Non-Newtonian Effects on the Squeeze Film Characteristics between a Sphere and a Flat Plate: Rabinowitsch Model
Abstract
The use of additives (polyisobutylene, ethylene-propylene, lithium hydroxy stearate, hydrophobic silica, etc.) changes lubricants’ rheology due to which they show pseudoplastic and dilatant nature, which can be modelled as cubic stress fluid model (Rabinowitsch fluid model). The present theoretical analysis investigates the effects of non-Newtonian pseudoplastic and dilatant lubricants on the squeezing characteristics of a sphere and a flat plate. The modified Reynolds equation has been derived and an asymptotic solution for film pressure is obtained. The results for the film pressure distribution, load carrying capacity, and squeezing time characteristics have been calculated for various values of pseudoplastic parameter and compared with the Newtonian results. These characteristics show a significant variation with the non-Newtonian pseudoplastic and dilatant behavior of the fluids.
1. Introduction
The objective of this paper is to extend the results [18–21] to squeeze film characteristics between a sphere and a plate by introducing a quantitative analysis using Rabinowitsch fluid model, which accounting for the effect of additives in the lubricant. The modified Reynolds equation governing the squeeze film pressure is derived. Squeeze film characteristics such as film pressure, load-carrying capacity, and squeezing time are presented. The importance of the present analysis lies in that the earlier theoretical investigations on sphere-plate squeezing [11–14] are based on couple stress or micropolar fluid models, which suffer the scarcity of experimental verification.
2. Constitutive Equations and Boundary Conditions
The physical configuration of a sphere-plate system is shown in Figure 1. The sphere is approaching towards the plate with a normal velocity (), separated by a lubricant thin film. The lubricant in the system is taken as a non-Newtonian Rabinowitsch fluid. The body forces and body couples are assumed to be absent.

3. Analysis
3.1. Load Carrying Capacity
3.2. Squeezing Time
4. Results and Discussions
Based on the Rabinowitsch fluids model, the effects of non-Newtonian rheology on the squeeze-film characteristics between a sphere and a plate are investigated using a dimensionless parameter α which accounts for the non-Newtonian nature of the lubricant, that is, for the induced nature due to the use of additives. The parameters α = 0, α < 0, and α > 0 describe the Newtonian, dilatant, and pseudoplastic lubricants, respectively. For the validity of the analysis, the numerical results for non-Newtonian lubricants are compared with the Newtonian results [12].
- (i)
- (ii)
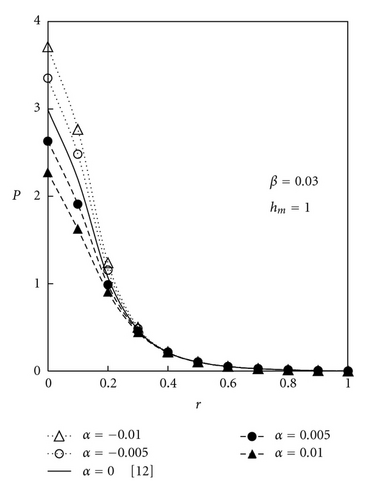
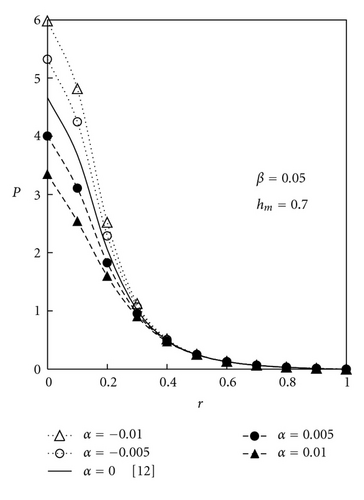
Figure 3 shows the variation of dimensionless maximum film pressure (pmax ) with respect to the dimensionless minimum film thickness (hm). The effect of dilatant lubricants is observed to increase the maximum film pressure from its value in Newtonian case whereas the effect of pseudoplastic lubricant decreases the maximum film pressure from its value in the Newtonian case. Furthermore, the maximum pressure increases with the decrease of pseudoplastic parameter α from 0.01 to −0.01. There is also a relative change in the maximum pressure for pseudoplastic and dilatant lubricants, which increases with the decrease of film thickness. For the sphere parameter β = 0.05, a small value of pseudoplastic parameter α = − 0.01 increases the maximum film pressure by nearly 12% to 25% as the minimum film thickness hm decreases from 1 to 0.7. For the same value of β and hm, the value of pseudoplastic parameter α = 0.01 (pseudoplastic fluids) decreases the film pressure nearly 15% to 30%. Therefore, it can be safely said that the higher the film pressure, the greater the change produced by pseudoplastic and dilatant lubricants is.
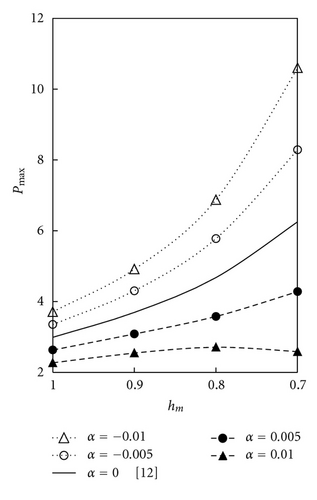
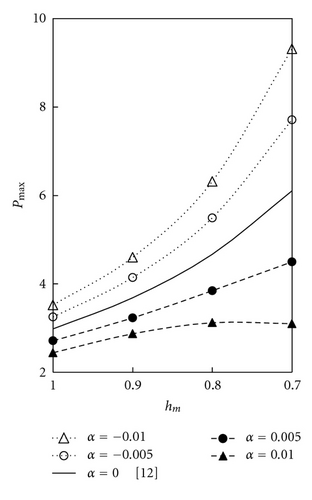
Figure 4 shows the variation of dimensionless load carrying capacity (W) of the system with respect to the dimensionless minimum film thickness (hm). It is observed that the load capacity obtained with dilatant lubricants is higher than that with Newtonian lubricants, and the load capacity obtained with pseudoplastic lubricants is lower than its value obtained with Newtonian lubricants. Furthermore, the load capacity increases with the decrease of pseudoplastic parameter α from 0.01 to −0.01. It is also observed that there is a relative change in load capacity obtained with the different values of pseudoplastic parameter, which increases with the decrease of film thickness. For the sphere parameter β = 0.05, the effect of dilatant lubricant α = − 0.01 increases the load capacity by 10% to 15% as the minimum film thickness hm decreases from 1 to 0.7 and for the same value of β and hm, the effect of pseudoplastic lubricants α = 0.01 decreases the film pressure from 15% to 20%.
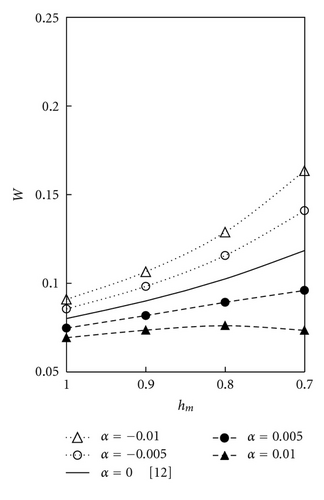
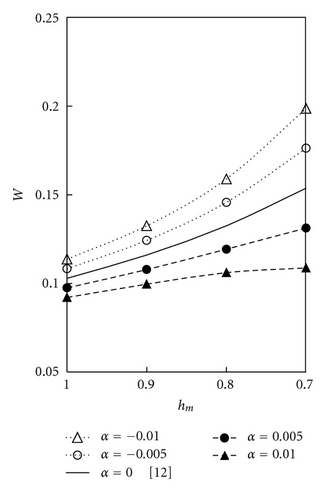
Figure 5 shows the time (t) elapsed in squeezing the film from its initial thickness hm = 1 to a final thickness hm = hf. It is observed that for each value of hf and β, the squeeze time for dilatant lubricants is longer than that with the Newtonian lubricants, whereas, the squeeze time for pseudoplastic lubricants is less than its value in the Newtonian case. Further, the squeeze time increases with the decrease of pseudoplastic parameter from 0.01 to −0.01. This phenomenon can be interpreted as a result of the increase in the film pressure from pseudoplastic to dilatant lubricants. For the sphere parameter β = 0.03, the time to squeeze the film to hf = 0.7 is increased by nearly 23% with dilatant lubricant α = − 0.01 in comparison with the Newtonian case, whereas the same is decreased by nearly 18% for pseudoplastic lubricants. For the sphere parameter β = 0.05, the time to squeeze the film from h = 1 to h = 0.7 is increased by nearly 14% with dilatant lubricant α = − 0.01 in comparison with the Newtonian case. For the same value of β and hf, the squeeze time is reduced by nearly 16% with pseudoplastic lubricants α = 0.01. Thus, dilatant lubricants increase and pseudoplastic lubricants reduce the squeeze time of the bearing.
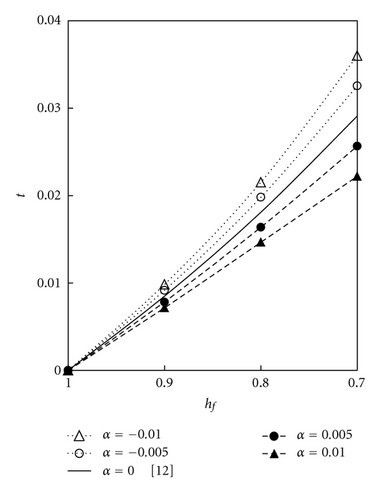
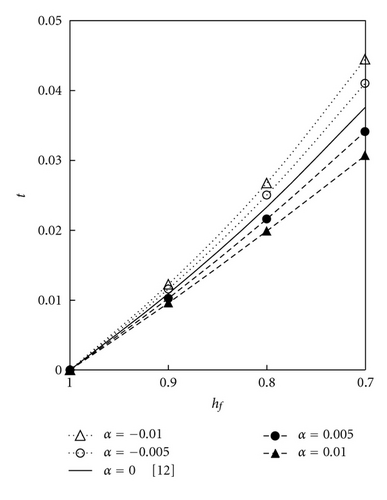
5. Conclusions
- (1)
Dilatant lubricants increase the pressure and load carrying capacity significantly, whereas the case is reversed with the pseudoplastic lubricants.
- (2)
On comparing with the Newtonian case, dilatant lubricants increase the squeeze time, whereas the pseudoplastic lubricants decrease it.
- (3)
As the squeezing time of the sphere-plate system is significantly increased with the dilatant lubricants, it is expected that the use of additives can reduce the vibration in the sphere-plate systems.
Nomenclature
-
- −:
-
- Bar denotes the dimensional quantities
-
- :
-
- Film thickness defined in (9),
-
- :
-
- Minimum film thickness,
-
- :
-
- Initial minimum film thickness
-
- :
-
- Film pressure,
-
- po, p1:
-
- Dimensionless perturbed film pressures
-
- :
-
- Radial coordinate,
-
- R:
-
- Radius of sphere
-
- :
-
- Time,
-
- :
-
- Components of velocity
-
- :
-
- Load capacity,
-
- α:
-
-
- β:
-
- Design parameter
-
- :
-
- Coefficient pseudoplasticity
-
- :
-
- Viscosity of lubricant
-
- :
-
- Stress component.
Acknowledgments
The authors, hereby, thank Dr. M. Fillon (Director of Research, Centre National de la Recherche Scientifique, University of Poitiers) and Dr. V. K. Kapur (Former Professor and Chairman, KNIT, Sultanpur, India) for providing useful materials and guidelines to enhance the content of the paper.