Application of Tire Pyrolysis Oil as an Alternative Fuel for Internal Combustion Engines—A Literature Review
Abstract
Tire pyrolysis oil (TPO) has been recently used as an alternative to conventional fuels for internal combustion (IC) engines in order to satisfy some environmental and economic concerns. The main focus of this review is to shed light on the importance of TPO as an alternative fuel for IC engines. This paper systematically describes the TPO productions, composition, properties, and application methods in IC engines, such as binary blend, ternary blend, dual fuel mode, and spark ignition (SI) mode. The results indicate that blending TPO in diesel fuel deteriorates the engine performance and emissions, which can be improved by adding biofuels or nanoparticles. Dual fuel mode is a promising method to enhance the overall fuel quality and reduce nitrogen oxide (NOx) emissions. TPO blended with alcohols can serve as fuel in SI engines and the ratio of TPO is less than 25 vol.%. The TPO–diesel blend had better performance at each test engine load in terms of energy, exergy, and sustainability when the ratio of TPO is 10 vol.%. In conclusion, it can be said that TPO is an important factor from the viewpoint of both waste management and the protection of fossil fuel resource depletion.
1. Introduction
The rapid depletion of fossil fuels has underscored the pressing need to explore eco-friendly alternative fuel sources. As a result, considerable research efforts have been dedicated to finding ways to extract energy from waste materials, including nonbiodegradable materials such as industrial waste, agricultural waste, and waste rubber and plastics [1–3]. End-of-life tires (ELTs) are a global challenge with 1.5 billion waste tires produced yearly worldwide [4]. Many ELTs are being stockpiled or disposed of in landfills, which is a critical environmental issue as rubber is a synthetic polymer that does not biodegrade [5].
The utilization of the pyrolysis method has garnered increased significance in addressing this matter due to its capability to transform ELTs into an alternative fuel source and streamline the waste management process. Hence, it can be inferred that pyrolysis represents the optimal approach for repurposing ELTs into valuable byproducts, such as tire pyrolysis oil (TPO), pyro-gas, and pyro-char. This technology holds significant promise for harnessing energy from discarded tires [6]. TPO is a versatile fuel in a wide range of applications, such as powering internal combustion (IC) engines, fueling industrial furnaces, and generating electricity in power plants. It is composed of a blend of diverse hydrocarbons spanning from C5 to C20. TPO’s impressive energy potential brings about numerous advantages, including the potential for carbon dioxide (CO2) recycling, the reduction of greenhouse gas emissions, and a significant decrease in environmental pollution compared to the open-air burning of ELTs [7]. The large-scale production of TPO is becoming increasingly feasible due to a 2% annual increase in the global collection of ELTs. To meet the quality requirements for commercial fuel components, TPO is separated into three different fractions based on their boiling points. The initial fraction volatilizes at temperatures below 140°C, the subsequent fraction volatilizes within the temperature range of 140°C–200°C, and the final fraction volatilizes at temperatures surpassing 200°C [8]. To enhance the quality of TPO, a variety of sediment crushers and 2-ethyl-hexyl-nitrate from different brands are introduced to TPO at varying ratios. With a research octane number of 92.8, TPO demonstrates the potential to bring the light product fraction in line with gasoline specifications. Furthermore, the versatility of TPO allows for its blending with marine fuels, catering to the requirements of the shipping industry [9].
It is important to note that TPO cannot be directly used in IC engines. Some studies have highlighted certain drawbacks of TPO, such as high viscosity, high density, high sulfur content, and low cetane number (CN). Therefore, it is essential to modify and refine TPO before it can be used as an alternative fuel [10]. There are various ways to use TPO in IC engines. These include blending it with diesel or other biofuels like biodiesel, or vegetable oil [11–22], using a dual fuel mode with bio-gas or hydrogen [23–25], adding nanoparticles [26–29], or blending it with alcohol in a spark ignition (SI) engine [30]. The experiments were carried out using different engines, so it is important to consider that the results may not apply to all engines. Moreover, the variations in fuel properties and operating conditions have resulted in diverse outcomes concerning engine performance, emissions, and combustion characteristics.
Review studies have been conducted on the utilization of TPO in IC engines. However, most of these studies have centered on TPO–diesel blends in compression ignition (CI) engines. It is rare to find review papers that discuss the different modes of utilizing TPO in IC engines. Hence, this paper aims to investigate the potential application methods of TPO as an alternative fuel and assess its performance, emissions, and combustion characteristics. The paper is divided into several sections: Section 1. Introduction: This section provides an overview of the problem statement, objectives, and potential benefits of using TPO in IC engines. Section 2. Production, Composition, and Physicochemical Properties: In this section, the production process of TPO is the focal point of discussion. Furthermore, an analysis of its composition and various physicochemical properties, including kinematic viscosity, density, heating value, CN, and sulfur content, will be undertaken. Section 3. Application in IC Engines: This section analyzes engine performance with a focus on power output, fuel efficiency, emissions, and combustion characteristics to identify areas for improvement with different application methods. Section 4. Energy, Exergy, and Sustainability Analysis: This section evaluates the economic viability of incorporating TPO as an alternative fuel in IC engines. Section 5. Conclusions and scope of future work: Finally, some conclusions and recommendations are provided for future work.
2. Production, Composition and Physicochemical Properties
2.1. TPO Production
The disposal of ELTs presents a significant environmental challenge due to the intricate chemical and physical composition of tire material, rendering its recycling and recovery arduous. In response to escalating global apprehensions regarding environmental issues, diverse methodologies have been explored for the conversion of ELTs into valuable products [31]. Among these methodologies, thermal degradation techniques such as incineration, pyrolysis, and gasification have been investigated, among which the pyrolysis process is considered the most promising alternative for waste management, particularly due to its suitability for large-scale applications [32–34]. Pyrolysis is the chemical transformation of materials through thermal decomposition at elevated temperatures in an inert atmosphere. The primary objective of pyrolysis is to generate environmentally sustainable energy products while mitigating the emission of hazardous gases [35]. This technology serves as a primary method, enabling the separate upgrading of each product fraction, thereby significantly enhancing profitability.
Figure 1 depicts the system boundary for the treatment of ELTs through pyrolysis. The process commences with the collection and transportation of ELTs to the pyrolysis plant. Upon arrival, the ELTs undergo storage, shredding, and separation into their constituent parts: metals, textiles, and rubber. The shredded rubber is subsequently directed to the pyrolysis plant, where it undergoes a transformation process, resulting in the generation of three distinct products: pyrolysis gas, pyrolysis oil, and pyrolysis char. It has been indicated that the primary driver of economic value lies in pyrolysis oil. Consequently, various methodologies are being employed to procure higher-value pyrolysis oil. To enhance the cost-effectiveness of the pyrolysis process, the introduction of a catalyst holds the potential to mitigate the need for extreme operating conditions. Catalytic pyrolysis leverages catalysts to optimize product yields and tailor the composition or properties of specific products. Detailed catalytic conditions and the corresponding product yields for the pyrolysis process are outlined in Table 1.
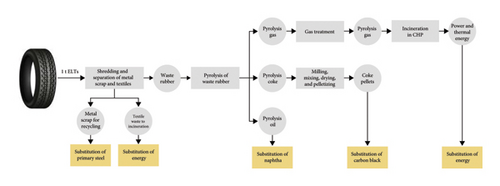
Catalytic type | Temperature (°C) | Catalytic rate | Yield (wt%) | Reference | ||
---|---|---|---|---|---|---|
Gas | Char | Liquid | ||||
HMOR | 500 | 13% | 11.90 | 46.30 | 41.80 | Dũng et al. [36] |
MCM-48 + 0.7% Ru | 500 | 25% | 26.00 | 46.00 | 32.00 | Witpathomwong et al. [37] |
KL | 500 | 25% | 13.00 | 43.00 | 44.00 | Muenpol and Jitkarnka [38] |
ZSM-5 | 500 | 1% | 6.49 | 37.86 | 55.65 | Arabiourrutia et al. [39] |
MgCl2 | 387 | 10% | 22.00 | 33.00 | 45.00 | Ahoor and Zandi-Atashbar [40] |
ZSM-5 + LBO | 430 | 5% | 9.30 | 42.70 | 48.00 | Qu et al. [41] |
CaC2 | 400 | 30% | 37.00 | 32.00 | 22.80 | Shah et al. [42] |
Perlite | 425 | 10% | 9.00 | 28.00 | 65.11 | Kar [43] |
HY-zeolite | 500 | 15 g | 2.50 | 35.70 | 61.80 | Aguado et al. [44] |
Al2O3 | 600 | 10% | 18.40 | 55.6 | 26.0 | Miandad et al. [45] |
CaCO3/OS | 500 | 1/30 | 30.00 | 25.00 | 45.00 | Kordoghli et al. [46] |
2.2. TPO Composition
The operating conditions of pyrolysis exert a significant influence on the compound distribution in the composition and the yield of TPO [47, 48]. Several researchers have documented the influence of tire pyrolysis temperature and heating rate on the elemental composition, oil yield, and the nature of compounds present in the TPO [49, 50]. Table 2 represents the effect of temperature on TPO types of compounds.
Pyrolysis temperature (°C) | 300 | 400 | 500 | 600 | 700 |
---|---|---|---|---|---|
Aromatics | 34.7 | 59.3 | 62.4 | 75.6 | 57.4 |
Aliphatics | 59.2 | 34.9 | 31.6 | 19.8 | 37.0 |
Nitrogenated | 4.5 | 3.7 | 4.2 | 2.6 | 3.8 |
Benzothiazole | 1.6 | 2.1 | 1.8 | 2.0 | 1.8 |
The integration of TPO in IC engines presents a significant challenge owing to its elevated levels of aromatic and unsaturated hydrocarbons, and sulfur content [51]. The predominant compounds identified are associated with aromatic compounds, primarily characterized by a single aromatic ring with alkyl substituents. Toluene and the mixture of xylenes exhibit the highest relative proportions. Substituted naphthalene and indene primarily account for the presence of heavier aromatic compounds. The prevalent aromatic composition and the significant presence of limonene and cymene have previously been documented in the literature [52]. During the analysis, it is observed that linear hydrocarbons, specifically alkanes and alkenes, are present in varying proportions. Notably, alkenes are found to predominate over alkanes. In addition to the primary hydrocarbons, sulfur-containing compounds and nitrogen-containing compounds are also identified, along with a small proportion of oxygenated compounds in the form of esters [53, 54].
2.3. TPO Properties
To determine whether TPO can be used in IC engines without additional treatment, its properties must be evaluated against that of fossil fuels. The crucial properties that must be met to consider TPO as an alternative fuel are density, viscosity, CN, sulfur content, etc. Table 3 contains information about the properties of TPO of the pyrolysis reactor.
Feedstock | Pyrolysis condition | Density @ 15°C (kg/m3) | Kinematic viscosity @ 40°C (cSt) | Heating value (kJ/kg) | Sulfur content (wt%) | Cetane number | Reference |
---|---|---|---|---|---|---|---|
Vehicle tire | 500°C | 945 | 3.80 | 43.34 | 0.90 | 44 | İlkılıç and Aydın [11] |
A mixture | Vacuum condition | 944 | 5.06 | 39.90 | 1.13 | — | Doğan et al. [12] |
Crushed tire | 300°C–500°C | 903 | 2.90 | 41.96 | 0.93 | 27 | Frigo et al. [51] |
Passenger car tire | 425°C | 992 | 6.52 | 42.70 | 1.46 | — | Kar [43] |
Passenger car tire | 520°C, 7 kPa | 950 | 9.70 | 43.70 | 0.80 | — | Roy et al. [55] |
Scrap tire | 450°C, vacuum | 941 | 2.87 | 41.90 | 0.97 | — | Wang et al. [56] |
A mixture | Slow pyrolysis | 910 | 6.30 | 42.10 | 1.45 | — | Williams et al. [57] |
Passenger car tire | 450°C–600°C | 935 | 3.20 | 42.83 | 0.95 | — | Murugan et al. [58] |
Granulated truck tire | 550°C | 832 | 3.13 | 42.32 | 1.10 | Şen et al. [21] | |
Used tire | 600°C | 850 | 5.18 | 42.72 | 0.035 | Osayi et al. [54] | |
Motorcycle tire | 330°C–550°C | 970 | 4.9 | 40.80 | 1.36 | Islam et al. [50] |
The density of engine fuel is a significant property that directly influences the energy content of the fuel as it enters the engine; however, fuel density does not show a significant influence on emissions from high-pressure common rail direct injection (CRDI) engines. An examination of TPO properties reveals that its density typically falls within the range of 903–992 kg/m3 [43]. The viscosity is a function of molecular weight and is not necessarily affected by the hydrocarbon class. The viscosity of TPO is usually in the range of 2.8–10 cSt, which is higher than that of diesel fuel, 1.3 cSt [55]. It is worth noting that TPO should be supplemented with alcohol or mixed with diesel fuel to reduce the viscosity [17, 18]. The heating value definitely signifies the heat of combustion, representing the precise amount of heat released when a specific quantity of fuel undergoes combustion under controlled conditions. On a mass basis, the heating value of TPO meets the specified range of 41–46 MJ/kg, with a defined specification of 42.5 MJ/kg. The sulfur content present in engine fuel has a direct impact on particulate matter (PM) emissions, as a portion of it undergoes conversion into sulfate particulates within the exhaust system. The sulfur content of TPO is higher than that of diesel fuel. However, blending TPO with diesel (or biodiesel) can solve this problem. Frigo et al. [51] discovered that benzothiazole is the primary carrier of sulfur from ELTs into TPO, while all other sulfur compounds in TPO are in the form of dibenzothiophenes. Previous literature suggests that TPO typically contains 0.2–1.5 wt% sulfur content [55]. CN is a crucial parameter that quantifies the fuel’s ability to ignite under specific engine conditions. A high CN signifies that the fuel undergoes rapid combustion after its injection into the cylinder, exhibiting a short ignition delay (ID) period. The low CN of TPO indicates the need for supplementation with a cetane improver or blending with diesel fuel. The low CN value can be attributed to the substantial presence of aromatic rings containing short side-chain molecules [59, 60].
3. Applications in IC Engines
TPO has attracted considerable attention due to its potential application as a fuel additive or direct fuel for IC engines, as evidenced in previous studies [61]. Vihar et al. [62] applied pure TPO in a turbocharged CI engine, demonstrating its effective utilization in non-intercooler CI engines under high load conditions. However, operating the engine without an intercooler was suboptimal, resulting in decreased engine efficiency, heightened temperature loading of the components, and elevated nitrogen oxide (NOx) emissions. Another study delved into the incorporation of pilot injection to enhance the thermodynamic parameters of a turbocharged intercooled diesel engine, facilitating effective operation at medium to high loads using pure TPO. Exhaust gas recirculation (EGR) combined with an injection strategy can extend the operating range of TPO [15]. The analysis of selected reviews has revealed that the utilization of TPO in CI engines often necessitates the use of cetane improvers, additional external energy, or higher compression ratios [63].
3.1. Blending With Diesel Fuel
To promote TPO adoption, the physical properties of TPO need improvement. Diesel fuel was often used to blend with TPO. In a study conducted by İlkılıç and Aydın [11], the utilization of varying concentrations of TPO in a CI engine was examined. The findings revealed that engine tests could be effectively executed without necessitating any engine modifications, provided that TPO was blended with diesel fuel at a maximum volume of 35%. Increasing the TPO concentration resulted in higher levels of carbon monoxide (CO), hydrocarbon (HC), sulfur dioxide (SO2), and smoke opacity. Doğan et al. [12] analyzed how different volumetric concentrations of TPO affected the performance and emissions of a CI engine. The findings revealed that as the proportion of TPO in the blends increased, there was a decrease in CO and HC emissions, while NOx emissions showed an increase. The introduction of TPO into diesel fuel did not significantly impact performance. Wang et al. [56] investigated the effects of mixing TPO with diesel fuel on cylinder pressure (CP), fuel consumption, engine power, and SO2 emissions in a direct-injection (DI) diesel engine. The results revealed that a higher proportion of TPO in the blend resulted in poor engine performance and increased SO2 emissions. In a study conducted by Zhang et al. [32], TPO–diesel blends were utilized in CI engines, with a comprehensive assessment of engine performance across varying engine speeds. The outcomes revealed that the introduction of a 20 wt% TPO blend with diesel fuel yielded negligible impact on engine performance and emissions. Frigo et al. [51] conducted a study to analyze the effects of utilizing fuel blends containing high proportions (20 and 40 vol.%) of TPO mixed with diesel fuel on a CI engine. The findings revealed that an escalation in TPO content resulted in decreased HC emissions but increased CO emissions under high engine loads. This trade-off was ascribed to extended ID, which was ultimately recognized as a constraining factor for fuels with exceedingly high TPO concentrations. Murugan et al. [58] mixed TPO with diesel fuel in different proportions and monitored the performance, emissions, and combustion characteristics of a CI engine. The experimental results indicated that the tested engine could operate with up to 70 vol.% TPO blended with diesel fuel. Using TPO reduced power output because TPO had a lower heating value than diesel fuel. The brake thermal efficiency (BTE) increased with higher percentages of TPO blends. The emissions of NOx were lower; however, HC and CO emissions were higher than diesel fuel, likely due to the presence of unsaturated hydrocarbons in TPO. Smoke emissions were also higher for TPO–diesel blends. The peak CPs were also higher at full load than those of diesel fuel. Longer IDs were observed for TPO–diesel blends, which resulted in a higher heat release rate (HRR) in the initial stages. The augmentation of the TPO fraction resulted in a postponement of the high-temperature reaction phase, attributable to TPO’s heightened viscosity and decreased volatility. This subsequently led to an increased proportion of fuel combustion during the premixed combustion phase. Hürdoğan et al. [64] found that the blends with the highest TPO content were too thick, affecting the engine performance. However, blends containing lower TPO content exhibited no significant changes in exhaust emissions compared to diesel fuel, except for a reduction in NOx emissions under high engine load conditions as the TPO fraction increased. It was concluded that adding 10 vol.% TPO to diesel fuel was the most efficient and environmentally friendly composition, as shown in Figure 2. Uyumaz et al. [65] thoroughly analyzed combustion characteristics for the blend consisting of 10 vol.% TPO and 90 vol.% diesel fuel. It was found that adding TPO led to a significant reduction in combustion duration (CD) and a notable increase in pressure rise rate. Shahir et al. [66] analyzed the performance and emissions of a CRDI diesel engine using blends of TPO ranging from 10 to 50 vol.% with diesel fuel. The engine tests revealed that the highest BTE was achieved for the TPO30. NOx and HC emissions were increased as the TPO fraction was raised.

Bodisco et al. [67] demonstrated that the impact of TPO on emissions is minimal under real driving conditions and well within the margin of error resulting from variations in the operating conditions of a diesel engine. Murugan et al. [68] observed that TPO–diesel blends exhibit a lower combustion temperature compared to conventional diesel fuel, resulting in reduced NOx emissions. However, an increase in TPO concentration within the blend is associated with elevated levels of HC, CO, SO2, and soot due to incomplete combustion [11]. In a study conducted by Pilusa [69], the performance and emission characteristics of a CI engine utilizing various blends of TPO with diesel fuel were examined. The experimental findings revealed that the performance of TPO–diesel blends compared well with diesel fuel in terms of torque and power output. Also, it was concluded that TPO10 blends can effectively be utilized in diesel engines without necessitating any engine modifications. Teoh et al. [70] compared the performance, emission, and combustion characteristics of a TPO–diesel blend in a CRDI diesel engine. The analysis revealed that the CP and HRR of the tested fuels are closely similar. The torque and brake power (BP) of the blend were greater than those of diesel fuel due to the higher heating value and oxygen content. It was determined that a blend with a 10 vol.% TPO was a suitable alternative fuel for diesel engines without requiring modification. Aydın and İlkılıç [71] tested the performance, emission, and combustion parameters of low-sulfur TPO and diesel blends in a CI engine. The analysis indicated that the CP and HRR values of the test fuels closely resembled those of conventional diesel fuel. However, there were slightly elevated levels of CO, HC, and smoke emissions, alongside reduced NOx emissions for low-sulfur TPO–diesel blends.
Martínez et al. [13] conducted an experiment in which they blended TPO with diesel fuel at a 5 vol.% and tested it in a CI engine. Figure 3 shows the comparison of specific gas emissions and PM emissions. The study’s findings indicated that the combustion of the TPO–diesel fuel blend led to elevated smoke emissions, which can be attributed to the higher concentration of aromatic compounds in TPO. These compounds are considered the precursors for soot generation. The heightened opacity correlated with an elevated boiling point and the presence of distillation residues of TPO. Furthermore, a comprehensive analysis of PM size distribution indicated that TPO significantly contributed to the generation of small-sized particles. Specifically, mitigating the sulfur content in TPO presented a formidable challenge, necessitating urgent attention to achieve reduced HC and PM emissions and to avert the catalyst poisoning due to sulfur content. Hossain et al. [72] conducted an engine experiment on a CI engine fueled with TPO–diesel blends. The blends demonstrated concurrent reductions in PM and NOx emissions when compared to diesel fuel. Specifically, the reduction in NOx emissions amounted to approximately 30%, while the decline in PM emissions varied between 35% and 60%. Additionally, CO levels increased by 10%. Interestingly, there was an insignificant change in BP, brake specific fuel consumption (BSFC), and BTE with the blends. Pote and Patil [73] conducted experiments on TPO–diesel blends using a CI engine. The experiments revealed that the highest increase in BTE was observed for the TPO90 blend, while mechanical efficiency peaked at TPO35. BSFC was lowest for the TPO10 blend at low load, but highest at TPO60. The findings also indicated that CO emissions decreased up to a moderate engine load, but consistently increased with higher engine loads. HC emissions decreased with higher proportions of TPO, reaching a minimum at TPO90. Moreover, NOx and smoke emissions gradually increased with a higher TPO proportion.
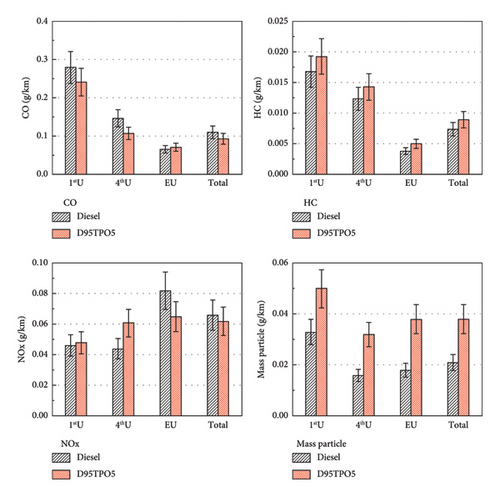
Table 4 summarizes major findings from research on TPO–diesel blend engines. Different studies have suggested varying ideal TPO–diesel fuel compositions for diesel engines. Additionally, conflicting trends in performance and emissions were observed across studies. These inconsistencies may arise from differences in operational conditions, TPO properties, and engine technologies affecting the mixture formation during the injection process. Overall, the results indicate that the TPO–diesel blend does not significantly improve engine performance compared to diesel fuel. The observed characteristics may be a result of the low oxygen content. Therefore, enhancing these attributes is possible by utilizing biofuels with higher oxygen content. Thus, several other groups of researchers turned their attention to blending TPO with biofuels.
Type of engine | Baseline | Blend | Performance parameter | Emissions parameter | References |
---|---|---|---|---|---|
6-Cylinder, turbocharged, engine | Diesel | TPO | IG▲CP▲HRR▲ | CO▲HC▲Smoke▼NOx▲ SO2▲ | Vihar et al. [62] |
4-Cylinder, turbocharged, CRDI engine | Diesel | TPO | IG▲HRR▲COV▲ | CO▲HC▲Smoke▲NOx▲ | Vihar et al. [63] |
4-Cylinder, CRDI engine | Diesel | Diesel-rapeseed oil-TPO | CP▲BTE▲ | CO▲HC▲NOx▲ | Mikulski et al. [19] |
Single-cylinder, DI engine | Diesel-TPO blend (10%) | BP▼BSFC▲ | CO▼HC▼NOx▲ | Frigo et al. [51] | |
Single-cylinder, DI engine | Diesel | Diesel-TPO | — | CO▲HC▲Smoke▲NOx▼ | Murugan et al. [58] |
Single-cylinder, naturally aspirated, DI engine | Diesel | Diesel-TPO | CP▲HRR▲BTE▼EGT▲ | CO▲HC▲Smoke▲NOx▲ | Murugan et al. [68] |
4-Cylinder, naturally aspirated, DI engine | Diesel | Diesel-TPO | BP▼BSFC▲ | CO▼NOx▼CO2▼ | Hürdogan et al. [64] |
Turbocharged, CRDI engine | Diesel | Diesel-TPO blend (10%) | CP▼HRR▲BP▲BTE▲BSFC▲ | CO▼HC▲Smoke▼NOx▼CO2▼ | Teoh et al. [70] |
Single-cylinder, DI engine | Diesel | Diesel-TPO blend (50%, 75%) | CP▼HRR▼BP▼BTE▼BSFC▲ | CO▲HC▲Smoke▲NOx▼ | Aydın and İlkılıç [71] |
4-Cylinder, turbocharged, CRDI engine | Diesel | Diesel-TPO (5%) | IG▲CP▲HRR▲BTE▼BSFC▲ | CO▼HC▲Smoke▲NOx▲PM▲PN▲ | Martínez et al. [13] |
6-Cylinder, turbocharged, CRDI engine | Diesel | Diesel-TPO | CP▼HRR▼BP = BTE = BSFC▲ | CO▲NO2▼NOx▼PM▼PN▼CO2▼ | Hossain et al. [72] |
Single-cylinder, DI engine | Diesel | Diesel-TPO blend + CeO2 | BTE▲ | NOx▲Smoke▼ | Kumaravel et al. [27] |
Single-cylinder, naturally aspirated, DI engine | Diesel | Diesel-TPO blend + Al2O3 | CP▼HRR▼BSFC▼BTE▲ | CO▼HC▼NOx▼ | Polat [28] |
4-Cylinder, naturally aspirated, DI engine | Diesel | Diesel-TPO + hydrogen (dual fuel mode) | BP▼BSFC▲ | CO▼NOx▼CO2▼ | Fırat et al. [24] |
3.2. Blending With Biofuels
Biodiesel’s poor oxidation stability necessitates the use of an antioxidant to meet storage requirements and ensure fuel quality for optimal performance. TPO contains some phenolic compounds that positively influence the improvement of oxidation stability when blended with biodiesel. The blend exhibited improved oxidation stability when 20 vol.% TPO was mixed with biodiesel based on volume [16].
Sharma and Murugan [17] conducted a study on the performance, emission, and combustion behaviors of a CI engine fueled with the blends of jatropha methyl esters and TPO at different compositions. The researchers observed that when the engine operated with fuel containing more than 20% TPO, the emissions and combustion characteristics deteriorated, resulting in a reduction in BTE at full engine load. The ignition of the blends with 10 and 20 vol.% TPO content occurred 1 crank angle (CA) earlier than that of diesel fuel at full engine load due to the higher oxygen content and CN of esters compared to diesel fuel. Additionally, HC, CO, and smoke opacity were lower than diesel fuel, while higher NOx emissions occurred. The authors suggested that a 20 vol.% addition of TPO was the optimal fuel composition. Nursal et al. [18] demonstrated the impact of TPO blending concentrations on the ID. Shorter ID values indicated better fuel combustion quality and efficiency. However, the findings on the blends indicated a marginal increase in ID at concentrations of 10 and 20 vol.%. This phenomenon can be attributed to the protracted duration necessary for thermal cracking of the high molecular weight fuel during the chemical response process. Sharma and Murugan [14] explored how adjusting the compression ratio of a diesel engine affects its performance when using a blended fuel consisting of 80 vol.% biodiesel and 20 vol.% TPO. The findings revealed that, when operating at a higher compression ratio of 18.5:1 and full engine load, the blend demonstrated a reduced ID, elevated maximum CP, and an augmented HRR in comparison to the original compression ratio. This increase in compression ratio also improved the BTE by approximately 8% at full engine load. In addition, the blend emitted about 10.5% less CO, and 32% less HC, and had a 17.4% reduction in smoke opacity compared to the original compression ratio.
Koc and Abdullah [74] conducted a study on the impact of biodiesel and TPO additives on diesel fuel in a diesel engine. The analysis of emissions from a diesel–biodiesel and diesel–TPO binary blend, and a diesel–biodiesel–TPO ternary blend showed that ternary blends resulted in lower NOx emissions. In addition, the combustion of the ternary blend yielded lower CO emissions in comparison to the binary blend. A key inference drawn was the potential of TPO addition to fuel or biofuel in effectively reducing NOx emissions. Auti and Rathod [75] blended diesel, biodiesel, and TPO and used in a DI diesel engine. The results revealed that the blends exhibited superior performance and combustion compared to diesel fuel. However, the emission of the blends limited its use. Krishania et al. [76] figured out a blend consisting of 80 vol.% Jatropha methyl ester and 20 vol.% TPO and used in a diesel engine. The results indicated a reduction in smoke emissions by 11.58%, PM emissions by 5.3%, and NOx emissions by 10.2% for the blend at full load conditions. Âgbulut et al. [77] conducted a comparative analysis of the performance, emission, and combustion characteristics of a CI engine utilizing TPO–diesel blends and TPO–diesel–biodiesel blends. The findings indicated that the utilization of a TPO–diesel blend resulted in a reduction of BTE by 9.13%. However, the introduction of biodiesel partially mitigated this reduction by 7.51%. The introduction of the TPO–diesel blend resulted in a 21.78% increase in BSFC. However, the negative impact was partially mitigated by an 8.89% reduction when biodiesel was added to the blend. The CO emissions for TPO–diesel fuel increased by 7.09% compared to conventional diesel. Conversely, the addition of biodiesel led to a 7.69% reduction in CO emissions due to its high oxygen content. Moreover, the TPO–diesel blend increased NOx by 7.09%, but this increased by 4.64% with the addition of biodiesel. In a study conducted by Sharma and Murugan [78], the influence of nozzle opening pressure on the performance of a diesel engine operating with TPO–biodiesel blends was investigated. The results demonstrated a notable increase of approximately 5.12% in BTE. Moreover, a reduction of about 9.5% in smoke opacity, 1.57% in CO emissions, and 6.26% in HC emissions was observed when the nozzle opening pressure increased at full engine load. Pinto et al. [79] carried out experiments in a CI engine fueled with a TPO–diesel–biodiesel blend. The findings indicated that the inclusion of modest proportions of TPO in the blends (up to 5 vol.%) resulted in a marginal reduction in BTE, while concurrently yielding lower CO and NOx emissions compared to diesel fuel. However, increasing the quantity of TPO results in a notable decrease in BTE, while elevating CO emissions, diminishing NOx emissions, and substantially increasing sulfur emissions. The partial replacement of diesel with biodiesel in diesel–TPO blends resulted in a decrease in CO emissions; however, it also led to an increase in NOx emissions. Mikulski et al. [19] conducted a study to assess the performance and emissions of different mixtures of diesel fuel and raw vegetable oil with a 5 vol.% addition of TPO in a diesel engine. The findings indicated that utilizing fuel comprising up to 55 vol.% raw vegetable oil and 5 vol.% TPO resulted in only marginal degradation of BTE when compared to that achieved with diesel fuel. The ternary blends exhibited a significant increase in HC and CO emissions compared to diesel fuel. Moreover, it was observed that the blends demonstrated elevated NOx concentrations only under high engine load and low engine speed conditions.
Table 5 summarizes major findings from research on TPO–biofuel blend engines. The research demonstrated that the detrimental effects of utilizing TPO–diesel binary blends on engine performance, emissions, and combustion characteristics can be significantly mitigated through the addition of biofuels. Previous research has shown that TPO–biodiesel and TPO–diesel binary fuel have demonstrated weaker antiwear properties when compared to biodiesel and diesel fuel. It was suggested that the effects of doping metal oxide–based nanoparticles into the TPO–diesel fuel blend on the performance, emission, and combustion characteristics of the IC engines be investigated.
Type of engine | Baseline | Blend | Performance parameter | Emissions parameter | References |
---|---|---|---|---|---|
Single-cylinder, naturally aspirated, DI engine | Diesel | Biodiesel-TPO blend (20%) | CP▼HRR▼BSEC▲BSFC▲ | HC▼Smoke▼NOx▲ | Sharma and Murugan [14] |
Single-cylinder, CRDI engine | Diesel | Biodiesel-TPO blend | IG▲ | — | Nursal et al. [18] |
Single-cylinder, naturally aspirated, DI engine | Diesel | Biodiesel-TPO blend (20%) | CP▼HRR▼BTE▼BSFC▲EGT▼ | Smoke▲PM▼NOx▼CO2▲ | Krishania et al. [76] |
Single-cylinder, naturally aspirated, DI engine | Diesel | Biodiesel-TPO blend (20%) | IG▼CP▼HRR▼CD▲BTE▲EGT▲ | CO▼HC▼Smoke▼NOx▲ | Wu and Yuan [84] |
Single-cylinder, naturally aspirated, DI engine | Diesel | Biodiesel-TPO blend (20%) | IG▼CP▼HRR▼CD▲BTE▼BSEC▲ | CO▼HC▼Smoke▼NOx▲ | Sharma and Murugan [17] |
Single-cylinder, DI engine | Diesel | Diesel-biodiesel-TPO blend | IG▲CP▲BTE▲BSFC▼ | CO▼HC▼NOx▲ | Auti and Rathod [75] |
4-Cylinder, naturally aspirated, DI engine | Diesel | Diesel-biodiesel-TPO blend | BP▲BSFC▼ | CO▼NOx▲ | Koc and Abdullah [74] |
Single-cylinder, naturally aspirated, DI engine | Diesel | TPO–ethanol | CP▲HRR▲BSFC▲BTE▼ | CO▼NOx▼CO2▲ | Âgbulut et al. [77] |
Single-cylinder, DI engine | Diesel | TPO–DEE (dual fuel mode) | IG▲CP▲HRR▲BTE▼ | CO▲HC▲NOx▼Smoke▲ | Hariharan et al. [20] |
3.3. Blending With Nanoparticles
TPO exhibited inferior antiwear properties in comparison to both biodiesel and diesel fuel. Consequently, research was undertaken to explore the potential of using nanoparticles as fuel additives to enhance lubrication performance. In a study by Kegl et al. [80], an examination of the impact of various nanoadditives on fuel in IC engines was conducted. The findings revealed that the utilization of nanofuels resulted in enhanced BTE and reduced exhaust emission, in comparison to fuels lacking nanoparticles. Loo et al. [26] presented the tribological behavior of TPO–biodiesel–diesel blended fuel with the addition of various types of nanoparticles. The results of the tribological experiments indicated that low concentrations of all nanoparticle additives yield improved antifriction performance in the blended fuel. This enhancement was attributed to the formation of a protective film between the contact surfaces. The images obtained through the scanning electron microscope demonstrated a notable reduction in wear and surface damage when utilizing a 0.1 wt% concentration of nano-fuel. Kumaravel et al. [27] created blends of TPO and diesel with cerium oxide (CeO2) nanoadditives and measured the properties according to the American Society for Testing and Materials standards. The analysis indicated that the viscosity and density of all blends exceeded those of diesel fuel, while the flash point and heating value of the blends were lower. Adding cerium oxide nanoadditives showed improvements in all fuel properties compared to blends without the nanoadditives. Additionally, the blends with 100 ppm of CeO2 showed higher BTE and NOx emissions, along with lower smoke emissions than those of diesel fuel. These findings suggested that using CeO2 nanoadditives in TPO–diesel blends could offer a more cost-effective and environmentally friendly alternative for CI engines. Polat [28] discussed a diesel engine’s performance, combustion, and emission characteristics fueled with a TPO–diesel blend adding aluminum oxide (Al2O3) nanoparticles. The results indicated that Al2O3 nanoparticles improved BTE while reducing maximum CP, HRR, BSFC, HC, NOx, and CO emissions compared with diesel fuel. This study has observed that, while the presence of TPO led to a deterioration in engine performance, emissions, and combustion characteristics, these adverse effects can be ameliorated through the addition of Al2O3. Figure 4 shows the BSFC, BTE, and emissions variation with the engine loads. Thangavelu and Arthanarisamy [81] conducted a comprehensive investigation into the performance, emissions, and combustion characteristics of a TPO–diesel blend featuring CeO2 nanoadditive in a CI engine. The findings indicated that the TPO5 blend demonstrated the highest level of BTE and closely approximated diesel fuel performance at full engine load. Furthermore, the emissions of HC and smoke were lower compared to those of diesel fuel. The incorporation of CeO2 nanoadditives resulted in increased BTE and reduced HC, CO, and smoke emissions. The study identified that TPO with CeO2 nanoadditives represents a viable and promising alternative fuel for CI engines.
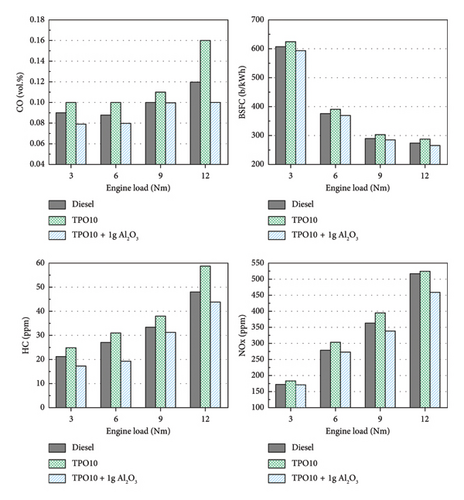
Upon conducting the aforementioned analysis, it was evident that the incorporation of nanoparticles in conjunction with TPO notably enhances engine properties. It was well established that the occurrence of phase separation and stability issues in test fuels containing nanoparticles is highly undesirable. Further research should be conducted to eliminate the negative features of nanoparticles.
3.4. Dual Fuel Mode
The properties of TPO make it not completely suitable as a replacement for traditional diesel fuel or other biofuel types. Many researchers have attempted to address these concerns, suggesting that it should be combined with other biofuels, rather than simply blending it with diesel. Injecting biogas into the intake manifold combined with TPO directed into the cylinder was an effective method to improve the performance of CI engines.
Hariharan et al. [20] conducted an investigation into the performance, emission, and combustion characteristics of a diesel engine fueled with TPO as the primary fuel and diethyl ether (DEE) as an ignition enhancer, introduced alongside the intake air. In the TPO–DEE operation, a 5% reduction in NOx emissions was observed compared to diesel fuel operation. However, HC, CO, and smoke emissions were 2%, 4.5%, and 38% higher than those resulting from diesel fuel usage respectively. Tunç et al. [23] analyzed the environmental pollution cost for a diesel engine using mixtures of TPO–diesel and biogas blends. When the engine was fueled with the binary blend, biogas was consistently injected at a stable flow rate into the suction line. The study found that the blend produced better environmental pollution outcomes than the diesel fuel and concluded that ternary blends of biogas, TPO, and diesel fuel could be used as an alternative fuel instead of diesel fuel. Fırat et al. [24] tested TPO as a low-reactivity fuel to achieve reactivity-controlled combustion ignition (RCCI). The port fuel injection system injected TPO into the intake port, while the CRDI system directly injected diesel fuel into the cylinder. The results demonstrated that the use of TPO in RCCI operations led to notable increases in BTE. The incorporation of TPO in RCCI engines has proven to be effective in reducing HC emissions. These findings suggested that TPO was a viable low-reactivity fuel for RCCI engines, demonstrating satisfactory performance, combustion, and emission characteristics. Hoang et al. [25] evaluated the performance, emissions, and combustion characteristics of a diesel engine utilizing a TPO–biodiesel blend. This blend was paired with compressed natural gas (CNG) injected with the air in both conventional mode and homogeneous charge compression-ignition (HCCI) mode. The findings revealed that a preheated blend, in conjunction with enriched CNG for the HCCI mode, demonstrated superior performance, emission, and combustion characteristics, albeit with a slightly lower BTE compared to diesel fuel. Karagöz et al. [83] conducted a study to evaluate the viability of utilizing TPO in conjunction with diesel and biogas as a dual fuel option for diesel engines. The ratio of TPO in the blend was 20 vol.%. The results revealed that engine performance decreased with the use of TPO due to its lower heating value. This resulted in an increase in BSFC and a reduction in BTE. The emissions of CO and HC significantly increased when TPO and biogas were present in the cylinder. However, the NOx levels initially exhibited an increase when using diesel–TPO blends, followed by a subsequent decrease upon the introduction of biogas into the combustion chamber. Figure 5 shows the BSFC, BTE, NOx, and HC emissions of dual-fuel engine behavior powered by TPO–biogas blends. Wu et al. [84] conducted an experiment involving the utilization of a blend of TPO and diesel fuel in a diesel engine, with the additional assistance of hydrogen. When the engine ran on TPO–diesel blends, it demonstrated torque and power output performance comparable to that of diesel fuel. TPO15 emerged as a highly promising alternative fuel, demonstrating exceptional performance and environmental attributes through substantial reductions in harmful emissions such as CO, CO2, and NOx. Hydrogen addition to the blend improved the performance and BSFC due to the high heating value. The utilization of TPO in combination with hydrogen enrichment presents a promising solution for reducing emissions and exerting a positive influence on the environment. This innovative approach has the potential to serve as a viable substitute for diesel fuel.
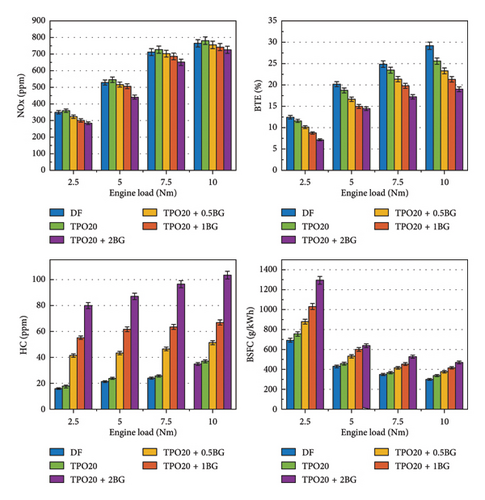
Based on the findings of prior research, it was evident that the incorporation of TPO as a blend led to heightened harmful emissions and a deterioration in engine performance. This holds despite the initial promise of TPO as a potential solution for the disposal of ELTs. However, these issues can be mitigated through the utilization of a cleaner fuel additive such as hydrogen, CNG, or DEE, thereby enhancing engine performance.
3.5. Spark-Ignition Engine Mode
The literature review revealed a scarcity of studies focusing on the utilization of TPO in an SI engine. Among others, Szwaja et al. [30] carried out an experiment in a single-cylinder SI engine fueled with n-butanol–TPO blend at a ratio of 3:1 by volume. Regular gasoline was proposed as a reference fuel. The investigation concluded that the blend could be successfully utilized as fuel for the SI engine and exhibited a higher susceptibility to inducing knocking. Increased levels of TPO in the blends were found to extend CD and raise the probability of knock. CO2 emissions closely approached gasoline levels, while the HC increased as the TPO rose to 50% in the blend. Figure 6 shows the tail pipe specific exhaust emissions of NO, CO, and UHC at optimal spark timing for tested fuels. Odejobi et al. [82] blended TPO with gasoline to power an electric generator. The results revealed that the fuel consumption rate was reduced with an increase in TPO content. TPO–gasoline blends resulted in a significant reduction in the CO emissions, but higher HC emissions with the TPO content. The application of the EGR approach could resolve the issues of high HC emissions in the exhaust stream. Experiments were conducted on an SI engine using TPO–ethanol blends to indicate that the admixture of TPO at a 25% volume concentration with ethanol did not manifest any knock symptoms at a compression ratio of 9.5:1, notwithstanding TPO’s relatively low octane rating [85]. In conclusion, TPO–ethanol blends at a volumetric ratio of 1:3 can effectively serve as a substitute for ethanol in SI engines. In a study conducted by Öztop et al. [86], an investigation was carried out to assess the performance and exhaust emissions of an SI engine when utilizing gasoline–TPO blends. The study findings indicated that TPO can effectively function as a partial substitute for gasoline fuel, with a blend ratio of up to 25 vol.%, without necessitating any modifications to the engine. This substitution can be accomplished while upholding performance parameters and adhering to emissions standards.
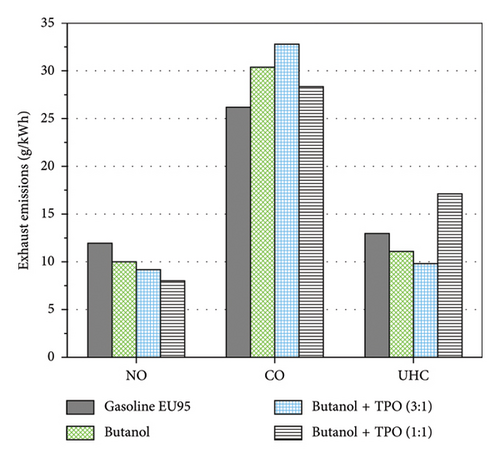
Summing up, TPO can serve as a viable fuel source for the SI engine provided it is blended with gasoline or alcohol. It is recommended that the TPO content in the blend does not surpass 25 vol.%.
4. Energy, Exergy, and Sustainability Assessments
In systems such as IC engines, it is imperative to move beyond sole reliance on energy analysis. Consequently, the conduction of exergy analyses becomes paramount in order to gauge the efficacy and caliber of energy within the confines of the system. This analytical approach furnishes a comprehensive picture of the manner in which input energy is harnessed within the system. The energy produced from fuel combustion in IC engines constitutes the input to the system, undergoing transformation into various forms. Exergy, a measure of the potential to perform useful work within a system, represents a fundamental concept in the analysis of second-law thermodynamics [87]. Sustainability aims to meet the present needs without compromising the ability of future generations to meet their own. It is based on protecting the environment, fostering economic growth, and promoting social development. The effective use of energy resources is crucial for advancing sustainability, with exergy and energy efficiency being vital for sustainable development [88]. An essential parameter for the comparison of alternative fuels for engines is the sustainability index [89]. This index serves to evaluate the environmental impact and economic feasibility of energy systems, enabling an assessment of their economic efficacy and environmental advantages [90].
TPO was investigated as an additive in diesel fuel with different ratios to evaluate the energy, exergy, and sustainability aspects in a CI engine [91]. It was found that the maximum energetic efficiency was achieved with a blend containing 10 vol.% TPO at all engine load conditions. Observations indicated that the introduction of TPO into diesel fuel has demonstrated enhancements in the engine’s performance characteristics, specifically in the domains of thermoeconomics and sustainability, surpassing those of pure diesel fuel. The investigations of the energy, exergy, and sustainability were carried out by using TPO–diesel blends and showed that TPO10 had the highest energy efficiency of 31.49%, exergy efficiency of 32.51%, and sustainability index value of 1.48 [92]. It was deemed justifiable to conclude that TPO10 represented the most sustainable fuel option and was deemed suitable for utilization in diesel engines without necessitating any modifications. Besides, the comparisons of TPO and diesel fuel demonstrated that the utilization of TPO in diesel engines yielded a thermal efficiency of 38% and a second-law efficiency of 58% [93]. Moreover, the sustainability index of diesel fuels was established at 2.7, whereas TPO exhibited a sustainability index of 1.42. Ertürk et al. [94] analyzed the energy, exergy, and sustainability parameters of TPO–diesel blends and revealed that the BTE and exergy efficiency decreased with the increase of TPO concentration in the blends. Therefore, the sustainability index was reduced because of the reduction in exergy efficiency. Yaqoob et al. [95] tested different blends of petrol containing TPO in an SI engine and found that the highest exergy and energy efficiencies of 16.91% and 17.81% were achieved using the 95 vol.% petrol and 5 vol.% TPO blend (P95TPO5). This blend also demonstrated a maximum sustainability index of 1.21. The P95TPO5 blend, in comparison to pure gasoline, demonstrated notably inferior performance across metrics such as energy efficiency, exergy efficiency, and sustainability index.
Blends of TPO and diesel can serve as an effective fuel additive for CI diesel engines without necessitating any modifications. Their application facilitates the repurposing of waste tires, energy retrieval, preservation of finite fossil fuel reserves, and mitigation of environmental harm.
5. Conclusions and Scope of Future Work
5.1. Conclusions
- •
Thermochemical processing through pyrolysis is a promising technology for recycling ELTs, which enables the recovery of pyrolysis oil and carbon black and has lower environmental impacts on global warming. The production of TPO plays a crucial role in waste management and environmental protection.
- •
TPO has different properties which depend on the feedstocks and pyrolysis conditions. The main factors that affect the performance of TPO in the engine are properties, injection timing, engine type, and operating conditions. Compared with diesel fuel, TPO has a higher viscosity, higher density, higher sulfur contents, and lower CN, which affect the atomization process and combustion characteristics in CI engines. The cetane improver, external energy addition, preheating intake air, or increased compression ratio are general methods for its application in CI engines.
- •
The use of TPO results in elevated NOx emissions attributable to the higher proportion of fuel-bound nitrogen. Additionally, heightened SO2 emissions are observed across the entire operational condition due to the sulfur content, while increased soot emissions can be attributed to the higher presence of polycyclic aromatic hydrocarbons.
- •
The engine does not need any modifications to run on TPO–diesel fuel blends, which can be used directly in CI engines. However, using a blend of TPO and diesel can negatively affect engine performance and emissions. It has been observed that adding biodiesel to the TPO–diesel blend improves performance, emission, and combustion characteristics.
- •
The incorporation of nanoparticles into the TPO–diesel blend has the potential to enhance engine performance and reduce emissions. This is attributed to the ability of nanoparticles to expedite heat transfer as a result of their superior catalytic effects, augment the surface-area-to-volume ratio, and enhance combustion efficiency.
- •
Dual fuel mode by infusing biogas (or other gaseous fuel) in the intake manifold to form a homogenous fuel–air mixture can enhance the overall fuel quality, and reduce NOx emission in the combustion contributing to the lower in-cylinder temperature. The combination of TPO and biogas presents a promising strategy for mitigating emissions and fostering a positive environmental impact.
- •
TPO can serve as a viable fuel for the SI engine, provided it is blended with other compatible fuels such as n-butanol, ethanol, etc. The TPO content in the blend should not surpass 25% and must remain uncontaminated by sulfur.
- •
In terms of energy, exergy, and sustainability assessment, TPO10 demonstrates outstanding performance and can be used as an advantageous fuel for CI engines without necessitating modifications.
5.2. Scope of Future Work
Despite great efforts made by researchers, TPO applications are still a crucial topic concerning TPO feasibility for long-term aspects, and it needs further improvement. The production of TPO from waste tires continues to be considered a costly process, despite significant technological advancements in recent years. It is imperative to direct further research efforts toward identifying methods to mitigate these costs. Investigating the influence of employing nanoparticle-reinforced test fuels on engine design parameters, phase separation, and stability is imperative. Investigating the impact of TPO utilization in IC engines on the deterioration of engine components is essential to assess prospective sustainability and thermodynamic methodologies. To the best of the authors’ knowledge, these issues have not been addressed in the existing literature and are likely to be of significant interest.
Nomenclature
-
- Al2O3
-
- aluminum oxide
-
- BSFC
-
- brake-specific fuel consumption
-
- BP
-
- brake power
-
- BTE
-
- brake thermal efficiency
-
- CA
-
- crank angle
-
- CD
-
- combustion duration
-
- CeO2
-
- cerium oxide
-
- CI
-
- compression ignition
-
- CN
-
- cetane number
-
- CNG
-
- compressed natural gas
-
- CO
-
- carbon monoxide
-
- CO2
-
- carbon dioxide
-
- CP
-
- cylinder pressure
-
- CRDI
-
- common rail direct injection
-
- DEE
-
- diethyl ether
-
- DI
-
- direct injection
-
- EGR
-
- exhaust gas recirculation
-
- ELTs
-
- end-of-life tires
-
- HC
-
- hydrocarbon
-
- HCCI
-
- homogeneous charge compression ignition
-
- HRR
-
- heat release rate
-
- IC
-
- internal combustion
-
- ID
-
- ignition delay
-
- NOx
-
- nitrogen oxide
-
- PM
-
- particulate matter
-
- RCCI
-
- reactivity-controlled combustion ignition
-
- SI
-
- spark ignition
-
- SO2
-
- sulfur dioxide
-
- TPO
-
- tire pyrolysis oil
Conflicts of Interest
The authors declare no conflicts of interest.
Author Contributions
Keji Qi: data curation, formal analysis, investigation, methodology, visualization, and writing – original draft preparation.
Xuehui Gan: conceptualization, funding acquisition, project administration, resources, supervision, validation, and writing – review and editing.
All authors agree to be accountable for the content and conclusions of this paper.
Funding
This research was supported by the National Key Research and Development Program of China ∗ 2023YFB3709605-02
Acknowledgments
This research project was supported by the National Key R&D Program of China under Grant number 2023YFB3709605-02.
Open Research
Data Availability Statement
The data that support the findings of this study are available from the corresponding author upon reasonable request.