Experimental Characterization of 3D Printed Structured Metal Packing with an Enclosed Column Wall
Abstract
Additive manufacturing is a promising tool for tailored solutions in chemical engineering. This applies in particular to the design of lab-scale packed bed columns. We present experimental results to characterize a lab-scale 3D printed structured metal packing and compare it to a conventional counterpart. The results indicate that necessary adjustments for the manufacturing process of the metal material have an influence on important operating parameters, resulting in higher specific pressure drop, slightly higher liquid holdup and lower mass transfer efficiency.
1 Introduction
Additive manufacturing (AM) offers great potential for the tailored design of individual structures and geometries, rendering it a powerful tool for specialized chemical engineering applications. There are several research groups that have already investigated additively manufactured structures for distillation and absorption tasks. Purpose of these studies was to analyze and exploit the potential benefits of tailored solutions through AM for different challenges, which include but are not limited to the design of new packing structures or measures for process intensification. Tab. 1 gives a systematic overview of the available literature on additive manufacturing applied to distillation and absorption processes.
Author (year) [Ref.] |
Structure and application |
Main contribution with respect to additive manufacturing |
---|---|---|
Gładyszewski et al. (2018) 1 |
Foam structure for rotating packed bed (RPB) |
Comparison of hydrodynamic performance and mass transfer efficiency for a conventional metal foam and a 3D printed polymer foam structure used for a distillation process in an RPB. |
Gładyszewski et al. (2021) 2 |
Foam structure for RPB |
Experimental characterization of anisotropic foam packing in RPB to reduce maldistribution of liquid along the radius of the packing and comparison to an isotropic foam packing with respect to hydrodynamics, mass transfer efficiencies and liquid distribution for the absorption of CO2. |
Qammer et al. (2019) 3 |
Zigzag structure for RPB |
Development of a zigzag packing structure for a RPB to combine advantages of structured packings (low pressure drop) with those of rotating zigzag beds (narrow residence time distribution) and comparison of performance to conventional elements in a RPB by means of distillation experiments. |
Lukin et al. (2021) 4 |
Spiral packing for RPB |
Design and application of a spiral packing for aroma absorption in a RPB to reduce liquid maldistribution and maintain separation efficiency at high gas and liquid loads. |
Bolton et al. (2019) 5 |
Printed packings with different configurations for carbon capture |
Investigation of different printed packings for the CO2 capture process and comparison of different packing diameter and material with respect to dry pressure drop. |
Miramontes et al. (2020) 6 |
Intensified device for CO2 capture process |
Printed process intensification device combining enhanced phase contact and improved withdraw of heat of reaction for the reactive absorption of CO2 in amines and experimental characterization of hydrodynamics and temperature profiles as well as CFD calculations for the identification of the overall heat transfer coefficient in the developed structure. |
Miramontes et al. (2020) 7 |
Intensified device for CO2 capture process |
Printed process intensification device combining enhanced phase contact and improved withdraw of heat of reaction for the reactive absorption of CO2 in amines and experimental demonstration of process intensification. |
Jang et al. (2021) 8 |
Intensified device for CO2 capture process |
Investigation of corrosion on the device presented in 6, 7 and prevention of corrosion by means of different coating schemes that are investigated. |
Jang et al. (2021) 9 |
Intensified device for CO2 capture process |
Investigation of the device presented in 6, 7 by using low-aqueous solvents for the absorption of CO2 to reduce the temperature and subsequently improve the efficiency of the absorption process. |
Thompson et al. (2021) 10 |
Intensified device for CO2 capture process |
Rigorous modeling and model validation for the intensified device for carbon capture developed by Miramontes et al. 6, 7. |
Neukäufer et al. (2019) 11 |
Scalable packings based on unit cells for lab-scale distillation application |
Framework for the identification and characterization of scalable packing geometries based on unit cells, CFD modeling and experimental investigations of pressure drop and liquid distribution. |
Neukäufer et al. (2020) 12 |
Scalable packings based on unit cells for lab-scale distillation application |
Measurement of static and dynamic contact angles on both conventional and additively manufactured packing material as a key property for wetting behavior. |
Neukäufer et al. (2021) 13 |
Scalable packings based on unit cells for lab-scale distillation application |
Presentation of a scalable lab-scale distillation test rig for additively manufactured packings and experimental characterization of HETP values at different operating points. |
Dejean et al. (2020) 14 |
Wire-based packing for gas-liquid contact systems |
Simple wire geometries are investigated regarding pressure drop, thickness of liquid film and liquid flow regimes at different diameter and length of the wire as well as different contact angles of the liquid. |
Kawas et al. (2021) 15 |
Wire-based packing for gas-liquid contact systems |
Further elaboration of the structures investigated in 14 with an experimental investigation of a wire-based structured packing with respect to hydrodynamics and mass transfer as well as a comparison to a conventional packing structure. |
Kawas et al. (2021) 16 |
Wire-based packing for gas-liquid contact systems |
Development of correlations for hydrodynamics and mass transfer efficiencies based on the results presented in 15. |
Zimmer et al. (2021) 17 |
TPMS based packings for gas-liquid contact systems |
Development of packing structures based on topology optimization and evaluation of the influence of the printing process and material on dry pressure drop by means of CFD simulations and experiments. |
Lab-scale structured packings are one important field of application for AM in distillation and absorption. This is due to some major advantages offered by AM, namely the individualization of structures, the reduction of column diameters and a fast reproduction of structures. These advantages can have a great impact on process development and scale-up. In particular, a reduction of column diameter is beneficial as the amount of liquid needed for the experiments corresponds to the diameter of the column. A reduced lab-scale column diameter can therefore lead to cost reductions during process development. However, a reduction of column diameter < 40 mm should be prevented as wall effects increase due to an increased ratio between surface area and column volume 18, 19.
Additionally, conventional structured packings are equipped with wall wipers. As the column diameter is reduced, the available space for wall wipers guiding the liquid back into the column is also reduced. One possible solution is to neglect wall wipers and account for a direct connection of the packing structures with the column wall. This measure also provides the benefit to print the packing structure with the enclosed column wall as one single part that is easily replaceable and recyclable.
In this contribution, we present the results of an experimental characterization of additively manufactured structured metal packings with enclosed column wall and compare the additively manufactured packing with a conventional packing of the same type equipped with wall wipers. The experimental characterization includes fluid dynamic parameters such as specific dry pressure drop, specific pressure drop of the two-phase flow, liquid holdup as well as mass transfer efficiency.
The article is organized as follows. In Sect. 2 the materials and methods are presented including main characteristics of the two investigated packings, the experimental setup and the measurement methods. In Sect. 3, we present the experimental results for fluid dynamic parameters and mass transfer efficiency that are discussed in more detail in Sect. 4. Finally, in Sect. 5 a conclusion and an outlook on future research activities is given.
2 Materials and Methods
In this section, the investigated packings, the experimental setup, and the methods applied to assess fluid dynamic parameters and mass transfer efficiency are described.
2.1 Packing Characteristics
Structured metal packings of the type Raschig Super-Pak 350Y (RSP 350Y) were investigated and the original packing with wall wipers was compared to a 3D printed version (RSP-AM) with an enclosed column wall. Images of one single element from both packings are shown in Fig. 1.
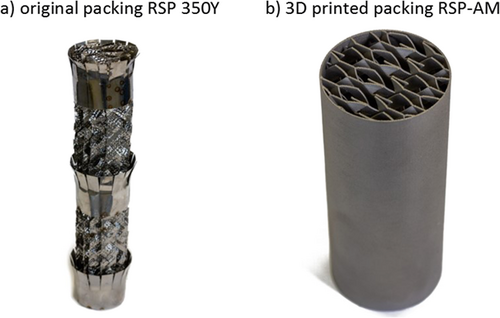
The printed packing elements were manufactured by selective laser melting (SLM) that used stainless steel 1.4404 as raw material. This manufacturing process is based on a complete melting of the raw material. The high temperatures required to melt the steel are provided by a laser. Therefore, for the SLM process some geometric adjustments of the packing geometry were necessary in order to assure accurate manufacturing of the single packing elements. To avoid excessive thermal tension within the packing material, the height of one single element was limited and set to half the height of a single element of the original packing. In fact, it was necessary to increase the wall thickness of the metal sheets within the packing. This led to a significant decrease in porosity from 97 % in the original RSP 350Y to 67 % in the printed RSP-AM.
Although the material is thicker in the printed packing, the distance between the metal sheets was set to the same value as in the conventional packing. With the missing wall wipers in the printed packing an increased volume for packing material was available, resulting in a specific surface area that is 14 % higher compared to the conventional packing. The available packing diameter is identical for both packings and includes the column wall for the printed packing and the wall wipers for the conventional packing, respectively. All geometric data for the investigated packings are summarized in Tab. 2.
Parameter |
RSP 350Y |
RSP-AM |
---|---|---|
Material thickness s [µm] |
100 |
700 |
Height of single element HE [mm] |
235 |
117.5 |
Available packing diameter dP [mm] |
48 |
48 |
Porosity ε [%] |
97 |
67 |
Specific surface area a [m2m−3] |
350 |
400 |
Another important difference between the two packings investigated resulted from the manufacturing process and concerns the microstructure of the metal surface. For the conventional packings, microstructured metal sheets are used to create the maximum possible surface area. This microstructuring cannot be achieved by the additive manufacturing process and is thus missing on the packing surface. This leads to a decreased absolute surface area to be wetted with a liquid film during operation.
Apart from differences resulting from the manufacturing process, the major characteristic of the 3D printed packing was the direct connection of the packing structure with the enclosed column wall. In comparison to the conventional packing, which was equipped with wall wipers, they were not considered in the design of the connection between the structure and the wall. Therefore, the aim of a thorough experimental characterization is to identify the impact of the direct connection between the packing structure and the column wall on relevant operating parameters. Moreover, for this novel design approach, we already studied the liquid phase and the radial phase distribution using a wire mesh sensor 20.
2.2 Experimental Setup
All experimental investigations were performed in a lab-scale test column with an inner diameter of dC2 = 0.05 m. The available height of the column was HC2 = 1 m, resulting in a total packing height of HP = 0.94 m if equipped with four elements of RSP 350Y and eight elements of RSP-AM, respectively. To ensure comparability, only every second packing element was rotated by 90° in axial direction for the RSP-AM, whereas every single element was rotated for the RSP 350Y. The elements of the conventional packing were clamped one after the other into a column shell made of glass. Measures to connect the elements were not necessary as they sat tightly in the glass column. However, this leads to possible deformation of the packing structure influencing experimental results. An effect that might also occur in industrial columns. Deformation of the packing structure was prevented in the printed packing elements as the enclosing column wall is directly connected to the packing structure. The elements of the printed packing sat on each other in the same column shell. During the experiments, a liquid film occured between the wall of the packing elements and the column shell sealing the gap between them. This liquid remained there even if liquid supply was stopped, e.g., for holdup measurements. Therefore, we do not expect this liquid to have a significant impact on the results.
The air supplied to the column was pre-humidified in a separate column (dC1 = 0.1 m) to ensure constant physical conditions before entering the test column. The air was supplied using an electrical fan and distributed by a cap-type distributor that was placed 70 mm beneath the packing. The liquid was distributed using a single drop point resulting in a droplet density of 509 m−2. Fig. 2 shows a flowsheet of the experimental setup that is in accordance with the VDI guideline 2761 part 2 21. Gas load factors can range between Fv = 0.5–3 Pa0.5 and liquid load (uL) is set to 5, 11, and 21 m3m−2h−1, respectively.
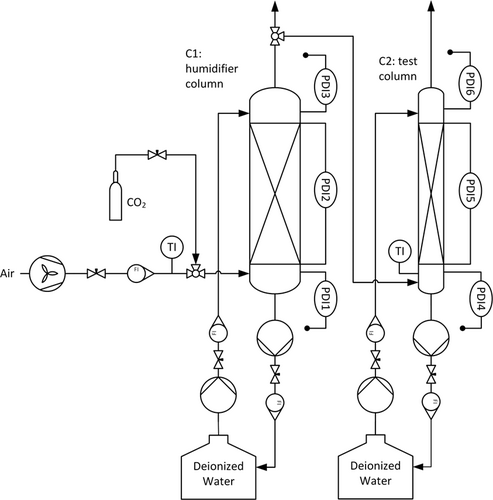
2.2.1 Fluid Dynamics
Fluid dynamic parameters include measurement of pressure drop and liquid holdup as a function of gas and liquid loads. Experiments regarding fluid dynamic parameters are conducted using deionized water and air.
The pressure drop was measured for the single-phase and the two-phase flow. Therefore, pressure was measured at various points within the test column using pressure manometer having an accuracy of 8.5 Pa. Measuring the pressure drop over the structured packings was facilitated using an inclined pressure manometer having an accuracy of 1 Pa. Dry pressure drop was measured before the experiments with the two-phase flow to prevent the influence of any remaining liquid within the packings on the results. Before measuring the pressure drop of the two-phase flow, the packings were wetted using high gas and liquid loads. Subsequently, the liquid was drained from the packings before gas and liquid load of the first operating point was set. Measurements were repeated three times for each operating point.
Holdup was measured by means of gravity. First, the column was operated at a defined operating point. Then, liquid supply and drainage was closed at the same time and countercurrent air flow was stopped. Thus, liquid accumulated to the sump of the column and was drained from the column by means of gravity. The different liquid levels in the sump after ten minutes represent the liquid volume drained from the column that can be converted into the liquid holdup. In this way, only the dynamic holdup was determined. The stationary holdup was neglected, as it is known that the stationary holdup is only a very small ratio of the liquid holdup 22. Again, all measurements were repeated three times for each operating point.
2.2.2 Mass Transfer
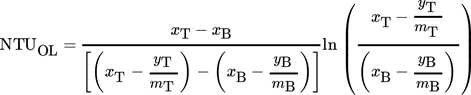

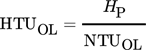
Before the measurement, deionized water was saturated with CO2 before the liquid was broad into contact with air and the CO2 is desorbed. Concentration of CO2 in the gas phase was measured using an IR analyzer (ULTRAMAT 23, Siemens). Liquid phase concentrations were determined using a TOC analyzer (TOC-L Analyzer, Shimandzu) in the IC mode. After reaching steady-state operation at a set operating point, liquid samples were taken from the feed pipe and from the sump of the column. The samples were directly mixed with diluted NaOH having a concentration of 0.1 mol L−1. CO2 concentrations were obtained by a NDIR sensor after being degassed from the liquid sample at a low pH value of 3. The method applied was described and validated in detail by Brinkmann et al. 27.
3 Experimental Results
In the following section, experimental results are described for the fluid dynamic parameters specific pressure drop and liquid holdup, as well as for mass transfer efficiency. Results are compared for the conventional structured packing RSP 350Y and the additively manufactured packing RSP-AM. All results presented represent mean values from three repetitions of the measurements.
3.1 Specific Pressure Drop
First, the specific dry pressure drop at a liquid load of uL = 0 was measured. Results are shown in Fig. 3 in terms of specific pressure drop as a function of the gas load factor. Relative standard deviation of the measurements was 0.8 % for the conventional packings (RSP 350Y) and 2.6 % for the additively manufactured packings (RSP-AM). Thus, reproducibility of the results was very high.
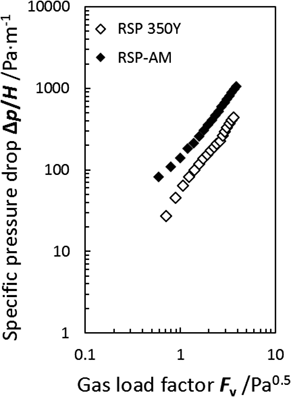
The specific dry pressure drop of the additively manufactured packing (RSP-AM) is higher than for the conventional packing (RSP 350Y) for all investigated gas loads. On average, the values are twice as high for the printed packing. At low gas load factors (Fv < 1 Pa0.5) differences between the two packings increase whereas for high gas load factors (Fv > 1 Pa0.5) the difference in specific dry pressure drop is constant.
Fig. 4 shows a comparison of the specific pressure drop for the two-phase flow for different liquid loads (uL = 5, 11, and 21 m3m−2h−1). Again, reproducibility of the measurements was very high, as the relative standard deviation is < 5 % for all operating points in both packings. The results show a higher specific pressure drop for the additively manufactured RSP-AM in comparison to the original RSP 350Y. With increasing liquid loads, the difference between both packings, RSP 350Y and RSP-AM, decreases. The same holds true for increasing gas load factors at specific liquid loads.
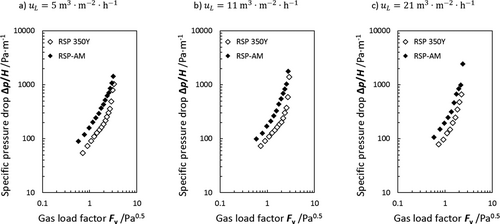
From these experimental results, it can also be observed that loading and flooding can be expected at different operating conditions for both packings. For the conventional RSP 350Y, the loading point is reached at lower gas load factors and is more pronounced at a gas load factor of Fv ≈ 2 Pa0.5. Additionally, flooding is reached for all investigated liquid loads in the conventional packing. For the additively manufactured packing, the loading point is less pronounced and shifted to higher gas load factors.
3.2 Liquid Holdup
Liquid holdup is another important parameter when considering the fluid dynamics of packed columns. Fig. 5 shows the liquid holdup for both investigated packings as a function of the gas load factor for the same liquid loads described before. The relative standard deviation was <5 % for all operating points and thus reproducibility for this measured variable was again very good. Results show a higher liquid holdup for the additively manufactured RSP-AM than for the conventional RSP 350Y. Exceptions can be observed at higher gas load factors (Fv > 2 Pa0.5) for uL = 5, 11, and 21 m3m−2h−1.
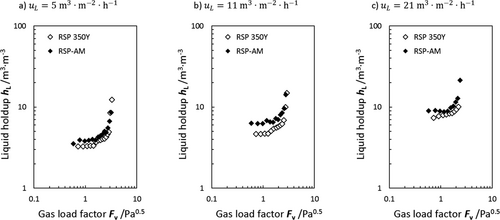
In contrast to the results for the specific pressure drop, no significant differences regarding loading and flooding point can be deduced from the results of the liquid holdup. On the contrary, for all liquid loads, loading can be detected at equal gas load factors for both packings, conventional and additively manufactured, respectively.
3.3 Mass Transfer
Finally, the mass transfer efficiency by means of HTUOL values is determined for both packings. Results are shown in Fig. 6 for varying gas and liquid loads. Different observations are valid for the different liquid loads investigated. At low liquid loads (uL = 5 m3m−2h−1), HTUOL values are almost unaffected by increasing gas load factors. The difference between the conventional packing and the additively manufactured packing is comparably small and values for HTUOL range between 0.2 and 0.25. For a liquid load of uL = 11 m3m−2h−1, HTUOL values of the RSP-AM are significantly higher compared to the conventional packing for low gas load factors. Only for a gas load factor of Fv ≈ 2 Pa0.5 the values are in the same range for both packings. A significant dependence of the HTUOL values on the gas load factor can be observed for the additively manufactured RSP-AM. For the third liquid load investigated (uL = 21 m3m−2h−1) both packings show increasing HTUOL values with decreasing gas load factors. Independent from the gas load factor, the HTUOL values for the additively manufactured packing are slightly higher compared to the conventional packings.
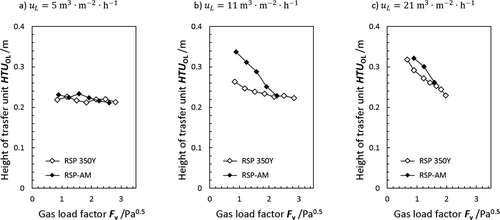
4 Discussion
The experimental results presented in Sect. 3 need to be linked to the packing characteristics and the results of our previous study 20 on the phase distribution within the two different packings.
Taking the results of the specific dry pressure drop into account, it becomes obvious that the reduced porosity resulting from the requirements of the manufacturing process in the RSP-AM leads to a significant higher dry pressure drop compared to the conventional packing. This effect is not compensated by the missing wall wipers in the printed RSP-AM that might lead to a reduced specific dry pressure drop.
The effect the increased porosity has on the specific pressure drop does not affect the liquid holdup to the same extend. For both investigated packings, the liquid holdup is a function of the gas load factor and shows expectable results. Between loading point and flooding, a continuous increase of liquid holdup is detected. This is due to increasing shear forces at the phase boundary between gas and liquid phase. Both, loading point and flooding can be identified from the results of the liquid holdup and their position does not significantly differ between both packings. Nevertheless, it can be observed that liquid holdup is higher for all investigated operating points in the RSP-AM compared to the RSP 350Y. This effect can be attributed to the increased specific surface area in the RSP-AM (aRSP-AM > aRSP350Y), see Tab. 2. With identical volume of the packed bed, the larger specific surface area results in a higher absolute surface area that is available and wetted with a liquid film. Consequently, a higher liquid holdup for the printed packing is reasonable. This effect is not compensated by enhanced local liquid holdup on the microstructure of the metal sheets in the conventional packing.
Considering the specific pressure drop of the two-phase flow, both packings show expectable results. Specific pressure drops increase in a linear manner as gas load factors increase until the loading point is reached. The specific pressure drops are higher for the two-phase flow than for the pure gas flow, as the liquid within the packing reduces the volume available for the gas to flow through the packing. With further increase of the gas load factor, flooding is detected if the gradient of the specific pressure drop is approaching infinite. This behavior is in particular valid for the conventional RSP 350Y. Both, loading point and flooding can be identified within the range of gas load factors investigated. The higher specific pressure drops in the RSP-AM result from significant lower porosity of the packing structure and are superimposed by the enhanced liquid hold-up within the printed packing.
In the conventional packing structure, the wall wipers are responsible for different effects. Most importantly, they guide the liquid from the wall back into the inner structure of the packing. At the same time, wetted wall wipers impose a higher resistance to the gas flow guiding also the gas back into the packing. 28 During the experiments, it was observable that flooding of the packing started locally at the wall wipers and evolved from there into the inner packing structure resulting in a more pronounced transition between loading and flooding. In contrast, for this specific packing structure, in the printed packing the loading point is reached at higher gas load factors and is not pronounced in the same manner. Taking the significantly smaller porosity of the printed packing into account, this behavior is counterintuitive. We assume that the accumulation of liquid with increasing gas load factors proceeds more evenly over the cross-sectional area of the packing structure resulting in less pronounced loading and a more continuous increase in specific pressure drop. A disadvantage of the RSP-AM is that one cannot see what is happening inside the packing structure. Those effects were also not detectable in our previous experiments using the wire mesh sensor to characterize the stationary phase distribution inside the packings.
Finally, mass transfer efficiencies are discussed in detail. At low liquid loads, none of the aforementioned characteristics seems to have an influence on the mass transfer efficiency. With increasing liquid loads mass transfer efficiencies differ significantly, in particular at low gas load factors. Here, phase distribution within the packing is of great importance. In a recent publication, we showed that the wall flow of the liquid is increased in the printed RSP-AM compared to the conventional RSP 350Y 20. Thus, with enhanced liquid wall flow at higher liquid loads, a reduced phase boundary is available for mass transfer, which reduces the mass transfer efficiency. However, the effect of enhanced liquid wall flow is pronounced in both packings at the highest investigated liquid load. It is therefore reasonable that mass transfer efficiencies are reduced in both packings for the corresponding operating points. Additionally, the microstructure on the metal sheets of the conventional packing is responsible for an intensification of the liquid sided mass transfer as turbulences within the liquid film are enhanced and local liquid holdup on the metal sheet is increased 29. As stated earlier, this microstructure is missing on the printed metal sheets, which might also be responsible for an overall lower mass transfer efficiency determined in the printed packing.
5 Conclusions and Outlook
The results of a comprehensive experimental characterization of two structured metal packings, one being the conventional RSP 350Y and the other an additively manufactured counterpart with an enclosed column wall, were presented. The experimental characterization included measurements of specific pressure drops, liquid holdups and mass transfer efficiencies in a lab-scale setup. Results show that the geometric adaptions of the packings necessary for the manufacturing process affect the fluid dynamic performance and mass transfer efficiency. Most notably, the resulting decrease in porosity leads to significantly higher specific pressure drops in the additively manufactured packing. Moreover, the direct connection of the packing structure with the column wall results in an increased liquid wall flow, which promotes higher HTUOL values. On the other hand, the additively manufactured packing is characterized by higher possible gas and liquid loads before flooding is reached and thus allows for a higher capacity. Nevertheless, for a thorough scale-up, the direct connection of the packing structure with the column wall should be neglected.
Reducing the wall thickness of the material is one important aspect to enhance the porosity of the additively manufactured packing structure. This would lead to a reduction in specific pressure drop. Therefore, advances in the manufacturing process are necessary to avoid high thermal tensions in the material. Additionally, design measures within the structure are necessary if a direct connection of the packing to the column wall is desired. Avoiding enhanced liquid wall flow is possible by effectively leading the liquid from the wall back into the packing and simultaneously avoid influencing the upstreaming gas. AM can provide the design flexibility that is necessary for this task.
Acknowledgements
The authors would like to thank Michael Schultes from Raschig GmbH for providing information on the geometric data for the Raschig Super-Pak 350Y and Giang Do as well as Christoph Hiller from Evonik Operations GmbH for their support within this study. The authors acknowledge financial support from the Research Department Closed Carbon Cycle Economy located at Ruhr University Bochum. Open access funding enabled and organized by Projekt DEAL.
Symbols used
-
- a [m2m−3]
-
specific surface area
-
- d [m]
-
diameter
-
- Fv [Pa0.5]
-
gas load factor
-
- hL [m3m−3]
-
liquid holdup
-
- H [m]
-
height
-
- He [Pa−1]
-
Henry coefficient
-
- HTU [m]
-
height of transfer unit
-
- HETP [m]
-
height equivalent to a theoretical plate
-
- m [–]
-
slope of the equilibrium line
-
- NTU [–]
-
number of transfer units
-
- Δp [Pa m−1]
-
specific pressure drop
-
- uL [m3m−2h−1]
-
liquid load
-
- s [µm]
-
thickness
-
- T [K]
-
temperature
-
- x [–]
-
liquid phase mole fractions
-
- y [–]
-
gas phase mole fractions
-
- ε [%]
-
porosity
Sub- and Superscripts
-
- B
-
bottom of the column
-
- C1
-
humidifier column C1
-
- C2
-
test column C2
-
- E
-
single packing element
-
- OL
-
overall liquid side
-
- P
-
packed bed
-
- T
-
top of the column
Abbreviations
-
- AM
-
additive manufacturing
-
- IC
-
inorganic carbon
-
- RPB
-
rotating packed bed
-
- RSP
-
Raschig Super-Pak
-
- SLM
-
selective laser melting
-
- TOC
-
total organic carbon
-
- TPMS
-
triple periodical minimal surface