Recycling Nd Magnet Scraps to Synthesize Carbon-Swaddled Fe3O4 Anode Material for Lithium-Ion Battery
Abstract
This study explores the innovative recycling of neodymium (Nd) permanent magnet scrap to synthesize Fe3O4, a high-capacity anode material for secondary batteries, by leveraging the Fe oxalate solution produced during recycling. The traditional process of recovering Fe from permanent magnets in the form of oxides produces products with limited economic viability and usability. For the first time, we have successfully synthesized Fe3O4 as an anode material for lithium-ion (Li-ion) secondary batteries from scrap Nd magnets. We address the existing challenge by employing a novel approach: hydrothermal synthesis of crystalline FeC2O4·2H2O from the Fe leachate, extracted via oxalic acid leaching from a mixed phase of NdF3-Fe2O3 controlled during fluorination heat treatment while recycling. The recovered FeC2O4·2H2O is subsequently phase-transferred to Fe3O4 under an Ar atmosphere. To overcome the inherent low conductivity and rate capability of Fe3O4, a carbon-coating process utilizing dopamine HCl is implemented. The developed C-Fe3O4 anode material exhibits a significant capacity retention of 428 mAh/g after 500 cycles at 1C, showcasing its potential for use in high-performance secondary batteries and contributing to the sustainable recycling of critical materials.
1. Introduction
Neodymium (Nd) permanent magnets, such as those used in microphone speakers, computer hard drives, electric vehicle (EV) motors, wind turbine generators, and medical magnetic resonance imaging machines, are among the strongest permanent magnets with the highest magnetic fields. The recovery of Nd is essential for stabilizing the supply and demand of rare earth elements, and various Nd recovery methods have been explored [1–4]. The average annual growth rate of Nd used in various applications exceeds 22.5%.
Expanding the pivotal role of Nd magnets in the green energy sector with a focus on EVs and wind turbines underscores their critical demand. EVs are increasingly reliant on NdFeB magnets, as each vehicle requires several kilograms of these magnets to power efficient high-performance electric motors. Similarly, wind turbines that are instrumental in harnessing renewable energy require several hundred kilograms of NdFeB magnets per unit to optimize their energy generation capabilities. The substantial demand for NdFeB magnets in key green technologies highlights the critical need for advancements in recycling technologies [5–8].
Traditional recycling efforts have predominantly focused on Nd recovery, often sidelining environmental implications and overlooking the potential utility of byproducts including Fe.
Such exclusions not only signify a gap in resource efficiency but also highlight the environmental detriments associated with reliance on potent chemicals and processes in recycling operations. The existing paradigm, characterized by its focus on singular recovery targets and high-cost, high-risk processes, calls for a shift toward more holistic, environmentally benign, and economically viable recycling methods [9–13]. Such methods can ideally leverage innovative approaches such as thermal treatment combined with mild acid leaching to enhance the recovery of Fe and other valuable byproducts, thereby broadening the scope of resource utilization and sustainability in recycling practices. Nd magnets contain up to 70 wt.% of Fe, but in terms of recycling, Fe is almost invariably recovered as simple red oxide, resulting in a significant loss of added value [14].
Exploring beyond the confines of magnet recycling, this study addresses the inherent limitations of graphite anodes within lithium-ion (Li-ion) batteries, a cornerstone of contemporary energy storage solutions. The intrinsic capacity limitations of graphite have prompted the search for alternative anode materials with high energy densities. Silicon, with its promising capacity attributes, has emerged as a viable additive; however, its application is hindered by significant challenges including substantial volume expansion during electrochemical cycling. This study pioneers an innovative pathway by advocating the utilization of Fe-oxide-based anodes derived from the recycling of Nd magnets as a sustainable and efficacious alternative to traditional graphite anodes. Our approach involving the fabrication of carbon-coated nanodot anode materials not only exemplifies a leap toward enhancing the performance and sustainability of battery materials but also underscores the broader implications of recycling to foster a circular economy and reduce dependency on finite resources [15].
Meanwhile, Fe3O4 has been an attractive candidate for Li-ion anode materials due to its high theoretical capacity (924 mAh/g) compared to currently commercialized anodes, such as graphite (372 mAh/g) and Li4Ti5O12 (175 mAh/g), although it suffers from relatively low retention and rate capability. The theoretical capacity of Fe2O3 is approximately 1007 mAh/g, slightly higher than 924 mAh/g of Fe3O4. However, Fe3O4 exhibits significantly better electrical conductivity (10−4 to 10−3 S/cm) and ionic conductivity, which enhance charge transfer efficiency and overall electrochemical performance in Li-ion batteries [16].
Recent advancements in Fe3O4-based anode materials for Li-ion batteries have focused on achieving high performance through the use of nanomaterials and surface treatments, such as carbon-supported materials [16–24], Fe3O4 composites [25–30], and conductive carbon coatings [31–33], which enhance electrical conductivity and structural stability during cycling. However, these approaches primarily rely on synthetic or commercially sourced Fe3O4 as the raw material. In this study, we propose a novel route utilizing Fe3O4 derived from Nd magnet scrap leachate as a precursor. This method contributes to material recycling efficiency while demonstrating high electrochemical performance suitable for secondary battery applications. The feasibility and performance characteristics of the recycled Fe3O4 were systematically evaluated through electrochemical analysis.
2. Experimental
2.1. Materials
2.1.1. Synthesis of FeC2O4·2H2O From Fe Oxalate Leachate
Waste permanent magnets were acquired from manufacturers in the form of scraps, which were pulverized by ball milling. The waste magnets were Nd permanent magnets, and the crystalline phase was identified as Nd2Fe14B. We did not perform pretreatments such as demagnetization, oxidation, or similar treatments. The fabrication of the Fe oxalate complex followed the procedure described in the literature for process [10]. The scraps from waste permanent magnets underwent oxidative heat treatment followed by fluorination heat treatment (using NH4HF2, Sigma–Aldrich, 98%). Through fluorination thermal treatment at 600°C, the Fe2O3-Nd2O3 system underwent a phase transition via the intermediate phase FeF3-NdF3, eventually forming Fe2O3-NdF3. Thermodynamic calculations revealed that FeF3 is easily reoxidized in the presence of moisture or oxygen, whereas NdF3 remains stable under such conditions. This phase stability was experimentally confirmed, resulting in the formation of an NdF3-Fe2O3 composite through fluorination at 600°C.
Then, the NdF3-Fe2O3 powder was leached in a 0.6M oxalic acid in D.I. water (using C2H2O4·2H2O, Daejung, 99.5%). Following leaching, inductively coupled plasma (ICP) analysis was conducted on the solution, which was approximately five times concentrated, resulting in measured Fe and Nd concentrations of 16,663 and 109 mg/L, respectively. To synthesize FeC2O4 in the leachate, ethylene glycol (Sigma–Aldrich, 99%) was added in a 1:3 vol.% ratio, along with multiwalled carbon nanotubes (CNT) (Korea Nanomaterials), followed by a hydrothermal reaction. The hydrothermal reaction was maintained at 105°C for 10 h to induce the precipitation of Fe oxalate.
2.1.2. Synthesis and Carbon Coating of Fe3O4
X-ray diffraction (XRD) analysis (X-ray diffractometer, XRD-6100, Shimadzu, Japan) was performed on the manufactured powder after its heat treatment at 400°C in Ar atmosphere for phase transition from FeC2O4·2H2O to Fe3O4. To achieve higher performance as the negative electrode active material in Li-ion batteries, dopamine HCl (C8H12ClNO2, Sigma–Aldrich, 99%) was stirred in a mortar at a ratio of 50 wt.%:50 wt.% for 30 min. The stirred powder was carbonized at 400°C through heat treatment in one pot. After carbon coating, the amount of carbon in the heat-treated powder was measured using thermogravimetric analysis (TGA) (using thermogravimetric analyzer; STA 449F5, Netzsch, Germany). Carbon analysis was performed using Raman spectroscopy (HEDA, WEVE, Korea), and Raman analysis was conducted using an excitation 532-nm laser source.
2.2. Electrochemical Performance
For analyzing the anode material in Li secondary batteries, electrodes were manufactured using 70, 15, and 15 wt.% of active material, additive carbon (Super P carbon black; MMM Carbon, Brussels, Belgium), and Kynar 2801 binder (PvdF-HFP), respectively. To prepare the electrodes, the powders were dissolved in 1-methyl-2-pyrrolidinone (NMP) solution to form a slurry. The slurry was uniformly applied to Cu foil through an applicator (doctor blade) and dried in a vacuum oven at over 100°C for more than 24 h. Electrochemical characterization was performed using CR2032-type coin cells with a diameter of 20 mm and a thickness of 3.2 mm. Further, Li metal was used as the anode material, and the produced Fe3O4 electrodes served as the cathode, with Celgard 2400 as the separator film. The electrolyte comprised 1M LiPF6 in ethylene carbonate and dimethyl carbonate (1:1 v/v; Soulbrain). Electrochemical testing of Fe3O4 was conducted using the galvanostatic discharge/charge cycling method. To analyzed cycle retention, the measurements were conducted at 1C and for the C-rate capability was performed at 0.1, 0.2, 0.5, 1, 2, 5, 10, 15, and 20C, respectively. Cyclic voltammetry (CV) was performed with the voltage range of each cell set from 0 to 3 V versus Li/Li+ at 0.1, 0.2, 0.4, 0.6, 0.8, and 1.0 mV/s, respectively. The electrochemical impedance spectroscopy (EIS) was measured with 5 mV amplitude between 0.015 Hz and 250 kHz at 25°C
3. Results and Discussion
3.1. Precipitation of Fe Oxalate Dihydrate
In our approach, we used a composite material of NdF3-Fe2O3, derived from oxidation–fluorination multistage heat treatment of Nd magnet scrap, and subsequently leached with oxalic acid to produce a solution that served as the starting material for our study. The overall reaction scheme is illustrated in Figure 1. In this study, Fe oxalate was synthesized from Nd permanent magnet leachate without any pretreatment. In the process, no pretreatment steps including addition of oxalic acid to match concentrations similar to references or removal of Nd (including rare-earth elements [REEs]) from the solution were performed. Instead, evaporation and solution concentration were performed to increase the Fe-ion content in the Nd magnetic leachate. Precipitation was attempted using an initially low-concentration Fe leachate, which resulted in particles with very large thicknesses. Thus, Fe-ion concentration affected the morphology and shape of Fe oxalate.

In the leachate, Fe ions existed in the form of Fe(C2O4)33-(aq). The Fe oxalate complex reacted with ethylene glycol and water to precipitate needle-like Fe oxalate. Upon concentrating the leachate solution, Nd, Dy, and Pr were measured as 109, 17, and 10 ppm, respectively. The total impurity content (excluding Fe) was 136 ppm, while the Fe concentration was measured at 16,663 ppm. Thus, the Nd content excluding Fe was calculated as approximately 0.81 wt.%, indicating expected purity of the recovered Fe oxalate over 99%.
After the hydrothermal reaction, ICP analysis of the residual solution showed that Nd and Fe were present at 9 and 158 ppm, respectively, while Dy and Pr were undetectable (N/D). Considering the total impurities before and after Fe oxalate precipitation, the purity of Fe oxalate was inferred to be approximately 99.24%. Through ICP analysis of the residual solution after precipitation, we concluded that impurities such as Nd possibly present in the synthesized material could be disregarded in relation to doping with Fe oxalate.
The Fe leachate, which is an Fe oxalate complex solution, had a pH of 0.9. In the NdF3-Fe2O3 compound, Fe3+ + 3C2O42− formed Fe(C2O4)33− via oxalic acid, and Fe3+ was reduced to Fe2+. The Fe leachate underwent a precipitation reaction as
Fe(C2O4)33− + 6H2O + EG = FeC2O4·2H2O + 2H2C2O4.
After the hydrothermal reaction, needle-like morphology of the recovered powder was observed. Furthermore, Fe oxalate could be synthesized using precursors such as ammonium Fe sulfate, Fe sulfate, or Cl-based compounds [34–37] at room temperature [38].
Dehydration of Fe oxalate often results in needle-like structures owing to its crystalline structure upon the addition of ethylene glycol, known to promote the Fe3+ to Fe2+ reaction. Maximizing the aspect ratio also yields needle-like structures [39]. Using commercial grade Fe(NO3)3·9H2O, the synthesis of Fe oxalate resulted in needle-like structures, as shown in Figure 2a. Relatively large morphologies were observed when the initial Fe-ion concentration was below 2000 ppm. The concentrated Fe leachate exhibited a morphology similar to that of commercial-grade precipitates, as shown in Figure 2d.
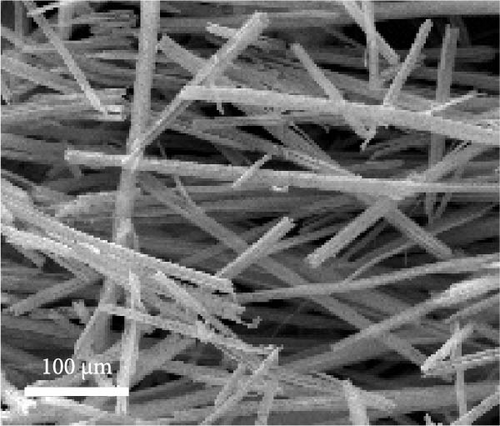
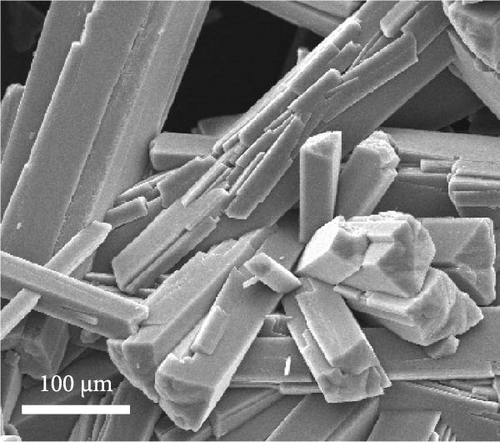
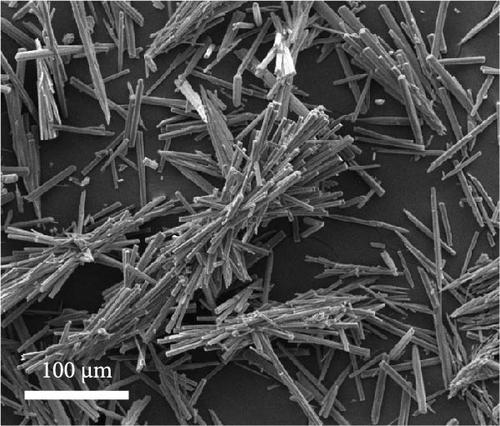
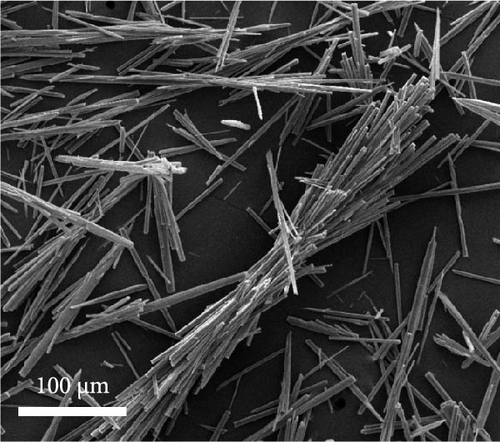
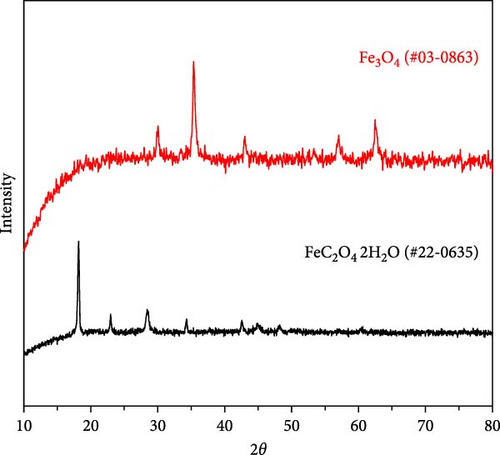
The material was calcined to produce Fe3O4, which was subsequently utilized as an anode material for Li-ion secondary batteries. As shown in Figure 2e, Fe oxalate (FeC2O4·2H2O, JCPDS #22-0635) synthesized and heat-treated in Ar was converted into Fe3O4 (JCPDS #03-0863) as a single phase. Upon high-temperature oxidation, the Fe oxalate nanorods underwent thermal decomposition, releasing CO2 and H2O, to form an array of nanoparticles from the original rod-like structure. The process was tested under identical conditions using a commercial grade Fe(NO3)3·9H2O precursor, as shown in Figure S1.
3.2. Phase Transformation From Fe Oxalate Dehydrate to Carbon-Swaddled Fe3O4
Particle aggregation increases interparticle resistance and decreases surface area available for reaction with Li-ions, potentially deteriorating the electrochemical properties. Preventing such aggregation can improve Li-ion diffusion and resolve the issue of increased interparticle resistance, thereby enhancing the overall electrochemical performance. Therefore, reducing nanoparticle aggregation and maintaining a high specific surface area are crucial. In contrast, metal oxides including Fe3O4 typically exhibit low electrical conductivity, which negatively affects their electrochemical properties, leading to a low irreversible capacity. To address such issues, carbon is often used to enhance the conductivity. Carbon coatings generally involve high-temperature heat treatment to effectively coat a material with carbon, thereby improving its conductivity and overall electrochemical performance.
In this study, Fe leachate selectively extracted from Nd magnet scraps was used to synthesize Fe oxalate dihydrates. During heat treatment for the phase transition from FeC2O4·2H2O to Fe3O4, dopamine HCl was employed as a carbon source [40]. The approach allowed for a simultaneous phase transition to Fe3O4 and carbon coating, enhancing the electrical conductivity and electrochemical performance of the material.
Regardless of the presence of dopamine HCl, a phase transition to the Fe3O4 single phase occurred after heat treatment. Consequently, TGA was conducted on Fe3O4 in the presence and absence of dopamine HCl. As shown in Figure 3a, a consistent weight increase to approximately 300°C was observed regardless of the presence of dopamine HCl. The increase in weight was attributable to the thermal transition to a more stable phase of Fe2O3. Scanning electron microscopy (SEM) analysis confirmed that the rod-like morphology of Fe3O4 grew shorter after heat treatment, as shown in Figure 3c.
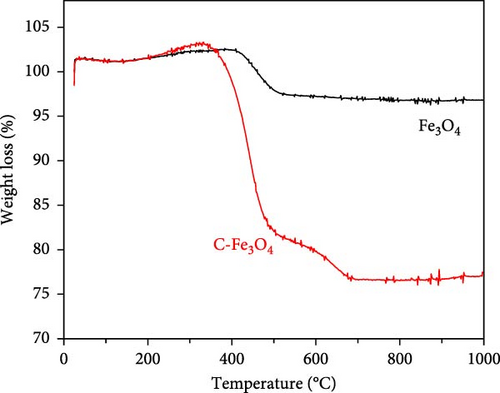
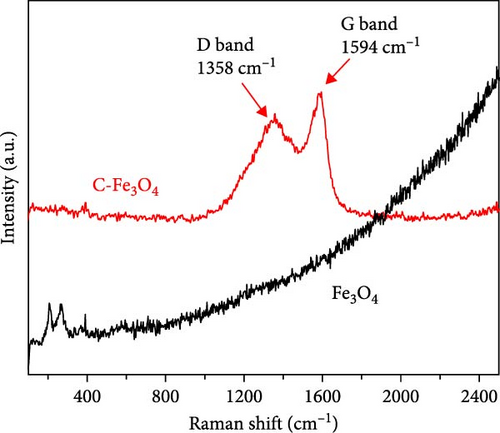
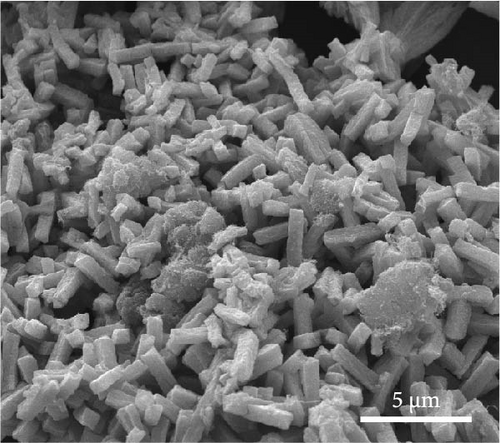
During the phase transition from FeC2O4·2H2O to Fe3O4, the presence of dopamine HCl led to simultaneous carbon coating, resulting in more complex behavior compared to the typical oxidation mechanism of FeC2O4·2H2O. Therefore, TGA analysis of FeC2O4·2H2O and carbon-coated Fe3O4 was conducted to illustrate the behavior. The TGA results demonstrated that the thermal decomposition of FeC2O4·2H2O involved dehydration up to 200°C, followed by the decomposition of CO2 and H2O to approximately 400°C in Figure S3. Dopamine HCl is known to decompose at temperatures above 243°C, which is relatively higher than other carbon sources such as sucrose (above 186°C) or citric acid (above 177°C). Dopamine HCl was specifically employed due to its decomposition at higher temperatures, which promotes the prevention of unintended oxidation of Fe3O4 to Fe2O3 by residual H2O.
For the phase transition to Fe3O4, heat treatment was performed in an Ar atmosphere. Without Ar, oxidation could lead to the stabilization of Fe3+ in Fe2O3, following the reaction 4Fe3O4 + O2(g) = 6Fe2O3 (ΔG = −74.982 kcal at 400°C). To maintain the Fe2+/Fe3+ state, Ar atmosphere heat treatment was applied, and the carbon-coated Fe3O4 was analyzed in air.
The TGA results revealed a weight increase to approximately 400°C, followed by a decrease to approximately 700°C, owing to the removal of carbon. In the case of non-carbon-coated Fe3O4, the weight decrease was attributed to the CNT content, as shown in Figure 3a.
Dopamine HCl decomposed and volatilized above 243°C, enabling the formation of carbon-coated C-Fe3O4 through 400°C heat treatment. Further, dopamine HCl began to decompose (melt) above 200°C and fully decomposed at approximately 248–250°C. Therefore, heat treatment at 400°C effectively carbonized dopamine HCl, resulting in carbon-coated Fe3O4.
- a.
Fe oxalate precipitation mechanism
- i.
Fe3+ + 3C2O42−→Fe(C2O4)33− (Fe3+ → Fe2+)
- ii.
Fe(C2O4)33− + 6H2O → FeC2O4·2H2O + 2H2C2O4
- i.
- b.
Oxidation of Fe oxalate and thermal decomposition of dopamine HCl
- i.
FeC2O4·2H2O + C8H12ClNO2 → FeC2O4 + COx + O2 + H2O + Cl2 + CxHy + NOx (<250°C)
- ii.
3FeC2O4 → Fe3O4 + 4CO + 2CO2 + O2 (250–400°C)
- iii.
4Fe3O4 + O2 → 6Fe2O3 (>400–500°C)
- i.
Volatilization of the components in dopamine HCl, such as Cl2, COx, H2O, NOx, and CxHy, led to simultaneous melting and decomposition. When combined with the high-temperature thermal decomposition of FeC2O4·2H2O, which released COx, H2O, and O2, the phase transition to Fe3O4 was observed. The complex interplay of dopamine HCl melting and FeC2O4·2H2O thermal decomposition created a carbon coating with disordered and irregular (closed pore) structures. The closed pores were evident in the SEM analysis of C-Fe3O4, where the rod lengths were relatively short and the thickness slightly increased. Thus, dopamine HCl melted, swaddled, and coated the Fe3O4 particles. The resulting carbon coating affected the morphology by increasing the thickness and creating shorter rods, as observed after the heat treatment.
The carbon formed by dopamine HCl was analyzed using Raman spectroscopy, and the ratio of the intensity of D band to that of the G band (ID/IG) was calculated to observe the carbon coating. The ID/IG ratio was measured as 0.92, as shown in Figure 3b. Additionally, weak peaks related to Fe3O4 were detected at 388 cm−1 and 596 cm−1 in the C-Fe3O4 sample, which were associated with the vibration modes of the Fe–O bond [41]. In contrast, the Fe3O4 sample without the carbon coating exhibited more pronounced peaks at 216 cm−1 and 282 cm−1, which were associated with oxidation reactions during Raman analysis. The peaks indicated the presence of the Fe3O4 phase and were more prominent when no carbon was present [42].
3.3. Carbon Coating on Fe3O4
To gain a more detailed understanding of the gases generated and the oxidation reactions leading to Fe3O4 during the simultaneous decomposition of dopamine HCl and oxidation of FeC2O4·2H2O, Brunauer–Emmett–Teller (BET) analysis was performed to analyze disordered and irregular pores. The analysis was conducted on samples with and without dopamine HCl after heat treatment. For the non-carbon-coated sample without the use of dopamine HCl, the BET surface area was measured at 49.15 m2/g. The adsorption/desorption behavior exhibited a relatively small hysteresis, indicating fewer and smaller pores, as illustrated in Figure 4a. Conversely, the carbon-coated sample with dopamine HCl exhibited a significantly larger hysteresis during adsorption/desorption, indicating the presence of increasingly larger disordered and irregular pores. The BET surface area for the sample was markedly reduced to 4.14 m2/g. The decrease in surface area suggested that the carbon coating formed during the decomposition of dopamine HCl created a more compact structure with fewer accessible pores.
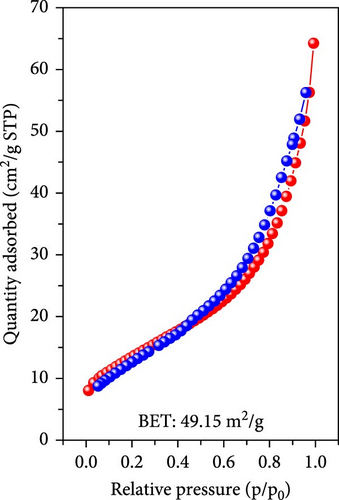
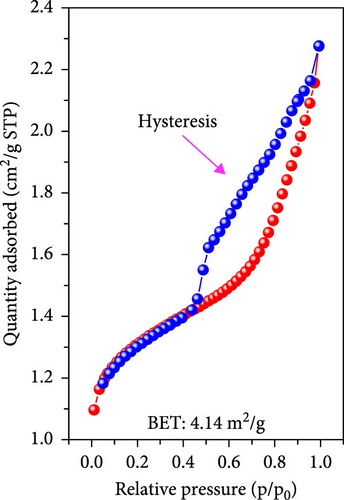
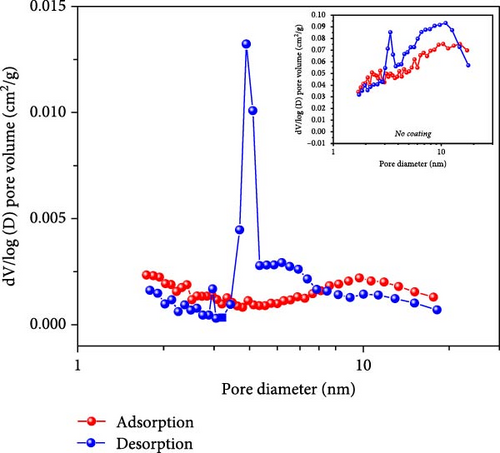
BET measurements, typically conducted at 0.1–0.3 p/po, yielded a correlation coefficient of 0.998. The adsorption and desorption of N2 gas showed significant hysteresis, and a Barrett–Joyner–Halenda (BJH) analysis was conducted, as shown in Figure 4c. The results indicated that during adsorption, some pores of approximately 10 nm were observed, whereas during desorption, pores with a high pore volume of 4 nm were identified. In contrast, the noncoated sample exhibited slight adsorption/desorption hysteresis, but the difference was not as pronounced as that for the coated sample. The behavior was attributable to the carbon coating process, in which dopamine HCl melted and carbonized. The gases generated during the thermal decomposition of FeC2O4·2H2O were not entirely expelled and remained trapped, causing a complex pore structure upon phase transition. Thus, significant hysteresis was observed in the gas adsorption/desorption analysis, indicating the formation of irregular and disordered pores under the carbon-coating heat treatment conditions of dopamine HCl.
In contrast, the BJH analysis of the noncoated sample showed relatively consistent adsorption/desorption BJH values, suggesting a more uniform escape of gases generated during the thermal decomposition of FeC2O4·2H2O without dopamine HCl, resulting in more uniform pores. The difference in pore structure between the coated and noncoated samples underscored the impact of dopamine HCl in creating a more irregular and disordered pore structure owing to the complex interaction between decomposition and carbonization.
The swaddle-type carbon coating with disordered and irregular inner pores, formed by the thermal decomposition behavior of dopamine HCl and FeC2O4·2H2O, was caused by the relatively low heat treatment temperature. We conducted transmission electron microscopy (TEM) analysis to observe Fe3O4 and carbon formed by the combined reactions of Fe oxalate oxidation and thermal decomposition of dopamine HCl. The results demonstrated that carbon-swaddled Fe3O4, with particles, with sizes not exceeding 20 nm, as shown in Figures 5a,b. Random and irregular carbon coating prevented the aggregation of individual Fe3O4. High-resolution TEM analysis revealed that the crystal growth direction of individual Fe3O4 particles was along the (311) plane, as shown in Figure 5c. Furthermore, TEM analysis was conducted on Fe3O4 without carbon coating, as shown in Figure S2. Both low- and high-magnification TEM analyses revealed the aggregation of Fe3O4, and no amorphous layers due to carbon coating were observed at the edge regions.
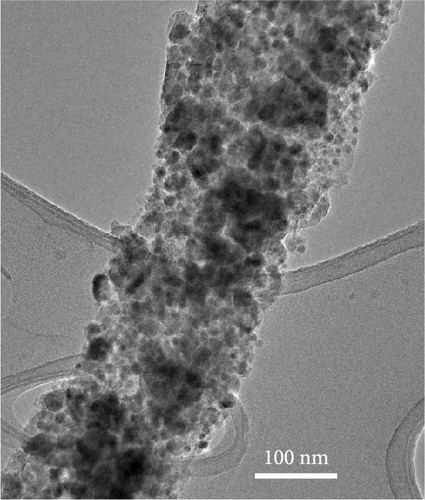
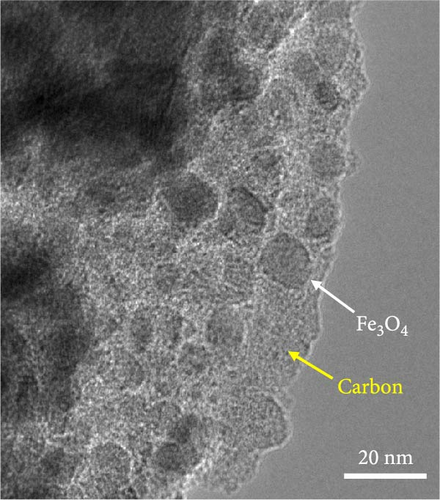
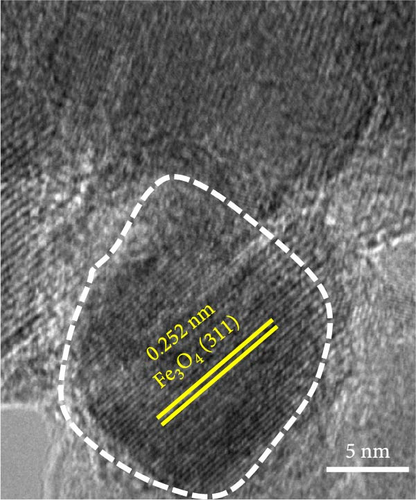
3.4. Electrochemical Properties of Carbon-Swaddled Fe3O4
A lower calcination temperature led to the formation of Fe3O4 with small size and low crystallinity. The carbon-swaddled Fe3O4, formed with disordered and irregular carbon coating, relatively small particle size, and dispersed in carbon, was predicted to exhibit superior electrochemical properties.
The half-cell evaluation results showed that the uncoated sample exhibited very poor rate capability and cycle retention, as shown in Figures 6a,b. Poor properties were observed owing to the low electrical conductivity and aggregation of Fe3O4 particles. In contrast, carbon-coated Fe3O4 demonstrated high performance, maintaining 100 mAh/g even at a current density of 18 A/g (20 C). For context, a current density of 20C corresponds to approximately 3.5 and 7.4 A/g for lithium titanate (LTO) (with a theoretical capacity of 175 mAh/g) and graphite, respectively. Although carbon-coated Fe3O4 showed reduced long-term stability at 20 C, it exhibited good high-rate charge/discharge responsiveness, as illustrated in Figure 6c. Thus, the disordered and irregular carbon coating and the resulting high entropy in the carbon-swaddled Fe3O4 contributed to its improved electrochemical performance, particularly at high current densities.
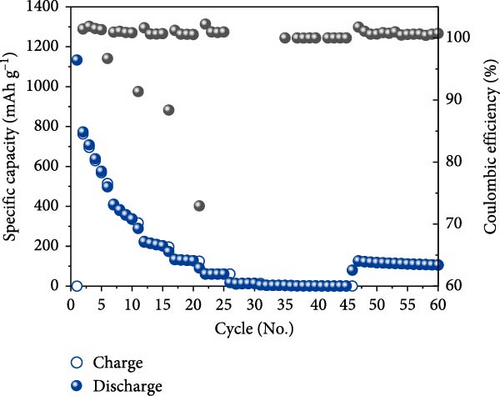
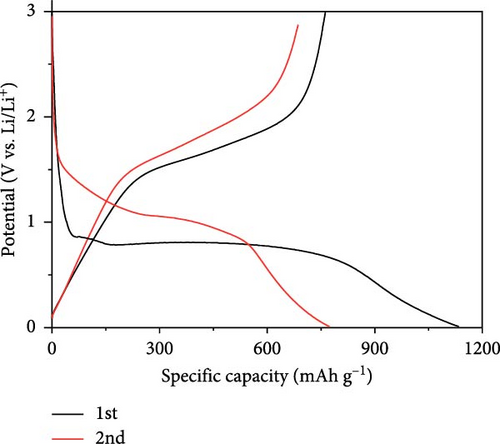
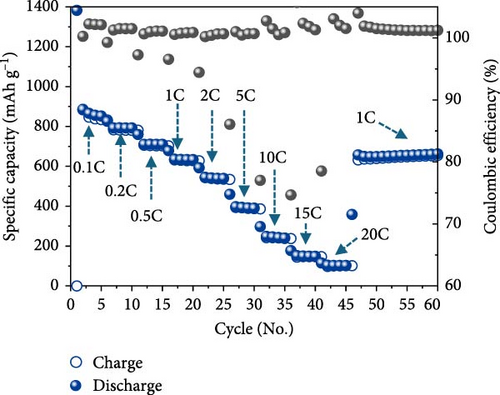
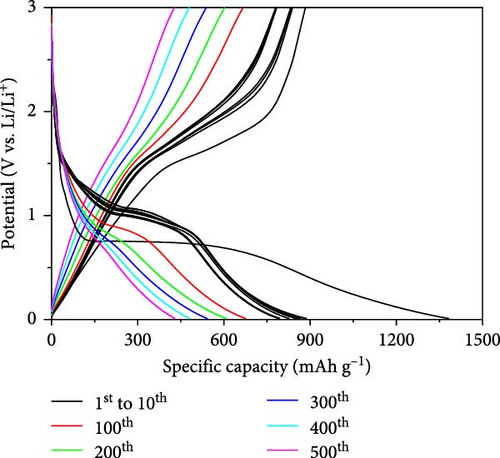
The observed behavior highlights the high discharge rate associated with the insertion mechanism in Li-ion battery anode materials. Further, Fe3O4 is a material with a complex conversion reaction mechanism and achieves high discharge rates and capacities using recycled materials, indicating significant advancements in its electrochemical performance.
The insertion mechanisms of graphite and LTO currently dominate the market owing to their stable insertion/extraction of Li-ions, despite their lower reversible capacities. However, this study exhibits few limitations.
Graphite has a relatively low capacity, whereas LTO suffers from high cost, limited capacity, and a narrow voltage window. Herein, Fe3O4 exhibits a conversion reaction mechanism with a narrow voltage window, offering a theoretical capacity of 934 mAh/g, which is significantly higher than that of LTO. Moreover, Fe3O4 is more cost-effective. The ability to achieve high discharge rates and capacities with Fe3O4 underscores its potential as an economically viable alternative with excellent electrochemical properties, particularly when sourced from recycled materials. This development can have a profound impact on the sustainability and performance of Li-ion batteries.
To observe the long-term capacity retention of the synthesized carbon-swaddled Fe3O4, an evaluation was conducted over 500 cycles at rata of 1C. The results demonstrated that the material maintained a high capacity of 428 mAh/g even after 500 cycles. The capacity was more than 15% higher than the theoretical capacity of graphite, demonstrating its excellent economic value, as illustrated in Figure 6d. We conducted differential capacity analysis (DCA) using dQ/dV plots to investigate the long-term stability behavior of uncoated Fe3O4 and carbon-swaddled Fe3O4. The dQ/dV plots were obtained after 100 cycles at 1C for each electrode in Figure S4a,b. The potential polarization was measured to be 0.77 V for carbon-swaddled Fe3O4 and 1.3 V for uncoated Fe3O4. This behavior indicated that the carbon coating accelerates the diffusion of Li-ions and more effectively facilitates the conversion reactions of Fe3O4, thereby improving the long-term performance of the battery [43–46].
We also conducted EIS analysis. Through EIS analysis, it was observed that the uncoated Fe3O4 initially exhibited relatively higher resistance values during the activation of the electrode, while the carbon-swaddled Fe3O4 showed lower resistance values, as shown in Figure S4c. This could be attributed to the increased interfacial resistance caused by the aggregation of Fe3O4 particles in the uncoated, whereas in carbon-swaddled Fe3O4, the improved dispersion of Fe3O4 particles and enhanced conductivity due to the carbon coating are believed to be the reasons for the lower resistance. After 100 cycles, the Nyquist plot revealed that the carbon-swaddled Fe3O4 maintained the semicircle, while the uncoated Fe3O4 no longer exhibited a semicircle, indicating the degradation of the electrochemical performance in Figure S4d. After 100 cycles, the Rct value for uncoated Fe3O4 was 132.5 ohms, whereas C-Fe3O4 showed a lower resistance of 79.44 ohms, approximately 1.6 times lower. This suggests that proper carbon coating alleviated Fe3O4 nanoparticle aggregation and increased conductivity, inducing it more advantageous in terms of long-term performance with Li-ion diffusion. We compared our data with previously reported Fe3O4-based anodes in Table S1 [47–55].
Additionally, CV analysis of the synthesized carbon-swaddled Fe3O4 was performed to calculate the b-plot and capacitive contribution. The CV results (Figure 7a) indicated that during the reduction reaction at 0.7 V verus Li+/Li, Fe3+ was reduced to Fe2+ and then to Fe0. Conversely, during the oxidation process, which occurred between approximately 1.6 V and 2.0 V, Fe0 was oxidized back to Fe2+ and then to Fe3+. CV analysis was performed within the voltage range of 0–3 V at scan speeds of 0.1, 0.2, 0.4, 0.6, 0.8, and 1 mV/s. The responses of both the anodic and cathodic peaks were calculated. For the anodic fit, the b-value was 0.728 with an R2 value of 0.998, whereas the cathodic fit yielded a b-value of 0.641 with an R2 value of 0.994. As shown in Figure S5, b-values between 0.5 and 1 indicated the nature of the reactions; values closer to 0.5 suggested a diffusion-controlled process, whereas values closer to 1 implied a capacitance contribution [56, 57]. In the anodic and cathodic reactions with b-values of 0.728 and 0.641, respectively, the contributions of diffusion and capacitance were nearly equal for the anodic reaction in Figure S5. The difference in the b values between the anodic and cathodic fits was 0.09, which was attributed to the conversion reaction mechanism. The mechanism involved complex oxidation/reduction reactions between Fe3O4 and Li-ions, in which Fe3O4 was converted to Fe0 to produce Li2O. The reversible formation and decomposition of these materials during electron transfer contributed to the differences observed in the b-plots.
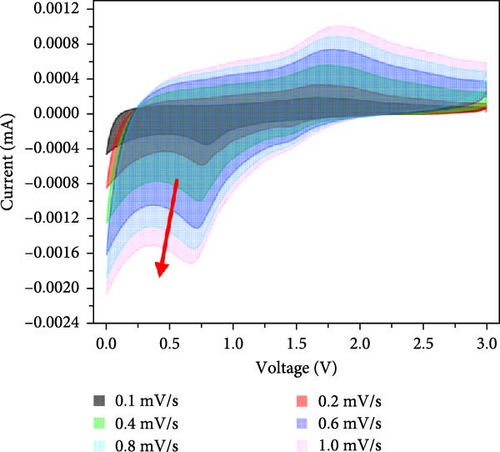
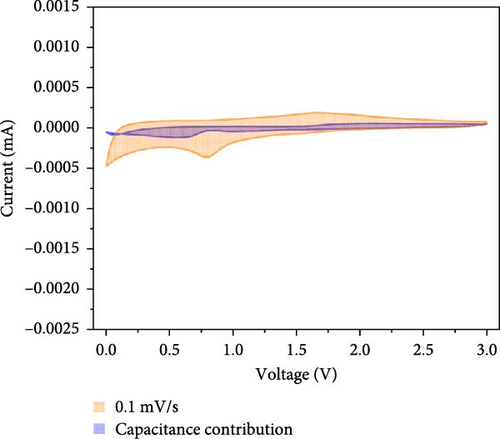
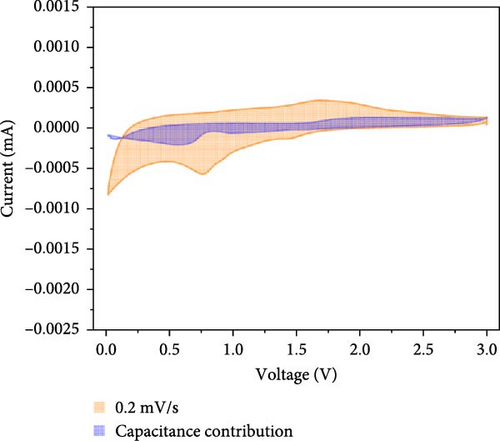
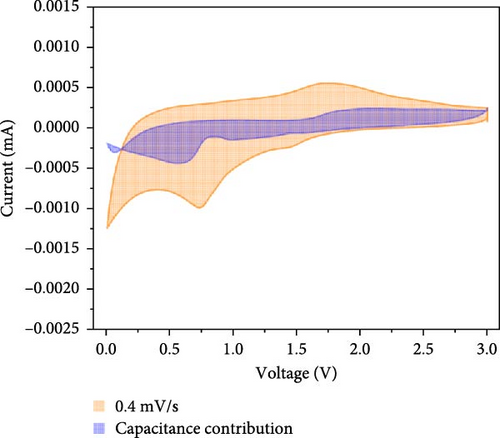
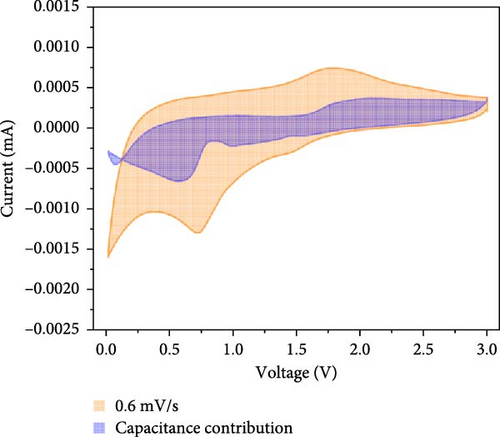
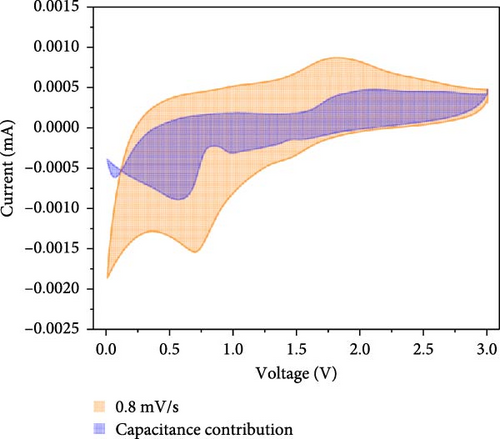
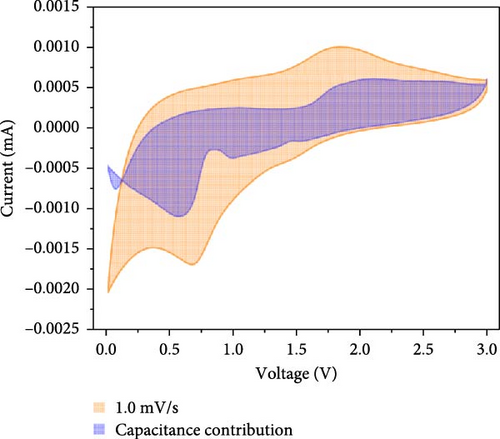
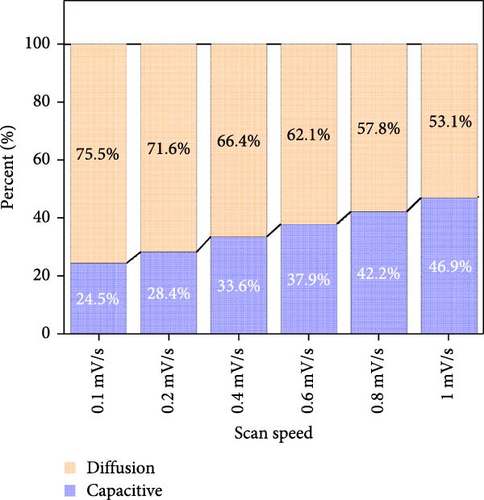
At all the scan speeds, the diffusion contribution was higher than the capacitance contribution. At a scan speed of 0.1 mV/s, the capacitive contribution was measured at 24.5%, increasing to a maximum of 46.9% at a scan speed of 1 mV/s. Thus, the capacitive contribution area increased with scan rate, as shown in Figure 7h. Our analysis indicated that the carbon-swaddled Fe3O4 exhibited a combination of diffusion-controlled and capacitive behaviors. Conversely, the material could be described as an excellent anode candidate that simultaneously exhibited high energy and power densities.
Graphite, a well-known Li-ion battery anode material, has a theoretical capacity of 372 mAh/g. The carbon-swaddled Fe3O4 synthesized from Nd magnet scrap not only allowed for rapid charge/discharge rates similar to those of the insertion materials but also demonstrated excellent cycle retention. Thus, the material exhibited high cost effectiveness considering its recyclability. Therefore, C-Fe3O4 can serve as a promising anode candidate in the current Li-ion battery market, effectively offsetting the limitations of conversion reactions while offering high capacity retention and rate capability.
4. Conclusions
We believed that our research would be the first case of using Nd magnets as a Li-ion battery anode material to harness the high value of the Fe element in permanent magnets. Using Nd magnet scrap, we prepared a composite material of NdF3-Fe2O3 through oxidation/fluorination heat treatment and selectively leached Fe2O3 using weak oxalic acid. The leached solution containing the Fe oxalate complex allowed us to recover needle-like Fe oxalate powder through a low-temperature hydrothermal synthesis reaction with ethylene glycol. Then, the recovered Fe oxalate was converted to single-phase Fe3O4 via heat treatment for use as an anode material in Li-ion secondary batteries. To enhance the electrochemical properties, dopamine HCl was used to produce carbon-swaddled Fe3O4. The resulting carbon-swaddled Fe3O4 exhibited high rate capability and maintained high capacity even after 500 cycles. It was confirmed that the potential polarization differed by 0.53 V depending on the presence or absence of carbon via dQ/dV plots. CV measurements indicated that the diffusion contribution was more dominant within the 0.1–1 mV/s range. However, long-term cycling stability remains a critical factor for the practical application of Fe3O4-based anodes. Future studies will focus on detailed microstructural analysis of C-Fe3O4 electrodes after extended cycling to elucidate the degradation mechanisms and develop strategies for enhancing durability and performance.
The use of Nd magnets is rapidly increasing due to the widespread adoption of EVs and renewable energy. Up to 600 kg of Nd magnets is used in a single wind turbine. The Fe component, found not only in Nd magnet but also various fields, has been considered to have low recycling value and has not been recognized for its potential. The proposed approach offers a viable alternative for addressing the critical issue of capacity shortages inherent in traditional insertion materials.
In addition to Fe recovered from Nd magnet leachate, alternative Fe-containing precursors such as industrial steel scrap, wasted pickling solution, spent catalysts, and electronic waste offer promising sources for Fe3O4 synthesis. These sources are often cost-effective, widely available, and environmentally sustainable. Future studies will focus on evaluating their chemical composition, purity levels, and electrochemical performance to ensure consistent material properties and scalability in battery applications. This approach will further enhance the circular economy’s goals by diversifying Fe recovery sources and minimizing resource dependency on Nd magnets alone.
Conflicts of Interest
The authors declare no conflicts of interest.
Funding
This research was supported by the Basic Science Research Program through the National Research Foundation of Korea (NRF) funded by the Ministry of Education (RS-2020-NR049594). This work was supported by the Korea Institute of Energy Technology Evaluation and Planning (KETEP) (20229A10100100) and the Ministry of Trade, Industry & Energy (MOTIE) of the Republic of Korea. This research was funded by Researchers Supporting Project number (RSPD2025R1045), King Saud University, Riyadh, Saudi Arabia.
Acknowledgments
This research was supported by the Basic Science Research Program through the National Research Foundation of Korea (NRF) funded by the Ministry of Education (RS-2020-NR049594). We thank the Korea Basic Science Institute for the technical support. This work was supported by the Korea Institute of Energy Technology Evaluation and Planning (KETEP) (20229A10100100) and the Ministry of Trade, Industry & Energy (MOTIE) of the Republic of Korea. This research was funded by Researchers Supporting Project number (RSPD2025R1045), King Saud University, Riyadh, Saudi Arabia.
Supporting Information
Additional supporting information can be found online in the Supporting Information section.
Open Research
Data Availability Statement
The data that support the findings of this study are included within the article and the Supporting Information and are also available from the corresponding author upon reasonable request.