Experimental study on mechanical behavior of bolted steel-neosinocalamus affinis-based bamboo scrimber and steel connections
Abstract
Bamboo materials are known for their excellent toughness and seismic performance, which makes them a promising option for advancing their application in the field of structural engineering to enhance the seismic resilience of engineering structures. This study focused on mechanical behavior of bolted steel-neosinocalamus affinis-based bamboo scrimber and steel connections, and conducted shear test research and analysis on 54 specimens divided into 18 groups, aiming to promote the application of bamboo scrimber in the field of structural engineering. The study indicates that connections with thin steel plates (t = 0.5d, t = 1d) predominantly exhibit a single-hinge yield mode, while those with thick steel plates (t = 2d) are inclined towards a double-hinged yield mode. The yield and ultimate load-carrying capacities of a connection are enhanced with the increase in bolt diameter. However, the influence of the steel plate's strength grade on these capacities is minimal. The yield load-carrying capacity of connections with thick steel plates has a significant increase compared with the connection with thin steel plates. The thickness of the steel plate does not significantly affect the connection ultimate load-carrying capacity. The initial stiffness of a connection is positively correlated with the bolt diameter, yet it remains unaffected by variations in the steel plate's thickness. The stiffness of a connection is categorized into two distinct types based on the steel plate strength grade. Connections using steel plates with a strength grade above Q235 exhibit similar stiffness levels, which are consistently higher than those using Q235-grade steel plates. The angle between the load direction and the grain direction has an effect on the connection ductility. The ductility coefficient across various connections predominantly centers around 2.5. The research also validates that the Foschi theoretical model, traditionally applied to wood structures with bolted, nailed, and similar dowel-type connections, accurately delineates the nonlinear load–displacement behavior of bolted steel–bamboo scrimber and steel connections for the entire duration of the process. When comparing the same configurations, connections utilizing neosinocalamus affinis-based bamboo scrimber demonstrate a higher load-carrying capacity than those using phyllostachys pubescens-based bamboo scrimber, with a maximum enhancement in load-carrying capacity of 18%. The design carrying capacity meets the test load requirements for the given end distances of 7d. This research can provide theoretical support for the engineering application of neosinocalamus affinis-based bamboo scrimber.
1 INTRODUCTION
In recent years, the reinforced concrete, as a major construction material,1, 2 has resulted in significant carbon emissions. The increasing global demand for resources and the pursuit of sustainable development have made ecofriendly building materials a pivotal trend in construction. Bamboo products offer significant ecological benefits and sustainability, due to their rapid growth, diverse applications, and notable mechanical strengths. Bamboo scrimber, a composite material, overcomes uneven size and limited durability in natural bamboo, having the advantages of customizable section, stable mechanical properties, and simple and efficient connection.3 Recent studies have extensively explored the fundamental physical and mechanical properties,4, 5 resistance to high temperatures,6-8 and creep characteristics9 of bamboo scrimber. Bamboo scrimber, derived from neosinocalamus affinis and phyllostachys pubescens, shows varied mechanical strengths. Tensile strengths are 248.15 and 144.75 MPa, while compressive strengths are 129.17 and 115.7 MPa, respectively.10 The result demonstrates neosinocalamus affinis-based scrimber superior mechanical performance over phyllostachys pubescens-based scrimber.
Bolted connections, due to simplicity, convenience, and reliability, have become a common method for structural components in the construction process, which can also be adopted in Chinese bamboo scrimber standards.11, 12 Recent researches13-15 conducted experiments on bolted connections with the phyllostachys pubescens-based bamboo scrimber and steel. The study focused on optimizing construction parameters for bamboo scrimber and steel bolted connections, evaluating the relevance of wood structure design standards like GB5000516 to bamboo constructions. The results revealed that current wood structure design standards do not accurately predict the load-carrying capacity of bolted steel–bamboo scrimber and steel connections. Zhou et al.17 and Wang18 conducted experimental analyses on the performance of bolted connections with the phyllostachys pubescens-based bamboo scrimber and glue-laminated bamboo with steel fill plates. The results revealed significant errors that the calculation error can reach more than 200% in the wood standard like national design specification for wood construction in predictions of the load-carrying capacity of engineered bamboo–steel fill plate-bolted connections. Li et al.19 studied the force performance of beam-column bolted connection of glued bamboo structures, and gave the design method of this type of connection. Research on the bolted connections of bamboo scrimber structures primarily focuses on exploring optimal construction parameters and evaluating the applicability of existing wood standards. However, studies are mainly conducted on the phyllostachys pubescens-based bamboo scrimber, with few study on the failure modes and mechanical properties of neosinocalamus affinis-based bamboo scrimber. Despite similar density and connections, neosinocalamus affinis scrimber shows better mechanical properties and holds great engineering potential.20 Thus, investigating the mechanical performance of connections in neosinocalamus affinis-based scrimber structures is crucial.
It is clearly stipulated that in the design of bamboo structures in earthquake zones, special attention should be paid to the design of connections between members, according to the Standard for the design of engineered bamboo structures.21 For the structure as a whole, the mechanical properties of the connection affect its seismic performance, such as strength, stiffness, and ductility.22 Therefore, in this paper, uniaxial compression test studies were conducted for a total of 54 specimens, analyzing the influence of steel strength and thickness, bolt diameter, and the angle between load direction and bamboo grain on failure modes and mechanical properties. It is of great significance for assessing the critical parameters and local response of bolted steel–bamboo scrimber and steel connection in seismic design, and provides a basis for further optimizing the design of the seismic performance of the structure.
2 EXPERIMENTAL INVESTIGATIONS OF CONNECTIONS
2.1 Materials
The bamboo scrimber was conducted by Sichuan Hongya Bamboo Era Technology Co., Ltd. The main production process of bamboo scrimber mainly includes bamboo tube splitting, bamboo slice thinning, preglue drying, glue impregnation, postglue drying, laying, and hot press molding. Bamboo scrimber was made by the hot-pressing process, with a moisture content of 8.9% and a density of 1.14 g/cm3. According to Test methods for physical and mechanical properties of small clear wood specimens23 and ASTM D143,24 the mechanical properties of the specific bamboo scrimber are shown in Table 1.25 The embedment strength26 and stiffness of bamboo with bolt diameters of 12, 16, and 20 mm were measured by 57 specimens and listed in Table 2. The steel plates are processed from Q235, Q345, #45, and Q390 grade steel materials, concluding five thickness specifications of 6, 8, 10, 12, and 24 mm. Bolts are made of #45 steel with a strength grade of 8.8, with three diameter specifications of 12, 16, and 20 mm. A #45 steel plate is a high-quality carbon structural steel used in the fields of machine building and engineering structures in China. The mechanical properties of the steel are given in Table 3, according to GB50017.27 The steel plates, bolts, and bamboo scrimber were machined to factory.
Compression strength (MPa) | Tensile strength (MPa) | Elastic modulus (GPa) | Bending strength (MPa) | Parallel grain shear strength (MPa) | Cross-grain shear strength (MPa) | ||
---|---|---|---|---|---|---|---|
L | R | T | 223.5 | 30.1 | 217.4 | 13.3 | 30.4 |
101.5 | 43.1 | 34.3 |
- Note: L represents the direction parallel to the grain, T represents the direction perpendicular to the grain, and R represents the perpendicular to the grain radial direction.
Direction | d (mm) | (kN/mm) | (MPa) |
---|---|---|---|
Parallel to the grain | 12 | 103.5 (2.5%) | 119.6 (2.4%) |
16 | 103.5 (4.1%) | 107.0 (5.3%) | |
20 | 111.4 (2.2%) | 95.7 (7.0%) | |
Perpendicular to the grain | 12 | 39.7 (4.5%) | 96.3 (2.7%) |
16 | 42.2 (8.7%) | 93.1 (6.8%) | |
20 | 46.5 (5.3%) | 85.4 (9.7%) |
- Note: d represents bolt diameter; is the average embedment stiffness of the bamboo scrimber; is the average embedment strength of the bamboo scrimber, with the coefficient of variation (COV) for both stiffness and strength indicated in parentheses.
Items | fy (MPa) | fu (MPa) | E (MPa) | ν |
---|---|---|---|---|
Q235 | 235 | 370 | 2.06 × 106 | 0.3 |
Q345 | 345 | 470 | ||
#45 | 355 | 600 | ||
Q390 | 390 | 490 | ||
Grade 8.8 bolts | 640 | 800 |
- Note: fy is the yield strength, fu is the tensile strength, E is the elastic modulus, and ν is Poisson's ratio.
2.2 Bolted connection design
The tests on bolted steel–bamboo scrimber and steel connections were designed with 18 groups based on variations in bolt diameter, steel plate thickness, steel plate strength grade, and the angle between the load and bamboo grain, totaling 54 specimens with three per group, as shown in Table 428. The distances at the loading end, nonloading end, and edge distance were set to 7d, 4d, and 60 mm, respectively, according to Eurocode 5,29 while the distances at the loading and nonloading ends of the steel plate complied with the Standard for design of steel structures GB50017.27 In accordance with Standard for design of steel structures GB50017,27 the diameter of the holes for ordinary bolts is 1.0–1.5 mm larger than the nominal diameter of the bolts. The predrilled holes were 1.5 mm larger than the bolt diameter. To prevent shear failure at the transition between the bolt's threaded and smooth sections, all bolts were made 10 mm longer than the combined thickness of the bamboo scrimber and steel plate, as illustrated in Figure 1. Since the performance of bolted steel–bamboo scrimber and steel connections primarily depends on bolt bending and embedment strength resistance to external loads, the effect of axial bolt load on connection performance is negligible. This experiment did not consider the impact of bolt pretension.
Items | G | d (mm) | t (mm) | α (°) | Number |
---|---|---|---|---|---|
SL235-12-0.5d | Q235 | 12 | 0.5d | 0 | 3 |
SL235-12-1d | 12 | 1d | 0 | 3 | |
SL235-12-2d | 12 | 2d | 0 | 3 | |
XL235-12-0.5d | 12 | 0.5d | 45 | 3 | |
HL235-12-0.5d | 12 | 0.5d | 90 | 3 | |
SL235-16-0.5d | 16 | 0.5d | 0 | 3 | |
HL235-16-0.5d | 16 | 0.5d | 90 | 3 | |
SL235-20-0.5d | 20 | 0.5d | 0 | 3 | |
HL235-20-0.5d | 20 | 0.5d | 90 | 3 | |
SL345-12-0.5d | Q345 | 12 | 0.5d | 0 | 3 |
SL345-12-1d | 12 | 1d | 0 | 3 | |
SL345-12-2d | 12 | 2d | 0 | 3 | |
SL45-12-0.5d | #45 | 12 | 0.5d | 0 | 3 |
SL45-12-1d | 12 | 1d | 0 | 3 | |
SL45-12-2d | 12 | 2d | 0 | 3 | |
SL390-12-0.5d | Q390 | 12 | 0.5d | 0 | 3 |
SL390-12-1d | 12 | 1d | 0 | 3 | |
SL390-12-2d | 12 | 2d | 0 | 3 |
- Note: SL, XL, and HL denote the direction of load relative to the bamboo grain as parallel, at a 45° angle, and perpendicular, respectively. The numbers following these letters represent the steel plate strength grade G, bolt diameter d, and steel plate thickness t. The angle α indicates the load direction relative to the bamboo grain, with α = 0° for specimens loaded parallel to the grain and α = 90° for those loaded perpendicular to the grain. For example, connection SL235-12-1d signifies a connection made with a Q235 steel plate one bolt diameter thick, a 12-mm diameter bolt, and the load applied parallel to the direction of the bamboo grain.
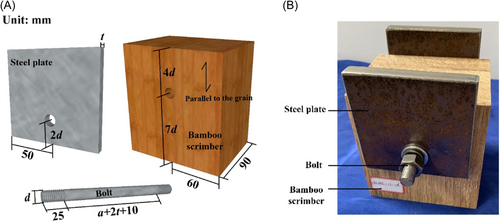
2.3 Experimental methods and setup
The experiment was conducted in the Structural Engineering Laboratory of Southwest Jiaotong University, using an E-type microcomputer-controlled electronic universal testing machine produced by Shenzhen Wan Test Equipment Co., Ltd., capable of providing a maximum test load of 300 kN. Load data during the experiment were collected by the testing machine force sensor, while displacement data were captured using a dial gauge with a range of 30 mm and an accuracy of 0.01 mm. According to ASTM D565230, a uniform load was applied to the specimens at a loading speed of 1 mm/min. The loading was halted when the specimens exhibited significant damage, displacement exceeded 15 mm, or the load dropped to 80% of the peak load. The setup30, 31 of the loading and measuring devices is shown in Figure 2.
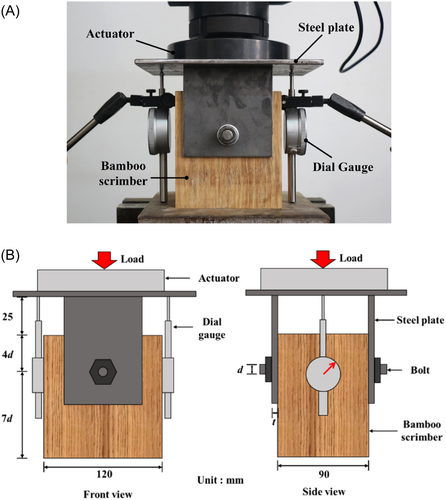
3 TEST RESULTS AND DISCUSSION
3.1 Test phenomena and damage patterns
3.1.1 Test phenomena
In the initial phase of loading, the displacement of all specimens gradually increased with the load, and nearly all specimens showed no significant damage before reaching a load of 100 kN, with only bending observed at the bolt ends. As the load exceeded 100 kN, connections with 12 mm diameter bolts began to show varying degrees of damage, especially those where the load direction was parallel to the grain, as shown in Figure 3. In these connections, bamboo scrimber components commonly experienced sudden cracking at the nonloading end towards the end of loading, with cracks rapidly progressing from the nonloading end towards the loading end. This phenomenon is attributed to the larger loading end distance and higher horizontal frictional forces at the bottom, making it difficult for cracks to initiate from the bottom of the loading end. The smaller nonloading end distance and the bending of the bolts exerting pressure on the upper part of the bamboo dowel slots made the nonloading end more susceptible to cracking.28
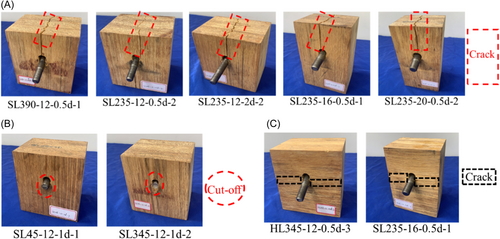
For connections with bolt diameters of 16 and 20 mm, the failure characteristics were almost identical to those with a 12-mm bolt diameter, with the only difference being the increased load-carrying capacity due to the larger bolt diameter.28 Unlike connections where the load direction was parallel to the grain direction, bamboo scrimber specimens with load directions perpendicular to the grain direction did not exhibit end cracking. During the entire loading process, only bolt bending was observed. After loading, the bamboo scrimber components showed cracks perpendicular to the load direction on both sides of the predrilled holes, along the width of the specimen, as illustrated in Figure 3B. In addition to these failure modes, approximately 9% of the specimens with load direction parallel to the grain direction failed due to bolt shear fracture, as shown in Figure 3C.
3.1.2 Failure mode
Johansen32 summarized the failure modes of common timber bolted connections, identifying three for double shear connections with steel plates. For thin main members, failure occurs through carrying at the dowel holes (Yield Mode I); With thin steel plates (t ≤ 0.5d), as the thickness of the main member increases, the failure shifts to local carrying and bolt bending (Yield Mode III); For thick steel plates (t > 1d) with substantial main member thickness, failure is through local carrying and bolt bending (Yield Mode IV), as depicted for Figure 4. Modes III and IV both involve local carrying and bolt bending, but Mode III shows a single hinge at each shear plane, whereas Mode IV exhibits a double-hinge.
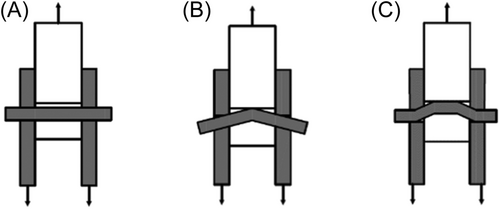
The results demonstrate that for thick steel plates (t = 2d) in bolted steel-based bamboo scrimber and steel connections, a double-hinge failure mode near each shear plane alongside the local carrying yield of the bamboo indicates Yield Mode IV, as shown in Figure 5. In contrast, connections with relatively thinner steel plates (0.5d–1d) exhibited a single hinge and local carrying yield. This aligns with Johansen findings32 in timber structures, though distinctions in steel plate thickness between Yield Modes III and IV differ. Specifically, a steel plate thickness of 1d does not mark the boundary between thin and thick plates, suggesting a critical point between 1d and 2d. Despite adherence to Eurocode 5 design requirements for end, spacing, and edge distances, all connections avoided failure in Yield Mode I, with no definitive preyield deformation in steel plates observed before bolt deformation. Previous studies and literature also confirm that connections meeting the thickness requirements of GB50005 and Eurocode 5 (a ≥ 4d) fail in Mode III or IV, not Mode I. This indicates that, under certain construction standards, bolted steel-based bamboo scrimber and steel connections effectively utilize the mechanical properties of their components, particularly the bending capacity of bolts.
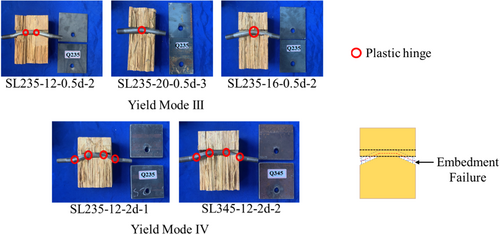
The steel plate, which plays a crucial role in the connection under load, exhibits varying degrees of local deformation depending on its different strength levels as depicted in Figure 6. Q235 steel plates experienced the most significant deformation at predrilled holes after loading. The deformation of predrilled holes in Q235 was approximately 1 mm greater than that in the other three grades, indicating steel plate strength grade significantly impacts connection performance28.
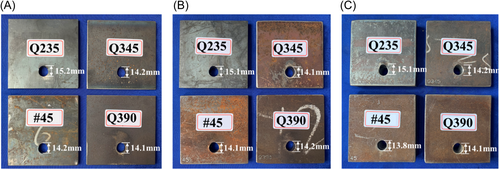
3.2 Analysis of mechanical properties of connections
3.2.1 Load–displacement curves
The load–displacement curves for most bolted steel-based bamboo scrimber and steel connections follow three stages: elastic, elastoplastic, and failure, as demonstrated in Figure 7A. In the elastic stage, the bolt initially deforms and bends under shear forces, tightly integrating with the predrilled holes of bamboo scrimber. As the load increases, the connections enter the yield stage, where bolts begin to yield and compress the holes until a plastic hinge forms. From 0 to 4 min, the deformation rate per minute is relatively minor, but from 5 to 9 min, the deformation per minute becomes significant, indicating a transition from elastic to elastoplastic behavior, resulting in stiffness changes during loading, as shown in Figure 7B.
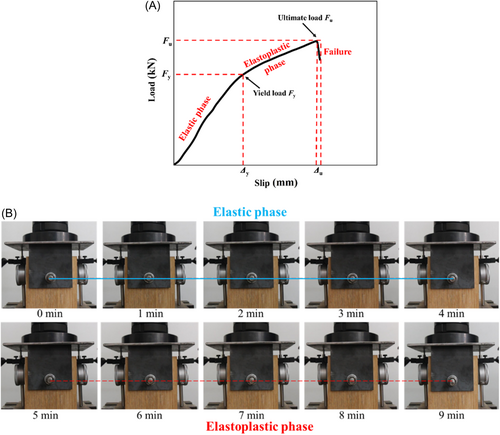
The load–displacement curves for different test groups are shown in Figure 8. The results reveal that connections with identical steel plate strength grades, bolt diameters, and load directions parallel to the grain direction of bamboo scrimber exhibit highly similar behaviors up to their ultimate load-carrying capacity28. This similarity indicates that these factors significantly influence the mechanical performance of the connections, showcasing consistent response patterns under load until reaching their peak strength.
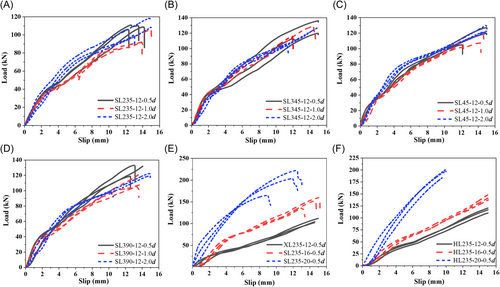
3.2.2 Load-carrying capacity
On the basis of the load–displacement curves of the bolted steel-based bamboo scrimber and steel connections, it is possible to calculate the average values for initial stiffness K0, yield load Fy, ultimate load capacity Fu, yield displacement ∆y, ultimate displacement ∆u, and ductility coefficient D for each group of connections.
The initial stiffness K0 is calculated using the formula K0 = (0.4Fu − 0.1Fu)/(∆0.4 − ∆0.1) according to EN 12512.33 The yield load Fy is determined by the 5% bolt diameter offset method recommended by ASTM D5652. The ultimate load Fu corresponds to the peak load on the load–displacement curve. Yield displacement ∆y is the displacement at the yield load, and ultimate displacement ∆u is the displacement at the ultimate load. The ductility coefficient D is calculated as D = ∆u/∆y. The methodology for determining these parameters is illustrated Figure 9. The load-carrying capacity performance results of the bolted steel-based bamboo scrimber and steel connections are shown in Table 5.28
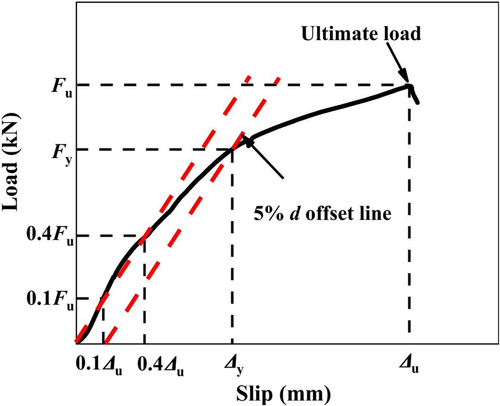
Items | Yield | K0 (kN/mm) | Fy (kN) | ∆y | Fu (kN) | ∆u | D |
---|---|---|---|---|---|---|---|
SL235-12-0.5d | III | 16.51 (7.1%) | 44.3 (1.7%) | 5.21 (4.6%) | 101.53 (4.9%) | 12.73 (12.9%) | 2.45 |
SL235-12-1d | III | 16.21 (2.8%) | 44.91 (3.1%) | 4.85 (6.7%) | 95.71 (6.2%) | 14.56 (2.3%) | 3.00 |
SL235-12-2d | IV | 14.71 (10.4%) | 66.08 (2.7%) | 5.28 (9.9%) | 108.81 (6.8%) | 14.32 (6.7%) | 2.71 |
XL235-12-0.5d | III | 12.53 (5.9%) | 50.19 (2.2%) | 6.50 (4.4%) | 105.67 (4.4%) | 15.00 (0.0%) | 2.31 |
HL235-12-0.5d | III | 10.22 (12.3%) | 57.91 (5.6%) | 7.34 (5.2%) | 115.76 (3.6%) | 15.00 (0.0%) | 2.04 |
SL235-16-0.5d | III | 23.35 (1.4%) | 74.51 (1.7%) | 5.28 (3.5%) | 149.24 (6.9%) | 14.25 (5.3%) | 2.70 |
HL235-16-0.5d | III | 15.11 (3.8%) | 70.86 (3.8%) | 6.89 (6.4%) | 142.21 (3.1%) | 15.00 (0.0%) | 2.18 |
SL235-20-0.5d | III | 31.12 (7.4%) | 137.97 (17.8%) | 5.25 (14.5%) | 196.46 (12.1%) | 11.11 (14.4%)) | 2.12 |
HL235-20-0.5d | III | 20.15 (5.1%) | 145.16 (2.3%) | 6.52 (6.2%) | 194.24 (3.9%) | 10.00 (0.0%) | 1.53 |
SL345-12-0.5d | III | 30.15 (3.2%) | 52.53 (5.5%) | 4.25 (9.6.%) | 122.25 (8.3%) | 14.07 (9.4.%) | 3.31 |
SL345-12-1d | III | 26.17 (3.7%) | 58.53 (13.5%) | 4.37 (25.8%) | 107.40 (19.4%) | 10.75 (32.7%) | 2.46 |
SL345-12-2d | IV | 27.37 (2.8%) | 74.42 (3.6%) | 5.47 (7.1%) | 117.73 (7.5%) | 13.45 (11.7%) | 2.46 |
SL45-12-0.5d | III | 27.86 (3.9%) | 54.72 (5.7%) | 4.72 (5.6%) | 116.55 (7.5%) | 14.00 (10.1%) | 2.97 |
SL45-12-1d | III | 27.21 (4.3%) | 54.48 (2.6%) | 4.29 (6.6%) | 111.91 (5.1%) | 13.69 (8.0%) | 3.19 |
SL45-12-2d | IV | 28.61 (7.1%) | 77.13 (3.2%) | 4.96 (6.5%) | 124.47 (2.6%) | 15.00 (0.0%) | 3.02 |
SL390-12-0.5d | III | 30.45 (2.5%) | 55.29 (6.7%) | 3.68 (9.7%) | 127.73 (5.0%) | 13.22 (4.5%) | 3.59 |
SL390-12-1d | III | 28.47 (3.2%) | 54.40 (11.9%) | 4.26 (12.2%) | 112.01 (6.6%) | 13.73 (1.6%) | 3.23 |
SL390-12-2d | IV | 28.63 (3.8%) | 69.54 (8.7%) | 4.77 (14.6%) | 112.93 (9.4%) | 13.43 (16.6%) | 2.82 |
Yield carrying capacity
The comparison of yield loads for bolted steel-based bamboo scrimber and steel connections is shown in Figure 10A. It indicates an increasing trend in yield load with bolt diameter, aligning with findings by Xiazhen et al.13 and Zhaoyan et al.14 on phyllostachys pubescens-based bamboo scrimber. The yield load Fy for connections with the load direction parallel to the grain direction increases from 44.3 to 138 kN as the bolt diameter increases from 12 to 20 mm, and for connections with the load direction perpendicular to the grain direction, Fy increases from 57.9 to 145.2 kN, with increments of 93.7 and 87.3 kN, respectively. The yield load for connections with a bolt diameter of 20 mm is approximately three times that of connections with a 12-mm diameter bolt. Under similar conditions, the yield loads for connections with the load direction parallel, at a 45° angle, and perpendicular to the grain direction are very close to each other. This analysis suggests that the angle between the load direction and grain direction has a minor effect on the yield load, while bolt diameter significantly influences it.
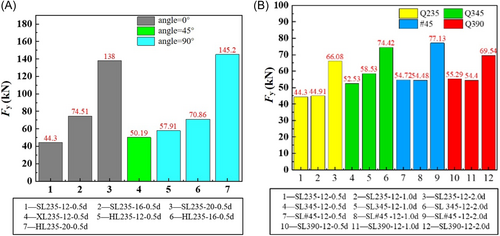
Further analysis with Figure 10B comparing yield loads across different steel material strength grades and steel plate thicknesses under the same bolt diameter shows that the difference in yield strength becomes negligible for steel material strength grades above Q235. For the same strength grade, connections with steel plate thicknesses of 0.5d and 1d exhibit nearly identical yield loads. However, as the steel plate thickness increases to 2d, the yield load increases by approximately 20 kN or 50% compared with connections with thicknesses of 0.5d and 1d.
In summary, for bolted steel-based bamboo scrimber and steel connections with a rational design, there is a positive correlation between the yield load and bolt diameter, while the load direction has no significant effect. Beyond a steel plate strength grade of Q235, the impact of this factor on the yield load becomes negligible. However, it is important to note that using thicker steel plates significantly increases the yield load of the connection.
Ultimate carrying capacity
Figure 11 shows the comparison of the ultimate carrying capacity of bolted steel-based bamboo scrimber and steel connections under different parameters. These findings indicate that the diameter of the bolts influences the ultimate load capacity in a manner similar to its effect on yield load. As the bolt diameter increases from 12 to 20 mm, the ultimate load capacity Fu for connections with the load direction parallel to the grain direction increases from 100.5 to 196.5 kN, and for connections with the load direction perpendicular to the grain direction, Fu increases from 115.8 to 194.2 kN. Under the same conditions, the ultimate load capacities for connections with the load direction parallel, at a 45° angle, and perpendicular to the grain direction are nearly identical.
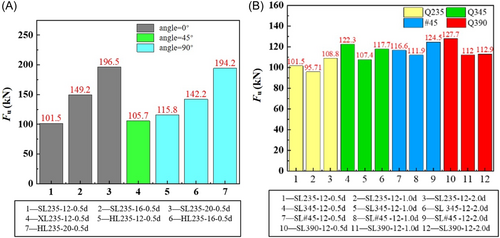
It was found that, given other conditions are the same, the ultimate load capacities for connections with four different steel material strength grades are almost equal, with the average ultimate load fluctuating between 95 and 130 kN. Additionally, the thickness of the steel plate has a minor impact on the connection's load-carrying capacity.
Initial stiffness
The comparison of initial stiffness for bolted steel-based bamboo scrimber and steel connections with different configurations, as depicted in Figure 12. The results show that the initial stiffness increases with the bolt diameter. Specifically, as the bolt diameter increases from 12 to 20 mm, the initial stiffness K0 for connections under both loading directions increases from 16.5 to 31.1 kN/mm and from 13.2 to 20.2 kN/mm, respectively. Notably, connections with the load direction parallel to the grain direction exhibit higher initial stiffness values.
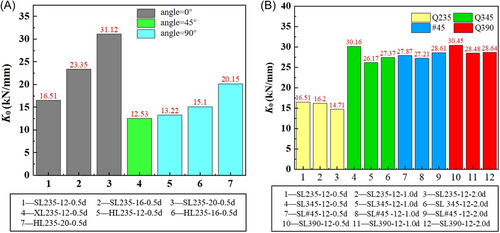
Additionally, the impact of steel material strength grade on the initial stiffness of connections is significant.28 When using steel plates with a grade of Q235, the initial stiffness of the connection ranges from 14.7 to 16.51 kN/mm. However, for steel grades from Q345 to Q390, the initial stiffness noticeably increases to a range of 26.17–30.45 kN/mm. It is also observed that within the same steel material strength grade, changes in steel plate thickness do not significantly affect the initial stiffness28.
Ductility ratio
Figure 13 illustrates the comparative results of ductility of the bolted steel-based bamboo scrimber and steel connections of different designs. The value of ductility under each connection is between 1.5 and 3.75, and the fluctuation of different connections is large, but the ductility coefficient is basically concentrated in 2.5, which does not show clear regularity. The angle between the load direction and the grain direction has an effect on the connection ductility. Connections with the load direction parallel to the grain direction exhibit ductility ratios of 2.12–3.59, whereas those with the load direction perpendicular to the grain direction have ductility ratios of 1.53–2.18. This suggests that bolted steel-based bamboo scrimber and steel connections achieve better ductility when the load direction is parallel to the grain direction, highlighting the influence of load orientation on the connections of deformability and resilience under load.
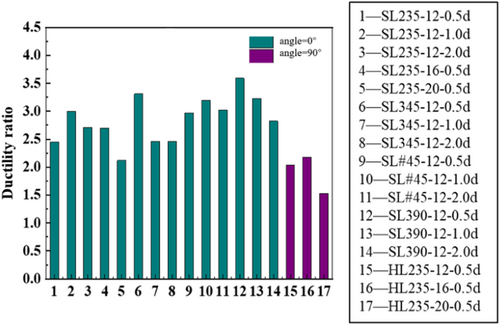
Load–displacement prediction model
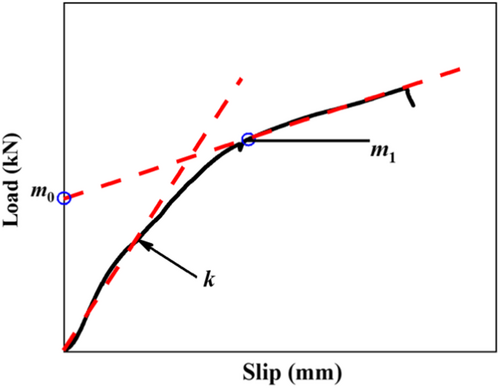
Where F is the applied load (kN), m0 is the intercept of the postyield asymptote on the Y-axis (kN), m1 is the postyield stiffness (kN/mm), k represents the initial stiffness (kN/mm), and Δ is the relative displacement (mm).
By analyzing the load–displacement curves from Figures 8 and 14, selected connections have been characterized with parameters needed for the Foschi model, and these parameters are listed in Table 6. Incorporating each connection parameters into Equation (1) provides a predictive model for the load–displacement relationship of each connection, as illustrated in Figure 15.
Item | m0 (kN) | m1 (kN/mm) | k | Connections | m0 (kN) | m1 (kN/mm) | k |
---|---|---|---|---|---|---|---|
SL235-12-0.5d | 19.64 | 7.05 | 16.51 | SL45-12-0.5d | 41.01 | 5.72 | 27.86 |
SL235-12-1.0d | 29.16 | 5.27 | 16.21 | SL45-12-1.0d | 37.40 | 5.81 | 27.21 |
SL235-12-2.0d | 48.17 | 4.17 | 14.71 | SL45-12-2.0d | 54.96 | 4.62 | 28.61 |
SL345-12-0.5d | 29.47 | 7.11 | 30.15 | SL390-12-0.5d | 33.51 | 7.48 | 30.45 |
SL345-12-1.0d | 24.35 | 8.11 | 26.17 | SL390-12-1.0d | 39.19 | 5.55 | 28.47 |
SL345-12-2.0d | 45.62 | 5.37 | 27.37 | SL390-12-2.0d | 54.99 | 4.39 | 28.63 |
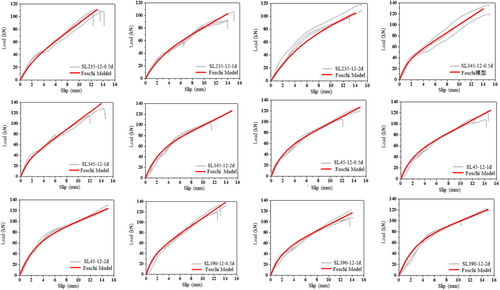
The comparison between the predicted models and actual load–displacement curves demonstrates that the Foschi theoretical model accurately predicts the entire load-carrying process of bolted steel-based bamboo scrimber and steel connections. This highlights the model's effectiveness in forecasting the mechanical behavior of such connections under load, offering valuable insights for design and analysis in structural engineering applications involving bamboo scrimber and steel.
Connections carrying capacity comparison
Considering the formula was initially developed based on phyllostachys pubescens-based bamboo scrimber, and this study focuses on Neosinocalamus affinis-based bamboo scrimber, applying the Equation (2) to calculate the bolt connections carrying capacity in this context requires a comparative analysis with experimental results for accuracy. The calculation using Equation (2) yielded carrying capacities for single bolt connections that were slightly higher than the experimental outcomes, as shown in Table 7. This discrepancy suggests that differences in the mechanical properties of the bamboo base materials could influence the formula's applicability. Consequently, an average correction factor of 1.1 is proposed to adjust the calculated values to more closely align with the experimental data, enhancing the precision of comparisons and ensuring the formula's relevance across different bamboo types.
Item | c (mm) | d (mm) | Yield | Fu (kN) | Nv (kN) | Ct = Nvt/Fu | |
---|---|---|---|---|---|---|---|
SL235-12-0.5d | 90 | 12 | III | 101.53 | 118.56 | 1.17 | 1.10 |
SL235-12-1d | 90 | 12 | III | 95.71 | 118.56 | 1.24 | |
SL235-12-2d | 90 | 12 | IV | 108.81 | 118.56 | 1.09 | |
XL235-12-0.5d | 90 | 12 | III | 105.67 | 118.56 | 1.12 | |
HL235-12-0.5d | 90 | 12 | III | 115.76 | 118.566 | 1.02 | |
SL235-16-0.5d | 90 | 16 | III | 149.24 | 184.94 | 1.24 | |
HL235-16-0.5d | 90 | 16 | III | 142.21 | 184.94 | 1.30 | |
SL235-20-0.5d | 90 | 20 | III | 196.46 | 240.44 | 1.22 | |
HL235-20-0.5d | 90 | 20 | III | 194.24 | 240.4 | 1.24 | |
SL345-12-0.5d | 90 | 12 | III | 122.25 | 118.56 | 0.97 | |
SL345-12-1d | 90 | 12 | III | 107.4 | 118.56 | 1.10 | |
SL345-12-2d | 90 | 12 | IV | 117.73 | 118.56 | 1.01 | |
SL45-12-0.5d | 90 | 12 | III | 116.55 | 118.56 | 1.02 | |
SL45-12-1d | 90 | 12 | III | 111.91 | 118.56 | 1.06 | |
SL45-12-2d | 90 | 12 | IV | 124.47 | 118.56 | 0.95 | |
SL390-12-0.5d | 90 | 12 | III | 127.73 | 118.56 | 0.93 | |
SL390-12-1d | 90 | 12 | III | 112.01 | 118.56 | 1.06 | |
SL390-12-2d | 90 | 12 | IV | 112.93 | 118.56 | 1.05 |
The applicability of Equation (2) was validated using experimental results from literature,13, 14 comparing calculated ultimate loads with experimental data from these studies. The comparison, as detailed in Table 8, shows that the discrepancies between the experimental results Fu and calculated values Nvt are less than 10%, indicating that Equation (2) can provide a unified basis for evaluating the load-carrying capacity of bamboo scrimber in various connection forms.
Number | c (mm) | fha (MPa) | d (mm) | Yield | Fu (kN) | Nvt (kN) | Error (%) | Nv (kN) | Difference |
---|---|---|---|---|---|---|---|---|---|
113 | 60 | 82.8 | 12 | III | 86.45 | 86.48 | 0.04 | 94.49 | 8.04 |
213 | 90 | 82.8 | 12 | IV | 98.22 | 107.77 | 9.73 | 117.75 | 19.53 |
313 | 135 | 82.8 | 12 | IV | 84.89 | 84.43 | −0.54 | 92.25 | 7.36 |
413 | 60 | 82.4 | 14 | III | 97.3 | 101.81 | 4.64 | 112.25 | 14.95 |
513 | 135 | 82.4 | 14 | IV | 151.53 | 139.26 | −8.10 | 153.54 | 2.01 |
613 | 60 | 82.4 | 14 | III | 109.14 | 101.81 | −6.71 | 112.25 | 3.11 |
713 | 90 | 82.4 | 14 | IV | 130.13 | 138.85 | 6.70 | 153.09 | 22.96 |
813 | 60 | 78.0 | 16 | III | 117.85 | 111.77 | −5.16 | 119.01 | 1.16 |
913 | 90 | 78.0 | 16 | III | 155.85 | 163.18 | 4.70 | 173.74 | 17.89 |
1-10-1014 | 80 | 73.4 | 10 | IV | 68.8 | 70.94 | 3.11 | 84.33 | 15.53 |
1-14-1014 | 70 | 69.8 | 14 | III | 108.5 | 108.08 | −0.39 | 129.47 | 20.97 |
- Note: Fu is the ultimate carrying capacity of phyllostachys pubescens-based bamboo scrimber, which is determined by the test results. Nvt and Nv are the single-bolt connection carrying capacity of the phyllostachys pubescens-based bamboo scrimber and the Neosinocalamus affinis-based bamboo scrimber, respectively, which are determined by Equation (2).
When comparing the ultimate load-carrying capacities Nv of Neosinocalamus affinis-based bamboo scrimber connections against the experimental results Fu of phyllostachys pubescens bamboo-based bamboo scrimber under similar configurations and failure modes, it was found that connections made from Neosinocalamus affinis-based bamboo scrimber exhibit higher load-carrying capacities than those made from phyllostachys pubescens bamboo-based bamboo scrimber, with a maximum enhancement in load-carrying capacity of 18%. This suggests that, overall, connections made from Neosinocalamus affinis-based bamboo scrimber have superior load-carrying capacities compared with those made from phyllostachys pubescens bamboo-based bamboo scrimber, highlighting the potential advantages of selecting specific bamboo species for structural applications.
Analysis of end distances on load-carrying capacity
When investigating the connection performance of bamboo scrimber members, end distances significantly affect the load-carrying capacity and damage mode. Proper design of end distance enhances connection strength and prevents early material failure. While design standards specify minimum end distances dimensions for fasteners, little research explores its impact on load-carrying capacity. Therefore, extensive data were collected to compare the difference between test values and theoretical calculations for end distances of 2d, 3d, 4d, 7d, and 10d on Equation (2), with results presented in Table 9.
Groups | Test value (kN) | d (mm) | c (mm) | e (mm) | Yield | Calculated value (kN) | Error (%) |
---|---|---|---|---|---|---|---|
2d-1 | 72.32441 | 12 | 90 | 2d | III | 120.2326 | 66.24 |
2d-2 | 66.5759 | 12 | 90 | 2d | III | 120.2326 | 80.59 |
2d-3 | 66.86702 | 12 | 90 | 2d | III | 120.2326 | 79.81 |
2d-4 | 69.04164 | 12 | 90 | 2d | III | 120.2326 | 74.15 |
3d-1 | 77.06944 | 12 | 90 | 3d | III | 121.7839 | 58.02 |
3d-2 | 80.88513 | 12 | 90 | 3d | III | 121.7839 | 50.56 |
3d-3 | 68.85919 | 12 | 90 | 3d | III | 121.7839 | 76.86 |
3d-4 | 78.21856 | 12 | 90 | 3d | III | 121.7839 | 55.70 |
213 | 85.28 | 10 | 60 | 4d | III | 73.40383 | −13.93 |
313 | 94.2 | 10 | 90 | 4d | IV | 79.26052 | −15.86 |
613 | 98.22 | 12 | 90 | 4d | IV | 107.7739 | 9.73 |
713 | 102.51 | 12 | 60 | 4d | III | 86.48118 | −15.64 |
1013 | 151.53 | 14 | 135 | 4d | IV | 139.5441 | −7.91 |
1113 | 109.14 | 14 | 60 | 4d | III | 102.0225 | −6.52 |
1313 | 117.85 | 16 | 60 | 4d | III | 111.7891 | −5.14 |
B235 | 98.222 | 12 | 90 | 4d | IV | 107.18 | 9.12 |
B535 | 151.533 | 14 | 135 | 4d | IV | 138.73 | −8.45 |
B735 | 85.283 | 10 | 60 | 4d | IV | 72.93 | −14.48 |
B935 | 109.136 | 14 | 60 | 4d | III | 101.44 | −7.05 |
B1335 | 102.507 | 12 | 60 | 4d | Ⅳ | 85.85 | −16.25 |
SL235-12-0.5d | 101.53 | 12 | 90 | 7d | III | 118.5584 | 16.77 |
SL235-12-1d | 95.71 | 12 | 90 | 7d | III | 118.5584 | 23.87 |
SL235-12-2d | 108.81 | 12 | 90 | 7d | IV | 118.5584 | 8.96 |
XL235-12-0.5d | 105.67 | 12 | 90 | 7d | III | 118.5584 | 12.20 |
HL235-12-0.5d | 115.76 | 12 | 90 | 7d | III | 118.5584 | 2.42 |
SL235-16-0.5d | 149.24 | 16 | 90 | 7d | III | 184.9447 | 23.92 |
HL235-16-0.5d | 142.21 | 16 | 90 | 7d | III | 184.9447 | 30.05 |
SL235-20-0.5d | 196.46 | 20 | 90 | 7d | III | 240.4401 | 22.39 |
HL235-20-0.5d | 194.24 | 20 | 90 | 7d | III | 240.4401 | 23.79 |
SL345-12-0.5d | 122.25 | 12 | 90 | 7d | III | 118.5584 | −3.02 |
SL345-12-1d | 107.4 | 12 | 90 | 7d | III | 118.5584 | 10.39 |
SL345-12-2d | 117.73 | 12 | 90 | 7d | IV | 118.5584 | 0.70 |
SL45-12-0.5d | 116.55 | 12 | 90 | 7d | III | 118.5584 | 1.72 |
SL45-12-1d | 111.91 | 12 | 90 | 7d | III | 118.5584 | 5.94 |
SL45-12-2d | 124.47 | 12 | 90 | 7d | IV | 118.5584 | −4.75 |
SL390-12-0.5d | 127.73 | 12 | 90 | 7d | III | 118.5584 | −7.18 |
SL390-12-1d | 112.01 | 12 | 90 | 7d | III | 118.5584 | 5.85 |
SL390-12-2d | 112.93 | 12 | 90 | 7d | IV | 118.5584 | 4.98 |
513 | 86.45 | 12 | 60 | 7d | III | 86.48118 | 0.04 |
913 | 97.3 | 14 | 60 | 7d | III | 102.0225 | 4.85 |
1413 | 155.85 | 16 | 90 | 7d | III | 163.1965 | 4.71 |
113 | 79.19 | 10 | 60 | 10d | IV | 73.40383 | −7.31 |
813 | 84.89 | 12 | 135 | 10d | IV | 84.4338 | −0.54 |
1213 | 130.13 | 14 | 90 | 10d | IV | 139.1348 | 6.92 |
B1435 | 130.125 | 14 | 90 | 10d | III | 138.32 | 6.30 |
The analysis of the experimental data reveals a clear trend in the relationship between end distance and the accuracy of bearing capacity predictions in bolt connections. The code specifies a minimum end spacing dimension of 7d. At end distances of 2d and 3d, the calculated errors were the highest, ranging from 50.56% to 80.59%. This indicates a reduction in reliability in these configurations. The maximum error is −16.25% at an end distance of 4d.
Due to the larger bolt diameter and end distance in the sample groups of SL235-16-0.5d, HL235-16-0.5d, SL235-20-0.5d, and HL235-20-0.5d at an end distance of 7d, the bamboo members can still withstand a certain amount of load after the bolts are damaged by bending, so there is a large difference between the test value and the theoretical value. Except for the above four specimen groups, the error at an end distance of 7d, essentially less than 10%, between the actual and theoretical values of the rest of the specimen groups is small.
At an end distance of 10d, the maximum error is −7.31%. On the whole, in line with the end distance of requirements, the design carrying capacity requirements can meet the test load-carrying capacity.
4 CONCLUSIONS
- 1.
Under construction conditions that meet relevant standards, the failure of bolted steel-based bamboo scrimber and steel connections typically occurs through local compression failure of the bamboo dowels and bending of the bolts, primarily exhibiting Yield Modes III and IV. For steel plate thicknesses of 0.5d and 1d, the bolts show single-hinge failure (Yield Mode III), while for a thickness of 2d, double-hinge failure (Yield Mode IV) is observed, with the critical point between single-hinge and double-hinge failures occurring between 1d and 2d thickness.
- 2.
The yield load capacity of connections increases with bolt diameter, with thick plate connections (t = 2d) showing greater yield capacities than thin plate connections (t = 0.5d and t = 1d). The angle between the load direction and grain direction and the steel grade do not significantly affect yield capacity. The ultimate load capacity also increases with bolt diameter, but the impact of steel grade, plate thickness, and load-grain direction angle is minimal. This underscores the importance of considering bolt diameter in the design of ductile systems to enhance the seismic resilience of structures.
- 3.
Initial stiffness increases with bolt diameter, with connections loaded parallel to the grain direction showing higher stiffness. A steel plate grade of Q235 represents a critical point, with connections using steel stronger than 235 MPa exhibiting higher initial stiffness than those with Q235-grade steel. However, initial stiffness is not significantly affected by steel strength grades above 235 MPa.
- 4.
The factors of steel plate strength grade, thickness, and bolt diameter do not significantly influence the ductility of connections. However, connections exhibit higher ductility when the external load direction is parallel to the grain direction.
- 5.
This model effectively describes the full load–displacement relationship curve for bolted steel-based bamboo scrimber and steel connections, accurately reflecting the entire force process of such connections.
- 6.
Comparing the single bolt connection load capacities of Neosinocalamus affinis-based and phyllostachys pubescens bamboo-based bamboo scrimber, the former shows superior load capacity, with a maximum enhancement in load-carrying capacity of 18%, indicating that Neosinocalamus affinis-based connections perform better. Comparing the carrying capacity of bamboo scrimber connection with various substrates demonstrates that selecting materials and optimizing connection design significantly enhance the toughness and seismic resistance of structures. This offers crucial design guidelines and experimental evidence for the elastic evaluation and enhancement of engineering structures.
- 7.
End distances of 2d and 3d exhibited the highest calculated errors, ranging from 50.56% to 80.59%, indicating a significant reduction in reliability. However, as the end distance increased, the errors decreased, with a maximum error of −16.25% at 4d and a notably smaller error at 7d, where the discrepancy between actual and theoretical values was less than 10%. The end distance of 10d produced the smallest maximum error of −7.31%. Overall, the results suggest that larger end distances, particularly 10d, offer more accurate and reliable predictions, meeting the design requirements. Overall, the design carrying capacity meets the test load requirements for the given end distances of 7d.
At present, the research on bamboo scrimber is usually carried out according to the existing timber structure specifications. Although both bamboo and wood are biomass materials, the applicability of wood structure specifications to bamboo scrimber structure still needs to be further studied due to the differences in the mechanical properties of the two materials. Taking this paper as an example, the structural form of the nodes designed according to the Eurocode 5 wood specification is found through experiments, but none of the node connections are broken in Yield Mode I. Therefore, it is necessary for scholars to deeply study and improve the relevant design basis and standards, improve the reliability and standardization of the bamboo scrimber structure, and then promote the innovative development of the bamboo scrimber structure, and inject new sustainability and environmental protection concepts into the architectural field. Given that bamboo scrimber structures are a relatively recent area of research, current studies predominantly focus on the basic mechanical properties under monotonic loading to establish a reliable theoretical foundation and experimental data. Future research plans include conducting cyclic loading tests to thoroughly evaluate the dynamic response and fatigue performance of the connections under seismic actions, thereby providing a more complete theoretical basis for the seismic design of bamboo scrimber structures.
ACKNOWLEDGMENTS
The present work was undertaken by the financial support from the Sichuan Science and Technology Program (No. 2023YFS0393), the National Natural Science Foundation of China (Grant No. 51608452) and Sichuan Energy Construction Engineering Group Co., Ltd. Projects (2023510101002689, 2023510101002690). The authors would also like to thank the Structural Engineering Laboratory of Southwest Jiaotong University, Sichuan Hongya bamboo era Tech Co., Ltd and SCEI Smart OPTOELECTRONIC Co., Ltd for the support provided on the performance of the experiments.
CONFLICTS OF INTEREST
The authors declare no conflict of interest.