Challenges and Opportunities to Enhance Flexibility in Design and Operation of Chemical Processes
Abstract
Flexibility receives increased interest in chemical engineering and is discussed as one measure to deal with upcoming challenges for the chemical industry. In this paper, different types of flexibility are presented, and flexibility needs are illustrated. The focus is on the evaluation and classification of available solutions to enhance flexibility. Solutions and future challenges across all length scales of chemical engineering are discussed: from tailored catalyst properties to decoupling of processes by means of storage.
1 Introduction
Reducing greenhouse gas emissions is one of the greatest global challenges for the coming decades to prevent a further rise in the global temperature level and, thus, mitigate the consequences of climate change 1. To achieve this, measures have recently been enacted at both national 2 and European 3 levels.
Thus, in the long term, the chemical industry is facing enormous challenges: handling fluctuating energy supply from renewable sources, increasing energy efficiency in existing and new plants, reduction of greenhouse gas emissions, and processing of alternative bio-based or recycled feedstock.
A combination of many different methods and measures is necessary to adapt to the named challenges 4-8, whereas enhanced flexibility in production can be one option. While Ausfelder et al. 9 carry out a comprehensive cross-industry analysis regarding flexibility options of the raw material industry, the focus of this article is on the chemical industry and its processes and equipment.
Therefore, this article is organized as follows: Sect. 2 gives an overview on the term flexibility and associated types of flexibility as well as related tasks for chemical engineering. Subsequently, in Sect. 3, possible solutions that are discussed in the literature are classified with relation to the relevant chemical engineering scales. In Sect. 4, these scales are taken up again and future challenges for consistent further developments in this area are derived.
2 Flexibility Types and Flexibility Needs
Flexibility is gaining increasing attention in chemical engineering 10. Anyhow, no consistent definition is available and motivations to deal with that term differ tremendously. Therefore, first, an overview on available flexibility types is given before specific flexibility needs are derived. In addition to the needs, specific engineering tasks are derived to comply with aforementioned challenges.
2.1 Flexibility Types
The subject of flexibility has been dealt with in process engineering since the 1980s. The first considerations on this topic go back to Grossmann et al. 11. In the German literature, there is an article by Gruhn and Fichtner from 1988 in which the subject of flexibility and possible types of flexibility are discussed in detail 12. The named work is mainly dealing with the flexibility of continuously operated plants. Further definitions are identified with regard to the operation of multi-purpose plants 13. Most of the more recent definitions and considerations, however, arise from the increasing importance of modular plants as a research topic 14-17. In general, the various authors deal with several types of flexibility, resulting in a whole series of different definitions over the decades. Not all types of flexibility are directly related to the operation of process equipment and processes. Modular process engineering in particular has led to more superordinate types of flexibility such as innovation flexibility 16 or relocation flexibility 17.
Tab. 1 provides an overview of the types of flexibility discussed in literature having a specific definition and relates them to the underlying plant type. The analysis of the flexibility types and the corresponding definitions shows that there is a large number of flexibility types that are dealt with for the different plant types. A more detailed analysis of the available definitions shows that, although the types of flexibility are named differently, similar process variables are covered by the different definitions. This applies above all to flexibility in capacity, which is, e.g., addressed by the type capacity flexibility, expansion flexibility, load flexibility, and volume flexibility. Bruns et al. 10 present a detailed analysis of the flexibility definitions and an approach to harmonize them for chemical engineering.
|
Flexibility type |
Plant type |
|||||||||||||||||
---|---|---|---|---|---|---|---|---|---|---|---|---|---|---|---|---|---|---|---|
Assortment flexibility |
Capacity flexibility |
Energy flexibility |
Expansion flexibility |
Feedstock flexibility |
Innovation flexibility |
Load flexibility |
Location flexibility |
Operational flexibility |
Parameter flexibility |
Process flexibility |
Product flexibility |
Relocation flexibility |
Structural flexibility |
Time flexibility |
Volume flexibility |
Mono plants |
Multi-Purpose plants |
Modular plants |
|
1983 11 |
|
|
|
|
|
|
|
|
X |
|
|
|
|
|
|
|
X |
X |
|
1988 12 |
|
X |
|
|
|
|
|
X |
|
X |
|
X |
|
X |
|
|
X |
X |
|
2006 13 |
X |
X |
|
|
|
|
|
|
|
|
|
|
|
X |
|
|
|
X |
|
2013 14 |
|
|
|
X |
|
|
|
|
|
|
|
|
|
|
|
X |
|
|
X |
2015 16 |
|
X |
|
|
X |
X |
|
X |
|
|
|
X |
|
|
|
|
X |
|
X |
2016 17 |
|
X |
|
|
|
|
|
|
|
|
X |
|
X |
|
|
|
|
X |
X |
2016 15 |
|
|
|
|
|
|
|
|
|
X |
|
|
|
|
X |
|
|
|
X |
2018 18 |
|
|
|
|
X |
|
X |
|
|
|
|
|
|
|
|
|
X |
|
|
2019 19 |
|
|
X |
|
|
|
|
|
|
|
|
|
|
|
|
|
X |
|
|
2.2 Flexibility Needs
Taking the above-mentioned future challenges for the chemical industry, transition of the energy system, reducing emissions of greenhouse gases, increasing energy efficiency, and changing feedstock into account it becomes obvious that only specific flexibility types are of high importance. Additionally, it is noteworthy that for these challenges high leverage can be expected from measures for energy-intensive, large-scale, and continuously operated plants. Therefore, the focus is on these plants when possible solutions are classified. In addition, processes being able to enhance cross-industrial coupling are of high relevance, e.g., Power-to-X (PtX) processes. Here, flexibility needs arise from changing boundary conditions for chemical production in the future. These needs are exemplified in Fig. 1 showing the relative power profile of a wind turbine (Pel(t)/Pnominal) over three days. This profile indicates that there is a need for enlarged operating windows and rapid transitions between different operating points. The first need is associated with a high capacity flexibility whilst the second need demands fast dynamics. These dynamics additionally include start-up as well as shut down that can be interpreted as time flexibility for continuously operated plants.

To adapt to bio-based or recycling-based feedstock additionally implies the need for feedstock flexibility, meaning handling varying feedstock compositions. This is necessary because bio-based mixtures, e.g., might be poorly specified and their composition often underlies local conditions. The same applies to material flows intended for material recycling in terms of a circular economy.
Building upon the hypothesis that flexible plants rely on flexible unit operations and chemical reactors, transferring this need for flexibility leads to a number of specific engineering tasks. These tasks differ whether reaction or separation takes place and whether a free phase interface (gas-liquid, liquid-liquid) or a solid phase interface (gas-solid, liquid-solid) is present. If there is a free phase interface present, the hydrodynamics within the apparatus is of main interest. For safe operation, stable flow conditions with varying gas and liquid loads are then a central task. In case of solid phase interfaces, the focus is on the solid with its properties. Here, activity and stability of the solid, e.g., a catalyst or a membrane, needs to be independent of operating point. Thus, measures to fulfill these purposes are needed to enhance flexibility of unit operations, chemical reactors, and the overall plants. The solutions available from literature are discussed in the subsequent Sect. 3.
3 Classification of Solutions to Enhance Flexibility
To increase the flexibility of unit operations and plants, various solutions are discussed in the literature. These solutions concern all relevant length scales with regard to the magnitude of the phenomena occurring in chemical engineering: from the course of the reaction on the catalyst particle surface to the interdependencies of the interconnected plants at one site. Fig. 2 gives a classification on the solutions assigned to the different length scales. Due to overlapping, this classification is not meant in a clear-cut manner. Hence, it is merely intended to provide orientation. The following discussion takes place along the shown technical levels linked to the scales.
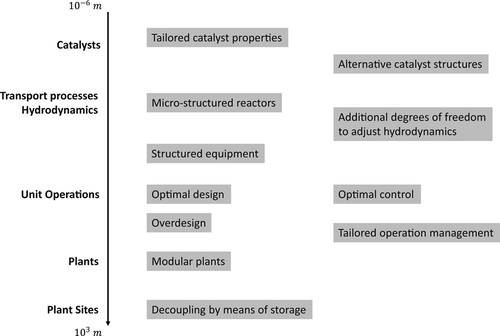
3.1 Catalyst Level
In general, the different phenomena occuring around the catalyst particle during dynamic operation of the chemical reactor are not yet fully understood 21. Therefore, the aspects discussed in the following do not primarily focus on influencing these individual phenomena but rather on adapting the catalyst properties to allow for an improved flexible operation.
Therefore, Zimmermann et al. 22 present an optimization-based approach for the example of the methanation of carbon dioxide (CO2). The reaction is highly exothermic and, thus, possesses a high thermal sensitivity. Due to its relevance for Power-to-Gas (PtG) processes, it is addressed in many of the studies described below. The bottleneck of this reaction lies in the removal of the heat of reaction, while at the same time too high temperatures have to be avoided to prevent deactivation of the catalyst. For this reason, Zimmermann et al. are investigating different catalyst designs. In their study, the particle porosity, the particle tortuosity, and the catalyst activity are varied and three scenarios for the determination of the optimal properties are considered: constant values for the entire particle, division of the particle into two zones of constant but different values, and particles with radially variable properties. The aim is to determine optimal catalyst properties for these three scenarios while maximizing the CO2 conversion and comply with the temperature limits of the catalyst. As a result, particles with two zones of constant properties show the best performance for flexible operation. In addition to high conversions at varying inlet velocities, the reactor-catalyst system for this case shows low thermal sensitivities as well as fast start-up and shutdown.
A similar approach, the improvement of the dynamic behavior by influencing the catalyst properties, is pursued by Fache et al. 23 for the same reaction system. The authors consider catalyst dilution along the longitudinal axis of the reactor to achieve high and constant yields even with varying feed flow rates. For this purpose, the fixed-bed reactor is divided into two zones with different mass fractions of active catalyst particles per reactor volume. The results show that by increasing the ratio of active catalyst particles in the second reaction zone, improved overall yields can be achieved for all feed flow rates investigated. Furthermore, the effect of magnetic induction in the second reactor zone is investigated. The aim of this additional measure is to mitigate negative effects on the temperature profile and, thus, the yield of the reaction.
The aforementioned approaches both refer to the use of spherical catalyst particles in the fixed bed. In contrast, Kiewidt et al. 24 propose the use of monolithic foams as alternative catalyst support structures for CO2 methanation. Due to better heat transport properties of the monolithic foam structures, it is expected that less critical temperature profiles occur. This expectation is verified by experimental and modeling studies. At the same time, the authors show that it is necessary to consider the layer of active catalyst material on the foam structures in the modeling explicitly. Furthermore, a comparison with experimental data shows that quasi-homogeneous reactor models restrict the identification of limiting transport processes.
Ratchahat et al. 25 follow a similar approach, in which they apply the catalyst to different honeycomb support structures. In experimental work, different arrangements of these catalyst support structures are investigated, which are manufactured in narrow segments. The segments are arranged one behind the other with different angles of rotation to achieve a better dispersion of the gas phase. Alternating arrangements of segments with and without coatings of active catalyst materials are also investigated. In this case, the uncoated segments serve as static mixers. Among other parameters, the heat transport properties and the reaction rates of the different arrangements are investigated. The results show, especially for the alternating arrangement, that only small hot spots appear at high yields and high feed rates.
3.2 Transport Processes and Hydrodynamics
Another possibility to increase the heat transfer performance for highly exothermic reactions is the use of microstructured reactors. These have a comparatively large surface-to-volume ratio and, thus, a particularly high potential for targeted reaction control. Consequently, these reactor concepts offer potentials to be implemented if dynamic operation is intended.
Kreitz et al. 26 are investigating a microstructured reactor concept for the methanation of CO2. The reactor is based on the concept of a plate heat exchanger with finned surface. Using a one-dimensional, heterogeneous model, the system response to a periodic change in feed composition is investigated. The frequency of this periodic change is varied on the one hand and the amplitude on the other hand. The results show that the investigated reactor concept is only conditionally suitable for a periodic operation of changing feed compositions. Especially for low frequencies, high hot spot temperatures are observed, which can lead to catalyst deactivation. At high frequencies, the hot spot is much less pronounced, but less methane is produced. In further work, it should be investigated whether the reactor concept shows more advantageous properties for varying feed flow rates.
Loewert et al. 27 investigate microstructured reactor concepts for the decentralized production of Fischer-Tropsch fuels from renewable hydrogen and CO2, which are in addition characterized by good scalability 28. In experimental studies, the authors were able to couple the operation of the reactor with the profile of a photovoltaics plant directly. Thus, the reactor concept is able to cover a comparatively large operating window without any loss of product quality or any negative effects on the catalyst. In addition, a significantly higher yield can be achieved for this reaction using a microstructured reactor, which makes further purification of the reaction products much easier. Experimental results also indicate that changes in feed composition, namely, the ratio between hydrogen and carbon monoxide, have no significant effect on product qualities.
For separation equipment, hydrodynamics is usually much more limiting than heat dissipation. This applies in particular to separation equipment in which mass and heat transfer takes place at free phase interfaces between gas and liquid. Consequently, the measures described in the literature to increase flexibility aim to specifically influence the hydrodynamics in the unit operation. One way to achieve this is to integrate additional degrees of freedom for adjusting the hydrodynamics within the apparatus.
This additional degree of freedom is available in rotating packed beds (RPBs) by the rotational speed. The capacity of the RPBs is additionally influenced by this parameter and operation in the centrifugal field leads to an intensification of heat and mass transfer within the apparatus and, thus, to a reduction of the needed equipment volume 29. Sudhoff et al. 30 investigate the influence of different design and operating parameters on the flexibility of RPBs for distillation. The authors focus on the investigation of different feed compositions. Results show that fluctuations in feed composition can be compensated by the specific design and operation of the RPB.
Reitze et al. 31 investigate a different degree of freedom in order to influence the hydrodynamics of a separation device. The authors propose a modular wetted-wall column for distillation, which possesses an adjustable inclination angle as additional degree of freedom. The inclination angle of the wetted wall influences on the one hand the film thickness of the liquid on the inclined plate and on the other hand the residence time of the liquid phase. In addition, the pressure drop is influenced by the inclination angle and simulation studies show that it decreases as the inclination angle approaches the horizontal. At the same time, only a slight influence of the mass transfer performance in terms of height equivalent of the theoretical plate (HETP) by the inclination angle is observed.
While the use of RPBs in industry is still restrained and the wetted-wall column described is designed for processing fine and specialty chemicals, a large part of industrial separation tasks is performed in conventional columns. Therefore, it is necessary to design suitable concepts for this type of equipment as well. This is particularly relevant as capacity, geometry, and hydrodynamics are dependent on each other. A variation in throughput is limited by the hydrodynamic phenomena that occur, e.g., weeping, entrainment, or flooding, the occurrence of which in turn is influenced by the design parameters of the column and trays. Consequently, it is necessary to break up these dependencies and, thus, increase the operating window of conventional columns.
One way to achieve this is to divide the column into hermetically sealed segments that do not allow cross-flow of gas and liquid. Based on a patent for batch distillation 32, Riese et al. 33 transfer this concept to continuous distillation. Steady-state simulations for this concept show that the operating window can be more than doubled by this design measure. At the same time, dynamic simulation studies show great potential to reduce start-up times 34. This is due to the additionally available degrees of freedom, which make it possible to start up individual segments with a predefined temperature and concentration profile. To implement this approach, a first important step is the hydrodynamic characterization of this novel column design. Fasel et al. 35 propose a corresponding concept.
The concept of segmentation is also pursued by Biegger et al. 36 and applied to the previously discussed methanation of CO2. In this case, the methanation reaction is carried out in a monolithic reactor. By using a monolithic reactor, cross mixing of the gas phase throughout the segments is prevented. Additionally, monolithic structures can be divided into individual segments easily due to their geometry. Another aim here is to extend the operating window and to achieve safe operation even with low gas loads.
3.3 Unit Operations
It is a matter of course that the levels catalyst, transport processes, hydrodynamics, and unit operations or chemical reactors cannot be considered independently of each other. However, the technical solutions discussed in this section primarily take up the level of unit operations. Thus, a classification on this scale is justifiable. The decisive factors at this level are, on the one hand, a tailored design and, on the other hand, appropriate control and operation strategies to enhance flexibility. Consequently, the solutions presented in the following paragraphs take up precisely these two points.
First methodological approaches to consider flexibility during the design stage of chemical reactors are available. These approaches are based on the concepts of elementary process functions 37. Maußner et al. 38 use this concept for a feedstock-tolerant design and Fischer et al. 39 for a capacity-flexible design of chemical reactors. The aim in each case is an optimal reactor design that can simultaneously meet the increased flexibility requirements. Maußner et al. are investigating the production of maleic anhydride from a butane-butene mixture. With the resulting optimal reactor design, it is possible to achieve high selectivities for a wide range of feed compositions 38. Fischer et al. are investigating the methanation of CO2 to integrate high capacity flexibility. For this purpose, critical dynamic states are already taken into account during the design phase. Thus, an optimal reactor can be operated safely in a large operating window 39.
Roh et al. 40 pursue an alternative approach to increasing flexibility through customized design for the example of chlor-alkali electrolysis. Here, flexible operation is realized by allowing a certain overdesign of the electrolysis cells. This approach is combined with the integration of several operating modes, as described by Brée et al. 41 and discussed in a subsequent paragraph.
In addition to new methods for designing unit operations, flexibility can be enhanced by new approaches for optimal control. Bremer et al. 42 show this for the example of CO2 methanation. The control strategy investigated aims at the extension and position of the main reaction zone. It is shown that stable operation for varying feed conditions can be achieved by specifically influencing the reaction zone with a tailored control scheme.
With regard to the operation of unit operations and chemical reactors, various approaches describe specific operation strategies to increase flexibility at the level of the individual equipment. Theurich et al. 43-45 investigate the influence of product recycling in CO2 methanation. While many authors investigate single-pass or multistage reactors for CO2 methanation, Theurich et al. propose a single-stage, adiabatic fixed-bed reactor with a product recycle loop. Based on the described concept, various systematic investigations are performed with regard to the operating window, transient states, and start-up. The results show on the one hand that adiabatic fixed-bed reactors with product recycling can be applied in a wide operating window 44 and on the other hand that the system response to varying feeds is weakened by the recycling loop, making the system less sensitive to changes 45. At the same time, the recycling quantity represents a further degree of freedom for dynamic operation. Iglesias Gonzales et al. 46, 47 pursue a similar approach for the CO2-based production of Fischer-Tropsch fuels. Here too, the recycling rate of the reaction products is used as a degree of freedom for reaction control to increase flexibility.
Electrochemical processes can play a particularly important role in meeting the challenges of energy system transformation, since electricity can be converted into chemical products directly. At the same time, electrochemical processes, such as water electrolysis and chlor-alkali electrolysis, are characterized by rapid dynamics 9. Nevertheless, solutions for flexible and economical operation are required in this context 48. For this reason, Brée et al. 41 propose flexible operation based on different operating modes for chlor-alkali electrolysis. Depending on the electricity price, it is switched between two operating modes. It is assumed that by using a bifunctional electrode and a cleaning cycle it is possible to switch between operation with a standard cathode and an oxygen depolarized cathode. The former is used when electricity prices are low. In this mode, hydrogen as a valuable by-product is produced additionally. The latter mode is used at times of high electricity prices with approx. 30 % less specific energy consumption. This ensures cost-optimized operation at varying electricity prices.
A flexible chlorine production consequently leads to the necessity of making the downstream processes, in which chlorine is used as feedstock, more flexible as well. This is in particular important as the storage of chlorine is very demanding in terms of safety. To avoid chlorine storage, Hoffmann et al. 49 propose to produce 1,2-dichloroethane directly from the variable chlorine stream. Therefore, the authors develop and validate a model for the column required. The aim of the model developed is to calculate all occurring operation points and the transition between these points with high reliability.
3.4 Plants and Plant Sites
Customized operation strategies can be a suitable approach to increasing flexibility not only at the unit operations level, but also with regard to plants or plant sites. Caspari et al. 50, 51 study an air separation unit with the aim of increasing the flexibility of the entire plant during operation. Due to the immense electricity consumption for compressing the gases, it can be advantageous from an economic point of view to link the operation of the plant to the fluctuating electricity price. For this purpose, the approach of different operating modes, which are switched depending on the electricity price, is pursued. For the example of the air separation unit, an additional liquefaction circuit for the nitrogen is investigated. This circuit is switched on when electricity prices are low. As the nitrogen for liquefaction has to be compressed, the energy consumption increases, but at the same time more product is produced at lower costs. If the electricity costs are high, this circuit is bypassed.
A process that is affected directly by the increasing relevance of volatile energy sources in the energy system is the separation of CO2 from power plant flue gases. On industrial scale, this is mainly realized by absorbing the CO2 with an aqueous monoethanolamine solution. Due to the increasing share of volatile energy sources, it is necessary to adapt the power plants in their electricity production to the demand. Consequently, the absorption process needs to be able to work with fluctuating flue gas quantities and compositions. One way to meet this challenge is to develop suitable control strategies for the entire process. Luu et al. 52 or Mechleri et al. 53 investigate this, for example.
Alternatively, various operating modes are conceivable for this process. For this purpose, Zaman et al. 54 are investigating the integration of a storage tank for the loaded monoethanolamine solution. In this way, the processes absorption and desorption are decoupled to a certain extent with regard to dynamics. According to Fig. 2, this is a further possible solution to enhance flexibility. In this way, the process or plant units, which have so far been less suitable for flexible operation, are decoupled from those that can be operated flexibly.
This approach is used in various studies to develop and evaluate solutions for storing renewable electricity in chemical molecules. Here, it is generally assumed that the hydrogen is made available as a reaction partner by means of a dynamically operated electrolysis. This hydrogen is then stored temporarily so that the subsequent synthesis can be operated at a steady state. This procedure is assumed for the production of methanol from hydrogen and CO2 55, 56, but also for the production of oxymethylene ether (e.g., 57) or Fischer-Tropsch fuels (e.g., 58).
Another way to increase the flexibility on plant scale is to use modular plants. Modular plants have the potential to contribute to increased flexibility for various reasons. One reason is the scaling concept of modular plants. The throughput can be adapted to requirements by simply numbering-up the modules or equipment 59, 60. At the same time, a high degree of standardization of the individual modules offers the possibility of changing the plant layout quickly and efficiently to suit new boundary conditions. This may not only concern the production capacity but also the product itself 61, 62.
The discussion of available solutions across the various relevant length scales of chemical engineering shows the manifold possibilities to enhance flexibility. A large number of the studies presented focus on capacity flexible operation by enabling wide operating windows. However, varying compositions of the feed streams are also of interest in some of the studies discussed.
Besides different length scales, different time scales play another essential role for flexibility considerations. Apart from the control layer that has already been briefly discussed in previous paragraphs, the scheduling layer needs to be considered. A prominent example of scheduling with respect to flexibility of a chemical engineering system is demand side management (DSM). Different processes from the chemical industry have already been investigated regarding their potential for DSM 63. As the goal of DSM is to adapt the operation of a plant according to electricity prices, suitable methods to account for time-variant production are necessary. Methods based on mixed-integer linear programming are commonly used in this area 63-65 to reduce computational efforts. Anyhow, as DSM demands for flexible operation, process dynamics are of high interest in this context. To account for nonlinear dynamic variables in scheduling, methods are proposed, e.g., based on chance-constraints 66 or moving horizon scheduling 67. Process dynamics are incorporated using scale-bridging models that link the scheduling and the control layer of the process. Alternatively, Schäfer et al. 68, 69 use wavelet transform to reduce the dimensionality of the scheduling optimization problem and simultaneously allow for global optimization. In addition, data-driven methods are also investigated to enable scale-bridging evaluation of time constants 70, 71 during scheduling for DSM. In contrast, Allman et al. 72 propose the integration of time-varying production into the design phase resulting in a scheduling-informed design approach.
4 Future Challenges
Considering the enormous challenges that are foreseeable for the future, the approaches outlined offer promising solutions. Nevertheless, there is still a number of challenges that must be taken into account for continuous development. Fig. 3 assigns the key challenges to the corresponding length scales discussed before. From Fig. 3, it is clear that the challenges are often present over several scales and that a clear assignment here is even more challenging than for the discussion in Sect. 3.
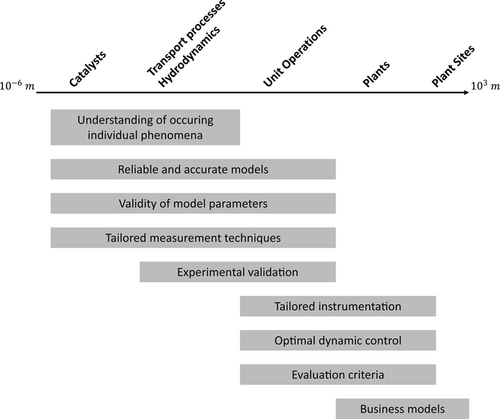
Even if the dynamic operation of process equipment and plants, with which a high degree of flexibility is inherently linked, is not a completely new task, not all individual phenomena are sufficiently understood. For heterogeneous catalysis, Kalz et al. 21 name some essential points that are of high relevance: understanding structural dynamics of catalysts and changes in surface properties under dynamic conditions, understanding influence of dynamics on the transport processes. Similar statements can be made for unit operations in which heat and mass transfer takes place at free phase interfaces. Here, too, it is important to understand the interaction between gas and liquid phase under varying operating conditions and the effects on heat and mass transfer.
It is also necessary to examine existing models for the prediction of, e.g., kinetics or overall system behavior critically, to determine whether they can be applied to the new boundary conditions. This applies from the description of dynamic microkinetic processes 21 to the continuous description of distillation columns under all operating conditions 49, 73 and their integration in flow sheet simulations 74. This is connected with the question of which model depths are adequate for which future task 75. Directly linked to this challenge is the question whether the required model parameters are valid for all addressed operating conditions.
The use of new measurement techniques can make a decisive contribution to all three of the above-mentioned challenges, i.e., the understanding of the individual phenomena, the existence of suitable models and model parameters valid for all operating conditions. Examples for all scales are available. For heterogeneous catalysis, investigation of the catalyst and pore structure from the nano- to the centimeter scale (e.g., 76, 77) or the measurement of temperature profiles with high spatial and temporal resolution in technical fixed-bed reactors for model validation 78 are prominent examples. Regarding multiphase flows, investigations from the scale of single bubbles (e.g., 79, 80) to the integral investigation of entire unit operation (e.g., 81-83) are presented in literature. The results show that the use of complex measuring techniques can provide valuable information about the occurring phenomena. Nevertheless, this additional information needs to be retrieved for flexible operation as well.
For many of the solutions presented in Sect. 3, experimental validation is currently lacking. In many cases, these are simulation studies, which are intended to show the potential of new approaches and concepts. Experimental validation is seen as a necessary next step by various authors. It would be reasonable to address the above-mentioned challenges in the implementation of experimental validation directly, thus, using innovative measurement techniques to obtain high-quality measurement data, preferably with high spatial and temporal resolution.
Irrespective of whether successfully validated new concepts or new methods for operation of conventional equipment are to be technically implemented, it is clear that, with flexible operation, the unit operations and plants are not only operated at an optimum operating point but in a large operating window. Therefore, it must be examined to what extent instrumentation of plants is needed to enable reliable plant control. To achieve this, it is necessary to implement this instrumentation in a cost-effective, safe, and low-maintenance manner. New evaluation algorithms for pattern recognition can also play a decisive role in the monitoring of plant conditions. As already mentioned, the system control is directly linked to the instrumentation.
Besides the technical challenges mentioned so far, there are numerous challenges for the evaluation of flexibility in chemical processes. In the field of modular plants, it has been shown that measures to increase flexibility can certainly lead to an economic advantage (e.g., 84, 85). Anyhow, for sector coupling by means of PtX processes and for already existing processes in the chemical industry, this assessment is not as clear-cut. One reason for this is that conventional evaluation parameters and key performance indicators fall short. Although there are a number of different flexibility indices for evaluation 86, their application is based on the solution of complex optimization problems and is limited, among other things, when considering systems that cannot be completely differentiated or are very large. Anyhow, new approaches are under investigation, e.g., to enable applicability of flexibility analysis to high-dimensional systems 87 or to perform flexibility analysis using machine learning tools 88. At the same time, economic business models and incentives, e.g., for providing flexibility not only in the short term, are often missing 89, 90.
Lastly, a major challenge is the integration and consideration of several of the aforementioned scales in future developments, thus using scale-bridging methods to identify holistic solutions. Anyhow, scale-bridging analysis and optimization of chemical engineering systems is a sophisticated task, even if flexibility is not explicitly considered. So far, only a few methods are available to deal with this challenge. Recent work uses, e.g., artificial neural networks to set up a surrogate model enabling multi-scale optimization exemplified with a membrane process 91 or thin film growth processes 92. Other solutions proposed to deal with multi-scale problems are model reduction methods or surrogate modeling approaches to reduce computational effort for complex nonlinear systems to allow for efficient control and scheduling 93-96. Some aspects concerning the above-mentioned challenges are expected to be treated using machine learning methods in chemical engineering in the future 97.
5 Conclusion and Outlook
The energy system transformation and latest political decisions to fulfil the Paris Agreement impose additional challenges on the chemical industry. These challenges are accompanied by increasing relevance of cross-industrial symbiosis, e.g., between power industry and chemical processes. Altogether, this leads to altered boundary conditions for production. To comply with this, a combination of various measures is necessary. One possible measure is to enhance the flexibility of the processes.
Various authors propose concepts to enhance flexibility on all relevant length scales of chemical engineering. The measures proposed mainly aim on enlarging the operating window of unit operations, chemical reactors, and processes and on accelerating transitions between steady-state operating points. Therefore, new design methods, e.g., for catalysts or chemical reactors, and operation modes, e.g., for unit operations or plants like air separation units, are discussed and show promising results. Furthermore, the time scale needs to be regarded if flexible operation is considered. Especially for DSM, new methods are developed to cope with process dynamics explicitly.
Despite the presented achievements across all scales, there are still challenges and questions left to be overcome in the future. In particular, this addresses the understanding of individual phenomena and processes along all length scales. This knowledge can then be used to develop accurate models for design and scale-up under dynamic conditions. The implementation of innovative measurement techniques and process instrumentation is supportive here. On a larger scale, questions regarding economic benefits and evaluation criteria for enhanced flexibility need to be solved to ensure successful technical implementation. Lastly, methods that link all scales need to be developed to generate a scale-bridging framework to incorporate flexibility in plant operation.
Acknowledgements
The authors acknowledge the financial support by the Federal Ministry of Education and Research, Germany in the project TransProMinC (project number 01LN1712A). Open access funding enabled and organized by Projekt DEAL.
Abbreviations
-
- DSM
-
demand side management
-
- HETP
-
height equivalent of a theoretical plate
-
- PtG
-
Power-to-Gas
-
- PtX
-
Power-to-X
-
- RPB
-
rotating packed bed
Biographies
Julia Riese received her diploma in Environmental Engineering and her Ph.D. in Mechanical Engineering at Ruhr-University Bochum. She is now research group leader at the Ruhr-University. In her research, she focuses on the flexibility of chemical and thermal engineering systems by means of modeling, simulation, and experimental investigation.
Marcus Grünewald studied Chemical Engineering at the Technical University Dortmund and received his Ph.D. in 2000. After postdoctoral research, he habilitated at the chair of Prof. Agar. From 2004 until 2009, he worked at Bayer Technology Services in Leverkusen (Germany) in the groups of Reaction Technology and Conceptual Design. Since 2009, he is head of the Laboratory for Fluid Separations at the Ruhr-University Bochum. He focuses on modular process technology, microtechnology, and multiphase applications.