Clothing Modular Design Based on Virtual 3D Technology
Abstract
In order to improve the effect of online clothing modular design, this paper adopts the improved linear skinning technology. Moreover, without changing the original input value, this paper uses the QLERP interpolation method to interpolate the rotations of multiple joints into one and determines the rotation angle through the calculation of the rotation center point, so as to subtly solve the problem of skin depression and distortion, and greatly improving the authenticity of the experiment. In addition, this paper combines the virtual 3D technology to build a clothing modular design system to improve the effect of online clothing design. The simulation test results show that the clothing modular design system based on virtual 3D technology proposed in this paper basically meets the current online clothing modular design requirements.
1. Introduction
Informatization is one of the important themes of contemporary society, and various embedded information systems are constantly integrated into people’s lives, becoming an important force for improving the quality of life. With the rapid development of microelectronic technology and material technology, various microprocessing devices are emerging, which provides a solid technical foundation for the integration of electronic equipment and clothing [1]. The digital clothing system improves the ability of users to obtain and process information anytime and anywhere by integrating data collection, wireless transmission, positioning and navigation, video collection, and other information processing functions in clothing. The combination of digital clothing and job requirements is of great significance to improve the efficiency of workers in different industries in dealing with problems [2]. The embedded computer system for clothing is centered on the wearer. Due to the limitations of people’s physical ability, feeling, and cognition, strict requirements are put forward for the function, performance, structural layout, and other aspects of the computer system [3]. The combination between soft clothing and hard computer modules, especially how to improve the practical performance of the system under special use environments and operating conditions through the integration of clothing and computer systems has become the key to the realization of the system.
The garment CAD system is involved in all aspects of garment production, including the creation of fashion designers, the drawing of clothing renderings, the drawing of clothing samples, the confirmation and modification of industrial patterns, and industrialized process processing, such as push plates and layouts. The garment CAD system can generally be divided into the garment design system and style design system. The garment piece design system includes three functional modules: template design, grading, and layout. The hardware devices required for the garment piece design system include a host computer, a digitizer, and a plotter. The advantage of CAD technology is in grading and nesting, especially the grading has been fully automated. The grading of garment pieces is a repetitive and tedious task. It takes a lot of time and energy to use manual methods. Due to the low efficiency of traditional grading, the size and specifications of garments are often incomplete.
Using CAD technology, you only need to input the corresponding specifications in the size table, and within a few minutes to ten minutes, the complete set of specifications can be quickly provided, and the accuracy is very high. However, manual grading will affect its accuracy because each person’s grading method is different. Using computer grading can also provide nonstandard body-shaped clothing pieces, which can meet market demand in time and improve product competitiveness. On the layout module, there are two methods of automatic layout and man-machine interactive layout in domestic and foreign systems. Compared with traditional methods, the advantages of CAD technology are obvious. The module itself has functions such as selection, translation, flipping, rotation, cutting, and automatic tightening. With the improvement of the requirements for the fit and comfort of clothing and the acceleration of clothing style changes, the establishment of 3D human models and the study of 3D clothing CAD technology have become the most important research direction and research focus of clothing CAD technology.
This paper combines the virtual 3D technology to construct a clothing modular design system, improves the effect of online clothing design, and provides a reference for the subsequent online clothing design.
2. Related Work
Literature [4] summarizes the necessity of combining the Internet and personalized clothing customization by analyzing the life cycle of clothing commodities, the situation of unsalable products, and the development status of Internet technology. Literature [5] analyzes the difference between the network and the traditional sales model, points out that the network personalized clothing is a new trend of clothing marketing strategy, and, on this basis, summarizes the effective measures to combine clothing personalized customization and network retail mode. Literature [6] starts from the concept of clothing personalized design and customization and studies and predicts the development direction of clothing style customization from a perceptual perspective. Literature [7] adopts the combination of questionnaire survey and expert interviews, uses SPSS software to scientifically analyze the survey data, summarizes the factors that affect consumers’ choice of online custom clothing, and provides effective suggestions for the clothing online customization industry. Literature [8], through the investigation and analysis of the homogenization phenomenon of the clothing market, concluded that the traditional single consumption can no longer meet the needs of consumers and other problems, and the clothing market needs personalized customization to obtain and protect the interests of enterprises and consumers. Literature [9] established a digital and intelligent MTM customization system on the basis of personalized customization process, pattern generation technology, and three-dimensional measurement technology to meet the individual needs of consumers and improve the level of digital and intelligent manufacturing of enterprises. On the basis of the existing research, in order to better meet the personalized customization needs of consumers, the clothing module is used as the customization unit, and the cheongsam style is coded based on the coding principle, and the module coding database is established to create a customized cheongsam. The basic principle of the module configuration of the process; based on this principle, the efficiency of the process design is verified through practical application to ensure the scientificity and rationality of the design results [10].
Reference [11] divides the design elements into three levels and makes a detailed study of the design elements. The first-level element refers to the shape of the element, such as circle, square, pocket, collar, T-shaped, and X-shaped. The secondary element refers to the quality of the element, such as color number, roughness, smooth wrinkle, tightness, bump, and soft and hard. The tertiary element refers to the quantitative state of the element, such as size, number, number, length, area, and quantity. Literature [12] analyzed several important characteristics in clothing design, including body shape change, clothing modeling, comfort function embodiment, clothing material selection, and decorative pattern design. Literature [13] focused on analyzing the interest of clothing in terms of outer contour, internal structure line, pattern, color, processing technology, etc., such as fabric splicing, color splicing, text pattern design, and internal structure line design; the interesting design is integrated into the interesting design of clothing. Xie Xiuhong analyzed the main points of clothing design and came to the conclusion: Only by grasping the brand positioning, developing the trend, and integrating the color and regional environment can the clothing products meet the new demands of the clothing market. Reference [14] analyzes the design and development process of clothing from the perspective of creating user experience value. In the experience economy, experience becomes an independent economic provision carried by products and services. The experience itself contains value at the same time, and the user experience value is a new user value, which comes from the user’s overall perception and evaluation of the experience provided by the enterprise. Through the user’s involvement in the development of clothing products, on the one hand, it can promote two-way communication, establish an effective feedback system, and make the product truly meet the needs of users; on the other hand, users become the cooperative developers of enterprise products, and the participation process also creates experience value [15]. Reference [16] starts from the perspective of bionic design of clothing, studies the method of bionic design of clothing, and discusses the laws of bionic design of clothing. Literature [17] pointed out that clothing bionic design has both entertainment function and obvious educational function. From the research of experts and scholars, in addition to ensuring the practicality of clothing, they should also pay attention to the safety of clothing. On this basis, they must add a certain interest to meet the needs of the market. From the perspective of the details of clothing, the elements of clothing design include silhouette, collar, sleeve, color, pattern, and fabric. The requirements for clothing should start from these design elements and use different combinations to achieve the ideal design
The perceptual engineering system based on information technology is a system that uses an expert system to convert consumers’ sensory images into detailed elements of design. It mainly includes a perceptual database, an image database, a knowledge database, and a design and color database. The methods used include brain waves, eye tracking, expressions, behaviors, and questionnaires [18]. Experts and scholars have conducted extensive research on Kansei Engineering and its applications and have had preliminary applications in many industries. Reference [19] conducted a systematic study on the perceptual design method according to the perceptual characteristics of clothing. It summarizes and analyzes the elements of clothing design, the perceptual characteristics of clothing, the relationship between the two, and the rules of clothing design and builds a knowledge platform for clothing perceptual design. Literature [20] proposed a complete study of expert knowledge acquisition and formal representation, clothing interaction design based on knowledge platform, and the realization of the unification of expert cognition and customer cognition in the process of recommendation interaction. Reference [21] studied the application of Kansei Engineering in clothing. They captured the user’s feelings about clothing according to the evaluation of ergonomics and psychology and then defined the design features of clothing through user sensibility and finally combined the consumer’s image with the clothing. Feeling translation becomes a design element and is used in clothing design.
3. Improvement of Bone Skinning and Optimization of Depth Information
The human body consists of two parts: skin and bones. Polygon static meshes constitute human skin and joint chains with topology structure constitute bones. When the bone node moves, its transformation matrix is mapped onto the skin static mesh, causing the skin to distort. In response to the above phenomenon, scientists have proposed a variety of solutions, the more typical ones are the multielement skinning algorithm and the linear skinning algorithm. Through the pair analysis of the two algorithms, this paper proposes an improved linear skinning algorithm based on it, which uses the QLERP interpolation algorithm to transform the skeleton matrix information. In this paper, the weight value of each vertex is allocated reasonably, and the purpose is to optimize the model. Moreover, this paper smoothes the joints of the limbs to solve the problem of skin depression and make up for the obvious seam phenomenon at the joints of limbs.
First, the barycentric coordinates are briefly introduced. Since the three-dimensional human body and cloth model meshes used in the virtual fitting system are all triangular meshes, and the triangle itself is a two-dimensional object, it is necessary to use the method of barycentric coordinates to convert the two-dimensional coordinates into coordinates associated with the triangular surface but not associated with its 3D coordinate space. The barycentric coordinates here are generalized coordinates, and the purpose is to rearrange and define the vertices of each local model in a linear combination. The barycentric coordinates must satisfy two properties. First, the defined value will not change when imitation transformation occurs. In addition, as long as there is a point in the defined space that satisfies the functional requirements of linear reconstruction, it is the barycentric coordinates.
In the formula, Sx represents a sphere centered on x, the unit is 1, v(t) and x are vectors in any direction, and (v(t) − x)/|v(t) − x| is the normal vector on Sx.
In the formula, the distances calculated by x and v(t) in the mean calculation are both Euler distances, and Euler distances do not include internal distances. When a concave polygon is encountered, errors will occur, and through the mean calculation, there may be negative coordinates, which is not in line with reality. In this case, it is only necessary to omit the value expressed as a negative coordinate.
The MVC barycentric coordinate method completes the transformation of coordinates from three-dimensional to four-dimensional, making the operation process simpler.
Single joint-driven or mesh-driven motion can make the model appear bulky and inflexible. The skeletal skinning technology combines the two, making the movement of the characters more flexible and realistic. The skinned mesh is used to render the character, and each bone that drives the movement of the human body will affect a part of its corresponding mesh. In particular, the node bones will share the same vertex and weight value. However, due to the hierarchical division of the human body structure, each bone needs to establish a separate mesh, and the skin is used as a mesh on top of the bone. When the bones move, the vertices of the skin mesh will also change accordingly. At this time, there will be obvious cracks at the joints of the limbs, and the skin mesh will appear obvious depression and distortion.
The three-dimensional space is extended to a four-dimensional space, which is used to deal with the mesh deformation problem in the skinning method. The calculation principle of the double quaternary method is as follows.
In the formula, is the conjugate complex of Q∗ and Q∗ is the adjoint matrix of Q.
The algorithm uses the double quaternary algorithm to successfully convert the points in the three-dimensional space into the points in the four-dimensional space, which makes the vector expression more accurate, effectively solves the problems of skin depression, and runs very fast.
In the formula, v represents the coordinates of the skin node under T-pose in world coordinates, the transformed coordinate value, Wj represents the weight value of the jth bone, and n represents the number of bound bone joints. For bones that are not related to motion, the weight is recorded as 0, and the bone weights of all control nodes satisfy the sum = 1.
In the formula, PQ represents the quaternion of the connected joints, respectively, w, and (1 − w) represent the weights corresponding to the joints p, q, respectively.
The comparison of the effect before and after skinning using the method in this paper is shown in Figure 1.
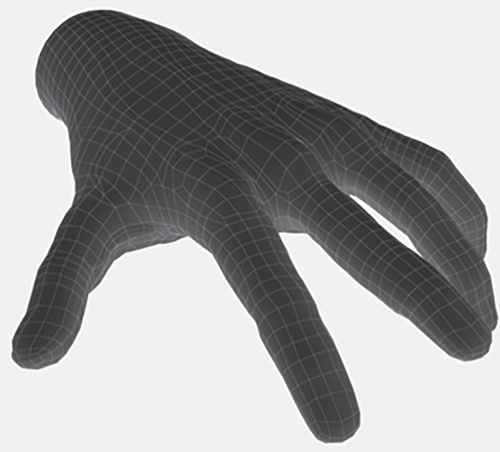
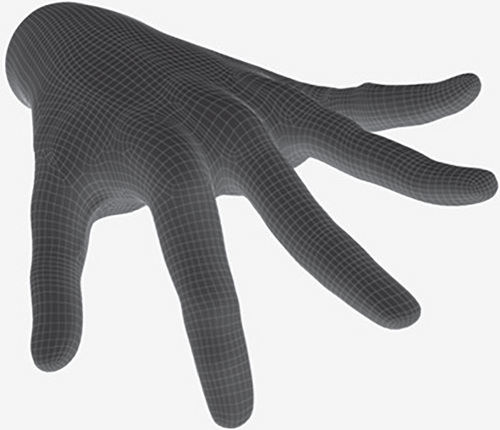
After experimental verification, the method uses the original data to make changes, avoids the reinput of data, greatly improves the running speed, and effectively avoids the skin distortion and sunken problems caused by overfitting.
The distance between the depth camera and the target object is limited to an integer set range, where the maximum distance is 255 and the minimum is 0, beyond which depth images cannot be recorded. When the value is larger, the distance between the object and the camera is farther, and the smaller the value is, the closer the distance between the object and the camera is. After obtaining the depth image, it firstly divides the obtained 640∗480 depth image into nine equal parts based on the kinect coordinate system. The central area is the target area, and similar pixels are found in the eight neighborhoods of each point to form the human body area pixel set R. Then, the threshold value T is set in the z-axis direction, and the points within the range of the central region R are binarized to obtain a segmented depth image. The comparison before and after using the domain segmentation R value to process the depth information is shown in Figure 2:
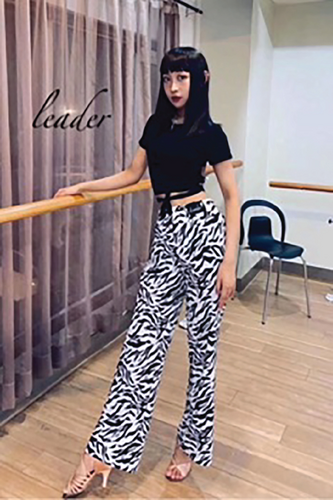
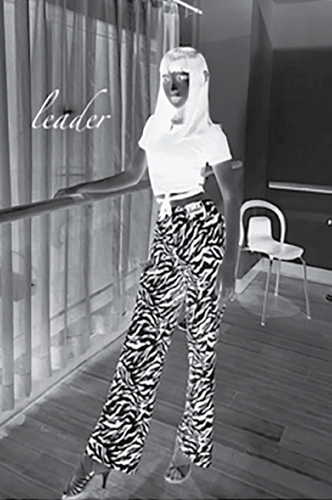
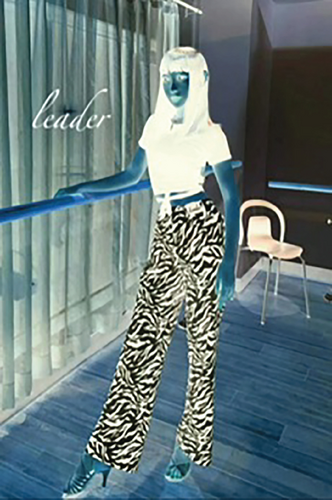
In this paper, the idea of domain segmentation is used, and a threshold value T is used to filter the input information according to the depth value. Moreover, the values of pixels in the neighborhood around each point are weighted to obtain pixels, which are combined into a human body region pixel combination R, and a complexity calculation is performed on them, thereby obtaining a pure target human body.
When using the Kinect device, the depth images acquired with the Kinect will appear noise and black holes due to uneven reflection values at the edges of the model and occluded areas. If it is directly applied to the virtual fitting system, it will reduce the quality of the depth image and affect the experimental effect. Then, how to reduce these noises outside the background and retain the edge of the target human silhouette is a problem that needs to be solved. This section introduces a variety of filtering methods, and carefully analyzes and compares them. Finally, a high-efficiency bilateral filtering method is selected to remove noise, which ensures the authenticity and real-time performance of virtual fitting.
In the formula, the set of points contained in the noise image to be processed is represented by n(i, j), and the weight value of a point in the pixel space is represented by w(i, j). The standard comparison value of all point weight values is denoted by wp, and the field set of pixel points is denoted by Ω. After formula operation, the most filtered image set I(x, y) is obtained.
In the formula, the standard deviation of the Gaussian function is represented by ∂r, which can determine the filtering performance. The weight value of the pixel (i, j) in the filter is denoted by W(i, j). When the weight value is larger, it means that the distance between the pixel points is farther and farther, and the correlation is smaller, and vice versa, the correlation is larger.
The advantage of the Gaussian filtering method is that it can be efficiently calculated by Fourier transform, and the calculation is simple, and the simple foreground and background can be effectively segmented, so as to obtain a relatively complete target human body. The disadvantage is that the edge processing is not smooth, the filtering effect is not obvious, and when changing a viewing angle, the image jumps to a large extent.
In the formula, Wr, Wt represents the spatial domain weight and image gray domain weight, respectively, and ∂r, ∂t represents the standard deviation of the amplitude range and the standard deviation of the spatial range, respectively. The closer (x, y) and (r, t) are, the closer the weight w is to the standard value.
Since bilateral filtering has dual function characteristics, its filtering effect is jointly controlled by two parameters. Since the two parameters are finally multiplied, when the value of a quantity in ∂r, ∂t tends to the minimum value of 0, the phenomenon of edge blurring will occur. Therefore, it is necessary to ensure that the two parameters are greater than 0 at the same time. Since the effect caused by the amplitude change is more obvious than the spatial change, it is best to set ∂r ≤ ∂t, that is, the change value ∂t of the amplitude is smaller than the change value ∂t of the spatial range. The main function of ∂t is to increase the constant in the image coverage interval, so as to make the obtained image smoother, and the main function is to preserve the edge information of the image. Therefore, multiplying the two parameters will increase the performance of the two parameters, effectively remove noise, smooth the picture, and protect the edge of the contour In the experiment of this paper, ∂r = 4 and ∂t = 4 are the parameters with the best effect of bilateral filtering. The before and after effect comparison chart is shown in Figure 3.
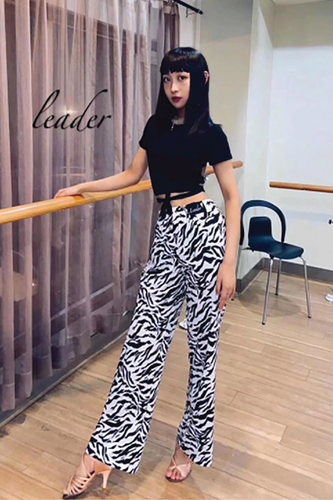
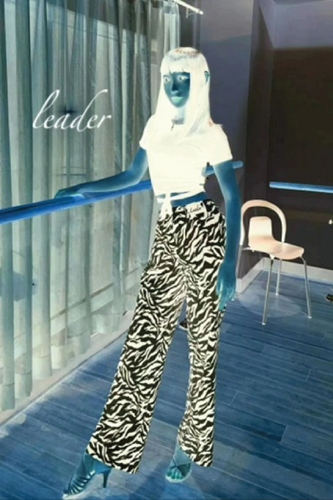
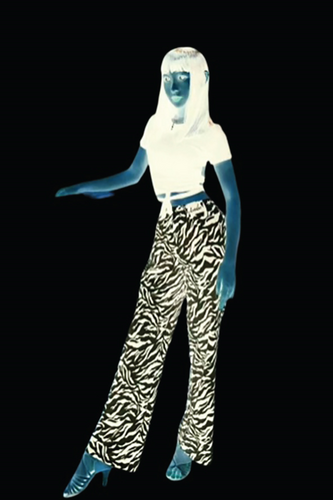
Using bilateral filtering method to effectively remove noise not only solves the problem that Gaussian filtering cannot preserve image edge information but also ensures the smoothness of the image, greatly improves the recognition rate of depth information, and has strong real-time performance.
4. Clothing Modular Design Based on Virtual 3D Technology
The database can display the types and information of stored fabrics, accessories, etc. for users. Users can choose their favorite fabrics and accessories according to the clothing styles they have determined and use the system’s image processing function to display the final clothing effect of personalized customized clothing to users in real time. The specific modular customization process is shown in Figure 4.
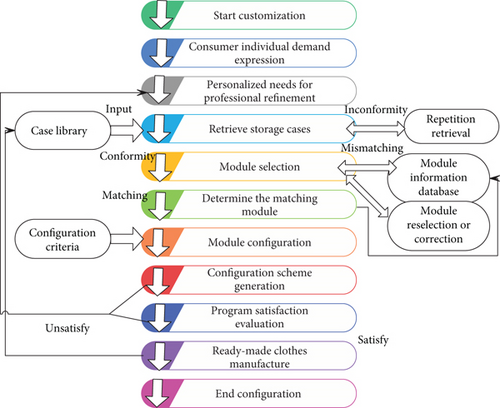
The personalized clothing design process is shown in Figure 5. The process contains 5 basic data information; data 1 and data 2 constitute the customer’s demand information. Among them, data 1 represents anthropometric data, which provides basic size information for clothing design. The accuracy of anthropometric data determines whether the clothing fits. Data 2 represents the customer’s perceptual demand data, which determines the personalized style of clothing products. Data 3 represents clothing design information, which is interactively transformed from data 2, including clothing styles. However, the design information at this time is still a preliminary result and needs to be fed back to obtain feedback information, that is, data 4. Data 4 enters the interactive selection stage and interacts again, and this cycle is repeated until a satisfactory configuration of clothing design information is obtained, and these clothing design information forms data 5. Data 5 is used as storage information and output with data 1 to provide data support for the next interaction.
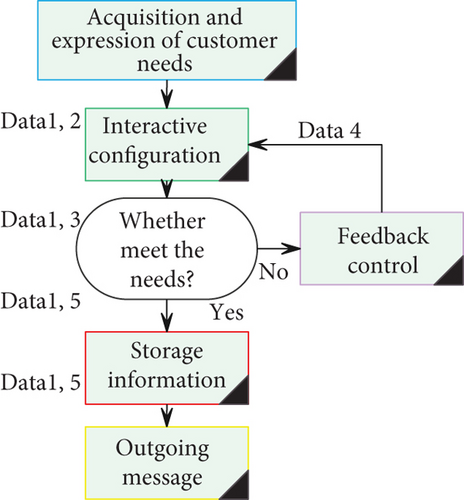
On the basis of the above research, the effect of the clothing modular design system based on virtual 3D technology proposed in this paper is verified, and the online clothing fitting effect and clothing design effect of the system in this paper are counted, and the results shown in Table 1 and Figure 6 are obtained.
Number | Fitting effect | Design effect | Number | Fitting effect | Design effect |
---|---|---|---|---|---|
1 | 93.32 | 89.28 | 24 | 87.47 | 86.00 |
2 | 87.12 | 87.42 | 25 | 93.34 | 87.66 |
3 | 87.17 | 88.91 | 26 | 89.56 | 85.20 |
4 | 93.48 | 90.79 | 27 | 87.87 | 89.32 |
5 | 88.51 | 83.47 | 28 | 89.43 | 89.42 |
6 | 88.63 | 88.68 | 29 | 92.03 | 85.58 |
7 | 88.43 | 83.28 | 30 | 88.74 | 85.03 |
8 | 87.92 | 83.45 | 31 | 92.10 | 89.55 |
9 | 93.29 | 91.86 | 32 | 89.06 | 85.51 |
10 | 93.94 | 87.70 | 33 | 88.62 | 91.25 |
11 | 91.87 | 85.88 | 34 | 92.79 | 87.95 |
12 | 87.63 | 91.07 | 35 | 90.84 | 85.87 |
13 | 88.82 | 84.50 | 36 | 92.58 | 90.95 |
14 | 88.18 | 86.00 | 37 | 88.98 | 85.99 |
15 | 90.09 | 89.89 | 38 | 92.96 | 86.16 |
16 | 93.77 | 88.20 | 39 | 93.37 | 84.90 |
17 | 91.07 | 84.00 | 40 | 87.62 | 90.04 |
18 | 93.70 | 88.95 | 41 | 91.34 | 89.91 |
19 | 88.79 | 84.59 | 42 | 89.92 | 88.20 |
20 | 91.95 | 84.77 | 43 | 87.07 | 89.61 |
21 | 90.14 | 88.56 | 44 | 87.06 | 86.63 |
22 | 87.52 | 91.70 | 45 | 88.90 | 86.69 |
23 | 89.69 | 88.15 |
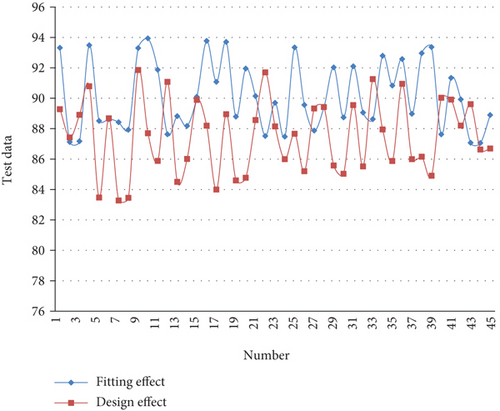
From the above research, it can be seen that the clothing modular design system based on virtual 3D technology proposed in this paper basically meets the current online clothing modular design requirements.
5. Conclusion
CAD technology leads garment enterprises to develop new products quickly and efficiently. It has the characteristics of sophisticated design, labor saving, time saving and material saving, high efficiency, and low consumption. Garment enterprises need to adapt to the fast-paced and multivariety needs of the international market under the new situation and provide high-quality products to the market at the lowest cost and in the shortest time. The use of advanced computer technology has become the first choice, which can transform and enhance the production structure and productivity of the traditional clothing industry. Nowadays, more and more garment enterprises realize the superiority and importance of using CAD system and gradually use CAD technology as a modern and effective means to replace traditional design work. This paper combines the virtual 3D technology to construct a clothing modular design system, improves the effect of online clothing design, and provides a reference for the subsequent online clothing design. The simulation test results show that the clothing modular design system based on virtual 3D technology proposed in this paper basically meets the current online clothing modular design requirements.
Conflicts of Interest
The authors declare no competing interests.
Acknowledgments
This work was funded by the Hunan Provincial Social Science Achievement Review Committee Project (XSP21YBC019).
Open Research
Data Availability
The labeled dataset used to support the findings of this study is available from the corresponding author upon request.