Improving the Performance of the Current Cook Stove to Realize Ethiopia’s Sustainable Development Goals
Abstract
Ethiopia’s Sustainable Development Goals (SDGs) can be greatly aided by improving cook stove performance because it will increase energy efficiency, lessen indoor air pollution, and reduce deforestation. This study evaluated the new stove using a comparative analysis with the current Mirt stove, considering its thermal efficiency, specific fuel consumption, cooking time, and pollution reduction. The conventional water boiling and control cooking experiments were carried out using eucalyptus wood as fuel, yielding insightful results about the new stove’s performance. Notably, the new stove’s double-wall construction and use of flue gas as an insulator resulted in notable advancements. With the new stove attaining a thermal efficiency of 28.42% as opposed to the Mirt stove’s 23.47%, there was a noticeable gain in combustion efficiency of 7.47%. Additionally, there was a 7.21% drop in the specific fuel consumption and a 5.55% rise in the firepower produced in the combustion chamber. The new stove showed a time savings of 12.15% in every injera baking activity, reducing the cooking time, which is one of the most significant results. One kilogram of injera took an average of 3.92 min to bake on the new, better stove, as opposed to 4.41 min on the Mirt stove. In addition, compared to the Mirt stove, the injera quality examination showed a 2.8% improvement in moisture content, consistency, and general sensory qualities. Apart from these improved performance gains, the new stove’s fuel savings are expected to result in a considerable reduction of greenhouse gas emissions, amounting to 0.198 t CO2/year. This highlights the wider environmental and sustainability advantages of the upgraded injera baking stove.
1. Introduction
Energy consumption is increasing in emerging nations as a result of population growth and urbanization. 2.5 billion people still use nonrenewable energy sources for cooking, while 1.06 billion people globally do not have access to electricity. Moreover, accessibility varies by area, and the situation in the least developed countries is quite concerning [1]. However, there has been a concerning rise in energy consumption in recent years. There has been a lot of study done on renewable and alternative energy sources because of the depletion of fossil fuel supplies and the pollutants they release into the atmosphere. These sources have a lot of advantages for the environment [2]. Ethiopia is seeing significant population growth similar to other emerging countries, but it also has the least access to power and clean cooking facilities. The country boasts some of the lowest per capita energy use and availability in the world [3]. In Ethiopia, almost 56% of the population lacks access to electricity. Households use the majority of the energy in the country for cooking and lighting. Nearly 95% of the electricity is generated by hydropower, and over 90% of people cook using solid biomass fuels, which accelerates the rate of deforestation [3]. Ten to 14% of all import expenses are made up of petroleum fuels, which are all imported. The primary energy source for this need is biomass [4]. Over 87% of Ethiopia’s total energy supply comes from biomass, making it the country’s primary energy source [5]. Firewood made up 69% of the various biomass resources, including animal dung (14%), agricultural residue (13%), and charcoal (4%) [6]. For cooking and home heating, the majority of rural communities gather firewood, agricultural leftovers, and animal manure. Cooking consumes more than 90% of the energy used in rural households [7]. Preparing sauce and making injera are the most common cooking tasks in both rural and urban families across the nation. By 2030, every person should have access to modern, affordable, sustainable, and reliable energy, according to the seventh Sustainable Development Goal (SDG 7) [8, 9]. Ethiopia has released several policy and strategy documents to ensure the Sustainable Development Goals (SDGs) are met. The National Energy Policy of Ethiopia, the Biomass Energy Strategy, and the Climate-Resilient Green Economy (CRGE) Strategy are the three most significant ones [1]. Aside from other policies and plans, the Green Economy Strategy has prioritized initiatives that could help sustainably grow the forestry sector and reduce the need for fuel wood. For instance, one can lessen the need for fuel wood and promote forest management, enhanced carbon sequestration, decreased forest degradation, and the afforestation and reforestation of woodlands by dispersing and using fuel-efficient stoves or by using alternative fuel cooking and baking techniques like liquefied petroleum gas (LPG), electric, or biogas stoves [1, 10].
In terms of energy sustainability, biomass is a well-liked renewable energy source that is affordable and easily accessible for residential use [4]. Ethiopia has a lot of biomass energy potential, but because of ineffective baking and cooking techniques, it is not being utilized to its full or best potential. Ethiopia’s potential for using its biomass is projected to be 141.8 million tons annually, whereas its present use is 70.9 million tons [11]. The three-stone stove and other conventional end-use devices continue to use biomass fuels. The excessive use of biomass fuels and the burning of biomass are major contributors to indoor air pollution, which includes carbon monoxide (CO), elemental carbon (EC), particulate matter (PM), volatile organic compounds (VOCs), and polycyclic aromatic hydrocarbons (PAHs). This is because of the high reliance on the use of low thermal efficiency technologies [12]. People frequently use open fireplace pits or crude stoves for cooking, which exposes them to air pollutants (such as carcinogens, nitrous oxides, CO, and PM) both immediately and over time. These methods also often have poor ventilation and inefficient combustion [13]. Traditional stoves often have harmful social repercussions in addition to their detrimental effects on fitness. For example, using inefficient stoves to bake injera and get gas takes longer, and women and children are more likely to do the work, devoting time away from income-generating activities like sports and education. Furthermore, cook stoves that run on fossil gas or biomass account for 7% and 22% of worldwide carbon emissions, respectively, making them the second-biggest source of contemporary global warming [14]. Because incomplete combustion products like methane and CO, which have a greater potential to cause global warming than carbon dioxide, are released during inefficient fuel combustion, cooking and baking using traditional, unsustainable, and collected biomass can have an impact on the environment. Additionally, the second-biggest source of the world’s current warming, biomass, and fossil fuel cook stoves releases 22% and 7% of global carbon (BC) emissions, respectively. In rural areas, three-stone open fires, which have an efficiency of 8%–12%, are the most common stoves used for home cooking [15]. Initially, improved cook stoves (ICSs) were created to address these detrimental effects on livelihood and health. When ICSs replace traditional cook stoves, cooking efficiency is increased, and less fuel is needed, which can lead to reduced fuel consumption, shorter cooking times, and better health and household income. Additionally, by reducing fuel wood collection (which reduces deforestation) and particulate emissions, this efficiency can improve the local environment as well as the climate globally [16]. Even though there is ample scientific proof of these innovations’ effectiveness, early attempts to promote them have encountered difficulties with implementation, diffusion, and dissemination. Most homes finish their injera baking system with an open fireplace, three stones, or a baking gadget, which is an inefficient and wasteful method of baking. The injera baking method is the topic of most household attention, as it is responsible for around 50% of a family’s annual biomass power usage [17, 18]. Additionally, people are acutely and continuously exposed to air pollution (nitrous oxides, CO, PM, carcinogens, and others) by open fire pits and simple bake ovens [19, 20]. Thus, exposure to air pollution in the home has been linked to several harmful health consequences in both adults and children, such as low birth weight, early mortality, lung cancer, tuberculosis, pneumonia, and chronic obstructive pulmonary disease [21].
The cook stove technologies that are now being disseminated and promoted are the rocket (tikikil), mint, Gonze, and Lakech stoves. However, because of the incomplete burning (direct combustion) of the biomass, these stoves not only have lower efficiency but also produce a lot of interior air pollution. Due to the high fuel consumption of these technologies, there is a significant rate of deforestation as a result of household fuel demand. An issue arising from incomplete combustion of biomass is the incapacity to obtain energy and the release of hazardous hydrocarbons and CO, many of which are carcinogenic [22].
The distinctive flavor of injera lies in its round, sour, and delectable pancake-like shape. Its dimensions are approximately 55 to 58 cm in diameter and 2–4 mm thick, with 400 g considered to be the average weight for one injera [23]. As shown in Figure 1, teff, a native grain of the area, is used to make most injera. Even though the majority of Ethiopians and Eritreans consume teff (Eragrostis tef), it was not well-liked until recently. Researchers have discovered that teff is free of gluten, which makes it a very appealing option for a nutritious diet [24, 25]. In Ethiopia, baking injera (IBS) is the most energy-intensive activity. The dough will be placed into the baking pan when the pan temperature reaches between 170°C and 200°C [23]. Most Ethiopians living in rural areas still bake injera over three stones.
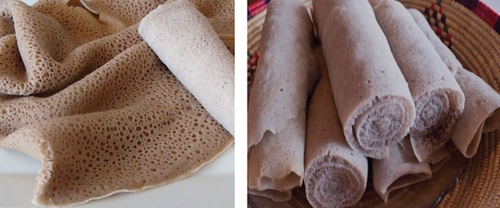
There are different types of injera baking stoves in Ethiopia, including three-stone open fires, mud stoves, Tehesh stoves, Sodo stoves, Awramba stoves, Gonziye baking and cooking stoves, and Mirt stoves as shown in Figure 2.
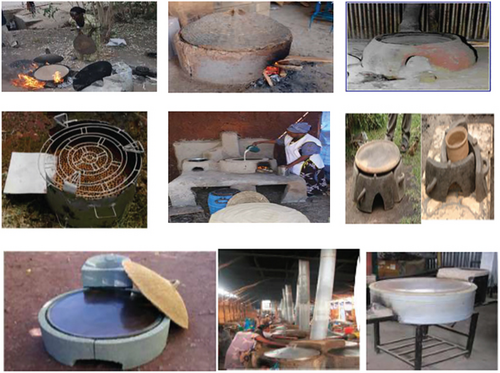
Reducing greenhouse gas emissions from energy production appears possible with the use of densified solid biofuel technology and efficient biomass-based combustion devices [26]. Therefore, increasing the efficiency of these clean cook stoves is a crucial step in improving the health and environmental circumstances of those who still rely on burning solid fuels for their daily home energy source [27].
Developments in energy-efficient technology are crucial and difficult in developing countries such as Ethiopia. Researchers have worked to increase the injera baking stoves’ efficiency both domestically and internationally to save energy and lower CO2 emissions and indoor air pollution [28]. This includes the initial initiatives in the late 1980s and early 1990s by the GIZ-Energy Coordination Office and the Ministry of Water, Irrigation, and Electricity, specifically the Alternative Energy Development and Promotion Directorate. The GIZ-Energy Coordination Office-Ethiopia has recorded a noteworthy accomplishment in the nation’s dissemination of around 455,000 upgraded injera baking stoves, particularly Mirt stoves [23]. Among the results of these efforts in Ethiopia are the creation of better baking and charcoal stoves, such as the “Mirt, Gonzie”; “Lakech, Merchayie, tikikil”; and Institutional Rocket Stove [29]. But injera is still primarily baked over open fire stoves in rural homes. Although Ethiopians typically use Gonze and Mirt stoves for cooking, their efficiency is insufficient to lower thermal energy loss and environmental pollution levels [29, 30]. By 2030, the national government wants to convert over 20 million homes to clean stoves [31]. Therefore, it is crucial to improve the performance of these commonly used cook stoves (Mirt stoves) by taking into account a variety of factors to conserve energy, lower pollution levels in the environment, and achieve SDGs. Therefore, improving thermal efficiency and reducing indoor air pollution are still important topics to research for Ethiopian Mirt stove cooking technology [32]. The metropolitan area with an electric grid connection is where the electric stove is located. in rural locations that are isolated from the electrical grid. Compared to earlier models, these stoves are better and have shown good performance [33]. Although there is room for development, this performance needs to be further enhanced by various methods. Cook stove losses are influenced by a number of variables related to the construction and functionality of the heating apparatus [34].
This study aims to produce an improved biomass injera baking stove that is more energy-efficient than currently maintained baking stoves, reduce heat loss in Injera baking stoves through various means, and design them to be fuel-efficient with reduced IAP and/or pollution. By lowering smoke emissions, improved cooking stoves are marketed as a way to lessen the negative effects on the environment, economy, and society. They also hold significant health benefits for both the environment and their users. An important development in this field was the creation of a novel injera baking stove that runs on biomass. In comparison to the current Mirt stove, the study’s main goals were to boost thermal efficiency, decrease specific fuel consumption (SFC), reduce emissions, and shorten cooking times. A thorough examination of the new stove’s thermal efficiency, SFC, cooking time, and emission reduction was conducted, along with a comparison with the Mirt stove that is now in use. Using eucalyptus wood as fuel, the conventional water boiling and control cooking experiments were carried out, yielding insightful results about the new stove’s performance. Notably, the new stove’s double-wall construction and use of flue gas as an insulator resulted in notable advancements.
2. Materials and Methods
2.1. Study Area
The performance evaluation of the improved injera baking Mirt stove was carried out at a field in Injibara town, Amhara region, located 125 km away from Bahir Dar, which is found at 10° 57 ′ N, 36° 56 ′ E with an elevation of 2544 m, an annual average temperature of 20°C, an annual average humidity of 56%, an average wind speed of 2.3 m/s, and an annual rainfall of 546 mm with a UV index of 5.
2.2. Materials
Local materials including red ash, water, cement, sheet metal (for mold-making purposes), pipe, cutter, angle iron, welding machine, welding rod/electrode, grinding machine, hammer, wrenches, bolts and nuts, and wood logs were collected in local suppliers.
Stove testing materials such as teff powder, water, bucket, cooking pot, dry eucalyptus wood, complete Mirt stove assembly, baking pan (65 cm wide and 58 cm effective diameter made from clay with a thickness of 2.1 cm), metal pan, small shovel/spatula to remove charcoal from stove and tongs for handling, dust pan for transferring charcoal, metal trays to hold charcoal for weighing, and heat-resistant gloves were collected from local suppliers.
ALH8.1 rod thermometer whose range of measurement is −10°C–250°C with ±1°C of accuracy available in the market was used. The thermometer was used to measure all the temperature-related measurements during the experimental tests of water boiling test (WBT) and controlled cooking test (CCT).
Measurement tools include spring balance, desk balance, thermometer, tape meter, and time counter.
2.3. Methods
2.3.1. Experimental Setup and Description
The experimental setup of the improved Mirt injera baking stove is shown in Figure 3. The newly designed stove was a natural draft stove made using a 3-cm-thick cement red ash mix (1:4 ratio).

2.3.2. Improved Mirt Stove Design Approach
To improve the performance of the current Mirt injera baking stove, preliminary design details were collected from the community that used an improved injera baking stove. During the survey, it was also observed that the amount of water and teff ratios in the dough were 60% and 40%, respectively [33]. The average dimension of the Mirt stove was 22 cm in height, and the fuel and air inlet area was 12 cm by 22 cm, respectively; the other parameters of the Mirt stove in different household levels are presented in Table 1.
S. No | Stove parameters | Number of households | Remark (taken) | ||||||
---|---|---|---|---|---|---|---|---|---|
9 | 4 | 5 | 2 | Mean | SD | SE | |||
1 | Outside dia. (cm) | 68 | 66 | 69 | 70 | 68.05 | 1.60 | 0.358 | 68 |
2 | Inner dia. (cm) | 60 | 57 | 61 | 62 | 59.85 | 1.05 | 0.234 | 60 |
3 | Pan dia. outer (cm) | 65 | 64 | 64.5 | 66 | 64.78 | 1.50 | 0.335 | 64.6 |
4 | Dia. of injera (cm) | 56 | 58 | 57 | 55 | 56.55 | 0.70 | 0.156 | 57 |
5 | Pan thickness (cm) | 2 | 2.2 | 2.1 | 2.3 | 2.095 | 0.00 | 0.000 | 2.1 |
6 | Cover dia. (cm) | 63.5 | 59.3 | 64 | 65 | 62.94 | 0.95 | 0.212 | 63 |
7 | Cover height (cm) | 15.5 | 14.5 | 13.5 | 16 | 14.85 | 0.43 | 0.096 | 15 |
8 | Stove height (cm) | 22 | 21.5 | 21 | 20.5 | 21.5 | 0.14 | 0.03 | 22 |
9 | Fuel feed A. (cm2) | 274 | 283 | 275 | 283 | 276.95 | 4.29 | 0.958 | 277 |
2.3.2.1. Stove Combustion Chamber Height (cc)
To improve the existing injera baking Mirt stove, different observations have been conducted in the community to identify the design parameters of the Mirt stove. The height-to-diameter (H/D) ratio of a stove combustion chamber is very important to improve the performance of the baking stove. Reports indicated that different fuel combustions have different ratios of H/D. For instance for wood combustion, the ratio of H/D is 0.35, and for dung combustion, it is in the range of 0.75–1.00 [35]. To improve the performance of the existing injera baking Mirt stove, an average of the two fuel types for the market purpose had been taken for this study assuming that 75% of the tasks shall be done using wood combustion. Considering the H/D relation, a ratio of 0.48 was taken and so that a stove combustion chamber height (hcc) was estimated and approximated. Once the combustion chamber height is determined, the area of the combustion chamber (Acc) is then given by the circular area equation: Acc = π∗Dcc2/4, where a constant number π = 3.14 and Dcc is the diameter of the combustion chamber.
2.3.2.2. Determination of Stove Chimney Size
2.3.3. Estimation of Generated Heat Energy to Bake Injera
The input energy for the injera baking process is a part of the heat generated by the combustion of fuel in a combustion chamber. The amount of energy utilized to bake injera to the required quality is a combination of sensible and latent heat.
2.4. Performance Evaluation
The performance of the improved Mirt stove was tested using a WBT and CCT and compared with the conventional Mirt stove performance, which was carried out at the same time.
2.4.1. WBT
Two bundles of fuel wood that weigh about 4 kg each for the cold and hot start high-power tests and one bundle of fuel wood that weighs about 5 kg to be used in the simmering test were set aside. Pot lids were not used during the phase of the WBT. The temperature of the water and stove wall body was measured and recorded every 5 min. The high-power (cold start) phase, high-power (hot start) phase, and low-power (simmering) test were carried out as per the Stove Manufacturers Emissions and Performance Test Protocol (EPTP) principle [36].
The local boiling temperature is given by (Tb) = (100 − h/300)°C, where h is the local elevation of (h = 2544 m) in an Injibara.
2.4.2. CCT
A CCT was carried out as per the official cook stove testing method [37].
In this case, (MCΔT)foodcooked could be zero, since only water was boiled (no food to be cooked).
2.4.3. Generated Heat Energy to Bake Injera
The input energy for the injera baking process is a part of the heat generated by fuel combustion in a combustion chamber. The amount of energy utilized to bake injera to the required quality is a combination of sensible and latent heat.
2.4.4. Combustion Analysis
Combustion: It refers to the rapid oxidation of a fuel accompanied by the production of heat and light. Complete combustion of a fuel is possible only in the presence of an adequate supply of oxygen. Biomass combustion is an extremely complex process, and its study involves chemical kinetics; conductive, convective, and radiative heat transfer processes; molecular diffusion; and other physical phenomena. Realistic modeling of these processes is not yet possible, and useful results are still almost entirely empirical. Thus, experimental measurements of biomass stove performance are always necessary. The structural components and chemical elements of biomass are influential factors in combustion characteristics and thermal utilization. These components and elements depend on the origin and type of biomass. Carbon, hydrogen, and oxygen are the main elements of the solid biomass even if other traces of elements are also present. Table 2 shows that theoretical stoichiometric O2 is required for the combustion of 1 kg of wood.
Molecules by weight | Oxygen is required for combustion | Remarks |
---|---|---|
C = 51% | Needs 1.36 kg of oxygen | C + O2⟷CO2 |
H = 5.8% | Needs 0.464 kg of oxygen | 2H2 + O2⟷2H2O |
S = 0.0594% | Needs 0.00055 kg of oxygen | S + O2⟷SO2 |
Cl2 = 0.04% | Needs 0.00036 kg of oxygen (negligible) | Cl2 + 2O2⟷2ClO2 |
|
Total 1.82486 − 0.387 = 1.4379 kg of O2 per kg of wood needed (by volume = 1.006 lit) | The air required≈6.252 kg of air/kg of wood |
Air required = 6.252 kg/kg fuel | Volumetric dry air by volume = 4.794 m3/kg of fuel |
Using mass compositions of biomass species, the theoretical air (dry) required for the combustion of 1 kg of fuel was calculated as 6.252 kg of air (as oxygen is 23% of air by mass). The stoichiometric AFR (m) becomes 6.252. The absolute humidity of air in Injibara at a bulb temperature of 15°C and an average humidity of 56% was approximated to 6 g of water/kg of air as seen in the psychrometric chart. The moist air required then becomes 6.252∗(1 + 1.61∗0.006) = 6.3124 kg of humid air.
Products of combustion: The product gases were also estimated to specify the chimney and gas emission concentrations. If the fuel is specified and combustion is complete, the respective amounts of the products can be determined by applying the conservation of mass principle to the chemical equation.
Estimation of excess air (EA): Normally, the amount of air supplied is either greater or less than the theoretical amount.
The stoichiometric mass of flue gas (Mg) becomes 5.96 m3/kg of fuel on a volume basis and Mgst = Mast + 1 = 7.252 kg/kg of fuel on the mass basis, whereas the real mass of flue gas was 8.23 m3/kg of fuel on a volume basis and 12 kg/kg of fuel on the mass basis. The stoichiometric and EA flue gas products are presented here in Table 3.
Flue gas products | Stoichiometric Qty | With excess O2 | Remarks | ||
---|---|---|---|---|---|
Kmole | Percentage | Kmole | Percentage | ||
CO2 | 0.0425 | 20.09% | 0.0425 | 14.03% | Dry basis |
H2O | 0.029 | 12.06% | 0.029 | 8.74% | Wet basis |
O2 | 0.000 | 0.00% | 0.01937 | 6.4% | Dry basis |
N2 | 0.169 | 79.90% | 0.2415 | 79.6% | Dry basis |
SO2 | 1.72∗10−5 | 0.008% | 1.72∗10−5 | 0.0057% | Dry basis |
Misc. | Negligible | ||||
Total | 0.2115 (dry) | 0.30289 (dry) |
2.4.4.1. Estimation of Adiabatic Flame Temperature in the Combustion Chamber
The adiabatic flame temperature is the maximum theoretical temperature that can be reached by the products of combustion of a specific fuel and air reaction assuming that no heat loss to the surroundings. EA is not involved in the combustion process; it only acts as a diluting agent and reduces the average temperature of the combustion products. The flame temperature was calculated theoretically at the core of the fireball in the stove which was evaluated based on Equation (21) from the balanced equation considering the mole fraction of products and reactants which was important for the theoretical estimation of velocity and temperature of flue gases.
By assuming an initial flame temperature, the required flame temperature was iterated which was used for CFD analysis of the stove system.
2.4.4.2. Heat Transfer Mechanisms in the Improved Mirt Stove
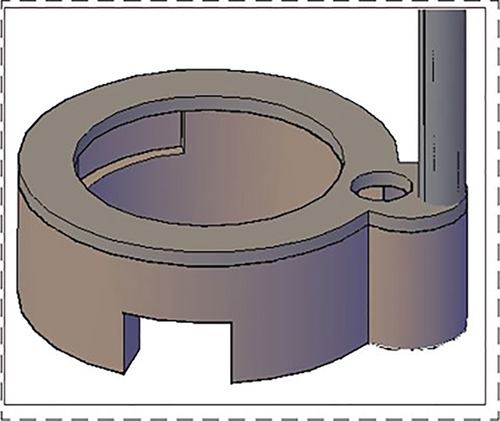
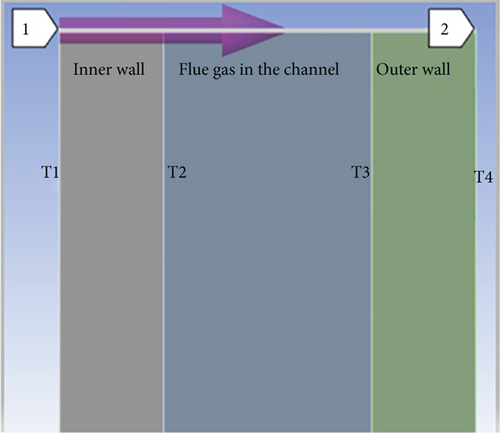
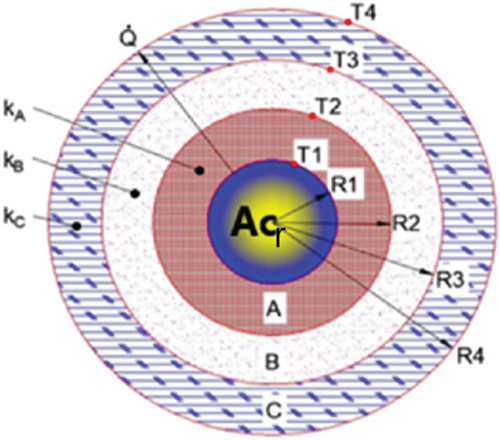
Furthermore, a mathematical model representing heat transfer of the baking pan during baking was analyzed based on the following modeling assumptions: Heat transfer is mainly in axial directions of the system and steady for the pan, the baking pan was modeled as axisymmetric, the diameter of the pan at which the area exposed to stove fire and on which injera would be baked is the same, and the effect of pressure gradient is negligible.
The general heat losses in the injera baking Mirt stove are presented in Figure 5. The heat losses through different modalities including conduction, convection, radiation, and flue gas were considered during the thermal analysis of the stove.
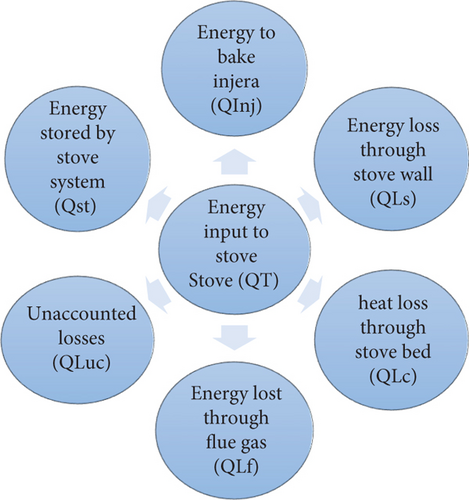
2.4.5. Emission Reduction
As reported by IPCC, the emission factor of CO was found to be 18.533 kg CO/ton. According to the World Health Organization, the acceptable amount of CO during 1 h of exposure is 30 ppm. The amount of soot or PM in a kitchen impacts the health of people in the room. The WHO standards that recommend concentrations were below 10 mg/m3 for annual exposure and 25 mg/m3 during 24 h of exposure.
3. Results and Discussions
3.1. WBT
The WBT determines how quickly a stove can boil in a given volume of water, hence evaluating its efficiency. Metrics like thermal efficiency, which indicates how well the stove transforms fuel into usable heat, are often included in the results. To help customers and academics find more economical and ecologically friendly solutions, this kind of testing is essential for assessing and contrasting cooking methods. Tables 4 and 5 illustrate that the thermal efficiency comparison shows that the newly designed stove outperforms by achieving an average thermal efficiency of 28.42%, which is 4.95% higher than the existing Mirt stove’s efficiency of 23.47%. As shown in Figure 6, a 2.17% efficiency difference was achieved by the new stove indicating that the new stove performs better than the existing one. The high-power cold start and hot start were allowed to run for 35 min in both stoves (even if the boiling time was shorter) to confirm the variation of temperature for any rising more than the local boiling temperature. The simmering phase was allowed to run for a total of 75 min (30 min to bring to a boil and 45 min for simmering time). From this, the double-wall stove consumes less fuel as compared to the single-wall stove within the same period.
Phases per test | Average mass of water | Average fuel-burning data | |||
---|---|---|---|---|---|
Mcs (kg) | Me (kg) | Uf (kg) | Mchar (kg) | Fcd (kg) | |
Mirt stove | |||||
Cold start | 4 | 3.897 | 2.83 | 0.194 | 2.257 |
Hot start | 4 | 3.898 | 2.77 | 0.185 | 2.217 |
Simmer | 4 | 2.45 | 2.67 | 0.150 | 2.179 |
Average | 4 | 3.415 | 2.757 | 0.1763 | 2.218 |
Improved Mirt stove | |||||
Cold start | 4 | 3.898 | 2.30 | 0.135 | 1.872 |
Hot start | 4 | 3.902 | 2.26 | 0.127 | 1.844 |
Simmer | 4 | 2.54 | 2.21 | 0.118 | 1.809 |
Average | 4 | 3.447 | 2.257 | 0.1267 | 1.842 |
Testing phases | Thermal efficiency (%) | |
---|---|---|
Mirt stove | Improved Mirt stove | |
Cold start | 21.38% | 26.08% |
Hot start | 25.56% | 30.75% |
Average efficiency (ηth) | 23.47% | 28.42% |
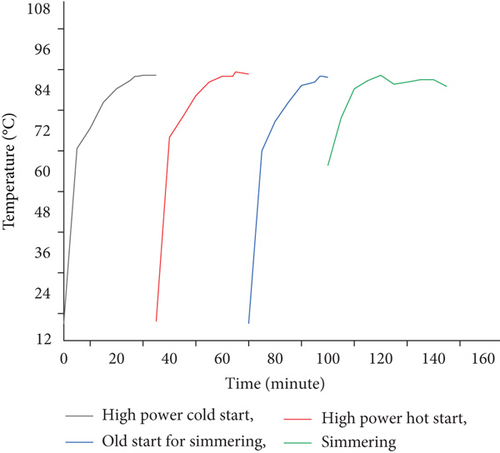
3.2. CCT
A systematic procedure called the controlled preparing test (CCT) is used to assess how well different fuels and cook stoves perform when preparing food. Through the measurement of fuel consumption, cooking time, and the quality of cooked food under controlled settings, it evaluates the efficacy and efficiency of cooking devices. The test usually consists of specified recipes and a predetermined process to guarantee that the results are comparable across various cook stoves and fuels. The CCT is a useful tool for academics and policymakers in energy and nutrition since it is especially crucial for understanding the effects of cooking technologies on health, the environment, and energy use. As seen in Table 6, the control cooking test depicted that the burning capacity was modified by applying an improved stove and could reduce the fuel consumption, the time of baking, and the charcoal production. It is important to bear in mind that the test was conducted for five injeras, and the initial heat absorbed by the stove system is high. The newly designed stove had the capability of burning 7.848 kg of fuel within an hour. In the same procedure for the conventional/existing Mirt stove, SFC was 542.2 g of wood/kg of food. And hence, 7.2% of fuel was saved. It had taken an average time of 13.58 min to perform one cycle, which means it would take 4.409 min to cook 1 kg of food, or on average, it would take 2 min and 43 s (2.717 min) to bake one injera. This results in 12.15% of the time saved in baking one injera. The burning capability of the Mirt stove was 7.416 kg of fuel within an hour showing that the new stove was 5.825% more efficient than the Mirt stove.
S. No | Performance indicators per test | Stoves | |
---|---|---|---|
Conventional Mirt stove | Newly designed Mirt stove | ||
1 | Total weight of food cooked (kg) | 3.08 | 3.04 |
2 | Total weight of injera baked (kg) | 2.033 | 2.028 |
3 | Total average weight of char produced (kg) | 0.359 | 0.356 |
Total average weight of wood burned (kg) | 2.453 | 2.293 | |
4 | Average equivalent dry wood consumed (kg) | 1.67 | 1.53 |
5 | Specific fuel consumption (g/kg of food) | 542.2 | 503.12 |
6 | Total average baking time (minutes) | 13.58 | 11.93 |
7 | Time required to make 1 kg of food (min/kg) | 4.4091 | 3.9243 |
8 | Evaporated water per minute (Mwe) (kg/min) | 0.0771 | 0.0849 |
9 | Burning rate (kg/s) | 0.00206 | 0.00218 |
10 | Time per one injera (min/Inj) | 2.716 | 2.386 |
11 | Amount of fuel burned per injera (kg/Inj) | 0.4906 | 0.4586 |
12 | Amount of fuel used per injera (kg/Inj) | 0.332 | 0.306 |
3.3. Quality Analysis of Injera
The quality of injera was characterized by the sense of palatability and pliability by testing and measuring its parametric consistency. These were done by visualizing the texture of injera, sensing the taste softness, and measuring the percentage of water content of injera. The weight of baked injera is dependent on the amount of moisture loss during baking, the temperature used for baking, the time of baking, and the water–flour ratio. As reviewed in the previous studies, the moisture content was reported to be 65.23% for injera baked at 72 h, and others reported that it is in the range of 62%–65% [39].
In this study, the water content percentage of injera was calculated as the percentage of injera water content = Wc/Ij, where Wc was the weight of water in injera and Ij was the weight of injera. The water content of injera baked by Mirt stove ranges from 36.9% to 40.9%, whereas injera baked by the new one was from 39.3% to 44.1%. This demonstrated that when injera absorbs moisture from its surroundings, its water content will grow with time, as suggested by the literature and verified at home. As shown in Figure 7, it was understood that the weight flux indicated in the chart below confirms the quality of injera as tasted (palatability) and sensed (pliability). Injera with a lower weight of the same diameter feels dry (lower water content, more water was vaporized) with a corresponding unfavorable test and physically found not good, and the vice versa is true.
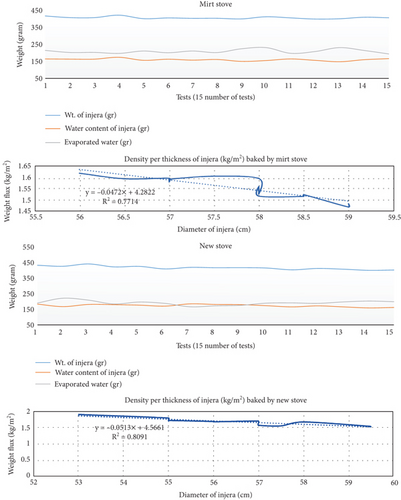
The regression plot above showed that the consistency of injera baking was observed on the new stove better than the existing Mirt stove concerning weight flux, confirming that the quality similarity of the new stove was consistent with that existing Mirt stove.
3.4. Combustion of Fuel
The investigation shows that higher carbon and hydrogen concentrations increase the calorific values, while higher oxygen, moisture, and ash content decrease the calorific value of wood. In real-world applications, incomplete mixing creates a need for a certain amount of surplus air, which is necessary to maximize the heat production from the fuel wood and achieve complete combustion. On the other hand, extra heat loss results from allowing more air to enter than what is required for full combustion, since the extra air heats up the chimney to its temperature. This leads to higher stack losses as a result.
Smoke would be produced, and incomplete combustion would occur from a decrease in air supply. As such, the ideal amount of extra air for each type of fuel is different. The amount of combustion air used in real-world applications frequently surpasses this ideal requirement. Consequently, a portion of the warm air leaves the stove through the flue without aiding in the combustion process. The iteration table shows that the CE neared zero at an ideal surplus air coefficient of 1.43, illustrating the discrepancy between the CE computed from the percentage compositions of CO2 and CO (CE2) and that determined by heat loss (CE1) [40]. Table 7 illustrates that combustion product gases confirm a longer residence time, giving a chance to burn CO produced in the combustion chamber. So the theoretical flue gas concentration in the atmosphere was approximately 2.256% and 3.277% of CO in the new improved stove and the Mirt stove, respectively.be unchanged while other products were disturbed with the same amount of EA.
Flue gas products | Mirt stove | Improved (new) stove | ||
---|---|---|---|---|
Moles (Kmole) | Percentage (%) | Moles (Kmole) | Percentage (%) | |
CO2 | 0.0324 | 10.53% | 0.0356 | 11.62% |
H2O | 0.029 | 0.029 | ||
O2 | 0.02433 | 7.9% | 0.02274 | 7.42% |
N2 | 0.241162 | 78.31% | 0.241162 | 78.72% |
SO2 | 0.0000093 | 0.003% | 0.0000093 | 0.003% |
CO | 0.010092 | 3.277% | 0.006912 | 2.256% |
Misc. gases | ||||
Total Kmole | 0.30794 | 0.30643 | Dry basis | |
Total mass | 9.241 kg | 9.241 kg |
The flame temperature (Tf) is the maximum temperature that could be developed within the baking stove CC by the combustion reaction. The iteration analysis showed that a small amount of CO was produced and some part of this CO produced in the CC was consumed by EA and converted to CO2 in the CC. This implies that prolonging the residence time facilitates the conversion of CO to CO2, and hence, it was evaluated that the CE was 83.74% and 76.26% for the new stove and Mirt stove, respectively. This confirms that a longer residence time gave a chance to burn CO produced in the combustion chamber. So the theoretical flue gas concentration in the atmosphere was approximately about 2.06% and 3.0% of CO in the new improved stove and Mirt stove, respectively. In the iteration to determine the flame temperature, the specific heat constants of the specious gases are temperature dependent and so determined from the corresponding flue gas temperature from the iteration done on the Excel sheet, and the final combustion reaction products were summarized which was used for all the analysis. The flame temperature that could be developed in the combustion chamber with the reaction of stoichiometric air was iterated as 1483.55 K (1210.55 OC). In real terms, the temperature is lower than this because it takes too much oxygen, nonburned products appear, fuel has moisture, and so on. From Equation 26, the flame temperature, Tf, that would be developed during the combustion of wood fuel in the stove with an EA of 43% and with the production of some amount of CO was calculated by iteration on an Excel sheet and was found to be 776.7 K (503.7 OC) when combustion takes place within the new stove CC and 706.94 K (433.94 OC) when combustion takes place within the Mirt stove. The combustion analysis results showed that the flame temperature produced during a combustion reaction of eucalyptus wood with stoichiometric air was higher than the temperature developed with EA. This is because there is EA, moisture in the fuel and air, the formation of some CO, and unburnt fuel. The flue gas temperature in the channel (Tgch) was taken at the mid radius of the flue gas enclosing the stove (that is at 6 cm measured from the inner surface of the stove) as seen in Figure 8.
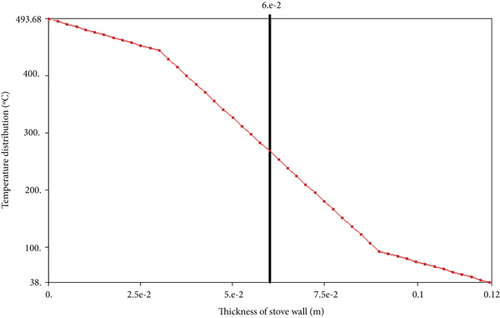
On the same principle, the analysis was done for the Mirt stove, and the result was summarized in Table 8. The energy carried by flue gas at CC energy is carried by flue gas at a point plus heat loss up to that point. Specific heats of the gas components were evaluated at that temperature.
Parameter | Mirt stove | New stove |
---|---|---|
Flame temperature CC (Tf, °C) | 433.94 | 503.7 |
Internal stove wall inner side temperature, °C | 220.61 | 493.68 |
Internal stove wall outer side temperature, °C | NA | 404.94 |
External stove wall inner side temperature, °C | NA | 104.67 |
External stove wall outer side temperature, °C | 69 | 38 |
Flue gas temperature (Tg) in CC (°C) | 327.3 | 498 |
Flue gas temp at chimney exit (Te), °C | 243 | 134 |
Fuel-burning rate (kg/s) | 0.00206 | 0.00218 |
Fuel-burning rate (kg/h) | 7.416 | 7.848 |
Firepower (kW) | 35.84 | 37.83 |
Mass flow rate of air (kg/s) | 0.02266 | 0.02398 |
Flue gas flow rate out of CC (m3/s) | 0.0427 | 0.0520 |
3.4.1. Heat Transfer Mechanisms in the Improved Mirt Stove
The heat transfer analysis shows that the newly improved double-wall stove lost less heat through stack gases and wall surfaces than the Mirt stove. The heat transfer coefficient of the stove in the combustion chamber side was the same, whereas the ambient heat transfer coefficient was different and calculated as 7.3 W/m2.k and 4.7 W/m2.k for the Mirt and the new stoves, respectively. The thermal resistances, from the combustion chamber to the outer surface of stove walls excluding the free stream resistance Rs and Rd, of the two stoves were significantly different that the Mirt stove has a resistance of Rs = 0.1454 k/W, whereas the new stove has a resistance of Rd = 1.8745 k/W. This implies that Rd > Rs which approved the new improved stove could lose less heat through the stove wall than the Mirt (existing) stove. The new stove heat flow rate behaves differently on different sections of stove wall. The analytical analysis indicates that the maximum heat flow rate across the stove wall was 251.87 W, while it was 250.45 W at the mid-height wall section (WS), 230.17 W at a junction of the stove wall and cover ring (J), and 228.35 W across the cover plate section (CS). For the Mirt stove, the analytical result shows that the heat loss rate on surfaces of stove walls (QWL) was steady in all sections and approximated to 2510 W (9.036 MJ per hour), while the maximum heat loss rate for the new stove was 251.87 W (0.907 MJ per hour). This shows that the heat loss rate through the wall of the Mirt stove was more than the new stove within an hour.
3.4.2. Total Energy Gain (Quse)
From the cooking test analysis, the amount of energy consumed by one injera was evaluated at an average weight of injera to be 0.57 MJ and 0.61 MJ in the new stove and the Mirt stove, respectively. This indicates that the new stove can cook a portion of food with less energy than the Mirt stove will do for the same cook. The heat required to heat the clay pan from its initial state to a baking temperature was from the heat supplied through the conduction of the stove wall via point of contact and the heat supplied by convention and radiation (cumulative effect of flue gas scratching it, flame temperature, and electromagnetics) in the combustion chamber; the pan body can store about 2.1988 MJ of heat, while the stove body stores about 3.538 MJ of heat. An energy of 3.979 kW was transferred to injera for a complete one-cycle baking. The heating time indicates that massive stone walls with no insulation warm slower and consume more energy generated from combustion and vice versa. The new improved stove trapped energy of 0.4784 kW (196.46 KJ within 11.93 min) from flue gas escaping the stove, while the Mirt stove trapped 0.58 kW (242.44 KJ within 13.58 min) from flue gas escaping the stove. The newly developed stove burned about 0.4586 kg of wood and consumed about 0.306 kg of dry equivalent wood fuel to bake one injera, while the Mirt stove burned 0.4906 and consumed about 0.332 kg of fuel wood to do so. The energy analysis showed that more than three extra injera can be baked in both stoves after the fire was extinguished. But it was done during the test that three injeras were baked.
3.4.3. Heat Losses
Heat storage sometimes serves as useful and is sometimes considered a loss depending on the device’s services. Here, it was partly considered a useful heat as it was used to heat up the pan first and then was used to bake extra injera after the fire had ceased. However, some are still stored in the body and taken away by atmospheric air. The analysis depicted that an improved stove made from a 3-cm-thick red ash wall with a clay pan stored a total energy of 8.53 MJ in the stove system, while a Mirt stove made from concrete material with a thickness of 4 cm stored about 8.303 MJ. The heat stored in the stove wall of the Mirt stove was 100% released from the combustion of fuel, while the new double-wall stove was 99.84% (the remaining 0.16% was supplied by the flue gas passing around the stove channel). This showed that a part of the heat energy carried by the flue gas to the atmosphere was recovered to be utilized in the new improved stove system in the heating stage too. A 10-cm-thick fire bed made with wood and mud coat with a thermal conductivity of 0.16 and 0.69 W/mK, respectively, has contributed to a countable heat loss in stoves as seen on the table. Based on the equations listed in Section 3.3, the thermal and physical parameters of stoves were summarized in Table 9.
Required parameter | Label | Value | |
---|---|---|---|
Stove 1 | Stove 2 | ||
Pan edge exposed area | Ae | 0.0045 m2 | 0.0045 m2 |
Stove wall area exposed to atm. | As | 0.4433 m2 | 0.7325 m2 |
Pan cover surface area | A cover | 0.3475 m2 | 0.3475 m2 |
Pan-to-wall contact area | Acont | 0.049 m2 | 0.049 m2 |
Effective pan top surface area | Apps | 0.264 m2 | 0.264 m2 |
Stove bed area (underneath) | Ab | 0.342 m2 | 0.554 m2 |
Av. pan surface temp. | Ts | 180°C | 185°C |
Outer wall temperature | Tw | 69°C | 38°C |
Pan cover temperature | Tc | 33°C | 33°C |
Stove bed temp. (underneath) | Tb | 28°C | 28°C |
Ambient temperature | Tᴔ | 15°C | 15°C |
Tg at the chimney exit | 243°C | 134°C |
The flue gas temperature exiting the chimney was smaller in the new stove than in the Mirt stove. This implies that heat loss through flue gas from the new stove was less than the Mirt stove. About 2.88 MJ of energy was carried out by the flue gases produced in the new stove. Within an average of 11.93 min, the temperature of water in a built-in auxiliary stove reached to 62°C. The general energy balance summary performed in the two stoves was presented in Figure 9 and Table 10 with a test (one full cooking test).
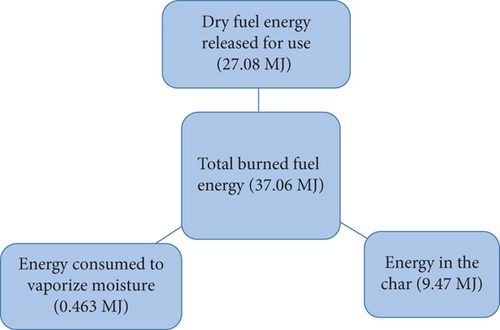
S. No | Parameters in MJ | M-stove | N-stove |
---|---|---|---|
Input energy (MJ) per test | 29.56 | 27.08 | |
1 | Loss by pan edge and pan cover (Pe, cL) | 0.54 | 0.54 |
2 | Loss through stove wall surface (WL) | 2.045 | 0.202 |
3 | Heat loss underneath the fire bed (BL) | 0.615 | 0.620 |
Total stove assembly loss (body loss) | 3.24 | 1.4 | |
4 | Carried by dry flue gases (QLdry) | 2.198 | 1.122 |
5 | Evap. of water formed by H2 in fuel (QLh) | 1.417 | 1.304 |
6 | Moisture in fuel (QLm) | 0.2362 | 0.2123 |
7 | Moisture in air (QLa) | 0.0393 | 0.0205 |
8 | Losses due to incomplete combustion and misc. | 0.3102 | 0.2186 |
Total loss along flue gases (QLf) | 4.2 | 2.88 | |
9 | Combustion efficiency (%) | 76.27 | 83.74 |
10 | Energy absorbed by stove body | 4.480 | 3.538 |
11 | Energy absorbed by pan body | 2.1988 | 2.1988 |
12 | Energy absorbed by other stove parts | 1.624 | 2.793 |
Total stored energy | 8.303 | 8.53 | |
13 | The energy utilized to bake injera | 3.505 | 3.421 |
14 | Unaccounted losses | 10.352 | 10.849 |
15 | Energy recovered by auxiliary stove (Qaux) | 0.24 | 0.196 |
The Mirt stove system stored 0.942 MJ more energy than the new one. Improved stove experiences more heat loss underneath the bed due to the wideness of the stove bed on which the stove was rested on and trapped less energy by an auxiliary stove. This was due to less temperature reaching the stove since the flue gas had lost some energy to the wall during the channeling path. As seen from the table, the new stove reduces the heat loss through the stove body and the flue gas by 1.84 MJ (56.79%) and 1.323 MJ (31.43%) as compared with the Mirt stove which was one of the main concerns.
The flow chart presented in Figure 10 shows the percentage loss of energy in the new stove (N) and Mirt stove (M).

As seen from Figure 10, the loss through the stove system (wall surface, pan cover, stove bed, and pan edge) and flue gas in the Mirt stove was higher than in the improved stove. The thermal storage in the stove bed was higher in the new stove than in the Mirt stove because the new stove was wider than in the Mirt stove. The flue gas loss was higher in the Mirt stove than in the new stove. The CE of the improved stove was greater than the Mirt stove. It was found that the Mirt stove stored more energy as thermal inertia than the improved stove. This was due to the insulation arrangements made and the stove material selection. The new improved stove utilized a higher percentage of energy released from dry wood than the Mirt stove. The new stove experiences more unaccounted losses than the Mirt stove. This energy was expected to be used in vaporizing the new stove’s body water content.
3.5. Gas Emissions
From the stove analysis, it was observed that the thermal performance of the stove was improved, which led to a decrease in fuel consumption and a reduction of gas emissions. Estimating the emission factor in this work involves computing the total number of moles of the respective combustion gases when a fuel is completely burned. The minimum fuel saved, 0.032 kg/injera (7.83%), was taken for emission estimation. As a reference, a family of five members was expected to bake 3120 pieces of injera annually (Liyew n.d.). So 3120 injera∗(0.4906 − 0.4586) kg of fuel/injera = 99.84 kg of fuel was saved annually.
GHG emission = (112 t CO2/TJ) ∗ saved fuel ∗ LHV (TJ): greenhouse gas emissions were reduced by approximately 0.198 t CO2/year. The existing Mirt stove released CO into the kitchen room, while the new stove kitchen room was assumed to be zero, as if the chimney had taken the gases out to the atmosphere. In comparison, a reduction of 0.935% of CO release into the atmosphere was achieved. However, the combustion flame temperature would not be able to produce nitrogen oxide products. Equation 35 yields a reduction of 5.904–9.032 ppmv (NOx to NO). This result will not give a guarantee since the calculation is not instrumental rather it was a theoretical analysis.
4. Conclusions
Ethiopia’s SDGs are being achieved through the improvement of cook stoves, particularly the injera baking stove. Recent design modifications aim to improve the heat transfer efficiency and overall performance, addressing sustainability challenges. The new improved stove achieved higher thermal efficiency, reduced fuel consumption, and cooking time, while also reducing emissions. The stove’s CE was 83.74% and 74.26%, with a burning rate of 7.848 and 7.416 kg within an hour, respectively. This reduction in fuel consumption is equivalent to a 0.198 t CO2/year reduction in greenhouse gas emissions.
However, the improved Mirt stove design has a potential for scalability across Ethiopia due to its adaptability to different fuel types and cooking styles. However, it may require increased maintenance costs, operational complexity, reliance on nonlocal materials, and limited accessibility in rural areas. Addressing these potential drawbacks is crucial to ensure the benefits of the stove outweigh the costs and challenges associated with its adoption.
Conflicts of Interest
The authors declare no conflicts of interest.
Funding
No funding was received for this research.
Open Research
Data Availability Statement
The data that support the findings of this study are available on request from the corresponding author. The data are not publicly available due to privacy or ethical restrictions.