Development of flexible Li-ion batteries for flexible electronics
Funding information: University of California, Riverside
Abstract
We provide a critical review on the recent development of flexible lithium-ion batteries (FLIBs) for flexible electronic devices. The innovative designs of cell configuration for bendable and stretchable FLIBs, selection of active materials, and evaluation methods for FLIBs are discussed. The grand challenges for FLIBs are energy density and scale-up fabrication as demonstrated in the review. Furthermore, the lack of quantitative evaluation methods for FLIBs' performance and nondestructive tools to probe the mechanical degradation may significantly hinder the development of FLIB technologies. Perspectives for future research directions, based on the current state of progress, are discussed.
1 INTRODUCTION
The fast-paced electronics industry foresees a unique demand for portable and flexible electronic devices such as roll-up mobile phones, flexible watches, and smart garments. These flexible electronics require incorporated batteries that can seamlessly comply with the intended deformation, including bending, stretching, and twisting, without compromising their electrochemical and safety performance. Therefore, flexible batteries have emerged as a new interest from both industry and academia in the past two decades. Many companies such as LG Chem, ST Microelectronics, Blue Spark Technologies, and Enfucell have delivered flexible battery prototypes or products. For instance, NEC Corp. announced their 0.3 mm thick flexible organic radical battery for use in IC cards in 2012.1 Samsung SDI in 2015 launched a band battery for wearable devices that could withstand 50 000 bends with a bending radius of the size of a human wrist.2 The global market for flexible batteries was valued at USD 69.5 million in 2015 and is expected to reach USD 958.4 million by 2022.3
Lithium-ion batteries (Li-ion) are the primary choice as the power source for portable electronics. However, conventional designs of Li-ion batteries cannot satisfy the requirements of flexible electronics. For example, it was estimated that 100 days of wearing wearable electronics in active daily life is approximately equivalent to one million mechanical loading-unloading (deformation) cycles.4 It is clear that the design and fabrication of flexible Li-ion batteries (FLIBs) are extremely challenging. In this review, we will focus on innovations in the research and development of FLIBs from the aspects of structural design, materials of electrodes and electrolytes, evaluation and characterization methods. We will also discuss future research directions for FLIBs.
2 DESIGN OF FLEXIBLE ELECTRODES
The flexibility of FLIBs typically refers to their bendability, stretchability, and twistability. It is worthwhile to point out that these properties are rather nominal terms, instead of strict scientific definitions. The deformation of FLIBs in realistic scenarios is extremely complex. For example, when a thin band battery is bent, the top layer is subject to tensile stress along the bending tangential direction and the bottom layer is subject to compressive stress. The FLIBs can also be bent in two dimensions with a twist, which makes analysis of the stress-strain relationship and the resultant impact on battery performance even more complicated. Therefore, the term “flexibility” in the majority of the current literature on FLIBs is loosely defined. From a practical point of view, bending and stretching are the most common deformation modes concerning FLIBs. Thus, we will discuss the designs and materials of electrodes focusing on bendability and stretchability. The current designs are summarized in Table 1, and discussed in the following sections.
Electrode design | Advantage | Disadvantage | Reference | |
---|---|---|---|---|
Thin film | Stacked | Mature fabrication | Low cell capacity | 5, 6 |
Coplanar | Improved flexibility | Low cell capacity and complex fabrication | 7, 8 | |
Island-bridge | Relatively high cell capacity, good flexibility and durability | Incompatible with liquid electrolytes, complex fabrication | 9-14 | |
Miura fold | Excellent flexibility | Complex fabrication and limited durability | 15, 16 | |
Wavy electrodes | Excellent stretchability | Complex fabrication | 17, 18 | |
Percolating network | Excellent flexibility, self-healing | Complex fabrication and moderate conductivity of current collectors | 19-23 | |
Porous electrodes/current collectors | Versatile designs and relatively high cell capacity | Poor uniformity of the porous structures and lack of reliable characterizations | 24-32 | |
1D and textile | Excellent flexibility and versatile designs | Low cell capacity and complex fabrication | 33-42 |
2.1 Bendable electrodes

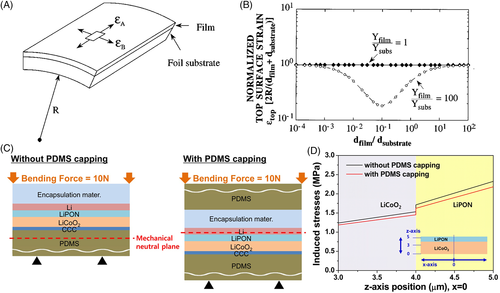
The selection of substrates is also important to the top strain, as illustrated in Figure 1B. With a more elastic substrate and a proper value of η, the top strain can be reduced by as great a factor as 9. The structure of realistic thin film FLIBs contains multiple layers, including encapsulation (packing), current collectors, electrodes, and electrolyte. When a multilayer slab is bent, tensile strain arises on the outer side and compressive strain arises on the inner side. As a result, there is a middle layer subject to minimum strain. Utilizing this property, the least elastic battery layer can be designed to withstand minimum mechanical strain by manipulating the encapsulation layer. Polydimethylsiloxane (PDMS), which is a crosslinked polymer with great flexibility and chemical inertness, has been the main material for encapsulation of bendable FLIBs for this purpose, as the example in Figure 1C 5 illustrates. The resulting reduction of stress under bending is shown in Figure 1D.5 Another type of thin film design is coplanar integrated Li-ion microbatteries.7, 8 In this design, all of the components are integrated on a single planar substrate, which displays superior flexibility to that of the traditional stacked thin film geometry.
Although the thin-film design can significantly improve the bendability of FLIBs,6 a clear disadvantage of thin-film FLIBs is their low capacity. Thin-film FLIBs also encounter difficulties in scaling up due to their complex and expensive processing methods. One strategy to address this challenge is to de-couple the flexibility of the current collector from that of the electrode. A successful design with this concept is the island-bridge structures9-12 displayed in Figure 2A-D, which contain “islands” of sandwiches of anode/electrolyte/cathode connected in series by flexible (metal) current collectors. These designs can increase the energy storage component up to 80% to 90% of the total cell volume.9 Similar strategies include the origami15 and kirigami16 design.
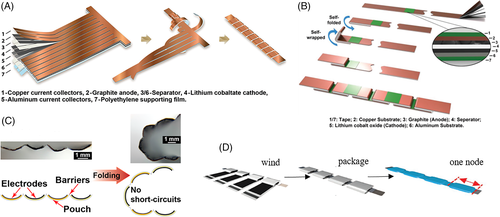
Another extensively explored design for bendable FLIBs is the use of porous-structured battery components, including electrodes and current collectors. It is believed that the Young's modulus of a porous structure decreases with increasing porosity.44-48 Porous structuring of active materials and/or current collectors can also increase adhesion strength, preventing delamination from deformation.49 Porous foams based on graphene or carbon nanotubes (CNTs) as flexible current collectors have received a lot of attention due to their excellent flexibility, conductivity, and three-dimensional (3D) structures that can host active materials.24-26 As shown in Figure 3A,24 Mo et al developed a graphene foam electrode with incorporated germanium quantum dots, which demonstrated identical lithiation-delithiation curves under zero-strain and 90° bending conditions. Porous active materials can also be deposited or grown on the flexible current collector to fabricate flexible electrodes.27, 28 As displayed in Figure 3B,28 Balogun et al reported a porous current collector composed of carbon cloth coated with an exfoliated porous carbon shell (CC@EC). NiCo2O4 nanowires were grown directly on the CC@EC current collector as the anode material with high gravimetric energy density and good deformability. The freestanding anode retained 84% of its specific capacity after 200 folding and 150 charge-discharge cycles. The porous CC@EC also served as the current collector for LiNi1/3Co1/3Mn1/3O2 (NMC) cathode in the full cell. Other representative porous electrodes include spinel lithium titanium oxide (Li4Ti5O12) nanowire array grown directly on titanium (Ti) foil,29, 30 porous lithium cobalt oxide (LiCoO2) nanosheet array,31 and porous LiMn2O4 nanowall array.32 However, it is worth noting that elastic deformation of porous materials depends on both intrinsic material properties and many structural parameters, and can be very complicated to model, design, and characterize. This presents a significant challenge to bendable (and stretchable) FLIBs based on porous structures: the local elasticity will be strongly affected by the uniformity of the porous structure, which can vary drastically within the FLIBs. Local deformation and the resulting mechanical fatigue can be extremely difficult to predict and monitor. Therefore, claims of successful designs of FLIBs with porous structure require careful validation.
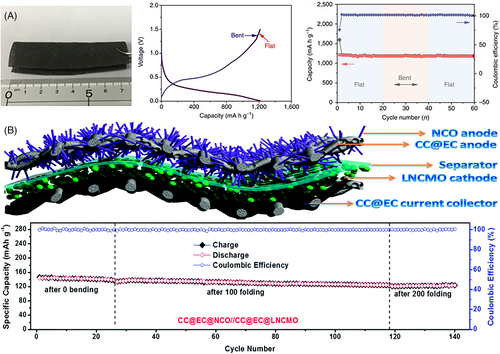
2.2 Stretchable electrodes

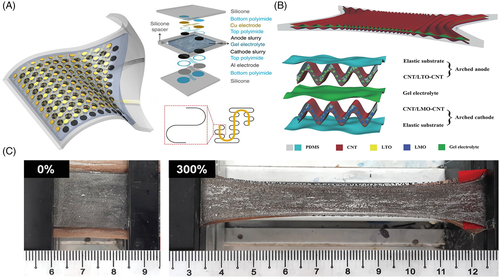
Among all stretchable designs, 1D structures and their resultant textile batteries may offer the best flexibility, especially in wearable applications. Fiber-shaped batteries, whether the configuration is parallel, twisting, or coaxial, can efficiently sustain deformation and can be transformed into textiles. The first fiber Li-ion battery was reported by Kim and coworkers in 201233 with a helically coaxial structure as shown in Figure 5A: Ni-Sn was electrochemically deposited on a copper spiral, onto which a polyethylene terephthalate separator was coated, after which an Al wire current collector was wrapped around it. LiCoO2 cathode composite was then coated onto the outer layer, followed by electrolyte impregnation and package coating. However, the use of liquid electrolyte in this battery may be problematic due to the potential leaking, and the conventional slurry coating method at the cathode limited its flexibility. The specific energy and energy density are also low due to the significant content of inactive materials. To overcome these challenges, much simpler electrode structures composed of CNT fibers have been produced and transformed to fabric FLIBs. Electrode materials including MnO2,34 Si/LiMn2O4,35 Li4Ti5O12/LiMn2O4,36 polyimide/LiMn2O4,37 and Li-ZnO/MoS238 have been incorporated into CNT fiber electrodes and evaluated. Peng and coworkers incorporated active materials into coiled CNT fibers as 1D stretchable electrodes.36, 39, 40 Specifically, a single string of coiled CNT fiber was produced by twisting a bundle of CNT fibers produced by spinning aligned CNT sheets. The coiled CNT fiber is capable of sustaining a large tensile strain during elongation due to the untwisting of the coiled fiber as displayed in Figure 5B.40 Metal-based coiled fibers have also been proposed to maintain electrochemical performance under strain.41 Hu and coworkers, utilizing similar materials, fabricated fiber FLIB via a 3D printing technique (Figure 5C) using elastic polymer electrolyte.42 Inspired by these 1D configuration designs, here we propose a FLIB design that combines the ideas of both thin film battery and fabric battery as illustrated in Figure 5D. The 1D anode (in blue) and 1D cathode (in red) are coated with a polymer electrolyte and woven into fabric with the anode as warp and cathode as woof or vice versa. An example of the possible anode and cathode is Si and LiCoO2 incorporated in CNT yarn, respectively. An elastomeric polymer can be used to encapsulate the battery to render bendability, stretchability, and twistability.
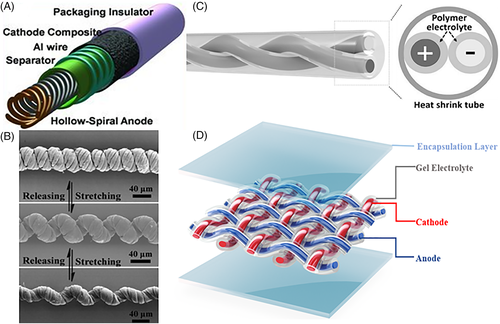
3 ELECTROLYTE FOR FLEXIBLE LI-ION BATTERIES
Although conventional organic liquid electrolytes offer high conductivity and good compatibility with electrodes, directly using them in FLIBs can be a considerable safety hazard considering the operation requirements for flexible electronics. Therefore, the majority of investigations of FLIBs employ polymer-based electrolytes due to their mechanical compliance and technical readiness. Based on the Li-ion conducting mechanism, polymer electrolytes can be either single-ion conductors that are ionomers with anions covalently tethered to the backbone, or dual-ion conductors which are mixtures of Li salts in polymers. Based on physical composition, polymer electrolytes can be categorized as solid-state polymer electrolyte (SPE), gel polymer electrolyte (GPE) containing solvent, and composite polymer electrolyte (CPE) incorporated with nanoparticles with or without solvent. Dual-ion conducting GPEs are routinely used in commercial Li-ion batteries. Therefore, it is the form of polymer electrolyte that faces the fewest technical challenges for adaptation to FLIBs. Typical polymers used in GPEs for FLIBs include poly(ethylene oxide) (PEO),13, 51, 52 polyimide,53 poly(ethyl cyanoacrylate),54 poly(vinylidene fluoride) (PVDF),55 poly(arylene ether),56 and poly(vinylidene fluoride-co-hexafluoropropylene) (PVDF-HFP).7, 12, 42, 57, 58 Despite its readiness for adaptation, potential leakage and flammability due to the organic solvents remain serious concerns. On the other hand, SPEs, particularly single-ion conducting SPEs, have been under extensive investigations for over 3 decades to improve their room-temperature Li-ion conductivity.59 These SPEs have significantly improved safety features, and their relatively easy processing procedure makes them great candidates for FLIB application.60, 61 However, their low ionic conductivity at room temperature and high contact resistance still remain as bottlenecks for practical applications. To overcome the low conductivity of SPEs, CPEs composed of SPEs and inorganic nanoparticles additives have been investigated.17, 36 In addition to conventional nanoparticle additives such as Al2O351, 62 and TiO2,63 inorganic Li-ion conductors were recently investigated as the additives in the CPEs, including NASICON Li1 + xAlxTi2 − x(PO4)3,64 Li1 + xAlxGe2 − x(PO4)3,65, 66 perovskite Li0.33La0.557TiO3,67 garnet Li6.4La3Zr1.4Ta0.6O12,68 Li6.75La3Zr1.75Ta0.25O12,69 and sulfide-based Li10GeP2S12.70 Yu and coworkers reported that 3D interconnected garnet Li6.28 La3Zr2Al0.24O12 provided a continuous Li-ion conducting pathway in PEO based electrolyte.71 Hu and coworkers reported an electrospun 3D nanofiber network of Li6.4La3Zr2Al0.2O12 incorporated in PEO polymer provided an interconnected pathway for Li-ion conducting.72 They also synthesized Al-doped garnet Li6.28Al0.24La3Zr2O11.98 textile by using cellulose textile as the template.73
In addition to polymer-based electrolytes for FLIBs, inorganic solid-state electrolytes have also been receiving increased attention due to their potential to enable Li metal anodes. To date, thin film lithium phosphorus oxynitride (LiPON)5, 74 is the most mature inorganic solid-state electrolyte for FLIBs, having been studied since 1997.75 However LiPON can only be used in thin film FLIB due to its low room-temperature ionic conductivity (approximately 10−6 S cm−1) and high Young's modulus (~77 GPa).76 Sulfide-based solid electrolytes face similar challenges in FLIBs due to their high Young's modulus (~20 GPa for Li2S − P2S577 and 37 GPa for Li10GeP2S1278) despite their high room-temperature ionic conductivities (>10−4 S cm−1).79 One method to mitigate the brittleness of the inorganic solid-state electrolytes is to use fiber reinforced composites. Nam et al fabricated poly(paraphenylene terephthalamide) (PPTA) nonwoven scaffold-reinforced Li3PS4 and Li10GeP2S12 composite electrolytes, which demonstrated promising performance in bendable FLIBs.80 Utilizing solid-state oxide electrolytes in FLIBs is even more challenging due to their higher Young's modulus (100-200 GPa for garnets Li7La3Zr2O1281 and perovskite type Li0.33La0.57TiO382) and moderate room-temperature ionic conductivity (10−5 to 10−3 S cm−1).83 Flexible garnet type Li7La3Zr2O12 (LLZO) was achieved via flame spray pyrolysis and a casting method.84 Large area (2 × 2 cm2) flexible LLZO thin film (20-30 μm) was fabricated with good ambient ionic conductivity at approximately 0.2 mS cm−1. He et al synthesized glass ceramic Li1.5Al0.5Ge1.5(PO4)3 (LAGP) fibers using a melt-spun method. This LAGP fiber shows excellent flexibility and good room-temperature ionic conductivity at 10−3 S cm−1, and as such can potentially be used as reinforcement for polymer electrolytes in FLIBs.85
Aqueous Li-ion electrolytes are a promising alternative to organic electrolytes due to their improved safety and environmental benignity. Because of this, aqueous Li-ion electrolytes for FLIBs have also been investigated as first reported in 2016.86 Due to the narrow electrochemical window of conventional aqueous electrolytes (~2.6 to 3.8 V vs Li+/Li), the choices of active materials for FLIBs are limited. Spinel lithium manganese oxide (LiMn2O4) has been studied as the cathode material (1 V vs SHE) in aqueous electrolyte FLIBs.37, 86-88 Polyimide37 (−0.56 V vs SHE), LiTi2(PO4)386, 87 (−0.5 V vs SHE), and polypyrrole coated LiV3O888 (−0.5 V vs SHE) have been studied as the flexible anode materials. Recently discovered “water in salt” concentrated aqueous electrolytes can expand the electrochemical stable window to higher than 3 V.89 This is a significant advance for aqueous Li-ion electrolytes, and enables more choices of active materials. Wang and coworkers reported a FLIB with “water in salt” aqueous electrolyte and symmetric LiVPO4F electrodes.90 A flexible high-voltage supercapacitor with high-concentration aqueous electrolyte was additionally reported by Tang and coworkers.91
4 EVALUATION OF FLEXIBILITY
Reliable and quantitative evaluation of the flexibility of FLIBs is key to the realization and commercialization of this technology. However, most of the evaluation methods reported in current literature remain coarse. As mentioned above, bending and stretching are the two most common deformation tests. Typically, stretchability can be evaluated by fixing the ends of a FLIB onto two fixtures which are moved back and forth by a linear actuator as displayed in Figure 6A.17 The strain on the device can be expressed as ε = (L/Lo) − 1, where L is the device length after elongation and Lo is the initial length. Three parameters can be used to describe the bendability as illustrated in Figure 6B 92: R is the radius of the bending curvature, θ is the bending angle, and L is curvature end-to-end distance. According to Equation (1), the radius of bending curvature can directly reflect the extent of bending. To obtain the bending radius, the bendable FLIB can be bent around a cylinder with a given diameter,94 and then R can be calculated from the geometry of the bending. θ and L are correlated with R and can be measured in the same fashion. Notably, this method (Figure 6B) does not fully characterize the flexibility of FLIBs designed to comply with arbitrary deformation as illustrated in Figure 6C.93

Currently, there have been few reports on quantitative methods to measure the robustness of FLIBs (ie, electrochemical properties, mechanical integrity, and safety features) under deformation. The most popular demonstration is to show that the power supply of an electric appliance such as LED light is not interrupted during the repeated deformation. However, this method is not reliable and can be misleading since it is unable to detect subtle electrochemical and mechanical degradation within the FLIBs.
5 PERSPECTIVES
We have briefly reviewed the key progress in the development of FLIBs for flexible electronic devices. From the materials perspective, the key challenges are the lack of intrinsically flexible active materials and the lack of fabrication methods that are both scalable and reliable. Electrolyte can be considered a lesser challenge since GPEs are feasible for use in most of the designs of FLIBs in spite of potential challenges concerning packing and mechanical robustness. LiPON is also a mature electrolyte for thin film bendable FLIBs suited for niche applications that do not require high-capacity batteries. Under the current framework of Li-ion chemistry (ie, carbon anode and lithium metal oxide cathodes), achieving high-capacity FLIBs can be very difficult. On the other hand, Li metal, a high-capacity anode with excellent ductility, is now beginning to attract attention as a promising anode material for FLIBs.34, 41 However, Li faces numerous challenges such as interfacial stability associated with either polymer electrolytes or inorganic solid-state electrolytes.
Another significant challenge is how to probe subtle electrochemical and mechanical degradations of the FLIBs under the simulation of real-world deformation. Quantitative and reliable operando methods during the mechanical testing of FLIBs need to be developed, as illustrated in Figure 6D which uses a bendable Li-ion battery as an example. The most straightforward and accessible method by which to probe the change of electrochemical properties during repeated bending (and other types of deformation) is electrochemical impedance spectroscopy (EIS), which measures the internal resistance change often associated with material and structure degradation and electrode/electrolyte interface change. EIS may not be sensitive enough to detect very subtle change with in the batteries, which is why high-resolution imaging techniques can be additionally beneficial. Recent studies demonstrated that operando X-ray computed tomography can be used to characterize the structural evolution and failure mechanisms of Li-ion batteries.95-98 This nondestructive technique can be used in the evaluation of FLIBs to clearly reveal cracks and fractures with μm-level resolution in the top surface or cross-section of the electrodes. Ultrasonic scans are another widely used imaging technique worth considering for this application. It can be used to detect the reflected and scattered waves of the internal defect due to the difference of acoustic impedances between the cracks and dense materials.99 The ultrasonic transducer can be placed on top of the FLIBs surface during the bending test. However, ultrasonic detection is only suitable for FLIBs with ultrathin structures100 due to the low penetration of high frequency ultrasonic waves and the low resolution of low frequency ultrasonic waves. In addition to imaging techniques, temperature profiles of the FLIBs during charge-discharge under deformation can also be very informative. Lock-in thermography101 using an infrared camera can be used to identify subsurface defects. Defects caused by deformation lead to a heterogeneous current density distribution that can be detected by the temperature responses. An acoustic emission system was also reported to be capable of detecting the cracks or fractures caused by local stress in Li-ion batteries.102, 103 A piezoelectric acoustic emission sensor can be applied to the FLIB surface to record emanating mechanical vibrations.
In summary, flexible Li-ion batteries for flexible electronic devices are still at an early stage of development, particularly for high-capacity FLIBs. Due to the lack of intrinsically flexible active materials, the development of FLIBs must rely on creative designs of flexible electrodes and cell configurations. A serious challenge for future development is the lack of standards and standardized methods by which to evaluate the degradation of FLBs. Quantitative operando techniques to probe the degradation mechanisms of FLIBs must be developed.
ACKNOWLEDGMENTS
The authors acknowledge the support from University of California, Riverside.
CONFLICT OF INTEREST
The authors declare no conflict of interest.
Biographies
Yifan Zhao obtained his BS degree from Zhejiang University and MS degree from University of Southern California. He is currently a PhD student in the Materials Science and Engineering Program at University of California – Riverside. His research interests are lithium-sulfur batteries, nickel-rich cathode materials for Li-ion batteries, and multivalent rechargeable batteries.
Juchen Guo is an Associate Professor in the Department of Chemical and Environmental Engineering and Materials Science and Engineering Program at University of California – Riverside. He earned his Bachelor's degree from Zhejiang University in 1999 and his PhD degree from University of Maryland in 2007, both in chemical engineering. He performed postdoctoral research at University of Maryland from 2007 to 2011 and Cornell University from 2011 to 2012. He was the recipient of 2014 Hellman Fellowship and 2018 NSF CAREER Award. His research interests are interfacial phenomena and material properties in electrochemical energy storage systems.