A Study on the Energy Condition and Quantitative Analysis of the Occurrence of a Coal and Gas Outburst
Abstract
With mining depths increasing, coal and gas outburst disasters are becoming more and more serious and complicated, which directly restricts the production efficiency of coal mines. In order to study the rules of energy dissipation during the occurrence of a coal and gas outburst based on the occurrence mechanisms, a simulation experiment of a coal and gas outburst with a ground stress of 16 MPa and a gas pressure of 0.5 MPa was carried out using a self-developed large-scale coal and gas outburst simulation experimental system. A quantitative analysis was given based on the energy model. The results showed the following: (1) In the process of the coal and gas outburst, the main energy source originated from the elastic potential energy of the coal body and the gas internal energy. The main energy loss was used for coal crushing and throwing. (2) The outburst coal sample in this experiment had a mass of 18.094 kg, and the relative outburst intensity was 1.21%. Additionally, the farthest throwing distance of the outburst coal samples was 3.3 m away from the outburst hole wall. The distribution of the outburst coal sample decreased along the roadway, and the proportion of the coal sample grain size in each area first decreased and then increased with the decrease of the grain size. The coal samples with a grain size less than 0.2 mm after the outburst accounted for 6.34% of the mass of the total coal samples. (3) The elastic potential energy of the coal body accounted for 0.34% of the total outburst energy, while the gas internal energy accounted for 99.66%. It was verified that gas internal energy was the key energy source for the coal and gas outburst, and this internal energy was two orders of magnitude more than the elastic potential energy, playing a leading role in the outburst process. After the outburst initiation, most of the energy was consumed in coal crushing, which was in the same order of magnitude as the gas internal energy. Moreover, the energy losses due to friction, vibration, and sound during the outburst process comprised no more than 10% of the total energy. The research results can provide certain guidance for clarifying the mechanism of a coal and gas outburst and the quantitative analysis of outburst energy.
1. Introduction
A coal and gas outburst is an extremely complex gas dynamic phenomenon during which a large amount of pulverized coal is suddenly ejected from a mining face into a roadway or stope in a very short time, accompanied by large amounts of gas, which can destroy underground equipment. With the mining depth increasing by an annual average growth of 10 m–30 m, the proportion of coal and gas outburst disasters has also gradually increased [1–4]. Since the first recorded coal and gas outburst accident, the former Soviet Union, Japan, China, Poland, and more than 20 countries have invested a large amount of resources to carry out research on the mechanism of coal and gas outbursts, and these countries have accomplished abundant achievements [5–8]. The gas dominance hypothesis, the geostress-dominant hypothesis, the chemical essential hypothesis, the comprehensive hypothesis, and other hypotheses have been proposed. At present, the understanding of the outburst mechanism has been united with the comprehensive hypothesis that an outburst is the result of the combined effects of gas, ground stress, and the physical-mechanical properties of coal. It is believed that an outburst result is due to the combined effect of gas, ground stress, and the physical-mechanical properties of coal. It has been recognized that an outburst is a mechanical process that releases energy and destroys coal.
Due to gravity stress, tectonic stress, and mining stress, high elastic potential energy accumulates in coal and rock bodies. Furthermore, there is a large amount of adsorbed and free gas in the pores and cracks of coal seams, which is characterized by high gas internal energy. With the advancement of the working face, stress concentration and gas accumulation occur in front of a coal face. When the elastic potential energy of coal and the gas internal energy increase to a certain level, under the perturbation caused by blasting or other underground operations, coal and gas outbursts may occur [9, 10]. Therefore, the study of the occurrence conditions for coal and gas outbursts from the perspective of energy is of great theoretical significance and practical engineering value.
To investigate the mechanism, evolution laws, and influencing factors of coal and gas outbursts, scholars and experts around the world have conducted a large amount of research [11, 12]. In the 1960s, the Soviet scholar XОДОТ BB [13] first proposed the energy balance equation for the occurrence of a coal and gas outburst from a gas-bearing seam and pointed out that the outburst was mainly caused by a gas emission along with coal deformation. This proposal was produced after an analysis of the variation of stress field in front of the coal face. In the 1990s, Zhu [14] believed that gas outburst energy existed in the form of potential energy in coal seams and surrounding rocks, in combination with some influences of the coal structural differences on outburst energy, and Zhu further revealed another inner link of gas outburst in tectonic failure zones. Xu and Jiang [15] studied the rules of energy dissipation in the process of a coal and gas outburst, and they found that a peak value of gas expansion energy was released at the initial releasing moment of the gas from the coal seam after it was damaged by ground stress. They also found that the magnitude of this value was closely related to the external perturbance. Zhang et al. [16] applied the thermodynamics process of energy release during a coal and gas outburst to the finite element analysis method of gas migration theory, and they proposed an energy release mechanism for the analysis of the coal and gas outburst process. Xian et al. [17] pointed out that the ground stress effect would produce elastic strain energy and plastic strain energy in the process of a coal and gas outburst, but only elastic strain energy could release external work. Wen et al. [18] established the energy relationship of a coal and gas outburst expressed by ground stress, gas pressure, the coal firmness coefficient, and the initial dispersion velocity through tests of mechanical work and the gas internal energy crushing of different coal samples, in combination with industrial analysis and measurements of the firmness coefficient and initial dispersion velocity. Hu et al. [19] believed that the occurrence of a coal and gas outburst must be satisfied by three conditions: the initial instability condition, the continuous failure condition, and the energy condition. They analyzed the energy conditions for outburst occurrences (including birth and development). Based on the coal and gas outburst mechanism, Wei et al. [20] proposed a gas desorption index that could reflect gas expansion energy by analyzing each energy and its effect on the outburst process, and they determined the critical value of the desorption index and gas content accordingly. By studying the scales and types of energy consumption in a gas outburst process, Xie et al. [21] determined that a gas outburst was mainly determined by whether the gas outburst dynamic energy and energy consumption could stay balanced during the dynamic incubation process. When a quantitative change or a mutation of the gas outburst dynamic energy reached or exceeded a certain critical value, a gas outburst would occur instantaneously or with a delay.
Theoretical research on coal and gas outburst energy has been undertaken for a long time, and rich results have been achieved, but most of these results only provide qualitative and simplified models, lacking support for highly similar simulation experimental data or verification with practical outburst cases. There is relatively little quantitative research on coal and outburst energy. Therefore, it is of great significance to establish an accurate and practical energy condition model of a coal and gas outburst and conduct in-depth quantitative research with experimental data obtained by large-scale coal and gas outburst simulation experiments in order to reveal the energy conversion mechanism in an outburst process under multifield coupling conditions and to quantify the occurrence conditions and criteria for a coal and gas outburst.
2. Energy Condition of a Coal and Gas Outburst
Based on the mechanics mechanism of a coal and gas outburst [12], it is believed that the process of a coal and gas outburst can be divided into four stages: inoculation, stimulation, development, and termination. Under certain conditions, the development stage will experience cycles of suspension, stimulation, and development. The conditions that need to be met when a coal and gas outburst occurs are shown in Figure 1. Specifically, when the initial instability condition and the energy condition are satisfied, the outburst will occur. When the continuous conditions and energy conditions of the failure are met, the further development of an outburst is possible. A complete coal and gas outburst consists of its occurrence and development. The initial instability conditions and the continuous conditions of failure are in different outburst stages. Therefore, the initial instability conditions must be met before the continuous conditions of failure can be met. The outburst energy conditions mentioned in this paper include both the energy of the excitation and the energy of the development. Satisfying the energy conditions indicates that a coal seam has an outburst risk, but it does not mean that an outburst will definitely occur. Because an outburst still needs to meet the initial instability conditions and the continuous conditions of failure, an outburst will occur only when all three conditions are met. The initial instability conditions and the energy conditions constitute the necessary and sufficient conditions for an excitation to outburst. The continuous conditions and the energy conditions of a failure constitute the necessary and sufficient conditions for outburst development. Energy conditions are also a necessary condition for excitation and the development of an outburst.
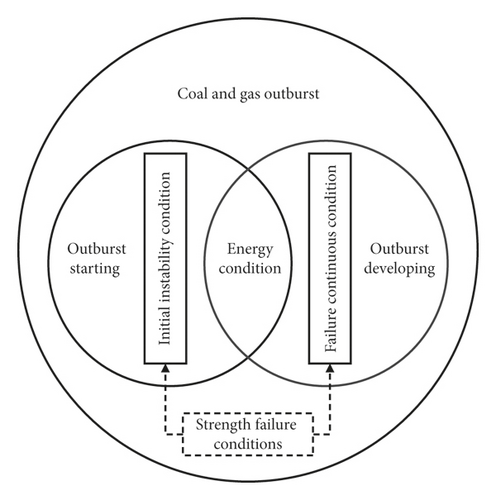
According to the above derivation process, it is known that the unknown numbers in formula (12) are the elastic modulus of coal (E), Poisson’s ratio of coal (μ), the firmness coefficient (f), the vertical stress under the original state of the coal seams (σ0), the coal density (ρ), and the mass of the outburst coal (B). It can be seen that once the specific values of these unknowns are determined, the energy analysis of a coal and gas outburst can be carried out, and the quantitative concept of the release energy and the various dissipative work of the outburst coal and gas can be obtained. The energy condition constructed by formula (12) is the energy condition necessary for the occurrence of a coal and gas outburst. Therefore, the determination of the value of these unknowns reasonably and accurately in formula (12) plays an important role in the energy analysis of a coal and gas outburst.
Taking E = 150 MPa, μ = 0.2, σ0 = 20 MPa, ρ = 1.4 kg/m3, ΔP = 20 ml/s, YP1 = 8%, v = 1 m/s, f = 0.2, different p values corresponding to the B value can be obtained, as shown in Figure 2. It can be seen from Figure 2 that the larger the gas pressure in the coal seam is, the larger the mass of outburst coal is. Under the same outburst conditions, the gas pressure directly determines the mass of outburst coal, and the greater the gas pressure is, the greater the risk of a coal seam outburst is.
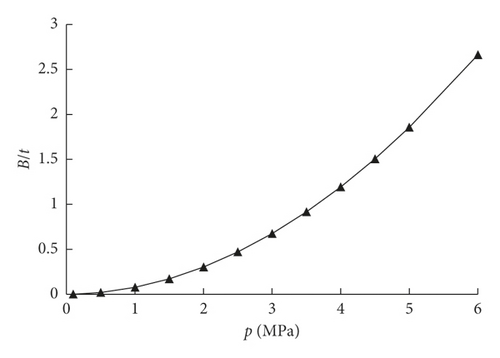
3. Experimental
3.1. Experimental Equipment
- (1)
Power system: A hydraulic subsystem with a stiffness of 3 × 1010 N·m−1, that had loading capacities of 3000 t (vertical loading) and 2000 t (horizontal loading).
- (2)
Sealing system: An outburst box with external dimensions of 2.2 m × 1.8 m × 1.48 m and with corresponding inner cavity dimensions of 1.5 m × 0.8 m × 0.8 m and a maximum inflation pressure of 6 MPa.
- (3)
The piping system was mainly used for the simulation of a coal mine roadway network and it consisted of pipeline components and pipeline supports. There were six sets of pipeline components, including a straight pipe (1.0 m, 1.5 m), a three-way pipe, a right-angle pipe, an inclined pipe (10°, 20°), etc., which could be connected by rubber pads and screws. The total length was up to 50 m. The cross section of the pipeline component was square, and the inner space size was 300 mm × 300 mm.
- (4)
The dust removal system was mainly used to clean the coal particles not deposited in the pipeline during the experiment to avoid the air pollution. It was composed of a cylinder, a ventilation pipe, a pipe interface, a ladder, a cleaning door, and other components. A sensor hole was designed over the cylinder to monitor the gas flow, concentration, and so on. The main structure was made of steel plate with a thickness of 8 mm. The corresponding dimensions were 3 m × 2 m × 4 m.
- (5)
The inflation system was mainly used for the gas inflation of the similar simulation experiment system of a coal and gas outburst. With a high-precision automatic control system, it could achieve automatic inflation, pressure regulation, monitoring and alarming, and so on.
- (6)
The data acquisition system was mainly composed of sensors, high-speed cameras, data acquisition cards, computers, regulated power supplies, transmitters, etc., which could automatically monitor and collect the changing processes of the gas pressure, temperature, gas concentration, and other parameters during the experiment.

3.2. Experimental Materials
In order to produce a high similarity simulation inversion of on-site outburst accidents, the production of similar coal materials is crucial. The specialty of similar materials determines the accuracy of similar models. The mechanical properties of coal have a significant influence on the occurrence and development of a coal and gas outburst [24, 25]. Based on the existing similar materials, cement was selected as the cementing agent, crushed coal was selected as the aggregate, and sand, activated carbon, and water were selected as auxiliary materials for this similar simulation experiment [26]. The specific properties are shown in Table 1.
Category | Material | Size fraction | Remarks |
---|---|---|---|
Grouting agent | Cement | 425# ordinary Portland cement | — |
Skeletal material | Crushed coal | 80∼40 mesh, 40∼20 mesh | Outburst coal seam |
Auxiliary material | Sand | 40∼20 mesh | River sand |
Activated carbon | Φ2.6 mm × 5.6 mm | Granule | |
Water | — | Ordinary tap water |
With consideration of the abovementioned raw materials, similar materials were produced by cold press molding. The pressing molding pressure was 25 MPa, the voltage stabilization time was 30 min, and the curing time was 30 days. Cement accounted for 7%, sand accounted for 5.5%, water accounted for 8.5%, activated carbon accounted for 0.84%, and coal accounted for 78.16% of the similar materials. The uniaxial compressive strength was 1.25 MPa, the coefficient of firmness was 0.343, the modulus of elasticity was 158.68 MPa, the density was 1.40 g/m3, and the porosity was 5.36%. The adsorption constant a was 33.98 and the constant b was 1.63.
Because gas has a danger of explosion, nonexplosive gases such as CO2 and N2 are often used as the experimental gases for outburst simulation experiments with large similar models. Considering the large geometric size of the similar model and the large amount of gas dispersion, to avoid the explosion risk of the experimental gas and to compensate for the adsorption property being reduced by nonabsorbing raw materials mixed into the similar materials, CO2 was selected as the experimental gas for the planned coal and gas outburst simulation experiment.
3.3. Experimental Scheme
- (1)
Model production: According to the similar material ratio plan determined above, the model size was 1.5 m × 0.8 m × 0.8 m and the gas pressure and stress sensors were arranged inside, as shown in Figure 4. Each sensor had to be calibrated, and the sensor test was maintained in the process of model pressing to ensure the reliability of the monitoring of each sensor.
- (2)
Air displacement: In this experiment, CO2 was used as the experimental gas. Before the experiment, the air outlet top at the sealed box was opened and filled with 0.2 MPa CO2 to displace the air.
- (3)
Stress loading: After the displacement, the initial lateral and axial stresses were applied to the model based on the prototype conditions and the similarity ratio design. The axial pressure was 16 MPa, the lateral pressure was 3 MPa, and the gas pressure was 0.5 MPa.
- (4)
Inflation adsorption: The air outlet was closed, the box and the balance chamber of the venting device were synchronously inflated, and the pressure on both sides of the rupture disc was kept less than 0.4 MPa. The device was kept in this state for a certain period of time (15 days in this experiment) to ensure that the filled gas essentially achieved adsorption equilibrium.
- (5)
Outburst excitation and data acquisition: After basic adsorption equilibrium, the balance chamber of the venting device was filled with the overpressure gas at a pressure higher than 0.4 MPa to trigger the occurrence of an outburst. The data inside the similar materials and the roadway were monitored in real time using the stress loading, and high-speed acquisition was started in the outburst excitation. After the outburst, presentational features like the distribution of coal powders in the roadway and the shape of the outburst hole were recorded so that the data could be statistically analyzed later.
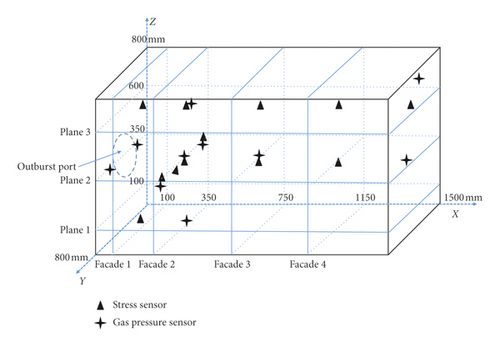
4. Results and Discussion
4.1. Variation Characteristics of the Gas Pressure
The arrangement of the gas pressure sensors and the gas pressure change curve are shown in Figure 5. Figure 5(b) shows the gas pressure change of sensor P09. It can be seen from Figure 5(b) that the outburst occurred at 30.4 s. As the gas inside the coal flooded out, the gas pressure near the outburst mouth rapidly dropped to zero, and the whole process lasted only 1.5 s. Figure 5(c) shows the gas pressure change of sensor P01, which was 10 cm below the outburst hole in the model. The whole process showed the rule of “the gas pressure slowly drops to a stable pressure (far higher than the atmospheric pressure of 0.1 MPa) after outburst excitation ⟶ the gas pressure keeps stable changing ⟶ the gas desorbs slowly.” This was due to the change in the stress of the coal body in the section of the outburst port after the opening of the outburst port, resulting in instability inside the coal body. Then, under the combined action of the gas internal energy, the elastic energy of the coal body, and the self-gravity potential energy of the unstable coal body, the unstable coal body was thrown out and the initial outburst hole was formed. This led that the pressure of position P9 rapidly dropped to zero. With the sudden exposure of the coal near the outburst hole, a large pressure gradient of position P1 occurred inside and outside the coal wall, and it slowly dropped to a stable pressure. As the coal gas around the hole continued to desorb, the pressure of the position P1 remained at a steady level. However, as the surrounding coal body was continuously thrown and the amount of desorption was continuously reduced, the pressure of the position P1 gradually decreased and gradually dropped to atmospheric pressure.
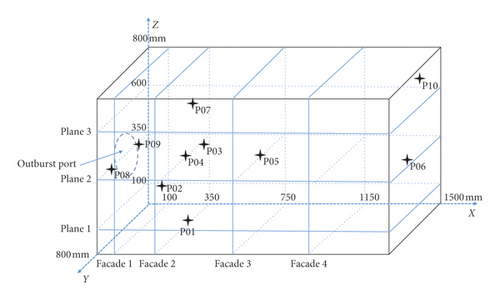
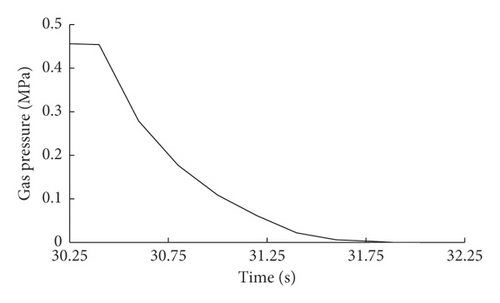
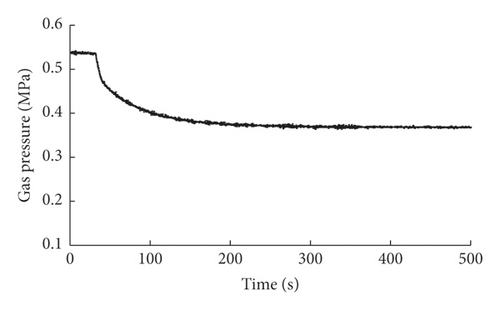
4.2. Variation Characteristics of Stress
The arrangement of the stress sensors and the stress changes during the outburst process are shown in Figure 6, in which F12 is the horizontal stress. It can be seen from Figure 6 that according to the stress sensors (F3, F5, and F6), on the same plane, the stress loading state at t = 0 s was F3 = 10.6 MPa, F5 = 16 MPa, and F6 = 13.9 MPa. This explains the fact that the stress along the outburst mouth to the inside (along the X-axis direction) before outburst showed a “low-high-low” pattern in distribution, which was consistent with the stress distribution rule in front of the mining work face.
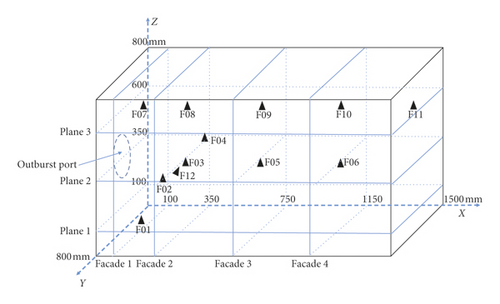

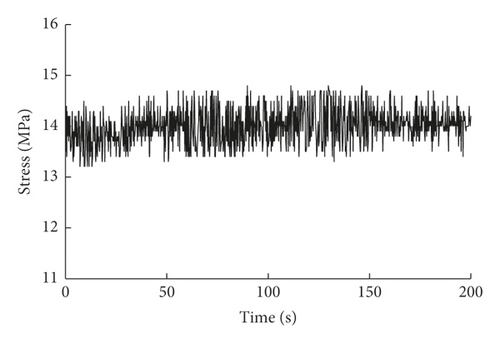
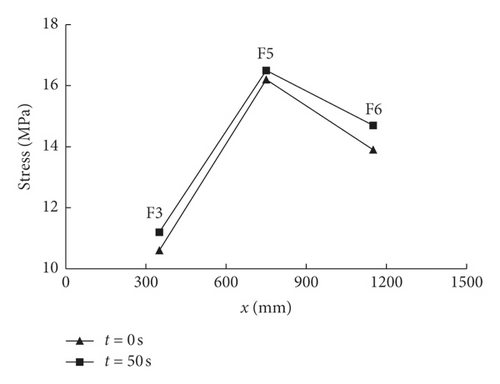
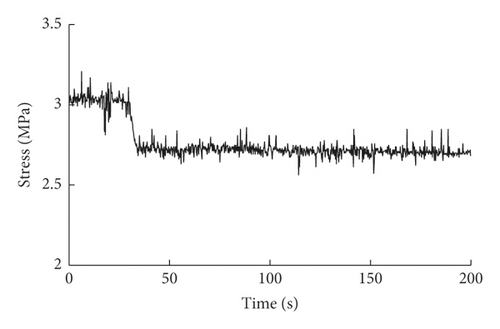
After the outburst excitation, the stress changes at different locations of the model were different. It can be seen from Figure 6 that the horizontal stress (sensor F12) of the outburst hole slowly decreased at first and then unload gradually 20 s–30 s after the excitation, while the stress at sensor F5 increased, and the stress at sensor F6 essentially had no change. When t = 50 s, the sensors show that F3 = 11.2 MPa, F5 = 16.5 MPa, and F6 = 14.7 MPa. The stress of sensor F5 increased by 3.13% compared with that at t = 0 s. This was because the mining work destroyed the original stress balance during the birth stage of the coal and gas outburst. This resulted in the load originally borne by the coal and rock mass in the mining space transferring to the surrounding mass, causing the stress redistribution to form a distressed zone, a concentrated stress zone, and an original stress zone. Therefore, the experimental rules achieved this time were correct.
4.3. Distribution of Outburst Holes and Coal Powders
The holes before and after the outburst are shown in Figure 7. The hole after the outburst was approximately 15 cm in depth and at most 30 cm in width at the mouth. It was similar to an irregular semiellipsoid in shape. The upper part of the coal wall in the hole had obviously broken in layers, most of the outburst coal sample was in the form of sheet, and the piling height could account for more than 2/3 of the hole diameter.
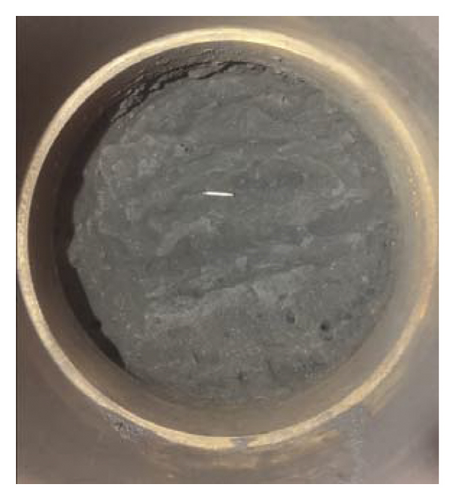
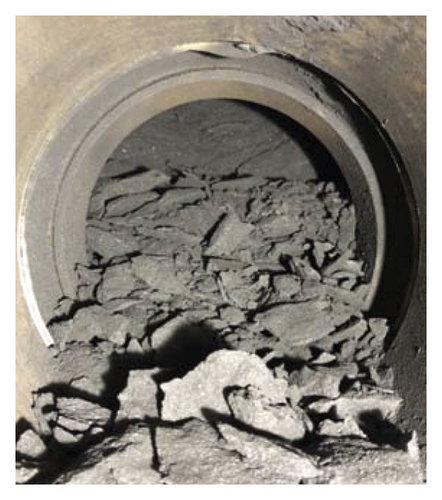
During the outburst process, the crushed coal moved, and it was deposited in the roadway under the action of the gas, which reflected the intensity to some extent, as shown in Figure 8. After the experiment, the coal powders were divided into five areas according to the distance from the outburst mouth, sampled, weighed, and sieved. The results are shown in Table 2.
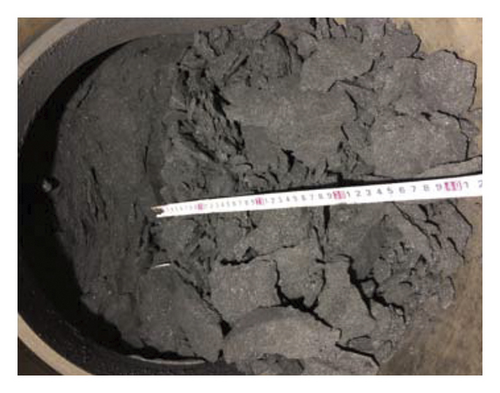
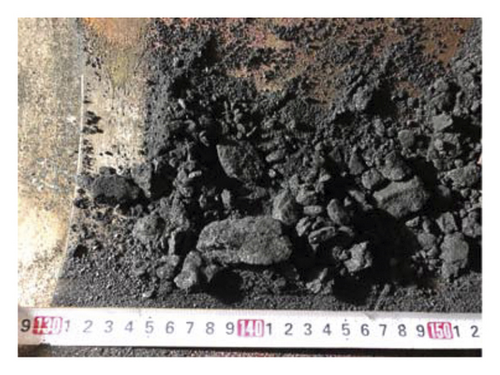
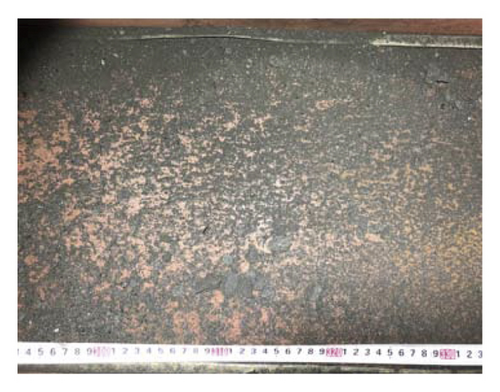
Particle size | Distance from the outburst hole | Total | ||||
---|---|---|---|---|---|---|
0∼0.15 m | 0.15∼0.6 m | 0.6∼1.3 m | 1.3∼1.8 m | 1.8∼3.3 m | ||
>10 cm | 1.500 | 0 | 0 | 0 | 0 | 1.500 |
5∼10 cm | 1.724 | 0.700 | 1.400 | 0 | 0 | 3.824 |
3∼5 cm | 0.626 | 0.621 | 0.628 | 0.678 | 0 | 2.553 |
9 mm∼3 cm | 0.665 | 1.565 | 1.065 | 0.565 | 0.135 | 3.995 |
3 mm∼9 mm | 0.168 | 0.731 | 0.508 | 0.294 | 0.062 | 1.763 |
1 mm∼3 mm | 0.087 | 0.580 | 0.270 | 0.171 | 0.037 | 1.145 |
0.25∼1 mm | 0.119 | 0.809 | 0.414 | 0.264 | 0.053 | 1.659 |
0.2∼0.25 mm | 0.026 | 0.257 | 0.119 | 0.090 | 0.015 | 0.507 |
<0.2 mm | 0.074 | 0.501 | 0.303 | 0.221 | 0.049 | 1.148 |
Total | 4.989 | 5.764 | 4.707 | 2.283 | 0.351 | 18.094 |
- (1)
In this experiment, there was a total 18.094 kg outburst coal sample, the relative outburst intensity was 1.21%, and the farthest distance was 3.3 m from the outburst hole.
- (2)
The outburst coal sample tended to decrease in distribution along the roadway. There was more coal within the range of 0.6 m from the wall of the outburst hole, accounting for 59.4% of the total outburst coal. Coal samples larger than 9 mm accounted for more than 80% of the hole (0 m–0.15 m). However, the distribution rules of the coal sample grain size were almost consistent in other areas. The proportion of coal sample grain size in each area first decreased and then increased with the decrease of grain size.
- (3)
After the outburst, the ratio of the mass of the coal samples with grain sizes of less than 0.2 mm to the mass of the total coal sample was as follows: 1.148/18.094 = 6.34%.
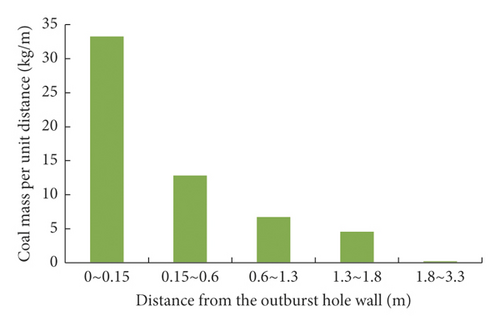
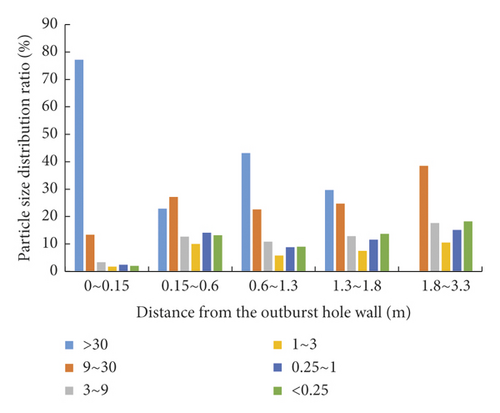
4.4. Energy Quantization Calculation
According to the above experimental analysis results, the outburst coal density of this simulation experiment was 1.40 kg/m3, the elastic modulus was 158.68 MPa, Poisson’s ratio was 0.25, the outburst intensity was 18.094 kg, the ground stress loading was 16 MPa, the f value was 0.343, ΔP was 30 ml/s, the outburst adsorption equilibrium pressure was 0.5 MPa, and the percentage of the coal samples with grain sizes of less than 0.2 mm after crushing compared to the mass of the total coal sample was 6.34%.
- (1)
In this process of the coal and gas outburst, the elastic potential energy of the coal was 0.0156 kJ, accounting for 0.34% of the total energy, while the gas internal energy was 4.5533 kJ, accounting for 99.66% of the total energy. This shows that gas internal energy was the most important energy source for the coal and gas outburst, two orders of magnitude more than the elastic potential energy of the coal, and it played a leading role in the outburst process.
- (2)
In this process of the coal and gas outburst, the coal crushing work was 4.0528 kJ and the throwing work was 0.1921 kJ, indicating that most of the energy was consumed in coal crushing after the outburst. The coal crushing work had the same order of magnitude as the gas internal energy.
- (3)
The sum of the elastic potential energy and the gas internal energy was 4.5689 kJ, which was greater than the sum of the coal crushing work and the throwing work of 4.2449 kJ, showing a difference of 0.324 kJ. This was mainly because there were losses of energy such as frictional heat, vibration, and sound during the throwing process after the outburst. In this outburst process, the losses of energy such as frictional heat, vibration, and sound accounted for only 7.09% of the total energy, which was consistent with the conclusion that “this part of energy is basically determined and finite, usually no more than 10% of the total energy” according to the literature [12].
5. Conclusion
- (1)
In the process of the coal and gas outburst, the main energy source existed in the form of coal elastic potential energy and coal gas internal energy. The main energy loss existed in the form of coal crushing work and coal throwing work.
- (2)
The total mass of the outburst coal sample in the coal and gas outburst simulation experiment under the conditions of a ground stress of 16 MPa and a gas pressure of 0.5 MPa was 18.094 kg, the relative outburst intensity was 1.21%, and the furthest distance was 3.3 m from the wall of the outburst hole. The distribution of the coal sample along the roadway showed a downward trend, and the proportion of the coal sample grain sizes in each area first decreased and then increased with the decrease of the grain size. The mass of the crushed coal samples with a grain size less than 0.2 mm after the outburst accounted for 6.34% of the mass of the total coal samples.
- (3)
The main energy source in the outburst process—the coal elastic potential energy accounted for 0.34% of the total outburst energy, and the gas internal energy accounted for 99.66% of the total outburst energy. It was verified that gas internal energy was the most important energy source for the coal and gas outburst, two orders of magnitude higher than the coal elastic potential energy, playing a leading role in the outburst process. After the outburst, most of the energy was consumed in the coal crushing process, and the crushing work had the same order of magnitude as the gas internal energy. In addition, the losses of energy such as frictional heat, vibration, and sound during the outburst process only accounted for 7.09% of the total energy, within 10% of the total energy.
Disclosure
The authors would like to declare on behalf of their coauthors that the work described was original research that has not been published previously, and not under consideration for publication elsewhere, in whole or in part. All the authors listed have approved the manuscript that is enclosed. Meanwhile, the founding sponsors had no role in the design of the study; in the collection, analyses, or interpretation of data; in the writing of the manuscript; and in the decision to publish the results.
Conflicts of Interest
The authors declare no conflicts of interest, and the manuscript is approved by all authors for publication.
Acknowledgments
This study was financially supported by National Natural Science Foundation of China (51874348, 51574280, 51604298, and 51774319), Science and Technology Innovation and Entrepreneurship Fund of China Coal Technology Engineering Group (2019-TD-QN037 and 2019-TD-QN040), National Key Research and Development Program (2016YFC0801402-4).
Open Research
Data Availability
The data used to support the findings of this study are available from the corresponding author upon request.