Experimental and Modeling of Sulfonation of Styrene-Based Resins Crosslinked With DVB and TMPTA
Abstract
This work investigates the sulfonation behavior of styrene-based resins crosslinked with divinylbenzene (DVB) and trimethylolpropane triacrylate (TMPTA) under varying conditions. TMPTA-formulated resins initially exhibited lower ion exchange capacity (IEC) (∼1.13 mmol g−1) than DVB-crosslinked resins (∼2.94 mmol g−1). However, optimized sulfonation conditions, including temperature and resin swelling, doubled the IEC of TMPTA-based resins. Modeling indicated SO3H groups in both resins, with higher accuracy (R2 = 0.9998) when using a sulfonic group molecular weight of 161 g mol−1. Differences in reactivity and degradation rates (6 × 10−3 min−1 for STY/DVB and 8 × 10−2 min−1 for STY/TMPTA) are also highlighted.
Abbreviations
-
- DCE
-
- 1,2-dichloroethane
-
- Dss
-
- styrene-DVB sulfonated resin treated with solvent
-
- DVB
-
- divinylbenzene
-
- TMPTA
-
- trymethilolpropane tryacrilate
-
- Ts
-
- styrene-TMPTA sulfonated resin
-
- Tss
-
- styrene-TMPTA sulfonated resin treated with solvent
1 Introduction
Ion exchange resins have been applied in various organic reactions over the past decades. Besides serving as excellent heterogeneous acidic catalysts, easily recyclable polymers crosslinked by divinylbenzene (DVB) or acrylates allow reactions to take place in different organic media [1]. These particles exhibit good mechanical strength, resistance to oxidation degradation, high temperatures, and hydrolysis. Commercially available resins, especially those crosslinked with DVB such as Amberlyst® [2], Amberlite® [3], Purolite® [4], Dowex® [5], and Lewatit® [6], have been extensively studied as catalysts. To incorporate fixed ionizable groups into its structure, the resin must undergo sulfonation. In this process, sulfonic groups are added to the aromatic rings through electrophilic substitution. The significance of these resins lies primarily in industrial and academic domains. Major industrial applications include catalytic support for biodiesel, esters, and ethers production; heavy metal removal in water treatment; deionization; and treatment of oily waters. Additionally, polymeric resins can be considered chemically sustainable materials because they can be regenerated, allow easy separation of the products, and prevent leaching of toxic materials into the environment [7].
Ion exchange resins have been widely utilized in various organic reactions. In recent years, numerous studies have focused on their synthesis using different crosslinkers. For instance, incorporating ethylene glycol dimethacrylate (EGDMA) as a crosslinker has demonstrated significant improvements in the yield of esterification reactions, such as in the synthesis of octyl oleate ester [8, 9]. Godoy et al. synthesized styrene/trimethylolpropane triacrylate (TMPTA) acidic resins using different crosslinker contents and feed times [10]. The authors observed that the catalytic efficiency decreased with increasing TMPTA content when applied to glycerol acetylation at 90 °C.
Polystyrene crosslinked with DVB has been studied for a long time as one of the most important crosslinked resins due to its high ion exchange capacity (IEC). Although it has good exchange capacity, the material has some limitations too, such as the relatively small chain length of DVB, which leads to the inaccessibility to the resin sites (sulfonic groups) that are influenced by hindering effects on regions of high crosslinking density [11]. A good strategy for overcoming this problem of accessibility is using a crosslinker with a longer chain to avoid hindering effects. Some studies have already shown good catalytic results for styrene resins copolymerized with different crosslinkers such as EGDMA, TEGDMA, and DEGDMA [8, 12]. However, the use of TMPTA still is a gap in the academic literature.
The advantages of using TMPTA instead of DVB are evident because the former is a trivinyl crosslinking agent, meaning each crosslinking point can form up to six chains, whereas DVB has a limit of four chains. Furthermore, resins crosslinked with acrylates exhibit higher polarity than styrene-DVB (Sty-DVB), potentially enhancing performance depending on the specific application medium.
Due to the high complexity and numerous variables involved in these previous studies, analyzing experimental data can be challenging. Therefore, employing mathematical modeling becomes a valuable approach allowing simulation of numerous characteristics and conditions, thereby enhancing the development of new resins [13]. Addressing this, the application of Sty-TMPTA resins as catalyst supports and the mathematical modeling of their sulfonation represent a gap in the existing literature, which is explored in this study. It was proposed to set a range of experimental conditions, varying TMPTA and DVB as crosslinker agents, along with sulfonation conditions. The kinetic model developed herein encompasses both sulfonation reaction and resin degradation. Through this model, it is feasible to simulate the IEC and the resin mass variation during the sulfonation process. This provides a valuable tool for comprehending and optimizing resin sulfonation.
2 Methods
2.1 Experimental Procedures
2.1.1 Suspension Copolymerization
The suspension copolymerization was performed on the basis of literature [14, 15]. The reactions were carried out in a 1L jacketed glass reactor under 350 rpm stirring at 80 °C. The copolymerization was fed as a mixture of aqueous and organic phases. Batch system: First, the aqueous phase was prepared, containing polyvinyl alcohol (0.1 wt%) and distilled water, and purged with nitrogen gas (15 mL min−1) for 1 h. Posteriorly, the organic phase containing 1 mol% of initiator (benzoyl peroxide) and a mixture of toluene + monomers (70:30 vol) was added to aqueous phase. Shot system: The same conditions of the batch system were considered, except for the crosslinker feeding, which was executed at pre-defined times along the reaction. The copolymerization reactions were carried out for 6 h.
Both the batch and shot addition methods were evaluated to investigate whether the distribution of the crosslinker throughout the polymerization process could improve the accessibility to catalytic sites. The experimental conditions were designed to use a relatively low crosslinker content while also assessing the effect of its distribution on catalytic performance. A lower crosslinker percentage is known to enhance resin flexibility, which, in turn, improves catalytic activity by increasing the accessible internal surface area.
2.1.2 Sulfonation Reactions
The sulfonation procedure was adapted from literature [10]. Dry copolymer, approximately 10 g, was kept in contact with sulfuric acid (150 mL) and then put on a thermostatic bath at pre-defined temperature and time of reaction, in accordance with each set of experiments. For Sty-DVB and styrene-TMPTA (diluted shot process) resins, the dry copolymer was kept in contact with 1,2-dichloroethane for 24 h before the reaction and then exposed to sulfuric acid. After the sulfonation reaction, the mixture of sulfuric acid and resins was diluted with water. To completely remove all acidic residues from the resin, an intensive washing process was conducted under magnetic stirring at 60 °C, with pH measurements taken over time. Once the pH stabilized and remained constant for at least one and a half hours in a basic medium (regardless of the pH value), the resin was filtered and then dried in an oven until a constant mass was achieved. Byproducts (transferred to the liquid phase) were not quantified due to the extremely acidic and complex nature of the medium, which hindered their characterization. For this reason, intermediate sampling during the sulfonation process was not feasible, and only the initial and final masses were used in the analysis and modeling.
Sty-DVB Resins
For the synthesis of Sty-DVB, the molar fraction of the crosslinker (YDVB) and its feed time (TDVB) were evaluated, based on the data presented in Tab. 1.
After the sulfonation reaction, the IEC and the mass variation (∆m) were calculated for each condition. The initial mass refers to the dry resin before sulfonation, whereas the final mass corresponds to the sulfonated and dried resin. Detailed results are presented in Sect. 3.
Styrene-TMPTA Resins
For the synthesis of resins crosslinked with TMPTA, a shot feeding system was used during the copolymerization. A series of experiments was conducted based on the approach used for DVB, with variations in parameters as shown in Tab. 2.
After the sulfonation reactions, the IEC and the mass variation were calculated. The results are presented in Sect. 3.
The variables and levels selected for the experiments detailed in Tabs. 1, 2, and 5, employing various crosslinkers (DVB and TMPTA for Tabs. 2 and 5), were chosen to modify the polymer structure. This approach aims to synthesize polymers with a lower crosslinking density throughout the polymeric network, thereby enhancing flexibility, as suggested in the literature [1].
Levels | Factors | |
---|---|---|
YDVB | TDVB [min] | |
1 | 0.06 | 0 |
2 | 0.10 | 60 |
3 | 0.14 | 120 |
- Note: YDVB: molar fraction of DVB in the monomer mixture; TDVB: feed time of DVB. TDVB = 0 denotes batch copolymerization, and greater than zero denotes the shot feeding process (every 20 min until 60 or 120 min).
Levels | Factors | |
---|---|---|
YTMPTA | TTMPTA [min] | |
1 | 0.02 | 30 |
2 | 0.06 | 150 |
3 | 0.10 | 270 |
- Note: T = styrene-TMPTA resin before sulfonation. YTMPTA: molar fraction of TMPTA in the monomer mixture; TTMPTA: feed time of TMPTA. The crosslinker was fed into the reactor every 10 min until the pre-defined time (30, 150, and 270 min).
2.1.3 Characterizations
Ion Exchange Capacity
Mass Variation
Swelling Index
2.2 Kinetic Modeling
A kinetic model was developed for the sulfonation of the resins, taking into account the sulfonation and resin degradation reactions. Among the degradation effects involved in the sulfonation of styrene-based resins, polymer chain breakage into fragments can occur through various pathways, resulting in low molecular weight products. [15] Polymeric materials containing aromatic rings, such as copolymers derived from styrene, may undergo chain scission in acidic media, as illustrated by the mechanism presented in Fig. 1 [16].

Due to the large excess of sulfuric acid in the reaction system, its concentration was considered constant, leading to a pseudo-first-order assumption for the sulfonation reaction. Although the reaction order with respect to the polymer could be adjusted as a model parameter, doing so would increase model complexity and reduce robustness. In systems where the acid concentration is not constant, a second-order rate law involving both polymer and acid concentrations should be considered.
The total polymer mass in the reaction medium can be described by the following balance: (final mass of particles) = (mass of fed polymer) + (mass of attached sulfonic groups) − (mass of degraded material).
The mass of fed polymer and the final particle mass were measured gravimetrically, as detailed in Sect. 2.1. Accordingly, the model assumes that at the beginning of the reaction, mps = 0 and mp = mp0, where mp0 is the mass of polymer initially fed, measured by weighing. At the end of the simulation, the sum mp + mps corresponds to the final mass of the particles after sulfonation and drying, also determined by gravimetry.
3 Results and Discussion
3.1 Experimental Results
The analyses were conducted following the method outlined in the preceding section. The sulfonation reaction procedure was the same for both resins (DVB and TMPTA), but the reaction temperatures were different due to the presence of acrylate groups in TMPTA. These groups are susceptible to hydrolysis [17], which causes resin degradation at higher temperatures. In contrast, DVB exhibits less degradation under similar conditions. For this reason, different temperatures were selected for each resin. Based on literature, the temperature for the DVB resin was set at 90 °C [18], whereas for TMPTA, it was set at 57 °C [8] to reduce hydrolysis and degradation. Tab. 3 summarizes the results obtained under identical analytical conditions.
Experiments | Conditions | Properties | |||
---|---|---|---|---|---|
YDVB | TDVB [min] | IEC [mmol g−1] | Si | Δm [g] | |
Dss1 | 0.06 | 0 | 3.18 | 1.82 | 0.39 |
Dss2 | 0.06 | 60 | 2.70 | 1.66 | 0.37 |
Dss3 | 0.06 | 120 | 3.00 | 1.61 | 0.24 |
Dss4 | 0.10 | 0 | 2.88 | 1.78 | 1.46 |
Dss5 | 0.10 | 60 | 2.76 | 1.70 | 2.58 |
Dss6 | 0.10 | 120 | 2.72 | 1.76 | 1.38 |
Dss7 | 0.14 | 0 | 3.12 | 1.65 | 1.91 |
Dss8 | 0.14 | 60 | 3.12 | 1.61 | 2.38 |
Dss9 | 0.14 | 120 | 3.00 | 1.62 | 2.12 |
- Note: Dss: styrene-DVB sulfonated resin treated with solvent. The sulfonation reactions were carried out at 90 °C. Before the reactions, the resins were swollen in 1,2-dichloroethane for 24 h using a ratio of 1 g of resin per 5 mL of solvent. The initial mass fed into the sulfonation step was 4 g.
- Abbreviations: Si, swelling index; Δm, mass variation; IEC, ion exchange capacity.
Based on the results presented, the resin from experiment Dss1, synthesized with 6 % crosslinker (DVB) using batch copolymerization, exhibited the highest content of sulfonic groups, achieving an IEC of 3.18 mmol g−1.
The IEC results for experiments Dss4–Dss6 averaged 2.79 mmol g−1, whereas experiments Dss7–Dss9 showed an average of 3.08 mmol g−1. In comparison, experiments Dss1–Dss3, synthesized with the lowest crosslinker content (6 %), had an average IEC of 2.96 mmol g−1. Although these differences may suggest slight variations, they should be interpreted as a possible trend only.
Regarding the mass variation data, there appears to be an increasing trend with higher DVB content, with average mass increases of 1.80 (10 % DVB) and 2.13 (14 % DVB), compared to 0.33 for 6 % DVB. One possible interpretation is that the higher mass gains could relate to the incorporation of sulfonic groups of different types—such as SO3H (81 g mol−1) and SO3SO3H (161 g mol−1)—as has been previously reported in the literature [19].
When compared to commercially available resins documented in the literature, the IEC of the synthesized resins was notably lower than the reported values for commercial resins (4.0–5.4 mmol g−1), except for Amberlyst 70 (2.55 mmol g−1). Moreover, it is recognized that the accessibility of a molecule to specific regions within the polymeric matrix depends on its size [11]. As for the swelling index, no significant variation was observed based on the crosslinker percentage. These findings align closely with the swelling index of the commercial resin Amberlyst 36 (1.73) [15]. As observed in Tab. 3, despite the partial degradation of the resin during the sulfonation process, the mass variations were positive due to the accumulation of sulfonic groups, as previously noted.
At the conclusion of each synthesis step, which included copolymerization followed by the sulfonation reaction, measurements of mass variation (Δm), IEC, and swelling index (Si) were recorded. Detailed results can be found in Tab. 4.
Experiments | Conditions | Properties | |||
---|---|---|---|---|---|
YTMPTA | TTMPTA [min] | IEC [mmol g−1] | Si | Δm [g] | |
Ts1 | 0.10 | 30 | 0.58 | 1.18 | −0.44 |
Ts2 | 0.10 | 150 | 0.54 | 1.34 | −0.72 |
Ts3 | 0.10 | 270 | 0.54 | 1.46 | −0.72 |
TS4 | 0.06 | 30 | 0.42 | 1.21 | −0.60 |
Ts5 | 0.06 | 150 | 0.64 | 1.44 | −0.28 |
Ts6 | 0.06 | 270 | 0.54 | 1.35 | −0.80 |
Ts7 | 0.02 | 30 | 0.36 | 1.24 | −0.68 |
Ts8 | 0.02 | 150 | 0.41 | 1.10 | −0.72 |
Ts9 | 0.02 | 270 | 0.41 | 1.58 | −1.08 |
- Note: Ts: styrene-TMPTA sulfonated resin. The sulfonations were conducted at 57 °C. The initial mass fed into the sulfonation step was 4 g.
Based on the data in Tab. 4, the resins showed moderate mass variation ranging from 10 % to 20 %. However, this may suggest some level of degradation, especially in resins containing acrylate groups that are prone to hydrolysis under sulfonation conditions [15, 20]. The hypothesis that hydrolysis may have occurred due to water present from the sulfuric acid equilibrium [21] remains a plausible explanation, although it cannot be confirmed based on the current data.
The IECs observed ranged from 0.36 to 0.64 mmol g−1, notably lower than those typically reported for commercial DVB-based resins, such as Amberlyst 36 (IEC = 5.45 mmol g−1) [22]. Although degradation during sulfonation is one possible contributing factor to the lower IEC values, no consistent effect of the factors studied could be identified. It is also worth noting that the limited number of experiments may restrict the ability to fully assess potential influences on the results.
To address the challenge of negative mass variation, a new set of experiments was proposed and conducted. The temperature of 30 °C was selected for these additional experiments with the aim of preventing resin degradation, while also examining the impact of sulfonation time on the IEC, in an effort to increase it without compromising the integrity of the resins. The conditions and subsequent results of this new approach are detailed in Tab. 5.
Experiments | Conditions | Properties | ||
---|---|---|---|---|
YTMPTA | Time [min] | IEC [mmol g−1] | Δm [g] | |
Tss1 | 0.02 | 60 | 1.26 | −0.97 |
Tss2 | 0.02 | 120 | 0.92 | −2.09 |
Tss3 | 0.02 | 180 | 0.90 | −1.99 |
Tss4 | 0.04 | 60 | 1.61 | 0.16 |
Tss5 | 0.04 | 120 | 0.96 | −1.27 |
Tss6 | 0.04 | 180 | 0.84 | −1.88 |
Tss7 | 0.06 | 60 | 1.20 | −2.16 |
Tss8 | 0.06 | 120 | 1.08 | −2.75 |
Tss9 | 0.06 | 180 | 1.43 | −2.74 |
- Note: Tss: styrene-TMPTA sulfonated resin treated with solvent. The sulfonations were conducted at 30 °C. Before the reactions, the resins were swollen in 1,2-dichloroethane for 24 h at a ratio of 1 g of resin per 5 mL of solvent. The initial mass fed into the sulfonation step was 4 g.
The results in Tab. 5 demonstrate an apparent increase in IEC values compared to those in Tab. 4. This improvement is more pronounced in experiments with shorter sulfonation times (60 min), which also show reduced mass loss in most cases. However, these observations are based on visual inspection of the data. Experiment Tss9, for example, presented a high IEC along with considerable mass variation, further illustrating the variability in the results. Although the resin swelling procedure carried out prior to sulfonation may have allowed greater acid diffusion and more extensive sulfonation in certain cases, a causal relationship cannot be confirmed based on the available data. The suggestion that improved acid accessibility may have contributed to the observed increase in IEC is a working hypothesis consistent with findings reported in the literature [23].
A broader look at the literature (Tab. 6) shows that a wide range of IEC values can be achieved depending on the resin structure and synthesis conditions. Although DVB-based systems often show higher IECs, various formulations have been used effectively depending on the application.
Resin | IEC [mmol g−1] | Application | Reference |
---|---|---|---|
PS-EGDMA | 4.00 | Esterification | [24] |
PS-TEGDMA | 4.05 | Esterification | [24] |
Styrene and 1,4-bis(4-vinylphenoxy) benzene | 5.23 | Acetilation | [25] |
Hypercrosslinked DVB | 5.06 | Removal of ammonium ions | [26] |
PolyHipe DVB | 3.08 | Removal of ammonium ions | [26] |
PS-DVB | 4.18 | Removal of ammonium ions | [26] |
Poly arilene ether ketone | 1.91 | H2/Air fuel cells | [27] |
PS-DVB | 3.18 | Esterification | This work |
PS-TMPTA | 0.641 | Esterification | This work |
Among the resins presented in Tab. 6, it is noticeable that those crosslinked with DVB generally demonstrate higher IECs compared to the other types of resins. In this study specifically, the mean IEC for a 14 % crosslinker concentration was 3.08 mmol g−1. In a study by Torquato et al. [26], comparisons among sulfonic DVB resins indicated that those derived from hypercrosslinked resins demonstrated even greater IECs, reaching 5.06 mmol g−1. This study similarly shows that resins with higher crosslinker concentrations had higher average IEC values.
Literature on swelling indices underscores the influence of different crosslinkers and their concentrations on resin swelling behavior, depending on the solvent used. For instance, Rana et al. [28] conducted swelling experiments on 11 distinct DVB crosslinked polystyrene resins across a wide array of solvents. Their data demonstrated that less crosslinked materials exhibited higher degrees of swelling. For example, when using CHCl3 as a solvent, a resin with a 3 % DVB exhibited up to nine times greater swelling compared to a resin with a 6 % DVB. This trend suggests that reduced crosslinking results in increased swelling compared to highly crosslinked resins.
3.2 Kinetic Modeling Results
The variables percentage of mass variation (Δm%) and IEC were predicted by the model through Eqs. (8) and (9).
It is noteworthy that YDVB and TDVB are variables related to the copolymerization step, which defines the structure of the polymer prior to sulfonation. Although these variables are not explicitly present in Eqs. (8) and (9), which calculate IEC and Δm%, they influence the model outcomes by modifying the polymer characteristics. In particular, the degree of crosslinking depends on YDVB and TDVB, and this, in turn, affects the values of the kinetic parameters kd and ks. As a result, the effects of YDVB and TDVB on IEC and Δm% are indirectly captured through their influence on kd and ks. The same reasoning applies to the crosslinker TMPTA, which also affects the polymer structure and, consequently, the model parameters.
The predictions of IEC and Δm% were compared to the experimental data, first, considering Ms = 81 g mol−1, which provided the fittings depicted in Fig. 2a,b. Kucera [19] states that the sulfonation of aromatic rings can yield different groups attached to them, such as SO3H (81 g mol−1) and SO3SO3H (161 g mol−1). It can be observed that Fig. 2b shows a reasonable fitting for IEC. In spite of being related to the IEC, most predicted values of Δm% are below the respective experimental values for Ms = 81 g mol−1, as illustrated in Fig. 2a. It can be noted that, a way of increasing Δm% with constant IEC is by considering a higher molar mass of the attached groups. In this sense, the authors repeated the simulation with Ms = 161 g mol−1, found by Kucera [19]. The results are illustrated in Fig. 2c,d.
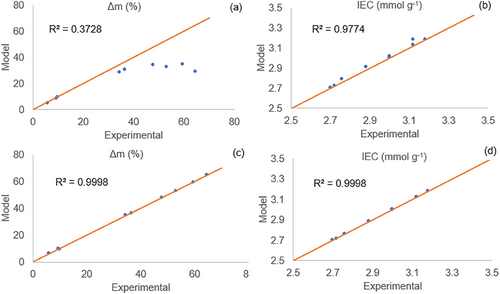
As discussed in the literature, sulfonation may lead to the incorporation of both ─SO3H and ─SO3–SO3H groups into the polymer structure [19]. In the present work, the model was used to evaluate the impact of two limiting values of molar mass: 81 g mol−1, corresponding to one ─SO3H group per site, and 161 g mol−1, associated with the ─SO3–SO3H structure. The best agreement between model and experimental data was obtained using 161 g mol−1, suggesting a predominance of ─SO3–SO3H units for the conditions studied herein, in-line with the mechanism proposed by Kucera and Jancar [19]. Future investigations may focus on intermediate average values or alternative reaction pathways, including the formation of sulfone-type crosslinks (─SO₂─), as discussed by Yu [29].
The modeling results of sulfonation of styrene-TMPTA resins are illustrated in Fig. 3.
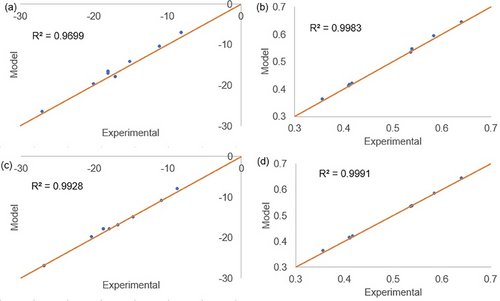
The fittings shown in Fig. 3 indicate a similar behavior than that observed in Fig. 2 for styrene-DVB resins. It suggests that, for styrene-TMPTA resins, the sulfonated rings may predominantly feature SO3–SO3H groups attached to them. The modeling of the sulfonation of styrene-co-TMPTA resins swollen in 1,2-dichloroethane also provided better fittings for Ms = 161 g mol−1 (R2 = 0.9941 for IEC and R2 ≈ 1 for Δm). The fitted parameters for all the simulations considering Ms = 161 g mol−1 are related in Tab. 7.
Resin | ks [min−1] | kd [min−1] |
---|---|---|
STY/DVB + DCE 90 °C | 5.39 × 10−3 ± 0.0012 | 3.89 × 10−3 ± 0.0018 |
STY/TMPTA 57 °C | 5.60 × 10−3 ± 0.0009 | 9.39 × 10−2 ± 0.0289 |
STY/TMPTA + DCE 30 °C | 1.37 × 10−2 ± 0.0056 | 7.00 × 10−2 ± 0.0427 |
- Note: DCE—1,2-dichloroethane. The table presents the average values of ks and kd, along with their respective standard deviations. These values were calculated based on the parameters obtained under different crosslinker feeding conditions for each case. Sulfonation of styrene/TMPTA using DCE was performed only for the crosslinker feeding time of 120 min.
It can be observed in Tab. 7 that the sulfonation of STY/DVB at 90 °C and STY/TMPTA at 57 °C without DCE yields quite similar ks values, despite the difference in temperatures. This result can be attributed to the natural swelling of STY/TMPTA in the reaction medium, which is more pronounced in comparison to STY/DVB resins. When STY/TMPTA is previously swollen in DCE, the sulfonation reactivities increase considerably, even conducting the reaction at 30 °C, as can be observed in Tab. 7.
In terms of degradation, it can be observed that styrene-DVB resins are way more resistant chemically in comparison to styrene-TMPTA resins. Even when sulfonation is carried out at 90 °C, the average kd value is considerably lower for STY/DVB than for STY/TMPTA processed at lower temperatures. These findings validate the experimental observations and suggest that TMPTA resins possess the benefit of enhanced swelling (improved accessibility). However, they also demonstrate a drawback, namely, a tendency toward easier degradation, likely attributed to the consumption of their acrylate groups during the sulfonation process.
As per literature, the stability of a resin is inversely related to its swelling properties. Consequently, TMPTA, known for its favorable swelling properties, tends to be more susceptible to degradation [30]. Similarly, Theodoro [8] observed that larger chains, such as sulfonated EGDMA and TEGDMA, exhibit increased vulnerability to degradation. Furthermore, degradation might also occur due to oxygen presence during copolymerization, resulting in the formation of peroxide bridges that weaken structural integrity [30].
4 Conclusion
Styrene-based resins crosslinked with DVB and TMPTA were synthesized and sulfonated with sulfuric acid. Initially, TMPTA-formulated resins demonstrated low IEC. However, upon modification of the sulfonation conditions—specifically, by lowering the sulfonation temperature and introducing solvent to the resins before the reaction—it facilitated the incorporation of sulfonic groups. This modification led to higher IECs in the TMPTA-based resins. For styrene-TMPTA resins, the effect of reaction conditions was evident, as the values of IEC almost tripled on average, from 0.493 mmol g−1 (experiments Ts1 to Ts9) to 1.133 mmol g−1 (experiments Tss1 to Tss9). This suggests that a pre-treatment with solvent followed by sulfonation at low temperature and for a short reaction time is recommended for styrene-TMPTA resins.
The modeling outcomes reveal insights into the sulfonation process of styrene-DVB and styrene-TMPTA resins. The comparison between experimental data and model predictions, considering different molecular weights of the attached groups, indicates that using the molecular weight of SO3–SO3H (161 g mol−1) yields significantly better fitting results. This suggests that sulfonation in both types of resins is mainly promoted by these larger sulfonating agents, rather than by the simpler SO3H species. The study also highlights differences in reactivity and degradation between styrene-DVB and styrene-TMPTA resins, with TMPTA-based resins exhibiting enhanced swelling properties but displaying increased susceptibility to chemical degradation, potentially linked to the consumption of acrylate groups during sulfonation. Additionally, the swelling behavior of TMPTA-based resins in reaction media can significantly impact their reactivity, leading to improved sulfonation reactivity when pre-swollen in solvent. Ultimately, these findings contribute to understanding the sulfonation mechanisms, providing valuable insights into the factors influencing IEC, mass variation, reactivity, and degradation behaviors of these resin systems.
The pseudo-homogeneous hypothesis was successfully applied to the present system, where different resins were compared for the same reaction time. The evolution of resin sulfonation with time involves a more complex approach that must consider the diffusion of acid through the particle layers, which might be subject of future studies.
Acknowledgments
The Article Processing Charge for the publication of this research was funded by the Coordenação de Aperfeiçoamento de Pessoal de Nível Superior - Brasil (CAPES) (ROR identifier: 00x0ma614).
The authors declare that they have no conflicts of interest.
Symbols used
-
- CHCl
-
- [mmol mL−1]
-
- CNaOH
-
- [mmol mL−1]
-
- M1
-
- [g mol−1]
-
- M2
-
- [g mol−1]
-
- Mp
-
- [g mol−1]
-
- Mps
-
- [g mol−1]
-
- Si
-
- [–]
-
- VNaOH
-
- [mL]
-
- Vt
-
- [mL]
-
- kd
-
- [min−1]
-
- ks
-
- [min−1]
-
- mf
-
- [g]
-
- mi
-
- [g]
-
- mp
-
- [g]
-
- mps
-
- [g]
-
- wd
-
- [g]
-
- ws
-
- [g]
-
- y1
-
- [–]
-
- y2
-
- [–]
-
- Δm%
-
- [%]
-
- Δm
-
- [g]
-
- IEC
-
- [mmol g−1]
-
- TDVB
-
- [min]
-
- YDVB
-
- [–]
Open Research
Data Availability Statement
The data that support the findings of this study are available from the corresponding author upon reasonable request.