Lignite-Based Hierarchical Porous C/SiOx Composites as High-Performance Anode for Potassium-Ion Batteries
Abstract
Silicon oxide (SiOx, 0 < x ≤ 2) has been recognized as a prominent anode material in lithium-ion batteries and sodium-ion batteries due to its high theoretical capacity, suitable electrochemical potential, and earth abundance. However, it is intrinsically poor electronic conductivity and excessive volume expansion during potassiation/depotassiation process hinder its application in potassium-ion batteries. Herein, we reported a hierarchical porous C/SiOx potassium-ion batteries anode using lignite as raw material via a one-step carbonization and activation method. The amorphous C skeleton around SiOx particles can effectively buffer the volume expansion, and improve the ionic/electronic conductivity and structural integrity, achieving outstanding rate capability and cyclability. As expected, the obtained C/SiOx composite delivers a superb specific capacity of 370 mAh g−1 at 0.1 A g−1 after 100 cycles as well as a highly reversible capacity of 208 mAh g−1 after 1200 cycles at 1.0 A g−1. Moreover, the potassium ion storage mechanism of C/SiOx electrodes was investigated by ex-situ X-ray diffraction and transmission electron microscopy, revealing the formation of reversible products of K6.8Si45.3 and K4SiO4, accompanied by generation of irreversible K2O after the first cycle. This work sheds light on designing low-cost Si-based anode materials for high-performance potassium-ion batteries and beyond.
1 Introduction
Among many new energy storage systems, lithium-ion batteries (LIBs) have dominated the energy storage market due to their high energy density and long cycle life.[1] They will continue to be the primary choice for energy storage in portable electronic devices and electric vehicles for some time to come.[2, 3] However, the supply risks of lithium resources and the growing cost raise concerns about the availability of lithium.[4] LIBs are less competitive in terms of economic and grid-scale applications.[5] Therefore, it is urgent to find an abundant element on the earth to replace lithium and realize sustainable development in the field of energy storage.[6, 7] Compared with lithium, the reserve of potassium in the earth's crust is 2.09%, which is much higher than lithium (0.0017%).[8] In addition, potassium shares similar physical and chemical properties with lithium, making potassium-ion batteries (KIBs) a promising candidate to replace LIBs.[9, 10] However, the commercially available LIBs anode, graphite, only can deliver a theoretical capacity of 279 mAh g−1 in KIBs, which greatly hinders the energy density in KIBs. Therefore, it is crucial to seek high-performance anode materials for efficient potassium ion storage.
In the past few years, potential anode materials, including organic materials, conversion-type materials, alloy-type materials, and carbon-based materials, have been extensively explored for alkali metal ion batteries. For LIBs, alloy-type materials, including Si, Sb, Sn, Bi, P, and Ge, all possess an excellent theoretical capacity.[11] Especially Si, owing to its relatively low working potential, high theoretical capacity (4200 mAh g−1), and reserve abundance,[12] has attracted researchers' attention as LIBs anode material. However, there are relatively less alloy-based anode materials available for KIBs, and only Sn,[13] P,[7] Sb,[14] and Bi[15] have been studied, realizing a reversible capacity of <700 mAh g−1. Although Si can be alloyed with K according to the K–Si phase diagram, electrochemical alloying of crystalline Si with K is difficult, as Si as anode material for KIBs is seldom reported.[16] Lee et al.[16] have proved that amorphous Si can be used as an anode material for KIBs using first principle calculations. The alloying of amorphous Si with K+ is thermodynamically favorable and finally forms the stable K1.1Si phase with a high theoretical capacity of 1049 mAh g−1. Sun et al.[17] have synthesized crystalline silicene from Zintl phase CaSi2 and confirmed that K+ can be inserted/extracted efficiently. As anode for KIBs, the obtained crystalline silicene realized a specific capacity of 180.1 mAh g−1 at 10 mA g−1 and a high Coulombic efficiency of about 99.4% after 3000 cycles at 0.5 A g−1. Moreover, Yang et al.[18] have designed 3D silicon-diamondyne (Si-DY), which is only composed of butadiyne units and sp3-hybridized Si atoms. Owing to the combination of abundant diyne and various inner channels in the stable diamond-like skeleton, this Si-DY delivers a high specific capacity of 496 mAh g−1 at 50 mA g−1 after 100 cycles and 90 mAh g−1 at 1 A g−1 after 500 cycles, respectively. In LIBs, silicon oxide (SiOx, 0 < x ≤ 2) possesses a high theoretical capacity of 1961 mAh g−1.[19] During the initial Li+ intercalation process, SiOx reacts with Li to in situ form Li2O, Li4SiO4, Li2Si2O5, and nano-Si, which are uniformly dispersed on the nanometer scale. Among them, Li4SiO4 and Li2O are electrochemical inert and have no Li+ storage capacity.[20] However, they can effectively prevent the agglomeration of nano-Si particles and buffer the volume expansion during charge/discharge processes, ensuring robust cyclic performance and excellent rate capability of SiOx. Therefore, SiOx anode has a great potential in commercial LIBs. Nonetheless, SiOx as an anode material for KIBs is seldom reported, and the electrochemical mechanism of SiOx in KIBs is still unclear.
Herein, we prepared a hierarchical porous C/SiOx KIBs anode using lignite as raw material via a facile carbonization and activation method. In this composite, SiOx nano-particles are uniformly distributed in the carbon skeleton, which is beneficial to improve the electrical conductivity of SiOx nano-particles, mitigate the volume expansion, and prevent aggregation during charge/discharge processes. The obtained C/SiOx has a hierarchical porous structure, which is favorable for facile electrolyte diffusion and K+ intercalation/de-intercalation. Finally, the potassiation of SiOx nano-particles will produce reversible products of K6.8Si45.3 (KSi) and K4SiO4, and irreversible K2O. The as-produced KSi and K4SiO4 are conducive to enhancing the potassium storage capacity of C/SiOx, while the irreversible K2O allows uniform dispersion of the reversible products, prevents aggregation, and buffers volume expansion. As a result, the hierarchical porous C/SiOx prepared at 600 °C exhibits a high reversible capacity of 370 mAh g−1 after 100 cycles at 0.1 A g−1 with capacity retention of up to 90% and also demonstrates excellent long-cycle stability of 208 mAh g−1 after 1200 cycles at 1.0 A g−1 when applied as anodes for KIBs. Importantly, these results show that the obtained hierarchical porous C/SiOx anodes are promising for promoting the commercial application of KIBs.
2 Results and Discussion
The detailed content of Lignite can be found in Table S1, Supporting Information. After dissolving metal impurities by acidic etching, lignite was soaked in hot alkali to remove Al2O3. Then, the lignite residue was activated and etched with residual alkali to obtain the final products (Figure 1a). According to the activation temperature, the synthesized porous C/SiOx composites were named as S-T500, S-T600, and S-T700, respectively. As a comparison, the sample obtained by direct carbonization of acid-washed lignite without KOH activation is named as N-T600. To distinguish the contribution of pure carbon and SiOx to the achieved capacity in S-T600, S-T600 powder was soaked in 5 m HF for 12 h to receive pure carbon without any SiOx, which is named as SF-T600. In addition, pure SiOx has also been synthesized by removing the carbon skeleton by high-temperature aerobic calcination. Detailed synthesis process can be found in Section 4. The morphology and microstructure of lignite particles with and without KOH activation were characterized by field emission scanning electron microscopy (FE-SEM) and transmission electron microscope (TEM). As shown in Figure 1b,c, N-T600 exhibits irregular particle shape, wide distribution of particle size, smooth surface, and no obvious pore structure. Similarly, S-T600 particles are also irregular and have a wide particle size distribution (Figure 1d,e). Nonetheless, S-T600 possesses a very rough surface, with abundant pores of different pore sizes and thinner pore walls (Figure 1e). The sharp contrast between SiOx and C can be clearly distinguished from the TEM observations of S-T600, where the dark region in the image corresponds to SiOx (Figure S1, Supporting Information). SiOx particles are uniformly dispersed into C skeleton and the encapsulated C layer effectively mitigates the volume expansion of SiOx during cycling and upgrades the electrical conductivity of C/SiOx composites.[21] From the high-resolution transmission electron microscope (HRTEM) image of S-T600, there are no clear lattice stripes and selected-area electron diffraction (SAED) shows a ring pattern, indicating the amorphous property of C skeleton and SiOx particles in S-T600 (Figure 1f). This is consistent with the results of X-ray diffraction (XRD). It is obvious that three elements O, C, and Si are evenly distributed in S-T600, which guarantees close contact between C skeleton and SiOx particles (Figure 1g). This is conducive to preventing the agglomeration of SiOx particles in the charge/discharge processes, alleviating their volume expansion, and improving their conductivity.[22]
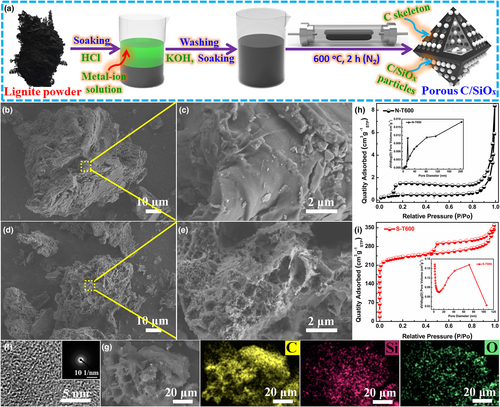
The porosity and pore structures for all samples were further explored by Brunauer–Emmett–Teler (BET) tests. According to the International Union of Pure and Applied Chemistry (IUPAC) classification, the N2 adsorption/desorption isotherm of N-T600 is a type III isotherm curve with an H3-type hysteresis loop at P/P0 from 0.1 to 1.0 (Figure 1h). The N2 adsorption/desorption isotherm of N-T600 is concave downwards and has no inflection point, signifying that N-T600 does not form a large number of pore structures on its surface.[23] Meanwhile, an H3-type hysteresis loop implies that N-T600 is a granular material with slit, cracks, and wedges structures on the surface, which corroborates the SEM observations.[24] After KOH activation, the obtained porous C/SiOx composites begin to form pores of different sizes on the surface (Figure S2, Supporting Information), and the N2 adsorption/desorption isothermal curves gradually change from type III curve to type IV with increased activation temperature (Figure 1i, Figure S3a, Supporting Information). These results indicate that micropores and mesopores are gradually formed on the surface during activation, and the amount of pores increases with raised temperature. In addition, the isothermal curve hysteresis loops of these C/SiOx composites gradually vary from H3 to H4 type, which further proves the formation of micropores and mesopores on the surface of these C/SiOx composites after the addition of KOH.[25] Furthermore, with increased activation temperature, the specific surface area and pore volume of C/SiOx composites increase at first and then decrease, while the pore size shows the opposite trend (Table S2, Supporting Information). This is because, with the same amount of KOH, the number of micropores and mesopores formed on the C skeleton of C/SiOx composites increases with activation temperature. However, when the temperature reaches 700 °C, the C framework between adjacent pores breaks, and thus larger pores are formed resulting in decreased specific surface area (Figure S2, Supporting Information). Significantly, the porosity of S-T600 is slightly increased after the removal of SiOx by HF (Table S2, Supporting Information). The porous structure of C/SiOx composites not only shortens the diffusion distance of K+ but also facilitates the insertion/extraction of K+ and improves their electrochemical properties, such as cycling stability and rate performance.[26]
The thermogravimetric analyzer (TGA) analytical methodology was used to further quantify SiOx and C content of S-T600 (Figure 2a, Figure S3b, Supporting Information). The mass loss of S-T600 begins at about 300 °C up to 800 °C in air atmosphere, due to the oxidation of carbon skeleton in S-T600. Therefore, the C content in the porous C/SiOx composites can be calculated by the mass loss. After KOH activation, the content of metal impurities in the porous C/SiOx composites is <1% (Table S3, Supporting Information). Therefore, the SiOx content in these composites can be calculated by the following equation: , where denotes the SiOx mass fraction, ωC denotes the carbon mass fraction, and ωM signifies the metal impurity mass fraction of the synthesized C/SiOx samples. From Table S4, Supporting Information, the addition of KOH not only plays a role for pore formation but also effectively removes the impurities of Al2O3 in synthesized C/SiOx composites. In addition, the content of SiOx in porous C/SiOx composites remains similar at different activation temperatures. As shown in the XRD patterns for C/SiOx samples and N-T600 (Figure 2b, Figure S3c, Supporting Information), there are comparable diffraction peaks centered at 22°, which may belong to the overlapped diffraction peaks of amorphous C and non-crystalline SiOx.[27] The chemical structure of C skeleton in porous C/SiOx composites was studied by Raman spectroscopy. The two distinct peaks located at about 1358 and 1592.3 cm−1 are corresponding to D band and G band, which were caused by disordered sp3 C or defective graphite structures and ordered sp2-hybrid graphite. It is well known that the ID/IG value can effectively reflect the degree of disruption of C-based materials. The higher the ID/IG value, the more defects the material has.[28] From Figure 2c and Figure S3d, Supporting Information, the ID/IG value obviously increases after KOH activation, and the value increases at first and then decreases with raised activation temperature. This verifies that with the addition of KOH and the increase of temperature, more edges and topological defects can be introduced into porous C/SiOx composites, resulting in more disordered or less crystalline structure,[29] providing more amount of active sites for the insertion/extraction of K+.[30] X-ray photoelectron spectroscopy (XPS) full spectra of N-T600 and porous C/SiOx composites (Figure 2d, Figure S3e, Supporting Information) have verified the presence of C, Si and O elements, which are consistent with energy-dispersive spectroscopy (EDS) analysis.
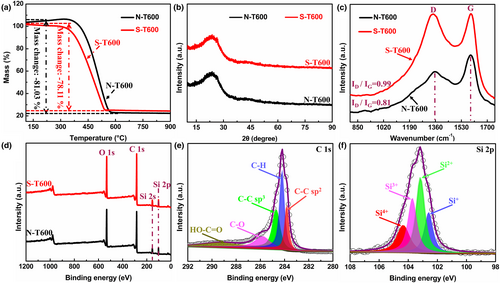
The C 1s spectrum of S-T600 is displayed in Figure 2e and the fitting results can be found in Table S5, Supporting Information. In C 1s XPS spectrum, five peaks at 283.81, 284.21, 284.69, 285.82, and 289.30 eV can be fitted, which are related to C–C sp2, C–H, C–C sp3, C–O, and O–C=O bonds, respectively.[31] Si 2p spectrum is deconvoluted into four small peaks at 102.6, 103.1, 103.7, and 104.35 eV, corresponding to four different oxidation states of Si (Figure 2f, Table S6, Supporting Information).[32] O 1s spectrum exhibits four peaks at 531.37, 532.15, 532.72, and 533.36 eV, corresponding to C=O, Si–O, C–O, and O=C–O, respectively (Figure S3f, Table S7, Supporting Information).[33] It is worth noting that the as-induced oxygen-containing functional groups on carbon surface can strengthen the wettability and increase the pseudocapacitive contribution, resulting in improved electrochemical performance.
The K+ storage behavior of S-T600 was investigated via cyclic voltammogram (CV) curves between 0.01 and 3.0 V (Figure 3a). In the first cycle, there is a sharp reduction peak between 0.01 and 1.0 V, which causes a very large capacity loss compared with the second cycle. This is due to the decomposition of electrolyte, the irreversible reaction of K+ with SiOx particles, and the formation of a solid-electrolyte interface (SEI) film, which results in a low initial Coulombic efficiency. There is a reduction peak at about 0.01 V, which is closely related to the formation of KC8 and reversible silicon-potassium compounds. Another weak oxidation peak is located at about 0.8 V, corresponding to the depotassiation of carbides and silicon-potassium compounds. After the first cycle, the CV curves almost overlap completely, which indicates that the porous C/SiOx electrode has good electrochemical reversibility and cycle stability.
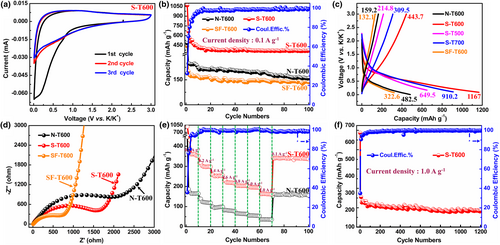
The cycle performance of these electrodes was also evaluated (Figure 3b, Figure S4a, Supporting Information), and it can be seen that these electrodes show good cycling stability after 10 cycles. After KOH activation, the reversible specific capacity of porous C/SiOx electrodes are obviously boosted, which increases first and then decreases with activation temperature. The initial discharge/charge capacities of S-T600 electrode at 0.1 A g−1 are 1167/443.7 mAh g−1 (initial Coulomb efficiency of 38%), surpassing those of N-T600 electrode (482.5/159.2 mAh g−1) (Figure 3c), SF-T600 (322.6/132.1 mAh g−1) (Figure 3c) and pure SiOx electrode (841.4/320.9 mAh g−1) (Figure S5, Supporting Information). Even after 100 cycles, the S-T600 electrode retains a comparatively high reversible capacity of 370 mAh g−1, which is higher than those of N-T600 (159.2 mAh g−1), SF-600 (143 mAh g−1) and pure SiOx (69.5 mAh g−1) electrodes. In addition, the capacity of S-T600 is much higher than those of hard carbon electrodes prepared using chemical reagents and biomass as raw materials (Table 1). Based on the discharge capacity of pure carbon (SF-T600, 143 mAh g−1 at 0.1 A g−1), the specific capacity of SiOx in S-T600 can be calculated to be 1194.4 mAh g−1 (143 mAh g−1 × 0.7811 (for pure carbon) + 1194.4 mAh g−1 × 0.2130 (for SiOx) = 370 mAh g−1 (for the composite)). Therefore, nearly 68.7% of the specific capacity in S-T600 is contributed by SiOx particles. Except for the SF-T600 electrode, the initial Coulomb efficiency of S-T600 is significantly higher than that of the other two porous C/SiOx electrodes (Figure 3c, Figure S6, Supporting Information). It is well known that the radius of K+ is larger than that of Li+. Therefore, non-porous materials or low-porosity materials are not conducive to the shuttle and storage of K+.[34] Nonetheless, after KOH activation, the specific surface area and porosity of the porous C/SiOx composites increased first and then decreased with temperature rise. High specific surface area and large porosity not only can provide abundant active sites for K+ storage,[35] but also provide an effective space to buffer the volume expansion in the process of K+ charge and discharge.[36] Consequently, the potassium storage capacity of these materials increases first and then decreases with activation temperature rise. In addition, the addition of KOH produces a large number of defects in the carbon skeleton, resulting in a large number of active sites, thus improving the reversible specific capacity of porous C/SiOx electrodes.[28] Finally, compared to N-T600, the content of SiOx in the porous C/SiOx composites is obviously higher (Table S4, Supporting Information). SiOx reacts with K+ to form reversible products such as KSi, K4SiO4, and Si.[12] The theoretical potassium storage capacity of Si is 995 mA g−1, which is much higher than that of C.[11] Therefore, the reversible capacity of porous C/SiOx electrodes is significantly larger than that of SF-T600. However, higher content of SiOx in the composites will also consume more K+ to produce irreversible product K2O in the first potassiation process, further limiting the initial Coulomb efficiency.[12] Therefore, the initial Coulomb efficiency of porous C/SiOx electrodes is obviously higher than that of the N-T600 electrode, and decreases with the increased SiOx content in porous C/SiOx composites (Figure 3c). To evaluate the practical application potential of the S-T600 anode, we employ the perylene-3,4,9,10-tetracarboxylic diimide (PTCDI) as the cathode to assemble a full cell. As shown in Figure S7, Supporting Information, the full cell displays an initial discharge capacity of 141.2 mAh g−1 with an initial CE of 89.33% at 1.0 A g−1. After 1000 cycles, the full cell still maintains a capacity of around 75 mAh g−1 and a Coulombic efficiency of nearly 100%, demonstrating the promising practicability of the synthesized C/SiOx anode.
Samples | Current density (mAh g−1) | Cycles | Capacity (mAh g−1) | Ref. |
---|---|---|---|---|
Hard carbon microspheres | 28 | 100 | 216 | [40] |
N/O co-doped hard carbon | 50 | 100 | 231 | [34] |
S/O co-doped hard carbon | 50 | 100 | 226 | [39] |
N-doped carbon nanotubes | 50 | 300 | 257 | [41] |
Graphitic carbon nanocage | 56 | 100 | 195 | [6] |
N-rich carbon nanosheets | 100 | 100 | 266 | [28] |
Carbon nanotubes sponge | 100 | 500 | 210 | [42] |
Bi-continuous nanoporous carbon sphere | 100 | 100 | 275 | [36] |
N-doped carbon nanofibers | 200 | 200 | 191 | [43] |
Hierarchical porous carbon | 200 | 100 | 168 | [44] |
Short-range ordered carbon | 200 | 200 | 197 | [45] |
Porous C/SiOx | 1000 | 1200 | 208 | This work |
100 | 100 | 370 |
The Nyquist plots of S-T600 and N-T600 anodes are shown in Figure 3d, displaying a depressed semicircle in the high-frequency region and a diagonal line in the low-frequency region.[37] The depressed semicircle corresponds to solid electrolyte interface (SEI) film resistance and charge transfer resistance, while the sloping line in the low-frequency region is related to K+ diffusion.[38] Compared with other C/SiOx samples, the S-T600 electrode has a smaller semicircle diameter at the high-frequency and a higher slope at low frequencies (Figure 3d, Figure S4b, Supporting Information), indicating a lower resistance to electron transport and faster diffusion of K+ (Table S8, Figure S8, Supporting Information).
As shown in Figure 3e, the discharge capacities of S-T600 are 357, 302, 253, 221, 203, 195, and 162 mAh g−1 at 0.1, 0.2, 0.4, 0.6, 0.8, 1.0, and 2.0 A g−1, respectively. In particular, when the current density returns to 0.1 A g−1, the discharge capacity of S-T600 can recover to 340.3 mAh g−1. The reversible capacity of N-T600 at 2.0 A g−1 is only 36 mAh g−1 and can be restored to 159 mAh g−1 when the current density returns to 0.1 A g−1. In addition, S-T600 still maintains a capacity of 208 mAh g−1 after 1200 cycles at 1.0 A g−1 (Figure 3f), and the Coulomb efficiency of S-T600 anode was enhanced to above 95% after the first 50 cycles. Figure S4d, Supporting Information shows the long-cycle performance of S-T700 and S-T500 anodes at 1.0 A g−1, which shows specific capacities of 142 and 103 mAh g−1 after 1200 cycles, respectively. In general, S-T600 anode has a surprisingly high reversible capacity, excellent rate performance, and top-notch long-cycle stability. It has surpassed the performance of most carbon-based anode materials reported to date (Table 1).[39]
Porous structures with high specific surface area have a higher pseudocapacitance contribution to the total capacity. Therefore, CV curves of S-T600 and N-T600 were measured at different scan rates from 0.1 to 10 mV s−1 as shown in Figure 4a and Figure S9a, Supporting Information. It can be found that the CV curves of S-T600 remained roughly consistent in shape (Figure 4a) under different scan rates.
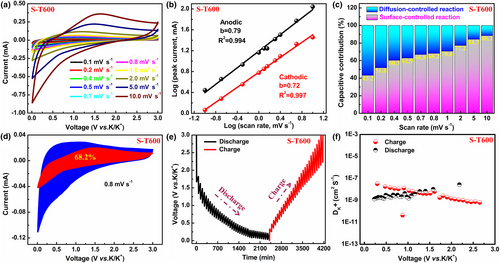
Figure 4f shows the versus voltage for S-T600 anode calculated according to Equation (3), with values of ranging from 10−6 to 10−10 cm2 s−1, which are larger than those of N-T600 anode (Figure S10b, Supporting Information). There is a lower diffusion coefficient in the starting zone of the discharge/charge plateau region. This may be due to the higher driving force of the electrochemical reaction driving the K+ diffusion.[51]
The surface morphology and thickness change of N-T600 and S-T600 electrodes were compared to corroborate the improved cycle stability of S-T600 during the cycling process. As shown in Figure 5a,b, there are a large number of cracks on the surface of N-T600 electrode due to volume expansion. Then, a new solid-electrolyte interface (SEI) film will be generated at the crack, which consumes K+ in the electrolyte and expedites capacity fading. On the contrary, there are no obvious cracks on the surface of S-T600 electrode except for some small protrusions (Figure 5c,d). The reason for this phenomenon is that the hierarchical porous structure of S-T600 can alleviate the volume expansion of SiOx particles during charge/discharge processes, and reduce the consumption of K+ in the production of new SEI film, which is favorable to achieving an excellent cycle stability. The active material layer of LC electrode expanded from 8.4 to 14.7 μm with a larger expansion ratio of 175% after 40 cycles (Figure 5e,f), which is bigger than that of S-T600 electrode (expanded from 10.5 to 13.7 μm with a expansion ratio of 130%) (Figure 5g,h). In addition, the electrical disconnection between the active materials and the current collector of N-T600 electrode is more obvious than that of S-T600 electrode with a serious cracking phenomenon. These phenomena fully indicate that the hierarchical porous structure of S-T600 anode materials can effectively relieve the mechanical stress caused by volume expansion during charge/ discharge processes and thus improving the cycle stability of C/SiOx materials.

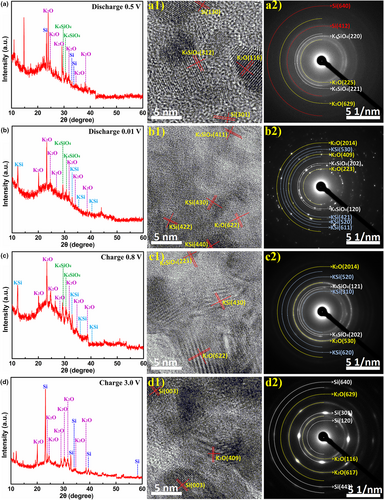
As the potential is further lowered to 0.01 V, as-generated elemental Si is further converted into K6.8Si45.3 (KSi), producing K2O, K4SiO4, and KSi discharge products in S-T600 electrode (Figure 6b). In other words, crystalline K6.8Si45.3 phase has been observed in the fully potassiated S-T600 electrode. When charged to 0.8 V, the K2O, K4SiO4, and KSi phases still exist in S-T600 electrode (Figure 6c). That is to say, the removal of K+ from the carbon skeleton of S-T600 electrode material is mainly completed during the charging process of 0.01–0.8 V, which further proves the experimental results of cyclic voltammetry. After the electrode was charged to 3.0 V, K4SiO4 and KSi phases completely disappeared, with remnant K2O phase (Figure 6d), manifesting the formation of reversible K4SiO4 and KSi phases and irreversible K2O phase during cycling. At the same time, formation of crystalline Si phase was also detected after potassiation/depotassiation of SiOx in S-T600 electrode, indicating that this crystalline Si contributes to the reversible K+ storage capacity in subsequent cycles. This result is different from the reports that pure crystalline Si shows an inert nature toward K+ storage, suggesting that the electrochemical mechanism of SiOx is complicated and more studies are needed.[16, 17] In addition, formation of K4SiO4 is reversible in the voltage range of 0.01–3 V, which is different from Li4SiO4.[52, 53] In order to clarify the difference between K4SiO4 and Li4SiO4, DFT (density functional theory) calculations are carried out to compare the corresponding voltages of Li4SiO4 (PDF#37-1472) (Figure S11a, Supporting Information) and K4SiO4 (PDF#46-0601) (Figure S11b, Supporting Information) extracting one metal ion.[52] It can be found that the charging voltage corresponding to the extraction of first Li+ in Li4SiO4 is 3.54 V (Figure 7a), while that of K4SiO4 is 2.87 V (Figure 7b). Moreover, two K+ can be extracted when K4SiO4 is charged from 0.01 to 3 V (Figure S11c, Supporting Information), thus K4SiO4 is not detected in S-T600 after charging to 3 V. As displayed in Figure S12a, Supporting Information, the SEM elemental mapping shows few K but rather C, Si, and O evenly distributed in the pristine S-T600 electrode. As a subsequent discharge proceeds, the significantly increased amount of K in the discharge products of the first cycle indicates the intercalation of K+ (Figure S12b, Supporting Information). After the first charge, a small amount of intercalated K+ is preserved, again indicating the formation of irreversible K2O (Figure S12d, Supporting Information).
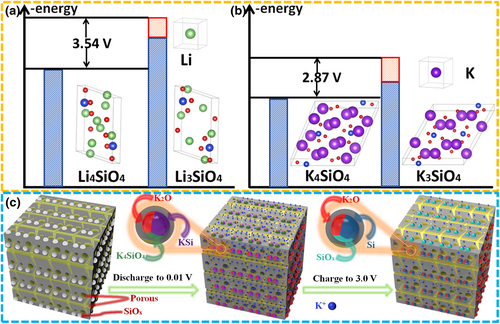
As shown in Figure 7c, K+ can enter the C skeleton and pores of porous C/SiOx anode materials, and react with SiOx particles to form K2O, K4SiO4, and KSi, when the electrode is discharged to 0.01 V. After the electrode was charged to 3.0 V, K4SiO4 and KSi phases completely disappear with the production of crystalline Si, but K2O phase still remains. The irreversible K2O can act as buffer components to mitigate the volume expansion caused by the potassiation of active SiOx. The amorphous C skeleton around SiOx particles not only provides good electronic conductivity but also buffers volume expansion. The hierarchical porous structure of C/SiOx anode materials can effectively shorten K+ diffusion distance, offer a large interface to accelerate electrochemical reactions, and supply sufficient void space, which successfully mitigates the mechanical stress caused by volume change. However, the diffusion of large K+ is limited in small micropores, producing dead K+ storage sites that lead to low initial Coulomb efficiency of the C/SiOx anode. Therefore, improving the initial Coulomb efficiency of C/SiOx anode in potassium ion battery will be of interest.
3 Conclusion
To summarize, C/SiOx materials with controllable pore structures are successfully prepared via a facile carbonization and activation method at different temperatures. A hierarchical porous C/SiOx with a maximum porosity synthesized at 600 °C exhibits the highest specific capacity, long-term lifespan, and rate capability. Such an outstanding performance originates from an appropriate specific surface area of this C/SiOx, the amorphous C skeleton, and active SiOx particles. SiOx particles contribute about 68.7% to the total capacity of the C/SiOx anode. Formation of crystalline Si phase by SiOx potassiation allows a reversible activity toward K+ storage. Formation of K4SiO4 is also reversible in the voltage range of 0.01–3.0 V as suggested by density functional theory calculations. More importantly, the performance of this hierarchical porous C/SiOx KIBs anodes is much superior to that of other reported carbon-based anodes.
4 Experimental Section
Materials and reagents
Lignite was purchased from Yuanbaoshan opencast Coal Mine in Chifeng City, Inner Mongolia Autonomous Region of China and its main components are given in Table S1, Supporting Information. After drying at 110 °C for a day, lignite was hand crushed into 60 mesh. All the other chemical reagents employed in this work were obtained from Tianjin Komeo Chemical Reagent Co., Ltd., and directly used without any further pretreatment.
Purification and impurity removal of raw materials
Lignite powder was impregnated in 2 mol L−1 HCl with a ratio of 1:6 (w/v, g mL−1) at room temperature for 24 h to remove metal oxide impurities except Al2O3. Afterwards, lignite powder was rinsed to neutral with deionized water and then baked overnight at 110 °C for follow-up experimental use.
Preparation of hierarchical porous C/SiOx composites
The purified lignite powder was evenly mixed with KOH at a 2:1 mass ratio in deionized water. Most Al2O3 in lignite can be removed after standing for 24 h at 60 °C and subsequent vacuum filtration. In addition, the lignite residue was dried at 110 °C for 12 h directly and then activated using residual KOH in a tubular furnace under an Ar atmosphere for 2 h. After washing with dilute hydrochloric acid and deionized water, the final hierarchical porous C/SiOx composites were obtained by vacuum drying at 110 °C for 8 h. Three temperatures of 500 °C, 600 °C, and 700 °C were used in the activation process and the synthesized porous C/SiOx composites were named as S-T500, S-T600, and S-T700, respectively. For comparison, the sample obtained by direct carbonization of acid-washed lignite without KOH in Ar atmosphere at 600 °C was named N-T600. To investigate the contribution of pure carbon and SiOx to the capacity in S-T600, S-T600 powder was soaked in 5 m HF for 12 h to receive pure carbon without any SiOx, which is named as SF-T600. Pure SiOx was synthesized by removing the carbon skeleton by high-temperature aerobic calcination.
Materials characterization
The amount of Metal elements (Al, Fe, Ca, Mg, K, and Na) in the obtained porous C/SiOx composites were determined by the inductively coupled plasma (ICP)–optical emission spectrometer. Scanning electron microscopy (SEM) and transmission electron microscope (TEM) were used to observe the morphology of C/SiOx samples. Element distribution of C/SiOx composites was performed by energy-dispersive X-ray spectroscopy (EDS) equipped on SEM. The pore structure and specific surface area of C/SiOx samples were tested using Brunauer–Emmett–Teller (BET) approach via measurement of N2 adsorption/desorption isotherms. Thermogravimetric analysis (TGA) was performed using a Mettler Toledo TGA/DSC 3+ thermogravimetric analyzer in air with a heating rate of 10 °C min−1. The phase structure of C/SiOx samples was analyzed by Rigaku D/MAX-3B X-ray diffraction (XRD) instrument. Raman spectroscopy analysis was performed with an inVia Raman microscope. The chemical valence of the elements in C/SiOx samples was characterized by ESCALAB 250Xi X-ray photoelectron spectrometer (XPS).
Electrochemical measurements
Electrochemical properties of C/SiOx were studied in CR2025 coin-type K-half cells. C/SiOx samples (80 wt.%), Super P carbon black (10 wt.%), and sodium alginate (10 wt.%) were mixed well into the mortar, and then a moderate amount of deionized water was added into this mixture to obtain a homogeneous slurry. Subsequently, the obtained slurry was spread evenly on Cu foil and vacuum-dried at 60 °C for 12 h. The mass loading of the active material (C/SiOx composites) on the collector is about 1.8–2.3 mg cm−2. In KIBs, K foil was used as the counter electrode, glass fiber as separator, and 1.0 m KPF6 dissolved in EC/DEC (volume ratio 1:1) as electrolyte. In the full cells, the cathode was made of 70 wt.% perylene-3,4,9,10-tetracarboxylic diimide (PTCDI), 20 wt.% acetylene black and 10 wt.% polyvinylidene fluoride, and the anode was an S-T600 electrode. The mass ratio of cathode to anode is about 3.5. Galvanostatic charge/discharge was performed on a CT3001A Land battery test system from 0.01 to 3.0 V at different currents. Cyclic voltammetry (CV) curves in the potential range of 0.01–3.0 V and electrochemical impedance spectroscopy (EIS) spectra were captured on a CHI760E electrochemistry workstation. The frequency range is 0.01–100 kHz and the amplitude is 10 mV for EIS testing. The voltage window of the S-T600//PTCDI full cell is set to 0.01–3.8 V.
Acknowledgements
Z.Y. and S.Z. contributed equally to this work. This project was performed with the National Natural Science Foundation of China (nos. 21968022 and 51962027), the Fundamental Research Funds for Inner Mongolia University of Science & Technology (no. 2023QNJS052), and the Natural Science Foundation of Inner Mongolia (no. 2019BS02002).
Conflict of Interest
The authors declare no conflict of interest.
Open Research
Data Availability Statement
The data that support the findings of this study are available on request from the author.