Effectiveness of Fish Scale-Derived Collagen as an Alternative Filler Material in the Fabrication of Polyurethane Foam Composites
Abstract
This study is based on the utilization of fish scale-derived collagen (FSC) as a potential filler material in polyurethane foam (PUF) composites. The composites were prepared with varying FSC concentrations (2.5%, 5 wt%, and 10 wt%) with the standard PUF matrix, while calcium carbonates in the standard sample (STD) were completely substituted with 50 wt% of collagen. When examining the effects of collagen concentration on mechanical characteristics, complex correlations emerge between tensile strength, elongation, tear resistance, and ductility. The results reveal that the addition of 2.5 wt% FSC increased tensile strength by 12.66% during heat aging, while the addition of 5 wt% at standard temperature increased elongation by 6.65%. Under normal conditions, collagen significantly enhanced the material’s resistance to tearing, demonstrating its potential for long-term durability. Under typical conditions, tear resistance showed notable gains, increasing by 84.85% (50 wt% FSC) and 33% (10 wt% FSC), respectively. The tear resistance, however, diminishes under heat aging for all concentrations. Morphological assessments indicate a consistent closed cell structure across all samples, with collagen potentially contributing to reinforcement. The study supports the sustainable use of fish scale-derived collagen as a filler, addressing waste management challenges and aligning with principles of environmentally conscious material development.
1. Introduction
Polyurethane foams (PUFs), widely used in various industries, are versatile materials known for their lightweight nature, insulation properties, and affordability [1, 2]. Polyurethanes (PU) are commonly used in engineering due to their adjustable mechanical properties and biocompatibility [3]. The composition and configuration of their constituent parts can be modified to tailor their properties. Traditionally, petrochemicals have been used to produce PU foams, but environmental concerns have recently emerged regarding their use [4, 5]. As a result, there is a growing movement toward the development and application of bio-based polyurethane (PU), which is derived from renewable sources such as soybeans [3]. While bio-based PU foams can be produced with different functionalities and hydroxyl group concentrations, their mechanical properties generally do not match those of petroleum-based PU [3, 6]. Alyamaç and Teke propose that adding reinforcing agents [3] can enhance soy-based PU formulations. Bio-based PU foams have been reinforced in the literature using a variety of micro- and nanoscale fillers, including hydroxyapatite[7, 8], calcium carbonates [9], wood fiber [10], sawdust [11], graphene oxide [12], magnesium hydroxide [13], montmorillonite [14], halloysite nanoclay [15], eggshells [16], and chitosan [17]. In particular, Zhang and Hu [8] looked at how hydroxyapatite nanofillers affected PU composites. According to their findings, the PU composite’s surface wettability rose with the addition of hydroxyapatite nanofillers, improving its biocompatibility [8]. Additionally, PU composites with CaCO3 fillers showed improved mechanical properties, according to a study by Choe and Lee [9].
In recent years, there have been an increasing demand for sustainable and ecofriendly materials that align with the principles of green chemistry and circular economy practices [18]. Fish scale-derived collagen emerges as a potential candidate for replacing traditional fillers in PU foam formulations. Naidoo et al. [19] investigated the effects of eggshells as a filler material in PU on different environmental conditions. The authors reported an improved mechanical property, which they attribute to the collagen constituents of the eggshell fillers [19]. Collagen, a fibrous protein abundant in animal tissues, particularly in fish scales [18], exhibits unique properties that make it an attractive additive in PU fabrications. Due to its biocompatibility, nontoxicity, and biodegradability, collagen is widely used in a variety of sectors [3]. However, little research has been done on the possible application of fish scale-derived collagen (FSC) as a support material in traditional biomaterials. FSC is a byproduct of the seafood business that is frequently regarded as waste and causes problems for the environment. Utilizing this collagen as a filler not only addresses the issue of waste management but also aligns with the principles of sustainable development [20].
Recognizing the enormous potential and critical role of collagen in spectrum of applications, we aim to assess its effectiveness in enhancing the mechanical properties of PU composite in comparison with commonly used filler material in the industry (calcium carbonates). The study investigated the fabrication of PU foams with the addition of different weight concentrations of collagen and temperature conditions. Temperature reportedly has a significant impact on the properties of PU composites, such as their mechanical and thermal properties[19, 21].
Consequently, it is imperative to examine how temperature affects the mechanical characteristics of PU-based composites reinforced with FSC. Tensile, shear, elongation, and FSEM tests were used to describe the mechanical and physical characteristics of the PU-based composites. Tensile, shear, elongation, and FSEM tests were used to describe the mechanical and physical characteristics of the PU-based composites. The composites were prepared with varying concentrations of FSC (2.5%, 5 wt%, and 10 wt%) in a standard PUF matrix, while the standard sample (STD) had 50 wt% collagen as a complete substitute for calcium carbonates. The concentration-dependent effects of collagen on mechanical properties were examined, revealing nuanced relationships with tensile strength, elongation, tear resistance, and ductility.
2. Methodology
The PUF chemicals such silicone L620 and color stabilizer CS-15 were purchased from Momentive. Methylene chloride 99.9% was sourced from local supplier in South Africa. Mesamoll was supplied by Lanxess (China), while desmodur T80 toulene-2,4-diisocyanate (TDI) and polyol Desmophen 1906 were supplied by Covstro. Catalyst Kosmo T9 was sourced from Evonik, and calcium carbonate called kulu powder was sourced from Idwala. Sodium hydroxide (NaOH, 0.1 M) and acetic acid (0.5 M) and sodium chloride (NaCI, 9% m/v) were sourced from local Laboratory Analytical Supplies in Durban South Africa. Tris-glycine buffer (×10 concentrated, pH = 8.8) was sourced from Shalom Laboratory Supplies and a dialysis membrane (MWCO 12–14 kDa, 30 mm diameter) from Lichro Chemicals. All chemicals and reagents were of analytical grade and ready to use.
2.1. Fish Scale Collagen (FSC) Preparation
Fish scale waste was collected from a local fish shop in Durban, South Africa. The scales were thoroughly washed and disinfected using distilled water and 5 mL of household bleach. To remove bacteria, the fish scales were defrosted to room temperature and then air-dried for 2 days to remove excess water. To obtain fish scale collagen (FSC), a well-established protocol involving demineralization and acid hydrolysis was used [18]. For 2 days, the scales were treated with 0.1 N NaOH to get rid of pigments and noncollagenous proteins. After washing and drying for 2–3 weeks, collagen extraction was carried out using various parameters. To extract collagen from the demineralized fish scales, 100 g of the scales was soaked in 0.5 M acetic acid for 48 hr at 4°C with occasional stirring. The solution was then centrifuged at 3,000 rpm for 30 min at 4°C. The supernatants were salted out by adding 9 % NaCl and automatically stirred for 1 day. They were then suspended in a tris-glycine buffer. Pellets were collected by centrifugation, washed with distilled water, and dialyzed using a dialysis membrane (MWCO 12–14 kDa) to remove residual salts. The resulting collagen was freeze-dried at −80 under vacuum conditions. The amino acid composition of the resulting collagen was used for characterization.
2.2. Fabrication of Polyurethane-Based Composites
The general formula utilized to prepare the PUF-based composites is highlighted in Table 1. Following a standardized process similar to that described by Naidoo and Onwubu [19], the PU foam samples were manufactured, and their qualities were methodically assessed. In this process, a mechanical stirrer was used to combine FSC and PUF to make PUFs. To create composites with various reinforcement levels, different weight percentages of FSC (2.5, 5, and 10 g) were added to the conventional PUF mix. In addition, 50 g of FSC (swap sample) was used in place of Kulu powder, or calcium carbonate, in the usual formula. This was done with the aim of assessing the possibilities of replacing the commonly used filler material in the foam industry. In order to get the target density of 16–17 kg/m³, the composition was changed. In the experimental setting, a manual mixing device was included in the foam laboratory. Weighing the polyol, additives, and additional ingredients, such as kulu powder, to precise proportions in a 3 L container was the process for making PUF-based composites. FSC in varying concentrations were then added as a substitute and an additional filler, followed by stirring. In a separate cup, toluene di-isocyanate (TDI) with an index value of 113.6 was weighed and added to the stirred mixture of polyol, water, and additives. The mixture was stirred again before being transferred into a mold for creaming and rise time recording. The foam was dried for 10 min at 70°C in an oven following a full rise. Three trials of this procedure were conducted, one with a standard sample and two with varying FSC doses. Before being subjected to physical property testing, the foam blocks were sliced using a band cutter and clicking press to ensure dimensional correctness. Correctly sized cut samples were subjected to two different temperatures: 24°C in a controlled laboratory setting and 140°C in an oven for heat aging.
Materials | Std | Swap out filler (Kulu powder) with fish scale collagen | Std + 2.5 g fish scale collagen | Std + 5 g fish scale collagen | Std + 10 g fish scale collagen |
---|---|---|---|---|---|
Polyol | 170.01 | 170.01 | 170.01 | 170.01 | 170.01 |
Tdi | 123.79 | 123.79 | 123.79 | 123.79 | 123.79 |
Water | 9.81 | 9.81 | 9.81 | 9.81 | 9.81 |
Catalyst mix | 2.75 | 2.75 | 2.75 | 2.75 | 2.75 |
Amine mix | 0.69 | 0.69 | 0.69 | 0.69 | 0.69 |
Silicone | 3.11 | 3.11 | 3.11 | 3.11 | 3.11 |
Blowing agent | 29.01 | 29.01 | 29.01 | 29.01 | 29.01 |
Color stabilizer | 3.01 | 3.01 | 3.01 | 3.01 | 3.01 |
Filler–Kulu powder (CaCo3) | 50.01 | 0 | 50.01 | 50.01 | 50.01 |
Fish scale collagen | 0 | 50 | 2.5 | 5 | 10 |
Cream time | 10 | 12 | 11 | 10 | 12 |
Rise time | 115 | 129 | 139 | 144 | 148 |
- Note. Std = standard sample; all preparations were in weight.
2.3. Calculating the Amino Acid Content of FSC
The Kjeldahl method was utilized to ascertain the amino acid content of the extracted FSC, while Stegmann method 19 was employed to evaluate the hydroxyproline concentration. An automatic amino acid analyzer was used to get the results of the amino acid composition tests for FSC, which are shown in Table 2. Amino acids are the building blocks of proteins, and their distribution is crucial in determining the overall characteristics of the protein. The composition of the amino acids in 100 g revealed 17 different types of amino acids. The high percentages of glycine (20.98%), proline (15.43%), and hydroxyproline (11.51%) suggest a significant presence of structural proteins like collagen. According to Gauza-Włodarczyk and Kubisz [22], glycine determines the regular structure of the collagen chain and allows for the formation of stabilizing bonds between chains.
Type of amino acid | Composition (%) (100 g) |
---|---|
Histidine | 1.19 |
Arginine | 6.69 |
Serine | 3.04 |
Glycine | 20.98 |
Asparagine | 6.63 |
Glutamic | 10.19 |
Threonine | 2.58 |
Alanine | 9.81 |
Proline | 15.43 |
Lysine | 4.53 |
Tyrosine | 0.24 |
Methionine | 2.85 |
Valine | 1.92 |
Isoleucine | 1.51 |
Leucine | 2.59 |
Phenylalanine | 1.55 |
Hydroxyproline | 11.51 |
2.4. Fourier Transform Infrared Evaluation of FSC
To examine the structural alterations in the PU composite, the Perkin Elmer Universal ATR was employed. An investigation into the background was done prior to scanning. Subsequently, every sample that had been cut was put in a sample holder and scanned at a resolution of 4 cm−1 between 400 and 4,500 cm−1.
2.5. Microscopic Evaluation of the FSC
Using a Carl Zeiss scanning electron microscope (SEM) with field emission, the surface morphology of PU composites was examined. The SEM was run in controlled air conditions at 20 kV. Before SEM inspection, a small layer of electrically conductive gold was put to the surface to prevent an accumulation of electrostatic charge.
2.6. Mechanical Testing
Standard test procedures were used to characterize the PUF-based composites’ physical characteristics. An Instron Universal Testing Machine was used to assess the tensile, elongation, and tear resistance. Two distinct temperatures were used to examine the samples: room temperature and heat aging.
A 2 kN Instron was utilized for the tensile test, which was conducted in accordance with SABS 640–1976 Section 6.8 regulations. The SANS 883 : 2009 was followed for conducting the elongation at break test. The item was shaped like a dog bone and was 150 × 27 × 17 mm. The gauge length was set at 45 mm, and the machine speed was set to 500 mm/min. Tensile strength findings were recorded in kPa, and the test was maintained until the sample burst. To get an average value for statistical analysis, five samples underwent tensile and elongation testing.
The SABS 640–1976 was followed in conducting the tear resistance test. The test was run with the machine speed set to 100 mm/min until the tear spread to the center of the sample. The highest force (N) measured throughout the experiment.
The sample size used for the density measurement was 100 × 100 × 50 mm. A steel ruler with a millimeter grade and a precision of 1 mm was used to measure the dimensions of the object’s length, width, and height. The mass of the sample was then ascertained by weighing it on a scale that had a sensitivity of 0.1 g.
2.7. Statistical Analysis
Using statistical packaged for social science (SPSS, IBM, version 29), one-way analysis of variance (ANOVA) was applied to test the mean differences in tensile strength, elongation at breaking point, and tear strength at α.05.
3. Results and Discussion
3.1. FTIR Characterization
FTIR analysis of PU foam reinforced with standard sample (calcium carbonates filler) and collagen under standard temperature and heat aging conditions are presented in Figure 1. The FTIR provides a detailed understanding of the molecular changes occurring in the composite materials. In the FTIR spectrum of standard sample (STD) at standard temperature (Figure 1(a), characteristic peaks associated with polyurethane are observed. Peaks around 3,300 cm−1 indicate the presence of N─H stretching vibrations, while peaks in the region of 1,720–1,650 cm−1 correspond to C=O stretching vibrations in urethane groups [6, 23]. The peaks around 1,400–1,600 cm−1 indicate the presence of calcium carbonate in the STD [24]. The peaks around 1,650–1,550 cm−1 related to amide groups associated with incorporation of collagen into the polyurethane matrix [25]. As shown in Figures 1(a) and 1(b), with addition of collagen, the relative intensity difference between bonded C=O and free C=O (1,720 cm−1 and 1,650 cm−1) decreased with the increase in filler contents. The finding is consistent with Han et al. [26]. The intensity and position of these amide peaks were consistent both in standard temperature and heat aging, indicating the stability of PU foams under different temperature conditions.

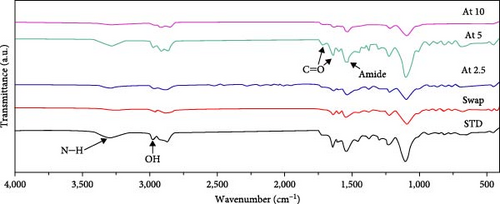
Under heat aging conditions (Figure 1(b), the FTIR spectrum of standard sample PU foam exhibits subtle changes. An increase in peak intensity around 3,000 cm−1 indicates potential changes in hydrogen bonding or the presence of degradation products.
3.2. Morphological Evaluation of the Cell Structure
Polyurethane foam can exist in two primary microstructure configurations: open-cell and closed-cell. These terms refer to the arrangement of voids or cells within the foam structure. Figure 2 shows the FESEM image of PUF-based foam cell structure at 27x magnification at standard temperature (Figure 2(a)–(e)) and at heat aging conditions (Figure 2(a1)–(e1)). Based on the observations, the standard sample showed a close-cell structure (Figure 2(a)–(a1)). Because of the increased dispersion of calcium carbonate throughout the entire surface of PU foams, the cells were likely adjacent to one another. On the other hand, it seems that a higher proportion of FSC causes visible variations in the cell structure. As an illustration, the addition of 10 g results in both an increase in the quantity of densely packed cells and a decrease in cell size (Figure 2(e). In comparison to the typical PU foams, the structure’s shape was likewise neater and more consistent (Figure 2(a)). Comparable patterns were noted when 50 g of collagen was substituted for calcium carbonate in the swap sample, as Figure 2(b)(b1)) illustrates. This could be explained by the bulk viscosity being raised to withstand cell expansion as the concentration of inorganic fillers rose [27]. In order to attain the desired qualities of PU composite foams, it is crucial to take into account the kind of suitable fillers.
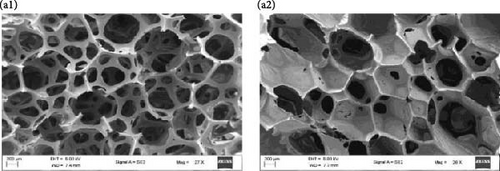
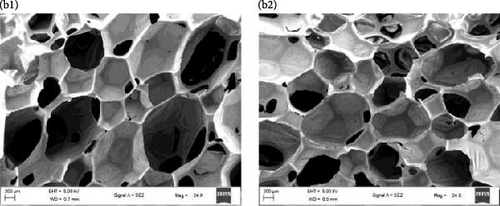
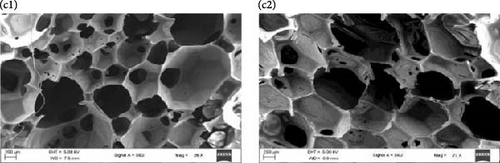
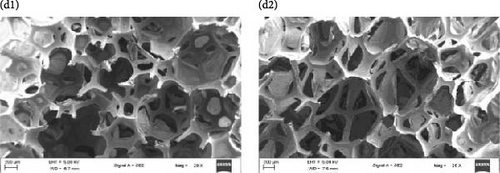
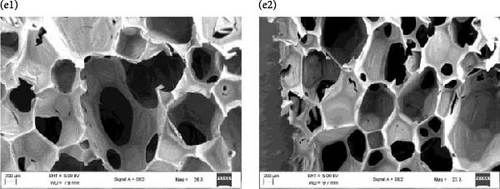
Research has revealed that the cellular makeup of polyurethane foam is pivotal in determining its mechanical properties, including compression and tensile strength [28]. Closed-cell structures have been observed to possess greater compression and tensile strength compared to open-cell structures [29]. The findings suggest that all samples maintain a closed-cell structure, regardless of standard temperature or heat aging, implying that temperature conditions do not impact the morphology of the PU foams. It is also well-known that fillers increase cell density and decrease cell size. This may be attributable to the fact that closed-cell foam is impermeable to air and moisture due to its sealed cell structure. Overall, the pores exhibit greater closure in fish scale collagen (FSC)–PU composites compared to unfilled PU. The greater closure of pores in FSC–PU composites compared to unfilled PU can be attributed to enhanced filler–polymer interaction increased crosslinking density, optimized filler dispersion, and/or the physical barrier effect provided by FSC particles. For instance, proper dispersion of FSC particles within the polyurethane matrix ensures uniform distribution and close packing of filler particles, leading to efficient space utilization and reduced pore size. Studies have indicated that well-dispersed fillers can act as nucleation sites for polymer crystallization, resulting in finer cell structures and improved pore closure [30, 31]. It is envisaged that by affecting the macroscopic cell in this way, collagen acts as reinforcement materials in polyurethane foam composite.
3.3. Mechanical Characteristics of Composites Based on PUF
3.3.1. Tensile Strength of Composites Based on PUF
Figure 3 provides a comprehensive analysis of tensile strength across various sample groups under standard temperature and heat aging conditions. The results reveal distinct patterns influenced by composition and environmental factors. At standard temperature, no significant difference in tensile strength was observed among sample groups (P = 0.805), suggesting that variations in composition, including collagen addition and calcium carbonate substitution (swap), do not substantially affect tensile strength under normal operating conditions. This implies that FSC could potentially substitute kulu powder in the foam industry, offering environmental benefits by utilizing fish scale waste [32]. However, in the “swap” condition where calcium carbonate was substituted, a decrease in tensile strength (65.0 ± 5.6 kPa) occurred compared to the standard (73.3 ± 8.91). The observed decrease may be related to how the different fillers interact with the polymer matrix. Despite this reduction, repositioning FSC for value-added products could be environmentally beneficial, considering the environmental, health, and economic damage associated with fish scale waste disposal [32].

The addition of collagen at different concentrations demonstrated a concentration-dependent effect on tensile strength. The most significant decrease (62.7 ± 6.97) occurred with 2.5 g collagen, indicating a substantial adverse effect with a percentage change of approximately −14.47%. Similar trends were observed with 5 and 10 g collagen, suggesting that increasing collagen content tends to decrease tensile strength compared to standard samples. These observations align with existing literature highlighting the sensitivity of material properties to changes in composition, particularly when introducing foreign elements like collagen [3].
Under heat aging conditions, tensile strength significantly differed among sample groups (P = 0.023). The substitution of calcium carbonate with 50 g of collagen in the “swap” sample led to a substantial decrease in tensile strength (65.0 ± 5.6), consistent with studies indicating that PU may become more detrimental under elevated temperatures [33]. Surprisingly, the addition of 2.5 g collagen resulted in a remarkable increase in tensile strength (86.9 ± 8.1), approximately 12.66% higher than the STD. This suggests a positive influence of this collagen concentration under heat aging conditions, possibly attributed to its reinforcing properties [34]. This finding contrasts with studies suggesting a loss of strength and modulus with increased temperature [35, 36]. Conditions with 5 and 10 g collagen exhibited decreases in tensile strength (71.1 ± 7.4 vs. 71.49 ± 9.5), albeit to a lesser extent than observed at standard temperature (77.1 ± 5.74). These variations indicate a nuanced relationship between collagen content and tensile strength, emphasizing the importance of optimizing composition for specific environmental conditions [9].
3.3.2. Elongation at Break of Composites Based on PUF
Figure 4 presents a detailed analysis of mean elongation, standard deviation, and P values for various PU sample groups under different environmental conditions, shedding light on the material’s flexibility and ductility. At standard temperature, standard samples demonstrated an elongation at the breaking point of 96.1% ± 2.10%, with comparable behavior across sample groups (P = 0.376). The substitution of calcium carbonate in the “swap” condition led to a nonsignificant increase (101.1% ± 19.0%) of approximately 5.20% in elongation, suggesting a potential influence on ductility. The addition of 2.5 g collagen resulted in a notable decrease (83.9% ± 9.77%) of approximately −12.64%, indicating a stiffening effect. In contrast, 5 g collagen exhibited a moderate, nonsignificant increase (102.5% ± 15.8%) of approximately 6.65%, enhancing material flexibility. The inclusion of 10 g collagen yielded a subtle, nonsignificant improvement (100.0 ± 3.6) of approximately 4.05% in ductility. This aligns with the general rule that the mechanical strength of PU composites increases with higher filler contents, as seen in other studies [9]. The probable increase in elongation of PU foam at higher concentration of the collagen filler may be attributed to the ability to resist compression load, thus enhancing the durability of the composite during service.
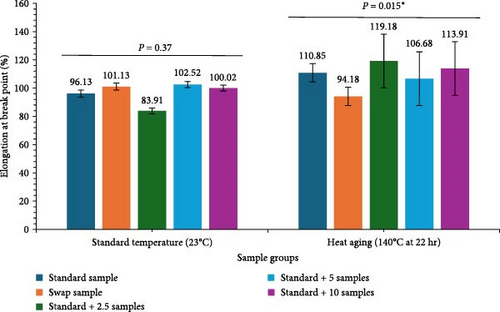
Under heat aging conditions, standard samples displayed a significant decrease in elongation (77.1% ± 5.74%, P = 0.015), indicating altered material properties. The “swap” condition with calcium carbonate substitution resulted in a substantial, significant decrease (65.0 ± 5.6) of approximately −15.63%, negatively impacting flexibility and ductility. Conversely, the addition of 2.5 g collagen led to a significant increase (86.9 ± 8.1) of approximately 12.66%, emphasizing a positive influence on material flexibility and ductility despite elevated temperatures. However, both 5 and 10 g collagen concentrations resulted in significant decreases (71.1 ± 7.4 vs. 71.49 ± 9.5) of approximately −7.77% and −7.27%, respectively, indicating a negative influence on material ductility under heat aging conditions.
These findings underscore the intricate interplay between PU filler contents and environmental conditions in determining elongation at the breaking point. While calcium carbonate and collagen concentrations influence material behavior, their effects vary under standard and heat aging conditions. According to Moo-Tun et al. [27], the use of FSC as a filler material may be advantageous in the real world for creating flexible and long-lasting polyurethane-based composites, especially in applications that are exposed to moderate temperatures.
3.3.3. Tear Resistance of Composites Based on PUF
Figure 5 provides a detailed analysis of tear resistance across various sample groups at standard temperature and under heat aging conditions. Tear resistance is a critical mechanical property, indicative of a material’s ability to resist tearing forces. At standard temperature, the standard samples exhibited a mean tear resistance of 0.2093 ± 0.01 N/mm, showcasing a significant difference compared to other sample groups (p = 0.001). Notably, the substitution of calcium carbonate in the “swap” with 50 g of collagen condition resulted in a substantial and statistically significant increase (0.3867 ± 0.06), marking an 84.85% enhancement in tear resistance compared to the standard. The addition of 2.5 g collagen significantly contributed to tear resistance (0.2567 ± 0.02), reflecting an increase of approximately 22.60%. Conditions with 5 and 10 g collagen displayed significant increases of approximately 25.50% and 33.00%, respectively, emphasizing collagen’s effectiveness in enhancing tear resistance under normal conditions. These results align with previous research, such as Naidoo et al. [19], Ghasemi et al. [37], and Uzoma et al. [38], which investigated natural materials as reinforcements in polyurethane foam composites, reporting improvements in tear strength.

Under heat aging conditions, standard samples exhibited a mean tear resistance of 0.3757 ± 0.02 N/mm, with a nonsignificant P value of 0.362. The substitution of calcium carbonate in the “swap” with 50 g of collagen led to a nonsignificant decrease (0.3453 ± 0.02) of approximately −8.09% in tear resistance compared to the standard. This reduction suggests a potential negative influence of collagen on tear resistance under elevated temperatures. Similarly, the addition of 2.5 g collagen resulted in a nonsignificant decrease (0.3383 ± 0.03) of approximately −9.93%, indicating a potential adverse effect on tear resistance. Conditions with 5 and 10 g collagen showed nonsignificant decreases of approximately −10.85% and −6.63%, respectively, hinting at a potential compromise in tear resistance with collagen additions under heat aging conditions. This decrease aligns with literature suggesting that temperature conditions can indeed impact material properties [33].
Tear resistance, tensile strength, and elongation at break point are all critical mechanical properties of polymer composites, but they measure different aspects of material performance and respond differently to compositional changes and environmental conditions. The differences in tear resistance (Figure 5), tensile strength (Figure 3), and elongation at break (Figure 4) arise from the distinct ways these properties interact with the material’s microstructure and their response to stress and environmental conditions. Tear resistance, being a localized property, is more sensitive to the material’s ability to resist crack propagation, which can be significantly influenced by filler content and environmental conditions [39]. In contrast, tensile strength and elongation at break measure the material’s overall ability to withstand deformation and stress under more uniform conditions [40]. These factors could have contributed to the subtle differences observed in the tear resistance, tensile strength, and elongation at break point.
3.3.4. Density of Composites Based on PUF
Figure 6 presents the density of PU foam at different temperature conditions. PUF-based composites, as investigated in this study, reveal a nuanced relationship between composition and density under both standard temperature (23°C) and heat aging conditions (140°C at 22 hr). The baseline standard sample, characterized by a mean density of 18.97 ± 0.06 kg/m³ at standard temperature, serves as a reference point for understanding the impact of introduced variations. At standard temperature, the substitution of calcium carbonate in the “swap” sample with 50 g of collagen yielded a substantial increase in density, registering at 20.37 ± 0.75 kg/m³—an augmentation of approximately 7.37% compared to the standard sample. This finding suggests that higher collagen filler content contributes to enhanced material density. Conversely, the addition of a modest 2.5 g of collagen resulted in a marginal decrease in density (18.87 ± 0.01 kg/m³) by approximately −0.53%. The delicate balance in material composition is evident, emphasizing the intricate relationship between components and resulting density.
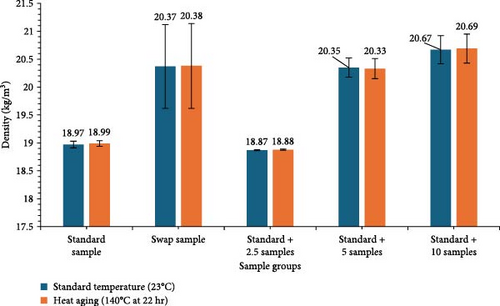
Further variations in collagen concentrations underscored the material’s versatility. Incorporating 5 and 10 g of collagen led to significant increases in density—20.35 ± 0.17 kg/m³ (7.27%) and 20.67 ± 0.25 kg/m³ (8.97%), respectively—compared to the standard sample at standard temperature. These results underscore collagen’s positive influence on material density, emphasizing its potential for optimization in composite materials.
Under heat aging conditions (140°C at 22 hr), the standard sample exhibited a mean density of 18.99 ± 0.05 kg/m³. Notably, the substitution of calcium carbonate in the “swap” sample induced a substantial and statistically significant increase in density (20.38 ± 0.76 kg/m³) by approximately 7.31%. This suggests a crucial role for collagen in enhancing material density under prolonged heat exposure. In contrast, under heat aging conditions, the addition of 2.5 g of collagen led to a slight decrease in density (18.88 ± 0.01 kg/m³) compared to the standard sample by roughly −0.58%. This subtle variation highlights the delicate interplay between composition and density, emphasizing the need for precision in material formulation. Conversely, the inclusion of 5 and 10 g of collagen, even under elevated temperature conditions, demonstrated significant increases in density—20.33 ± 0.18 kg/m³ (7.06%) and 20.69 ± 0.26 kg/m³ (8.95%), respectively, compared to the standard sample.
Overall, the findings showed that density measured is within the range obtainable for a flexible PU foam. The practical implications of these findings extend to industries where material density is a critical factor. Lower-density materials, for example, offer advantages such as improved lightweight properties, facilitating handling and transportation. This is particularly relevant in applications like automotive and aerospace, aligning with previous research emphasizing the importance of weight considerations in these industries [41, 42]. Additionally, lower-density materials may contribute to enhanced thermal insulation characteristics due to increased porosity, as indicated by prior studies [43].
4. Conclusions
In this study, collagen, derived from fish scales, was explored as a sustainable and environmentally friendly alternative to traditional fillers like calcium carbonate in PUF composites. The concentration-dependent effects of collagen on tensile strength were evident, with a remarkable increase (12.66%) observed with 2.5 g collagen under heat aging conditions. This result signifies a positive influence of collagen, especially in environments with elevated temperatures. While higher collagen concentrations exhibited a decrease in tensile strength under standard conditions, the nuanced relationship suggests the need for careful optimization based on application-specific requirements. The study demonstrated varying effects on elongation at break, emphasizing the intricate relationship between collagen content and material flexibility. Higher concentrations of collagen, particularly 5 g, exhibited promising improvements (6.65%) in ductility under standard temperature conditions, suggesting potential advantages in applications where flexibility is crucial.
Furthermore, collagen emerged as a significant enhancer of tear resistance under standard temperature conditions, showcasing its potential for reinforcing PUF composites. The substantial increase (84.85%) in tear resistance with collagen substitution in the “swap” condition indicates its efficacy in improving material durability. Collagen positively influenced material density, showcasing its potential benefits in applications where specific densities are critical. The observed increases in density with collagen additions, even under heat aging conditions, highlight its role in enhancing material compactness.
The morphological assessment using FESEM revealed a consistent closed-cell structure across all samples, indicating the stability of PU foams. The ability of collagen to maintain a closed-cell structure, irrespective of temperature conditions, suggests its resilience and suitability for diverse environmental settings. Beyond mechanical properties, the utilization of fish scale-derived collagen addresses waste management challenges associated with the seafood industry. By repurposing collagen, a byproduct often considered waste, the study aligns with the principles of sustainable development, contributing to environmentally conscious material practices.
Conflicts of Interest
The authors declare that they have no conflicts of interest.
Acknowledgments
We acknowledge the support provided by the National Research Foundation. Open Access funding enabled and organized by SANLiC Gold.
Open Research
Data Availability
The corresponding author will make the datasets created and/or analyzed during the current study available upon reasonable request.