Commercial Vehicle Ride Comfort Optimization Based on Intelligent Algorithms and Nonlinear Damping
Abstract
The method chosen to conduct vehicle dynamic modeling has a significant impact on the evaluation and optimization of ride comfort. This paper summarizes the current modeling methods of ride comfort and their limitations. Then, models based on nonlinear damping and equivalent damping and the multibody dynamic model are developed and simulated in Matlab/Simulink and Adams/Car. The driver seat responses from these models are compared, showing that the accuracy of the ride comfort model based on nonlinear damping is higher than the one based on equivalent damping. To improve the reliability of ride comfort optimization and analysis, a ride comfort optimization method based on nonlinear damping and intelligent algorithms is proposed. The sum of the frequency-weighted RMS of the driver seat acceleration, the RMS of dynamic tyre load, and suspension working space is taken as the objective function in this article, using nonlinear damping coefficients and stiffness of suspension as design variables. By applying the particle swarm optimization (PSO), cuckoo search (CS), dividing rectangles (DIRECT), and genetic algorithm (GA), a set of optimal solutions are obtained. The method efficiency is verified through a comparison between frequency-weighted RMS before and after optimization. Results show that the frequency-weighted RMS of driver seat acceleration, RMS values of the suspension working space of the front and rear axles, and RMS values of the dynamic tyre load of front and rear wheels are decreased by an average of 27.4%, 21.6%, 25.0%, 19.3%, and 22.3%, respectively. The developed model is studied in a pilot commercial vehicle, and the results show that the optimization method proposed in this paper is more practical and features improvement over previous models.
1. Introduction
Commercial vehicles are an essential part of the modern transport network and are responsible for the bulk of freight transport around the world. The demand for better ride comfort and safety in these vehicles is increasing, as such commercial vehicle ride comfort optimization has been an active area of research. Ride comfort in commercial vehicles provides the following advantages: (1) increased driver’s comfort and driving safety, ensuring good ride ability, and reducing the incidence of traffic accidents; (2) assurance goods arrive in better condition, increasing the utility value of commercial vehicles; and (3) improved service life of commercial vehicle parts, as vehicles are subjected to reduced impact and vibration forces constantly [1–4].
Typically, software used for vehicle ride comfort simulation includes Adams and Matlab. The former adopts the structure-oriented modeling method, which is more accurate, and the simulation is reliable. However, the modeling procedures need to set characteristic parameters and curves for a large number of parts, resulting in a complex and time-consuming modeling solution. The latter establishes a ride comfort model from the perspective of mechanics and mathematics with lower accuracy but simpler modeling, a shorter simulation time, and convenient parameter setting and adjustment, with a powerful ability to perform algorithm-based optimization.
Many studies have been devoted to vibration control and ride comfort optimization of vehicles. Ding et al. [5] established an eleven degree-of-freedom (DOF) ride comfort model for a three-axle truck that assumes the body is slightly vibrating near the equilibrium position. Li et al. [6] studied the synthetic mechanical model of plane rigid-frame heavy-duty vehicles, considering only the microvibrations caused by road excitation. A dynamic model is developed that aims to reduce the road excitation transmitted to the vehicle body and improve the ride comfort by using optimization algorithms. The spring stiffness and damping coefficient are regarded as a fixed value [7–9]. The ride model is used to study the relationship between ride comfort and the in-wheel motor. There is a linear relationship between damping and damping force [10, 11]. Zhu et al. [12] established a ten-DOF ride model for analyzing vehicle ride comfort and driving safety, and the damping force is considered a linear parameter in this analysis.
Most of the research on simulation and optimization for vehicle ride comfort make the following assumptions on the actual situation: (1) the microvibration caused by road excitation is only considered and (2) the damping force is a linear function of its velocity and is regarded a constant value (equivalent damping). The research on ride comfort mainly focuses on equivalent damping when the model consists of passive suspension, with work based on nonlinear damping poorly established. However, in terms of the analysis for the ride comfort of commercial vehicles, the above assumptions are different from the actual situation. Commercial vehicle suspension damping is mostly a nonlinear damping curve that varies with extension or compression velocity. In addition, the driving conditions of commercial vehicles is far from ideal, with additional factors contributing to this, which goes against the assumption that only microvibration should be considered. Furthermore, this work is mainly focused on ride comfort and disregards the suspension working space and dynamic tyre load, which affect handling stability. The reduction of suspension stiffness has a negative effect on the suspension working space and dynamic tyre load.
In this paper, the ride comfort models of a commercial vehicle based on nonlinear damping and equivalent damping are developed. The responses of theoretical models are verified by simulation performed in Adams/Car on a multibody dynamic model of the target vehicle. To improve ride comfort, more performance criteria are considered and optimized. To achieve this, a ride comfort optimization method based on nonlinear damping of suspension and intelligent algorithms is proposed. The objective functions are optimized by algorithms, and the optimal design variables that consider nonlinear damping are obtained. Lastly, the theoretical model and optimization are validated by experiment. In short, the method is more practical and accurate for vehicle ride comfort optimization compared to those based on equivalent damping.
2. Ride Comfort Model
In this section, the equations are serially developed for the vibration system, road excitation model, nonlinear damping, and equivalent damping model. The effectiveness of the ride comfort model using nonlinear damping is demonstrated and compared with equivalent damping and multibody dynamic models.
2.1. Vibration Model
Generally, there are three types of vehicle ride comfort models, including the 1/4 vehicle model, half vehicle model, and full vehicle model. When a vehicle is symmetrical to its longitudinal axis, the main vibrations affecting ride comfort are vertical vibration along the z-axis and pitch vibration around the y-axis of the vehicle coordinate system. Therefore, a half commercial vehicle model that consists of five basic subsystems of the tires, suspension systems, frame, cab, and seat is selected in this paper, as shown in Figure 1. For this model, the vibration differential equation (1) is generated by using Newton’s second law of motion:where xf and xr are the displacement along the z-axis of the front wheel and the rear wheel, respectively; xfu, xru, xb, xc, and xp represent the displacement of the front axle unsprung mass, rear axle unsprung mass, sprung mass, mass of cab, and mass of the seat, respectively; θc, θb, and θ are the pitch angle displacements of the cab, sprung mass, and rear axle balance suspension around the y-axis, respectively. Moreover, the fixed parameters are presented in Table 1, and the nonlinear damping curves are shown in Figure 2(b).
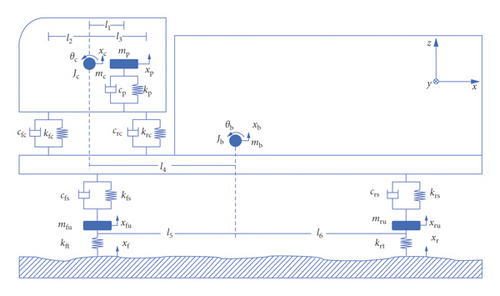
Symbol | Description | Value | Unit |
---|---|---|---|
mp | Driver and seat mass | 100 | kg |
mc | Cab mass | 850 | kg |
mb | Sprung mass | 14238 | kg |
mfu | Unsprung mass of front axle | 607 | kg |
mru | Unsprung mass of rear axle | 1054 | kg |
Jc | Rotational inertia of cab mass around y-axis | 560 | kg·m2 |
Jb | Rotational inertia of sprung mass around y-axis | 115000 | kg·m2 |
J | Rotational inertia of rear axle balance suspension mass around y-axis | 615 | kg·m2 |
kp | Seat stiffness | 20000 | N/m |
kfc | Front suspended stiffness | 25000 | N/m |
krc | Rear suspended stiffness | 25000 | N/m |
kfs | Front suspension stiffness | 410000 | N/m |
krs | Rear suspension stiffness | 1476000 | N/m |
kft | Front wheel stiffness | 1800000 | N/m |
krt | Rear wheel stiffness | 3600000 | N/m |
cp | Equivalent damping coefficient of driver seat | 800 | N·s/m |
cfs | Equivalent damping coefficient of front suspended | 5000 | N·s/m |
crs | Equivalent damping coefficient of rear suspended | 5000 | N·s/m |
cft | Equivalent damping coefficient of front suspension | 12000 | N·s/m |
crt | Equivalent damping coefficient of rear suspension | 15000 | N·s/m |
l1 | Distance between the center and seat of the cab | 0.2 | m |
l2 | Distance between front suspended and the center of the cab | 0.76 | m |
l3 | Distance between rear suspended and the center of the cab | 0.87 | m |
l4 | Distance between the center of the cab and the center of target commercial vehicle | 2.47 | m |
l5 | Distance between the front suspension and the center of target commercial vehicle | 2.1 | m |
l6 | Distance between the rear suspension and the center of target commercial vehicle | 3 | m |
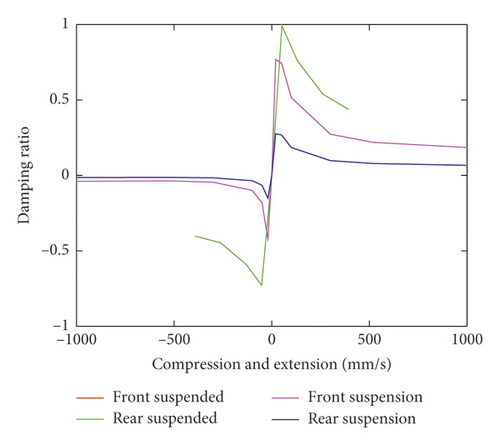
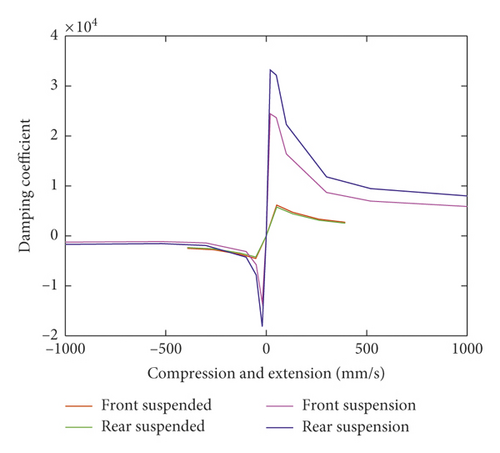
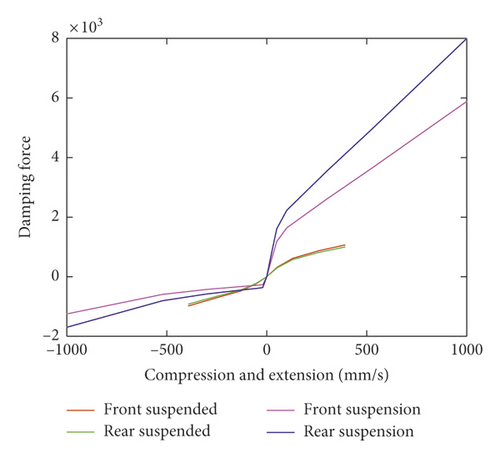
2.2. Road Excitation Model
Figure 3 shows a road profile when the vehicle travels on the C-level road at 60 km/h. The profile PSD and standard road PSD according to ISO 8608 are presented in Figure 4 and show that a simulation model of road excitation is feasible.
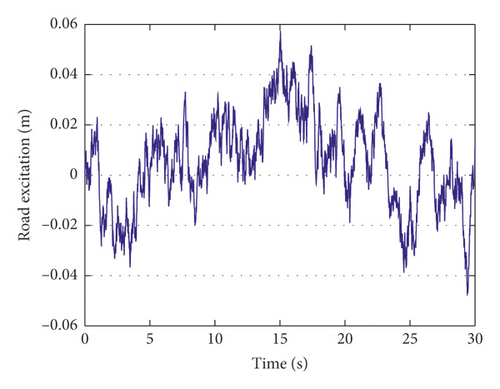
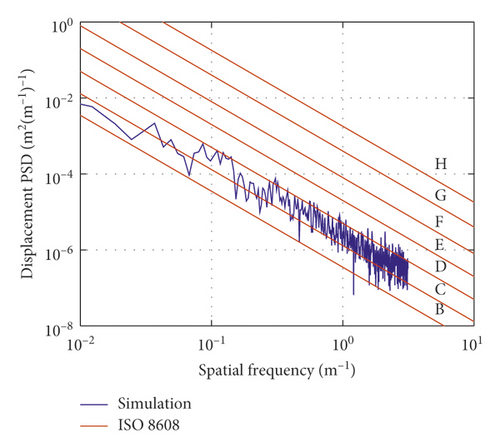
2.3. Nonlinear Damping Model
2.4. Equivalent Damping Model
2.5. Verification of Ride Comfort Model
Equations (1), (3), and (5) have been solved using Matlab/Simulink and validated through a multibody dynamic model in Adams/Car. The multibody dynamic model is shown in Figure 5. The response of the driver seat, obtained from the Simulink models based on nonlinear damping, equivalent damping, and multibody dynamics model, is compared through time-domain curves and frequency-weighted RMS to verify the accuracy of the nonlinear damping ride model.
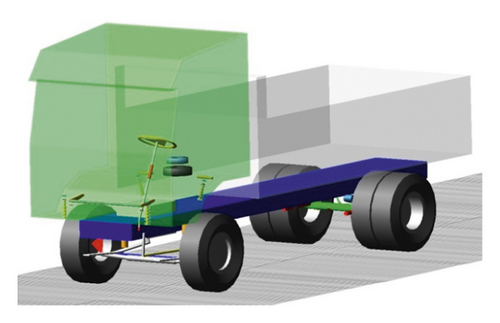
The time-domain curves are shown in Figure 6. Overall, the Matlab-based model has the same level of acceleration amplitude as the Adams-based model. The acceleration amplitude of the model based on nonlinear damping is greater than the one based on equivalent damping, leading to a higher frequency-weighted RMS, and the situation is consistent with the RMS in Figure 7. The difference in the curves is typically caused by the different methods of road modeling in Adams and Matlab and the bushings in the Adams model.

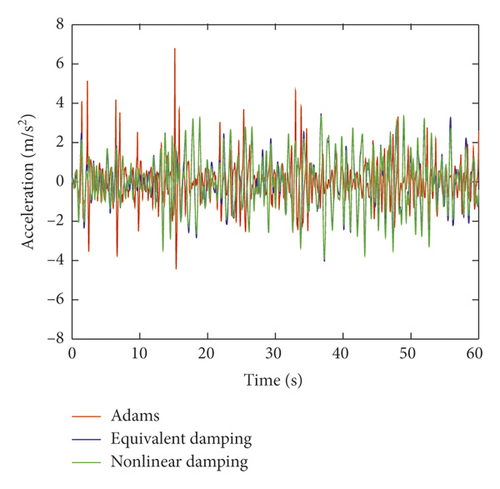
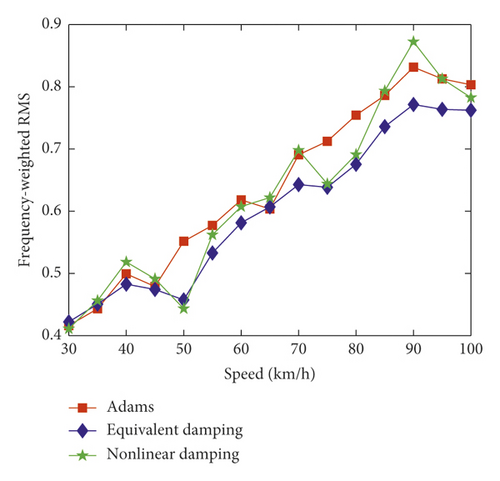
As shown in Figure 7, there is a similar tendency that ride comfort increases with speed among the three models. The results show that simulation results of the model based on the nonlinear damping are more consistent with the Adams model than the model based on equivalent damping. Therefore, the ride comfort model based on nonlinear damping has improved accuracy compared to equivalent damping models.
3. Multiobjective Optimization
In this section, the optimization of suspension systems based on nonlinear damping is presented. The efficiency and robustness of the optimization method affect the results. PSO, CS, DIRECT, and GA are chosen as the optimization methods to optimize performance with respect to comfort, dynamic tyre load, and suspension working space.
3.1. Intelligent Algorithms
3.1.1. Particle Swarm Optimization
3.1.2. Cuckoo Search
- (1)
Each cuckoo has only one egg and selects the nest position randomly
- (2)
The best nests with high-quality eggs will be carried to the next generation
- (3)
The host nest number is constant during iteration, and the probability of the host finding eggs is pa ∈ [0, 1]
3.1.3. Dividing Rectangles
The DIRECT algorithm is composed of potentially optimal hyper-rectangles and the dividing strategy for hypercubes [19].
Then, si is the new center of a hyper-rectangle with the smallest function value. This pattern is repeated for all dimensions on the center of the hyper-rectangle, choosing the next dimension by determining the next smallest si [20].
3.1.4. Genetic Algorithm
The GA is an optimization method based on the principles of natural genetics and natural selection. The basic elements of GA are performed by three operations as reproduction, crossover, and mutation. Solutions are evaluated with respect to their fitness value that indicates how well the individual will solve the problem [21].
3.2. Objectives
3.2.1. Ride Comfort
3.2.2. Dynamic Tyre Load
3.2.3. Suspension Working Space
3.3. Design Variables
The range of variables should not be too large or too small. When the variation ranges are too large, other performances of the vehicle may be drastically reduced after optimization, and the matching and installation of the entire vehicle will be affected. In contrast, the effect of optimization is not obvious. Therefore, variables are altered up and down by 10% as the optimization interval, and the bounds are defined in Table 2.
Variables | Original | Lower | Upper |
---|---|---|---|
kfs (N/m) | 410000 | 369000 | 451000 |
krs (N/m) | 1476000 | 1328400 | 1623600 |
cf1 | 36.54 | 32.886 | 40.194 |
cf2 | 1.487 | 1.338 | 1.636 |
cf3 | 0.5996 | 0.540 | 0.660 |
cr1 | 49.66 | 44.694 | 54.626 |
cr2 | 1.487 | 1.338 | 1.636 |
cr3 | 0.5996 | 0.540 | 0.660 |
3.4. Constraints
3.5. Nonlinear Ride Optimization Method
A ride potimization method based on nonlinear damping and intelligent lagorithms is presented, and the procedure is shown in Figure 8.
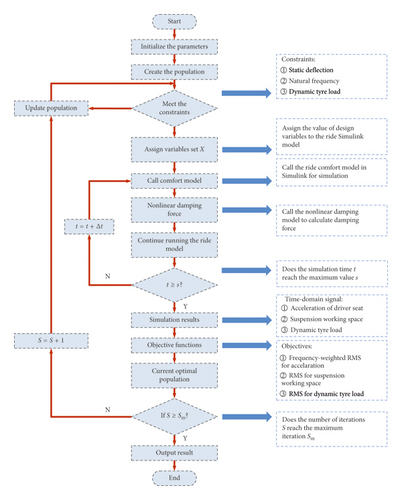
4. Optimization Results
In this section, the results of ride optimization are discussed. First, the iterations of algorithms are shown in Figure 9, and the optimal design variables are listed in Table 3. The responses, which represent the time-domain signals of objective functions based on original design variables and optimized ones, are shown in Figure 9. The indexes for objectives are calculated and presented in Table 4.
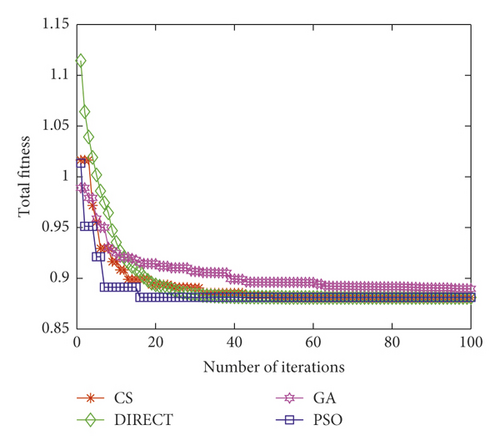
Variables | kfs (N/m) | krs (N/m) | cf1 | cf2 | cf3 | cr1 | cr2 | cr3 |
---|---|---|---|---|---|---|---|---|
Original | 410000 | 1476000 | 36.54 | 1.487 | 0.5996 | 49.66 | 1.487 | 0.5996 |
CS | 369000 | 1330000 | 40.18 | 1.635 | 0.6599 | 54.63 | 1.636 | 0.6600 |
DIRECT | 371000 | 1345000 | 40.06 | 1.631 | 0.6578 | 52.97 | 1.608 | 0.6578 |
GA | 381000 | 1340000 | 40.19 | 1.636 | 0.6600 | 54.62 | 1.636 | 0.6600 |
PSO | 369000 | 1328000 | 40.19 | 1.636 | 0.6600 | 54.63 | 1.636 | 0.6600 |
Speed (km/h) | 30 | 40 | 50 | 60 | 70 | 80 | 90 | 100 | |
---|---|---|---|---|---|---|---|---|---|
f1 | Original | 0.4107 | 0.5190 | 0.4430 | 0.6077 | 0.6988 | 0.6914 | 0.8738 | 0.7832 |
Optimized | 0.3067 | 0.3531 | 0.3527 | 0.4318 | 0.4742 | 0.5284 | 0.5786 | 0.6012 | |
Fall ratio (%) | 25.3 | 32.0 | 20.4 | 28.9 | 32.1 | 23.6 | 33.8 | 23.3 | |
Average (%) | 27.4 | ||||||||
f2 | Original | 0.2442 | 0.2903 | 0.3118 | 0.3740 | 0.4085 | 0.4042 | 0.4731 | 0.4755 |
Optimized | 0.1922 | 0.2263 | 0.2557 | 0.2908 | 0.3122 | 0.3275 | 0.3584 | 0.3701 | |
Fall ratio (%) | 21.3 | 22.0 | 18.0 | 22.2 | 23.6 | 19.0 | 24.2 | 22.2 | |
Average (%) | 21.6 | ||||||||
f3 | Original | 0.1413 | 0.1672 | 0.2050 | 0.2405 | 0.2577 | 0.2674 | 0.3045 | 0.3021 |
Optimized | 0.1075 | 0.1314 | 0.1567 | 0.1756 | 0.1875 | 0.2014 | 0.2196 | 0.2282 | |
Fall ratio (%) | 23.9 | 21.4 | 23.6 | 27.0 | 27.2 | 24.7 | 27.9 | 24.5 | |
Average (%) | 25.0 | ||||||||
f4 | Original | 0.0142 | 0.0166 | 0.0171 | 0.0215 | 0.0233 | 0.0218 | 0.0271 | 0.0261 |
Optimized | 0.0113 | 0.0132 | 0.0148 | 0.0172 | 0.0183 | 0.0186 | 0.0207 | 0.0209 | |
Fall ratio (%) | 20.4 | 20.5 | 13.5 | 20.0 | 21.5 | 14.7 | 23.6 | 19.9 | |
Average (%) | 19.3 | ||||||||
f5 | Original | 0.0086 | 0.0101 | 0.0125 | 0.0150 | 0.0159 | 0.0161 | 0.0188 | 0.0183 |
Optimized | 0.0068 | 0.0082 | 0.0099 | 0.0114 | 0.0119 | 0.0127 | 0.0139 | 0.0144 | |
Fall ratio (%) | 20.9 | 18.8 | 20.8 | 24.0 | 25.2 | 21.1 | 26.1 | 21.3 | |
Average (%) | 22.3 |
The iterations of ride comfort optimization are shown in Figure 9. Obviously, the CS, DIRECT, and PSO get the similar and ideal results besides GA, and the iteration of PSO is better than others, which is usually caused by the following reasons: (1) different algorithms have different characteristic for various problems and (2) the generation of individuals and population is random during the optimization processing. Consequently, it is necessary to compare the results among different algorithms that can ensure a relatively better result. Then, we listed the original variables and optimized ones in Table 3.
To verify the feasibility and effectiveness of the ride comfort optimization method, nonlinear damping based on intelligent algorithms is proposed in this paper. A comparative analysis of ride comfort based on the original and optimized design variables is performed. Design variables are substituted into the ride comfort model based on nonlinear damping. Then, the optimized responses of the time history of the acceleration of driver seat, dynamic tyre load, and suspension working space at 40 km/h and 80 km/h are obtained. Data are presented in Figure 10 in comparison with the original response. The evaluation indexes for objective functions are calculated from 30 to 100 km/h and shown in Table 4 according to equations (15), (19), and (21)
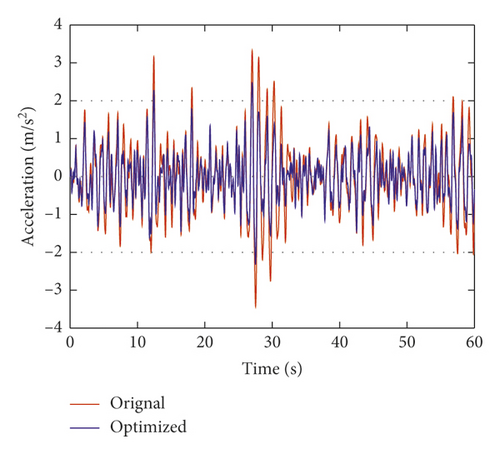
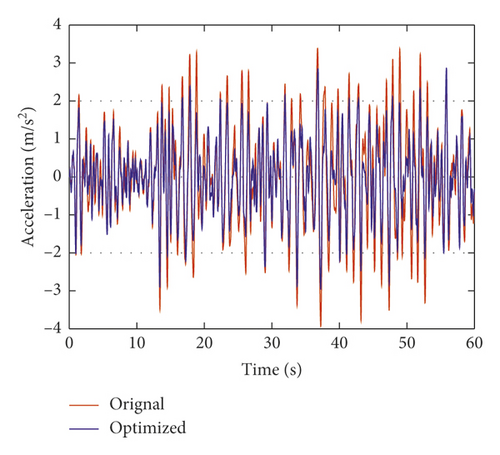
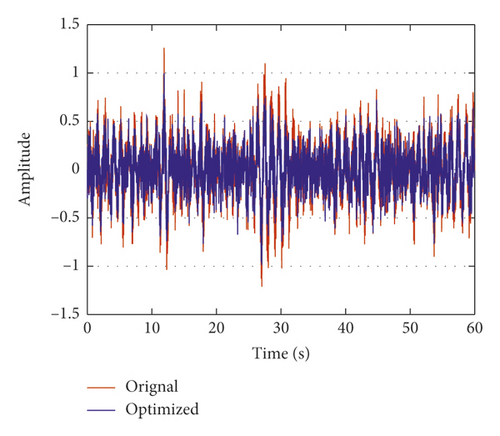
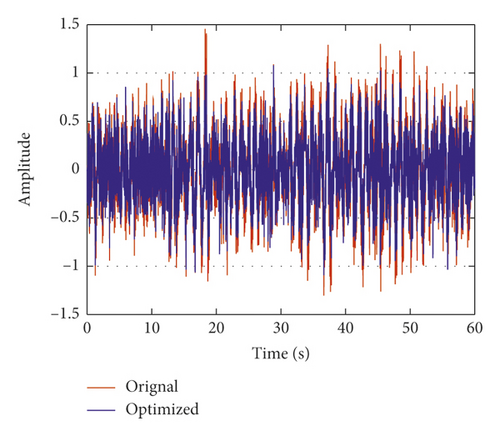
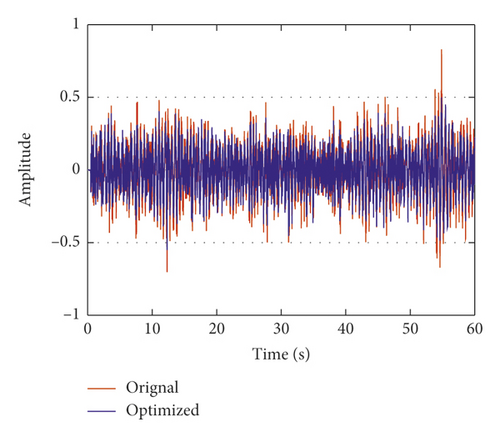
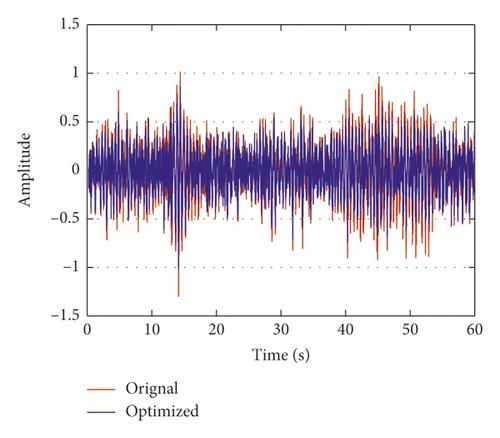
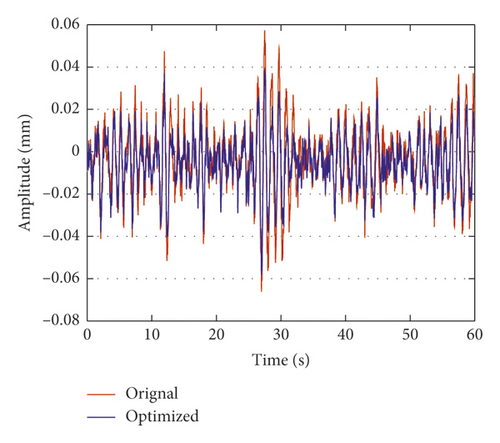
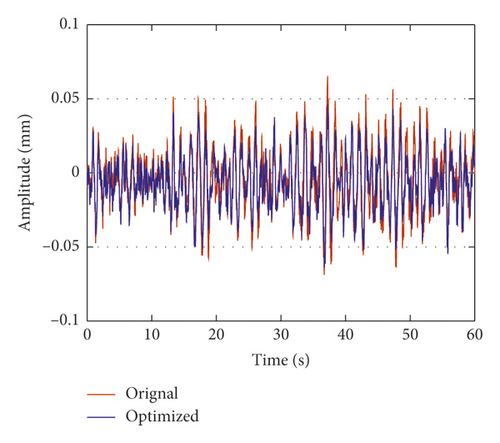
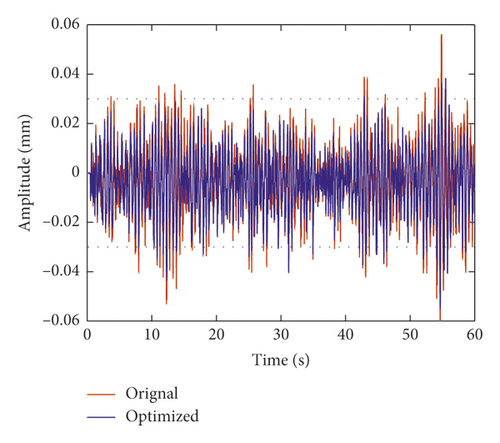
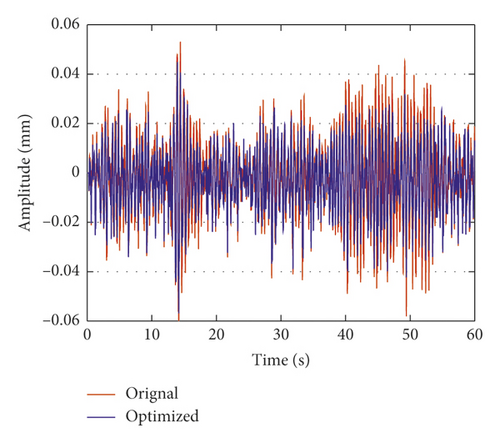
As shown in Table 4, the target commercial vehicle ride comfort is significantly improved after optimization. The proposed optimizer with intelligent algorithms and nonlinear damping successfully optimized the design variables with an average fall ratio of 27.4%, 21.6%, 25.0%, 19.3%, and 22.3% for f1, f2, f3, f4, and f5. Additionally, the evaluation indexes for objective increase with increased vehicle speed; that is, ride comfort deteriorates totally as speed increases.
5. Experiment
To further verify the feasibility and efficiency of the ride optimization method in this paper, the ride comfort experiment of target commercial vehicle traveling on the C-level road with 30–100 km/h was conducted in accordance with GB/T 4970-2009 “Method of running test—Automotive ride comfort.” The experimental vehicle is shown in Figure 11(a). A section of the cement road is selected as the ride comfort experiment road, and its surface is shown in Figure 11(b). The sensor is used to measure the vertical vibration acceleration of the seat. The installation position is shown in Figure 11(c). The CPCI signal acquisition instrument is used for data acquisition, as shown in Figure 11(d).
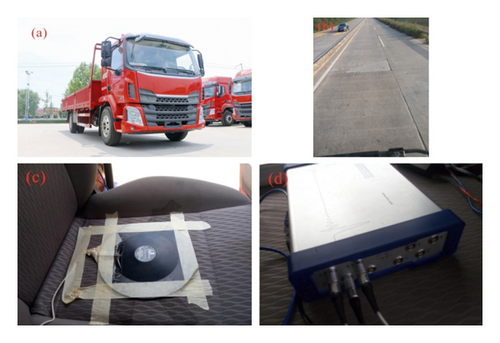
The ride comfort experiment test requirements are as follows: (1) The road surface is even and straight, and there is an acceleration section initially. (2) The target commercial vehicle is fully loaded with standard driving equipment. The components of the vehicle are in good condition, and the tyre pressure complies with regulations. (3) When the test truck speed reaches the speed to be analyzed, the tester starts timing for 60 s. (4) The speed of vehicle ride comfort experiment is 30–100 km/h, and the speed is increased by 5 km/h each test. The target commercial vehicle drives evenly at the specified speed during the experiment.
Figure 12 shows that the frequency-weighted RMS of optimized seat vibration acceleration is significantly lower than the original situation. The results in Figure 12 are similar to those in Figure 7, demonstrating that the ride comfort model based on nonlinear damping constructed in this paper is feasible and the optimization method is effective. In addition, the fluctuations of the experimental result after 70 km/h may be affected by engine vibration because of increased rotating speed.
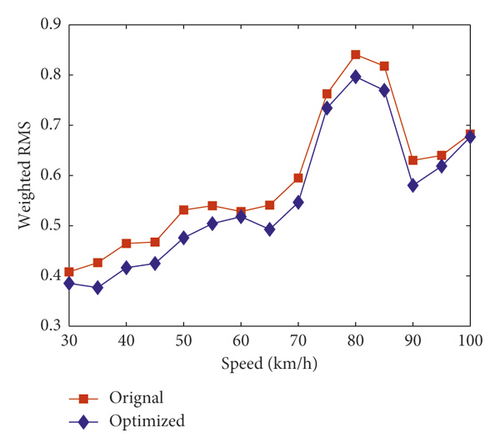
6. Conclusions
- (1)
The frequency-weighted RMS values of seat vibration acceleration based on models with nonlinear damping and equivalent damping are obtained and compared with the response of a multibody dynamic model. The result indicates that the ride comfort model based on nonlinear damping has higher accuracy than a model based on equivalent damping.
- (2)
The comparison of driver seat vibration acceleration and relevant responses before and after optimization is performed, and the evaluation indexes at different speeds are obtained. The frequency-weighted RMS of driver seat acceleration, RMS of suspension working space of front and rear axle, and RMS of dynamic tyre load of front and rear wheel are decreased by an average of 27.4%, 21.6%, 25.0%, 19.3%, and 22.3%, respectively, through the optimization. Thus, the ride comfort of the commercial vehicle is improved. In addition, the optimization method developed in this paper has theoretical and practical significance for similar problems.
Conflicts of Interest
The authors declare that there are no conflicts of interest regarding the publication of this paper.
Acknowledgments
This research was financially supported by the project of the National Natural Science Foundation of China (Grant no.51565008), the Innovation-Driven Development Special Fund Project of Guangxi (Grant nos. Guike AA18242033 and AA18242036), the Scientific Research and Technology Development in Liuzhou (Grant no. 2016B020203), the Basic Ability Promotion Project for Young and Middle-Aged Teachers in Guangxi Province (Grant nos. 2017KY0869 and 2018KY0205), the Innovation Project of GUET Graduate Education (Grant no. 2019YCXS001), and the GUET Excellent Graduate Thesis Program (Grant no. 17YJPYSS02).
Appendix
Simulink Model
The relatedly Simulink models developed in the paper are illustrated in Figures (13–15).
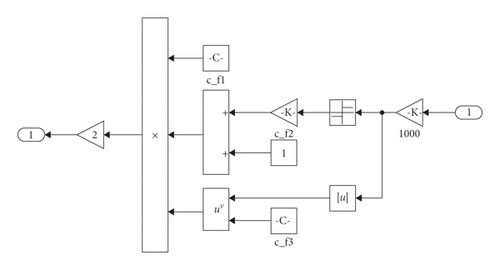
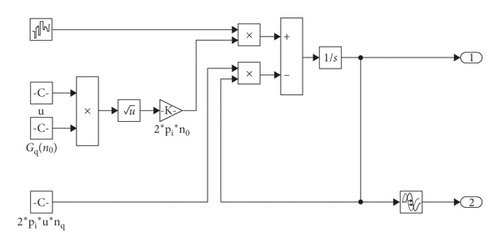
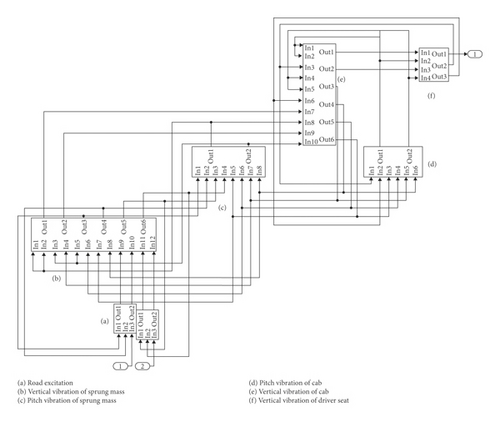
Open Research
Data Availability
The data used to support the findings of this study are available from the corresponding author upon request.