Efficient Passive Cooling for Photovoltaic Cells via Self-Hygroscopic Polyvinyl Alcohol/Graphene Films
ABSTRACT
Photovoltaic (PV) technology plays a pivotal role in energy transformation processes, especially for sustainable energy systems. However, the conversion efficiency of the PV cells is adversely affected by increasing temperature, leading to a reduction in their overall performance. In this study, a self-hygroscopic polyvinyl alcohol/graphene (SPG) cooling film, comprising a graphene layer and a polyvinyl alcohol (PVA) hydrogel layer with lithium bromide (LiBr), is introduced to passively reduce the working temperature of the PV cells. The graphene layer, as a heat-conducting layer, can efficiently conduct heat from the heat source to the self-hygroscopic PVA hydrogel layer used as an evaporation cooling layer. In addition, the introduction of LiBr endows the PVA hydrogel with an excellent self-hygroscopic property. The SPG cooling film demonstrates an outstanding cooling performance under the synergistic effect of the graphene film and the self-hygroscopic PVA hydrogel. In the outdoor experiments, the SPG cooling film can reduce the temperature of the PV cells by 20.6°C and increase its average output power from 74 to 93 W/m2, about a 25.7% increase. This cooling film demonstrates significant potential for enhancing cooling performance in electronic devices and could be widely used in the thermal management of PV cells.
1 Introduction
Photovoltaic (PV) cells, as one of the representative clean and renewable energy technologies, are attracting increasing interest due to the global energy transition and climate change [1-5]. As reported by the International Energy Agency, the global installed capacity of renewable energy reached nearly 510 GW in 2023, with photovoltaic systems comprising more than 380 GW [6, 7]. By 2027, the global solar photovoltaic power generation is expected to triple, surpassing coal and becoming the largest source of electricity globally. However, the performance of PV cells is adversely affected by the increase in temperature [8, 9]. As temperature rises, the output power of the PV cells diminishes due to the accelerated recombination rate of electrons and holes. An incremental rise in cell temperature by 1°C leads to a corresponding decline in photovoltaic conversion efficiency of approximately 0.4% [10]. To mitigate this effect, various cooling strategies have been developed, including both active and passive cooling techniques, aiming at ensuring stable power generation in PV cells [11-17].
Active cooling technologies typically require external energy to drive the flow of the cooling medium to remove the heat generated by the PV cells [18-23]. A typical method is to use a pump to circulate water to reduce the temperature of PV cells, which improves the power output of PV cells by nearly 17% [24]. Although the active cooling techniques are effective and suitable for maintaining the high power density of PV cells, they usually require additional energy consumption and entail high maintenance costs. In contrast, passive cooling technologies, such as natural convection and evaporative cooling, have gained extensive research due to their energy-independent operation without consumption [25-28]. For the natural convection cooling technology, the metal heat sinks are usually used to improve the cooling effects, while the corrosion associated with the metal heat sinks significantly impedes their application in outdoor environments, necessitating supplementary maintenance procedures [29]. As known, the evaporative cooling technology is one of the most used cooling technologies in the PV cell industry due to the high latent heat of vaporization of water (2450 J/g) [30-33]. For example, Zhao et al. [34] reported the fabrication of a porous hydrogel coating as a cooling layer for absorbing and immobilizing water to improve the thermal management efficiency of PV cells, in which the hydrogel coating demonstrated the ability to absorb and immobilize water for evaporative cooling. However, the regeneration of the hydrogel after the evaporation of water has not been realized. Therefore, the evaporative cooling methods still encounter challenges, such as insufficient cooling effects and slow regeneration rates, which greatly influence the efficiency of the PV cells.
In this study, we combine a highly thermal conductive graphene film with a self-hygroscopic polyvinyl alcohol (PVA) hydrogel containing LiBr to fabricate passive cooling films. The graphene film with a high thermal conductivity of 1400 W/(m·K) and the self-hygroscopic PVA hydrogel with a high moisture absorption capacity are used as the heat conducting layer and the evaporation cooling layer, respectively. Under the synergistic effect of the graphene film and the self-hygroscopic PVA hydrogel, the cooling film demonstrates superior cooling performance and regeneration capacity. In outdoor experiments, the cooling film can lower the temperature of PV cells by 20.6°C, increasing the average output power by 25.7%.
2 Experimental Section
2.1 Preparation of Thermal Conductive Graphene Films
Graphene oxide (GO) nanosheets were dispersed ultrasonically in deionized water (Supporting Information S1: Figure S1). A GO aqueous solution with a concentration of 15 mg/mL was scraped onto a microporous filter membrane. After drying, the GO film was peeled off and reduced using hydriodic acid at 90°C for 1 h. The reduced GO film was then mounted in a fixture and placed in a graphite furnace. Following the evacuation of the furnace, argon gas was introduced. The temperature was gradually increased to 1200°C at a rate of 2°C/min and maintained for 2 h. Subsequently, the temperature was raised to 3000°C at a rate of 5°C/min and held for 1 h. The graphitized film was then compressed using a hydraulic press at 300 MPa pressure between polished tungsten plates. The thickness of the graphene film is 20 μm.
2.2 Preparation of Self-Hygroscopic Polyvinyl Alcohol/Graphene (SPG) Films
PVA powder was added to deionized water and heated to 90°C to dissolve to obtain a 10 wt% aqueous solution of PVA. Added LiBr powder to the PVA aqueous solution using the specified weight ratio and mixed well. The solution was then poured onto a graphene film substrate and frozen in liquid nitrogen for 0.5 h. Finally, the hydrogel was thawed at room temperature, and the SPG cooling film was obtained. In addition, the cooling films with LiBr content of 0, 10 wt%, 30 wt%, and 50 wt% in PVA hydrogel were labeled as SPG0, SPG10, SPG30, and SPG50, respectively. PVA hydrogels with 0 and 30 wt% LiBr added were marked as LiBr0%-PVA hydrogel and LiBr30%-PVA hydrogel, respectively.
2.3 Characterization
Scanning electron microscopy (SEM) was used to characterize the morphology and microstructure of the hydrogel and the graphene film. To analyze the elemental composition, X-ray photoelectron spectroscopy was employed using an ESCALAB 250 instrument. Raman spectroscopy (MacroRAM, Horiba Scientific) and X-ray diffractograms (D8 Advance, Bruker) were used to characterize the structure of substances. The thermal diffusion coefficients and specific heat capacities of the samples were determined by a flash thermal conductivity meter (LFA 467 NanoFlash, Netzsch) and a differential scanning calorimeter (DSC 214, Netzsch). Infrared photographs were taken using a thermal imaging camera (K20, Hikmicro). The stress-strain curve of the hydrogels was obtained using a stretching tester model UH 6502. Digital source meter (Keithley 2400) for measuring current-voltage characteristic curves of PV cells.
3 Results and Discussion
3.1 Design Principle and Characterization of the Cooling Film
Figure 1A illustrates the structure and principle of the SPG cooling film. The SPG cooling film consists of a graphene thermal conduction layer and a PVA hydrogel layer containing 30% LiBr, which can absorb and release water. The graphene layer could effectively transfer heat from the device to the hydrogel layer. Figure 1B(i) presents a scanning electron microscope (SEM) image of the graphene film. The thermally conductive graphene film is obtained from a GO film after high-temperature graphitization and mechanical calendaring (Supporting Information S1: Figures S2,S3). The top layer of the SPG film is the LiBr30%-PVA hydrogel (Figure 1B(ii)). The water evaporation process within the hydrogel could cool the device. Importantly, the massive hydrophilic functional groups of PVA along with the strong hygroscopic properties of the LiBr component within the hydrogel layer, enable it to absorb moisture from the atmosphere for reuse. SEM images from the dried hydrogel show the presence of a large number of micropores, providing extensive channels for moisture collection and evaporation (Figure 1B(iii)). Meanwhile, the results of thermogravimetric analysis showed that evaporation water accounted for 61% of the total weight of the LiBr30%-PVA hydrogel (Supporting Information S1: Figure S4).
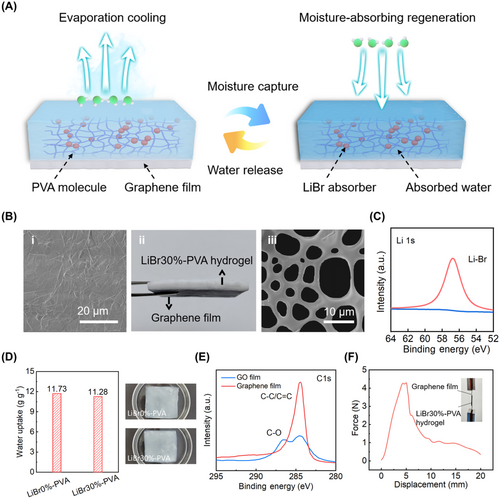
The X-ray photoelectron spectroscopy (XPS) analysis and the X-ray diffraction (XRD) pattern demonstrate that the moisture-absorbent LiBr was successfully introduced into the PVA hydrogel (Figure 1C; Supporting Information S1: Figures S5,S6). The hygroscopic properties of hydrogels affect the regeneration performance of SPG. Dehydrated LiBr0%-PVA hydrogels and LiBr30%-PVA hydrogels were placed into deionized water to test the hygroscopic properties. After 10 h of hygroscopic process, the absorption capacity for water of LiBr0%-PVA hydrogels and LiBr30%-PVA hydrogels is 11.73 and 11.28 g/g, respectively, which indicates that LiBr rarely affects the hygroscopic performance of hydrogel (Figure 1D). Additionally, the LiBr30%-PVA hydrogel exhibited a wide strain range of over 200% (Supporting Information S1: Figure S7). The stress-strain curve of the LiBr30%-PVA hydrogel matched well with that of the LiBr0%-PVA hydrogel, indicating that the incorporation of LiBr scarcely influences the conformation of polymer chains. As a result, the mechanical strength of the hydrogel remained good after the addition of the LiBr.
Due to the low thermal conductivity of water, it adversely affects the cooling of the device. Therefore, the graphene film prepared by GO graphitization is used as a heat diffusion layer for the SPG cooling film. The XPS survey spectrum revealed the presence of C and O elements in the GO film (Supporting Information S1: Figure S8). However, the graphene film exhibited a prominent C 1s peak after graphitization, while the O 1s peak was nearly undetectable. The carbon/oxygen atomic ratio in the graphene film significantly increased from 2.8 to 97.8, indicating the effective removal of oxygen-containing functional groups. As shown in Figure 1E, the graphene film displayed a sharp and intense C–C/C = C peak around 284 eV, indicating a significant restoration of the sp²-bonded structure of carbon. Additionally, the XRD pattern exhibited a sharp and narrow (002) peak at 26.6°, indicative of an interlayer of the graphene film (Supporting Information S1: Figure S9). Raman spectroscopy was employed to evaluate the internal defects within the film (Supporting Information S1: Figure S10). The D peak corresponds to lattice defects, while the G peak reflects the degree of carbonization. The intensity ratios of D peak to G peak (ID/IG) in the GO and graphene films are determined to be 0.87 and 0.008, respectively, demonstrating the structural integrity after graphitization. Furthermore, there are strong interfacial interactions between the graphene film and the hydrogel. The interfacial adhesion was measured by applying a 1 mm-thick layer of hydrogel between two graphene films with the size of 15 mm (length) × 10 mm (width). From the mechanical testing curve in Figure 1F, the interface exhibited no sign of fracture until the tensile force exceeded 4 N.
Figure 2A presents a photograph of a large-area SPG cooling film. The film can be cut into various sizes and shapes for application in different cooling environments. The graphene layer renders the SPG cooling film with high thermal conductivity, which could facilitate the cooling process (Figure 2B). As shown in Figure 2C, the graphene film exhibited a high thermal conductivity of up to 1400 W/(m·K), significantly surpassing those of metallic copper foil (413 W/(m·K)) and silicon thermal pads (6 W/(m·K)). In addition, the graphene film is also capable of extremely high thermal stability (Supporting Information S1: Figure S11). The high thermal conductivity of the graphene film is attributed to the high phonon propagation velocity and the oriented arrangement of the nanosheets. Most of the thermal conductivity reported in the literature is generally in the range of 800–2000 W/(m·K) [35-37]. Figure 2D shows the heat transfer performance of different thermally conductive samples on a heater with a maximum power of 5 W. The temperature of the heater quickly raised to 80°C upon applying power. When the temperature exceeded 45°C, the thermochromic sticker attached to the sample changed from red to yellow. After 60 s of heating, the thermochromic stickers on the graphene film completely changed to yellow, suggesting that the film's temperature had surpassed 45°C. In contrast, the stickers on the copper foil showed a yellow color near the heat source and remained red outside the heat source, indicating slower heat diffusion compared to the graphene film. The silicon thermal pad exhibited minimal color change after 30 s, with most of the area remaining red, and only a small area near the heater turned into a slight yellow after 60 s, demonstrating its difficulty in evenly distributing heat. To quantitatively compare the thermal performance of different samples, a high-resolution infrared thermal imaging camera was used to monitor the heating effect of the samples (Supporting Information S1: Figure S12). One end of the sample was fixed to a heat source at 80°C, while the other end was attached to a heat sink. Figure 2E compares the thermal performance of the silicon thermal pad, the copper foil, and the graphene film. The graphene film displayed the largest red region and heat diffusion distance, indicating that its heat diffusion rate and thermal flux are significantly higher than those of the copper foil and the silicon thermal pad (Supporting Information S1: Figures S13,S14). Furthermore, at the same heat diffusion distance, the maximum temperature difference between the graphene film and the silicon thermal pad is approximately 20°C.

3.2 Hygroscopic Regeneration of the Cooling Film
Traditional hydrogels primarily consist of liquid water, which gradually evaporates under saturated vapor pressure, leading to complete dehydration. In this case, as the evaporation continues to grow, the efficiency of cooling diminishes over time. The SPG cooling film containing LiBr hygroscopic agent could be recovered after dehydration. The SPG cooling films consisting of PVA hydrogels with concentrations of 0, 10 wt%, 30 wt%, and 50 wt% LiBr are defined as SPG0, SPG10, SPG30, and SPG50, respectively. Figure 3A shows the saturated vapor pressure of the SPG cooling films at different temperatures. The saturated vapor pressure of all SPG cooling films increases with temperature. At 20°C, the saturated vapor pressure of the SPG30 is 0.98 kPa, which is much lower than that (2.2 kPa) of the SPG0. This shows that the SPG30 is less susceptible to water loss at around 20°C (Supporting Information S1: Figure S15). When the temperature reaches 80°C, the saturated vapor pressure of SPG50 increases from 0.43 to 7.9 kPa, while SPG30 reaches 20.7 kPa, indicative of easier evaporation. Figure 3B illustrates the thermal characteristics of the SPG films as determined by differential scanning calorimetry (DSC). The results show that the SPG0 begins to release water at around 40°C, exhibiting a significant peak around 110°C, which signifies rapid water evaporation. In contrast, the SPG50 shows a major peak around 172°C. Figure 3C presents the evaporation enthalpy of the SPG films with varying LiBr concentrations. The enthalpy of evaporation decreases with increasing LiBr concentration. The enthalpy of evaporation for the SPG0 is 1463.9 J/g, while it drops to 539.1 J/g for the SPG50. The higher LiBr concentration of SPG films leads to less heat absorption during evaporation, which is further supported by the specific heat capacity measurements of the SPG films with different LiBr concentrations (Supporting Information S1: Figure S16). Specifically, the SPG0 requires 4.07 J of heat for each degree Celsius increase in temperature, whereas the SPG50 needs only 2.03 J, representing a 50% reduction in heat absorption capacity.
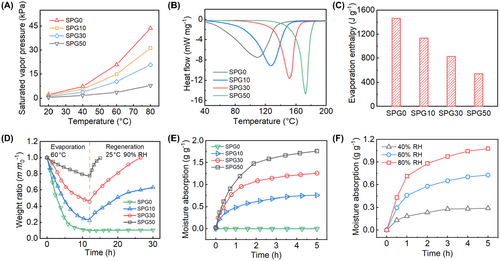
Figure 3D presents the variation of the weight ratio during the evaporation and regeneration processes for the SPG cooling films. During the evaporation process, the SPG films with higher LiBr concentrations exhibit less water evaporation. The SPG0 is almost completely dehydrated after evaporation at 60°C for 6 h and weighs only 17% of the initial weight, whereas the weights of SPG10, SPG30, and SPG50 are 36%, 56%, and 85% of the initial weight, respectively. More importantly, there is only a small decrease in the weight ratios of SPG10, SPG30, and SPG50 after the evaporation of up to 12 h. The weight ratios are 22%, 45%, and 77% of the initial weight, respectively. During the regeneration process, the higher LiBr concentrations of the SPG films absorb more moisture under the same condition. Specifically, the SPG50 can recover up to 100% of its weight after 3 h of regeneration at 25°C and 90% RH, whereas SPG10 and SPG30 can recover 38% and 64% of their weight, respectively. After 14 h of hygroscopicity, the SPG30 recovers to 100%, while the SPG0 only recovers to 60%. The SPG0 has almost no regeneration capacity during the whole hygroscopic process, and its weight remains almost the same.
The concentration of LiBr not only affects the evaporation of moisture but also significantly impacts the regeneration capabilities of the SPG films. As shown in Figure 3E, the SPG films with different LiBr content were subjected to moisture absorption experiments after dehydration. In the first 1 h, the moisture absorption weights of SPG10, SPG30, and SPG50 are 0.48, 0.81, and 0.96 g/g, respectively, while the absorption weights in the subsequent 4 h are only 0.27, 0.46, and 0.79 g/g at 90% RH. The SPG10 shows limited regeneration capability, with a moisture absorption of only 0.75 g/g after 5 h, which is less suitable for sustained evaporative cooling. The SPG50 with a lower enthalpy of evaporation absorbs less heat during evaporation. Thus, the SPG30 offers a balance between effective cooling and good moisture regeneration capability. In addition, the moisture absorption characteristics of the SPG30 at different humidity levels were also investigated (Figure 3F). Under high humidity conditions, the SPG30 is prone to absorb moisture. For example, the moisture absorption of SPG30 at 40% RH for 1 h is 0.18 g/g, while the moisture absorption at 60% RH and 80% RH are 0.45 and 0.71 g/g, respectively. The evaporation process of SPG30 is also analyzed at different temperatures. The higher the temperature, the faster SPG30 evaporates. The weight of SPG30 decreased by 9.5% after 2 h of continuous evaporation at 40°C. At higher temperatures, such as 80°C and 100°C, the weight of SPG30 decreased by 32.4% and 52.7%, respectively (Supporting Information S1: Figure S17).
3.3 Evaporative Cooling Performance of the Cooling Film
The SPG cooling film was used for evaporative cooling tests at different power densities of the heat source (Figure 4A). Under a heat source of 500 W/m2, the temperature with the SPG30 film can be kept to < 40°C for more than 12 h. At heat source power densities of 1500 and 2000 W/m2, the SPG30 film could reduce the temperature below 55°C for 5 and 3 h, respectively. With the increased thickness of the SPG film, the cooling time could also be extended (Figure 4B). For example, 3 mm-thick SPG30 can reduce the temperature of a 2000 W/m2 heat source to below 55°C for 7 h, while 5 mm-thick SPG30 lasts for 12 h. This result shows that the cooling films can satisfy the cooling needs of multiple scenarios. Additionally, the prepared SPG30 films can be reused after a regeneration process (Supporting Information S1: Figures S18,S19). More importantly, the cooling performance of our SPG30 film is compared with the graphene film and the LiBr30%-PVA hydrogel. Figure 4C shows the temperature profiles of a heater with a diameter of 30 mm and a power of 5 W using different cooling samples. After 1 min of operation, the surface temperature of the heater rapidly increased to 67°C under natural cooling, while the temperature only rose to 43°C with the SPG30 film. Specifically, as in Figure 4D, the temperature increase of the SPG30 is the lowest compared to the heater with LiBr30%-PVA hydrogel or graphene film. After 6 min of operation, the surface temperature of the heater with the graphene film and PVA hydrogel is 74.6°C and 62.3°C, respectively. In comparison, the SPG30 film shows the lowest temperature of 55.2°C, indicating excellent cooling ability. The superior performance of the SPG30 is attributed to the high in-plane thermal conductivity of the graphene film, which facilitates rapid heat diffusion across the entire hydrogel surface, thereby maximizing the cooling effect.

To further validate the exceptional cooling performance of the SPG30 film, it was applied to practical PV cells (Figure 5A). The SPG30 cooling film was attached to the back of a commercial polycrystalline silicon PV cell with dimensions of 15.7 cm × 9.4 cm. The maximum power of the PV cell is 2 W, and the operating current is 0–400 mA. During the operation of the PV cells, a large portion of the absorbed solar energy is converted into heat, leading to elevated cell temperature that substantially diminishes the efficiency of PV cells (Supporting Information S1: Figure S20). Under a simulated solar condition of 1000 W/m2, the surface temperature of the PV cell increased slowly from 32.4°C to 40.8°C after 30 min (Figure 5B). In contrast, without the SPG30 film, the PV cell temperature surged from 32.8°C to 61.3°C under the same solar irradiation. Figure 5C shows the conversion efficiency of the PV cell operating at 1000 W/m2 of simulated solar irradiation for 30 min. The conversion efficiency is negatively correlated with the temperature of the PV cell (Supporting Information S1: Figure S21). Without the SPG30 cooling film, the conversion efficiency decreased from 19.44% to 15.49%. The efficiency of the PV cells with SPG30 cooling film decreased only slightly from 19.64% to 19% during the test, a decrease of 0.64%, which is 6 times lower than that of the natural cooling.
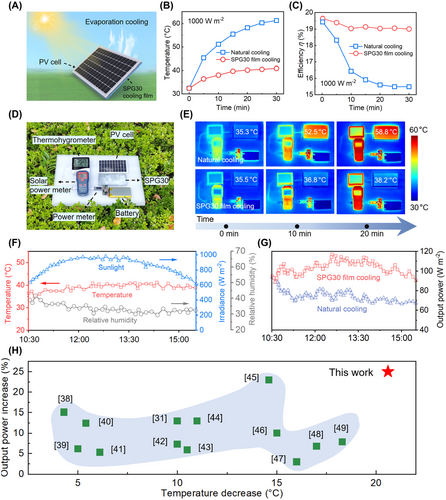
To test the performance of the SPG30 cooling film in real outdoor conditions, an experimental test platform was set up (Figure 5D). The SPG30 film, with the size of 15 cm (length) × 8 cm (width) × 0.4 cm (height), is used to cool the commercial PV cell. The PV cells are placed horizontally on the surface of the SPG30 cooling film, and the light-absorbing side of the cell faces the sky. The thermal conductive layer of SPG30 and the backside of the PV cell are in close contact to rapidly spread the heat. The input of a digital power meter is connected to the output of the PV cell to record the output power. The output of the power meter is connected to a battery with a capacity of 5000 mA·h. A thermohygrometer and a solar power meter are used to measure the temperature and humidity of the experimental environment and the solar irradiance. All components of the experimental test are placed on a white insulated polyethylene sheet with a thickness of 2 cm. Under outdoor conditions with a solar irradiance of 894 W/m2 and an ambient temperature of 37°C, the temperature of the PV cells increased to 58.8°C after 20 min of sunlight exposure. However, with the SPG30 cooling film, the temperature of the PV cells was kept at 38.2°C under the same condition (Figure 5E). Figure 5F shows the temperature, humidity, and solar irradiance of the outdoor environment from 10:30 a.m. to 3:30 p.m. During the experiment, the average irradiance was 853 W/m2, and the average temperature was 40°C. Figure 5G compares the output power of PV cells under SPG30 film cooling and natural cooling conditions. The PV cell with the SPG30 cooling film exhibited an average output power of 93 W/m2, which exceeded the naturally cooled cells by 19 W/m2. These results indicate that the SPG30 film exhibits sustained and efficient cooling performance for PV cells during practical application. Notably, the SPG30 film possesses one of the best cooling performances and regenerative capabilities among the previously reported cooling films (Figure 5H and Supporting Information S1: Figure S22) [38-49].
4 Conclusions
In summary, we have developed a SPG cooling film with automatic evaporation and moisture regeneration for the passive cooling of PV cells. The SPG cooling film consists of a high thermal conductivity graphene layer and a hygroscopic hydrogel layer. The graphene layer has a high thermal conductivity 1400 W/(m·K), which can efficiently transfer heat from the source to the hydrogel layer (evaporation cooling layer) uniformly and quickly. In addition, the incorporation of LiBr imparts exceptional self-hygroscopic properties to the PVA hydrogel, resulting in a moisture absorption capacity of 0.81 g/g in an environment of 25°C and 90% relative humidity. Under the synergistic effect of the graphene film and the self-hygroscopic PVA hydrogel, the SPG cooling film exhibits outstanding cooling performance and moisture regeneration capabilities. In outdoor experiments, the SPG30 cooling film can successfully reduce the temperature of the PV cell by 20.6°C and significantly increase its average output power from 74 to 93 W/m2. The introduction of high thermal conductivity graphene and powerful hygroscopic agents (LiBr) endows the SPG30 cooling film with efficient and sustainable cooling, which offers great promise for improving the reliability and stability of the device.
Acknowledgments
This study is financially supported by the Key Research and Development Program of Jiangsu Province (BE2023009), the Natural Science Foundation of Chongqing (2022NSCQ-MSX2366), and the Open Research Fund of Key Laboratory of MEMS of Ministry of Education, Southeast University. This study is also being supported by Shanghai Pilot Program for Basic Research and the Fundamental Research Funds for the Central Universities.
Conflicts of Interest
The authors declare no conflicts of interest.