Destillation auf der ACHEMA 2022
Distillation at ACHEMA 2022
Abstract
deEines der meistverwendeten thermischen Verfahren zur Trennung und Reinigung von Prozessströmen in der chemischen Industrie ist die Destillation. Die dabei eingesetzten Rektifikationskolonnen besitzen, zur Steigerung der Trenneffizienz, Einbauten in Form von Böden, Packungen und Füllkörpern. Durch den hohen Einsatz der Kolonnen besteht fortlaufend ein Interesse an einer Effizienzerhöhung, einer Energieeinsparung und einer Erweiterung des Einsatzgebietes. Zu diesen Themen wurden die Unternehmen der ACHEMA 2022 befragt. Einige der Neuigkeiten werden in diesem Bericht zusammengefasst.
Abstract
enOne of the most widely used thermal processes for separating and purifying process streams in the chemical industry is distillation. The used rectification columns have internals like trays and random or structured packings to increase separation efficiency. Due to the high use of the columns, there is an ongoing interest in increasing efficiency, saving energy and expanding the area of application. Companies at ACHEMA 2022 were asked about these topics. Some of the news are summarized in this report.
1 Einleitung
Fortlaufend stellt die Zerlegung synthetischer oder natürlicher Produkte in ihre Einzelkomponenten einen der zentralen Aspekte in der chemischen Industrie dar. Eine Vorreiterrolle nimmt dabei immer noch die sehr energieintensive Destillation ein. Aufgrund der zahlreichen Anwendung in so gut wie jedem chemischen Prozess waren auch in diesem Jahr auf der ACHEMA zahlreiche Aussteller vertreten. Neben Herstellern von konventionellen Gegenstromanlagen und deren Einbauten im Labor- bis Industriemaßstab waren ebenfalls Austeller vertreten, die sich auf die unterschiedlichsten Bereiche der Destillation spezialisiert haben. Mess- und Regelungstechniken, Simulationssoftware, Steuerungstechniken und Spezialanwendungen sind nur ein kurzer Einblick in die vertretenen Bereiche.
Im Rahmen dieses Artikels wird sich im Wesentlichen auf die Neuentwicklungen im Bereich der konventionellen Gegenstromdestillation bezogen. Ein besonderer Fokus liegt dabei auf den Neuentwicklungen der letzten Jahre hinsichtlich Einbauten und einem optimierten Einsatz der Destillation gerade im Hinblick auf gesellschaftlich und politisch getriebene Forderungen.
Alle Angaben und Daten in diesem Bericht beziehen sich auf ausgelegte Produktbroschüren oder direkten Kontakt mit den genannten Herstellern. Es wird lediglich die Meinung der Autorinnen widergespiegelt und es wird nur ein kleiner Teil der präsentierten Hersteller aus subjektiver Sicht in diesem Artikel erwähnt. Die Aufzählungen sind in keinem Fall vollständig.
2 Neuentwicklungen
Die aktuelle Weltlage und die allgemein seit Jahren gültige Forderung nach Energieeinsparung stellt gerade die Destillation immer wieder vor neue Herausforderungen. Als sehr energieintensive Unit-Operation bietet sie demnach nicht nur erhöhtes Einsparpotenzial, sondern auch die Möglichkeit zur stetigen Forschung. Damit einhergehend treten immer wieder Neuentwicklungen bei den einzelnen Herstellern auf, die in diesem Beitrag präsentiert werden.
2.1 Einbauten
Im klassischen Fall der Gegenstromdestillation fallen neben Flüssigkeitsverteilern vor allem die trennwirksamen Einbauten ins Gewicht. Im Wesentlichen werden diese unterschieden in strukturierten Packungen, Füllkörpern und Böden. Ziele beim Design oder der Neuentwicklung sind dabei stets die Reduzierung des Druckverlusts und damit der Betriebskosten, die Erweiterung des möglichen Arbeitsbereichs und die Erhöhung der Trennleistung. Zusätzliche Anforderungen bezüglich Temperaturen, Verhalten bei unterschiedlichen Stoffsystemen und die generellen Herstellungskosten der Einbauten spielen ebenfalls eine wichtige Rolle. So ist z. B. in den letzten Jahren der 3D-Druck von strukturierten Packungen stärker in den Vordergrund gerückt wohingegen sich das Verfahren aufgrund der höheren Kosten bei den Füllkörpern bisher nicht durchsetzen konnte. Vorherrschend auf der ACHEMA in diesem Jahr waren vor allem Neuentwicklungen im Bereich der Materialien zu finden.
Sulzer Chemtech präsentierte den NeXRing™ Füllkörper der 4. Generation aus Polyetheretherketon (PEEK), der sowohl chemisch als auch thermisch (bis 250 °C) sehr beständig ist (vgl. Abb. 1b). Zudem ist das Material sehr leicht und korrosionsbeständig. Neben der Entwicklung des neuen Füllkörpers wurden auch strukturierte Packungen und entsprechende Einbauten (Flüssigkeitsverteiler und Tragrost) aus PEEK entwickelt. Der Werkstoff PEEK eignet sich hervorragend für industrielle Anwendungen im Bereich von Säuren und Laugen sowie halogenierten organischen Stoffen.
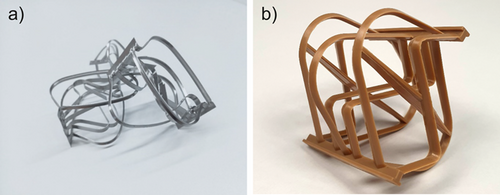
Auch das Unternehmen Julius Montz GmbH (Hilden, D) stellte einen Füllköper aus Polytetrafluorethylen (PTFE) vor, um den Ansprüchen höherer Temperaturen gerecht zu werden. Im Gespräch mit dem Unternehmen wurde vor allem die Differenzierung in den Materialien bei den einzelnen Herstellern als größte Weiterentwicklung herausgestellt. Weiterentwicklungen im Bereich von Böden fokussieren sich in den letzten Jahren vorwiegend auf die Ausweitung des Arbeitsbereichs der Böden.
Die RVT Process Equipment GmbH (Marktrodach, D) stellte vordergründig den neuen RMXR-Ring aus Metall vor, der sich vor allem durch eine erhöhte Leistung bei geringerem Druckverlust auszeichnet (vgl. Abb. 1). Laut RVT liegt die Kapazität dieses patentierten Hochleistungsfüllkörpers mit bis zu 25 % deutlich über den Ringen der 2. und 3. Generation. Der neue Ring kann somit zu einer erheblichen Einsparung von Energie beitragen.
Neben der Präsentation von unterschiedlichen Einbauten aus unterschiedlichen Materialien steht aber weiterhin vor allem ein optimierter Einsatz der Destillation hinsichtlich des Energieeintrages im Vordergrund.
2.2 Optimierter Einsatz der Destillation
Gesellschaftlich oder politisch getriebene Forderungen wirken sich indirekt auf den Einsatz der Destillation aus. Auf der ACHEMA 2022 wurden u. a. zwei unterschiedliche Trends in der Anwendung der Destillation deutlich. Zum einen wurde ein verstärkter Einsatz der Kurzwegdestillation vermerkt und zum anderen wird das Ziel der Energieeinsparung immer mehr fokussiert.
Die Kurzwegdestillation, auch bekannt als Molekulardestillation, wird für wärmeempfindliche und viskose Produkte eingesetzt. Charakteristisch sind kurze Verweilzeiten, geringe Betriebstemperaturen durch hohes Vakuum und hohe Effizienz in Stoff- und Wärmetransport (Pope Scientific Inc. (Wisconsin, USA)). Das Unternehmen Pope Scientific Inc. stellt Dünnschichtdestillationsanlagen für eine Vielzahl von Anwendungen sowohl in der Pharma- und Lebensmittelindustrie als auch in der Öl-, Polymer-, und Spezialchemie her. Hierbei wächst die Nachfrage gerade hinsichtlich pflanzenbasierter Produkte, womit die Kurzwegdestillation für die Herstellung unterschiedlichster Oleochemikalien eingesetzt wird. Herausfordernd ist dabei vor allem das Fouling, das durch die richtige Auslegung und den Betrieb der Kurzwegdestillation reduziert werden kann 1.
Neben dem optimierten Einsatz der Destillation bezüglich des Produktportfolios besteht auch bei der konventionellen Anwendung Optimierungspotenzial. Energieeinsparung ist seit Jahren ein wichtiges Thema, das durch die aktuelle Gaskrise noch mehr in den Fokus tritt. Rund die Hälfte des Energieverbrauchs für industrielle Trennung wird für die Destillation benötigt 2. Energiesparende Maßnahmen hinsichtlich der Destillation einzuleiten, ist daher eines der Hauptziele. In diesem Bericht soll es um zwei Beispiele gehen. Das erste beinhaltet ein alternatives Verfahren der Firma ENVIMAC Engineering GmbH (Oberhausen, D) zur Abluftreinigung von organischen Schadstoffen. Zunächst wird die industrielle Abluft mittels Absorption von Schadstoffen befreit. Anschließend wird das organische Waschmittel in einer Vakuum-Rektifikationskolonne regeneriert und in einem Kreislaufprozess zur Absorption zurückgeleitet. Das Verfahren ersetzt bei einem Produktionsbetrieb eine thermische Nachverbrennungsanlage und ermöglicht eine Einsparung von ca. 50 % der Energieaufwendungen.
Das zweite Beispiel bezieht sich auf die Anwendung einer Rektifikationskolonne als Trennwandkolonne. Die Technologie dahinter sei keine innovative aber vor dem wichtigen Hintergrund der Energieeinsparung eine bedeutende, betont das Unternehmen Julius Montz GmbH. Dabei wird eine Trennwand vertikal über eine bestimmte Höhe in eine konventionelle Rektifikationskolonne eingebaut (vgl. Abb. 2). Ziel ist es, ein Mehrstoffgemisch mittels einer Kolonne in reine Fraktionen aufzutrennen. Bei einem beispielsweise ternären Gemisch findet im ersten Teil vor der Trennwand eine scharfe Trennung zwischen Schwer- und Leichtsieder statt und in dem zweiten Teil der Kolonne werden alle Komponenten rein gewonnen. Im Vergleich zu einer Mehrkolonnen-Verschaltung können die Betriebskosten um ca. 25 % reduziert werden. Das Unternehmen Julius Montz GmbH (Hilden, D) bietet verschiedenste Formen und Ausrüstungen dieses Kolonnensystems an, so dass eine Umrüstung oder ein kompletter Neuaufbau unkompliziert wird.
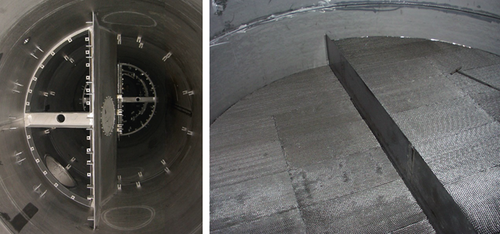
3 Fazit
Hinsichtlich der drei Faktoren Effizienzerhöhung, Energieeinsparung und Erweiterung des Einsatzgebietes lässt sich festhalten, dass zum einen durch andere Formgebung bestehender Füllkörper Verbesserungen hinsichtlich Druckverlust und Kapazität erreicht werden können und zum anderen durch den Einsatz anderer Materialien für (nicht)trennwirksame Einbauten extremere Temperatur- und Chemikalienbereiche möglich sind. Das Einsatzgebiet der Destillation wird weiterhin durch den steigenden Bedarf an beispielsweise pflanzlich basierten Chemikalien erweitert und somit rückt die Kurzwegdestillation in den Fokus. Die aktuelle Weltlage zeigt einmal mehr, dass Energieeinsparungen nötig sind. Mittels Trennwandkolonnen und auch Prozessoptimierungen werden Einsparungen ermöglicht. Grundlegend zeigt sich, dass durch den sich stetig ändernden Markt und aktuelle politische Themen, Rektifikationskolonnen auch in Zukunft weiterentwickelt und optimiert werden müssen.
Danksagung
Wir bedanken uns bei allen Unternehmen für die hervorragende Zusammenarbeit. Open Access Veröffentlichung ermöglicht und organisiert durch Projekt DEAL.