Development of Li-Coated NiO Catalyst for Enhanced Alkaline Oxygen Evolution Reaction
Abstract
Oxygen evolution reaction (OER) properties of nickel oxide electrodes are improved by the transition of its oxidation state due to lithium incorporation. The high solubility of Li into the NiO electrode lattice structure synergistically enhances the average oxidation state of Ni3+/2+ ions, improving the reaction kinetics on active sites. The optimal incorporation level of Li into NiO is found to be 10 wt.%. The cobalt and lanthanum coating catalysts exhibited inherent properties without synergistic improvement. The electrochemical analysis results using a rotating disk electrode (RDE) system indicated the lowest OER overpotential for 10 wt.% Li-incorporated catalyst (480 mV), compared with Co-coated (534 mV) and bard NiO (696 mV) catalysts. The obtained results are expected to improve the reaction kinetics of oxygen evolution catalysis using nickel oxide-based catalysts, specifically for clean and sustainable hydrogen production via alkaline electrolysis.
1. Introduction
The production of hydrogen through a clean and sustainable process is attracting attention for its potential applications in diverse energy storage and conversion systems [1, 2]. Catalytic materials for the oxygen evolution reaction (OER) play a key role in the development of electrolysis cells, water splitting, and metal–air batteries [3, 4]. The catalytic properties of the OER tend to be sluggish due to the four-electron involved reaction steps, which decrease the reaction kinetics with high overpotential [5, 6]. Noble metal-based OER catalysts, including IrO2, RuO2, and Pd, have been widely considered to enhance the OER activity in both acid and alkaline electrolyte systems [7–9]. These noble metal catalysts exhibit excellent electrochemical properties; however, their high cost and scarcity limit their practical applications [10, 11].
Transition metal and its oxide-based catalysts could be feasible candidates to overcome these limitations [12–15]. Nickel-based electrocatalysts are considered a promising alternative to conventional noble metal OER catalysts due to their affordable cost, catalytic activity, and durability. The Ni-based OER catalysts have been extensively studied to improve their inherent properties for the development of heterogeneous OER catalysis in the form of oxides, metal alloys, or layered hydroxides [16–21].
Several studies on Ni-based OER catalysts have reported synergistic improvements in their catalytic properties through nanoscale surface coating or heterogeneous cation doping inside the NiO lattice structure [22–25]. Doping of metal cations with different ionic size and valence state provides additional active sites for enhancing OER activity. The Li+ ion doped into NiO significantly improves the OER performance through modifying the electronic structure of catalyst for fast OER kinetics [26, 27]. The doping of Li+ ions increases the average oxidation state of Ni ions (Ni2+ to Ni3+), which is regarded as the more favorable for alkaline OER. The surface modification of NiO catalysts with diverse metal oxides facilitates electrical conductivity and electrochemical active surface area (ECSA), thereby improving charge transfer kinetics. These synergistic effects are primarily attributed to the controlled surface adsorption and desorption energies between reaction species, which significantly enhance the reaction characteristics [5, 28, 29].
In this work, we prepared nanosized Li, Co, and La surface coating on bare NiO via wet chemical coating and following sintering method to investigate the effect of heterogenous doping and synergistical performance improvement between host Ni ions and coating metal elements. The doped Li+ ions inside the NiO lattice structure successfully reduced the OER overpotential in an alkaline electrolyte system, by constructing the Ni3+-rich phase on the NiO catalyst. The Li+ ion doping also created an additional hole state near Fermi level, which facilitates the surface chemisorption of reaction intermediates. The Co and La coating sample only exhibited their inherent OER characteristics without synergistical improvement between NiO catalysts. The results obtained here suggest the possible utilization of Li+ doping in design of advanced Ni-based OER catalysts for diverse energy conversion systems, specifically for sustainable hydrogen production via water splitting or alkaline electrolysis.
2. Experimental
2.1. Material Preparation
All the catalysts were prepared through conventional powder infiltration process. The fine NiO (Kojundo) powder was first stirred and dispersed in a deionized water and ethanol (1:9 vol.%) solution with 30 min of ultrasonication. The stoichiometric amounts of La(NO3)3·6H2O (Sigma Aldrich, 99.99%), Co(NO3)2·6H2O (Sigma Aldrich, 99.8%), and LiNO3 (Sigma Aldrich, 99.99%) were mixed with the NiO suspension under stirring condition. The loading amounts of each metal nitrate was determined to be 1, 3, 5, 10, and 15 mol.% relative to the NiO powder. The urea (Sigma Aldrich, 99.0%) was also used to improve the dispersion of nanometal coating on the NiO surface. The loading amounts of urea was 10 times higher than the concentration of cations from the metal nitrates. The coating solutions were dehydrated on a stirring plate at 60°C for 24 h. The dehydrated powders were then calcinated at 650°C for 12 h to remove the organic residuals and to provide enough driving forces for cation diffusion between the NiO lattice structure and coating metals. The prepared catalytic materials were ground and sieved (200 mesh) before the electrochemical test.
2.2. Material Characterization
Structural characteristics of the prepared catalytic materials were determined by HR-XRD (Smart Lab., Rigaku) in a range of 10°–90°. The Rietveld refinement method was employed to analyze the structural differences before and after surface coating processes. The FE-SEM (JSM-7800F, JEOL), HR-TEM, and EDS were utilized to examine the morphological and chemical properties of the surface coating. The ICP-OES (iCAP Q, Thermo) method was used to investigate the concentration of Li after the coating processes. The surface chemical composition and adsorption properties were analyzed with XPS (ULVAC, PHI 5000) before and after surface coating.
2.3. Electrochemical Analysis
The electrochemical characteristics of the prepared samples were measured using a rotating disk electrode (RDE) system (RRDE-3A, ALS). A glassy carbon electrode (GCE), Pt wire, and Hg/HgO (1 M NaOH) were used as the working, counter, and reference electrodes, respectively. The N2-purged 0.1 M KOH (Sigma Aldrich, 99.99%) solution was used as an alkaline electrolyte. The catalyst suspension ink was composed of catalytic materials (4 mg), conductive carbon (6 mg, Vulcan XC72R), Nafion solution (70 uL, Sigma Aldrich), and isopropyl alcohol (1 mL). The ECSA before and after each coating material was determined by measuring double-layer capacitance via cyclic voltammetry (CV) at different scanning rates. The oxygen evolution reaction (OER) and oxygen reduction reaction (ORR) characteristics were evaluated in O2-saturated 0.1 M KOH electrolyte system at a scanning rate of 10 mV/s and a rotating speed of 1600 rpm. The redox stability of the prepared catalysts was evaluated by CV method for 100 cycles of OER and ORR redox reactions.
3. Results and Discussion
3.1. Material Characteristics
Figure 1 shows the XRD and Rietveld analysis results for the prepared catalysts after surface coating with Li, Co, and La. All the samples exhibit the diffraction peaks position of the NiO structure (JCPDS, No. 04-0835), which correspond to (111), (200), (220), (311), and (222) planes [30]. The Li and Co coating samples on the nickel oxide support were synthesized without any secondary phases following the heat treatment at 650°C. Figure 1a indicates the XRD patterns of Li-coated NiO samples from 1 to 15 mol.% concentration. The NiO diffraction peaks are slightly shifted to a higher angle as the concentration of Li increases. This observation arises from the substitution of surface coated Li inside the NiO lattice structure, which leads to a shrinkage of the lattice structure [31, 32]. The Co coating samples showed a peak shift to a lower diffraction angle as the surface Co coating is increased (Figure 1b). This result suggests an ionic exchange between surface Co and Ni. The slightly larger ionic radius of Co2+ (0.72 Å) compared to Ni2+ (0.69 Å) leads to an expansion of the lattice parameters of the supporting NiO structures [33]. The diffraction patterns of La coating samples suggest the formation of the LaNiO3 (JCPDS, No. 34-1028) phase with (110), (021), and (122) facets (Figure 1c) [34, 35]. The La2O3 phase (JCPDS, No. 05-0602) also appears as the concentration of La exceeds 10 mol.% (Figure 1c). These tendencies originate from the different thermodynamic characteristics between lanthanides and transition metals in relation to NiO [36]. Figure 1d illustrates the calculated lattice volumes of the prepared catalytic materials via Rietveld refinement method. The NiO support prior to surface coating processes was also investigated for comparison (Figure S1). The reference NiO support shows the lattice volume of 72.873 Å. The Li-coated samples showed a decrease in their lattice volume from 72.807 to 71.016 Å for 1 mol.% and 15 mol.% Li coating, respectively. The lattice volume of Co coating sample illustrates a lattice expansion from 72.937 to 73.068 Å for 1 mol.% and 10 mol.% of its coating ratios, respectively. After a 10 mol.% Co coating, the lattice constant of NiO support appears to have saturated, regardless of the Co concentration (Figures S2–S4). These results suggest that the maximum Co doping level inside NiO is limited to 10 mol.%. The lattice constant of NiO with surface La coating catalysts remained constant compared to the reference NiO support before the coating process. This observation also suggests that the surface-coated La formed only the LaNiO3 and La2O3 phases without substitution into the NiO lattice structure.
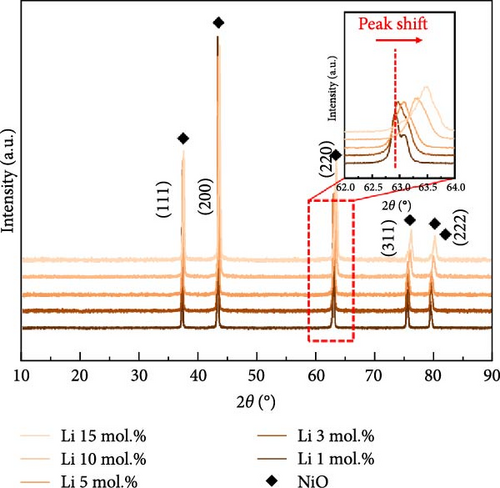
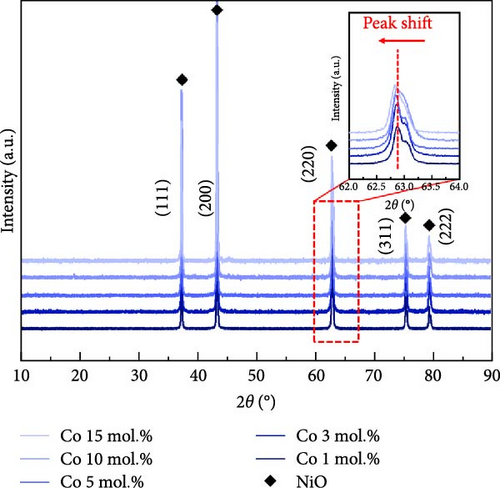
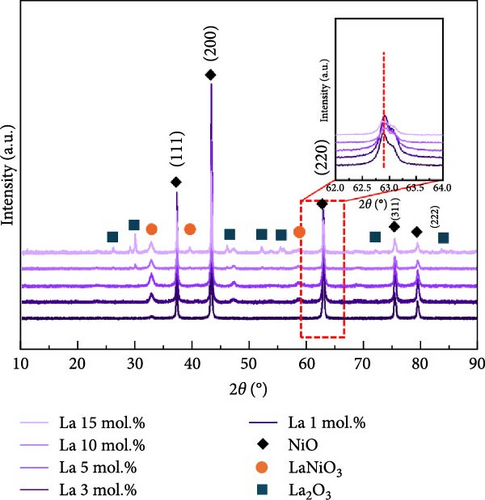
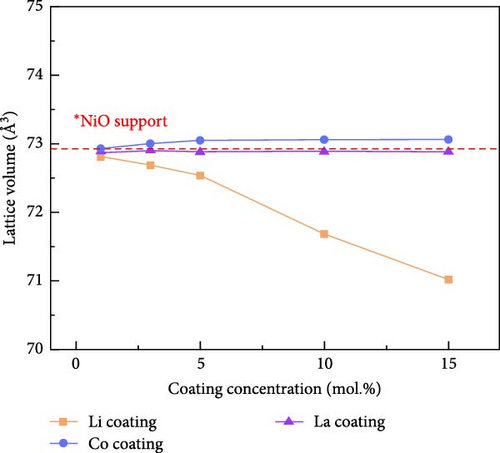
Figure 2 illustrates the XPS spectra of the prepared catalytic materials with 10 mol.% of Li, Co, and La nanoparticles. All the elements of Ni, Co, La, and O were detected in the survey spectra at ~853, 797, 852, and 530 eV, respectively (Figure 2a). Figure 2b illustrates the La3d, Co2p, and Li1s spectra of La 10 mol.%, Co 10 mol.%, and Li 10 mol.% coated samples, respectively. All the prepared samples exhibit the surface coated chemical species in the binding energy region at ~835 eV (La 3d3/2), ~782 eV (Co 2p3/2), and ~83 eV (Li 1 s), indicating the successful surface deposition of metal coating on the NiO support. Figure 2c exhibits the deconvolution of Ni2p spectra with increasing Li coating ratios from 5 to 15 mol.%. Due to the limited number of core-level electrons in Li ions, characterizing their chemical state via XPS is challenging. The surface chemical investigation of prepared samples, therefore, was mainly conducted by deconvolution of Ni2p spectra. The binding energy region of the Ni2p spectra could be deconvoluted into Ni2+ peaks for 853.6, 871.5 eV, and Ni3+ peaks for 855.1, 873.4 eV, respectively [37, 38]. The calculated Ni2+/Ni3+ ratio tends to decrease as the concentration of Li is increased. The Ni2+/Ni3+ ratio of the NiO support before Li coating was 0.66, while the Li 5, 10, and 15 mol.% coating samples were 0.39, 0.37, and 0.35, respectively. This observation implies the successful doping of Li+ ions into the NiO lattice structure, which causes the transition of Ni2+ to Ni3+ (Table S4). The O1s peaks of the 10 mol.% Li-, Co-, and La-coated samples were also analyzed for further investigation. The O1s binding energy was deconvoluted for lattice oxygen (OLatt., ~529.1 eV), oxygen vacancy (OVac., ~530.6 eV), and surface-adsorbed oxygen (OH−, ~531.5 eV), respectively (Figure 2d). The bare NiO support without any coating showed the lowest OH−/ (OLatt.+OVac.) ratio of 0.13, while the 10 mol.% Li-, Co-, and La-coated samples depicted 0.17, 0.21, and 0.42, respectively (Table S5). The higher concentration of OH− species on the surface can be considered a prerequisite for OER catalysts, as the surface-adsorbed OH− ions play a key role in oxygen evolution steps under alkaline electrolyte conditions [39, 40]. The results obtained suggest that the surface coating with Li, Co, and La could be a feasible approach for improving OER catalytic activity in NiO-based catalytic materials.
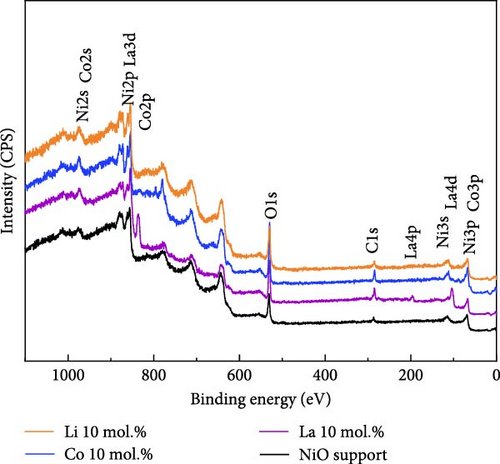
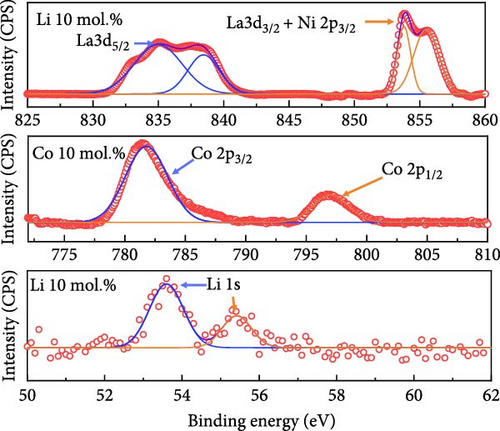
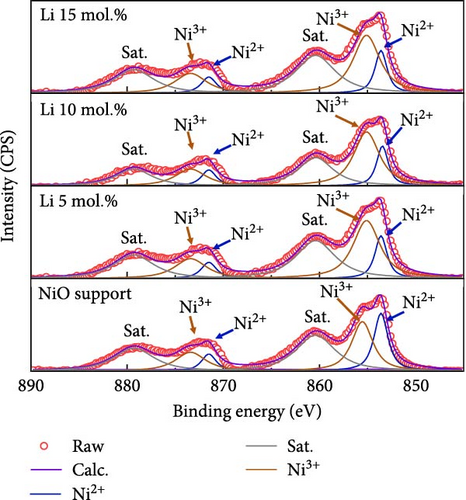
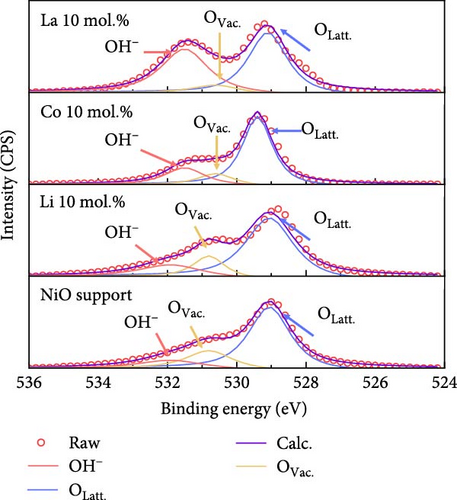
Figure 3 shows the SEM images of catalysts coated with Li, Co, and La at different coating concentrations. The average diameter of supporting NiO powder was ~3.5 μm after calcination at 650°C for 12 h. The nanosized Li, Co, and La oxides were homogenously distributed on the surface of NiO when the coating ratio exceeded 3 mol.%. The 1 mol.% coated Li, Co, and La samples showed the limited surface coating on the NiO support after the calcination processes. This observation implies that the coating concentration needs to be higher than 3 mol.% to achieve a highly distributed surface coating. When the coating ratio exceeds 15 mol.%, the supporting NiO particles are fully covered by the nanosized Li, Co, and La oxide particles. The surface distribution of Co and La was also investigated using SEM/EDS (Figures S5–S6). Unfortunately, the investigation of Li ions via EDS method is limited due to their low atomic number. The EDS mapping results of Co and La coating sample indicate that the Co and La oxide on the NiO support do not exhibit significant agglomeration after coating and high-temperature calcination (650°C). The TEM/EDS analysis of 10 mol.% La and Co coating sample also indicates the highly distributed La and Co on the surface of NiO support (Figure S7).
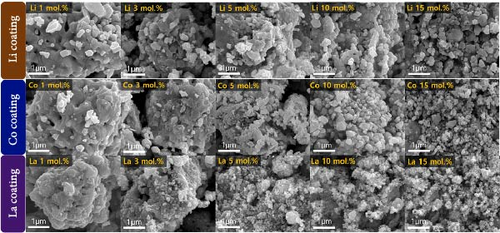
The chemical composition of each sample is illustrated in Figure S8. The chemical composition of the Li-coated samples was analyzed by using the ICP-OES method at different doping ratios. The concentration of Li relative to Ni was 1.58, 4.31, 6.09, 13.12, and 16.02 mol.% for Li coatings of 1, 3, 5, 10, and 15 mol.%. These results indicate that the Li coating concentration on NiO was precisely controlled. The concentration value of Co and La showed relatively higher value than the Li samples. The calculated Co concentrations in the Co-coated catalysts were 1.15, 3.11, 6.01, 14.86, and 24.05 mol.% relative to Ni ions. The calculated La concentration also exhibited higher values than the coating ratios, with 1.25, 5.17, 9.74, 19.28, and 26.09 mol.% for the 1, 3, 5, 10, and 15 mol.% coating samples, respectively. These results probably originated from the lower solubility of Co and La in the NiO lattice structure, which led to a higher surface concentration of these elements on the NiO support compared to the Li-coated samples. A coating ratio higher than 15 mol.% appears to cause overcoating on the NiO support, which probably leads to additional overpotential due to the mass transport limitations.
3.2. Electrochemical Properties
Figure 4 illustrates the OER and ORR properties of Li-, Co-, and La-coated catalysts with different concentrations. The ORR is regarded as a reverse reaction of OER, which electrochemically reduces the oxygen molecules to oxygen ions. The reversibility between OER and ORR activity enables its utilization in reversible fuel cells and electrolysis cell application. The electrochemical analysis of the prepared samples for both OER and ORR was conducted to investigate its possible utilization on reversible systems. The schematic illustrations of OER and ORR mechanisms are shown in Figure S9. The Li-coated samples show improved OER properties as the coating ratio increases from 1 to 10 mol.%. The Li-coated samples exhibit sluggish overpotential when the coating concentration exceeds 15 mol.% (Figure 4a). This observation likely originates from the overcoating of Li on the NiO surface, which limits the electrochemically active site on the NiO surface and impairs mass transport steps at high current region. The higher Li coating sample (Li 15 mol.%) also exhibits ferromagnetic properties due to the increased Ni3+ ions, which cause the possible agglomeration [41, 42]. The Co-coated samples indicated enhanced OER characteristics as their coating concentration increased from 1 to 15 mol.% (Figure 4b). These results are attributed to the inherently higher OER activity of Co oxide-based catalytic materials, which provide additional OER active sites on the surface of the NiO support after coating. The enhancement of catalytic properties in Co-coated samples is further supported by the polarization curve for the ORR. The Co-coated samples also showed improved ORR performance as their coating concentration increased (Figure 4e). Other coating elements exhibited no significant differences with varying surface coating ratios (Figure 4d,f). This observation suggests that the oxygen redox activity of Co-coated samples is primarily related to the amount of surface-dispersed Co oxide rather than a synergistic effect between the NiO support and the Co oxide. The La-coated samples showed minimal improvement in OER properties. While low concentration La coating slightly enhanced the OER performance compared to the reference NiO support, higher La coating ratios (La 10 and 15 mol.%) degraded the OER performance (Figure 4c). This observation is attributed to the formation of LaNiO3 and La2O3 on the surface of NiO support materials, as shown in Figure 1a. The formation of the LaNiO3 phase on the surface could partially enhance the OER catalytic activity, due to the inherent OER catalytic activity of the LaNiO3 perovskite oxide [34, 35]. The catalytically inert La2O3 phase in the high La coating samples (La 10, 15 mol.%) probably degraded the OER performance.
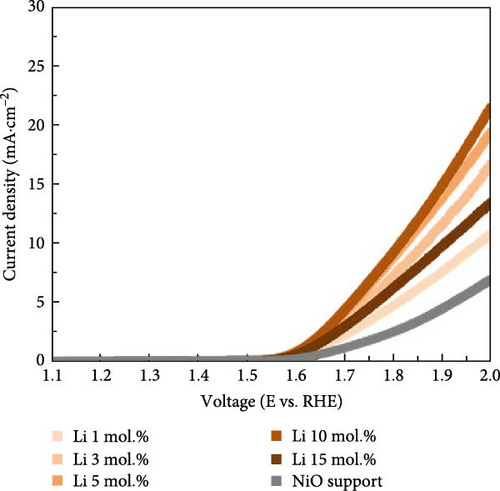
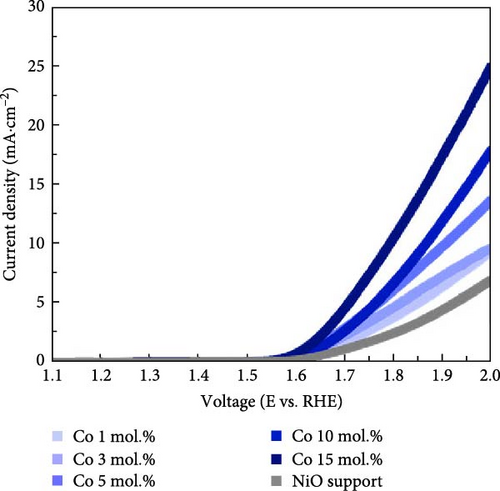
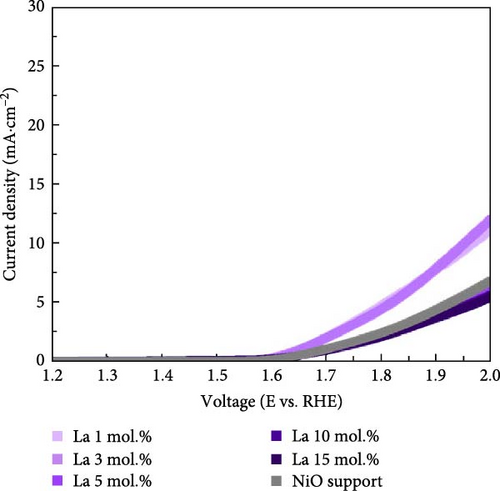
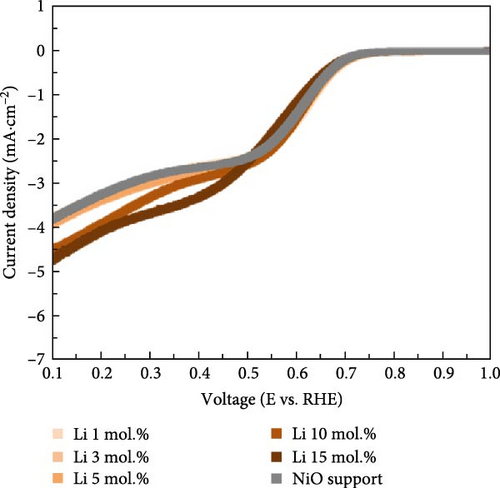
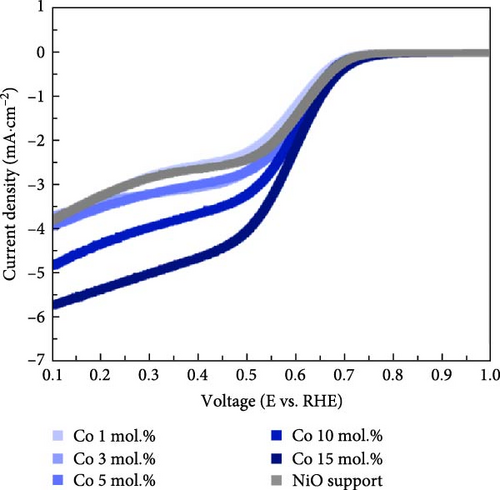
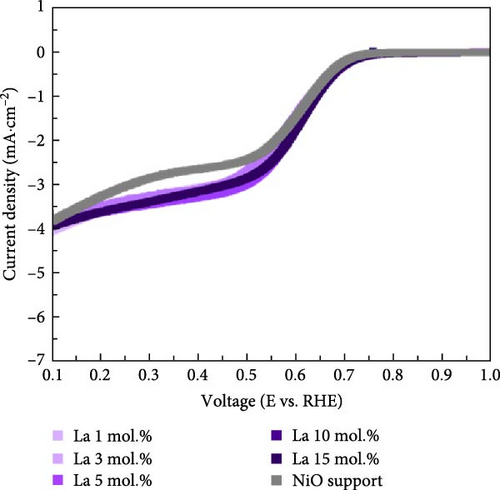
Figure 5a exhibits the electrochemical OER polarization curves for La 10 mol.%, Co 10 mol.%, Li 10 mol.%, and Li 3 mol.% + Co 10 mol.% coating catalysts, as well as the reference bare NiO support. The Li 3 mol.% + Co 10 mol.% (Li–Co dual coating) sample was also prepared to investigate the synergistic effect of Li and Co on the NiO support. The Li 10 mol.% coating sample showed the smallest overpotential of 480 mV, whereas the Co-, Li–Co-, La-coated, and reference NiO samples showed 534, 506, 739, and 696 mV, respectively. The Li 3 mol.% and Co 10 mol.% dual coating sample demonstrated enhanced OER performance compared to the Co 10 mol.% coating sample. Although the dual coating sample showed a slightly higher overpotential than the Li 10 mol. % coating sample, its polarization curve surpasses the Li 10 mol.% sample in the high current density region. This result indicates that the Li coating on the NiO support could also enhance electrical conductivity, which is crucial for electrochemical catalysis.
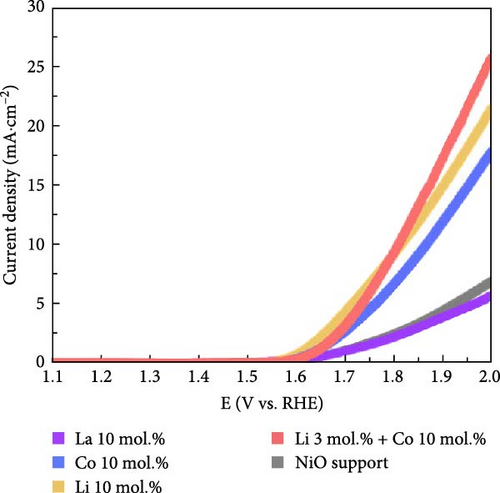
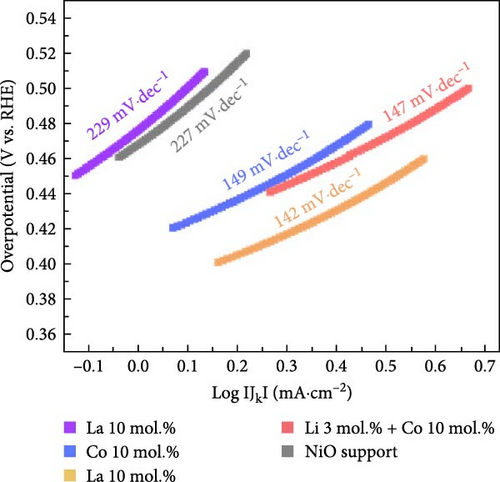
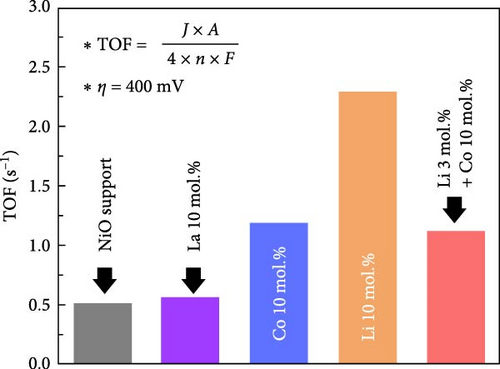
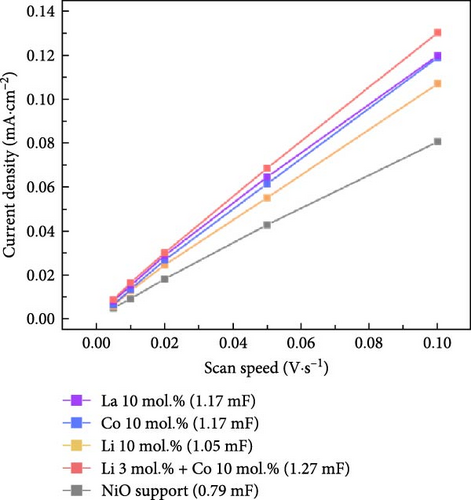
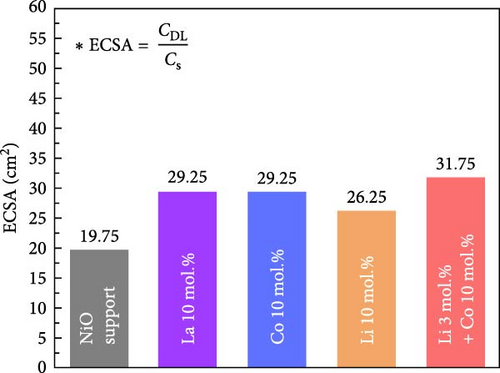
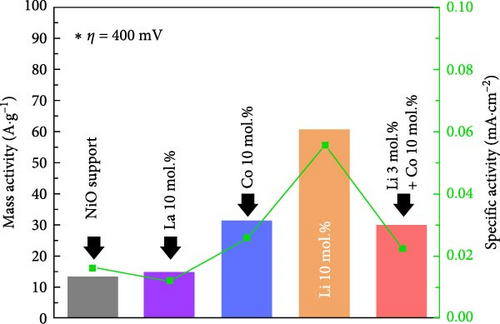
The Li 10 mol.% coating sample also showed the lowest Tafel slope of 142 mV dec−1, while the Co and Li–Co dual coating sample exhibited slightly higher values of 149 and 147 mV dec−1, respectively. The La coating and NiO support samples exhibited much higher Tafel slope of 229 and 227 mV dec−1 in the activation potential region (Figure 5b). This observation indicates that the reaction kinetics of the catalysts are improved through surface Li and Co coating. Figure 5c shows the calculated turnover frequencies (TOFs) of the prepared catalysts at an overpotential of 400 mV. The Li 10 mol.% coating sample exhibited the highest TOF value of 2.30 s−1, while the Co 10 mol.% and Li–Co dual coating samples showed 1.19 and 1.12 s−1, respectively. The La 10 mol.% and NiO support samples exhibited much lower values of 0.51 and 0.57 s−1. These results further support the improved reaction kinetics of Li 10 mol.% coated sample compared to the other catalytic materials. The overall TOF values of prepared samples are illustrated in Figure S10.
The electrochemical stability of Li 10 mol.% coated NiO sample was investigated under cyclic OER and ORR test (Figure S11). The Li 10 mol.% sample exhibited slightly improved OER characteristics after 100 times of redox cycle without performance degradation. The slightly reduced overpotential and the increased current density are believed to originate from the possible activation of OER active sites or removal of surface residuals (Figure S11b). The ORR property was slightly degraded after the cyclic test (Figure S11c). The degradation in ORR property is probably caused by surface oxidation of the catalytic materials, which is more favorable for OER and less optimal for ORR. The electrochemical performance is also significantly influenced by the active surface area; therefore, the ECSA of the prepared catalytic materials was investigated, as shown in Figure 5d–e. The detailed calculations of the double-layer capacitances and ECSA values are illustrated in Figure S12. The calculated double-layer capacitance (CDL) and ECSA values for the bare NiO support were 0.79 mF and 19.75 cm2, respectively. The Li–Co dual coating sample showed the highest CDL (1.27 mF) and ECSA (31.75 cm2) values. The La 10 mol.% and Co 10 mol.% samples showed the same CDL (1.17 mF) and ECSA (29.25 cm2). The Li 10 mol.% coating sample exhibited slightly lower CDL (1.05 mF) and ECSA (26.25 cm2) than other coating samples. The results indicate that the surface coating process could successfully improve the active surface area compared to the bare NiO support. The slightly lower CDL and ECSA values of the Li 10 mol.% sample could be attributed to its higher diffusivity and solubility within the NiO lattice structure, which reduces the amount of Li present on the surface. The overall ECSA values of all prepared samples are listed in Table S6 for better comparison.
Figure 5f illustrates the mass and area specific activity of the prepared catalyst at an overpotential of 400 mV. The Li 10 mol.% sample showed the highest mass activity (60.64 A g−1) and specific activity (0.055 mA cm−2), while the Co 10 mol.% and Li–Co dual coating samples indicated (31.46 A g−1, 0.026 mA cm−2) and (29.66 A g−1, 0.022 mA cm−2), respectively. The La 10 mol.% coating and bare NiO sample showed the similar values of (14.90 A g−1, 0.012 mA cm−2) and (13.43 A g−1, 0.016 mA cm−2), respectively. The obtained results also support the inherently improved OER properties of the Li coating sample compared to the other catalysts. The performance comparison tables of OER and ORR using similar chemical compositions is shown in Tables S7 and S8, respectively.
3.3. Effect of Li Coating on Bare NiO Support
The aforementioned electrochemical analysis results indicate that the Li coating on the bare NiO support effectively enhances the OER properties in an alkaline electrolyte system. A fundamental and mechanistic understanding of this improvement is essential for further optimization of OER catalysis. The OER mechanism in alkaline solution is illustrated in Figure S9a. In the adsorbate evolution mechanism (AEM), the four-electron involved electrochemical reaction proceeds with the surface adsorption and desorption of hydroxyl ( ∗OH−) ions. The increased electronic conductivity and interconnectivity between catalytically active materials could improve OER efficiency, which plays a crucial role in electrochemical catalysis. Furthermore, the Li coating on NiO increased the average oxidation state of Ni2+ ions to Ni3+ due to the interdiffusion of surface-coated Li into the NiO lattice structure. The Ni3+-rich surface on Li-coated NiO catalysts is believed to facilitate the surface chemisorption of ( ∗OH−) ions under potential applied conditions, resulting in improved OER properties [43–45]. According to Sabatier’s principle, the adsorption between the reaction intermediates should be optimized for heterogeneous catalysis [46, 47]. The electronic structure of high oxidation state of Ni3+ (t2g6, eg1) is considered an efficient active site for OER compared to that of Ni2+ (t2g6, eg2), which facilitates the adsorption and desorption of reaction intermediates with optimized surface adsorption energies (Figure S13). The transition of surface electronic structure is also believed to improve the OER performance of Li+ ion doped NiO catalysts. The Li ion doping not only increases the concentration of Ni3+ ions but also creates a hole state near the Fermi level through hybridization between Ni3d eg and O2p orbitals (Figure S13a). The formation of hole state and lower Fermi level facilitates the adsorption of reaction intermediates, improving the overall OER performance of Li doped NiO catalysts. The optimized surface concentration of Ni3+ and the subsequent hole state formation via Ni 2p and O 2p hybridization, therefore, are believed to primarily improve the overall OER performance of the Li-coated NiO catalyst.
4. Conclusion
In summary, the surface of bare NiO support was decorated with highly dispersed Li, Co, and La nano-oxides by wet chemical coating processes to enhance its inherent alkaline OER performance. The surface coating of Li and Co successfully increased both the ECSA and the electronic conductivity. The surface-deposited Li exhibited high interdiffusivity and solubility within the NiO lattice structure, increasing the concentration of Ni3+ ions through the substitution of Li+ ions. The Co and La coating samples showed only inherently induced OER characteristics without significant synergistic effect with bare NiO support. The optimal coating concentration of Li was determined to be 10 mol.%. The Li 10 mol.% coating catalyst exhibited the lowest overpotential of 480 mV, while the bare NiO showed an overpotential of 696 mV at 5 mA cm−2 current density. The Li 10 mol.% sample also exhibited improved OER kinetics with the smallest Tafel slope of 142 mV dec−1, compared to Co 10 mol.% (149 mV dec−1) and bare NiO (227 mV dec−1). The synergistic effect of Li ions within the NiO tailored the electronic structure of host Ni ions from Ni2+ (t2g6, eg2) to Ni3+ (t2g6, eg1), thereby facilitating the overall OER processes. The results obtained in this study are believed to be utilized for various energy conversion and storage systems, specifically for clean and efficient hydrogen production via electrochemical alkaline electrolysis.
Conflicts of Interest
The authors declare no conflicts of interest.
Funding
This research was supported by the Korea Institute of Energy Technology Evaluation and Planning (G032542411) and Incheon National University Research Grant in 2020.
Acknowledgments
This study was supported by the Korea Institute of Energy Technology Evaluation and Planning (KETEP) grant funded by the Korea government (MOTIE) (G032542411) and Incheon National University Research Grant in 2020.
Supporting Information
Additional supporting information can be found online in the Supporting Information section.
Open Research
Data Availability Statement
The data that support the findings of this study are available from the corresponding author upon reasonable request.