Nonuniform Corrosion in the Vertical Direction of Q345 Steel in a Real Ocean Environment
Abstract
The aim of this investigation was to study nonuniform corrosion in the vertical direction of Q345 steel in the South China Sea. First, a metal corrosion monitoring system was designed and applied based on the coulometer principle and array electrode technology. Then, through coulometer testing, weightlessness analysis, electrochemical testing, and surface morphology observation, the corrosion behavior of Q345 steel used in an offshore wind turbine in Zhanjiang Bay in the South China Sea was studied. The results revealed that within the first 30 days of the experiment, the array electrodes connected by electricity exhibited sacrificial anode/cathode protection with self-coupling. Therefore, the corrosion rates of the electrodes were slowed. Between 60 and 120 days, the array electrodes underwent a transition in the anode/cathode region. In actual marine environments, the most severely corroded areas of long metal structures were near the sea surface and seabed and had to be prioritized for protection.
1. Introduction
Steel pipe piles have been increasingly used in the development of offshore wind power [1, 2]. However, in harsh marine environments, due to the inhomogeneity of the marine environment, steel piles undergo nonuniform corrosion [3–5]. Seawater corrosion is a complex process involving electrochemical reactions, ion migration, and metal dissociation [6]. Corrosive behavior in the sea accelerates material damage and metal corrosion, reducing the strength and durability of materials and thus increasing the risk of accidents [7]. Corrosion losses in China have been estimated to amount to about 3.4% of GDP, with marine corrosion making up almost one-third of those costs [8]. There are many factors that cause seawater metal corrosion, such as dissolved oxygen (DO), temperature, salinity, pH, and velocity of the seawater [9–11].
There are significant differences in the degree of corrosion depending on the location. According to different corrosion mechanisms, marine environments can be divided into the atmospheric, splash, tidal zone, and immersion zones [12, 13]. In general, the corrosion rate of steel pipes in the splash zone is 3–10 times higher than in other areas, which corresponds to an increase in structural defects in the middle of the steel member, weakening the stable load-bearing capacity of the structure [14]. There are many methods to judge the corrosion area of steel pipe pile, such as acoustic waves detection [15], electrochemical detection [16], magnetic memory [17], X-ray detection [18], and computer vision [19, 20]. Although all of the above methods can be used to detect to the corrosion degree of steel pipe piles, but the operation steps are cumbersome, expensive equipment or certain limitations, it is difficult to use on a large scale. Some scholars deployed a distributed optical fibre sensor beneath a simulated anticorrosion wrapping system to monitor the nonuniform corrosion of steel piles. In addition, these scholars established models of the nonuniform corrosion-induced mass loss of steel piles in marine environments [21]. Some scholar examined the corrosion characteristics of steel pipe piles in the East China Sea for approximately 5 years and summarized the overall nonuniform corrosion features of steel pipe pile walls [22]. A nonuniform corrosion distribution along the column height could be observed on corroded steel pipe piles in a marine environment, and the maximum corrosion depth in the splash zone could be 5 times greater than that in the full immersion zone [23]. In the research field of non-uniform corrosion, the current mainstream research method is to construct relevant models to study the corrosion situation [24–26]. However, this method has limitations and it is difficult to obtain the real-time corrosion information of metal.
Based on array electrode technology [27] and the Coulomb principle [28], the purpose of this research is to establish a new corrosion monitoring system that can be used to characterize the non-uniform corrosion of offshore wind power steels under natural environments, allowing for study the longitudinal and localized nonuniform corrosion characteristics of offshore wind power steels in marine environments, which is highly important for evaluating corrosion severity and ensuring safety.
2. Design and Working Principle of the Monitoring System
2.1. Monitoring System Design
The corrosion rates of large steels at different positions vary with depth because corrosion factors, such as temperature, DO, pH, hydrostatic pressure, and biological fouling, change with depth [29, 30]. By using the array electrode chain method, the distributions of surface potential and current in long-gauge metal structures at various locations can be assessed. In this study, two types of chain array electrodes—electrical connection electrodes (ECEs) and nonelectrical connection electrodes (NECEs)—are used. ECEs can simulate the corrosion behaviors of long metal structures in marine environments, and NECEs can reflect the influences of the corrosion environment. The design of the experimental device includes a single detachable electrode (a metal electrode and its shell), and the coulometer design is presented in Figure 1.
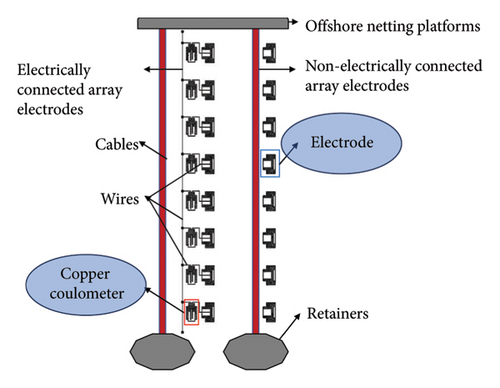
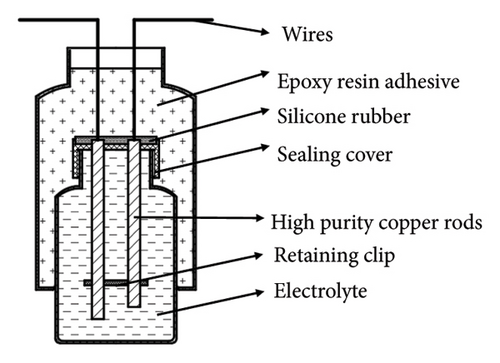
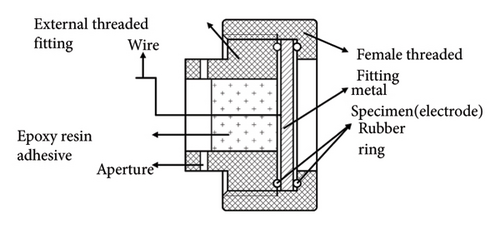
2.2. Principle of Galvanic Corrosion Monitoring by a Coulometer
A schematic diagram of the experimental device is shown in Figure 2. When the corrosion potential of the metal electrode is low, galvanic corrosion occurs, releasing electrons. The electrons flow through the wire to the coulometer and to a high-potential electrode. During the flow of electrons, those generated by corrosion first reach the surface of the copper rod of the coulometer and combine with the copper ions in the electrolyte, causing an increase in the weight of the copper rod. Moreover, in another coulometer, a copper rod loses electrons and undergoes an oxidation reaction. Finally, the electrons flow to the high-potential electrode. Therefore, the change in weight of the short copper rod in the coulometer can determine the polarity of the corresponding electrode; an increase in weight indicates an anode, while a decrease in weight indicates a cathode.
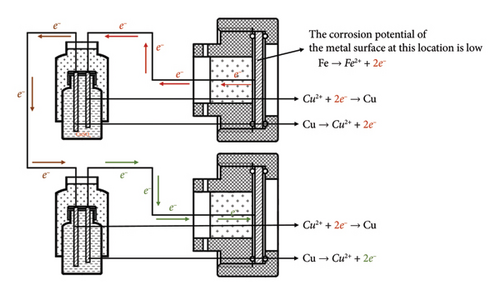
3. Materials and Methods
3.1. Material and Specimens
The Q345 low-alloy steel used in the present work was fabricated by Baosteel. The chemical composition (wt. %) of this alloy is listed in Table 1. All the samples were machined into circular specimens 76 mm in diameter and 5 mm in thickness. The #1000-ground samples were cleaned with anhydrous ethanol and acetone, air-dried, and placed in a drying box for later use.
Element | C | Si | Mn | S | P | Fe |
---|---|---|---|---|---|---|
Quality fraction | 0.16 | 0.35 | 1.34 | 0.11 | 0.22 | 97.82 |
3.2. Marine Environmental Exposure Experiment
The prepared marine environment metal corrosion monitoring device (in Figure 3(b)) was placed on a cage in Zhanjiang Bay at the coordinates N 21°16′7″, E 110°25′5″ for the exposure corrosion experiment in the marine environment, as shown in Figure 3(a). The sea water depth was approximately 13 m. In this study, chain array electrodes were used for coulometry, weight loss, electrochemical and morphology analyses on the 30th, 60th, and 120th days.
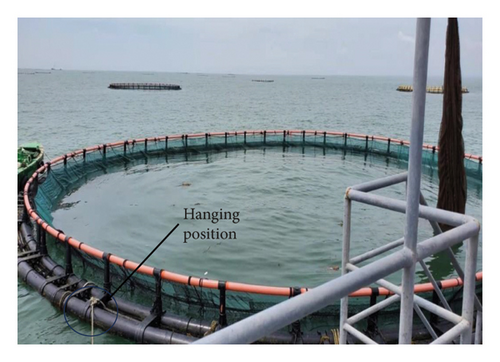
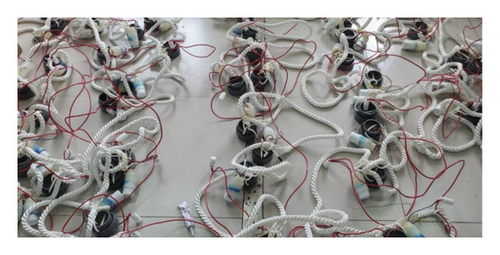
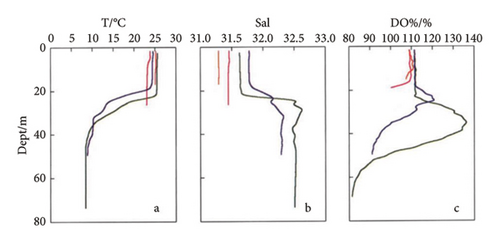
3.3. Calculation of Galvanic Corrosion
3.4. Total Corrosion Rate of the Q345 Steel Specimen
3.5. Electrochemical Characterization
The electrochemical impedance spectra and linear polarization curves of the Q345 steel specimens were measured by an AUTOLAB potentiostat. The specimens both used a three-electrode cell, the saturated calomel electrode was the reference electrode, the 2 × 2 cm platinum plate was the counter electrode, and an electrode from the regularly collected array was the working electrode. EIS was carried out under an OCP, and the amplitude of the AC excitation signal was 10 mV in the frequency range of 10−2 ∼ 105 Hz. After the EIS test was performed, the polarization curves were tested, and the linear polarization scan voltage range (vs. OCP) was ±10 mV with a scan rate of 0.1667 mV/s.
3.6. Morphology Observation
At different stages of the experiment, the macroscopic surface morphologies of the electrodes at each stage of variation were examined by a digital still camera (DSC). The microscopic corrosion morphologies of the electrodes were recorded by a super depth-of-field (SDM) method.
4. Results and Discussion
4.1. Corrosion Rates of the ECE and NECE
The weight loss rates of the Q345 specimens at different depths are shown in Figure 4. The weight loss rates of the electrically connected electrodes are much lower than those of the nonelectrically connected electrodes on the 30th day. In addition, nonelectrically connected electrodes have much greater fluctuation ranges than electrically connected electrodes. Because of the cathodic protection of the self-coupling sacrificial anode (Figure 5), the potential of the anode gradually increases, while the potential of the cathode gradually decreases until it reaches equilibrium, which effectively slows the initial corrosion rate. However, due to the long-term influences of harsh marine corrosion environments, the potential balance is disrupted, and the cathodic protection of the self-coupled sacrificial anode fails. In addition, the self-corrosion rate of the electrode decreases to a certain extent due to the large level of coverage of the barnacles. The self-corroded electrons are consumed on the surface of the metal electrode and not transferred to other electrodes; thus, the weight loss rates of the electric and nonelectric connections are similar on the 120th day.
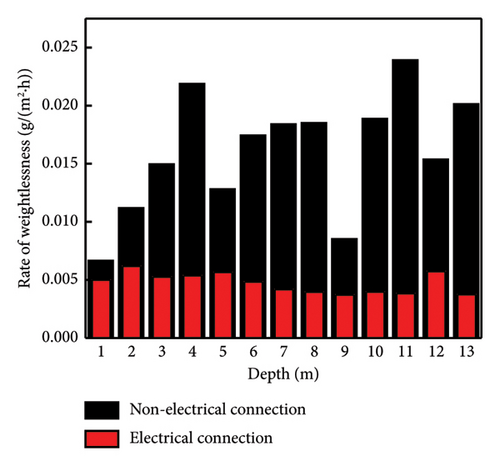
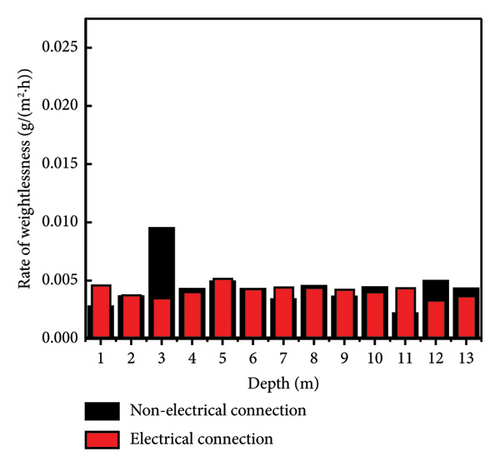
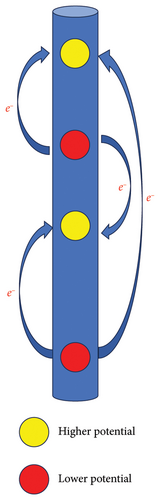
4.2. Electrode Anode/Cathode Transformation
According to the working principle of the galvanic corrosion monitoring device (Figure 2), the increase in weight of the copper rod represents the metal electrode connected to the copper rod as the anode, while the weight loss represents the cathode. As shown in Figure 6, the distributions of the cathode and anode phases on the 30th day indicate that the galvanic corrosion potentials are relatively heterogeneous. By the 60th day, the numbers of corroded cells increase in both the single cathode and anode zones, which is either a transitional stage of anode to cathode reversal or a process of conversion. On the 120th day of the experiment, the chain array electrodes complete the conversion of the cathode and anode zones, with the upper part becoming an anode zone and the middle part and lower part becoming cathode zones.
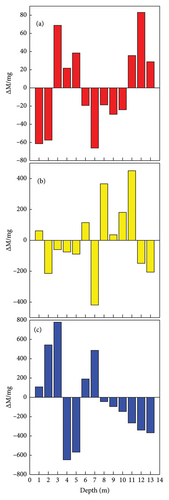
The macroscopic morphologies of the Q345 steel specimens are shown in Table 2. The rust product has a protective effect on the metal matrix, with large rust products present on the 120th day, providing protection to Q345 steel. Therefore, from the 60th day to the 120th day, Q345 steel undergoes an anode–cathode transition. Moreover, the macroscopic and microscopic morphologies after derusting are observed (Table 3). The numbers and densities of pitting holes at the upper and lower ends are the highest, and the corrosion degree of the middle part of the electrode is slightly lower than the degrees of the other parts, indicating that the anode/cathode transition is complete on the 120th day.
(d) | −1 m | −4 m | −7 m | −10 m | −13 m |
---|---|---|---|---|---|
30 | ![]() |
![]() |
![]() |
![]() |
![]() |
60 | ![]() |
![]() |
![]() |
![]() |
![]() |
120 | ![]() |
![]() |
![]() |
![]() |
![]() |
Depth | 30 DSC | SDM × 500 | 60d DSC | SDM × 500 | 120d DSC | SDM × 500 |
---|---|---|---|---|---|---|
1 | ![]() |
![]() |
![]() |
![]() |
![]() |
![]() |
4 | ![]() |
![]() |
![]() |
![]() |
![]() |
![]() |
7 | ![]() |
![]() |
![]() |
![]() |
![]() |
![]() |
10 | ![]() |
![]() |
![]() |
![]() |
![]() |
![]() |
13 | ![]() |
![]() |
![]() |
![]() |
![]() |
![]() |
4.3. Electrochemical Characteristics of Q345 Steel
As shown in Figure 7, on the 30th day, a cathodic protection effect occurs for the self-coupled sacrificial anode, causing the potential of Q345 steel to trend towards an average value. The corrosion potential of this sample exhibits the smallest fluctuation range. However, as time progresses, the cathodic protection effect of the self-coupling sacrificial anode gradually decreases. Furthermore, due to the transitions of the anode and cathode areas, the electrode surface accumulates self-corrosion products. In addition, galvanic coupling corrosion products accumulate on the electrode surface. When the corrosion products accumulate to a certain extent, they detach, causing the barnacles attached to the Q345 steel substrate to detach (Table 2). Moreover, barnacles have a protective effect on the substrate, delaying corrosion; hence, the late-stage corrosion potential fluctuation range is the largest, almost reaching twice that of the previous two periods. On the 30th day, with increasing seawater depth, the overall corrosion current density gradually increases. However, on the 60th and 120th days, the opposite trend is observed, and with increasing depth, the overall corrosion current density gradually decreases. During the first 30 days, barnacle growth is influenced by temperature, as temperature decreases with depth. Therefore, the degree of barnacle attachment is greatest on electrodes close to sea level, resulting in a low corrosion current. From the 60th day to the 120th day, the barnacle coverage reaches saturation, and DO becomes the dominant factor controlling corrosion. The DO gradually decreases with increasing depth. In seawater, oxygen acts as a depolarizer for metal corrosion. The higher the oxygen concentration is, the faster the corrosion rate and the greater the corrosion current [32].
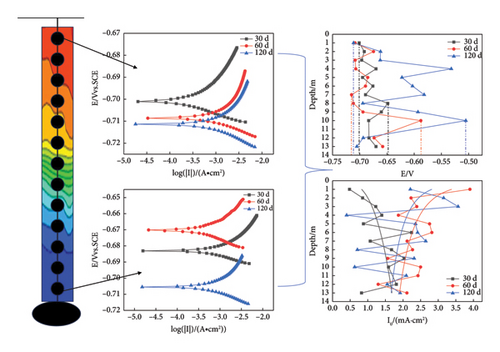
5. Corrosion Mechanism Analysis
The model of the corrosion mechanism of the steel with barnacle adhesion is depicted in Figure 8. On steel surfaces with barnacle adhesion, the diffusion of corrosive ions Cl-is hindered owing to the shielding effect [33–37]. Meanwhile, the oxygen concentration in the attached area of barnacle is lower, and oxygen concentrations are high at non-barnacle attachment sites, forming oxygen concentration difference batteries, which facilitate the formation and expansion of local corrosion pits in the marginal region of barnacle attachment [38]. After the formation of local corrosion pits, Cl-enrichment will occur in the pits, resulting in autocatalysis, which makes the pH value in the pits decrease continuously and the corrosion is further accelerated [39], which made the steel corrosion more serious.
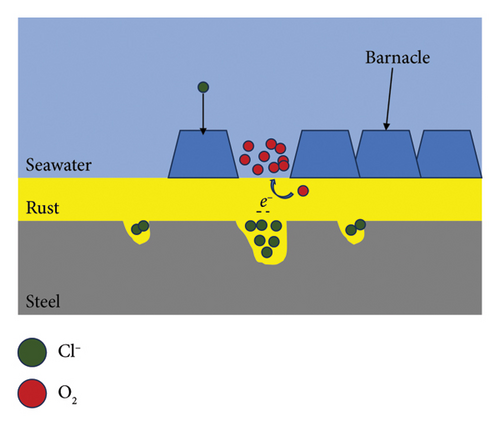
In the early stage of soaking, the high temperature of the upper layer of seawater helps the barnacle to adhere, so the corrosion rate of the upper layer electrode is the lowest. The Corrosion of Q345 was related to the concentration of oxygen in seawater. The higher the concentration of oxygen in the upper seawater, the faster the electrode corrosion rate was.
6. Conclusions
- 1.
The self-designed corrosion monitoring system for metal materials in marine environments can be effectively applied in actual marine environments and can effectively solve the problem of difficult galvanic current testing in actual marine environments. Long metal structures near sea level and at the bottom of the sea, which are the locations that experience the most severe underwater corrosion, should be prioritized for protection.
- 2.
During the whole experiment, galvanic corrosion occurs at each electrode of the electrical connection, the cathode and anode are alternately distributed during the first 30 days, and cathodic protection of the self-coupling sacrificial anode occurs at the electrode of the ECEs. The potentials of all electrodes gradually become uniform, and the rates of galvanic and natural corrosion decrease significantly. On the 120th day, the chain electrode completes the conversion of the cathode and anode areas.
- 3.
The primary controlling factor of Q345 corrosion is highly correlated with the degree of barnacle attachment. In the initial immersion stage, the closer the electrode is to the sea level, the higher the barnacle attachment degree and the smaller the corrosion current density. As the seawater depth increases, the corrosion current density exhibits a gradually ascending trend. When the barnacle attachment reaches a saturated state, the corrosion rate is governed by DO. With the augmentation of depth, the corrosion current density progressively decreases.
Conflicts of Interest
The authors declare no conflicts of interest.
Author Contributions
Jiezhen Hu: writing–original draft, methodology, and formal analysis. Huan Huang: data curation and conceptualization. Xin Hu: writing–review and editing and data curation. Peichang Deng: methodology and writing–review and editing. Guo Zheng: formal analysis. Jiahong Chen: investigation. Zhiwen Tu: investigation.
Funding
The authors are sincerely grateful for the financial support from the Natural Science Foundation of China (51801033), the Science & Technology Development Fundation of Zhanjiang (2022A01029), and the Postgraduate Education Innovation Project of Guangdong Ocean University.
Acknowledgements
The authors are sincerely grateful for the financial support from the Natural Science Foundation of China (51801033), the Science and Technology Development Fundation of Zhanjiang (2022A01029), and the Postgraduate Education Innovation Project of Guangdong Ocean University.
Open Research
Data Availability Statement
The data that support the findings of this study are available on request from the corresponding author. The data are not publicly available due to privacy or ethical restrictions.