Enhanced Catalytic Activity and Reusability of Porous Niobium Oxide for Esterification of Acetic Acid With Butanol
Abstract
Through this study, porous niobium (V) oxide catalysts for esterification of acetic acid with butanol to make butyl acetate are made and characterized. The catalysts were synthesized using a sol-gel method and characterized using X-ray diffraction (XRD), Raman spectroscopy, BET surface area analysis, and TPD acidity measurements. The XRD results confirmed the hexagonal structure of both fresh and regenerated catalysts, and the low-angle XRD analysis revealed the material’s porous nature. Raman spectroscopy showed the characteristic Nb-O-Nb stretching band at 698 cm−1, which was retained even at higher calcination temperatures. The catalytic performance was evaluated under various conditions, including different reactant mole ratios, catalyst amounts, and reaction temperatures. The optimal conditions were 1:2 mol ratio of acetic acid to butanol, 0.1 g of catalyst, and a reaction temperature of 120°C, achieving a maximum ester yield of 89%. The catalyst’s performance was superior to that of Al2O3, ZrO2, and bulk Nb2O5, highlighting the importance of the porous structure in providing a more significant number of active sites. Recyclability tests demonstrated that the catalyst maintains stable activity over five cycles, with only a slight decrease in yield. This stability is attributed to the retention of the porous structure and the high number of acidic sites at the optimal calcination temperature of 300°C.
1. Introduction
Niobium (V) oxide, or compositions containing it, is a water-tolerant and versatile solid acid material widely studied for various catalytic reactions [1–3]. However, the lower surface area of bulk niobium oxide diminishes its catalytic activity. The catalytic performance can be significantly improved by creating porous niobium oxide materials through specific preparation methods that increase the surface area. Niobium oxide materials have been utilized in various catalytic transformations [4–8]. Research studies led by Shinzato et al. found that porous niobium (V) oxide was much better at absorbing and releasing hydrogen than its crystalline or bulk forms [3]. Skrodczky et al. discovered that nanoparticles of niobium compounds with larger surface areas exhibited superior performance as catalysts in the synthesis of acetophenone [5]. The study conducted by Marin et al. focused on exploring the versatility of different forms of niobium (V) oxide in ring-opening acid-catalyzed reactions [6]. Tao et al. pioneered high-surface-area niobium (V) oxide as a heterogeneous catalyst in aniline oxidative coupling, with H2O2 as the oxidant [7]. In addition, Uozumi et al. synthesized polymers using high-surface-area niobium (V) oxide for transamidation reactions [8]. Researchers continue to invest a significant effort into the development of high-surface-area niobium catalysts due to their wide range of applications in various reactions, such as the production of acetophenone, ring-opening reactions, oxidative coupling of aniline, and transamidation reactions. This study uses a synthesized porous niobium catalyst to explore the esterification reaction, highlighting its superior catalytic capabilities.
The catalytic conversion of acetic acid to butyl acetate is necessary due to its utilization in drugs, chemicals, and several other areas [9–12]. On the other hand, sulfuric acid catalysts are commonly used for the bulk production of n-butyl acetate. The conventional method for ester synthesis encounters difficulties, including problems with separation, potential damage to the reactor, and limited selectivity for the desired product. In addition, the process is relatively inefficient because it requires a significant amount of water to separate H2SO4 from the reaction mixture. This is advantageous in meeting green methodology standards and enhancing yield while simplifying ester isolation during the reaction. Bulk catalysts or materials have lower activity compared to porous materials [13]. Studying porous materials is essential for improving catalytic performance. The sol-gel method produced a porous niobium (V) oxide catalyst containing P123 surfactant. We explored different reaction parameters using the porous catalyst to enhance the conditions for improved ester yields. This study explores the impact of niobia porous characteristics and establishes a correlation between catalytic performance, surface area, and acidity.
2. Materials and Methodology
2.1. Chemicals and Materials
The materials (AR grade of > 99.5% in purity, purchased from Merck and Sigma-Aldrich Company) used for the synthesis of porous Nb2O5. Niobium (V) ethoxide, P123, Nb2O5, TiO2, ZrO2, acetic acid, ethanol, butanol, and deionized water.
2.2. Synthesis (Preparation of Porous Nb2O5)
2.3. Characterization Techniques
The synthesized materials were analyzed using X-ray powder diffraction with a D8 diffractometer (Advance, Bruker, Germany), using Cu Kα radiation (1.5406 Å) at 40 kV and 30 mA. We used temperature-programmed desorption (TPD) of ammonia on an AutoChem 2910 instrument (Micromeritics, United States of America) to measure acidity. The peak integration was executed using GRAMS/32 software. The surface area of the BET studies was carried out using the Auto Chem 2910 analyzer. The SEM images of materials were recorded on S-4800 microscope.
2.4. Catalytic Activity Study
The niobium material was tested for the esterification of acetic acid with butanol in a 100-mL round-bottom flask at reflux temperature. The experiment (Scheme 1) combined 10 mmol of acetic acid, 20 mmol of butanol, and 0.1 g of the catalyst and refluxed for 5 h. The reaction mixture was carefully monitored using a gas chromatograph with a flame ionization detector. The recycled catalyst was tested under the same conditions to evaluate its reusability.
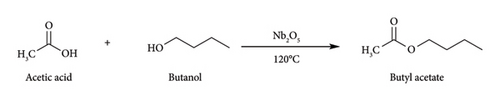
3. Results and Discussion
The wide-angle X-ray diffraction (XRD) patterns of both the freshly synthesized and regenerated niobium catalysts are depicted in Figure 1. The observed diffraction peaks can be attributed to the crystal planes (001), (100), (101), (002), (110), (102), (111), and (200), which are known to be characteristic of hexagonal niobia according to the JCPDS 00-007-0061 reference [14]. Observing these peaks in fresh and regenerated catalysts, the authors suggest that the niobium oxide maintains its hexagonal crystal structure during regeneration. The observation indicates that the catalyst retains its structural integrity following the reaction and regeneration procedures, verifying its stability and potential for subsequent use. And also, even the catalyst calcined at higher calcination temperature at 600°C retains its structure of the catalyst.
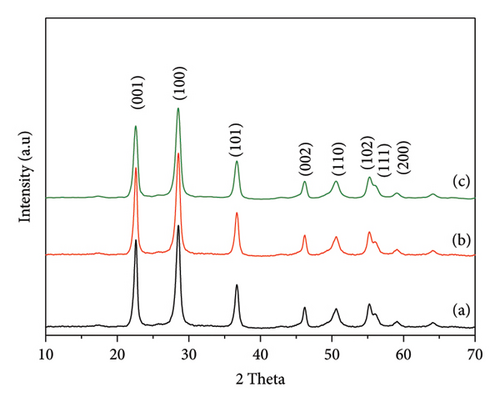
The low-angle XRD profiles of the synthesized fresh and regenerated niobium catalysts are depicted in Figure 2. The presence of diffraction peaks at a 2θ value of 2.9° suggests that the material exhibits a porous structure [15–17]. The results indicate that the fresh and regenerated niobium catalysts display the characteristic peak, indicating that the regenerated catalyst maintains its porous structure following the reaction. The significance of this finding lies in its demonstration of the catalyst’s structural stability and reusability. Preserving the porous structure in the regenerated catalyst is of utmost importance in sustaining high catalytic activity and efficiency. The low-angle XRD results support this. The low-angle XRD data prove that the regenerated catalyst maintains its advantageous porous structure, like that of the fresh catalyst.
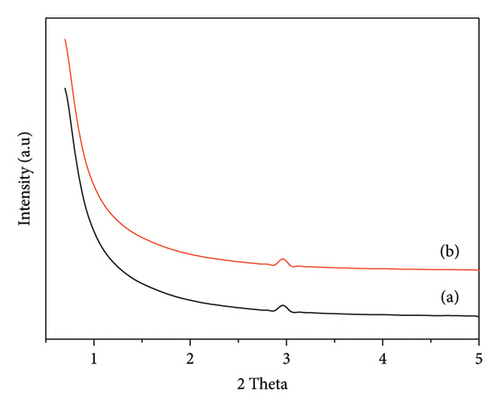
The Raman spectra of the niobium catalyst that was synthesized and subsequently calcined at different temperatures are depicted in Figure 3. The spectra were recorded within the wavelength range of 400–1000 cm−1. A characteristic Raman band at 698 cm is observed, attributed to the stretching mode of Nb-O-Nb. The band observed in the niobium oxide structure is a notable characteristic that remains intact even when subjected to elevated calcination temperatures. The observed persistence of the 698-cm−1 Raman band at various calcination temperatures indicates that the structure of niobium oxide remains stable during thermal treatment. The stability of the material is of utmost importance in preserving its catalytic properties. The material must maintain its structural integrity under different conditions, as this is necessary for ensuring consistent performance. The findings presented here are consistent with previous studies conducted by Shepa et al. [18] and Qu et al. [19]. These studies also observed the presence of the characteristic band in nanoporous niobium catalysts. The correlation with these studies further validates our niobium catalysts’ synthesis and thermal stability. The Raman spectra confirms that the synthesized niobium catalysts maintain their structural characteristics, even when exposed to high temperatures. This suggests that these catalysts can be used in high-temperature catalytic applications.
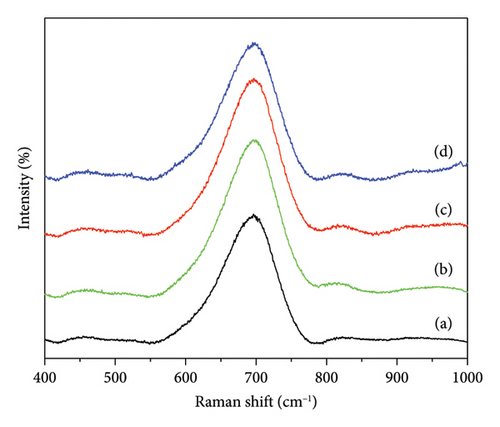
An evaluation was conducted on the BET surface area and acidity measurements, with the results presented in Table 1. The surface area of niobium catalysts decreases as the calcination temperature increases. The BET surface area decreases from 93 m2/g at 300°C to 39 m2/g at 600°C. The acidity values exhibit a decreasing trend as the calcination temperature increases. Specifically, the acidity decreases from 0.89 mmol/g at 300°C to 0.23 mmol/g at 600°C. The decrease in the surface area is directly associated with the drop in the acidity of the material. The decrease in the surface area reduces the available acidic sites, thereby decreasing the overall acidity of the catalyst. The correlation between the surface area and acidity is of utmost importance due to its influence on the catalytic efficiency of the material. Maintaining a high surface area and acidity is crucial for optimal catalytic activity. By studying the changes in these properties at different calcination temperatures, one can better customize the synthesis process to enhance catalyst performance.
Calcination temperature (°C) | BET surface area (m2/g) | Acidity (mmol/g) |
---|---|---|
300 | 93 | 0.89 |
400 | 75 | 0.56 |
500 | 50 | 0.34 |
600 | 39 | 0.23 |
The structural and functional properties of the synthesized niobium catalysts were characterized. The stability of the hexagonal structure was confirmed by XRD and Raman spectroscopy. In addition, the BET surface area and acidity measurements indicated a decrease as the calcination temperature increased from 300°C to 600°C. Nevertheless, the catalysts exhibited structural solid integrity and notable catalytic properties, rendering them appropriate for various applications.
To know the external morphology of synthesized and regenerated porous niobia catalysts were identified by the SEM analysis (Figure 4). These SEM images of fresh and regenerated catalysts are indicating that hexagonal like morphology.
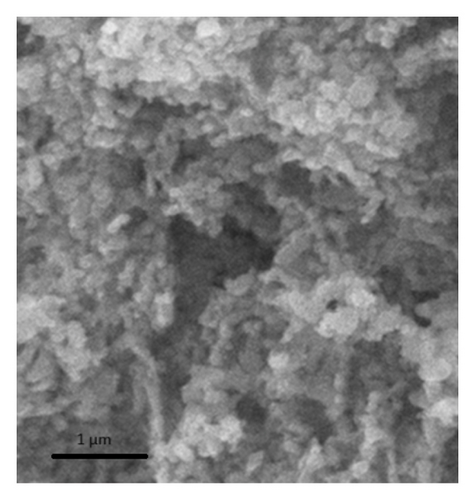
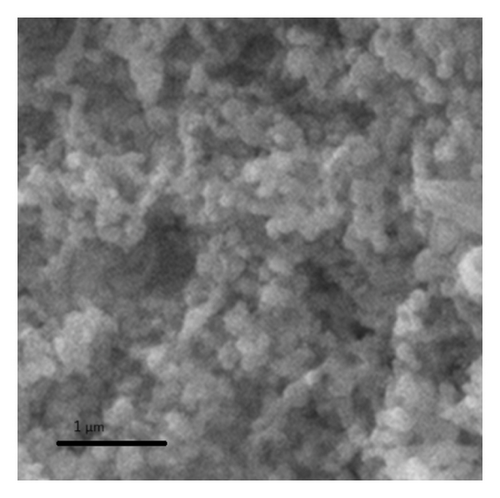
The catalytic performance of the niobium catalysts was assessed for the esterification reaction using different catalysts prepared at varying calcination temperatures (Table 2). The reaction without a catalyst resulted in a conversion rate of 4.5% to butyl acetate. The niobium catalyst, subjected to calcination at 300°C, demonstrated a remarkable yield of 89% for butyl acetate. The yield of ester decreased as the calcination temperature increased (Table 2). The catalytic studies conducted in this research emphasize the significant influence of calcination temperature on the catalytic efficiency of the niobium catalysts. The optimal calcination temperature of 300°C yields the highest results, aligning with the BET surface area and acidity measurements. The catalyst calcined at 300°C demonstrates the highest surface area (93 m2/g) and acidity (0.89 mmol/g), as indicated in Table 1. The catalytic activity decreases as the calcination temperatures increase due to decreased surface area and acidity.
Catalyst calcination temperature (°C) | Conversion (%) | Butyl acetate yield (%) |
---|---|---|
Blank | 4.5 | 4.5 |
300 | 89 | 89 |
400 | 77 | 77 |
500 | 62 | 62 |
600 | 53 | 53 |
- aReaction conditions: 10 mmol (acetic acid), 20 mmol (butanol), catalyst = 0.1 g, and reaction temperature = 120°C.
To sum up, the calcination temperature dramatically affects the structure and catalytic qualities of the niobium catalysts. It is essential to keep the calcination temperature at the right level to get the most surface area, keep the acidity, and ensure the catalyst has much activity in the esterification processes.
We studied how well the Nb2O5 catalyst worked in the esterification process with different amounts of acetic acid and butanol when the catalyst was heated to 300°C (Table 3). The results show that 89% of the butyl acetate can be made when acetic acid and butanol are mixed in a 1:2-mol ratio. After the mole ratio exceeded 1:2, the ester output slowly decreased. A yield of 78% was seen at a mole ratio of 1:3, and a yield of 65% was seen at a mole ratio of 1:4. The dilution effect is what causes the ester yield to go down as the mole ratio of acetic acid to butanol goes up. Compared to acetic acid, more butanol is added, and less acetic acid is present in the mixture. Because of this dilution effect, fewer acetic acid molecules are available at the catalyst’s active sites. This lowers the catalyst’s activity, lowering the amount of ester. This concludes that the Nb2O5 catalyst heated to 300°C works very well to change acetic acid into butanol. The best results happen when the reactants are matched 1:2 mol. This ideal ratio guarantees high catalytic activity and maximizes the yield of butyl acetate, making it a state that looks good for real-world use.
Mole ratio (acetic acid/butanol) | Conversion (%) | Butyl acetate yield (%) |
---|---|---|
1:1 | 67 | 67 |
1:2 | 89 | 89 |
1:3 | 81 | 81 |
1:4 | 73 | 73 |
- aReaction conditions: 10 mmol (acetic acid), 10–40 mmol (butanol), catalyst = 0.1 g, and reaction temperature = 120°C.
Table 4 displays how well different amounts of porous niobium catalyst (Nb2O5) work as a catalyst for making butyl acetate. The results show that increasing the catalyst from 0.05 g to 0.1 g yields 89% more butyl acetate. Further catalyst increases to 0.2 and 0.3 g only slightly enhance ester yield, hitting 91% and 92%, respectively. Because there are more active sites for the process, increasing the catalyst quantity from 0.05 to 0.1 g significantly increases catalytic activity. More efficient use of the catalyst’s surface area and active sites increases reactant-to-product conversion rates. The catalyst particles may be aggregating or overlapping, reducing reaction active sites. A yield of 89% can be achieved with 0.1 g of catalyst because the active sites are fully used without significant advantages from adding more catalysts. These results emphasize the need to adjust catalyst amounts for catalytic efficiency and yield. In conclusion, the Nb2O5 catalyst is ideal for butyl acetate production at 0.1 g, which maximizes catalyst active site use, yielding 89%. Increasing the catalyst amount has slight advantage, demonstrating the efficiency of employing the optimal catalyst amount for actual applications.
Catalyst amount (g) | Conversion (%) | Butyl acetate yield (%) |
---|---|---|
0.05 | 56 | 56 |
0.1 | 89 | 89 |
0.2 | 91 | 91 |
0.3 | 92 | 92 |
- aReaction conditions: 10 mmol (acetic acid), 20 mmol (butanol), catalyst = 0.05–0.3 g, and reaction temperature = 120°C.
Table 5 displays the results of the catalyst’s evaluation at various reaction temperatures ranging from 110°C to 130°C. The ester yield increased substantially from 75% at 110°C to 89% at 120°C. Nevertheless, yields reached a plateau at 90%, and further temperature increases to 125°C and 130°C yielded only minor enhancements. In order to achieve the maximum yield of 89%, the optimal reaction temperature is 120°C. Higher temperatures did not significantly increase the yield, most likely because the reaction had reached its maximum efficiency or because active sites might have become inactive at those temperatures. In summary, the Nb2O5 catalyst is most efficient at 120°C, which guarantees the maximum possible yield of butyl acetate. The minimal benefits of additional temperature increases underscore the significance of temperature optimization for optimal catalytic efficiency.
Reaction temperature (oC) | Conversion (%) | Butyl acetate yield (%) |
---|---|---|
110 | 72 | 72 |
120 | 89 | 89 |
130 | 90 | 90 |
- aReaction conditions: 10 mmol (acetic acid), 20 mmol (butanol), catalyst = 0.1 g, and reaction temperature = 110°C–130°C.
Combining acetic acid with butanol to form an ester was examined utilizing several catalysts, namely, Al2O3, ZrO2, bulk Nb2O5, and porous Nb2O5 (Table 6). The catalytic data demonstrate that the porous Nb2O5 catalyst exhibits the highest butyl acetate yield at 89%, surpassing Al2O3 (29%), ZrO2 (43%), and bulk Nb2O5 (56%). The enhanced efficiency of the porous Nb2O5 catalyst can be attributed to its elevated surface area and augmented quantity of active sites compared to the other catalysts (Table 6). The porous nature of niobium oxide improves the availability of reactants to the active sites, leading to enhanced catalytic efficiency and, consequently, higher ester yields. The Nb2O5 catalyst, which has a porous structure, exhibits outstanding catalytic efficiency in the esterification reaction between acetic acid and butanol, resulting in maximum butyl acetate production. The enhanced performance can be attributed to the enlarged surface area and greater quantity of active sites offered by the porous structure, providing better catalytic performance compared to other catalysts (Table 6).
Catalyst | Conversion (%) | BET surface area (m2/g) | Acidity (mmol/g) | Butyl acetate yield (%) |
---|---|---|---|---|
Al2O3 | 29 | 98 | 0.14 | 29b |
ZrO2 | 43 | 20 | 0.28 | 43b |
Bulk-Nb2O5 | 56 | 43 | 0.35 | 56b |
Por.Nb2O5 | 89 | 93 | 0.89 | 89 |
- aReaction conditions: 10 mmol (acetic acid), 20 mmol (butanol), catalyst = 0.1 g, and reaction temperature = 120°C.
- bCommercial catalysts.
The reusability of the porous niobium catalyst for the esterification of acetic acid with butanol was assessed over five cycles (Figure 5). The catalyst exhibits consistent activity throughout five cycles, with a marginal decline in yield from 89% in the initial cycle to 85% in the fifth cycle. The consistent performance of the porous niobium catalyst throughout multiple uses highlights its resilience and long-lasting nature. The maintenance of catalytic activity can be ascribed to the preservation of the catalyst’s porous structure, as validated by the low-angle XRD data (Figure 2). The presence of a porous structure guarantees that a considerable number of active sites remain available for the reaction, even after undergoing numerous rounds of regeneration. The durability of its catalytic efficacy is attributed to the preservation of its porous structure, which maintains the accessibility of active sites. The high durability of the porous niobium catalyst makes it an excellent choice for sustainable and recurrent usage in industrial applications.

3.1. Mechanism Butyl Acetate Formation
Initially (Scheme 2), the lone pair of oxygen of the carbonyl group in acetic acid make dative bond with empty orbital of porous Nb2O5 catalyst. Further the lone pair of oxygen from butanol is attack on carbonyl carbon in acetic acid results intermediate. Now the intermediate is dehydrated to yield butyl acetate [20].
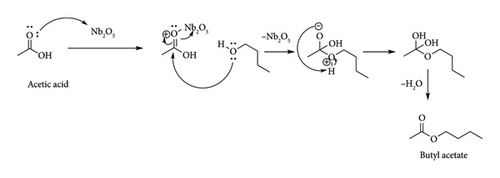
3.2. Comparison Study
The catalytic results of esterification of acetic acid with butanol over porous niobia catalyst is compared with pyridinium-based acidic ionic liquids, and results are tabulated in Table 7. The present work illustrates that not required solvent as well as easy isolation of catalyst from reaction mixture and exhibits better catalytic activity during reaction. When compared to pyridinium-based acidic ionic liquids, it provides 76% yield, and also solvents of hexane/heptane were used for reaction results separation of the solvent, and product isolation is difficult. Therefore, the present work exhibits higher yield compared to pyridinium-based acidic ionic liquids [12] such as [H-Pyr]+[NO3]−, [H-Pyr]+[H2PO4]−, and [H–Pyr]+[HSO4]−.
4. Conclusions
This study demonstrates that the niobium catalyst with a porous structure has a remarkable efficiency in promoting butyl acetate production. The XRD examination verifies the hexagonal structure of both the fresh and regenerated catalysts, thereby demonstrating the durability of the porous niobium structure. The BET surface area analysis reveals that the catalyst subjected to calcination at 300°C exhibits a markedly greater surface area than those subjected to higher temperatures. The NH3-TPD analysis shows that the catalyst calcined at 300°C has a higher concentration of acidic sites, which enhances its catalytic activity. The XRD and BET data show that the porous niobium catalyst has superior stability in butyl acetate production compared to bulk niobium, zirconia, and alumina catalysts. The catalyst, freshly prepared and then heated to 300°C, constantly exhibits exceptional activity throughout the reaction. In addition, the catalyst underwent testing for its reusability across five cycles. The recycling investigations demonstrate that the catalyst maintains a consistent activity level, emphasizing its long-lasting nature and potential for multiple uses in industrial applications.
Conflicts of Interest
The authors declare no conflicts of interest.
Funding
The authors received no specific funding for this work.
Acknowledgments
The authors gratefully acknowledge the GMR Institute of Technology-Rajam, Sri GCSR College-Rajam, Koneru Lakshmaiah Education Foundation-Guntur and Chungnam National University-Daejeon.
Open Research
Data Availability Statement
The data that support the findings of this study are available from the corresponding author upon reasonable request.