Applications of Biopolymers in Construction Engineering
Abstract
- Introduction
- Historical Outline
- The Construction Industry
- Size of the Industry
- Building Materials
- Chemicals Used in Construction
- Major Building Materials
- Concrete
- Fundamentals of Concrete Technology
- Ready-mix Concrete
- Precast Concrete
- Self-compacting Concrete
- Chemicals Used in Concrete
- Grouts and Mortars
- Floor Screeds
- Self-leveling Underlayments
- Tile Adhesives
- Joint Fillers and Compounds
- Injection Grouts
- Wall Plasters
- Plasterboards
- Paints and Coatings
- Oil and Gas Well Construction
- Drilling Fluids
- Oil Well Cementing
- Well Cement Spacers
- Concrete
- Biopolymers Used in Construction
- Lignosulfonates
- Biopolymers from Soil
- Humic Acid
- Lignite
- Hydrocarbon-based Biopolymers
- Natural Oils
- Waxes
- Bitumen and Paraffin
- Protein-based Biopolymers
- Casein
- Protein Hydrolysates
- Starch and Cellulose Derivatives
- Starch and Derivatives
- Cellulose Derivatives
- Seed Gums
- Guar Gum
- Locust Bean Gum
- Exudate Gums and Root Resins
- Oil of Turpentine and Colophonium
- Root Resins
- Microbial Biopolymers
- Xanthan Gum
- Scleroglucan
- Welan Gum
- Succinoglycan
- Curdlan and Rhamsan
- Chitosan
- Biodegradable Polymers
- Polyaspartic Acid
- Polyesters
- Biopolymers with Potential for Future Use
- Tannins
- Collagen and Gelatin
- Alginates and Carrageenan
- Pectin
- Tamarind and Cassia
- Gum Arabic, Gum Karaya and Gum Tragacanth
- Dextran and Pullulan
- Outlook and Perspectives
1 Introduction
The construction industry has become a major field of use for biopolymers. In 2000, an estimated $1–1.5 bn in sales was made at the manufacturer's level, and this growth is expected to continue. Applications of biopolymers in construction are widespread and diverse. In some cases, biopolymers offer distinct advantages in performance and/or cost over synthetic polymers, while in other areas biopolymers may be the only product available that can provide certain properties for building materials. Biopolymers also bear the image of being environmentally more acceptable than synthetic polymers produced in a chemical plant, and although this point can be argued it does influence the choice of materials used, especially for interior home building.
This review begins with a brief description of the construction industry and its usage of chemicals, in order to introduce the market. The technology of building materials using biopolymers is then presented to enable the reader to understand the functionality and benefits of biopolymers, after which the main applications of biopolymers in various segments of the construction industry are described. Because of limited space, only biopolymers with a significant usage volume are discussed here. Although many more biopolymers are in current use, their volume is often very limited, and so they were omitted from this discussion. Rather, an attempt was made to present details of the major biopolymers, to highlight their advantages over synthetic materials, and to identify their overall contribution to modern construction technology. Finally, an overview of selected biopolymers which are used in industries other than construction is presented. The aim of this chapter is to stimulate ideas among readers for new applications in building products, and in this respect the article concludes with a discussion of trends and perspectives for biopolymers in construction. For those readers interested in studying the subject in greater detail, selected references are provided throughout each section.
2 Historical Outline
The urbanization of mankind was made possible only because of the development of advanced construction engineering techniques and building materials. Under the Romans, construction technology flourished and significant discoveries were made, one of these being the manufacture of a cementitious material called “opus caementitium”. This was used, for example, in the foundations of the Roman Coliseum. Marcus Vitruvius Pollio (84–10 bc) described the astounding knowledge of his time about construction and materials in his famous encyclopedia, De architectura libri decem. This proves that the Romans had already recognized the role of admixtures to improve their building materials; for example, dried blood was used as an air-entraining agent, while biopolymers such as proteins served as set retarders for gypsum.
Most of the Roman construction know-how was lost when their empire perished, but in the 19th century Aspdin and Bleibtreu reinvented cement and developed industrial methods for its production. The 20th century became the age of admixtures, the history of which started in the 1920s with the introduction of lignosulfonate, a biopolymer, for concrete plastification. This was the first functional polymer in construction to be used on a large scale, though later on the use of lignite, cellulosics, and microbial biopolymers also became popular.
An overview of major milestones in the development of biopolymeric and synthetic admixtures is provided in Table 1. Biodegradable polymers are the most recent trend in the ongoing quest for improved functional materials in construction.
Year of Introduction |
Admixture chemistry |
Function |
Type of admixture |
---|---|---|---|
1920s |
Lignosulfonate |
Concrete plasticizer |
Biopolymer |
1940s |
Lignite |
Bentonite thinner |
Biopolymer |
1960s |
Xanthan gum |
Viscosifier |
Biopolymer |
1962 |
Melamine, naphthalene condensates |
Concrete super plasticizer |
Synthetic polymer |
1970s |
Cellulose ethers |
Water-retention agent |
Biopolymer |
1980s |
Vinylsulfonate Copolymers |
Water-retention agents |
Synthetic polymer |
1980s |
Polycarboxylate Copolymers |
Concrete super plasticizer |
Synthetic polymer |
1990s |
Polyaspartic acid |
Biodegradable dispersant, retarder |
Biopolymer |
3 The Construction Industry
Construction – one of the earliest industries – was developed to provide safe shelters for mankind. Today, while the industry provides basic housing and functional buildings, the breath-taking architecture of high-rise buildings and bridges also serves as an expression of our culture and civilization. It is only to be expected that, because of its importance and size, the construction industry still plays a significant role in our economy.
3.1 Size of the Industry
The construction industry is clearly one of the largest industries. In 2000, an estimated $3 trillion were spent worldwide on the construction of homes, industrial buildings and infrastructure such as roads, bridges, railway tracks, and water supply lines. In Europe, the total turnover of the construction industry in 2000 reached 835 bn Euros. A detailed break-down of European construction expenditure is given in Figure 1 (Becker, 2002). According to this source, home construction accounted for almost half of the construction expense, and industrial construction for about one-third. The remainder was spent on civil engineering projects. Of all expenses, 57% went into new construction and 43% into repair and renovation.
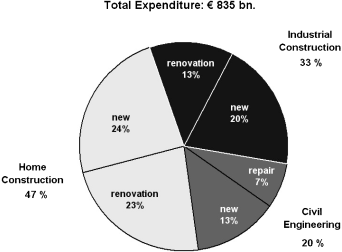
European construction expenditure in 2000.
3.2 Building Materials
Common building materials include:
-
inorganic, non-metallic materials (85% of total material consumption), e.g., binders, clay, ceramics
-
metallic materials (10% of total consumption), e.g., iron, steel, aluminum, copper
-
organic materials (5% of total consumption), e.g., lumber, plastics, polymers, textiles
Clay is still by far the most widely used inorganic building material, followed (albeit at long distance) by cement. Many types of cement that differ in composition, grinding size, etc., are available commercially, and in Germany alone over 600 different cements have been registered for construction use. Overall, in 2000, an estimated total of 1.5 billion tons of cement was produced for construction.
Gypsum and its dehydrated forms, hemihydrate and anhydrite, form another important group of building materials. Approx. 150 million tons of CaSO4 products are used in construction, with the bulk (∼60%) being added to cement to control cement setting time. Other major uses of gypsum products include wall plaster, anhydrite-based floor screeds and plasterboards. A comprehensive description of gypsum and its use in construction is provided by Kuntze (1984).
3.3 Chemicals Used in Construction
Modern construction often relies on the use of chemical admixtures to achieve the desired property of a building product. For example, the addition of lignin-based plasticizers to concrete enhances its flowability and workability, and permits the amount of mixing water in concrete to be reduced. The result is a gain in compressive strength of the concrete, and a better building product.
Other uses of chemicals in construction include higher labor efficiency, improved economics, and less environmental impact. Some products have helped to reduce heavy labor to a more acceptable level. For example, a self-leveling floor screed which contains a superplasticizer requires minimal labor to be spread and to achieve an even surface, whereas traditional floor screeds are a thick paste and are hard work to lay in place.
A wide variety of chemicals are used for different purposes and applications (Figure 2) (Becker 2002), and of the $50 bn spent on chemicals for construction, 48% were used in coatings such as interior and exterior paints.

Chemicals used in construction applications.
Building materials based on inorganic binders and coatings constitute the segment of the construction industry where biopolymers find their greatest application. Here, they are used as chemical admixtures for a variety of purposes, including:
-
dispersing/thinning effects
-
viscosity enhancement
-
water retention
-
set acceleration and retardation
-
air-entrainment
-
defoaming
-
hydrophobing
-
adhesion and film forming
Biopolymers clearly dominate the fields of rheology control (dispersing/thinning or thickening) and water-retention. In the latter application, the market relies almost entirely on biopolymers. With the exception of oil well construction, very few synthetics are used in conventional construction for water-retention.
4 Major Building Materials
Biopolymers are used in a great diversity of construction applications which will be unfamiliar to most readers. Therefore, the fundamentals of building systems using biopolymers are introduced first, the aim being to provide a better understanding of product requirements and an appreciation of the benefits accrued from the use of biopolymers.
4.1 Concrete
Concrete is the most widely used of all man-made building materials, and in 2000 approx. 5 bn m3 of concrete were produced.
4.1.1 Fundamentals of Concrete Technology
Concrete is made from cement, aggregates, chemical and mineral admixtures, and water. The active constituent of concrete is cement paste, the nature of which largely determines the performance of the concrete produced.
Cement is made by heating calcareous materials such as limestone or chalk and a source of silica and aluminum oxide such as shale, clay or slate in a rotary kiln to a temperature of about 1300–1450°C. The resultant clinker is cooled and ground with about 2–5% gypsum and/or anhydrite to a specified degree of fineness. The surface area of cement typically ranges between 2500 and 6000 cm2 g−1.
The major constituents of Portland cement are the four clinker phases:
-
tricalcium silicate (3 CaO⋅SiO2), C3S
-
dicalcium silicate (2 CaO⋅SiO2), C2S
-
tricalcium aluminate (3 CaO⋅Al2O3), C3A
-
tetracalcium aluminate ferrite (4 CaO⋅Al2O3⋅Fe2O3), C4AF
Upon contact with water, the phases hydrate in an exothermic reaction, and a hardened cementitious matrix mainly consisting of calcium silicate hydrate (C-S-H), is formed. C-S-H forms tiny needles which are 600 nm to 2 µm in length and 5–10 nm thick (Figure 3). The needles intertwine as in a zip fastener, and this gives hardened cement its considerable compressive strength. A comprehensive presentation of cement chemistry and technology has been provided by Taylor (1988).
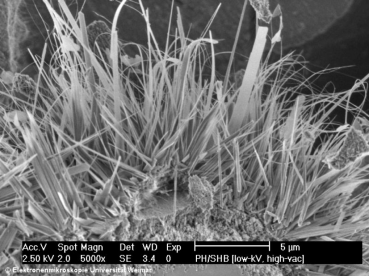
Environmental scanning electron micrograph of calcium silicate hydrate (C-S-H) in hardened cement.
Aggregates consist of fine or coarse silica sand and gravel. A mix of cement, water and aggregates of particle size <4 mm is called a mortar. Concrete also contains coarse aggregates with particle sizes up to 32 mm.
Mineral admixtures such as ground or granulated blast-furnace slag, fly ash, silica fume and others are incorporated into concrete to improve its quality.
Chemical admixtures confer beneficial effects such as flowability, water reduction, retardation or acceleration, air-entrainment and anti-settling properties.
The performance of concrete depends on the quality of the ingredients, their proportions, placement, and exposure conditions. For example, the hydraulic activity of the clinker, the fineness and particle size distribution of the cement and the amount of mixing water influence the physico-chemical behavior of the hardened cement paste. As a general rule, a fine cement and a low water-to-cement (w/c) ratio result in high compressive strength. Typical w/c ratios in concrete range from 0.30 to 0.70. A w/c ratio below 0.30 does not provide enough water for the cement to hydrate completely, and therefore is undesirable. A concise description of cement chemistry and concrete properties is given by Lea (1970), while general aspects of concrete technology are described by Neville (1981) and a valuable review of material science aspects of concrete has been provided in a recent article (Moranville-Regourd, 1997). These articles contain valuable information for those wishing to learn more about cement hydration, structures of hydrates, the colloidal chemistry of cement setting and hardening, the microstructure of concrete, concrete durability, high-performance concrete and organo-cement composites.
4.1.2 Ready-mix Concrete
Today, about 50% of the concrete produced is made in so-called ready-mix concrete plants. These units store cement in huge silos, with different grades of aggregates in covered compartments, and liquid chemical admixtures in dosage tanks (Figure 4). Ready-mix concrete is prepared by dosing the ingredients according to a recipe through automatic dosage units into a large concrete blender. Ready-mix trucks deliver the concrete to the construction site while the mixing drum is slowly rotated to ensure homogeneity upon delivery. The main advantages of ready-mix plants are better quality control of the concrete ingredients and improved quality consistency of the concrete batches. Many of these plants are equipped to recycle waste concrete and concrete wash water rather than attend to their disposal.
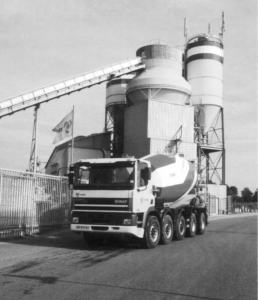
A ready-mix concrete plant.
4.1.3 Precast Concrete
Large concrete elements such as beams, pillars, floors or walls are often produced at so-called precast concrete plants. There, concrete is poured into molds to produce large numbers of elements of the same shape and size (Figure 5). Steam curing is applied to accelerate the development of early strength of the concrete, thereby improving the economics of the expensive molds. In comparison with ready-mix plants, precast plants typically produce concrete with a higher compressive strength. This is achieved by reducing the amount of mixing water, thus lowering the w/c ratios; consequently, precast plants use a significant volume of water-reducing polymers, referred to as plasticizers or superplasticizers.
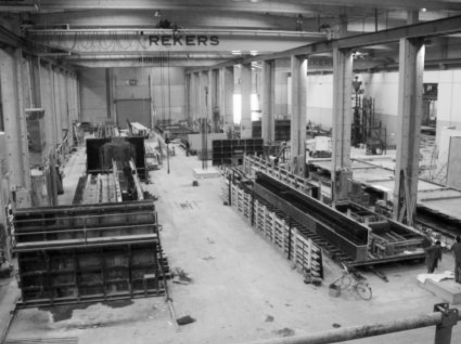
A precast concrete plant.
Approximately 25% of all concrete is produced in precast plants, 50% as ready-mix, and 25% in small mixers, or by hand.
4.1.4 Self-compacting Concrete
In 1983, Okamura and Ouchi in Japan began to develop a concrete with such exceptional fluidity that it later became known as self-compacting concrete (SCC). This concrete is so fluid that it requires little if any vibration to densify and release air after placement. In fact, it has almost self-leveling properties (Okamura and Ouchi, 1999).
The flowability of concrete is commonly measured by the slump test, as described by ASTM C 143. The test uses a frustum of cone 30 mm (12 inches) high. The test procedure is illustrated in Figure 6. Concrete is filled into the cone, which is lifted slowly. Concrete flowability is determined by measuring the decrease in height of the center of the slumped concrete, with the greater the decrease, the better the flowability. For structural concrete, a slump of 75–100 mm (3–4 inches) is sufficient for placement in forms. Highly workable, so-called flowing concrete shows a slump of about 150–200 mm (6–8 inches).
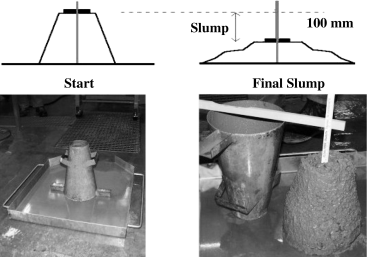
Slump test for measuring concrete flowability.
Other methods are also used to determine concrete flowability, and the German flow table method has recently become accepted as the European norm and is now included in the DIN EN 12 350 standard.
Powerful superplasticizers based on polycarboxylate chemistry are used to obtain SCC with a slump of 270–300 mm. It is easy to imagine that, because of its fluidity, such concrete has a tendency to segregate, but this is only apparent if bleeding water occurs on the concrete surface or if heavy aggregates settle at the bottom.
Two approaches have been taken to stabilize SCC. One method is to add larger amounts of fine aggregates or filler (particle size <0.1 mm), particularly fine sand or limestone. The fine aggregates, by virtue of their large surface area, tie up large amounts of water and prevent bleeding. They also impart some viscosity into the cement paste and reduce the settling of large aggregates. This type of SCC loaded with fine aggregates is referred to as “powder-type” SCC.
An alternate method of stabilizing SCC is to add a polymeric viscosifier that prevents bleed and sag. As will be discussed later, biopolymers have proven extremely effective for this purpose.
4.1.5 Chemicals Used in Concrete
Concrete uses almost exclusively liquid chemical admixtures, the main reason being ease of dosing and mixing. Major chemical admixtures for concrete include: dispersants based on lignosulfonates, β-naphthalenesulfonate resins (BNS), melamine formaldehyde sulfite resins (MFS), or polycarboxylates [PC; e.g., methacrylic acid-poly(ethyleneglycol)methacrylate ester copolymers]; retarders based on sodium gluconate or sugar-rich lignosulfonate; accelerators based on calcium nitrate or calcium formate; air-entraining agents based on root resin extracts, alkylsulfates of phenol ethoxylates; foamers based on protein hydrolysates; anti-segregation admixtures based on welan gum or starch; anti-washout admixtures based on hydroxypropyl cellulose; shotcrete accelerators based on sodium aluminate or fine, amorphous aluminum oxide; and shrinkage-reducing admixtures based on neopentyl glycol. Comprehensive overviews on chemical admixtures used in concrete have been produced by Ramachandran (1995) and Rixom and Mailvaganam (1999).
Clearly, the concrete industry uses a great diversity of admixtures, some important members of which belong to the group of biopolymers.
4.2 Grouts and Mortars
In contrast to concrete, grouts consist of fine and not coarse aggregates, a binder (cement or gypsum), and water. Most grouts contain aggregates with particle sizes <1 mm. Grouts with coarse aggregates up to 4 mm are called a mortar, and include floor screeds, self-leveling underlayments (SLUs), tile adhesives, joint fillers and compounds, and injection grouts.
4.2.1 Floor Screeds
Floor screeds are placed on concrete or wooden panels of floors to provide a firm, planar basis for laying floor carpets or parquet in homes and buildings. The most common are the “non-slump” cement-based floor screeds which are thick and require heavy labor to be placed and smoothed (Figure 7). Anhydrite-based floor screeds using a superplasticizer for high fluidity were introduced during the mid-1970s, and a typical formulation is shown in Table 2. Because of their fluidity, these grouts can be pumped and are easily placed by spreading them on the floor, with minimal labor needed to achieve an even surface (see Figure 7). Recently, calcium aluminate cement-based flowing floor screeds were developed and introduced, and a description of this technology has been produced (Harbron, 2001).
Component |
Parts [g] |
---|---|
Anhydrite |
350 |
Portland cement (CEM I 42,5 R) |
10.5 |
Quartz sand (0–2 mm) |
534.7 |
Limestone filler |
100 |
K2SO4 |
2.5 |
Methyl cellulose |
0.3 |
Superplasticizer (melamine resin) |
2.0 |
Water (w/b=0.54) |
195 |
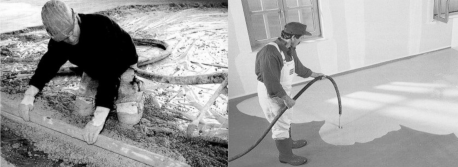
Placing of “non-slump” cement-based floor screed (left) and flowing anhydrite-based floor screed (right).
The high fluidity sometimes causes sag of aggregates and bleeding water to appear on the surface, though microbial biopolymers such as xanthan gum may be added to stabilize the grout (see below).
4.2.2 Self-leveling Underlayments
SLUs are placed on floor screeds, concrete or other bases to achieve a completely even surface. They are usually applied in thin layers of up to 15 mm, whereas floor screeds typically have a thickness of 20–50 mm. To achieve a thin layer, only very fine aggregates (particle diameter <0.1 mm) can be used.
SLUs require special dispersants to achieve uniform spread-out and a self-healing effect. Self-healing means that while being placed, the SLU grout does not show any furrowing if it is cut, for example, with a knife (Figure 8). Casein, a natural biopolymer obtained from milk, is the main product on the market to provide self-healing properties. The flowability of an SLU can be measured according to EN 12706 (edition November 1999). SLUs are usually formulated as dry compounds based on either cement or CaSO4-α-hemihydrate, though on occasion a highly reactive mixture of calcium alumina cement, Portland cement and CaSO4-anhydrite is used. When mixed with water, this grout gives a workability time for placement of approximately 1 h, and the grout (when laid) can be walked on after only 2 h. SLUs are often mixed by machine and therefore are referred to as machinery grouts.
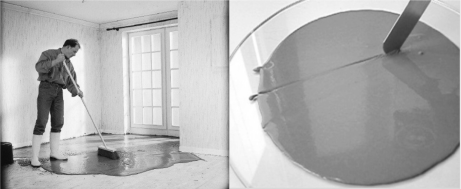
Placing of a cement-based self-leveling underlayment (left) and knife cut test (right).
4.2.3 Tile Adhesives
Tile adhesives are cementitious grouts which are used to fix tiles onto the floor or onto walls. The voids between individual tiles are filled with grouts (see Section 4.2.4).
Modern tile adhesives contain a cellulose-based water-retention and thickening agent and a redispersible powder for adhesion. (A typical tile adhesive formulation is shown in Table 3.) Because tiles are often placed on porous surfaces such as brick, water-retention is highly critical, as tiles will not hold firm, or may loosen or even fall off if the tile adhesive dehydrates from loss of water. During the 1970s, highly efficient cellulose ethers achieving water-retention of >97% were introduced; these not only provided a firm glue with the wall, but also allowed a reduction to be made in the overall amount of cementitious grout needed for tile adhesion. So-called “thin-bed” grouts, which are obtained by making furrows in the tile adhesive with a metal claw, have begun to become popular. These grouts are more expensive than conventional tile adhesives because they contain costly admixtures, but the overall material savings is more economic and the technique has become the standard method for tile setting (Figure 9).
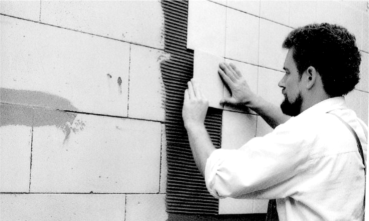
Tile setting using a thin-bed tile adhesive.
Component |
Parts [% (wt/wt)] |
|
---|---|---|
Standard adhesive |
Flexible Adhesive |
|
Portland cement |
35–50 |
30–45 |
Quartz sand 0.1–0.5 mm |
45–60 |
45–55 |
Calcium carbonate <0.1 mm |
5–10 |
5–10 |
MC |
0.37–0.7 |
0.3–0.5 |
HP starch |
0–0.06 |
0–0.06 |
Cellulose fibers |
0–0.5 |
0–0.5 |
Redispersible powder |
0–2 |
4–7 |
Calcium formate |
0–1 |
0–1 |
Tile adhesives constitute a huge market, especially in countries where ceramic tiles are popular. Germany alone, for example, produces in excess of 1 million tons of tile adhesives per year and uses about 5000 tons of cellulose ethers for this application.
4.2.4 Joint Fillers and Compounds
Joint fillers and compounds comprise a group of materials used to fill voids. Their function is to fill the void entirely without cracks, and to be wipe-resistant even in thin layers. The most important of these compounds include:
-
Tile grouts: these are used to fill tile voids in tile setting (Figure 10, left); they are cement-based, dry-bagged compounds, and only water is added at the construction site.
Figure 10Joint fillers for tile (left) and plasterboard setting (right).
-
Joint fillers for filling voids between plasterboards (Figure 10, right); these are gypsum-based dry compounds which are mixed with water on location.
-
Joint compounds for interior finishing are typically provided as a ready-mixed paste and are used as is. They do not contain an inorganic binder, but contain latex or polymer compounds which harden on drying and form a firm film. A state-of-the-art description of gypsum-based joint compounds citing numerous publications and patents has been produced by Patel (1998).
Joint fillers would not function well without the water-retention agents and thickeners which provide adhesion, ensure complete hydration of the binder, and prevent solids settling and crack formation. Once filled, the void must not sink in. Cellulose-based ethers (e.g., methylcellulose) are frequently used to provide water-retention and adhesiveness in these fillers; a typical formulation of a joint filler for tile setting is given in Table 4.
Component |
Function |
[% (wt/wt)] |
---|---|---|
Portland cement |
Binder |
35–50 |
Lime |
Binder |
0–5 |
Quartz sand <0.3 mm |
Aggregate |
35–45 |
Limestone powder <0.1 mm |
Aggregate |
10–15 |
Cellulose fibers |
Suspension aid |
0–0.5 |
Methyl cellulose |
Water-retention |
0.3–0.6 |
Dispersion powder |
Adhesion |
0.5–2 |
Calcium formate |
Cement accelerator |
0–0.7 |
4.2.5 Injection Grouts
Cracks in concrete, for example, are repaired by injecting cementitious grouts of very fine particle size. These grouts must be very fluid to achieve optimum penetration into the crack, and therefore high dispersant concentrations are used to provide extreme fluidity. However, this introduces the risk of sedimentation and the formation of bleeding water.
Biopolymers such as xanthan or welan gum, which provide a shear-thinning type of viscosity, are used to prevent the grout from disintegrating.
4.3 Wall Plasters
Wall plasters are either hand-troweled or machine sprayed on walls (Figure 11).
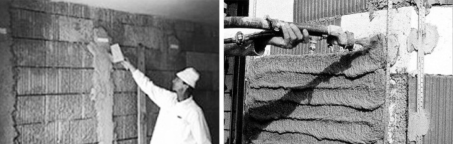
Plastering by hand-troweling (left) and machine spraying (right).
Plasters can be either cement-, cement/lime- or gypsum-based. Cementitious plasters are preferred on exterior walls, whereas gypsum is more common on interior walls. Since the mid-1970s, machine spraying has become the dominant method of placing plaster on walls, though this technology was only made possible by the development of new admixtures serving the following purposes:
-
Water-retention: most walls consist of highly porous materials such as brick, light-weight or porous concrete. Capillary forces cause these materials to suck water from the plaster, thus dehydrating it. The plaster cannot develop its full strength and will show cracks or spall off. In earlier times, the wall was completely soaked with water prior to placing the plaster, though this was clearly a laborious process. Water-retention agents (including biopolymers based on cellulose ethers) were developed to rationalize plaster placing. With this technology, 50 m2 per man-hour of plastering is possible, whereas previously only 20 m2 per man-hour might have been achievable.
-
Adhesion and sag prevention: machine spraying requires a viscosifier that provides enough adhesion to the wall to prevent the sag of aggregates or even of complete layers of the plaster and the formation of surface bleeding water. Again, derivatized biopolymers such as starch, guar and cellulose ethers have been introduced to achieve these properties.
To combine all these properties, modern plasters are based upon complicated formulations provided by specialized ready-mix or dry-mix mortar manufacturing companies. Formulations for cement-, cement/lime- and gypsum-based wall plasters are listed in Table 5.
Component |
Type of wall plaster |
||
---|---|---|---|
Cement |
Cement/lime |
Gypsum |
|
based |
based |
based |
|
Portland cement |
15–20 |
10–15 |
– |
Multiphase gypsum |
– |
– |
85–98 |
Lime |
0–2 |
5–10 |
0–3 |
CaCO3 or quartz <1 mm |
65–78 |
65–75 |
0–10 |
CaCO3 powder <0.1 mm |
5–10 |
5–10 |
– |
Perlite <1 mm |
0–2 |
0–2 |
0–1 |
Water-retention agent (e.g., MC) |
0.08–0.15 |
0.10–0.15 |
0.18–0.23 |
Adhesion agent (e.g., HP starch) |
0–0.03 |
0–0.03 |
0–0.05 |
Foamer (e.g., lauryl sulfonate) |
0.01–0.03 |
0.01–0.03 |
0.01–0.03 |
Gypsum retarder (e.g., tartaric acid) |
– |
– |
0.05–0.15 |
4.4 Plasterboards
Plasterboards are large thin gypsum panels covered with cardboard. They are made from CaSO4-β-hemihydrate, commonly known as plaster of Paris.
Figure 12 shows a schematic diagram of the manufacturing process. β-Hemihydrate plaster is fed into a continuous mixer from controlled feeding devices, mixing it continuously with water and additives to form a homogeneous slurry. This slurry is spread onto a continuous sheet of cardboard, covered with a second sheet, and passed over a molding platform. The gypsum hardens within minutes and is cut into separate panels which are dried in a continuous tunnel dryer. For more details on the process, plasterboard properties etc., refer to Wirsching (1985).
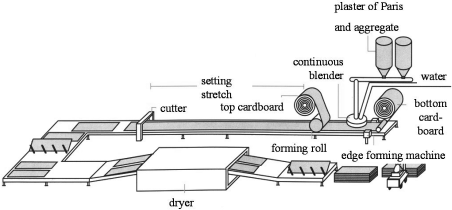
Schematic of plasterboard manufacture.
Three types of plasterboard, distinguished among other characteristics by their weight, are used in construction:
-
Partition panels are used in interiors as lightweight dividing walls. They are screwed to wooden or metal frames or pasted on bricks or concrete with special building plaster. Figure 13 shows a mason placing such boards. The joints between two panels are covered and finished with joint fillers or compounds (see Section 4.2.4) to form a smooth surface. Partition panels typically do not require chemical admixtures other than foamers to reduce density or starch adhesives to glue the cardboard.
Figure 13A mason fixing plasterboards.
-
Heavy plasterboards have a density between 800 and 1200 kg m−3 and are used for soundproofing or fire resistance. To achieve a higher density, the gypsum slurry is mixed with less water and more hemihydrate. The resultant slurry would be too viscous to be processed. Therefore, dispersing agents, in particular ammonium lignosulfate (see Section 5.1) are used to fluidify the slurry.
-
Gypsum fiberboards are fiber-reinforced gypsum elements made for optimum fire resistance and improved strength. Glass or polymer fibers are used. Again, they usually have a higher density and require biopolymer-based dispersants in the manufacturing process.
Modern plants for plasterboard manufacture have capacities of about 20 million m2 per year, and an annual consumption of 15,000 tons of hemihydrate plaster. Their use of biopolymer-based dispersants (mainly lignosulfonates) is appreciable.
4.5 Paints and Coatings
Generally, paints are suspensions of pigments in an aqueous or solvent-born liquid containing the binder. State-of-the-art descriptions of paint and coatings technology have been provided by Freitag and Stoye (1998) and Paul (1995).
Binders are required to achieve adhesion to the underground and to form a film binding the pigment particles through cohesion or adhesion together, thus producing homogeneous appearance of the color. Binders are either inorganic or organic and develop their binding properties upon drying of the paint.
An equally important property of the binder is to thicken the paint and prevent pigment sag. To achieve this and good workability (e.g., nondripping, good spread, etc.), rheology is tailored by using highly sophisticated, custom-made thickening agents. Cellulose ethers represent an important group of biopolymers used in this field and will be discussed in Section 5.5.2
An example of an inorganic binder is alkali silicate; typically, potassium silicate is used because of its lower toxicity. Upon drying of the paint, the silicate condensates to form a polysilicate layer which is immobilized by calcium from the base material. The result is an inorganic calcium polysilicate coating that has long-lasting properties.
The most common organic binders are based on latex dispersions, especially with styrene-butyl acrylate and ethylene-vinylacetate. Upon drying, the emulsified droplets of the dispersion coalesce and form a consistent film (Figure 14). Biopolymer-based binders that are also used (albeit to a lesser extent) include casein, cellulose ethers, and alginates.
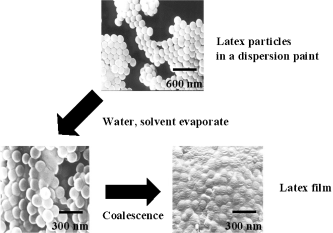
Coalescence of dispersion particles forming a consistent paint film.
Solvent-borne paints typically contain alkyde resins or linseed oil as an organic binder, while coatings (e.g., metal or floor coatings) are often based on reactive resins such as polyurethanes or epoxy resins. Coatings require less chemical admixtures such as thickeners and so are not discussed at this point.
4.6 Oil and Gas Well Construction
The construction of oil or gas wells to produce hydrocarbons from subterranean reservoirs is a technically challenging task, and one which utilizes significant amounts of biopolymers. Reservoir temperatures of up to 250°C, formation pressures up to several hundred bar, and drilling strata of 10,000 m and beyond require the use of sophisticated technology. As a consequence, oil and gas well construction has tended to foster new technology which has been used later for conventional constructions. An indication of the market size is given by the fact that, in 2001, some 88,000 oil and gas wells were drilled, and these had a combined strata of 120,000 km.
The construction of an oil well includes the following steps:
-
For land wells, to construct a concrete platform on which the drilling rig is to be mounted.
-
To drill a hole by a rotating drill bit and to remove drill cuttings from the borehole with a drilling fluid.
-
To cement a casing into the borehole for zonal isolation.
A schematic of oil well construction is shown in Figure 15, and a comprehensive overview of technologies and processes used in petroleum exploration has been produced by Economides et al. (1998).

Schematic of an oil well construction.
4.6.1 Drilling Fluids
Drilling fluids, also called “muds”, are circulated (as shown in Figure 15) in order to cool and lubricate the drill bit, to carry drill cuttings to the surface for separation from the fluid, and to counter the formation pressure, thus preventing influxes of oil, gas or reservoir fluids into the borehole. For a comprehensive overview of drilling fluid technology, history, products, processes and test methods, see Darley and Gray (1988).
The most common types of drilling fluids include:
-
water-based fluids; these consist of water, 1–5% clay (e.g., bentonite) for viscosity, a weighting agent (most commonly barite), and chemical admixtures such as thickeners, thinners or fluid loss agents.
-
oil-based drilling fluids; these consist of mineral or synthetic oil (e.g., C16–17 α-olefin or palm oil esters) as the primary liquid phase and up to 35% of water, saturated with CaCl2, emulsified in oil. Huge amounts of primary and secondary emulsifiers are needed to achieve a stable emulsion.
Water-based drilling fluids fall into two categories: “dispersed”, or nondispersed “polymer” mud systems. Dispersed muds contain high amounts of solids and bentonite and therefore require the addition of thinners to reduce viscosity to a sufficiently low level to provide high penetration rate of the drill bit. A basic formulation for a dispersed lignite mud and its properties is provided in Table 6. These fluids represent the classic type of water-based muds and initially used quebracho, tamarind or tannin extracts for thinning. During the 1950s, lignosulfonates and lignite were introduced as a new group of mud thinners, and the resultant chrome lignite/chrome lignosulfonate (CL-CLS) mud subsequently became one of the primary drilling fluid systems used worldwide, thus providing a huge market for the lignite and lignosulfonate biopolymers.
Mud additives |
Function |
Concentration [% (wt/wt)] |
---|---|---|
Bentonite |
Viscosifier |
6.0 |
Chrome lignosulfonate |
Thinner |
1.2 |
Caustic lignite |
Thinner |
1.8 |
Asphalt |
Filter-cake builder |
1.5 |
Sulfonated copolymer |
Filtration control |
1.0 |
Barite |
Weighting agent |
40 |
Mud properties: |
||
Mud weight |
1.67 g mL−1 |
|
Plastic viscosity |
20–24 |
|
Yield point |
16–18 |
|
Gel strengths (10 s/10 min) |
2–4/10–15 |
|
pH |
10.5 |
|
API filtrate (30 min, 7 bar, 20°C) |
1–1.5 mL |
|
HTHP filtrate (30 min, 35 bar, 80°C) |
6–6.5 mL |
Since the 1980s, “polymer” muds have become increasingly popular, one reason being less formation damage from decreased bentonite concentrations. Viscosity is mainly generated by polymers with thickening effect, and cellulose and starch ethers have been used extensively in this type of fluid.
In addition to providing viscosity for cuttings suspension, these biopolymers also control drilling fluid leak-off into tiny formation pores. This effect, which is also referred to as fluid loss or filtration control, is a key performance characteristic of a drilling fluid. As mentioned previously, drilling muds are weighted to achieve a density which is higher than the formation pressure, and because of this pressure differential the mud is pressed against the porous borehole wall. In the absence of fluid loss control chemicals, quick dehydration of the fluid would occur, resulting in a viscous, unpumpable mud. The filtration process on the borehole wall is shown schematically in Figure 16.
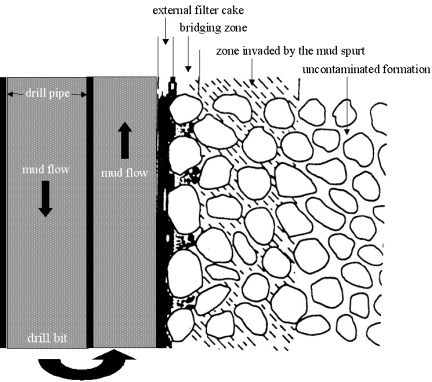
Filtration process of drilling fluid on borehole wall.
It is important to note that this filtration or fluid loss process is not related to the loss of fluid in larger cracks or voids of the formation. Rather, fluid loss refers to micropores in the formation with, for example, an average pore size in the range of several microns. To seal this off, the drilling fluid must form an impermeable filter-cake after releasing an initial spurt loss. Biopolymers are widely used to reduce filtration rate and to build thin, impermeable filter cakes. This effect is similar to the water-retention effect shown by the same polymers in conventional building systems such as plasters (see Section 4.3).
It is difficult to appreciate fully the benefits that such filtration control agents have provided in modern well construction; indeed, without their introduction the production of hydrocarbons from deeper reservoirs would not have been possible.
4.6.2 Oil Well Cementing
The construction of all oil and gas wells necessitates the cementing into place of a tubular pipe referred to as the casing. The main purpose of this is to create zonal isolation, i.e., adjacent reservoir zones of different pressures which in an uncased borehole may communicate, are sealed off by a cement sheath and casing (Figure 17).
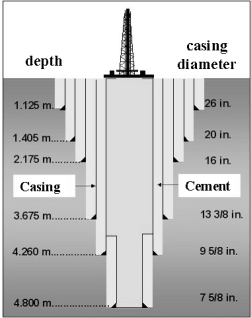
Schematic of cementing casing into an oil or gas well.
A borehole is cemented in intervals, which means that a certain strata (e.g., 1000 m) is first drilled and then cemented. Formation properties such as pore pressure, rock composition will dictate the casing program for the well. Complete descriptions of oil well cementing technology, equipment, processes and products have been provided by Nelson (1990) and Smith (1976), while details of field practice are described by Smith (1984).
For oil well cementing, a special Portland cement is used. Several types are available, and these are specified according to standards from the American Petroleum Institute (API, 1990). In the manufacture of API grade oil well cements, only pure clinkers can be used, and no secondary raw materials or alternative fuels (e.g., automobile tires) are permitted. The high purity is needed to obtain predictable rheological, hydration and setting properties at elevated borehole temperatures.
Oil well cement commonly is retarded to avoid premature setting while it is pumped downhole. The most common retarders are based on lignosulfonates (see Section 5.1). At increased temperature, they are capable of delaying the set of cement for several hours, and typically a pumping time (i.e., the duration of a fluid state of a cement slurry) of 4–6 h is required. After placement of the slurry, cement setting and strength development should occur immediately.
Like drilling fluids, cement slurries are pumped with overburden pressure against porous rock, and therefore filtration control is as important in well cementing as it is for drilling fluids. The only difference is that cement slurries have somewhat relaxed requirements for water-retention because their filter-cake is laid down on a filter-cake from the drilling fluid. Nevertheless, huge volumes of cellulose-based biopolymers are used for this purpose (see Section 5.5.2).
4.6.3 Well Cement Spacers
Before pumping oil well cement slurry into the hole, a so-called spacer fluid is pumped to displace the drilling fluid and some of the mud filter-cake.
Initially, spacer fluids consisted of abrasive materials (e.g., sharp quartz particles) and a dispersing agent, and were pumped in turbulent flow at high velocity to clean out mud, debris and filter-cake from the hole. Field experience showed, however, that dispersive spacers pumped under turbulent flow often resulted in severe channeling. Thick mud and the filter-cake on the borehole wall were bypassed, thus defeating some of the purpose of spacer application (Figure 18).
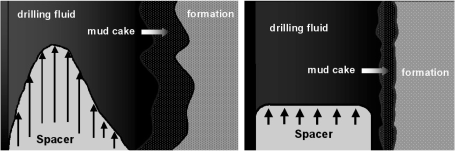
Hole-cleaning effects of a dispersive spacer pumped under turbulent flow (left) and a shear-thinning spacer pumped under plug flow (right).
Therefore, novel spacers based on shear-thinning rheology and pumped under plug flow conditions were introduced. These were found to be more effective in pushing thick mud upward and in cleaning the hole for the subsequent cement slurry. A schematic illustration of the hole-cleaning effect of a shear-thinning spacer is shown in Figure 18. Spacers rely on microbial biopolymers to achieve shear-thinning rheology, and represent a significant application for these products. Without good spacer fluids, many well bores would not achieve a tight cement sheath, and safety hazards would make costly repairs or even abandonment of the wells necessary. A state of the art report on modern spacer technology has been provided by Crook et al. (2001).
5 Biopolymers Used in Construction
The term “biopolymer” is somewhat ambiguous and requires clarification. In some cases, the term biopolymer is understood to be a polymer based on naturally occurring raw materials, while in others any biodegradable polymer – be it synthetic or of natural origin – is referred to as a biopolymer. Others use the term biopolymer only for polymers produced by microorganisms. For the purpose of this chapter, the term biopolymer comprises polymers which are:
-
naturally occurring polymers (e.g., starch) which may or may not be processed and/or chemically modified (e.g., carboxymethyl starch);
-
polymers produced in an industrial fermentation process by microorganisms; and/or
-
biodegradable polymers which can be based on naturally occurring or synthetic polymers.
A great diversity of biopolymers according to the definition above is used in construction, and an overview of the important classes of such biopolymers is provided in Table 7.
Biopolymer |
Source |
Chemically |
Function |
Major application(s) |
|
---|---|---|---|---|---|
Modified |
Primary |
Secondary |
|||
Lignosulfonate |
Wood lignin |
Yes |
Dispersant/Thinner |
Retarder |
Concrete, plasterboards, oil well construction |
Humic acid |
Soil |
Yes |
Water-retention |
Dispersant |
Oil well construction |
Lignite |
Coal |
Yes |
Dispersant/Thinner |
Water-retention |
Oil well construction |
Vegetable oils |
Plants |
Yes & No |
Carrier Fluid |
– |
Oil well construction; concrete |
Waxes |
Plants, Insects |
No |
Coating |
– |
Paints & Coatings |
Bitumen |
Coal, Petroleum |
Yes & No |
Coating |
Water repellant |
Road construction |
Asphalt |
Petroleum |
Yes & No |
Coating |
Lubricant |
Road construction; oil well construction |
Casein |
Milk |
No |
Dispersant |
– |
Grouts, paints |
Protein extract |
Animal hair, hides, hoofs |
Yes |
Air-entraining agent |
– |
Concrete, mortar |
Starch |
Corn, potato |
Yes & No |
Viscosifier |
Water-retention |
Grouts, plasters, oil well construction |
Cellulose |
Cotton, wood |
Yes |
Water-retention |
Viscosifier |
Grouts, plasters, oil well construction |
Guar gum |
Guar plant |
Yes & No |
Viscosifier |
Water-retention |
Plaster, oil well construction |
Xanthan gum |
Bacterium |
No |
Viscosifier |
Anti-settling agent |
Oil well construction, floor screeds, paints |
Welan gum |
Bacterium |
No |
Viscosifier |
Anti-settling agent |
Concrete, oil well construction |
Scleroglucan |
Fungus |
No |
Viscosifier |
Anti-settling agent |
Oil well construction |
Succinoglycan |
Bacterium |
No |
Viscosifier |
Anti-settling agent |
Self-leveling compounds |
Curdlan |
Bacterium |
No |
Viscosifier |
Anti-settling agent |
Concrete |
Rhamsan |
Bacterium |
No |
Viscosifier |
Anti-settling agent |
Grouts |
Chitosan |
Chitin |
Yes |
Viscosifier |
Anti-settling agent |
Oil well construction |
Polyaspartic acid |
Synthetic |
Yes |
Dispersant |
Retarder |
Gypsum retarder |
Polyester |
Synthetic |
Yes |
Dispersant |
– |
Grouts, plaster |
As can be seen in Table 7, the large majority of biopolymers act as thickeners or provide water-retention – two properties which often are intrinsic in the same product, the reason being the high molecular weight (>100,000 Da) that many of these materials possess. Biopolymers made by fermentation are often unsurpassed in that they impart a specific shear-thinning type of viscosity. As will be discussed later, this specific effect is of great value in certain building systems and explains the large use of these very expensive polymers. Dispersing effects are typically achieved by chemically modified, anionic polymers with rather low molecular weight (e.g., lignosulfonates). Some biopolymers have surface-active properties (e.g., protein extracts) and are efficient air-entraining agents for concrete or mortar, while others containing carboxylic groups (e.g., polyaspartic acid) are powerful set retarders for gypsum and cement.
The main groups of biopolymers used in construction are discussed in the following section, while those with random or potential future use are described in Section 6
5.1 Lignosulfonates
Lignosulfonates are produced by chemical processing of lignin, which is a natural biopolymer that occurs in wood and grass. The cell-wall tissue of wood is a complex mixture of polymers; holocellulose, which consists of cellulose and hemicellulose, comprises 70–80% of the tissue, while lignin forms the remainder. In the sulfite process, lignin and hemicellulose are dissolved in a hot acid sulfite solution and degraded. Calcium bisulfite is most commonly used for this process. The spent sulfite liquor contains about 10% solids, those being raw lignosulfonate, wood sugars, organic acids and resinous materials. A typical composition for raw sulfite liquor obtained from soft wood (e.g., spruce) is shown in Table 8.
Component |
[% (wt/wt)] |
---|---|
Lignosulfonate |
55 |
Hexose sugars |
14 |
Pentose sugars |
8 |
Hemicelluloses, sugar acids |
12 |
Acetic-, formic acid |
4 |
Resins, tall oil |
2 |
Ashes |
5 |
A variety of processes have been used to purify the sulfite liquor and render it suitable for different applications (Figure 19). For concrete applications, desugarification and sulfomethylation are the most important steps as this leads to the production of a less retarding and more water-soluble product. Even complete sugar removal from the liquor does not produce a nonretarding lignosulfonate. It has been shown that the phenolic hydroxyl group which forms part of the highly complicated lignosulfonate structure (Figure 20) exerts a certain retarding effect on cement, but this retardation is reduced by ethoxylation of the phenolic hydroxyl group (Chatterji et al., 2000).
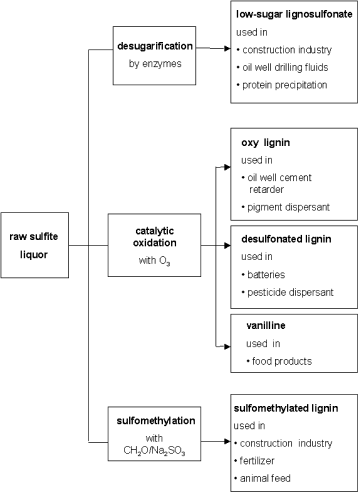
Processing of raw sulfite liquor into lignosulfonates.
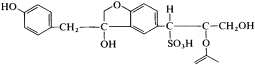
Repeating unit of a lignosulfonate molecule.
Lignosulfonates are the most common concrete plasticizer, their primary function being dispersion of the cement particles and improvement of concrete flowability. A secondary effect is that of cement retardation.
A typical lignosulfonate used as concrete plasticizer constitutes of a brown, 20–40% active liquor with a characteristic sweet odor. Its sugar content is 0.2–1% by weight of dry substance. The most common salts are those of calcium and sodium, but magnesium or ammonium salts (e.g., in plasterboard manufacture) are sometimes used. Typical average molecular weights range from 20,000–100,000 Da, with 80,000 Da being an optimum for concrete plastification. The degree of sulfonation may vary between 0.2 and 1.2 sulfonate groups per phenolic group, with 0.5–0.6 being the most common.
Lignosulfonates are used in concrete for two different purposes: first, to increase the flowability or workability of a concrete with a given w/c ratio; or second, to reduce the w/c ratio of a concrete without reducing flowability.
The effectiveness of sodium lignosulfonate on concrete slump at a given water content (w/c=0.68) is shown in Table 9. At an application of 0.1% lignosulfonate by weight of cement, slump was increased from 95 mm to 135 mm, indicating improved flowability and workability of the lignosulfonate-treated concrete.
Admixture |
||
---|---|---|
Property |
None |
0.1% Na lignosulfonate* |
w/c ratio |
0.68 |
0.68 |
Slump (mm) |
95 |
135 |
Slump increase (mm) |
– |
40 |
- * Dosage by weight of cement; concrete with 300 kg m−3 cement content.
The second use of lignosulfonates in concrete is that of water-reduction. A reduction in w/c ratio leads to a higher compressive strength of the concrete, which is highly desirable. Test results illustrating the gain in compressive strength by reduced w/c ratios achieved with a lignosulfonate admixture are shown in Table 10, the gain being particularly significant after 3 days and decreasing somewhat after 28 days.
Lignosulfonate dosage |
w/c ratio |
Air content |
Compressive Strength [% of control w/o admixture] |
|
---|---|---|---|---|
[% (wt/wt)] |
[% (vol/vol)] |
3 days |
28 days |
|
– |
0.58 |
1.3 |
100 |
100 |
0.14 |
0.54 |
2.4 |
125 |
112 |
0.28 |
0.52 |
2.9 |
130 |
115 |
The effectiveness of water-reducing admixtures is expressed as percentage reduction in w/c ratio of the untreated concrete. The data in Table 10 indicate that a 7% water reduction is achieved with 0.14% lignosulfonate, while a 10% water reduction is obtained with 0.28% lignosulfonate.
In general, the water-reduction achieved with lignosulfonates ranges between 5% and 15%, though some highly refined products obtained by ultrafiltration achieve 20% water reduction. This is almost as high as the water-reduction achieved with a more powerful group of dispersants that are known as superplasticizers (Table 11) which consist of synthetic polymers and achieve water-reductions up to 60%. As a consequence, lignosulfonates are mainly used for less demanding applications such as ready-mix concrete. Their slight retarding effect benefits this application because the initial slump obtained on addition of lignosulfonate at the mixing plant is retained better than with either MFS or BNS. The latter materials are preferred in the precast industry where high-strength concrete is the predominant product.
Chemistry of Product |
Classification |
Water-reduction [%] |
|
---|---|---|---|
Average |
Maximum |
||
Lignosulfonate |
Plasticizer |
5–15 |
20 |
BNS |
Superplasticizer |
10–25 |
30 |
MFS |
Superplasticizer |
10–25 |
30 |
Polycarboxylate |
Superplasticizer |
20–30 |
40 |
Amphoteric polycarboxylate |
Hyper-plasticizer |
30–45 |
60 |
In 1995, over 1 million tons of lignosulfonate were used in concrete – significantly above the combined volume of all other types of superplasticizers (Table 12). However, recent years have seen a decline in lignosulfonate usage, mainly because their main advantage of competitive price has been eroded as more pulp plants producing spent lignin liquor have been closed due to environmental problems. As a result, lignosulfonates are more scarce and so prices are rising. Some admixture companies have initiated programs to reduce or eliminate lignosulfonates from their formulations, but in years to come the availability and pricing of lignosulfonates compared with alternatives such as BNS, MFS and polycarboxylates will determine their future usage.
Product |
Worldwide use [tons] |
---|---|
Lignosulfonate |
800,000 |
BNS |
330,000 |
MFS |
100,000 |
Polycarboxylate |
50,000 |
Lignosulfonates are the most common retarders for oil well cementing. As described in Section 4.6.2, oil well cement must be retarded to avoid premature cement set in the well-bore induced by high temperature. Lignosulfonates are effective retarders to about 125°C bottom-hole circulating temperature, and function best with low-C3A cements. Carefully refined products are being used because their consistent performance is critical to the overall success of well cementing. Oxidized and sulfomethylated lignosulfonates are the most frequently used of these materials (see Figure 19).
Typical lignosulfonate dosages are 0.1–0.5% by weight of cement, and they show a sharp increase in retardation at higher concentrations (Figure 21). Consequently, overdosage in error runs the risk of over-retardation and is undesirable. Synthetic copolymers used at very high temperatures (>125°C) show a more linear correlation of dosage with retardation, but high cost prohibits their use at the low to medium temperatures where lignosulfonates remain dominant.
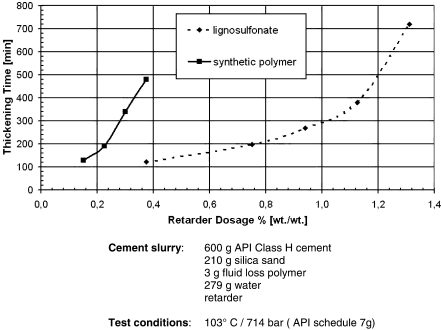
Retardation of oil well cement by lignosulfonate and synthetic polymer.
Another major use of lignosulfonates is in oil well drilling fluids. In about 1947, calcium lignosulfonate was introduced as a thinner for lime-treated muds, and became known as the “break-over chemical”, minimizing the viscosity hump or “break-over” that was caused by the addition of lime to freshwater-bentonite muds. Numerous lignosulfonate products have since entered the market. For high-temperature stable muds, chrome lignosulfonate has proved to be an effective thinner and filtration control agent, and when combined with chrome lignite (the CL-CLS mud) produces an easy-to-control water-based mud system with stability up to 225°C. The toxicity of chromium(VI) however drastically reduced the use of this additive, and today mainly sodium and calcium lignosulfonates are used at low to medium temperatures (50–125°C). At higher temperature, synthetic polymeric thinners (e.g., based on polyacrylate chemistry) are most often used (Plank, 1992).
5.2 Biopolymers from Soil
The anaerobic degradation of plants over many centuries has led to the production of the biopolymers that occur in soil or in deeper sections of the Earth's crust. These are precursors for the formation of coal, oil and gas, and humic acid and lignite (brown coal) represent two examples which have been used in the construction industry.
5.2.1 Humic Acid
Humic acid is an important soil constituent and an intermediate in the conversion of vegetation to coal. Because of the complexity of the source materials, details of the structure of humic acid have not yet been agreed upon (Steelink, 1963), though various studies have shown it to contain phenolic and carboxylic compounds. The molecular weights range from 300 to 4000 Da (Steelink, 1966).
Humic acid is the starting material for graft polymers used in oil well cementing. Giddings and Williamson (1987) have patented a process of grafting 2-acrylamido-2-methylpropane-sulfonic acid, N,N-dimethylacrylamide and acrylonitrile monomers on a humic acid backbone, and the resultant graft polymer was seen to exhibit excellent filtration control properties in well cement slurries. The effectiveness of this graft polymer in fresh water cement slurries is shown in Table 13.
FANN® rheology [@600-300-200-100 rpm] |
Fluid loss [@85°C, 1000 psi] |
---|---|
224-111-71-34 |
28 mL |
- * Slurry from 500 g API Class H cement, 225 g water, 6 g graft polymer, 175 g silica sand, 6.5 g lignosulfonate retarder, 1 g defoamer.
5.2.2 Lignite
Lignite, variously also called leonardite, mined lignin, brown coal or slack, represents a further degraded humic acid. A natural deposit in North Dakota is the principal source of lignite used in construction applications.
Mined lignite is made water-soluble by addition of alkali such as caustic soda. The resultant sodium lignite, commonly known as “causticized lignite”, is an inexpensive, multi-functional oil well drilling fluid additive. Initially considered only as thinner for water-based muds, it now serves also for filtrate reduction, oil emulsification, and stabilization of mud properties against the effects of high temperature.
The excellent properties of lignite, particularly in combination with lignosulfonate, resulted in the development of a famous water-based drilling fluid system, the CL-CLS mud (chrome lignite-chrome lignosulfonate; see Section 4.6.1). After 1960, this fluid became very common in US land wells, and represented a highly dispersed mud system with a relatively high bentonite content (3–10%) in which both lignite and lignosulfonate dispersed the solids. The chromium salts provided optimum stability at temperatures up to 225°C (Darley and Gray, 1988).
Since the 1980s, cellulose- and synthetic-based polymers have gradually replaced the dispersed CL-CLS muds. Another problem arose due to environmental concerns over the toxic effects of chromium which leached from mud spills or disposed drill cuttings into the ground water. The industry has responded to these concerns by introducing less toxic zirconium salts or synthetic polymers for high-temperature drilling, though at low to medium temperatures sodium or potassium lignite still is used.
A vinyl grafted lignite fluid loss additive has been developed for water-based drilling fluids and oil well cement slurries (Huddleston and Williamson, 1990). For example, a graft polymer containing 20 wt.% lignite, 60 wt.% 2-acrylamido-2-methylpropane-sulfonic acid and 20 wt.% methacrylamido propyltrimethyl ammonium chloride considerably reduces the fluid loss of a drilling fluid aged at 350°F.
Oil-based drilling fluids typically are an emulsion of ∼70% of an oil phase (e.g., diesel) and 30% of an aqueous phase saturated with calcium chloride. Emulsifiers are used to achieve homogeneity and stability of the fluid. A reaction product of sodium lignite with quaternary amines having 12 to 22 carbon atoms in one of the alkyl chains, functions as an effective primary emulsifier and filtration control agent (Jordan et al., 1966), and is often combined with secondary emulsifiers such as organophilic clays.
Although the use of lignite in oil well drilling has declined in recent years, approximately 50,000 tons are still consumed annually by this industry.
5.3 Hydrocarbon-based Biopolymers
Numerous hydrocarbon-based polymers found in nature are either produced by plants or were formed by anaerobic degradation of biomass in the Earth's crust.
5.3.1 Natural Oils
These are divided into subgroups of drying and semi- or nondrying oils. The first group includes linseed oil and fish oil, both of which represent important constituents in paints and lacquers. The second group contains soybean, sunflower, rape, palm, coconut and castor oil, and these have found limited use in the paint industry. The substitution of nonbiodegradable mineral oils used in oil well drilling fluids has become a major application for vegetable oils consisting of C16–C24 unsaturated monocarbonic acids, and esters of C2–C12 alcohols are produced specifically for this purpose (Müller et al., 1989). In offshore drilling, palm oil- and coconut oil-based esters have successfully replaced toxic diesel oil fluids and have greatly reduced the load of nonbiodegradable hydrocarbon which is disposed of together with drill cuttings into the sea (Degouy and Demoulin, 1993). Recently, biodegradable oils such as rape or beet oil which have replaced the mineral oils are used as surface coating on concrete molds. Their purpose is to prevent concrete adhesion to the wooden mold and to provide an impeccable concrete surface.
Some vegetable oils (particularly soybean oil) contain lecithin, which is a phosphatide and is recovered from raw soybean oil by steam processing. Lecithin is an effective emulsifier which has found some use in solvent-born paints and coatings. Another application is in emulsifier packages to make water-in-oil emulsions for use as a drilling fluid.
5.3.2 Waxes
Many plants form an oil or wax layer on the surface of their leaves to provide protection against desiccation. Waxes from Euphorbia or Copernica cerifera are recovered and used as an important polish for wooden floors and furniture. Like exudate gums, they are complex mixtures, with linear aliphatic C16–C34 mono carbonic acids being the backbone to which C22–C36 alcohols are bound by ester bonds.
Insects can also produce waxes, the most well-known being bees wax, shellac and the wool wax of sheep. These waxes are sometimes used in wood polishes or as anti-graffiti coatings.
5.3.3 Bitumen and Paraffin
Some brown coal deposits contain fossil waxes known as bitumen or pitch, and which were formed from resins or waxes of plants that have degraded over the ages. Paraffins are particularly pure waxes which may occur in such natural deposits. Today, bitumen and pitch are produced by distillation of petroleum and coal, respectively. Bitumen is considered to be harmless to humans, whereas pitch has been proven to be relatively toxic.
Bitumen is a colloidal system in which polar asphaltenes and naphthenic petroleum resins are dispersed in a hydrocarbon phase called maltenes. Bitumen consists of a mixture of alkanes, cycloaliphates or aliphatic substituted aromates, and for industrial use is produced exclusively from the residues of petroleum distillation. Different viscosity grades are manufactured and sometimes oxidized by blowing air at 250–350°C through molten bitumen.
Asphalt is a mixture of bitumen and aggregates or fillers (e.g., sand, limestone etc.), and was used as early as 3000 bc in Mesopotamia as an organic binder in adobe buildings. Today, road construction represents the largest use of asphalt. Tarmac roads use three types of bitumen: distillation bitumen; flux bitumen (distilled bitumen dissolved in low-volatile mineral oils); and cold bitumen (distilled bitumen in highly volatile mineral oils). Occasionally, emulsions of bitumen in water containing emulsifiers and stabilizers (see Section 5.8.2) are also used. Polymer-modified bitumen is also used as a water-repellent coating on basements.
Gilsonite is a naturally occurring asphaltide which has found some use in oil well drilling fluids as a lubricant and filter-cake builder (Davis and Tooman, 1988). As the mud is pumped downhole and the temperature increases, gilsonite melts and forms a thin layer on the borehole wall; this helps to control fluid loss to the porous formation. Sulfonated gilsonite is used for improved dispersion in the aqueous drilling fluid. Likewise, a process for the manufacture of sulfonated asphalt and its use in drilling fluids has been developed (Stratton et al., 1962). However, a lack of biodegradability has reduced the usage volumes of both gilsonite and sulfonated asphalt in recent years.
Pitch (also called “carbolineum”) is produced from the distillation of coal and tar. Previously, huge volumes of pitch were used as a wood preservative, for example on railroad girders or fences. Pitch contains polyaromatic compounds which have been shown to be carcinogenic, and consequently pitch coatings have been used much less in recent years. Today, other less toxic coatings based on synthetic organic compounds such as carbamates are used.
Molten paraffin is sometimes injected into building walls as a moisture barrier, perhaps when a damp wall is continually drawing water from the soil to create an ideal substrate for molds and provide an unhealthy living environment.
5.4 Protein-based Biopolymers
Two protein-based admixtures, casein and protein hydrolysates, have gained a foothold in construction applications.
5.4.1 Casein
Casein is a biopolymer which is found in milk and is recovered by acid precipitation. Studies have shown that milk casein consists of a mixture of hydrophilic κ-casein and hydrophobic β-casein. Together, these form micelles with specific diameters of 90–140 nm (Figure 22). Further information on casein chemistry can be obtained from a web site (http://class.fst.ohio-state.edu/FST822/lectures/Cafunc.htm).
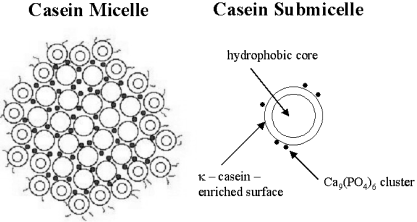
Casein micelles.
In construction, casein has found two distinct applications, namely paints and self-leveling underlayments.
Paints require additives which not only viscosify, but also impart self-leveling properties to achieve a leveled layer of paint. Caseinates, obtained by neutralizing casein with alkali hydroxides, provide both properties. At 0.5–4% concentration, they are a major ingredient in water-born casein paints. Their disadvantage is rapid biodegradability, such that the paint must be used quickly before it degrades and develops an evil smell. Synthetic, nondegradable latex compounds such as styrene-butylacrylate dispersions have been developed to replace casein in paints, but casein remains the product of choice for customers who require building paints based on natural, biodegradable products and who believe these products to provide a healthier living environment.
Self-leveling underlayments are another building application in which casein still plays a significant role on the market. SLUs are poured onto uneven floor screeds to provide an even surface before floor carpets are laid and glued with adhesives. SLUs are either based on Portland cement, or mixtures of Portland cement, calcium aluminate cement and anhydrite. Casein provides excellent self-healing properties to SLUs. After being cut with a knife, the scar will immediately close and re-form a totally even surface (see Figure 8). Even today, the mechanism of this self-healing property is not well understood, but over many decades this unique property of casein has made it the product of choice for this application. The typical composition and properties of a casein-based SLU are shown in Table 14. Only very recently have new polycarboxylate-based superplasticizers been presented which provide similar dispersing and self-healing effects in SLUs, and these now appear to have gained a limited foothold (Strauß, 2001).
Component |
Function |
Parts [g] |
---|---|---|
Portland cement (CEM I 42.5) |
Binder |
185 |
Calcium alumina cement (40% Al2O3) |
Binder |
115 |
CaSO4-anhydrite |
Binder/ retarder |
65 |
Quartz sand (0.1–0.315 mm) |
Aggregate |
410 |
Limestone powder (10–20 µm) |
Aggregate |
194 |
Redispersible powder |
Adhesion |
20 |
Casein |
Superplasticizer |
4 |
K/Na-tartrate |
Retarder |
4 |
Lithium carbonate |
Accelerator |
1 |
Methyl cellulose |
Water-retention |
0.5 |
Glycol |
Defoamer |
1.5 |
Paste flow of SLU according to EN 12 706: |
|||||
Time [min] |
5 |
15 |
30 |
45 |
60 |
Flow [mm] |
157 |
153 |
154 |
148 |
140 |
5.4.2 Protein Hydrolysates
Protein hydrolysates are extracts obtained by cooking animal blood, hair, hides or hoofs, particularly from cattle, with sulfuric acid or, more recently, with enzymes. The resultant extract contains degraded proteins, mainly oligo and polypeptides, of various compositions. Refinement is by filtration and precipitation of inorganic salts. Protein hydrolysates occur typically as 30–35% active, brown aqueous solutions; their nitrogen content (as determined by the Kjeldahl method) is used to specify their quality.
Protein hydrolysates reduce the surface tension of water significantly and are used to prepare foam concrete. This is made by feeding a homogeneous foam, generated by a foam pistol or a large foam aggregate, into a premixed mortar or concrete. By mixing the foam and mortar or concrete together, foam concrete with specific density as low as 0.5 kg dm−3 can be obtained. Foam concrete is used to fill ditches, to provide a basement for roads on unconsolidated soil in marshes and moors, and for prefabricated dividing walls in homes.
Compared with synthetic foamers and surfactants such as alkyl sulfonates, alkyl sulfates and betains which are also used to prepare foam concrete, protein hydrolysates are more difficult to apply. They require excellent mixing in a high-quality foam pistol or aggregate (Figure 23) to achieve a foam. The reason why the industry still uses these materials is their superior foam quality. When used correctly, protein hydrolysates produce spherical foam bubbles whereas synthetic surfactants typically generate hexagonal bubbles in concrete. Concrete of the same specific density containing spherical bubbles has been shown to provide 20–30% higher compressive strength, compared with concrete containing hexagonal bubbles. As a consequence, when foam concrete with a low specific weight and a compressive strength as high as possible is required, protein hydrolysates are still preferred over synthetic surfactants. This is an excellent example of how, on occasion, it is difficult to mimic the properties of biopolymers with synthetic materials.
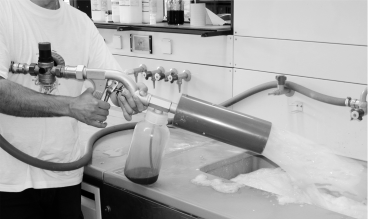
Foam preparation in a foam pistol using a protein hydrolysate surfactant.
5.5 Starch and Cellulose Derivatives
Starch and cellulose are two readily available polysaccharides which are produced in large volumes and are excellent starting materials for the preparation of more sophisticated derivatives. Both polysaccharides undergo modification rather easily by chemical reaction. In this way, the production of a great variety of products is possible, and certain properties can be custom-tailored into starch and cellulose molecules.
In spite of sometimes considerable product prices, the starch and cellulose manufacturers have successfully managed to provide significant value to the construction industry. Of all biopolymers used in building, starch and cellulose derivatives probably represent the largest product group, measured in terms of value.
5.5.1 Starch and Derivatives
Starches from whatever source are composed of one or more glucans. The two principal molecular components of starch are the polysaccharides amylose and amylopectin. Amylose is composed of long, straight chains of α-glucose (Figure 24), with molecular weights ranging from 10,000 to 100,000 Da.

Amylose structure, showing repeating glucose units.
Amylopectin, the main component, consists of a mixture of branched molecules (Figures 25 and 26), and has a molecular weight of 40,000 to 100,000 Da.
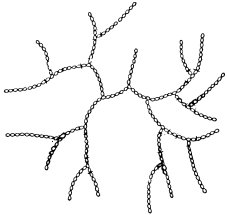
Schematic of amylopectin structure.
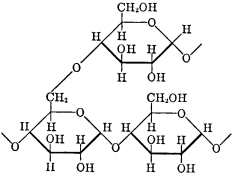
Formula of a branch point of amylopectin.
Commercial starch mostly is produced from corn (maize), though potatoes are another major source, particularly in Europe. The origin of a starch can be identified using microscopy because the sizes and shapes of starch granules are specific for the plant (Whistler et al., 1984).
In construction, very little native starch is used, but pregelatinized and derivatized starches are common. Pregelatinization is a modification process for starch which greatly enhances its cold water solubility and its viscosity yield – two properties which are clearly important in construction. The process consists of heating aqueous slurries of native starch, which causes the granules to swell and the viscosity to increase; the resultant viscous gel of pregelatinized starch is dehydrated to a powder on a drum drier.
Pregelatinized starch is used as an inexpensive, low-temperature fluid loss agent for water-based drilling fluids. It is mainly applied in top-hole drilling or drilling of shallow wells where the temperature stays well below 100°C. Typically, 0.5–2% of this starch is used to obtain an API fluid loss of 2–5 mL at 25°C and 7 bar differential pressure. As seen below, conversion from pregelatinized starch to carboxymethyl starch occurs as the temperature increases.
Pregelatinized starch is also used for plasterboard manufacture (see Section 4.4), where starch is added to the β-hemihydrate slurry. During the drying process, starch migrates to the surface of the gypsum body and glues the cardboard to the gypsum surface.
Among starch ethers, carboxymethyl and hydroxypropyl starch are the most important derivatives used in construction.
Carboxymethyl starch is also prepared by reacting alkali-treated starch with monochloroacetate. This causes some of the hydroxyl groups in the anhydroglucose units to be transformed into ethers with carboxymethyl groups. The degree of substitution (DS) may vary, but cannot exceed 3; commercial products used in construction typically have a DS between about 0.2 and 1.2.
Carboxymethyl starch is an important drilling fluid additive, its main advantage over pregelatinized starch being a higher temperature stability (up to 120°C).
In conventional construction, hydroxypropyl (HP) starch, when prepared by the reaction of propylene oxide with starch, is used to thicken wall plasters. For this purpose, HP starch with a DS of about 0.5 is dry-blended with other ingredients into a dry-mix mortar that is then mixed with water and machine-sprayed onto the wall (see Section 4.3). The primary function of the HP starch is to provide instant high viscosity so that the plaster adheres to the wall – a property known as green-strength. This effect also prevents the plaster from sagging after it has been sprayed onto the wall. Secondary effects of HP starch include: (i) augmentation of the water-retention ability of other additives present in the formulation; (ii) reduction of plaster stickiness on the trowel; and (iii) provision of surface viscosity when the plaster is first leveled and smoothed. Anybody who has ever attempted this leveling process (Figure 27) could not imagine the advantage that an appropriate surface viscosity of the plaster provides in the time needed for application. Hence, the industry has gone to great lengths to develop optimized products.
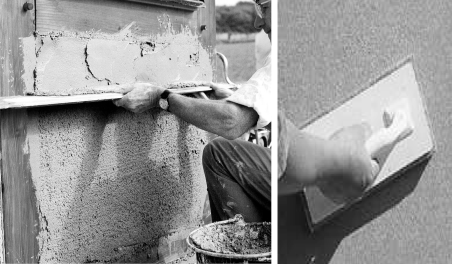
Leveling (left) and smoothing (right) of a wall plaster.
A typical formulation for a machine-sprayed gypsum plaster is shown in Table 15 (Aqualon Technical brochure, 1996). Clearly, as little as 0.01% of HP starch is required to obtain the desired properties.
Component |
Parts [% (wt/wt)] |
---|---|
Multiphase plaster |
50 |
Lime |
8.7 |
CaCO3 sand |
40 |
Perlite |
1 |
Methyl cellulose |
0.2 |
HP starch |
0.01 |
Foamer |
0.01 |
Tartaric acid |
0.08 |
The use of starch ethers in tile adhesives has been patented (Schinski and Wunderlich, 1990), but appears to be limited. Crosslinked starch has also found some use in cementitious grouts (Axmann, 1996).
5.5.2 Cellulose Derivatives
Cellulose products represent a very significant portion of the total construction chemicals market. It is estimated that in excess of 100,000 tons of derivatives are consumed annually by the construction industry, representing a value of approximately $500 mio at the manufacturer's level.
Among construction applications, cellulose is mostly used in the form of ether derivatives, with carboxymethyl cellulose and methyl cellulose representing the lion share.
The ethers most commonly used in construction are listed in Table 16. The nonionic cellulose ethers play a dominant role in this market, and a review of nonionic cellulose derivatives, their chemistry, manufacture, performance and market data has been produced by Dönges (1990). Very small quantities of cellulose products other than ethers are used, though one such material is micronized cellulose fibers that are occasionally used as a thickener in dry-mix mortar formulations such as tile adhesives (see Table 3).
Ether |
Abbreviation |
---|---|
Methyl cellulose |
MC |
Methyl hydroxyethyl cellulose |
MHEC |
Methyl hydroxypropyl cellulose |
MHPC |
Hydroxyethyl cellulose |
HEC |
Hydroxypropyl cellulose |
HPC |
Na-carboxymethyl cellulose |
CMC, PAC |
Na-carboxymethyl hydroxyethyl cellulose |
CMHEC |
Ethyl cellulose |
EC |
Ethyl hydroxyethyl cellulose |
EHEC |
Generally, cellulose products are applied in building products to provide water-retention and viscosity. An overview of the major fields of application for cellulose ethers in construction is provided in Table 17.
Field of application |
Function |
Cellulose ether |
---|---|---|
Building products Gypsum plaster Lime plaster Cement plaster Tile adhesive Joint fillers Wall paper glue Coatings and paints Water-borne latex paints Solvent-borne coatings Oil well construction Drilling fluids Cementing Completion fluids Ceramics |
Water-retention, Anti-sagging properties, Adhesiveness, Workability Pigment suspension, Thickener, brushability, Flexibility Emulsifier Water-retention Water-retention, Retarder Viscosifier Binder Water-retention |
MC MHEC MHPC CMC, PAC HEC MHEC MHPC EC EHEC CMC, PAC HEC, CMHEC HEC MHPC MHEC |
Clearly, the use of cellulose ethers is widespread throughout the industry, and some typical applications are outlined in the following text to illustrate the performance characteristics and special advantages of these materials.
Methyl cellulose (MC) is by far the most important chemical admixture used in dry-mix mortars and grouts as a provider of water retention. Major applications include tile adhesives, cement-, gypsum- or lime-based plaster, and joint fillers for wall boards.
A major use of MC is in machine-applied wall plasters, particularly those based on gypsum which are especially popular in England and Germany. Machine-spray applications cause additional requirements for the MC product in that besides properties of water-retention, anti-sag, and wall adhesiveness, the MC must mix and hydrate within 10–30 s. For this purpose, MC is milled to a particle size of <60 µm, thereby allowing the MC to develop its full effect by the time the plaster hits the wall.
A detailed description of the use of MC, methyl hydroxyethyl cellulose (MHEC) and hydroxyethyl cellulose (HEC) in gypsum machine plaster has been prepared (Schweizer, 1997), in which details of rheology, water-retention and mechanistic aspects are also discussed. The adsorption of cellulose ethers [MHEC, methyl hydroxypropyl cellulose (MHPC), HEC] on CaSO4 binder has also been shown to be governed by the DS – namely, the higher the DS, the lower the adsorption. For example, at a DS ≤1.2, typically 60–85% of the cellulose ether is adsorbed. It is interesting to note that MC and MHEC with regular DS significantly lose water retention ability at temperatures above 40°C.
Numerous patents on MC and MHEC formulations for plaster applications have been issued, and two are incorporated here for reference (Bietz et al., 1989a, 1989b). In these reports, the MC described had a DS of 1.4–1.95, while the MHEC had a DS of 1.53 and a molar degree of substitution (MS) of 0.3.
Other applications of MC, MHEC and MHPC include among others hand plaster, self-leveling compounds, wall board adhesives, and masonry mortars. A wealth of building product formulations containing cellulose ethers for these diverse applications is provided in a technical brochure (Aqualon, 1996).
Another typical MC application is that of standard and flexible tile adhesives, the compositions of which are detailed in Table 3. Here, the MC provides water retention, adhesiveness of heavy tiles even on vertical walls, and viscosity to allow the formation of a thin-bed on which the tiles may be set.
It has been established that MC viscosity greatly influences the degree of water retention achieved in a binder system (Clariant Technical brochure). Data provided in Table 18 suggest that MC of viscosity grade >60,000 provides maximum water retention, though in practical applications there is always a trade-off between optimum water retention and workability (i.e., viscosity). An MC which imparts too high a viscosity can impede the overall applicability of a system to a point where a slightly lower water retention would be preferable.
- a Viscosity of 1.9% aqueous solution.
- b measured in cementitious grout.
Rheological studies on cellulose ethers in mortars using oscillatory rheology technique have been described by Schweizer and Dewald (1996).
Nonionic cellulose ethers are universal thickeners for the paint industry and, by volume, are probably the most important group of thickeners in this field. Among water-borne dispersion paints, MHEC, MHPC, EHEC and HEC are the most common. They provide structural viscosity to the paint, as well as the water retention that is greatly needed on walls or underlayments with capillary suction forces. Other benefits include improved spreadability and enhancement of abrasion resistance. Medium-viscosity MHEC and HEC (2000–6000 mPa⋅s) was found to be best for low-spattering paint formulations. Typical concentrations of cellulose ethers range from 0.15 to 0.60%, though on occasion cellulose products are combined with associative thickeners to reduce pseudoplastic behavior. In solvent-borne paints, or in paints with a low water content, solvent-compatible ethers such as EC and EHEC are preferred. For a review on the use of cellulose derivatives in the paint and building industry, see Mondt (1990).
Considerable volumes of cellulose ethers are also used in oil well drilling. In fact, the water-retention properties of cellulose ethers was first recognized in the oil field, and by 1948 carboxymethyl cellulose had already been added to a water-based, bentonitic drilling fluid to successfully control filtration to the formation (the porous rock on the borehole wall. E.g., sandstone or limestone). This discovery revolutionized the drilling industry by making it possible to drill much longer hole sections without having to case off. Some ten years later, HEC was first mixed into an oil well cement slurry which was pumped into a well in Oklahoma. Again, excellent fluid loss rates were obtained, and this led to the introduction of an entire family of fluid loss polymers. It is an interesting anecdote that in conventional building products, the cellulose ethers did not become established until the mid-1970s.
Carboxymethyl cellulose (CMC), or its purified, desalted form known as polyanionic cellulose (PAC), are the main components of what is referred to as a polymer mud (see Section 4.6.1). This type of drilling fluid has a low content of bentonite as it obtains much of its viscosity from the cellulose product. Bentonite is preferred to provide solids for the filter-cake build up on the borehole wall. The industry provides low-, medium- and high-viscosity CMCs or PACs, with low-viscosity grades being preferred in high-density muds (specific gravity >1.7 g mL−1) and vice versa. Typical concentrations range from 0.2 to 2%. Commercial CMC used in the oilfield typically has a DS of 0.7–0.9, while the DS for PAC is slightly higher and ranges between 1.05 and 1.15.
CMC and PAC are both sensitive to divalent cations such as calcium and, to a lesser extent, magnesium. Low concentrations of divalent cations require increased dosages of cellulose products, and high concentrations of calcium (>3%) render them ineffective. In this case, hydroxypropyl starch or synthetic sulfonated copolymers based on vinylsulfonates are used as these tolerate high calcium/magnesium concentrations. Another limitation for CMC/PAC is temperature stability, as above 150°C they rapidly degrade in the drilling fluid and lose effectiveness. Typically, vinylsulfonate-based copolymers such as 2-acrylamido-2-methylpropane sulfonic acid-N-vinylacetamide-acrylamide terpolymers (Engelhardt et al., 1982) are used at higher temperatures. These are considerably more expensive than CMC/PAC, but are stable up to at least 225°C.
HEC and carboxymethyl hydroxyethyl cellulose (CMHEC) have become important fluid loss additives for oil well cementing. HEC provides good fluid loss under diverse salinity conditions up to 150°C, and even low-viscosity grades cause cement slurries to thicken considerably. However, this effect is generally undesirable as huge pump pressures are then required to transfer the slurry. Consequently, dispersants (also known as friction reducers) are added to the cement slurry containing HEC partly to offset this thickening effect. Test data on the rheology of dispersed and nondispersed HEC cement slurries are listed in Table 19. Typical HEC products used in well cementing have a DS of 1.5 to 2.5.
Additive |
FANN® rheology @ 600-300-200-100-6-3 rpm |
AV |
PV |
YP |
Fluid loss @70 bar |
---|---|---|---|---|---|
– |
171-136-119-99-34-25 |
85 |
35 |
101 |
Complete dehydration |
0.25% HEC |
230-156-124-87-39-36 |
115 |
74 |
82 |
190 mL |
0.25% HEC + |
|||||
1% dispersant |
174-115-79-40-3-2 |
87 |
59 |
56 |
44 mL |
- * Slurry: API Class H cement, w/c=0.38; temperature: 78°C.
CMHEC has also gained a foothold in this market. As the carboxylic group introduces a retarding effect on cement, CMHEC can be used as a retarding fluid loss additive for well cementing. Typical commercial products used in well cementing have a DS of 0.3 to 0.4 (CM) and an MS of 0.3 to 2.0 (HE).
In well cementing, cellulose ethers have better maintained their position compared with competing groups of fluid loss chemicals such as polyethyleneimines and polyvinyl alcohols. Reasons for this include their superior stability as well as their overall better environmental acceptability.
5.6 Seed Gums
Most seeds contain starch or similar polysaccharides as the principal food stored for use by the embryonic plant in its initial growth. Mankind has learnt in ancient times to harvest these gums from quince, psyllium, flax and locust seeds for food. In the industrial age it was discovered that seed biopolymers such as guar, tara, carob and locust bean gum are useful thickeners for a variety of applications including mining, textile printing, ceramics, explosives, and oil recovery.
So far, the construction applications of seed gums other than starch have been relatively few in number, and guar gum and locust bean gum are the only two seed biopolymers currently in use.
5.6.1 Guar Gum
Guar gum is obtained from the seed of the legume Cyamopsis tetragonolobus, an annual plant which grows mainly in India and Pakistan. The seed's endosperm predominantly contains guar galactomannan. Guaran, the polysaccharide in guar gum, consists of a chain of (1→4)-linked β-d-mannopyranosyl units with single α-d-galactopyranosyl units connected by (1→6)-linkages to, on the average, every second main chain unit (Figure 28). The average molecular weight is 1–2×⋅106 Da – one of the highest molecular weights of all naturally occurring, water-soluble biopolymers.
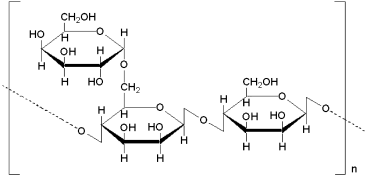
Repeating guar gum unit.
Guar gum is an excellent viscosifier for aqueous systems, though until recently its use in the construction industry was negligible, with only small amounts of highly substituted hydroxypropyl guar (HPG) being used in dispersion paints to provide viscosity and stabilization. The problem with guar is its susceptibility to bacterial degradation such that preservatives are required to prevent the paint from being spoiled.
More recently, HPG was introduced as a new water-retention and viscosifying agent for cementitious and gypsum-based plasters and grouts (Molteni et al., 1998; Alvarez Berenguer et al., 1999). A high DS and uniform distribution of the hydroxypropyl groups attached to guar in the substitution process are thought to be the key to functionality in building systems. There appears to be a synergistic effect with MC which is used for the same purpose. Details of the chemistry of HPG specifically developed for plaster and grout applications, its solution properties (pseudoplasticity and thixotropy), pH and temperature stability have been provided in a Lamberti Technical brochure. Likewise, formulations illustrating the effects of HPG in plasters and grouts may be found in a brochure produced by the same company.
Native guar is also used to some extent in well construction as a viscosifier in top-hole drilling. Here, the biopolymer provides initial viscosity to a water-based drilling fluid. However, the main advantage of environmental acceptability due to rapid biodegradability occasionally causes problems from a technical point of view. This occurs particularly in top hole sections, where the soil and rock is rich in microorganisms that cause an accelerated biodegradation of guar. In this situation, biocides must be added to the drilling fluid as a preservative for guar.
For the same environmental reason, guar gum is also used as thickener in trench-less drilling operations. Here, large-diameter holes (75–150 cm; 30–60 inch) are drilled using mobile units to lay cables or pipelines under rivers or highways. A common formulation for a guar-based trenchless drilling fluid consists of fresh water, 0.5% guar gum and soda ash, adjusted to a pH of 9–10. A typical rivercross drilling operation is shown in Figure 29.
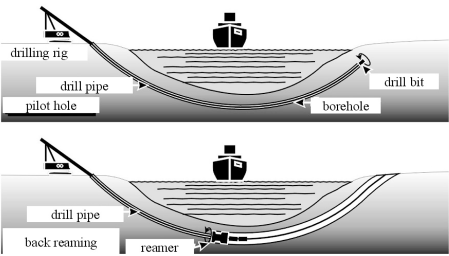
Trenchless drilling operation.
Guar and guar ethers are used in very large quantities (approximately 20,000 tons) for the stimulation of oil and gas wells to improve production rates.
5.6.2 Locust Bean Gum
Several attempts have been made to use locust bean gum or synergistic combinations of locust bean gum with other hydrocolloids in building materials. Locust bean gum provides a synergistic viscosity-enhancing effect with xanthan, agar and κ-carrageenan. Addition of locust bean gum to xanthan gum (see Section 5.8.1) at a 1:1 ratio, for example, almost triples the viscosity, while higher concentrations of the two hydrocolloids result in a thermoreversible gel. The mechanism behind this is a crosslinking of the rigid helical xanthan gum molecules by the galactomannan strands of locust bean gum. It is interesting to note that guar gum, a galactomannan similar to locust bean gum (see Section 5.6.1), does not exhibit such a synergistic effect.
Although some positive effects of the synergistic blend were observed, its use in construction was ceased due to poor economics. The relatively high price of locust bean gum appears to deter potential users, and the development of synergistic blends with other hydrocolloids that are more acceptable on a cost-effect basis will be required if any volume is to be reached.
5.7 Exudate Gums and Root Resins
Exudate gums and resins such as oil of turpentine, colophonium and other balsams are biopolymers belonging to the group of natural terpenes. They are produced in plant cells as a means of protection against lesions and dehydration, and also as an insecticide. Undoubtedly, the observation of glassy layers formed from wood resins on plant trunks has inspired mankind to develop lacquers and coatings for furniture and wood used in construction.
Exudate gums and resins differ widely in their composition, depending on the producing plant. Although typically they are complex mixtures of different substances, they all contain 2-methyl-1,3-butadiene, or isoprene, as a characteristic structural unit in their molecule.
Applications of wood resins are quite diverse and include uses in medicine, cosmetics, printing inks, oil paints, polishes, lacquers, textile coating and hair sprays. Their main use in construction is varnishes and adhesives for wood, and air-entrainment into concrete.
5.7.1 Oil of Turpentine and Colophonium
Oil of turpentine, sometimes also called resin oil or pine gum, is the volatile constituent of resin balsam and is isolated by steam distillation of the natural resin. Oil of turpentine essentially contains monoterpenes with 10 carbon atoms and terpenoid compounds derived from the monoterpenes (Figure 30).
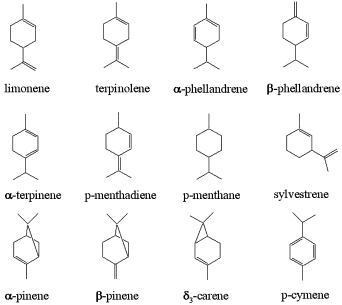
Cyclic monoterpenes contained in oil of turpentine.
Oil of turpentine is used as a solvent and binder for natural resin-based lacquers applied as wood varnish. Its toxic effects must not be ignored; it is an irritant and was shown to cause neurological paralysis when inhaled over a longer period of time. A potential substitute is shellac, a resin produced in the metabolism of female coccids (Tachardia lacca).
Pure colophonium is produced by steam distillation of resin balsam, and contains a mixture of several resin acids, particularly laevo pimaric acid and abietic acid. Colophonium is the film-forming component in many wood glues, varnishes and polishes. It has been shown that these film-forming properties are caused not only by the formation of a dry resin layer, but also by the reaction of its carbon-carbon double bonds with oxygen, thereby forming hydroperoxides and polymers of higher molecular weight.
5.7.2 Root Resins
Root resin extracts, particularly from the roots of conifer trees, have found a significant application as air-entraining agents. Their main use is in the production of freeze–thaw-resistant concrete.
Air-entrainment is regarded as essential for the durability of concrete that will become wetted and then exposed to freeze–thaw conditions. Studies have shown that this protection is best afforded by micro air bubbles with diameters of 10–300 µm. Homogeneous distribution of the bubbles in the concrete is also important, and for optimum performance the inter-bubble distance should not exceed 0.2 mm. The mechanism behind freeze–thaw resistance is disruption of the capillary pore system in the concrete so as to greatly reduce the penetration of water into the concrete. As a result, air-entrained concrete can withstand several thousand cycles of freeze–thaw changes without destruction, whereas untreated concrete cracks and disintegrates after only a few hundred cycles. The effect of freeze–thaw cycles on air-entrained and plain concrete is shown in Figure 31.
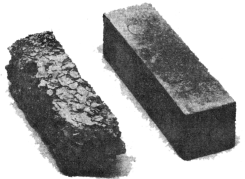
Effect of 300 freeze–thaw cycles on plain (left) and air-entrained concrete (right).
Extracts produced from naturally occurring root resins represent one of the most effective and widely used air-entraining agents in concrete. The distillation and extraction of pine stumps leaves a residue which consists of a mixture of phenolics, carboxylics, and other substances. Neutralization with sodium hydroxide renders this soluble; the resultant brown solution, the main active ingredient of which is abietic acid (Figure 32) retains a pine smell and is sold under the name VinsolTM resin within the construction industry.
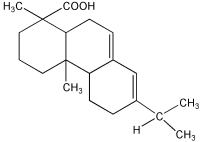
Abietic acid.
Root resin-based air-entraining agents are used in very small dosages. The superiority of the root resin extract over an alkyl sulfate-based synthetic surfactant is illustrated in Figure 33.
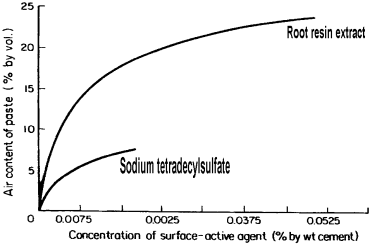
Air-entraining effect of root resin extract and sodium tetradecylsulfate.
5.8 Microbial Biopolymers
Extracellular polysaccharides produced by microorganisms offer a variety of useful and, for specific construction applications, indispensable products. Selected and often carefully mutated bacteria or, to a lesser extent, fungi are used to produce the gum in a fermentation broth. A comprehensive overview of microorganisms capable of producing such biopolymers is given by Dimitru (1998). Low-cost energy sources, such as molasses, are the feed for the organisms, and the fermentation process typically yields a viscous broth which is 5–7% active in high molecular-weight gum. The biopolymer is precipitated from the broth by addition of isopropanol, and then dried and carefully milled to a specific particle size. The construction industry uses microbial biopolymers almost exclusively in powder form.
Since the mid-1960s, microbial biopolymers have been used in construction applications in ever-increasing quantities. Numerous products are available commercially, including xanthan gum, welan gum, gellan, rhamsan, scleroglucan, succinoglycan, curdlan, dextran, diutan, and pullulan. Applications for those biopolymers which have found a more significant use in construction will be discussed in the following sections. It is estimated that these biopolymers account for annual sales of almost $100 million on the manufacturers' level; a breakdown of tonnage by individual type of biopolymer used in construction is shown in Table 20.
Biopolymer |
Annual consumption [mton] |
Applications |
---|---|---|
Xanthan gum |
10,000 |
Grouts and plaster; Oil well drilling fluids |
Scleroglucan |
250 |
Asphalt emulsions; Oil well drilling fluids |
Welan gum |
500 |
Oil well spacer fluids; Concrete |
Succinoglycan |
100 |
SLUs and floor screeds; oil well completion |
5.8.1 Xanthan Gum
Xanthan gum, produced by the bacteria Xanthomonas campestris, was the first microbial biopolymer to be used in construction. The US Department of Agriculture, Northern Regional Center, Agricultural Research Service, Peoria, Illinois, developed a xanthan gum production method during the 1950s in an effort to enhance molasses consumption and provide financial help to those farmers who were growing maize. An aerobic fermentation process is used to produce the gum; this involves a multi-step inoculation preparation followed by fermentation, pasteurization, precipitation, drying and milling.
Xanthan gum is an exocellular heteropolysaccharide consisting of a poly-β(1→4) d-gluco-pyranose backbone linked with a trimer of mannose, glucuronic acid, and mannose every second glucose unit (Figure 34). The mannose units contain anionic acetate and pyruvate groups which render this biopolymer more water-soluble than other microbial products. As will be seen later, this relatively higher anionic charge in the side chain is less desirable in certain construction applications where other biopolymers excel. The molecular weight of the gum is reported to be ∼2×106 Da, and the molecular conformation is described as helical with the side chains aligned with the backbone (Yanaki et al., 1981).
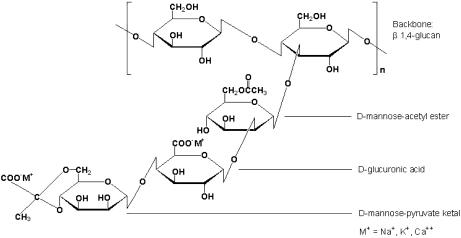
Structure of xanthan gum.
When dissolved in water, xanthan gum develops significant viscosity. Its main characteristic and advantage is the type of viscosity: While starch- and cellulose-based biopolymers usually increase the plastic viscosity (PV) of their aqueous solutions, xanthan gum and most other microbial biopolymers increase the yield point (YP) and show a low PV. The resultant viscosity profile is referred to as shear-thinning. Figure 35 illustrates a typical viscosity curve as measured with a FANN® rotational viscometer, obtained by addition of various doses of xanthan gum to fresh water. As can be seen, xanthan gum solutions are distinguished by a high YP/PV ratio.
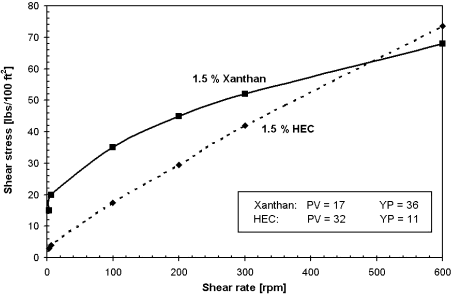
Xanthan gum and HEC viscosity in fresh water.
The shear-thinning type of fluid viscosity is extremely useful in certain oil well construction applications. As pointed out earlier (see Section 4.6.1), drilling fluids need to be low in viscosity when being pumped through the hole, but highly viscous when circulation is halted. Xanthan gum exactly provides this property; by way of its shear-thinning rheology, xanthan gum-treated drilling fluids require low pump pressures to circulate the fluid and to clean the hole from drill cuttings. However, when circulation stops and the fluid is at rest, it suspends the cuttings quite well because of its high YP. Consequently, settling of drill solids and weighting materials (e.g., barite) that are suspended in the drilling fluid is greatly reduced. This effect is extremely important, because solids settling at the bottom of the hole may bury the lower part of the drill string. Likewise, when restarting rotation of the drill string, a large quantity of settled material may cause rupture of the drill pipe, the latter effect being considered a major accident. If this happens, it is necessary to side-track the hole from the point of disruption, which clearly adds extra cost to the construction of the well bore and is highly undesirable.
During the mid-1960s, the KELCO Company introduced xanthan gum as a novel drilling fluid component under the name “XC polymer”. Since then, most water-based drilling fluids are treated with 0.01 to 0.2% of xanthan gum, though for viscous sweeps to clean out large debris in the hole concentrations of up to 0.8% may be used.
Xanthan gum is also effective in high-salt brines based on sodium chloride. For example, NaCl brines of 27%, weighted with ground salt or calcium carbonate, are used in workover operations on well bores. Xanthan viscosifies these brines, though somewhat more gum is required to achieve the same viscosity increase in salt solution as compared with fresh water.
The application of xanthan gum in well construction is limited by its temperature stability and sensitivity to divalent cations. Rheology data produced on an HT/HP rotational viscometer (e.g., FANN®50 of Halliburton Co.) indicates that xanthan gum viscosity starts to decline at 60°C and is completely lost at 120°C. Interestingly, the viscosity is regained when the fluid is cooled back to moderate temperatures (Figure 36).
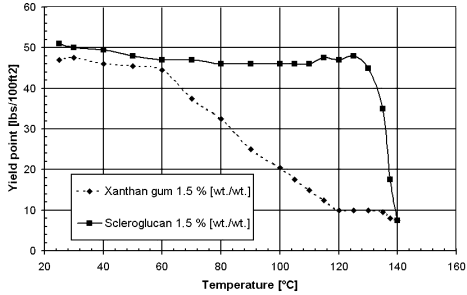
Xanthan gum and scleroglucan viscosity, as measured by the yield point, as a function of temperature.
These data suggest that the gum should not be used at well bore temperatures significantly exceeding 100°C unless continuous replenishment is possible. Fortunately, there are other, more temperature-stable microbial biopolymers to take over at elevated temperatures. From a market point of view, the temperature limitation does not pose a major problem for xanthan gum, because by far the majority of oil and gas wells drilled never reach a bottom-hole temperature of 100°C. For example, the average well depth of all wells drilled in 2000 in the US was ∼1700 m, which corresponds to an average bottom-hole temperature of 60°C. This explains why, in comparison with other microbial biopolymers, so much more xanthan gum is used in drilling.
The shear-thinning type of rheology imparted by xanthan gum is also appreciated in building materials. Highly fluid floor screeds based on anhydrite, for example, sometimes have a tendency to drop out the binder or aggregates. Bleeding water may appear on the surface, and coarse particles may settle at the bottom, and such inhomogeneity of the screed results in reduced compressive strength and poor surface. Xanthan gum (0.03 to 0.1% weight of binder) may be added to the dry formulation to prevent disintegration of the floor screed.
Other minor uses of xanthan in building materials include gypsum-based wall plasters to enhance plaster adhesion to the wall; and water-borne paints and coatings. In the latter application, xanthan gum addition supports the formation of a film when applying the paint by brushing or spraying. Dripping of the paint, for example from ceilings, is also reduced.
As approximately 9000 tons of xanthan gum is used annually in well construction, this application by far exceeds the use of the gum in conventional building products. Although expensive, xanthan gum provides benefits to the overall drilling process which makes its use worthwhile from performance and safety points of view and, as indicated below, the oil drilling industry has accepted the use of even more expensive microbial biopolymers for the sake of their overall cost benefits. In conventional building products, however, xanthan gum is more often than not a “nice-to-have” additive, allowing the technical perfection of certain products, albeit at great expense. In fact, this added cost is often significant and prevents a more widespread use of xanthan gum in the highly competitive market for building products. Hope persists, however, that this situation may ease in the future as biopolymer manufacturers increase their capacity such that unit costs for xanthan gum reach a downward trend.
5.8.2 Scleroglucan
Scleroglucan is a branched homopolysaccharide which consists of a main chain of (1→3)-linked β-d-glucopyranosyl units. Every third unit bears a single β-d-glucopyranosyl unit linked (1→6) (Figure 37).
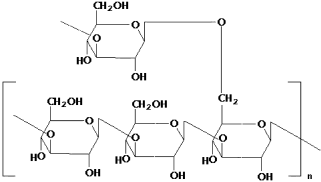
Scleroglucan repeating unit.
Scleroglucan is produced by an aerobic submerged culture of a selected strain of the fungus Sclerotium rolfsii. The fermentation medium contains ∼3% d-glucose as a carbon source, corn-steep liquor, nitrate, and mineral salts. Fermentation takes place at 28–30°C and requires ∼60 h for completion. Mycelial growth and polysaccharide production occur simultaneously, the rates of mycelium to polysaccharide being about 1:3. In construction applications, native scleroglucan is used still containing the mycelium. Purified scleroglucan, from which the mycelium has been removed by filtering the dilute broth, is used as thickener in cosmetic applications.
Dissolved scleroglucan chains assume a rod-like triple helical structure in which the d-glucosidic side groups are on the outside and prevent the helices from coming close to each other and aggregating (Yanaki et al., 1981).
Scleroglucan has found a major application in oil well drilling. Today, horizontal wells are drilled to extract oil and gas from extended, yet thin, reservoirs. These wells are often drilled over distances of several thousand feet (500–3000 m) and typically are not cemented and cased off. Rather, sand screens are placed in the hole to prevent plugging from sand influx. Because of this technique, these wells are referred to as open-hole completions. Figure 38 shows the drilling of a horizontal well and illustrates the importance of suitable drilling fluid properties.
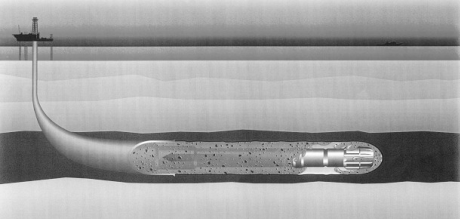
Schematic illustration of a horizontal well construction.
Drilling fluids used in open-hole completions must provide shear-thinning rheology, and this property is provided equally by xanthan gum and scleroglucan. A fluid for open-hole completions also must not plug the micro pores of the oil- or gas-bearing reservoir, as this will severely reduce the flow of hydrocarbons to the borehole and reduce the production rate that determines the overall profitability of a well bore. Oil producers therefore are prepared to undergo significant expense to ensure high productivity of their well.
In 1996, Johnson discovered and patented a novel nondamaging reservoir drilling fluid essentially consisting of 2.6 parts scleroglucan viscosifier, 10.4 parts carboxymethyl starch fluid loss control additive and 87 parts graded calcium carbonate weighting agent and filter cake builder (Johnson, 1996). Tests conducted with a so-called return permeability apparatus indicate this fluid to show significantly less pore plugging than a xanthan-based system. The improved performance is attributed to the nonionic character of scleroglucan. Xanthan gum, with its anionic charge in the side groups, is believed to adhere more to the rock and hence plug reservoir pores. Because of its field-proven advantages, scleroglucan-based so-called drill-in fluids have found a significant use in horizontal well drilling as they allow the extraction of more oil from a given reservoir. The introduction of such “nondamaging” fluid systems represent a major technological advance in oil and gas production.
Another advantage of scleroglucan over xanthan gum is its higher temperature stability. The viscosity of a fresh water scleroglucan solution in comparison with xanthan at temperatures ranging from 20°C to 150°C is illustrated in Figure 36. The gain in temperature stability by using scleroglucan is clear, and as a result when bore hole temperatures exceed 100°C, a conversion from xanthan gum to scleroglucan is recommended to control solids settling. It must be noted however that once heated above a threshold temperature of 140°C, scleroglucan viscosity abruptly breaks down and is not retrieved on cooling (unlike xanthan gum). It is believed that the excessive temperature destroys the helical structure of scleroglucan, thereby destroying its viscosifying effect.
In conventional building products, scleroglucan has found a niche application in asphalt emulsions. Generally, road tarring is carried out either by laying down molten asphalt or by spraying an aqueous asphalt emulsion onto the road. The latter method is popular in warmer climates. When the water evaporates from the emulsion an asphalt layer is formed. Scleroglucan is used to thicken these asphalt emulsions, thus preventing them from seeping away on steep roads or inclined curves.
5.8.3 Welan Gum
Welan is produced by bacteria from the Alcaligenes species (ATCC-31555) in an aerobic, submerged fermentation. The medium contains d-glucose as the carbon source, phosphate as a buffering agent, ammonium nitrate and soy peptone as sources of nitrogen, and trace elements (iron, magnesium, cobalt, zinc, copper, manganese, and molybdenum) (Dimitru, 1998).
The welan repeat unit shows a single sugar side chain containing either l-rhamnose or l-mannose substituted on C3 of every (1→4)-linked glucose unit (Figure 39). The welan side chain shields the carboxylate group in the double helix, thereby rendering welan unsusceptible to cation-mediated bridging. The welan molecule is rather stiff, whereby it becomes relatively insensitive to temperature and pH variation. This, together with its tolerance of high calcium ion concentrations, makes it ideal for applications in concrete, mortars, cement grouts and high-temperature drilling.
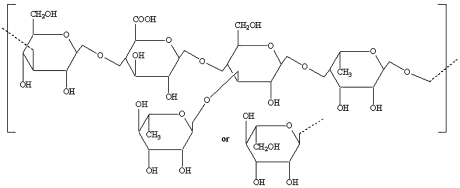
Welan gum repeating unit.
The usefulness of welan gum in construction was first documented in patents describing cement compositions with low-viscosity welan (Allen et al., 1990), but later on further reports were made for the use of welan in grouts (Skaggs et al., 1994; Skaggs, 1997).
There are two major applications of welan in construction, namely its use in concrete as a stabilizer, and in oil well construction for spacer fluids.
As discussed in Section 4.1.4, highly fluid concrete such as SCC with a slump in excess of 270 mm has a tendency to disintegrate. Of all microbial biopolymers, welan gum has been found the best to stabilize this concrete and to prevent surface bleeding. With concrete requiring liquid admixtures rather than dry powders for ease of homogeneous mixing, considerable effort was devoted to develop a liquid, yet highly concentrated colloidal welan suspension (Skaggs et al., 1996, 2001). Dial et al. (2001) discovered and patented an aqueous suspension containing 10% welan gum, 40% of a sulfonated melamine formaldehyde condensate, 0.75% ultra-fine cellulose fibers for suspension stability, with the remainder being water.
Published test data (Hibino, 2000) suggest that in concrete the welan gum suspension effectively prevents the formation of surface bleeding water and the sag of large aggregate particles. It does however impede early strength development to some extent when used at higher concentrations. Nonetheless, welan gum suspensions are the most widespread admixture used to stabilize highly fluid concrete.
Liquid welan-superplasticizer suspension is also used in cementitious injection grouts, generally for crack repair, for sealing of submerged anchorages, and for filling post-tensioned ducts. With these applications, as for SCC, it is essential to control the bleeding of mix water and sedimentation of suspended cementitious materials. Details on grouts treated with the welan suspension, their rheology, set times, etc. have been presented by Khayat and Yahia (1997), while the use of welan powder in a dry formulation of an injection grout is described by Teichert and Umlauf (2000).
Among all applications, probably the largest volume of welan is used in spacer fluids for well construction (Carpenter et al., 1997). In this application, welan has several advantages over any other commercially available biopolymer, including:
-
rapid development of viscosity in solution;
-
high viscosity efficiency at concentrations as low as 0.1% in solution;
-
temperature stability up to 150°C; and
-
relative stability to divalent cations such as calcium.
This combination of properties has turned the market almost exclusively to welan. As described earlier (see Section 4.6.3), spacer fluids are pumped and circulated through the bore hole to separate the drilling fluid from the cement slurry. While previous spacers typically contained dispersing and abrasive agents and were pumped under turbulent flow at high annular velocity to achieve complete removal of drilling fluid and mud cake, it is generally accepted now that spacer fluids showing a shear-thinning type of viscosity imparted by a microbial biopolymer and pumped under plug flow conditions are more efficient for the job. Typical compositions of dispersed and shear-thinning spacer formulations used in well construction are listed in Table 21.
Dispersed spacer [%] |
Shear-thinning spacer [%] |
---|---|
Quartz sand 35 |
Welan gum 5 |
Diatomaceous earth 39 |
Wyoming bentonite 75 |
Sepiolite 14 |
Lignosulfonate dispersant 20 |
BNS dispersant 10 |
|
Defoamer 2 |
Typically, 25 kg of the above dry spacer formulation is mixed with 1 m3 of water and circulated through the hole prior to cementing the casing. When surfacing after circulation, the spacer fluid either is blended into the drilling fluid to be used later on, or is disposed of.
5.8.4 Succinoglycan
Succinoglycan, a β-(1→3)-linked d-glucan, was discovered in 1966, the producing organism being of the Alcaligenes faecalis type. In addition to the pyruvate groups, the polysaccharide contains covalently bound succinic acid and therefore was referred to as succinoglycan (Matulova, 1994).
Succinoglycan has found some interesting uses in the construction industry for self-leveling underlayments. These cementitious grouts require an admixture which imparts shear-thinning rheology. Succinoglycan seems to provide similar or even better effects than casein (see Section 5.3). Detailed test data on succinoglycan performance in an SLU based on Portland cement and calcium alumina cement have been reported by Charrin (1997).
The use of succinoglycan as an anti-sag and stabilizing agent for SCC, similar to welan gum, has also been proposed. A liquid admixture consisting of 5% active suspension of succinoglycan in a vegetable oil (e.g., rape oil ester) has been reported to work well in concrete when combined with nanosilica (Sari et al., 1999).
When heated above 55–60 °C at concentrations >1%, succinoglycan forms a firm, resilient gel, with gellation occurring over a wide range of pH values from 3 to 10. On occasion, this property has been used in drilling operations to shut off water influxes into bore holes or to prevent water influx into product reservoirs.
The major draw-back of succinoglycan use in construction is its high cost, and while this persists its uses will be limited to highly specialized niche applications.
5.8.5 Curdlan and Rhamsan
Curdlan is a β-(1→3)-glucan that was first described in 1964 by Harada and Yoshimura (1964). These authors isolated a soil bacterium that grew in a medium with 10% ethylene glycol as the sole carbon source and produced Curdlan in high yield. The bacterium was a member of the Alcaligenes faecalis family which also produces succinoglycan.
In Japan, Curdlan is used to some extent as an anti-sag and stabilizing agent in SCC, similar to welan gum. Performance details and studies on the swelling and solubility behavior of Curdlan in concrete have been described by Matsuoka et al. (1997). It is proposed that Curdlan forms a calcium complex with cement, and this enhances concrete flowability.
Rhamsan has a two glucose side chain substituted on C6 of every 3-linked d-glucose residue. Its disaccharide side chain partially shields the carboxylate group and reduces cation-mediated cross-linking. In comparison with welan and xanthan, rhamsan produced by far the highest viscosity in Portland cement grouts (Skaggs, 1997), and also showed the best effect with respect to reduction of bleeding water. Commercially, rhamsan plays a far smaller role in construction than welan or scleroglucan, with its high cost being the major reason for its limited use.
5.9 Chitosan
Chitosan is a partially or fully deacetylated form of chitin, a naturally occurring polysaccharide. Structurally, chitin is a polysaccharide consisting of β-(1→4) 2-acetamido-2-deoxy-d-glucose units, some of which are deacetylated. Chitin is not one polymer with a fixed stoichiometry, but rather a class of polymers of N-acetylglucosamine with different crystal structures and degrees of deacetylation. Chitosan is obtained from chitin by more extensive deacetylation of typically between 50 and 100%. Chitosan is structurally similar to cellulose, but is unique in that it is a polysaccharide which contains primary amine groups.
A chitosan-containing well drilling and servicing fluid was described in a recent patent (House and Cowan, 2001). Data were provided which showed that similar shear thinning rheology was obtained with chitosan as with microbial biopolymers such as xanthan and welan gum.
5.10 Biodegradable Polymers
Unlike in many other industries, biodegradability still plays a relatively minor role in construction products, with one exception. This is because admixtures typically are imbedded into a hardened binder matrix and do not show significant leaching. Rather, the industry has followed a strategy of using products based on naturally occurring raw materials such as cellulose, starch, guar, and casein, as well as biopolymers obtained by fermentation, such as xanthan and welan gum. Most of these products are also used in the food industry and therefore are recognized as harmless.
The one exception where biodegradability is of great importance is in well construction. During the 1990s, North Sea governmental agencies which issue the drilling permits to oil companies, introduced HOCNF, a harmonized scheme for the environmental evaluation of chemicals used in offshore drilling operations (Thatcher and Payne, 2001). For each chemical used, there is a requirement to generate extensive test data on its toxicological and environmental properties. A final selection of those chemicals with the lowest hazard quotient is made by using the CHARM model (Still, 2001). Among other test data, bioaccumulation and biodegradation properties are important criteria for the assessment of chemicals. For water-soluble substances, a biodegradability of >20% in 28 days, determined by the OECD 306 D closed-bottle seawater test, is required. Any substance with lower biodegradability is assumed to be persistent and will receive only temporary permission for use on the grounds that the supplier demonstrates to the authority serious efforts to substitute this chemical with more biodegradable materials. Ultimately, chemicals to be used shall have biodegradabilities in 28 days of >70% according to OECD 301 A or 301 E, or >60% according to OECD 301 B, 301 C, 301 F of 306 (Henriquez, 2001). Clearly, this stringent requirement poses a severe problem to the industry because almost any cement or drilling fluid additive in use today fails to meet these criteria. With other countries considering the introduction of similar legislation, this has become a major challenge for those companies which supply chemicals for well construction, and the industry has consequently embarked on extensive research programs to develop new chemicals that comply with the necessary requirements.
The following section describes two of the few examples of biodegradable polymers used in construction applications, though it should be noted that this is only the beginning of the saga and improved technology will need to be developed.
5.10.1 Polyaspartic Acid
Polyaspartic acid is made by reacting maleic anhydride with ammonia. The linkage of the aspartic acid unit can occur on either the α- or β-position to the amide groups (Figure 40).
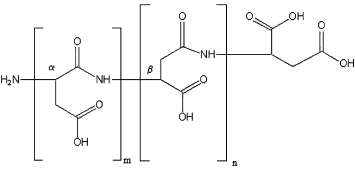
Schematic of polyaspartic acid structure.
Polyaspartic acid has been recognized as a cement dispersant (Vickers et al., 2001) and gypsum retarder (Staffel et al., 2001) that shows significant biodegradation. Published test data indicate a biodegradability of >70% in 28 days, according to OECD 302 B test protocol (Bayer Technical brochure, 2000).
5.10.2 Polyesters
A snag for polyaspartic acid in cement is its strong retardation effect. Esterification of polyaspartic acid with poly(ethylene oxide) has been demonstrated to reduce the retardation exerted by the carboxylic groups (Vijn et al., 2002), though unfortunately the ester side chains reduce the biodegradability to some extent.
Another polyester with significant biodegradability has been proposed for the dispersion of hydraulic binders (Wegener et al., 1996). The polyester can be prepared by reacting a diol (e.g., diethylene glycol) with a dicarboxylic acid (e.g., maleic anhydride), followed by sulfitation with sodium bisulfite or sodium pyrosulfite. The sulpho group-containing polyester shows a biodegradability of >80% in 28 days according to OECD 302 B test protocol. Test data describing the plastification of Portland cement and gypsum are presented by Wegener et al. (1996).
6 Biopolymers with Potential for Future Use
Many more biopolymers exist which have found only random or no use at all in the construction industry. The reason is not always a lack of functionality, as in some cases the degree of technical development for certain biopolymers in specific applications is more advanced than for others. As building material technology progresses, improved admixtures will be needed. This can be achieved by further refining biopolymers already in use or by introducing new biopolymers to construction applications.
The following describes biopolymers which are commercially available, are already in use by other industries, and which seem to have a potential for future application in construction. These products and their source, basic chemistry, general function and a property which distinguishes them from other biopolymers are presented in Table 22. It is possible that the following description will inspire readers to take a closer look at these materials and to develop some use in building products.
Biopolymer |
Source |
Basic chemistry |
Function |
Unique Property |
---|---|---|---|---|
Tannins |
Plants |
Polyphenolic acid |
Dispersant |
Graft polymer backbone |
Gelatin |
Animals |
Protein |
Viscosifier & gelling agent |
Thermoreversible gelation |
Alginates |
Seaweed |
Polysaccharide |
Viscosifier & gelling agent |
Calcium – induced gelation |
Carrageenan |
Seaweed |
Sulfated galactose |
Viscosifier & gelling agent |
Potassium - induced gelation |
Pectin |
Fruits |
Polyanhydrogalacturonic acid |
Viscosifier & gelling agent |
LM pectin: thermoreversible gelation |
Tamarind |
Plant seed |
Polysaccharide |
Viscosifier & gelling agent |
Strong viscosifier |
Cassia |
Plant seed |
Polysaccharide |
Viscosifier |
Synergistic with Xanthan |
Gum arabic |
Acacia tree |
Polysaccharide |
Viscosifier & emulsifier |
Adhesive |
Gum karaya |
Tree |
Polysaccharide |
Viscosifier & emulsifier |
Emulsion stabilizer |
Gum tragacanth |
Tree |
Polysaccharide |
Viscosifier & emulsifier |
Thickening emulsifier |
Dextran |
Bacterium |
Polysaccharide |
Viscosifier |
Shear-thinning viscosifier |
Pullulan |
Fungus |
Polysaccharide |
Viscosifier |
Complete tolerance to NaCl |
6.1 Tannins
The word tannin is a collective term for a group of astringent substances, the principal use of which is to convert animal skin into leather. Tannins are classified chemically as either hydrolysable or condensed tannins. The former group consists of esters of one or more polyphenolic acids, such as gallic acid, and are also called gallotannins. The latter group consists of phenolic units from which catechol or protocatechuic acid can be derived, and are also referred to as catechol tannins. The average molecular weight of tannins is in the range of 300 to 1000 Da.
Tannins occur in many plants and are recovered by extraction. Typical sources include the barks of wattle, mangrove and eucalyptus, or the woods of quebracho and chestnuts.
Quebracho are hardwood trees growing in Argentina and Paraguay. Their red wood contains 15–25% tannin which is extracted using hot water. Quebracho tannin has many similarities with lignin: first, its major source is wood and it also contains phenolic groups; second, it can be made cold-water-soluble by treatment with bisulfite in alkaline solution (pH>10); and third, it is a very effective bentonite thinner. Before World War II, quebracho tannin was an important thinner for water-based, bentonite drilling fluids used in the oilfield, but the introduction of lignosulfonate brought about a major reduction in quebracho usage during the late 1950s. Nevertheless, sulfoalkylated quebracho, prepared by adding formaldehyde and sodium bisulfite to a solution of quebracho and caustic soda, principally is an effective thinner and dispersant.
With lignosulfonate supply gradually declining, tannins may find an entry into the construction market as replacement for lignosulfonates. Another potential use of tannin is to prepare functional graft polymers. For example, Huddleston et al. (1992) found that 2-acrylamido-2-methylpropanesulfonic acid, acrylamide and methylene bis-acrylamide grafted onto wattle tannin produced a very effective fluid loss additive for oil well cement slurries.
6.2 Collagen and Gelatin
Collagen is a natural protein that occurs in animal skins, bones and connective tissues, in which it provides elasticity. Collagen is made up of rod-like tropocollagen molecules which are linked covalently (Figure 41). Tropocollagen consists of three peptide strands arranged in a triple helix which is stabilized by covalent bonds between the strands.
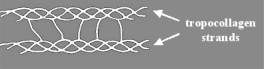
Schematic of collagen structure.
Collagen is the insoluble precursor from which gelatin is produced in a careful extraction and degradation process. The conversion can be achieved by two different routes: acid extraction yields gelatin of type A, whereas alkali extraction results in gelatin of type B. The resultant 30–45% active gelatin solutions are sterilized at 145°C and cooled to create a gel that can then be extruded in the form of noodles to increase its surface area and allow faster drying. The dried noodles are then ground to produce a yellowish gelatin powder.
In the gelatin extraction process, the insoluble collagen is transformed into soluble gelatin. The acid and alkaline processes break bonds between the tropocollagen molecules on the same strand, and all or part of the bonds between individual strands. In this way different gelatin molecules are obtained, depending on which bonds between strands are broken. Figure 42 shows the principal structures of α-, β- and γ-collagen chains contained in gelatin. If all bonds between the strands are broken, then α-collagen chains with a molecular weight of 80,000–125,000 Da are formed, but if only some of the bonds are broken, then β- or γ-collagen chains with molecular weights up to 375,000 Da are obtained.
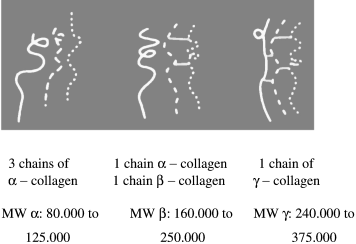
α-, β- and γ-collagen chains contained in gelatin.
Gelatin is a protein containing approximately 20 amino acids linked by peptide bonds, the main constituent amino acids being glycine (27%), proline (16%), and hydroxyproline (14%). All amino acids essential to man occur in gelatin, except for tryptophan. A simplified structure of gelatin is shown in Figure 43.
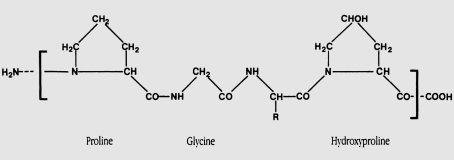
Simplified structure of gelatin chain.
Gelatin is an amphoteric, polydisperse macromolecule. Type A gelatin, obtained by the acid process described above, shows an isoelectric point at pH 6.3 to 9.5, whereas type B gelatin produced in an alkaline medium shows an isoelectric point at pH 4.5 to 5.2.
Gelatin stands out among other viscosifiers because it forms thermoreversible gels. When placed in cold water, gelatin swells and absorbs five to ten times its own volume of water. Then, when heated to a temperature of 50–60°C, the swollen gelatin dissolves, producing a solution, or “sol”, which forms a gel when cooled. The sol/gel conversion process is reversible and can be repeated for many cycles.
Gelatin is an excellent stabilizer for colloidal suspensions and emulsions as its protein molecule chain forms a monomolecular film around the micelles. The viscosity increase of the aqueous phase enhances the stability of suspensions and emulsions. Based on this behavior, very significant volumes of gelatin are used in the food industry for sauces, desserts, etc., and in the film industry for photographic emulsions. Apparently, there is no application of gelatin in construction, though it might be worthwhile considering it for use as a stabilizer for building material suspensions and emulsions.
6.3 Alginates and Carrageenan
Alkali extraction of seaweed yields the polysaccharides alginate and carrageenan, both of which are viscosifiers.
Alginates are obtained by the alkali extraction of brown seaweed, followed by coagulation in an acid medium and neutralization to alginate salts. Alginates are composed of three blocks:
-
homogeneous β-d-mannuronic blocks …-M-M-M-M-….
-
homogeneous α-l-guluronic blocks …-G-G-G-G-….
-
alternating blocks …-M-G-M-G-….
Alginates are unique viscosifiers in that they show a calcium-induced gelation. The salts of alginates (typically sodium, potassium, ammonium) are soluble in cold water in the absence of calcium. Small amounts of calcium result in a viscosity increase, whereas higher concentrations induce gel formation, caused by the crosslinking of alginate chains. Very high calcium levels result in the formation of calcium alginate which is insoluble in water. The ability to adjust viscosity by means of the calcium concentration is used in diverse industries such as food, textile, paper, cosmetics and pharmaceuticals. In construction, paints occasionally contain alginates. It appears that in building systems which almost always contain calcium from cement or gypsum, alginates could provide an option for viscosity generation and stabilization.
Carrageenan is recovered by extraction of red seaweed occurring, for example, on the Atlantic ocean coast of France, off Normandy and Brittany. It differs from alginates in that it is made up of sulfated galactose units. The carrageenan family is extremely diverse and can be broadly classified into two groups, each with two subgroups:
-
gelling carrageenans: kappa (κ) and iota (ι) carrageenan
-
thickening carrageenans: lambda (λ) and Ksi (ξ) carrageenan
The chains of λ-carrageenan are separated from each other and do not have any tendency to self-associate, hence they do not form gels. The presence of three sulfate groups per disaccharide causes so much electrostatic repulsion and steric hindrance that the chains cannot form a double helix. As a result, λ-carrageenan solutions show the shear-thinning properties of flexible coil molecules.
In ι- and κ-carrageenan, unlike in the λ-form, the sulfate groups are all on the outside of the helix; hence, electrostatic repulsion does not prevent the formation of double helices.
The ι-carrageenan network is made up of a succession of double helices linked by portions of free chain which together form a transparent, elastic gel (Figure 44). This loosely connected network is easily broken by mechanical shear, though it is reinstituted quickly when the mechanical action has ceased. The resultant thixotropic behavior is made use of in the food industry, for example in cold-fill dairy desserts such as milk-shakes.
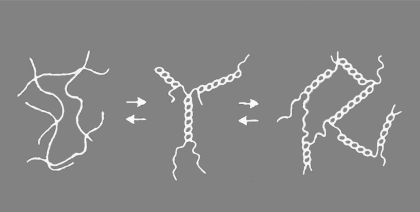
Structure of iota-carrageenan gel.
κ-carrageenan shows a remarkable effect in the presence of potassium and calcium ions, with potassium ions inducing gel formation at very low concentrations. Because of their small hydrated size, potassium ions can fit into the helix and partially neutralize the sulfate groups; this causes the double helices to associate and form aggregates that create a strong, brittle gel. In comparison, sodium ions do not fit into the helix and so cannot induce gelation at normal concentrations. The calcium ion acts as a bridge between two sulfates from two different double helices and forms a crosslink; low calcium concentrations increase the gel strength, but higher concentrations have a reverse effect.
The food industry is successfully using these ionic effects on κ-carrageenan to obtain thickening and gelation as needed.
6.4 Pectin
Pectin is a natural polysaccharide frequently found in plants as a component of the cell walls. There, it is linked to the cellulose and constitutes both the supply tissue and the “cement” which gives texture to plant cells.
Pectin is present in all fruits, in variable quantities, as well as in some roots (beets, carrots). Its name is derived from the Greek word pektos (firm, stiff), alluding to its main property, that of forming stiff gels.
Apple pomace and citrus peel are the two sources for commercial pectin. Acid hydrolysis of the protopectin in hot water extracts the pectin which is purified by precipitation in alcohol and several rinses of alcohol/water mixtures, followed by drying and sieving. This process produces high-methoxyl (HM) pectin (degree of methoxylation >50%), whereas demethoxylation using acid or alkali leads to low-methoxyl (LM) pectin (degree of methoxylation <50%).
The pectin molecule consists of partially methoxylated polyanhydrogalacturonic acid (Figure 45). The presence of rhamnose in the principal chain results in a deviation from the axis of the helix of about 90°, and this is generally known as the “pectic elbow”. This feature facilitates the formation of a three-dimensional gel network with sugar.
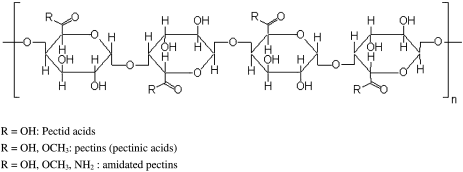
Structure of the pectin chain.
Pectin is not readily water-soluble – a fact which may affect its chances ever to be used in construction applications. First, it needs to be dispersed well under vigorous shear, and the dispersed pectin takes a relatively long time to hydrate (the swelling time). The completely hydrated pectin molecule can bind water at 15 to 25 times of its own weight, a remarkable capacity.
HM pectins form nonthermoreversible gels at pH between 2.5 and 4. Warm acidification in a pectin and sugar medium induces gellation when cooling to ambient temperature. The gellation mechanism is based on the effect of the “pectic elbow” described above.
Unlike HM pectins, LM pectins form thermoreversible gels via interaction with calcium. Post-saturation of the network by calcium reinforces the texture of the gel, giving it excellent thermal resistance (up to 230–250°C).
Although their thickening and gelling behavior is quite complex, pectins – because of their enormous water-binding capacity – should be given consideration for future construction applications.
6.5 Tamarind and Cassia
Tamarind and cassia are seed gums which in certain respects resemble guar and locust bean gum (see Section 5.6).
Tamarind trees (Tamarindus india) are common forest in India, Bangladesh and Sri Lanka. Their seed contains a gum which is a more powerful viscosifier than starch. Tamarind kernel powder disperses rapidly in cold water, but requires 20–30 min of boiling to achieve a uniform solution with maximum viscosity. Solutions are non-Newtonian and thin on increase in shear.
The exact composition of tamarind endosperm polysaccharide is not fully known, but it has been suggested that the main chain is cellulose with frequent branching at O-6 positions with short side chains of one or two d-xylopyranosyl units capped with d-xylopyranosyl, d-galactopyranosyl, or l-arabinofuranosyl units (Srivasta and Singh, 1967). Tamarind is used extensively in the textile industry for sizing of jute and cotton.
Cassia, a seed gum produced by the botanical species Cassia occidentalis, Cassia tora and Cassia obtusifolia, all of which grow in India, is another galactomannan-based viscosifier. Used alone, cassia gum does not impart much viscosity to water (Table 23), but when combined with other hydrocolloids such as xanthan, agar and κ-carrageenan, an even stronger synergistic effect than is known from locust bean gum (see Section 5.6.2) is observed (Bayerlein et al., 2000). Depending on the type of hydrocolloid added, cassia develops 20–50% more viscosity. The best effect was found to occur with a cassia/xanthan gum 1:1 blend. The presence of salts such as NaCl or KCl does not impair the synergistic behavior.
Hydrocolloid 1% dosage |
Viscosity [mPa⋅s]1 |
|
---|---|---|
cold water (20°C) |
hot water (90°C)2 |
|
Cassia gum |
<10 |
260 |
Locust bean gum |
78 |
2450 |
Xanthan gum |
3200 |
3200 |
Guar gum |
5100 |
5300 |
- 1 Measured on Brookfield RVT viscometer at 20 rpm.
- 2 Viscosity measured at 20°C after heating hydrocolloid solution to 90°C and cooling to 20°C.
6.6 Gum Arabic, Gum Karaya and Gum Tragacanth
On injury of the bark, many plants – and particularly these growing in semiarid regions – exude an aqueous solution thickened with gum to cover the injury; subsequently, this solution hardens to prevent infection and desiccation of the plant. Gum arabic, gum karaya and gum tragacanth are commercially available exudate gums with remarkable properties.
Gum arabic is probably the oldest industrial gum. It is hand-picked from Acacia trees growing particularly in Sudan, where the Darfur and Kordofan provinces produce around 100,000 tons per year. Gum arabic is a branched molecule with a main chain of (1→3)-linked β-d-galactopyranosyl units having side chains, consisting of (1→3)-β-d-galactopyranosyl units, joined to it by (1→6)-linkages.
Gum arabic dissolves in water remarkably well, and because it imparts little viscosity, concentrations of 50% are possible. Gum arabic is mainly used for its adhesive and emulsifying characteristics. The food industry, for example, uses this gum in caramels, toffees, fruit gums and gum drops, while the paper industry uses it as an effective adhesive.
Gum karaya is exuded from Sterculia urens, a bushy tree growing in India. Natural gum karaya is a partially acetylated polysaccharide with ∼8% acetyl groups. It contains ∼37% uronic acid and occurs as the calcium and magnesium salt; its molecular weight is 9,5000,000 Da (Kubal and Gralen, 1948).
Gum karaya is one of the least soluble exude gums. Particles in water do not dissolve but swell. Gum karaya absorbs water rapidly to form dispersions with viscosities ranging from ∼400 mPa⋅s at 0.5% dosage to 10,000 mPa⋅s for a 3% dispersion. At higher concentrations, non-flowing pastes are formed. Gum karaya is used in the paper industry as a binder in long-fibered papers and in the food industry as a stabilizer in French dressings, for example.
Gum tragacanth is also an ancient gum exuded by Astragalus trees growing in the eastern Mediterranean region and Iran. The name tragacanth is derived from the Greek tragos (goat) and akantha (horn), referring to the white curled ribbons of the best grades. Gum tragacanth consists of two fractions: one fraction, called tragacanthin, dissolves in water to give a hydrosol, whereas the second fraction, termed bassorin and representing 60–70% of the gum, swells to a gel. Gum tragacanth has a molecular weight of ∼840,000 Da. Gum tragacanth differs from other gums in its bifunctional action as a thickening emulsifier. It increases the viscosity of the aqueous phase, and at the same time lowers the interfacial tension between oil and water. Oil-in-water emulsions are stabilized because the gum delays coalescence of oil globules by increasing the viscosity of the external aqueous phase, thus slowing movement of the dispersed oil phase. Gum tragacanth is used in many oily salad dressings such as French, Italian or Roquefort, and in bakery emulsions. Very limited use of the gum occurs as a binding agent in ceramics.
All exudate gums offer unique properties which deserve exploration for use in construction applications. For example, the remarkable adhesive property of gum arabic might be useful in plasterboard manufacture where starch is currently used to glue the cardboard to the gypsum corpus. Gum karaya and gum tragacanth are both stabilizers for oil-in-water dispersions and might find application in asphalt emulsions or oil-based drilling fluids.
6.7 Dextran and Pullulan
Dextran and pullulan are two microbial biopolymers which so far have not found entry into the construction chemicals market.
Dextran is produced by bacteria of the Leuconostoc species, mainly for medical and analytical applications. In medicine, dextran is used as a blood plasma substitute and has been shown to reduce the risk of thrombosis. The introduction of crosslinked dextran beads (Sephadex®) in 1959 heralded a new era in separation science. Several anion- and cation-exchangers based on Sephadex® were developed and are being used in chromatography. One important application is the industrial separation of plasma protein, in particular albumin, immunoglobulins, pro-insulin and other blood factors (Curling, 1983).
Pullulan is a linear glucan produced by a fungus of the genus Aureobasidium. It consists of repeating units of maltotriose joined by α-d-(1→6) linkages. Pullulan dissolves readily in water to form a viscous solution. Its viscosity yield at 1% concentration resembles that of gum arabic, and is much lower than the viscosities of guar or xanthan gum. Pullulan is especially recognized by its high stability in sodium chloride; heating at 100°C for 6 h in saturated brine causes no noticeable change in viscosity. This property should be explored further for oil well drilling fluids and completion brines. Another remarkable feature is its strong adhesiveness on wood, with aqueous solutions of pullulan having been shown to adhere several times better to wood than starch, cellulose ethers or phenolic resins. This adhesive nature is used in reconstituted tobacco sheet.
In summary, it is fair to say that the industry offers many more biopolymers than are currently being used today in construction. With this in mind, the reader is encouraged to study the usefulness of these materials, hopefully to expand (in time) the range of biopolymers contributing to modern construction technology.
7 Outlook and Perspectives
Biopolymers have found a solid place in construction applications, and a wide variety of product families is now being used, with significant sales turnover. A further increase can be expected for the group in total, albeit with significant differences between individual families of biopolymers.
Lignosulfonate use in construction has already peaked and most likely will continue to fall, mainly due to a scarcity of sulfite liquor (its sole raw material; see Section 5.1), and technology shifts. In the case of concrete and gypsum products, new synthetic superplasticizers based on polycondensate or polycarboxylate chemistry already have made inroads. The substitution process will continue. In oil well drilling, polymer muds based on cellulose, starch or synthetic polymers have gradually taken over from dispersed lignite-lignosulfonate muds. New drilling fluid systems based on biodegradable oils such as palm oil esters or α-olefins are now also available and further encroach on the market share of lignosulfonate and lignite. Thus, there is likely to be a downward trend for these products.
Starch and particularly cellulose derivatives seem to enjoy a continued strong position in the construction market, and volumes are expected to grow further as more sophisticated building products requiring these very additives are developed. Another reason for this growth is the dissemination of advanced technology such as machine plastering to countries which so far have used more conventional building methods. This transition from a labor-intensive to a more industrial approach to construction using prefabricated building materials represents an opportunity for those suppliers in possession of derivation technology. With respect to technology, the industry likely will continue to further refine its products for specific applications, either by chemical modification or by blending with other chemicals. This is typical of a business which is in a rather mature state, and major innovations can be expected by employing new gums such as guar gum, and by applying highly sophisticated derivation knowledge from starch and celluloses on these new raw materials.
Clearly, the greatest growth potential is offered by microbial biopolymers. Their domain is to thicken of all types of aqueous systems used in construction, and particularly to provide shear-thinning rheology. Their continued growth is driven by both technology and economies and, as described in Section 5.8, they offer unique performance characteristics unmatched by other biopolymers or synthetics. Industry research aims at providing novel products by employing either new or mutant microorganisms capable of producing biopolymers with further improved properties. The degree of adaptation to specific product needs is astounding, a very recent example being the introduction of Diutan, a new biopolymer which is produced by Shingomonas (Navarrete et al., 2001) and has been shown superior to all existing microbial products with respect to temperature stability (up to 160°C) and ultra-high zero-shear rate rheology.
Although expensive to impart, these innovations will undoubtedly find a market niche because they can be used to perfect building systems such as SCC, SLU or oil well drill-in fluids. The added value provided to the user is significant and therefore the costs are accepted. Another general reason for increased use of microbial biopolymers is improved economics; as existing producers add capacity and develop better nutrients and create more productive organisms, the unit prices for these biopolymers will continue on a downward trend. Decreasing cost encourages users to find new applications and to expand existing ones. It is probably safe to say that this group of biopolymers will increase in importance for future construction technology. At this time, no significant technology based on synthetic polymer chemistry appears to be able to compete with products made by fermentation.
Biodegradable polymers form a subgroup which is expected to develop a niche market in certain construction applications, with well construction clearly leading the development in this field. It can be predicted that once biodegradable products have been established in one segment, the entire construction industry will take a closer look and consider their use in more diverse applications.
Biopolymers appear to have a perceived advantage over synthetic polymers. Whether justified or not, the “bio” image appeals to many end-users as being environmentally more preferable. This perception may have its foundations in previous cases of contamination and emissions from, for example, wood varnishes emitting PCPs. In Japan, for example, some people developed “sick house syndrome”, and as a result the industry learned that it must carefully investigate any potential health risks for its products. Therefore, an effort is made to provide non-toxic, emission-free building products. Industry associations such as the German GEV (Gütegemeinschaft emsissionskontrollierter Verlegewerkstoffe or Quality Association for emission-controlled flooring products) have been formed to establish standards for VOC/TVOC emissions from flooring products.
Finally, there is a growing need to recycle, rather than to dispose of, building materials. In Germany, environmental authorities consider the introduction of mandatory documentation for any material used in new buildings. A “building passport” will list all materials and identify all admixtures used in the construction of the building. If introduced, it will mean another push for “green” materials, and biopolymers will likely benefit.
In summary, the future challenge of the construction industry will be to provide admixtures which allow economic, high-quality and labor-friendly methods, without sacrificing environmental aspects. The products will need to be nontoxic, low in emission and leaching, and to show no effects on either inhabitants or the environment. It is safe to assume that biopolymers will make a major contribution towards this target.
-
- API
-
- American Petroleum Institute
-
- AV
-
- apparent viscosity
-
- ASTM
-
- American Society for Testing and Materials
-
- BNS
-
- β-naphthalene sulfonic acid formaldehyde condensate
-
- CHARM
-
- chemical hazard assessment and risk management
-
- CL-CLS
-
- chrome lignite-chrome lignosulfonate
-
- C-S-H
-
- calcium silicate hydrate
-
- DS
-
- degree of substitution
-
- ESEM
-
- environmental scanning electron microscope
-
- HT/HP
-
- high temperature/high pressure
-
- MC
-
- methyl cellulose
-
- MFS
-
- melamine formaldehyde sulfite resin
-
- MS
-
- molar degree of substitution
-
- PC
-
- polycarboxylate
-
- PCP
-
- perchlorated phenol
-
- PV
-
- plastic viscosity
-
- SCC
-
- self-compacting concrete
-
- SLU
-
- self-leveling underlayment
-
- TVOC
-
- total volatile organic compound
-
- VOC
-
- volatile organic compound
-
- YP
-
- yield point