Enhancing the Mechanical Performance of Laminated Silicone Bearings With Fumed Silica and Selected Primers
ABSTRACT
Compared with conventional elastomers, silicone elastomers offer superior thermal stability, durability, and enhanced resistance to environmental factors, making them promising candidates for seismic isolation bearing elastomers. However, their relatively low hardness and weak bonding potential have hindered their widespread application. In this context, this study examines the effect of fumed silica as a reinforcing filler on enhancing the mechanical properties of silicone elastomers, as well as the influence of three selected primers on the interlayer bond strength in laminated silicone bearings. Shore A hardness tests revealed that fumed silica increased hardness by up to 185%, with CX32-2036 cured silicone elastomers demonstrating superior performance. Lap shear tests revealed that the AQ1 primer improved the bond strength by up to 400%, particularly when combined with CX32-2036 cured elastomers. Quasi-static shear tests confirmed that prototypes fabricated with optimized filler and primer combinations exhibited excellent hysteretic behavior, consistent damping ratio, and stable shear stiffness. These findings demonstrate the potential of silicone elastomers, enhanced with fillers and primers, as effective materials for next-generation seismic isolation bearings. Further studies are recommended to evaluate long-term durability and dynamic performance under real-world conditions.
1 Introduction
Despite their maintenance-free nature, cost-effectiveness, and extended seismic isolation performance, the long-term reliability of elastomeric seismic isolation bearings is crucial for safeguarding infrastructure during earthquakes [1]. However, among the widely used materials in elastomeric bearings, such as natural rubber and high-damping rubber, durability under harsh environmental conditions remains a persistent challenge [2, 3]. Factors such as crack formation induced by ultraviolet radiation, the Mullins effect, and temperature-dependent and strain-rate-dependent performance compromise their predictability and effectiveness over extended service periods [4, 5].
Numerous studies have focused on experimental solutions to address these limitations, with a view to extending the lifespan and improving the mechanical properties of elastomeric bearings [6, 7]. As civil engineering moves toward developing the next generation of seismic isolation devices, incorporating materials that are not only durable and maintenance-free but also cost-effective, and easy to design and deploy becomes increasingly important. Efforts to increase the performance of elastomeric bearings have typically focused on modifying material properties through fillers, improving adhesion between layers, or exploring alternative materials.
While conventional fillers such as carbon black and calcium carbonate can improve certain mechanical properties, limitations including degradation under ultraviolet radiation exposure or reduced mechanical performance, make them suboptimal for seismic isolation applications [4, 5]. However, the discovery of advanced elastomers has shown promise and one material that stands out in addressing these needs is silicone elastomer.
The ability of silicone elastomers to withstand temperatures ranging from −100°C to 350°C while maintaining their mechanical properties [8, 9], along with their resistance to ultraviolet radiation, oxidation, and weathering [8, 10], makes them highly attractive alternatives to conventional elastomers. Furthermore, silicone elastomers are inherently inert, offering the added benefits of recyclability and being environmentally friendly [10], which constitute important considerations in modern sustainable engineering practices.
Despite the promising attributes of silicone elastomers, their potential in seismic isolation bearing applications remains underexplored. Research, especially in the fields of dental care and aircraft manufacturing, has produced encouraging results, particularly in terms of mechanical performance and resistance to environmental factors [11-14]. However, for bearing applications, substantial challenges remain, particularly in terms of increasing the hardness of the elastomers to bear higher compression loads and achieving strong bonds with other materials [9].
Originally introduced as a means of reducing production costs, fillers play a pivotal role in increasing the hardness and enhancing tensile strength, tear resistance, damping performance, and abrasion resistance of elastomer matrices [9, 15, 16]. By reinforcing elastomers, fillers can also improve their thermal stability and reduce their susceptibility to environmental factors such as ultraviolet radiation and oxidation [17]. Moreover, fillers can improve the processability of a material and endow it with specific functional properties, such as enhanced electrical conductivity, gas impermeability, or flame retardancy, depending on the filler type and application [8, 18, 19].
Various fillers, including carbon black, silica, clay, calcium carbonate, talc, and more recently, nanofillers such as carbon nanotubes and graphene, have been used to enhance the mechanical properties of elastomers. Carbon black is known for its ability to enhance mechanical reinforcement and electrical conductivity, but it can degrade under ultraviolet radiation exposure and requires careful dispersion [20, 21]. Silica improves tensile strength and tear resistance while maintaining transparency, although it can be difficult to disperse uniformly [14, 22]. Clay enhances barrier properties but may increase stiffness and reduce elasticity [23]. Calcium carbonate is cost-effective and improves stiffness but offers limited reinforcement [24]. Talc enhances processing and surface properties but may reduce elongation at break [25]. Nanofillers such as carbon nanotubes and graphene provide exceptional mechanical, thermal, and electrical properties but are expensive and challenging to incorporate uniformly [26].
However, fumed silica has emerged as one of the most promising options for enhancing the performance of silicone elastomers. Its high surface area allows for increased interaction with the silicone matrix, which in turn improves the tensile strength and tear resistance without notably influencing the elongation at break of the resulting composite material [24, 27]. The interaction between the filler and the silicone chains creates a robust network that restricts chain mobility, enhancing the overall mechanical performance [28]. Additionally, in contrast with carbon black, fumed silica maintains the transparency of silicone elastomers, which is beneficial when monitoring the integrity of the elastomer bulk. Furthermore, its inertness aligns well with the chemical properties of silicone molecules.
In parallel, one of the primary challenges in using silicone elastomers for seismic isolation applications arises from their inherent inertness, which poses a significant obstacle when attempting to achieve a strong bond with other substrates [29-31]. In laminated elastomeric bearings, this bond is essential for the effective transfer of loads and for maintaining their structural integrity under seismic forces. To increase the bond strength between silicone elastomers and metals, primers are commonly used. Primers act as adhesion promoters, creating a chemically stable interface between the elastomer and the substrate [32]. In this context, the primers suited for silicone elastomers can be broadly categorized into two main types: silane-based and resin-based. Silane-based primers employ silane coupling agents to form covalent bonds with hydroxyl groups on the surface of metals, creating a strong and durable interface [33]. These primers are particularly effective for bonding silicone elastomers to glass, ceramics, and metals [31, 34].
Resin-based primers, on the other hand, rely on silicone resin polymers to form an adhesive layer through mechanical interlocking and chemical bonding, offering a different approach to improving bond strength by offering flexibility and toughness, which is especially suitable for applications requiring elasticity [35].
Thus, this study aims to investigate the potential of fumed silica as a filler in silicone elastomers to enhance their mechanical properties. Additionally, the effectiveness of three different primers—AQ1, NO4, and PPX—in improving the bond strength between silicone elastomers and metal substrates is evaluated. To these ends, a systematic experimental approach was employed to assess the effectiveness of fumed silica and selected primers in improving both the internal structure of the elastomer and its adhesion to steel substrates. Furthermore, as a real case verification, quasi-static shear testing of a set of bearing prototypes designed from selected filler proportions and primer combinations was conducted.
2 Materials and Methods
2.1 Elastomer Formulation and Filler Addition Processes
The silicone elastomers used in this study were composed of the silicone monomer KE1316 cured at room temperature with either the CAT1316 curing agent or the CX-32-2036 curing agent, which were all provided by Shin Etsu Chemicals Co. Ltd. KE-1316 is a vinyl-terminated polydimethylsiloxane that cures via platinum-catalyzed hydrosilylation, forming Si–C bonds between vinyl and Si–H functional groups. CAT-1316 is a standard platinum-based catalyst formulation that, when combined with KE-1316 at a 10% ratio, initiates a moderate crosslinking reaction yielding a soft elastomer with relatively low Shore A hardness. In contrast, CX-32-2036 acts as a methylhydrosiloxane-dimethylsiloxane copolymer, rich in Si–H functionalities. When mixed with KE-1316, assuming the presence of residual or added platinum catalyst, it promotes a denser crosslink network due to the increased availability of reactive Si–H groups.
The preparation process began by mixing the silicone monomer KE1316 with one of the curing agents in proportions of 10%. Hence, two batches of elastomers were prepared: the monomer was mixed with the CAT1316 curing agent for batch H1 and with the CX-32-2036 curing agent for batch H2 at a mixing rate of 200 rpm. After mixing, the resulting blend was placed in a vacuum chamber for 30 min to remove entrapped air bubbles. This deaeration process is critical for preventing voids in the elastomer, which could compromise its mechanical integrity. Following deaeration, the mixture was allowed to cure in a low-temperature incubator at 23°C (room temperature) for 24 h to ensure full polymerization of the silicone elastomer.
To improve the hardness of the resulting elastomers, fumed silica, was incorporated into selected batches as a reinforcing filler. The preparation of the filled silicone elastomers followed the same procedure as the unfilled ones, with the additional step of adding fumed silica in a proportion of 1.25 or 2.50 phr (per hundred rubber). The fumed silica was mixed with the silicone monomer and curing agent mixture before deaeration. Proper blending was ensured to achieve a homogeneous dispersion of the filler throughout the silicone matrix.
Shore A hardness tests and uniaxial tensile tests were conducted to evaluate the effectiveness of fumed silica in enhancing the mechanical properties of the resulting elastomers. In this study, following the ASTM D2240 specifications, the Shore A hardness of both filled and unfilled silicone elastomers, which is related to their equivalent elastic modulus and viscoelastic behavior, was measured using a Shore A durometer. Test samples were prepared by vulcanizing silicone elastomer mixtures in molds to create uniform pieces, which were then conditioned at room temperature for 24 h to ensure consistent testing conditions. The samples were fabricated as smooth-surfaced, parallelepipedal blocks with nominal dimensions of 50 × 50 × 20 mm. To avoid potential anomalies and ensure the reproducibility of the experiment, 12 elastomer blocks were prepared for each batch. Furthermore, five measurements were taken at different locations on each block, with the arithmetic mean of these values representing the Shore A hardness of the sample.
Additionally, uniaxial tensile tests were conducted to evaluate the tensile properties of the prepared silicone elastomers, including their tensile strength, elongation at break, and equivalent modulus at 300% strain. For those tests, the JIS K 6251 standard, prepared on the basis of ISO 37 and corresponding to ASTM D 412, was used. To avoid any eventual singularity, for each batch of elastomer, 12 test samples were prepared using a dumbbell-shaped No. 7 cutting die to create uniform samples. On each sample, two dots were placed at each extremity of the gauge to observe the gauge deformation easily. The prepared samples were clamped into the grips of an MCT 1150 001 tabletop tensile compression testing machine. The machine applied a uniaxial tensile force at a constant strain rate of 100 mm/min until the sample ruptured. Using a digital camera in addition to integrated measurement instruments, the force and elongation were recorded continuously during the test.
2.2 Primer Application and Bond Strength Assessment
To achieve strong and reliable bonds, primers were used to enhance the adhesion between the silicone elastomers and metal surfaces. Before the application of primers, both substrates were cleaned from contaminants. The cleaning solvent used was mostly composed of acetone. Additionally, abrasion with fine-grit sandpaper to create a slightly roughened surface can increase the metal surface area for bonding.
Three different primers—AQ1, NO4, and PPX—were selected. AQ1 is an n-hexane solvent-based silicone resin primer provided by Shin Etsu Chemicals and is designed for use on glass, metal, enamel, tile, plastic, and similar surfaces. The NO4 primer is a silane-based primer provided by Shin Etsu Chemicals suitable for use on resin, metal, and glass with n-heptane solvents. The PPX primer is a resin-based primer provided by Cemedine Co. Ltd. for cyanoacrylate adhesives, glass, metal, plastic and other surfaces, and contains n-heptane solvents. Each primer was placed in a pen-style container and was applied by pressing the pen tip against the substrate, ensuring an even and thin coating. The primers were applied at room temperature, and no drying process was needed, as the pens ensured good thickness and instant drying.
Lap shear tests were performed to assess the shear strength of the silicone elastomer and metal substrate bonds, following the ASTM D1002 specifications. To ensure that the results do not account for any eventual singularity, 12 samples were prepared and tested for each combination of primer and silicone elastomer. Each test sample was prepared by bonding two steel pieces with a thin layer of silicone elastomer, following the previously described primer application procedures. The lap shear tests were conducted via the MCT 1150 001 tabletop testing machine, which applied a shear force parallel to the bond interfaces, at a constant strain rate of 50 mm/min until failure occurred.
2.3 Quasi-Static Shear Tests for Prototype Evaluation
Alongside the previous experiments, quasi-static shear tests were conducted to evaluate the mechanical performance of silicone elastomeric bearing prototypes under constant compression and simple shear loading conditions. The results from the lap shear tests were assessed to identify the best-performing combinations of silicone elastomers and primers, which were then used to fabricate the bearing prototypes.
As depicted in Figure 1, the quasi-static testing apparatus consisted of a rigid reinforced metallic beam, supported by two reinforced metallic columns and a basement block. A vertical actuator, a Riken D5-50 hydraulic pump with a load capacity of 500 kN and a maximum stroke of 50 mm, was fixed under the beam to provide a constant vertical load. A horizontal actuator, an SFL-20-350 load cell with a maximum stroke of 200 mm and a loading capacity of 200 kN, was positioned on one of the columns to apply cyclic shear displacements. This actuator was controlled by a servo controller 4830, enabling precise control of both displacement and force. The test specimen was positioned between the vertical actuator and the basement block, with a sliding rail system installed to ensure quasi-frictionless movement during testing. Additionally, two laser displacement sensors were positioned at the top and lower loading plates to verify the real-time displacement values.
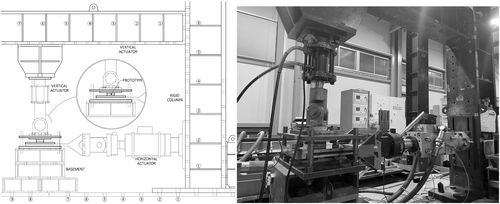
The design load is equivalent to a compression of 6 MPa, whereas the ultimate load is equivalent to 9 MPa. As depicted in Figure 2, each prototype was square-shaped, with dimensions of 100 mm by 100 mm, resulting in a shear surface area of 10,000 mm². Each bearing had a total thickness of 45 mm and was composed of a structured layer assembly of 15 mm between two 15-mm-thick loading plates. The structured layer assembly included four 3-mm-thick elastomer sheets laminated with three 1-mm-thick steel plates.
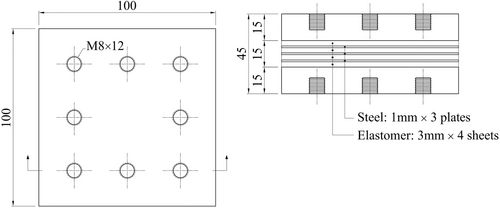
The loading method consisted of a combination of compression and cyclic shear. In accordance with ASTM D 4014 compression test protocols, a vertical compressive force was incrementally applied until reaching the design compression stress of 6 MPa, which was then maintained for 30 s. During this stage, the deflection was measured to calculate the compression stiffness. Subsequently, the load was incrementally increased to reach the ultimate compression stress of 9 MPa, followed by a visual inspection.
After inspection, the vertical load was reduced back to match the design compression stress, and cyclic shear displacements, following a given loading protocol were applied. The loading rate was maintained at 2 mm/s, and each displacement cycle was repeated three times to account for potential variations in the mechanical response due to cyclic fatigue. After completing three cycles at a given shear amplitude, the loading amplitude was increased incrementally, corresponding to 50% strain, until the bearing either ruptured or exhibited unacceptable performance degradation.
3 Experimental Results
3.1 Hardness Shore A Tests
Figure 3 shows the hardness Shore A test results for each batch described in Table 1. The results indicate that the unfilled elastomers cured with CAT1316 exhibited a Shore A hardness of approximately 18. In contrast, elastomers cured with CX32-2036 demonstrated a slightly higher initial Shore A hardness of approximately 21. The difference in reactivity and network architecture between the two systems, particularly the Si–H content and the nature of the catalyst, thus provides a clear mechanistic rationale for this observed variation in hardness.
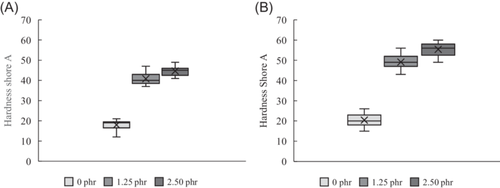
No | Silicone material | Curing agent |
---|---|---|
H1 | KE1316 | CAT1316 |
H2 | KE1316 | CX32-2036 |
For both batches, the results showed that fumed silica impaired a notable increase in Shore A hardness in the filled elastomers. This increase is very pronounced as the filler proportion rises from 0 to 1.25 phr but the rate of increase diminishes from 1.25 to 2.50 phr. This pattern suggests a diminishing reinforcement effect at higher filler concentrations, likely due to saturation of the reinforcing network within the silicone matrix. At a filler proportion of 2.50 phr, the filled elastomers cured with CAT1316 reached a Shore A hardness of 50, whereas those cured with CX-32-2036 reached a hardness Shore A of approximately 60, corresponding to increases of 180% and 185%, respectively.
3.2 Uniaxial Tensile Tests
No | Silicone material | Curing agent | Filler (phr) |
---|---|---|---|
T1 | KE1316 | CAT1316 | 0 |
T2 | KE1316 | CAT1316 | 1.25 |
T3 | KE1316 | CAT1316 | 2.50 |
T4 | KE1316 | CX32-2036 | 0 |
T5 | KE1316 | CX32-2036 | 1.25 |
T6 | KE1316 | CX32-2036 | 2.50 |
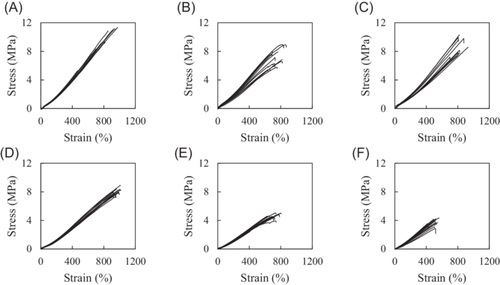
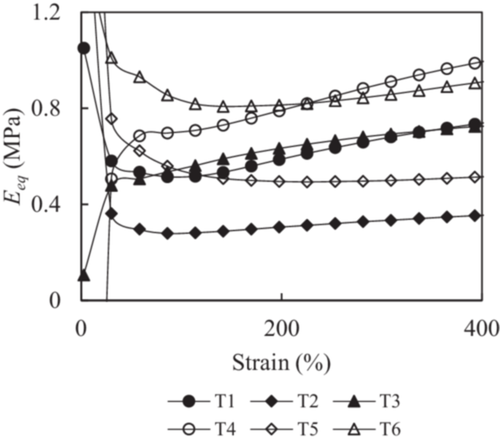
No | Eq. modulus (MPa) |
---|---|
T1 | 0.67 |
T2 | 0.33 |
T3 | 0.69 |
T4 | 0.90 |
T5 | 0.50 |
T6 | 0.85 |
where, is the force measured at a given strain. and are the initial width and initial thickness of the gauge, respectively. is the gauge length at a given stress, and is the initial gauge length.
In Figure 4, the comparison of curves (a) and (d) confirmed that the silicone elastomers cured with CAT1316 exhibited greater elongation at break, reaching an average of 1000%, whereas those cured with CX32-2036 demonstrated elongation at break of approximately 800%. The average tensile strength of the CAT1316-cured elastomers was approximately 7.50 MPa, whereas the CX32-2036-cured elastomers presented a higher tensile strength reaching 12 MPa. Moreover, in Figure 5, batches featuring CX32-2036 exhibited higher equivalent elasticity moduli than those cured with CAT1316. These findings confirm that CAT1316 produces a more flexible and ductile material, whereas CX32-2036 results in a stiffer and less flexible elastomer. At 2.50 phr of fumed silica, the CAT1316 cured elastomers exhibited, on average, an elongation at break of 500% and an ultimate stress of approximately 4 MPa. At the same filler proportion, the elastomers cured with CX32-2036 demonstrated, on average, an elongation at break of approximately 800% and an ultimate stress of approximately 10 MPa.
3.3 Lap Shear Tests
Lap shear tests were conducted to evaluate the bond strength between the silicone elastomers and steel substrates, with different primers used to enhance adhesion. The samples were prepared by bonding thin layers of silicone elastomer with steel substrates using three different primers: AQ1, NO4, and PPX. The silicone monomer used was KE1316, which was cured with either CAT1316 or CX32-2036 curing agents and filled with a given percentage of fumed silica as described in Table 4.
No | Silicone material | Curing agent | Filler (phr) | Adhesive primer |
---|---|---|---|---|
S1 | KE1316 | CAT1316 | 0 | AQ1 |
S2 | KE1316 | CAT1316 | 0 | NO4 |
S3 | KE1316 | CAT1316 | 0 | PPX |
S4 | KE1316 | CX32-2036 | 0 | AQ1 |
S5 | KE1316 | CX32-2036 | 0 | NO4 |
S6 | KE1316 | CX32-2036 | 0 | PPX |
S7 | KE1316 | CX32-2036 | 1.25 | AQ1 |
S8 | KE1316 | CX32-2036 | 1.25 | NO4 |
S9 | KE1316 | CX32-2036 | 1.25 | PPX |
S10 | KE1316 | CX32-2036 | 2.50 | AQ1 |
S11 | KE1316 | CX32-2036 | 2.50 | NO4 |
S12 | KE1316 | CX32-2036 | 2.50 | PPX |
The lap shear test samples were fixed on the testing machine, and a constant displacement rate of 50 mm/min was applied until failure occurred. The applied loads and the corresponding displacements were recorded to determine the lap shear behavior of each sample, as reported in Figure 6.
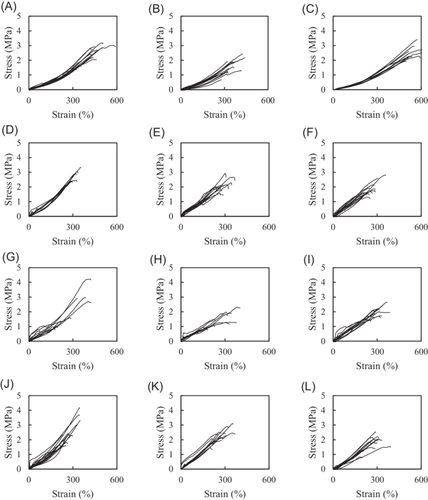
For comparison, two additional batches of lap shear test samples, bonded with an epoxy resin-based adhesive only, were fabricated and tested. Their compositions are summarized in Table 5 and the corresponding test results are illustrated in Figure 7.
No | Silicone material | Curing agent | Filler (phr) | Adhesive primer |
---|---|---|---|---|
S13 | KE1316 | CAT1316 | 0 | — |
S14 | KE1316 | CX32-2036 | 0 | — |
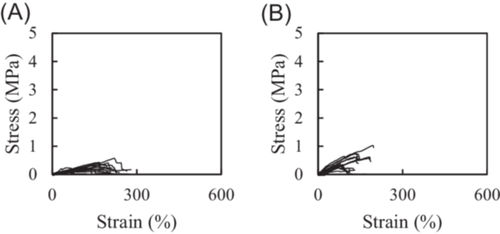
Overall, the average rupture strains of the primed samples ranged from 220% to 550%. The batches featuring the AQ1 primer presented the highest lap shear strength, with average values of 2.20 MPa. The samples enriched with the NO4 primer demonstrated moderate lap shear strengths, with average values as low as 1.90 MPa, whereas the samples enriched with the PPX primer displayed comprehensive lap shear strengths, with average values of 2.02 MPa. The rupture mode of the samples enriched with the AQ1 primer was mostly cohesive, with a percentage above 90%. The NO4 primer provided the least effective bond strength, especially when combined with the CAT1316 curing agent.
Its rupture was mostly adhesive, with a percentage greater than 80%. The PPX primer provided stable and consistent lap shear behavior with a cohesive failure mode of 100%.
3.4 Quasi-Static Shear Tests
The combinations selected for the quasi-static tests, summarized in Table 6, were chosen based on two main reasons. First, although the samples assembled with the PPX primer did not consistently yield the highest shear strengths, they demonstrated stable and consistent behaviors. Second, the chosen range of filler contents enables a thorough evaluation of the influence of the filler on the bearing performance, and the inclusion of both curing agents in the selected combinations ensures a comprehensive assessment of their impacts.
No | Silicone material | Curing agent | Filler (phr) | Adhesive primer |
---|---|---|---|---|
P3 | KE1316 | CAT1316 | 0 | PPX |
P6 | KE1316 | CX32-2036 | 0 | PPX |
P9 | KE1316 | CX32-2036 | 1.25 | PPX |
P10 | KE1316 | CX32-2036 | 2.50 | AQ1 |
P11 | KE1316 | CX32-2036 | 2.50 | NO4 |
P12 | KE1316 | CX32-2036 | 2.50 | PPX |
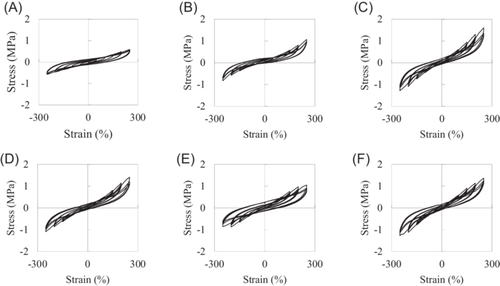
where, represents the applied shear force, represents the contact area between each interface, , the shear displacement and , the total thickness of all elastomeric layers.
P3, made from an unfilled elastomer cured with CAT1316, exhibited the lowest maximum shear stress, which was 0.59 MPa at 250% strain. In contrast, P6, which used a CX32-2036 cured unfilled elastomer, achieved a stress of 1.07 MPa. P11, bonded with primer NO4, experienced gradual bond failure, resulting in lower performance than other prototypes with the same filler proportion, reaching a maximum stress of 1.05 MPa. P9, P10, and P12 demonstrated excellent shear behavior without any bond failure, each achieving a maximum stress greater than 1.50 MPa.
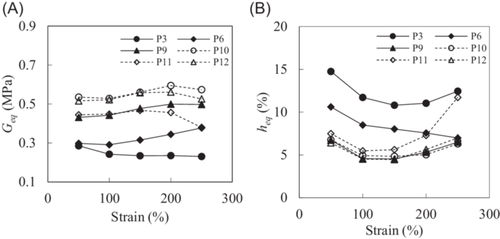
where, represents the area delimited by the hysteresis curve and , the equivalent strain energy defined between the extreme strains (−) and (+).
Figure 9a reveals that the equivalent shear coefficients increase with the incorporation of fumed silica filler and are consistently higher in samples cured with the CX32-2036 agent. For instance, prototype P3 displays the lowest moduli, ranging from 0.23 to 0.29 MPa across the strain levels. In contrast, prototype P10 shows a significantly higher range of 0.53–0.59 MPa. This trend confirms the reinforcing effect of the filler and the more robust crosslink network produced by CX32-2036, both contributing to higher shear stiffness.
Figure 9b further illustrates the inverse relationship between shear stiffness and damping behavior. P3 exhibits the highest damping ratio, peaking at approximately 14.75%, which gradually decreases with increasing filler content and with the use of CX32-2036. The stiffest prototypes (P10–P12) consistently yield the lowest damping values, with minimums around 4.45%–6.42%. This indicates that while filler addition and crosslinking density enhance load-bearing capacity, they simultaneously limit the material's energy dissipation ability, which constitutes an important trade-off in seismic isolation design. Notably, P11's damping ratio shows irregularities, likely due to premature debonding caused by the NO4 primer, emphasizing the importance of interfacial adhesion quality in preserving damping performance.
4 Discussion
4.1 Result Interpretation
The findings of this study provide compelling evidence of the potential for silicone elastomers, enhanced with fumed silica and primers, to address the challenges associated with seismic isolation bearings. The discussion is organized around the three primary aspects of the study: mechanical property enhancements, interlayer adhesion improvements, and the overall performance of bearing prototypes under quasi-static loading.
The addition of fumed silica to silicone elastomers resulted in increased Shore A hardness, which can be correlated with improved load-bearing capacity. This enhancement is particularly advantageous in elastomers cured with CX32-2036, suggesting that this combination could be suitable for applications requiring greater load bearing capacities. The increase in hardness Shore A with increasing filler content followed a logarithmic trend: very pronounced initially and leveled off at higher filler proportions. This behavior can be attributed to the high crosslinking density achieved with the curing processes, which limits further reinforcing improvements.
Furthermore, tensile tests revealed trade-offs associated with these enhancements. While the addition of fumed silica was expected to not drastically affect the tensile behavior of the elastomers, the filled samples cured with CAT1316 exhibited reduced elongation capacities.
This phenomenon can be caused by poor filler dispersion or a negative interaction with the elastomer matrix, which could be influenced by various factors including the heterogeneity of the raw mixture and the chemical composition of the KE1316 curing agent. In fact, poor filler dispersion may lead to agglomeration, which can create microscale localized weaknesses and thereby reduce the tensile performance of the material. In contrast, elastomers cured with CX32-2036 did not display meaningful changes in their elongation at break, although the ultimate stresses were slightly reduced. These results assert that elastomers featuring the CX32-2026 curing agent perform better when reinforced with fumed silica, whereas those cured with CAT1316 experience performance loss.
Lap shear tests revealed that the use of a primer considerably influences the bond strength between silicone elastomers and steel substrates. The superior performance of the AQ1 primer, particularly when combined with CX-32-2036 cured elastomers, indicates a promising direction for optimizing interlayer bonding in laminated bearings. The comparison of Figures 6 and 7 indicates a pivotal influence of primer application on the bond strength between silicone rubber and steel substrates. Notably, both silicone rubber batches without primer displayed significantly lower rupture stresses. In contrast, the use of primers has been shown to increase these values by up to 400%, underscoring their key role in optimizing bonding strength.
The quasi-static shear test results illustrate the performance characteristics of the tested laminated silicone elastomer bearing prototypes, with a focus on the equivalent shear moduli and corresponding damping ratios. The equivalent shear coefficients ranged between 0.3 and 0.6 MPa, whereas the damping ratios ranged from 5% to 15%. Notably, both parameters remain stable across the strain range of 50% to 250% for all samples, indicating consistent material behavior under stress. When comparing the prototypes, those utilizing the CX32-2036 curing agent demonstrated higher shear coefficients but lower damping ratios than their counterparts using the CAT1316 curing agent. Furthermore, an increase in filler proportion correlates with elevated shear coefficients and diminished damping ratios, highlighting the key impact of filler content on the mechanical properties of the resulting bearings. Thus, the results underscore the pivotal role that the curing agent and filler proportion play in influencing both the shear performance and damping potential of laminated silicone elastomers.
The results collectively highlight the potential of fumed silica-reinforced silicone elastomers as next-generation materials for seismic isolation bearings. The combination of enhanced mechanical properties, improved adhesion, and stable hysteresis behavior addresses key limitations of existing elastomers. However, the trade-offs, observed through reduced ductility with increased filler content and variability in primer performance, underscore the importance of optimizing material formulations and testing under application-specific conditions.
4.2 Limitations and Perspectives
Despite these promising results, several limitations of this study should be acknowledged and addressed to provide a more comprehensive understanding of the material performance and support its application in real-world scenarios.
While experimental insights investigated into the mechanical enhancement of silicone elastomers through fumed silica incorporation, a comprehensive theoretical understanding of the underlying filler-polymer interactions remains to be developed. Future direction should focus on elucidating the molecular mechanisms that govern these interactions, particularly how the surface chemistry and morphology of silica fillers influence the crosslinking density and network structure of the silicone matrix. Incorporating theoretical models can offer a more detailed perspective on how filler characteristics affect macroscopic properties like stiffness and damping.
Since this study focused on short-term mechanical properties, although the results highlighted the feasibility of the proposed enhancements, they do not account for long-term durability under operational conditions. While silicone elastomers have naturally lasting properties, further research is needed to evaluate the long-term durability and aging characteristics of other components under various environmental conditions.
In the same vein, while quasi-static tests provide valuable insights into the intrinsic hysteretic behavior of bearing prototypes, they do not fully replicate the complex dynamic loads experienced during seismic events. Factors such as high-frequency vibrations, multidirectional forces, and temperature variations were not considered in this study. Future work can incorporate dynamic seismic simulations, hybrid tests, and environmental conditioning to better evaluate the performance of prototypes under real-world conditions.
Furthermore, this study primarily focused on laboratory-scale experiments, with prototype bearings fabricated for quasi-static testing. Scaling up the manufacturing process to produce full-sized bearings may introduce additional challenges, such as ensuring uniform filler dispersion, maintaining consistent adhesion across large surfaces, and optimizing the curing process. Collaboration with industry stakeholders and field trials will be important in bridging the gap between laboratory findings and practical deployment.
5 Conclusions
This study investigated the potential of silicone elastomers, enhanced with fumed silica and primers, as next-generation materials for seismic isolation bearings. Through a comprehensive series of mechanical tests, the effects of different filler proportions and three selected primers on the mechanical and adhesive properties of silicone elastomers were evaluated, culminating in a performance assessment of bearing prototypes under quasi-static shear conditions.
The results demonstrated that the incorporation of fumed silica largely enhanced the rigidity of the silicone elastomers, as indicated by the Shore A hardness tests, with increases of up to 185%. The choice of curing agent strongly influenced these enhancements, with CX32-2036 outperforming CAT1316 because of its ability to form a denser and more effective crosslink network. While the addition of fillers improves the load-bearing capacity, it also reduces the ductility, highlighting the need for careful optimization of filler proportions.
The primers were found to play a critical role in improving interlayer adhesion, with the AQ1 primer achieving bond strength improvements of up to 400%. The combination of the CX32-2036 cured elastomers and the AQ1 primer provided the strongest adhesive performance, while the PPX primer offered consistent and stable results across varying conditions. These findings underscore the importance of tailored primer-elastomer combinations for specific applications.
Quasi-static shear tests of prototype bearings confirmed the viability of the proposed material system. Prototypes fabricated with CX32-2036 cured elastomers and either AQ1 or PPX primers demonstrated excellent hysteresis behavior, consistent damping capacity and stable shear stiffness, making them suitable for seismic isolation applications. However, the observed trade-offs between stiffness and damping properties, as well as partial bond failures with certain primer types, emphasize the need for further optimization.
Conflicts of Interest
The authors declare no conflicts of interest.