An Adaptive Metamodel-Based Optimization Approach for Vehicle Suspension System Design
Abstract
The performance index of a suspension system is a function of the maximum and minimum values over the parameter interval. Thus metamodel-based techniques can be used for designing suspension system hardpoints locations. In this study, an adaptive metamodel-based optimization approach is used to find the proper locations of the hardpoints, with the objectives considering the kinematic performance of the suspension. The adaptive optimization method helps to find the optimum locations of the hardpoints efficiently as it may be unachievable through manually adjusting. For each iteration in the process of adaptive optimization, prediction uncertainty is considered and the multiobjective optimization method is applied to optimize all the performance indexes simultaneously. It is shown that the proposed optimization method is effective while being applied in the kinematic performance optimization of a McPherson suspension system.
1. Introduction
The suspension K&C characteristics have directly effects on vehicle handling and riding performances and thus gain much effort and are of great importance in vehicle development. With bush uncertainty and mechanical flexibility, it is very difficult to predict sensitivity of hardpoints locations in the kinematic performance of a suspension system as they are highly nonlinear and coupled [1, 2]. Traditional chassis developing, which benefits from the development of modern virtual prototyping technology, can now do system design effectively through some techniques, like the DOE (design of experiment) technique, as well as other experience-based attempts [3–5]. However, the mechanism of the suspension system is designed by trial and error based on the designer’s experiences and intuition, which will be time-consuming in finding a sufficiently good solution since a lot of attempts may be needed in doing virtual prototyping simulations. A featured optimization technique may be useful to give guidance through the design process.
The performance index of a suspension system is a function of the maximum and minimum values over the parameter interval [6, 7]. Thus, it is impossible to apply directly a well-developed optimization algorithm based on gradient information. It can be very difficult to evaluate the analytical design sensitivity of the hardpoints locations because the deviation is defined by using the maximum and minimum values over the parameter interval. Metamodeling techniques, which were initially developed as “surrogates” of the expensive simulation process for improving the overall computation efficiency and quality [8], are useful in such a field. Metamodel-based methods in vehicle design area mainly focused on FEM related problems [9]. Much work has been done in suspension design area, most of which focused on complex structural related area. The authors in [10] studied a mechanical analysis of a suspension optimal design for suspension system based on reliability analyses, taking into consideration tolerances and grafting a reliability analysis that applied the mean-value first order method with tolerance optimization. Choi et al. recently studied optimal design for automotive suspension systems based on reliability analyses for enhancing kinematics and compliance characteristics; they performed reliability optimization with the single-loop single-variable method by using the results from a deterministic optimization as initial values. The robust design problem was solved with 1700 analyses for 15 design variables and four random constants [11]. Recently, researches on applying metamodel-based optimization techniques to the K&C performance design of vehicle suspension systems were tried and gained reasonable good results. Kang et al. introduced a robust suspension system design approach, which takes into account the kinematic behaviors influenced by bush compliance uncertainty, using a sequential approximation optimization technique. The robust design problem has 18 design variables and 18 random constants with uncertainty [12]. After then, the team proposed a so-called target cascading method for the robust design optimization process of suspension system for improving vehicle dynamic performances [13]. The design target of the system is cascaded from a vehicle level to a suspension system level. The design problem structure of suspension system is defined as a hierarchical multilevel design optimization, and the design problem for each level is solved using the robust design optimization technique based on a metamodel. The researches above opened the way for doing suspension system optimization by using metamodel-based techniques with their effectiveness tested, which motivated us to further research along the direction. However, the former research neither considered optimizing several objectives simultaneously to make them stable in comparable intervals, nor gave the searching guidance for each design parameter in accelerating the convergence of objective parameters.
In this paper, we employ a new adaptive metamodel-based optimization approach for guiding suspension system design in determining appropriate hardpoints locations. The following characteristics distinguish the approach from other metamodel-based applications in suspension system design. (1) As we have several vehicle performance related parameters to be optimized, adaptive weighting factors are used for multiobjective optimization to ensure that all the objectives are optimized simultaneously. (2) For each iteration of the adaptive optimization, both predicted mean value and prediction standard deviation are considered in case of the system converging to the wrong optimum values. (3) We select kriging method as it is more accurate and efficient than other metamodeling methods in solving highly nonlinear problems. (4) The optimization approach provides the possible trends in selecting hardpoints locations for optimizing the system performances. We organize the paper in the following manner. Section 2 introduces the engineering requirements for the optimization problem in suspension system design. Section 3 presents the methodology of adaptive metamodel-based optimization considering modeling uncertainty. The application of adaptive optimization method in suspension system is given in Section 4. Section 5 compares the results of proposed adaptive metamodel-based optimization considering modeling uncertainty and the regular adaptive metamodeling approach. At last, Section 6 summarizes the contents of this research.
2. Optimization Problem in Suspension System
In multibody dynamics point of view, a suspension system can be classified into several groups according to the mechanical joints. In this study, we take McPherson type suspension system in consideration, which is sensitive to the kinematic performance. Figure 1 shows a kinematic structure model of a McPherson suspension system. Major components include the strut, the lower control arm, the tie rod, and the knuckle. Connections between individual components are spherical, revolute, and universal joints, as well as compliance elements such as springs, dampers, and bushings. The design purpose of this study is to determine the locations of the hardpoints according to the system kinematic performances, without considering the elastic deformations of the rigid components except for compliance elements. The commercial software ADAMS, which can easily get the suspension system performance, is employed for modeling and analyzing the suspension system.
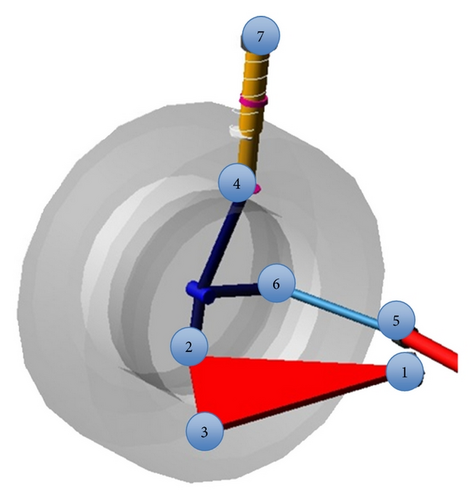
The kinematic characteristics of the system include the positions of the fixed points of the suspension system. To achieve optimal solution for suspension system, designing a good kinematic performance is the first step and we thus carry out kinematic optimization of the suspension system in this study. For that purpose, the chosen suspension performance indexes are the deviations in the camber angle, the caster angle, the kingpin incline angle, and the toe angle during the wheel stroke. Camber angle is the angle between the vertical axis of the wheels used for steering and the vertical axis of the vehicle when viewed from the front or rear. It is defined as positive when the top of the wheel moves to the outside. The camber angle alters the handling qualities of a suspension system; in particular, a negative camber angle improves grip when cornering. Caster angle is the angular displacement from the vertical axis of the suspension of a steered wheel in a vehicle, measured in the longitudinal direction. It is the angle between the pivot line (in a car, an imaginary line that runs through the center of the upper ball joint to the center of the lower ball joint) and vertical line. On most modern designs, the kingpin is set at an angle relative to the true vertical line, which is the kingpin inclination angle, as viewed from the front or back of the vehicle. The angle has an important effect on the steering, making it tend to return to the straight ahead or center position. Toe angle is the symmetric angle that each wheel makes with the longitudinal axis of the vehicle, as a function of static geometry and kinematic and compliant effects. The toe angle change plays an important role in determining the apparent transient oversteer or understeer. Positive toe is the front of the wheel pointing in towards the centerline of the vehicle. Negative toe is the front of the wheel pointing away from the centerline of the vehicle. Large errors will have a negative effect on the behavior of the chassis when braking or accelerating.
In suspension system design, the locations of hardpoints are the most important influencing factors that determine the system kinematic performances. Although engineers obtained some experiences on adjusting the locations of the hardpoints, much effort is still needed on trying different trials. Furthermore, all the geometric parameters of suspension system are coupled, which make finding the influence of the hardpoints locations on the system performances a more tough work, not mentioning there are several objectives to be determined. In this study, while determining the locations of the key hardpoints, we select the important characteristics, that is, the variations of the camber angle, the caster angle, the kingpin incline angle and the toe angle, for the objectives since they are related much to the kinematic performance. An adaptive metamodel-based optimization approach will be proposed in the next section considering modeling uncertainties.
3. Adaptive Metamodel-Based Optimization Method
3.1. Metamodeling Method
When metamodeling is used for solving specific problems, collection of sample data in specific parameter space, rather than the whole parameter space, is then required to improve the quality and efficiency. This issue is critical when expensive or extensive experiments/simulations are required to collect the sample data. Since the relationship is unknown at the beginning, initial samples are usually collected to build the initial metamodel. This developed metamodel is then used to identify the input parameters that have the best potential to lead to the expected output result. Due to the errors of the metamodel, the actual output obtained from experiment/simulation is usually different from the expected one. The previously obtained metamodel is subsequently updated to improve its quality using the new pair of input-output data. The method to iteratively modify the metamodel through an iterative sampling process is called adaptive metamodeling.
3.2. Adaptive Metamodel-Based Optimization
The process of identifying the potential optimal input parameters, obtaining the output parameter through experiment/simulation, and updating the metamodel is continued iteratively until the optimization criteria are satisfied.
3.3. Adaptive Optimization considering Modeling Uncertainty
We will formulate the specific problem for McPherson suspension system using the adaptive metamodel-based optimization considering prediction uncertainty in the coming section.
4. Adaptive Optimization considering Modeling Uncertainty in McPherson Suspension
To investigate the performance of the designated suspension system, a classic McPherson suspension system is modeled in ADAMS, as shown in Figure 2. The classic parallel wheel travel suspension system analysis can be employed to do system analysis. Vertical bound and rebound of 50 mm are used. By changing the locations of each hardpoint, the corresponding change of kinematic characteristics can be obtained.
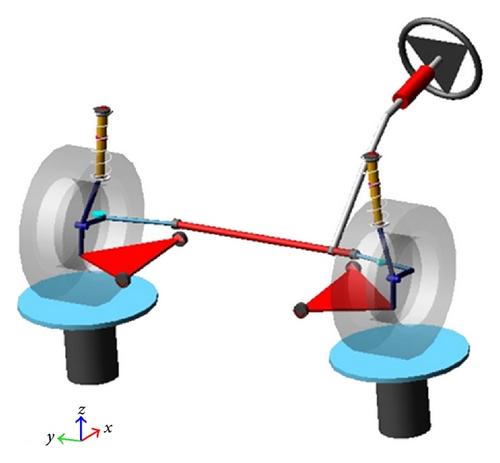
In this study, we take the locations of the 7 key hardpoints labeled in Figure 1 as variables, 3 variables at each hardpoint, that is, the coordinates of the hardpoint along axes x, y and z of the vehicle coordinate. Therefore we have 21 variables (v1–v21) for the designated suspension system. Table 1 listed the 21 variables versus the hardpoint coordinate.
Number | Hardpoint name | Coordinates | Variables |
---|---|---|---|
1 | LCA_front | x, y, z | v1, v2, v3 |
2 | LCA_outer | x, y, z | v4, v5, v6 |
3 | LCA_rear | x, y, z | v7, v8, v9 |
4 | Struct_lwr | x, y, z | v10, v11, v12 |
5 | Tierod_inner | x, y, z | v13, v14, v15 |
6 | Tierod_outer | x, y, z | v16, v17, v18 |
7 | Top_mount | x, y, z | v19, v20, v21 |
For the kinematic characteristics, as stated in Section 2, we choose the camber angle, the caster angle, the kingpin incline angle, and the toe angle as the objective parameters to be designed and optimized. For McPherson suspension system, small variations of the four estimate angles surely are more acceptable. Thus, we choose the four optimization objectives to be the minimum deviations of the four angles versus wheel travel from rebound −50 mm to bound 50 mm.
The initial metamodel is built on the data generated from Latin hypercube sampling [20], which has the following advantages: (1) its sample mean has a relatively smaller variance compared with simple random sampling, (2) it can be used for generating design points when the number of input variables is large and a great many runs are required, and (3) it is cheap in computing and easy for implementation compared with other more complex sampling methods. By using ADAMS batch processing tools, the initial sets samples can easily be obtained. With the built initial metamodel, the adaptive optimization method introduced in Section 3.3 can be used.
The new pair of data, (xM+1, YM+1), together with all the previously collected sample data are used to update the metamodel into a new relationship. The optimization process is stopped when the change of the objective function in several consecutive iterations is less than a predefined value, or the maximum number of iterations is reached.
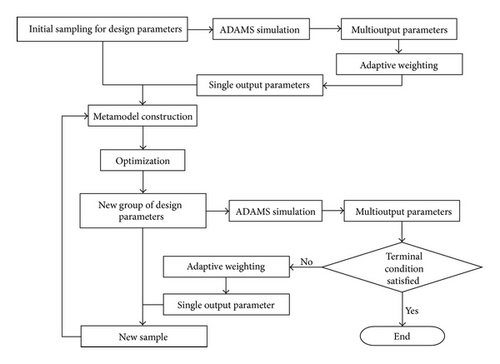
5. Comparisons and Analysis of the Optimization Results
The number of the initial sample is selected as 50 to build the initial metamodel. 50 initial samples may not be enough for a metamodeling problem with 21 variables; however, due to the cost consideration in engineering design, we just initially choose 50 samples and gradually add new samples during the design process. Based on the initial metamodel, more trails are sampled sequentially and adaptively to approach the optimum value. When the total sample size reaches 100, the values of the output parameters are generally stable. We analyze each of the 4 output parameters individually every time while we update the metamodel. For this high dimensional (21D input) problem, 100 samples may not be enough to reach the optimum value. However, we can evaluate its effectiveness through its convergent trend. The optimization results are shown in Figure 4. The value of the objective function is well converged and the variations of the 4 output parameters are generally stable.
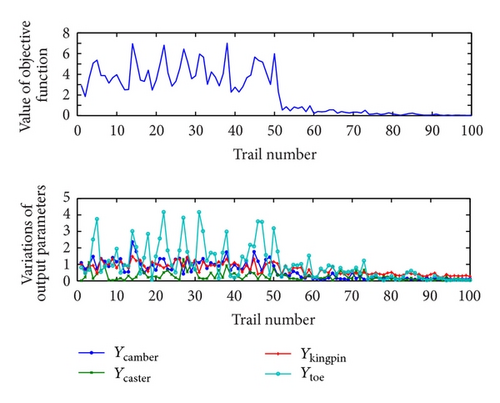
The 4 types of curves with “•”, “×”, “+”, and “o” indicate the camber angle variation, the caster angle variation, the kingpin incline angle variation, and the toe angle variation. The trail distributions from 1 to 50 are obtained from Latin hypercube sampling in the whole design space for building the initial metamodel. From Figure 4, we can see that corresponding to the same design interval (−50, 50), the variation interval for the camber angle, the caster angle, the kingpin incline angle, and the toe angle are (0, 2.5), (0, 4.5), (0, 1.5), and (0, 4.5). While adaptive optimization is applied for the trails from 51 to 100, the variation intervals decrease and the curves become smooth. The adaptive weighting factors help the output parameters with different variation intervals converge to the same variation interval (0, 0.33). It can be seen from Figure 4 that our method succeeds in optimizing the 4 output parameters simultaneously while the value of the objective function is well converged. Table 2 listed the initial and the optimized hardpoints locations for the suspension system. We have chosen the 100th sample as the optimized result.
Variables | Initial | Optimized |
---|---|---|
v1, v2, v3 | 160, −410, 265 | 195.7, −381, 234 |
v4, v5, v6 | −80, −710, 165 | −95, −710.6, 213 |
v7, v8, v9 | 190, −395, 185 | 190.6, −366, 166 |
v10, v11, v12 | 50, −630, 530 | 64.6, −622, 531.3 |
v13, v14, v15 | 155, −440, 355 | 130, −391.2, 305 |
v16, v17, v18 | 210, −700, 240 | 219.5, −749, 290 |
v19, v20, v21 | 7.5, −603.8, 850 | 35.2, −642, 873.6 |
Optimization objective function | Camber angle variation |
Caster angle variation |
Kingpin angle variation |
Toe angle variation |
---|---|---|---|---|
Adaptive optimization considering modeling uncertainty | 0.1056 | 0.0916 | 0.3044 | 0.0577 |
Regular adaptive optimization | 0.1616 | 0.1585 | 0.4717 | 0.1045 |
α | 53.03% | 73.03% | 54.96% | 81.11% |
From Table 3, we could see that the adaptive optimization method with consideration of modeling uncertainty performs better. The adaptive optimization performs better up to 81.11% for all the four output parameters. The reason should be that the number of sample points is far from sufficient to build an accurate metamodel, especially at the very beginning. Thus the optimization result based on the built metamodel only considering predicted mean value may not converge to the right direction. With the prediction standard deviation being considered at the same time, the inaccuracy of the metamodel can be compensated to some extent to approach the right direction.
What is interesting is that the approach can illustrate a suggested trend that the hardpoints should be moved over to. Figure 5 shows the approximate trends that the hardpoints tierod inner and tierod outer stay around during the optimization procedure, and other hardpoints perform similarly. From this figure, it can be seen that the 3 coordinate values for each input parameter tend to change in a smaller interval rather than change in the original design interval (−50, 50). This result from our research can help to reduce the design space in the process of adaptive optimization, in order to greatly improve the optimization efficiency, which would be especially significant for higher dimensional problems.
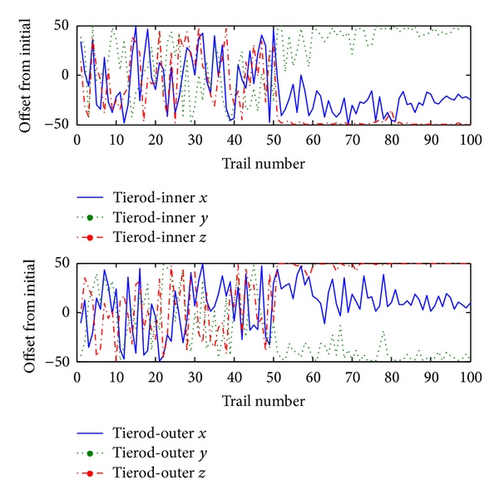
The apparent result that the optimization procedure can achieve is reducing the variation of the design objectives. Figure 6 gives the variations of the camber angle, the caster angle, the kingpin incline angle, and the toe angle, versus the wheel travel for the optimized trail number 100 and the initial trail during the parallel suspension travel analysis. We can see that the optimized data significantly reduced the variation of the camber angle, the kingpin incline angle, and the toe angle, while also slightly reducing the caster angle. This shows the effectiveness of the proposed approach on guiding to search for the optimized solution for kinematic performance design of vehicle suspension systems. Other related parameters can be considered in a similar way.
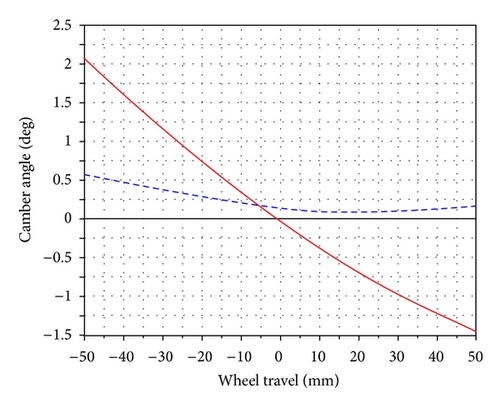
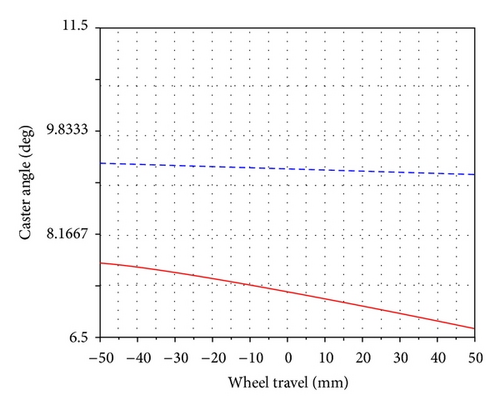
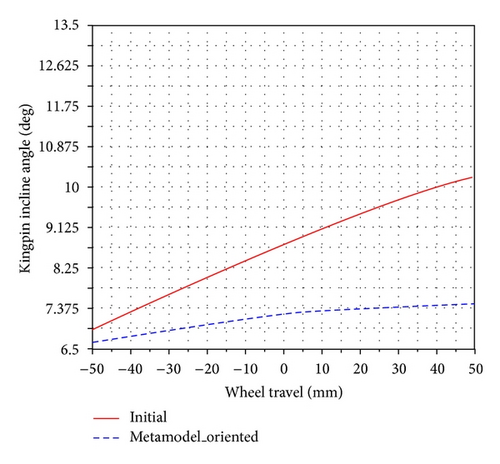

6. Conclusion
This study introduced adaptive metamodel-based optimization considering modeling uncertainty to optimize the kinematic performance of a McPherson suspension system. The optimization design problem is of 21 input parameters and 4 output parameters. The multioutput optimization in the McPherson suspension system is transformed to a single output optimization problem using adaptive weighting factors. 50 initial samples and 50 sequential trails are generated to analyze the convergent trend of the objective parameters. It shows that the proposed optimization method provided a set of relatively good results of the 4 output objective parameters simultaneously for the 50 sequential trails. Possible optimal design trends of the hardpoints are given as the trail goes on. Comparisons showed that the adaptive metamodel-based optimization method considering modeling uncertainty worked better than general adaptive metamodel-based optimization for the suspension design problem.
Conflict of Interests
The authors declare that there is no conflict of interests regarding the publication of this paper.
Acknowledgment
This work is supported by NSFC Grant no. 11302074.