Location Planning for the Production of CO2-Based Chemicals Using the Example of Olefin Production†
English version of DOI: https://doi.org/10.1002/cite.201800147
Abstract
A methodology for identifying suitable locations for the CO2-based production of olefins in Germany is presented. Based on electricity and CO2 requirements, locations are identified that can provide sufficient CO2 and renewable energy for the conversion of CO2 to olefins. In addition, the use of existing infrastructures is taken into account. The regional, technical renewable energy potential in Germany is sufficient to produce ∼ 800 kt of olefins from CO2-based methanol per year in one plant. But the currently available CO2 point sources with high CO2 concentrations of around 100 % are not sufficient to meet the CO2 requirement of an 800 kt a−1 methanol-to-olefins plant. If existing refineries are preferred due to existing infrastructure services, locations in the north of Cologne, in Lower Saxony, and in Brandenburg are particularly suitable. A full substitution of fossil olefins by CO2-based olefins is possible in Germany. The challenge is to provide sufficient renewable electricity for the production of H2 with a low CO2 intensity.
1 Introduction
Carbon dioxide (CO2) is a greenhouse gas that is mainly produced when fossil fuels are burned. However, the use of CO2 as a raw material is increasingly important as an option for climate protection and as an alternative raw material 1-7. To use CO2 as raw material, it is often captured at point sources, i.e., localized emitters from which CO2 is produced in large quantities and at a high concentration. In the next step, the separated CO2 is converted with hydrogen (H2) into basic chemicals (e.g., methanol) or higher value-added chemicals (e.g., polymers). Electrochemical direct synthesis is an alternative to these thermochemical processes. During direct synthesis, CO2 and water, e.g., are converted into C1–C4 alcohols in a single-stage electrochemical process. The advantages of such electrochemical processes include the completely electrically powered mode of operation, the single-stage process, and the possibility of decentralized production 8.
Thermochemical processes and electrochemical direct synthesis both share an increased demand for thermal and electrical energy 9. This is due to the thermodynamic stability and kinetic inertia of CO2 10. Thermochemical processes for CO2 conversion require a reactant that is highly reactive 10. This is, e.g., H2, which can be produced via energy-intensive processes such as water electrolysis 11. In electrochemical direct synthesis, the reaction is the driver of energy intensity. Therefore, CO2 conversion does not necessarily lead to environmental impact reduction 12.
In view of the energy transition and the decentralized electricity supply, low-emission and, at times, inexpensive electricity is to be expected in the future 13-15. From an environmental perspective, the local availability of CO2 and renewable energy sources (RES) is particularly relevant for CO2-based chemical production. This article, therefore, presents a methodology for deriving suitable locations for CO2-based chemical production in Germany, taking into account the local availability of CO2 and RES. The methodology is applied in an illustrative manner for CO2-based olefin production.
The basics of carbon capture and utilization (CCU), CO2 sources and uses, and H2 production are presented in the following section. In Sect. 3, the methodology and procedure for identifying suitable locations and in Sect. 4, locations for CO2-based chemical production in Germany are presented. In Sect. 5, the main results are summarized and possible limitations of the analysis as well as future research needs are discussed.
2 Carbon Capture and Utilization
According to von der Assen et al. 16, CCU involves the industrial capture of process and energy-related waste gases in order to obtain concentrated CO2 along with the separate functional utilization of CO2. Industrial capture comprises the capture of CO2 directly from the atmosphere or from CO2 point sources such as fossil fuel-based power plants. The functional utilization of concentrated CO2 involves a recycling process that goes beyond the storage of CO2. This can include the direct use of CO2 as a product (e.g., as a solvent) or the conversion of CO2 into other products such as fuels or basic chemicals. Processes that store CO2 without further use are defined as carbon capture and storage (CCS) 17.
2.1 CO2Sources
In Germany, CO2 is produced at various point sources, with different degrees of purity and in varying quantities. Tab. 1 presents CO2 sources including the CO2 concentration in the gas phase or atmosphere. Larger quantities of almost pure CO2 are produced during ammonia, ethylene oxide, and H2 production as well as biogas upgrading. Gas mixtures with a CO2 concentration of 3–40 % are obtained in the majority of industrial plants. In the case of fossil fuel-based power plants, in particular, coal-fired power stations, the service lives of these plants must be pointed out, as the end of the operation is to be expected 18. The percentage of CO2 in the air is approx. 0.04 %. From an economic and ecological perspective, CO2 sources that emit CO2 with high purity due to the process are particularly interesting.
Type of CO2 source |
CO2 concentration [%] |
CO2 emission quantity in DE [t a−1] |
Number of plants in DE |
---|---|---|---|
Air |
– |
– |
|
Natural gas-fired power plants |
16 986 000 24 |
56 24 |
|
Refineries and steam cracker units |
23 512 000 24 |
17 24 |
|
Coal-fired power plant |
258 351 000 24 |
65 24 |
|
Integrated pulp and paper mill |
7–20 25 |
7 815 000 24 |
24 24 |
Metallurgical plant and steelworks |
32 355 000 24 |
20 24 |
|
Cement works |
18 450 000 24 |
33 24 |
|
Ammonia production |
2 175 325 28 |
4 28 |
|
Ethylene oxide production |
284 700 29 |
4 29 |
|
Biogas upgrading |
1 153 146 30 |
189 30 |
|
H2 production |
2 995 898 31 |
28 31 |
-
post-combustion flue gas scrubbing with suitable absorbent agents (often monoethanolamine) in steam power plants
-
pre-combustion separation in integrated gasification combined cycle (IGCC) power plants
-
production of CO2-rich waste gases by combustion with pure oxygen instead of air (oxyfuel process) in steam and gas power plants.
Depending on the process (post- or pre-combustion incl. water gas reaction), flue gases may contain other main and trace components in addition to CO2. Before the CO2 can be used as a raw material, these components must be separated from the CO2 33. Trace compounds containing sulfur and nitrogen (SOX, NOX, H2S), can interfere with further processing as these trace compounds can contaminate the catalyst. In the case of CO2 capture via absorption (amine scrubbing), retrofitting power plants with amine scrubbing increases the energy demand of the power plant by approx. 25–40 % 33, which corresponds to an efficiency loss of up to 12 % 34.
2.2 CO2Utilization
The recycling of emissions containing CO2 essentially has two positive effects. Firstly, CO2 emissions can be retained in greenhouse gas-intensive industries. Secondly, the use of carbon emissions as a raw material may help to conserve fossil resources and establish carbon cycles by reducing the demand for carbon from fossil raw materials such as natural gas, crude oil, or coal. There is a wide range of options available for recycling CO2. Overviews of various utilization paths based on CO2 can be found in the literature 35-40. CO2 is already used in the food industry as a protective gas to preserve food or to produce carbonic acid in the beverage industry 41. Further fields of application include the agricultural industry (as fertilizer in the form of pure CO2 or as input for urea production), the textile industry, in which CO2 serves as a cleaning agent, and the use of CO2 as an extinguishing agent in gas extinguishers 3, 40, 41.
The importance of taking CO2 as a raw material for the chemical and manufacturing industries has increased in recent decades 32, 42. Technologies that can be used to activate the inert molecule CO2 and to bind it in different molecules have thus been (further) developed. An overview with a selection of possible synthesis routes, products, and their areas of application is given in Fig. 1.
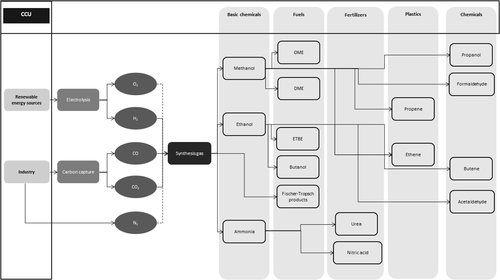
The feasibility of thermo-catalytic conversions of CO2 into basic and specialty chemicals were investigated in the work by Müller, Otto, and Peters et al. 6, 38, 43. While basic chemicals serve as a building block for a variety of downstream products and thus address a large sales market, the conversion of CO2 into specialty chemicals is more suitable for lower plant capacities due to the often limited market for target products and higher profit margins. In order to substantially reduce fossil resource use and greenhouse gas emissions, basic chemicals should be addressed first. Besides methanol, C2–C4 alcohols are important building blocks of the chemical industry. Ammonia is also one of the most important basic chemicals in the chemical industry and is the building block for industrially produced nitrogen-containing compounds such as urea, ammonium salts, and nitric acid.
Major advances in the commercialization of CO2-based syntheses are currently evident in methanol synthesis. Techno-economic studies on the operation of CO2-based methanol synthesis can be found, among others, in Abdelaziz et al., Atsonios et al., Kar et al., and Belotti et al. 44-47. In addition to methanol, processes for converting CO2 and H2 into alcohols (C2–C4) are also being developed. Muhler and Kaluza 48 describe the state-of-the-art in the conversion of syngas into higher alcohols and the increase in selectivity to ethanol.
In many industrial processes, N2 is present in the waste gas due to the supply of air and is available in the gas mixture in addition to CO2 for further use in the post-combustion processes mentioned above. The synthesis of nitrogen into ammonia with electrochemically produced H2 from renewable energy sources (RES) and the subsequent conversion with CO2 into urea enables the binding of CO2 32, 49. In this way, fossil raw materials, such as natural gas, could be substituted and process-related carbon-containing waste gas streams could be used.
2.3 Hydrogen Supply from Renewable Energy Sources
Due to the inertia of CO2, CO2-based synthesis requires large amounts of energy 43. This energy can be provided by the reactant H2. The recycling of CO2 to produce chemical raw materials can only achieve significant CO2 reductions in comparison to the conventional production of the materials if the necessary energy, in this case, the provision of H2, is largely carbon-neutral. A tried and tested process for producing H2 is water electrolysis 50. During this, water is split into its components H2 and O2 by applying an electrical voltage. If the necessary electricity can be provided by RES, H2 can be produced almost carbon-neutral.
In water electrolysis, a fundamental distinction can be made between alkaline electrolysis, polymer electrolyte membrane (PEM) electrolysis, and high-temperature steam electrolysis 32. In chloralkali electrolysis, which has been operated commercially since the end of the 19th century, dissolved sodium chloride or potassium chloride is electrolyzed in an endothermic reaction to produce chlorine, sodium hydroxide or potassium hydroxide solution, and H2 as a by-product. An overview of current systems for water electrolysis and their manufacturers can be found in Buttler and Spliethoff 51.
The capacity expansion of RES plants, caused by global climate protection targets, has increased significantly in recent years and led to the temporary production of more electricity than demanded 15, 52-54. Various storage technologies are discussed to store these unused amounts of electricity 55, 56. A promising option is to store this electricity in the form of chemically bound energy carriers such as H2. The electrochemical produced H2 can then be used either as an energy source or as a material.
The provision of energy for H2 production is guaranteed via the electricity grid. However, due to the homogeneity of the product, electricity consumed via the grid cannot be allocated to the source. This means, e.g., that it is not defined whether the consumed electricity was generated in a lignite-fired power plant or using photovoltaic systems. The consequence is that the electricity obtained from the grid is always a representation of the current electricity mix. By using locally generated RES, on the other hand, it would be possible to partially dispense with purchasing grey electricity from the grid and use a high proportion of self-generated RES-based electricity, similar to the use of electricity from domestic photovoltaic systems. In addition to this advantage, local grid bottlenecks, caused by the selectively increased feed-in of RES, could be avoided through reduced grid usage and thus, if necessary, local regulations on electricity production using RES could be reduced.
An alkaline electrolysis system with a specific electricity consumption of 5 kWh Nm−3 H2 57 was taken as the basis for calculating the necessary quantities of electricity for H2 production. Current forecasts for 2030 predict specific electricity consumption of 3.9–4.2 kWh Nm−3 H2 58. In order to assess the necessary RES, the H2 supply potential is defined. It describes the potential amount of electricity from RES to meet the demand for H2.
3 Methodological Procedure
-
CO2-based products and associated CCU technology
-
Type and regional availability of CO2 sources
-
Regional RES potentials
The methodological procedure for determining suitable locations is illustrated in Fig. 2.
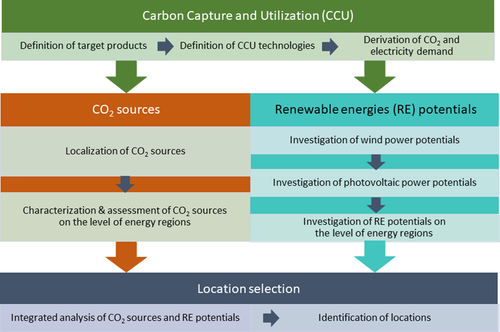
The first criterion serves to select the CCU technology. Only CCU technologies that have already been commercially implemented are taken into consideration. A CCU technology is the conversion of CO/CO2/H2-containing waste gases into propene and ethene via the intermediate product methanol. Both CO2-based methanol synthesis and the synthesis of methanol into olefins are already operated on a commercial scale and have a high degree of technological maturity 40, 59, 60. Processes to produce olefins from methanol are also called methanol-to-olefins (MTO) processes 61. A special process modification with increased selectivity to the target product propene is the methanol-to-propylene (MTP™) process developed by Lurgi (now Air Liquide) 62. So far, commercial MTO and MTP™ plants can only be found in China. The reason for this is the high availability of cheap natural gas and coal to produce syngas. The largest MTO plants have capacities of 600–800 kt propene and ethene per year 60. Air Liquide currently operates three MTP™ plants, each with propene capacities of around 500 kt per year 60, 62.
As this technology has already been widely implemented compared to other CCU technologies, it is used for location analysis. The focus on the CO2-based production of propene and ethene is also supported by the existing distribution infrastructure in Germany and Europe. New processes could thus be integrated more efficiently into the existing supply chains. The operating companies for the propene and ethene pipeline are the Duisburg-based companies ARG mbH & Co. KG (ethene) and PRG Propylenpipeline Ruhr GmbH & Co. KG (propene). Technical data for the pipelines can be found on the respective company websites.
Olefins are traditionally produced via rectification and the cracking of crude oil 63. The crude oil is first broken into different fractions by means of atmospheric and vacuum distillation. Around 10 % of the crude oil is rectified into naphtha for the chemical industry 64. The naphtha fraction is then converted by splitting heavy, long hydrocarbon chains into light, shorter hydrocarbon molecules (“cracking”). Detailed comparisons of the energy demands and CO2 emissions of the various ethene and propene production processes based on crude oil, natural gas, shale gas, CO2, and biomass are given in Zhao et al. 65 and Ren 66.
Large petrochemical production plants with refineries, steam crackers, and the necessary pipelines for crude oil, ethene, and propene in Germany can be found in Germany Trade & Invest 67. To identify and evaluate possible locations to produce olefins from CO2, the necessary mass and energy flows for the production of 1 t olefins are presented in Fig. 3 which addresses the CO2 demand (criterion 2) and the demand for electricity from RES (criterion 3) for olefin production. The energy required for the provision of CO2 is not included, as it depends on the CO2 source and the respective separation process (see Sect. 2.1). In addition, life cycle assessments have shown that the greatest environmental impact is associated with the provision of H2 55. Water demand and oxygen produced from electrolysis were also not taken into account in the location planning.

The electrical power demand for the production of H2 and the operation of the plants as well as the necessary amount of CO2 are standardized at one metric ton of olefins (the term olefins is used below to refer to the composition of 0.643 t propene and 0.357 t ethene) in order to enable a comparison with conventional production. The energy demands shown in Fig. 3 take into account the thermal and electrical energy required for the respective sub-processes. Only in the case of electrolysis, it was assumed that only electrical energy is needed.
The product spectrum in the Lurgi MTP process consists of 67 % propene, 3 % ethene, 30 % liquefied petroleum gas (LPG), and light gasoline 62. A product distribution of the MTO process according to Jasper and El-Halwagi 61 of 64 % propene and 36 % ethene is assumed for further calculations.
In order to consider the second criterion, i.e., CO2 sources, industrial CO2 sources were determined with the help of a systematic literature analysis 68, 69. The locations, quantities, and quality of the CO2 point sources in Germany are assessed using the European Pollutant Release and Transfer Register (E-PRTR) 24. In addition, other literature sources are used for plants not subject to reporting requirements (e.g., biomethane plants) 28-31. CO2 sources are classified according to their CO2 purity and CO2 concentrations given in Tab. 1.
For the third criterion, namely, RES potentials, a technical potential is established for the provision of RES. The aim is to determine the general suitability of deploying RES-using power plants in a region. The work of Fraunhofer Institute for Environmental, Safety, and Energy Technology UMSICHT and Advanced System Technology (AST) Branch of Fraunhofer Institute of Optronics, System Technologies, and Image Exploitation IOSB will be considered for this purpose 70, 71. The technical potential represents part of the theoretical potential, in which restrictive factors that exclude certain areas of a region are employed. To determine the technical potential, geographical conditions and topological and infrastructural land availability were taken into account as reasons for exclusion. Legal restrictions and distance regulations such as protected areas or buffer distances from settlement areas and infrastructure facilities were also included in the analysis 71. In the analysis key figures for the technical installations, which have a direct influence on the performance data, and key figures that have an effect on the placement options and space requirements of the installations, such as the hub height and rotor diameter of wind turbines, are used. A distinction is made between the installed capacity of wind turbines and photovoltaic (PV) systems and the expansion potential.
The methodology used to determine the area and potential of wind energy usually follows a fixed sequence, such as that carried out in studies commissioned by the German Wind Energy Association 72 or the State Agency for Nature, Environment, and Consumer Protection North Rhine-Westphalia (NRW) 73. In order to determine the potential for the use of wind power, the following analyses were carried out: restriction analysis, potential wind energy analysis, and energy yield analysis. Dummy wind turbines are placed on the identified suitable areas. The respective plant parameters can be taken to calculate the number of installable plants, the installable capacity, and the associated energy yields at the wind turbine locations.
The solar potential for electricity generation takes into account the roof area and open space solar potential. To analyze potential open-space PV plants, areas were selected that are fundamentally suitable for establishing a solar park to produce eligible electricity in terms of the German Renewable Energy Sources Act (EEG). These include, e.g., edge strips along freeways and railroads, stockpiles, or even parking lots 74. From these, areas were subsequently excluded that are not suitable as solar parks due to their specific properties, e.g., areas which are under nature protection, oriented towards the north, in the immediate vicinity of shading objects such as forest areas or buildings, or are smaller than a defined minimum size. For the remaining areas, the installable module area and the potential electricity yield are determined from information on sunshine duration or global radiation, taking into account the geographical location.
A complete individual analysis of all roof areas in Germany would be data-intensive and time-consuming. Hence, an aggregated form of analysis was applied. The potential of roof-mounted PV systems was determined based on the settlement structure. Model regions were investigated, potentials of typical settlement structures for residential, commercial, and industrial areas, city centers, and rural areas were determined, and these results extrapolated to the building stock in Germany 74.
Applying this approach results in a total potential of 6975 TWh, which corresponds to a higher potential compared to the net electricity generation of 3000 TWh in 2050 forecasted by the German Federal Environment Agency (UBA) 75. The calculated potentials lie above the wind potentials determined by the German Wind Energy Association (BWE) and UBA 72, 76. The installable capacity of 2459 GW identified in this study is higher than the wind potential of 1188 GW determined by UBA 76 and 1500 GW calculated by the BWE 72. This is due to less restrictive assumptions on the use of wind energy in forest areas, whereby the potential usable area increases to 30 % (BWE: 22 %). In addition, the potential calculated in this study includes many wind farms with densely packed plants.
Three scenarios were developed for the location analysis for CO2-based olefin production (see Tab. 2). In scenario 1, locations are sought where the plant network of methanol and MTO plants is supplied with sufficient CO2 and RES for the production of 800 kt of olefins per year. Scenario 2 examines existing refineries and their potential production volumes of CO2-based olefins. The advantage of integration into existing refineries is that the infrastructure needed to distribute the olefins is already in place. In scenario 3, the substitution of petroleum-based olefin production by CO2-based olefin production throughout Germany is investigated. An annual production volume of ethene and propene in Germany is 9094 kt 77.
|
Scenario 1 |
Scenario 2 |
Scenario 3 |
---|---|---|---|
Brief description |
Installation of the currently largest commercially operated plant. |
Additional CO2-based production at refineries. |
Substitution of the entire German ethene and propene production |
Olefin production |
800 kt a−1 olefins (515 kt propene and 285 kt ethene) |
Depending on the site-specific quantity of CO2 available. |
9166 kt a−1 olefins (5156 kt propene and 4010 kt ethene) |
Methanol production |
1824 kt methanol |
20 898 kt methanol |
|
CO2 demand |
2510 kt a−1 CO2 |
28 538 kt a−1 CO2 |
|
H2 demand |
345 kt a−1 H2 |
3920 kt a−1 CO2 |
|
Electricity demand |
21.28 TWh a−1 |
243.82 TWh a−1 |
Using geographic information systems (GIS) and taking into account the amount of CO2 available regionally, potentially suitable locations for MTO plants are identified according to the scenario-specific data from Tab. 2 and the regional potential availability of RES. For this purpose, the CO2 point sources and the RES potential are spatially aligned at the level of the energy regions. The classification according to energy regions is carried out as in the Fraunhofer Institute for Environmental, Safety, and Energy Technology UMSICHT and AST Branch of Fraunhofer Institute of Optronics, System Technologies and Image Exploitation IOSB 70. In addition to settlement density, this is based on the degree of centralization. In total, 146 energy regions were defined in Germany. Other location factors such as the availability of labor are not considered but would have to be taken into account in the case of specific location analysis.
4 Results and Discussion
To analyze the distribution of industrial CO2 sources and to conduct location planning for future chemical plants with CO2 use, two overview maps of the CO2 point sources were developed (see Fig. 4). The maps provide an overview of the spatial distribution of the CO2 point sources and the available CO2 quantities. The overview map of point sources with a low CO2 concentration in flue gas (≤ 35 %) for lignite-fired power plants, coal-fired power plants, natural gas-fired power plants, refineries, steel mill gas power plants, waste incineration, steel and iron production, cement production, lime production, and pulp and paper production is based on the data from operators subject to mandatory reporting from the E-PRTR for the reference year 2015 24. The European Union 78 requires all operators of facilities above an emission threshold of 100 kt CO2 per year to report to their competent authority. In 2015, this included 397 emitters from 41 different economic sectors 24. The number of emitter types was reduced to 20 different CO2 point source types and 351 emitters based on the minimum contribution of 1 % to the total emissions.

Fig. 4 (right) summarizes the corresponding distribution of industrial CO2 point sources with a low concentration (≤ 35 %) for Germany. The figure shows that in Germany CO2 emissions from lignite-fired power plants (162 105 kt a−1 CO2) and hard-coal-fired power plants (96 246 kt a−1 CO2) dominate in terms of volume, although CO2 is present in low concentrations in the flue gas of these plants. It can also be concluded that the majority of emitters with low CO2 flue gas concentrations are located in NRW, both in terms of quantity (187 283 kt a−1 CO2) and number (104 emitters). CO2 use is, therefore, a particularly interesting option for NRW, as CO2 emitters and consumers are located in close proximity 64. There are also plants in which CO2 separation takes place due to the primary production, e.g., CO2 separation in ammonia production 79.
In addition to process-related CO2 separation in ammonia plants, biomethane, ethylene oxide, and H2 production, CO2 is obtained in high purity as a by-product. According to the Industrieverband Agrar e.V. (IVA) 28, ammonia was produced at four sites in Germany in 2015. Actually, 189 biogas plants with gas processing exist in Germany 29. Rebsdat and Mayer 30 identified four ethylene oxide production plants and Maisonnier et al. 31 28 plants where H2 is produced from methane by means of steam reforming. The locations of the CO2 point sources with high CO2 content are indicated in Fig. 4a. An extensive distribution of CO2 point sources with high CO2 content (100 %) is evident. In particular, the high density of CO2 point sources in Lower Saxony (34 plants) and Saxony-Anhalt (33 plants) should be highlighted. H2 plants (2996 kt a−1), ammonia plants (2175 kt a−1), and biomethane plants (1153 kt a−1) represent the highest contributions to the total CO2 emissions (6609 kt a−1) from sources with high CO2 concentrations.
The use of pure CO2, which is obtained during ammonia, ethylene oxide, biomethane, and H2 production, makes sense from both an ecological and an economic viewpoint, since expensive processing steps, which are associated with increased energy demands, are avoided. However, the quantitative share of industrial CO2 sources with a high concentration of all CO2 point sources is only 1.46 %. The currently largest point source with highly concentrated CO2 (ammonia plant) emits up to 850 kt a−1 CO2 and thus allows for the production of 270 kt a−1 olefins. Compared to commercially established MTO plants with a production capacity of approx. 800 kt a−1 olefins, these smaller plants would probably not be competitive in standalone operation, as an analysis of existing plants in China demonstrates 60. For this reason, only CO2 point sources with low CO2 concentrations are taken into account in the identification of locations in the scenarios examined. The three scenarios (see Tab. 2) investigated for the assessment of possible locations for CO2-based syntheses are presented and evaluated below.
4.1 Scenario 1: 800 kt MTO Plant
The locations for the potential plants producing 800 kt olefins per year are indicated in Fig. 5 with green dots. Only locations where the aggregated amount of CO2 and the RES potential in the energy region are sufficient to cover the specific CO2 and H2 demands of the currently largest installed MTO plant (800 kt a−1 olefins) are marked. In addition to these locations, the ethene (red) and propene (yellow) pipelines are also shown. Furthermore, the green shades in the figure reflect the H2 supply potential in predefined energy regions. A dark green shade indicates a greater potential for H2 production. The potentially producible amount of H2 was examined and it was found that in all German energy regions the demanded amount of H2 can be provided for the olefin synthesis if the use of RES by other sectors and for other purposes is excluded.
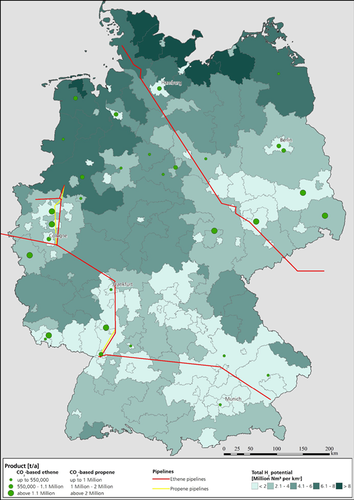
Locations where the olefin production potential is high and where there is a connection to the ethene and propene pipeline (see scenario 2) are interesting. These requirements are met by the sites located in NRW. Examples include the production plants of ThyssenKrupp Steel Europe AG in the north of Duisburg, the Oxea GmbH plants in Oberhausen, Ruhr Oel GmbH in Gelsenkirchen, INEOS Köln GmbH, and the Basell Polyolefine GmbH plants in Wesseling. Only the H2 supply potential there is lower than, e.g., in most RES regions in northern Germany. Locations near Hamburg, such as the Vattenfall Moorburg power plant and Holborn Europa Raffinerie are interesting as well. Good distribution channels are available for these locations via the pipeline and there is a connection with an energy region with high H2 supply potential.
4.2 Scenario 2: Refineries
Suitable locations for the production of olefins in the immediate vicinity of existing refineries are marked with blue triangles in Fig. 6. Only the CO2 generated in the refineries is taken into account for the potential production of olefins. This results in plant capacities of less than 800 kt. The potentially producible amount of H2 was examined and it was shown that in all energy regions the required amount of H2 can be provided for the olefin synthesis if the use of RES by other sectors and for other purposes is excluded.
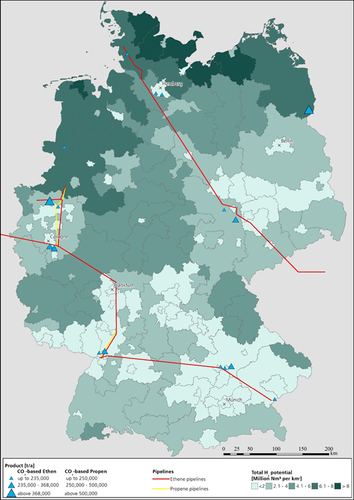
In particular, preference should be given to refineries where the olefin production potential is high. Connection to the ethene and propene pipelines is present at all but two of the identified locations. The refineries north of Cologne, in particular, emit large amounts of CO2 and are therefore particularly suitable for the CO2-based production of olefins. In Lower Saxony and Brandenburg each is one site that is not in the immediate vicinity of the ethene and propene pipelines. If CO2-based olefins were to be produced, a pipeline connection would first have to be established. The location in Brandenburg would be particularly interesting due to the high potential olefin production capacities.
Refineries are CO2 point sources with a lower concentration of CO2 in the flue gas. For this reason, the energy demand for the capture of CO2 from the flue gas must be taken into account in the specific location planning. If necessary, the energy demand could be covered by using excess heat at the plant.
4.3 Scenario 3: Substitution of Petrochemical Olefins in Germany
If the total German demand for propene and ethene is covered by CO2-based synthesis, the aim should be to provide this demand at as few locations as possible in order to benefit from economies of scale in large plants. An amount of 28 538 kt a−1 CO2 is required to produce the total demand for propene and ethene in Germany (9166 kt a−1). The largest CO2 point source in Germany is the Neurath power plant in Grevenbroich; 32 100 kt a−1 CO2 was emitted at this power plant in 2015 and this amount would cover the entire carbon demand for the CO2-based synthesis of propene and ethene in Germany. The limiting factor is the provision of the necessary H2 quantities of 3920 kt a−1 based on electricity from RES. The required amount of electricity from RES is equivalent to 244 TWh a−1. In total, only 64.47 % of the required electricity from RES could be provided by the respective energy region if the use of RES by other sectors and for other purposes is excluded. This means that RES would have to be sourced from other energy regions or the missing production capacity would have to be provided elsewhere.
5 Summary and Outlook
-
Scenario 1: Locations in Germany that are potentially suitable for producing 800 kt olefins per year were identified. The production capacity corresponds to the currently largest MTO plant in the world. Interesting locations are the Hamburg region and locations in NRW.
-
Scenario 2: The focus was on existing refineries. Locations in the north of Cologne, in Lower Saxony, and in Brandenburg, among others, are suitable for CO2-based olefin production. In the last two cases, a connection to pipelines would have to be established.
-
Scenario 3: In this scenario, the entire ethene and propene production of Germany is assumed to be produced by the MTO process. The limiting factor in such a scenario is the provision of sufficient electricity from RES for the production of H2. The demand for electricity from RES is 244 TWh a−1 (3.5 % of the German RES potential).
The analysis did not consider that, in addition to CO2 separation and purification, it might be necessary to transport CO2 present in the region due to differences in the spatial distribution of CO2 emitters and consumers. CO2 can be transported by pipeline, ship, rail, or truck. In order to reduce transport costs, CO2 can be compressed 80. The compression of CO2 is also necessary for methanol synthesis due to the production process. Possible compression steps are environmentally relevant as they are associated with increased electricity demand. Other studies have shown that CO2-based polymer production saves greenhouse gas emissions, but is associated with increased raw material costs 81.
Further restrictions will have to be investigated in future research. This applies, in particular, to economic considerations, especially taking rapidly changing framework conditions into account (e.g., prices of CO2 certificates). Current studies demonstrate that CO2-based polymer production is not economically competitive 82. In a large-scale implementation, the effects on the existing energy network and production structures must be investigated 83. The planning of specific plant concepts requires further region-specific investigations, which are currently being developed in various projects by Fraunhofer UMSICHT. It should also be noted that some of the considered CO2 point sources would play a tangential role in the future, such as coal-fired power plants due to the approaching phase-out of coal as an energy source.
Acknowledgements
The authors would like to thank Franziska Rapp for her support in creating the GIS maps. The authors also thank the Fraunhofer Gesellschaft for its financial support within the lighthouse project ‘Electricity as a Raw Material' and the German Federal Ministry of Education and Research (BMBF) for its financial support as part of the Carbon2Chem® project (grant number 03EK3037D).
The authors have declared no conflict of interest.
Abbreviations
-
- AST
-
advanced system technology
-
- BMBF
-
Bundesministerium für Bildung und Forschung/German Federal Ministry of Education and Research
-
- BWE
-
Bundesverband WindEnergie e.V/German Wind Energy Association
-
- CCS
-
carbon capture and storage
-
- CCU
-
carbon capture and use
-
- DME
-
dimethyl ether
-
- E-PRTR
-
European Pollutant Release and Transfer Register
-
- EEG
-
Erneuerbare-Energien-Gesetz/German Renewable Energy Sources Act
-
- ETBE
-
ethyl tert-butyl ether
-
- GIS
-
geographic information systems
-
- IGCC
-
integrated gasification combined cycle
-
- IVA
-
Industrieverband Agrar e.V.
-
- MTO
-
methanol-to-olefins
-
- MTP
-
methanol-to-propylene
-
- NRW
-
North Rhine-Westphalia
-
- OME
-
oxymethylene ether
-
- PEM
-
polymer electrolyte membrane
-
- RES
-
renewable energy sources
-
- UBA
-
Umweltbundesamt/German Federal Environment Agency