Performance Evaluation Criterion at Equal Pumping Power for Enhanced Performance Heat Transfer Surfaces
Abstract
The existing equations for the thermal performance evaluation, at equal pumping power for the artificially roughened and smooth surfaced multitube and rectangular duct heat exchangers, have been critically reviewed because the literature survey indicates that a large number of researchers have not interpreted these equations correctly. Three of the most widely used equations have been restated with clearly defined constraints and conditions for their application. Two new equations have been developed for the design constraints not covered earlier.
1. Introduction
Artificial roughness in the form of ribs or baffles has been employed to enhance heat transfer in conventional heat exchangers, gas turbine blade cooling channels, and solar air heaters. However, the enhancement in heat transfer is also associated with significant increase in pressure drop and pumping power. Various thermal performance evaluation criteria, which take account of both heat transfer enhancement and pumping power, have been suggested for these enhanced performance surfaces based on different design constraints and objectives [1–6]. However, the criterion based on equal pumping power for the roughened and smooth surfaces suggested by Webb and Eckert [2] has been most widely used [7–41].
One of the old references where an equation similar to (1) has been given is that of Walker and Wilkie [1] for flow along the axis of a cluster of heated roughened rods in a smooth channel for the fixed mass flow rate and pumping power as constraints and the flow area as variable. Webb and Eckert [2], while discussing three different design objectives for multitube heat exchangers, proposed (1) for the design objective of enhanced heat transfer rate at equal pumping power for the roughened and smooth tubes. However, they developed this equation for a particular set of constraints and this equation is applicable only when a condition of specified ratio of mass velocities through the smooth and rough tubes is fulfilled. These constraints and conditions are discussed later. Many investigators [8–19], while using (1), did not take notice of the condition specified by Webb and Eckert [2] or Walker and Wilkie [1], and some of them [11–19] have used the performance ratio R1 for the square and rectangular ducts without mentioning the modification of the original constraints and condition specified for the multitube exchangers.
The performance ratio given by (2) has been suggested for enhanced surfaces by Bergles et al. [3] when the basic geometry of the exchanger is kept fixed and the mass flow rate is variable for fixed pumping power. These constraints are different from those specified by Webb and Eckert for (1). However, the researchers have, generally, regarded the two as equivalent.
When Re = Res and Pr = Prs, St/Sts = Nu/Nus and (1) will transform to (3). Such transformation is justified only when Re = Res for the constraints and condition of (1), but some of the investigators while using (3) failed to satisfy this condition [20–30]. However, it is worth investigating whether such equation can be developed from fundamentals for design constraints different from those specified by Webb and Eckert for (1) and Bergles et al. for (2).
The performance ratios R1 and R3 have been presented in the form of plots of these ratios versus the relative mass velocity [2], the roughness parameters [8–10, 12], and the friction factor [10] and versus the roughness Reynolds number [11, 33]. A number of researchers [13–23, 25–31] have used Reynolds number as the abscissa parameter while Sara et al. [32] preferred Res as the abscissa parameter for the plots of performance ratios. Bergles et al. [3] advocate abscissa Res as a convenient reference for plot of ratio R2 and the same has been used by Sethumadhavan and Raja Rao [34, 35]. However, such choice must be based on some logical ground and not on convenience.
Looking to the above discussion, the following objectives have been outlined for this paper: (i) to critically review the above-mentioned performance ratio equations, and to clearly restate and differentiate between the conditions and constraints for application of (1), (2), and (5); (ii) to specify the conditions and constraints for the application of (3); and (iii) to develop a performance ratio for the rectangular ducts when mass flow rate is kept fixed. To achieve the outlined objectives, the authors have thought that it is necessary to critically review the development of these equations from fundamentals, especially looking to the errors or omissions in application of different performance ratios.
For the development of the performance ratios in the present work, the fluid properties, and the temperature difference between the heat transferring surface and the bulk fluid have been assumed to be the same for both the rough and smooth surfaces. The error due to these assumptions is small for exchangers operating with low temperature differences. The analyses and results are based on the comparison of thermal performances of roughened and smooth channels of equal heat exchange surface area at equal pumping power.
2. Performance Ratio for Multitube Heat Exchangers
In case of heat exchange between fluids on the two sides of a surface, the thermal resistance external to the surface under consideration (including scale, tube wall, and secondary fluid resistances) has been assumed to be the same for the rough and smooth heat exchangers.
For different constraints and mass flow rate conditions, the transformations of the above equations yield the equations of thermal performance evaluation as explained below.
Case (A): Flow Rate and Tube Diameter Fixed, Heat Exchanger Length, and Number of Tubes Variable. Webb and Eckert [2] gave a single expression for the performance evaluation based on the assumptions that the heat exchanger mass flow rate, m, and tube diameter, D, are held constant, and G* is changed by varying number of tubes. For flow through tubes, G* = Res/Re.
Equation (15) has been obtained from (12) and is the same as (4) when put in the terms of the Reynolds number. It means that the values of the Stanton number and friction factor for the smooth duct must be calculated at Res corresponding to Gs. To avoid the confusion, the present authors suggest that the smooth duct variables be written with asterisk (*) to indicate that their values are to be evaluated at different Reynolds numbers.
Webb and Eckert arrived at (14) with the assumption of Ds = D. Hence, the equal surface area constraint yields NsLs = NL. It implies that the length of the equivalent smooth surfaced exchanger will be Ls = (N/Ns)L.
For the given condition of Res = Re, the ratio St/Sts in (20) can be replaced by Nu/Nus, which will give the performance ratio of (3). Since , the ratio of (3) equals h/hs.
It must be noted that (20) of performance ratio is of the same form as (14), but the values of Stanton number and friction factor for the rough and smooth tubes in (20) are to be evaluated at the same Reynolds number.
Case (C): Basic Geometry Fixed and Flow Rate Variable. The performance ratio equation of Bergles et al. [3], given by (2), can be deduced from (7). They assumed a fixed geometry condition (Ds = D, Ls = L, Ns = N), which gives As = A. Equation (4) is satisfied when mass velocity Gs through the smooth tubes is greater than the mass velocity G through the roughened tubes. Therefore, for the fixed geometry constraint, the mass flow rate for the smooth surfaced exchanger will be higher than the mass flow rate for the roughened one. The ratio can be replaced by since Ds = D.
3. Performance Ratio for Rectangular Ducts
The equal pumping power condition for the square or rectangular ducts can be achieved either by keeping duct geometry fixed and changing the mass flow rate or by keeping mass flow rate fixed and changing mass velocity by varying the duct cross-section.
For a duct with heat transfer from all the four walls, the areas for heat transfer and pumping power equations will be equal. While for an asymmetrically heated duct, the two will have different values. However, for a fixed geometry duct, the above given results will be applicable without any change.
For the duct with heat transfer from all the four walls, the surface area A = 2(W + L) ≈ 2WL, and for an asymmetrically heated duct (with broader wall heated), A = WL.
The boundary condition of asymmetric heating of a high aspect ratio duct is encountered in solar air heaters. Gas turbine blade cooling channels are modeled as rectangular ducts of various aspect ratios with heat flux at all the four walls.
4. Presentation of Results
Various performance ratio equations discussed and developed in this paper have been listed in Table 1 along with the constraints and the conditions to be fulfilled. All the geometric and flow parameters have been fully defined.
Investigators | Performance ratio | Constraints | Conditions to be fulfilled |
---|---|---|---|
Multi-tube Exchangers | |||
Webb and Eckert [2] | (St/)/(f/)1/3 |
|
|
Present authors | Nu/ (= h/) |
|
|
Present authors |
|
|
|
Bergles et al. [3] |
|
|
|
Rectangular Duct | |||
Liou and Hwang [36] | Nu/ = h/ |
|
|
Present authors |
|
|
|
- *The parameters with asterisk (*) are to be evaluated at the Reynolds number Res defined in column 4.
Basically, all the tabulated performance ratios are heat transfer enhancement ratios. They are of two forms: either h/hs when Dhs (or D) ≠ Dh (or D) or when Dhs (or D) = Dh(or D). However, the ratio for heat transfer between two fluids cannot be replaced by . It is to note that the choice of the performance ratio depends on the constraints of the application. It is also desirable that an investigator using any of the performance ratio equations should explicitly mention the design constraints associated with that equation and also the conditions to be fulfilled.
For the two out of the six performance ratios given in Table 1, the Reynolds numbers for the rough and smooth surfaces are equal, that is, Re = Res. Therefore, Re or Res is a logical parameter for the plots of the performance results when these criteria are used. For the remaining four performance ratios, values of the Stanton number and friction factor for the roughened and smooth surfaces are calculated at different Reynolds numbers. Further, the roughness parameters, such as the relative roughness height, pitch, and orientation of the roughness elements with respect to the flow, are not having any meaning for a smooth surface. Therefore, neither the Reynolds number nor the roughness parameters can be the logical abscissa parameter for presentation of the performance of the roughened surfaces versus a smooth surface when these four criteria are applied. In these cases, the common parameter for the smooth and rough surfaces is or (f1/3Re). Some researchers have used this abscissa parameter for enhanced performance rectangular ducts as mentioned earlier.
It must be noted that the value of the friction factor for the smooth channel in the equation corresponds to the Reynolds number Res and, therefore, this equation must be converted to an explicit form by substitution of friction correlation of smooth duct and rearranging the terms. In case of a heat exchanger with heat transfer between two fluids, the present criteria represent upper limits to heat transfer enhancement [3]. Once the preferred type of roughness is selected, the thermal resistances external to the enhanced surface and effects of variable fluid properties may be considered.
4.1. Application to Solar Air Heater Ducts with Roughened Absorber Plate
In order to illustrate the application of the performance evaluation criteria presented above for high aspect ratio rectangular ducts with asymmetric heating, data from an earlier experimental study of the first author [42] have been used. The flow and thermal boundary conditions of the roughened duct of their study correspond closely to those of solar air heater ducts. The discrete and discontinuous repeated rectangular cross-section rib roughness arrangements employed in the study are shown in Figure 1. The ribs have been arranged in both v-up and v-down patterns. They compared the thermal performance of different rib arrangements based on equal pumping power for roughened and smooth ducts using performance parameter defined by (25) and presented the performance plots of this parameter versus the parameter f1/3Re as shown in Figure 2. The constraints and conditions for the application of this criterion, as detailed in Table 1, are basically fixed geometry and reduced flow rate for the roughened ducts. It is an appropriate criterion when the smooth surfaced absorber plate of an existing solar air heater is replaced by a roughened absorber plate.
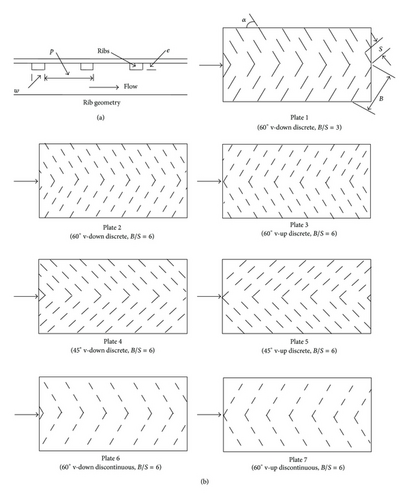
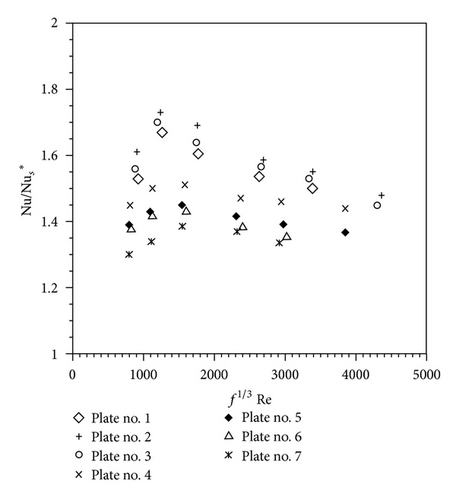
Alternatively, the thermal performance at equal pumping power has been presented in Figure 3 as plots of versus the Reynolds number. The basic conditions and constraints, as outlined in Table 1, are those of equal mass flow rates for smooth and roughened ducts and an increased height of the roughened duct as compared to the smooth duct.
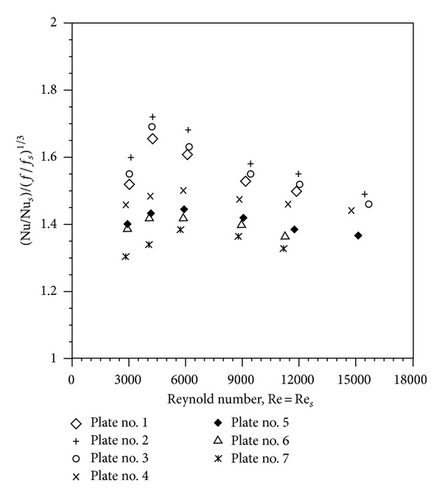
It is interesting to note that the ordinate values of the above discussed performance plots and hence the conclusion drawn from these plots regarding the selection of the preferred roughness type are the same. But the first criterion specifies the operational condition of reduced flow rate for the existing solar air heater when the smooth surfaced absorber plate is replaced by a roughened one, while the second criterion gives design recommendation of increased duct height for the roughened duct solar air heater.
5. Conclusions
Various existing equations for the thermal performance evaluation at equal pumping power for the roughened and smooth surfaced multitube and rectangular duct heat exchangers (such as solar air heater and gas turbine blade cooling channels) have been critically reviewed. The design constraints and conditions for their application have been explicitly stated. Two new performance ratio equations have been developed for the constraints not covered earlier. Finally the logical abscissa parameters for the plots of performance evaluation results have been suggested.
Nomenclature
-
- A :
-
- Heat transfer surface area [m²]
-
- B/S:
-
- Relative roughness length of discrete ribs [—]
-
- cp:
-
- Specific heat of air [Jkg−1K−1]
-
- D:
-
- Pipe inside diameter [m]
-
- Dh:
-
- Hydraulic diameter of duct = 4WH/[2(W + H)] [m]
-
- e:
-
- Rib height [m]
-
- e/Dh:
-
- Relative roughness height [—]
-
- f:
-
- Fanning friction factor [—]
-
- G:
-
- Mass velocity [kgs−1m−2]
-
- G*:
-
- Relative mass velocity = Gs/G [—]
-
- h:
-
- Heat transfer coefficient [Wm−2K−1]
-
- H:
-
- Duct height [m]
-
- k:
-
- Thermal conductivity of fluid [Wm−1K−1]
-
- K:
-
- Overall heat conductance = hA [WK−1]
-
- L:
-
- Length of the flow passage [m]
-
- m:
-
- Mass flow rate [kg/s]
-
- N:
-
- Number of parallel tubes in flow passage [—]
-
- Nu:
-
- Nusselt number [—]
-
- p:
-
- Rib pitch [m]
-
- P:
-
- Pumping power [W]
-
- P′:
-
- Perimeter of rectangular section duct [m]
-
- Pr:
-
- Prandtl number [—]
-
- p/e:
-
- Relative roughness pitch [—]
-
- q:
-
- Heat transfer rate [W]
-
- Re:
-
- Reynolds number, DG/μ or DhG/μ [—]
-
- St:
-
- Stanton number, h/(Gcp) [—]
-
- ΔT:
-
- Temperature difference [°C]
-
- U:
-
- Overall heat transfer coefficient [Wm−²K−¹]
-
- w:
-
- Width of rib [m]
-
- W:
-
- Width of the duct [m].
Greek Symbols
-
- Δp:
-
- Pressure drop [Pa]
-
- μ:
-
- Viscosity of fluid [Pa s]
-
- ρ:
-
- Density of fluid [kg/m3].
Subscript
-
- s:
-
- Smooth surface—unsubscripted variables refer to rough surfaces.