Production of Sustainable Liquid Fuel From Waste Polymeric Materials via Thermal Pyrolysis
Abstract
The widespread use of polymeric materials has become an environmental threat as they are durable and nonbiodegradable in nature, which is directly responsible for severe ecological consequences. Thermal pyrolysis offers a sustainable and efficient approach to converting these polymeric waste materials into liquid fuel, which is also referred to as pyrolysis oil (PO). In this study, a novel method was developed for producing oil from a composite of waste polymers that include vehicle tires, tubes, and medical waste. A fixed-bed stainless steel reactor is used to thermally breakdown the waste polymeric feedstock (300–750°C) in an inert environment. The PO was characterized by using Fourier transform infrared spectroscopy (FTIR), GC–MS spectroscopy, and 1H NMR to identify its chemical composition, which confirms the presence of long-chain hydrocarbons, both aliphatic and aromatic. The PO undergoes into further characterization for its physicochemical properties, which indicates that it meets petroleum standards and showing its promise as an alternative fuel. The kinetics of pyrolysis processes were investigated in a batch reactor, which indicating its potential for using in large industrial production. This research highlighted the potential of polymeric waste as a sustainable fuel that paves the way for alternative energy sources and minimizing the environment pollution.
1. Introduction
In today’s world, energy is regarded as the main driving force for the economic development of modern civilization [1–3]. The need for sustainable energy sources has become a great concern to address the issue of fossil fuel reserves and their extensive consumption. The rapid growth of industrial establishments has led to a rise in energy demand [4–7]. Noteworthy observations indicate a multifaceted relationship between energy consumption and economic growth. This connection is underscored by two primary factors: the accessibility of economically viable and environmentally sustainable energy sources and the discernible level of economic development, as gauged by the corresponding energy requisites [8]. Due to the rapid population growth and economic development, energy consumption has been increasing day by day. According to World Data Information, the total liquid fuel consumption in Bangladesh is 122,500 barrels per day, while the country’s fuel production capacity is only 13,500 barrels per day (World Data Information, 2023) [9]. There is a huge shortage of energy in the South Asian region, especially in Bangladesh. These shortages of energy are extremely affecting the economy of Bangladesh as it relies greatly on imports. The potential of waste polymeric materials as an alternative energy source is underscored by its availability, diverse advantages, and myriad applications in our daily lives [10].
Waste management is a major challenge in Bangladesh as it is drawing attention for the efficient recycling and disposal strategies. For instance, a recent study from the pandemic era found that ~82,553 tons of medical waste were generated between March 2021 and May 2022, which is pointing out poor healthcare waste management systems [9, 11]. The annual disposal of automobile tires and tubes is around 20.5 million, which increasing the polymeric waste problem across the world [12]. This is pointing out that it requires necessary efficient recycling methods for sustainable waste management’s solution in both automotive and medical waste. The improper disposal of these materials through combustion poses significant environmental and health concerns. When these materials are burned in the open air, they release pollutants such as CO2, CO, SOx, and NOx, which contribute to air, soil, and water pollution. These emissions from the air create widespread environmental and health consequences, also intensifying the global warming. These emissions are worsening climate conditions and, therefore, it creating ecological imbalances like storms and coastal flooding. That is why making a proper waste disposal system is a top priority.
Conversely, these waste materials possess characteristics of renewable polymer materials, making them increasingly fascinating to the scientific community. Recycling these materials can be advantageous for both environmental pollution control, economically profitable, and reducing energy crises. Particularly, the waste tires produce huge energy after pyrolysis, which is generated in large numbers every year in Europe (2.5 × 106 Tons), North America (2.5 × 106 Tons), and Japan (1 × 106 Tons) [13].
Cars have been a need in our daily life, and more and more cars mean creating more and more waste tires. In this manner, how to manage these waste tires has turned into a troublesome issue, besides recycling waste tires by using a shredder machine or rubber powder production line for further reprocessing. In a waste conversion system, waste materials are usually converted into more useable fuel which can be used as energy sources. There are many ways of converting waste into energy, for instance, pyrolysis, incineration, and gasification. The waste materials also can be converted biologically through fermentation, anaerobic digestion, or a combination of both systems. Recycling waste materials is challenging due to their complex polymeric structure, which requires advanced separation and processing techniques. Two primary factors contribute to the inherent difficulty in this process. First, the principal constituents of waste materials consist of chemically cross-linked polymers characterized by insolubility and nonfusibility. Consequently, transformation into alternative materials is unfeasible without degrading the intricate structural bonds. Second, the composition of waste materials encompasses diverse elements such as carbon blacks, rubbers, steel cords, as well as inorganic and organic components [13]. The pyrolysis technique, as outlined in our manuscript, introduces a less conventional method for recycling waste materials. However, it has attracted growing interest within the scientific community due to its effectiveness in recycling a range of complex waste materials [14–16]. These materials pose challenges for transformation into alternative forms [17, 18]. In the pyrolysis process, chemical compounds are thermally decomposed in the absence of oxygen [19, 20]. Typically, pyrolysis occurs under controlled pressure and at temperatures exceeding 430°C. The thermal decomposition process is particularly effective when semi-volatile or volatile materials are present in the waste feedstock [21–24].
During pyrolysis, the organic compounds in waste materials decompose into three main fractions: gases, liquid fuels, and solid residues consisting of ash and carbon [25]. The produced gases are typically directed to a secondary treatment system for thermal oxidation, often requiring specialized removal equipment to ensure environmental safety. Industrially, various pyrolysis systems, such as rotary hearth furnaces, rotary kilns, and fluidized bed furnaces, are employed to optimize the process for different feedstocks [26–28]. Compared to incineration, pyrolysis operates at lower temperatures (300–800°C) and in an oxygen-deficient environment, making it a more controlled and efficient method. This controlled operation not only minimizes harmful emissions but also enhances the recovery of valuable byproducts like syngas, pyrolysis oil (PO), and biochar, offering significant advantages over conventional waste-to-energy processes. In fact, the global energy crisis is exacerbating the demand of fossil fuel supplies, which leads to an exploration of alternative energy resources. Despite the advancement of waste-to-energy technologies there is limited research that has been conducted on the thermal cracking of complex polymeric waste composites to generate high-quality liquid fuels.
This study explores the feasibility of thermal cracking for processing the polymeric waste materials, from medical waste to rubber derivatives, to produce high-quality PO while conducting a detailed chemical analysis. The methodology involves thermally cracking these polymeric wastes in a batch reactor with the analysis of the chemical and physical properties of the produced fuels. Additionally, a comparative assessment was also conducted of the PO with commercially available fuels to evaluate the quality and applications of PO.
2. Materials and Methods
2.1. Preparation and Characterization of Feedstock
The experiment was performed for vehicle tires, tubes, and medical waste content. Figure 1 illustrates the thermal pyrolysis process of polymeric waste materials. The waste tires were collected from a garage in Jashore City, Bangladesh. Waste tires were cut into small pieces (2–3 mm), and steel wires and fabric fibers were removed. Waste tubes were collected from a garage near around from Jashore University of Science and Technology. It was cut into an approximate size of 2 cm. The medical wastes (plastic infusion bags and infusion sets) were collected from Shaheed Shaikh Abu-Naser Specialized Hospital in Khulna City, Bangladesh. The mass ratio between the plastic infusion bag and infusion set is 2:1. It was cut into small pieces (0.5–1 mm). The collected waste materials underwent a thorough washing process with deionized water, followed by drying in a dryer set at 80°C for a duration of 6 h. This dryer makes this content moisture-free and makes it suitable for the thermal pyrolysis process. The samples were subjected to proximate and ultimate analysis, and the resulting characteristics are presented in Table 1. The American Society for Testing and Materials (ASTM D3173-75) method was utilized for the proximate and ultimate analyses. The proximate analysis of the feedstock was conducted using a muffle furnace (Barnstead), while the ultimate analysis was performed with an elemental CHNS analyzer (Vario MICRO, Model EA 1108). The high calorific value (HCV) of the feedstock was determined using a Bomb Calorimeter. The thermal degradation of the sample turns into more volatile content and compounds with moderately fixed carbon which is described in Table 1. At a suitable operating condition, around 55% of the waste materials are converted to pyrolytic products [29].
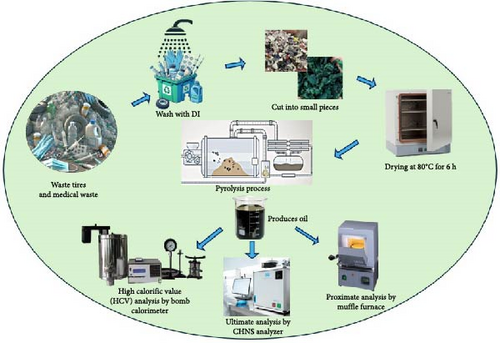
Properties | Vehicle tires | Vehicle tube | Medical waste | Diesel | Kerosene |
---|---|---|---|---|---|
Proximate analysis | |||||
Moisture content | 0.81 | 0.59 | 0.38 | 0 | 0 |
Volatile matter | 61.30 | 56.20 | 98.6 | 100 | 100 |
Fixed carbon | 30.80 | 25.80 | 1.02 | 0 | 0 |
Ash content | 7.09 | 17.41 | — | 0 | 0 |
Ultimate analysis | |||||
C | 82.17 | 40.18 | 82.05 | 86.5 | 85.8 |
H | 9.22 | 4.63 | 11.38 | 13.20 | 14.10 |
N | 0.69 | 0.09 | 0.23 | 0 | 0 |
S | 1.54 | 2.03 | 0.19 | 0.30 | 0.10 |
O | 6.38 | 53.07 | 6.15 | 0 | 0 |
HCV (MJ/kg) | 41.11 | 10.89 | 43.10 | 45.70 | 46.50 |
LCV (MJ/kg) | 38.07 | 9.86 | 40.59 | 42.82 | 43.42 |
The proximate and ultimate analyses of the vehicle tires, tubes, and medical waste compared to other research work on diesel and kerosene in Table 1 [30]. Here, HCV and lower calorific value (LCV) of the vehicle tires and medical wastes are nearly similar to diesel and kerosene, but in-vehicle tubes have very little.
2.2. Instrument Setup and Experimental Procedures
The instrument setup and the experimental procedure are displayed in Figure 2. In this research work, a fixed bed-type reactor of stainless steel was used [13]. At first, the reactor is heated at a maximum temperature of around 750°C [31], and the reactor is designed in such a way that it is insulated from the ambient [32]. U-shaped electric heaters with a total capacity of 1000 W were fixed inside the reactor. The temperature profile in the reactor was observed by a chromel-alumel (K-type) thermocouple, which was capable of measuring 0–1200°C and where the accuracy of measurement was ±2.5°C with a temperature controller. The temperature controller was put at the bottom of the reactor chamber, which was connected to a PID control unit to measure the temperature of the reactor. Hot insulation by glass wool was applied to the reactor which can insulate up to 700°C. N2 gas cylinder with a pressure regulator and a rotameter with a mass flow meter were used. Initially purged reactor with N2 to keep the inert atmosphere and line up oxygen analyzer. At below 2% oxygen, it stopped purging, and pressure was released to the water seal tank, which contained demineralized water (DM) (pH = 6, conductivity = 0.5 µs/cm, total dissolved solids (TDSs) = 0.25 ppm) water. It was released by valves 2 and 3 (needle valve). To remove vapor product from the condensers and to make the reactor inert N2 gas was purged continuously into the reactor system. The produced vapor was passed through two sets of shell-and-tube or Liebig condensers constructed from stainless steel, which facilitated the condensation of vapor into liquid. The condensed liquid was then collected in the glass bottles. Chilled water was used in the second condenser, but cooling water was used in the first condenser to avoid thermal shock. The uncondensed gas passed through an activated carbon column and was collected in a Teflon gasbag. Activated carbon was used here for gas purification and restriction of oil vapors. Restricted oil vapors were condensed after some time, and it was collected by valve 5 (needle valve). The bottom products were also weighted after cooling the reactor to calculate the conversion percentage. Experiments were carried out at 450–650°C (vehicle tires), 375–575°C (vehicle tubes), and 300–500°C (medical waste). The percent composition of different products (% conversion, % liquid, % residue, and % gas) was calculated using the following formula [32] (Equations (1)–(4)):
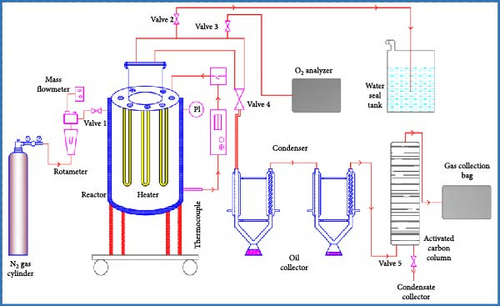
2.3. Characterization Methods
GC–MS of the produced PO was carried out using an Agilent 7890AGC analyzer, where the composition of the produced oil was measured in a DB-5 capillary column (30 m × 0.25 μm) connected with an Agilent 5975C, USA, spectrometric detector. Around 99.99% of helium gas was used as a carrier, which was passed at a particular flow rate of 1.0 mL/min. The introductory temperature was 40°C and was maintained for 5 min; after that, the temperature was increased to 300°C with a heating rate of 5°C/min. The sample (1.5 μL) was injected at 300°C, and the temperature for the ion source was maintained at 230°C. Additionally, the mass spectrometric peak detector was set in a full scan mode, and the scan range was 33–533 m/z. NIST spectral data library was used to detect the chromatographic peaks, comparing their retention time with the retention time of standard chemical compounds, where the matching of the spectrums should be around 85%. Additionally, the compound’s percentage was measured based on the peak area of the total ion chromatogram (TIC).
1H NMR (Proton Nuclear Magnetic Resonance) spectra of the PO were determined in D2O using an NMR spectrometer (Varian UNITY INOVA 400NB) at 400 MHz. Tetramethylsilanen was used as an internal reference during the measurement of 1H chemical shifts. In addition, Fourier transform infrared spectroscopy (FTIR) was carried out for the as-prepared PO to determine the functional groups present in the sample. The FTIR spectra were recorded using an FTIR-4100, JASCO, Japan, with a wavenumber range of 400–4000 cm−1.
3. Results and Discussion
3.1. Physical Properties Analysis of Prepared Liquid Oil
The results calculated using Equations (1)–(6) reveal that the properties of tires, tubes, and medical waste POs exhibit notable similarities with commercial fuels like kerosene and diesel, making them viable alternatives. The oil produced from heating the rubber and plastic waste through pyrolysis has a strong smell and dark brown color. Table 2 presents the fuel properties of PO. Furthermore, the properties of PO are compared with those of commonly used kerosene and diesel. The data in Table 2 reveal that tire PO shares notable similarities with commercially available fuels like diesel and kerosene. For instance, the density of tire PO (919.5 kg/m3) and tube PO (910.6 kg/m3) is slightly higher than that of diesel (820–860 kg/m3) but aligns well with fuel standards. Besides, the gross calorific value (GCV) of the oil’s ranges from 40.11 to 43.10 MJ/kg, slightly lower than kerosene (46.5 MJ/kg) and diesel (45.7 MJ/kg), indicating good energy potential. Flashpoints for all POs (53.7–58.8°C) are comparable to diesel (≥55°C) and fall within the range for kerosene (37–65°C), ensuring safety for handling and storage. The cloud points (−20 to −40°C) and viscosities (1.19–5.98 mm2/s) of the POs also align with diesel and kerosene [34], reflecting their ability to perform under varying temperature conditions. These results demonstrate the potential of POs as alternative fuels to conventional kerosene and diesel. To enhance the GCV, the pretreatment process, including the removal of moisture and inorganic filler, can also improve fuel quality. On the other hand, using appropriate catalysis like zeolites or metal-based catalysts can influence the hydrocarbon length, which will help to improve the fuel combustion efficiency’s processing.
Property | Tire pyrolysis oil | Tube pyrolysis oil | Medical waste pyrolysis oil | Kerosene | Diesel |
---|---|---|---|---|---|
Density (kg/m3) | 919.5 | 910.6 | 840 | 800 | 820–860 |
Gross calorific value (MJ/kg) | 40.11 | 41.89 | 43.10 | 46.5 | 45.7 |
Flashpoint (°C) | 53.7 | 58.8 | 57.1 | 37–65 | ≥55 |
Cloud point (°C) | −20 | −40 to −30 | −25 | −47 | −40 to -30 |
Viscosity (mm2/s) | 1.19 | 5.98 | 4.5 | 2.39 | 2–4.5 |
3.2. FTIR Analysis
FTIR spectra of the PO obtained from medical waste, waste tires, and tubes are displayed in Figure 3. The peak positions and corresponding chemical compounds are shown in Table 3. According to Figure 3, the peaks at around 1458 cm−1 symbolize the presence of C─H bending. The peaks from the range 3000–3100 cm−1 represent the C─H stretching of aromatic rings. The broad peaks at 3000–3500 cm−1 symbolize the presence of amines in the produced PO. Similarly, the peaks at 2850–2960 cm−1 are attributed to the functional group of C─H stretching. The presence of C─H bending and stretching peaks in the FTIR spectrum indicates the existence of alkane in the produced oil. The existence of a hydrocarbon group (C─H) in the liquid indicates that the produced PO has the potential to be used as fuel [35, 36].
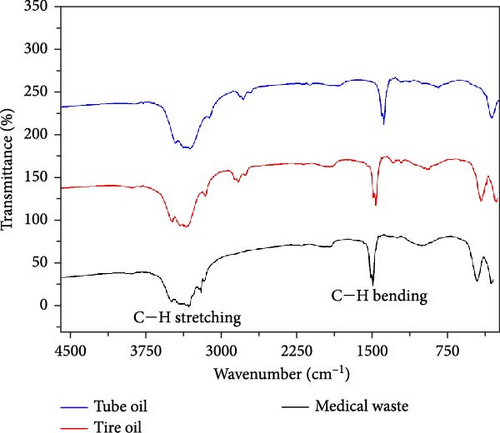
Compound type | Wavenumber (cm−1) |
---|---|
C─H aromatic rings | 3000–3100 |
Alkanes | 2850–2960 |
Amines | 3000–3500 |
Aldehydes, ketones, carboxylic acids, esters | 1100–1300 |
Nitro compounds | 1260–1390 |
Alkenes | 675–1100 |
Alkynes | 610–750 |
3.3. GC–MS Analysis of the POs
The GC–MS analysis reveals the composition of PO, specifically the ratio of aliphatic to aromatic compounds. Aliphatic compounds are desirable in PO due to their higher energy yield with superior combustion efficiency and lower emissions. Aromatic compounds, although improve the chemical stability of the oil but it can decrease combustion efficiency and increase environmental concerns due to higher soot generations. The proper portion between these two components is key to optimizing the performance and environmental impact of PO as an alternative fuel.
The GC–MS analysis of POs extracted from medical waste, waste tires, and tubes reveals a complex mixture of chemical compounds, which are classified as aromatic and aliphatic hydrocarbons. These compounds are formed through the thermal cracking of polymeric waste materials, with their composition varies depending on the source material.
POs derived from abandoned tires and tubes predominantly consist of aromatic compounds. For waste tires, aromatic compounds account for an overwhelming 96.54% of the composition, whereas tubes exhibit a slightly lower but still dominant aromatic content of 74.8%. This dominance can be attributed to the molecular structures of these materials, which are derived primarily from rubber and other polymeric substances with aromatic backbones. In contrast, PO derived from medical waste exhibits a distinct composition, with aliphatic hydrocarbons making up 68.2% and aromatic hydrocarbons comprising 31.8%. In our previous study, plastic-based medical wastes were employed as a potential feedstock of liquid fuel oil by the thermal cracking process. GC–MS study showed that the chemical constituents of degraded yield were mostly aliphatic compounds that are mainly of alkane (16.28%), alkene (10.67%), and nondegraded yield was classified as alcohol (14.65%), and ester (10.38%) and predominant compound of phthalate (42.02%) group [34]. This variation arises from the diverse chemical structures found in medical waste, which typically includes a mix of polyethylene and other plastic materials with less aromatic content.
The GC–MS spectra further identified a variety of chemical compounds within each type of PO. Waste tires and tubes contained notable aromatic compounds, including benzene derivatives and naphthalene compounds. In comparison, the POs from medical waste exhibited significant amounts of aliphatic compounds, such as methyl esters and fatty acid derivatives, alongside smaller proportions of aromatic compounds.
Mechanistically, the pyrolysis of polyethylene and polypropylene-containing materials follows a radical chain scission mechanism. During this pyrolysis process the primary radicals generated through pyrolysis are stabilized via different pathways, including the formation of aromatic compounds through H+ discharge. Additionally, the yielding of olefins or paraffins by proton acceptance and the radical recombination facilitating the synthesis of cyclic hydrocarbon. This aids in elucidating the transportation of polymer waste in POs. The high concentrations of aromatic hydrocarbons (96.54% in waste tires and 74.8% in tubes) indicate their suitability as high energy density fuels due to the HCV of aromatic hydrocarbons. In contrast, medical waste-derived oil is rich in aliphatic hydrocarbon (68.2%) that is suggesting its potential as a cleaner burning alternative.
The GC–MS spectra indicate the composition of the liquid oil obtained from waste tires, tubes, and medical waste, as shown in Table 4.
Component of liquid oil from waste tires | Composition |
---|---|
Benzene, 1-ethyl-3,5-dimethyl naphthalene | 1.85% |
2,3,6-Trimethyl naphthalene | 2.16% |
1,3,8-p-Menthatriene | 8.28% |
Dihydrocarvyl acetate | 10.34% |
Benzene, 1-methyl-3- (1-methylethenyl) | 3.36% |
Benzene, 1,2,4,5-tetramethyl | 2.29% |
Cycloprop[a]indene, 1,1a,6,6a-tetrahydro | 2.54% |
Naphthalene, 2,6-dimethyl | 2.93% |
Component of liquid oil from waste tubes | Composition |
3,5-Octadiyne | 3.20% |
1,3,5,7-Cyclooctatetraene | 2.02% |
Mesitylene | 2.74% |
p-Octyloxybenzonitrile | 4.0% |
D-Limonene | 5.32% |
2-Pentene, 2,3,4-trimethyl | 2.62% |
4-Phenylbut-3-ene-1-yne | 4.33% |
Naphthalene, 1-methyl | 2.43% |
Diisooctyl phthalate | 4.11% |
Component of liquid oil from medical waste | Composition |
Cyclopropaneacetic acid, 2-hexyl | 2.20% |
2-Propanol, 1,3-dichloro | 7.02% |
1-Propanol, 2,3-dichloro | 2.39% |
Cyclotetrasiloxane, octamethyl-trisiloxane | 4.12% |
1,1,1,5,5,5-Hexamethyl-3-[(trimethylsilyl)oxy] | 2.75% |
2,2-Dimethyl-3-hexanol acetate | 2.18% |
Benzoic acid | 2.02% |
Phthalic anhydride | 2.13% |
Hexadecanoic acid, methyl ester | 28.46% |
Methyl stearate | 17.32% |
The high aromatic content in oils derived from tires and tubes suggests a potential for higher energy density, making them suitable for fuel applications. The identification of specific compounds, such as benzene derivatives, naphthalene, esters, etc., underscores the variability in fuel characteristics and highlights the need for tailored refining processes to optimize these oils for specific energy applications. The presence of methyl esters and fatty acid derivatives in medical waste-derived oils indicates a different chemical behavior. Similar to the findings of Cit et al. [37], polyethylene-rich wastes generate fewer polycyclic compounds, whereas polypropylene generates more complex aromatic structures. The as-produced primary radicals are usually not stable and need to be stabilized. The stabilization can be attained by discharging an H+ from the structure to generate aromatic or any other highly stable hydrocarbon. The radicals also can be stabilized by forming olefins or paraffin accepting a proton (H+) or primary radicals can combine with other radicals to form a cyclic structure [38, 39].
The GC–MS analysis underscores the influence of feedstock composition on the chemical profile of POs. These insights not only highlight the potential of converting diverse waste materials into valuable energy resources but also emphasize the need for customized treatment and utilization strategies based on the specific chemical characteristics of the pyrolysis products. The present work is an effort to produce liquid fuel oil from plastic-based medical wastes through the thermal cracking process under oxidizing conditions.
By linking the GC–MS results to fuel properties, this study underscores the versatility and potential of POs in contributing to sustainable energy solutions.
3.4. 1H NMR Analysis of the POs
The information on the chemical environment of H2 molecules in the liquid oil is determined using a 1H NMR [40, 41]. Figure 4a–c describes the NMR spectrum of different POs obtained from waste tires, tubes, and medical waste. This technique identifies the distribution of aromatic and aliphatic H atoms (hydrogen chemical shifts), correlating the structural properties of the oil to its source materials.
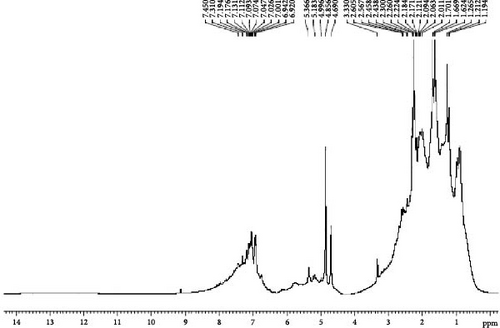
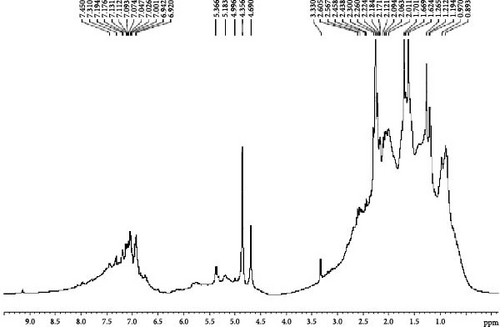
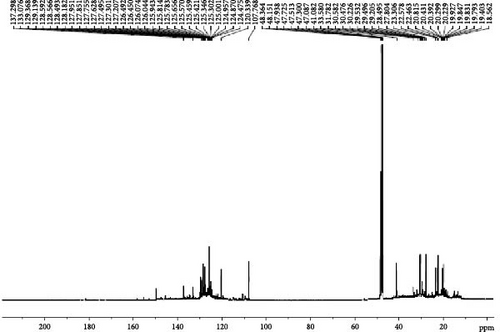
The chemical composition of POs can be further elucidated through the analysis of proton signals in the NMR spectrum, particularly in the regions corresponding to aromatic and aliphatic hydrogens. In the atomic region of the NMR spectrum (6.1–8.1 ppm) the proton signals were observed that correlate with hydrogen atoms bonded to aromatic rings. These chemical shifts are characteristics of aromatic compounds in POs that exhibit the presence of conjugated π-electron systems that influence the deshielding of protons in this spectral region.
The aliphatic area of the NMR spectrum (0.89–2.6 ppm) reporting that the hydrogen atoms are associated with aliphatic groups, such as ─CH, ─CH2, and ─CH₃ groups. Notably, in this region, the oil obtained from medical waste had higher signal intensities than tire and tube oils, which clearly indicating the presence of aliphatic hydrocarbons. This variation emphasizes the impact of feedstock composition on the pyrolysis process, reflecting the chemical diversity and different molecular properties of the precursor components. This variation in feedstock composition significantly impacts the pyrolysis process due to the chemical diversity and distinct molecular characteristics of the precursor materials. The study reveals that waste tires and tubes contain POs with high aromatic compounds that are attributed to their polymeric structure. However, medical waste oil has a higher proportion of aliphatic hydrogens, likely due to the presence of polyethylene and nonaromatic plastics in the feedstock. This highlights the impact of feedstock composition on the chemical properties of POs.
The 1H NMR findings corroborate the GC–MS data, highlighting similar trends in the distribution of aromatic and aliphatic compounds across the different POs. An interesting observation is the parallel trend between the aromatic and olefin content in the oils, suggesting that the production of olefins during pyrolysis contributes to the aromatic content, possibly through stabilization and structural rearrangement of primary radicals.
The chemical profile of the PO, as reflected in the 1H NMR spectra, is strongly influenced by the feedstock composition, particularly the proportion of aromatic versus aliphatic polymers. The higher aromatic hydrogen content in tire and tube oils suggests a potential for high-energy-density fuels, whereas the aliphatic-rich medical waste oil may have unique applications due to its distinct chemical properties. The relation in between olefinic and aromatic hydrogen content depicts the stabilization mechanism of radicals during the pyrolysis process, specifically in the conversion of olefins to aromatic hydrocarbons.
Through 1H NMR analysis, the distinct chemical environments of hydrogen atoms are characterized, which not only validate the GC–MS results but also offer clear understandings into the structural and chemical behavior of the produced oils. This supports the oil’s extensive possibilities for the energy and industrial sectors.
3.5. Pyrolysis Mechanism
The proposed mechanism for the production of PO from waste tires, tubes, and medical waste is shown in Figure 5. The process begins with the random β-scission of polymeric materials, where weaker sp3 C─C bonds break, generating free radicals. The cleavage of the polyolefin C─C bonds produces a significant number of primary radicals and molecular fragments. These primary radicals undergo further degradation through mid-chain and end-chain scission, leading to the formation of secondary radicals and low molecular weight products. The hydrogen chains are subsequently rearranged via intra-molecular and intermolecular hydrogen transfer reactions. During intramolecular transfer, protons are relocated from the end to the middle of the radical chain, resulting in an increase in isomerization and olefin formation. Concurrently, paraffins are formed through intermolecular hydrogen transfers between radicals and other molecules in the reactor. In the termination phase, radicals are stabilized through disproportionation or recombination reactions. This stabilization promotes the formation of aromatic or cyclic compounds via cyclization and aromatization processes. Homogeneous heat transfer within the reactor enhances proton transfer, ensuring efficient stabilization of radicals generated from β-scission. Consequently, the yield of olefins, paraffins, and aromatic compounds is significantly increased. This mechanistic pathway highlights the intricate interplay of bond cleavage, radical formation, hydrogen transfer, and stabilization reactions, ultimately producing a variety of hydrocarbon products with potential energy applications [42].
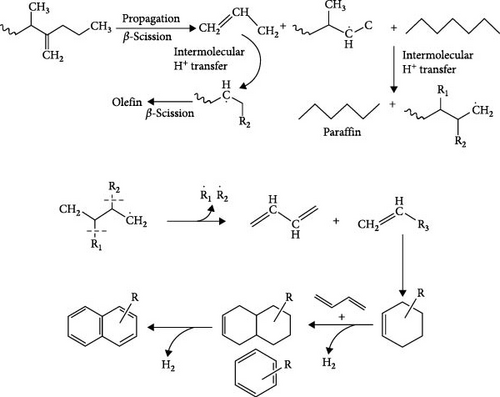
The goal of the mechanism is to produce a variety of hydrocarbons with potential energy applications. By understanding the interplay of bond cleavage, radical formation, hydrogen transfer, and stabilization, researchers and engineers can optimize the pyrolysis process to create alternative fuels that align with sustainability goals. The mechanistic understanding supports the utilization of waste materials, such as tires, tubes, and medical waste, which are challenging to manage. Converting these wastes into valuable fuels reduces environmental pollution, provides an alternative to fossil fuels, and contributes to a circular economy. However, the described mechanism serves as a blueprint for understanding and refining the pyrolysis process, enabling the production of high-quality fuels from waste materials. It integrates fundamental chemistry with practical applications, making it essential for advancing waste-to-energy technologies.
4. Conclusions
The growing accumulation of polymeric waste poses a significant environmental challenge due to its durability and nonbiodegradable nature. Despite global dependence on fossil fuels, pyrolysis offers a sustainable solution by converting waste polymers into valuable hydrocarbon fuels. This study demonstrates the feasibility of producing PO with comparable fuel properties. The pyrolysis experiment is conducted in a fixed bed stainless steel reactor to ensure the complete decomposition of waste tires, tubes, and medical wastes. Where the temperature was around 750°C for yielding maximum desirable hydrocarbon products from polymeric waste. The PO that produced has a wide variety of organic compounds with carbon chains ranging from C5 to C20. The variation of carbon chain lengths indicating that the complete breakdown of the polymeric waste, which resulting the formation of aliphatic and aromatic compounds. While the oil from medical waste resulted 68.2% aliphatic and 31.8% aromatic hydrocarbons. On the other hand, higher aromatic contents were found from used tires and tubes that were 96.54% aliphatic and 74.8% aromatic. These compositional differences have significant consequences in produced oil as the higher the aromatic content in oils exhibits higher hydrocarbons, which is more suitable for automotive or residential heating applications as it emits lower emissions, faster ignition, and cleaner combustion. Although these oils have various compositions, but the physical and chemical compositions are closely resembled with commercial diesel and kerosene. FTIR spectra exhibited characteristic hydrocarbon (C─H) by identified peaks at 2850–2960 cm⁻1, confirming the significance for fuel performance. The GC–MS analysis revealed a balanced composition of aromatic and aliphatic compounds, which contributing to high energy density and enhanced combustion characteristics. Furthermore, the oils aromatic content was examined by 1H NMR spectroscopy, which reveals the presence of aromatic hydrogens in the 6.1–8.1 ppm range. These investigation results show that the oils are good candidates for use as efficient alternative fuels in various applications. Pretreatment of fuel, including moisture and inorganic filler removal, will enhance GCV and fuel quality. Catalysis using zeolites or metal-based catalysts has an effect on hydrocarbon length; thus, it will help in improving combustion efficiency. Refining methods like fractional distillation can separate lighter hydrocarbon for petrol and higher hydrocarbon for diesel. Blending the PO with traditional fuels such as diesel or biodiesel will improve fuel stability and ignition characteristics. Sulfur-containing fuels can produce sulfur oxides, which lead to acid rain and respiratory issues. So, desulfurization will also be important as it ensures environmental compliance and reduces emissions.
Conflicts of Interest
The authors declare no conflicts of interest.
Funding
This research did not get a particular award from subsidizing organizations in general society, business, or not–revenue driven areas.
Acknowledgments
The authors acknowledge the technical support of the Laboratory of Materials, Energy and Nanotechnology (MENTECH Labs), Jashore University of Science and Technology, Bangladesh.
Open Research
Data Availability Statement
The data underlying this article will be shared upon reasonable request to the corresponding author.