Investigation of the Temperature-Dependent Precompaction and Flow Behavior of Hot Mix Asphalt
Abstract
The flow behavior and precompaction resistance were investigated for the first time as part of this study. New laboratory methods were developed and applied for this purpose, some of which were based on already established methods. In order to evaluate the influence of temperature on the paving behavior of the asphalt paver, the flow behavior and precompaction resistance were investigated for three selected asphalt mixes (AC 11 DS, SMA 11 DS, AC 16 BS). The temperature was varied in three steps (130°C, 160°C, and 190°C). An extensive literature review of possible laboratory tests was conducted, which concluded that static compaction and the funnel fall test are suitable for investigating the corresponding properties of the asphalt mixes. The results showed that the bulk density of a loose fill asphalt mix is significantly dependent on temperature. Higher temperatures result in higher poured density due to the thermoviscosity of the bitumen, specifically, the viscous τvisc and cohesive τc resistance components. Considering the performed laboratory tests, this phenomenon results in the loose fill of all tested asphalt mixes having a lower precompaction resistance at lower temperatures. In addition, the influence of temperature on the flow behavior and thus the internal friction of the asphalt mixes was demonstrated. Higher test temperatures resulted in a substantial reduction in flow time up to 225% and thus significantly improved flow behavior.
1. Introduction
To ensure that asphalt pavements can withstand the loads from traffic without experiencing harmful deformations, it is crucial to have adequate deformation resistance and proper load transfer to the subgrade or ground. Achieving the necessary level of deformation resistance and the ability to withstand temperature and weathering stresses depends largely on the quality of its compaction. Poor paving quality and insufficient compaction can have a significant impact on the durability and longevity of the asphalt [1]. To achieve sufficient compaction, the hot mix asphalt (HMA) undergoes a two-step process, which includes precompaction by the paver screed and final compaction by rollers. Although the paver can compact the material to a high degree of Marshall density, achieving the final compaction level requires using rollers [2].
If the precompaction is too low, the rollers shift the asphalt mix, which can lead to unevenness and inhomogeneity. On the other hand, if the precompaction is too intense, the rolling compaction scheme of the rollers can no longer work, which is supposed to cause a horizontal orientation of the aggregate and, in turn, positively influences the stiffness and the overall properties of the asphalt pavement [3, 4].
The material behavior of the asphalt mixture during the precompaction paving process is very complex. Although the final compacted condition of the asphalt mixture is decisive for assessing the quality of the asphalt pavement, it is important to research the precompacted condition. Paving errors resulting from the paver screed can never be completely reversed, even by the skillful use of rollers [5].
Paving with the paver screed is realized according to the “floating screed principle.” The screed rests freely on the asphalt material and is only attached to the height cylinder by the truck via the levelling arm. The asphalt mix then flows from the auger tunnel under the screed as a loose mixture due to the forward movement of the screed. The screed furthermore compacts the loose asphalt mix by its own weight and the shearing movement [6]. According to [7], the vibration of the screed favors this process only to a small extent.
If no levelling system is in use or if the height cylinder is set to a constant value, the specific paving height will be determined by the properties and quantity of the asphalt material under the screed [8]. The properties depend on many factors, such as the asphalt mixture itself and the mix temperature. However, the temperature of the asphalt mixture can fluctuate and depends on many factors, such as the processes at the mixing plant, the transport vehicles, the ambient temperatures, and the travelling lengths and times. Concerning final compaction by rollers, a strongly reduced asphalt mix temperature results in an increase in compaction resistance and thus in insufficient compaction. The extent to which a drop or increase in mix temperature leads to a rise or drop of the screed is discussed oppositely in literature, as the influence of temperature on precompaction resistance and flow behavior has not been fully investigated. For instance, in [9], it is claimed that a drop in asphalt mix temperature should lead to an increase in layer thickness. Investigations in [10], on the opposite, confirming the statements in [4], were able to prove that a drop in the mix temperature actually leads to a decrease in layer thickness and justifies this by the changed flow behavior of the asphalt mix.
The paver must consequently be adapted to the properties of the asphalt mix. Thus, it is important to understand how the paving screed behaves when the material properties change. Since these findings are missing on the scientific side, no definite paving recommendations can be defined. The paving quality of asphalt pavement remains highly dependent on the individual experience of the paving personnel.
2. Literature Study
2.1. Bulk and Pouring Properties of an Asphalt Mixture
According to [2], when a loose asphalt mix of a specific poured density is progressively compacted by applying a normal stress σ, the initial deformation is mainly plastic and depends mainly on the properties of the loose heap and the mortar. As compaction progresses, the elastic component becomes more pronounced. Overall, the influence of the loose heap and mortar properties decreases while the influence of the grain-to-grain contacts increases.
According to [6], the deformation resistance τdr and thus the compaction properties of an asphalt mixture can be characterized as a function of initial resistance τi, internal friction τϕ, and viscosity τvisc (cf. Equation (1)). The initial resistance component τi is the sum of resistances that are not influenced by normal stress σ or deformation rate but are mostly determined by the temperature-dependent cohesive resistance τc of the binder, specifically, the mortar. The internal friction component τϕ = σ · tan(ϕ) is proportional to the normal stress on the shear surface and depends on factors such as the shape, size, and roughness of mineral grains, as well as the gradation of aggregate mixtures. The resistance to deformation decreases as the minerals become more rounded and the degree of nonuniformity decreases. Asphalt mixtures with cubic grains that have rough surfaces, crushed sand, and a large maximum grain size increase the deformation resistance. The viscous resistance component τvisc arises from the viscosity of the binder, specifically, the mortar, and is dependent on deformation rate .
While in the case of rolled asphalt, the internal friction of the solid phase is hardly affected by temperature changes, the cohesion and viscosity of the liquid phase are strongly temperature-dependent quantities. The relationship between the cohesive resistances τc, the viscous resistance τvisc, the resistance from internal friction τϕ, and the resulting deformation resistance τdr and the mix temperature T is shown in the adapted hypothetical model of Utterodt [11] in Figure 1. Accordingly, an increase of the mix temperature reduces the cohesive τc and viscous τvisc resistances, promoting the movement of grains in the asphalt structure. The grains can then consolidate more strongly, increasing the internal friction component τϕ through increased density and more intensive interlocking of grains by penetrating thinner binder shells. Combining the individual curves, the cumulative curve τdr for deformation resistance can be obtained, which exhibits a parabolic shape with a minimum at a specific mix temperature Tτ,opt..
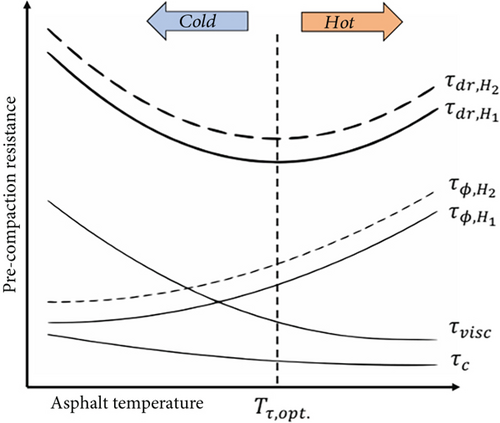
If the height H of a pile is also considered, a greater poured height should lead to an increase in deadweight and thus to an increase in internal frictional resistance . The components τc and τvisc are unaffected by the poured height. Overall, the deformation resistance τdr nevertheless increases with a higher poured height H leading to . Thus, in addition to the temperature T, the precompaction resistance should also be dependent on the poured height H [11].
2.2. Choice of Adequate Laboratory Tests
In asphalt road construction, there are only few standardized tests with which the properties of loose asphalt mixes can be assessed. This also applies to flowability and precompaction resistance, which is why suitable laboratory tests are researched and selected in the following.
2.2.1. Precompaction Resistance
Numerous laboratory tests exist to describe the compaction resistance of asphalt mixes. In Europe, impact compaction using a Marshall hammer per EN 12697-30 [12] is the most applied test for determining compaction resistance. In America, the Superpave gyratory compactor (SGC) according to AASHTO T 312 [13] is used to determine compaction resistance against vertical and shear stresses. This method is also standardized in Europe with EN 12697-10 [14]. The resistance to vibration compaction can also be determined by laboratory testing. EN 12697-32 [15] and EN 12697-10 [14] provide a method in which a (hand-held) vibratory hammer and a compaction pad are used to evaluate compactability. This method is mainly used in Great Britain. In Asia, the vertical vibration testing method (VVTM) [16, 17] or the asphalt vibratory compactor (AVC) [18, 19] is being used.
The vibratory compactors cover a special case where static compaction is combined with dynamic compaction. In [16, 17] and in [18, 19], two eccentric shafts are used which run parallel to each other in opposite directions of rotation. This leads to a directed vibration in vertical direction, which does not correspond to the vibration scheme of a paver screed. In addition, vibration is subordinate during precompaction. Compaction using a Marshall hammer with high-impact stresses is unsuitable for describing the precompaction process, in which low stresses occur in contrast to roller compaction. The same applies to the stresses occurring around the compaction schemes of the SGC and the roller compactor. The Marshal hammer, SGC, and roller compactor tests all require a defined final thickness and consider the compaction process to achieve that thickness [12, 13].
However, using the static compaction method has the advantage that it is able to describe the compaction resistance of an asphalt mixture at low stresses and is capable to consider individual final thicknesses. It has already been used multiple times for discrete element method (DEM) calibration to investigate the change in microstructure during compaction [18, 20]. In [21], it was applied to investigate the interparticle contacts, and in [22], static compaction was used to investigate the volumetric performance on cold-in-place recycled (CIR) asphalt. Therefore, the static compaction method will be used in this research.
2.2.2. Flow Behavior
Considering the interparticle friction of individual grains, the angle of repose test is a widely used method to determine the flow properties of bulk materials. It is regularly performed in the medical industry [23] and in the field of geotechnics [22]. According to [24], it is applicable for a vast range of application fields. It has already been repeatedly applied for the calibration of granular materials within the framework of a DEM simulation (e.g., in [25–27]). The static angle of repose can be determined using the tilting box method, the fixed funnel method, and the hollow cylinder method which are further described in [24]. Roessler and Katterfeld [26] proved that the static angle of repose test is capable of determining the friction parameters of a cohesive bulk material. Besides the interparticle friction, the angle of repose is influenced by the surface on which it is located. High friction between the base and the bulk material results in a steeper angle of repose [24].
The static angle of repose test also determines the discharge flow time and/or rate. Since there is a close correlation between internal friction and discharge time [28], this parameter is often used to characterize the flow behavior of granular material as it has been done, for example, in [29]. Amidon Meyer, and Mudie [30] state that “it is thought to be a more direct measure of flow than measurements such as angle of repose […].” However, the results of the discharge flow time strongly depend on the experimental setup, for example, the diameter of the orifice plate.
3. Laboratory Program
3.1. Asphalt Mixtures for Testing
To determine how temperature changes affect the precompaction and flow properties, three fundamentally different mixes were tested at three different temperature levels in this study (cf. Table 1). Additional information on the asphalt mixes used is presented in Table 2. The grading curve information can be found in Table 3. Two asphalt wearing courses (AC 11 DS and SMA 11 DS) were tested, both of which were produced with a polymer-modified binder (cf. Table 2) in accordance with the German guideline TL Asphalt-StB. In addition, an AC 16 BS asphalt binder is tested, which is compared with the asphalt wearing course mixes.
Asphalt mixture | Temperature | Sample ID |
---|---|---|
AC 11 DS | 130°C | AC11-TL |
160°C | AC11-TM | |
190°C | AC11-TH | |
SMA 11 DS | 130°C | SMA11-TL |
160°C | SMA11-TM | |
190°C | SMA11-TH | |
AC 16 BS | 130°C | AC16-TL |
160°C | AC16-TM | |
190°C | AC16-TH |
HMA properties | AC 11 DS | SMA 11 DS | AC 16 BS |
---|---|---|---|
Binder type | 25/55-55A | 25/55-55A | 30/45 |
Binder content | 6.2 M.-% | 6.6 M.-% | 4.6 M.-% |
Aggregate bitumen affinity (24 h) | 60% | 60% | 35% |
Reclaimed asphalt | 0% | 0% | 40% (16 RA 0/11) |
Aggregate type | Quartzite | Granite | Quartzite |
Aggregate shape | Mainly cubic shaped | Mainly cubic shaped | Mainly cubic shaped |
Maximum density aggregate mix | 2.660 g/cm3 | 2.710 g/cm3 | 2.709 g/cm3 |
Impact value (aggregates ≥ 2 mm) | 18% | 15% | 18% |
Reference bulk density | 2.351 g/cm3 | 2.357 g/cm3 | 2.388 g/cm3 |
Young’s modulus according to [31] | 3.00e + 07 Pa | 3.50e + 07 Pa | 2.00e + 07 Pa |
Sieve size (mm) | Cumulative passing weight (M.-%) | ||
---|---|---|---|
AC 11 DS | SMA 11 DS | AC 16 BS | |
22.4 | 100.0 | 100.0 | 100.0 |
16.0 | 100.0 | 100.0 | 97.3 |
11.2 | 99.1 | 97.3 | 72.6 |
8.0 | 78.1 | 54.2 | 58.7 |
5.6 | 63.3 | 38.2 | 46.3 |
2.0 | 45.8 | 22.9 | 28.0 |
0.125 | 10.4 | 12.3 | 9.1 |
0.063 | 7.8 | 11.1 | 6.8 |
The investigated temperature levels 130°C, 160°C, and 190°C are based on the values given in the German regulation ZTV Asphalt-StB. There, specifications are given for the maximum and minimum temperatures during the paving and production of asphalt mixes depending on the type of binder used. The temperature of 130°C falls below the specified minimum temperature of 150°C, specifically, 155°C, on purpose in order to be able to determine the temperature influence more clearly. In addition, it is not uncommon in construction practice for delays to occur in the delivery of asphalt mixes and thus for the requirements of the ZTV Asphalt-StB to be fallen short of.
Before testing, all HMA samples were prepared according to European standards. The test equipment and the HMA samples were placed in a drying cabinet at 160°C for 3–5 h prior to the start of the test. To avoid segregation, the asphalt material is filled and placed evenly in layers with a shovel in accordance with the specifications of EN 12697-33 [32].
3.2. Static Press Test
The experimental setup for the static press test is relatively trivial. It consists of a large Marshall sample vessel according to the European standard EN 12697-20 [12] which is also used to determine impact compaction resistance [27], a hydraulic press which can apply a force up to 50 kN, a stamp, and a vertical displacement transducer and a load cell for recording applied forces and deformation during compaction (cf. Figure 2).

To conduct the test, the asphalt mix samples were prepared according Section 3.1. The entire specimen vessel is filled so that a cone of asphalt mix is formed above the specimen vessel. This is then pulled off with a slider, resulting in a corresponding total weight or density depending on the pouring properties of the asphalt material (cf. Figure 3).
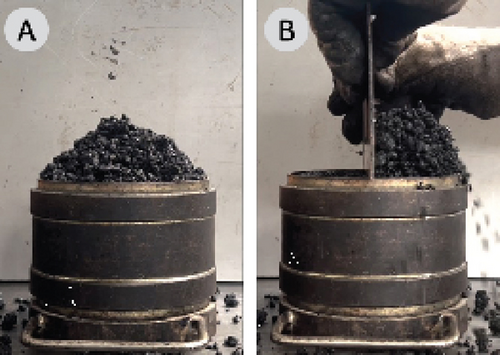
The sample is then loaded with the static compaction device up to a total force of approximately 45 kN. The value that finally describes the resistance to precompaction is the displacement d20 at a force of 20 kN (cf. Figure 4). Preliminary investigations have shown that this results in a degree of compaction of approximately 88% Marshall density. The higher the value of displacement d20, the easier it is to compact the specimen and the lower the precompaction resistance. d20 is therefore a value that is suitable for describing the precompaction resistance of HMA against a static load such as the deadweight of a screed.
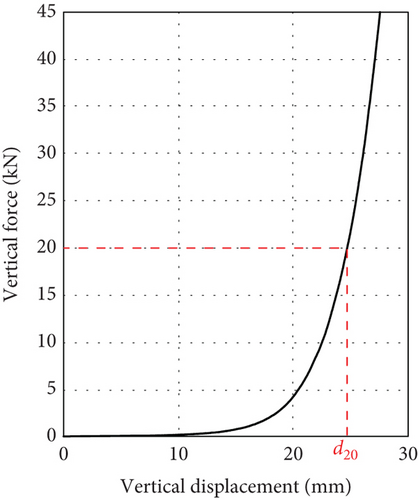
3.3. Flow Behavior Test
The flow properties of the asphalt mixtures in this study are evaluated using the fixed funnel method, measuring both the angle of repose and the discharge flow time. The funnel setup is based on the European standard EN 12696-15 [33]. In practice, it has proven useful to measure the angle of repose on a round plate that is completely covered with sample material (e.g., for powder investigations in DIN ISO 4324 [34]). The diameter is 30 cm to ensure complete coverage and to keep the excess material to a minimum. In order to perform the test, the asphalt mixture and all the test components must first be heated in a heating chamber also. Subsequently, a mass of 10 kg of the respective asphalt mix sample is filled into the funnel according to the procedure described in Section 3.1. Then, the orifice plate of the funnel is opened and the material drops from a specific height onto the preheated steel plate. The discharge flow time tF characterizes the delta time from when the asphalt material starts to flow evenly to the exit of the last grain. After the total discharge of the asphalt mixture from the funnel, a specific angle of repose Φ is obtained which is calculated via the height h and width D of the pile. The test dimensions and setup of the funnel test are displayed in Figure 5.
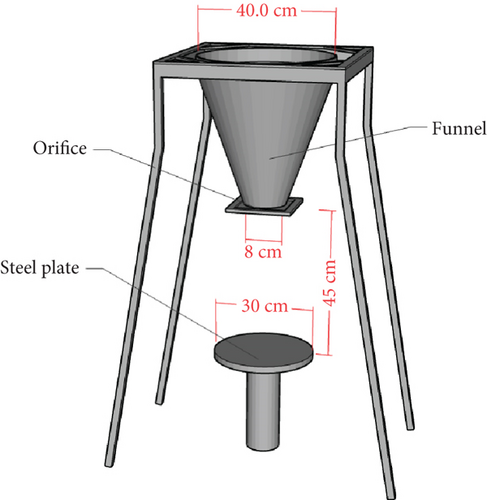
4. Results
To evaluate if the temperature or the use of different asphalt mixtures has a significant impact on the results, the least significant difference (LSD) [35] test was used. In order to obtain statistical certainty, three individual tests were carried out for all trials. All results in Figures 6, 7, 8, and 9 are therefore an arithmetic mean value from three individual tests. The black bars within the diagrams indicate the respective standard deviations.
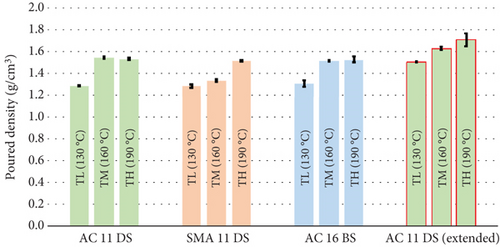
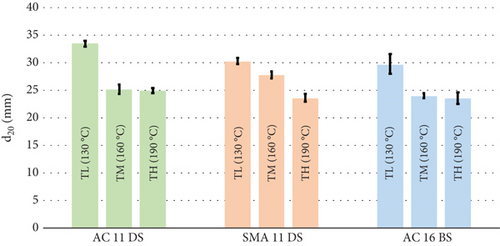

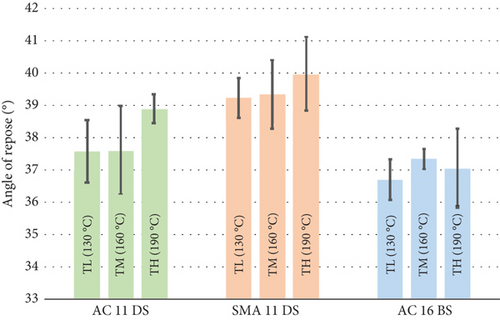
4.1. Poured Density Properties
Before the resistance to precompaction can be evaluated, it is first necessary to consider the poured density resulting from the pouring procedure described (cf. Figure 6). For the asphalt mix AC 11 DS, it can be noticed that a significantly lower poured density occurs at the lowest temperature level TL compared to the temperature levels TM and TH (cf. Figure 6). This is caused by the increase in viscous τvisc and cohesive τc resistance at colder temperatures (cf. Figure 1). Above a temperature of 160°C, no more difference between the poured densities can be observed because an increase in temperature at a high temperature level should only have a minor effect on viscous τvisc and cohesive τc resistance (cf. Figure 1). The asphalt mix AC 16 BS shows the same behavior. The poured density for the temperature level TL is also significantly lower. The difference between the poured densities of the asphalt mixture SMA 11 DS for the temperature levels TL and TM is minimal and not significant. At the high temperature level of 190°C, however, the poured density is significantly higher and comparable to the other asphalt mixes. Since the grain size distribution influences the deformation resistance [3], this is probably due to the higher coarse grain content of the SMA, which could already be noticeable under the deadweight of the fill. This is further supported by the significantly lower viscous resistance τvisc at high temperatures and the fact that the binder film becomes thinner, increasing the likelihood of dominant grain-to-grain contacts.
As an example, the poured density for an extended Marshall specimen (same diameter but height of 20.7 cm instead of 9.7 cm) was determined using the AC 11 DS asphalt mix (cf. Figure 6). It can be noted clearly that the poured densities for all temperature levels are above those of the standard Marshall specimen. Thus, this asphalt mix with the higher poured height H would be more difficult to compact and lead to a larger deformation resistance τdr, confirming Utterodt’s [11] reasoning in Figure 2.
To determine the extent to which consolidation of the asphalt mix takes place as a result of its own weight, sections were cut out of the extended Marshall specimen and an asphalt petrological analysis according to [36] was carried out. This allows the vertical distribution of air voids to be analyzed. The results can be found in Figure 10, which shows a slight decrease in the proportion of voids over depth for all temperatures. The effect is most pronounced at the TL temperature level. The hypothesis that consolidation occurs as a result of the deadweight can thus be confirmed.
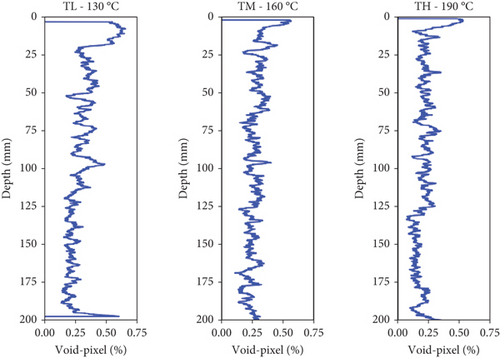
4.2. Precompaction Resistance
The results of the precompaction resistances using the deformation value d20 are shown in Figure 7. There is a strong relation between the poured density and the compaction resistance for each asphalt mixture as displayed in Figure 11. Obviously, the samples with the lower poured density can be compacted more easily. However, the temperature does not seem to affect the precompaction resistance under a static load up to 20 kN. Even for the asphalt mix specimens with uniform pouring characteristics but at different temperature levels (ID: AC11-TM/AC11-TH and AC16-TM/AC16-TH), no difference in precompaction resistance is evident.
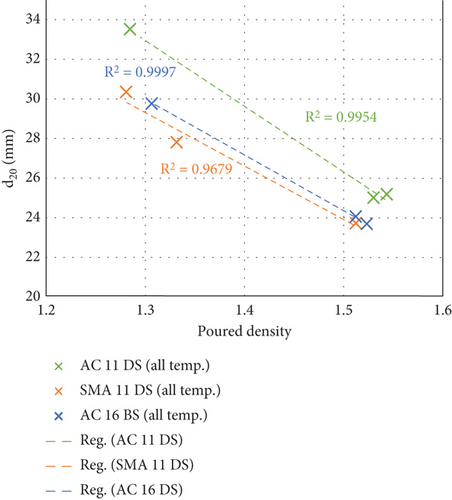
It can be concluded that a change in temperature for the asphalt mixes AC 11 DS, SMA 11 DS, and AC 16 BS has no direct effect on the precompaction resistance, since it has a much greater effect on the poured density. During subsequent precompaction, the reduced cohesive τc and viscous τvisc resistances of the mortar at high temperatures are wholly superimposed. By comparing the asphalt mixes, it can be noted that the AC 11 DS asphalt mix is the easiest to compact.
4.3. Flow Behavior
The flow behavior is evaluated according to the angle of repose Φ and the discharge flow time tF. Figure 8 shows the angles of repose exemplary for the asphalt mixes AC 11 DS, SMA 11 DS, and AC 16 BS at temperature level TM (160°C).
The results are given in Figure 9. Already the high standard deviations show that the results are not statistically significant. Furthermore, it is unclear to what extent a temperature change affects the angle of repose. At least for the AC 11 DS and SMA 11 DS asphalt mixes, the increase in temperature seems to lead to an increase in the angle of repose, which contradicts expectations. Since more flowable materials generally lead to a flatter angle of repose [30] and HMA should be more flowable at high temperatures, the angle of repose Φ is therefore considered unsuitable for describing the flow behavior of HMA.
The results of the discharge flow time tF are shown in Figure 12. In contrast to the angle of repose, the temperature-relevant results differ statistically significantly from each other, with the exception of samples SMA11-TM versus SMA11-TH and AC16-TM versus AC16-TH. Comparing the asphalt mixes with each other in most cases, the asphalt mix–relevant results do not differ significantly from one another. Thus, it can be assumed that even the coarser grading curve of the AC 16 BS asphalt mix (cf. Table 3) does not shorten the discharge flow time. It should be noted, however, that the discharge flow time of the AC 16 BS at the TL temperature level is noticeably lower than that of the AC 11 DS and SMA 11 DS asphalt mixes, which is probably due to the properties of the binder used (cf. Table 2) having a different viscous resistance τvisc. The AC 11 DS and SMA 11 DS asphalt mixes show similar times at around 7 s.
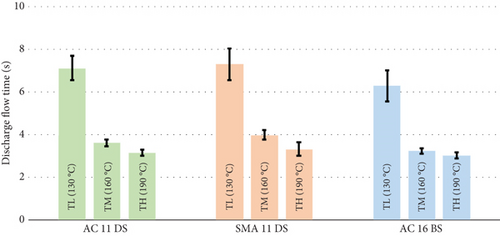
Smaller differences can be found between the higher temperature levels TM and TH. It can therefore be assumed that the temperature range between 190°C and 160°C in particular is critical for the flow properties of an asphalt mix. Nevertheless, a further significant shortening of the discharge flow time for the asphalt mixes AC 11 DS and AC 16 BS at the temperature level TH can be seen. When comparing the asphalt mixes with each other at the mean temperature level, no significant difference can be detected between the asphalt mixes AC 11 DS and SMA 11 DS. Since both mixes were produced with the same binder but have clearly different grading curves, it can be again assumed that the grading curve only has a minor influence on the flow behavior of the asphalt mixes under consideration.
5. Conclusion
- •
A broad literature research showed that the static compaction test adequately describes the precompaction process. Laboratory tests confirmed this, and a corresponding characteristic value d20 was developed. The literature research also showed that the angle of repose is generally suitable for describing the internal friction and thus the flow behavior of a bulk material. However, the fixed funnel test has shown that the angle of repose is unsuitable for describing the flow behavior of HMA. The discharge flow time tF on the other hand turned out to be an adequate parameter.
- •
Studies on loose asphalt mix have shown that temperature has a significant effect on the poured density of a loose fill, which can be attributed to the thermoviscosity of the bitumen, specifically, the viscous τvisc and cohesive τc resistance components. It was also found that a larger mix quantity results in a higher poured density for loose fill. Asphalt petrological results showed that the consolidation due to the deadweight takes place predominantly in the lower part of the fill.
- •
Only an indirect correlation could be found between the precompaction resistance d20 and the temperature. Since a lower poured density result from low temperatures, the colder asphalt mixes exhibit a lower precompaction resistance which contradicts the general understanding in the literature because the pouring density is usually not taken into account. The higher viscous τvisc and cohesive τc resistances of the mortar at lower temperatures are completely superimposed by this effect.
- •
The measurement of the discharge flow time tF with the fixed funnel test showed that the flow behavior is significantly dependent on the temperature. Higher temperatures favor the flow behavior and lead to lower discharge flow times by up to 225%.
It can therefore be concluded that in practical paving with the paver screed (levelling system not in use), a higher mix temperature actually leads to the screed floating up resulting in an increased layer thickness. The HMA as loose fill has a higher precompaction resistance due to the increased poured density and an increased flowability at higher temperatures. This means that larger quantities of asphalt mix can flow under the screed more quickly. The observations and preliminary investigations in [7] can thus be confirmed. If a levelling system is used or manual levelling is performed, fluctuating HMA temperatures can be compensated for by adjusting the height cylinder accordingly. However, this means that the angle of attack of the screed constantly changes, which in turn can lead to irregularities in the surface and an inhomogeneous microstructure. When paving, it is therefore still essential to ensure that the paving temperature is uniform.
Disclosure
This paper reflects only the authors’ view. Neither the European Climate, Infrastructure and Environment Executive Agency (CINEA) nor the European Commission is in any way responsible for any use that may be made of the information it contains.
Conflicts of Interest
The authors declare no conflicts of interest.
Funding
This paper was carried out in the framework of the InfraROB project (Maintaining integrity, performance and safety of the road infrastructure through autonomous robotized solutions and modularization), which has received funding from the European Union’s Horizon 2020 research and innovation program under Grant Agreement No. 955337.
Acknowledgments
This paper was carried out in the framework of the InfraROB project (Maintaining integrity, performance and safety of the road infrastructure through autonomous robotized solutions and modularization), which has received funding from the European Union’s Horizon 2020 research and innovation program under Grant Agreement No. 955337.
Open Research
Data Availability Statement
The data supporting this study’s findings are available from the corresponding author upon reasonable request.