Simulations on polymer nanocomposite crystallization
Funding information: National Natural Science Foundation of China, Grant/Award Number: 21404050; Natural Science Foundation of Jiangsu Province, Grant/Award Number: BK20190866; Program on Open Innovation Platform with Enterprises, Research Institute, and Academia, Grant/Award Number: CNMGE202101013; Research Foundation of Jiangsu University, Grant/Award Number: 14JDG059
Abstract
Polymer nanocomposites are widely used in industry due to their excellent mechanical properties. Polymer crystallization in polymer nanocomposites can effectively enhance the interfacial interactions between polymer matrix and nanofillers, thereby providing new ideas for preparing high-performance polymer materials. In recent years, molecular simulation has gradually become a powerful research tool for the investigation of polymer materials and physics. In this article, the latest simulation research progress on the crystallization behaviors of polymer nanocomposites under different conditions is reviewed, and the influences of various factors on the crystallization behaviors of homopolymers, copolymers, and oriented polymers filled with nanofillers, as well as polymers grafted on nanofillers are summarized and discussed. It is highly expected that the current review can supply some new insights into the development and design of new nanohybrid structures and then the control of the physical properties of polymer nanocomposites.
1 INTRODUCTION
Polymer nanocomposites are among the most important materials in the industry and attract considerable attentions nowadays. As we all know, the preparation of polymer nanocomposites provides the possibility of the synergy between nanofillers and polymer matrix, leading to the combination of the advantages of these two different materials. Compared with the traditional composite materials, polymer nanocomposites exhibit new and unique properties in terms of electrical,1, 2 optical,3, 4 mechanical,5, 6 and thermal properties.7 Therefore, polymer nanocomposites are widely used in aerospace, transportation, weapon manufacturing, sports equipment, and other fields.
Generally, the performance of polymer nanocomposites mainly depends on the following two factors: the dispersibility of nanofillers and the interfacial interactions between polymer matrix and nanofillers. In the past few decades, a great effort has been made by researchers to improve the interfacial interactions between polymer matrix and nanofillers, and some meaningful results have been achieved.8-10 So far, a large number of methods to achieve strong interfacial adhesions have been reported, such as surface modification of nanofillers, functionalization of polymer matrix, addition of solubilizers, and preparation of polymer composites by in situ polymerization.8-10 In addition to these above methods, interfacial crystallization can also effectively enhance the interfacial interactions between polymer matrix and nanofillers, thereby fabricating high-performance polymer nanocomposites. For the crystallizable polymers, nanofillers can act as heterogeneous nucleating agents to induce polymer chains to crystallize on their surfaces, leading to the formation of various unique nanohybrid structures.
Since interfacial crystallization provides a new strategy for reinforcing the mechanical properties of polymer nanocomposites, it has attracted considerable attentions of researchers.11-15 It should be noted that the influences of nanofillers on the crystallization behaviors of polymers are complicated, and so far, the corresponding mechanisms have not been fully elucidated.16 On one hand, the addition of nanofillers in the polymer matrix can significantly shorten the nucleation induction period. However, the change of crystallization rate depends on nanoparticle size and its volume fraction.17, 18 Based on molecular dynamics (MD) simulations, Jabbarzadeh et al. demonstrated that crystallization would be impeded due to the confinement effect, when the interparticle free space becomes smaller than the characteristic extended length of the polymer molecule chain.17, 18 Similarly, Papananou et al. reported that polymer crystallinity can be controlled by introducing a varying degree of chain confinement and of chain adsorption capability.19 In other words, both of the confinement effect and the adsorption effect of nanofillers would restrict the polymer crystallization process. Otherwise, in the systems containing relatively low contents of nanofillers, the crystallization rate of polymers will be accelerated owing to the nanofiller-induced heterogenous nucleation.11, 14, 15
On the other hand, the nanofillers of different dimensions can induce the formation of various complex nanohybrid structures. In order to reveal the formation mechanism of nanohybrid crystalline structures, the origin of interfacial crystallization has been extensively investigated.20-26 Epitaxial crystallization of polymer matrix is often found in many polymer composites and is the most widely accepted crystallization mechanism of hybrid crystalline structures. Unfortunately, for some nanofillers with smaller diameters, such as carbon nanotubes (CNTs), epitaxial crystallization is no longer suitable for explaining the formation of nanohybrid structures. In this case, the formation of the nanohybrid structures strongly depends on the geometry of nanofillers. Therefore, researchers proposed a new theory of soft epitaxy (geometric confinement) to interpret this phenomenon.20 According to this theory, the geometric confinement effect of nanofiller with smaller diameters restricts interfacial polymer chains to be aligned parallel to the long axis of the one-dimensional nanofillers. Under this condition, a novel nanohybrid shish-kebab (NHSK) structure, in which the lamellae are perpendicular to the long axis of the nanofillers, can be observed. However, this theory is still insufficient to describe the microscopic details of the nucleation process, and some unresolved issues still exist.
Furthermore, the structure of polymer chains plays an essentially crucial role in polymer crystallization. Specifically, the symmetry, regularity, copolymerization, branching, and crosslinking of polymer chains all have tremendous effects on polymer crystallization. Compared with linear homopolymers, copolymers change the intra-chain structure of the polymer, and cyclic polymers change the configuration structure of polymer chains. Therefore, both copolymers and cyclic polymers exhibit fascinating crystallization behaviors different from linear polymers. Different chain structures also affect the crystallization behaviors of polymer nanocomposites. For instance, due to the unique microphase separation of block copolymers, one-dimensional nanofillers can induce polymer chains to form hierarchical structures, which establishes the foundation for the design and development of sophisticated hybrid structures.27-29
Besides, the external flows or stretching also plays a decisive role in the crystallization behaviors of polymer nanocomposites.30-33 The presence of flow can cause some amazing phenomena in flow-induced crystallization. For instance, some special oriented crystalline morphologies (i.e., shish-kebabs) appear due to the effect of shear or extension flows.34, 35 Crystallization rate and crystallinity of flow-induced polymer crystallization are affected by shear rate and strain. Ma et al. detected that crystalline structure can be directly formed during flow under high shear rates.36, 37 Rutledge et al. performed MD simulations to investigate crystallization of oriented polyethylene melts, and observed a competition between the rate of nucleation, the rate of chain extension, and the rate of chain conformational relaxation.38 Jabbarzadeh et al. used MD simulations to study the effects of shear rate and strain on flow-induced polymer crystallization.39, 40 They found that strain plays a major role in flow-induced polymer crystallization, and there exists an upper limit shear rate, above which polymer crystallization would be suppressed.39, 40 Besides, the flow-induced nucleation of polymer chains belongs to one typical nonequilibrium phase transition, and always exhibits a multiscale and multistep process, which is more complicated than that of polymers in quiescent state.34, 35 Due to the coexistence of flow and nanofillers, some new phenomena may appear. For instance, the interfacial chain segments in polymers containing one-dimensional nanofillers will be subject to two different effects: the geometric confinement of one-dimensional nanofillers inducing the local orientations along the long axis and the flow-induced orientation of polymer chains.31 Then, under the combined influences of these above two effects, the flow-induce crystallization of polymer nanocomposites would exhibit different crystallization behaviors. However, to our best knowledge, there are still few works focusing on this field.
Some literatures have reported the crystallization behaviors of polymer nanocomposites under different conditions, such as polymers with different chain topologies or oriented polymers, and some important results have also been obtained.27-35, 41-43 Nowadays, with the fast developments of computer technology, computer simulation has been widely used in scientific researches. Some research groups have studied the crystallization behaviors of various polymers based on molecular simulations, and discovered interesting phenomena that are difficult to observe in experiments.44-51 For instance, Gee et al. used MD simulations to investigate the structural changes of polymer melts in the early ordering stages before crystallization, and successfully observed the spinodal phase separation preceding polymer crystallization.52 Compared with experimental researches, molecular simulations provide the possibility to directly explore the details of molecular motions, and thus it can also be used to study the formation mechanisms of nanohybrid structures in polymer nanocomposites. However, as far as we know, there are no reviews focusing on molecular simulations of crystallization behaviors of polymer nanocomposites. Then, this review is based on the latest simulation studies of the crystallization behaviors of polymer nanocomposites, and is organized according to the following topics: (1) simulations of nanofiller-induced homopolymer crystallization; (2) simulations of nanofiller-induced copolymer crystallization; (3) simulations of crystallization of grafted polymers on nanofillers; (4) simulations of flow-induced crystallization of filled polymers; (5) conclusions and perspectives.
2 METHODOLOGIES
In general, there are two effective simulation methods to investigate the microscopic mechanisms of polymer crystallization: Monte Carlo (MC) simulation and MD simulation.38-40, 53, 54 Hu's group used dynamic MC simulations of lattice polymers to systematically to investigate polymer crystallization.53 For this simulation method, lattice polymers can only move on lattice sites via a micro-relaxation model, which allows monomer jumping from an occupied site to a neighboring vacancy site, sometimes with partial sliding diffusion along the chain. Besides, double occupation and bond crossing are forbidden due to the volume exclusion of polymer chains. The conventional Metropolis sampling algorithm is employed for each step of micro-relaxation with potential energy penalty. In general, two different energies are usually introduced: Ep that is the potential energy change for each pair of nonparallel packed bonds, reflecting the molecular driving force for polymer crystallization, and Ec that is the potential energy change for noncollinear connection of two consecutive bonds along the chain, reflecting the chain flexibility.35
MD simulations were also successfully used to study polymer crystallization by several groups, such as Rutledge's group38, 51 and Yamamoto's group.45 In general, the corresponding simulation work based on MD simulations are usually performed on the Lammps package55 or Materials Studio software. The polyethylene unit atom model38, 51 and the coarse-grained poly(vinyl alcohol) (CG-PVA) model proposed by Meyer and Müller-Plathe56, 57 are suitable for the study of polymer crystallization.
Subsequently, we briefly describe the simulation details of the different topics of crystallization of polymer nanocomposites based on MC simulations.
2.1 Simulation details of nanofiller-induced homopolymer crystallization
Since nanofillers are added into the simulation box, the interfacial interaction between polymer and nanofiller should be taken into account. Then, the potential energy change (B) for each monomer-filler pair, representing the polymer-filler interaction, is introduced. In this condition, for MC simulations, the values of B/Ec can be used to reflect the strength of the interfacial interaction. Besides, in order to systemically study the effect of the nanofillers on polymer crystallization, the number of nanofillers, the shape, or aspect ratio of nanofillers can also be changed.
2.2 Simulation details of nanofiller-induced copolymer crystallization
For MC simulations of copolymer crystallization, the crystallizable and the non-crystallizable beads can be distinguished by setting different values of Ep. Namely, the value of Ep for the parallel packing of two bonds both belonging to the crystallizable beads is larger than zero, while the value of Ep for the parallel packing of two bonds containing at least one bead belonging to the non-crystallizable beads is set to zero. Based on the definition, the non-crystallizable beads cannot crystallize. For block copolymers, another energy parameter representing the mixing interaction between crystallizable beads and non-crystallizable beads, which drives the occurrence of microphase separation can also be introduced. For homogeneous random copolymer polymers, each occupied lattice site can be defined as either a crystallizable bead or a non-crystallizable bead based on an ideal addition copolymerization process for random copolymers with a preset comonomer fraction.
2.3 Simulation details of crystallization of grafted polymers on nanofillers
For polymers grafted on the surfaces of nanofillers, the chain segments that are directly grafted on the nanofillers are not allowed to move during simulations. By changing the distribution of grafting points on the surfaces of nanofillers, the grafted polymer systems with different grafting densities can be established. In addition, the grafted polymer systems with different molecular weights can also be set up by the change of the chain length of grafted polymers.
2.4 Simulation details of flow-induced crystallization of filled polymers
There are two methods to achieve oriented chains in MC simulations. For the first method, the initial chains with extended conformation were relaxed under athermal conditions (athermal conditions correspond to an infinitely high temperature). Then, during relaxation crystallinity decreases much faster than the mean-square radius of gyration. When the crystallinity values drop to 0, the corresponding mean-square radius of gyration is still higher than that of the random coils; that is, although the crystals are melted, the polymer melts can still have a certain degree of orientation. In other words, oriented melts that have no crystalline structures but a certain degree of chain orientation can be obtained in a certain period of relaxation time.31
For the second method, a gradient potential Es is introduced into the energy penalty in the conventional Metropolis sampling algorithm for a trial move of monomers in each step of the micro-relaxation process.35 It was demonstrated that Es/Ec is the external potential field of driving forces, corresponding to the driving-force aspect of shear stress in a shear field imposed along shear flow direction onto each bead.35
3 SIMULATIONS OF NANOFILLER-INDUCED HOMOPOLYMER CRYSTALLIZATION
It is well known that nanofillers can be used as heterogeneous nucleating agents to promote the polymer crystallization process and also induce the formation of various nanohybrid structures. Furthermore, the dimensionality of nanofillers is one of the main factors affecting polymer crystallization, which will be discussed in detail in the following sections. As a special homopolymer with unique topological structures, the crystalline behaviors of filled cyclic polymers will be further compared with these of filled linear polymers. However, in some special conditions (e.g., polymers are confined in nanopores or nanospheres, or near nanopatterned, flat, and curved surfaces), crystallization of confined polymers would exhibit different crystallization behaviors compared with that of unconfined polymers.58-60
3.1 Crystallization of polymers in nanopores, nanospheres, and near nanopatterned, flat, and curved surfaces
Müller's group performed systematically investigations on the crystallization of confined polymers.58 In general, the increase in the confinement degree can lead to a decrease of the predominance of heterogeneous nucleation, a very large decrease of the solidification temperature, a decrease of the degree of crystallinity, and a moderate decrease in melting point.58 In addition, surface nucleation plays a dominant role in the crystallization of polymers confined in an isolated ensemble of heterogeneity free microdomains, since surface nucleation requires lower degree of supercooling than classic volume homogeneous nucleation.58 Wang's group observed the existence of surface freezing in microencapsulated n-alkanes, and also found that the confinement suppresses lamellar ordering and longitudinal diffusion.59
With the help of MD simulations, Jabbarzadeh et al. studied crystallization of polymer as a drop in isolated state and on a surface.60 They found that the crystallization rate of polymer systems decreases with the increase of the roughness ratio, but is still faster than that of the isolated polymer drop.60
3.2 Formation mechanisms of NHSK structures in homopolymer solutions
As mentioned above, in order to explain the microscopic mechanisms of the formation of the NHSK structures, Li's group proposed the geometric confinement theory, which describes that the one-dimensional nanofillers with small diameters can exert confinements on the chain conformations of the interfacial chain segments, and further make them to orient along the long axis of the nanofillers.20, 21 However, they did not give a clear explanation about the details of the special “confinements.” Interestingly, based on molecular simulations, the formation details of the NHSK structures become clearer. Liu et al. used MD simulations to study the isothermal crystallization of one single polymer chain on one CNT, and observed that the chain is firstly adsorbed onto the filler surface, and then oriented along the long axis to form an oriented crystal.61
In order to obtain in-depth information for the formation of the NHSK structures, our group further used MC simulations to investigate the nucleation details of the NHSK structures.62 Figure 1A shows the variations of the monomer density and the orientational-order parameter of amorphous segments along the long axis of the filler in the polymer-filler interface at the early stage of crystallization. Both the monomer density and the orientational-order parameter of amorphous segments along the long axis of nanofiller increase fast at first and then reach a plateau, indicating the absorption of chain segments onto the filler surface with small lateral size belongs to an anisotropic process. Figure 1B displayed that the orientational-order parameter along the X-axis direction (i.e., the long axis of the nanofiller) is obviously higher than these along with the Y-axis and Z-axis directions, further confirming that chain segments prefer to orient along the long axis of the nanofiller during absorption. Using MD simulations, both Yang et al. and Zong et al. observed that absorbed chain segments are oriented along the long axis of CNTs.63, 64 In addition, Figure 1A also showed that the crystallinity increases much slowly than the monomer density and the orientational-order parameter, demonstrating that the adsorption and orientation processes are the prerequisite for the NHSK formation. After the adsorption and orientation processes, the adsorbed oriented segments begin to participate in crystallization based on heterogenous nucleation.62
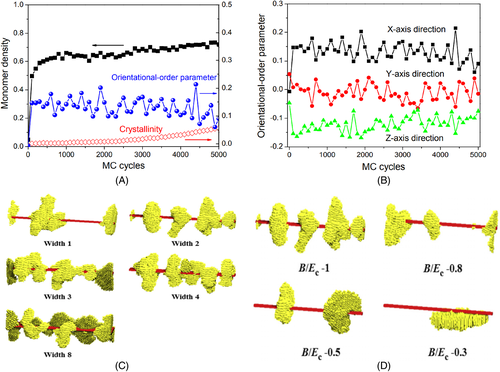
Reprinted with permission from Nie et al.62 Copyright (2015) Elsevier
In experiments, it was demonstrated that the diameters of the nanotubes can influence the formation of the NHSK structures.11 According to the dynamic MC simulations, we also found that the perfect NHSK structures can also form in the systems with the nanofillers of relatively small lateral sizes, while in the systems with the nanofillers of relatively large lateral sizes some lamellar crystals with other different orientations will also form, as illustrated in Figure 1C.62 The increase of the lateral sizes can cause the increase of the orientational-order parameter along the lateral-dimension direction, and then lead to the formation of some lamellar crystals with other orientations. The interfacial interactions between fillers and polymers also play an important role for the NHSK formation. Our simulation results showed that the interfacial chain segments under high polymer-filler interfacial interactions have higher orientational-order parameters along the long axis of the nanofiller that these under the low polymer-filler interfacial interactions, and thus the perfect NHSK structures prefer to form in the systems with high interfacial interactions rather than that with low interfacial interactions, as shown in Figure 1D.62
In addition, we also observed that a new NHSK structure with multiple shish appears in the systems containing aligned anisotropic filler networks, illustrated in Figure 2A.65 In this special structure, several aligned one-dimensional fillers form the multiple shish, and the polymer lamellar crystals form the kebabs. During crystallization, nuclei first form inside the filler networks, and then grow up to connect the nanofillers to form the special NHSK structure with multiple shish, as illustrated in Figure 2B.65 Due to the confinement effect of the aligned anisotropic filler networks and the interfacial interactions, the inside polymer chains have higher degree of orientation along the long axis of the nanofillers and higher monomer density (as seen in Figure 2C,D), then resulting in stronger nucleation ability of the inside chains.65

Reprinted with permission from Nie et al.65 Copyright (2016) Royal Society of Chemistry
The influences of filler dimension and size on the crystallization of polymer systems have been widely reported in experiments. The effects of one-dimensional CNTs and two-dimensional graphene nanosheets on polymer crystallization are often compared. For example, Xu et al. found that compared with graphene, CNTs with a larger aspect ratio exhibit a higher ability to induce polymer crystallization.22 Based on MD simulations, this phenomenon was also discovered and confirmed in the crystallization processes of alkanes induced by nanotubes and graphene.63 Ning et al. comprehensively summarized the crystalline structures induced by nanofillers of different dimensions (including one-dimension, two-dimension, and three-dimension).11
In our previous work, the crystallization behaviors of polymers filled with the nanofillers with different dimensions (i.e., zero-dimensional nanofillers, one-dimension nanofillers, and two-dimension nanofillers) were studied by dynamic MC simulations.66 It was found that the one-dimensional nanofiller has the strongest ability to induce polymer crystallization, while the zero-dimensional nanofiller has the weakest ability. The crystalline morphology of polymer composite systems will also be affected by the filler dimension. Differing from the one-dimensional nanofiller that can induce the formation of the NHSK structures, the two-dimensional nanofiller can only induce the formation of the crystals with stem orientations parallel to the nanofiller surface, as shown in Figure 3A.66 In the system containing the zero-dimensional nanofiller, the three-dimensional crystal growth happens, resulting in random crystal orientations. This difference of the crystalline morphologies in these systems containing nanofillers with different dimensions can be attributed to the different ability to induce the orientation of interfacial segments. As shown in Figure 3B,66 the orientational-order parameters of interfacial amorphous bonds along with X-axis, Y-axis, and Z-axis directions are almost the same, indicating that the zero-dimensional nanofiller cannot induce segmental orientation in the interfacial regions. As shown in Figure 3C,66 the values of the orientational-order parameters of interfacial amorphous bonds along the X-axis direction are obviously higher than these along with Y-axis and Z-axis directions. That is, the interfacial segments are inclined to align along the long axis of the nanofiller. As shown in Figure 3D,66 the values of the orientational-order parameters of interfacial segments along X-axis and Y-axis directions are nearly the same, both of which are higher than these along Z-axis direction. Under the effect of the polymer-filler interaction interfacial segments prefer to “lie” on the filler surface (XY plane), and chain conformations are unfolded in interfacial regions, resulting in the higher orientational-order parameters along with X-axis and Y-axis directions. Wang et al. also detected that graphene platelet can induce the orientation of absorbed segments based on MD simulations.67
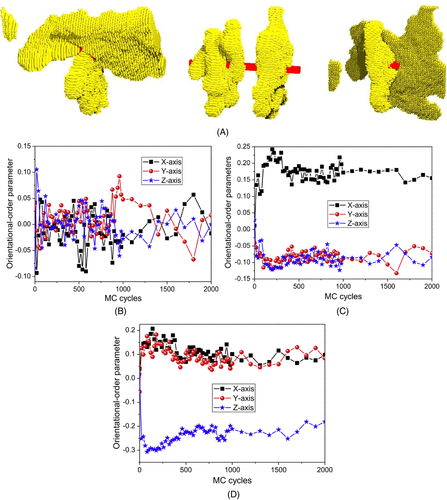
Reprinted with permission from Nie et al.66 Copyright (2018) Elsevier
Nowadays, the precise morphology control is paramount among many challenges as polymer nanocomposites move beyond commodity plastic applications.68-71 In general, the semi-crystalline polymers with uniform crystal orientation exhibit high mechanical properties.11 However, the crystals induced by the two-dimensional nanofillers, such as graphene, exhibit random orientations.11, 72 Then, to achieve the polymer crystals with uniform orientation (similar to the NHSK structure) in polymers containing the two-dimensional nanofillers is a very interesting topic.73 Nowadays, applying shear flow field is the most commonly used method for the improvement of polymer crystal orientation.72, 73 The oriented chains in sheared systems can induce the formation of oriented crystals or shish-kebabs.72, 73 From another point of view, if oriented chains are fixed on the filler surface, oriented crystals may be obtained even without shear flow. In our previous work, using dynamic MC simulations, we modified the two-dimensional nanofiller with two-end grafted oriented chains (loops, as seen in Figure 4A),74 and then successfully obtained the crystal structure with uniform orientation in polymer solutions, as shown in Figure 4B.74 These simulation findings provide a new method to control polymer crystal orientation.
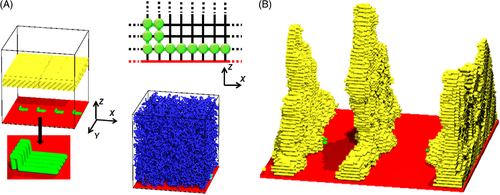
Reprinted (adapted) with permission from Nie et al.74 Copyright 2017 American Chemical Society
3.3 Differences in crystallization behaviors between cyclic and linear polymer nanocomposites
Cyclic polymers belong to fascinating materials due to the unique topology. Compared with linear polymers, cyclic polymers differ only in that their lack of chain ends. However, owing to this difference in topological structure, cyclic polymers exhibit some special microscopic structures and macroscopic physical properties.75, 76
Based on molecular simulations, extensive researches have been performed on the crystallization behaviors of cyclic polymers and their linear analogs.77, 78 Previously, Sommer and coworkers found that the crystallization temperature, melting point, stem length, crystallinity, and latent heat of melting/crystallization of cyclic polymer melts are significantly higher than their linear counterparts subjected to the same thermal history.77 In contrast, Iyer and Muthukumar investigated the crystallization behaviors of cyclic polymers by Langevin dynamics simulation, and observed that cyclic polymers melt at a lower temperature compared to linear counterparts.78 These controversial conclusions have also been reported in some experimental researches. For instance, Pérez et al. reported that under the same crystallization conditions, cyclic poly(ε-caprolactone) (PCL) exhibits faster nucleation rate and higher crystallization rate compared to the analog linear PCL.75 Similar phenomena are also observed for cyclic poly(ethylene oxide),76 and cyclic poly(l-lactide) (PLLA).79 However, completely opposite results have been reported for cyclic poly(tetrahydrofuran)80, 81 and PE.82 Pérez and coworkers summarized these opposite research conclusions and conducted the theoretical analysis.83 The above contrastive behavior between cyclic polymer melts and linear polymer melts could be interpreted from the following two viewpoints: kinetic factors determined by diffusion and thermodynamic factors controlled by different supercooling.84, 85
The addition of nanofiller also affects the crystallization behaviors of cyclic polymers. Nucleating effect has been found in cyclic PCL systems incorporating single-walled CNTs functionalized with octadecylamine.86 In addition, it was also found that adding graphene oxide nanosheets to cyclic ultrahigh-molecular-weight PE helps to form crystals with high melting temperatures.87 Previously, with the help of dynamic MC simulation, our group comparatively studied the crystallization behaviors of cyclic and linear polymer nanocomposites, and found that the filled cyclic polymers exhibit higher melting temperature, higher crystallization temperature, and faster crystallization rate, especially in the systems with relatively short chains.88 In other words, the nanofiller exhibits the same promotion effects on the crystallization process of cyclic and linear polymers. Moreover, it is also observed that the NHSK structure can be formed in both the systems (as shown in Figure 5A), indicating that the chain topology has little influence on the final crystal morphology.88
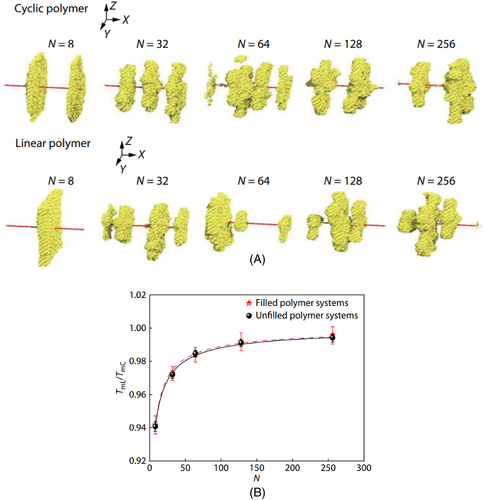
Reprinted with permission from Nie et al.88 Copyright (2020) Elsevier
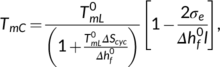



4 SIMULATIONS OF NANOFILLER-INDUCED COPOLYMER CRYSTALLIZATION
As we all know, copolymerization can effectively change the structure of polymer chains and then influence the performance of polymers. Among the numerous copolymers, block copolymers, and random copolymers are the most widely used copolymers. Nanocomposites based on block and random copolymers also exhibit different crystallization behaviors compared with filled homopolymers.
4.1 Crystallization behaviors of block copolymer nanocomposites
Block copolymers have been widely investigated because of their fascinating ability to self-assemble into different sophisticated structures. As we all know, in block copolymers, the repulsive interaction between chemically different blocks will cause sequence separation, while the chemical bonds connecting the sequences hinder the macroscopic phase separation as in the blend.87-92 In the delicate balance of these two effects, microphase separation will occur between different blocks. For the crystalline-amorphous diblock copolymers, the final crystal morphology is mainly governed by the crystallization process and microphase separation, resulting in more complex, and richer structures.93-95
Furthermore, due to the unique structural characteristics of block copolymers, block copolymer nanocomposites also exhibit special crystallization behaviors. For instance, the NHSK structure has also been observed in block copolymers filled with CNT bundles.96 Interestingly, a novel nanohybrid epitaxial brush (NHEB) structure, which is formed by a central CNT, disc-shaped folded-chain lamellar crystals of PE blocks decorating on filler surface and random coils of amorphous polyvinyl cyclohexane (PVCH) blocks surrounding PE crystals, was found in triblock copolymers (PVCH-PE-PVCH).97 Based on molecular simulations, similar structure has also been observed in crystalline-amorphous diblock copolymer systems filled with one-dimensional nanofiller, and the formation mechanism has also been revealed.98, 99 At the beginning of crystallization, due to the attractively interfacial interactions between the crystallizable blocks and the nanofiller, the amorphous chain segments (segments in crystallizable blocks that have not crystallized) are adsorbed into the interface area of the nanofiller and orient along the long axis of the filler. These amorphous segments grow into small crystallites (segments in crystallizable blocks that have crystallized) oriented along the long axis of the filler through heterogeneous nucleation, and finally form the NHSK structure. In this case, with the nanofiller as the center, the crystallizable segments are decorated on the surface of the nanofiller, while the non-crystallizable segments (segments in non-crystallizable blocks) are wrapped in the outermost layer. The formation of this hierarchical NHEB structure indicates that microphase separation occurs between the crystalline block and the non-crystallizable block. The distribution of different chain segments in the NHEB structure was also observed and counted. From Figure 6,98 one can see that the crystallizable segments are mainly distributed on the surface area of the filler due to the interfacial interaction, while the non-crystallizable segments are mainly distributed in the area away from the surface of the filler due to microphase separation. In general, the above-mentioned research results reveal the details of the formation of NHEB structure from the molecular scale (Figure 698).
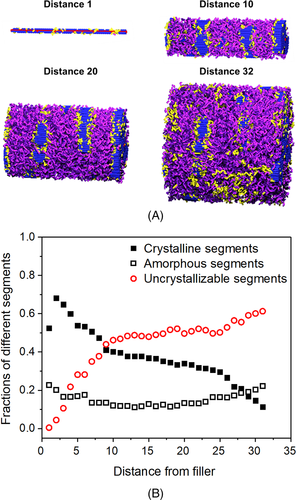
Reprinted with permission from Nie et al.98 Copyright (2019) Elsevier
Microphase separation can significantly affect the crystallization behaviors of block copolymers filled with nanofillers. It is reported that the enhancement of repulsive interaction between different blocks can promote microphase separation, which in turn leads to the local stretching of crystallizable blocks.99 Under this condition, the crystallization process through homogeneous nucleation is promoted, as shown in Figure 7A.99 In general, the repulsive interaction between the two blocks is the main driving force for microphase separation. In addition, the different crystallizability and the different polymer-filler interactions of various blocks will also promote the occurrence of microphase separation. For crystalline-amorphous diblock copolymers, the polymer-filler interfacial interaction enhances the heterogeneous nucleation, while the local stretching of the crystallizable segments caused by microphase separation promotes homogeneous nucleation. Thus, the final crystal morphology of the system is codetermined by these two factors, as shown in Figure 7B.99 In the systems with relatively weak repulsive interaction between blocks, the crystallizable segments preferentially crystallize through heterogeneous nucleation, and finally form a regular NHSK structure. In the systems with relatively strong repulsive interaction between blocks, the local stretching of the crystallizable segments is strengthened, and the pre-stretched crystallizable segments preferentially crystallize through homogeneous nucleation. Under this condition, homogeneous nucleation and heterogeneous nucleation compete with each other, leading to the degradation of crystal morphology.
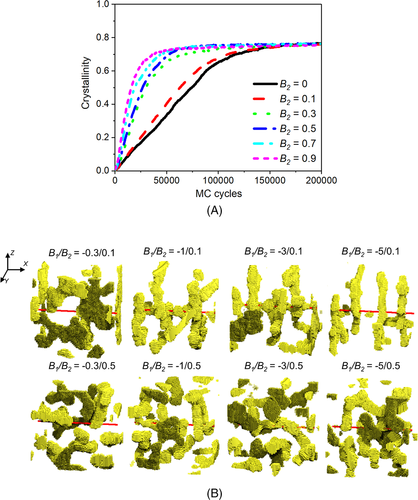
Reprinted with permission from Nie et al.99 Copyright (2018) John Wiley and Sons
In general, here we mainly introduce the crystallization behaviors of crystalline-amorphous diblock copolymers filled with one-dimensional nanofiller, and summarize the formation mechanism of the NHEB structure and the influence of microphase separation on the crystallization behaviors. These simulation results provide new ideas for the development and design of complex nanostructures. However, the crystallization behavior of filled crystalline–crystalline diblock copolymers and multi-block copolymers still needs further studies.
4.2 Crystallization behavior of random copolymer nanocomposites
Another type of copolymer that has been studied extensively is random copolymer composed of crystallizable monomers and non-crystallizable comonomers. Compared with homopolymers, the sequence regularity of the molecular chains of statistical random copolymers is destroyed, which makes it difficult to form thicker lamellae structure, resulting in a decrease in the melting point of the system. Based on the assumption that the non-crystallizable comonomers are uniformly distributed in space, Flory100 deduced the theoretical formula for equilibrium melting point of statistical random copolymers. Subsequently, Colson and Eby101 further derived the melting point formula under the condition that the non-crystallizable copolymer unit can enter the crystal region, and found that the decrease in melting point is proportional to the content of non-crystallizable comonomers. In addition, in random copolymers, the addition of non-crystallizable comonomers can hinder the crystallization process and reduce the crystallization rate.102 Furthermore, the crystal morphology will also be significantly affected due to the presence of non-crystallizable comonomers. As the content of non-crystallizable comonomers increases, the crystal morphology gradually degenerates from spherulites formed in homopolymer bulks to granular-based morphology or even small crystallites, which has been confirmed in experimental studies and computer simulations.103-105 In fact, the addition of a small amount of non-crystallizable copolymerization units can significantly reduce the melting point and the crystallinity of the random copolymer system, which is often used in industry to control the semi-crystalline structure of polymers and improve the toughness of materials.106
The crystallization behavior of random copolymer nanocomposites is also an interesting research topic. Similar to homopolymer nanocomposites, the addition of nanofillers in random copolymers can also promote the crystallization process and accelerate the crystallization rate.107-109 For example, Verma and Choudhary107 investigated the crystallization process of PP random copolymers under isothermal conditions in presence of multiwalled carbon nanotubes (MWCNT), and found that MWNT lowers the nucleation barrier, thereby accelerating the crystallization process. In addition, for the random copolymer nanocomposite systems, the crystallization behavior and crystal morphology also depend on the content of non-crystallizable comonomers. Based on molecular simulations, the isothermal crystallization process of a series of random copolymer nanocomposites with different contents of non-crystallizable comonomers has been studied.110 The simulation results indicate that increasing the comonomer content will slow down the nucleation rate and reduce the final crystallinity. Moreover, the crystalline morphology is also affected by the comonomer content. In the random copolymer nanocomposites with lower contents of non-crystallizable comonomers, the one-dimensional nanofiller can induce the formation of the NHSK structures.110 However, in the random copolymer nanocomposites with very high contents of non-crystallizable comonomers, the presence of a large number of comonomers with no ability of parallel arrangements hinders the formation of the NHSK structures. Under this condition, the formed crystallites usually exhibit different orientations.
5 SIMULATIONS OF CRYSTALLIZATION OF GRAFTED POLYMERS ON NANOFILLERS
Generally, adding nanofillers into the polymer matrix can promote the nucleation and crystallization process of polymers, which greatly enhances the performance of the composite material. However, when the polymer-filler interaction is weak, the nanoparticles may agglomerate, resulting in poor mechanical properties.111 In order to avoid this situation, researchers usually graft one end of molecular chains on the surface of nanofillers.112-117 At present, a large number of studies on the crystallization behaviors of grafted polymers have been carried out by experiments and simulations, and some controversial conclusions have been obtained. On one hand, some reports believe that nanofillers can act as nucleating agents in the crystallization process, thus reducing the activation energy of nucleation and accelerating the nucleation process. For instance, Wu et al. grafted PLLA into silica nanoparticles and found that the crystallization rate of PLLA is greatly improved.118 On the other hand, some studies indicated that the grafting of polymer chains on the filler surface inhibits the nucleation process. Previously, the decreased crystallization temperature and crystallinity as well as the reduced crystal size have been observed in the CNT-graft-aminated poly(phenylene sulfide) derivative, implying that CNTs may play an negative nucleating role. In fact, many factors, such as grafting density,119 molecular weight,120 polymer-filler interaction,121 and filler content,122 all directly affect the crystallization behaviors of grafted polymer systems. Therefore, the above-mentioned inconsistent conclusions can be attributed to the competitive effect between these factors. In the following, the effects of these factors on the crystallization behaviors of grafted polymers will be discussed in detail.
5.1 Effect of grafting density on polymer crystallization
Grafting density can affect the crystallization process of grafted polymer systems. Previously, our group systematically investigated the crystallization behaviors of polymers grafted on the surface of nanofillers with different dimensions based on dynamic MC simulations, and found that a higher grafting density can result in a shorter nucleation induction period and a higher final crystallinity.122-131 This phenomenon can be attributed to the decreased conformational entropy of the grafted chains and the decreased critical free energy nucleation barrier caused by the increased segment density in the regions near the grafting points and the chains with highly stretched conformations.123
Second, grafting density also affects the nucleation mode and the orientation of chain segments, which in turn changes the crystalline morphology. It has been reported that the crowding effect of molecular chains is relatively weak for the polymer systems with lower grafting density, which leads to the tendency of molecular chains to participate in the nucleation and growth of crystals in the form of intramolecular chain-folding nucleation.123-125 However, for the polymer systems with higher grafting density, the crowding effect of molecular chains is very strong and the degree of conformational extension is high, which results in the preferential crystallization of the molecular chains through intermolecular fringed-micelle nucleation. Due to the different nucleation modes, the systems with different grafting densities exhibit different crystal morphologies. The final crystal morphologies of the polymer systems grafted on two-dimensional nanofillers with different grafting densities were shown in Figure 8.123 It can be seen that the crystalline stems tend to crystallize parallel to the filler surface when the grafting density is low, and the crystalline stems prefer to crystallize perpendicular to the filler surface when the grafting density is high.
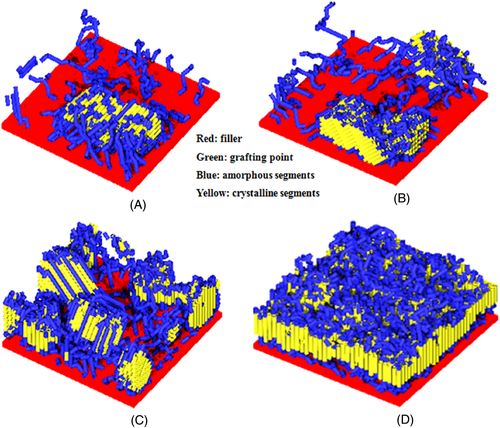
Reprinted with permission from Nie et al.123 Copyright (2016) Elsevier
5.2 Effect of molecular weight on polymer crystallization
The molecular weight will affect the conformations of polymer chains, thus significantly changing the crystallization behaviors of grafted polymers. Jana et al. found that the increasing molecular weight of PCL grafted onto MWNT leads to higher crystallization temperature and higher crystallinity.116 In the PCL systems grafted onto MWNT, Zhou, and coworkers also observed that the growth of molecular weight can reduce the activation energy of crystallization.119, 120 The detailed microscopic mechanisms of the influence of molecular weight on the crystallization behaviors of grafted polymers have also been further revealed by molecular simulations.127, 128 For example, our group reported that the increasing molecular weight leads to shorter nucleation induction period and higher final crystallinity, which is consistent with the experimental results.127 In addition, the nucleation mode and the orientation of crystalline stems are also affected by molecular weight. It has been reported that the chain segments prefer to choose the intermolecular nucleation mode in the grafted polymer systems with lower molecular weight, while the chain segments exhibit the intramolecular nucleation in the grafted polymer systems with higher molecular weight.127, 128 The difference in nucleation modes can be attributed to the limiting effect from grafting points. Namely, when the molecular weight is low, the limiting effect from grafting points is stronger, and then the formation and growth of crystal nuclei are mainly through the intermolecular nucleation. When the molecular weight is high, this limiting effect is weaker and the molecular chains are much easier to bend and fold, and thus the molecular chains tend to grow into crystals through the intramolecular nucleation. Furthermore, as the molecular weight increases, the crystalline bonds gradually deviate from the initial orientation perpendicular to the filler to the orientation parallel to the filler, and eventually return to the orientation perpendicular to the filler again, as shown in Figure 9. This phenomenon can be explained by the crowding effect caused by the increase of the molecular weight.127
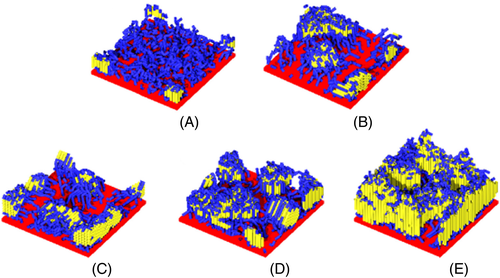
Reprinted with permission from Nie et al.127 Copyright (2018) Elsevier
5.3 Effect of interfacial interactions on polymer crystallization
Polymer-filler interaction is another important factor affecting the crystallization behaviors of polymer nanocomposites. Based on molecular simulations, the crystallization process and crystal morphology of polymer systems grafted onto two-dimensional nanofillers under different conditions have been reported, as displayed in Figure 10.129 For the systems with lower grafting density, the polymer-filler interaction plays a dominant role in the crystallization behaviors of these systems. Under this condition, the increase of the attractive interfacial interaction will cause the occurrence of heterogeneous nucleation and the shortening of the nucleation induction period, but the orientation of the chain segments will not be changed. Similar heterogeneous nucleation has also been observed in PLLA grafted on SiO2 by Wu and coworkers.118 For the systems with medium grafting density, the crowding effect caused by the increasing grafting density will drive more segments to move away from the interface, while the attractive interfacial interaction will cause the filler to adsorb more segments on the surface. Due to the competition of these two effects, the crystallization behaviors of the system are more complicated. The enhanced interfacial interaction can compensate for the conformational entropy loss caused by the restriction of the nanofiller, resulting in the increasing segments density in the interface regions and the enhanced nucleation ability. Therefore, the improved interfacial interactions can also shorten the nucleation induction period, but the system does not undergo heterogeneous nucleation. Li et al. also found this phenomenon in the study on the crystallization of PLLA on the surface of CNT.15 In addition, as the polymer-filler interaction increases, the nucleation mode changes from the intermolecular nucleation mode to the intramolecular nucleation mode. Under the competition of crowding effect and attractive interaction, the increase of interfacial interaction will cause crystals to gradually change from perpendicular to the filler surface to parallel to the filler surface. For systems with higher grafting density, the excessive crowding effect controls the crystallization process, and the crystallization ability is hardly affected by the polymer-filler interaction. Under this condition, the system does not undergo heterogeneous nucleation, and the crystal orientation of all systems tends to be perpendicular to the filler surface.
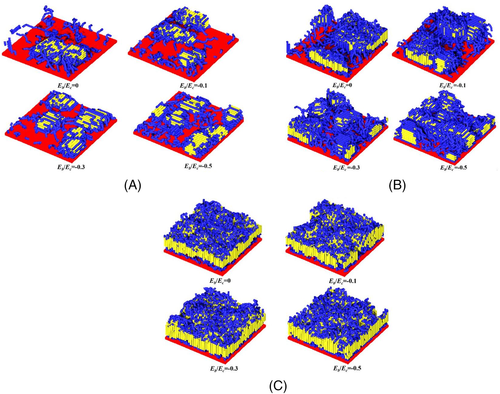
Reprinted with permission from Nie et al.129 Copyright (2017) Elsevier
6 SIMULATIONS OF FLOW-INDUCED CRYSTALLIZATION OF FILLED POLYMERS
In addition to adding nanofillers, applying shear flow to the system can also greatly promote the crystallization of polymers.132-137 In actual industrial production, a certain number of nanoparticles are usually added into the polymer matrix instead of a single nanoparticle, which may lead to the formation of filler networks. Some studies have shown that filler networks can impose strong confinements on the conformation and restrict chain mobility or diffusion.138, 139 Under this condition, polymer-filler interaction, filler content, and filler spacing will further affect polymer crystallization behaviors. Here, we summarize the research progress of the effect of nanofiller on oriented polymers.
First, the crystallization behavior of oriented polymer melts can be significantly affected by polymer-filler interaction. Rastogi et al. found that compared with the polymer system with zinconia nanoparticles, the polymer system with CNTs has stronger polymer-filler interaction, and then the shear-induced precursor is more stable.30 The strong interfacial interaction can effectively reduce the surface free energy of the crystal nuclei, thus promoting the nucleation process. However, excessive interfacial interaction decreases the mobility of the segments near the filler, thereby hindering the nucleation process. Therefore, only proper interfacial interaction can greatly improve the nucleation and crystallization ability of the polymer.31
Second, filler content also plays an important role in the crystallization process of oriented polymer melts. Previous simulation results indicated that as the filler content increases, the crystallization ability of filled polymer systems first increases and then decreases.31 On one hand, the increase of the filler content can lead to the increase of the interfaces, and then more chain segments can participate in the crystal nucleation based on heterogenous nucleation. On the other hand, due to the increase of the interfaces, more oriented chain segments would be absorbed by the fillers, and then the relaxation of the oriented chains would be hindered. Then, these chains that maintain a higher degree of segmental orientation would have higher nucleation ability. However, in the systems with very higher filler content, more segments with low mobility are adsorbed on the surfaces of the filler, and then the activation energy for short-distance diffusion increases, resulting in the increasing nucleation barrier and decreased nucleation ability. In experiments, it was found that the presence of the nanofiller networks with a high concentration of graphene oxide leads to a decrease in crystallization rate due to the restrictions on chain mobility or diffusion.140
Third, the filler spacing also affects the crystallization behavior of the oriented polymer melts. The simulation results showed that for systems with small filler spacing, crystal nuclei are first formed near the internal interface of the filler network.31 As the filler spacing increases, the restriction effect of the filler network on the oriented chains is weakened, and crystal nuclei no longer tend to form inside the filler network.31 Obviously, optimum filler spacing is needed for enhancing the polymer crystallizability.
In short, the synergistic effects of segmental orientation and nanofillers are closely determined by the polymer-filler interaction, filler content, and filler spacing. Therefore, only choosing appropriate values for these factors can effectively promote the crystallization process.
7 CONCLUSIONS AND PERSPECTIVES
In summary, the crystallization behaviors of various polymer nanocomposites under different conditions have attracted tremendous attention for decades. In this article, we summarized the crystallization behaviors of homopolymer, copolymer, and oriented polymer systems filled with nanofillers, as well as polymer systems grafted on nanofillers. First, the crystallization behaviors of the polymer nanocomposites, such as the crystalline morphology, strongly depend on the geometry of the filler. Second, due to the competition between microphase separation and crystallization of crystallizable blocks, the block copolymer nanocomposites exhibit unique crystallization behaviors, which can provide a new strategy for the development and design of sophisticated nanohybrid structures. Third, the preparation of grafted polymers can effectively avoid the agglomeration of nanoparticles, and its crystallization behavior is controlled by many factors, such as grafting density, molecular weight, interfacial interaction, and filler dimension. Fourth, the crystallization behavior of oriented polymers is codetermined by the degree of segmental orientation and the nanofillers. Under this condition, multiple parameters of the nanofillers, including polymer-filler interaction, filler content, and filler spacing, all play important roles in the crystallization of polymer nanocomposites.
The following are some perspectives based on the authors' comprehensions: (1) although the crystallization behaviors of polymer nanocomposites have been widely studied, the corresponding crystallization mechanisms still need further studied. In addition, the current simulation results show that there is no difference in the crystalline morphology between linear polymer nanocomposites and cyclic polymer nanocomposites, but there must be some differences in chain-folding modes due to the different chain topologies. Thus, we believe that more work is necessary to investigate the chain-folding mode in the crystallization process of cyclic polymer nanocomposites. (2) Hierarchical nanohybrid structures can be formed in block copolymers, and these structures supply opportunities for filler surface modification and functionalization. As a result, further researches on the crystallization behaviors of crystalline–crystalline diblock copolymers and multi-block copolymers are beneficial for the developments of more new hybrid structures. In addition, the flow-induced crystallization of block copolymers containing nanofillers is also a charming and interesting topic, the corresponding research results of which can provide theoretical guidance for the precise design and regulation of crystalline block copolymers and also enrich people's understanding of the complex and attractive nonequilibrium phase transition process. (3) For grafted polymers, in order to establish the relationship between the crystalline structures and the mechanical properties of grafted polymers, the investigations on the tensile behaviors and also the corresponding strain-induced crystallization of grafted polymer are needed. (4) For oriented polymers filled with nanofillers, the effects of the external force field (i.e., shear flow or elongation flow) on polymer nanocomposites still need further investigations. For instance, how the presence of the nanofillers affects the formation mechanisms of flow-induced precursors and the nucleation process.
ACKNOWLEDGMENTS
The financial support from the National Natural Science Foundation of China (No. 21404050), the Open Research Fund of CNMGE Platform & NSCC-TJ (No. CNMGE202101013), the Research Foundation of Jiangsu University (No. 14JDG059), and the Natural Science Foundation of Jiangsu Province (No. BK20190866) are gratefully acknowledged.