Effect of Surface Roughness on the Squeeze Film Characteristics of Circular Plates in the Presence of Conducting Couplestress Fluid and Transverse Magnetic Field
Abstract
The combined effect of surface roughness and magnetic field on the performance characteristic of the circular plates lubricated with conducting couplestress fluid (CCSF) has been studied. On the basis of the Christensen Stochastic model, the generalized stochastic Reynold’s equation is derived. Modified equations for the nondimensional pressure, load load-carrying capacity, and squeeze film time are derived. The results are presented both numerically and graphically and compared with conducting smooth surface case. It is observed that the surface roughness effects are more pronounced for couplestresses as compared to nonconducting Newtonian fluid (NCNF) in the presence of magnetic field.
1. Introduction
In recent years, the characteristics of Magnetohydrodynamics (MHD) in flow analysis are important for many engineering and industrial applications. The MHD bearings with conducting fluids possess the high thermal-conductivity and high electrical-conductivity features over the conventional bearings. The squeeze film lubrication for different configuration of bearings under the action of transverse magnetic field has been discussed by several authors [1–6]. Stochastic model for hydrodynamic lubrication of rough surfaces is studied by Christensen [7]. The combined effect of MHD and surface roughness has been studied by many authors [8–11] and it is found that effect of surface roughness in the presence of transverse magnetic field is significant on the squeeze film characteristics of the bearings.
It is known that the theory of couplestress fluid by Stokes [12] is a generalization of viscous fluid theory with couplestresses and body couples. Couplestress fluids are consequence of the assumption that the interaction of one part of the body on another across a surface is equivalent to a force and momentum distribution. It consists of rigid randomly oriented particles suspended in a viscous medium such as electrorheological fluids and synthetic fluids. Many studies have investigated the effect of couplestress on the squeeze film lubrication in the presence of transverse magnetic field [13–15]. The MHD bearings with conducting fluids possess numerous advantages over the conventional bearings.
Recently, Lin et al., [16] studied hydromagnetic non-Newtonian cylindrical squeeze film and its application to circular plates by derivation of modified lubrication equation. They found that the improved characteristics are further emphasized for circular plates operating with a larger magnetic field parameter and non-Newtonian parameter.
The effect of surface roughness on MHD conducting couplestress squeeze-film characteristics between the circular plates has not been studied so far. Hence, in this paper, an attempt has been made to study the combined effect of surface roughness and conducting couplestresses on the MHD squeeze-film characteristics between circular plates. Expressions for the MHD squeeze-film pressure, load carrying capacity, and the time height relation are obtained. Results are compared numerically with the corresponding conventional case for different values Hartmann number M0 studied by Lin et al., [16].
2. Mathematical Formulation of the Problem
Consider a squeezing flow between two rough circular plates approaching each other with squeezing velocity V ( = dH/dt), where H is the film thickness between the two plates, p is the film pressure, u and w are the velocity components, μ is the lubricant viscosity, η is material constant responsible for couplestresses, and σ is the conductivity of the lubricant. A uniform transverse magnetic field is applied to the bearing in the Z-direction as shown in Figure 1. It is assumed that the fluid film is thin and the body forces and the body couples are negligible. The third term in (1) is a Lorentz body force coming from JyB0 under the assumption that the induced magnetic field is much less than the applied magnetic field as described by Kuzma [17]. Then, from Ohm’s law, the axial current density becomes Jy = σB0u. Therefore, the term appears in (1).
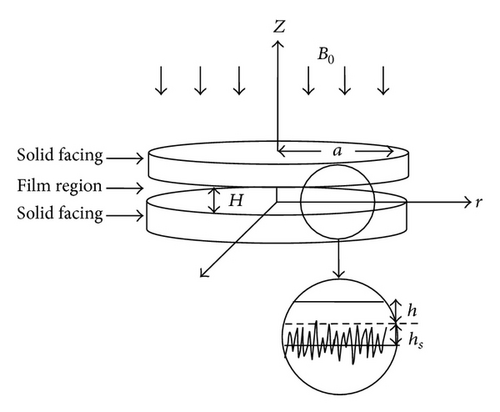
- (1)
At the lower surface, z = 0
- (2)
At the upper surface, z = H
In context of Christensen stochastic theory for the hydrodynamic lubrication of rough surfaces, two roughness patterns are considered, namely, radial roughness pattern and azimuthal roughness pattern.
2.1. Radial Roughness Pattern
2.2. Azimuthal Roughness Pattern
3. Results and Discussions
The combined effect of surface roughness and MHD on the conducting couplestress fluid lubrication between circular plates is analysed on basis of Christensen’s stochastic theory [7] for two types of roughness patterns. The squeeze film characteristics are analysed with respect to three nondimensional parameters, namely, the Hartmann number , conducting couplestress parameter l*, and the roughness parameter C.
Figure 2 depicts the variation of nondimensional mean pressure P* with the axial coordinate r as a function of the roughness parameter C with the parametric values M0 = 3, l* = 0.3, and H* = 0.4 for both roughness patterns. It is observed that, at C = 0, the radial roughness pattern coincides with the azimuthal roughness pattern. Further, the increase in P* is more pronounced with azimuthal roughness pattern as compared to radial roughness pattern. Figure 3 represents the variation of nondimensional load carrying capacity W* with H* for different values of l*. It is observed that, with the increasing of values of l*, there is significant increase in the load carrying capacity W*. The effects are more prominent for CCSF as compared to conventional NCNF. Figure 4 shows the variation of nondimensional mean load carrying capacity W* with H* for different values of M0. It is seen that increasing effect of M0 is to enhance the mean load carrying capacity for circular plates as compared to smooth plate case. Figure 5 shows the variation of nondimensional load W* with H* as a function of roughness parameter C with M0 = 3 and l* = 0.3. As seen from the figure that the load carrying capacity is significant with increasing values of roughness parameter and the effects are more prominent for azimuthal roughness pattern than those for radial roughness pattern. Variation on nondimensional squeeze film time T* with for different values of l* is shown in Figure 6. It is observed that, with the increasing of values of l*, there is significant increase in squeeze film time T*. The variation of response time T* as function is given in Figure 7 for various values of M0. It is observed that the effect of magnetic parameter is to enhance the squeezing effect for rough circular plates as compared to smooth plates. Figure 8 shows the variation on nondimensional squeeze film time T* with for different values of C. It is observed that T* increases with increasing values of C. The effects are more pronounced for CCSF as compared to NCNF. It is observed that the effect of azimuthal/radial roughness patterns is to increase/decrease T* as compared to conventional case (i.e., C = 0). The time of approach is more pronounced for azimuthal roughness patterns as compared to the radial roughness pattern.
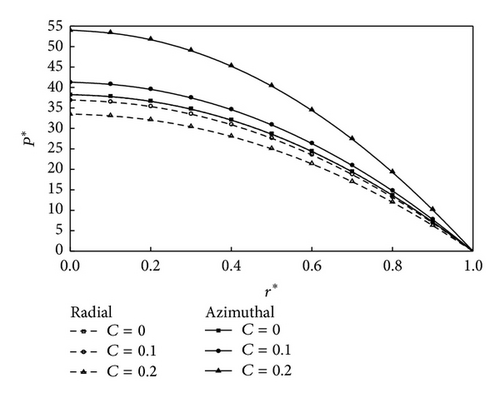
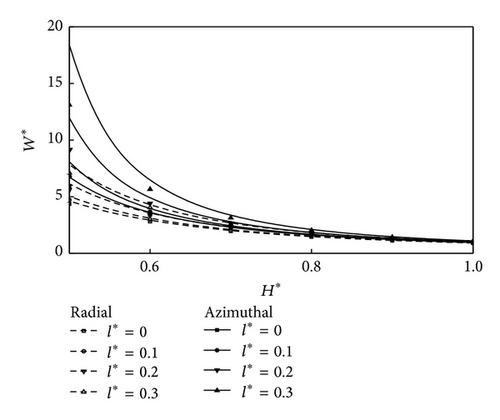
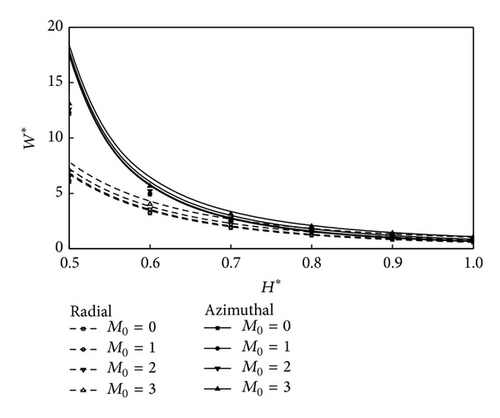
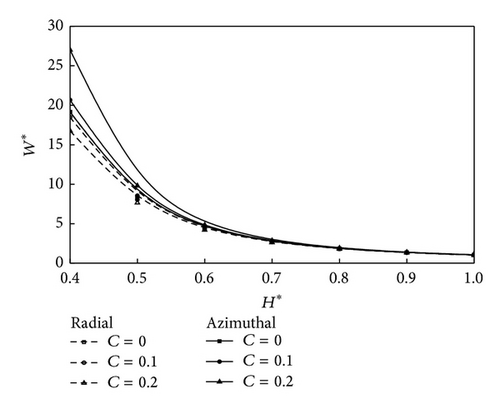
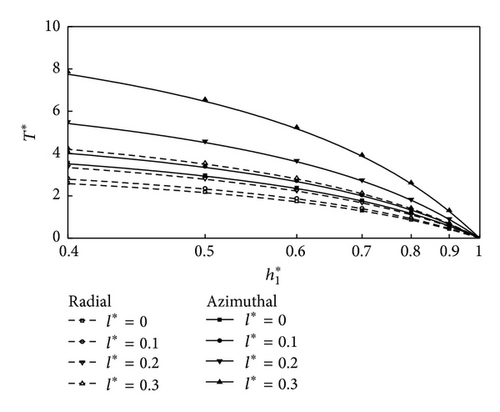
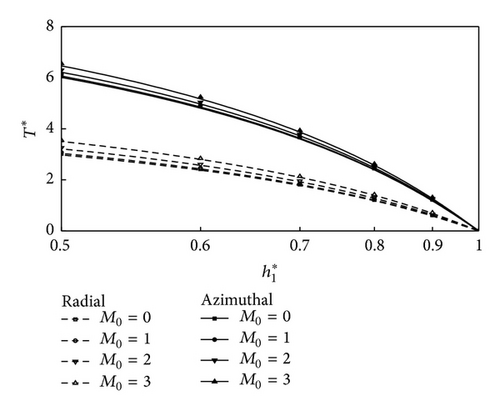
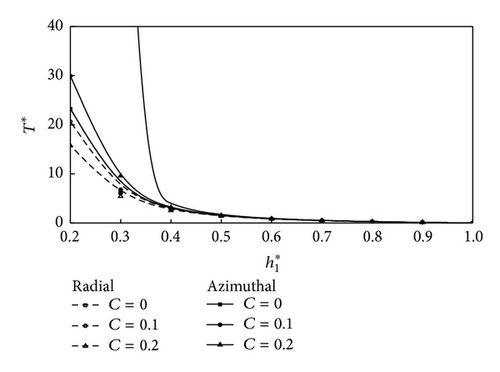
Table 1 shows the comparison between the previous analysis by Lin et al., [16] and the present analysis. It is observed from the table that there is significant increase in load and time for both the roughness patterns. An increase of 14.50%/52.28% in radial/azimuthal roughness pattern is observed for M0 = 3, C = 0.3.
Nondimensional load carrying capacity W* | Nondimensional squeezing time T* | |||||||
---|---|---|---|---|---|---|---|---|
M0 | Lin et al. [16] | Present analysis | Lin et al. [16] | Present analysis | ||||
C = 0 | C = 0.3 (radial) | C = 0.3 (azimuthal) | C = 0 | C = 0.3 (radial) | C = 0.3 (azimuthal) | |||
0 | 18.0346 | 18.0345 | 13.068 | 51.1056 | 1.1262 | 1.1262 | 1.00394 | 1.51557 |
1 | 18.1567 | 18.1566 | 13.2377 | 51.2369 | 1.15996 | 1.15996 | 1.04196 | 1.55012 |
2 | 18.5232 | 18.5231 | 13.7416 | 51.6309 | 1.26118 | 1.26118 | 1.15448 | 1.65369 |
3 | 19.1338 | 19.1338 | 14.5654 | 52.2874 | 1.42968 | 1.42968 | 1.33827 | 1.82611 |
4. Conclusions
- (i)
In the presence of a conducting couplestress fluid and externally applied transverse magnetic field, one-dimensional radial/azimuthal roughness patterns on the circular plates decrease/increase the load-carrying capacity and response time as compared to the nonconducting case.
- (ii)
As the surface asperity increases, the large amount of load is delivered in the bearing and enhances the response time of squeeze-film motion as compared to the smooth case.
- (iii)
In the limiting case, as C → 0, the result for both roughness patterns for one-dimensional circular plates can be reduced to smooth surface studied by Lin et al., [16] and the comparison is shown in Table 1.
Nomenclature
-
- a :
-
- Radius of the circular plates
-
- B0:
-
- Applied magnetic field in the z-direction
-
- c:
-
- Maximum asperity deviation from the nominal film height
-
- C:
-
- Dimensionless roughness parameter (c/h0)
-
- H:
-
- Film thickness
-
- h0:
-
- Initial film thickness
-
- h1:
-
- Film thickness at time t1
-
- :
-
- Dimensionless film thickness after time Δt
-
- hs:
-
- Stochastic film thickness
-
- M0:
-
- Hartmann number ( = B0h0(σ/μ) 1/2)
-
- l:
-
- Couplestress parameter (η/μ)1/2
-
- l*:
-
- Dimensionless couplestress parameter 2l/h0
-
- r, θ, z:
-
- Radial, angular, and axial coordinates
-
- u, v, w:
-
- Velocity components in film region
-
- E(P):
-
- Pressure in the film region
-
- P*:
-
- Dimensionless pressure
-
- t:
-
- Mean time of approach
-
- T*:
-
- Dimensionless time of approach
-
- V:
-
- Squeezing velocity (−dH/dt)
-
- W*:
-
- Dimensionless load carrying capacity .
Greek Symbols
-
- σ:
-
- Conductivity of fluid
-
- :
-
- Standard deviation
-
- η:
-
- Material constant responsible for couplestress
-
- μ:
-
- Lubricant viscosity
-
- ξ:
-
- Random variable.
Conflict of Interests
The authors declare that there is no conflict of interests regarding the publication of this paper.