Experimental Evaluation of Bio-Based Materials in Epoxidation Techniques
Abstract
Epoxy composites as per their excellent adhesive behavior, mechanical strength, electrical insulation, and chemical resistance have been utilized in a number of applications and constitute a major chunk of polymer industry. Epoxy, since ages, has been derived from petrochemicals which has been a major source of environmental pollution and has drawn a limit at various applications. This datum highlights the dire need of bio-based materials, for their nontoxic, eco-friendly, economical, and renewable behavior. To counter the pollution factor associated with petrochemical-derived epoxies, various epoxidation strategies on bio-based materials have been reported with designed reagents (catalyst, acid, enzyme, or metal). This review has been compiled for latest progressions in epoxidation approaches of bio-based materials, considering them as potentially eco-friendly green replacements of petrochemical resources. It has a lot of information of usage of bio-waste and their property. The thermal and photocuring discussed with the different techniques. In thermal technique hardening agent which gave epoxy the definite structure and in photocuring PI agent used for curing and making them polymer but they showed crucial effect on environment. After that other bio-based epoxidation (BBEP) strategical techniques introduced such as hypochlorination (most primitive technique at small scale and gave 93% selectivity with minimum by-products), homogeneous and heterogeneous catalysis, chemoenzymatic method, and metal catalyzed reactions have been compared in this review based on chemistry involved in epoxidation reaction. This article summarizes a large number of precursors, reagents, and reaction conditions for a wide variety of end products and applications, allowing the reader to see experimental alternatives and their potential benefits in a single place.
1. Introduction
Epoxy thermosets are sustainable cross-linked polymers, with exceptionally unique chemistry of cross-linking with self or curative (nucleophiles/hardeners). This review is particularly designed over green synthetic approaches for epoxy, utilizing bio-based materials rather than petrochemicals. This comprehensive study of epoxidation approaches has data compilation for qualitative as well as quantitative control over product, specifically highlighting structure-activity relationship of epoxidized materials. A shortage of petroleum resources due to their excess use in daily life brought nanotechnology into the game which replaced petrochemical-based epoxidized materials with bio-based eco-friendly alternatives. Synthetic polymers were at the center of attention because of wide range of their properties including but not limited to mechanical [1, 2], chemical, electrical [3], gel contents, and percent crystallinity. Now alternate bio-based polymers are available, providing option of desired changes in mechanical, thermal, and electrical properties. Epoxy thermoset polymers have been used in aerospace, athletic, marine, and biomedical devices [4]. Epoxy resins have been used in the coating industry as anti-corrosion due to adhesive behavior. Epoxy coatings have been used in food packaging to prevent microbial attack [5, 6]. Epoxy adhesives have been reported for automobiles, boats, aircraft, and bicycle [7].
Any industry that produces molds, laminating sheets, and plastic repairing materials, under heavy pressure, can make use of epoxies for durable products. High-quality glass with thermal and mechanical stability has been reported with epoxidized materials resulting in economical and eco-friendly options [8]. Epoxy resins have also been reported as heat insulators in electronics to protect the appliances from short circuit [2]. Bypass vascular graft, wound dressing, orthopedic fixation, plastic surgery, and medicines are few examples of biodegradable polymeric applications [9]. The bio-based polymers have applications in restoration of nose cavity and in treatment of ear and construction of pinna. These have variety of applications in these fields [10]. A range of applications for these polymers have been reported due to high performance, low friction without external lubricants, and light weight [11].
Novel epoxidation techniques include a vast range of approaches like hyperchlorination, peroxy acid epoxidation, and chemoenzymatic epoxidation. Additionally, advancements in homogeneous and heterogeneous catalysts, such as acid ion exchange catalysts as well as metal-catalyzed epoxidation, offer enhanced selectivity and efficiency. These innovations pave the way for greener and more sustainable production processes, promising to revolutionize the synthesis of bio-epoxies with improved performance and reduced environmental impact.
To understand unique reactivity of epoxy, structural comparison of ethylene oxide with dimethyl ether has been made that explains angle strain in epoxy ring at C-C bond (Figure 1) [12, 13]. This increased angle strain is due to reduction in bond angle from 112° (in ether) to 61°.24′ (in epoxy), which evidences augmented reactivity of epoxy ring in comparison to ether [12]. Likewise, structural comparison of epoxy with cyclopropane revealed the difficulty for oxirane ring to have 60° angle of sp3 hybridized carbon as in cyclopropane, so sp2 hybridized carbon overlaps with atomic orbital of oxygen to formulate epoxide ring. The distortion in the tetrahedral carbon angle from 109° to 59° also contributes to increased angle strain [12]. Comparison of bond length and angles in oxirane ring with cyclopropane (Figure 1) gives a clue of augmented reactivity for oxirane ring. Moreover, presence of electronegative oxygen affects the geometry of epoxide ring. Swern and Marmer [14] studied thermokinetics of epoxy and observed 13 kcal strain energy gap between experimental and theoretical heat of formation, which benefits highly strained epoxy structure to offer feasibility of ring opening reactions, in the curing process.
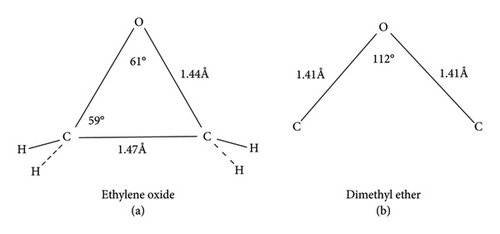
2. Materials and Methods
2.1. Eligibility Criteria
This review paper is based on previously published research articles, related to epoxy formation, its different strategies, and epoxy curing techniques. All topic-related data have been regarded as reliable to write result and discussion.
2.2. Focus Questions
Major focus questions were about problem, investigation, comparison, and outcome (PICO). Research questions were as follows: What is epoxidation? What is bio-based epoxidation? What are the methods of epoxy curing? What are epoxidation strategies? Which techniques are applicable at industrial scale? Which technique gives limited side reactions? What are the benefits of epoxidation method? What are the future trends for epoxidation?
2.3. Search Strategy
- 1.
“Epoxidation” showed 244,000 articles, out of which only those articles were selected which passed the filter of secondary keywords.
- 2.
“Introduction to epoxy resins” showed 452,000 searches and only those articles were selected which passed through filter of secondary keywords.
- 3.
“Epoxidation of VO” showed 17,700 searches from which articles were selected with specific key word filters.
- 4.
Bio-based + epoxidation showed 17,800 searches.
- 5.
Method + epoxy curing.
- 6.
Thermal curing + epoxy.
- 7.
Advantages and application of epoxidation.
- 1.
“Epoxidation of oils” showed 4202 searches, out of which 2669 articles were selected through filters of secondary key words.
- 2.
“Bio based epoxidation of oils” showed 207 searches, out of which 97 articles were selected through filters of secondary key words.
- 3.
“Method of epoxy curing” showed 31,286 searches, out of which 20,007 articles were selected through filters of secondary key words.
- 4.
“Advantages and application of epoxidation” showed 3659 searches, out of which 2127 articles were selected through filters of secondary key words.
- 5.
“Introduction to epoxy resin” showed 61,802 searches, out of which 44,447 articles were selected through filters of secondary key words.
- 6.
“Epoxidation strategies” showed 3728 searches, out of which 1907 articles were selected through filters of secondary key words.
- 1.
“Epoxidation of oils” showed 11,744 searches, out of which 8103 articles were selected through filters of secondary key words.
- 2.
“Bio based epoxidation of oils” showed 417 searches, out of which 187 articles were selected through filters of secondary key words.
- 3.
“Method of epoxy curing” showed 04 searches.
- 4.
“Advantages and application of epoxidation” showed 8219 searches, out of which 4108 articles were selected through filters of secondary key words.
- 5.
“Introduction to epoxy resin” showed 27,471 searches, out of which 19,179 articles were selected through filters of secondary key words.
- 6.
“Epoxidation strategies” showed 11,771 searches, out of which 6043 articles were selected through filters of secondary key words.
2.4. Study Selection
The authors screened the titles and abstracts of all selected research articles independently, as mentioned in Table 1. They finalized research papers and wrote down different components of review paper.
Order | Steps in PRISMA | Inclusion criteria | Exclusion criteria | On the basis |
---|---|---|---|---|
1 | Identification | • Epoxidation articles in each language were identified, but mostly English language-based articles were preferred. | • Studies were reviewed. | The search was based on the key words “epoxidation,” “epoxidation techniques” |
• Selected those papers in which at least word “epoxidation” is present | • Irrelevant articles were skipped, particularly those which were not clearly defining epoxidation methods and techniques. | |||
2 | Screening | Bio-based epoxidation articles were identified and studied | Studies with non-bio-based epoxidations were excluded | Key words included “epoxidation” and “biobased epoxidation” |
3 | Eligibility | Articles with elaborated methods of epoxy formation and curing techniques were studied | Irrelevant methodologies were excluded | Search was based on the key words “biobased epoxidation” and curing strategies. |
4 | Inclusion | Articles with desired data for review were included | Articles out of review standard were excluded | Selected articles were screened to include related ones in review. |
2.5. Data Extraction Process
Data have been collected from topic-related research articles. Authors made self-grouping for data collection and extraction. First group collected introduction-based data, along with data for different curing techniques, including thermal and photochemical. Another group collected and screened data about epoxidation strategies while the third group collected data about epoxidation advantages as well as conclusion.
3. Result and Discussion
3.1. Eligible Study
During searching, a huge number of 400,742 articles were identified, but after title and abstract screening, only 206 articles were shortlisted for full text review (Figure 2). Out of these, 159 articles were excluded due to certain reasons, like 104 articles did not explain epoxidation clearly and 55 articles had short follow-up time period. 47 articles were finally selected for qualitative and quantitative analysis.
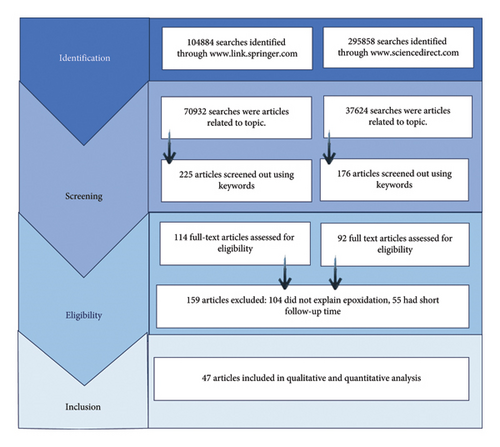
4. Epoxy Curing Strategies
Epoxidation of long chain olefins produces oxirane group which is highly reactive and forms various derivatives [55]. To convert epoxy resin to hard network, cross-linking agents like hardener or curing agents are used. Curing may terminate with the catalytic curing agent (CCA) or copolymerization reaction with different specific curing agents. It is pertinent to mention that these changes are irreversible. Curing agents are divided into amine type curing agent, alkali curing agent, anhydrous, and CCA depending upon the composition [56].
Primary and tertiary amines are used as alkali curing agents [57] while phthalic anhydride (PA), 3,4,5,6-tertiary dropthalic anhydride (DA), and methyl tetrahydrophthalic anhydride (MTHPA) are commonly used as anhydride curing agents along with tertiary amines [58]. CCAs are condition specific. These agents could be benzyl sulfonium, benzylpyridinium, benzyl ammonium, and phosphonium salt [59, 60]. Few epoxidation strategies along with the reagent, their yield, their FTIR results, and precursors are mentioned in Table 2.
Precursor | Epoxidation strategy | Reagent | Reaction temperature/time | % yield | FTIR result | Ref | |
---|---|---|---|---|---|---|---|
Precursor (cm−1) | Product (cm−1) | ||||||
Isosorbide | Homogeneous catalysis through percarboxylic acid | Octanoic acid, palmitic acid, oleic acid, Ti (IV) butoxide, myristic acid | 35°C for 2 h, removed moisture at 120°C | 97 | Isosorbide 3392 (OH), 1421 (OH), ISODO 2925 (CH2), 2856 (CH3), 1737 (C=O) |
|
[15] |
Cashew nut shell liquid (CNSL) | Heterogeneous AIER | DGEBA, citric acid, MWCNT | CA and CNSL mixed in ethanol stirred for 10 min, sonication | 92 |
|
|
[16] |
Linseed oil (LO) | Carboxylic acid | MWCNT, KMnO4 | Malenization of linseed oil at 210°C for 6 h continuously stirring | 95 | 1646 (-C=C- str) |
|
[17] |
Cashew nut shell liquid (CNSL) | Homogeneous carboxylic acid | DGEBA, citric acid, MWCNT | CA and CNSL mixed in ethanol stirred for 10 min, sonication | — |
|
|
[16] |
Tannic acid (TA) | Percarboxylic acid |
|
7 mL NaOH (0.5) 65°C, stirring for 1 h | — |
|
|
[18] |
Sesame oil–based polyurethanes | Percarboxylic acid | Sesame seed oil, H2O2, percarboxylic acid, formic acid, acetic acid, alcohol, orcein | 80°C–65°C for 1.5 h, separatory flask, cure with reagents | 94.4 |
|
|
[19] |
Vanillin | Carboxylic acid | Tri glycidyl ether of phloroglucinol (TGPh), diglycidyl ether of vanillyl alcohol (DGEVA), hexahydro-4-methylphthalic, methyl nadic anhydride (MNA) | Reaction at 35°C–70°C | — | 854, 904 (C-O-C) |
|
[20] |
Syringaldehyde | Hypochlorination (HC) | 4,4′-Diamino diphenylmethane, epichlorohydrin, tetrabutylammonium bromide, furfuryl-amine | 90°C for 2 days under N2 environment, cured at 120°C/2 h | — |
|
1006 (C-O-C str) | [21] |
Tung oil | Percarboxylic acid | 2-Hydroxy-2-methyl-1-phenyl-1-acetone, 2-benzyl-2dimethylamino-1-(4-morpholinphenyl) butanone | 6 h reaction time | — | FTIR=NR | FTIR=NR | [22] |
CNLS | Natural fiber–based epoxidation | Vitrimer, carbon fiber, citric acid, DGEBA | Mixture of CA, CNLS, DGEBA stirred for 10 min, cured at 690 kPa for 5 min | 97 |
|
|
[23] |
Guaiacol | Metal catalyzed |
|
125°C under N2 environment | — | 854,904 (C-O-C) |
|
[24] |
Magnolol | HC | 4,4′-diaminodiphenyl sulfone, DGEBA, benzyl triethylammonium chloride | Stirring at 80°C for 3 h under N2 environment | 92 |
|
|
[25] |
Resveratrol | AIER |
|
Reflux at 90°C at 2.5 h under N2 environment | — | 4530 (C-O-C) sharp peaks | 7000 (O-H) | [26] |
Epoxidized linseed oil (ELO) | Homogenous catalysis |
|
110°C for 2 h | — | FTIR=NR | FTIR=NR | [27] |
CSO | Through percarboxylic acid | Acetic acid, H2O2, H2SO4 | 55°C–70°C | 95 |
|
1720–1760 (C=O str) | [28] |
Jatropha oil | AIER, chemoenzymatic | Amine, acetic acid, amberlite IR-120, hydrogen peroxide | 24 h, 73°C | — |
|
|
[29] |
ELO | Carboxylic acid | Maleic anhydride, dipropylene glycol, 2-methyl imidazole | 105°C | — |
|
|
[30] |
Trans limonene oxide | AIER | Triethyl borane, polyethyleneimine, ethane-1,2-dithiol, azobis(isobutyronitrile) | 100°C, 24 h | 98 | NR | 1250 (C-O-C) | [31] |
VO | Through percarboxylic acid | Hydrogen peroxide, acetic acid/formic acid | 80°C, 3 h, cont. stirring | — | FTIR=NR | FTIR=NR | [32] |
Tannic acid | Ion exchange resin | Glycerol, curing agent | 600°C | 98 | FTIR=NR | FTIR=NR | [33] |
Tall oil (TO) | Chemoenzymatic, AIER | Acetic acid, hydrogen peroxide, montmorillonite K10, 4 (dimethyl amino) pyridine, amberlite IR-120, acetanhydride | Thermostatic temperature control (40°C), rotary evaporator |
|
|
|
[34] |
Castor oil | AIER, chemoenzymatic |
|
5 h stirring, curing for 6 h and 2 h at 150°C and 120°C | — |
|
|
[35] |
High oleic soybean oil (HOSO) | Bio-based, natural fiber–based | Cellulose nanocrystals (CNCs), azobisisobutyronitrile (AIBN), nitrogen | 72 h/90°C dryer at 40°C, polymerizations at 75°C, 72 h oven, curing for 24 h/100°C | — | — |
|
[36] |
Eugenol and 2,5 furan dicarboxylic acid (2,5 FDCA) | Heterogenous AIER | Sodium sulfite, triethylamine, sodium carbonate, ethyl acetate, tetrahydrofuran (THF), DGEBA, m-CPBA, N,N-dimethylformamide (DMF), methyl hexahydrophthalic anhydride (MHHPA) | Heating for 3 h at 25°C, rotary evaporator, 48 h heating at 40°C, curing at 170°C, 150°C and 130°C for 2 h | — |
|
|
[37] |
Eugenol | Percarboxylic acid |
|
Vacuum oven, 12 h and 3 days reaction, curing at 190°C and 150°C for 2 h | 92 |
|
|
[38] |
Soybean oil (SO) | Percarboxylic acid | Formic acid, acetic acid, sulfuric acid, H2O2 | Calorimetric reactor, 65°C | 20 increment | FTIR=NR | FTIR=NR | [39] |
2,5-Furandimethanol | AIER | IPDA, TBAB, oxalyl chloride, dichloromethane, sodium hydroxide, ethyl acetate and hexane, maleic anhydride, triethylamine, ECH |
|
— | FTIR=NR | FTIR=NR | [40] |
Epoxidized soybean oil (ESO) | Metal catalyzed | Methanol, boron trifluoride ethyl etherate, toluene and sodium hydroxide, ECH, tri ethylene tetramine (TETA), aqueous ammonia and fluoroboric acid, sodium dihydrogen phosphate | Reaction on water bath for 3 h at 70°C, curing at 140°C, 100°C and 60°C for 2 h | — | 3009 (C-H str) |
|
[41] |
Eugenol (4-allyl-2-methoxyphenol) | HC | α,α′-dichloro-p-xylene, dichloromethane, sodium sulfite and sodium hydroxide, N,N-dimethylformamide, 4,4′-diaminodiphenyl methane (DDM) as curing agent, m-CPBA | 6 h at rt, 3 days at 60°C and 7 days at rt, vacuum at 40°C and 80°C | 38 | — |
|
[42] |
Eugenol | Percarboxylic acid | m-CPBA, triethylamine, phosphorus oxychloride, 2,2’-(ethane-1,2-diylbis(oxy))bis(ethan-1-amine), DGEBA, meta-xylenediamine (MXDA) | 16 h and 24 stirring at rt | 33–36 | FTIR=NR | FTIR=NR | [42] |
Eugenol | Percarboxylic acid |
|
6 h dryer at 120°C, 4 h stirring at rt |
|
|
[43] | |
Acrylated epoxidized castor oil (AECO) | Homogenous catalysis | DGEBA, acrylic acid | 70°C, vacuum oven | — |
|
|
[44] |
ESO | HC | KOH, HCl, ethyl ethyl ketone, isophorone diisocyanate (IPDI) | Different T for different steps (70°C, 80°C, 98°C) | 95.3 | 3200–3600 (O-H str) | 823 (polyol curve) | [45] |
Ether based epoxidized cardanol (EBEC) and ester epoxidized itaconic acid (EIA) | Homogenous percarboxylic aid | Tetra butyl ammonium bromide (TBAB), starch, acetone and toluene | 100°C for 24 h, for 12 h at 80°C | — |
|
Epoxidized ethanoic acid grafted successfully | [46] |
Rosin | Homogenous catalysis | m-CPBA, DGEBA, isophorone diamine (IPDA), KOH, dichloromethane, ECH | 10 h/36 h 90°C, 80°C/1 h and stirring/6 h, 160°C and 100°C curing/2 h | — |
|
|
[47] |
Itaconic acid | Homogenous percarboxylic aid | Allyl bromide, N,N dimethyl formamide acetone, potassium carbonate, dichloromethane, m-CPBA, MHHPA | 12 h at rt, 7 h 40°C, curing 180°C, 150°C, 80°C for 2 h | 60 |
|
|
[48] |
|
Heterogeneous catalysis | THF, DGEBA, Jeffamine D400, (IPDA) | 170°C for 30 min, 120°C for 5 h | 3030 | FTIR=NR | FTIR=NR | [49] |
Rosin acid and eugenol | Heterogeneous catalysis | ECH, (HHPA) and abietic acid mCPBA, 1-ethyl-4-methylimidazole (EMID), acetic/maleic anhydride | Vacuum evaporation, 4 h reflux at 85°C | — |
|
1800–1818 (C=O str) | [50] |
Palm oil | Percarboxylic acid | Formic acid, acetic acid, H2O2 | Stirring at 45°C |
|
|
|
[51] |
2,5-bis(hydroxymethyl)Furan | Metal base epoxidating | Tetrabutylammonium hydrogen sulfate (TBAHS), furfuryl glycidyl ether (FGE) | 1 h stirring for 50°C, rotary evaporator |
|
|
[52] | |
Itaconic acid | Homogenous catalysis through percarboxylic acid |
|
120°C 2 h vacuum oven for 5 h at 90°C, 48 h at 30°C and 3 h mixing at 25°C, 12 h refluxing, curing at 190°C and 120°C/2 h |
|
1740 (C=O) |
|
[53] |
Cinnamic acid | AIER |
|
Rotary evaporator, 12 h and 48 h stirring at rt, 24 h stirring at 50°C | 96.4 | FTIR=NR | FTIR=NR | [54] |
Epoxy curing requires either hardener or photoinitiator (PI) to make desired changes in polymer. Epoxy is usually cured by two approaches having different polymerization mechanisms [61], i.e., either by heat (thermal curing) or by light (photocuring). Epoxides belong to a special class of cyclic ethers which easily polymerize through ring opening reactions in the presence of a reagent. In thermal polymerization, the reagent is a major ingredient of the recipe, termed as hardener, whereas in photochemical reactions, the reagent is a minor ingredient of the recipe, termed as PI. Cured epoxy resins have excellent adhesive behavior, mechanical strength, electrical insulation, and chemical resistance [61].
4.1. Thermal Curing
Thermal curing mechanism utilizes a two-component system, i.e., epoxy and hardener (Table 3) [62]. Typical examples of commonly used hardeners are amines, anhydrides, acids, thiols, phenols, or alcohols [63]. The choice of hardener for polymerization of epoxies is critical as its structure determines thermomechanical behavior of composites. Bifunctional reagent (hardener) gives linear polymeric structure, i.e., low cross-linking ratio, whereas trifunctional hardener produces three-dimensional cross-linked network of polymers. Among various curing agents, amines are most popular and common ones for epoxies because they have the capability of cross-linking both as bifunctional as well as trifunctional hardener [64]. For thermal curing, microwave radiation technique (MWR) has been reported with steady effectiveness and eco-friendliness [65, 66]. It effectively works for polar compounds and speeds up the reaction. MWR heats sample equally, hence reported for food preservation from antimicrobial activates [65, 66]. Thermally cured epoxy composites are most commonly used materials with significant industrial importance. DGEBA is a popular epoxy monomer which is cured by various curatives, but in two-component systems, it is mostly amines, i.e., DETA (Scheme 1). Anhydrides like PA, second most important curing agents for epoxies, form more stable bond with epoxies than amines. Hardener upon reaction with epoxy releases energy (exothermic reaction) that affects quality of product, and almost 100% cured material may be obtained.
Hardener | Structure | Composites | Ref. |
---|---|---|---|
Amines (50%) | ![]() |
Epoxy composites | [67] |
Polyamides (14%) | ![]() |
Multifunctional superhydrophobic composites | [68] |
Anhydrides (15%) | ![]() |
Bio-composites | [69] |
Polymercaptan and polysulphides (14%) | ![]() |
Nanocomposites | [70] |
Urea formaldehyde (4.5%) | ![]() |
Nanocomposite foams | [71] |
Percarboxylic polyesters (22%) | ![]() |
Fire retardant recyclable and bio-based composites | [72] |
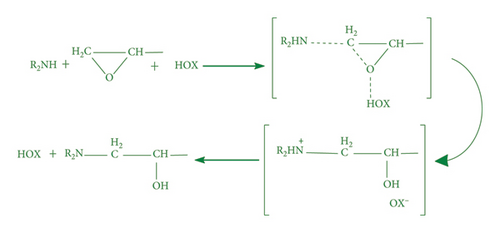
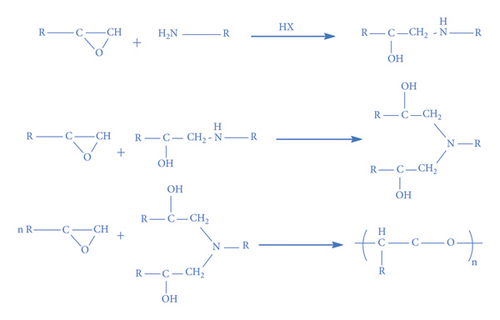
4.2. Photocuring
Photo-induced epoxy polymerization is carried out in the presence of PI that generates active centers to initiate polymerization. These reactions follow either cationic or anionic curing protocols. Since this curing system consumes only epoxy to generate matrix, it is termed as one-component curing [73]. PI absorbs UV light to generate active species. In cationic curing, two types of mechanisms (activated chain end mechanism and activated monomer mechanism) are involved, where protonated epoxide attacks on the other epoxide ring for polymerization (Scheme 2) [74].

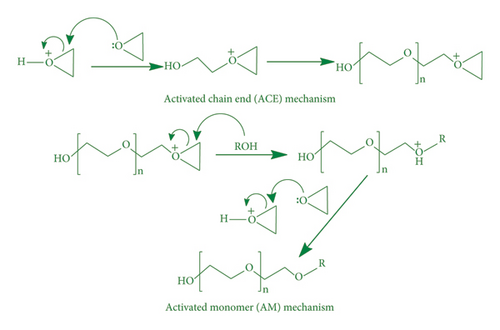
Due to noticeable increase in environmental issue sensitivity during last decades, petrochemical-based epoxies are becoming crucial. Polymer materials with bio-based origin have gained much attention because of their feasibility to replace petroleum-based materials. Epoxy synthesis from bio-based oils has taken significant attention in various fields (Figure 3) because of nontoxic, economical, and renewable competences. Epoxy adhesives have wide range of applications in industry, i.e., construction [75], electronics [76], automotive [77], and aerospace [78, 79]. Bio-resourced epoxy foams are extensively used for thermo-insulating and dye-decontaminating applications [33, 80]. Epoxy resins are used for coating applications on commercial level, divided in two categories: structural coatings and protective coatings. High biomass content epoxy resins have also been prepared for green coating and composite applications [27]. Recently, radiation curable coatings have been growing fast because of energy efficient and environment friendly coatings [81]. In biomedical field, epoxy resins have been utilized in food and human clinical applications [82–84]. Bio-based epoxy (BBE) paints and coatings have been reported for anti-corrosive properties [85, 86]. Cross-linked epoxy polymers are high-cost materials in comparison to other resins. Combination of properties or high performance/engineering properties is incorporated into final products to realize added value of epoxy resins [87]. Several epoxy products on commercial level are prepared with a mixture of epoxies in order to attain desired processing and properties. In order to attain higher Tg, modulus, or stiffness, epoxides with higher functionality are required. Epoxides are available in market for various applications from low-cost simple adhesives to highly engineered conductive adhesives, to high-strength structural composites. A wide range of interesting properties of epoxides could be obtained at a reasonable cost. Researchers have reported various synthetic methods (Table 1) for BBEs with specific properties.
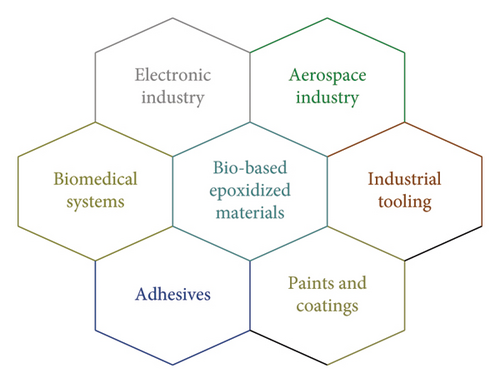
5. Epoxidation Strategies
- •
Radical epoxidation (O2 with catalysts, molecular oxygen)
- •
Single oxygen donor/nonradical process (peracids, H2O2, and hydroperoxides)
In bio-based materials, mostly VOs are used for epoxidation. It is important to note that these oils mostly have unsaturation in certain amounts on which epoxidation is carried out to attain epoxidized materials. Route adopted for epoxy synthesis decides the stereochemistry of obtained product. For instance, methyl oleate undergoes nonradical epoxidation and forms cis epoxide product. On the other side, the route of radical epoxidation gives both the cis and trans epoxidized products [106]. Hydrogen peroxide was majorly utilized for many epoxidation reactions because it is a relatively economical oxidant, easy to store/handle, and gives only water as by-product. Few epoxidation protocols (reagent, reaction conditions, their outcomes, and applications) for bio-based materials have been studied in Table 4. Various approaches for epoxidation of natural oils have been discussed below.
Sr. # | Precursor | Reagents | Reaction conditions | Outcomes | Applications | Ref. |
---|---|---|---|---|---|---|
1 | Cottonseed oil (CSO) | Glacial acetic acid, aqueous H2O2, H2SO4 | Variable temperature (from 55°C to 70°C) |
|
As plasticizer and polymer stabilizer | [28] |
2 | Epoxidized soybean oil (ESO) |
|
Different temperature for different reaction steps (70°C, 80°C, 98°C) |
|
As stabilizer and plasticizer. In pigments, PVC, and dispersing agent | [88] |
3 | ESO |
|
30 min in heating at 50°C, ∼10 mm Hg reduced pressure curing at 190°C for 3 h and 130°C for 1 h |
|
In cutting oils and lubricants | [89] |
4 | (ELO) |
|
Isothermal curing (110°C/2 h) |
|
Agricultural resources, composites | [27] |
5 | EBEC and EIA | (TBAB), starch, acetone, and toluene | Vacuum dryer at 100°C for 24 h, for 12 h at 80°C |
|
Biopolymers for industrial scale plastic applications | [46] |
6 | Rosin | m-CPBA, DGEBA, IPDA, KOH, dichloromethane, ECH | 10 h reaction, 36 h heating at 90°C, 80°C for 1 h and stirring for 6 h, 160°C and 100°C curing temperature for 2 h |
|
Renewable co-additives | [47] |
7 | TO | Acetic acid, hydrogen peroxide, montmorillonite K10, 4 (dimethyl amino) pyridine, amberlite IR-120, acetanhydride | Thermostatic temperature control (40°C), rotary evaporator |
|
Polyurethane processing | [34] |
8 | AECO |
|
70°C, vacuum oven | ➢ Ea (69–61 KJ/mole and 63 to 59 KJ/mole) | Nanocomposites | [44] |
9 | Eugenol |
|
43193 h | ➢ Highest yield (70%–80%) | As bioactive molecules | [90] |
10 | Trans limonene oxide | Triethyl borane, polyethyleneimine, ethane-1,2-dithiol, azobis(isobutyronitrile) | 100°C, 24 h |
|
For network polymers | [31] |
11 | Jatropha oil | Amine, acetic acid, amberlite IR-120, hydrogen peroxide | 24 h, thermostatic temperature (± 1°C) |
|
Bio-composite materials | [29] |
12 | VO | Hydrogen peroxide, acetic acid/formic acid | — |
|
For synthesis of polymers, glycol, alcohol, poly esters | [32] |
13 | ELO | Maleic anhydride, dipropylene glycol, 2-methyl imidazole | 105°C |
|
Coatings, adhesives and composites | [30] |
14 | 2,5-Furandimethanol | IPDA, TBAB, oxalyl chloride, dichloromethane, maleic anhydride, triethylamine, ECH ![]() |
5 h reaction at 65°C, 7 days stirring at rt and 12 h stirring at 30°C, rotary evaporator, 60°C and 90°C curing for 2 h, 120°C curing for 10 h |
|
Plasticizers | [40] |
15 | 2,5-bis(hydroxymethyl)Furan |
|
1 h stirring for 50°C, rotary evaporator |
|
Renewable thermosetting polymers | [52] |
16 | TA | Glycerol, curing agent | 600°C |
|
Thermo-insulating applications, epoxy foams | [33] |
17 | Itaconic acid |
|
12 h mixing at rt, 40°C temperature for 7 h, rotary evaporator, curing at 180°C, 150°C, 80°C for 2 h |
|
In coatings, adhesives and electronic materials | [48] |
18 | Castor oil |
|
5 h stirring, curing for 6 h and 2 h at 150°C and 120°C respectively | ➢ Reactive, sustainable and green diluents | For structural and coating application | [35] |
19 | HOSO | CNCs, AIBN, nitrogen |
|
|
— | [36] |
20 | Limonene |
|
For 4 h and 1 h curing at 120°C/180°C and 140°C/190°C, 1 × 10−1 mbar reduced pressure, rotary evaporator, 16 h heating at 60°C |
|
— | [91] |
21 | Eugenol |
|
6 h dryer at 120°C, 4 h stirring at rt |
|
Flame retardant and powder materials for some applications | [43] |
22 | Eugenol (4-allyl-2-methoxyphenol) | α,α′-dichloro-p-xylene, dichloromethane, sodium sulfite and sodium hydroxide, N,N-dimethylformamide, DDM as curing agent, m-CPBA | 6 h at rt, 3 days at 60°C and 7 days at rt, vacuum at 40°C and 80°C |
|
Industrially well-established process | [42] |
23 | Eugenol |
|
16 h and 24 stirring at rt |
|
Flooring and paving application | [92] |
24 | Gallic acid |
|
15 h and 48 h mixing at rt, vacuum evaporation at 80°C |
|
Fire resistant application | [93] |
25 | Itaconic acid |
|
120°C for 2 h,Vacuum oven for 5 h at 90°C, 48 h at 30°C and 3 h mixing at 25°C, 12 h refluxing, curing at 190°C and 120°C for 2 h |
|
Fire resistant application | [53] |
26 | ESO | Methanol, boron trifluoride ethyl etherate, toluene and sodium hydroxide, ECH, briethylene tetramine (TETA), aqueous ammonia and fluoroboric acid, sodium dihydrogen phosphate | Water bath for 3 h at 70°C, curing at 140°C, 100°C and 60°C for 2 h |
|
Coatings, paints, structural materials | [41] |
27 | Cinnamic acid |
|
Rotary evaporator, 12 h and 48 h stirring at rt, 24 h stirring at 50°C |
|
Perfumes, food additives, pharmaceutical applications | [54] |
28 | Eugenol and 2,5 FDCA | Sodium sulfite, triethylamine, sodium carbonate, ethyl acetate, THF, DGEBA, m-CPBA, DMF, MHHPA | Heating for 3 h at 25°C, rotary evaporator, 48 h heating at 40°C, curing at 170°C, 150°C and 130°C for 2 h |
|
— | [37] |
29 | 2,5 FDCA | MHHPA, 2-ethyl-4-methylimidazole, ECH, TPA, m-CPBA, poly(propylene glycol)-bis(2-aminopropyl ether) D230, allyl bromide |
|
|
Substitution with petrochemical TPA, in thermoplastic synthesis | [94] |
30 |
|
|
170°C for 30 min, 120°C for 5 h |
|
Coatings | [49] |
31 | Rosin acid and eugenol |
|
Vacuum evaporation, 4 h reflux at 85°C |
|
Engineering polymers | [50] |
32 | Eugenol | 1,4-Dibromobutane, zinc acetylacetonate hydrate, mCPBA, K2CO3, Na2SO3, KI, SA·MgSO4 | Vacuum oven, 12 h and 3 days reaction at 190°C and 150°C for 2 h |
|
Preparation of vitrimers, bio-based polymer synthesis, Reconversion of thermoset polymers | [38] |
33 | Palm oil | Formic acid, acetic acid, H2O2 | Stirring at 45°C |
|
Biolubricant, coating, polymer industry, plasticizer | [51] |
34 | SO | Formic acid, acetic acid, sulfuric acid, H2O2 | Calorimetric reactor, 65°C |
|
Plasticizers, lubricants | [39] |
35 | Herb roots |
|
Stirring for 30 min, dissolve epoxy + PDM + PDD, curing 80°C-140°C |
|
Thermosetting coating | [95] |
36 | TA |
|
7 mL NaOH (0.5) at 65°C, stirring for 1 h |
|
Eco-friendly coating material | [96] |
37 | Vanillin | TGPh, DGEVA, hexahydro-4-methylphthalic, MNA | Reaction temperature 35°C–70°C |
|
Thermosets for space, aerospace, or naval industry. | [20] |
38 | Phytic acid-tyramine salt | Ammonium polyphosphate | Deionized water as solvent |
|
Flame retardant for plastic-wood composite | [97] |
39 | Isosorbide | Octanoic acid, palmitic acid, oleic acid, titanium (IV) butoxide, myristic acid | Heated at 35°C for 2 h, removed moisture content at 120°C | ➢ High plasticizing and thermomechanical properties | Plasticizer for the application of PVC | [98] |
40 | Linseed oil (LO) | MWCNT, KMnO4 | Malenization of linseed oil at 210°C for 6 h continuously stirring | ➢ 99.9% protection against corrosion | Corrosion prevention for mild steel | [99] |
41 | Cashew nut shell liquid (CNSL) | DGEBA, citric acid, MWCNT | CA and CNSL mixed in ethanol stirred for 10 min, sonication |
|
As anti-corrosive | [16] |
42 | Castor oil |
|
80°C for 1 h, rotary evaporation was used to remove 2-butanone, stirring at 60°C for 8 h |
|
Coating industry | [100] |
43 | Syringaldehyde |
|
90°C for 2 days under N2 environment, cured at 120°C/2 h |
|
Fire-safe applications | [21] |
44 | Castor oil |
|
Stirring at 40°C/10 min, maintained pH 7 |
|
— | [101] |
45 | Salinized natural diatomite |
|
Mixture was heated at 50°C for 30 min |
|
— | [102] |
46 | CNLS |
|
Mixture of CA, CNLS, DGEBA stirred for 10 min, cured at 690 kPa for 5 min |
|
As repairing material | [23] |
47 | Tung oil |
|
6 h reaction time |
|
LED UV-coating | [22] |
48 | Guaiacol |
|
125°C under N2 environment | ➢ Flame retardant | — | [24] |
49 | Magnolol |
|
Stirring at 80°C for 3 h under N2 environment |
|
Cutting-edge applications | [25] |
50 | Resveratrol |
|
Reflux at 90°C at 2.5 h under N2 environment |
|
Aerospace industry | [26] |
51 | Protocatechuic acid |
|
Stirring at r.t for 5 days | ➢ High CF sizing (56%) | As sizing agent | [103] |
52 | Linseed oil |
|
Stirring at r.t |
|
Optical materials, casting, encapsulation, epoxy composites | [104] |
5.1. Hypochlorination
HC of olefins is the most primitive process for epoxy monomer synthesis, on a small scale [107]. DGEBA has been synthesized from bisphenol-A and epichlorohydrin: chloro-addition of propylene produced allyl chloride which upon HC gave epichlorohydrin [108]. However, this method has not been found suitable for large-scale production as dehydrohalogenation and side product formation affect % yield [109]. Other researchers have prepared DGEBA from glycerol and epichlorohydrin [110]. Compared to the former preparation method, higher selectivity (93%) has been reported with minimum side products. However, in DGEBA synthesis, 67% of BPA is derived from fossil fuel.
5.2. Epoxidation Through Peroxy Acids
HC method failure regarding high yield on industrial level has brought in situ generated peroxy acid method in industry [106]. Reaction mechanism is presented in Scheme 3.
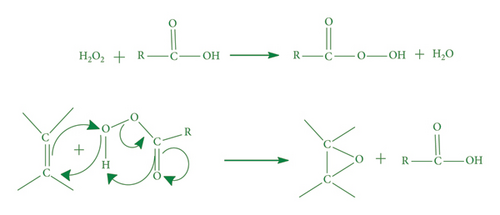
It was observed that sometimes peroxy acids require catalyst. Major peroxy acid oxidants are peracetic acid and performic acid with H2O2 (as oxygen donor), where the former requires catalyst and the latter does not [111]. Unsaturated fatty acids do not show any reaction with H2O2 in absence of organic peracids because peracids are responsible for oxygen transfer to oils [112].
5.2.1. Homogeneous Catalyst
Inorganic acids, e.g., HCl, HNO3, H2SO4, or H3PO4, work as catalyst in peracetic acid epoxidation [113]. However, these acids have the drawbacks of low epoxy content and nonselectivity of final material. Highly strained epoxy group undergoes ring opening and side reactions that is hydroxyl esters, dimer, and diol formation in the presence of acid (Scheme 4) [114]. Ninety-one percent epoxy yield has also been reported from cyclohexene and peroxy acids prepared by catalytic (Fe-N/C) oxidation of iso-butyraldehyde in air or O2 [115].
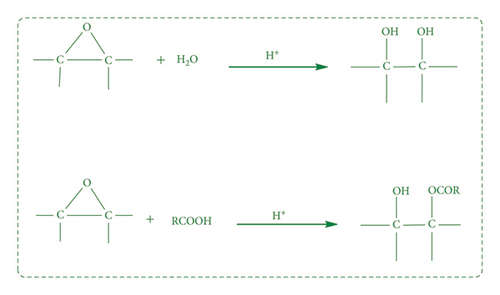
On large scale, peracid handling is very difficult and hazardous because of their instability and explosive nature in high concentrations. The acid used in reactions must be removed from products or neutralized because it corrodes the equipment and causes many health and environmental issues [116]. Hong et al. [117], reported the optimized conditions for epoxidation process of Jatropha curcas oil for in situ generation of peroxy formic acid (Scheme 5). Seventy percent yield with 80.4% oxirane conversion was found at 45°C for 2 h, having molar ratios of formic acid:oil and H2O2:oil as 2:1 and 12:1, respectively.
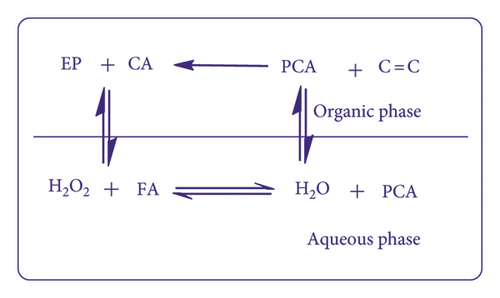
Epoxidation of SBO was performed by in situ peroxy-formic acid generation with hydrogen peroxide and formic acid in the presence of inorganic sulfuric acid as catalyst. The optimized conditions for the reaction were checked by varying mole ratio of hydrogen peroxide (1, 1.5, 2), temperature (50°C, 60°C), and time (2 h, 4 h). Thirty-eight percent yield and 2.86% OOC were reported within 50°C–60°C for 4 h. Experimental analysis revealed the low epoxide yield with some side products. It was concluded that there is longer time required for epoxidation reaction [118].
Nahor oil is nonedible, easily available feedstock with high iodine value and bio-lubricant for chemical industries. Dinda et al. [119] worked on Nahor oil epoxidation by in situ peracetic acid generation in batch reactor. The reaction was performed at 60°C for 5 h in the presence of H2SO4 and 72% yield was obtained. Drawbacks of this process were negligible mass transfer resistance and increased glycol formation. In 2017, epoxidation of Nahor oil was again carried out with formic acid, acetic acid, propionic acid, and Amberlite IR120. It was observed that formic acid use is better than acetic and propionic acid. Glycol was also formed as by-product in case of formic acid with H2SO4 [120]. Ion exchange Amberlite was found best from all other carboxylic acids with 70% yield. Glycol was also formed as by-product in case of formic acid with H2SO4 [120].
Researchers reported the epoxidation of economically inexpensive and efficient used/waste cooking oil having highly unsaturated content. The mineral acids HCl, HNO3, and H2SO4 were utilized in this process as homogeneous catalysts. Conventional process was performed for in situ peracetic acid generation in double bond oxidation. For sulfuric acid (2%) catalyst, 20% oxirane conversion, 3.1% oxygen content, and 74.9% conversion of iodine value were obtained for 5 h at 60°C higher than other used acids. Although less epoxidation was concluded in this method, higher temperature could reduce selectivity or initiate the ring opening reaction [121].
Crude oleic acid epoxidation was carried out by in situ preparation of peroxy formic acid with acid catalyst (H2SO4). In the presence of acid, highly reactive oxirane ring opens and undergoes side reactions, i.e., synthesis of α-glycol or diol. It was investigated that low concentration of formic acid should be used as its high amount in in situ generation decreases the yield. It was also studied that maximum yield with formic acid could be attained as compared to acetic acid [122].
Comparative study of peracetic acid and performic acid has been reported [123]. Stoichiometric amounts of SBO, formic/acetic acid, and hydrogen peroxide were taken as 1:0.5:2, 1:0.5:1, and 1:0.5:0.5 for the synthesis with constant temperature (50°C). The reaction time was kept at 2, 4, and 6 h as per requirement. Formic acid was proved to be effective than acetic acid for high yield and oxirane contents. Moreover, more reaction time and high concentration of hydrogen peroxide are required for acetic acid. The calculated/estimated optimized conditions for the reaction were 2 mol of hydrogen peroxide with the time of 6 h giving 98% yield and 7.45% oxirane contents.
Jalil [124] has also worked in 2019 on epoxidation of palm oleic acid by performic acid (in situ generation). Most stable and high yield (85.6%) of epoxide ring was obtained by optimized reaction conditions, i.e., 55°C, 200 rms speed, and 1:1:1.5 ratios of oil, formic acid, and H2O2.
In 2019, epoxidation of CSO was carried out on reflux condenser using RBS [28]. CSO was heated on condenser at 55°C. After reaching the required temperature (55°C), sulfuric acid (0.8 mL) and acetic acid (9.8 mL) were added. 58 mL hydrogen peroxide was poured drop by drop and temperature was increased (70°C) for 8 h. Synthesized product was separated by solvent extraction process. Ninety-five percent yield was obtained. These epoxidized oils were used to make polymers of higher stability and 1 MPa tensile strength.
5.2.2. Heterogeneous Catalyst (Acid Ion Exchange Catalyst)
Nowadays, VOs in major proportion are being converted into epoxidized materials through conventional methods using peracids. However, this approach has diverse impediments such as explosiveness and instability of peracids, epoxy ring opening, less selectivity, and corrosion because of acidic by-products [125, 126]. Therefore, ion exchange catalytic epoxidation was introduced. One such popular catalytic method for epoxidation is ion exchange process that has the advantage of minimum oxirane decomposition. Neutral pH and no solvent are required for acidic ion exchange method [127]. AIERs are heterogeneous catalysts introduced in place of acidic inorganic catalysts to improve selectivity and yield of epoxide products. AIER is an insoluble catalyst of gel type with small polymer beads of yellowish color. When carboxylic acid (HCOOH/CH3COOH) reacts with H2O2, the peracid forms and interacts with the catalyst by entering its pores. Thus, peroxy acid (formic acid or acetic acid) fills the pores of AIER after contact. Low epoxy ring degradation was observed with AIER process because gel type AIER structure blocks the interruption of triglycerides [128]. The experimental work for ion exchange resin is similar to homogeneous catalyst, i.e., ion exchange catalyst is added in place of H2SO4.
Desalegn Zeleke and Ayana [129] reported Vernonia oil epoxidation with the help of ion exchange Amberlite catalyst. They obtained 78% conversion with minimum epoxide ring opening. In situ performic acid was generated by AIER and utilized as oxidant for the reaction. This epoxidized oil has its applications in preparation of bio-lubricants.
CSO was epoxidized using biochar catalyst and compared with VPOC 1800 (cationic resin) [130]. Both catalysts have excellent selectivity. However, VPOC exhibited 34% yield and relatively better reusability while biocatalyst showed 14% yield with higher activity. Two round neck flasks were taken in which 100 g CSO, 22 g catalyst and 16 g acetic acid. The mixture was stirred and heated at 65°C. After some time, H2O2 was added slowly and reaction was performed for 300 min. Both the catalysts were epoxidized with the same procedure.
Researchers [131] have reported epoxidation of cottonseed oil and oleic acid using cation exchange catalyst Amberlite IR120 for in situ generation of per-propionic acid or peracetic acid. The reaction was conducted both in microwave irradiation and conventional heating. Acetic acid was found more efficient for epoxidation than propionic acid while epoxidized CSO gives better and stable yield compared to oleic acid. Microwave heating gives better results/yield in the absence of catalyst. Microwave process is beneficial for mixing, recycling of catalyst, and reducing mechanical wear and mass transfer limitations [131]. In microwave setup, RBS was connected with turbine engine at 1200 rpm stirring. Calculated amounts of oil and carboxylic acid were sent into the reactor and H2O2 was added after that within 1 min. After adding all the reagents, heat exchanger was switched on and the reaction was performed completely.
Waste cooking oil was epoxidized both with the homogeneous mineral acid catalysts (H2SO4 and H3PO4) and heterogeneous ion exchange catalyst (Amberlite IR120). In situ peracetic acid was generated with both the catalysts at 65°C–70°C. By sulfuric acid catalyst, 81% conversion was obtained with lower selectivity. For the ion exchange resin, 55% conversion with 74% selectivity of epoxide was investigated [132]. Amberlite 39 was used as catalyst in place of homogeneous ion exchange amberlite IR120 catalyst for the first time [133]. Sunflower oil was epoxidized with mole ratios 1:0.2:0.11 of oil, acetic acid, and hydrogen peroxide, respectively. Under these conditions, 0.98 selectivity of epoxidized product for 240 min and 87% oxirane yield was acquired. Amberlite 39 was a promising deterioration resistant catalyst with 10-time reusability, low pore size, and low surface area contribution. Sacha inchi oil due to a number of double bonds has also been converted into epoxy by H2O2 treatment, in the presence of Na2WO4, benzyl-dimethyl-stearyl-ammonium chloride hydrate, and H3PO4 as catalyst. The reaction was maintained for 8 min at 60°C with 0.85 catalytic activity and 82% yield [134].
5.3. Chemoenzymatic Epoxidation
Enzyme catalysts were preferred for more environment friendly and avoiding side product processes. The immobilized Candida antarctica lipase is extensively utilized as enzyme catalyst and added step wisely to improve epoxidation reaction. It is better alternative to chemical process for epoxidation, but low stability under reaction conditions is the main limitation of the enzymatic method [135]. It was investigated that enzyme activity may be lost in bio-catalyzed reactions due to elevated temperature or higher H2O2 concentrations. However, Candida antarctica B lipase showed retained stability above 50°C in recent studies, although decomposition of H2O2 is unfavorable for it. At higher temperatures, catalytic activity of enzymes is decreased due to nonaccessibility in the inner regions [136]. Enzymatic epoxidation provides selective properties to the obtained products and flexibility of chemical reactions [137]. Medium temperature is required in this method, and therefore it also has the advantage of heat safety. Björking et al. were the first who reported chemoenzymatic-based epoxidation results. Later, more acceptable procedures were introduced to make enzymes better alternatives for oil-based transformations [138]. Ursula et al. investigated that lipase catalysts show excellent activity and stability in epoxide formation reactions. They have also the ability to reuse many times [105].
In 2016, scientists worked on activity of different catalysts for epoxidation of SBO [139]. They used H2SO4, AIER (Zeolite 325, Amberlite 15, and Zeolite Y), and enzymatic catalyst (Novozyme 435). They studied that enzymatic catalyst showed excellent activity (increased selectivity) with highest epoxide value (0.345 mol/100 g), then H2SO4 (0.323 mol/100 g), and ion exchange resins (0.277 mol, 0.260 mol, 0.020 mol/100 g) in the end. The highest unsaturation conversion was obtained for Novozyme 435 (99.7%). 24 h reaction at 25°C was performed for enzymatic epoxidation.
Bajwa et al. [140] carried out three different lipase-mediated chemoenzymatic epoxidation reactions of Karanja oil using three different solvents (toluene, hexane, and benzene). Seventy-two percent and 82% epoxide conversion were obtained for benzene and toluene, respectively, by Novozyme 435 catalyst without side products. Chemoenzymatic epoxidation is a green and clean technology with four run reusability. It is expecting 100% selectivity of this method for future. One reason for high selectivity was the absence of sulfuric acid that causes ring opening of epoxy. Moreover, relatively fewer amounts for hydrogen peroxide are required compared to chemical epoxidation. To further improve the chemoenzymatic method, Bhalerao et al. [141] have reported lipase-mediated (Novozyme 435) epoxidation of SBO. This process was performed in ultrasonic irradiation to reduce the reaction time and 91.22% oxirane conversion was calculated within 5 h. The enzyme lipase exhibited remarkable stability, later recovery, and six times reusability for epoxidation. Optimized conditions (4 wt. % enzyme, 40°C, and 200 rms stirring speed) for the reaction were investigated. When conventional enzymatic method was compared with ultrasonication method, three significant results were obtained. For the conventional method, 27% yield in 5 h and 85% in 20 h was obtained with stirring. By ultrasonication process, 91% yield with stirring, 45% yield without stirring and significant rate increment was investigated. Ultrasound method is more energy efficient because only 11.44 kJ/g per unit wt. was needed as compared to conventional process (21.02 kJ/g).
The influence of various parameters on VO epoxidation by enzymatic method was reviewed by Sustaita-Rodriguez et al. [142]. They investigated enzyme inactivation with increasing temperature and increasing amount of hydrogen peroxide. Therefore, their amounts should be carefully added to avoid deactivation of enzyme catalyst. Sapindus mukorossi fatty oil was epoxidized by Candida lipase enzyme [143]. They observed the effect of reaction temperature, time, H2O2 addition, and different solvents on the epoxidized product. Eighty-three percent yield was obtained with optimum conditions of 35°C for 2 h, 30°C for 6 h, and 15 wt % enzyme loading. Shorter time was needed as compared to Novozyme 435 catalyst at low temperature that gave similar conversion. Among various organic solvents, n-hexane was the only one that increased the oxirane value. In 2019, group of researchers reported enzymatic epoxidation of SBO using three different lipase catalysts and checked their stability. They observed that Aspergillus oryzae lipase exhibited excellent conversion with maximum stability (Table 5) [144].
Substrate | Catalyst | Time (h) | Temp (oC) | Solvent | C=C/H2O2 mole ratio | Stirring (rmp) | % yield | Ref |
---|---|---|---|---|---|---|---|---|
SBO | Novozyme 435 | 24 | 25 | Toluene | 1:2 | NR | 82.6 | [139] |
Karanja oil | Novozyme 435 | 8–9 | 30 | Toluene | 1:1.5 | 400 | 80–84 | [140] |
SBO | Novozyme 435 | 5 | 60 | Toluene | 1:1-2 | 200 | 91.22 | [141] |
TOFA | Novozyme 435 | 11 | 40 | Not specified | 1:1/1.1/1.2 | 600 | 74.4 | [143] |
SBO | Aspergillus oryzae lipase | 24 | Rt | Octanoic acid CHCl/sorbitol | 1:0.5–2.5 | 500 | 96.8 | [144] |
Oleic acid | Lipase | NR | 50 | 2-Propanol | 1:2 | NR | NR | [145] |
5.4. Metal-Catalyzed Epoxidation
The use of metal catalysts is more advanced process which improves epoxy contents and epoxidation performance. To improve latest existing technology, scientists and researchers are always in continuous struggle and search to find new methods and techniques. Many workers and their coworkers have contributed to improve efficiency and oxirane contents of epoxidation processes. An ideal catalyst should not only have best performance in reactions but also: (1) easy and cheap to form, (2) robust, stable and usable, (3) to be used for many types of substrates, versatile, etc. [146]. Metal-catalyzed materials are typically used as catalysts for epoxidation. Low oxidation potential and high Lewis acidity of metals in their highest oxidation states make them superior catalysts which shows following order in activity: Mo > W > Ti > V [147]. The use of peracid is unfavorable for health and environment due to safety requirements in handling and wastage of considerable amounts of acid. Thus, it has dealt in recent papers to overcome these drawbacks using more efficient and sustainable technologies and compounds.
For radical pathway of epoxy synthesis, molecular oxygen (O2) is used as oxygen donor. Aldehyde is utilized as co-oxidation in epoxide synthesis process. High oleic or methyl oleate materials were epoxidized obtained from different VOs [148]. Cumene-O2 catalyst with Cu-mediated materials was used for epoxidation process. Single-pot reaction was performed at 100°C. The selectivity and conversion results against two different catalysts are shown in Table 6.
Substrate | Time (h) | Catalyst | Selectivity (%) | Conversion (%) |
---|---|---|---|---|
|
7 | CuO/PVPy | 89 | 96 |
6 | CuO/Al2O3 | 78 | 99 | |
|
9 | CuO/PVPy | 80 | 81 |
6 | CuO/Al2O3 | 79 | 98 | |
|
9 | CuO/PVPy | 82 | 99 |
7 | CuO/Al2O3 | 79 | 95 |
VOs and their derivatives were epoxidized using silica-based complex catalyst [149]. This catalyst exhibited highest pore volume, surface area, peroxide value, and excellent activity with 5 times recyclability. 92.76% yield was gained for methyl linoleate at rt. High yield of linseed oil and olive oil was also successfully obtained at rt. 0.3 mL of oil with 12.5 mL DCM was poured in RBS and stirred at rt. The reaction was performed for 1 h after adding catalyst. The obtained solid was filtered and washed. DCM was removed using vacuum evaporator and epoxide product was obtained. Palm oil–derived oleic acid was used for epoxy synthesis with performic acid [150]. Eighty-six percent oxirane conversion of oleic acid has been reported with sulfuric acid as catalyst at 90°C for 10 h. This work involved synthesis of dihyroxysteric acid by hydrolysis of palm oil–derived oleic acid, for cosmetic applications.
Methyl oleate–based epoxide was synthesized using molecular oxygen with aldehyde reductant (Mukaiyama reaction). The reaction was performed in highly efficient and safer continuous flow process. Improved productivity, better mass transfer, and high selectivity (> 99%) were achieved through this method [151]. Only in 4 min, 99% selectivity was obtained at rt with ∼25/74% cis/trans ratio. A special reactor was used in which reactant solution of 50 mL was loaded. Oxygen and organic phase were fed in reactor using T-mixer. 5 bar pressure was applied.
FAMEs were epoxidized using niobium mesoporous silica catalysts (Nb-SiO2) [152]. They exhibited excellent selectivity toward monoepoxides over Nb grafted silica catalysts. Sixty-five percent conversion and 95% selectivity were obtained in the presence of hydrogen peroxide.
Campanella et al. reported the epoxide synthesis method of SO and soybean methyl esters using heterogeneous Ti/SiO2 catalyst in ter-butyl alcohol. No degradation of epoxy ring was observed under the conditions applied in this experiment. 6 wt. % diluted solution of H2O2 was used with the catalyst. Highly effective oxidation has been shown recently with Ti on amorphous silica in the presence of H2O2 [153]. Gunam Resul et al. [154] have worked on tungsten-based polyoxometalates for epoxidation of limonene using hydrogen peroxide as an oxidant. Highly selective (100%) product was achieved with excellent yield (95%). Saturated sodium sulfate was used to prevent hydrolysis. The mole ratios for limonene/H2O2/catalyst were 4:1:0.005 with 373 K temperature. No solvent is required for epoxidation. Activation energy for the reaction was ∼36 kJ/mol. Less than 0.04 M acid concentration was used for maximum selectivity. H2O2 was added with H3PO4 and Na2SO3 to achieve complex catalyst. Then, H2SO4 was poured with them for the maintenance of pH. Limonene was added and reaction was further proceeded to complete the epoxidation.
Charbonneau et al. [155] reported the catalyst-free epoxidation of limonene and some other terpenes. Both the conventional and semibatch heating techniques were utilized for the reaction. Cheapest oxidizing agent (Oxone) was used with acetone and sodium bicarbonate for in situ generation of DMDO. DMDO is a green oxidant, comparable to m-CPBA, and reduces the time for reaction under ultrasound process. However, DMDO cannot epoxidize double bonds of low electron density. The results obtained through semibatch heating methods are shown in Table 7 which showed high yield.
Substrate | Time (min) | Conversion (%) | Yield (%) |
---|---|---|---|
Carveol | 5 | 100 | 95 |
Carvone | — | 100 | 99 |
Farnesol | — | 100 | 100 |
β-Pinene | 5 | 100 | 100 |
α-Pinene | 4 | 100 | 100 |
Limonene | 4.5 | 100 | 100 |
The use of sulfated zirconia for epoxidation of castor oil has been reported by Yuan et al. [156]. Autoclave reactor was utilized for the reaction in which 20 g castor oil, 2 g formic acid, and 3 g catalyst were placed at 25°C. 38 g H2O2 was added during first 2 h, then reaction was performed for 2–10 h at 65°C. The product was extracted by centrifugation and vacuum distillation. However, catalytic activity of this zirconia-based catalyst was not so valuable because of less surface area and nonordered pores in catalyst. SiO2-supported TiO2 was used as catalyst for epoxidation of FAMEs [157]. Methyl oleate, naphthalene, and acetonitrile were mixed with 1:100:0.6 ratio, at 50°C, and 70 mg hydrogen peroxide was added slowly. The reaction was carried out for 5 h. Catalyst was removed by filtration and product was obtained after workup. The metal-based epoxidation of various oils is discussed in Table 8.
Substrate | Catalyst | Time | Temp. (°C) | Solvent | % yield | Ref. |
---|---|---|---|---|---|---|
Methyl oleate | Copper | 6 h | 100 | Cumene, toluene | 87 | [148] |
Methyl linoleate | SiO2 | 1 h | rt | CH2Cl2 | 92.76 | [149] |
Methyl oleate | Mn | 4 min | rt | Isobutyraldehyde | 99 | [151] |
FAMEs | Nb-SiO2 | 4 h | 90 | CH3CN | 95 | [152] |
Rubber seed oil | Tungsten | 1 h | 60 | No solvent | 94 | [153] |
Limonene | Tungsten | 15 min | 50 | Solvent free | 95 | [154] |
Limonene | Catalyst free | 4.5 min | rt | DMDO | 100 | [155] |
Castor oil | Sulfated zirconia | 2–10 h | 25–65 | — | — | [156] |
Methyl oleate | TiO2/SiO2 | 5 | 50 | Acetonitrile | 38.52 | [157] |
Cardoon seed oil | Alumina | 4 h | 65 | — | 88.2 | [158] |
Cardoon seed oil | Alumina | 5h | 78–80 | H2O2with peracid | 85.5–88.2 | [158] |
SO | Dioxo-molybdenum | 4h | 110 | TBHP | 37.9 | [159] |
Grape seed oil | Co-N-C/SiO2 | 5h | 35 | n-Butyraldehyde | 71 | [160] |
Recently, various epoxidation methods have been compared with cheap and nonedible cardoon oil, as starting material [158].Various metal-based heterogeneous catalysts have been used, where high-quality products have been achieved with Al2O3. Epoxidation was performed in batch reactor that was kept in oil bath for heating. Catalyst, solvent, and hydrogen peroxide were added in it together with the cardoon oil. The reaction was performed for 5 h at 70°C–80°C.
6. Conclusion
Over time, improved epoxidation approaches have affected quantity and quality of product [161]. In this study, a range of reported epoxidation methodologies have been compared. In situ generation of peroxy acid is beneficial for large-scale epoxy production [162]. Enzymatic epoxidation delivers high selectivity and little by-products [136]. Catalyst-based epoxidation with green oxidants is an eco-friendly approach [163]. Commercially, epoxidized bio-based oils are used as stabilizers and plasticizers. Industrial sector spending epoxidized bio-resources, has the option to play with material properties within required frame, by controlling epoxy contents and elastic behavior after reacting with proper curing agents [164].
Conflicts of Interest
The authors declare no conflicts of interest.
Author Contributions
It is hereby confirmed that all listed authors have made a substantial contribution to the work.
Syed Zulqarnain Shah (data collection, data compilation, and write-up), University of Education Lahore, Chemistry Department, Vehari Campus, Vehari, Punjab, Pakistan, Muhammad Atif (conceptualization, supervision, and write-up: first draft and revision), University of Education Lahore, Chemistry Department, Vehari Campus, Vehari, Punjab, Pakistan, Muhammad Imran (resources and write-up: revision), Chemistry Department, Faculty of Science, King Khalid University, P.O. Box 9004, Abha 61413, Saudi Arabia, Musinguzi Alex (conceptualization and write-up: first draft and revision), Busitema University, P.O. Box 236, Tororo, Uganda, Jawairia Fatima (data collection, data compilation, and write-up: revision), University of Education Lahore, Chemistry Department, Vehari Campus, Vehari, Punjab, Pakistan, Dilawaiz (data collection, data compilation, and write-up: revision), University of Education Lahore, Chemistry Department, Vehari Campus, Vehari, Punjab, Pakistan, Maria Abrar (data collection, data compilation, and write-up: first draft), University of Education Lahore, Chemistry Department, Vehari Campus, Vehari, Punjab, Pakistan, and Hafiz Zeshan Haider (data collection, data compilation, and write-up: first draft), University of Education Lahore, Chemistry Department, Vehari Campus, Vehari, Punjab, Pakistan.
Funding
The authors express their appreciation to the Deanship of Scientific Research at King Khalid University, Saudi Arabia, for this work through a research group program under grant number RGP-2/232/45.
Open Research
Data Availability Statement
The data supporting this systematic review are from previously reported studies and datasets, which have been cited. The processed data are available from the corresponding author upon request.