Improving Renewable Energy Recovery Efficiency in Variable Pressure Source Systems Through BP Neural Network Optimization
Abstract
The variable pressure source system is widely used in renewable energy recovery scenarios. However, the instability of the new energy input and the nonlinearity of the power generation system can lead to problems such as more difficult tracking and control of the maximum power point and poor power generation quality. To address the problem of lower efficiency under varying inputs, which is prevalent in renewable energy generation, this paper establishes an energy recovery system model based on power conversion rectifier topology, designs a speed current double closed-loop control strategy, proposes an online variable-step maximum efficiency point tracking method based on experience curves, and tests the overall energy recovery effect through system simulation and comparative experiments. The simulation results show that the maximum efficiency point tracking method proposed in this paper reduces the number of optimization searches by 50% and improves optimization speed. The experiment results show that, under the drastic changes of the input, the method proposed in this paper could reduce the total harmonic distortion to 5.65%, improve the energy recovery efficiency by 10.976%, and reduce the fluctuation ratio of the voltage to 2.43%. This study can provide an important reference for the collection and utilization of new energy sources.
1. Introduction
Energy is an important foundation for the development of human society and a key factor affecting global economy, politics, environment, and security [1]. In recent years, the problem of energy shortage has become increasingly prominent, and the consumption of traditional energy resources has continued to intensify [2]. Currently, countries around the world are committed to finding ways to efficiently recycle and utilize energy. Improving the efficiency of energy recovery is an extremely important means to solve the current problem of low energy utilization rate. In the system design of energy recovery, hydraulic systems are often used as an intermediary for energy capture [3–8]. Among them, compared with the constant pressure source system, the variable pressure source system has more applicable scenarios in energy recovery and has wider application fields [9]. Improving the energy recovery efficiency of variable pressure source systems will help improve equipment endurance, reduce reliance on traditional energy, promote the development of green energy, and alleviate energy shortages.
Researchers have conducted extensive research on this type of system. Sheng et al. constructed a variable pressure source system using a combination of eagle shaped structure, double acting hydraulic cylinder, accumulator, and hydraulic valve and built a 500-kW eagle-shaped wave energy power generation device called “Zhoushan” [10]. Wei et al. [11] proposed an energy storage wind power generation system converting wind energy into hydraulic energy, achieving short-term energy storage and stable energy output, avoiding the impact on the generator during operation. Fan, Mu, and Ma [12] proposed a variable pressure source system strategy that combines wind energy and seawater. The constructed hydraulic energy storage system can store/release excess energy and has smooth, stable, and flexible characteristics. Yang et al. [13–16] has developed a new type of underwater profiler, which relies on temperature difference energy to independently perform 160 cyclic profiling movements. The variable pressure source system, combined with a binary mixture of n-hexadecane and n-octane PCM, achieves energy storage between the surface and deep layers of the ocean.
Balancing the tradeoff between computational complexity and real-time efficiency is critical in modern control strategies. The adaptive fuzzy model predictive control method detailed in Mollajafari’s work on microgrid frequency regulation addresses this by using an adaptive mechanism to adjust control parameters dynamically, thereby optimizing computational resources without compromising performance [17]. Additionally, the V2V communication study by Mollajafari highlights how advanced communication algorithms can be designed to optimize energy efficiency and performance in plug-in fuel cell vehicles, despite the increased computational demands [18]. These studies provide valuable insights into designing efficient control systems that manage complexity and computation time effectively.
To improve power generation, the current approach is mostly to introduce the maximum power point tracking (MPPT) methods into energy recovery systems, such as constant voltage tracking method [19], perturbation and observation (P&O) method [20–23], and incremental conductance method [24, 25]. Researchers have also improved some MPPT methods. For example, Ben et al. proposed a novel MPPT control based on the improved PSO algorithm using an adaptive factor selection strategy, which obtained maximum power under different temperature and lighting conditions [26]. Ncir, Akchioui, and Fathi [27] developed an intelligent MPPT approach based on the differential evolution algorithm and an adaptive feedforward neural network, which reduced the instability of photovoltaic systems at high tracking speeds. Mendi, Pattnaik, and Srungavarapu [28] proposed an adaptive step size MPPT control method based on single current sensor, which utilized load current information to track the maximum power of a small wind energy conversion system. Dong et al. [29] proposed a MPPT control strategy based on frequency and amplitude control, which realized the efficient conversion of pendulum-type wave energy. Mollajafari and Shahhoseini [30] proposed a repair-less genetic algorithm for scheduling tasks onto dynamically reconfigurable hardware, demonstrating the efficiency of such algorithms in optimizing the scheduling process and enhancing system performance. Their research highlights the potential of genetic algorithms in improving the operational efficiency of complex systems, which is highly relevant to the optimization of energy recovery systems. Additionally, Mollajafari and Shojaeefard [31] introduced TC3PoP, a time-cost compromised workflow scheduling heuristic customized for cloud environments, which balances the time and cost of executing workflows in cloud computing environments. This heuristic is significant in ensuring efficient and cost-effective scheduling, which can be adapted to enhance the scheduling of tasks in energy recovery systems.
However, these optimization algorithms are mostly used in unlimited input systems based on photovoltaics and are less applied to energy storage power generation systems with variable pressure sources. They are mostly used to find and track the instantaneous maximum power point. There are also many shortcomings in the current research on optimization algorithms both domestically and internationally, and there is a lack of in-depth exploration of introducing optimization algorithm solutions for variable pressure source systems. This paper analyzes the main components that affect energy recovery efficiency in variable pressure source systems and identifies controllable factors that affect efficiency. Use BP neural network to empirically optimize the variable pressure source system and obtain the maximum efficiency curve under experimental conditions. Propose an optimization strategy that combines online adjustment, and propose an improvement plan for the commonly used disturbance observation method in online adjustment, including combining gradient information and adding weight information, to form an overall strategy for tracking and controlling the maximum efficiency of energy recovery in variable pressure source systems.
This paper conducts research on the optimization method and application of energy recovery efficiency in variable pressure source systems against the backdrop of current energy scarcity and low renewable energy recovery efficiency. The main content includes constructing an energy storage variable pressure source power generation system, building simulation models and analyzing them, designing lower level control strategies, proposing upper level maximum efficiency tracking methods, designing circuit systems, and developing software systems. The contribution of this article is the construction of an energy recovery system for an energy storage variable pressure source, proposing the use of Vienna rectifier topology as the main circuit for electrical energy conversion, and forming a PMSG Vienna rectifier speed and current dual closed-loop direct control strategy to enhance control capability and improve conversion efficiency. And propose an online variable-step size maximum efficiency tracking method based on experience curve, which combines experience curve with online adjustment to ensure accurate and fast optimization in external environmental changes such as temperature. In response to the problems of current online optimization methods, a combination of gradient information and weight information is used to improve and optimize the speed and accuracy of optimization.
The paper is organized as follows: Section 2 introduces the power generation principle of the variable voltage source system, including the system components and the mathematical model of the electrical energy conversion module. Section 3 describes the maximum efficiency point tracking control strategy proposed in this paper, designs the closed-loop control strategy for efficient conversion of electric energy, and empirically optimizes it using BP neural network. In Section 4, the maximum efficiency point tracking method is simulated, and the three strategies are verified by comparison tests. Finally, Section 5 is the conclusion.
2. Energy Recovery Solution for Variable Pressure Source System
In order to study the characteristics of the variable pressure source system, this section constructs a unified model of variable pressure source energy recovery. The system mainly includes energy supply module, energy storage stability module, energy conversion module, power conversion module, and energy storage module.
2.1. Principle of Power Generation in Variable Pressure Source System
Figure 1 shows the energy recovery solution of the variable voltage source system, which consists of an oil tank, hydraulic pump, safety valve, switch valve, pressure sensor, airbag accumulator, flow meter, axial piston quantitative motor, torque sensor, encoder, permanent magnet synchronous generator, rectifier circuit, and battery pack. The external energy is captured in the form of hydraulic energy and stored in the accumulator. Then the switching valve 1 is closed, and the switching valve 2 is opened, releasing the oil through the hydraulic pipeline and driving the hydraulic motor to rotate, converting the hydraulic energy into mechanical energy. The synchronous generator converts mechanical energy into electrical energy, converts the form of electrical energy through the circuit topology, and finally stores the energy in the battery.
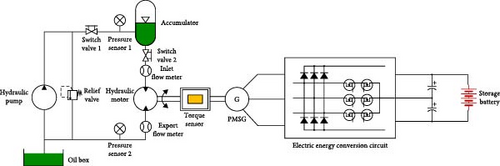
2.2. Mathematical Model of the Electrical Energy Conversion Module
The power conversion module composed of a permanent magnet synchronous generator, and rectifier circuit is an important part of the energy recovery of the variable pressure source system, and the power loss in the power conversion process affects the final recovery efficiency. The generator in the variable pressure source system sends out alternating current (AC) with variable frequency and amplitude, and the conversion of variable-frequency and variable-amplitude AC into controllable direct current (DC) is a prerequisite for the normal recovery of energy from the variable pressure source system.
This paper proposes the use of Vienna rectifiers as a topology for power conversion. Compared to other traditional three-phase rectifier topologies, Vienna rectifiers share a common drive signal for each bridge arm by virtue of structural characteristics, eliminating the need to set a dead time, and their inductor currents are continuous and can be directly controlled. The three-level characteristics make the power device voltage stress small, which is conducive to high power density design, and the power factor can be operated in unit, and the current has a low THD value [32]. The power conversion module of the Vienna rectifier shown in Figure 2 is a novel midpoint clamped three-level rectification topology.
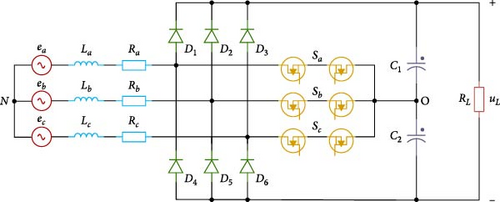
The above derivation shows that when the inlet and outlet pressures of the hydraulic motor are constant, the higher the rotational speed, the higher the voltage of the generator and the lower the load current. Since the outlet pressure is much smaller than the inlet pressure, and the outlet pressure is always a certain value during the energy recovery process, the inlet pressure can be regarded as the differential pressure for the convenience of subsequent calculations and tests. Therefore, under the condition of constant pressure, there exists an optimal rotational speed to maximize the total energy conversion efficiency of the energy storage power generation system, and this optimal working point is the maximum efficiency point.
3. Maximum Efficiency Point Tracking Control Strategy for Energy Recovery in the Variable Pressure Source System
3.1. Control Strategies for Efficient Conversion of Electrical Energy
For Vienna rectifier, the use of appropriate control strategy can make the DC-side voltage and current stable output but also make it work under the unit power factor to reduce the conversion loss. In the process of energy recovery, the energy loss mainly occurs in the mechanical loss of the hydraulic motor rotation and the loss generated by the high harmonics of the current on the AC side, and the mechanical efficiency and volumetric efficiency of the hydraulic motor are greatly affected by its rotational speed, so this paper designs the double closed-loop direct control strategy of the rotational speed outer loop and the current inner loop as shown in Figure 3 to realize the efficient energy recovery. This figure presents the control model diagram for the PMSG-Vienna rectifier within the d–q coordinate system. The diagram details the double closed-loop control strategy designed to enhance energy conversion efficiency. The outer loop controls the rotational speed of both the permanent magnet synchronous generator and the hydraulic motor, ensuring stable operation. The inner loop manages the current, maintaining synchronization with the AC voltage signal to minimize harmonic loss. Additionally, the midpoint potential balancing loop ensures the upper and lower capacitor voltages on the DC side remain balanced, further reducing power conversion losses. This comprehensive control strategy ensures high-efficiency power conversion and stable system operation.
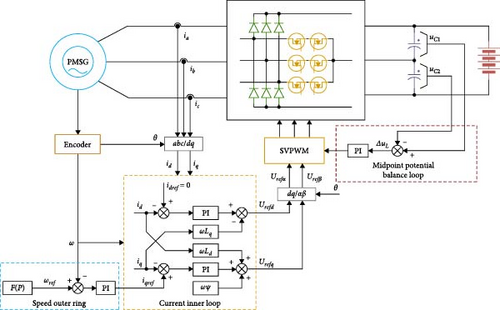
The function of the rotational speed outer loop is to stabilize and control the rotational speed of the permanent magnet synchronous generator and the hydraulic motor; the current inner loop is to realize current following, so that the current on the AC side always stays synchronized with the AC voltage signal, and to reduce the harmonic loss of the power conversion module; the midpoint potential balancing loop is to balance the upper and lower capacitor voltages on the DC side and to reduce the work loss of the power devices. The SVPWM is a bridge between the control loop and the switching tube, which can link the switching state of the rectifier and the corresponding vector to realize the tracking of the target vector and achieve the purpose of stabilizing the output target value. By this control strategy, high efficiency power conversion can be maintained while the speed is adjusted.
3.2. Empirical Optimization Based on BP Neural Networks
The main components that affect the energy recovery efficiency of the variable pressure source system are hydraulic valves, hydraulic motors, permanent magnet synchronous generators, and electrical energy conversion devices. In terms of hydraulic valves, energy loss mainly occurs at the valve port. When the flow rate is constant, the larger the valve port area, the smaller the pressure difference, and the smaller the energy loss. Therefore, this article uses larger diameter switching valves and relief valves to achieve minimal energy loss. In terms of hydraulic motors, pressure, displacement, and speed directly affect their working efficiency, which includes mechanical efficiency and volumetric efficiency. To ensure the operating efficiency of hydraulic motors, this article selects small displacement motors. After selecting the hydraulic motor, the conversion of hydraulic energy to mechanical energy is only related to the pressure and speed of the hydraulic motor port. Permanent magnet synchronous generators suffer from mechanical losses, copper losses, iron losses, and stray losses. The input torque and speed directly affect their working efficiency. As analyzed earlier, when the torque is constant, there exists an optimal working speed that maximizes their efficiency. There are mainly switch losses, conduction losses, driving losses, and losses caused by the control process in the electric energy conversion circuit. This article uses Vienna rectification topology to ensure high power factor and adopts dual-loop control to achieve AC-side current tracking and reduce harmonic effects. The relationship between efficiency loss and impact of the power generation system is shown in Figure 4.
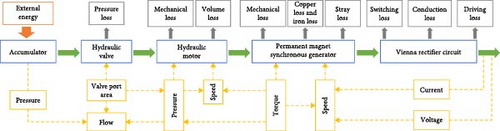
According to the inductive relationship diagram, it can be seen that there are numerous factors that affect the energy recovery efficiency of variable pressure source systems, and they are interrelated and mutually influential. Based on the modeling in Chapter 2 and the combination of the efficiency losses of the power generation system in Figure 4, it can be seen that the controllable factors affecting the efficiency of the system are pressure and speed.
To realize the maximum efficiency point tracking and ensure that the system always works at maximum efficiency, it is necessary to explore the correspondence between pressure, rotational speed, and total system efficiency. However, the variable pressure source system is a nonlinear system with a complex composition structure, and the parameters are difficult to obtain. The BP neural network is adaptable, can deal with nonlinear problems, and has high accuracy and scalability [33], so this paper adopts the method of BP neural network to process the data obtained by traversing the test.
The first step is to design the traversal test to obtain the initial data, and the design idea is to obtain the data by traversing the rotational speed under constant pressure and then traversing the pressure. In the experimental process, the pressure is firstly kept at the set constant value through the relief valve, the switching valve is opened to start generating electricity, and the motor speed is changed by sending the step-variable speed command through the upper computer to obtain the voltage and current data under a certain constant pressure and different speeds. Then change the setting of the relief valve to adjust the output pressure value of the accumulator, and repeat the above steps to obtain the data under multiple pressures. In this paper, a set of experiments is conducted using an input pressure range of 4.5–7.5 MPa in pressure steps of 0.5 MPa. For each set of tests, experiments are conducted using a rotational speed step of 100 r/min, respectively. After obtaining the data for the BP neural network setup, the pressure and rotational speed data are used as the input layer, the efficiency data are used as the output layer, and the number of neurons in the hidden layer is set to 10. If the training error does not become smaller after six consecutive trainings, the training is stopped.
The regression value R in Figure 5 represents the correlation between the predicted output and the target output. The closer the R value is to 1, the closer the relationship between the predicted and output data. The closer the R value is to 0, the greater the randomness of the relationship between the predicted and output data. Through neural network regression data, it can be seen that the R values of the fitted training are all above 0.99, indicating that the neural network used in this article has a better fitting effect. The error histogram with 20 bins in Figure 6 means that the error range is divided into 20 equally wide intervals; each interval is called a “bin.” If the histogram follows a normal distribution, it indicates that the error distribution of the model is uniform, and the error values are concentrated. The distribution of error values can be quickly understood through the results in Figure 6. It can be seen that the entire histogram basically presents a normal distribution shape, indicating that the error distribution of the model is relatively uniform, and the concentration of error values is also relatively high.

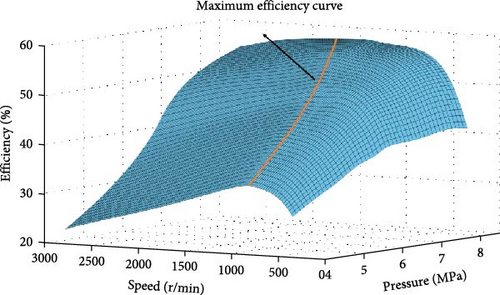
From the training results, it can be seen that the efficiency of the variable pressure source system corresponds to the pressure and rotational speed. In the pressure range, the maximum efficiency value increases gradually with increasing pressure, while the optimum speed value corresponding to the maximum efficiency also increases.
3.3. Online Variable-Step Maximum Efficiency Point Tracking Method Based on the Experience Curve
The maximum efficiency curve obtained through the neural network can represent the optimal speed and efficiency under the experimental environment. However, when the variable pressure source system is running, the temperature and other environmental factors often change, and the maximum efficiency curve at this time may have been shifted, so it is not accurate enough to rely only on the acquired experience curve for optimization. In order to reduce the error of relying only on the experience curve, the method of combining empirical curves with online optimization has been proposed for real-time maximum efficiency point tracking. The online adjustment operation can utilize the idea of the perturbation observation method to observe the changes in the energy recovery efficiency by applying a speed perturbation. However, the traditional perturbation observation method needs to set the step size manually, which has the problems of “oscillation” phenomenon, “out-of-bounds” phenomenon, and the problem that the optimization speed and the optimization accuracy cannot be combined, and needs to be improved [34].
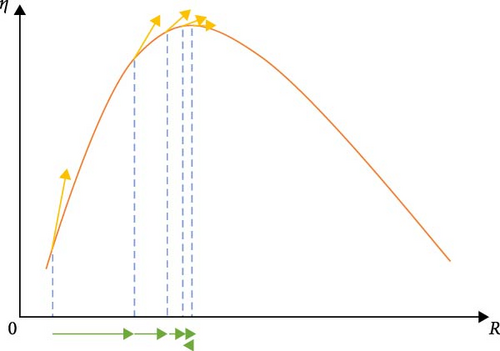
Finally, the mode of online optimization using the optimal point of the empirical curve as the starting point is also set to combine with the a priori data to make the online optimization reach the fastest speed. The method is adaptable to different objective function patterns and is easy to realize and adjust. The adaptive adjustment process of online optimization is shown in Figure 8.
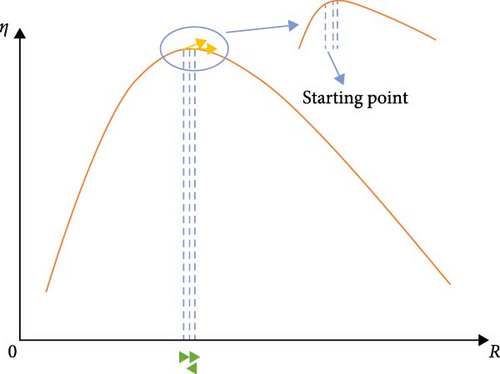
3.4. Overall Strategy for Energy Recovery in the Variable Pressure Source System
Comprehensively, the maximum efficiency point tracking control method for energy recovery of variable pressure source system consists of three parts, which are the a priori link that traverses the system to obtain the pressure, rotational speed and efficiency data, the online optimization link that is adjusted in real time through the sampling information, gradient information and weight information, and the lower closed-loop execution link that controls the switching tubes by inputting the rotational speed command and current information. The a priori link mainly adopts the BP neural network to obtain the maximum efficiency curve, through which the starting point and gradient information of the online optimization link are obtained, and then the online optimization link is formed through the proportioning weights. The lower level execution link mainly adopts the above closed-loop control method based on coordinate transformation to ensure the accurate tracking of speed command. The overall composition of the maximum efficiency point tracking control method for energy recovery of the variable pressure source system is shown in Figure 9.
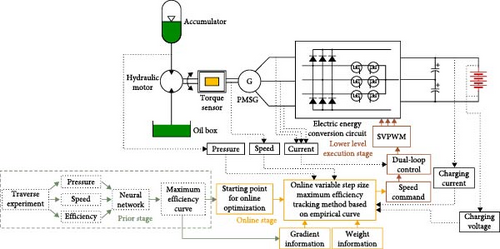
4. Simulation and Experiment Results
4.1. Simulation Results
In order to more intuitively and visually observe the optimization effects of the constant prescribed step-size perturbation observation method and the maximum efficiency point tracking method proposed in this paper, the optimal function curves of the system efficiency at 7 MPa are used as an example to simulate the effects of different methods. The optimal function curve and curve gradient values of the system efficiency at 7 MPa are shown in Figure 10.
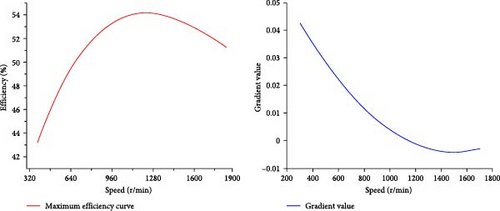
The MATLAB simulation results of the empirical curve-based fixed-step perturbation observation method and the online variable-step maximum efficiency point tracking method are shown in Figure 11. The starting point of the fixed-step perturbation observation method is specified to be the default rotational speed of 300 r/min, and the step size is 100 r/min. In order to avoid falling into a dead loop of optimization, the maximum number of optimization searches is set to be 20 times. Since the external environment (e.g., temperature) of the system may change, the curves obtained from the previous tests are not sufficient to accurately represent the actual operating conditions, so a random function is introduced to simulate the impact of the external environment changes on the system.
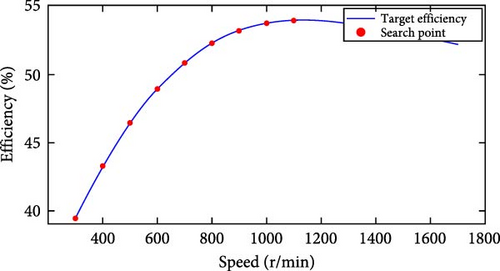
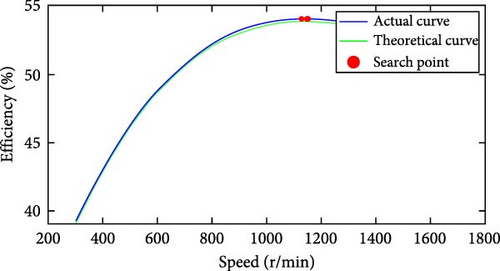
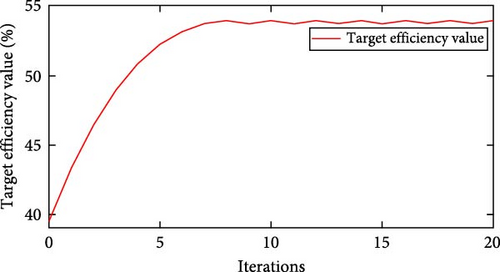
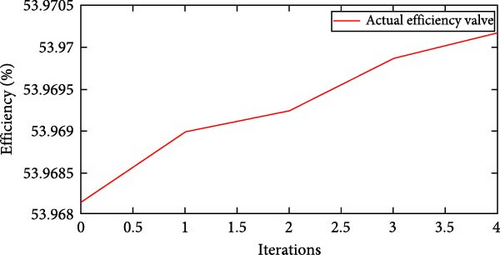
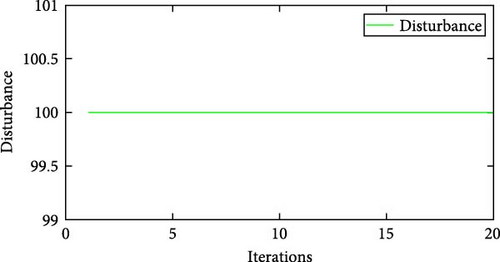
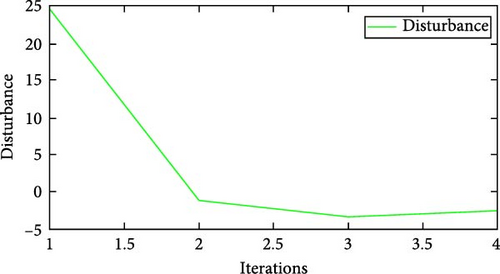
From the simulation results, it can be seen that the first search for the maximum efficiency point takes eight times using the constant step size perturbation observation method. However, due to the existence of the “oscillation” phenomenon, the number of optimization times is 20 times; i.e., it has been searching for optimization and failed to stabilize at the maximum efficiency point. On the other hand, the optimization times of the online variable-step maximum efficiency point tracking method based on experience curves proposed in this paper is only four times, which reduces the optimization times by 50%. It can be seen that there is a certain advantage in the optimization speed. At the same time, the maximum efficiency value of the commonly specified step-size perturbation observation method is 53.9041%, the optimal speed is 1080 r/min, and the optimal point is widely distributed. The algorithm in this paper basically gathers in the vicinity of the maximum efficiency point for dynamic adjustment, and the optimization point always maintains higher efficiency, and the maximum efficiency value after optimization is 53.9702%, and the optimal speed is 1140.7738 r/min. It can be seen that the method in this paper can quickly find the optimal point so as to obtain the optimal command speed in a very short time, which is conducive to the realization of the lower level control and ensure the effectiveness of the lower level regulation. The improvement of the efficiency means the improvement of the recovery efficiency of the recovered energy at each instant under the pressure change, and the improvement of each recovery process means the improvement of the final recovery efficiency.
4.2. Experiment Results
4.2.1. Experimental Design Concept
The energy recovery test setup of the variable pressure source system is built according to the design of this paper as shown in Figure 12.

The experimental design idea is to first use a hydraulic pump to uniformly charge the accumulator with oil to 7.2 MPa and then close the inlet switching valve of the accumulator and open the outlet switching valve, so as to observe the energy recovery related indexes of the variable pressure source system under different schemes. The compared schemes are the traditional uncontrolled rectification strategy, the constant step-size perturbation observation control strategy, and the maximum efficiency point tracking control strategy proposed in this paper.
4.2.2. Control Performance Test Results
From Figure 13a, it can be seen that the A-phase current waveform of the AC side with the uncontrolled rectification strategy has serious distortion and poor sinusoidality, which indicates that it has a large number of harmonics. From Figure 13b, it can be seen that the AC-side A-phase current waveform is highly sinusoidal when the tracking control strategy is adopted in this paper. And the current and voltage waveforms are highly coincident, without obvious “misalignment” phenomenon, indicating that the power factor is high and the control effect of current inner loop is good.
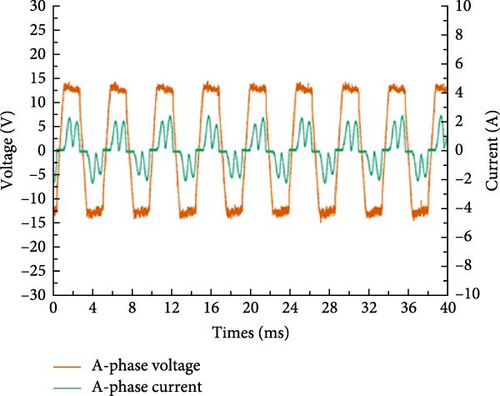
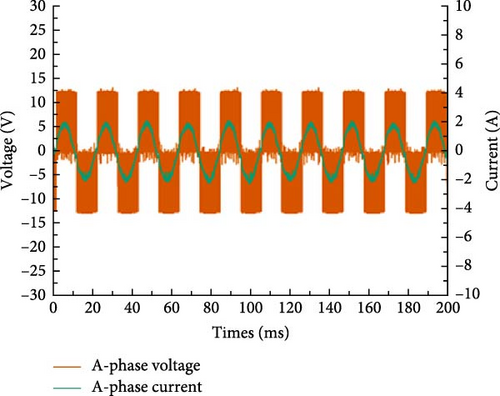
From Figure 14a, it can be seen that the three-phase currents are highly symmetrical and highly sinusoidal when using the tracking control strategy in this paper. Figure 14b shows the FFT analysis results of the AC-side A-phase current waveforms, and the results show that the total harmonic distortion of the AC-side current is as low as 5.65% under this strategy, which indicates that the harmonic content and the power conversion losses in the actual test are low under this strategy.
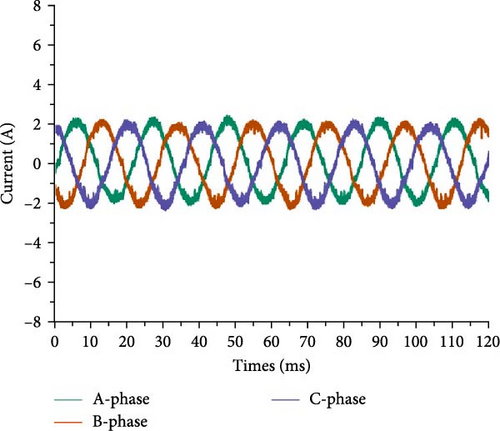

As can be seen from Figure 15, the upper and lower capacitor voltages on the DC side using the tracking control strategy of this paper have a high degree of overlap, and the voltage fluctuation is within the range of ±0.15 V, and the fluctuation ratio is only 2.43%, so the control effect of the midpoint potential balancing loop is excellent. As can be seen from Figure 16, the tracking control strategy proposed in this paper has a high degree of overlap between the target rotational speed in the ideal state and the actual rotational speed during operation, with an average rotational speed tracking error of only ±2.05 r/min and an average rotational speed tracking error rate of only 0.631%. This indicates that the rotational speed during the test is the optimal rotational speed, which verifies that the upper maximum efficiency point tracking strategy proposed in this paper can quickly find the optimal rotational speed point and can realize real-time tracking in the case of pressure change. At the same time, it indicates that the control strategy proposed in this paper has a sufficiently short adjustment time, good tracking effect, and good dynamic performance; that is, the control cycle and control effect of the speed outer loop meet the requirements.
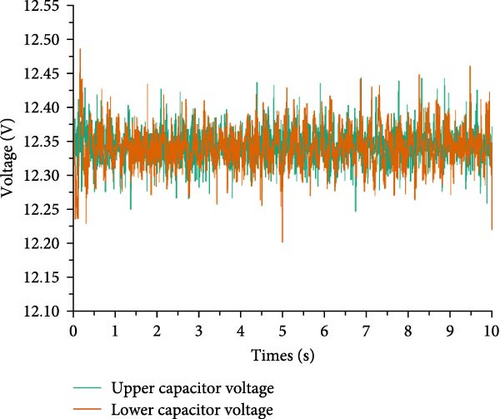
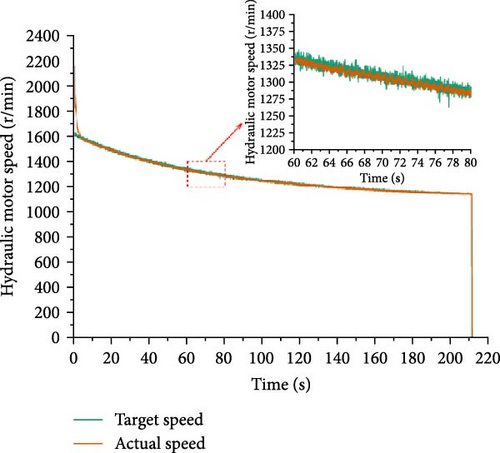
5. Energy Recovery Test Results
It can be seen from Figure 17 that when the oil pressure in the accumulator is not enough to drive the hydraulic motor to rotate, the charging current drops rapidly to 0 A, and the system stops working at this time. During the power generation process of the system, the charging current of the traditional uncontrolled rectification strategy quickly decreases from 2.904 to 0.946 A, and the charging current of the conventional step-size disturbance observation control strategy decreases relatively slowly from 2.437 to 0.476 A, and the charging current of the tracking control strategy decreases very slowly from 1.964 to 0.495 A. Therefore, the charging current extreme value of uncontrolled rectification is the highest, and the charging current changes the fastest, while the charging current under the maximum efficiency point tracking control strategy proposed in this paper is the gentlest. Similar to the charging current trend, the charging power of the three strategies decreased rapidly from 72.603 to 23.651 W, slowly decreased from 60.096 to 11.738 W, and very slowly decreased from 48.731 to 12.282 W. Therefore, the power change of the traditional uncontrolled rectification strategy is the most drastic, while the charging power change under the maximum efficiency point tracking control strategy proposed in this paper is the most gentle, which is beneficial to protecting the battery, avoiding damage to the battery caused by instantaneous large current, and extending the service life of the battery.
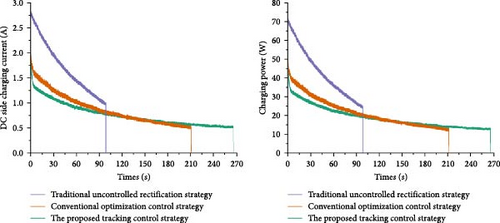
As can be seen from Figure 18a, the time it takes for the three strategies to release the pressure of 7.2 MPa is 98.83, 210.95, and 265.69 s, respectively, and the electrical energy recovered is 4215.456, 4636.909, and 5145.877 J, respectively. The conventional optimization control strategy has improved the energy recovery efficiency by 9.998% compared to the uncontrolled rectification strategy, while the tracking control strategy in this paper has improved the energy recovery efficiency by 22.072% compared to the traditional uncontrolled rectification strategy and 10.976% compared to the conventional optimization control strategy. The maximum efficiency point tracking control strategy proposed in this paper has significant advantages in energy recovery. As shown in Figure 18b, the real-time efficiency during the energy recovery process using the three strategies ranges from 55.461% to 30.988%, from 57.044% to 35.459%, and from 67.501% to 46.633%, respectively. The recovery efficiency of the tracking control strategy proposed in this paper is always higher than the other two strategies; that is, it has an advantage in recovery efficiency at every moment during the recovery process. This also indicates that the tracking control strategy proposed in this paper is far ahead of other traditional methods in maintaining efficient system operation.
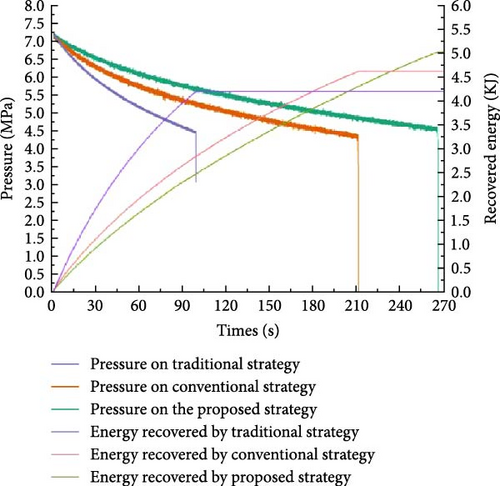
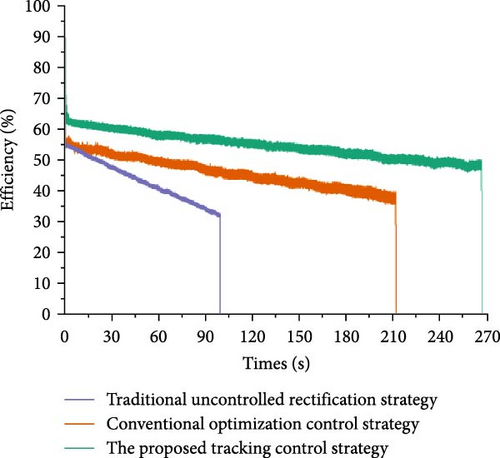
6. Conclusions
This paper conducts research on optimization methods for renewable energy recovery efficiency in variable pressure source systems. To solve the problems of low energy recovery efficiency and poor power generation quality, we propose an online variable-step maximum efficiency point tracking method based on empirical curves. The method combines empirical optimization with online optimization, using BP neural networks to address nonlinearities and achieve real-time efficiency optimization. We also designed a double closed-loop control strategy to enhance energy conversion and reduce process losses. Through simulation verification, the proposed MEPT method reduces the number of optimization searches by 50% and improves optimization speed. Comparative experiments demonstrate that under drastic input changes, the proposed method reduces total harmonic distortion to 5.65%, improves energy recovery efficiency by 10.976%, and reduces voltage fluctuation ratio to 2.43%. These results highlight the significant advantages of the proposed method in enhancing energy recovery efficiency and power quality in variable pressure source systems.
Future research should explore the following areas to build upon the results obtained in this study: integration with advanced machine learning techniques, such as deep learning and reinforcement learning, to further enhance the adaptability and efficiency of the MEPT method; developing and testing real-time implementations of the proposed control strategies in various renewable energy systems, including wind, solar, and wave energy, to validate their robustness and effectiveness in different scenarios; examining the scalability of the proposed methods to larger and more complex energy recovery systems, ensuring that the strategies can be generalized to different types of renewable energy sources; exploring the application of the proposed methods in hybrid energy systems that combine multiple renewable sources and optimizing the overall energy recovery and utilization; and assessing the environmental impact and sustainability of the optimized energy recovery systems, ensuring that the methods contribute to long-term ecological balance and energy sustainability. By addressing these future research directions, the proposed optimization methods can be further refined and adapted to meet the evolving needs of renewable energy systems, contributing to more efficient and sustainable energy recovery solutions.
Conflicts of Interest
The authors declare no conflicts of interest.
Funding
This research was funded by the National Natural Science Foundation of China (no. 52205074) and the National Key Research and Development Program of China (no. 2021YFC2800202, no. 2021YFC2800X00, and no. 2023YFC2810000).
Open Research
Data Availability Statement
The data that support the findings of this study are available from the corresponding author upon reasonable request.