Improving product performance by forming surface compositions from shape memory effect materials with a gradient of properties and phase transformation temperatures
Abstract
We have developed a flow chart for structure and architecture of multilayer surface composition made of multicomponent materials with shape memory effect (SME materials) for different purposes. These compositions have different temperatures of phase transformations. Complex technology of surface composition was carried out in a proprietary installation in conditions of complex high-energy effects. These effects included mechanical activation of deposited powder material, high-velocity oxygen fuel spraying with the subsequent thermal, and thermomechanical treatment in a single vacuum cycle with the ability to supply powder to different zones of the gas flow. The deposition sequence of functional layers, their composition, thickness, structure-phase state, and dispersity are determined by operating conditions and control of the processing mode. For example, surface composition, “Steel-Ni-TiNiZr-TiNiCo,” shows that the use of SME materials allows to create a surface composition, which is functionally oriented not only to improve the performance properties, such as wear strength and corrosion resistance, but also to improve durability and vitality because of the special properties of materials with shape memory composition and architecture. Experimental studies have demonstrated the effectiveness of technologies developed in improving the performance properties.
1 INTRODUCTION
In modern engineering, multifunctionality is a brand new requirement for competitive materials.1-5 Given the crucial role of the surface layer in damage accumulation and destruction, the task of ensuring multifunctionality, as well as increasing reliability and resource, can be successfully solved at the finishing stage of processing using technologies based on the principles of layer-by-layer synthesis by means of combined, functionally oriented macro-, micro-, and nanotechnology.5, 6
To increase the reliability and operational characteristics of products, we have developed a number of devices and technologies using materials with a shape memory effect (SME): a bypass device for space lithium-ion rechargeable batteries; technology to increase the durability and life cycle of the ship's propeller blades, a composite crankshaft in which the crank cheeks with the main and crank journals are connected using material with an SME, bolted connection with material elements with an SME for working under vibration conditions, details a centrifugal pump for operation in conditions of increased abrasive wear at oil production facilities; patent No. 2667571). Known is an innovative approach for applying coatings from an alloy with a SME based on TiNi as applied to aircraft structural elements to weaken the deformation of the underlying base (fuselage body and aircraft wing) in order to increase rigidity while ensuring strength, integrity of damaged structural elements and corrosion protection, and use massive TiNi coatings obtained by explosion welding as an active component of a multiple-action thermomechanical drive capable of restoring not elastic deformation even in the presence of opposing forces.
A promising direction in the layered synthesis technologies is the intellectualization of products using materials with SME (SME materials). These materials have a wide range of functional and mechanical capabilities: effects of thermomechanical memory and superelasticity, high strength and damping properties, thermomechanical reliability and durability, and wear and corrosion resistance. This is especially important in the conditions of the so-called unmanned production technologies or limited personnel technologies (nuclear power, aviation, and space technology). The use of SME materials as surface layers1, 2 or as part of a layered structure can provide an effective response of materials to external factors and the use of micro- and nanotechnology provides self-diagnosis and their adaptation to external influences. At present, there is a number of technologies for surface layers with two-component (TiNi and NiAl), three-component, and four-component (TiNiHf, TiNiHfCu, TiNiZr, TiNiMo, and TiNiNb)2, 7 SME materials using laser and argon-arc welding, plasma, and high-velocity oxygen-fuel spraying (HVOF) as well as surfacing by an explosion.1 The researchers have obtained durable and reliable surface layers of the desired thickness and dispersion.5, 7, 8 The purpose of this study is to develop a composite design of multifunctional surface layers made of SME materials with a gradient of functional and mechanical properties in depth, in the context of complex high-energy effects in order to increase reliability and increase the life cycle of engineering products.
2 METHODS AND RESULTS
2.1 Technology of composition formation
The complex formation process of a multifunctional composition using SME materials for working under multifactor effects (cyclic loading, reverse friction, and media exposure) includes the following steps: analysis of the requirements for the product; the choice of the chemical composition of functional materials that meet these requirements; selection rationale of the structural-phase state of the layers and the architecture of the surface composition; and preparation of the base and the deposited material, equipment selection for an integrated modification process (Figure 1).
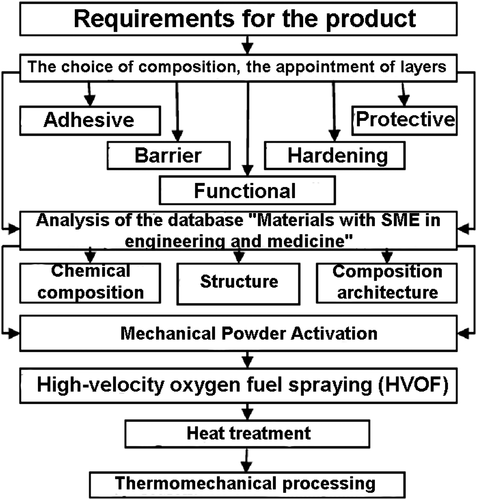
Base preparation includes creating the necessary surface relief to ensure reliable adhesion of the surface layer and the base, as well as surface cleaning. In case of surface layer formation in the vacuum cycle, there is also an ion cleaning of the surface. One of the important steps to ensure the nanostate of the formed surface composition is the preliminary dispersion and mechanical activation of the sprayed material, including the stages of high-velocity deformation, polygonization, and recrystallization.6 Mechanical activation was carried out in a planetary ball mill of the centrifugal type Hephaestus-2 (AGO-2U). Studies have shown that mechanical activation is not only an effective way to optimize the particle size distribution but also allows, due to large plastic deformations, to pump energy into the processed material with the formation of amorphous and nanostructural states. This energy is released during the subsequent surface modification and activates the process of nanostructuring. The mechanism of this process during the formation of surface layers made of SME materials with a thermomechanical treatment based on TiNi is described in Rusinov and Blednova.6
The formation of the surface composition was carried layer by layer by HVOF of multicomponent mechanically activated powders on the upgraded GLC unit (patent number 2535432). Figure 2 shows a technological complex for the formation of a nanostructured surface composition “steel - SME material,” including a (1) vacuum chamber, (2) a gas-flame burner, (3) a control unit, (4) a power source, (5) a compressor, (6) a device for surface plastic deformation, (7) a gas station providing oxygen, (8) argon, and (9) methane. The upgraded GLC-720 unit allows the powder to be supplied by four independent powder dispensers to different zones of the gas stream. In order to impart a multiple reversible SME effect or properties of pseudoelasticity, we performed a TMT. It is a process of surface plastic deformation by rolling a functional layer of a SME material in the temperature range of martensitic transformations with intermediate annealing. When implementing a full processing cycle, layers with ultra-fine crystalline and nanostructure with a grain size from 20 to 170 nm are formed on the surface.
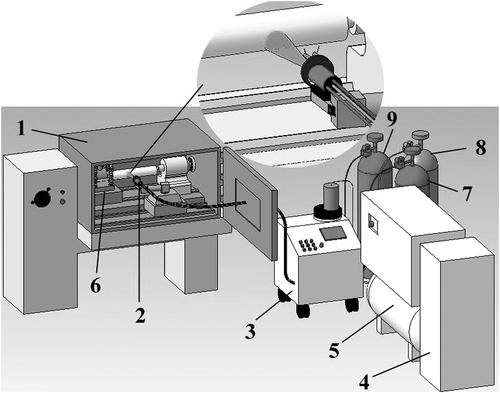
2.2 Materials and research methods
Steel 1045 was used as the base material. TiNi-based multicomponent powder SME materials with different phase transformation temperatures (Table 1) were used as a deposited material in order to control the functional and mechanical properties of the constituent layers under operational conditions with the help of composite design.
The Chemical Composition of the Layers Surface Composition | Temperatures of Phase Transformations, K | |||
---|---|---|---|---|
Мf | Мs | Аs | Аf | |
Ti-48,7%at. Ni-1,3%at. Co | 188.7 | 244.6 | 263.5 | 331.4 |
Ni-33%at. Ti-18%at. Zr | 459.0 | 522.0 | 488.0 | 571.0 |
Ni-30%at. Ti-20%at. Hf | 456.5 | 517.6 | 570.4 | 619.8 |
Ni-44%at. Ti-6%at. Ta | 269.8 | 307.2 | 316.4 | 352.1 |
Ni-36%at. Ti-15%at. Hf-5%at. Cu | 365.4 | 424.3 | 467.2 | 521.3 |
The applied surface layers of the composition were investigated using metallographic, durometric, X-ray diffraction, and spectral analyzes. X-ray phase analysis was performed on a Dron-7M diffractometer in Cu-Kα radiation. X-ray phase analysis of the samples was carried out at room temperature (293-295 K), relative humidity 40% to 50%. The microstructure was examined on a JSM-7500F scanning electron microscope. The temperature of phase transformations of SME material was determined by calorimetric method. To assess the quality of the functional layers and composition, the deposited metal layers were tested for adhesion, microhardness, wear, and fatigue strength. The endurance limit was determined based on the test for high-cycle bending fatigue with rotation on the MUI-6000 machine, with a test base of 107 cycles. The wear tests were carried out on a SMT-1–2070 friction machine, which makes it possible to control the temperature of the sample during the test.
2.3 The results of the study
In order to form the structure and architecture of the surface composition made of SME materials, we used a function-oriented approach for products working under conditions of a wide variety of operational impacts. The multifunctional surface layer was formed on the basis of the principle of a multilayer compositional architecture, each layer of which has its own functional purpose. Figure 3 presents the results of metallographic and X-ray analysis of the multifunctional steel-Ni-TiNiZr-TiNiCo surface composition, operating under multifactor effects: cyclic loading, wear, and sea water. In the case of abrasive wear, the outer wear-resistant layer of TiNiCo can be replaced or the composition can be supplemented with a highly wear-resistant layer with cNB-10% Co (Figure 3).7
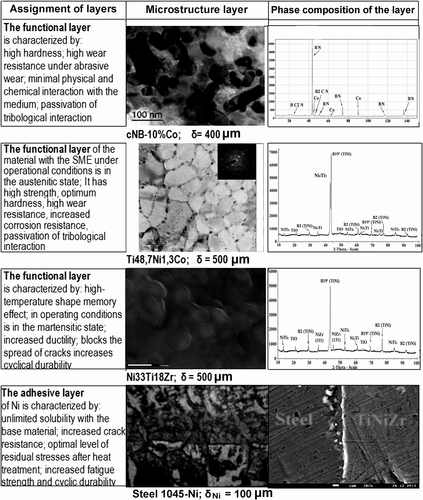
The outer layer, which is in contact with the working medium, must have a high wear resistance with high bearing and damping capacity and corrosion resistance, with an optimal combination of strength and toughness. Multicomponent alloys with a TiNi-based SME in the austenitic state meet these requirements. The purpose of the intermediate layer is to relax the stresses, damp the oscillations, and block the cracks that occur in the outer layer and propagate deep into the material. An intermediate functional layer made of SME materials in the martensitic state, which has an increased elasticity, helps to reduce the stress concentration at the tip of the crack and inhibits or blocks its movement. The gradient of properties in the outer contact and functional layers of SME materials is provided by the temperature gradient of phase transformations, which are set by means of controlling the chemical composition and thermomechanical processing.
When alloy based on TiNi is used as a SME material, it is most advisable to use Ni as a connecting adhesive layer on steel, since Ni and steel base are characterized by unlimited solubility of the main elements. In this case, we observe the crystal chemical affinity of the base material, connective, and functional layers. What is important, all components have similar values of the thermal expansion coefficient.
The peculiarity of the considered surface composition is that, under actual operating conditions, the functional layers of SME materials are in different phase states and are characterized by a gradient of mechanical characteristics of strength, ductility, and elasticity. The functional TiNiZr layer is characterized by a high-temperature SME, and at normal temperature is in the martensitic state. This contributes to stress relaxation, reducing stress concentration in case of cracking or propagation of cracking defects and thus increases the product durability and prolongs its life cycle.5, 8
It is known that alloys based on TiNi have a high corrosion resistance, which is proved by their wide use in medicine. The tests of steel, surface modified by TiNi, (Figure 4) showed that the mass loss in the Black Sea water during aging for 1500 hours at a temperature (293 ± 2 K) amounted to 0.0035 g/m2/h for steel 321, for steel 34NiCrMoV14-5-0.076 g/m2/h, close to zero for TiNi.
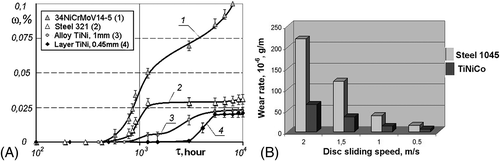
SME alloys also exhibit high resistance to corrosion and erosion wear. From the data given in Table 2, it can be seen that surface modification with TiNi-based SME materials leads to an increase in microhardness, a decrease in wear rate by 3 ÷ 3.5 times (Table 2), and an increase in endurance limit, on average, by 35%. Obviously, the achievement of high wear resistance characteristics of modified layers is greatly influenced by their high corrosion resistance.
Material | Grain Size, nm | Microhardness НV, GPa | The Decrease in Wear Rate, times | Increase Endurance Limit by, % |
---|---|---|---|---|
Ti-NiCo | 30-190 | 9.2-11.6 | 3.0-3.5 | 34.5 |
Ti-Ni-Zr | 80-100 | 9.4-9.5 | 3.5-3.6 | 36.8 |
TiNiТa | 50-90 | - | 3.5-3.6 | 35.6 |
TiNiHf | 80-120 | 9.7-12.6 | - | - |
TiNiHfCu | 95-140 | 9.5-11.8 | - | 36.3 |
The wear resistance of the modified layers is greatly affected by their high corrosion resistance. The high wear resistance of the surface layers made of TiNi SME-based alloy is explained by the effect of deformation pseudoelasticity. The pseudoelasticity of SME alloys leads to the fact that, firstly, in the contact zone of the microroughness of the friction surface, there is a significant increase in the actual contact area. This leads to a decrease in stress concentration, and, consequently, the probability of crack generation. Secondly, with the relative movement of friction surfaces, because of the reversibility of the “plastic” deformation of SME material, the total value of the residual deformation of the material is much less than for traditional wear-resistant materials. Therefore, to achieve the critical value of fracture strain, a much greater stress or test duration is required than for conventional materials.
In the process of testing for wear of samples with the surface layer made of TiNiCo, an increase in the surface temperature in the friction zone and in the intermediate layer is observed, which causes a martensitic-austenitic transformation and an increase in the strength characteristics. At the same time, rather large pressures arising from friction cause the effect of transformation plasticity because of the formation of stress martensite.5, 8 The combination of these processes determines the wear resistance and fatigue strength of the sample.
3 CONCLUSION
We proposed a model of the structure and architecture of a multilayer composite surface layer for products operating under conditions of friction, cyclic loading, and media exposure. The adhesive layer is made of nickel, which has unlimited solubility and high affinity with the base material and functional layer. Functional layers consist of alternating layers of multicomponent SME materials on the basis of TiNi of various dispersity (20-170 nm) and mechanical characteristics with significantly different temperatures of phase transformations. We justified the choice of multicomponent SME materials, which are included in the configuration, structure, and architecture of the composition. We also justified ways to optimize them in order to improve the performance properties and product life cycle. An experimentally confirmed increase in wear resistance is by 3 to 3.5 times, and the endurance limit of samples with a composite surface layer is by 35%.
CONFLICT OF INTEREST
Authors declares no conflict of interest.
FUNDING INFORMATION
The work was performed as part of a grant from the Russian Science Foundation (Agreement No. 19-19-00331).