Poly(Methyl Methacrylate) Composites With Modified Human Hair and Their Static and Dynamic Mechanical Properties
Abstract
In this work, the impact of using grafted hair as reinforcing agent for making composites has been studied and compared with composites using virgin hair. For this purpose, the composites have been prepared via compression molding using a thermoplastic resin, poly(methyl methacrylate) (PMMA), as matrix, and virgin or grafted human hair (HH), HHact-g-PMMA_1.75, and HHact-g-PMMA_2, with 56% and 78% of grafting percentages, respectively, were taken as reinforcement material, and their properties have been compared. The hair weight fractions in composites were varied from 15% to 60%. The SEM micrographs of the fractured surface of the tensile specimen of virgin HH-reinforced PMMA composites show hair pullouts. In contrast, in graft copolymer-reinforced PMMA composites, failure mainly occurs at the hair and not at the hair–matrix interface, showing better adhesion. This was supported by AFM images in which a decrease in surface roughness for grafted hair-reinforced composites was observed. The PMMA composites with grafted hairs showed improved mechanical properties than PMMA in contrast to composites with virgin hairs in which there was loss of tensile strength. On addition of 15% of HHact-g-PMMA_1.75, the tensile strength raised by 21.86%, while in the case of HHact-g-PMMA_2 graft copolymer, the tensile strength was increased by 87.44% w.r.t virgin HH. The hair content up to 45% showed improvement in mechanical properties; however, further increase in hair content leads to a decrease in the mechanical strength. Dynamic analysis also showed an increase in storage (E′) and loss modulus (E′′), enhanced with the increase in hair concentration and reached the maximum for the 55:45::PMMA:hair ratio. The increase in E′ and E′′ was more when grafted hairs were used as the reinforcing agents. As compared to composites with virgin HH, an increase of 57–98% for E′ and 46–80% for E′′ was observed for composites with HHact-g-PMMA_1.75. Similarly, for HHact-g-PMMA_2 hairs, an increase of 49–102% in E′ and 45–98% for E′′ was observed. The present work thus shows that the use of grafted hairs results in the enhancement of adhesion of hair and matrix resulting in the improved properties.
1. Introduction
Natural fiber-reinforced materials have gained considerable importance due to the growing need of lightweight material with less environmental impact. They offer numerous benefits, low hazard, low cost, biodegradability, easy availability, etc. [1]. Every year, more than 5 million tons of animal fiber such as feather-, human hair (HH)-, and wool-based byproducts are produced from slaughterhouses, barber shop, the poultry, etc. [2]. Recent studies have demonstrated that animal fiber can be useful to create biodegradable polymer composites without affecting the fibers’ inherent qualities. However, some disadvantages, such as inferior surface quality and moisture absorption, affect the interfacial adhesion between the matrix and the fiber. The modification of hairs via several methods, such as graft copolymerization, acid/alkali treatment, and silane treatment, enhances the potential of cross-linking between matrix and hair [3].
HH is a slow-degrading fiber; open dumping of hair in large quantities generates several environmental concerns and is considered as a biological waste. Leachate from these wastes gradually raises the amount of nitrogen in water bodies, leading to eutrophication issues. The thermal breakdown of hairs can create a strong odor and foul smell due to sulfur, which causes severe discomfort and uneasiness [4]. HH is made up of keratin protein and contains ~45%–50% carbon, 25%–27% oxygen, 6% hydrogen, 15%–17% nitrogen, and 3%–5.0% sulfur. It is mainly composed of three layers: the medulla, the intermediate layer cortex, and the outermost layer cuticle [5]. It is the cortex that is mainly responsible for the tensile properties of HH, not the cuticle. Elasticity is one of the significant properties of HH, due to which it can undergo moderate stretching. The durability and elasticity of the HH are governed by the interactions of proteins in the cortex. The cortex is a cross-linked polymeric system comprising low-sulfur and high-sulfur proteins [6]. HH is highly abundant and low cost, and it is also a fact that a single strand of HH can withstand a load of 100–140 g. This fiber is intensely flexible and regains its initial mechanical characteristics with minimal degradation even after undergoing multiple deformations [7]. The vast majority of the mechanical property studies of HH are on the macroscales and employ conventional methods such as tension, torsion, and bending tests. The mechanical properties of HH are mainly determined by the microfibrous structures known as keratin intermediate filaments, which contain highly ordered microfibrils, and matrix impart toughness to the hair fiber [8].
Poly(methyl methacrylate) (PMMA) is lightweight, has excellent optical clarity, and is compatible with the human body. PMMA, chosen for the present study, represents a good choice, because of its great variety of practical applications and has been modified with a wide range of reinforcements. PMMA applications gets limited due to its brittle nature and lower mechanical strength when it is exposed to heavy loading [9]. Many studies have been carried out to investigate the mechanical properties of PMMA. From the literature, it is evident that keratin fibers can substantially modify the mechanical and thermal behavior of PMMA and therefore has been considered as suitable matrix for HH as well [10–14]. HH as reinforcement material, due to its high tensile strength and stiffness, can significantly alter the mechanical behavior of PMMA, making it a useful model system for other polymers.
The uses of HH as reinforcement material for composites have been investigated over the years by various research groups. Saif and Islam [15] investigated the mechanical properties of epoxy composites reinforced with bagasse and HH fibers. They reported that the hybrid composite fibers wih HH shows better tensile and flexural properties than the composite with untreated fiber. Ragul et al. [16] prepared the HH-reinforced HDPE composites using compression molding. They found that tensile strength and modulus improved on increasing the fiber’s weight percentage in the composites. These composites can be utilized in sewage pipes, cables, etc. Choudhry and Pandey [17] studied the flexural and impact properties of HH-reinforced polypropylene (PP) composites. They concluded that reinforced composites had improved flexural and impact strength compared to neat PP. Prasad, Rao, and Kiran [18] evaluated the mechanical properties of HH-reinforced polyester sheets. They found that on increasing the hair loading, composites have effectively improved tensile and flexural properties. Suman, Naidu, and Rao [19] prepared HH-reinforced epoxy composites with different ratios (0%–30%) and lengths (0.5–2 cm). The maximum values 17.5 MPa, 42 MPa, and 7J, for tensile, bending, and impact tests, respectively, were recorded for the samples with a length of 1.5 cm with a 20% reinforcement of HH. Salih et al. [20] fabricated the HH-reinforced epoxy composite via hand layup technique using a fiber weight ratio of 10%. The results showed an increase in modulus of elasticity, impact strength, and compressive strength of the composite to ~15%, 35%, and 35%, respectively, compared to unreinforced epoxy. Jain and Kothari [21] studied HH fiber-reinforced concrete. They found a tremendous increment in the mechanical properties of concrete on increasing the weight ratio of HH. The addition of HH improves the tensile and compressive strength and binding properties of concrete.
To the best of our knowledge, most of the research studies in the area of natural fiber composites are focused on cellulosic fibers but not so well explored with HH. The main drawbacks of cellulosic fibers are poor moisture resistance, finite length, and incompatibility with the polymer matrix [3]. This is due to their inherent characteristics, such as the hydrophilicity of cellulose fibers, which can decrease interfacial adhesion.
In our previous work [22], we reported the modifications of HH surface through graft copolymerization of MMA and studied the effect of grafting on topography, adsorption behavior, and thermal and mechanical properties of grafted hairs. We anticipated that these modified graft copolymers of HH can be used as a reinforcement material in composites and will show better interfacial adhesion as compared to HH used without grafting, that is, virgin HH. This is because the oligomeric chains of the matrix are now covalently linked with the hair. The better interfacial adhesion will in turn result in improved mechanical properties. Thus, the objective of present work is to show the effect of using modified hair via grafting for making composites. For this, the hairs grafted with 56% and 78% of PMMA chains designated as HHact-g-PMMA_1.75 and HHact-g-PMMA_2, respectively, have been used. The numbers 1.75 and 2 represent the weight ratio of MMA with hair in the feed. In addition to the effect of percent grafting, the effect of hair content has also been studied by varying the hair content in composites from 15% to 60%. The natural choice of matrix to prepare the composites is PMMA as the hairs are grafted with oligomeric chain of PMMA. Thermal, mechanical, and dynamic mechanical properties of composites have been investigated and compared.
2. Experimental
2.1. Materials
The HH was collected from a nearby salon and washed twice using a shampoo solution to get rid of any oil and dirt. Azobisisobutyronitrile (AIBN), MMA, and tetrahydrofuran (THF, AR grade) were purchased from Loba Chemie Pvt. Ltd., India. AIBN was purified by crystallization before use. MMA was made free from stabilizers by following standard procedure.
Three types of sample hairs were used for composite preparation: virgin HH and graft copolymers, HHact-g-PMMA_1.75, and HHact-g-PMMA_2, with 56% and 78% of grafting percentages. Both graft copolymers were prepared via graft copolymerization technique using the method reported in our earlier works [22]. The grafted copolymers are known as HHact-g-PMMA_n where n represents the weight ratio of MMA w.r.t. HH. For instance, the grafted copolymer of HH and MMA with a weight ratio of 1:1.75 is denoted by the symbol HHact-g-PMMA_1.75. The 1–2 cm average length of the HH is used for composite preparation. The nomenclature used for PMMA-HH composite is shown in Table 1.
Composites | Description |
---|---|
PMMA-com-(virgin HH)_ x:y | Virgin human hair reinforced PMMA composites with a ratio of PMMA and fiber as 40:60, 55:45, 70:30, and 85:15 |
PMMA-com-(HHact-g-PMMA_1.75)_x:y | HHact-g-PMMA_1.75 graft copolymer-reinforced PMMA composites with a ratio of PMMA and copolymer as 40:60, 55:45, 70:30, and 85:15 |
PMMA-com-(HHact-g-PMMA_2)_x:y | HHact-g-PMMA_2 graft copolymer-reinforced PMMA composites with a ratio of PMMA and copolymer as 40:60, 55:45, 70:30, and 85:15 |
- Note:x (weight percent of matrix) = 40, 55, 70, or 85, and y (weight percent of hair) = 60, 45, 30, and 15.
2.2. Preparation of HH-Reinforced PMMA Composites
Initially, the inhibitor-free MMA was prepolymerized at 65°C temperature using AIBN (2%) for 2 h in a water bath under a nitrogen atmosphere to produce viscous PMMA syrup. We mixed the required hairs and prepolymer syrup to develop the composite in a predetermined ratio. Hairs were trimmed to a length of 1–2 cm and well combed to prevent clumping in the preparation of composites. The mold was made up of steel and specially designed to produce 3-mm-thick composite sheets. The HH-PMMA composite sheets were prepared using a hand layup technique followed by compression molding. The first layer of PMMA prepolymer syrup was spread evenly with the use of a brush in the mold. After that, hairs were evenly spread over the syrup layer. Then, again, PMMA syrup was applied over the hairs until all the hairs got wet, followed by another layer of hairs. The excess PMMA syrup was removed by gently pressing the upper mold onto the lower mold. It was kept for at least 3–4 h to cure at room temperature. Then, the steel mold was transferred into the compression molding machine, and the temperature was gradually increased up to 120°C and 2000 PSI for 3 h. Then, the prepared composites with 3 mm thickness were cooled down and gradually removed from the mold. Silicon spray was used as a release agent to avoid the sticking of composites with mold. The same method was applied to prepare various composites using different hairs.
2.3. Methods
2.3.1. Tensile Test
Tensile tests were carried out in accordance with ASTM D638 standards using a computerized universal testing machine (UTM) (Instron model 5982, Loadcell 30 kN). The cross-head speed (5 mm/min) and the room temperature (23°C) are maintained throughout the test till rupture of the specimen. Five samples were tested for each composition to determine the tensile strength, modulus, and toughness. Figure 1a displays the specimen before and Figure 1b after tensile testing.

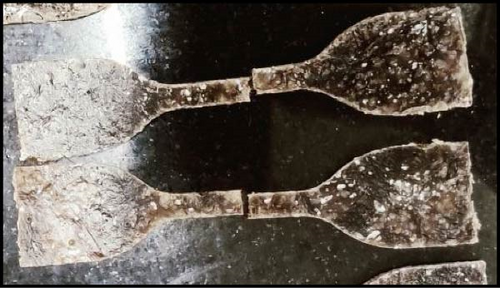
2.3.2. Flexural Test
The flexural tests were done following ASTM D790 standard at room temperature (23°C) using the UTM (Instron model 5982) in a three-point bending configuration. Five samples of each composite were prepared for various hair loadings (15–60 wt.%). Figure 2a displays the specimen before and Figure 2b after flexural testing.
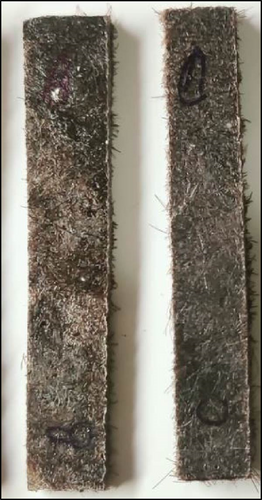
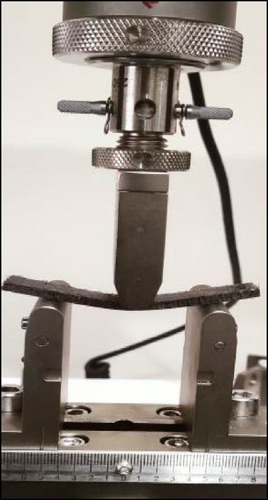
2.3.3. Impact Test
The impact tests were carried out per ASTM D256 standard using a standard Izod impact tester at room temperature (23°C) to determine the impact strength. The digital image of the specimen before and after is shown in Figure 3a,b.

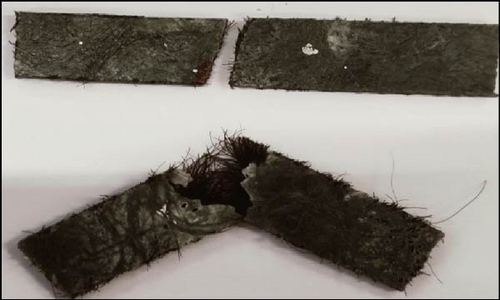
2.3.4. Dynamic Mechanical Analysis (DMA)
DMA test was done as per ASTM D5023 standard in a typical single cantilever configuration using a Q 800 DMA supplied by TA Instrument, USA. The samples were tested from 30 to 130°C at a frequency of 1 Hz. In DMA, a fluctuating force is applied to the composite material, and the viscoelastic behavior of the material in terms of storage modulus (E′), loss modulus (E″), and tan δ has been found.
2.3.5. FT-IR and SEM Analysis
FT-IR analysis of copolymer and composites was carried out on the Shimadzu IRAffinity-1S spectrophotometer using the KBr pellets method. The range 4000–400 cm−1 was used. SEM was used to analyze the morphology of the composites (Quanta FEG 250). Fractured specimens were sputter-coated in gold and placed onto aluminum stubs before SEM analysis.
2.3.6. Atomic Force Microscopy (AFM)
Small pieces of dimensions of 10 × 2.5 × 2.5 mm from the fractured surface of HH-reinforced PMMA composites in tensile tests were taken. The surface was further polished with a grit paper of size 800. High-resolution AFM Ntegra Prima (NT-MDT Spectrum Instruments, Moskow, Russia) was used to investigate topography and roughness of composite specimens. The measurements were carried using an HA_HR/25 probe, with the tip having a typical spring constant of about 34 N/m and resonant frequency of about 395.263 kHz. Randomly five areas were chosen from each sample, and two-dimensional (2D) and three-dimensional (3D) images were taken of 5 × 5 µm plane with 1024 × 1024 resolutions at a scan rate of 0.6 Hz. The images were taken in a semicontact mode and were treated with a third-order plane fit to accurately calculate roughness parameter (Rq) which is the root mean square of height value, obtained from the data collected.
3. Results and Discussion
3.1. FT-IR Analysis of HH-Reinforced PMMA Composites
FT-IR spectra of virgin HH, graft copolymers, and composites were helpful for the structural analysis of composites and are shown in Figure 4. The region 3310–3142 cm−1 corresponds to amide I and amide II bands in virgin HH. The O─H stretching vibrational peaks of the free and hydrogen-bonded hydroxy group in the hairs was observed in the range of 3580–3282 cm−1. The C─H stretching peaks for methyl and methylene groups were observed at 2957 and 2923 cm−1 [23]. The characteristic peak of the carbonyl group of amide I was observed at 1633 cm−1. On the other hand, for amide II bands, C─N stretching and N-H bending peaks were observed in the regions of 1560–1517 cm−1. The characteristic peak at 1734 cm−1, due to the carbonyl group of ester, confirms the presence of PMMA chains on both grafted copolymers of HH. The O─H stretching in the 3615–3118 cm−1 region of PMMA composites reinforced with virgin HH and graft copolymers is due to the presence of moisture. This region also shows amide I and amide II bands of keratin protein. The peaks at 2993 and 2948 cm−1 are attributed to C─H stretching in the composites. The peak for the carbonyl group of the PMMA was observed at 1730 cm−1, whereas the carbonyl group of amide I was observed at 1620 cm−1. The symmetric vibrational peaks at 1143 and 980 cm−1 showed the presence of C─O─C and –OCH3 in the PMMA matrix [24]. The reduced peak intensities of the functional groups in the composites w.r.t. graft copolymers and virgin HH signify that functional groups are engaged in bonding between hair and matrix.
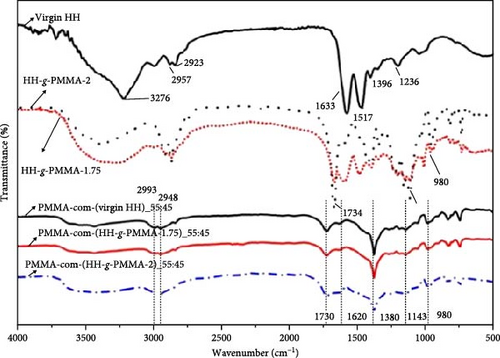
3.2. SEM and AFM Analysis of Fractured Surfaces of HH-Reinforced PMMA Composites
Interfacial studies were done using SEM to study the effect of grafting on hair splitting, hair pullout, debonding, matrix cracking, and hair–matrix adhesion in virgin HH and graft copolymer-reinforced PMMA composites. The surface of the graft copolymers of HH becomes increasingly rough and porous as the grafting percentage increases, and a thick coating of polymer covers the hair almost completely, which is evident from our previous work [22]. The roughness along the surface can contribute to interfacial strength in the composite, which is one of the possible applications for this fiber. The SEM micrographs of the fractured surface of the tensile specimen are shown in Figure 5a–f. The typical fractured surface of virgin HH-reinforced PMMA composite is shown in Figure 5a,5b. The fiber pullouts are observed due to the weak interfacial bonding between the PMMA matrix and the virgin HH. This insufficient interlocking is due to the waxy layer of the cuticle of virgin HH. The SEM images of graft copolymer-reinforced PMMA composites confirm that failure mainly occurs at the hair, not at the fiber–matrix interface, as evidenced by the broken fiber ends and/or sites, as shown in Figure 5c–f. The introduction of polar groups, such as carboxyl and ester, and roughness on the surface of hairs due to grafting resulted in the strong interfacial bonding between the graft copolymers and PMMA matrix. This increases the interlocking of graft copolymers more as compared to virgin HH with the matrix. From the SEM micrographs of PMMA-com-(HHact-g-PMMA_1.75)_55:45 and PMMA-com-(HHact-g-PMMA_2)_55:45 composite, it is evident as the grafting percentage increases, the pits become lesser in the composite due to the effective cross-linking between grafted hair and PMMA matrix. Hence, the monomer concentration in the graft copolymer also affects the interfacial bonding.
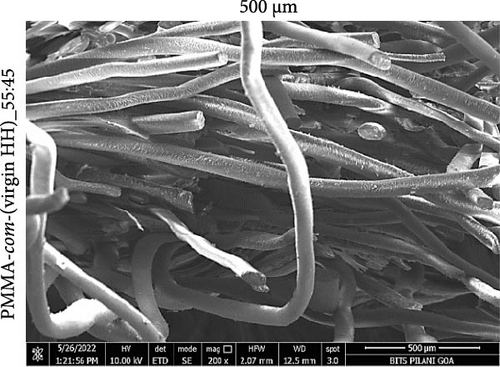
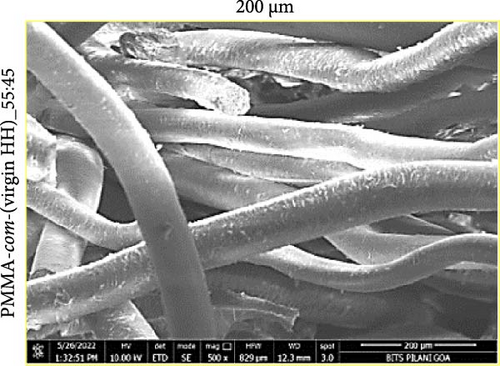

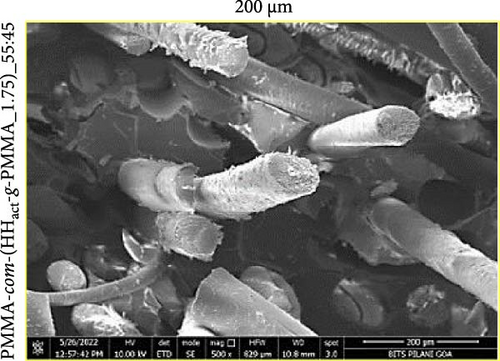
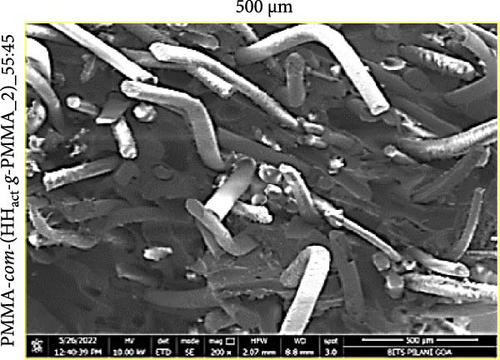
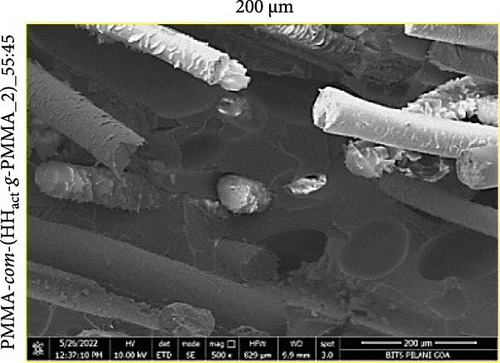
This is further supported by the AFM images of PMMA-com-(HHact-g-PMMA_1.75)_55:45 and PMMA-com-(HHact-g-PMMA_2)_55:45 composites shown in Figure 6. It was difficult to take the AFM images of PMMA-com-virgin HH_55:45 and PMMA due to very rough surfaces. PMMA sheet made under the same conditions as of composites was highly brittle, and the roughness of surface measure in nm was found to be 261 ± 100. The surface roughness increased for PMMA-com-(virgin HH)_55:45 and was observed to be 318 ± 143. This increase in surface roughness further supports the weak adhesion between the fiber and the matrix leading to surface debonding during tensile fracture. A decrease in surface roughness, that is, 162 ± 37 and 213 ± 123, was found for PMMA-com-(HHact-g-PMMA_1.75)_55:45 and PMMA-com-(HHact-g-PMMA_2)_55:45, respectively. The presence of PMMA grafts on HH results in better interlocking of PMMA resin with grafted hair, thus giving a smoother surface. The increase in roughness for PMMA-com-(HHact-g-PMMA_2)_55:45 surface as compared to PMMA-com-(HHact-g-PMMA_1.75)_55:45 may be attributed to the increased roughness of HHact-g-PMMA_2 fiber due to increased density of covalently linked oligomeric chains of PMMA graft on the hair surface. The presence of these chains on hair surface result in increased unevenness of the surface during debonding and an increase in the diameter of the pits [25, 26 ]. The diameter in nm for PMMA-com-(virgin HH)_55:45, PMMA-com-(HHact-g-PMMA_1.75)_55:45, and PMMA-com-(HHact-g-PMMA_2)_55:45 were measured to be 3474 ±, 2112 ±, and 2748 ± respectively.
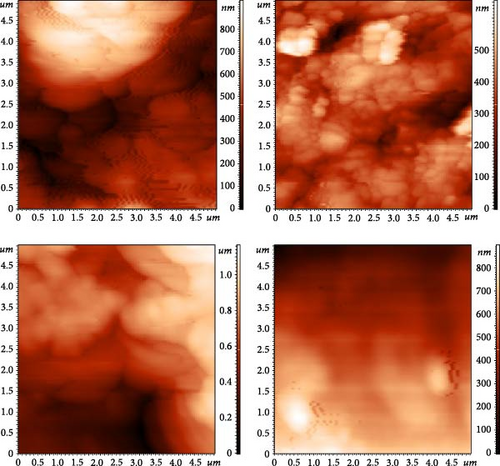
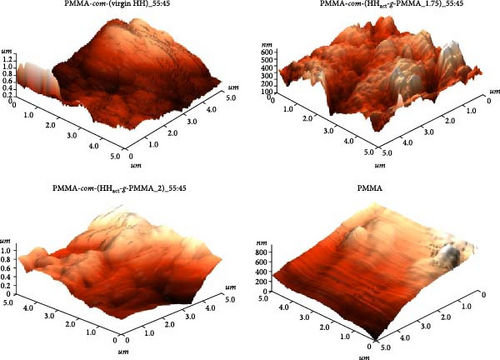
3.3. Mechanical Properties of HH-Reinforced PMMA Composites
3.3.1. Tensile Test
The tensile test of the HH-reinforced PMMA composites was done to determine the effect of percentage grafting and fiber loading on Young’s modulus (E), ultimate tensile strength (UTS), and ultimate elongation (εmax). The typical stress–strain plots for PMMA and HH-reinforced PMMA composites are shown in Figure 7a–d.
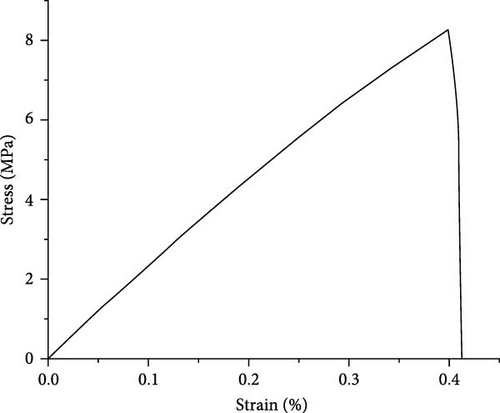
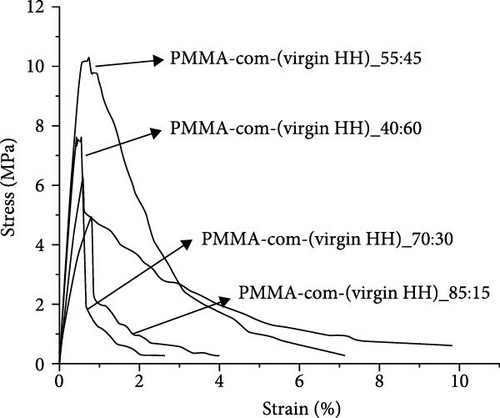
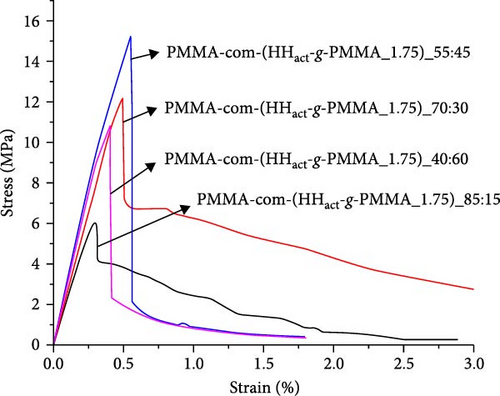
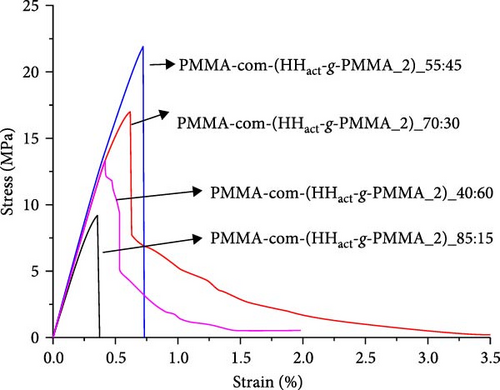
The overall stress–strain behavior of PMMA composites is nonlinear, as expected. According to Figure 7a, a pure PMMA sheet shows a tensile strength of 8.2 MPa and ultimate elongation (εmax) of less than 0.5%, showing its brittle behavior [27].
The UTS of PMMA composites reinforced with virgin HH fiber was lower than that for PMMA, as shown in Figure 8a. It could be the result of poor adhesion of HH and matrix. With an increase in fiber concentration, an increase in UTS was seen, which reached the maximum and subsequently decreased again. The initial increase is due to the introduction of fibers with greater tensile strength [22]. As the amount of grafting increases in the graft copolymer, the tensile strength also improves with respect to virgin HH. The addition of 15% HHact-g-PMMA_1.75 graft copolymer raised the tensile strength by 21.86%, while on adding 15% of HHact-g-PMMA_2 graft copolymers, the tensile strength was increased by 87.44% w.r.t. addition of virgin HH. This observation is in fairly good correlation with the observation made from SEM, where poor adhesion was observed between matrix and virgin HH compared to matrix and graft copolymers. From the SEM images of ruptured samples from the tensile test of virgin HH-reinforced composites, it is visible that failure occurs at the fiber–matrix interface due to the waxy layer of the cuticle. The chemical modification of HH via graft copolymerization improves the surface and makes it more compatible with the PMMA matrix.
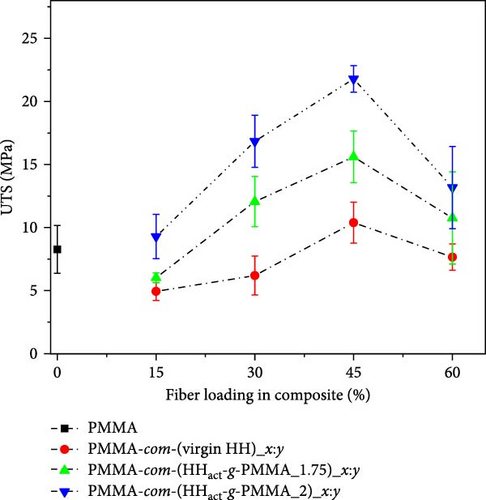
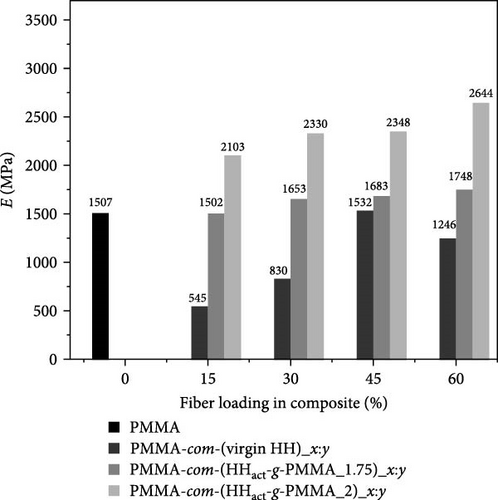
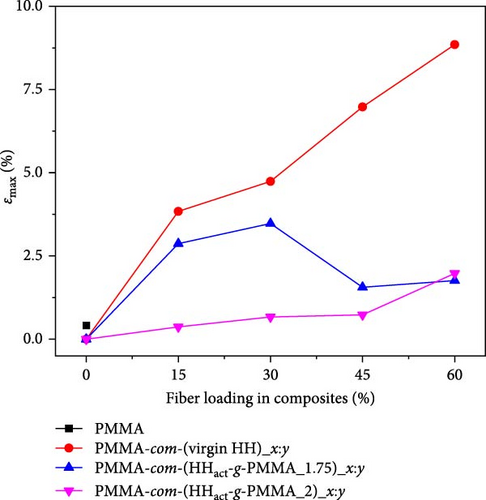
For varied fiber loading concentrations, the optimum tensile strength value is observed at 45% hair loading on comparing with PMMA. The tensile strengths of PMMA-com-(virgin HH)_55:45, PMMA-com-(HHact-g-PMMA_1.75)_55:45, and PMMA-com-(HHact-g-PMMA_2)_55:45 were increased by 25.63%, 88.63%, and 163.48%, respectively. A sudden fall in tensile strength, when hair concentration was raised to 60%, could be attributed to insufficient wetting of hair by the matrix, leading to poor interlocking. In addition to this, the void formation due to the random orientation increases with the increase in hair concentration. This leads to microcrack formation under load and, therefore, reduces the tensile strength [28].
The effect of varied percentage grafting as well as varied feed ratio of hair and matrix on E of PMMA composites is shown in Figure 8b. There was a 10%–64% decrease in E for PMMA-com-(virgin HH)_x:y compared with the PMMA sheet. On the other hand, using HHact-g-PMMA_1.75 as the reinforcing agent resulted in an increase in E of 10%–16%, while using graft copolymer HHact-g-PMMA_2 led to an increase in E of 40%–77%. The increase in E is observed with an increase in hair concentration in the PMMA matrix, as shown in FIgure 8b, and the detailed changes in E are recorded in Table 2. The E is the measure of stiffness of the composite and represents the transfer of elastic deformation of the composite. The stiffness of composites as expected increases with an increase in the interlocking of matrix and hair. This further supports the increased adhesion between hair and matrix with the increase in percent grafting.
Fiber | 15% | 30% | 45% | 60% | ||||||||
---|---|---|---|---|---|---|---|---|---|---|---|---|
UTS | E | εmax | UTS | E | εmax | UTS | E | εmax | UTS | E | εmax | |
Virgin HH | −40.2 | −63.8 | 3.8 | −25 | −45 | 4.74 | 25.6 | 1.6 | 6.9 | 7.3 | −17 | 8.8 |
HHact-g-PMMA_1.75 | −27.2 | −0.3 | 2.8 | 46 | 9.7 | 3.4 | 88.6 | 11.6 | 1.5 | 30.1 | 16 | 1.7 |
HHact-g-PMMA_2 | 12.3 | 40 | 0.3 | 103.6 | 54.6 | 0.6 | 163.4 | 55.8 | 0.7 | 59.2 | 76.7 | 1.9 |
- Abbreviations: HH, human hair; PMMA, poly(methyl methacrylate); UTS, ultimate tensile strength.
Grafting increases the roughness on the graft copolymer surface and improves the adhesion between the PMMA matrix and grafted hair. However, it is also visible that as the grafting percentage increases, the ductility of the PMMA composite is reduced. Therefore, grafting eventually results in less εmax in PMMA composites, as shown in FIgure 8c. The slight increase in εmax is again attributed to the poor adhesion and insufficient interlocking between hair and matrix, leading to the slipping of polymeric chains [29, 30].
The results are summarized in Table 2.
3.3.2. Flexural Test
The flexural test of the polymeric sheets was done using ASTM D790 using the 3-point test. The effect of % grafting on fiber, as well as the effect of fiber loading concentration on flexural strength (σF) flexural modulus (EFlex), has been shown in Figure 9a,b. In the flexural mode test, only one half of the sample is under stress, in contrast to tensile mode, where the whole sample is under tension. This results in higher value of σF 10–35 MPa compared to a tensile strength of 5%–25% for polymer composites as shown in Figure 9a. An increase of 0.3%–41% in σF compared to the PMMA sheet was observed using virgin HH as the reinforcing agent. The increase in σF was observed in the range of 6% to 218% when grafted fibers have been reinforced in the composites. This indicates that as the fiber content increases in PMMA composite, σF also increases. This is because of the multiple cracking processes with increased fiber content, which provide more bridging effect. The fiber strength increases to an optimum value at 45% fiber content and then starts decreasing due to the more nonuniform distribution of fibers in the matrix. The improper orientation due to the nonuniformity causes the reverse effect on strength [31]. On the other hand, EFlex decreased on the incorporation of fibers at lower concentrations and then reached the plateau at 45% virgin HH fiber content. The addition of grafted fibers in PMMA composites leads to an increase in EFlex by 7%–117% (Figure 9b). The results are summarized in Table 3.
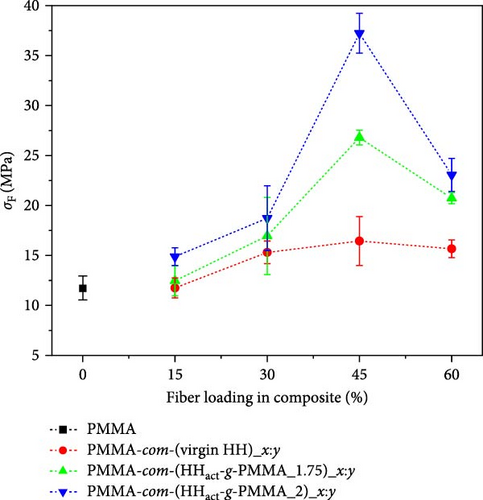
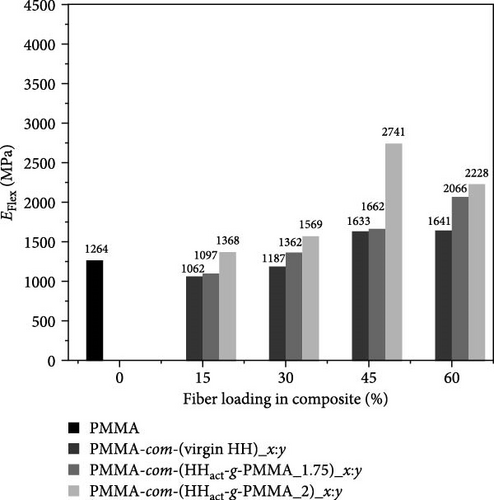
Fiber | 15% | 30% | 45% | 60% | ||||
---|---|---|---|---|---|---|---|---|
σF | EFlex | σF | EFlex | σF | EFlex | σF | EFlex | |
Virgin HH | 0.3 | −15.9 | 30.7 | −6.0 | 40.4 | 29.1 | 33.8 | 29.8 |
HHact-g-PMMA_1.75 | 6.4 | −13.2 | 44.8 | 7.7 | 128.8 | 31.4 | 77.0 | 63.4 |
HHact-g-PMMA_2 | 27.1 | 8.2 | 59.9 | 24.1 | 217.9 | 116.8 | 96.9 | 76.2 |
3.3.3. Impact Test
The impact testing was done to determine the toughness of the polymer composites using the Izod test. The V-notched sample was hit by the pivotal arm of the instrument which was first raised and then released from the known height. The impact strength, that is, energy absorbed on catastrophic failure per cross-section, was then calculated, shown in Figure 10.
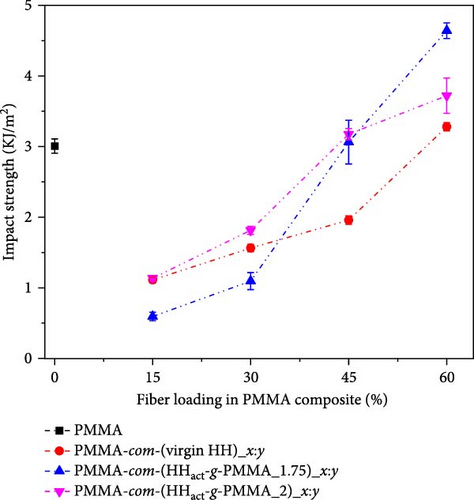
The introduction of fibers in the PMMA matrix resulted in a lowering of impact strength at lower concentrations. This may be due to the void formation at the interface. An increase in the impact strength was observed with grafted fiber. This may be due to better bonding between the PMMA and the HH fiber. The grafted hair, as discussed earlier in Section 3.2, shows better matrix adhesion. An increase in impact strength was observed at a higher concentration of fiber in the PMMA matrix. It can be observed that virgin HH-reinforced composites have shown 9.36% increase in impact strength while HHact-g-PMMA_1.75 and HHact-g-PMMA_2 graft copolymers have shown 54.7% and 24% increase in impact strength at 60% fiber loading with respect to PMMA. The increase in toughness could be due to the bridging of microcracks formed in the brittle matrix of the fibers by the fibers which intersect these cracks, thus avoiding the propagation of crack.
3.3.4. DMA of HH-Reinforced PMMA Composites
The effect of composition and fiber concentration on the viscoelastic properties of HH-PMMA composites was studied using DMA. Storage modulus (E′), loss modulus (E″), and damping (tan δ) curves for composites, PMMA-com-(virgin HH), PMMA-com-(HHact-g-PMMA_1.75), and PMMA-com-(virgin HH) and PMMA-com-(HHact- g-PMMA _2) with varied compositions were obtained and are shown in Figures 11–13. The energy stored in the elastic region in polymer composites is given by E′, whereas E″ gives the amount of energy dissipated, thus representing the viscous part of the polymer composite. The damping or the relative degree of energy dissipation in the material is represented by tan δ, which is the ratio of E″ to E′. These parameters, that is, E′, E″, and tan δ, are affected by the nature of the fiber as well as the matrix used for making composites. The length, size, composition of fiber, and the interfacial interaction also affect these parameters. At room temperature, for all three different composites, E′ and E″, enhanced with the increase in fiber concentration and reached the maximum for the 55:45::PMMA:fiber ratio. On the other hand, both parameters decreased on increasing the concentration of fiber (60%) in feed, as shown in Figure 11a–c. In all cases, E′ was higher than the loss modulus, indicating the dominance of the elastic region in the polymer composites.
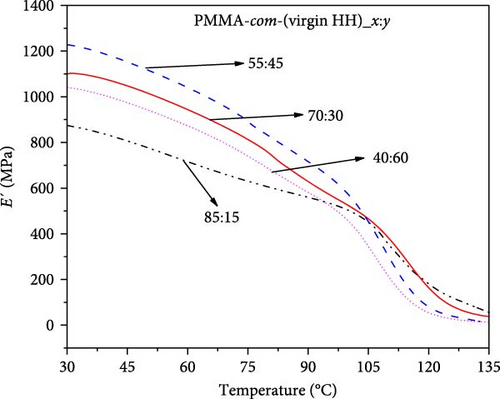
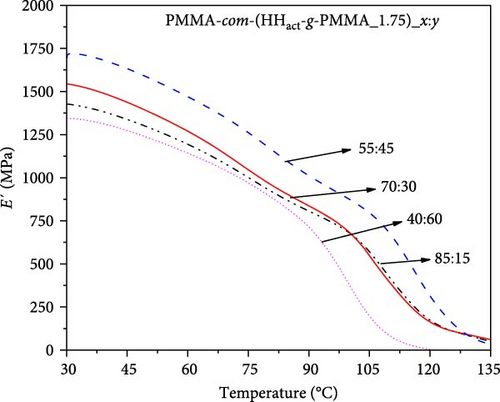
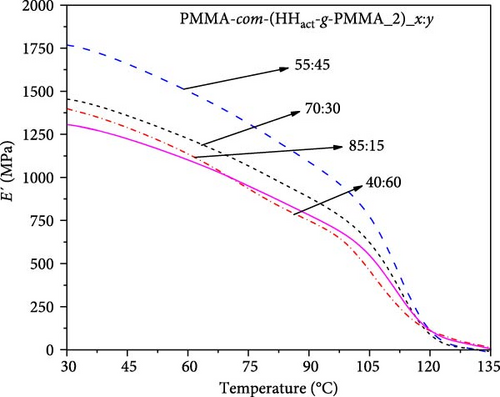
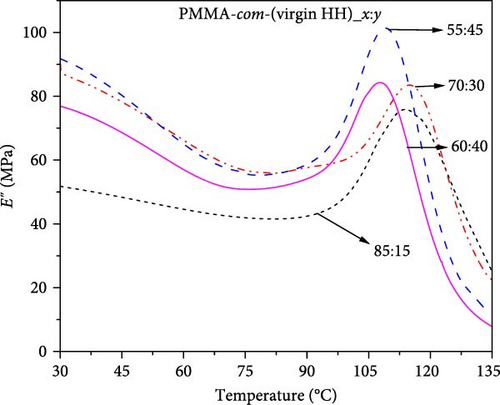
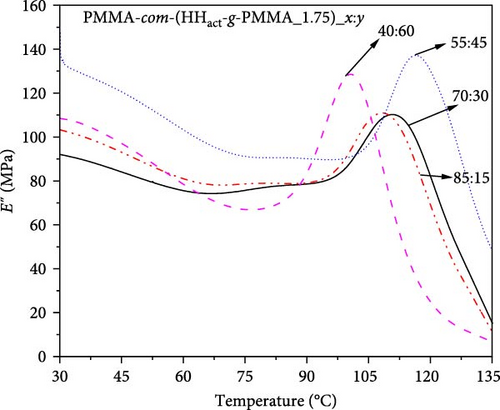
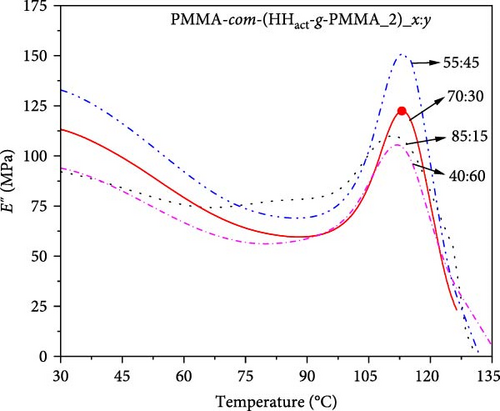
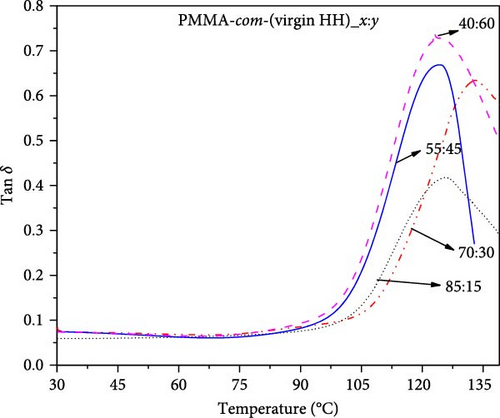
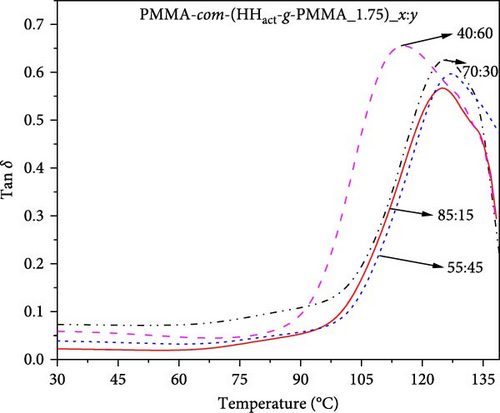
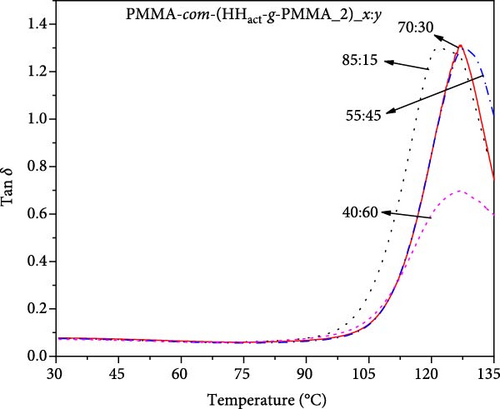
Both the E′ and E″ of PMMA composites increased in the order PMMA-com-(virgin HH) 85:15 < PMMA-com-(virgin HH)_60:30 < PMMA-com-(virgin HH)_55:45 for virgin HH-reinforced composites. This is attributed to the addition of HH fiber in the PMMA matrix, which increases the stiffness of the PMMA composites. The higher the concentration of HH fibers, the higher will be the stiffness, thus increasing the storage modulus. A higher concentration of HH fibers (60%), due to higher random orientation and the nonuniform distribution in the PMMA matrix, results in the decrease of physical entanglements. Thus, the modulus has been decreased. A similar trend was observed for PMMA composites reinforced with graft copolymers. An increase in storage modulus was observed when grafted hairs were used as the reinforcing agents. This increase was 57%–98% for HHact-g-PMMA_1.75 and 49%–102% for HHact-g-PMMA_2 fibers. Similarly, the increase in loss modulus was 46%–80% for HHact-g-PMMA_1.75 and 45%–98% for HHact-g-PMMA_2 fibers (Figure 12a–c).
This shows better interfacial adhesion between the grafted HH and the PMMA matrix, which leads to load transfer from PMMA to fiber, thus increasing the moduli. The grafting of the polymeric chain on the fibers leads to a mechanical interlock between matrix and fiber. The E′ reduced to low values near glass transition temperature (Tg) due to the increased mobility of chains. On increasing the temperature further, after Tg, the difference in the moduli was reduced, and the values came close to each other. The increase in temperature enhanced the segmental motion. An increase in Tg of PMMA resin was observed on the incorporation of fibers as a reinforcing agent. The literature reported value for Tg of PMMA is ~100–105°C, whereas the Tg was observed in the range of ~105–110°C for composites. The variation in Tg on using grafted HH was negligible. This could be due to the cross-linking of resin during composite formation. Damping depends on the fiber and matrix adhesion level, and their plot is shown in Figure 13a–c.
Tan δ peak (position and height) indicates the structural changes in the composite. Among the composites, increasing tan δ peak height upon fiber loading was observed. This is due to the movement of polymer molecules by incorporating virgin HH and graft copolymers. The Tg of neat PMMA and composite remains stable and does not change much in composites, which means that the incorporation of fibers does not affect the Tg of the PMMA. The tan δ of PMMA composites decreases due to the attachment of polymeric chains of PMMA with HH fibers. This diminishes their mobility and reduces the friction among them. The tan δ peak height in the composites appears due to the fiber’s internal energy dissipation between the fiber and matrix interphase [32].
The results are summarized in Table 4.
Reinforced composites | E′ (30°C) | E′ (120°C) |
E″ (30°C) |
E″ (120°C) |
Tg (E′ ∗) |
Tg (tan δ) |
---|---|---|---|---|---|---|
PMMA-com-(virgin HH)_55:45 | 1,228 | 77.41 | 91 | 51 | 109 | 122 |
PMMA-com-(HHact-g-PMMA_1.75)_55:45 | 1736 | 308 | 136 | 129 | 115 | 126 |
PMMA-com-(HHact-g-PMMA_2)_55:45 | 1768 | 142 | 132 | 99 | 113 | 128 |
- ∗Tg is expressed as the inflexion point of the curve.
3.4. Differential Scanning Calorimetry
Differential scanning calorimetry was done for PMMA composites to understand the effect of grafting on the thermal behavior of composites. The DSC scans are shown in Figure 14. The Tg of composites prepared using grafted polymers are found to be higher than the Tg of composites using virgin HH. Similar results were obtained via DMA, and the results are summarized in Table 4. The Tg depends on factors such as intermolecular forces, crystallinity, and cross-linking. Here the grafting of fibers leads to stronger bonding between fiber and matrix, thus decreasing the free volume and increasing the Tg.
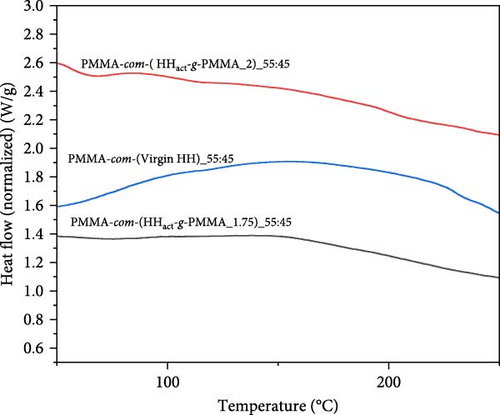
3.5. Thermogravimetric Analysis of Composites
Thermogravimetric analysis was done for PMMA composites to understand the effect of grafting on the thermal degradation of composites. The TGA and DTG curves are shown in Figure 15a–b. The TGA behaviors of PMMA and fibers, that is, virgin HH, and graft copolymers HHact-g-PMMA_1.75 and HHact-g-PMMA_2, are shown in Figure 15. At the temperature range from ambient to 100°C, a small amount of weight loss was observed due to the removal of moisture contents. The major weight loss in the PMMA 91.02% was found in the region of 270–430°C, which is attributed by the random scission of C─C and C─H bonds [33]. In virgin HH and HHact-g-PMMA_1.75 (Figure 15a), degradation of microfibrils and denaturation of HH happened in the range 363–515°C and showed almost 30%–35% weight loss, whereas the weight loss of 42%–45% weight loss happened in the region 520–750°C because of the random scissions of chain which leads to complete degradation of hair leaving negligible char at 750°C (~2.4%). The TG curves of grafted copolymer HHact-g-PMMA_2 have shown major weight loss of around 90% in the range of 270 to 530°C. The TGA thermograms of PMMA-com-(virgin HH)_55:45, PMMA-com-(HHact-g-PMMA_1.75)_55:45, and PMMA-com-(HHact-g-PMMA_2)_55 : 45 composites are shown in Figureee 15. In virgin HH-reinforced composites, the weight loss of 4%–10% is observed in the region of 60–100°C due to loss of moisture content. In the range of 360–490°C, 35%–40% weight loss is observed due to the open chains and PMMA labile groups. The second step of degradation was observed in the temperature range of 500–665°C. This process is determined by the pyrolysis of C─C and C─H bonds, which in this case consists in the PMMA depolymerization initiated in the labile thermal groups. The weakest bonds are broken with temperature, producing volatile monomer units in a process inverse to the polymerization. From the TG curve of graft copolymer-reinforced PMMA composites, it can be seen that maximum weight loss was observed in the middle zone of the temperature range 360–540°C, and up to 89.48% weight reduced due to breakage of chemical bonding. The residue was found around 2%–3% after the final zone degradation of the composite at a temperature of 550°C. The graft copolymers HHact-g-PMMA_2 enhanced the degradation temperature of the composites after reinforcement because of highly cross-linked chains with the matrix as compared to other reinforcements. In the case of virgin HH reinforcement, the interaction between the hair and matrix is less effective, but the hair-reinforced composites are thermally more stable than the neat PMMA matrix.
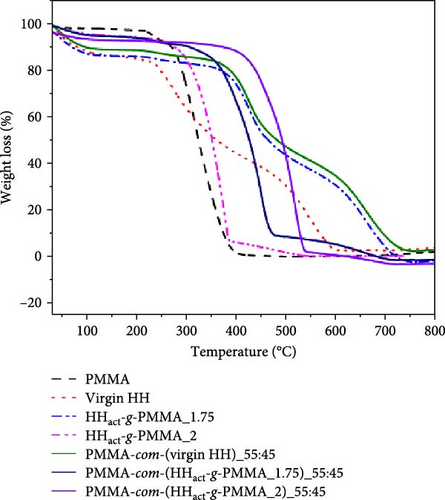
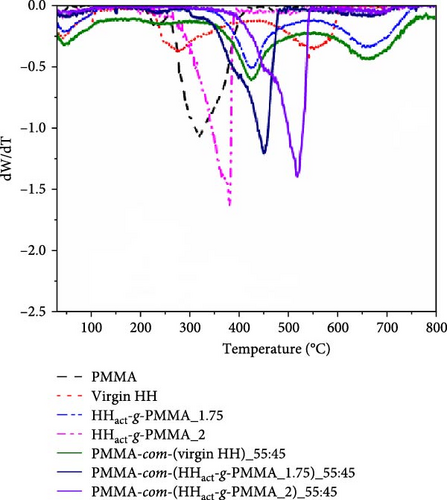
4. Conclusion
In this study, the effect of using grafted and nongrafted hair fibers on thermal and mechanical properties of PMMA composites has been investigated and compared. The results showed that the graft copolymer-reinforced PMMA composites possessed better properties than PMMA as compared to virgin HH-reinforced PMMA composites which showed inferior properties than PMMA.
In the FT-IR spectra, the characteristic peaks of HH and PMMA such as carbonyl of amides of HH and carbonyl of PMMA in the region 1600–1800 cm−1 were obtained with a reduced intensity signifying the engagement of the functional groups in bonding between fiber and matrix. The stronger interactions between grafted HH and matrix were confirmed via SEM which shows broken HH ends or sites as compared to fiber pull out in composites of PMMA and virgin HH. This was also supported by the AFM analysis of composites in which the surface roughness of composites of grafted hair was found to be less. The stronger adhesion between fiber and matrix makes the surface smoother.
The stronger interfacial adhesion between matrix and fiber increases the mechanical properties and enhanced mechanical properties as expected. Pure PMMA sheet is brittle in nature with tensile strength of 8.2 MPa. The introduction of 15%–30% of HH fibers in matrix further decreased the tensile strength to lower values due to poor adhesion between matrix and fiber. The UTS increased with the introduction of grafted gibers in the matrix. On 15% addition of HHact-g-PMMA_1.75 and HHact-g-PMMA_2 graft copolymers, a respective increase of 21.86% and 87.44%, in UTS, was observed as compared to virgin HH. With the increase in fiber loading, UTS further increased due to better adhesion, reached to a maximum at 45% content of fiber, and then further decreased due to random orientation of fibers. The tensile strengths of PMMA-com-(virgin HH)_55:45, PMMA-com-(HHact-g-PMMA_1.75)_55:45, and PMMA-com-(HHact-g-PMMA_2)_55:45 increased by 25.63%, 88.63%, and 163.48%, respectively, when compared with PMMA sheets.
The storage modulus which is a measure of stiffness decreased by 10%–64% for MMA-com-(virgin HH) and increased by 10%–16% for PMMA-com-(HHact-g-PMMA_1.75)_55:45 and 40%–77% for PMMA-com-(HHact-g-PMMA_2)_55:45. A decrease in ductility was observed, and hence, ultimate elongation when grafted HH was used and again can be attributed to good adhesion and interlocking between matrix and fiber. Similarly, an increase of 6% and 218% in flexural strength was observed for PMMA-com-(HHact-g-PMMA_1.75)_55:45 and PMMA-com-(HHact-g-PMMA_2)_55:45, respectively. A similar trend was obtained for flexural and impact strength. The flexural strength of PMMA-com-(HHact-g-PMMA_1.75)_55:45 and PMMA-com-(HHact-g-PMMA_2)_55:45 is increased by 88.78% and 190% with respect to PMMA. The storage and loss modulus determined using DMA also shows increase with increase in grafted fiber content in composite, reached to maximum at 45% fiber content, and decreased further. An increase of 57%–98% for HHact-g-PMMA_1.75 and 49%–102% for HHact-g-PMMA_2 fibers was obtained. Similarly, the increase in E′ was 46%–80% for HHact-g-PMMA_1.75 and 45%–98% for HHact-g-PMMA_2 fibers, respectively. E′ was higher than E indicating the dominance of elastic region in the composites. An enhancement if Tg and thermal stability was observed for PMMA-com-(HHact-g-PMMA_1.75)_55:45 and PMMA-com-(HHact-g-PMMA_2)_55:45.
Thus, we can conclude that using HH with modified surface by grafting enhances the thermal and mechanical properties due to better adhesion of fiber and matrix.
Conflicts of Interest
The authors declare no conflicts of interest.
Author Contributions
Honey Srivastava conducted the experimental work and was involved in data interpretation and manuscript writing. Nidhi Nitin Parmekar was involved in topographical studies using AFM, data interpretation, and manuscript writing. S. Pozhil was involved in carrying out mechanical tests. Sachin Waigaonkar provided the mechanical testing facilities and was involved in manuscript writing. Rashmi Chauhan has conceived the idea, provided raw materials, and was involved in data interpretation and manuscript writing. All authors have approved the final version of the manuscript.
Funding
No funding was received for this research.
Acknowledgments
The authors acknowledge CSIF, BITS Pilani K. K. Birla Goa Campus, for SEM and UTS facilities needed for this study. Rashmi Chauhan and Honey Srivastava are thankful to the Mechanical Engineering Department of BITS Pilani K. K. Birla Goa Campus for providing the hydraulic press for compression molding and DMA. Rashmi Chauhan and Nidhi Nitin Parmekar are thankful to the Department of Chemistry, BITS Pilani K. K. Birla Goa Campus, for providing AFM facility. Honey Srivastava and Nidhi Nitin Parmekar gratefully acknowledge BITS Pilani K. K. Birla Goa Campus for providing the fellowship.
Open Research
Data Availability Statement
The data that support the findings of this study are available from the corresponding author upon request.