increased. This necessitates the reduction of both static and dynamic phonon scattering in the crystalline area.
Phonon scatter is a typical issue in organic insulating resins, which is majorly due to their amorphous structure, and this has a significant influence on their thermal conductivity. Hence, it is realized that the improvement of the intrinsic thermal conductivity of polymer-based materials is a highly challenging task and this may be achieved through novel methods such as molecular design and direction alignment.[16]
Akatsuka et al. from Japan focused on the enhancement of the intrinsic thermal conductivity of polymers. The enhancement of thermal conductivity of four different liquid epoxies was demonstrated by transforming the microscopic anisotropy crystal structure (random network) into macroscopically isotropic (ordered structure). Such an orderly arrangement of the liquid crystalline epoxy monomers with biphenyl groups was synthesized, and the thermal conductivity of the cured epoxy is reported as 0.96 Wm−1K−1, which is five times higher as compared to traditional epoxy resin (0.17 to 0.21 Wm−1K−1). Recently, researchers have shown substantial interest in controlling the network structure of polymeric materials to establish new functionalities.[12]
Luo et al. prepared liquid crystalline epoxy (LCE)/graphene (Gr) composites through a simple blending technique and incorporated polyethylene glycol (PEG) as an interface agent to enhance the compatibility between the LCE and Gr. For this research, epoxy monomer named 3, 3′, 5, 5’ – tetramethyl l – 4, 4′ biphenyl diglycidyl ether was used as the matrix, which is referred to as LCE, since it is composed of biphenyl mesogenic unit. Generally, molecules of LCE forms highly ordered structure during processing; this is the distinguishable property of LCE compared to conventional epoxy monomer, such as Bisphenol-A type epoxy. As mentioned earlier, such ordered structures could enhance thermal conductivity by suppressing phonon scattering. It was reported that the thermal conductivity of LCE reached the maximum of 10 Wm−1K−1 for the reinforcement quantity of 80 wt.% PEG/Gr (in which the PEG/Gr ratio was 1:2). They were able to generate multiple filler-to-filler contact points in the matrix at this level of higher filler addition, resulting in the formation of large thermal conductive networks that contributed to the composite's ultrahigh thermal conductivity.[17]
In another research, Pourakbar et al. synthesized Janus / non-Janus HGO micro-and nanoparticles through a one-step hydrothermal method and used them as reinforcement to improve the thermal conductivity of the PS/PMMA blend. It was found that both micro-and nano-sized HGO and Janus HGO reinforcements were capable of increasing the thermal conductivity of pure PS/PMMA blend. However, the performance of nano-sized HGO and Janus-HGO was more significant than the micro-sized fillers. This was due to the uniform dispersion of nanoparticles inside the matrix. The thermal conductivity of the pure polymer blend was 0.194 Wm−1K−1, and it reached up to 1.148 Wm−1K−1 when nano-Janus HGO/HGO micro/HGO nanofillers concentration (wt.%) of 34/33/33 were added.[18] In another research, An et al. used 3D structured chemically modified BNNS's as filler to enhance the thermal conductivity of NR matrix. The BNNS/NR interface composites were prepared by establishing covalent chemical bond connections of BNNS and NR. An insufficient 3D heat conduction network was developed when BNNS content was 5 wt.%, and a gradual development of such a network was observed when the filler level reached 10 and 15 wt.%, however, alignment structures were not apparent. This network formation was found to be good at a BNNS concentration of 25 wt.% and at this level, the BNNS/NR composite showed maximum through-thickness thermal conductivity of 0.79 W m−1 K−1. Their findings showed that 3D network architecture and chemical interactions between BNNS and NR, played a key role in lowering the interfacial heat resistance. The faster thermal response, adequate electrical insulation and better mechanical properties of BNNS/NR composites made it an appropriate choice for the TIMs applications.[19]
Hence, for an effective thermal conductivity enhancement of polymers, modification of physical characteristics is also highly required. In addition, ultra-high thermal conductivity enhancement can also be possible when making changes in both physical and structural levels. Perhaps, the physical changes deal with the design of molecular-level activities and structural changes may deal with the presence of various constitutions in polymer composites.
1.3 Enhancement of Thermal Conductivity of Polymers using 2D or 3D Nanosheets
Foremost, Wang et al. used carbon nitride nanosheets (CNNS) to improve the thermal conductivity of PI nanocomposite films. The distribution of CNNS in PI was studied using a scanning electron microscope (SEM), and it was found that the stacks of CNNS lead to a formation of a heat conduction network, as a result of this, rapid heat transfer in the horizontal direction was realized. The maximum thermal conductivity (2.04 Wm−1K−1) of PI/CNNS nanocomposite was noticed when the amount of CNNS reinforcement reached 20 wt.%, which is 11 times higher than pure PI. Due to strong interactions with PI and the orientation of PI molecules during imidization process, CNNS was able to achieve in-plane self-orientation under solvent evaporation and developed a continuous thermal network in the PI film.[20] In recent years, 2D materials such as CNNS, graphene, BNNS, etc., have captured significant attention in the heat transfer enhancement in polymers because of their layered structure and high thermal conductivity.[21] A parallel improvement of thermal conductivity and thermal stability of polymers could increase the possibilities of their utility in different applications. In this way, Wu et al. developed ultra-strong, flexible, high thermally-conductive, and thermally-stable polymer nanocomposite films which contain 1D rods like aramid nanofiber (ANF) and 2D boron nitride nanosheets (BNNS). The prepared ANF/BNNS films showed in-plane thermal conductivity of 46.7 Wm−1K−1 at 30 wt.% BNNS content. The out-of-plane thermal conductivity of ANF thin films increased gradually with the addition of BNNS filler. On the other hand, the in-plane thermal conductivity increased more quickly. The effect of both molecular chain orientation and strong interactions at the organic/inorganic interface contributed to the high thermal conductivity.[22] Similarly, Zhao et al. used 1D-ANFs and 1D edge-hydroxylated BNNTs as reinforcement in PEI and found enhanced thermal conductivity of PEI nanocomposites paper of 9.9 Wm−1K−1 at 15 wt.% of BNNT. This improvement in thermal conductivity exists due to the extent of BNNT–BNNT interactions and this connection predominantly improved as the BNNTs filler content increased, potentially leading to the establishment of effective thermal flow routes in the manufactured PEI nanocomposite paper.[23]
It is realized that the formation of a heat conduction path/network is the primary factor to obtain higher thermal conductivity polymer composites. Notably, such network formation is better when using 3D structured reinforcements in the development of polymer composites as compared to 2D nanosheets such as Gr or BNNS. The conversion of 2D lamellar Gr into a freestanding 3D network structure has received enormous interest in the past few decades, because these structures have greater electron, phonon, and ion transport capacities compared to Gr sheets.[24-27]
Zhao et al. developed two different PDMS composites using Gr nanosheets (GrNS/PDMS) and 3D Gr foam (3DGrF/PDMS). At 0.7 wt.% of reinforcement level, the thermal conductivity of GrNS/PDMS and 3DGrF/PDMS reached 0.46 and 0.56 Wm−1K−1, respectively, and these values are 2.42 and 2.95-times higher compared to pure PDMS.[28] The outcomes of the research[28] apparently show that the 3D Gr foam structure has a greater influence on thermal conductivity enhancement than the 2D GrNS. Similarly, Wang et al. followed a facile technique to develop 3D Ti3C2Tx (3D-MXene) nanosheets without using adhesive agents. The prepared MXene nanosheet reinforcement was utilized to improve the electrical and thermal conductivity of PDMS. It was found that only the lowest quantity of MXene nanosheet reinforcement was sufficient to obtain high thermal conductivity. For instance, MXene/PDMS nanocomposites reinforced with 2.5 vol.% of MXene nanosheet showed a 220% increase in thermal conductivity (0.576 Wm−1 K−1) in comparison to pure PDMS. However, there was a considerable reduction in thermal conductivity when the MXene nanosheet concentration reached 3 vol.% and beyond. The heat flow takes in the least resistance path and in the MXene/PDMS nanocomposites, the heat transfer occurs through the MXene flakes, because MXene has greater thermal conductivity compared to pure PDMS. The interconnection between MXene flakes leads to reduced interfacial thermal resistance in the MXene skeleton, resulting in enhanced heat flow due to great thermal conductivity enhancement in the 3D-MXene composites at an optimum filler concentration. However, at a lower filler concentration (i.e., 1.5 vol.% and below), the flakes interconnections were unsuccessful in the MXene skeleton, resulting in restricted improvement of thermal conductivity. Similarly, at a higher filler concentration (i.e., 3.0 vol.% and beyond), the excess of MXene flakes may act as a barrier and leads to imperfect orientation in the through-plane direction resulting in minimum flakes-to-flakes contact.[29] At higher filler concentrations, adequate infiltration of the polymer through narrow gaps is unlikely; resulting in the entrapment of air. Consequently, there was a limited enhancement in the thermal conductivity of resultant nanocomposites. Vu et al. prepared vertically aligned 3D–SiC sheet scaffolds through the template-assisted chemical vapor deposition (TA-CVD) technique. The authors demonstrated a methodology to synthesize SiC sheet scaffolds from graphene base for the first time and used them as reinforcement in epoxy composites. The developed SiC/epoxy composites exhibited anisotropic thermal properties with ultrahigh thermal conductivity of 14.32 Wm−1K−1 in through-thickness direction at a SiC sheet concentration of 3.71 vol.%. The presence of silicon (Si) on the boundary of the packed pores was confirmed through energy dispersive spectroscopy (EDX), and was continuously well-stacked and highly aligned in the entire volume of the composite. The aligned and interconnected SiC sheets are able to form a heat conduction network throughout the volume of the composite. The SEM images of the fractured surfaces confirmed good adhesion between vertically aligned SiC nanosheets and epoxy, this minimizes the risk of debonding at the interface between the SiC surface and epoxy. As a result of this, good mechanical strength and ultra-high thermal conductivity were obtained.[30] Amplified power density and remarkable shrinkage of device size are the major concern in electrical and electronic systems such as integrated circuits (ICs) and light-emitting diodes (LED). In many engineering applications, EMI shielding is provided to absorb electromagnetic radiation and dissipate it into heat energy.[31, 32] Conversely, the substantial quantity of generated thermal energy from the parts of the electronic gadgets elevates the device temperature, and this causes the depletion of device span, thermal fatigue, and or even failure.[33]
Fang et al. used in-situ fabricated nano-size hollow Fe3O4 spheres onto a 3D Gr foam surface, and it was reinforced in PDMS to develop high heat conductive, electrically conductive, and effective EMI shielding nanocomposites. A 12 wt.% Gr foam/hollow Fe3O4 reinforced PDMS showed the maximum in-plane thermal conductivity of 28.1 W/mK at room temperature. The four factors which defined the thermal conductivity improvement by the graphene are purity of Gr, interconnected networks, high density, and orientation.[34]
Note: f-BN: Functionalised BN, GrNS: Graphene nanosheets, NR: Natural Rubber, GF: Graphene foam, 3DGrW: 3D multilayer graphene web, CNF – 3D – BNNS: cellulose nanofiber supported 3D interconnected BNNS, SiC-NW: SiC nanowire, VA-SiC20: vertically aligned – SiC (where the “20” indicates VA-SiC was formed from the VA-GO suspensions with concentrations of 20 mg mL−1), BN-PDA-KH570: functionalized BN with poly(dopamine) (PDA) subsequently grafted with γ-methacryloxypropyl trimethoxy silane (KH570), m-BN: micron BN, BN-SH: thiol-functionalized BN, PU: Polyurethane, SiO2@MWCNT: Silica coated MWCNTs, BN@MWCNT: BN coated MWCNTs, MgO@MWCNTs: MgO coated MWCNTs, Al2O3@GrS: Al2O3 coated Gr sheets, SiO2@TrGO: silica-coated thermally rGO, SiCNW@GrS: 1D SiC nanowires grown on 2D Gr sheets, ETDS: epoxy-terminated dimethylsiloxane, QIGF: Quasi-isotropic graphene framework.
Table 1 makes it clear that adding one of the 1D, 2D, or 3D fillers can improve the heat conductivity of polymers. Additionally, the effectiveness of each filler in improving heat conductivity varies.
Reinforcement (s) | Matrix | The concentration of reinforcement* | Thermal conductivity (Wm−1 K−1) | Increment# | Ref. | |
---|---|---|---|---|---|---|
Matrix | Composite | |||||
Gr | PI | 5 wt.% | 0.28 | 1.05 | 3.75 times | [35] |
BN | 30 wt.% | 0.174 | 0.696 | 4 times | [36] | |
MWCNT + rGO | 10 wt.% | 0.27 | 1.6 | 6 times | [37] | |
f-BN | 30 wt.% | — | 0.71 | — | [38] | |
rGO | 2 wt.% | 0.17 | 0.26 | 1.5 times | [39] | |
SiC + Gr | 7 wt.% | — | 0.577 | 138% | [40] | |
Nanodiamond + h-BN | 40 wt.% | — | 0.98 | 5.2 times | [41] | |
CNNS | 20 wt.% | 0.18 | 2.04 | 10.3 times | [20] | |
Gr | Epoxy | 10 vol.% | 0.201 | 5.1 | 25 times | [42] |
GrNS + GF | NR | 10.27 vol.% | 0.13 | 11.16 | 86 times | [43] |
3DGrW | Epoxy | 8.3 wt.% | 0.2 | 8.8 | 44 times | [44] |
3D-BNNS aerogels | Epoxy | 9.29 vol.% | 0.16 | 2.85 | 18 times | [45] |
CNF – 3D –BNNS | Epoxy | 9.6 vol.% | 0.184 | 3.13 | 17 times | [46] |
3D BN platelets + rGO | Epoxy | 13.16 vol.% | 0.18 | 5.05 | 28 times | [47] |
BNNS | Epoxy | 15 vol.% | 0.2 | 6.07 | 30 times | [48] |
Aligned – BNNS | PVDF | 33 wt.% | — | 16.3 | — | [33] |
SiC-NW | Epoxy | 2.17 vol.% | 0.18 | 1.67 | 9.3 times | [49] |
VA-SiC20 | Epoxy | 3.71 vol.% | 0.23 | 14.32 | 62.3 times | [30] |
BN-PDA-KH570 platelets | NR | 30 vol.% | 0.10 | 0.39 | 4 times | [50] |
rGO | NR | 5 wt.% | 0.157 | 0.219 | 1.4 times | [51] |
rGO | NR | 38.53 vol.% | 0.11 | 0.56 | 5 times | [52] |
m-BN | Thiol- epoxy | 60 wt.% | 0.27 | 1.058 | 4 times | [53] |
BN-SH | NR | 25 wt.% | 0.18 | 0.79 | 4.4 times | [19] |
SiO2@MWCNT | PU | 1 wt.% | 0.177 | 0.31 | 1.75 times | [54] |
BN@M | ||||||
WCNT | PI | 3 wt.% | 0.188 | 0.388 | 2 times | [55] |
MgO@MWCNTs | Epoxy | 2 wt.% | 0.19 | 0.29 | 1.5 times | [56] |
SiO2@rGO | Epoxy | 30 wt.% | — | 0.452 | 200% | [57] |
Al2O3@GrS | PVDF | 40 wt.% | 0.205 | 0.586 | 3 times | [58] |
SiO2@TrGO | Epoxy | 1 wt.% | 0.2 | 0.322 | 1.6 times | [59] |
SiCNW@GrS | PI | 7 wt.% | — | 0.577 | 138% | [40] |
SiO2@BN | PMMA | 40 vol.% | 0.16 | 5.6 | 35 times | [60] |
Gr | PP | 10 wt.% | — | 1.53 | — | [61] |
rGO | PI | 8 wt.% | 0.18 | 2.78 | 1440% | [62] |
Gr | PS | 10 wt.% | 0.18 | 2.6 | 1344% | [63] |
CNT@rGO | SBR | 3 wt.% | — | 0.45 | 2 times | [64] |
BNNS | Epoxy | 40 wt.% | 0.22 | 5.86 | 2500% | [65] |
3D Gr | PI | 0.35 wt.% | 0.15 | 1.7 | 1033% | [66] |
3D Gr foam | PDMS | 0.7 wt.% | 0.19 | 0.56 | 195% | [28] |
3D Gr foam | Epoxy | 19 vol.% | 0.21 | 35.5 | 16 800% | [67] |
3D GrA | PMMA | 2.5 vol.% | 0.2 | 0.7 | 250% | [68] |
3D Gr | Epoxy | 0.92 vol.% | 0.16 | 2.13 | 1231% | [69] |
3D Gr (QIGF) | Epoxy | 5.5 wt.% | 0.18 | 10 | 5455% | [70] |
- * Concentration of reinforcement at which the composite exhibited maximum thermal conductivity.
- # Increment in thermal conductivity compared to pure polymer.
1.4 Enhancement of Thermal Conductivity of Polymers Through Filler Alignment Method
From the previous section, it is understood that the reinforcement of ceramic nanofillers is the collateral method to obtain high thermal conductivity polymer composites. Usually, literature has reported two different types of thermal conductivity known as in-plane thermal conductivity (IPTC) and through-plane thermal conductivity (TPTC) of materials. Out of these two values, IPTC is less pertinent in heat transfer applications but higher IPTC helps to reduce hot spots.[71-73] Hence, it is obvious to devote more attention to the TPTC enhancement of a thermal interface material that opens the way to achieve good processing stability and life span of an electronic gadget.[74] For instance, though the Gr exhibits superior IPTC value (varies from 1000 to 3000 Wm−1K−1), it offers relatively low TPTC (ca. 5 to 6 W m−1 K−1).[75, 76] Similarly, due to the anisotropic nature, h-BN shows much higher IPTC (≈600 W m−1 K−1) than the TPTC (≈30 W m−1 K−1).[77] To take advantage of the high IPTC, positioning and aligning the BN (or) Gr filler along the in-plane direction could result in the required polymer composites with superior thermal conductivity. Subsequently, the resultant polymer composite material conducts more heat in the through-plane direction. Hence, the development of a universal approach for aligning 2D materials in a preferred orientation is critical. Many advanced techniques were demonstrated in literature to improve the TPTC of polymer nanocomposites, and magnetic alignment is one of them. In the magnetic alignment technique, the major impediment encountered is that nanoceramics are diamagnetic and thus need high power magnets.[78] Therefore, when using the magnetic alignment method, it is required to reinforce magnetically responsive components into the composite like FeO3-BH,[79] FeO3-rGO.[80] To rectify this issue, Yu et al. prepared BN/TPU composite films and used hot-pressing technique to align the h-BN particles in an impeccably oriented network and reduce interfacial adhesion. The hot-pressed BN/TPU composite film which contained 95 wt.% of BN manifested the highest IPTC and TPTC of 50 and 6 W m−1K−1, respectively. It was noticeable that in the BN/TPU composite, the quantity of polymer was reduced when using 95 wt.% of h-BN. Certainly, this is due to the decreased low thermal conductivity polymer between adjacent sheets and the significant interfacial contacts between the h-BN and TPU phases, which reduced the composite's interface thermal resistance. The ensuing hot-pressing procedure resulted in the production of a densely packed structure, which boosted thermal performance even further.[81]
1.5 Enhancement of Thermal Conductivity of Polymers using Hybrid Fillers
The usage of a hybrid form of reinforcement in polymer composite preparation could enhance the primary properties of the resultant material and also helps in improving/sustaining the secondary properties.[82] For instance, in microelectronics, the polymer with good thermal conductivity (primary property) is highly essential; however, it should not affect the electrical insulation (secondary property). Wu et al. prepared BNNS/epoxy and Ag-BNNS/epoxy composites and compared their performance in the heat transfer process. Due to insufficient filler concentration, both the above-mentioned composites exhibited a similar rise in thermal conductivity by up to 10 vol.%. However, this improvement was apparent in Ag-BNNS/epoxy composites beyond 10 vol.%. At a level of 25 vol.%, the thermal conductivity of Ag-BNNS/epoxy was observed to reach a maximum of 2.14 W m−1K−1, which was almost two times higher than the BNNS/epoxy (1.13 W m−1K−1). It was revealed that the Ag-BNNS produced better property enhancement than the bare BNNS reinforcement in an epoxy matrix. The synergistic effect of Ag and BNNS helped in building a healthy thermal conduction network with a minimum interfacial gap, and this augmented the high thermal conductivity of nanocomposites. The BNNSs formed the primary heat conduction routes in epoxy nanocomposites and Ag nanoparticles helped to bridge the gaps between BNNSs (refer to Figure 4). This inter-filler connectivity and less heat flow resistance at interfaces enriched the thermal conductivity of Ag-BNNS/epoxy nanocomposites.[83] In another research, Xiao et al. developed epoxy nanocomposites and revealed a significant increase in the thermal conductivity of epoxy. Hybrid fillers namely SiC nanowires and functionalized BNNSs were incorporated in epoxy, and this resulted in a maximum thermal conductivity of 4.22 W m−1K−1 when the hybrid filler level was 21.9 vol.%, which is 1658% more than that of pure epoxy. The surface functionalized BNNSs fillers invaded interstitial gaps between SiC nanowire networks and entangled. This provided a synergistic effect with low interfacial resistance (both filler-to-filler and filler-to-matrix). Due to the entanglement of SiC nanowires/functionalized BNNS fillers and the enhanced interface interaction by BNNS modification, the interfacial thermal resistance between filler/filler and filler/matrix reduced a lot compared with the random dispersion method. The surface characteristics of pure and functionalized BNNS were compared using FTIR pattern, and the formation of hydroxyl surface groups on the edge of BNNS was found. In addition, the FTIR spectra of functionalized BNNS showed that the silane produced a covalent bond with BNNS. This surface modification of BNNS was considered to optimize the interface contact between filler and matrix, resulting in the reduction of thermal resistance.[84]
Feng et al. fabricated epoxy composites in which the reinforcements used were functionalized Gr and h-BN. The hybrid fillers exhibited a synergistic effect on the thermal conductivity enhancement of epoxy composites. Typically, the RGO@Ni(OH)2 showed excellent dispersion and interfacial interaction in epoxy. It resisted the agglomeration of h-BN nanosheets and acted as a bridging agent for adjacent h-BN sheets. As a result of these factors, a high thermal conductivity (2 W m−1K−1) of ternary epoxy composites was achieved which was 39.4% higher than epoxy/h-BN.[85]
Ren et al. used a novel method to prepare hybrid nanofillers, which contained Gr and BNNS. The surface of the Gr was decorated with BNNSs and used as reinforcement in epoxy composites. The heat could be transported via interconnected BNNSs that operate as phonon transport bridges. Besides, the BNNS filler minimized the contact between adjacent Gr particles, which acted as a barrier for electrical charge flow. Few BNNSs were dispersed on the surface of Gr in the hybrid structure at low BN/Gr ratios (shown as GBN1 in Figure 3). More BNNSs were detected without any noticeable aggregation as the BN/Gr ratio increased (GBN10). A huge number of BNNSs covered the surface at high BN/Gr ratios (GBN50), and observable aggregation could be seen through the micrograph of the samples. Strong electrical resistance and good heat flow behavior were found when using 500 mg of BNNSs and 50 mg of Gr particle (refer to GBN10 in Figure 3).[86]
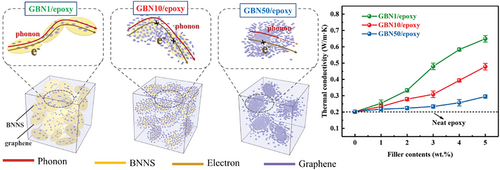
Liu et al. investigated the synergistic effect of short-CF and BN reinforcement on the thermal conductivity and electrical conductivity of PDMS. The spin coating process was used to fabricate short-CF/BN/PDMS composites and the 15 wt.% short-CF and 20 wt.% BN loaded PDMS film exhibited 2.3 W m−1 K−1 thermal conductivity, which was 990% greater than pure PDMS. The increase in thermal conductivity can be attributed to two factors.[87] To begin with, both short-CF and BN have high intrinsic thermal conductivity, which means they may significantly improve the thermal conductivity of polymer composites, and such a trait has been reported in the literature.[88, 89] Furthermore, the formation of “bridge-island” type structure between short-CF with a high aspect ratio and BN nanoparticles provides a complete heat conducting pathway (refer Figure 4) in the matrix, and owing to this the film's heat conduction ability significantly improved.[87] Similarly, Jiang et al. used functionalized Gr and BN to have a synergistic influence on the thermal conductivity of polystyrene composites. When the mass ratio of GO/hydroxylated BN was 7:3, the thermal conductivity of the PS composites reached a peak value and showed a thermal conductivity enhancement of up to 20%. However, it was less than the synergistic progression of the thermal conductivity of Gr/BN with the same filler loading, and a thermal conductivity improvement of ≈21.5% was recorded. According to the study, the oxygen-containing groups on the 2D thermal conducting fillers did not actively contribute to the improvement of heat conduction.[90]
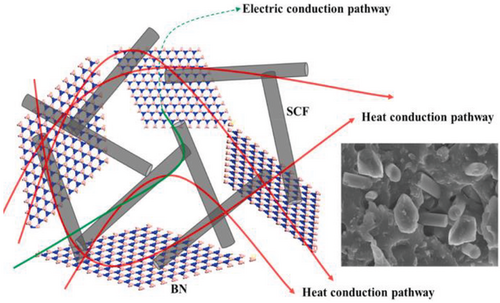
Large enhancement of thermal conductivity is appreciated in electronic device packaging applications and hybrid fillers reinforcement is the potential route to attain such enhancement. For instance, Dong et al. worked on the improvement of the thermal conductivity of PI using two-hybrid fillers such as BNNS and AgNW. The authors used the ice-template method followed by the hot pressing technique to fabricate high thermal conductivity PI composites. It was noticed that the hybrid fillers formed a thermal conduction network with reduced interfacial resistance, which led to rapid heat transfer. The developed PI nanocomposite that possessed 20 wt.% BNNS/AgNW showed the highest in-plane thermal conductivity of 4.7 W m−1 K−1, this was 324% higher than the pure PI (refer Figure 5). In addition, the PI/BNNS/AgNW nanocomposites had outstanding electrical insulation and dielectric properties, as well as a low thermal expansion coefficient (refer to Figure 5c).[91] Tsai et al. found that the addition of micron-sized BNNS to the matrix phase can enhance the polymer chain orientation (particularly at the interface zone between the matrix and reinforcement), which results in a reduction in the thermal expansion coefficient of the matrix phase.[92]

2 Advancement of 3D Printing of Polymers and Their Composites
Recently, polymer-based 3D printer has become more accessible and has opened opportunities to carry out further research in material printing. The stereolithography type of 3D printing process was initially described by Charles Hull and this process is frequently called additive manufacturing (AM), rapid prototyping (RPT), or solid-freeform (SFF) manufacturing.[93, 94] 3D printing was poised to refashion the research and manufacturing sectors, owing to Hull's efforts and Scott Crump's evolution of fused deposition modeling (FDM) in 1990. Subsequently, the introduction of the first “3D printer” in 1993 by MIT professors Michael Cima and Emanuel Sachs and the contribution of numerous groups on this technology enabled the usage of 3D printers for commercial purposes.[95, 96]
Modern resin-printing methods are continuously being developed. The process starts with a small spinning glass filled with liquid resin. A projector shines a loop of video onto the glass as it spins, corresponding to 2D slices of the exact final shape. The completed object solidifies the liquid resin which is inside in seconds – no layers are required.[97, 98] Now the technology has grown vigorously as well as 3D printing technology. Researchers from the Institute for Advanced Architecture of Catalonia in Barcelona, Spain, created the world's first 3D-printed concrete pedestrian bridge, which was put in a park in Alcobendas, near Madrid, in 2016. The bridge is 12 meters long and has a lattice construction created with algorithms that enhance strength with less material usage. Similar structures have been built by other teams, including a 26-meter-long bridge built by engineers at Tsinghua University in Beijing, China. In addition, 3D-printed display houses have been built by teams and corporations in China and the Netherlands.[99] Recently, Tvasta's fabricated a concrete 3D printer and demonstrated a complete house fabrication. It is anticipated that a 2000 ft2 home could be built in less than a week utilizing this technology, which is 1/8th of the time it takes to build a working house today. When it comes to waste materials, this technology generates only a third of the waste generated by typical construction methods.[100] The research group from NIT Trichy has recently developed a 3D model mimicking the bone structure (refer to Figure 6) using Resin based 3D printer (Creality) for application in the automotive industry.
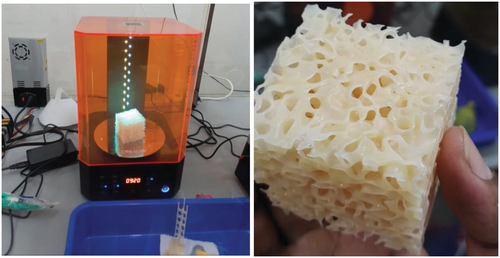
Conventional product manufacturing processes such as injection molding, compression molding, and so on are highly fit for mass manufacturing of geometrically identical objects. However, in the case of low-quantity manufacturing, material wastage increases and the process becomes extravagant.[101] All these factors imply the remarkable development of 3D printing in various sectors. Due to its ease of use, production of objects with unique geometry, portable device setup, upgraded physical and operating conditions, low material cost, capability to print versatile material, and secure manufacturing environment, FDM has become one of the most extensively used 3D printing technologies in real life and also for research.[102-104] In addition, the FDM technology has several unique favorable features in the prospect of additive manufacturing and geometric design, particularly for complex 3D structures, when compared to traditional production methods for electronic components.[105-107]
Hence, adopting new technology like 3D printing in the manufacturing of electronic components, automobile components, and so on is highly essential and this would lead to easy manufacturing, and low material wastage.
2.1 Printability of Nanocomposites
Development of new material for 3D printing is not an easy task and the engineers must consider many factors like strength, glass transition temperature (Tg), viscosity, change of these properties with temperature variation, and so on.[108] The rheological behavior of polymer-based composite materials is critical to the successful implementation of FDM 3D printing.[109] The printability of a filler-reinforced polymeric material differs from that of pure polymers. Therefore, it is mandatory to analyze the rheological properties of prepared polymer composites. Among many rheological properties, the viscosity of the material is the utmost essential characteristic when choosing the best processing parameters for FDM 3D printing. The viscosity measures the resistance to flow and offers a relationship between stress and deformation rate. A force is provided to the filament in the FDM process as it is pushed down by the driving roller, which pushes the heated filament toward the nozzle, where it would be subjected to varied shear rates. The shear rate at the printer liquefier chamber is determined by its dimensions and printing speed, and it is often very high because of the low nozzle diameter.[110, 111] Importantly, the filament utilized in FDM printing must be sufficiently rigid to withstand the force exerted by the counter-rotating rollers. When the pressure applied by the guide rollers surpasses the material's ultimate buckling stress, the filament will begin to buckle.[112] In FDM printing, filament materials must be heated above Tg and then brought back to room temperature. Tg is thus the first and most important characteristic to be measured before any 3D printing.[113] Most of the polymeric filaments used in the 3D printing process have significantly higher Tg than ambient temperature or a high enough degree of crystallinity to give the filament enough strength to avoid buckling. Flexible materials, on the other hand, are frequently amorphous and have a Tg near ambient temperature. As a result, the filament lacks adequate strength to force the melt into the nozzle, resulting in filament buckling. This issue is exacerbated in some designs, such as Bowden-type printers, where the guide rollers/gears are considerably far away from the printing head.[114]
In addition, the viscosity of the material can be greatly affected by a change in working temperature. For instance, Elhattab et al. studied the rheological behavior of β-Tricalcium phosphate (TCP) mixed PLA filament under various operating temperatures (from 190 °C to 220 °C) in FDM printing. At higher nozzle temperatures, it was noticed that the rheological characteristics improved. The pure polymer and composite melts had low viscosity and rigidity, resulting in improved polymer melt flowability and interlayer bonding between the consecutive printed layers. A good bonding between the adjacent layers leads to a considerable increase in mechanical properties such as tensile strength and modulus of elasticity (Refer to Figure 7a,b). It was revealed that the pure PLA exhibited better tensile strength in all temperature ranges than the TCP – PLA composite and this was due to the development of voids (shown in Figure 7c,d) when the TCP particles delaminated.[115]
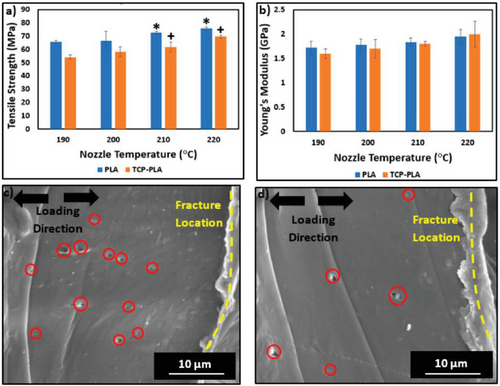
All of these factors must be taken into account when manufacturing a filament for 3D printing, and filament development is a prerequisite for performing FDM 3D printing. Many researchers have reported the twin screw extrusion technique to produce polymer composite filament, which was then used in FDM-based 3D printing.[116, 117] Figure 8 helps to understand the working principle of the twin screw extrusion technique followed by FDM printing and the various printing parameters.
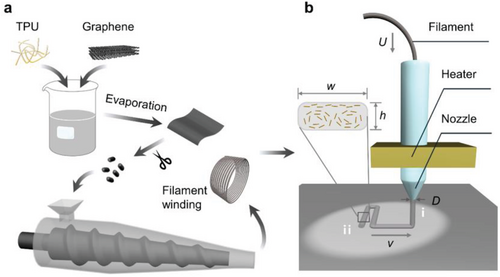
The extruded filaments should be characterized thoroughly and it is important to notice their rheological properties with respect to temperature change. For instance, Díaz-García et al. studied the variation of rheological properties under the reinforcement of different fillers. Figure 9 supports the idea that as filler content increases, rheological parameters (including apparent viscosity) decrease. Generally, as filler concentration rises, so does the flow viscosity of polymers containing fillers.[118] Nevertheless, calcium carbonate (CaCO3) in PVC[119] and glass beads in polycarbonate (PC)[120] have also been found to reduce viscosity with the inclusion of fillers, correlating with the outcomes for PLA including maraging steel particles in their study. According to these researchers, the decrease in viscosity was caused by a reduction in the contacts between layers of the molten polymer and spherical particles, or the so-called “ball-bearing” effect, which becomes more evident with an increase in filler content. This result was seen for both shear rheology at lower shear rates as well as high shear capillary viscosity.[121] Such characterization studies are important to set the input parameters of any 3D printing process.
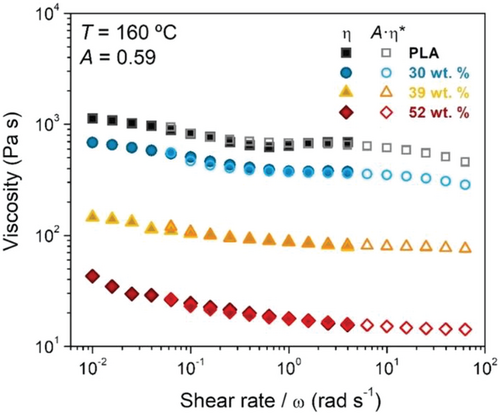
2.2 Thermal Conductivity of 3D Printed Polymer Composites
3D printing, often known as additive manufacturing, is a versatile manufacturing method for fabricating polymer and polymer-based composite goods.[122] A layer-by-layer material addition procedure can be used to create the composites.[123] Such advanced printing method was employed to create high thermal conductivity polymer composites in the recent age.[124] The filament or input material in this case has two materials: a polymer matrix and filler reinforcement, and the resulting composite material is critical in the heat removal process from electrical and electronic devices. Many studies have explored the influence of filler reinforcement in polymers on mechanical strength and thermal stability; nevertheless, their performance in heat transfer applications has lately accelerated. As a result, it is necessary to investigate the use of 3D printing in the manufacture of polymer nanocomposites with enhanced properties compared to the parent material. Fillers in the polymer matrix enhance the FDM's functional applications, such as mechanical,[125] magnetic,[126] thermal conductive,[127, 128] and electric conductive[129] characteristics. This instigated the authors to give a slight overview of 3D printing on polymer composites, and this approach has unique features (both advantageous and disadvantageous) in terms of surface quality, production quantity, the demand of postprocessing, complex geometry handling, and so on. In 2015, Gr/ABS nanocomposites were 3D printed for the first time.[130]
It is vital to compare the performance of composites created using different manufacturing procedures in order to assess the performance of 3D-printed composites. Because of their delicate structure and weak areas between the layers, 3D-printed samples have lower mechanical strength than injection molded ones.[131] Some studies, on the other hand, have found that both 3D printed and injection molded polymer composites have improved thermal conductivity. For instance, Bragaglia et al. prepared h-BN reinforced PA-6 composites using two different manufacturing methods namely compression molding and 3D printing. Because of its excellent thermal conductivity, h-BN appears to be one of the most promising functional fillers. It was found that the thermal conductivity of 25 wt.% and 45 wt.% h-BN/PA-6 compression-molded composites was 1 and 2.5 W m−1 K−1, respectively. For the same level of filler loading, the 3D printed h-BN/PA-6 composites showed the TPTC of 0.67 and 0.92 W m−1 K−1, respectively. The thermal conductivity of h-BN/PA-6 increased with respect to filler concentration in both processes. Because of the high porosity of the 3D printed samples, the compression molded samples demonstrated superior thermal conductivity. The travel of phonons in the material drives the thermal conductivity of the entire nanocomposite, and the discontinuities and interfaces in nanocomposites restrict the flow of phonons which creates a crucial problem.[132] From the above, it is clear that h-BN is a potential option to improve the thermal conductivity as well as the biocompatibility of polymeric composites.[133] It is apparent that the improvement of the thermal conductivity of polymer composites depends on the type of manufacturing method (refer to Figure 10). In a slightly different approach, Hamzah et al. used copper ferrite (CuFe2O4) in ABS matrix and showed 93% thermal conductivity enhancement compared to pure ABS.[134] Commonly, it is perceived that the crystallinity of the composites is reduced when thermally conductive filler is reinforced. This is due to the fact that when thermally conductive fillers are introduced, the resultant composites thermal conductivity increases. This increase in thermal conduction is detrimental to crystallization.[135] Furthermore, the well-dispersed fillers in the matrix may act as a physical barrier to the matrix crystals, this prevents crystallization and decreases the crystallinity of the composites with the addition of conductive fillers.[136] In addition, it is obvious that the intrinsic alignment of the thermally conductive nano-fibers (instead of nano-particles) in the printing direction can help to regulate the flow of heat through 3D printed composites. For instance, Ibrahim et al. demonstrated an increase in thermal conductivity up to ≈3 W m−1 K−1 using continuous carbon fiber reinforcement in nylon, whereas, pure nylon showed the thermal conductivity of 0.26 W m−1 K−1.[137] A unique stereolithographic (STL) 3D printing technique that incorporates magnetic alignment and vibration has been recently reported by Gurijala et al. Through their investigation, they were able to show that thermal conductivity had greatly improved.[138] Figures 10 and 11 and Table 2 show the influence of the manufacturing process (conventional vs. 3D printing) on the thermal conductivity enhancement of various polymers.
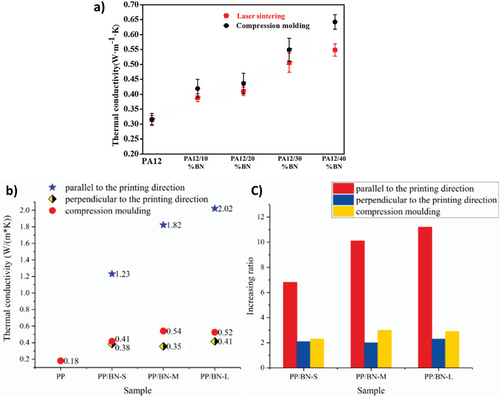
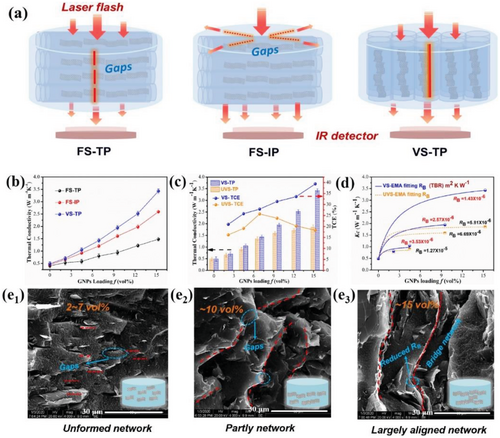
Reinforcement (s) | Matrix | The concentration of reinforcement* | Thermal conductivity (W m−1 K−1) | Ref. | ||
---|---|---|---|---|---|---|
Matrix | 3D printed composite | Conventional manufactured composite | ||||
h-BN | PA-6 | 45 wt.% (TPTC) | 0.29 | 0.92 (FDM) | 2.5 (CM) | [132] |
45 wt.% (IPTC) | 0.28 | 1.52 (FDM) | 2.4 (CM) | |||
BN | PA12 | 40 wt.% | — | 0.55 (SLS) | ≈0.65 (CM) | [139] |
CF and Al2O3 | silicon rubber | 12 vol.% CFs and 30 vol.% Al2O3 | 0.15 | 7.36 | 4.22 | [140] |
Gr flakes | PA6/POE-g-MAH/PS blend | 50 wt.% | — | 5.5 (SP) | 2.4 (IM) | [71] |
GrNP | LLDPE | 15 vol.% (VS-TP) | 0.4 | 3.43 (SSSM+FDM) | 1.98 (MC) | [141] |
Gr | TPU | 45 wt.% (TPTC) | 0.25 | 12 (FDM) | — | [117] |
BN | PA6 | 30 vol.% (TPTC) | — | 2 (FDM) | 1.1 (IM) | [142] |
Microdiamonds | ABS | 60 wt.% | 0.17 | 0.94 (FDM) | — | [143] |
Cu | ABS | 50 wt.% | 0.6 | 0.9 (FDM) | — | [144] |
Gr | PLA | 12 wt.% | ≈0.2 | ≈1 (FDM) | — | [145] |
h-BN | TPU | 40 wt.% | — | 2.56 (FDM) | — | [146] |
BN | PCL | 50 wt.% | 0.23 | 2.46 (FDM) | — | [147] |
AlN | 70 wt.% | 1.54 (FDM) | — | |||
BN | PLGA | 63.2 wt.% | — | 2.1 (DIW) | — | [148] |
Carbon+Graphite | Epoxy | 7.6 + 9.3 wt.% | 0.2 | ≈2 (DIW) | — | [149] |
BN | PDMS | 21 wt.% (TPTC) | 0.18 | 1.5 (DIW) | — | [150] |
h-BN – Ag | Epoxy | 20 wt.% (TPTC) | 0.23 | 2.5 (DIW) | — | [151] |
- Note: CM: Compression moulding; TPTC: through-plane thermal conductivity; IPTC: In-plane thermal conductivity; SLS: Selective laser sintering; POE-g-MAH: Maleic anhydride grafted poly (ethylene 1-octene) (POE-g-MAH); PS: Polystyrene; SP: Stand-3D printing; FP: Flat-3D printing; VS-TP: Vertical 3D printed sample – through plane; SSSM: Solid-state shear milling; IM: Injection Moulding; MC: Melt-compounded; TPU: Thermoplastic polyurethane; PCL: Polycaprolactone; DIW: Direct Ink Writing; Ag: Silver;
Over the decade, significant contributions have been made by the research community for obtaining high thermal conductivity polymer composites through 3D printing. However, more attention needs to be paid for acquiring improved thermal conductivity using low filler concentration (below 30 wt.%) because at higher filler concentration the mechanical properties start to diminish.[9]
3 Conclusions
- High thermal conductivity polymer nanocomposites have a strong role in microelectronics applications, which improves the heat dissipation traits. The most important parameter to obtain such nanocomposite is the formation of a conduction network by employing appropriate reinforcements.
- In general, high thermally conductive and electrically insulative ceramic particles were randomly scattered in polymer matrices. Thermal conductivities in ceramic-filled polymers have thus far been restricted as most of the studies reported that the thermal conductivity of the composites is well below 3 W m−1 K−1. This was predominantly attributed to huge phonon scattering in the polymer matrix and great conduction resistance at the matrix-filler interfaces.
- The production of high thermal conductivity polymer composites (more than 10 W m−1 K−1) through facile manufacturing needs to be implemented to enable higher power densities in electronic devices.
- In another way, the 3D printing technique is found to be helpful in developing high thermal conductivity polymer composites by establishing a strong property flow network. But still, the fillers used in many studies were as-received h-BN or rGO. This would suggest the research community look for appropriate filler materials that could be helpful in developing a good thermal conductivity network through 3D printing.
- The usage of iron oxide-coated particles could combine the benefits of magnetic particle alignment and 3D printing. This will be very much helpful in the technological advancement of the electronic sector.
- Although many research articles reported the development of high thermal conductivity polymer composites in many ways,no studies were found on the recycling of materials or usage of waste materials as reinforcement.
- It is recommended that suitable advanced manufacturing techniques are to be identified and employed for material recycling.
Conflict of Interest
The authors declare no conflict of interest.
Biographies
T. R. Vijaybabu is currently working as an associate professor in the Department of Mechanical Engineering, GMR Institute of Technology, Rajam, India. He conducted his doctoral research on the hydro-thermal behavior of various porous bodies under the influence of the magnetic field, buoyancy force, and nanofluid through the lattice Boltzmann method, at the Indian Institute of Technology, Indore. He has also studied the nanofluid's local variation of thermal conductivity on the flow, thermal and concentration outcomes in and around the porous medium. He is currently working on the double-diffusive, MHD, and EHD phenomena to realise the scope of thermal dissipation control and enhancement for the porous medium with different thermal conductivity ratios.
T. Ramesh is currently working as an associate professor in the Department of Mechanical Engineering, National Institute of Technology, Tiruchirappalli, Tamilnadu, India. He has published in more than 40 renowned international journals and presented his research works at international conferences. His research areas are polymer composites, MEMS, biomaterials and biomechanics.
Suman Pandipati is working as an assistant professor in the Department of Mechanical Engineering at Aditya Institute of Technology and Management, Tekkali, Srikakulam, Andhra Pradesh, India. He completed his M.Tech in mechanical engineering with a specialisation in design and manufacturing and he has 12 years of teaching experience. He has published papers in various fields such as composites, welding and integration of CAD/CAM. Currently, he is doing a Ph.D. at Centurion University.
Sujit Mishra presently serves as an assistant professor and head of the Mechanical Engineering Department, SoET, at Centurion University of Technology and Management, Paralakhemundi campus. He obtained his Ph.D. from Centurion University of Technology and Management, and his M.Tech. and B.Tech. at the Biju Patnaik University of Technology, Odisha. He has ten years of teaching experience with subject interests such as machine design, fluid mechanics, computational fluid dynamics, computer-aided drafting, computer-aided manufacturing, and computer-aided engineering at both undergraduate and postgraduate levels. His research areas include the influence of dust particles in predicting aerodynamic parameters for simplified cars using the computational fluid dynamics approach. He also keeps interested in providing technical simulation solutions for various industrial problems. He has published in more than 11 international journals, two book chapters, and one book. He is also a part of an active Life Member of the Indian Society of Technical Education (ISTE).
G. Sridevi is an assistant professor at the Department of Mechanical Engineering, at Centurion University, Odisha, India. She completed her M.Tech. in mechanical engineering with a specialization in design and manufacturing and has nine years of industrial experience in EPC bulk material handling turnkey projects and over eight years of experience in teaching. Currently, she is perusing her Ph.D. at Centurion University. Her research interests are composite materials, nano-technology and advanced manufacturing processes.
C Pradeep Raja is a research scholar in the Department of Mechanical Engineering at the National Institute of Technology Tiruchirappalli. He obtained his master's degree from Anna University Chennai and a graduate degree from Vels University Chennai. Currently, He is pursuing a Ph.D. in the Department of Mechanical Engineering at the National Institute of Technology, Tiruchirappalli and has published his research works in over three international journals.
Rhoda Afriyie Mensah is currently a postdoc at the Structural and Fire Engineering division of Luleå University of Technology. Rhoda is supervised by Oisik Das, and her research involves sustainable carbon materials, flammability analyses, building fire-safety, and artificial intelligence predictive modelling. Rhoda got her Ph.D. degree from Nanjing University of Science and Technology in 2020.
Oisik Das is currently a senior lecturer and associate professor at the Department of Civil and Natural Resources Engineering in Luleå University of Technology in Sweden. Additionally, he is the international coordinator for the aforementioned department. With the help of a prestigious Auckland University doctoral scholarship, Dr. Das received his Ph.D. from the University of Auckland in New Zealand, in 2017, and received the Dean's list award for excellence for his Ph.D. thesis. He received the e8 Sustainable Energy Development Scholarship, awarded to only seven students worldwide in 2007–2008, which helped him to get his M.S. in engineering from the Washington State University in the USA. The overarching topic of Dr. Das's research is on sustainable materials/structures, with specialisation on polymeric composites, fire, and biochar. He has authored more than 100 peer-reviewed articles, nine book chapters, one academic textbook and has one WIPO patent. He is currently the associate editor of Sustainable Process Engineering.
Manjusri Misra is a professor and Tier 1 Canada Research Chair (CRC) in sustainable biocomposites in the School of Engineering and holds a joint appointment in the Department of Plant Agriculture at the University of Guelph. She is also the research program director of the Bioeconomy Panel for the Ontario Agri-Food Innovation Alliance, a program between the Ontario Ministry of Agriculture and Rural Affairs (OMAFRA) and the University of Guelph. Dr. Misra completed her bachelor's, master's, M.Phil. and Ph.D. from Ravenshaw College (currently Ravenshaw University) at Utkal University in India focusing in chemistry with a specialization in polymer chemistry and natural fibers. Dr. Misra's current research focuses primarily on novel bio-based composites and nanocomposites from agricultural, forestry and recycled resources for the sustainable bioeconomy moving toward the circular economy. She has authored more than 800 publications, including 445 peer-reviewed journal papers, 25 book chapters, and 55 patents. She was the editor or co-editor of six books in the area of biocomposites and nano-composites.
Amar Mohanty is a Distinguished Research Chair in sustainable biomaterials at the Ontario Agriculture College and the director of the Bioproducts Discovery and Development Centre. He is a professor both in the Department of Plant Agriculture and School of Engineering at the University of Guelph, Canada. He is a former Michigan State University professor and currently holds an adjunct professor position at the State University of New York, Syracuse, in the USA; a distinguished professor position at the Indian Institute of Technology Guwahati, Guwahati, in India; and a visiting professor status at the University of Portsmouth, in the UK. Dr. Mohanty is the Editor-in-Chief of Sustainable Composites at Composites Part C. He is one of the most cited researchers worldwide with more than 850 publications to his credit, including 457 peer-reviewed journal papers, 71 patents (awarded/applied), six edited books, 25 book chapters, 300+ conference papers and over 150 plenary and keynote presentations.
Karthik Babu NB is an assistant professor at the Department of Mechanical Engineering, Assam Energy Institute, A centre of RGIPT, Sivasagar, Assam, India. He pursued his Ph.D. at the National Institute of Technology, Tiruchirappalli in the year 2021. His research interests are polymer composites, biocomposites, characterisations of polymers, and additive manufacturing. He has authored in over 20 international journals and over five book chapters.