Improved Pressure Distribution in Elliptic Elastic Contacts between High-Order Surfaces
Abstract
The improvement of mechanical contacts or microcontacts seeks a nearly uniform current density over most of contact area. When microtopography is homogeneous, this aim is achieved if nominal shape of contacting surfaces yields a nearly uniform central pressure which decreases monotonously to zero in contour points. These authors derived recently this shape for circular contacts by employing high-order surfaces. This paper extends this result to elliptical contacts. Some results are used to this end, derived for elliptical elastic contacts between high-order surfaces. As homogeneous high order surfaces lead to a highly nonuniform pressure distribution, central pressure is flattened by making the first derivatives of pressure vanish in contact center. Then, the contacts between fourth, sixth, and eighth, order surfaces are analyzed and recurrence relations for pressure distribution and contact parameters are proposed.
1. Introduction
Both high-load-carrying capacity of the contact and the avoidance of pressure and stress risers require a contact pressure distribution as even as possible over most of contact area. Shape improvement of circular contacts uses a pressure distribution made of a central plateau surrounded by a narrow annulus of monotonous decrease to zero [1]. Such a pressure distribution yields if the equivalent rigid punch is bounded by polynomial surface of a higher order than two [1]. Hertz theory fails when dealing with such surfaces. Therefore, a new Hertz kind of theory is needed for high-order bounding surface.
For revolution surfaces, Shtaerman [2] proofed that a rigid punch of equation z ∝ r2n, pressed against an elastic half-space, generates a pressure expressed by the product between an even order polynomial in radius r, of degree 2n − 2, and typical Hertz square root , a being the outer contact radius. Klubin, and later on Popov, quoted in [3], found that a pressure given by the ratio of a Legendre polynomial of order 2n, P2n, to the Hertz square root generates a normal surface displacement which, within the circle, is proportional to P2n.
For elliptical contact domains, Shtaerman [2] showed that a pressure written as the ratio between an even order polynomial of degree n in 1 − ρ2 and typical Hertz square root gives rise to a surface potential expressed by an even polynomial of degree 2n in x and y when applied to an elastic half-space. This potential leads to an explicit integral expression of normal displacement in the points of bounding plane. In 1953, Galin [3] proved the following theorem: if a punch of front surface described by a polynomial of degree n is pressed against an elastic half-space over a domain bounded by an ellipse of semiaxes a and b, the contact pressure can be written as the ratio between another polynomial, of the same degree n, and Hertz square root. Gladwell [4] supplied an alternative proof of Galin’s theorem for a general anisotropic half-space. For transversely isotropic half-spaces, Gladwell found a polynomial for the displacement, expressed by definite integrals, when the pressure is the ratio between associated Legendre function and typical Hertz square root. The problem of normal indentation of an elastic half-space by a rigid frictionless axisymmetric punch described by a fractional power series of radial coordinate was analyzed by Borodich [5].
Later on, these authors [6] found that circular contacts bounded by even monomial surfaces of order 2m lead to a nonuniform pressure distribution, having a local minimum in contact center, a circumferential maximum near contact boundary, and zero value in contour points. This pressure distribution was improved by imposing that the difference between current and central pressures p(r) − p0 possesses a multiple root in the origin of multiplicity order 2m − 2. Because all odd order derivatives vanish in the origin, this requirement is satisfied if all even order derivatives of pressure, up to order 2m − 2, are zero for r = 0. These conditions yield the required central pressure plateau.
This paper derives a similar procedure for elliptic elastic contacts between high-order surfaces aiming to get a flat central pressure. A generalized Hertz pressure of order n is chosen to this end. This is defined as the product between typical Hertz square root H and an even polynomial of degree n in a−2x2 + b−2y2, Pn(a−2x2 + b−2y2), and of order 2n in x and y. First, a recurrence relation is derived for the coefficients of polynomial Pn which yield pressure distributions possessing a flat central plateau. Then the paper derives the surfaces of equivalent punches which generate the proposed pressure distribution when the punch is pressed against an elastic half-space. Finally, equations are derived for contact parameters, namely, contact ellipse half-axes, maximum central pressure, and normal approach or indentation of half-space.
2. Basic Equations
Equation (6), in which Ik is given by (4), defines an explicit one to one correspondence between generalized Hertz pressure and punch surface. A generalized Hertz pressure of order n yields an even polynomial punch surface of degree 2n + 2 with respect to co-ordinates x and y, with no free term.
3. Contact of Homogeneous Surfaces
4. Flat Central Pressure
These pressure profiles exhibit a well-defined central pressure plateau surrounded by a monotonous decrease to zero in contour points. Moreover, as n increases, the central flat region of pressure distribution extends, whereas maximum pressure decreases. This means that either maximum pressure decreases for the same load or load carrying capacity increases for the same maximum pressure. It is thus obvious that newly proposed pressure distributions are superior with respect to classical Hertz pressure.
5. Punch Surface and Contact Parameters
Once pressure distribution is known, the coefficients ai of polynomial surface of equivalent punch result by coefficient identification in (6). Several surfaces leading to flat central pressure are derived below for n = 1, n = 2 and n = 3 by using the expressions of integrals Ik given in [6].
5.1. Fourth-Order Surfaces
As guessed initially, the surfaces of equivalent punch leading to a flat central pressure are non-homogeneous. They contain all even powers of coordinates, up to 2n + 2.
5.2. Sixth-Order Surfaces
The solution of (48) is found numerically. Once knowing the eccentricity, all remaining coefficients a2, a3, and a5 to a9 result from (40), (41) and (43)–(47). Therefore, surface polynomial possesses only two independent coefficients, in this case a1 and a4, which define ellipse eccentricity. The remaining coefficients must have specific values given by above-mentioned equations.
5.3. Eighth-Order Surfaces
6. Discussion
An improved pressure distribution between elastic bodies bounded by high-order symmetrical surfaces is a generalized Hertz pressure in which coefficients ci result from recurrence (12).
As shown in [7], the newly advanced framework can also be used to get a nearly flat maximum pressure along the line contact. The severe end effects in the contact between parallel cylinders of different lengths can be attenuated by various methods such as partial crowning, hollow ended roller or generatrix profiling, the latter usually based on the logarithmic profile proposed by Lundberg [8]. Reusner [9] evidenced the advantages of a new special logarithmic profile used by SKF, while Teutsch and Sauer [10] advanced a fast method for roller-race contact analysis in roller bearings, based on a theoretical and implicit load-deflection relationship.
In the framework reviewed and extended herein, maximum extension of flat central pressure results if pressure coefficients for a given polynomial order are adequately chosen. Following this idea, a different approach to end effect attenuation in elastic finite length line contact between revolution bodies was advanced in [7], by allowing the roller generatrix to be a polynomial yielding a nearly flat maximum pressure along most of the contact length. A special choice of polynomial coefficients results in a contact width constant along most of the contact length, which can be interpreted as a contact area in a modified line contact. The central region of contact width increases with the degree of the surface polynomial. Eventually, the generatrix of the equivalent rigid roller, found numerically by aid of interference equation, proves to be a high-order even polynomial. For imposed load, contact area extents and degree of the polynomial, the procedure advanced in [7] establish a convenient pressure distribution in line contacts, which in its turn yields to a symmetrical polynomial roller generatrix and a central roller cross radius. While coefficients ai yielding the equivalent punch surface need to be recomputed every time a perturbation is introduced in the input (i.e., in load, contact half-axes, or surface degree), as they depend explicitly on central pressure and on contact ellipse eccentricity, formulas (12) for ci hold in all cases.
7. Numerical Validation
The frictionless contact of elastic bodies assimilated to elastic half-spaces can be simulated numerically for an irregular initial clearance using the well-known algorithm based on the conjugate gradient (CG) method advanced by Polonsky and Keer, [11]. The method is fast because the rate of convergence of CG is superlinear and robust because there is mathematical proof of convergence for the CG when the system matrix is symmetrical and positive definite.
The system arising from digitization of geometrical condition of deformation with respect to z direction is essentially nonlinear due to presence of rigid-body approach. Early attempts to linearize it resulted in an additional outer loop, in which normal approach was iterated with respect to static force equilibrium. Another difficulty stems from the fact that the contact area, which determines the size of the system having the nodal pressures as unknowns, is also a priori unknown, and a trial-and-error technique is required. Different techniques to overcome these difficulties are overviewed and benchmarked by Allwood, [12].
The algorithm developed by the authors is based on the work reported in [11]. Linearization is achieved by assessing, in every iteration, estimates for the rigid-body translations and rotations, the latter being related to bending moments transmitted through conformal contacts [13]. These estimates are numerically derived through the least square method, as the best fit of an overdetermined system of equations, assembled from equations corresponding to grid cells included in the current contact area. In order to force the solution to verify the static equilibrium equations, a correction of pressure is imposed after every iteration in the CG algorithm. The size of the system, that is, the contact area, is also adjusted at every CG cycle, according to boundary conditions expressed in terms of pressure and gap. Although the algorithm is essentially based on one level of iteration only, a reset of descent directions in the CG minimization process is required every time the contact area changes.
On every iteration of the CG, two convolution type products must be calculated. The order of computation of O(N2) when using direct multiplication—summation can be reduced significantly to O(Nlog N) if convolution is performed in the frequency domain, as element-wise multiplication. The errors introduced by problem periodization, implicitly assumed when the spatial series of pressure and influence coefficients are transferred to frequency domain via fast Fourier transform are avoided with a minimal additional computational cost using the Discrete Convolution Fast Fourier Transform (DCFFT) technique advanced by Liu et al. [14]. The computer code obtained using the CG combined with the DCFFT technique is fast enough to solve grids of up to 106 points in the contact area in a reasonable amount of time, allowing for simulation of deterministic rough contact scenarios.
An implementation of this algorithm is used herein to validate the framework for the smooth contact between high-order surfaces. The initial contact clearance fully authorizes the use of half-space assumption, allowing for the use of appropriate Green functions when computing free-surface deflections.
All simulations are performed with a normal load Q = 1 kN. The data used for validation was generated by imposing a major half-axis of contact ellipse of 1 mm and an aspect ratio of contact ellipse β = 0.5, using appropriate formulas advanced in this work (see Table 1). With these parameters fixed (but otherwise arbitrarily chosen), contact geometry was readily available as input for the numerical program, as all terms ai can be computed explicitly, using corresponding closed-form relations advanced in this work.
To assure that the discretization error is reduced to an acceptable level, a 256 × 256 uniformly spaced rectangular grid, usually assumed for smooth contact scenarios, was imposed in a surface domain exceeding with 20% symmetrically the contact axes predicted by the analytical framework. The imposed precision for pressure convergence was fixed at ε0 = 256−3/2, according to numerical experimentations reported in [11].
The predictions of the numerical program are found to agree well with the closed-form relations advanced in the theoretical framework, as shown in Tables 2, 3, and 4. The most important errors are found when assessing contact half-axis and can be attributed to grid resolution, as the numerical prediction for this parameter can only vary with integers of grid steps. The analytical and numerical solutions for pressure profiles along contact major half-axis are depicted in Figure 1. Dimensionless pressure is defined as ratio to Hertzian pressure corresponding to the imposed load and contact area.
Contact major half-axis, | Central pressure, | Rigid-body approach, | ε, (%) | |
---|---|---|---|---|
a, (m) | p0, (Pa) | δ, (m) | ||
Analytical | 1e − 3 (imposed) | 7.9577e + 8 | 8.3660e − 6 | 5.4011e − 2 |
Numerical | 9.9844e − 4 | 7.9567e + 8 | 8.3659e − 6 |
Contact major half-axis, | Central pressure, | Rigid-body approach, | ε, (%) | |
---|---|---|---|---|
a, (m) | p0, (Pa) | δ, (m) | ||
Analytical | 1e − 3 (imposed) | 7.4272e + 8 | 8.1336e − 6 | 6.0842e − 2 |
Numerical | 9.9844e − 4 | 7.4268e + 8 | 8.1335e − 6 |
Contact major half-axis, | Central pressure, | Rigid-body approach, | ε, (%) | |
---|---|---|---|---|
a, (m) | p0, (Pa) | δ, (m) | ||
Analytical | 1e − 3 (imposed) | 7.1620e + 8 | 8.0065e − 6 | 6.4630e − 2 |
Numerical | 9.9844e − 4 | 7.1629e + 8 | 8.0068e − 6 |
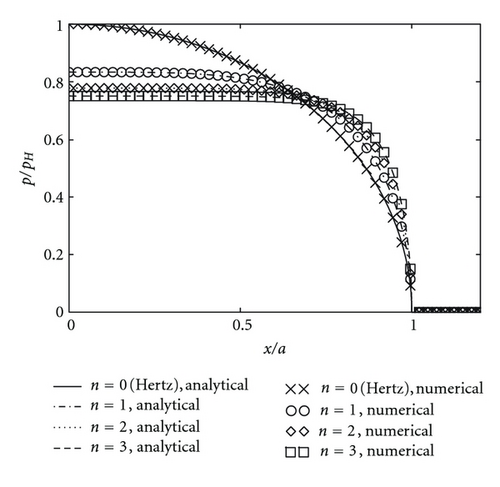
As shown in [15], a central plateau of uniform pressure can also be found in the elastic-plastic nonconforming contact, when the residual term of displacement and of subsurface stresses becomes significant. The residual print due to permanent deformation of the surface, acting together with the hardening of the elastic-plastic material, decrease the central pressure computed according to the elastic model. The elastic-plastic material responds to loading by developing residual stresses, which decrease stresses induced by pressure, as to oppose further plastic yielding. In the framework proposed herein, the flattened pressure plateau results in purely elastic conditions, and is related only to the fine-tuning of the surface profile. It is clear that the newly advanced indenter will accommodate larger loadings prior to yield inception compared to the quadratic one, when the same contact area is established.
8. Conclusions
Pressure distribution in elastic elliptic contacts between high-order homogeneous surfaces is nonuniform, possessing a local minimum in contact center, maxima in peripheral region, and zero value in contour points, thus reducing the load carrying capacity of the mechanical contact.
A more advantageous pressure distribution must possess a flat central region surrounded by a peripheral monotonous decrease to zero. Such pressure distribution yields from a generalized Hertz pressure if coefficients ci result from a recurrence equation. As the degree of generalized Hertz pressure increases, the central plateau of pressure extends and maximum pressure decreases, giving overall a better pressure distribution.
The surfaces of equivalent rigid punch generating these favorable pressures when pressed against an elastic half-space are nonhomogeneous and contain all even power terms up to 2n + 2. Analytical expressions of surface coefficients involve η, p0, a, b, and algebraic combinations of complete elliptical integrals of first and second kind. Only two of these coefficients can be independent to get an elliptical contact area. Although these can be arbitrarily chosen, it is convenient to take a1 and an+2 as the independent coefficients yielding contact eccentricity. All remaining parameters result from equations proposed in the paper.
Analytical expressions of contact half-axes a and b, maximum pressure p0, and normal approach δ are derived by similarity to Hertz equations for fourth, sixth, and eighth order surfaces. These are expressed as roots of order 2n + 3 of involved parameters and they can be applied directly to calculate contact elements.
General or recurrence equations are established for main contact parameters, which reduce to the results derived in here when n = 1, n = 2, and n = 3. The newly advanced formulas are verified well by a numerical program for the elastic contact with known, but otherwise arbitrarily distributed initial clearance, giving confidence in the proposed framework.
Nomenclature
-
- A :
-
- Contact domain or contact area;
-
- :
-
- Typical Hertz square root;
-
- K, E :
-
- Complete elliptical integrals of first and second order, respectively;
-
- :
-
- Symbol for the number of combinations;
-
- a, b :
-
- Major and minor half-axis of contact ellipse, respectively;
-
- :
-
- Eccentricity of contact ellipse;
-
- x, y :
-
- Coordinates in the plane bounding the half-space;
-
- z:
-
- Coordinate along normal in initial contact point;
-
- β = b/a:
-
- Aspect ratio of contact ellipse;
-
- :
-
- Elastic constant of the contact;
-
- ρ:
-
- Elliptic parameter: ρ2 = a−2x2 + b−2y2;
-
- ν1, ν2, E1, E2:
-
- Poisson’s ratios and Young moduli, respectively, of contacting materials.
Acknowledgments
This paper was supported by the project “Progress and development through post-doctoral research and innovation in engineering and applied sciences—PRiDE—Contract no. POSDRU/89/1.5/S/57083”, project co-funded from European Social Fund through Sectorial Operational Program Human Resources 2007–2013.